1000W Laser Cleaning Machine
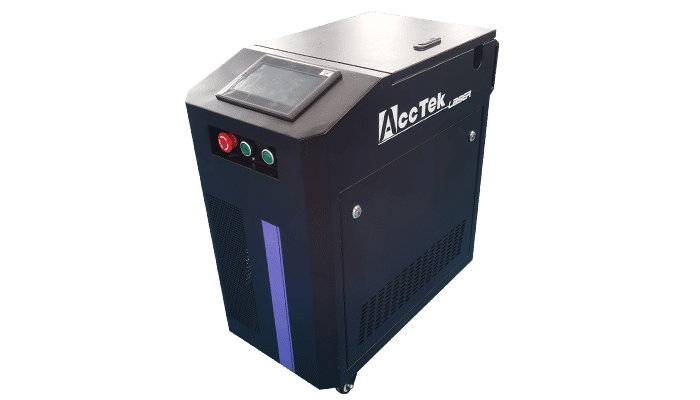
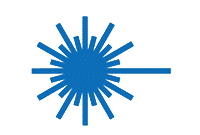
Photoelectric Technology
AccTek Laser focus on designing and manufacturing photoelectric-related system. We provide accurate and exquisite processing quality with leading R&D capability.
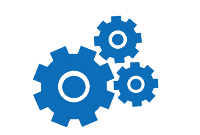
Integration Ability & Experienced
With an experienced, completed, and elite R&D team, customized such as automated, integrated with the robot, system integration, etc. are all available.
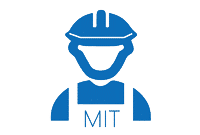
Professional Service
AccTek Laser's laser cleaning machine is a professional laser cleaning machine designed and manufactured in China. Our elite engineering team provides related service support.
Equipment Features
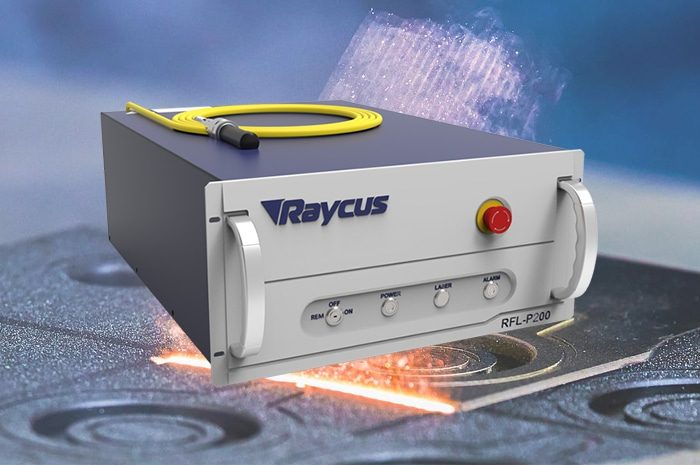
Famous Laser Generator
Using a well-known brand laser generator (Raycus / JPT / Max / IPG), the pulse width and frequency are independently adjustable and can maintain a stable peak power output, suitable for a wider range of cleaning scenarios. The high photoelectric conversion rate ensures the laser power and makes the cleaning effect better. Acctek can design different configurations to meet customer needs.
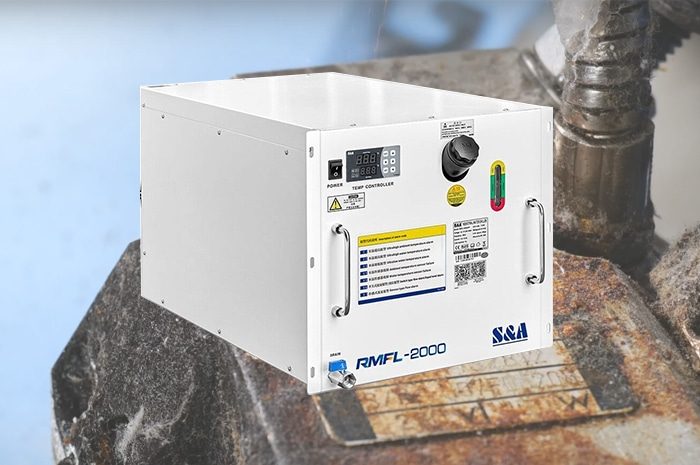
Industrial Water Chiller
The industrial water cooler ensures the heat dissipation of the core optical path components, allowing the welding machine to provide consistent welding quality and helping to improve the overall quality of the weld itself. It can also increase welding output by reducing the downtime of fiber laser welding machines. In addition, an excellent industrial water cooler can also prolong the service life of the laser welding machine.
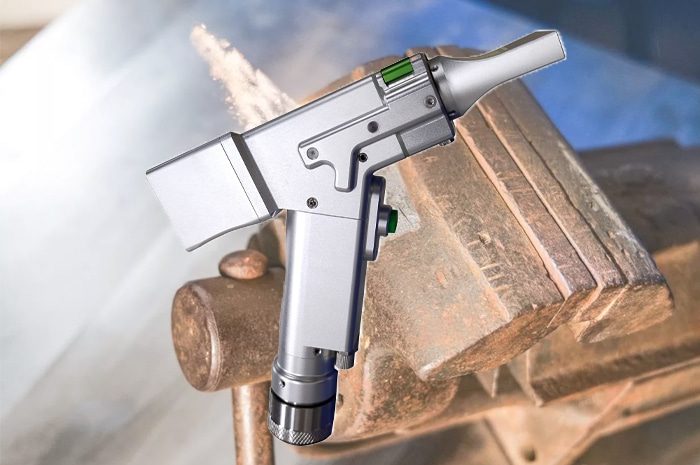
Laser Cleaning Head
The laser cleaning head is ergonomically designed, small in size, comfortable to hold, and easy to control and operate. The hand-held cleaning head is easy to hold and can be used for a long time, and can be operated at any angle, making cleaning more convenient and flexible.
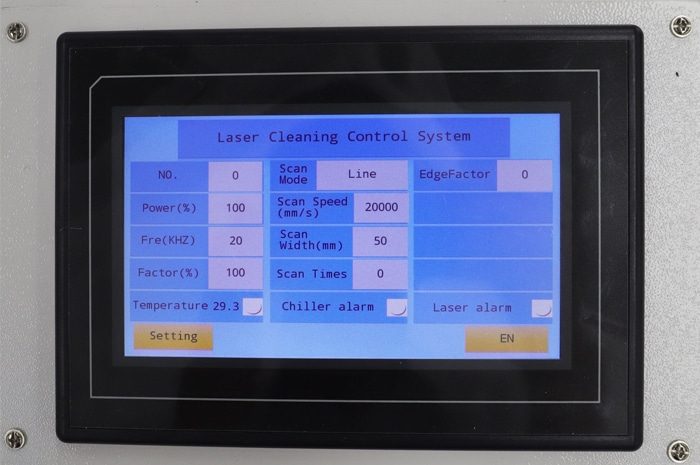
Interactive Touch Screen Control System
Acctek provides high-performance, intuitive, and easy-to-use operating systems. You can quickly set cleaning power, width, and other parameters through the screen, and provide a better cleaning effect. The operating system supports Chinese, English, Korean, Russian, Vietnamese, and other languages.
Technical Specifications
Model | AKQ-1000 | AKQ-1500 | AKQ-2000 | AKQ-3000 |
---|---|---|---|---|
Laser Power | 1000W | 1500W | 2000W | 3000W |
Laser Type | Fiber laser | |||
Laser Generator | JPT / Raycus / Reci / IPG / Max | |||
Pulse Formation | Q-Switched (Quality factor) | |||
Output Range (If Adjustable) | 0-100% | |||
Cleaning Efficiency | 12㎡/h | |||
Scanning Width | 10-80mm | |||
Expected Focal Distance | 160mm | |||
Cooling Type | Water Cooling |
Comparison With Traditional Clean Methods
Comparision | Laser Cleaning | Chemical Cleaning | Mechanical Grinding | Dry Ice Cleaning |
---|---|---|---|---|
Washiing Method | Non-contact cleaning | Contact cleaning | Abrasive contact cleaning | Non-contact cleaning |
Harm To Base Material | None | Yes | Yes | None |
Washing Efficiency | High | Low | Low | Mid |
Consumable | Power | Chemical detergent | Abrasive paper, grinder, abrasive stone | Dry ice |
Washing Result | Very good, very clear | Medium, uneven | Medium, uneven | Good, uneven |
Precision Washing | Accuracy controllable, High precision. | Uncontrollable, Low precision. | Uncontrollable, Medium precision. | Uncontrollable, Poor precision. |
Safety/Environment | No pollution | Chemical pollution | Dust pollution | No pollution |
Operation | Easy to operate, portable or automation optional. | Complicated process, higher technical requirement of the operator. Pollution prevention measures required. | Need more time & manpower. Pollution prevention measures required. | Easy to operate, portable or automatic. |
Investment | High investment on machine. But no consumable, low maintenance cost. | Low investment on machine. But expensive consumables. | Medium investment on machine. High man-power cost. | Medium investment on machine. High consumable cost. |
- These are only indicational values for Reference, based on our own experience, each case must be checked specifically and results depend on the layers and the underground.
- The laser cleaning machine produced by AccTek Laser basically follows these parameters.
Product Features
- Non-contact 360° cleaning, not limited by space and location, no consumables.
- No damage to the substrate. It has a better cleaning effect for substrates with high precision requirements, such as molds.
- It can better control the heat input and prevent the substrate temperature from being too high or micro-melting.
- The cleaning surface has high cleanliness and no pollution and can be used directly without secondary treatment.
- The red light focusing is easy to operate, and the cleaning is repeated automatically.
- The life of the laser source is 100,000+ hours, and it can work continuously for 24 hours.
- Strong single-pulse light energy and high cleaning efficiency.
- Wide range of material applicability, the cleaning laser is a flexible and efficient application to a variety of industrial processing scenarios;
- Low requirements for the working environment, it is safe and stable maintenance-free;
- The laser cleaning head is extremely lightweight and can be operated by hand for a long time.
- Patented red light-assisted focusing technology, can adjust the focus position according to different field lenses.
- With real-time monitoring of optical path temperature, motor abnormality, laser abnormality, and automatic motor standby protection. The system is safer and more stable.
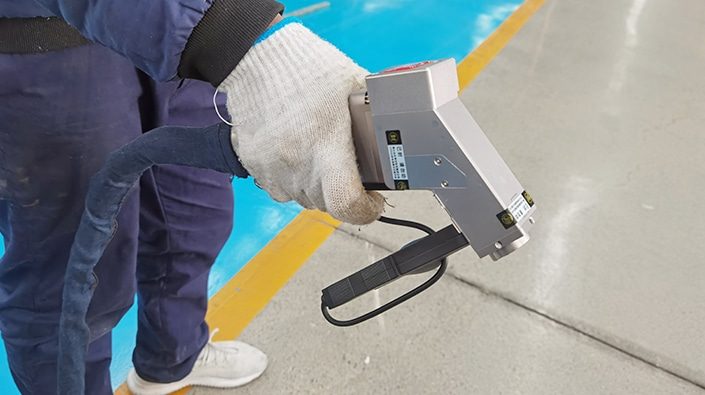
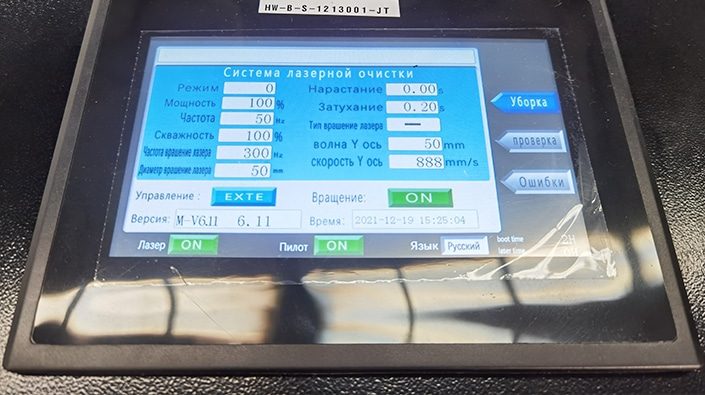
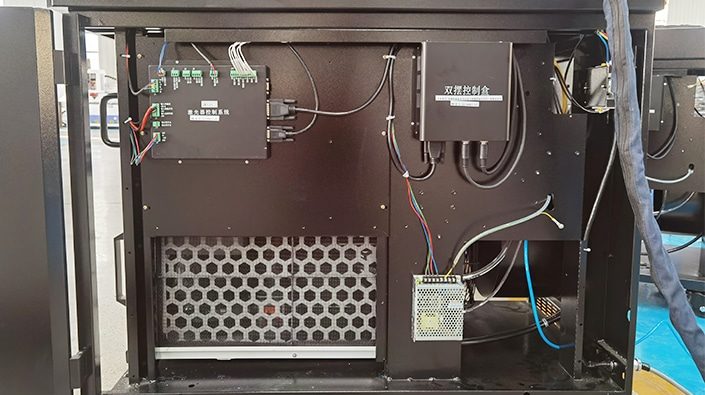
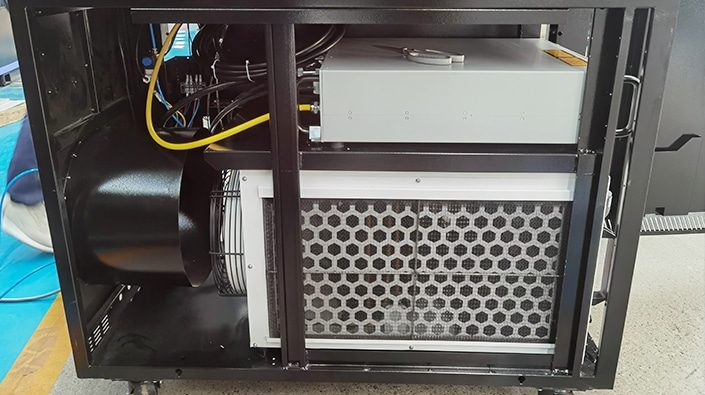
Product Application
- Surface Preparation: Pulsed laser cleaning is an effective method of preparing surfaces for bonding, welding, and painting. It allows for better adhesion and a stronger bond by removing contaminants and oxides from the surface.
- Rust Removal: It can be used to remove rust from metal surfaces such as steel or iron. Laser energy precisely removes rust without damaging the underlying metal surface.
- Paint Removal: It can be used to remove old paint from a variety of surfaces including wood, metal, and plastic. Laser energy removes paint without damaging the underlying surface.
- Mold Cleaning: It cleans molds used in plastic and metal manufacturing, removing residues and improving mold quality.
- Cleaning of Historical Relics: It is also used for cleaning and restoration of historical relics, such as statues, monuments, buildings, etc. Laser energy removes dirt and contaminants without damaging the surface of the artifact.
- Electronics Cleaning: It removes contaminants from delicate electronic devices such as circuit boards and sensors.
Frequently Asked Questions
- Energy Consumption: Laser cleaners consume electricity to operate. The power consumption of the 1000w laser cleaning machine will be higher than that of the low power consumption model. You can estimate your electricity bill based on the energy consumption provided by the manufacturer.
- Consumables: Depending on the machine and application, laser cleaners may require additional consumables such as protective lenses, protective gas, or filters. These consumables will constitute the overall operating costs and should be factored into the budget. The frequency of replacement and associated costs will depend on machine design and usage.
- Laser Generator Maintenance: The laser generator is a critical component of the machine and may require regular maintenance or replacement over time. Depending on the exact model and manufacturer, the cost to maintain or replace a laser generator can vary widely.
- Optics Cleaning And Replacement: The optical components of a laser cleaning machine, such as lenses and mirrors, may require periodic cleaning or replacement to ensure optimal performance. The cost of cleaning supplies or replacing optics should be considered as part of maintenance costs.
- Maintenance And Care: Laser cleaning machines require regular maintenance to ensure optimum performance and longevity. This may include cleaning optical components, aligning the system, checking for any wear, and replacing worn parts. The cost of maintenance and service may vary, depending on the complexity of the machine and the service provider’s fees.
- Cooling System: Laser cleaning machines often require a cooling system to keep the laser generator and other components within the optimum operating temperature range. Cooling systems may involve the use of water or other cooling mechanisms. You may want to consider the cost of water or coolant and maintenance of the cooling system.
- Operator Training: If the operator is not yet familiar with laser cleaning techniques, training may be required to ensure safe and effective operation. Operator training expenses and labor costs should be considered as part of the overall operating costs.
- Metals: Laser cleaning is especially effective for cleaning metal surfaces such as steel, stainless steel, aluminum, copper, brass, and titanium. It removes rust, paint, scale, oil, grease, and other surface contaminants.
- Plastics: Laser cleaning can be used on certain types of plastics, such as acrylic or polycarbonate, to remove coatings, adhesives, and surface contaminants. However, it is important to note that laser cleaning may damage or melt certain types of plastics, so a small-scale test should be done before cleaning to determine the laser’s compatibility with the material.
- Stone And Concrete: Laser cleaning can be applied to stone surfaces such as marble, granite, and limestone, as well as concrete surfaces. It removes dirt, grime, graffiti, and other surface deposits without damaging the stone.
- Wood: Laser cleaning can be used to clean wooden surfaces such as antique furniture, wooden sculptures, and historical artifacts. It removes dirt, smoke residue, and aged finishes without damaging the wood.
- Glass: Laser cleaning removes dirt, soot, coatings, and residue from glass surfaces without causing damage. It is commonly used to clean glass in automotive, architectural, and optical applications.
- Automotive Components: Laser cleaning is commonly used in the automotive industry to clean engine parts, chassis components, and other metal surfaces. It removes grease, oil, coatings, and other contaminants without damaging the underlying material.
- Historic Artifacts And Conservation: Laser cleaning is used to restore and preserve historical artifacts, sculptures, statues, and works of art made of materials such as stone, metal, or wood. It allows precise and gentle cleaning without damaging delicate surfaces.
- Paint And Coating Removal: Laser cleaning can effectively remove paint, coatings, varnishes, and other surface layers from a variety of materials, including metals, plastics, and composites.
- Electronics: Laser cleaning can be used in electronics manufacturing and repair processes to clean circuit boards, connectors, and other sensitive electronic components. It removes flux residue, solder splatter, and other contaminants without damaging electronic parts.
- Laser Safety Standards: Laser cleaning machines should comply with laser safety standards and regulations established by the relevant authorities in your region. These standards specify the safety requirements for the design, construction, and operation of laser equipment to ensure the protection of personnel and prevent accidents.
- Laser Safety Training: Operators should receive proper laser safety training before operating a laser cleaning machine to understand the potential hazards associated with the laser cleaning machine and how to operate it safely. Training should cover topics such as laser classification, beam hazards, personal protective equipment (PPE), safe operating procedures, and emergency plans.
- Eyewear Protection: Laser cleaners emit intense laser beams that may be harmful to eyeglasses. Appropriate laser safety goggles or glasses designed for the wavelength and power of the laser used by the laser cleaner must be worn. Goggles should comply with relevant safety standards and provide adequate protection.
- Ventilation And Fume Extraction: Depending on the material being cleaned, laser cleaning can produce fumes or particulate matter. Adequate ventilation and smoke extraction systems should be installed to prevent the accumulation of potentially hazardous airborne contaminants. This helps maintain a safe working environment and protects operators from inhalation or exposure to hazardous substances.
- Compliance: Depending on your location, there may be additional regulatory requirements and certifications related to laser safety and workplace safety that you need to consider when purchasing a laser cleaning machine. Make sure to follow local laws and regulations related to laser safety and operation.
- Regular Maintenance And Inspections: Regular maintenance of your laser cleaning machine is essential to ensure its safe and efficient operation. Follow the manufacturer’s guidelines for routine maintenance, inspections, and repairs to keep your machine in top condition and minimize any potential risks associated with faulty components or improper operation. This includes checking laser generators, cooling systems, safety interlocks, and other critical components.
- Fire Safety: Laser cleaning generates intense heat and, depending on the material being cleaned, there may be a risk of igniting flammable substances. Make sure to implement proper fire safety measures, such as having fire extinguishers at hand and following established fire safety protocols.
- Manufacturing And Industrial Cleaning: Laser cleaning is widely used in the manufacturing industry to clean and prepare surfaces prior to processes such as welding, bonding, coating, or painting. It removes rust, oxide layers, contaminants, and coatings from metal surfaces, ensuring better adhesion and the quality of subsequent processes.
- Automotive Industry: Laser cleaning is used in the automotive industry to clean auto parts, such as engine parts, brake systems, and chassis parts, and even vulnerable surfaces such as car interiors. It removes coatings, dirt, oil, and grease without damaging the underlying surface.
- Aerospace: Laser cleaning is very beneficial to the aerospace industry. It effectively removes contaminants, coatings, and oxides from aircraft components, engine components, turbine blades, and other surfaces without causing damage. Laser cleaning helps maintain the performance, reliability, and longevity of critical aerospace equipment.
- Historic Restoration And Conservation: Laser cleaning technology can be used to restore and preserve historical artifacts, sculptures, statues, and artworks made of various materials such as stone, metal, or wood. Its precise yet gentle cleaning power removes dirt, stains, and other unwanted layers without damaging delicate surfaces.
- Electronics And Semiconductor Manufacturing: Laser cleaning can be applied in the electronics manufacturing and semiconductor industries for the cleaning of circuit boards, connectors, and other sensitive electronic components. It removes solder residue, flux, and other contaminants from surfaces without damaging sensitive electronics. This ensures improved functionality, reliability, and longevity of electronic equipment.
- Marine And Shipbuilding: Laser cleaning is used in the marine and shipbuilding industry to clean ship surfaces and remove marine growth, rust, and paint coatings. It helps maintain the integrity of the vessel’s surface and improves fuel efficiency.
- Paint And Coating Removal: Laser cleaning is used to remove paint, coatings, varnishes, and other surface layers from a variety of materials, including metals, plastics, composites, and wood. Such applications are common in industries such as automotive, construction, and furniture manufacturing.
- Medical And Pharmaceutical: Laser cleaning can be used in the medical and pharmaceutical industries to clean and decontaminate medical instruments, surgical instruments, and production equipment. It cleans medical instruments, and production equipment, helps maintain high cleanliness standards, and reduces the risk of contamination.
- Oil And Gas: Laser cleaning technology is used in the oil and gas industry to clean and maintain pipelines, storage tanks, valves, and other equipment. It removes rust, scale, and other contaminants, improving operating efficiency and extending the life of the equipment.
- Laser Safety Training: Operators should receive laser safety training to understand the potential hazards associated with laser radiation and how to reduce the risk. The training covers topics such as laser classification, laser hazards, proper use of personal protective equipment (PPE), and safe work practices in laser environments.
- Machine Operator Training: Operators should be trained on the specific model of laser cleaning machine they will be using. This includes understanding the machine’s control panel, and software interface, and how to set the proper laser parameters for different cleaning tasks, such as power, pulse duration, and spot size.
- Material Knowledge: Different materials and surfaces may require specific laser settings and parameters for optimal cleaning without causing damage. Operators should have a good understanding of the different materials and surfaces that a laser cleaning machine can handle. This includes understanding how various materials respond to laser cleaning, appropriate laser settings for different materials, and potential risks or limitations associated with certain materials. This knowledge helps to optimize the cleaning process and minimize the risk of material damage.
- Troubleshooting And Maintenance: Proper maintenance and calibration are very important to the life and performance of your laser cleaner. Operators should be trained in basic troubleshooting procedures and routine maintenance tasks to keep the machine running smoothly. This includes tasks such as cleaning optics, replacing consumables, aligning laser beams, and diagnosing and resolving common problems that may arise during operation. Also, it’s important to know how to perform basic troubleshooting and when to seek professional help.
- Emergency Procedures: Operators should be familiar with emergency procedures in the event of an accident or failure. This includes knowledge of emergency shutdown protocols, knowledge of how to deal with laser-related incidents such as reflections or accidental exposure, and training in basic first aid procedures specific to laser-related injuries.
- Cleaning Techniques And Strategies: Laser cleaning involves a variety of techniques and strategies, depending on the specific cleaning requirements and the material being processed. Operators should be trained in proper scan patterns, spacing, and motion control to achieve a uniform and thorough cleaning. They should also know how to adjust laser parameters for different cleaning tasks and surface conditions.
- Regular Updates And Continuing Education: It is important for operators to stay abreast of the latest developments in laser cleaning technology, safety guidelines, and best practices. Regular updates and continuing education help operators keep up with the ever-evolving field and improve their skills.
- Life expectancy: The life expectancy of a laser cleaning machine is affected by the quality and durability of its components, especially the laser generator. Laser generators typically have a specified lifetime, usually measured in tens of thousands of hours of operation. However, actual life expectancy will be affected by factors such as operating conditions, maintenance, and intensity of use. Regular maintenance and following recommended usage guidelines will help maximize the life of your machine.
- Maintenance Requirements: Regular maintenance is essential to ensure the optimal performance and longevity of your laser cleaning machine. Some common maintenance requirements may include:
- Cleaning Optical Components: Optical components such as lenses and mirrors may require periodic cleaning to remove dust, debris, or residue that may affect the quality of the laser beam. Regular cleaning of these parts is critical to maintaining the efficiency of the machine and preventing degradation of the laser beam.
- Cooling System Maintenance: Laser cleaning machines usually have a cooling system to dissipate the heat generated during operation. Regular inspection and maintenance of your cooling system, including checking coolant levels, ensuring proper airflow, and cleaning or replacing filters, can help prevent overheating and ensure efficient operation.
- Replace The Laser Generator: Depending on the specific laser generator and its service life, the laser generator may need to be replaced after a certain period of operation. The specific lifespan and replacement process will depend on the type of laser generator used in the machine and it is recommended to follow the manufacturer’s guidelines and recommendations for replacement.
- Calibration And Alignment: Over time, the calibration of a laser cleaning machine may drift, affecting its effectiveness. Regular calibration and alignment of the laser cleaning machine’s components may be required to ensure accurate and consistent cleaning results. This may involve adjusting laser parameters, verifying beam quality, and ensuring proper alignment of optics.
- Periodic Inspection: The machine’s components, electrical connections, and safety features should be inspected regularly, which is important to identify and resolve any potential problems or wear and tear. Detecting problems early can prevent more serious damage and increase machine reliability.
- Software And Firmware Updates: Laser cleaning machines may have software or components that require periodic updates to improve functionality, resolve bugs or security issues, and benefit from performance enhancements.
- Manufacturer’s Guidelines: Always refer to the manufacturer’s guidelines and recommendations for specific maintenance requirements and schedules for the model of the laser cleaning machine you are using. Manufacturers can provide detailed guidelines and maintenance checklists regarding maintenance intervals, specific procedures, and any other requirements for a particular machine model.
- Power Requirements: Laser cleaning machines generally require a stable and reliable power source to operate effectively. Power requirements may vary depending on the exact model and power rating of your machine. It is important to ensure that the power supply meets the specifications provided by the manufacturer, which includes factors such as voltage, frequency, and power capacity. Note that it is important to follow the manufacturer’s guidelines to prevent any electrical issues and keep the machine running safely and efficiently.
- Power Stability: Laser cleaners are sensitive to fluctuations in the power supply. Ensuring a stable power supply with consistent voltage and frequency is important to maintain the performance and reliability of your machine. Power surges, voltage drops, or electrical noise may interfere with the operation of the laser cleaner and may require the use of additional power conditioning equipment or surge protection.
- Power Capacities: Laser cleaning machines can have different power capacities, including the 1000w mentioned in your previous question. You need to make sure that the power sources available in your facility can meet the power requirements of the laser cleaning machine. Insufficient power supply capacity may cause poor performance or damage to the machine, while excessive power supply capacity may cause safety hazards.
- Compatibility With Auxiliary Equipment: Laser cleaning machines may require auxiliary equipment such as cooling systems, exhaust systems, or compressed air supplies for optimal operation. It is important to ensure compatibility between the laser cleaning machine and any auxiliary equipment to ensure smooth integration and efficient operation of the entire system.
- Laser Safety Regulations: Laser cleaning machines are classified as laser equipment and must comply with laser safety regulations specific to your region. These regulations often include guidelines for power limits, safety features, and controls to ensure safe operation. Before purchasing or operating a laser cleaning machine, be sure to verify that the machine complies with the applicable laser safety standards and regulations in your region.
- Environmental Considerations: Laser cleaning machines should be operated under suitable environmental conditions to maintain optimum performance and prevent damage. Factors to consider include ambient temperature, humidity level, and cleanliness of the operating environment. Excessive heat, extreme temperatures, high humidity, or the presence of excessive dust or contaminants can all negatively affect a machine’s performance. In addition, adequate ventilation and environmental controls should be considered to ensure proper operation.
- Compatibility With Materials: Laser cleaning machines are designed to handle specific types of materials. You need to consider the compatibility of the laser wavelength with the material you intend to clean. Different materials have different absorption characteristics for laser energy, and certain materials can be cleaned more effectively with specific laser wavelengths. It is recommended to consult the manufacturer’s guidelines and recommendations to determine the laser cleaning machine’s compatibility with the material you plan to clean.