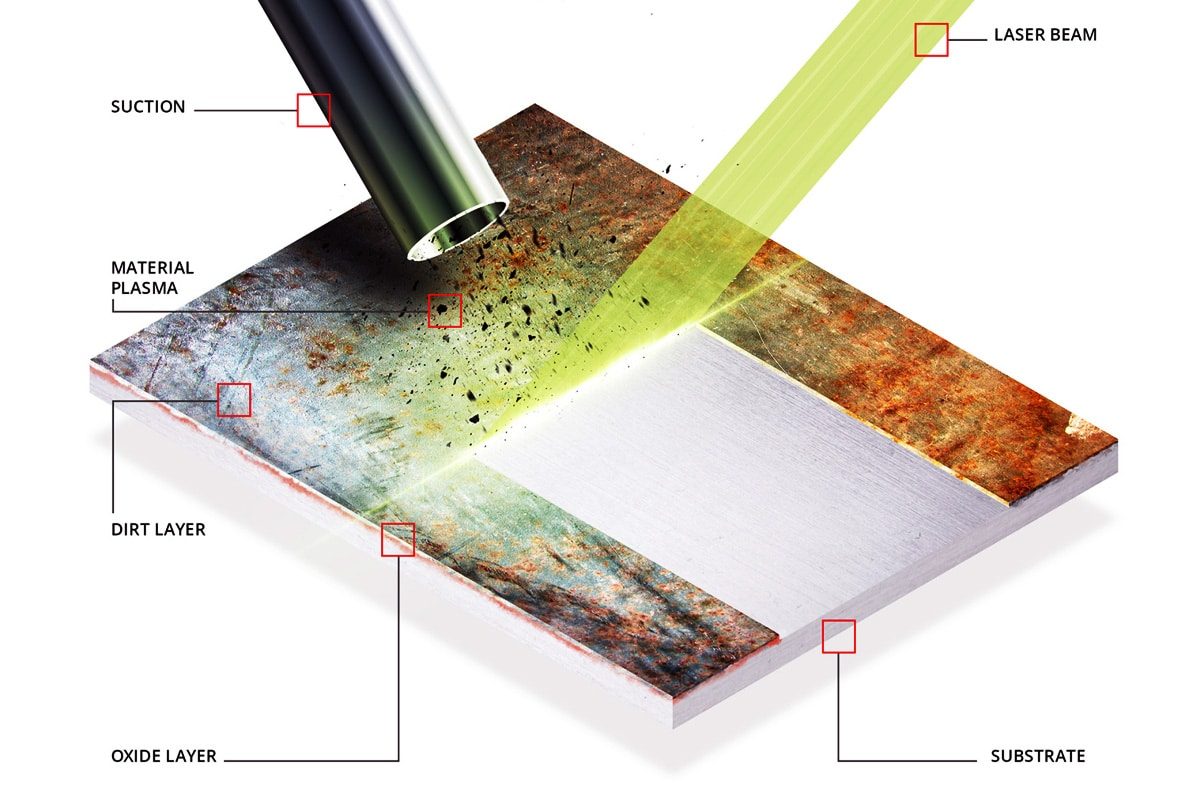
A Comprehensive Guide to Evaluating Surfaces After Laser Cleaning
Laser cleaning technology has been widely used in many industries due to its precision, selectivity, environmental friendliness, and non-contact process. Whether metal processing, automotive manufacturing, aerospace, or cultural relic restoration, laser cleaning machines can remove pollutants without damaging the substrate. However, it is not enough to just complete the cleaning. How to evaluate the cleanliness of the surface is crucial. It not only affects the quality of the final product but also involves compliance and long-term performance.
Table of Contents
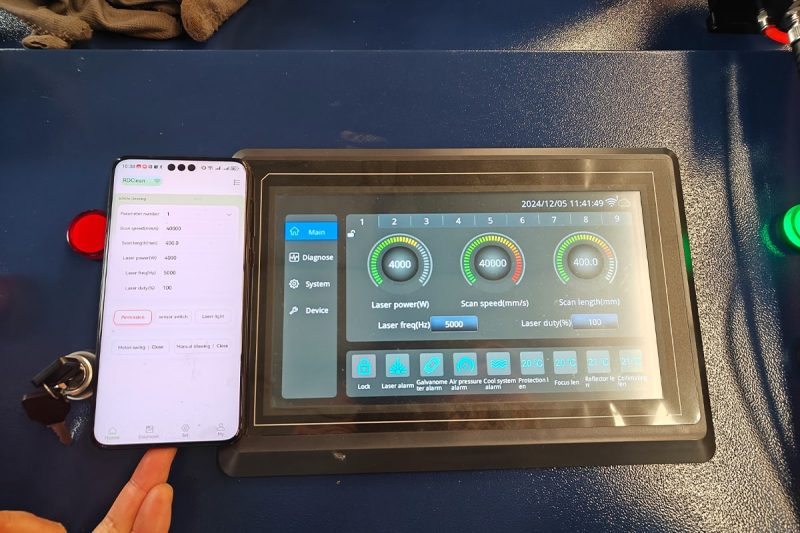
Learn about laser cleaning
Laser cleaning is an efficient, precise, and environmentally friendly surface treatment technology, widely used in industrial applications such as metal rust removal, oxide layer removal, coating stripping, welding pretreatment, etc. Compared with traditional chemical cleaning or mechanical grinding, laser cleaning can remove pollutants without damaging the substrate, improving process stability and product quality. The following are the four core advantages of laser cleaning.
Precision: Laser cleaning uses a high-energy laser beam to focus on the surface of the material, acting only on the contaminated area, achieving precise cleaning at the micron level. This precise control can effectively remove dirt, rust, or coating and avoid material wear, deformation, or chemical corrosion that may be caused by traditional cleaning methods. The accuracy of laser cleaning is particularly critical for industries such as aerospace, precision electronics, and mold manufacturing, which have extremely high requirements for surface quality.
Selectivity: Unlike chemical solvent or sandblasting cleaning, laser cleaning can precisely adjust parameters according to different materials, types of pollutants, and application requirements to achieve highly selective cleaning. For example, in the coating removal process, the laser can only remove the surface coating without affecting the substrate; in the field of cultural relic restoration, the laser can remove pollutants while protecting the original material of the cultural relic. This selectivity greatly improves the controllability of the cleaning process and reduces unnecessary losses.
Environmental protection: Traditional cleaning methods usually rely on chemical solvents or abrasive materials, which may produce harmful waste liquids, toxic gases, or dust pollution, posing a threat to the environment and the health of operators. Laser cleaning is a purely physical process that relies solely on laser energy to vaporize or decompose pollutants. It does not require the use of chemical reagents and does not produce secondary pollution. It fully meets the requirements of modern industry for environmental protection and sustainable development. Therefore, laser cleaning has been widely used in industries that have strict requirements on cleanliness and environmental protection standards, such as automobile manufacturing, medical equipment, and food processing equipment.
Non-contact process: Another notable feature of laser cleaning is non-contact operation, which means that there is no need for direct contact with the substrate during the cleaning process, avoiding material wear caused by friction, pressure, or mechanical damage. This advantage is particularly suitable for cleaning precision equipment, microelectronic components, or fragile materials, such as semiconductor chips, precision molds, etc. In addition, non-contact cleaning also supports automated integration and can be combined with robots, CNC systems, or assembly line operations to achieve efficient and stable industrial cleaning processes.
Laser cleaning is becoming one of the mainstream technologies in the field of modern industrial cleaning due to its precision, selectivity, environmental friendliness, and non-contact process. Compared with traditional cleaning methods, laser cleaning can not only improve the cleaning quality, but also reduce environmental pollution, reduce maintenance costs, and is suitable for various complex application scenarios. With the continuous advancement of technology, laser cleaning will play its advantages in more industries and provide enterprises with more efficient and sustainable cleaning solutions.
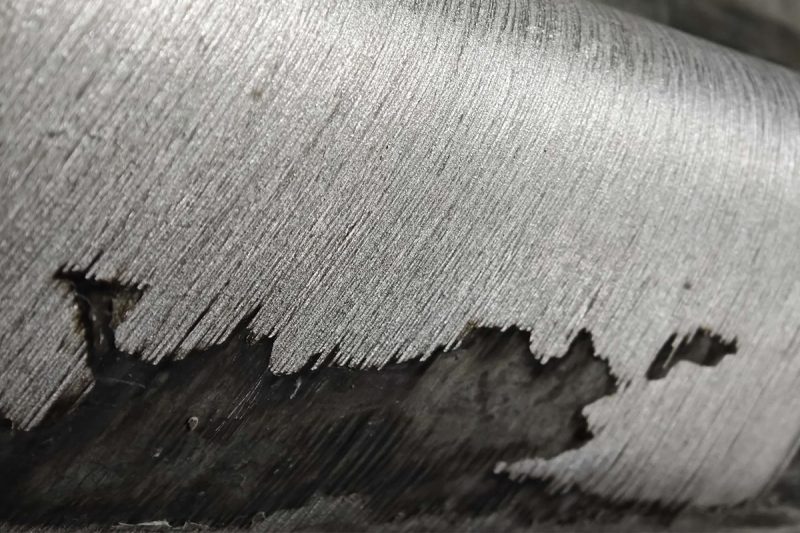
Understanding Cleanliness Assessment
As an efficient surface treatment technology, laser cleaning is widely used in many fields such as metal manufacturing, electronics industry, automobile restoration, aerospace, and cultural relic restoration. However, the measurement of the cleaning effect does not rely solely on visual observation but also requires systematic cleanliness evaluation. This process involves multiple aspects such as contaminant identification, surface sensitivity, regulatory compliance, and performance verification to ensure that the cleaned surface meets industry standards and application requirements.
Contaminant identification: In cleanliness assessment, the first step is to accurately identify the type and distribution of contaminants. Contaminants on the surface of different materials may include oxide layers, rust, grease, coating residues, dust, chemical residues, etc., and each contaminant has different adaptability to the cleaning process.
- Organic pollutants (such as oil, resin, and lubricant) usually require high-energy short-pulse laser vaporization to remove.
- Inorganic pollutants (such as oxides, rust, and metal residues) rely on the high-temperature evaporation of lasers.
- Particle pollution (such as dust, and fine particles) may require vacuum adsorption or airflow assistance to prevent secondary contamination.
Accurately identifying contaminants can not only optimize cleaning parameters but also ensure the accuracy of cleanliness assessment to avoid residues after cleaning that affect product quality.
Surface sensitivity: Different materials have different sensitivities to the cleaning process. Laser cleaning needs to adjust parameters such as power, wavelength, and scanning speed according to the characteristics of the material to ensure that pollutants can be effectively removed without damaging the substrate.
- Highly reflective materials (such as aluminum and copper) have low laser absorption rates and require the use of laser generators with specific wavelengths or increased pulse energy.
- Brittle materials (such as ceramics and glass) may crack due to thermal shock and require the use of low-power, short-pulse lasers to reduce the heat-affected zone.
- Precision components (such as semiconductors and electronic circuits) require extremely high cleanliness standards while avoiding laser damage to sensitive circuits or insulating layers.
An important part of cleanliness assessment is to confirm whether the surface of the material after cleaning still maintains its original physical and chemical properties. For example, the metal surface cannot have microcracks or excessive surface roughness after cleaning, otherwise, it may affect subsequent coating, welding, or assembly.
Regulatory compliance: Different industries have strict standards and regulations for surface cleanliness. Cleanliness assessment must comply with relevant industry specifications and quality management systems to ensure that the product can pass quality inspection smoothly.
- Aerospace: As specified by NASA and FAA, no contaminants that may affect bonding or corrosion should remain on the surface of spacecraft components.
- Automotive: ISO 16232 (VDA 19) standard specifies cleanliness testing methods for automotive parts to ensure that key components such as engines and fuel systems are free of contaminants.
- Medical devices: ISO 13485 stipulates that medical devices must meet strict cleanliness standards to avoid any contaminants that may affect patient safety.
- Electronics industry: IPC standards require that the surface of circuit boards reach extremely high cleanliness before soldering to prevent short circuits or poor soldering.
During the cleanliness assessment process, companies must conduct tests based on relevant standards and record the cleaning results to meet compliance requirements and improve the market competitiveness of their products.
Performance verification: Laser cleaning not only needs to remove contaminants but also needs to ensure that the cleaned surface can meet the requirements of subsequent processes or final use. Therefore, performance verification is a key link in cleanliness assessment, including the following aspects:
- Surface integrity testing: Ensure that there is no microscopic damage to the material after cleaning, such as microscopic cracks, surface roughness changes, etc.
- Adhesion testing: If the surface after cleaning needs to be coated, painted, or welded, the bonding strength of the new attachment must be tested to avoid adhesion loss due to surface contamination.
- Corrosion resistance evaluation: Some metal materials may face oxidation or corrosion risks after cleaning, and corrosion resistance evaluation such as salt spray testing is required.
- Optical microscopic analysis: Use a microscope, scanning electron microscope (SEM), or X-ray spectroscopy (XPS) to detect microscopic contaminants to ensure that there is no residue on the surface after cleaning.
Through systematic performance verification, the reliability of laser cleaning technology in different application scenarios can be ensured to meet customers’ quality requirements.
Cleanliness assessment is the core link to ensure the quality of laser cleaning, covering four key aspects: contaminant identification, surface sensitivity, regulatory compliance, and performance verification. By accurately identifying contaminants, optimizing cleaning parameters for different materials, following industry standards, and conducting strict performance verification, companies can ensure that the cleaning effect meets the needs of industrial applications. With the continuous advancement of cleaning technology, laser cleaning will become the preferred surface treatment solution for more and more industries, providing more efficient and environmentally friendly cleaning solutions for high-end manufacturing.
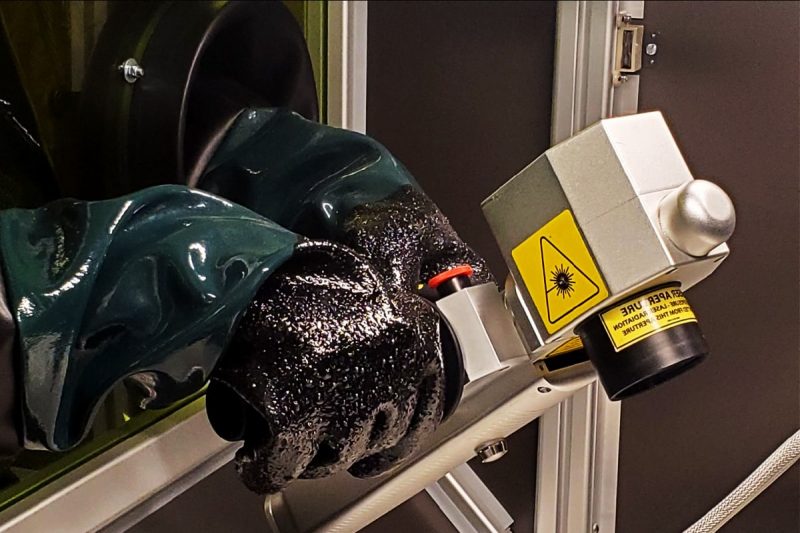
Importance of Assessing Cleanliness After Laser Cleaning
In industrial applications, it is very important to evaluate the cleanliness after laser cleaning. It not only determines the product quality but also affects the reliability of subsequent processes. The following are the four core values of cleanliness evaluation:
- Comply with industry standards: Different industries (such as aviation, automotive, electronics, and medical) have strict requirements for surface cleanliness. Ensuring compliance with ISO, VDA, IPC and other standards will help products pass quality certification smoothly and improve market competitiveness.
- Optimal performance and reliability: If there are still contaminants on the surface after cleaning, it may affect the effect of subsequent welding, coating, or bonding. Accurately evaluate cleanliness to ensure that parts maintain optimal performance in long-term use and reduce the risk of failure.
- Quality assurance: Cleanliness is directly related to product consistency and durability. Scientific evaluation methods can reduce production errors, improve overall manufacturing quality, and meet customers’ high standards.
- Cost-effectiveness: Effective cleanliness assessment can avoid repeated cleaning or rework, scrap, and repair costs caused by contamination while reducing downtime, improving production efficiency, and thus reducing overall operating costs.
Cleanliness assessment is not only a part of quality control but also an important link to ensure production stability, optimize process flow, and improve economic benefits.

Evaluation technology for cleanliness assessment
To ensure that the surface after laser cleaning reaches the ideal state, a variety of evaluation techniques are required to detect cleanliness. Common methods include:
- Visual inspection: Use the naked eye or a magnifying glass to conduct a preliminary inspection to quickly determine whether there are obvious contaminants or defects on the surface.
- Surface profile analysis: Use a roughness meter to detect changes in the surface microstructure to ensure that subsequent processing or coating is not affected after cleaning.
- Surface analysis: Use X-ray spectroscopy (XPS) or energy dispersive spectroscopy (EDS) to analyze the surface composition and detect whether there are residual oxides or organic contaminants.
- Chemical analysis: Use titration, fluorescence detection, or gas chromatography (GC-MS) to analyze surface chemical residues to ensure compliance with industry cleaning standards.
- Optical microscope: Magnify and observe micron-level contaminants, especially suitable for precision manufacturing fields such as electronics and medical devices.
- Adhesion test: Evaluate the adhesion strength of surface coatings, welding, or bonding through pull-off tests or tape peel tests to ensure the quality of subsequent processes.
Combining multiple evaluation techniques can more accurately judge cleaning results and ensure that laser cleaning meets industry standards and application requirements.
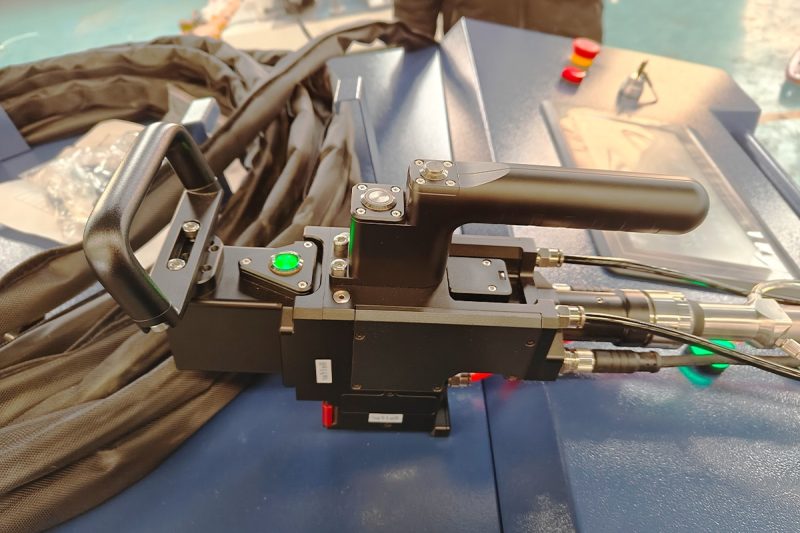
Best Practices for Cleanliness Assessment
To ensure consistent and reliable surface quality after laser cleaning, companies should follow a series of best practices to improve the accuracy and consistency of assessments.
- Establish clear standards: Develop cleanliness standards based on industry specifications (such as ISO, VDA, IPC, etc.) to ensure that all products meet quality requirements and are suitable for different application scenarios.
- Use multiple technologies: A single detection method may have limitations. Combining multiple technologies such as visual inspection, surface analysis, chemical testing, microscopic observation, and adhesion testing can obtain more comprehensive evaluation results.
- Calibrate instruments: Regularly calibrate the testing equipment to ensure the accuracy of the measurement data and avoid evaluation errors caused by equipment deviation.
- Standardized procedures: Establish a unified cleanliness detection process to ensure that all operators follow the same steps, reduce human errors, and improve data comparability.
- Train personnel: Regularly provide professional training to test personnel to improve their ability to identify contaminants, test methods, and data interpretation, and ensure the reliability of evaluation results.
- Record results: Record the data of each cleanliness evaluation in detail, including contaminant type, test method, equipment parameters, and final results, to trace and analyze, optimize the cleaning process, and meet quality management requirements.
Through these best practices, companies can improve the accuracy and consistency of cleanliness assessments and ensure the reliability of laser cleaning processes, thereby improving product quality and market competitiveness.
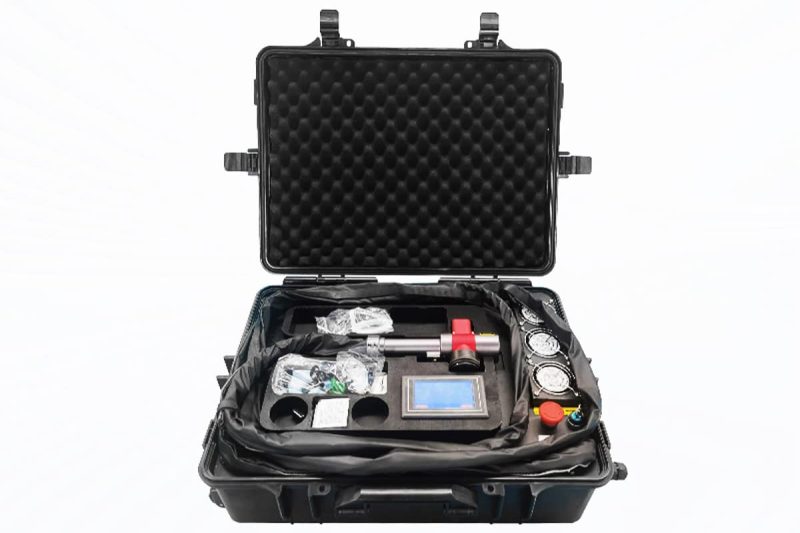
Summarize
Laser cleaning is not only about removing surface contaminants but also an important part of improving manufacturing quality and optimizing process flow. A thoroughly clean and standard surface can ensure the smooth progress of subsequent coating, welding, bonding, and other processes, and avoid product defects caused by residual contaminants. Through precise cleanliness assessment, companies can quantify the effect of laser cleaning and ensure that each workpiece meets industry standards, thereby improving product stability and service life. In addition, strict cleanliness management helps reduce rework and scrap rates, optimize production costs, and improve overall manufacturing efficiency.
In a highly competitive market environment, the use of scientific evaluation technology, standardized processes, and efficient testing methods can not only improve product quality but also enhance the company’s market reputation and customer trust. Therefore, cleanliness evaluation after laser cleaning is not only a key step in quality control but also an important guarantee for achieving long-term manufacturing optimization and industry leadership.
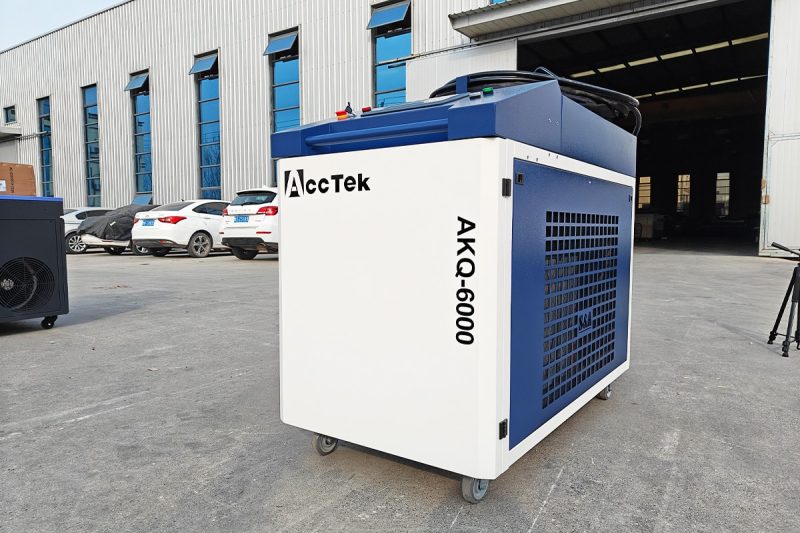
Get Laser Solutions
AccTek Laser specializes in providing efficient, accurate, and safe laser cleaning machines, which are widely used in many fields such as automobile manufacturing, aerospace, electronics industry, metal processing, cultural relics restoration, etc. Our laser cleaning technology can effectively remove surface contaminants such as oxide layer, oil stains, coatings, rust, etc., ensuring high-quality processing of parts while being environmentally friendly and low maintenance cost.
If you are looking for a reliable laser cleaning solution, our professional team can provide personalized customized solutions according to your specific needs to ensure that the equipment perfectly matches your production process, improves work efficiency, and reduces operating costs. Whether it is large-scale industrial applications or precision parts cleaning, AccTek Laser can provide you with advanced technical support and perfect after-sales service.
Welcome to contact us for professional consultation, product demonstration, and detailed technical solutions, and let laser cleaning technology help your company move towards higher production standards!
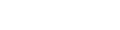
Contact information
- [email protected]
- [email protected]
- +86-19963414011
- No. 3 Zone A, Lunzhen Industrial Zone,Yucheng City , Shandong Province.
Get Laser Solutions