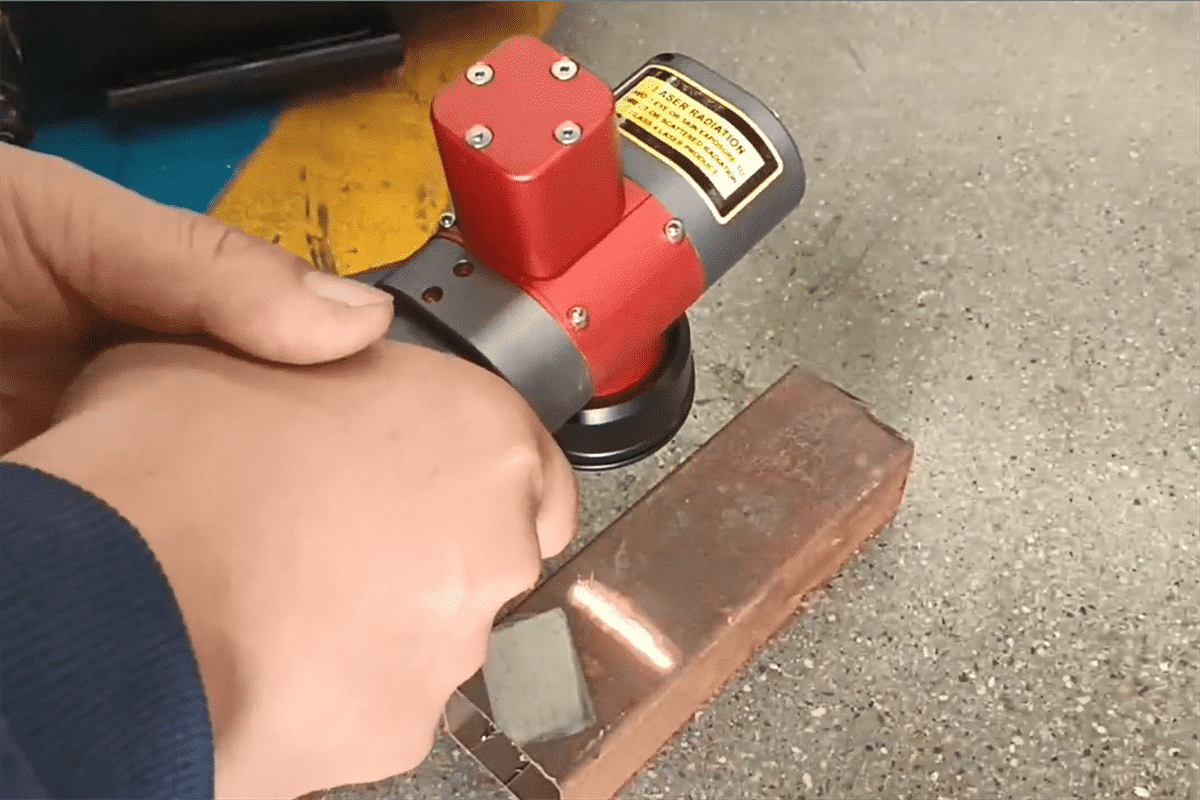
Advantages And Disadvantages of Laser Cleaning
Laser cleaning is a process used to safely remove paint, rust, or other unwanted contaminants from surfaces on a variety of materials. It’s the world’s most innovative approach to deep cleaning of materials. Laser cleaning machine can be used in a variety of scenarios from large industrial projects to home projects. Laser cleaning is very effective in any environment by simply changing the laser parameters according to the material properties and types of contaminants. In this article, we will discuss the principles, advantages, and disadvantages of laser cleaning. If you are considering purchasing a laser cleaning machine and are unsure about the investment, keep reading so you can further confirm whether laser cleaning is the cleaning process you need.
Table of Contents
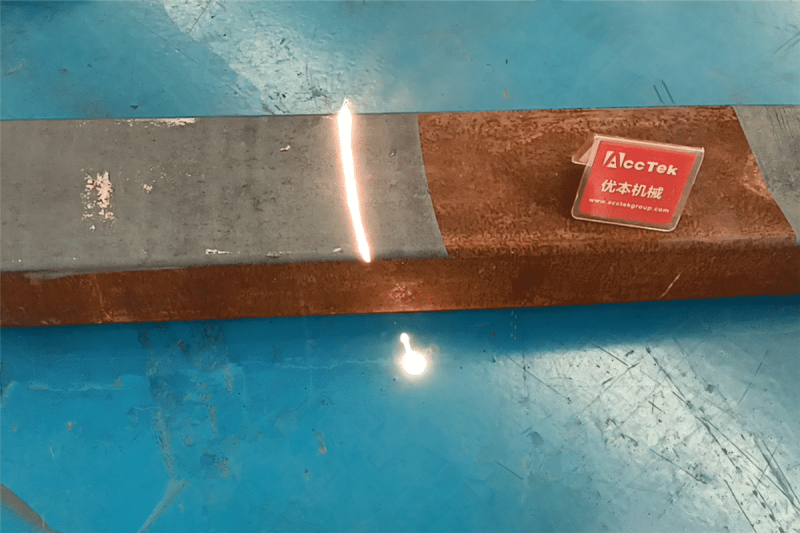
What is laser cleaning technology?
Laser cleaning is a new non-contact cleaning process that uses laser beams to remove contaminants from the surfaces of various materials. The concept of laser cleaning dates back to the 1980s, when lasers were first used to clean delicate surfaces in the aerospace industry. Since then, laser cleaning technology has continued to be refined and used in a variety of industrial and commercial applications. In recent years, laser cleaning has become widely popular due to its efficient cleaning ability and non-damage to the substrate.
Principle of laser cleaning
Laser cleaning technology works by firing a high-power laser beam at the surface of a material. When it interacts with contaminants that absorb laser light, the contaminant or coating particles will turn into gas, or the pressure of the interaction will cause the particles to break away from the surface.
The appropriate laser type and optimal parameters are different for each different material cleaning application. During the laser cleaning process, laser output parameters can vary on a large scale. Therefore, the user needs to select specific laser output parameters based on the material/contaminants being removed.
How laser cleaning works
Laser cleaning is primarily a form of laser ablation, which occurs when a laser beam is used to remove contaminants deposited on the surface of a material. For example, metal surface rust removal is based on the laser ablation process. However, laser ablation of the material will only occur when the energy of the emitted laser beam is higher than the ablation threshold of the material.
Each material has a specific ablation threshold based on its molecular bonds, and this threshold differs from other materials. Therefore, when the difference between the ablation thresholds of the two materials is large enough, the unwanted material can be removed in a highly selective manner during laser cleaning without affecting other materials. For example, rust has a significantly lower ablation threshold compared to the thresholds of steel or aluminum, allowing the use of a laser cleaner to completely vaporize the rust without damaging the underlying steel.
The parameters of the laser cleaning machine (i.e., power, wavelength, repetition rate, scan speed, and beam diameter) are carefully selected so that only the ablation threshold of the contaminant is reached, and not that of the substrate itself. This targeting of the correct ablation threshold, combined with the fact that laser cleaning can be controlled with micron-level precision, ensures that the underlying substrate is not damaged or is damaged very little. This process of scanning the laser beam is repeated until all contaminants have been removed and the material surface is clean.
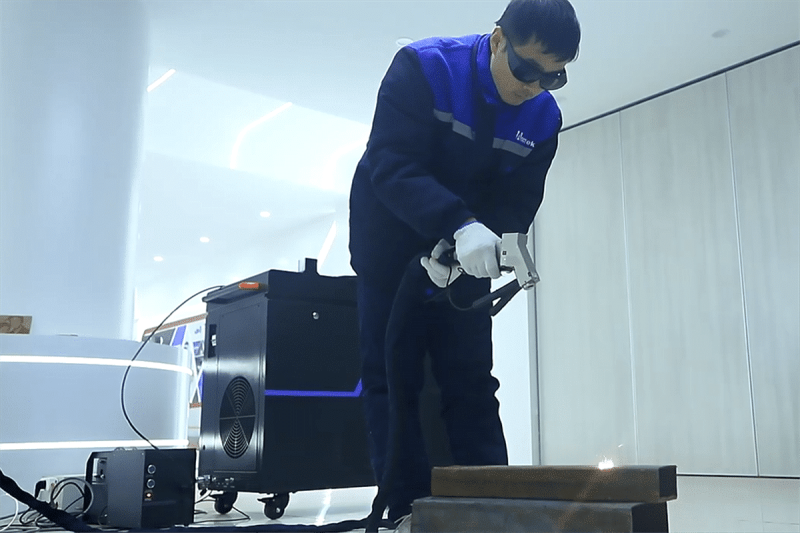
What are the advantages of laser cleaning?
As a new industrial cleaning method, laser cleaning machine is widely welcomed in the industrial market. Compared with mechanical cleaning, chemical cleaning and ultrasonic cleaning, laser cleaning technology has greater advantages. Some of its advantages include:
- No damage to the substrate. Laser surface cleaning systems work by aiming a powerful, high-pulse laser at rusty, painted or coated surfaces. This energy breaks down existing contaminants and effectively removes them from the substrate. Removal of the degraded layer or coating affects only a few microns. It doesn’t continue to burn away the solid surface underneath, making the laser’s effects more specific. This non-contact cleaning method does not use any cleaning media and avoids the problems of mechanical wear and chemical corrosion in traditional cleaning.
- Cleaning speed is fast. Powerful laser cleaning machines deliver short, powerful bursts of power ensuring the most consistent beam path. These characteristics enable the laser beam to quickly and efficiently remove dirt, rust, coatings and other contaminants on the surface of the material, greatly improving the cleaning efficiency.
- Cleaning quality is high. Laser cleaning machines can effectively clean sub-micron particles adsorbed on the surface of materials that are difficult to clean by other methods.
- In line with the concept of environmental protection. The laser cleaning process does not use chemicals, so it does not produce pollutants and is more environmentally friendly. The contamination-free cleaning method allows laser cleaning machines to be used in the food and pharmaceutical industries.
- High security. Laser cleaning machines can precisely control the range and intensity of the laser beam, reducing risks to the operator and the surrounding environment. Moreover, laser cleaning does not produce splashes and does not require contact with corrosive liquids. Therefore, workers do not need to wear heavy protective clothing and protective gloves, and only need to wear laser protective glasses. Starting work according to the correct cleaning method will not harm the health of workers.
- Simple operation and real-time monitoring. At present, many laser cleaning machines are designed with handheld laser cleaning guns. The operator only needs to aim the laser beam at the area to be cleaned and scanned, and the laser cleaning process can be monitored in real time to ensure that the expected results are achieved.
- Easy to move. Compared with other traditional cleaning equipment, laser cleaning machines are smaller in size and can be easily transported and brought to other workplaces with cleaning needs. This easy mobility makes it an ideal solution for on-site cleaning tasks. In particular, backpack-type laser cleaning machines can meet the needs of long-term outdoor or high-altitude operations.
- Cost effective. Laser cleaning machines have the lowest operating costs of all industrial cleaning methods. Laser cleaning does not require the use of any media and only consumes a small amount of electrical energy. Moreover, laser cleaning is many times faster than other cleaning methods, thus reducing labor costs. Because laser cleaning leaves behind no waste or debris, the cost of disposal is avoided, and return on investment is typically seen in less than a year.
- Selectively and accurately peel off cleaning layers. Unlike sandblasting, lasers are selective and can easily focus on very small spots or strips without affecting adjacent material. Precise and spot cleaning is easier with laser cleaning methods. Additionally, using laser cleaning makes it easier to reach the nooks and corners of complex design objects. The final product after laser cleaning is much finer than other cleaning methods.
- Easy to automate. The laser cleaning machine can be transmitted through optical fiber and cooperated with industrial robots to easily realize automatic control and long-distance remote control. In this way, parts that are difficult to reach with traditional methods can be cleaned, preventing operators from entering dangerous places.
- Wide range of applications. From surface preparation to paint and rust removal, laser cleaning machines can be used in a variety of industries, including automotive, aerospace, machine building, ships and historical artifacts.
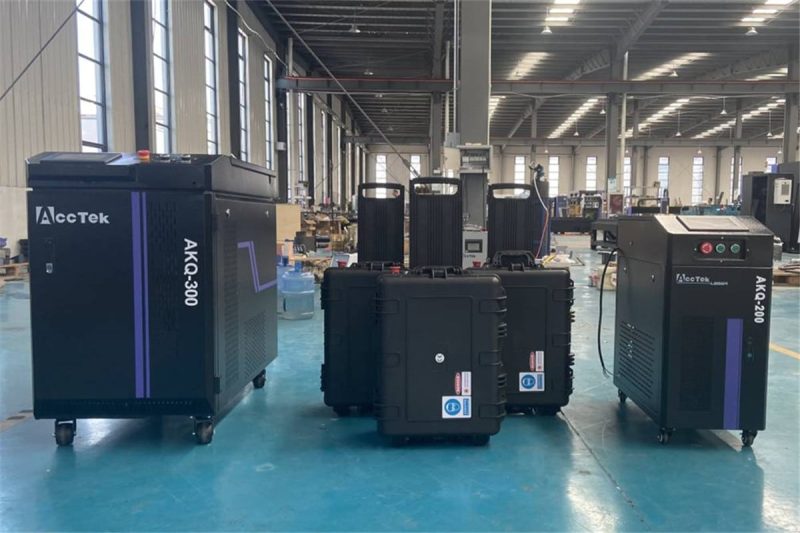
What are the disadvantages of laser cleaning machines?
While laser cleaning has its place in many industrial applications due to its many advantages, it is not a one-size-fits-all cleaning solution. Like any surface treatment process, laser cleaning has its limitations.
- Machine costs are high. Compared with other traditional cleaning equipment such as dry ice cleaning machines and ultrasonic cleaning machines, the cost of laser cleaning machines is relatively high. While large manufacturing companies can accept the high initial cost of a laser cleaning machine, it is not a cost-effective solution for small businesses providing surface cleaning.
- Not suitable for workpieces with narrow space. Laser cleaning is good at treating surface dirt on flat materials, but it is difficult for laser cleaning to work on workpieces with narrow spaces. For example, when cleaning the inner wall of a pipeline, it is difficult for the laser to be irradiated for cleaning. For this type of material, chemical or ultrasonic cleaning is more effective.
- Highly reflective materials are not suitable. If the material is reflective, the laser does not apply heat to the contaminants and therefore cannot remove them.
- The limitations of laser cleaning also show up on tougher jobs. For example, the effect is not ideal when removing thick rust or paint from a large area. Of course, this is also a problem faced by many other traditional cleaning methods.
Summarize
Laser cleaning is an interesting new technology that excels at performing a variety of cleaning tasks, such as surface rust removal, paint removal, and oil removal. It’s clear that while laser cleaning isn’t right for every job or business, it does work well on most cleaning projects. If you are considering adding laser cleaning to your surface preparation plan, consider whether the advantages listed above outweigh the disadvantages. Only by choosing the appropriate cleaning technology according to the cleaning project can the enterprise truly benefit. AccTek Laser focuses on the expertise and application of laser cleaning solutions, if you are interested in laser cleaning, you can always contact us for more information.
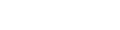
Contact information
- [email protected]
- [email protected]
- +86-19963414011
- No. 3 Zone A, Lunzhen Industrial Zone,Yucheng City , Shandong Province.
Get Laser Solutions