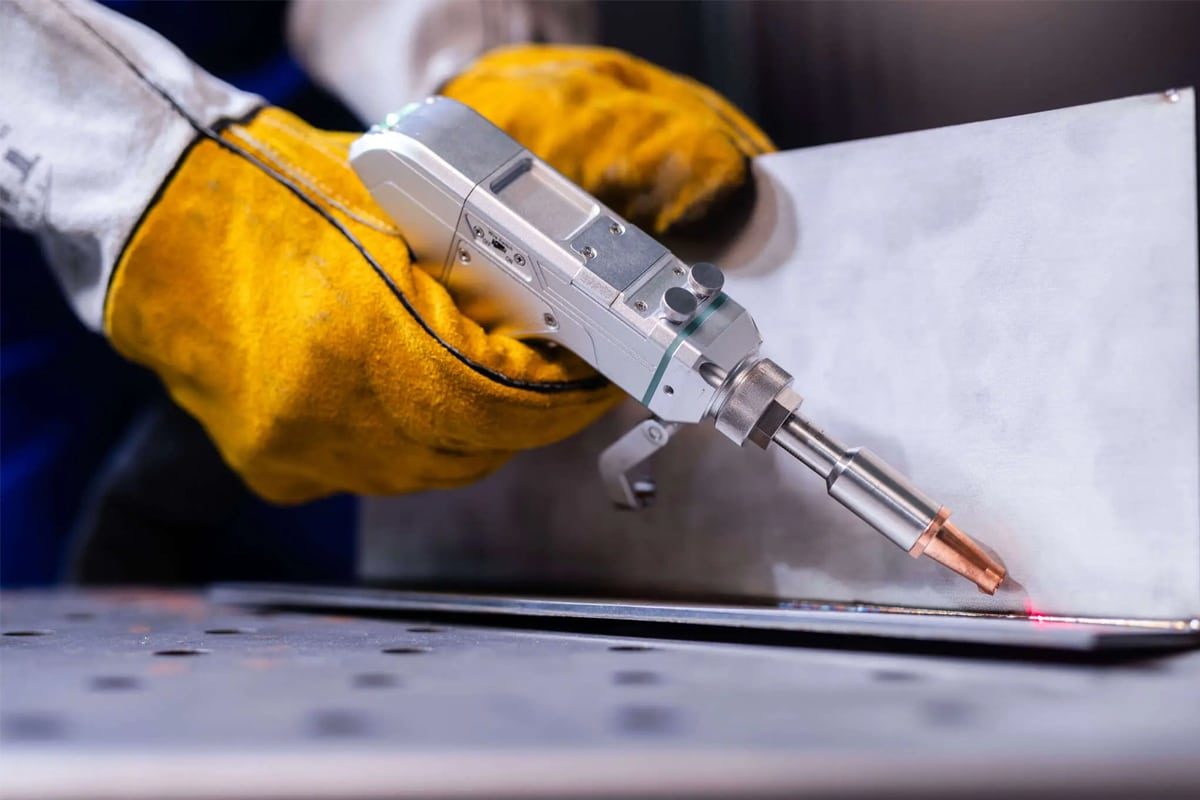
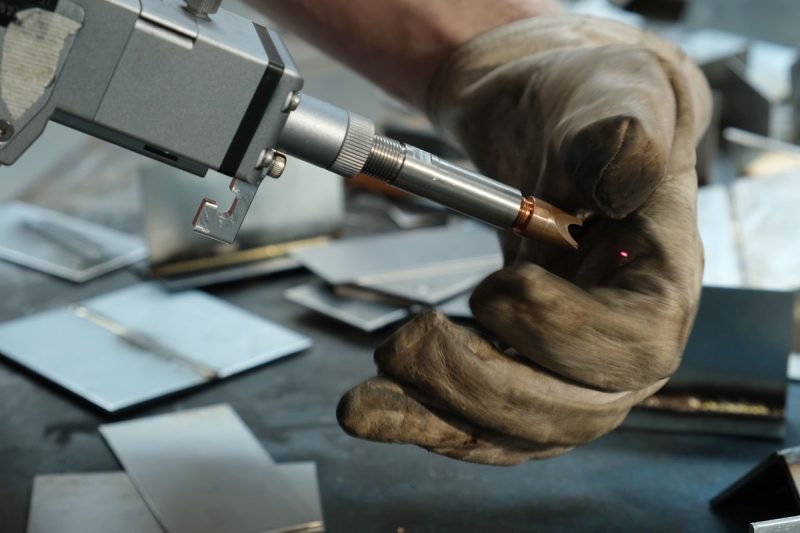
How Laser Welding Works
Principles of Laser Welding
Laser welding works by focusing high-energy laser light on a small area of the material. This concentrated energy heats the material rapidly, causing it to melt and fuse. Unlike traditional welding, which often relies on broader heat zones, laser welding focuses on creating minimal heat-affected zones, reducing distortion, and providing cleaner, high-quality joints. The fusion occurs in one of two primary modes: Conduction Mode or Keyhole Mode.
- Laser Power and Focus: The laser’s power density and spot size determine the depth and width of the weld. Higher power densities produce deeper welds, while lower power settings are used for finer, shallow welds.
- Heat Control: Laser welding allows for precise control over the heat input, essential for joining heat-sensitive materials or intricate parts.
Types of Laser Welding Modes
Conduction Mode Welding
Features:
- Shallow weld penetration, typically less than 2 mm.
- Smooth, wide welds with minimal surface deformation.
- Minimal risk of keyhole formation, reducing the likelihood of porosity or voids.
Applications:
- Commonly used for thin materials and applications where visual quality is crucial.
- Ideal for applications in jewelry, medical devices, and electronics where a clean surface finish is required.
Keyhole Mode Welding
Features:
- Deep weld penetration (up to several centimeters) with narrow width.
- High aspect ratio, resulting in strong, focused welds.
- Efficient energy absorption due to multiple reflections within the keyhole promotes deeper weld penetration.
Applications:
- Suitable for heavy-duty applications requiring strong, durable joints, such as in automotive and aerospace components.
- Effective for thick materials and high-strength metals where deep fusion is required.
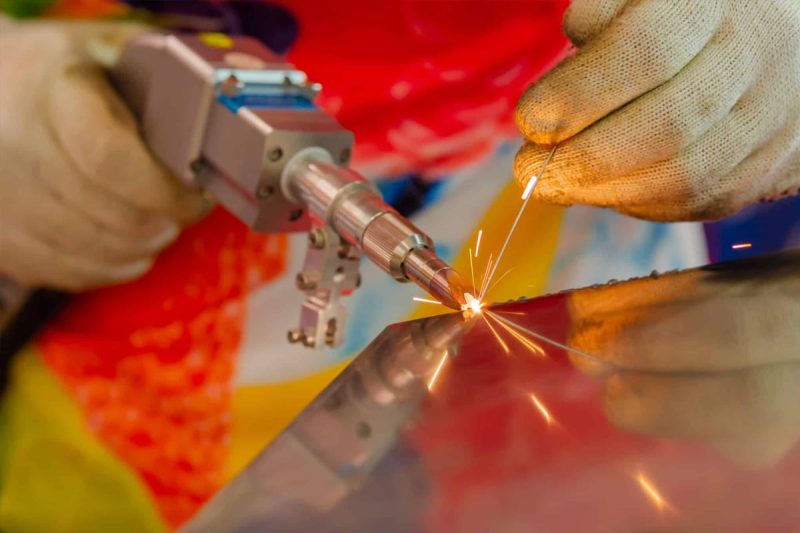
Advantages of Laser Welding
Precision and Accuracy
High Welding Speed
Non-Contact Process
Deep Penetration and Narrow Welds
Ability to Weld Difficult Materials
Minimal Distortion and Heat-Affected Zones
Clean and Aesthetic Welds
Low Maintenance and Operational Costs
Energy Efficiency
Automation and Flexibility
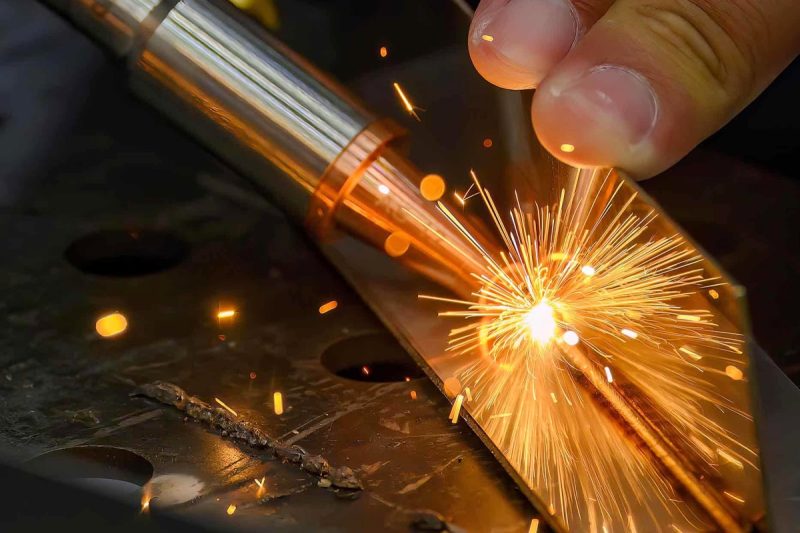
Disadvantages of Laser Welding
High Initial Investment
Limited Thickness Welding
Sensitivity to Joint Fit-Up
Safety Concerns
Reflectivity Issues
Technical Complexity
Equipment Sensitivity
Limited Field Use
Requires Skilled Operators
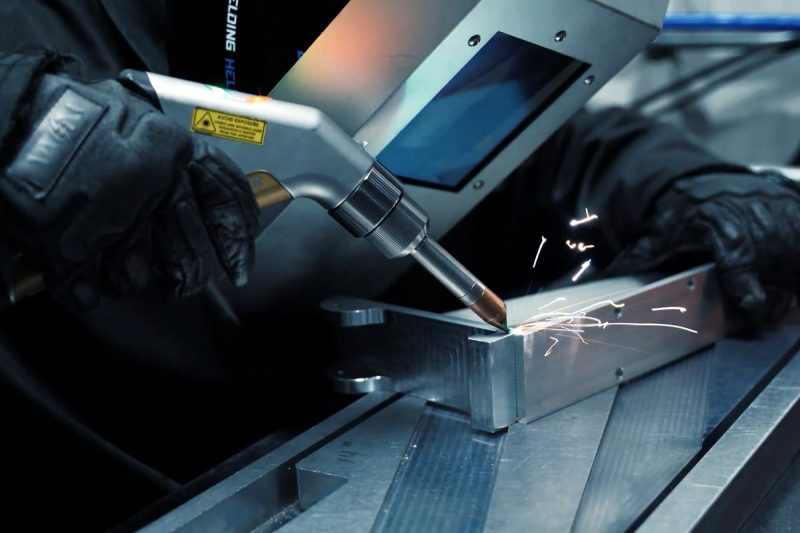
Applications of Laser Welding
Automotive Industry
Applications in Automotive:
- Body panels and tailored blanks.
- Engine components, including transmission parts.
- Airbag casings require precision and reliability.
- Exhaust systems, need welds that can withstand high temperatures and pressures.
Aerospace Industry
Applications in Aerospace:
- Fuel systems and hydraulic lines require leak-proof welds.
- Structural components, including fuselage parts and landing gear.
- Turbine blades and other engine parts, where strength and temperature resistance are critical.
- Aerospace electronics, need precise, clean welds to ensure long-term reliability.
Medical Device Manufacturing
Applications in Medical Device Manufacturing:
- Surgical instruments, where corrosion resistance and cleanliness are essential.
- Medical implants, such as pacemaker casings and orthopedic devices, require biocompatible, airtight welds.
- Catheters and endoscopes need fine, precise welds on small components.
- Battery enclosures for medical devices, where the integrity of the weld is critical for long-term use.
Electronics Industry
Applications in Electronics:
- Circuit board connections, provide fine, accurate welds without damaging nearby components.
- Sensor housings and battery connections require strong, durable joints.
- Enclosures for sensitive electronic components, ensuring protection from environmental factors.
- Micro-welding in semiconductor manufacturing, where precision and cleanliness are crucial.
Jewelry Industry
Applications in Jewelry:
- Repairs on existing jewelry, such as resizing rings or fixing broken chains.
- Stone setting, enabling secure welds near precious stones without heat damage.
- Intricate metalwork on custom jewelry designs, where detailed, delicate welds are required.
- Creating mixed-metal designs, such as joining gold and platinum, with clean, invisible weld seams.
Energy Sector
Applications in Energy:
- Battery manufacturing, where laser welding creates durable connections between cells and terminals.
- Fuel cells and solar panel components, benefit from clean, precise welds.
- Oil and gas piping, where high-strength welds are essential for safety under high pressure.
- Wind turbine components, including structural parts need to endure weather exposure and mechanical stresses.
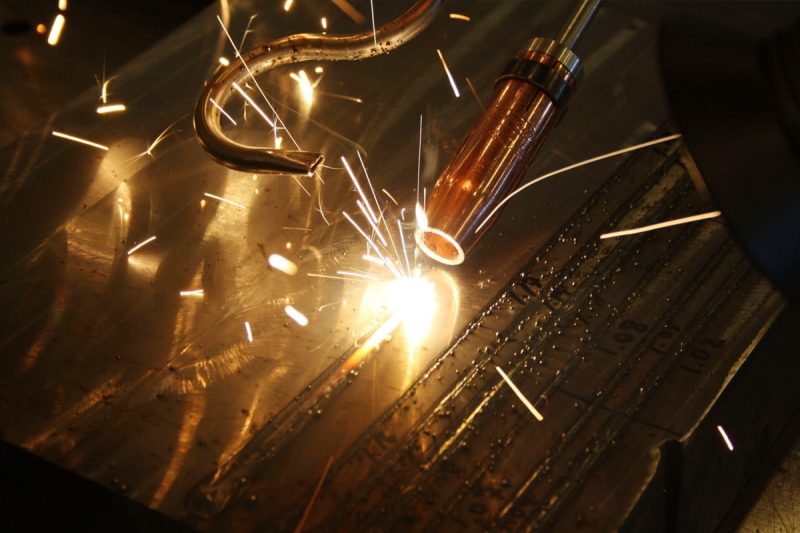
Comparison with Traditional Welding Methods
Laser Welding vs. TIG Welding
- Tungsten Inert Gas (TIG) Welding is known for producing high-quality, clean welds on a wide range of metals, including aluminum, stainless steel, and copper. TIG welding uses a tungsten electrode to create an arc between the electrode and the workpiece, melting the metal and often requiring a filler material.
- Precision and Accuracy: Both laser and TIG welding offer high precision, but laser welding has an edge due to its focused beam, which can create extremely narrow welds with minimal heat-affected zones (HAZ). TIG welding requires more manual control and is slower, making it less suited for small, intricate welds on sensitive components.
- Heat Input and Distortion: Laser welding’s concentrated energy input creates a much smaller HAZ compared to TIG welding. This reduces the risk of thermal distortion, which is particularly important for thin materials and heat-sensitive applications. TIG welding, while controlled, generates more heat spread over a larger area, which can cause warping in thinner materials.
- Speed: Laser welding is significantly faster than TIG welding, making it more suitable for high-volume production. TIG welding, while capable of producing high-quality results, is slower due to the manual operation and precision required, making it more appropriate for smaller projects or repairs.
- Applications: TIG welding is often used in small-scale and precision projects like aerospace and automotive parts but is generally limited in speed and automation compatibility. Laser welding is ideal for applications needing both speed and precision, such as electronics, medical devices, and high-volume automotive components.
Laser Welding vs. MIG Welding
- Metal Inert Gas (MIG) Welding is a common welding method used for joining thicker materials, especially in applications where speed and production volume are priorities. MIG welding uses a continuously fed wire electrode that melts to form a weld, often producing a broader weld area and requiring post-processing to remove spatter.
- Penetration and Weld Width: Laser welding can achieve deep penetration with a narrow weld bead, even on thick materials, without the need for filler material. MIG welding produces a wider, less precise weld that often requires additional cleaning and finishing. For applications requiring strong, narrow welds, laser welding is more suitable.
- Heat-Affected Zone: MIG welding generates more heat than laser welding, creating a larger HAZ and increasing the risk of thermal distortion. Laser welding’s concentrated heat reduces the HAZ, preserving the mechanical properties of the surrounding material and minimizing post-weld distortion, especially in thin or heat-sensitive materials.
- Automation and Production Speed: Laser welding is highly compatible with automation and can operate at much higher speeds, making it ideal for high-volume production environments. MIG welding, while faster than TIG, is generally more suitable for manual or semi-automated processes due to the need for wire feed and shielding gas.
- Materials: MIG welding is effective for thicker materials and commonly used metals like steel and aluminum, but it struggles with dissimilar materials and very thin materials, where precision and low heat input are required. Laser welding excels in joining both thin and dissimilar metals, such as copper to stainless steel, due to its precise energy control.
Laser Welding vs. Electron Beam Welding
- Electron Beam (EB) Welding is a high-energy welding process similar to laser welding in its ability to produce deep, precise welds. EB welding uses a focused beam of electrons in a vacuum to join materials, making it suitable for demanding applications requiring very deep penetration and a controlled environment.
- Environment and Setup: Unlike laser welding, which can operate in open air, EB welding requires a vacuum chamber to maintain the electron beam. This vacuum setup makes EB welding more complex, costly, and less flexible than laser welding, which can be used in a broader range of environments, including clean rooms or semi-automated production lines.
- Penetration Depth and Strength: EB welding can achieve deeper penetration than laser welding, making it ideal for thick materials or structural applications that require very strong welds. However, for moderately thick to thin materials, laser welding is often more efficient and easier to implement.
- Speed and Automation: Laser welding can achieve higher speeds and is easier to integrate into automated production lines, making it suitable for high-volume production. EB welding, while effective, is generally slower and less adaptable to automated, fast-paced production environments due to the vacuum chamber requirements.
- Cost and Maintenance: EB welding systems are costly and require specialized maintenance, particularly for the vacuum system. Laser welding has lower maintenance requirements, making it more accessible and cost-effective for regular manufacturing. Additionally, the setup time and maintenance for EB welding can lead to longer downtimes compared to laser welding.
Comparison
- Precision and Clean Welds: Laser welding surpasses MIG and TIG welding in precision while competing with EB welding for clean, precise results.
- Speed: Laser welding is faster than both TIG and MIG welding and generally more suitable for automated, high-speed production, especially where precision is required.
- Environment: Laser welding’s flexibility in air-based environments makes it more versatile than EB welding, which requires a vacuum.
- Heat-Affected Zone: Laser welding’s minimal HAZ makes it ideal for thin and heat-sensitive materials, outperforming TIG and MIG welding in this regard.
- Cost and Complexity: Laser welding has a high initial cost but offers lower maintenance and operating costs compared to EB welding, which involves more complex equipment and maintenance needs.
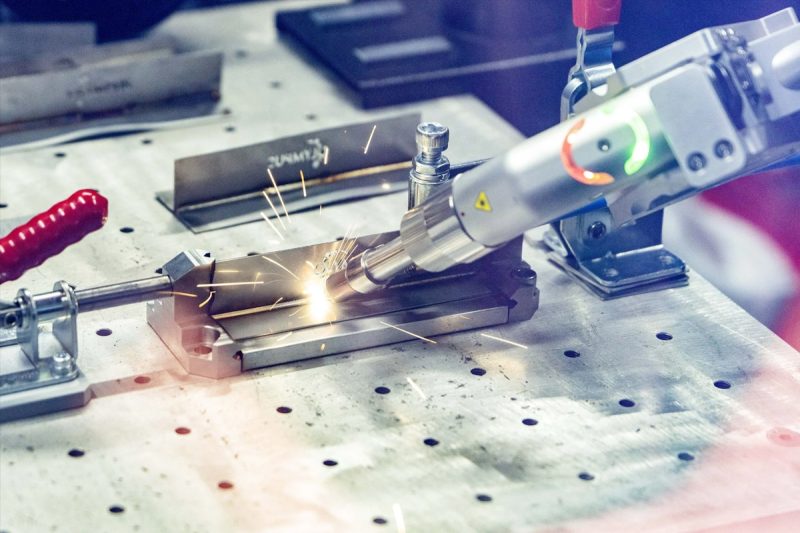
Factors Affecting Laser Welding Quality
Laser Parameters
The settings and characteristics of the laser itself play a crucial role in determining the quality of the weld. Key laser parameters include power, focus spot size, welding speed, and pulse frequency (for pulsed lasers).
- Laser Power: Higher power increases penetration depth and allows for faster welding but can lead to excessive heat if not controlled properly. Too much power may cause spattering or burning, while too little power can result in weak or incomplete welds.
- Welding Speed: The speed at which the laser moves over the workpiece affects weld quality. High welding speeds can reduce heat input, minimizing the heat-affected zone (HAZ) and reducing distortion. However, speeds that are too high may prevent full fusion of the materials, resulting in weak joints. Slower speeds allow for deeper penetration but can increase heat buildup, potentially causing thermal distortion.
- Focus Spot Size: A smaller focus spot size concentrates energy on a tiny area, allowing for fine, narrow welds. The focus spot size should match the joint width; if it’s too large, it may cause excessive heat and distortion. If it’s too small, it may not penetrate deeply enough for thicker materials.
- Pulse Frequency (Pulsed Lasers): For applications requiring pulsed lasers, adjusting pulse frequency helps control the amount of energy delivered to the weld. Higher pulse frequencies can provide smoother, continuous welds, while lower frequencies deliver intermittent energy bursts, useful for applications that need minimal heat input.
Material Properties
The material being welded influences how the laser interacts with the surface and penetrates the metal. Factors like reflectivity, thermal conductivity, and alloy composition all affect the weld quality.
- Reflectivity: Materials with high reflectivity, such as aluminum and copper, can reflect a significant portion of the laser’s energy, reducing absorption. Lower laser wavelengths or pre-treating reflective materials can help increase absorption and improve weld quality.
- Thermal Conductivity: Materials with high thermal conductivity, such as copper, quickly dissipate heat, requiring higher laser power or adjusted parameters to achieve proper penetration. Materials with low conductivity, like titanium, retain heat, allowing for deeper welds with less power.
- Alloy Composition: Alloys often have varying melting points and may require different laser settings to achieve consistent welds. Some alloys also produce more spatter or require different pulse frequencies to avoid cracking, particularly those with elements that can evaporate at welding temperatures.
- Surface Condition: The cleanliness and finish of the material’s surface impact how well the laser beam is absorbed. Oxides, oils, or surface contaminants can disrupt the welding process and lead to weaker joints. Cleaning or surface preparation before welding can help enhance weld consistency and strength.
Joint Design and Fit-Up
The design of the joint and the fit-up quality significantly affect the final weld quality. Proper joint design and tight fit-up ensure that the laser can precisely fuse the materials without gaps or misalignment.
- Joint Design: Different joint types (such as butt joints, lap joints, and fillet joints) require specific laser settings and focus to ensure optimal results. For instance, butt joints may need deeper penetration, while lap joints can be shallower but require control to avoid excessive heat spread.
- Fit-Up Precision: Precise alignment between the parts is essential for consistent weld quality. Any gaps or misalignments can lead to incomplete fusion, creating weak spots in the weld. Tight fit-ups ensure the laser energy is effectively absorbed across the joint, minimizing the chance of defects. For applications that require extremely close tolerances, clamping and fixturing systems may be used to hold parts securely during welding.
- Thickness Compatibility: Joint thickness also affects the weld’s strength. When welding thick materials, the laser parameters must be adjusted to penetrate fully without overheating the surrounding material. Thin materials, in contrast, require lower power settings to avoid warping or burn-through.
Shielding Gas
Using shielding gas helps protect the weld area from contamination and oxidation, which can impact weld quality and appearance. The choice and flow of shielding gas play a significant role in achieving high-quality welds.
- Gas Type: Common shielding gases include argon, helium, and nitrogen. Argon provides a stable atmosphere and is widely used for a variety of metals. Helium is often used for deep penetration due to its high thermal conductivity, but it’s more expensive. Nitrogen is sometimes used for specific materials, like stainless steel, but can cause nitrides in some metals, potentially affecting strength.
- Gas Flow Rate: The flow rate of the shielding gas must be adjusted according to the material and welding parameters. Too high a flow rate can disrupt the weld pool and lead to turbulence, while too low a flow rate may not fully protect the weld, allowing oxidation and leading to discoloration or porosity.
- Delivery Method: Shielding gas can be delivered directly through a nozzle near the laser head or, in some cases, through a secondary gas line for more coverage. Proper gas delivery ensures even distribution, protecting the weld from air exposure and promoting a clean, aesthetic weld finish.

Summary
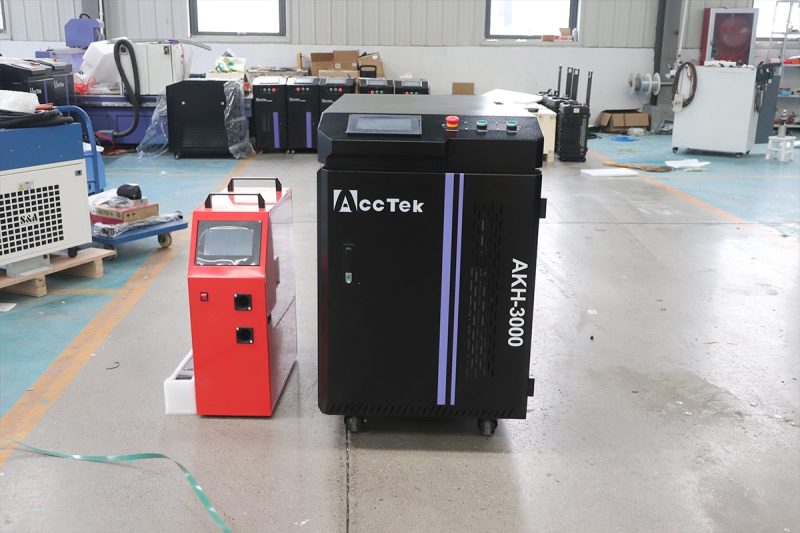
Get Laser Welding Solutions
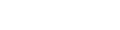
- [email protected]
- [email protected]
- +86-19963414011
- No. 3 Zone A, Lunzhen Industrial Zone,Yucheng City , Shandong Province.