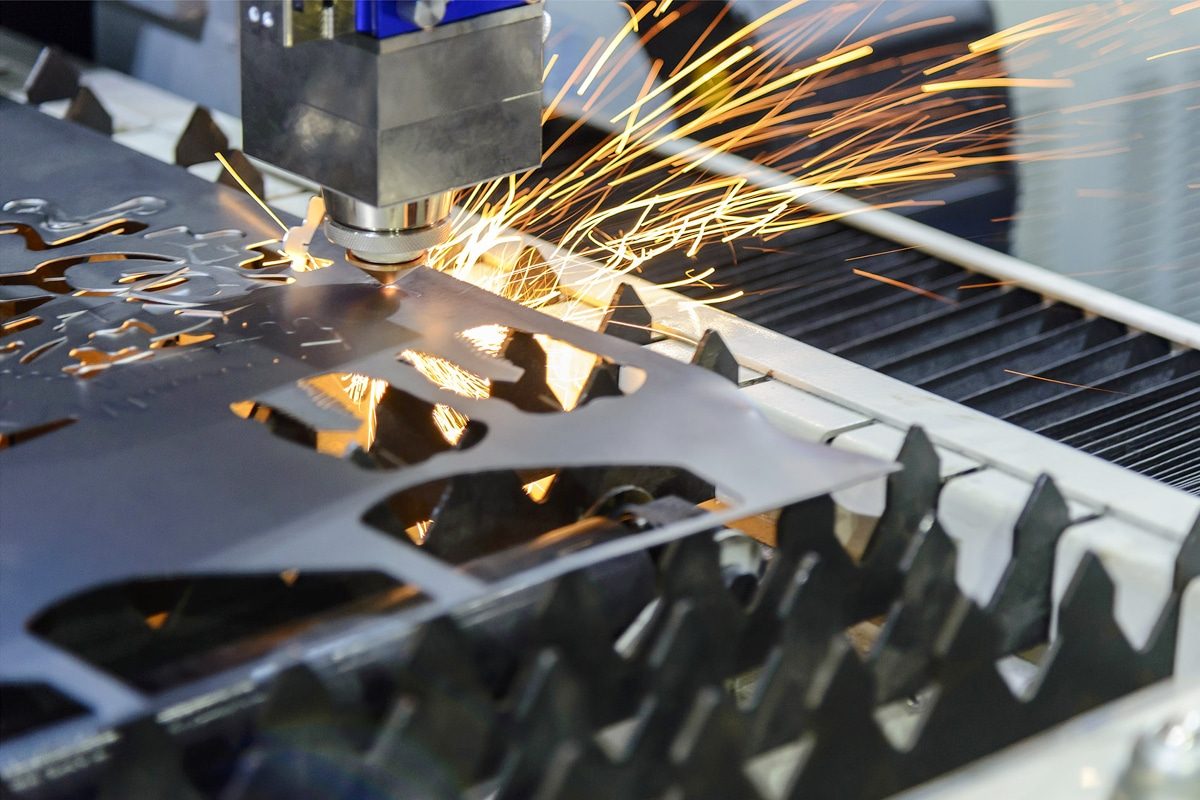
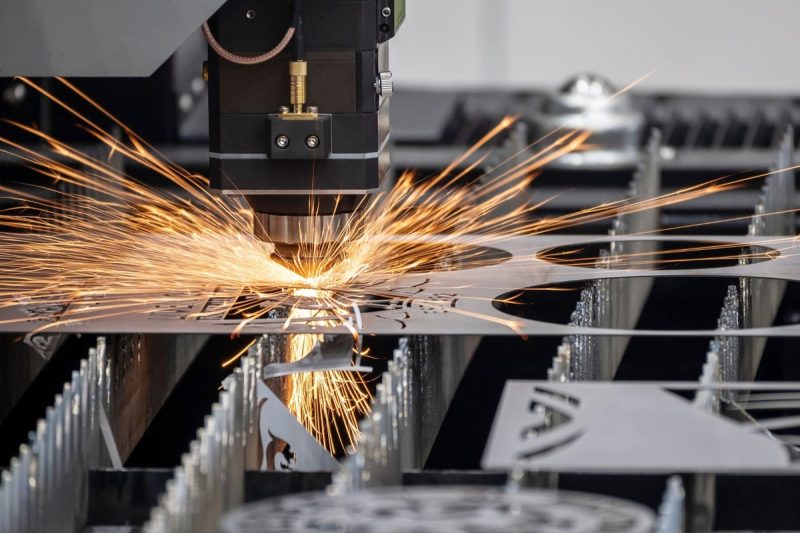
تعرف على القطع بالليزر
وصف القطع بالليزر
أنواع الليزر المستخدم في تطبيقات القطع
ليزر الألياف
ليزر ثاني أكسيد الكربون
مكونات نظام القطع بالليزر
نموذجي نظام القطع بالليزر يتكون من عدة مكونات رئيسية تعمل معًا لتوفير أداء قطع دقيق وفعال:
- مصدر الليزر: هذا هو المكون الأساسي الذي ينتج شعاع الليزر. اعتمادًا على التطبيق، يمكن أن يكون مصدر الليزر عبارة عن مولد ليزر ألياف، أو مولد ليزر ثاني أكسيد الكربون، أو أي نوع آخر من مولدات الليزر.
- البصريات: تستخدم المرايا والعدسات لتوجيه شعاع الليزر وتركيزه على المادة التي يتم قطعها. تؤثر جودة البصريات على دقة وكفاءة عملية القطع.
- رأس القطع: يحتوي رأس القطع على عدسة التركيز والفوهة التي يتم من خلالها توجيه شعاع الليزر والغاز المساعد. وهي مسؤولة عن الحفاظ على البعد البؤري الصحيح وضمان ظروف القطع المثالية.
- طاولة العمل: تدعم المادة التي يتم قطعها وتتضمن عادة آلية لتحريك المادة تحت رأس القطع.
- جهاز التحكم CNC: يقوم جهاز التحكم CNC بإدارة حركة رأس القطع بالليزر وقطعة الشغل، باتباع مسار القطع المبرمج لإنتاج الشكل والنمط المطلوب.
- مساعدة إمداد الغاز: يساعد الغاز المساعد في عملية القطع عن طريق نفخ المواد المنصهرة، وتبريد منطقة القطع، ومنع الأكسدة. تشمل الغازات المساعدة الشائعة الأكسجين والنيتروجين والهواء المضغوط.
- نظام العادم: يزيل الأبخرة والحطام الناتج أثناء عملية القطع للحفاظ على بيئة عمل نظيفة وحماية البصريات ومكونات الليزر.
- نظام التبريد: يولد القطع بالليزر الكثير من الحرارة التي يجب تبديدها لمنع تلف مصدر الليزر والمكونات الأخرى. وتستخدم أنظمة التبريد، مثل مبردات المياه، للحفاظ على درجات حرارة التشغيل المثلى.
المعلمات الرئيسية التي تؤثر على أداء القطع بالليزر
يمكن أن تؤثر العديد من المعلمات على أداء وجودة عملية القطع بالليزر. يمكن أن يساعد فهم هذه المعلمات وتحسينها في تحقيق النتائج المرجوة:
- طاقة الليزر: يحدد خرج الطاقة لمصدر الليزر سمك ونوع المادة التي يمكن قطعها. تسمح القوى الأعلى بقطع المواد السميكة، ولكن قد يلزم تعديل المعلمات الأخرى للحفاظ على جودة القطع.
- سرعة القطع: السرعة التي يتحرك بها رأس القطع عبر قطعة العمل. تضمن سرعة القطع المثالية التوازن بين الإنتاجية وجودة القطع. يمكن أن تؤدي السرعة العالية جدًا إلى قطع غير مكتمل، في حين أن السرعة البطيئة جدًا يمكن أن تسبب تراكمًا مفرطًا للحرارة وتلفًا للمواد.
- الموضع البؤري: موضع النقطة المحورية لشعاع الليزر بالنسبة لسطح المادة. ويضمن التركيز الصحيح أقصى كثافة للطاقة عند نقطة القطع، مما يؤدي إلى عمليات قطع نظيفة ودقيقة. يمكن أن يؤدي عدم المحاذاة إلى ضعف جودة القطع وانخفاض الكفاءة.
- نوع الغاز المساعد وضغطه: إن نوع وضغط الغاز المساعد المستخدم (الأكسجين أو النيتروجين أو الهواء المضغوط) له تأثير كبير على عملية القطع. يعمل الاختيار الصحيح للغاز والضغط على تحسين إزالة المواد المنصهرة، ومنع الأكسدة، وتحسين جودة القطع.
- نوع المادة وسمكها: تتفاعل المواد والسماكات المختلفة بشكل مختلف مع القطع بالليزر. عند تحديد معلمات القطع، يجب مراعاة خصائص المواد مثل الانعكاس، والتوصيل الحراري، ونقطة الانصهار.
- جودة الشعاع: تؤثر جودة شعاع الليزر، التي تتميز بتركيزه وبنيته الوضعية، على دقة القطع وجودته. ينتج شعاع عالي الجودة ذو حجم بؤري صغير قطعًا أدق مع الحد الأدنى من عرض القطع.
- تصميم الفوهة: يؤثر تصميم الفوهة، بما في ذلك قطرها وشكلها، على تدفق الغاز المساعد وإزالة المواد المنصهرة. يعمل تصميم الفوهة الأمثل على تحسين كفاءة القطع وجودته.
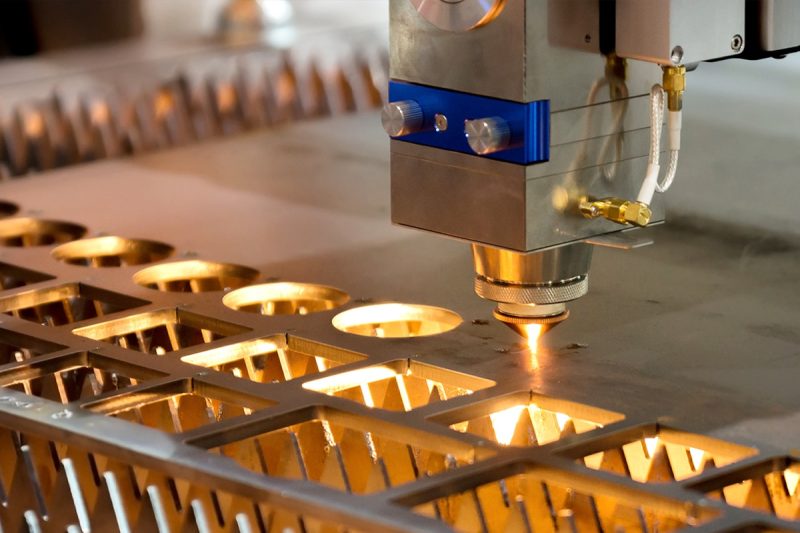
دور الغازات المساعدة في القطع بالليزر
إزالة المواد المنصهرة
أثناء عملية القطع بالليزر، يقوم شعاع ليزر عالي الكثافة بإذابة المادة عند نقطة القطع. يتم توجيه الغاز المساعد من خلال فوهة إلى منطقة القطع، حيث يساعد على إزالة المواد المنصهرة من الشق (الفجوة التي أحدثها الليزر). إن إزالة المواد المنصهرة بشكل فعال يحافظ على جودة القطع ويمنع العيوب.
- النفث الفعال: يعمل الضغط العالي للغاز المساعد على نفخ المواد المنصهرة بعيدًا عن الشق، مما يمنعها من إعادة التصلب على قطعة العمل ويضمن قطعًا نظيفًا.
- منع تكوين الخبث: من خلال إخلاء المواد المنصهرة بسرعة، يقلل الغاز المساعد من تكوين الخبث (المادة المتبقية الملتصقة بالسطح السفلي للقطع)، مما يقلل الحاجة إلى المعالجة اللاحقة.
- الحفاظ على عرض الشق: تساعد الإزالة المستمرة للمواد المنصهرة في الحفاظ على عرض الشق المطلوب، مما يضمن دقة الأبعاد ودقة القطع النهائي.
تبريد منطقة القطع
يمكن أن تسبب الحرارة الشديدة الناتجة عن شعاع الليزر تأثيرات حرارية كبيرة على قطعة العمل، بما في ذلك الاعوجاج والتشوه والتغيرات في خصائص المواد. يساعد الغاز المساعد في التحكم في هذه التأثيرات الحرارية عن طريق تبريد منطقة القطع.
- تبديد الحرارة: يمتص تدفق الغاز المساعد الحرارة الزائدة في منطقة القطع ويبددها، مما يمنع ارتفاع درجة الحرارة ويقلل التشوه الحراري للمادة.
- تقليل المنطقة المتضررة بالحرارة (HAZ): يساعد تبريد منطقة القطع على الحد من حجم المنطقة المتضررة بالحرارة، والحفاظ على الخواص الميكانيكية للمادة وتقليل مخاطر الالتواء أو أي ضرر حراري آخر.
- زيادة سرعات القطع: يعمل التبريد الفعال على زيادة سرعات القطع لأن المادة تكون أقل عرضة لتطور العيوب الناجمة عن الحرارة، مما يؤدي إلى إنتاج أسرع وأكثر كفاءة.
حماية العدسة
تقوم العدسة الموجودة في رأس القطع بتركيز شعاع الليزر على قطعة العمل. يمكن أن تؤدي الملوثات مثل الدخان والغبار والحطام المتولدة أثناء عملية القطع إلى إتلاف العدسة أو تقليل أدائها. يساعد الغاز على حماية العدسة من الملوثات.
- حماية العدسة: يشكل الغاز المساعد حاجزًا بين العدسة ومنطقة القطع، مما يمنع الملوثات من الوصول إلى سطح العدسة وترسبها.
- الحفاظ على الجودة البصرية: من خلال الحفاظ على العدسة نظيفة وخالية من الحطام، يضمن الغاز المساعد التركيز الأمثل للشعاع وأداء القطع المتسق.
- إطالة عمر العدسة: يؤدي منع التلوث إلى تقليل تآكل العدسة، مما يطيل عمرها ويقلل تكاليف الصيانة.
تعزيز رد فعل القطع
يمكن أن تؤثر الغازات المساعدة على التفاعلات الكيميائية التي تحدث أثناء القطع بالليزر، وبالتالي تحسين أداء القطع للمواد المختلفة. يمكن لنوع الغاز المستخدم أن يعزز أو يمنع تفاعلات معينة، مما قد يؤثر على جودة القطع وكفاءته.
- الأكسجين (O₂): يستخدم الأكسجين عادة لقطع الفولاذ الكربوني. إنه يعزز التفاعل الطارد للحرارة مع المعدن المنصهر، مما يولد حرارة إضافية، مما يزيد من سرعة القطع. يساعد هذا التفاعل في إنتاج قطع نظيف بكمية أقل من الخبث ولكنه يمكن أن يسبب أكسدة على حافة القطع.
- النيتروجين (N₂): النيتروجين هو غاز خامل يستخدم عادة لقطع الفولاذ المقاوم للصدأ والألومنيوم والمعادن غير الحديدية الأخرى. يمنع الأكسدة عن طريق تكوين جو خامل حول منطقة القطع. وينتج عن ذلك حافة نظيفة وخالية من الأكسيد، مما يجعلها مثالية للتطبيقات التي تتطلب تشطيب سطحي عالي الجودة.
- الهواء المضغوط: يعد الهواء المضغوط بديلاً فعالاً من حيث التكلفة ويمكن استخدامه لقطع مجموعة متنوعة من المواد. فهو يجمع بين خصائص الأكسجين والنيتروجين لتوفير أداء القطع المناسب بتكلفة أقل. ومع ذلك، يمكن أن يؤدي ذلك إلى ظهور شوائب تؤثر على جودة القطع.
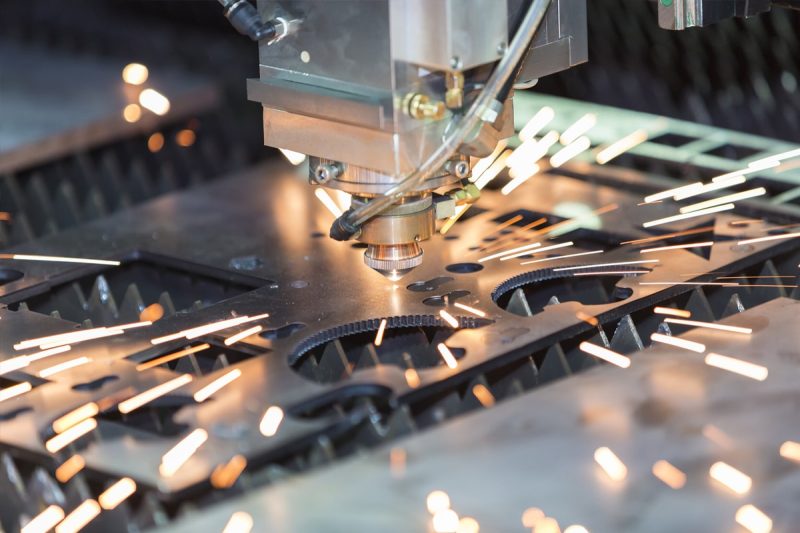
أنواع الغازات المساعدة
الأكسجين (O₂)
مزايا
- زيادة سرعة القطع: يتفاعل الأكسجين مع المادة في تفاعل طارد للحرارة، مما يؤدي إلى إطلاق حرارة إضافية. تعمل هذه الحرارة الإضافية على زيادة سرعة القطع، مما يجعل القطع بمساعدة الأكسجين أسرع بشكل ملحوظ، خاصة مع المواد السميكة.
- كفاءة محسنة: يعمل التفاعل الطارد للحرارة على تقليل طاقة الليزر اللازمة لقطع المادة، مما يحسن كفاءة الطاقة الإجمالية لعملية القطع.
- قطع أنظف على المواد السميكة: يساعد الأكسجين في إنتاج قطع أنظف على المواد السميكة، مما يقلل من الخبث والخبث، مما يقلل من الحاجة إلى معالجة لاحقة واسعة النطاق.
سلبيات
- الأكسدة: يمكن أن يتسبب التفاعل بين الأكسجين والمادة في أكسدة حافة القطع، مما يؤدي إلى تشطيب سطح أكثر خشونة ومشاكل تآكل محتملة.
- المنطقة المتأثرة بالحرارة (HAZ): تعمل الحرارة الإضافية الناتجة عن التفاعل الطارد للحرارة على زيادة حجم المنطقة المتضررة بالحرارة، مما قد يغير الخواص الميكانيكية للمادة القريبة من حافة القطع ويسبب مشكلات مثل التزييف أو انخفاض السلامة الهيكلية.
- القيود المفروضة على المعادن غير الحديدية: الأكسجين ليس فعالا مثل المعادن غير الحديدية مثل الألومنيوم والنحاس، والتي لا تتفاعل بسهولة مع الأكسجين.
النيتروجين (N₂)
مزايا
- القطع الخالي من الأكسدة: النيتروجين هو غاز خامل لا يتفاعل مع المادة أثناء عملية القطع. تمنع هذه الخاصية الأكسدة، مما يؤدي إلى الحصول على حافة نظيفة ومشرقة وخالية من الأكسيد، مما يجعلها مثالية للتطبيقات التي تتطلب تشطيب سطحي عالي الجودة.
- تشطيب سطحي عالي الجودة: يؤدي غياب الأكسدة إلى حافة أكثر سلاسة وسطحًا أكثر سلاسة، مما يقلل أو يلغي الحاجة إلى المعالجة اللاحقة.
- المنطقة المصغرة المتأثرة بالحرارة (HAZ): يساعد النيتروجين في الحفاظ على منطقة صغيرة متأثرة بالحرارة، مما يحافظ على الخواص الميكانيكية للمادة ويقلل التشوه الحراري. ويمكن استخدام ذلك لتحقيق عمليات قطع دقيقة وتطبيقات تتطلب تفاوتات مشددة.
سلبيات
- سرعات قطع أبطأ: بدون التفاعل الطارد للحرارة الذي يوفره الأكسجين، يؤدي القطع بمساعدة النيتروجين عادةً إلى سرعات قطع أبطأ، خاصة مع المواد السميكة. تؤثر هذه السرعة البطيئة على الإنتاجية الإجمالية.
- متطلبات طاقة الليزر الأعلى: نظرًا لأن النيتروجين لا يوفر حرارة إضافية لعملية القطع، فيجب أن يوفر الليزر كل الطاقة اللازمة لقطع المادة. يمكن أن يؤدي هذا المطلب إلى ارتفاع استهلاك الطاقة وتكاليف التشغيل.
- اعتبارات التكلفة: يمكن أن يكون النيتروجين أكثر تكلفة من الغازات الأخرى، كما أن الاستهلاك المتزايد الناتج عن ارتفاع متطلبات طاقة الليزر يمكن أن يؤدي إلى زيادة تكاليف التشغيل.
هواء مضغوط
مزايا
- فعال من حيث التكلفة: الهواء المضغوط متاح بسهولة أكبر وأقل تكلفة من الغازات النقية مثل النيتروجين والأكسجين. وهذا يجعله خيارًا اقتصاديًا للعديد من تطبيقات القطع بالليزر، خاصة تلك التي تتضمن مواد أقل سمكًا.
- تعدد الاستخدامات: يمكن استخدام الهواء المضغوط لقطع مجموعة واسعة من المواد، بما في ذلك الفولاذ الطري والفولاذ المقاوم للصدأ والألمنيوم. إن تعدد استخداماته يجعله خيارًا عمليًا للقطع للأغراض العامة.
- انخفاض تكاليف التشغيل: نظرًا لأن الهواء المضغوط غير مكلف ومتاح على نطاق واسع، فإن استخدام الهواء المضغوط يمكن أن يقلل من تكاليف التشغيل الإجمالية، مما يجعله مناسبًا للعمليات الصغيرة أو المشاريع ذات الميزانية المحدودة.
- الفوائد البيئية: يؤدي استخدام الهواء المضغوط إلى تقليل الاعتماد على الغاز المعبأ، مما يؤدي بدوره إلى تقليل البصمة الكربونية المرتبطة بإنتاج الغاز ونقله، مما يوفر فائدة بيئية.
سلبيات
- انخفاض جودة القطع: يمكن أن يؤثر الأكسجين والشوائب الموجودة في الهواء المضغوط على جودة القطع، مما يؤدي إلى حواف أكثر خشونة وزيادة الخبث واحتمال تلوث سطح القطع. هذه المشكلة ملحوظة بشكل خاص في التطبيقات التي تتطلب جودة سطح عالية أو دقة.
- سرعات القطع المحدودة: يقوم الهواء المضغوط عمومًا بالقطع بسرعات أبطأ من القطع بمساعدة الأكسجين، خاصة بالنسبة للمواد السميكة. يؤثر هذا القيد على الإنتاجية وقد لا يكون مناسبًا للإنتاج بكميات كبيرة.
- نتائج غير متناسقة: يمكن أن تكون جودة وأداء القطع بالهواء المضغوط غير متناسقين بسبب الاختلافات في تكوين وضغط مصدر الهواء. هذا التناقض يجعل من الصعب تحقيق نتائج موحدة من مهمة قطع إلى أخرى.
- الأكسدة وتكوين الخبث: يحتوي الهواء المضغوط على مجموعة متنوعة من الغازات، بما في ذلك الأكسجين، والتي يمكن أن تسبب الأكسدة وتكوين الخبث على حافة القطع، مما يتطلب معالجة لاحقة إضافية لتحقيق النتائج المرجوة.
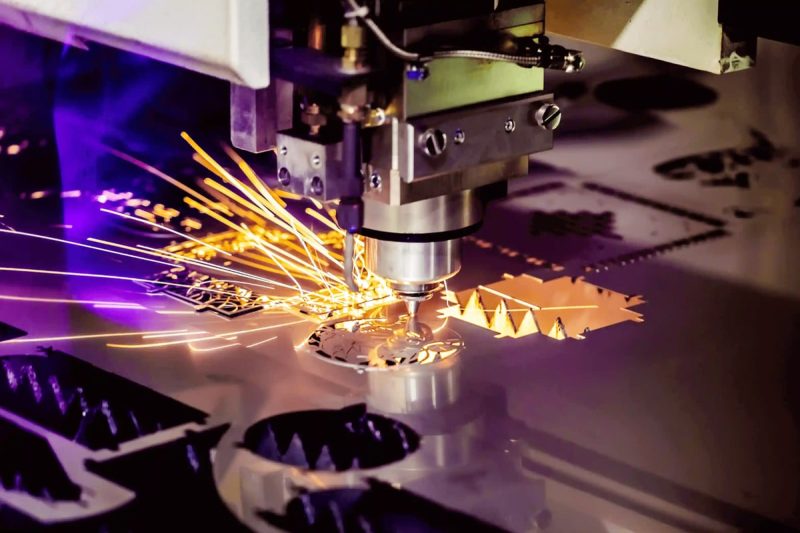
التأثير على مواد مختلفة
الكربون الصلب
الأكسجين
- المزايا: غالبًا ما يستخدم الأكسجين لقطع الفولاذ الكربوني لأنه يتفاعل طاردًا للحرارة مع المادة. يولد هذا التفاعل حرارة إضافية، مما يزيد بشكل كبير من سرعة القطع وكفاءته. عادة ما تكون القطع الناتجة نظيفة مع الحد الأدنى من الخبث، وتساعد الحرارة المعززة على قطع مقاطع الفولاذ الكربوني السميكة.
- العيوب: التفاعل الطارد للحرارة مع الأكسجين يسبب الأكسدة، والتي، إذا لم تتم معالجتها، يمكن أن تؤدي إلى تشطيب سطح أكثر خشونة واحتمال التآكل. كما أن المنطقة المتأثرة بالحرارة (HAZ) أكبر أيضًا، مما قد يؤثر على الخواص الميكانيكية للمادة القريبة من حافة القطع.
نتروجين
- المزايا: لا يتفاعل النيتروجين مع الفولاذ الكربوني، مما يمنع الأكسدة وينتج قطعًا نظيفًا وخاليًا من الأكسيد. وينتج عن ذلك تشطيب سطحي عالي الجودة وHAZ أصغر، مما يحافظ على الخواص الميكانيكية للمادة.
- العيوب: عدم وجود تفاعل طارد للحرارة يعني أن القطع بمساعدة النيتروجين يكون أبطأ من القطع بمساعدة الأكسجين. لتحقيق نفس سرعة القطع، يلزم وجود طاقة ليزر أعلى، مما يزيد من تكاليف التشغيل.
هواء مضغوط
- المزايا: الهواء المضغوط هو بديل فعال من حيث التكلفة لقطع الفولاذ الكربوني. إنها تحقق التوازن بين التكلفة والأداء وهي مناسبة لقطع مقاطع الفولاذ الكربوني الرقيقة.
- العيوب: الأكسجين الموجود في الهواء المضغوط يمكن أن يسبب بعض الأكسدة وتكوين الخبث، مما يؤثر على جودة القطع. تكون سرعات القطع وجودته أقل بشكل عام من استخدام الأكسجين النقي أو النيتروجين.
ستانلس ستيل
الأكسجين
- المزايا: يمكن استخدام الأكسجين لقطع الفولاذ المقاوم للصدأ، مما يوفر سرعات قطع عالية بسبب التفاعل الطارد للحرارة. يمكن أن يساعد رد الفعل هذا أيضًا في تحقيق عمليات قطع نظيفة بأقل قدر من الخبث.
- العيوب: استخدام الأكسجين يمكن أن يسبب الأكسدة، مما قد يؤدي إلى تغير لون الحواف ومشاكل التآكل المحتملة. قد تتطلب طبقة الأكسيد معالجة لاحقة إضافية لتحقيق جودة السطح المطلوبة.
نتروجين
- المزايا: يعتبر النيتروجين هو الغاز المفضل لقطع الفولاذ المقاوم للصدأ لأنه يمنع الأكسدة، مما يؤدي إلى الحصول على حافة نظيفة ومشرقة وخالية من الأكسيد. تنتج الطبيعة الخاملة للنيتروجين قطعًا عالية الجودة مع الحد الأدنى من الحاجة إلى المعالجة اللاحقة. يساعد النيتروجين أيضًا في الحفاظ على الخواص الميكانيكية للمادة عن طريق تقليل المنطقة المتأثرة بالحرارة.
- العيوب: يتمتع النيتروجين بسرعات قطع أبطأ ويتطلب طاقة ليزر أعلى من الأكسجين، مما يؤدي إلى زيادة استهلاك الطاقة وتكاليف التشغيل.
هواء مضغوط
- المزايا: يمكن استخدام الهواء المضغوط لقطع الأجزاء الرقيقة من الفولاذ المقاوم للصدأ. وهو أكثر فعالية من حيث التكلفة من الغاز النقي وهو خيار قابل للتطبيق للتطبيقات التي لا تتطلب دقة عالية.
- العيوب: الأكسجين الموجود في الهواء المضغوط يمكن أن يسبب الأكسدة وتكوين المخلفات، مما يؤثر على جودة القطع. قد تتطلب الحافة تنظيفًا إضافيًا وتشطيبًا بعد القطع.
الألومنيوم والمعادن غير الحديدية
الأكسجين
- المزايا: لا يُنصح عمومًا باستخدام الأكسجين لقطع الألومنيوم والمعادن غير الحديدية الأخرى نظرًا لانعكاسها العالي وانخفاض امتصاصها لشعاع الليزر. ومع ذلك، في بعض الحالات، يمكن أن يساعد الأكسجين في قطع الأجزاء السميكة من خلال تعزيز التفاعل الطارد للحرارة.
- العيوب: يمكن أن يسبب الأكسجين أكسدة شديدة، مما يؤدي إلى قطع سطح خشن ومسامي. يمكن أن تؤثر هذه الأكسدة سلبًا على خصائص المادة ومظهرها، مما يتطلب معالجة لاحقة واسعة النطاق.
نتروجين
- المزايا: يعتبر النيتروجين فعالاً جداً في قطع الألمنيوم والمعادن غير الحديدية الأخرى. يمنع الأكسدة، مما يؤدي إلى حافة نظيفة ومشرقة وعالية الجودة. ويساعد النيتروجين أيضًا على تقليل المنطقة المتأثرة بالحرارة، مما يحافظ على الخواص الميكانيكية للمادة.
- العيوب: القطع بمساعدة النيتروجين أبطأ من استخدام الأكسجين، ويتطلب طاقة ليزر أعلى لقطع المواد، مما يزيد من تكاليف التشغيل.
هواء مضغوط
- المزايا: يعد الهواء المضغوط خيارًا فعالاً من حيث التكلفة لقطع الأجزاء الرقيقة من الألومنيوم والمعادن غير الحديدية. يمكن أن يوفر أداء قطع مرضيًا للتطبيقات التي لا تكون فيها الدقة أمرًا بالغ الأهمية.
- العيوب: الأكسجين الموجود في الهواء المضغوط يمكن أن يسبب الأكسدة وتكوين المخلفات، مما يؤثر على جودة القطع. قد تتطلب الحواف معالجة لاحقة إضافية لتحقيق اللمسة النهائية المطلوبة.
المواد غير المعدنية
الأكسجين
- المزايا: يمكن استخدام الأكسجين لقطع المواد غير المعدنية مثل الخشب والأكريليك والبلاستيك. يمكن أن يؤدي التفاعل الطارد للحرارة مع الأكسجين إلى زيادة سرعة القطع وكفاءة بعض المواد.
- العيوب: استخدام الأكسجين يمكن أن يسبب حرق واحتراق مواد مثل الخشب والأكريليك، مما يؤثر سلبًا على جودة السطح. قد يؤدي ذلك إلى الحاجة إلى عمليات تشطيب إضافية لتحقيق المظهر المطلوب.
نتروجين
- المزايا: يعتبر النيتروجين مناسبًا تمامًا لقطع المواد غير المعدنية مثل البلاستيك والسيراميك، والتي يجب حمايتها من الأكسدة. يمنع تغير اللون وينتج حواف نظيفة وعالية الجودة مع تقليل الضرر الحراري.
- العيوب: يمكن أن يكون القطع بمساعدة النيتروجين أبطأ من الأكسجين، مما يتطلب طاقة ليزر أعلى لتحقيق سرعة القطع المطلوبة.
هواء مضغوط
- المزايا: يعد الهواء المضغوط حلاً فعالاً من حيث التكلفة لقطع المواد غير المعدنية ويوفر أداء قطع مناسبًا لمجموعة متنوعة من التطبيقات. إنها مناسبة للتطبيقات التي لا تكون فيها الدقة والجودة حاسمة.
- العيوب: يمكن أن تؤثر الشوائب الموجودة في الهواء المضغوط على جودة القطع، مما يؤدي إلى حواف خشنة وتلوث محتمل. قد لا تكون جودة القطع وسرعته مماثلة لتلك الخاصة بالغازات النقية مثل الأكسجين أو النيتروجين.
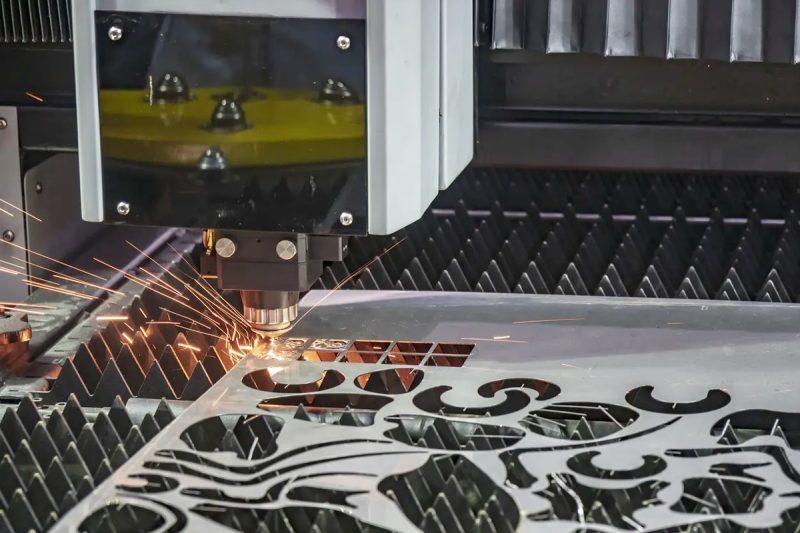
تحسين اختيار الغاز المساعد
نوع المادة وسمكها
يعد نوع وسمك المادة التي يتم قطعها من الاعتبارات الرئيسية عند اختيار الغاز المساعد. تتفاعل المواد المختلفة بشكل مختلف مع الغازات المختلفة، مما يؤثر على جودة القطع وكفاءته.
- الفولاذ الكربوني: غالبًا ما يكون الأكسجين هو الخيار الأول لقطع الفولاذ الكربوني لأنه يتفاعل طاردًا للحرارة، مما يزيد من سرعة القطع وكفاءته. بالنسبة للفولاذ الكربوني السميك، يمكن للأكسجين توفير الحرارة اللازمة لقطع المادة بشكل فعال. بالنسبة للفولاذ الكربوني الرقيق، يمكن استخدام النيتروجين للحصول على قطع نظيف وخالي من الأكسدة، وإن كان بمعدل أبطأ.
- الفولاذ المقاوم للصدأ: يعتبر النيتروجين مثاليًا لقطع الفولاذ المقاوم للصدأ لأنه يمنع الأكسدة وينتج حافة ناعمة عالية الجودة. بالنسبة للفولاذ المقاوم للصدأ السميك جدًا، يمكن استخدام الأكسجين لزيادة سرعات القطع ولكنه سيتسبب في الأكسدة، مما يتطلب معالجة لاحقة.
- الألومنيوم والمعادن غير الحديدية: النيتروجين هو الخيار الأول لقطع الألومنيوم والمعادن غير الحديدية لتجنب الأكسدة وتحقيق قطع نظيف. بالنسبة للتطبيقات الأقل أهمية، يمكن أن يكون الهواء المضغوط بديلاً فعالاً من حيث التكلفة، على الرغم من أنه قد يسبب بعض الأكسدة.
- المواد غير المعدنية: لقطع المواد غير المعدنية مثل البلاستيك والسيراميك والخشب، غالبًا ما يستخدم النيتروجين لمنع تغير اللون وتحقيق حافة عالية الجودة. يمكن استخدام الأكسجين لقطع بعض اللافلزات بشكل أسرع ولكنه قد يسبب حرقًا أو حرقًا.
جودة القطع المطلوبة
تعد جودة القطع المطلوبة عاملاً أساسيًا في اختيار الغاز المساعد المناسب. تتطلب التطبيقات الدقيقة عادةً قطعًا عالي الجودة مع الحد الأدنى من الأكسدة والحواف الناعمة.
- تشطيب سطحي عالي الجودة: غالبًا ما يكون النيتروجين هو الخيار الأفضل للتطبيقات التي تتطلب قطعًا دقيقًا ونظيفًا وخاليًا من الأكسدة. يمنع الأكسدة، مما يؤدي إلى حواف ناعمة وسطح نهائي عالي الجودة.
- الجودة العامة: يمكن أن يوفر الأكسجين قطعًا عالي الجودة بأقل قدر من الخبث، لكن الحواف قد تتطلب تنظيفًا إضافيًا بسبب الأكسدة. قد يكون الهواء المضغوط مناسبًا للتطبيقات الأقل أهمية حيث لا يكون من الضروري الحصول على تشطيب سطحي عالي الجودة.
سرعة القطع والكفاءة
تتأثر سرعة القطع وكفاءته بنوع الغاز المساعد المستخدم. الهدف هو تحقيق أعلى سرعة ممكنة دون المساس بجودة القطع.
- السرعة القصوى: توفر أسرع سرعات قطع للفولاذ الكربوني والمواد السميكة بسبب التفاعل الطارد للحرارة للأكسجين، مما يضيف حرارة إضافية إلى عملية القطع.
- موازنة السرعة والجودة: يحقق النيتروجين توازنًا بين السرعة والقطع عالي الجودة، على الرغم من أنه قد يتطلب طاقة ليزر أعلى ويقطع بسرعة أبطأ مقارنة بالأكسجين.
- سرعة فعالة من حيث التكلفة: يوفر الهواء المضغوط حلاً وسطًا بين السرعة والتكلفة، وهو مناسب للتطبيقات التي تكون فيها سرعات القطع المعتدلة والجودة المعقولة مقبولة.
اعتبارات التكلفة
تعتبر التكلفة عاملاً مهمًا في المساعدة على اختيار الغاز، مما يؤثر على نفقات التشغيل وفعالية التكلفة بشكل عام.
- انخفاض تكاليف التشغيل: الهواء المضغوط هو الخيار الأكثر اقتصادا لأنه متاح بسهولة وأرخص من الغازات النقية مثل الأكسجين والنيتروجين. إنه مثالي لقطع المواد الأقل أهمية أو عندما تكون قيود الميزانية أولوية.
- جودة أعلى وتكلفة أعلى: يوفر النيتروجين، على الرغم من كونه أكثر تكلفة، جودة قطع أفضل. يتم تبرير التكلفة الإضافية من خلال تحسين الجودة وانخفاض الحاجة إلى المعالجة اللاحقة.
- موازنة التكلفة والكفاءة: يوفر الأكسجين حلاً وسطًا، حيث يوفر سرعات قطع سريعة وجودة معقولة بتكلفة معتدلة. إنها مناسبة للعديد من التطبيقات الصناعية حيث تعد السرعة والجودة أمرًا مهمًا.
متطلبات ما بعد المعالجة
يمكن أن تؤثر احتياجات ما بعد المعالجة على اختيار الغاز المساعد، حيث تنتج بعض الغازات قطعًا أنظف، مما قد يقلل من أعمال التشطيب.
- الحد الأدنى من المعالجة اللاحقة: ينتج النيتروجين قطعًا نظيفة وخالية من الأكسدة، مما يقلل الحاجة إلى معالجة لاحقة واسعة النطاق، ويوفر الوقت والتكلفة في عمليات التشطيب.
- مرحلة ما بعد المعالجة المعتدلة: قد يتطلب قطع الأكسجين خطوات إضافية لإزالة الأكاسيد وتحقيق السطح النهائي المطلوب. ومع ذلك، فإن سرعات القطع الأعلى يمكن أن تعوض بعض التكاليف الإضافية.
- زيادة ما بعد المعالجة: قد يتسبب الهواء المضغوط في المزيد من الخبث والأكسدة، مما يتطلب معالجة لاحقة أكثر شمولاً لتنظيف الحافة وإنهائها. وهذا يمكن أن يزيد من وقت الإنتاج الإجمالي والتكلفة.
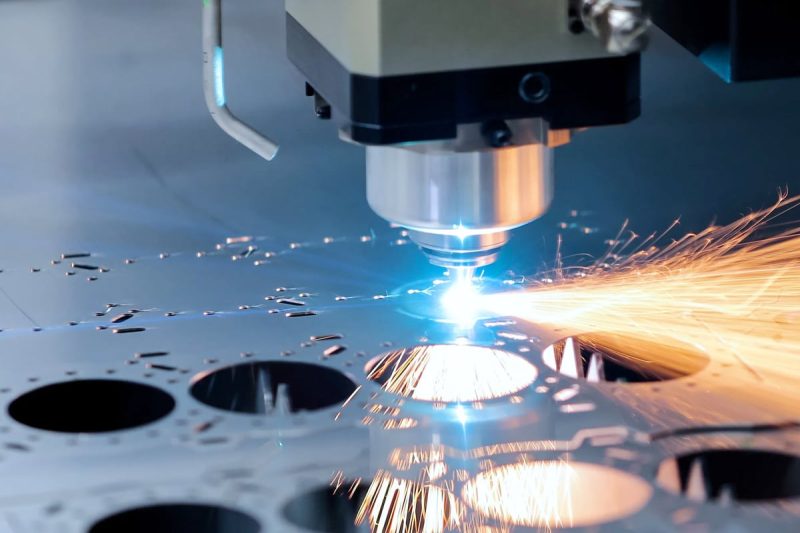
ملخص
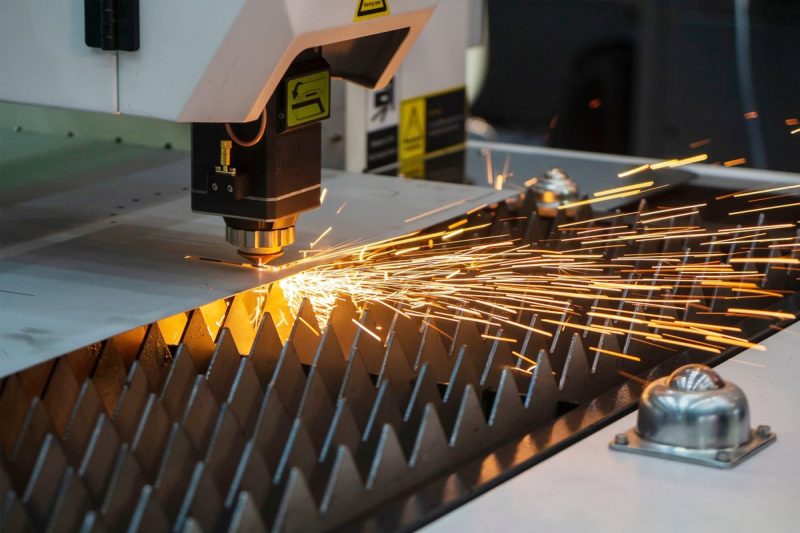
احصل على حلول القطع بالليزر
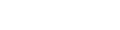
- [email protected]
- [email protected]
- +86-19963414011
- رقم 3 المنطقة أ ، المنطقة الصناعية لونجين ، مدينة يوتشنغ ، مقاطعة شاندونغ.