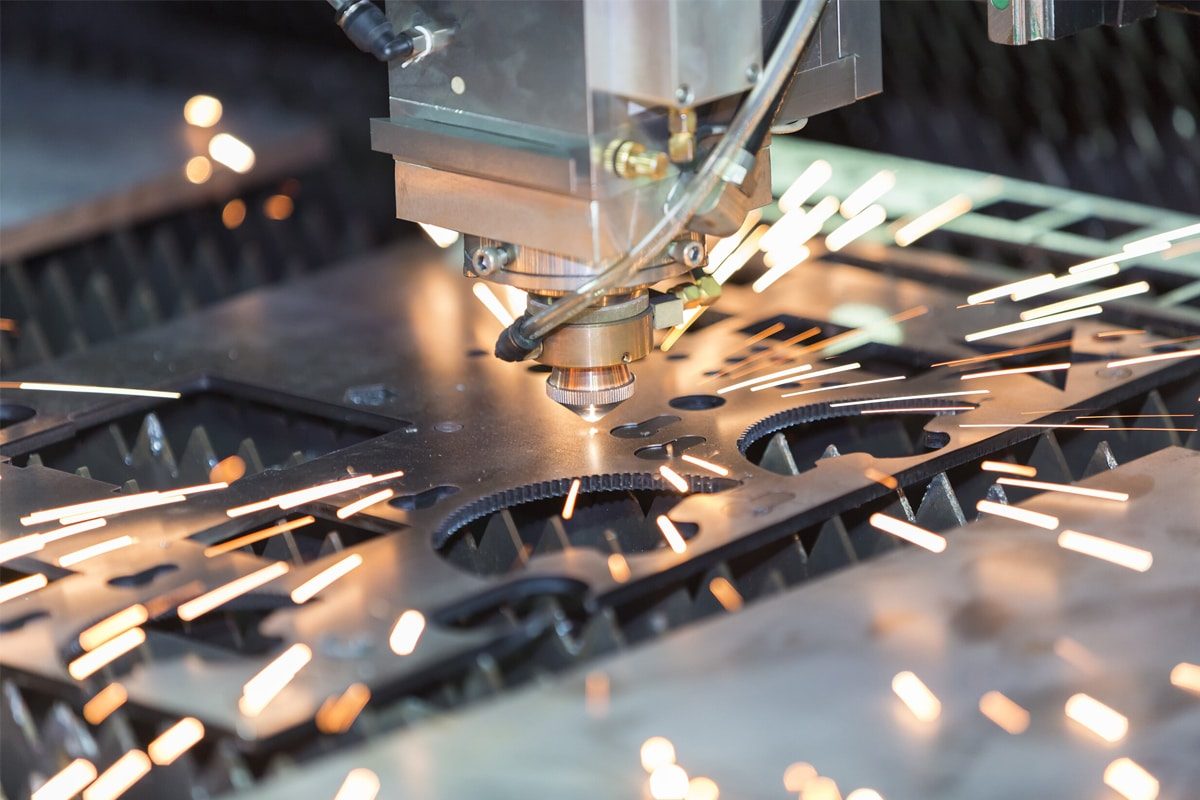
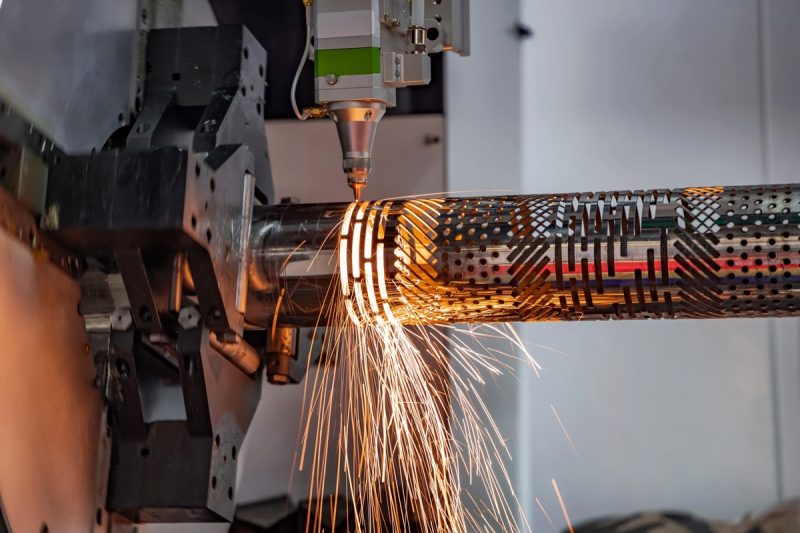
فهم قوة الليزر
ما هي قوة الليزر؟
كيف تؤثر قوة الليزر على عملية القطع
تلعب طاقة الليزر دورًا رئيسيًا في عملية القطع بالليزر، حيث تؤثر على العديد من الجوانب الرئيسية:
- سرعة القطع: تسمح قوة الليزر الأعلى بسرعات قطع أسرع. وذلك لأن المزيد من الطاقة متاحة لإذابة أو تبخير أو حرق المواد، مما يسمح بقطع أسرع. بالنسبة للتطبيقات الصناعية حيث تكون الإنتاجية العالية أمرًا بالغ الأهمية، فإن اختيار قوة ليزر أعلى يمكن أن يقلل بشكل كبير من وقت الإنتاج.
- جودة الحافة: تتأثر جودة الحافة المقطوعة بقوة الليزر. يؤدي ضبط الطاقة الأمثل إلى إنتاج حافة ناعمة ونظيفة مع تقليل النتوءات والتشوهات الحرارية. ومع ذلك، قد تؤدي الطاقة العالية جدًا إلى احتراق الحافة، والإفراط في الذوبان، واتساع منطقة التأثر بالحرارة (HAZ)، مما قد يؤثر سلبًا على جودة الحافة.
- اختراق المواد: تحدد قوة الليزر القدرة على قطع مواد ذات سماكات مختلفة. تتطلب المواد الأكثر سمكًا قوى أعلى لضمان قدرة شعاع الليزر على اختراق العمق الكامل للمادة. بالنسبة للمواد الرقيقة، غالبًا ما تكون إعدادات الطاقة المنخفضة كافية ويمكن أن تمنع تراكم الحرارة غير الضروري وتلف المواد.
- معدل إزالة المواد: يتأثر معدل إزالة المواد بقوة الليزر. تؤدي القوى الأعلى إلى معدلات إزالة مواد أعلى، وهو أمر مفيد للمواد الأكثر سمكًا ولكنه قد يؤدي إلى ذوبان أو احتراق المواد الأكثر رقة.
- الدقة والتفاصيل: بالنسبة للتصاميم المعقدة والتفاصيل الدقيقة، غالبًا ما تكون قوى الليزر المنخفضة هي الخيار الأفضل. وهذا يسمح بالتحكم الدقيق في شعاع الليزر، ويقلل من خطر الإفراط في القطع، ويضمن تقديم الميزات التفصيلية بدقة.
- التأثيرات الحرارية: يمكن أن تؤدي قوة الليزر الزائدة إلى تأثيرات حرارية ملحوظة، مثل الانحناء أو تغير اللون، وخاصة في المواد الحساسة للحرارة. يمكن أن يؤدي معايرة الطاقة المناسبة إلى تقليل هذه التأثيرات الضارة.
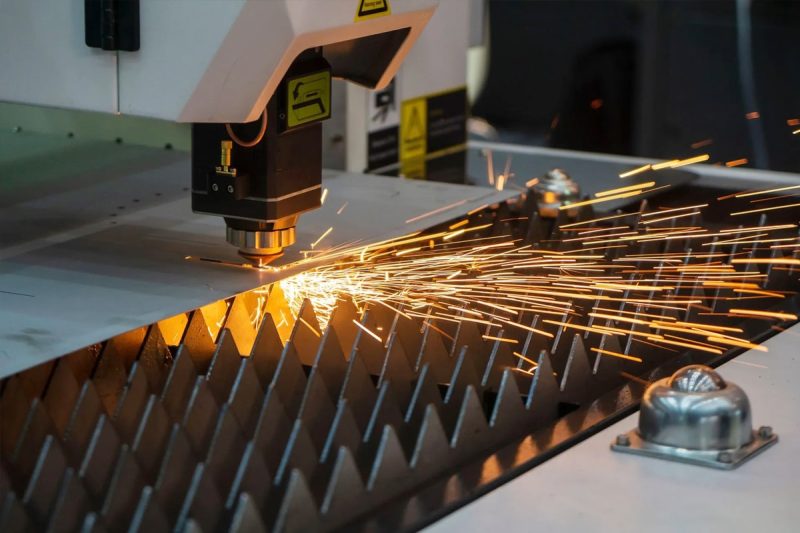
أنواع آلات القطع بالليزر
آلة قطع ألياف الليزر
الميزات الرئيسية
- الطول الموجي: عادة ما يكون حوالي 1.06 ميكرون، مما يجعله مثاليًا لقطع المعادن.
- الكفاءة: كفاءة كهروضوئية عالية، عادة ما تكون أعلى من 30%، مما يؤدي إلى انخفاض تكاليف التشغيل واستهلاك الطاقة.
- جودة الشعاع: تتيح جودة الشعاع العالية قطعًا أدق وأكثر دقة، خاصة على المواد الرقيقة.
- الصيانة: نظرًا لعدم وجود أجزاء متحركة في مصدر الليزر، فإن متطلبات الصيانة منخفضة.
التطبيقات
- المواد: مثالية لقطع المعادن، بما في ذلك الفولاذ والفولاذ المقاوم للصدأ والألومنيوم والنحاس والنحاس الأصفر.
- السمك: مناسب للقطع عالي الدقة للمواد الرقيقة إلى المتوسطة السمك.
- الصناعات: تستخدم على نطاق واسع في صناعات الطيران والسيارات والإلكترونيات وتصنيع المعادن.
مزايا
- السرعة: سرعات قطع أسرع مقارنة بأشعة الليزر CO₂ وNd، وخاصة عند قطع المواد الرقيقة.
- الدقة: دقة عالية وجودة حافة عالية بسبب الشعاع الرقيق.
- كفاءة كهروضوئية عالية: كفاءة أعلى، مما يؤدي إلى انخفاض استهلاك الطاقة وتكاليف التشغيل.
- فعالية من حيث التكلفة: عمر خدمة طويل ومتطلبات صيانة منخفضة.
سلبيات
- التكلفة الأولية: استثمار أولي أعلى مقارنة بمولدات الليزر ثاني أكسيد الكربون.
- القيود المادية: أقل فعالية على المواد غير المعدنية مثل الخشب والبلاستيك.
آلة القطع بليزر CO2
الميزات الرئيسية
- الطول الموجي: حوالي 10.6 ميكرون، مثالي لقطع مجموعة واسعة من المواد، بما في ذلك المواد غير المعدنية.
- الكفاءة: الكفاءة الكهربائية أقل مقارنة بألياف الليزر.
- جودة الشعاع: جودة شعاع جيدة، مناسبة لمجموعة واسعة من مهام القطع والنقش.
- الصيانة: تتطلب صيانة منتظمة، بما في ذلك تجديد الغاز ومعايرة المرآة.
التطبيقات
- المواد: قادرة على قطع مجموعة واسعة من المواد، بما في ذلك المعادن والخشب والأكريليك والزجاج والمنسوجات والبلاستيك.
- السمك: فعال لقطع المواد الرقيقة والسميكة.
- الصناعات: تستخدم في صناعة اللافتات والتغليف والأعمال الخشبية والسيارات والمنسوجات.
مزايا
- التنوع: يمكنه قطع مجموعة واسعة من المواد، بالإضافة إلى المعادن.
- التكلفة: تكلفة أولية أقل مقارنة بأجهزة الليزر الألياف.
- التوفر: تكنولوجيا ناضجة، متوفرة في مجموعة متنوعة من النماذج والتكوينات.
سلبيات
- السرعة: أبطأ لقطع المعادن مقارنة بأجهزة الليزر الألياف.
- الصيانة: متطلبات الصيانة عالية، بما في ذلك تجديد الغاز وضبط المرآة بشكل منتظم.
- استهلاك الطاقة: استهلاك الطاقة مرتفع بسبب انخفاض الكفاءة الكهربائية.
آلة القطع بالليزر Nd
الميزات الرئيسية
- الطول الموجي: حوالي 1.064 ميكرون، مشابه لليزر الألياف، ومناسب لقطع المعادن.
- أوضاع التشغيل: يمكن تشغيلها في كل من وضعي الموجة المستمرة (CW) والنبضية، مما يوفر المرونة لتطبيقات القطع والنقش.
- جودة الشعاع: جودة شعاع عالية للقطع والحفر الدقيق.
- الصيانة: صيانة منخفضة عادةً، وتصميم قوي، وعمر طويل.
التطبيقات
- المواد: مناسبة لقطع المعادن والسيراميك وبعض البلاستيك.
- السمك: مناسب للقطع الدقيق وحفر المواد الرقيقة.
- الصناعات: تستخدم عادة في الصناعات الإلكترونية، وتصنيع الأجهزة الطبية، والمجوهرات، والفضاء الجوي.
مزايا
- الدقة: دقة عالية، قادرة على إنتاج تفاصيل دقيقة.
- التشغيل النبضي: قادر على التشغيل النبضي، مثالي للحفر والنقش الدقيق.
- التوافق المادي: فعال لمجموعة واسعة من المواد، بما في ذلك المواد الصلبة والهشة.
سلبيات
- السرعة: سرعات قطع أبطأ مقارنة بمولدات الليزر الليفي.
- التكلفة: تكلفة أولية أعلى وكفاءة أقل مقارنة بالليزر ثاني أكسيد الكربون.
- متطلبات التبريد: يتطلب نظام تبريد فعال لإدارة تبديد الحرارة.
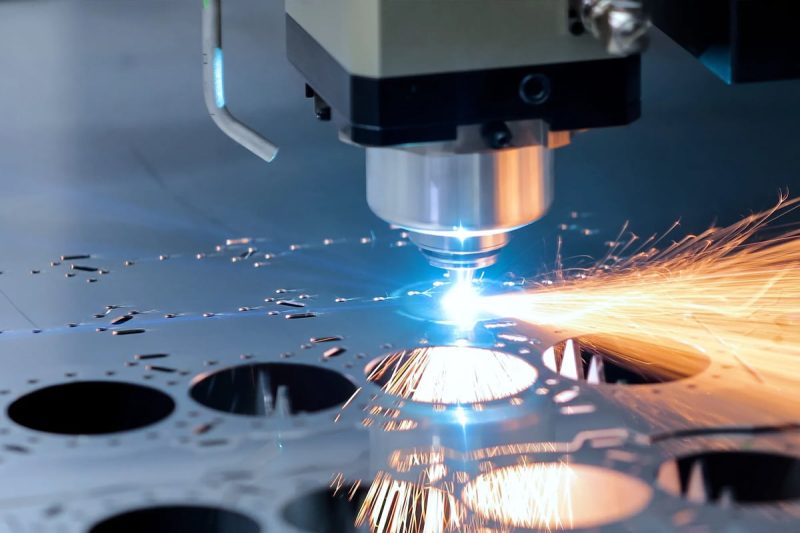
العوامل المؤثرة على قوة الليزر
نوع المادة
المعادن
- الفولاذ: نظرًا لنقطة انصهاره العالية، فإنه يتطلب عمومًا طاقة ليزر أعلى. قد يكون للفولاذ الصلب والفولاذ المقاوم للصدأ وسبائك الفولاذ الأخرى متطلبات طاقة مختلفة.
- الألومنيوم: بسبب انعكاسيته العالية وتوصيله الحراري، فإنه يتطلب قوى ليزر عالية.
- النحاس والبرونز: تتمتع هذه المواد بقدرة عالية على الانعكاس والتوصيل وتتطلب مستويات طاقة أعلى أو مولدات ليزر متخصصة، مثل مولدات الليزر الليفي، لضمان القطع الفعال.
المواد غير المعدنية
- البلاستيك والأكريليك: يتطلبان عمومًا طاقة أقل من المعادن. وقد تختلف الطاقة المطلوبة حسب نوع البلاستيك وسمكه.
- الخشب: يتطلب طاقة معتدلة، ولكن الطاقة المطلوبة يمكن أن تختلف بشكل كبير اعتمادًا على نوع الخشب ومحتواه من الرطوبة.
- القماش والورق: نظرًا لكون هذه المواد رقيقة وقابلة للاشتعال، فإنها تتطلب طاقة أقل عند القطع.
سمك المادة
يتناسب سمك المادة بشكل مباشر مع قوة الليزر المطلوبة. تتطلب المواد الأكثر سمكًا قوة أكبر للقطع لأن الليزر يجب أن يخترق بشكل أعمق ويزيل المزيد من المواد.
- المواد الرقيقة (≤ 1 مم): مستويات الطاقة المنخفضة كافية. تسمح الطاقة المنخفضة بالدقة العالية والتفاصيل الدقيقة.
- سمك متوسط (1-5 مم): يلزم توفر مستويات طاقة متوسطة. تعتمد الطاقة المطلوبة على نوع المادة وسرعة القطع المطلوبة.
- المواد السميكة (> 5 مم): يلزم استخدام طاقة عالية لضمان الاختراق الكامل والقطع الفعال. بالنسبة للمواد السميكة للغاية، قد يلزم استخدام طريقة متعددة التمريرات أو مولد ليزر عالي الطاقة متخصص.
متطلبات سرعة القطع
تؤثر سرعة القطع المطلوبة بشكل كبير على اختيار قوة الليزر. فكلما زادت سرعة القطع، كلما كانت القوة المطلوبة عادة أعلى للحفاظ على جودة القطع ومنع القطع غير المكتمل أو النتوءات الزائدة.
- القطع عالي السرعة: بالنسبة للتطبيقات التي تكون فيها السرعة بالغة الأهمية، مثل الإنتاج الضخم، يلزم استخدام طاقة ليزر أعلى. وتضمن الطاقة الأعلى أن يتمكن الليزر من قطع المواد بسرعة دون التضحية بالجودة.
- القطع بسرعة متوسطة: في السيناريوهات التي لا تكون فيها سرعة القطع مهمة، يمكن استخدام إعدادات الطاقة المتوسطة. وهذا هو الحال غالبًا في حالة الإنتاج على دفعات صغيرة أو التصنيع المخصص.
- القطع بسرعة بطيئة: بالنسبة للقطع التفصيلية أو المعقدة للغاية، يمكن استخدام سرعات قطع أقل وإعدادات طاقة أقل. وهذا يسمح بمزيد من الدقة والتحكم.
جودة القطع المطلوبة
ستؤثر جودة القطع المطلوبة أيضًا على إعداد طاقة الليزر. تختلف معايير جودة الحافة والدقة واللمسة النهائية باختلاف التطبيقات.
- القطع عالي الجودة: بالنسبة للتطبيقات التي تتطلب حواف ناعمة وجودة عالية ومعالجة لاحقة بسيطة، عادة ما تكون هناك حاجة إلى قوى ليزر أعلى وسرعات قطع أبطأ. وهذا يضمن قطعًا نظيفًا مع الحد الأدنى من الشوائب والنتوءات.
- قطع بجودة قياسية: بالنسبة للتطبيقات التي تكون فيها العيوب البسيطة مقبولة، تكون مستويات الطاقة المتوسطة كافية. وهذا هو الحال غالبًا في التطبيقات الصناعية الثقيلة حيث تكون السرعة لها الأولوية على الجودة الجمالية.
- القطع الخشن: عندما تكون السرعة هي الاهتمام الأساسي وليس جودة الحافة، يمكن استخدام قوى أعلى وسرعات قطع أسرع. غالبًا ما يتم استخدام هذا النهج في مراحل القطع الأولية أو للمواد التي ستخضع لمزيد من المعالجة.
تعقيد التصميم
يؤثر تعقيد التصميم أو النمط المراد قطعه أيضًا على طاقة الليزر المطلوبة. تتطلب التصميمات المعقدة والمفصلة عمومًا تحكمًا أكثر دقة في الليزر، مما يؤثر على ضبط الطاقة.
- التصميمات المعقدة: تتطلب الأنماط المعقدة ذات الزوايا الحادة والثقوب الصغيرة والميزات التفصيلية التحكم الدقيق في طاقة الليزر. تساعد إعدادات الطاقة المنخفضة جنبًا إلى جنب مع السرعات البطيئة في تحقيق دقة عالية وتجنب ارتفاع درجة حرارة المادة أو تشوهها.
- التصميمات المتوسطة: يمكن قطع التصميمات ذات التعقيد المتوسط بإعدادات طاقة متوازنة. قد تتضمن هذه التصميمات منحنيات وسمك خطوط متفاوت ولكنها لا تتطلب دقة شديدة.
- تصميمات بسيطة: يمكن إجراء قطع بسيطة مع الحد الأدنى من التفاصيل، مثل الأشكال البسيطة والخطوط المستقيمة، بإعدادات طاقة أعلى وسرعات أسرع.
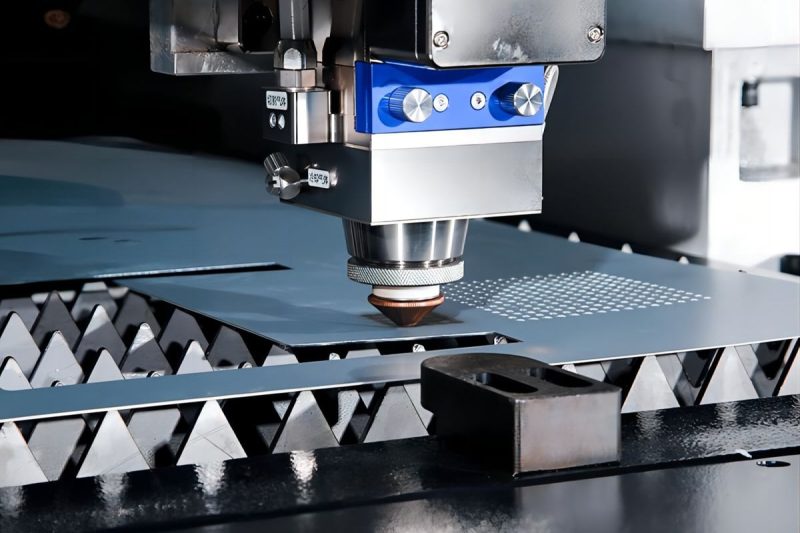
نطاقات طاقة الليزر للمواد المختلفة
المعادن
الفولاذ الطري
- لوحة رقيقة (حتى سمك 3 مم): 1000-2000 واط
- سمك متوسط (3-6 مم): 2000-4000 واط
- لوحة سميكة (6-12 مم): 4000-8000 واط
- لوحة سميكة جدًا (أكثر من 12 مم سمكًا): 8000-12000 واط
ستانلس ستيل
- لوحة رقيقة (حتى سمك 2 مم): 1000-2000 واط
- سمك متوسط (2-5 مم): 2000-4000 واط
- لوحة سميكة (5-10 مم): 4000-6000 واط
- لوحة سميكة جدًا (أكثر من 10 مم سمكًا): 6000-12000 واط
الألومنيوم
- لوحة رقيقة (حتى سمك 2 مم): 1000-2000 واط
- سمك متوسط (2-6 مم): 2000-4000 واط
- لوحة سميكة (6-10 مم): 4000-8000 واط
- لوحة سميكة جدًا (أكثر من 10 مم): 8000-12000 واط
النحاس والنحاس
- لوحة رقيقة (حتى سمك 1 مم): 1000-2000 واط
- متوسط السُمك (1-3 مم): 2000-4000 واط
- لوحة سميكة (3-6 مم): 4000-6000 واط
- لوحة سميكة جدًا (أكثر من 6 مم): 6000-8000 واط
المواد غير المعدنية
المواد البلاستيكية (مثل البولي كربونات والبولي بروبيلين وPVC)
- صفائح رقيقة (حتى سمك 2 مم): 25-40 واط
- سمك متوسط (2-5 مم): 40-100 واط
- صفائح سميكة (5-10 مم): 100-150 واط
- ألواح سميكة جدًا (أكثر من 10 مم سمكًا): 200-600 واط
أكريليك
- صفائح رقيقة (حتى سمك 2 مم): 60-100 واط
- سمك متوسط (2-5 مم): 100-200 واط
- صفائح سميكة (5-10 مم): 200-400 واط
- ألواح سميكة جدًا (أكثر من 10 مم سمكًا): 400-600 واط
الخشب (على سبيل المثال الخشب الرقائقي، MDF، الخشب الصلب)
- صفائح رقيقة (حتى سمك 3 مم): 100-150 واط
- سمك متوسط (3-6 مم): 150-300 واط
- ألواح سميكة (6-12 12 مم): 300-500 واط
- ألواح سميكة جدًا (أكثر من 12 مم): 500-600 واط
المنسوجات والجلود
- سمك رقيق ومتوسط: 60-150 واط
- المواد السميكة: 150-300 واط
المركبات
البوليمر المقوى بألياف الكربون (CFRP)
- صفائح رقيقة (حتى سمك 1 مم): 100-200 واط
- سمك متوسط (1-3 مم): 200-400 واط
- صفائح سميكة (3-6 مم): 400-600 واط
البوليمر المقوى بالألياف الزجاجية (GFRP)
- صفائح رقيقة (حتى سمك 1 مم): 100-200 واط
- سمك متوسط (1-3 مم): 200-400 واط
- صفائح سميكة (3-6 مم): 400-600 واط
مركبات أخرى (على سبيل المثال، مركبات الكيفلار والبورون)
- صفائح رقيقة (حتى سمك 1 مم): 100-200 واط
- سمك متوسط (1-3 مم): 200-400 واط
- صفائح سميكة (3-6 مم): 400-600 واط
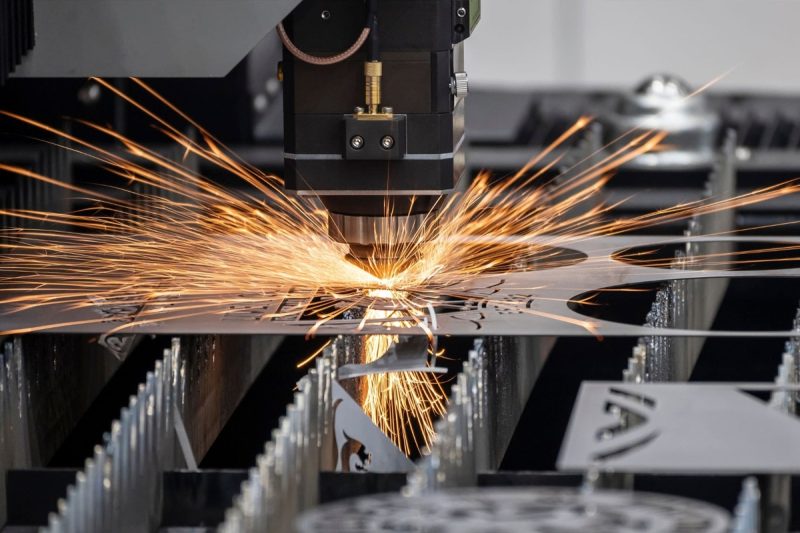
طرق تحديد قوة الليزر
مخططات توافق المواد
تمثل مخططات توافق المواد موردًا قيمًا يوفر إرشادات عامة حول إعدادات طاقة الليزر المطلوبة للمواد المختلفة.
- الغرض: تساعد هذه المخططات المستخدمين على تحديد إعدادات الطاقة الأولية بسرعة لمختلف المواد استنادًا إلى نوع المادة وسمكها.
- الهيكل: تسرد مخططات التوافق عادةً المواد في عمود واحد، تليها إعدادات الطاقة الموصى بها، وسرعات القطع، والمعلمات الأخرى ذات الصلة.
- المصادر: يمكن العثور على هذه المخططات في أدلة المستخدم، وبرامج القطع بالليزر، ومواقع الويب الخاصة بالشركات المصنعة.
مزايا
- مرجع سريع: يوفر إرشادات فورية دون الحاجة إلى حسابات أو تجارب مكثفة.
- الإعدادات القياسية: توفر إعدادات طاقة قياسية استنادًا إلى أفضل ممارسات الصناعة.
سلبيات
- المعلومات العامة: قد لا يأخذ هذا في الاعتبار الاختلافات المحددة في جودة المواد أو الظروف البيئية.
- نقطة البداية فقط: يجب أن تكون بمثابة خط أساس لمزيد من التعديلات والتحسينات.
اختبار المواد
يتضمن اختبار المواد إجراء اختبارات فعلية لضبط إعدادات طاقة الليزر لمواد وتطبيقات محددة.
- الإعداد الأولي: ابدأ بالإعدادات الموصى بها الموجودة في مخطط توافق المواد أو دليل الشركة المصنعة.
- الضبط التدريجي: اضبط قوة الليزر والسرعة والمعلمات الأخرى تدريجيًا أثناء مراقبة النتائج.
- التقييم: قم بتقييم جودة القطع، ونعومة الحافة، وأي علامات تشير إلى تدهور المادة أو ارتفاع درجة حرارتها.
مزايا
- الدقة: تسمح بالمعايرة الدقيقة بناءً على خصائص المواد المحددة ومتطلبات القطع.
- التحسين: يسمح بإجراء ضبط دقيق لأداء القطع الأمثل، وتحسين الكفاءة والجودة.
سلبيات
- مستهلك للوقت: يتطلب الوقت والموارد لإجراء اختبارات وتقييمات متعددة.
- هدر المواد: يتضمن استخدام بعض المواد أثناء الاختبار.
توصيات الشركة المصنعة
يعد اتباع توصيات الشركة المصنعة طريقة أساسية لتحديد قوة القطع بالليزر المناسبة.
- المصدر: يمكن العثور على التوصيات في أدلة المستخدم، ووثائق الدعم الفني، والاتصالات الرسمية من مصنعي آلات القطع بالليزر.
- المحتوى: تتضمن هذه الأدلة عادةً إعدادات الطاقة التفصيلية، وسرعات القطع، والمعلمات الأخرى المستندة إلى اختبارات مكثفة وتطبيقات في العالم الحقيقي.
مزايا
- الموثوقية: تعتمد توصيات الشركة المصنعة على اختبارات شاملة ومصممة خصيصًا للقدرات المحددة لآلة القطع بالليزر.
- الدعم: يتوفر الدعم الفني من الشركة المصنعة لأي أسئلة أو مخاوف.
سلبيات
- التوصيات العامة: على الرغم من أن هذه التوصيات موثوقة، إلا أنها قد تحتاج إلى ضبط دقيق بناءً على حالات الاستخدام المحددة وظروف المواد.
- الاعتماد: إن الاعتماد المفرط على توصيات الشركة المصنعة قد يحد من استكشاف الإعدادات المحسنة للتطبيقات الفريدة.
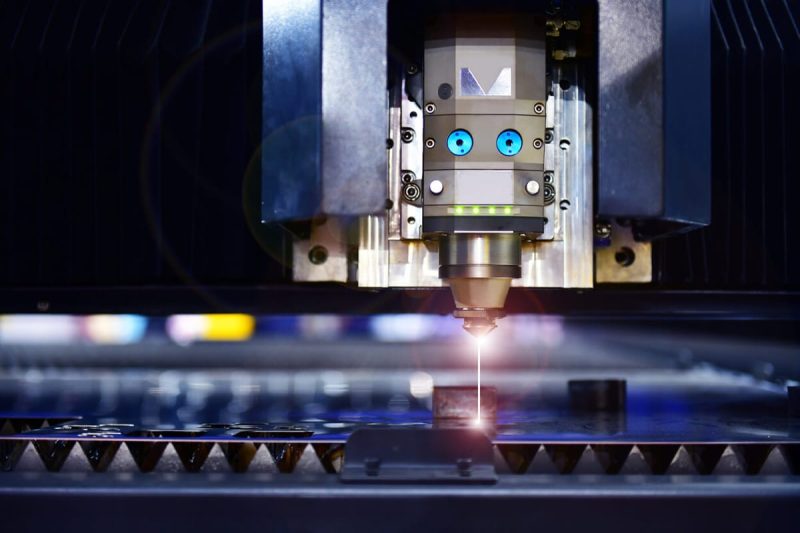
اعتبارات عملية لاختيار قوة القطع بالليزر
مواصفات الماكينة
الحد الأقصى والحد الأدنى لإخراج الطاقة
- المدى: تأكد من أن جهازك قادر على التعامل مع إعدادات الطاقة المطلوبة لمادتك. تتراوح قوة الليزر الليفي عادةً من 1000 إلى 12000 واط (للمعادن)، بينما تتراوح قوة الليزر ثاني أكسيد الكربون من 60 إلى 600 واط (للمواد غير المعدنية).
- المرونة: توفر الآلات ذات نطاق القدرة الواسع مرونة أكبر لقطع مواد وسمك مختلف.
جودة الشعاع
- حجم التركيز: تؤثر جودة شعاع الليزر على دقة القطع. تسمح جودة الشعاع العالية وحجم التركيز الأصغر بإجراء قطع أدق.
- الاستقرار: تضمن جودة الشعاع الثابتة قطعًا متساوية وتقلل من الحاجة إلى التعديلات المتكررة.
سرعة القطع والتسارع
- قدرة السرعة: تسمح طاقة الليزر العالية بسرعات قطع أسرع، ولكن يجب أن تدعم المكونات الميكانيكية للجهاز هذه السرعات دون المساس بالدقة.
- التسارع: يمكن للآلة ذات قدرات التسارع العالية التعامل مع التغييرات السريعة في اتجاه القطع، مما يساعد على تحقيق تصميمات معقدة.
نظام التحكم
- البرمجيات: يمكن لبرنامج التحكم المتقدم تحسين مسارات القطع وإعدادات الطاقة، مما يؤدي إلى تحسين الكفاءة والجودة.
- التكامل: تأكد من إمكانية دمج نظام التحكم بسلاسة مع معدات الإنتاج والبرامج الأخرى لتبسيط التشغيل.
التكلفة وكفاءة الطاقة
تكاليف التشغيل
- استهلاك الطاقة: تستهلك إعدادات طاقة الليزر الأعلى قدرًا أكبر من الكهرباء. قم بتقييم متطلبات الطاقة وتكاليف التشغيل المرتبطة بمستويات الطاقة المختلفة.
- الغاز المساعد: يمكن أن يؤثر نوع وكمية الغاز المساعد المستخدم (على سبيل المثال، الأكسجين، والنيتروجين، والهواء المضغوط) على التكلفة الإجمالية. قد تتطلب إعدادات الطاقة الأعلى كمية أكبر من الغاز المساعد للحفاظ على جودة القطع. إذا كنت تريد معرفة المزيد عن الغازات المساعدة، فراجع "تأثير اختيار الغاز المساعد على القطع بالليزر" شرط.
الاستثمار الأولي مقابل الادخار الطويل الأجل
- التكلفة الأولية: تتطلب آلة القطع بالليزر ذات الطاقة الأعلى عمومًا استثمارًا أوليًا أعلى. ومع ذلك، يمكنها توفير وفورات طويلة الأجل من خلال زيادة سرعات القطع وكفاءته.
- زيادة الكفاءة: يمكن لليزر الأكثر قوة أن يقلل من وقت القطع ويزيد من معدل الإنتاج، مما يوفر العمالة ونفقات التشغيل.
كفاءة الطاقة
- كفاءة الليزر: تُعد مولدات الليزر الليفي أكثر كفاءة في استخدام الطاقة بشكل عام من مولدات الليزر ثاني أكسيد الكربون. ضع في اعتبارك كفاءة الطاقة لنوع مولد الليزر عند اختيار إعداد الطاقة.
- نظام التبريد: يمكن لنظام التبريد الفعال أن يقلل من استهلاك الطاقة ويطيل عمر مولد الليزر.
الصيانة ووقت التوقف
صيانة روتينية
- التردد: تعمل إعدادات الطاقة الأعلى على تسريع تآكل مكونات الماكينة. قم بإنشاء جدول صيانة منتظم لفحص الأجزاء واستبدالها حسب الحاجة.
- الأجزاء: تتطلب المكونات الأساسية مثل العدسات والمرايا والفوهات التنظيف والاستبدال المتكرر للحفاظ على الأداء الأمثل.
إدارة وقت التوقف
- وقت التوقف المخطط له: قم بالتخطيط لأنشطة الصيانة أثناء وقت التوقف المخطط له لتقليل الانقطاع في الإنتاج.
- الصيانة الوقائية: تنفيذ استراتيجية الصيانة الوقائية لتحديد المشكلات المحتملة وحلها قبل أن تتسبب في فشل الماكينة.
دعم الشركة المصنعة
- اتفاقيات الخدمة: ضع في اعتبارك اتفاقيات الخدمة وحزم الدعم التي تقدمها الشركات المصنعة. يمكن أن توفر لك هذه الاتفاقيات راحة البال وتقلل من خطر التوقف المطول.
- المساعدة الفنية: ضمان الوصول إلى الدعم الفني لاستكشاف الأخطاء وإصلاحها وتحسين أداء الماكينة.
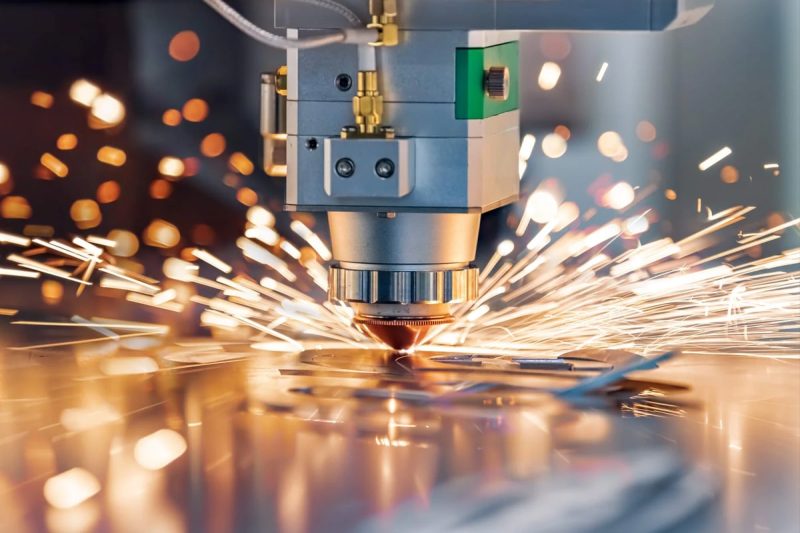
استكشاف مشكلات طاقة الليزر وإصلاحها
عدم القطع بعمق كافي
قوة غير كافية
- السبب: قد يكون إعداد طاقة الليزر منخفضًا جدًا لقطع المادة.
- الحل: قم بزيادة قوة الليزر تدريجيًا وقم بإجراء قطع تجريبية حتى تصل إلى العمق المطلوب. تأكد من أن مستوى الطاقة يقع ضمن نطاق التشغيل الآمن للجهاز.
سرعة القطع عالية جدًا
- السبب: قد تكون سرعة القطع سريعة جدًا، مما لا يسمح بوقت كافٍ لليزر لاختراق المادة بالكامل.
- الحل: قم بتقليل سرعة القطع للسماح بتركيز المزيد من الطاقة على المادة. وازن بين إعدادات السرعة والقوة لتحسين عمق القطع.
التركيز المفقود
- السبب: قد لا يتم تركيز شعاع الليزر بشكل صحيح على سطح المادة، مما يقلل من كفاءة القطع.
- الحل: اضبط ارتفاع التركيز للتأكد من تركيز شعاع الليزر بشكل صحيح على المادة. استخدم أداة التركيز الخاصة بالجهاز أو اضبط الارتفاع يدويًا حسب الحاجة.
سمك المادة
- السبب: قد تكون المادة أكثر سمكًا من المتوقع، مما يتطلب المزيد من الطاقة أو المرور المتعدد.
- الحل: تحقق من سمك المادة واضبط إعداد الطاقة وفقًا لذلك. بالنسبة للمواد السميكة جدًا، فكر في المرور عدة مرات أو استخدام ليزر أعلى طاقة.
الحرق أو الذوبان المفرط
القوة المفرطة
- السبب: قد يكون إعداد طاقة الليزر مرتفعًا جدًا بالنسبة للمادة التي يتم قطعها.
- الحل: قم بخفض طاقة الليزر تدريجيًا حتى يتم تقليل الاحتراق أو الذوبان إلى الحد الأدنى. تأكد من أن إعداد الطاقة مناسب للمادة.
سرعة القطع البطيئة
- السبب: قد تكون سرعة القطع بطيئة للغاية، مما يؤدي إلى تراكم الحرارة الزائدة والحرق.
- الحل: زيادة سرعة القطع لتقليل وقت التعرض للحرارة. ابحث عن التوازن الصحيح بين السرعة والقوة لتحقيق قطع نظيف دون احتراق.
التركيز غير الصحيح
- السبب: قد يكون تركيز الليزر مركّزًا للغاية، مما يؤدي إلى ارتفاع درجة الحرارة في منطقة صغيرة.
- الحل: اضبط ارتفاع التركيز بحيث يتم توزيع طاقة الليزر بشكل أكثر توازناً عبر منطقة القطع. تأكد من محاذاة الشعاع وتركيزه بشكل صحيح.
حساسية المواد
- السبب: بعض المواد أكثر حساسية للحرارة وتميل إلى الاحتراق أو الذوبان.
- الحل: استخدم مواد ذات قدرة أفضل على تحمل الحرارة كلما أمكن ذلك. كما يمكنك أيضًا التفكير في استخدام غاز مساعد مثل النيتروجين، والذي يمكن أن يساعد في تقليل الاحتراق عن طريق إزاحة الأكسجين حول منطقة القطع.
نتائج القطع غير المتسقة
خرج الطاقة المتغير
- السبب: قد يتقلب خرج الطاقة لمولد الليزر، مما يؤدي إلى أداء قطع غير متناسق.
- الحل: افحص مولد الليزر بحثًا عن مشكلات الاستقرار وتأكد من أنه يعمل بشكل صحيح. يمكن أن تساعد الصيانة والمعايرة المنتظمة في الحفاظ على خرج طاقة ثابت.
اختلافات المواد
- السبب: يمكن أن تؤدي الاختلافات في خصائص المواد، مثل السُمك أو التركيب، إلى قطع غير متناسق.
- الحل: استخدم مواد عالية الجودة وموحدة لضمان اتساق المواد. قم بإجراء قطع اختبارية على دفعات مختلفة من المواد لضبط الإعدادات حسب الحاجة.
معايرة غير صحيحة للآلة
- السبب: قد لا يتم معايرة الماكينة بشكل صحيح، مما يؤثر على دقة القطع واتساقه.
- الحل: قم بمعايرة آلة القطع بالليزر بانتظام وفقًا لإرشادات الشركة المصنعة. تحقق من وجود مشكلات ميكانيكية أو عدم محاذاة قد تؤثر على أداء القطع.
البصريات المتسخة أو التالفة
- السبب: يمكن للبصريات المتسخة أو التالفة أن تبعثر شعاع الليزر، مما يؤدي إلى نتائج قطع غير متسقة.
- الحل: نظّف البصريات بانتظام وافحصها بحثًا عن أي تلف. استبدل أي مكونات تالفة لضمان جودة الشعاع واتساقه على النحو الأمثل.
العوامل البيئية
- السبب: يمكن للتغيرات في درجة الحرارة المحيطة أو الرطوبة أو تدفق الهواء أن تؤثر على عملية القطع.
- الحل: حافظ على بيئة خاضعة للرقابة لآلة القطع بالليزر الخاصة بك. تأكد من ثبات مستويات درجة الحرارة والرطوبة لتقليل تأثير العوامل البيئية على عملية القطع.
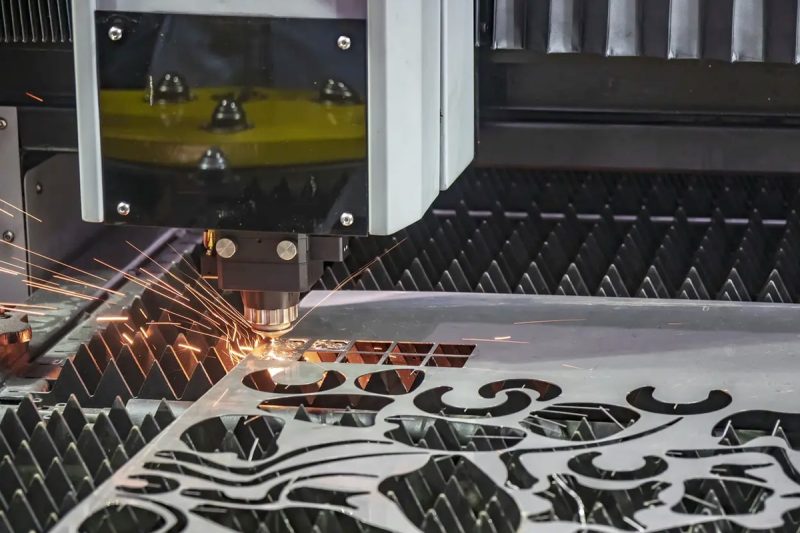
ملخص
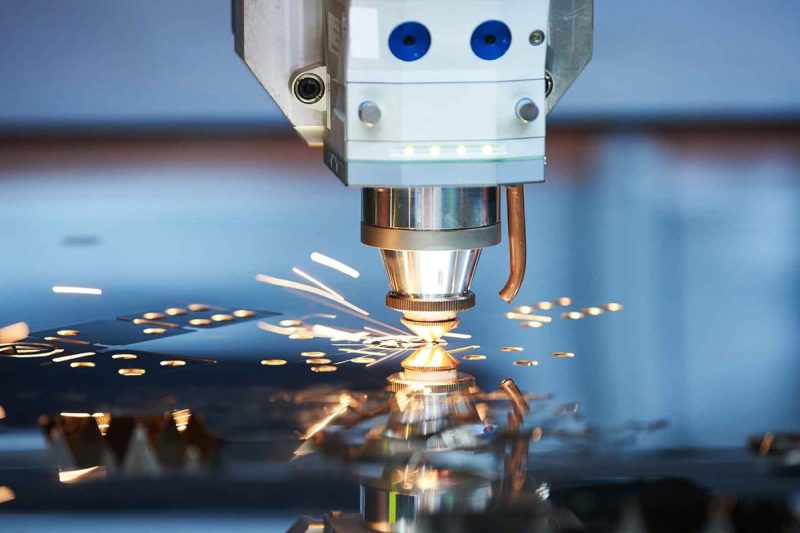
احصل على حلول القطع بالليزر
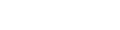
- [email protected]
- [email protected]
- +86-19963414011
- رقم 3 المنطقة أ ، المنطقة الصناعية لونجين ، مدينة يوتشنغ ، مقاطعة شاندونغ.