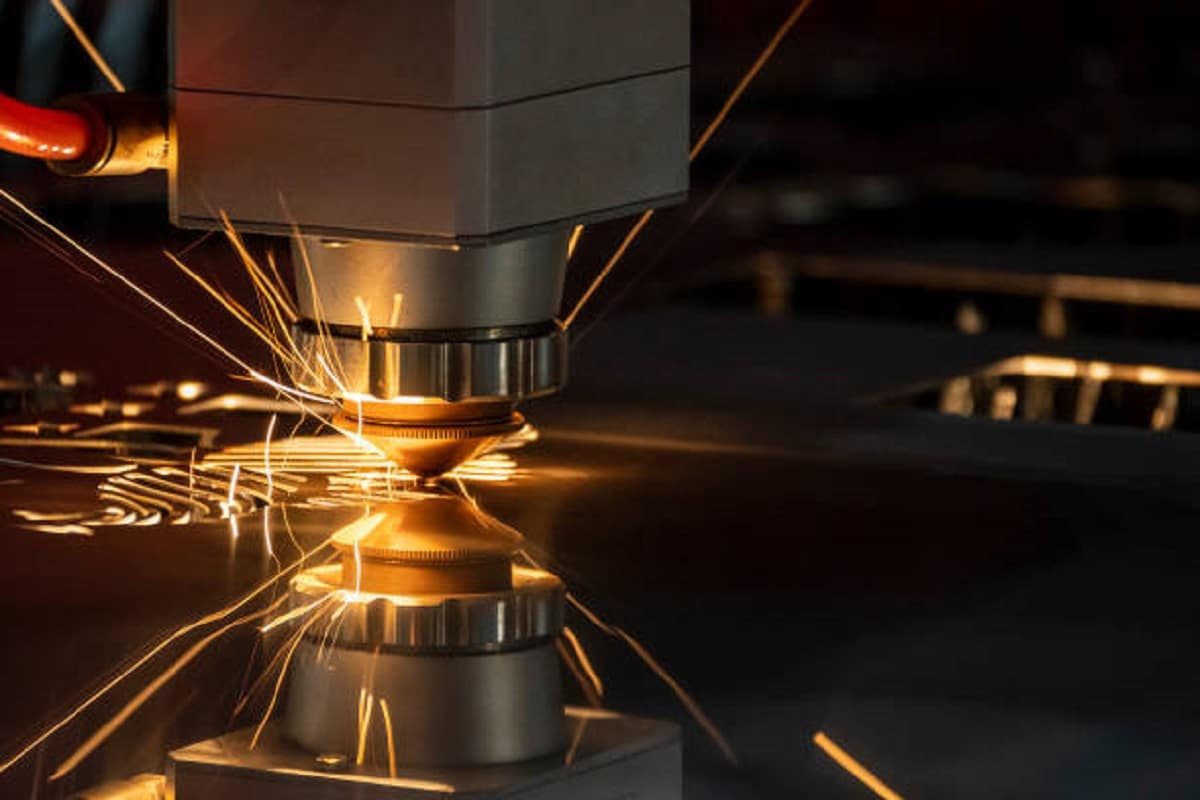
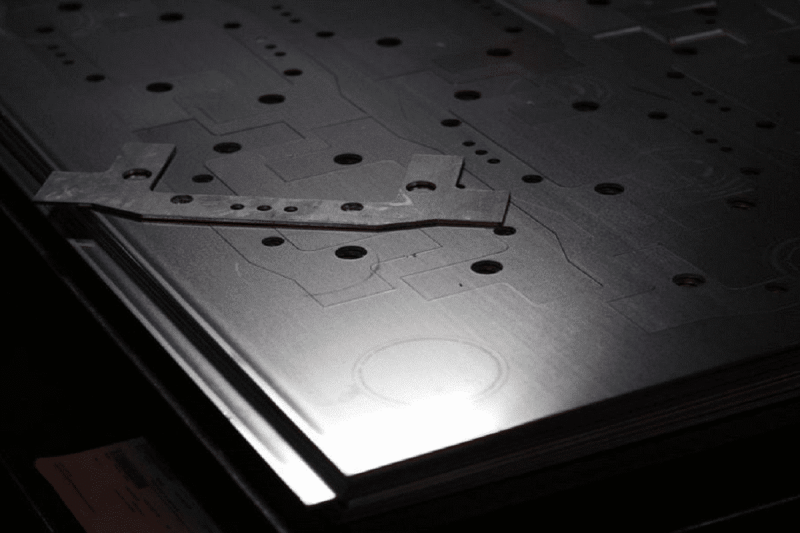
Principles of laser cutting and CNC machining
What is a laser cutting machine?
The laser cutting machine is a machine tool that uses a high-energy laser beam to cut materials. Its principle is to convert electrical energy into light energy, and then concentrate the light energy into a high-energy laser beam, which is used to cut various materials. The working method of the laser cutting machine can be summarized as follows:
- Laser emission: The laser cutting machine contains a laser generator inside, which generates a high-energy laser beam.
- Laser beam transmission: Through the lens and lens system, the laser beam is focused into a highly concentrated light spot.
- Material cutting: The laser beam is precisely focused on the workpiece surface, heating it to a high enough temperature to evaporate or melt the material in a short time. Control software translates the design and guides the movement of the laser head to trace the path of the desired pattern to achieve the cut.
- The main features of laser cutting machines include high precision, high speed, adaptability to various materials (such as metal, plastic, wood, etc.), contactless cutting, and no need for physical tool changes. It is widely used in automobile manufacturing, electronic manufacturing, metal processing, and other fields.
What is CNC machining?
The term “CNC” is widely used to refer to computer-controlled drills and milling machines, also known as numerically controlled machine tools. CNC machining is an automated manufacturing process that uses a computer program to control the relative movement between a tool and a workpiece. Its principle is to precisely control the movement of the tool through a numerical control system to cut, engrave, or shape the workpiece. CNC machining works as follows:
- Programming: First, the engineer or operator needs to create a CNC program that contains the tool’s path, speed, feed rate, and other relevant parameters.
- Control system: CNC machine tools are equipped with a numerical control system, which converts CNC programs into actual movement instructions for the tool and workpiece.
- Processing process: The tool on the CNC machine tool cuts, engraves, or processes the workpiece according to the path and parameters in the program.
- The main features of CNC machining include high precision, repeatability, suitability for a variety of materials, high flexibility (different parts can be cut by simply changing the program), and wide application in various fields of manufacturing, such as aerospace, medical Equipment, mold manufacturing, etc.
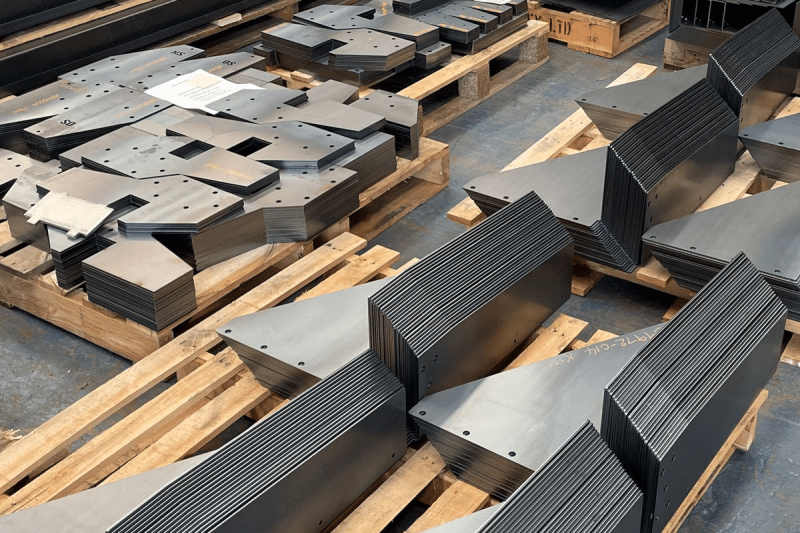
The difference between laser cutting and CNC machining
Differences in working principles
- Laser cutting: Laser cutting is a process that uses high-energy laser beams to cut materials. Its principle is to convert electrical energy into light energy, and then focus the light energy into a high-energy laser beam for cutting various materials. The laser cutting process is a non-contact cutting method. The laser beam can heat the material to a high temperature in a very short time to achieve cutting.
- CNC machining: CNC machining is a process that uses a computer program to control the relative movement between the tool and the workpiece to complete cutting, engraving, or processing. Its principle is to convert the pre-written CNC program into the actual movement instructions of the tool through the numerical control system, thereby realizing processing. CNC machining typically uses physical tools such as milling cutters, drills, or blades to cut materials.
Differences in working methods
- Laser cutting: The laser cutting machine includes a laser generator inside, which generates a high-energy laser beam, and then focuses the beam onto the workpiece surface through a lens and lens system. The laser beam heats the material to a high enough temperature that it vaporizes or melts, allowing the cutting to occur. This is a very fast, precise, and contact-free method of processing.
- CNC processing: The tools on the CNC processing machine tool cut, engrave, or process the workpiece according to the path and parameters specified in the CNC program. The movement of the tool is precisely controlled by the numerical control system of the machine tool and can move in a three-dimensional coordinate system. CNC machining typically requires physical tool contact with the workpiece, thus generating friction and cutting forces.
Differences in applicable scope
- Laser cutting: Laser cutting is suitable for various materials, including metals (such as steel, aluminum, and stainless steel), plastics, wood, ceramics, and composite materials. It is widely used in automobile manufacturing, electronic manufacturing, metal processing, advertising production, and jewelry processing, especially where high precision and complex cutting shapes are required.
- CNC processing: CNC processing is also suitable for a variety of materials, including metal, plastic, wood, ceramics, and composite materials. It is widely used in aerospace, medical equipment, automobile manufacturing, mold manufacturing, and general machinery manufacturing, and is especially suitable for occasions requiring multi-axis machining, high-speed milling, and multi-function operations.
Differences in maintenance and replacement
- Laser cutting: Laser cutting machines generally require less maintenance because there are no physical cutting tools that need to be replaced and worn regularly. However, the laser part needs to be calibrated and maintained regularly.
- CNC processing: CNC processing machine tools require regular maintenance, including tool replacement, lubrication, machine tool calibration and cleaning, etc. Additionally, operating CNC machining requires a well-trained operator.
Differences in security
- Laser cutting: Laser cutting requires special safety measures to prevent laser radiation damage. Operators need to wear appropriate protective gear and ensure equipment is equipped with safety features.
- CNC machining: CNC machining generally does not have the same laser radiation risks as laser cutting machines, but you still need to pay attention to the safe operation of the tool to prevent cutting accidents and operator injuries.
Differences in performance characteristics
Laser cutting
- High precision: Laser cutting usually has extremely high precision, especially on thin materials.
- No tool changing required: No physical tools are required, so there is no need to change tools frequently.
- High speed: Laser cutting can achieve fast cutting speed.
- Non-contact processing: Laser cutting is a non-contact processing method that will not damage the surface of the workpiece.
CNC machining
- Flexibility: CNC machining is more flexible in manufacturing parts of different shapes and sizes, just by changing the CNC program.
- Wide applicability: CNC machining is suitable for various processing tasks, from rough machining to fine machining.
- Suitable for complex parts: CNC processing is suitable for manufacturing complex three-dimensional parts, such as molds and tooling.
- A variety of operations can be performed: CNC processing machine tools can perform a variety of processing operations such as milling, drilling, turning, and boring.
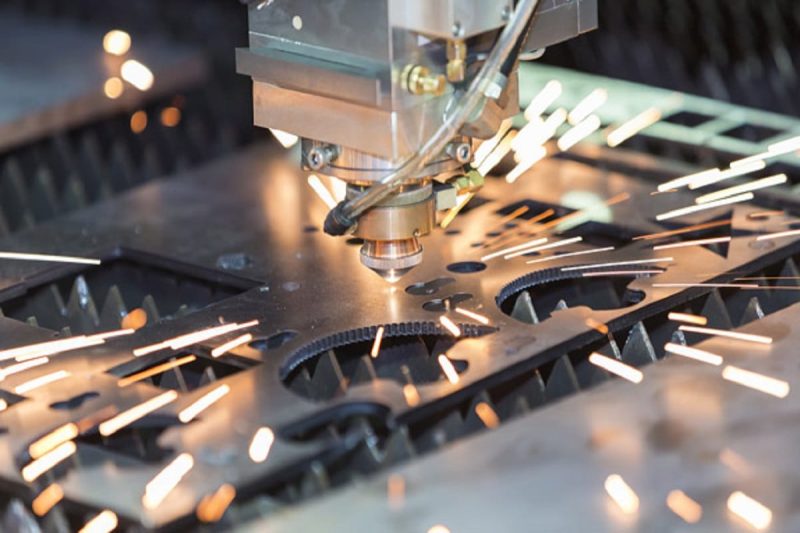
Similarities between laser cutting and CNC machining
Application of CNC technology
Automated production
High-precision machining
Multi-material adaptability
Formulate custom parts
Summarize
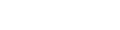
- [email protected]
- [email protected]
- +86-19963414011
- No. 3 Zone A, Lunzhen Industrial Zone,Yucheng City , Shandong Province.