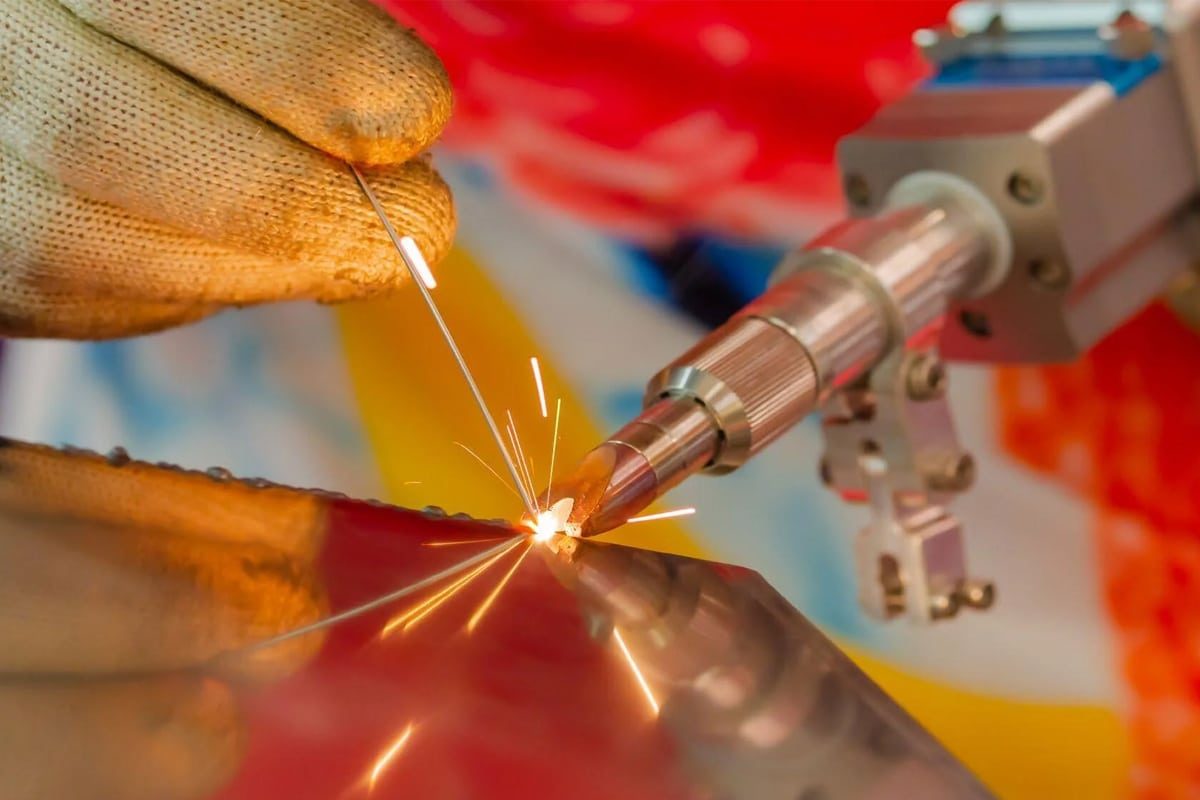
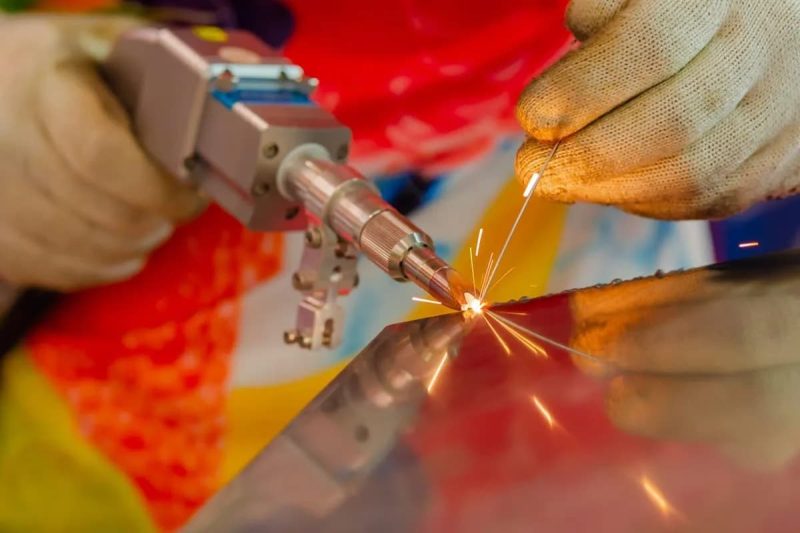
Laser Welding Introduction
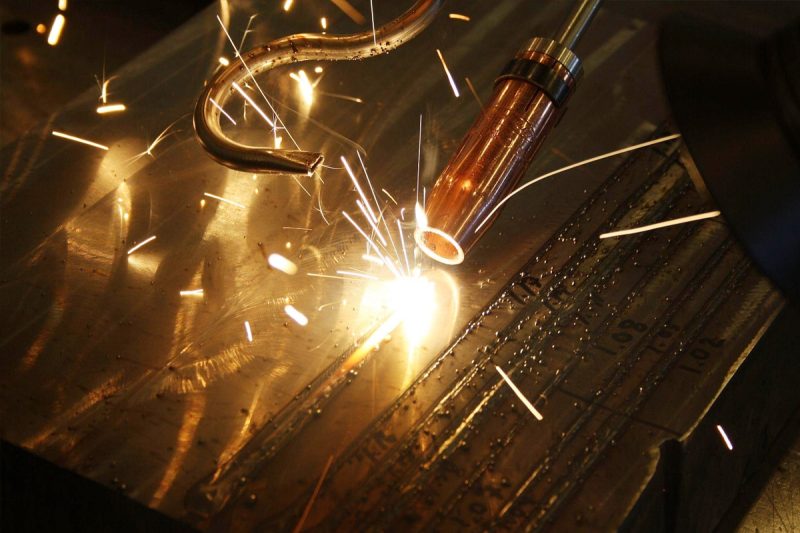
Autogenous Laser Welding
Definition and Process
- Preparation: The workpieces are thoroughly cleaned to remove any contaminants such as oil, dirt, or oxides that may interfere with the welding process.
- Alignment: The edges of the workpieces are precisely aligned to ensure a uniform joint.
- Laser Beam Delivery: A focused laser beam is directed to the joint. The energy density of the laser is sufficient to melt the edges of the material.
- Fusion: The molten edges fuse and as the laser beam moves along the joint, the material cools and solidifies, forming a weld.
Mechanism
- Heat Conduction Mode: Applicable to thin materials, the laser energy is absorbed by the surface and conducted through the material, causing melting.
- Keyhole Mode: Used for thicker materials, the laser forms a keyhole by evaporating the material, resulting in deeper penetration and a stronger weld.
Technical Considerations
To achieve the best results with autogenous laser welding, several technical factors must be considered:
- Laser Parameters: Power, focus, beam quality, and speed must be precisely controlled to ensure adequate penetration and fusion.
- Material Properties: The weldability of a material, including its thermal conductivity, reflectivity, and melting point, affects the process.
- Joint Design: The geometry of the joint, including gap width and alignment, must be precisely controlled to ensure a consistent weld.
- Shielding Gas: An inert gas such as argon or nitrogen is typically used to protect the weld pool from oxidation and contamination.
- Cooling Rate: Controlled cooling prevents thermal stress and distortion in the welded material.
Advantages
- High Precision: The focused laser beam allows for precise control of welding, suitable for complex and delicate applications.
- Clean Welds: The absence of filler material eliminates potential contamination, resulting in clean and aesthetically pleasing welds.
- Minimal Heat Affected Zone: Localized heat input reduces thermal deformation and maintains the mechanical properties of surrounding materials.
- Speed and Efficiency: The process can be performed at high speeds, resulting in increased productivity and reduced cycle times.
- Automation Compatibility: Easy integration into automated systems, enhancing consistency and repeatability.
Limitations
- Material Compatibility: Not all materials are suitable for autogenous welding, especially those with widely different melting points or poor weldability.
- Joint Preparation: Precise alignment and clean surfaces are required, which can be time-consuming and challenging for some applications.
- Thickness Limitations: Welding thicker materials can be difficult without a filler material to fill the gap, limiting the method’s suitability for thin sections.
- Stress Concentration: The absence of a filler material can lead to stress concentrations at the weld joint, which can affect its mechanical properties.
Applications
Autogenous laser welding is used in a variety of industries that require high precision and clean welds:
- Electronics: Welding small parts and delicate assemblies in consumer electronics and semiconductor devices.
- Medical Devices: Used in the production of surgical instruments, implants, and other medical tools that require high precision and cleanliness.
- Aerospace: Joining thin materials and components in aircraft and spacecraft, thereby reducing weight and maintaining structural integrity.
- Automotive: Used in the manufacture of body parts, exhaust systems, and other components that require precise, high-quality welds.
- Jewelry: Makes fine, accurate welds of precious metals without changing their appearance or properties.
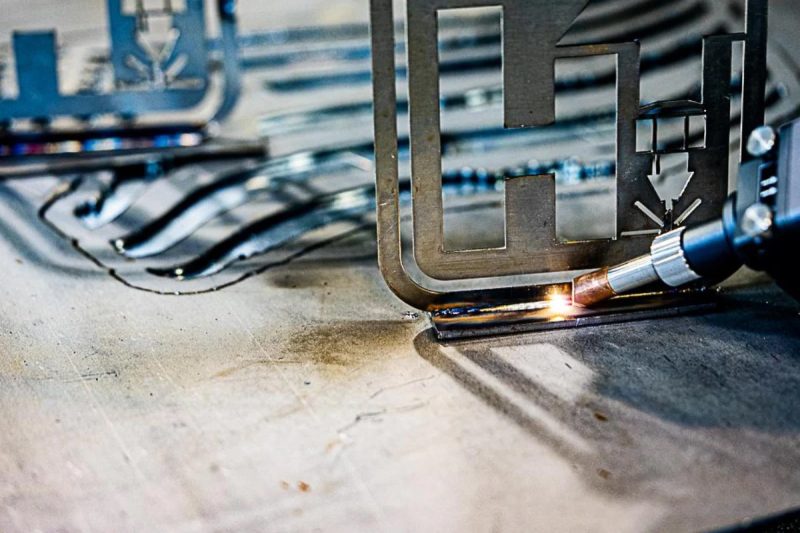
Filler Laser Welding
Definition and Process
Filler laser welding is a technique that adds a filler material to the weld joint and combines it with a laser beam to join the materials. This method is particularly useful for joining materials with dissimilar properties or for applications that require enhanced joint strength and the ability to bridge gaps.
- Preparation: Clean the surfaces of the materials to be joined to remove contaminants and properly align the joint.
- Filler Material Addition: Manually or automatically introduce filler material, which can be in the form of wire, powder, or pre-set strips, into the weld area.
- Laser Beam Delivery: A focused laser beam is directed onto the joint, melting both the base material and the filler material.
- Fusion: The molten filler material combines with the molten base material to form a uniform weld pool.
- Solidification: Upon cooling, the molten pool solidifies, forming a strong weld joint that contains the filler material.
Mechanism
The mechanism of filler laser welding involves several key stages:
- Absorption: The laser energy is absorbed by both the base and filler materials, resulting in rapid heating.
- Melting: The intense heat generated by the laser melts the edges of both the base and filler materials simultaneously.
- Fusion Zone Formation: The molten filler material and base material fuse to form a uniform fusion zone, filling the gap and strengthening the joint.
- Solidification: As the laser moves away, the molten pool cools and solidifies, forming a continuous, strong weld containing the filler material.
Technical Considerations
Several technical factors must be considered to optimize the performance and quality of filler laser welding:
- Filler Material Selection: The filler material must be compatible with the parent material in terms of melting point, chemical composition, and thermal expansion, such as mechanical properties and corrosion resistance.
- Laser Power and Beam Quality: Sufficient laser power is required to melt both the base material and the filler material. High beam quality ensures precise energy delivery.
- Filler Material Delivery: The method of delivering the filler material (wire, powder, or pre-set material) must be carefully controlled to ensure consistent and uniform addition of material to the weld pool.
- Welding Speed and Feed Rate: The speed of the laser and the rate at which the filler material is introduced into the weld area must be carefully controlled to achieve a uniform weld.
- Shielding Gas: The use of a shielding gas can improve weld quality by preventing oxidation and contamination of the weld pool.
- Joint Design and Preparation: Proper joint design and preparation can help accommodate filler materials and ensure a strong, defect-free weld.
Advantages
- Enhanced Joint Strength: Adding filler material can improve the mechanical properties of the weld, making it stronger and more durable.
- Flexibility in Material Selection: This method allows for the welding of dissimilar materials and materials with different melting points, providing greater versatility.
- Gap Bridging Capability: Filler materials can bridge gaps and accommodate joint misalignments, reducing the need for precise joint preparation.
- Versatility: Applicable to both thin and thick materials and provides strong, reliable joints.
Limitations
- Complexity: Additional equipment and control systems are required to manage filler materials, adding complexity to the welding process.
- Potential for Contamination: The introduction of filler materials increases the risk of contamination, which can affect weld quality.
- Higher Cost: The use of filler materials and the need for additional equipment can increase the overall cost of the welding process.
- Process Control: Maintaining consistent filler material addition and laser parameter control can be challenging.
Applications
Filler laser welding is used in a wide range of industries that require strong joints and material versatility:
- Automotive: For welding thicker materials, parts with larger gaps, and structural parts that require extra strength.
- Aerospace: For ensuring strong and durable joints in the manufacture and repair of complex parts.
- Construction: For structural welding tasks that require high-strength joints and the ability to accommodate different joint configurations.
- Manufacturing: For making strong, reliable joints in machinery, equipment, and various industrial components.
- Oil and Gas: For pipes and other parts that need to withstand high pressures and harsh environmental conditions.
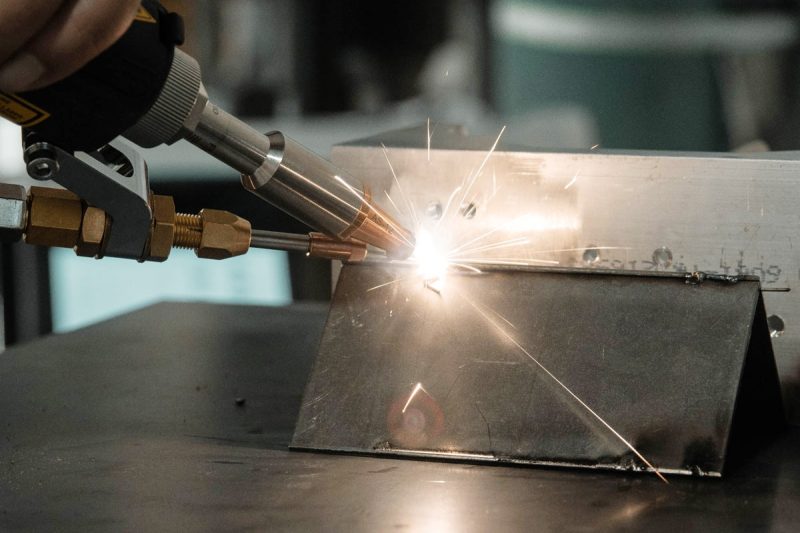
Comparative Analysis
Material Compatibility
Autogenous Laser Welding
- Material Requirements: Autogenous laser welding works best with materials that weld well and have similar melting points. It works especially well with metals that have high thermal conductivity and homogeneous composition.
- Limitations: This method has difficulty with dissimilar metals or materials with widely different melting points and coefficients of thermal expansion. For example, welding aluminum to steel using autogenous welding is a challenge due to the vast differences in the physical properties of aluminum and steel.
Filler Laser Welding
- Material Flexibility: Filler laser welding is more flexible in terms of material compatibility. The addition of filler material allows for the welding of dissimilar metals and materials with different properties. This makes it suitable for a wider range of applications, including those involving metals such as aluminum, titanium, and stainless steel.
- Enhanced Joint Quality: Using filler material helps bridge the differences in melting points and thermal expansion, resulting in a stronger, more reliable weld.
Joint Preparation and Fitting
Autogenous Laser Welding
- Precision Requirements: Autogenous welding requires precise joint preparation and alignment. The edges of the workpieces must be clean, free of contaminants, and fit tightly together to ensure a strong weld. Any gaps or misalignments will affect the quality of the weld.
- Surface Cleanliness: The absence of filler material means that any impurities on the surface of the substrate will directly affect the integrity of the weld, so the workpieces need to be thoroughly cleaned and prepared.
Filler Laser Welding
- Forgiving Process: Filler laser welding is more forgiving in terms of joint preparation and fit-up. The filler material can fill gaps and accommodate slight misalignments, making it easier to achieve a strong weld even when the joint preparation is not perfect.
- Gap Bridging: This method is particularly useful in applications where a precise fit is difficult to achieve or where there is variation in joint geometry. The filler material helps bridge gaps, resulting in a more consistent, stronger weld.
Strength and Durability
Autogenous Laser Welding
- Strength Depends on the Parent Material: The strength and durability of the weld in autogenous laser welding are entirely dependent on the parent material. If the parent material has excellent mechanical properties, the weld will generally exhibit similar properties.
- Limited Enhancement: Without the addition of filler material, there is little opportunity to increase the mechanical properties of the weld above the level of the parent material.
Filler Laser Welding
- Strength Enhancement: The use of filler materials can significantly increase the strength and durability of the weld. Filler materials can be selected to complement or improve the mechanical properties of the parent material, resulting in a stronger joint.
- Customizable Properties: By selecting the appropriate filler material, the mechanical properties of the weld, such as tensile strength, toughness, and fatigue resistance, can be tailored to meet specific application requirements.
Cost Considerations
Autogenous Laser Welding
- Lower Material Cost: Autogenous welding generally results in lower material costs because no filler material is used. This is very beneficial for high-volume production, as material cost savings can add up.
- Simpler Equipment: No need for filler material simplifies welding equipment and reduces the need for additional control systems, which can reduce initial investment and maintenance costs.
- Efficiency: Autogenous welding is extremely efficient, especially for thin materials and applications where precise joint preparation can be performed. Fast welding speeds and reduced need for post-weld processing contribute to cost savings.
Filler Laser Welding
- Higher Material Cost: Adding filler material increases the overall material cost of the welding process. The choice of filler material can also affect cost, especially when specialized alloys are required.
- Complex Equipment: Managing filler material requires more complex equipment and control systems, which can increase initial investment and maintenance costs.
- Versatility and Quality: Despite the higher cost, filler laser welding can offer better overall value in applications where material compatibility, joint strength, and gap bridging are critical. In many industrial applications, the ability to produce high-quality, durable welds can justify the additional expense.
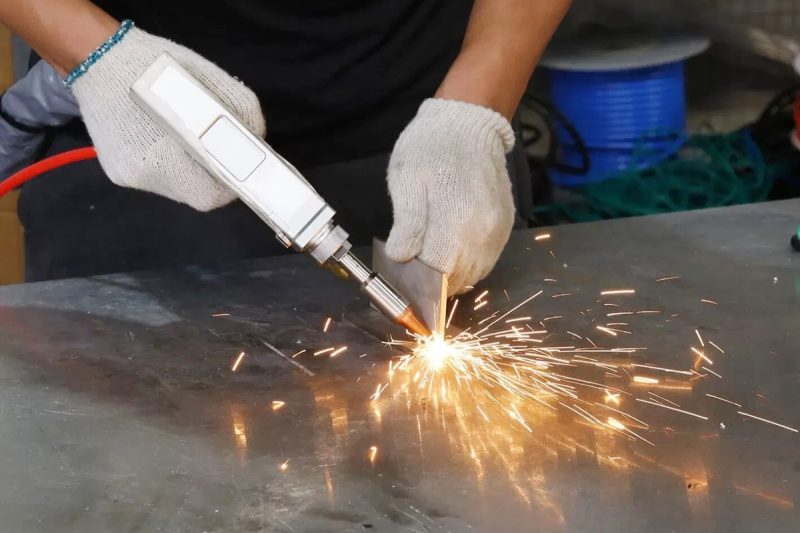
Summary
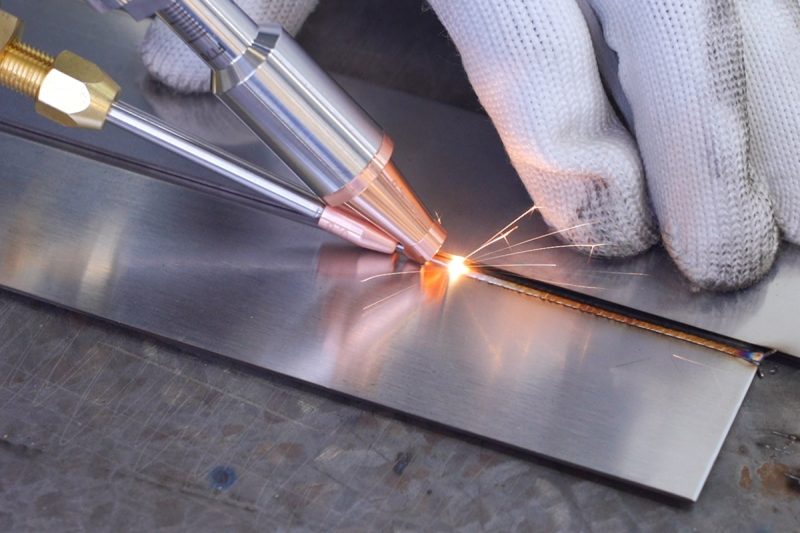
Get Laser Welding Solutions
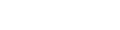
- [email protected]
- [email protected]
- +86-19963414011
- No. 3 Zone A, Lunzhen Industrial Zone,Yucheng City , Shandong Province.