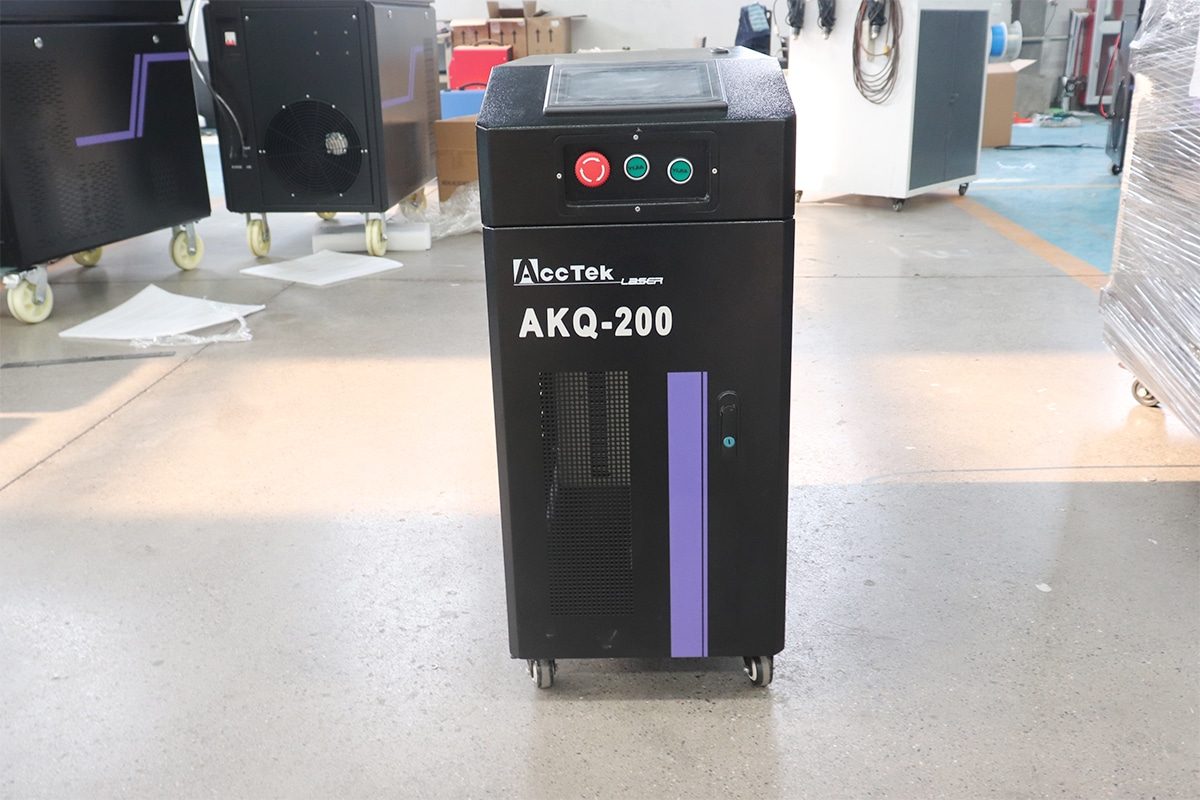
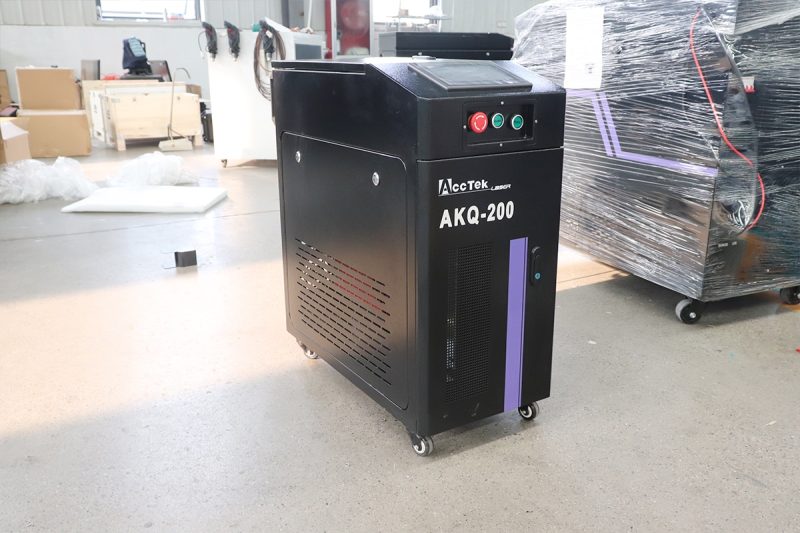
Understanding Laser Cleaning Machines
How Laser Cleaning Works
Types of Laser Cleaning Machines
- Pulsed Laser Cleaning Machines: Pulsed lasers emit short bursts of high-energy laser pulses. These are ideal for cleaning delicate surfaces where precision is essential, such as removing oxidation or paint without damaging the base material. Pulsed laser cleaning machines are often used in applications requiring fine control, such as in the aerospace or electronics industries.
- Continuous Wave (CW) Laser Cleaning Machines: Continuous-wave lasers emit a constant laser beam, providing high power for heavy-duty cleaning tasks. CW laser cleaning machines are better suited for larger surfaces where fast and efficient cleaning is required, such as in the automotive or shipbuilding industries. They are particularly effective for removing thick layers of rust, paint, or other tough contaminants.
- Portable Laser Cleaning Machines: Designed for flexibility and ease of use, portable laser cleaning machines are compact, lightweight systems that can be moved to different locations. These machines are ideal for fieldwork or applications in hard-to-reach areas, providing the same high-quality cleaning performance as stationary machines but with greater mobility. They are often used for on-site maintenance in industries like construction, aviation, and infrastructure.
- Stationary Laser Cleaning Systems: Stationary laser cleaning systems are larger, integrated machines that are typically part of a production line. These systems offer automation and high throughput for industries that require large-scale, repetitive cleaning tasks. Ideal for high-volume production environments, stationary systems provide consistent and efficient cleaning performance with minimal operator involvement.
Key Components and Features
- Laser Source: The laser source is the heart of the machine, providing the energy needed for the cleaning process. The power and type of the laser source determine the machine’s capabilities, with higher-power lasers being used for tougher cleaning tasks. Pulsed and continuous wave lasers are the two main types of sources, each offering different benefits based on the application.
- Beam Delivery System: The beam delivery system consists of the optics and mechanisms that direct the laser beam to the surface being cleaned. This system can include mirrors, lenses, and fiber optics to ensure the laser is accurately focused on the target. A well-designed beam delivery system ensures the precision and efficiency of the cleaning process, allowing for uniform coverage and consistent results.
- Control Unit: The control unit is the machine’s interface, allowing operators to adjust settings like laser power, beam focus, and scanning speed. Advanced control systems often come with pre-programmed cleaning modes, making the operation more user-friendly and allowing for repeatable, high-quality results. Some systems also feature automation capabilities, enabling integration into larger production lines.
- Cooling System: Laser cleaning generates heat, so a cooling system is necessary to maintain optimal operating temperatures and prevent overheating. Depending on the machine, the cooling system can be air-cooled or water-cooled. Proper cooling ensures the longevity of the laser source and other critical components, preventing performance degradation over time.
- Safety Mechanisms: Laser cleaning machines are equipped with various safety features to protect operators and prevent accidents. These may include interlocks, emergency stop buttons, protective enclosures, and sensors that monitor the machine’s operation. Operators are also required to use personal protective equipment (PPE), such as laser safety goggles, to protect their eyes from the intense light emitted by the laser.
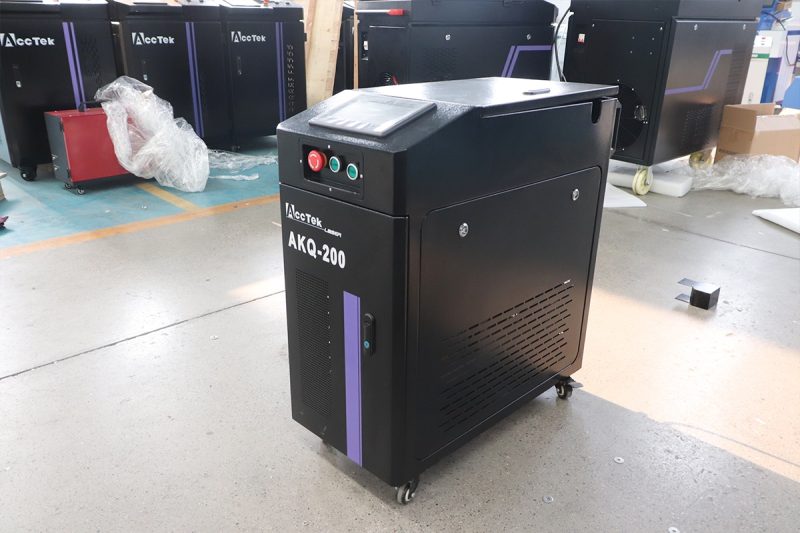
Applications of Laser Cleaning Machines
Industries Using Laser Cleaning
- Automotive Industry: Laser cleaning plays a critical role in the automotive sector by preparing surfaces for welding, bonding, and coating. It removes rust, paint, and production residues from car body parts, engine components, and molds, ensuring high-quality finishes and improved product durability. This technology also enhances efficiency in cleaning delicate parts without causing damage.
- Aerospace Industry: Precision is paramount in the aerospace industry. Laser cleaning is used to prepare surfaces for bonding, coating, and inspection. Aircraft components, including turbine blades and fuselage parts, benefit from laser cleaning’s ability to remove contaminants without damaging sensitive materials. The non-contact nature of the process also minimizes mechanical stress, ensuring safety and structural integrity.
- Manufacturing Industry: In manufacturing, laser cleaning ensures high-quality production by cleaning molds, tools, and fixtures. It removes residues, oxidation layers, and contaminants from metal and non-metal parts, reducing downtime and enhancing product consistency. The ability to automate laser cleaning also makes it suitable for integration into production lines, boosting efficiency and throughput.
- Cultural Heritage Restoration: Laser cleaning offers a safe and precise solution for restoring historical artifacts, sculptures, and paintings. It allows conservators to remove dirt, pollution residues, and oxidation from sensitive surfaces without harming the underlying material. The controllability of the laser beam ensures that even delicate works of art can be restored with minimal risk.
- Shipbuilding Industry: In shipbuilding, laser cleaning is used to remove rust, marine growth, and old paint layers from hulls and other structural components. It provides a fast and efficient method for surface preparation before repainting or welding, improving corrosion resistance and reducing maintenance costs. The mobility of portable laser systems also enables cleaning in hard-to-reach areas onboard vessels.
- Electronics Industry: Laser cleaning is essential in the production and maintenance of electronic components, where cleanliness is critical. It effectively removes oxides, dust, and residues from circuit boards, connectors, and enclosures, ensuring the reliability and performance of the final product. Laser cleaning’s precision makes it particularly suitable for microelectronics and delicate assemblies.
Common Use Cases
- Rust and Corrosion Removal: Laser cleaning excels in removing rust and corrosion from metal surfaces, preparing them for further processing. By selectively targeting oxidation layers without damaging the base material, laser cleaning enhances the lifespan and appearance of products in industries such as automotive, shipbuilding, and manufacturing.
- Paint Stripping: Traditional paint removal methods involve chemicals or abrasives that can harm the environment and underlying surfaces. Laser cleaning offers an eco-friendly alternative, efficiently stripping paint from metal, plastic, or other surfaces without the use of solvents or abrasives. This makes it ideal for automotive, aerospace, and marine applications.
- Oil and Grease Cleaning: In industrial settings, laser cleaning is used to degrease parts and tools, ensuring they are clean before assembly or coating. It removes oils, greases, and lubricants with precision, minimizing contamination risks in processes like welding or bonding. This non-contact cleaning method is particularly useful in electronics and automotive manufacturing.
- Surface Preparation: Laser cleaning prepares surfaces for coatings, welding, and bonding by removing contaminants and enhancing surface adhesion. It is widely used in the automotive and aerospace industries, where clean surfaces are essential for high-quality results. Surface preparation using laser cleaning ensures better adhesion and reduces the risk of defects.
- Residue Removal: After production processes such as machining, molding, or welding, laser cleaning removes residues like oxides, dust, and scale. This ensures that components meet strict quality standards, reducing rework and improving product consistency. Laser cleaning is particularly effective in industries with tight tolerances, such as aerospace, manufacturing, and electronics.
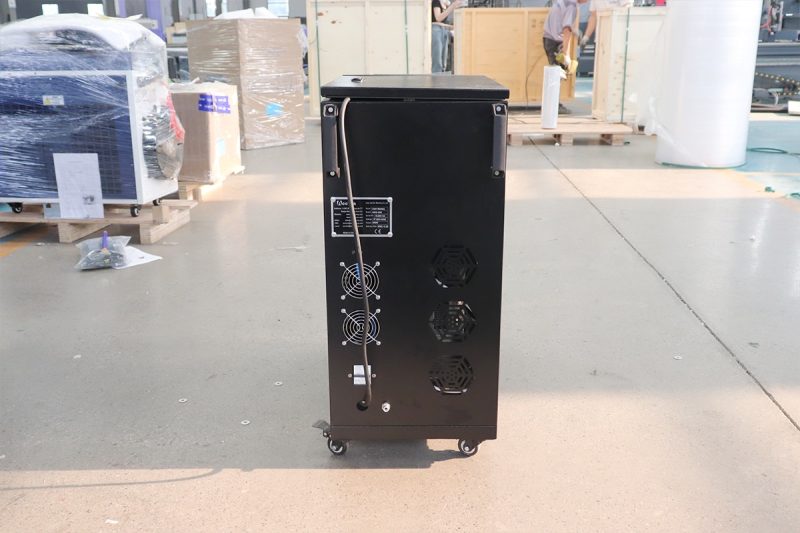
Benefits of Laser Cleaning Machines
Environmental Benefits
- No Chemical Waste: Unlike conventional cleaning processes that rely on solvents, acids, or other chemicals, laser cleaning eliminates the need for such hazardous substances. As a result, no chemical waste is generated, reducing environmental pollution and eliminating the need for costly disposal of toxic materials. This eco-friendly approach also ensures compliance with increasingly stringent environmental regulations.
- Energy Efficiency: Laser cleaning machines are designed to be energy-efficient, consuming less power than other industrial cleaning methods such as sandblasting or chemical baths. Additionally, modern laser systems can operate continuously without frequent downtime, further enhancing energy savings over time. The ability to precisely target contaminants reduces the need for multiple cleaning cycles, maximizing efficiency with minimal energy input.
- Minimal Air Pollution: Traditional cleaning methods, especially abrasive blasting, release fine dust particles and pollutants into the air, potentially harming workers and the environment. In contrast, laser cleaning emits minimal airborne contaminants. Some systems also include built-in dust collection units, capturing any residue generated during the cleaning process. This results in a cleaner, safer work environment with improved air quality.
Cost Benefits
- Lower Operating Costs: Laser cleaning machines require minimal consumables, such as chemicals or abrasive media, significantly reducing operational costs. Once the machine is installed, the primary expense is electricity, which is far less than the recurring costs associated with traditional cleaning methods. Moreover, automated systems can reduce labor requirements, saving additional costs over time.
- Minimal Maintenance: With fewer moving parts and no need for chemical handling, laser cleaning machines are easy to maintain. Regular maintenance typically involves simple tasks such as checking optics and keeping the cooling system operational. This reduces downtime, repair costs, and the need for specialized technicians, ensuring uninterrupted performance in industrial environments.
- Long-Term Savings: While the initial investment in a laser cleaning machine can be substantial, the long-term savings quickly outweigh the upfront costs. Reduced operational expenses, fewer maintenance requirements, and increased productivity lead to a higher return on investment (ROI). Laser cleaning’s durability and longevity also mean fewer replacements or upgrades, contributing to long-term financial benefits.
Efficiency and Effectiveness
- Precision Cleaning: One of the most significant advantages of laser cleaning is its precision. The laser can be adjusted to target specific contaminants while leaving the underlying material intact, making it ideal for delicate surfaces or intricate components. This level of precision is unmatched by traditional methods, ensuring that only the unwanted material is removed.
- Speed: Laser cleaning machines can perform tasks faster than manual or chemical cleaning methods. Continuous-wave lasers, in particular, provide high-speed cleaning for large surfaces, reducing downtime and improving production efficiency. This speed is crucial in industries like manufacturing, where every minute counts toward meeting tight deadlines.
- Consistency: Unlike manual cleaning methods, laser cleaning offers consistent results across every application. Automated laser systems ensure uniform cleaning quality, reducing the risk of human error. This consistency is especially important in industries such as aerospace, automotive, and electronics, where precision and repeatability are essential to meet quality standards.
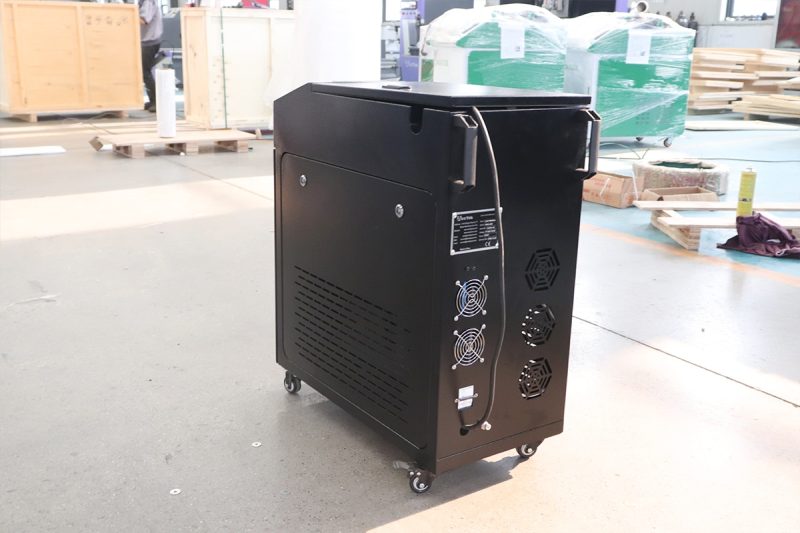
Factors to Consider Before Buying a Laser Cleaning Machine
Type of Material to Be Cleaned
Different materials respond differently to laser cleaning, so it is essential to match the machine’s capabilities with the type of material and contaminant you need to remove.
- Substrate Material: The material being cleaned—whether metal, plastic, glass, or stone—determines the required laser parameters. Metals, such as stainless steel or aluminum, may need higher-powered lasers, while more delicate surfaces may benefit from pulsed lasers for precision cleaning.
- Contaminant Type: The type of contamination—such as rust, paint, oil, or oxidation—affects the choice of laser. Thick rust or heavy paint layers will require higher power settings, while lighter residues or delicate coatings need less aggressive cleaning to prevent surface damage.
- Surface Sensitivity: Some surfaces are more sensitive to heat or abrasion than others. For example, historic artifacts or thin metal sheets may require pulsed lasers with lower energy levels to avoid damage, while industrial components can withstand more intense laser exposure.
Level of Contamination
Understanding the extent and uniformity of the contamination will help you choose a machine with the right power and functionality.
- The Thickness of Contaminant Layer: The thicker the contaminant layer, the more power and time will be required for effective removal. Heavy-duty cleaning applications, such as rusted metal surfaces, may require a continuous wave laser to quickly penetrate and remove layers.
- Uniformity: Contaminants may be evenly distributed or appear as uneven patches. Machines with adjustable beam width and scanning parameters help address non-uniform contamination. Systems with programmable settings allow you to switch between fine and heavy-duty cleaning modes.
Required Power and Specifications
Laser power, pulse frequency, and wavelength are critical specifications that determine how well the machine will perform for your specific cleaning tasks.
- Laser Power: Higher power (e.g., 1000W or more) is recommended for removing thick rust or heavy paint layers, while lower power settings are ideal for precision cleaning tasks. The choice of power will also affect how quickly the machine completes the job.
- Pulse Frequency: Pulsed lasers, with adjustable pulse frequencies, offer better control for delicate cleaning tasks, while continuous wave lasers provide consistent power for large, tough surfaces. Selecting the right frequency ensures both efficiency and precision.
- Wavelength: The laser’s wavelength affects how well it is absorbed by different materials and contaminants. A common wavelength for industrial laser cleaning is 1064 nm, which works well on metals and rust. For specialized tasks, other wavelengths may be required.
Portability and Size
Whether the cleaning needs are on-site or in a workshop will influence your choice between portable or stationary laser cleaning machines.
- On-Site Cleaning Needs: Portable laser cleaning machines are compact and easy to move, making them ideal for fieldwork, shipyards, or construction sites. These models ensure that cleaning can be performed directly at the point of need, even in hard-to-reach areas.
- Space Constraints: If space is limited, choosing a compact laser system or one with a modular design is essential. For production lines, a stationary system with a dedicated cleaning area may be more suitable. Make sure to measure available space to ensure seamless installation.
Automation and Integration with Existing Systems
Modern laser cleaning systems often offer automation capabilities, which improve efficiency and consistency. Integration with existing systems is key for seamless operation.
- Robotic Integration: In manufacturing environments, laser cleaning systems can be integrated with robotic arms to automate the cleaning process. This setup allows for high-speed, repetitive tasks with minimal operator involvement, boosting productivity.
- Software Control: Advanced laser cleaning machines come with user-friendly software interfaces, allowing operators to customize settings for different tasks. Automation features, such as pre-set cleaning programs and remote control options, enhance usability and consistency.
Safety Considerations
Laser cleaning involves powerful lasers that can pose safety risks. Understanding the safety measures required will ensure the protection of operators and bystanders.
- Laser Safety Class: Most laser cleaning machines fall under Class IV, which means they pose a potential hazard to the eyes and skin. Proper safety measures, including protective barriers and interlocks, are essential for these machines.
- Protective Equipment: Operators must wear personal protective equipment (PPE), such as laser safety goggles, to protect their eyes from harmful laser radiation. Additional safety gear, like gloves and protective clothing, may also be required for certain tasks.
- Training Requirements: Operating a laser cleaning machine requires proper training to ensure safe and effective use. Manufacturers often provide training programs for operators, ensuring they understand machine settings, safety protocols, and maintenance procedures.
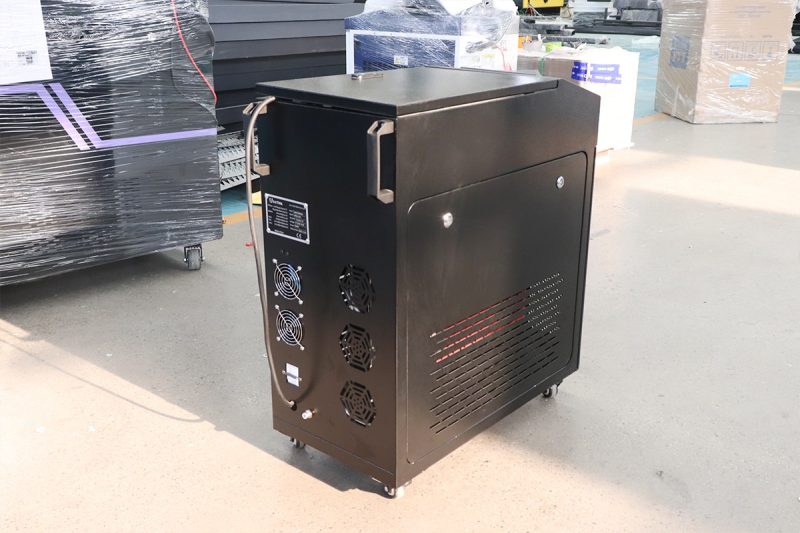
Choosing the Right Laser Cleaning Machine
Comparing Different Models
To find a laser cleaning machine that fits your needs, it’s important to assess various performance indicators and features.
- Performance Metrics: Evaluate the machine’s power, cleaning speed, and efficiency. Higher-powered models offer faster cleaning for tough contaminants like rust and paint, while lower-powered machines may be sufficient for lighter tasks. Look at the laser’s precision, beam stability, and scanning ability to ensure it meets the demands of your application.
- Versatility: Some laser cleaning machines are optimized for specific tasks, while others offer multi-functionality, such as switching between pulsed and continuous wave modes. Choosing a versatile machine ensures it can handle a variety of cleaning applications, from rust removal to delicate surface preparation, maximizing its utility across different tasks.
- Durability: Industrial environments demand robust equipment. Look for models with high-quality construction and protective features like dustproof enclosures or water-cooling systems. Durable machines reduce the need for frequent maintenance and replacement, resulting in lower downtime and operating costs over time.
Considering the Manufacturer
The quality and reliability of the machine are often tied to the reputation and expertise of the manufacturer. Assessing the manufacturer ensures you’re partnering with a company that can meet your expectations.
- Reputation: Opt for manufacturers with a solid track record in producing high-quality laser equipment. Trusted companies like AccTek Laser have built reputations for delivering reliable, effective machines backed by positive customer feedback. Checking online reviews and testimonials can provide insight into customer satisfaction and product performance.
- Technological Innovation: A forward-thinking manufacturer invests in research and development to deliver cutting-edge technologies. Look for companies offering innovative features, such as automation compatibility, user-friendly interfaces, or improved energy efficiency. Advanced technology ensures your machine stays relevant and competitive over time.
- Customization Options: Every operation has unique requirements. Some manufacturers offer customization options, allowing you to tailor the machine to your needs. Whether it’s adding automated controls, adjusting laser power, or integrating the machine into your production line, customization ensures you get the most out of your investment.
After-Sales Service and Support
A reliable after-sales service ensures smooth operation and long-term satisfaction with your purchase. The right support can minimize downtime and ensure you get the best performance from your machine.
- Warranty: A comprehensive warranty protects your investment by covering defects or issues during the initial period of ownership. Ensure the warranty includes critical components like the laser source and control systems, providing peace of mind in case of unexpected breakdowns.
- Technical Support: Access to fast and effective technical support is crucial, especially when using advanced technology. Manufacturers that offer 24/7 customer service, online troubleshooting resources, and remote diagnostics can help resolve issues quickly, minimizing operational disruptions.
- Training and Installation: Proper installation and training are essential for safe and efficient operation. Many manufacturers provide on-site setup and operator training to ensure your team is fully prepared. Comprehensive training helps operators understand the machine’s capabilities, settings, and safety protocols, leading to improved productivity and performance.
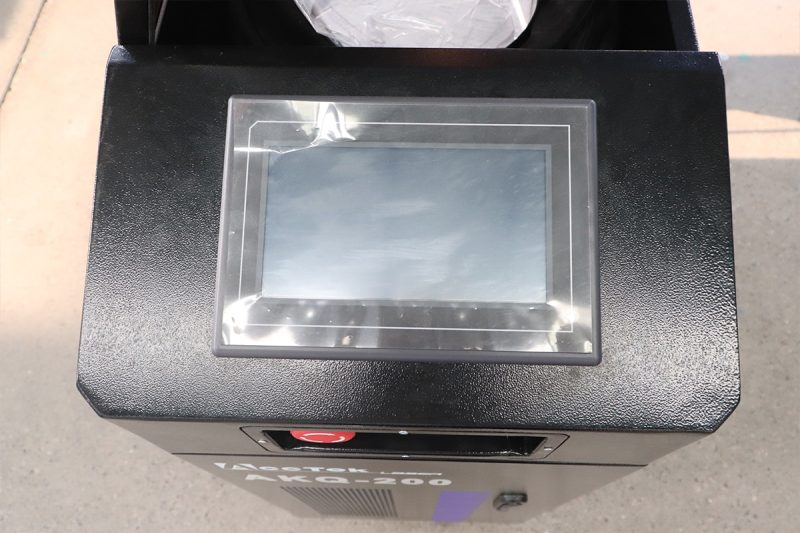
Cost Analysis
Initial Investment
- Purchase Price: The purchase price of a laser cleaning machine varies depending on the laser type, power, and additional features. Basic portable models typically cost less, while high-powered, stationary systems designed for industrial use can be more expensive. It’s essential to balance your budget with the performance capabilities required for your applications.
- Installation Costs: Installation costs can include expenses for setup, calibration, and integration into your existing workflow. Some manufacturers offer installation services as part of the purchase package. However, if additional infrastructure, such as electrical upgrades or ventilation, is needed, these costs should also be factored in.
Operating Costs
- Energy Consumption: Laser cleaning machines are energy-efficient, but power consumption still varies depending on the machine’s power and frequency of use. Higher-powered continuous wave lasers consume more electricity, so understanding your machine’s energy requirements helps estimate monthly utility costs. Comparing energy consumption between models can guide you toward a more cost-effective solution.
- Consumables: One of the advantages of laser cleaning is its minimal use of consumables compared to traditional methods. However, some machines may require protective optics, dust filters, or extraction systems to maintain performance. These consumables are generally low-cost but should still be included in your operational budget.
Maintenance Costs
- Routine Maintenance: Laser cleaning machines require regular maintenance to ensure optimal performance. This typically includes cleaning optics, checking cooling systems, and updating software. Routine maintenance helps extend the machine’s lifespan and prevent unexpected breakdowns, which could disrupt operations.
- Repairs and Parts Replacement: While laser machines are known for their durability, components like optics or cooling systems may require occasional replacement. It’s essential to account for repair costs and ensure the manufacturer provides easy access to spare parts. Having a maintenance plan in place or purchasing extended warranties can help manage these costs efficiently.
Return on Investment (ROI)
- Productivity Gains: Laser cleaning machines deliver fast and precise cleaning, reducing downtime and increasing operational efficiency. Automation options further enhance productivity, allowing operators to focus on other critical tasks. Faster cleaning means more throughput, leading to higher profitability.
- Quality Improvement: Consistent and precise cleaning ensures high-quality results, reducing the risk of defects or rework. This is especially important in industries like aerospace and automotive, where surface preparation impacts the quality of coatings and welds. High-quality results lead to improved customer satisfaction and fewer production delays.
- Cost Savings: Although the initial investment may be substantial, laser cleaning offers significant long-term savings. Lower energy consumption, minimal consumables, and reduced maintenance costs contribute to overall savings. Additionally, by eliminating the need for chemicals or abrasive materials, companies can reduce waste disposal costs and comply with environmental regulations more easily.
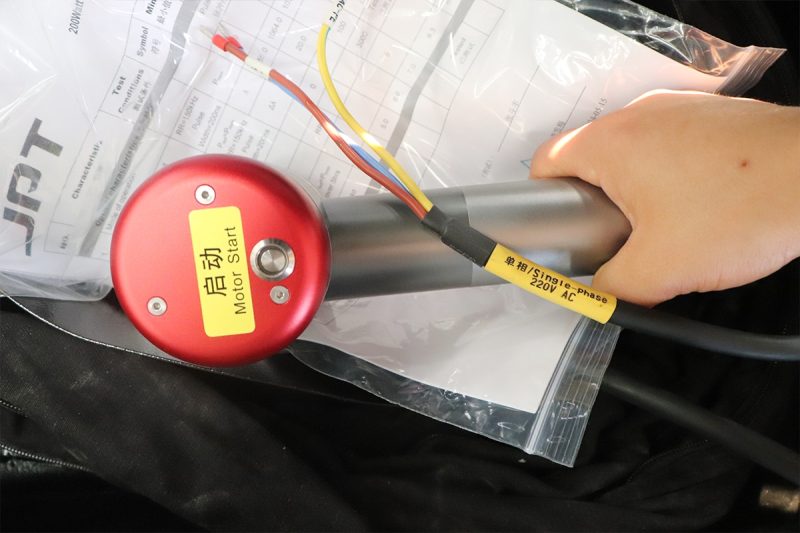
Legal and Safety Regulations
Safety Standards
To ensure safe operation, laser cleaning machines must adhere to various safety standards, which are often defined by both international and local regulatory bodies.
- International Standards: Laser cleaning machines are classified based on their potential risk to users. Most laser cleaning systems fall under Class IV—the highest risk category—due to their high-power output. These machines must meet strict international safety standards, such as those set by the International Electrotechnical Commission (IEC 60825-1), which outlines laser safety requirements and defines necessary protective measures. Additionally, the machine should comply with the ISO 11553-1 standard, which governs the safety of machinery using lasers, ensuring it’s safe for use in industrial environments.
- Local Regulations: In addition to international standards, local laws and regulations must be followed. Countries and regions may have specific guidelines for the installation, operation, and maintenance of laser equipment. For example, in the United States, laser machines must adhere to OSHA (Occupational Safety and Health Administration) guidelines. Similarly, the European Union mandates compliance with the European Machinery Directive and specific laser safety standards. Always consult with local authorities or industry experts to ensure full compliance in your region.
Training Requirements
Ensuring that your operators are properly trained is a critical part of safely running a laser cleaning machine. Without the right training, improper use can lead to accidents, injuries, or equipment damage.
- Operator Certification: In many countries, operators of high-powered laser equipment, including laser cleaning machines, are required to obtain certification. This certification ensures that the operator has the necessary skills and knowledge to safely handle, operate, and maintain the machine. Certification programs typically cover laser physics, safe operating practices, and emergency procedures. Some manufacturers offer certification programs as part of their after-sales support.
- Safety Training: Laser safety training is essential for everyone working in proximity to laser cleaning machines, not just operators. Training programs should cover the potential hazards associated with laser operation, such as eye and skin damage, and how to use personal protective equipment (PPE) like laser safety goggles. Training should also include an understanding of the machine’s safety features, such as interlock systems, emergency stop buttons, and protective enclosures. Regular refresher courses are recommended to keep operators up to date on safety procedures and best practices.
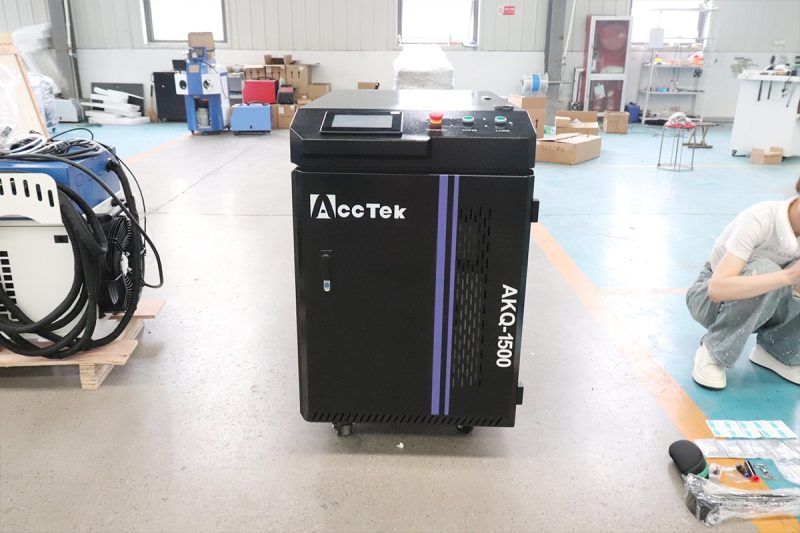
Summary
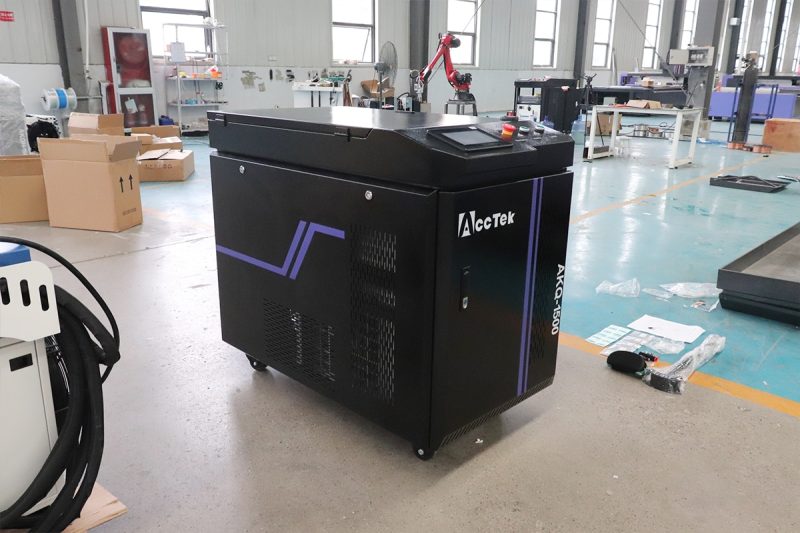
Get Laser Cleaning Solutions
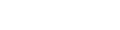
- [email protected]
- [email protected]
- +86-19963414011
- No. 3 Zone A, Lunzhen Industrial Zone,Yucheng City , Shandong Province.