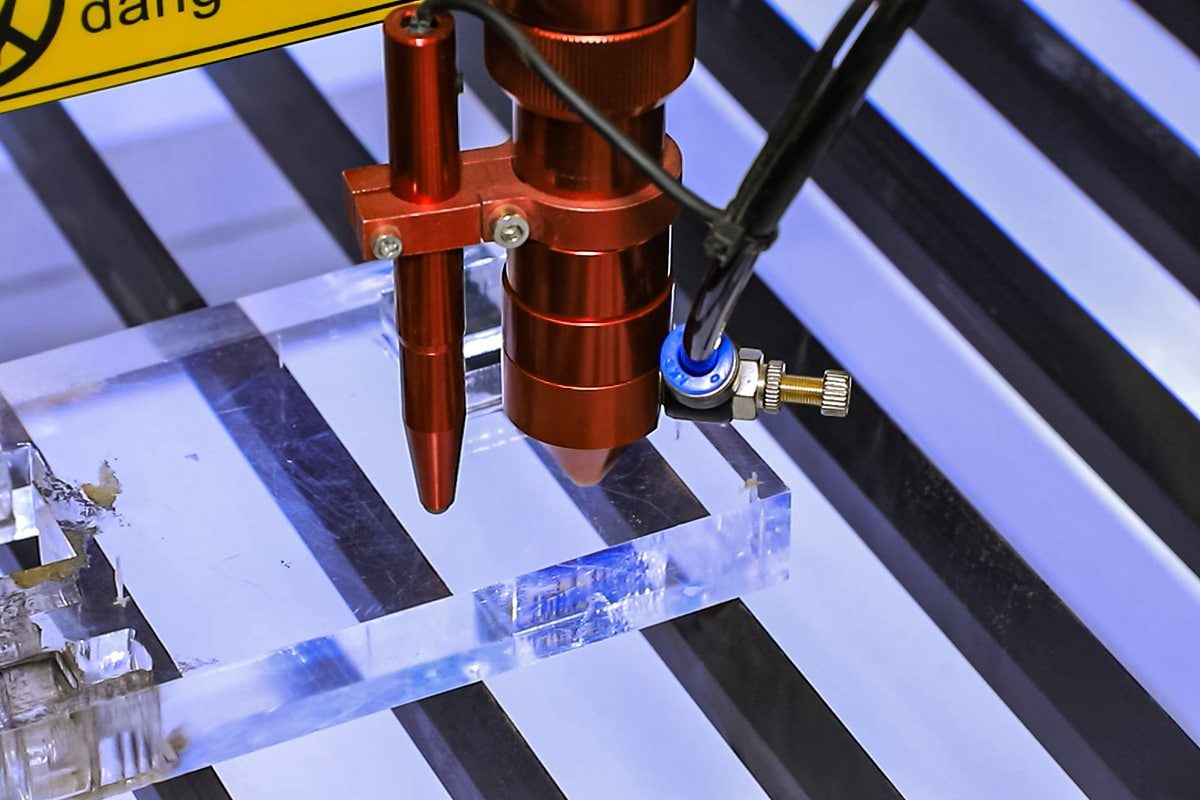
Can CO2 Laser Cutting Achieve High-Precision Complex Designs?
CO2 laser cutting has become a cornerstone technology in modern manufacturing, revolutionizing the way industries approach material processing. By harnessing the power of a concentrated laser beam, the technology is able to precisely cut a wide range of materials, including metals, plastics, and composites. Its non-contact nature minimizes material deformation, making it ideal for applications that require high precision and intricate details. The versatility of CO2 laser cutting machines has enabled them to be used in a variety of fields, from industrial manufacturing to creative design, demonstrating their adaptability and efficiency.
CO2 laser cutting demonstrates unparalleled high precision in complex designs, and can easily process complex patterns and details to ensure strict tolerances. This not only improves the quality of finished products and reduces the need for secondary processing, but also significantly reduces costs and improves production efficiency. With the continuous innovation of the industry, CO2 laser cutting has become a key driving force for precision engineering and advanced manufacturing.
Table of Contents
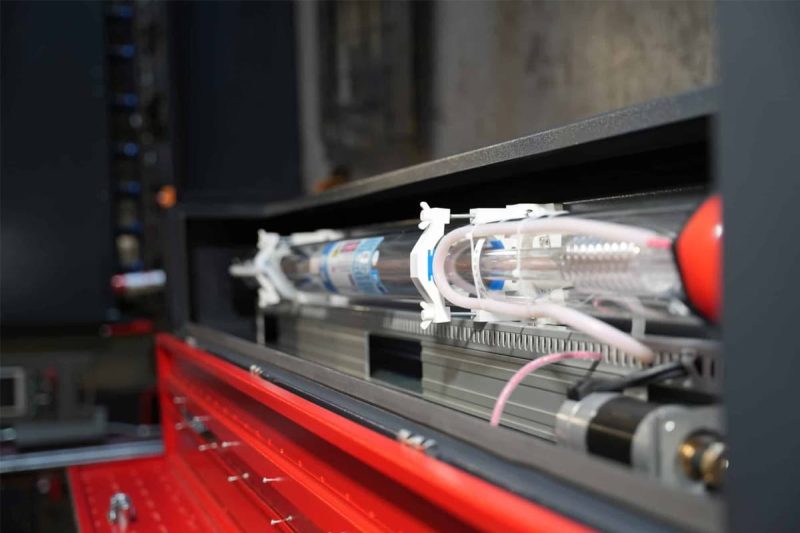
Understanding CO2 Laser Cutting
CO2 laser cutting has become a key technology in modern manufacturing and design due to its high precision and complex design capabilities. A deep understanding of its principles and functions can help companies maximize its potential and meet diverse application needs.
Principles of CO2 Laser Cutting
CO2 laser cutting uses a carbon dioxide laser generator to emit a high-energy infrared beam to cut, engrave or etch materials with extremely high precision. Its core principles include: using a laser medium mixed with carbon dioxide, nitrogen and helium to generate a laser beam; focusing the beam onto the surface of the material through lenses and lenses; using automated systems such as CNC to accurately guide the laser head to complete complex patterns; and using auxiliary gases such as oxygen, nitrogen or air to improve cutting efficiency, avoid oxidation and remove slag.
Overview of Cutting Technology and Precision Capabilities
The cutting process of CO2 laser system ensures accuracy and quality through highly controlled steps, including laser beam generation, material absorption of energy causing melting or vaporization, and assist gas to remove molten material, leaving a clean edge. Its precision capabilities are reflected in high accuracy (cutting tolerance to ±0.1 mm), narrow kerf to reduce material waste, automated system to ensure repeatability, and wide compatibility for a variety of materials such as metal, acrylic, wood, etc.
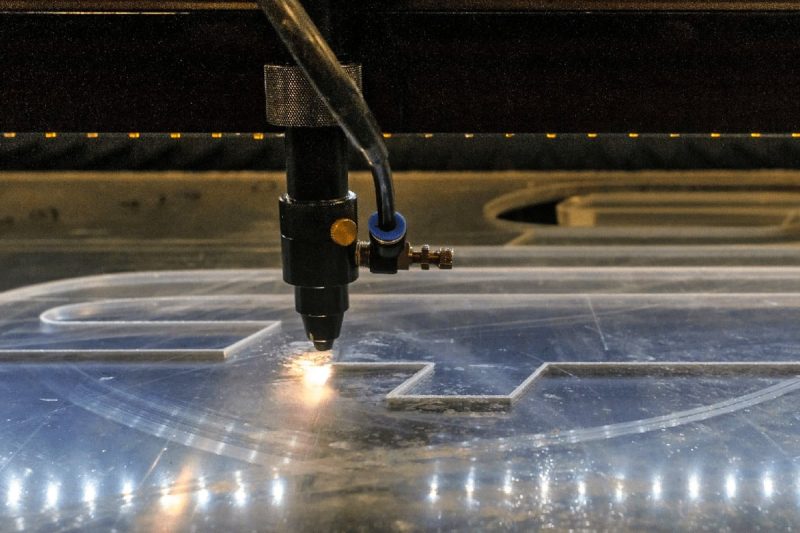
Key Factors Influencing CO2 Laser Cutting Precision
Achieving high precision with CO2 laser cutting depends on several critical factors. Understanding and optimizing these elements can enhance cutting accuracy and efficiency.
Laser Beam Quality:The quality of the laser beam is measured by the M2 factor. The closer the M2 value is to 1, the more concentrated the laser beam is and the finer the cutting effect is. A high-quality laser beam can provide a smaller spot, improve cutting accuracy, and reduce the heat-affected zone, thereby ensuring the accuracy of the cutting path.
Focus Settings:The focus position affects the fineness of the cutting edge. The correct focus setting ensures that the laser beam forms a suitable spot on the material surface, providing precise cutting depth and high-quality edges.
System Stability:The stability of the laser cutting machine determines the cutting accuracy. Unstable laser power or mechanical vibration will cause fluctuations in accuracy. A stable laser generator and precise motion system can ensure continuous high-precision cutting.
Achievable Tolerances:CO2 laser cutting can achieve an accuracy of ±0.1 mm, which makes it suitable for fields that require high precision, such as the processing of precision parts and electronic products.
Edge Quality:CO2 laser cutting provides smooth cut edges. The high-quality laser beam and focus control reduce burrs and heat-affected zones, improving cut quality and reducing the need for secondary operations.
Motion Control Systems:The positioning accuracy and dynamic response of the cutting machine directly affect the accuracy of the cutting path, especially when dealing with complex designs.
Material Properties and Thickness:The density, thermal conductivity, and thickness of the material will affect the absorption efficiency of the laser energy, thereby affecting the cutting effect and accuracy.
Cutting Speed and Power:Cutting speed too fast or insufficient power may result in incomplete cutting, while excessive power may ablate the material or affect the edge quality.
In short, CO2 laser cutting provides high-precision cutting and high-quality edge effects through precise laser beam control and system stability and is widely used in high-precision processing fields.
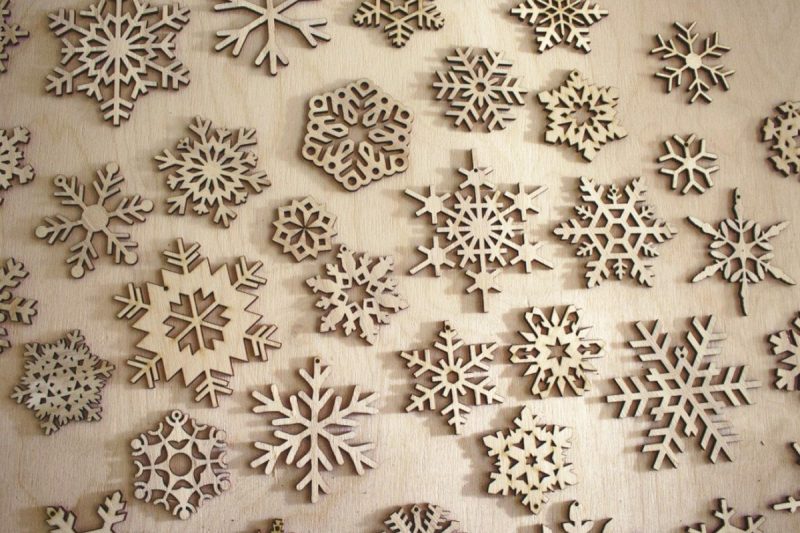
Complexity of Design
In the field of laser cutting, complex designs refer to projects that contain fine details, and complex patterns, and require strict tolerances. The realization of these designs places extremely high demands on the accuracy, stability, and processing capabilities of the equipment, and also brings new challenges to the processing technology.
Definition of Complex Design in the Context of Laser Cutting
Complex designs usually refer to designs that require high precision and careful operation, including:
- Fine details: such as micro-engravings or decorative patterns require the laser cutting machine to achieve stable and high-precision positioning.
- Complex patterns: Involving irregular shapes or hierarchical geometric designs, the cutting path requires multiple adjustments and efficient planning.
- Tight tolerances: In manufacturing that require extremely high precision, cutting deviations need to be controlled within the range of microns or 0.1 mm.
These designs place high demands on the core performance of laser-cutting equipment, such as beam quality, motion control, and power stability.
Challenges of Complex Patterns
Handling complex patterns is a major challenge in laser cutting technology, especially when accurately reproducing multi-layered or asymmetrical designs. The following issues are particularly prominent:
- Complex path planning: When cutting complex patterns, the CNC system needs to optimize the variable cutting path to reduce time loss and errors.
- Accumulation of thermal effects: Long-term continuous cutting of complex patterns may lead to local heat accumulation, causing material warping or deformation.
- Consistency control: For repetitive processing tasks, it is necessary to ensure that each finished product remains consistent in complex designs without any deviations or defects.
The Challenge of Fine Details
Achieving fine detail cutting places higher demands on the performance of the laser cutting machine:
- Beam diameter limitation: To achieve fine cutting lines, the spot diameter of the laser beam must be very small, usually in the micrometer range.
- Power stability: Power fluctuations in the laser output directly affect the clarity of details and the quality of the edges, which may cause uneven cutting or burrs.
- High dynamic response requirements: The motion control of the laser head needs to respond quickly to ensure that the path is not offset or overlapped when performing complex cutting in fine areas.
These technical requirements make processing fine details a very challenging task in laser cutting.
The Challenges of Tight Tolerances
Tight tolerances are an indispensable requirement in high-end manufacturing, especially in industries such as medical and aerospace. To meet these requirements, laser cutting faces the following difficulties:
- High-precision positioning: The laser cutting machine must be equipped with a high-resolution position feedback system to ensure the micron-level positioning accuracy of the cutting head.
- Thermal deformation compensation: The material may expand or deform due to heat during the cutting process. The laser cutting machine needs to be monitored in real-time and automatically adjusted to ensure the cutting size.
- Beam quality: The use of high-quality optical components can reduce beam scattering and deviation, ensuring the clarity and accuracy of the cutting edge.
The need to maintain high processing efficiency while meeting strict tolerances further complicates the cutting process.
By addressing these challenges, laser cutting technology has become an essential tool for realizing complex designs, bringing new possibilities to the world of precision manufacturing.
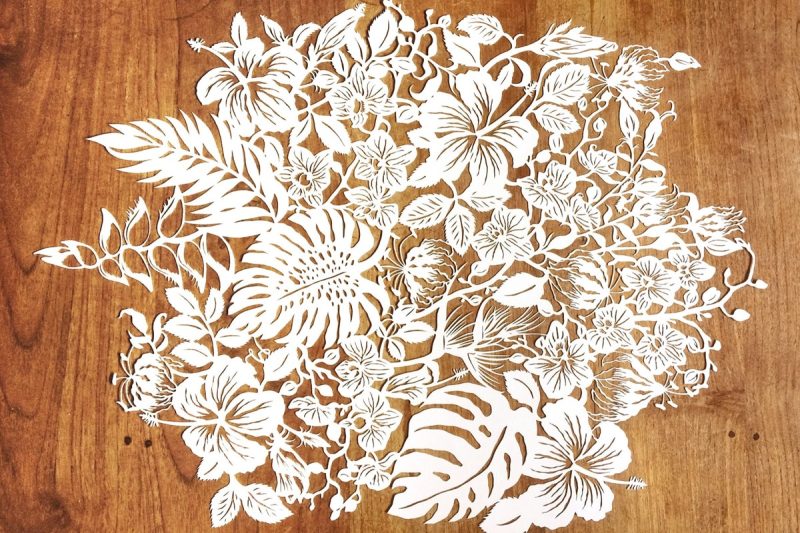
Laser Cutting Precision Improvement Technology
In the constantly evolving field of laser cutting, technological advancements have greatly improved precision, efficiency, and versatility. These innovations address challenges related to accuracy and consistency, especially when handling intricate designs and varying material types. Below, we explore three key breakthroughs in CO2 laser cutting: auto-focus adjustment, real-time monitoring systems, and CAD/CAM integration.
Auto-Focus Adjustment: Enhancing Accuracy Across Materials
Auto-focus adjustment is a transformative feature in CO2 laser cutting systems. It allows the laser to dynamically adjust to different material thicknesses and surface contours, ensuring the laser beam stays at an optimal focal point, which is crucial for precision cutting.
- Precision Across Material Types: Different materials (e.g., metals, plastics, glass) require specific focal settings for clean cuts. Auto-focus eliminates the need for manual adjustments, reducing both downtime and human error.
- Improved Edge Quality: By maintaining the correct focal distance, auto-focus minimizes issues like rough edges, incomplete cuts, or material burn-through, particularly in intricate patterns.
- Increased Efficiency: Automated adjustments streamline the cutting process, making it faster and more reliable, especially when switching between materials or working with multi-layered designs.
Real-Time Monitoring Systems: Ensuring Consistency Through Live Adjustments
Real-time monitoring systems allow CO2 laser cutting machines to maintain precision and consistency throughout the cutting process. These systems use sensors and feedback loops to monitor parameters like power output, beam alignment, and material interaction.
- Dynamic Adjustments: Monitoring systems can automatically adjust settings such as laser power and cutting speed to account for variations in material density or unexpected irregularities.
- Minimized Defects: Real-time detection of issues like heat distortion or beam misalignment prevents defects before they occur, ensuring higher-quality results.
- Enhanced Productivity: Continuous feedback reduces the need for post-cut inspections and rework, increasing throughput and cost efficiency.
CAD/CAM Integration: Precision Design and Execution
The integration of computer-aided design (CAD) and computer-aided manufacturing (CAM) software with CO2 laser cutting systems has revolutionized how designs are translated into physical components. This synergy enables seamless design execution and optimization.
- Accurate Path Planning: CAD/CAM software generates precise cutting paths, ensuring that even the most intricate designs are executed flawlessly. This is crucial for industries requiring tight tolerances, such as aerospace and medical device manufacturing.
- Material Optimization: Advanced software simulates cutting paths and material usage, reducing waste and enhancing cost efficiency.
- Customizable Parameters: Operators can pre-define laser generator settings (such as power and cutting speed) within the software, ensuring consistency across multiple production runs and materials.
- Automation and Scalability: CAD/CAM integration supports automated workflows, facilitating scalable production without compromising precision or quality.
The combination of automatic focus adjustment, real-time monitoring, and CAD/CAM integration sets a new standard for CO2 laser cutting accuracy. These technological advances not only increase cutting accuracy, but also improve efficiency, reduce material waste, and reduce operating costs. Together, they enable manufacturers to tackle complex designs and achieve excellent consistency across a wide range of applications.
By adopting these cutting-edge technologies, companies can maximize the potential of CO2 laser generators and provide high-quality results that meet the needs of modern industry. Whether it is complex jewelry designs, precision medical components, or automotive parts, these technological advances are paving the way for the future of laser cutting solutions.
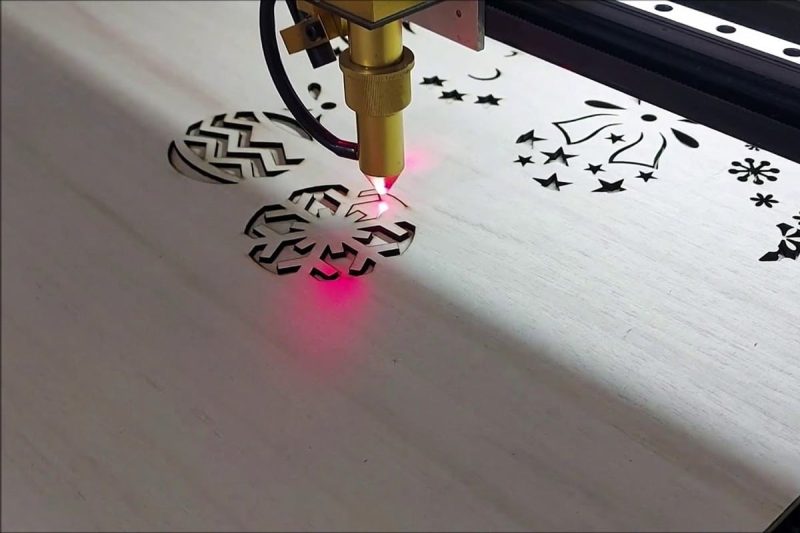
Advantages of High-Precision CO2 Laser Cutting
Improved Part Quality and Consistency
High-precision CO2 laser cutting provides superior surface finishes and uniformity. This technology ensures that every product maintains high consistency in size and shape, whether in mass production or custom-made parts. Compared to traditional cutting methods, CO2 laser cutting significantly reduces deviations caused by human error or mechanical accuracy issues, thereby greatly enhancing product consistency and quality. Especially in industries with strict surface quality requirements, such as automotive, aerospace, and medical device manufacturing, laser cutting produces smoother edges with fewer burrs and irregular shapes.
Reduction in Secondary Processing Needs
The precise cutting capabilities of CO2 laser generators significantly reduce the need for post-cutting adjustments. Traditional cutting methods often require multiple secondary operations to refine cut edges or adjust dimensions. In contrast, high-precision laser cutting can achieve the desired cutting results in one pass, saving time and cost on subsequent adjustments. This benefit is especially valuable for manufacturing complex or precision parts, such as precision tools, aerospace components, and electronic housings, reducing labor costs and production time.
Cost Savings and Productivity Boost
By minimizing secondary processing and optimizing the cutting process, high-precision CO2 laser cutting significantly boosts production efficiency. Laser generators can perform efficient cutting with minimal human intervention, shortening production cycles and ensuring consistent part quality, which reduces rework and material waste. This automated and precise production method not only lowers operational costs but also increases throughput, thus improving the overall productivity of businesses. For large-scale manufacturers, high-precision CO2 laser cutting is a key tool for streamlining production processes and enhancing competitiveness.
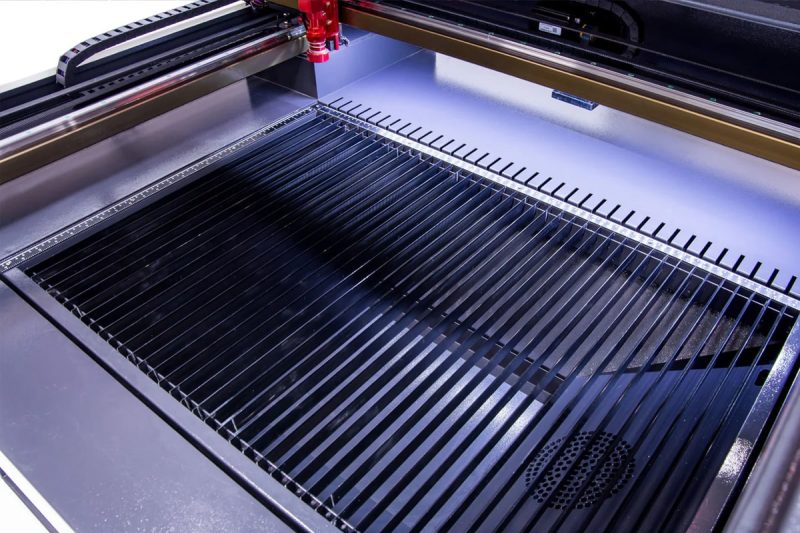
Applications Requiring High-Precision Cutting
High-precision cutting is used in a wide range of fields, some of the key applications include:
Aerospace Components: The aerospace industry requires extremely high cutting accuracy to ensure the performance and safety of components. For example, the production of engine components, structural frames, and precision parts requires laser-cutting technology to ensure that each component meets strict requirements in terms of size, shape, and strength. Any slight deviation may affect the overall performance or safety, so high-precision cutting technology is essential.
Electronics and Microelectronics: As electronic devices become increasingly miniaturized, microelectronic components have increasingly stringent precision requirements. In applications such as chip packaging, PCB board cutting, and sensor manufacturing, laser cutting can achieve extremely high precision to ensure that each circuit and component is connected correctly, thereby ensuring the reliability and performance of electronic devices.
Medical Devices: Medical devices and equipment, especially minimally invasive surgical instruments and implants, require very high cutting accuracy. These devices often involve complex geometries and extremely small sizes, and laser cutting can cut metals, plastics, and other biocompatible materials with extremely fine precision to ensure that the device meets strict medical standards in terms of function and safety.
Architectural Models and Prototypes: In architectural design and prototyping, laser cutting technology is used to create complex architectural models and delicate components. It can accurately cut a variety of materials such as wood, plastic and metal for design verification and sample production. This is very important for demonstrating design concepts, testing engineering solutions and customer communication.
These applications demonstrate the irreplaceable role of high-precision cutting technology in various fields, which can meet strict tolerances and complex design requirements to ensure product performance and quality.
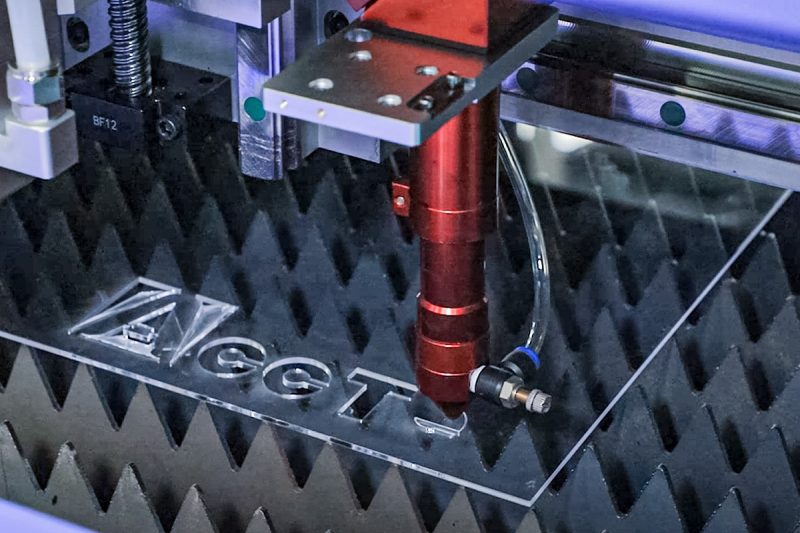
Summarize
CO2 laser cutting technology, with its high precision and excellent adaptability, has proven its unparalleled advantages in the field of complex designs and strict tolerances. From laser beam quality to automation functions, every aspect supports the realization of high-precision cutting. Whether it is key parts for aerospace or the precision needs of microelectronics and medical equipment, CO2 laser cutting not only improves the consistency and quality of parts but also significantly reduces secondary processing costs and improves overall production efficiency.
Looking to the future, with the continuous innovation of technology, CO2 laser cutting will show its potential in more fields, providing more efficient and economical solutions for precision processing and complex design in the manufacturing industry. This technology is not only a core tool for high-end manufacturing, but will also continue to drive industries toward a more precise and efficient future.
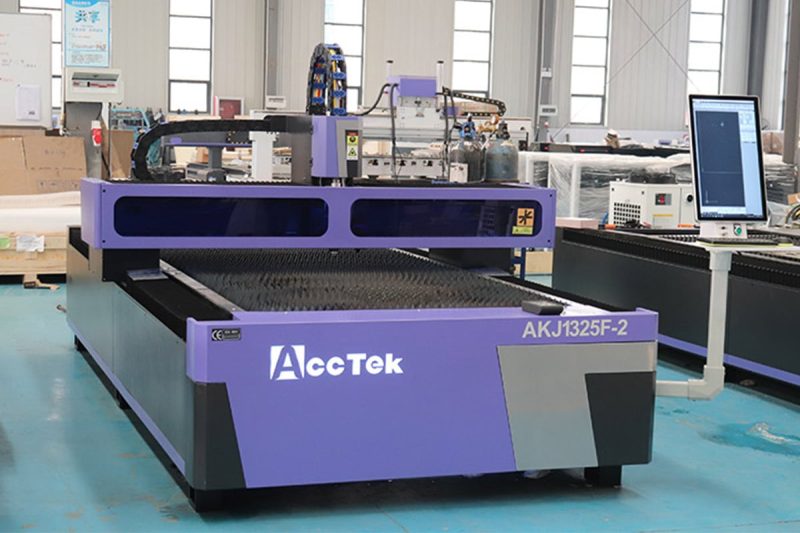
Get Laser Solutions
Want to achieve high-precision cutting of complex designs? AccTek Laser provides you with the perfect solution! As experts in laser technology, we focus on providing customers with high-performance and high-reliability CO2 laser-cutting machines to meet your various needs in precision manufacturing. From aerospace parts to micro-machining of electronic devices, our cutting equipment helps you easily meet complex design challenges with excellent accuracy and stability. Contact us now to get a customized laser-cutting solution for you to make your manufacturing process more efficient and better!
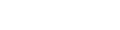
Contact information
- [email protected]
- [email protected]
- +86-19963414011
- No. 3 Zone A, Lunzhen Industrial Zone,Yucheng City , Shandong Province.
Get Laser Solutions