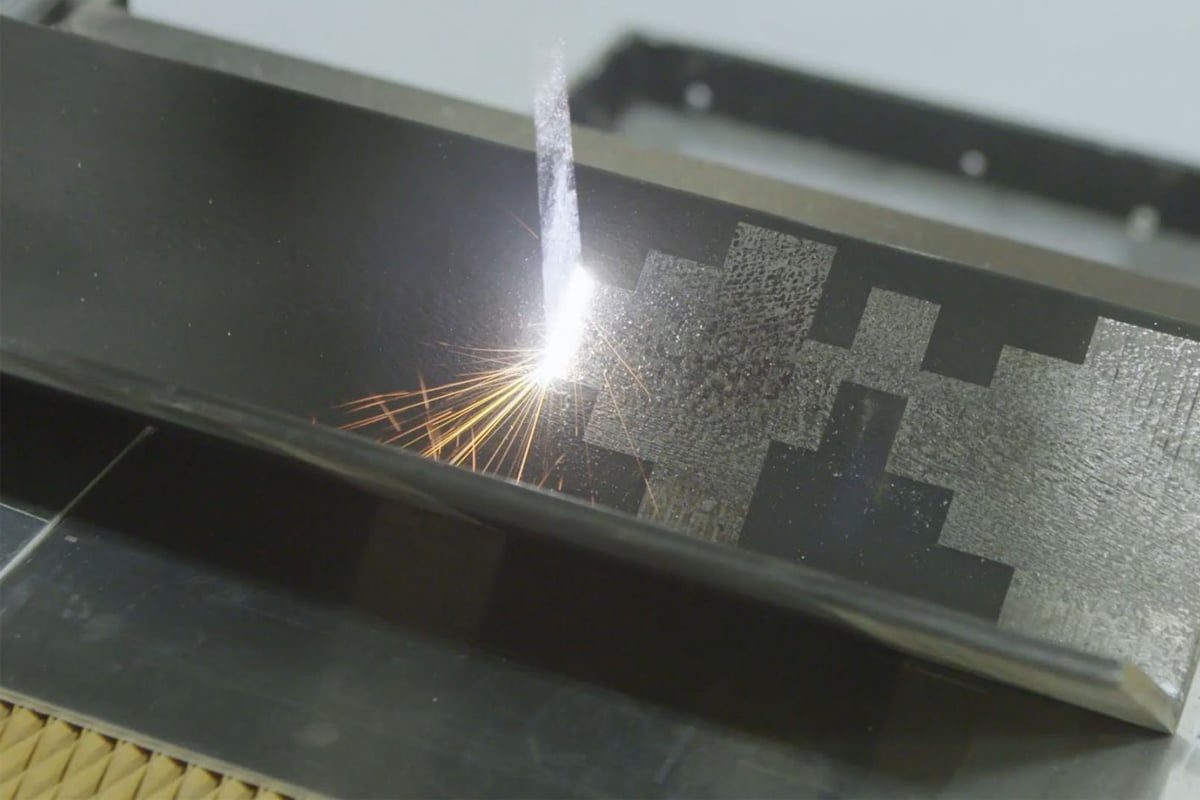
Can Laser Cleaning Be Used on Sensitive Materials Without Causing Damage?
As an innovative technology, laser cleaning has been widely used in recent years. It irradiates the target surface with a high-energy laser beam to accurately remove surface rust, dirt, oxides, coatings, or other impurities, thereby achieving efficient and environmentally friendly cleaning. This technology not only improves the accuracy and efficiency of the cleaning process but also reduces the waste and chemical use caused by traditional methods. However, for some particularly sensitive materials, such as cultural relics, electronic components, or aerospace parts, the application of laser cleaning technology should be treated with caution. Because these materials usually have high value or specific physical and chemical properties, their potential risk of damage has become the focus of attention. For example, ancient cultural relics may cause changes in surface structure or loss of original texture due to the high energy of the laser; electronic components may cause circuit performance degradation due to the thermal effect of the laser; and aerospace parts need to pay special attention to the microcracks that may be generated during laser cleaning, which may affect the overall strength and service life of the material. Therefore, when applying laser cleaning technology in these sensitive fields, detailed evaluation and adjustment must be carried out to ensure that irreversible damage to the material will not be caused. This article will explore the application potential of laser cleaning technology in these sensitive fields in depth and analyze whether it will cause substantial damage to the material.
Table of Contents
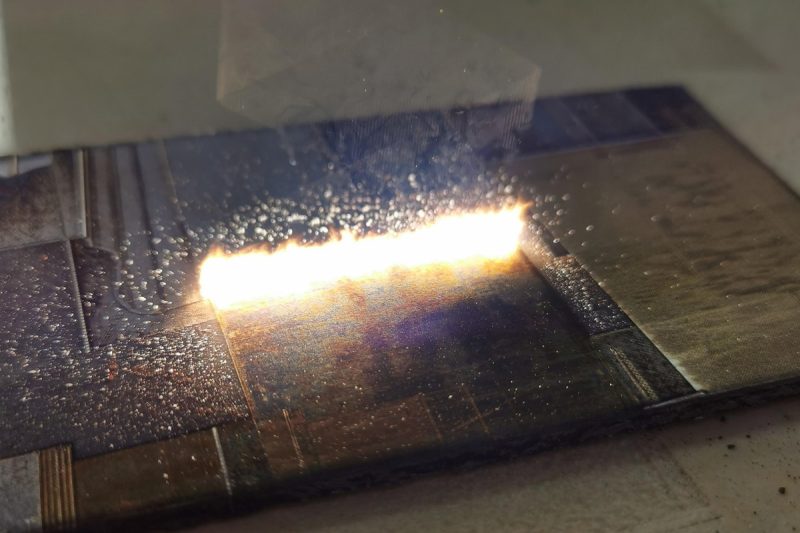
Learn About Laser Cleaning Technology
Laser cleaning technology is a non-contact cleaning method that uses a high-energy laser beam to irradiate the surface of an object to remove impurities such as dirt, oxides, grease, and coatings. In recent years, this technology has gradually become one of the preferred cleaning processes in various industries due to its high efficiency, environmental protection, and precision.
How Laser Cleaning Works
The core principle of laser cleaning is to use a high-energy laser beam to interact with contaminants or unwanted coatings on the surface of an object. The laser energy is focused on a very small area, causing the contaminants to heat up, expand, or evaporate instantly, and then be removed. During the cleaning process, the laser energy can be absorbed by the contaminant layer without affecting the object’s bulk structure. This process is divided into several mechanisms, mainly including:
- Thermal decomposition: The laser heats the target material to its decomposition temperature, causing it to evaporate or vaporize.
- Photopressure effect: The shock wave generated by the laser causes the contaminant to be peeled off from the surface.
- Pulsed laser peeling: Pulsed lasers are used to peel off surface contaminants without damaging the underlying substrate.
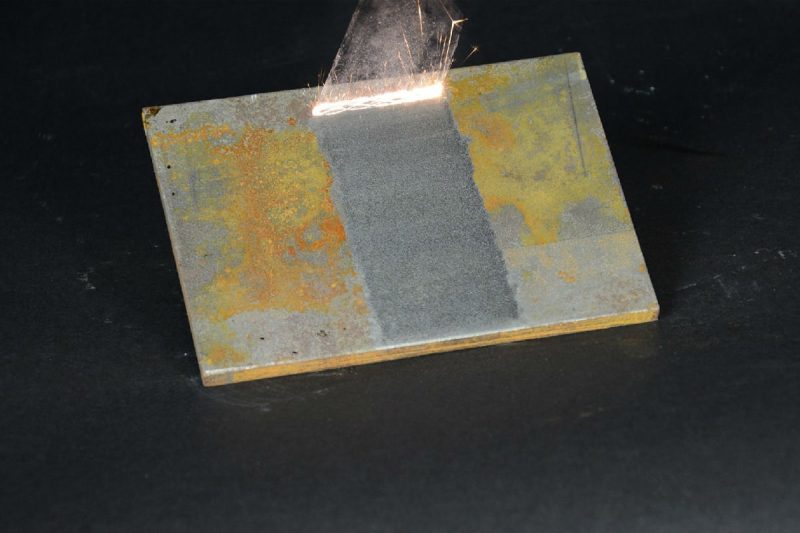
Key Benefits of Laser Cleaning
The main advantages of laser cleaning not only provide new possibilities for various industrial cleaning applications but also play a key role in improving production efficiency, reducing environmental impact, and protecting sensitive materials. The following is a detailed explanation of several of its core advantages:
High Accuracy
The focusing properties of the laser beam enable it to achieve extremely high levels of precision. Laser cleaning systems can target very small areas on the target surface for cleaning without affecting the surrounding material. For applications that require the removal of contaminants, rust or coatings on complex or delicate structures, such as mold cleaning, cultural relic restoration or microelectronics cleaning, laser cleaning allows for non-destructive operations. This highly controllable precision makes it ideal for industries that require strict quality control and detail requirements.
High Cleaning Efficiency
Laser cleaning uses a high-energy laser beam to quickly vaporize and remove surface impurities such as grease, rust, coatings, and oxide layers. Its extremely short pulse time and high-speed scanning capability greatly shorten the overall cleaning time, thereby improving production efficiency. Compared with traditional cleaning methods such as sandblasting or chemical cleaning, laser cleaning is not only faster, but also reduces downtime while ensuring quality, greatly optimizing the production process.
Environmentally Friendly and Safe
Laser cleaning technology is considered one of the green and environmentally friendly options. Unlike traditional chemical cleaning methods, laser cleaning does not use any chemicals or solvents, so no harmful chemical waste is generated. It only removes pollutants or coatings through laser beams, without causing secondary pollution to operators or the environment. In addition, the smoke or microparticles generated during laser cleaning can be collected by specialized filtering devices, further reducing the impact on the environment. For industries with strict environmental protection requirements, laser cleaning is a safe and efficient alternative.
Highly Adaptable
Laser cleaning is not limited to a certain type of material. It can be applied to a variety of substrates, such as metal, glass, stone, composite materials and even plastic. This versatility makes it widely used in industries such as aerospace, automobile manufacturing, and building restoration. Whether it is removing rust from the metal surface or cleaning the oxide film on the glass, laser cleaning can process different materials in a non-destructive way and provide consistent cleaning results.
Non-Contact Process
Since laser cleaning is a non-contact process, no mechanical stress is applied to the target surface during the cleaning process, making it particularly suitable for cleaning fragile, sensitive, or high-value materials. For example, laser cleaning can clean sensitive materials such as cultural relics and artworks without damaging their surface structure. In addition, when cleaning industrial equipment, wear caused by physical friction is avoided, extending the service life of the equipment.
Laser cleaning is rapidly becoming the tool of choice for modern industrial and technical cleaning due to its precision, efficiency, environmental friendliness, versatility, and non-contact advantages. These features not only meet the stringent requirements of different industries but also provide new ways for sustainable development and high-quality production.
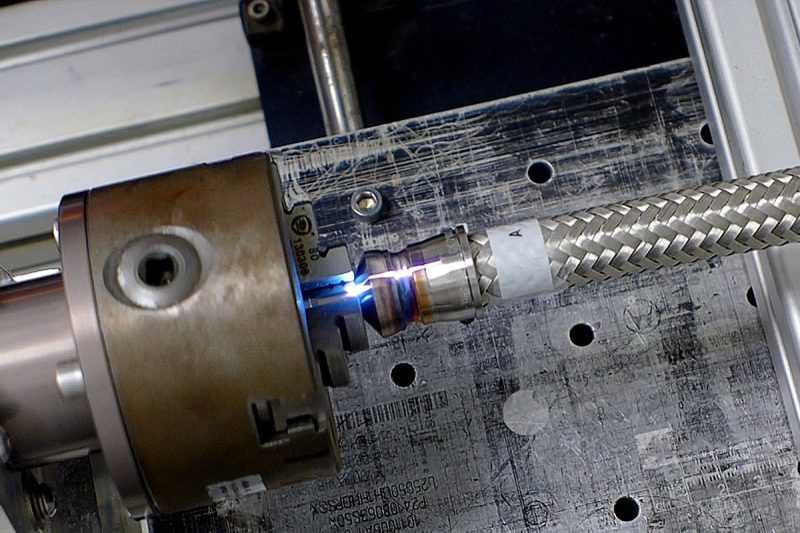
Will Laser Cleaning Damage Sensitive Materials?
Laser cleaning technology does provide the possibility of cleaning a variety of sensitive materials, but great caution is required when handling these materials. The cleaning effect and whether sensitive materials will be damaged mainly depends on the combination of several key factors:
The Characteristics of the Material Itself
The cleaning requirements of sensitive materials depend first on the physical and chemical properties of the material itself. For example, heat-sensitive materials such as synthetic materials, plastics, and rubber may melt, deform, or fade due to the heat accumulation of the laser. At the same time, historical artifacts such as ancient artifacts, paper archives, or delicate works of art are also easily affected by the heat or vibration generated during the laser cleaning process due to their aging and fragile characteristics. For these materials, the laser parameters must be set very accurately to ensure that contaminants are removed without damaging the material itself.
Complexity of Surface Morphology
Some materials have very complex microstructures or engravings on their surfaces, such as micron-scale lines in precision electronic components, engraved artwork, or high-precision mechanical parts. The complexity of these materials means that they are extremely sensitive to the energy and pulses of the laser. Excessive energy can cause damage or deformation of the microstructure, especially in applications that require surface texture and functional integrity. To avoid damage, the laser power, pulse duration, and focus position must be carefully adjusted to ensure that the laser only acts on contaminants or impurities without affecting the underlying material.
Precise Control of Laser Parameters
The key to laser cleaning is the precise control of parameters, including the wavelength, pulse duration, frequency, and power output of the laser. Appropriate parameter settings are crucial for different materials. Too high a power may cause melting or ablation of the material surface, and too long a pulse duration may cause heat accumulation and negatively affect the material structure. The choice of wavelength is closely related to the absorption characteristics of the material. If the material absorbs laser light of a specific wavelength too strongly, thermal damage may occur. Therefore, when cleaning sensitive materials, operators need to optimize the laser parameters through experiments or technical means to find the ideal settings that can effectively remove contaminants without damaging the material.
Impact of Cleaning Environment
The effect of laser cleaning is also closely related to the environmental conditions of the operation, especially when cleaning high-precision or sensitive materials. Ambient temperature, humidity, and impurities in the air can all have an impact on the cleaning process. For example, higher ambient temperatures may exacerbate thermal expansion or thermal damage to the material, while excessive humidity may change the absorption characteristics of the material surface. In addition, airflow during the cleaning process also needs to be controlled to prevent smoke and particles generated by the laser from re-contaminating the cleaning area.
In short, although laser cleaning is an efficient and environmentally friendly cleaning technology, material properties, surface morphology, laser parameters, and environmental conditions must be fully analyzed and adjusted when processing sensitive materials. By adopting appropriate technical measures, laser cleaning can effectively remove surface impurities while maintaining material integrity and provide ideal cleaning effects.
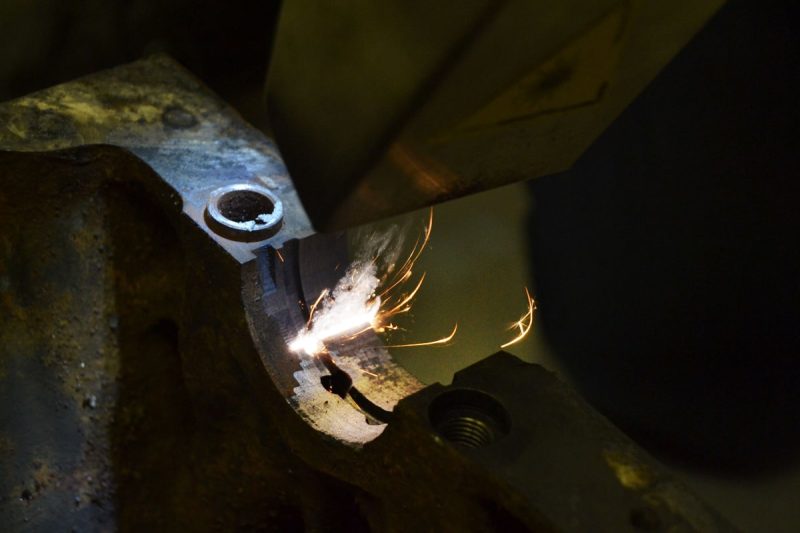
Factors Affecting Suitability of Sensitive Materials
When deciding whether a sensitive material is suitable for laser cleaning, multiple factors need to be fully analyzed to ensure that the material itself is not damaged while being cleaned. The following is a detailed description of several key factors that affect the suitability of laser cleaning for sensitive materials:
Material Composition
The composition of a material directly determines its response to laser energy. Different materials have different absorption and reflection characteristics for specific wavelengths of laser light. For example, metal materials generally have higher absorption rates for shorter wavelength laser light, which makes it easy to remove surface contaminants during laser cleaning. However, some ceramics and organic materials, such as plastics and composites, may have weaker absorption of laser light, more reflection, and higher heat sensitivity, so they are prone to deformation, ablation, or fading under the action of laser light.
In addition, the thermal expansion coefficient and thermal conductivity of the material are also important considerations. Materials with larger thermal expansion coefficients are prone to cracking or surface peeling due to thermal stress during laser cleaning, while materials with lower thermal conductivity may cause local overheating due to laser energy concentration, thereby damaging the material structure. Therefore, understanding the characteristics of the material composition and reasonably selecting laser parameters are key to ensuring that laser cleaning is suitable for sensitive materials.
Laser Parameter Setting
The effect of laser cleaning and the adaptability of materials depends largely on the setting of laser parameters, including the wavelength, pulse energy, frequency, and duration of the laser. Different materials have different absorption capabilities for lasers of different wavelengths. For example, some plastics or organic materials may absorb too much near-infrared lasers, resulting in surface damage, so it is necessary to select a suitable laser wavelength to avoid overheating.
In addition, the setting of pulse energy needs to be particularly cautious. For sensitive materials, too high pulse energy may cause melting or mechanical stress accumulation on the surface of the material, while too long pulse duration may cause heat accumulation and eventually cause thermal damage to the material. Lower pulse frequencies are generally more suitable for cleaning fragile or heat-sensitive materials because they allow the material to have enough time to dissipate heat after each pulse, thereby reducing the risk of damage. Therefore, when processing sensitive materials, it is crucial to accurately adjust these laser parameters to ensure a balance between cleaning effect and material safety.
Material Surface Treatment and Condition
The surface characteristics of materials have a significant impact on the effectiveness and safety of laser cleaning. The presence of coatings, oxides, or other pre-treatment layers on the material surface is an important factor in determining the laser absorption rate. For example, the oxide layer on the metal surface can usually effectively absorb the laser energy, making it easier to remove. However, if the coating is too thin or too fragile, laser cleaning may damage the substrate.
In addition, the roughness of the surface is also an influencing factor. Rough surfaces will cause uneven distribution of laser energy, which may cause local overheating in certain areas. The type, thickness, and uniformity of contaminants must also be considered. Different types of contaminants (such as grease, rust, paint, etc.) have different absorption characteristics for lasers and may require different cleaning strategies. To ensure that sensitive materials are not damaged, their surface conditions must be carefully analyzed and the cleaning parameters adjusted according to actual needs.
Laser Delivery Systems and Controls
A high-precision laser transmission system is another key factor in ensuring that sensitive materials are cleaned without errors or damage. The quality, focusing accuracy, and energy distribution of the laser beam must be highly consistent to ensure the stability of the cleaning process. Any deviation, scattering, or uneven distribution of the laser beam may lead to uneven cleaning and damage to the material.
Modern laser cleaning systems are equipped with advanced optical transmission and control technologies, which can monitor and adjust the laser parameters during the cleaning process in real-time. For example, through the feedback control system, the operator can adjust the output power of the laser in real-time according to the surface temperature or reflectivity changes of the material to prevent over-cleaning. In addition, the automated system can also be pre-programmed according to the characteristics of different materials to ensure that each cleaning is carried out within a safe range. These high-precision systems greatly reduce the risk of damage to sensitive materials during the cleaning process.
By carefully evaluating these key factors, laser cleaning can achieve the desired results in sensitive material applications while ensuring that the material is not damaged. Operators must develop an appropriate cleaning plan based on each factor to achieve an efficient and safe cleaning process.
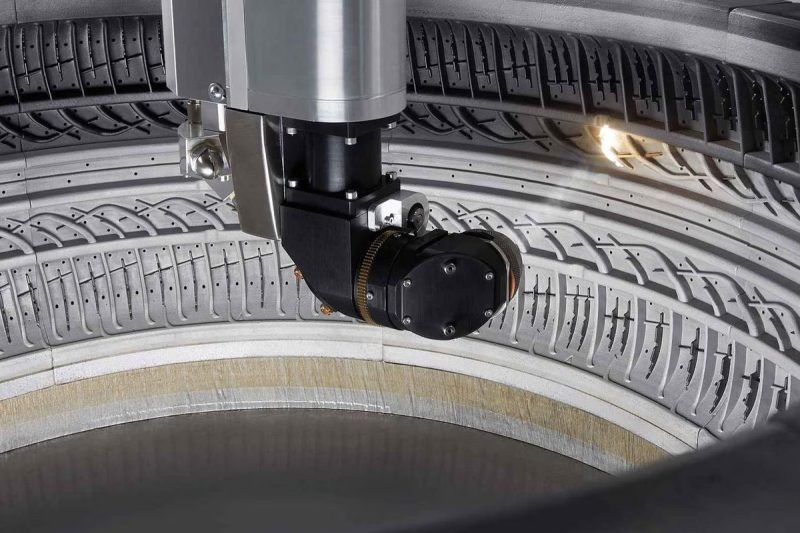
Laser Cleaning of Sensitive Materials
Laser cleaning has become an indispensable tool in many industries due to its high precision and flexibility in processing sensitive materials. The following are some important application areas of laser cleaning technology in sensitive materials:
Art Restoration and Cultural Heritage Protection
Laser cleaning technology is widely used in art restoration and ancient cultural relic protection, especially for some extremely sensitive and irreplaceable cultural relics and artworks. In these applications, traditional chemical or mechanical cleaning methods may cause irreversible damage to the surface of the cultural relic, while laser cleaning can achieve delicate and non-destructive cleaning through non-contact operation and adjustable laser energy. For example, laser cleaning technology is used to remove dirt, soot, lime, or other oxide layers on sculptures, paintings, murals, and buildings. By precisely controlling the wavelength and power of the laser, the cleaning process can remove surface contaminants in a targeted manner without damaging the underlying substrate, ensuring the integrity of the cultural relic and the preservation of its historical value.
Electronics and Semiconductor Manufacturing
In the semiconductor and microelectronics industries, the accuracy of laser cleaning is critical to production quality. The surface of semiconductor wafers is extremely susceptible to dust, grease or other tiny contaminants, which may interfere with the electrical performance of the wafer or even cause device failure. Laser cleaning technology provides an efficient and safe solution for removing contaminants from the wafer surface, and is particularly suitable for handling these ultra-sensitive materials.
Through precise adjustment of laser parameters such as pulse duration, wavelength, and power, operators can remove only contaminants without affecting the integrity of the wafer surface. At the same time, laser cleaning does not require the use of chemical reagents, avoiding the risk of residue or liquid corrosion, and is suitable for operation in environments with extremely high cleanliness requirements. This non-contact cleaning method plays a key role in improving the production efficiency and quality of semiconductor products.
Aerospace
In the aerospace industry, laser cleaning is widely used to maintain and repair key components such as aircraft engine blades, composite structures, and precision metal parts. Since the materials of aerospace equipment usually have complex structures and high-performance requirements, laser cleaning has become an ideal non-destructive maintenance tool.
Laser cleaning technology can effectively remove coatings, corrosion, and other contaminants on the surface of components without affecting the shape, size, or material properties of the components. In engine maintenance, the precise control of the laser during the cleaning process can ensure that the cleaning range is concentrated in the target area and will not spread to the parts that do not need to be treated, ensuring the overall performance and life of the components. At the same time, the high efficiency and environmental protection characteristics of laser cleaning make it an important means to reduce downtime and maintenance costs in the aerospace industry.
Through in-depth understanding and optimized operation of laser cleaning in different application scenarios, the cleaning needs of sensitive materials can be effectively met while ensuring the integrity of product performance and appearance. This makes laser cleaning technology widely used in multiple industries and provides solid support for improving production efficiency and product quality.
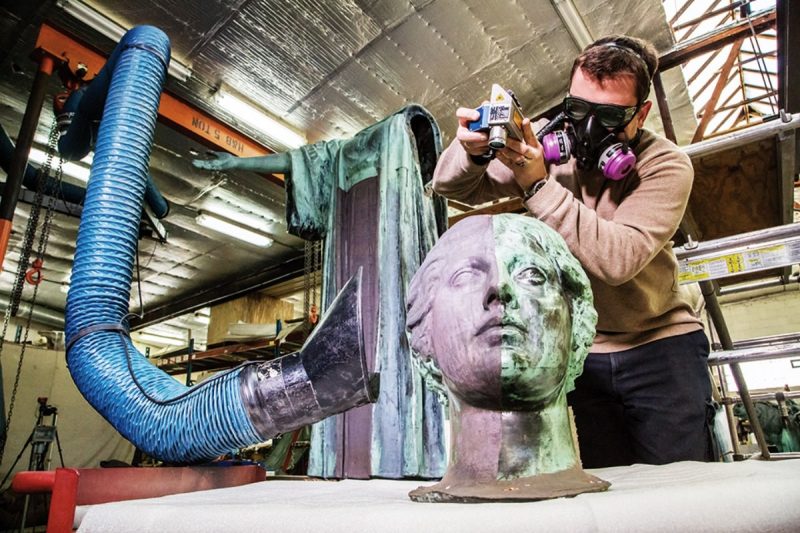
Best Practices for Laser Cleaning Sensitive Materials
When laser cleaning sensitive materials, it is critical to follow a series of best practices to ensure that no damage is caused to the material. The following are specific operating guidelines to help optimize the results of laser cleaning, especially when dealing with sensitive materials:
Material Evaluation
Before laser cleaning can be performed, a detailed assessment of the material’s properties and characteristics is required. Sensitive materials often have specific thermal sensitivities, fragility, or high sensitivity to laser energy. The material’s composition, surface structure, thermal conductivity, expansion coefficient, and absorption characteristics at the laser wavelength should be considered during the assessment. For example, ancient materials, composite materials, or high-precision instruments that may be encountered in cultural relic restoration require rigorous preliminary assessments to determine whether they are suitable for laser cleaning and the key points to focus on during the cleaning process.
Test Cleaning
Before formal cleaning, it is best to perform a test clean on a sample or unimportant area of the material. This small-scale test can provide valuable feedback for subsequent formal cleaning to ensure that the selection of laser parameters (such as power, frequency, and wavelength) will not hurt the material. Test cleaning can also help operators determine the temperature changes during the cleaning process, the efficiency of contaminant removal, and the degree of material response. For example, in art restoration, sample testing can avoid irreversible damage to valuable artifacts and ensure that the laser energy only acts on contaminants and does not damage the substrate.
Parameter Optimization
The success of laser cleaning depends largely on the precise optimization of laser parameters. Depending on the different characteristics of the material, the operator needs to adjust parameters such as the laser power, pulse frequency, duration, and wavelength. For heat-sensitive materials, it is usually necessary to reduce the laser power and pulse energy to reduce heat accumulation. At the same time, choosing the appropriate wavelength ensures that the laser only acts on surface contaminants without overheating the material itself. By gradually adjusting these parameters, the ideal balance point can be found to achieve harmony between cleaning efficiency and material protection. For example, in the semiconductor and electronics industries, optimized laser parameters can remove tiny surface particles without damaging the microstructure.
Use Protection Measures
In some cases, even if the laser parameters are optimized, there is still a risk that the material may be overexposed to the laser. To reduce this risk, additional protective measures can be taken, such as applying a peelable protective layer to the surface of the material. This protective layer can act as a buffer during the laser cleaning process, preventing the laser from directly contacting the substrate, which is particularly suitable for processing special materials such as extremely fragile or historical artifacts. In addition to the protective layer, physical barriers or optical filters can be used to limit the range of the laser, thereby reducing the risk of cleaning sensitive areas.
Monitoring and Control
Real-time monitoring and precise control are key steps to ensure the safety of sensitive materials during laser cleaning. Advanced monitoring equipment (such as infrared temperature sensors, spectrometers, etc.) can track the temperature changes, reflectivity, and energy distribution of the cleaning area in real-time. These data can help operators make necessary adjustments to avoid local overheating or over-cleaning. At the same time, the automated feedback control system can dynamically adjust the laser power or frequency according to the changes monitored in real-time to ensure that the cleaning process is always within a safe range. This high-precision monitoring technology is particularly important in aerospace and high-precision manufacturing.
Post-Cleaning Assessment
After cleaning is complete, a comprehensive quality assessment of the material is an important step to verify cleaning results and material safety. The assessment should include physical and chemical analysis of the material surface to ensure that contaminants are completely removed while detecting any possible damage or deformation. For some demanding industries such as electronics, medical and art restoration, the post-cleaning assessment may even include microscopic inspection, surface hardness testing or surface morphology analysis. If any potential problems are found, the cleaning process can be further optimized to avoid similar problems in future operations.
Through these best practices, operators can effectively reduce the risks of laser cleaning when handling sensitive materials and ensure optimal cleaning results. Accurate material assessment, precise laser parameter control, and the application of full-process monitoring and protection measures are all key to ensuring a safe and effective cleaning process. This systematic cleaning strategy not only improves cleaning efficiency, but also maximizes the protection of material integrity and functionality, and is widely used in cultural relics protection, semiconductor manufacturing, precision engineering, and other fields.
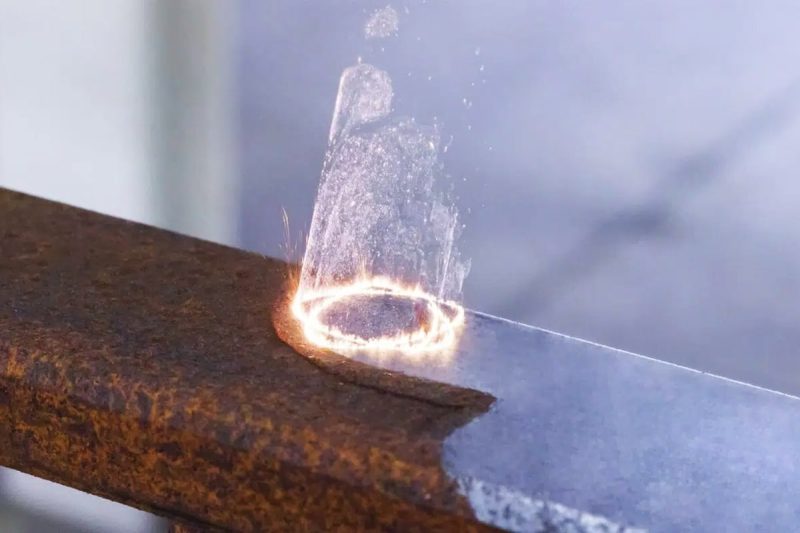
Summarize
Laser cleaning technology has demonstrated excellent application capabilities in many industries with its efficient and non-contact working principle, especially in the treatment of sensitive materials, it provides a highly precise cleaning solution. This technology has played an important role in the fields of cultural relics restoration, semiconductor manufacturing, precision machinery, and aerospace, not only effectively removing contaminants, but also minimizing the physical damage or chemical corrosion caused by traditional cleaning methods.
However, whether laser cleaning will cause damage to sensitive materials depends on multiple factors. First, the characteristics of the material are key, including the composition, thermal sensitivity, surface structure, and absorption and reflection ability of the laser energy. Different materials show different responses during the cleaning process, and some materials may be damaged due to heat accumulation or mechanical stress. Therefore, when choosing laser cleaning, the characteristics of the material must be fully analyzed and evaluated.
Secondly, the selection of laser parameters is crucial to the cleaning effect and material safety. The wavelength, power, pulse frequency, and action time of the laser will affect the interaction between the laser and the material. For sensitive materials, the operator needs to accurately adjust these parameters according to the specific situation to ensure uniform energy distribution during the cleaning process and avoid local overheating or excessive cleaning. Scientific and reasonable parameter control can ensure that the integrity of the material is not affected while removing surface contaminants.
The operating environment and conditions are another key factor in determining the effectiveness of laser cleaning. High-precision optical transmission systems, real-time monitoring and feedback technology, and the application of protective measures all help to improve the safety and effectiveness of laser cleaning. By monitoring the entire cleaning process, operators can adjust the laser energy and range of action at any time to avoid unnecessary damage.
To ensure the safety of cleaning sensitive materials, it is essential to follow a series of best practices. Comprehensive material evaluation is the basis, and sample test cleaning should be performed to optimize laser parameters before cleaning officially begins. In addition, protective layers or barriers can be used when necessary to reduce the direct impact of the laser on the material. During the cleaning process, advanced monitoring equipment and control systems can effectively avoid operating errors or energy overloads to ensure a safe and reliable cleaning process. After cleaning is completed, a detailed quality assessment of the material is required to verify the cleaning effect and confirm that no irreversible damage has occurred.
In short, through scientific evaluation and practice, laser cleaning technology can provide ideal cleaning results while maintaining the integrity of sensitive materials. This makes laser cleaning an irreplaceable solution in many industries, not only improving work efficiency but also effectively reducing the risk of material damage.
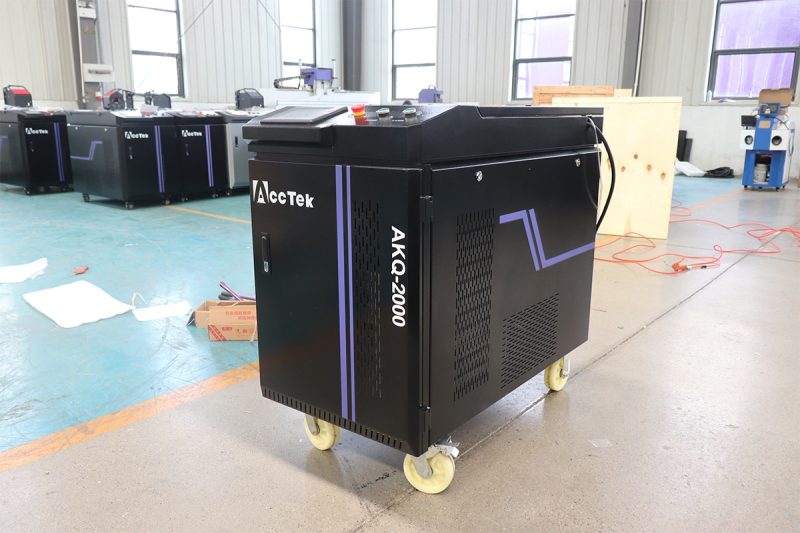
Get Laser Solutions
Choosing the right laser cleaning machine is the key to improving cleaning results and protecting materials. When working with a reliable partner, you can get advanced technical support, professional solutions, and continuous service. At AccTek Laser, we offer a wide range of laser cleaning equipment for all types of industrial cleaning needs. Our experts will help you optimize cleaning parameters to ensure efficient and safe cleaning results and maximize production efficiency. We also provide advanced features such as precise energy control and intelligent monitoring systems to ensure the stability and accuracy of the cleaning process. In addition, our technical team provides comprehensive support services to ensure that your equipment is always in optimal operating condition. By working with AccTek Laser, you will get efficient and non-destructive cleaning results, reduce operational risks, and improve production quality. Contact us now to learn more about our innovative cleaning solutions to help your business grow.
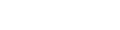
Contact information
- [email protected]
- [email protected]
- +86-19963414011
- No. 3 Zone A, Lunzhen Industrial Zone,Yucheng City , Shandong Province.
Get Laser Solutions