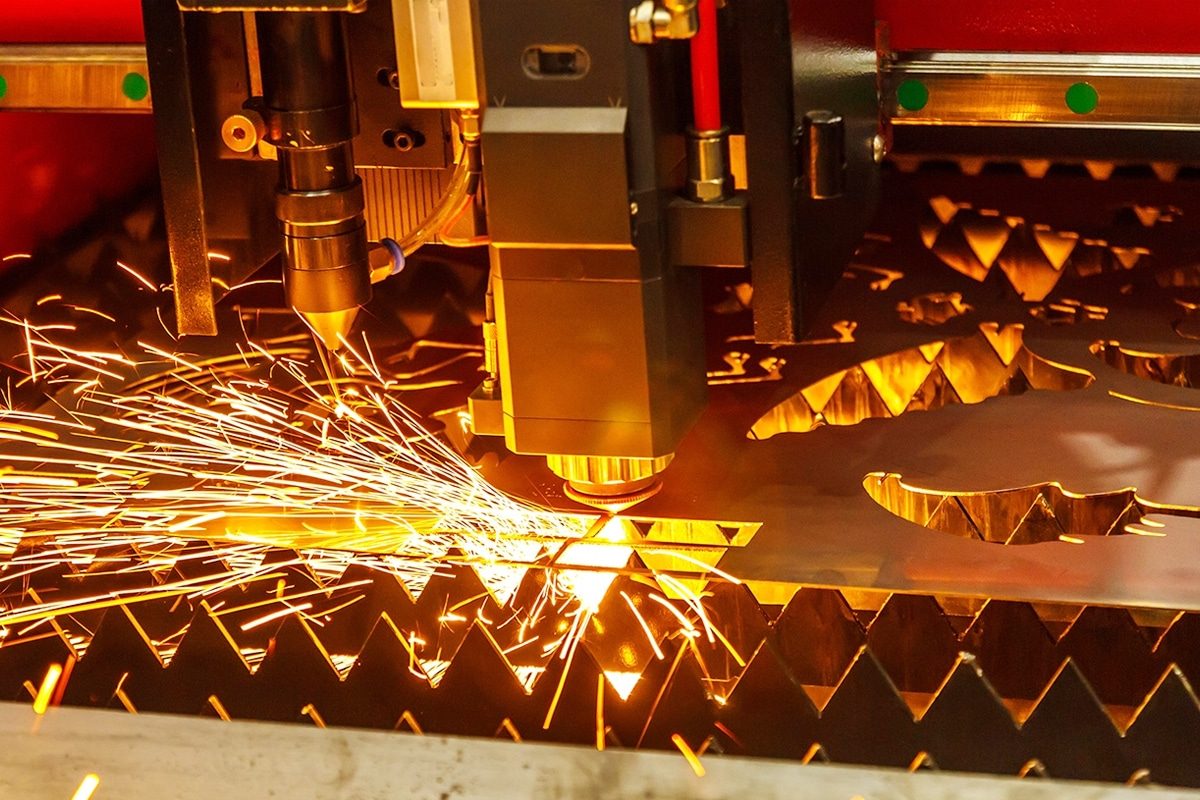
Choosing The Right Fiber Laser Cutting Machine: Comprehensive Guide
Choosing a fiber laser cutting machine in the manufacturing industry is a critical decision for companies aiming to improve production processes and precision. Fiber laser technology has become a transformative force, offering unparalleled capabilities to cut a wide range of materials with extreme speed and precision.
The decision to invest in a fiber laser cutting machine depends on several key factors. Understanding specific requirements, such as the type and thickness of material to be processed, the required cutting speed, and production volume is essential. In addition, considerations such as budget constraints and long-term operating costs play a key role in selecting the best machine configuration.
This comprehensive guide aims to demystify selecting the right fiber laser cutting machine. By exploring key technical specifications, industry applications, and strategic decision criteria, companies can confidently navigate the complexities of this technological landscape, ensuring their investment is perfectly aligned with operational needs and growth goals.
Table of Contents
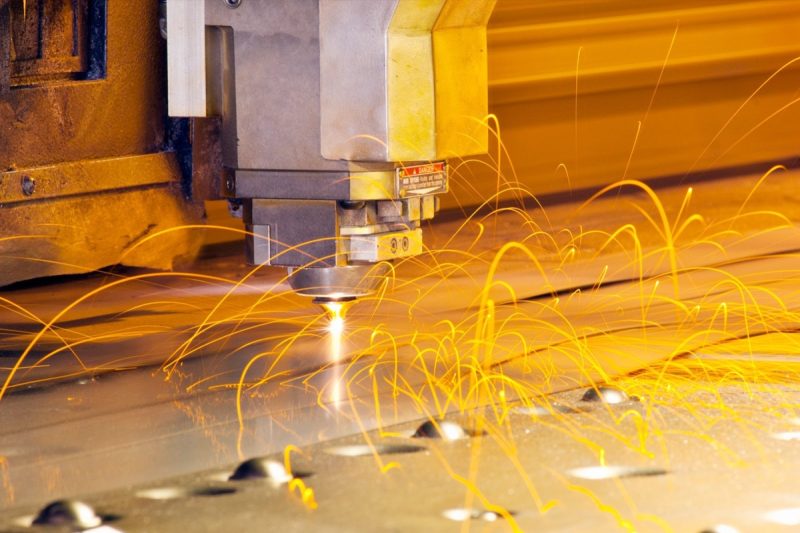
Understanding Fiber Laser Cutting Technology
What Is Fiber Laser Cutting
Fiber laser cutting technology utilizes a high-power laser beam generated within an optical fiber that is doped with rare earth elements such as erbium, ytterbium, or neodymium. This setup enables the laser to achieve high energy density, making it very efficient at cutting a wide range of materials.
Fiber laser generators work on the principle of stimulated emission of radiation within the optical fiber, producing a concentrated beam that can be precisely controlled and focused onto the workpiece. Fiber lasers cut significantly faster and more energy efficiently than conventional CO2 lasers.
Key Components of a Fiber Laser Cutting Machine
- Laser Source: The heart of the system is typically the fiber laser oscillator that produces the laser beam. Common brands include IPG Photonics, Raycus, and Maxphotonics, offering a variety of power outputs (ranging from 1 kW to 60 kW and above) to meet different cutting requirements.
- Cutting Head and Optics: Includes the focusing lens and nozzle through which the laser beam passes. Advanced cutting heads feature autofocus and capacitive height sensing for optimal cutting results.
- Control System: manages the operation of the machine, controlling parameters such as power output, cutting speed, and axis motion. Software platforms such as FSCUT and CypCut provide user-friendly interfaces and CAD/CAM integration to achieve precise cutting paths.
- Motion System: uses servo motors and high-precision linear guides to accurately move the cutting head along the programmed path. This ensures consistent cutting quality and positional accuracy.
- Cooling System: maintains the optimal operating temperature of the laser generator and other key components. Common cooling methods include water chillers or air cooling systems, depending on the design and power requirements of the machine.
Understanding these components can help evaluate the functions and performance of different fiber laser cutting machines. The quality and configuration of each component can significantly affect the overall efficiency of the machine, cutting accuracy, and suitability for specific industrial applications.
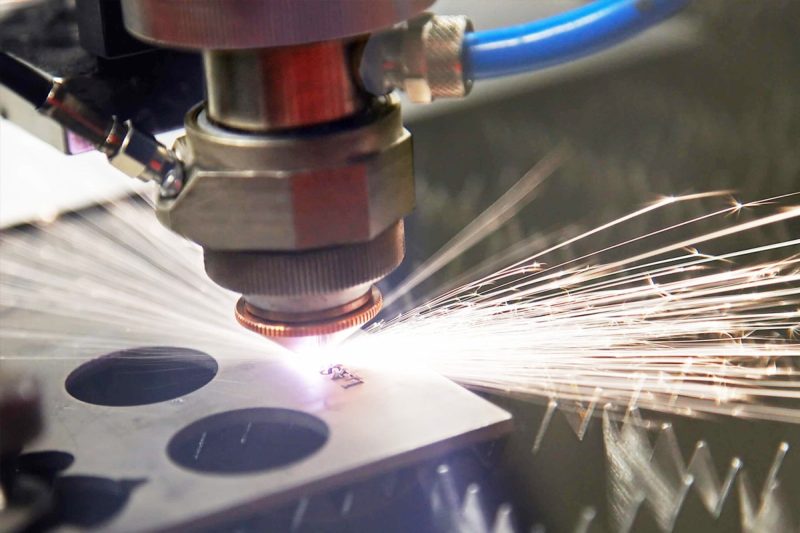
Identify Your Needs and Requirements
Choosing the right fiber laser cutting machine starts with a thorough assessment of your specific operational needs and production requirements. Consider the following key factors to make an informed decision:
Material Considerations
- Material Type: Identify the materials you primarily work with, such as stainless steel, aluminum, copper, brass, and titanium. Make sure the machine you choose can efficiently cut the materials you want and their varying thicknesses.
- Material Thickness: Evaluate the range of thicknesses you typically need to cut. Different fiber laser cutting machines have different capabilities, and higher-powered machines can generally handle thicker materials more effectively.
Production and Throughput
- Production Volume: Determine your expected production volume, whether it is small batches, batch production, or continuous high-volume production. This factor affects the machine’s duty cycle requirements and its ability to meet your throughput needs.
- Cutting Speed: Consider the cutting speed required to meet your production schedule. Higher-power laser generators and advanced cutting heads can significantly increase cutting speeds, optimizing overall efficiency.
Precision and Speed
- Cutting Precision: Define the level of precision required for your application. Factors such as laser power, cutting head stability, and motion system accuracy contribute to precise cuts with clean edges.
- Cutting Speedvs Precision: The balance between cutting speed and precision depends on the needs of your operation. Faster cutting speeds can increase productivity, but not at the expense of precision on complex designs or delicate materials.
Budget and Long-Term Investment
- Initial Investment Cost: Consider your budget constraints and the initial cost of purchasing a fiber laser cutting machine. Consider not only the upfront purchase cost but also installation fees and any necessary infrastructure upgrades.
- Operational Cost: Evaluate ongoing operating costs, including power consumption, maintenance requirements, and consumables such as assist gases and replacement parts.
- Return on Investment (ROI): Calculate potential ROI based on increased productivity, reduced material waste, and improved cut quality. A higher initial investment in a quality machine may result in greater long-term savings and productivity gains.
By thoroughly evaluating these factors, you can align the specifications and capabilities of a fiber laser cutting machine with your specific operational requirements and business goals. This strategic approach ensures that your investment in laser-cutting technology maximizes efficiency, quality, and profitability over the life of the machine.
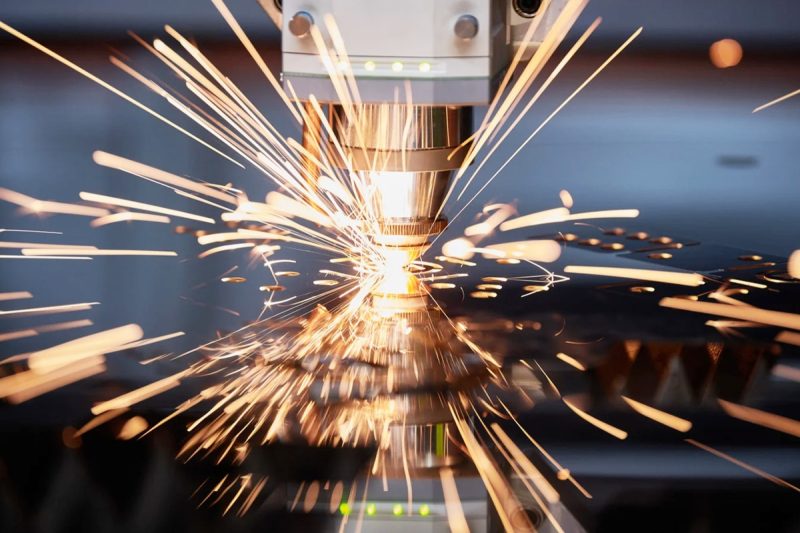
Understand Laser Cutting Machine Configurations
Choosing the right configuration for your fiber laser cutting machine can help optimize performance and achieve desired results. Here’s a comprehensive overview of key configurations and their implications:
Open Body and Closed Body Designs
- Open Body: Provides accessibility from all sides, facilitating ease of material loading and adjustments. Suitable for applications requiring frequent changes in material types or sizes.
- Closed Body: Encloses the cutting area for enhanced safety, environmental control, and noise reduction. Ideal for operations with strict cleanliness standards or automated production environments.
Cutting Head Options
- Manual Focus Laser Cutting Head: Requires manual adjustment of the focus lens to optimize cutting quality for different material thicknesses. Offers simplicity and cost-effectiveness for basic cutting tasks.
- Automatic Focus Laser Cutting Head: Automatically adjusts the focus position based on material thickness and cutting parameters. Enhances cutting precision and efficiency, reducing setup time and operator intervention.
- 3D Laser Cutting Head: Enables cutting of materials with irregular or angled surfaces. Ideal for applications requiring complex shapes and contours, such as automotive components and architectural models.
Laser Power
- Determines cutting capabilities, including maximum thickness and cutting speed. Higher power levels accommodate thicker materials and increase cutting speed, suitable for heavy-duty industrial applications.
Laser Generator Brand
- IPG Photonics: Known for reliability, high efficiency, and advanced fiber laser technology.
- MAX Photonics: Offers a wide range of power options with robust performance and cost-effectiveness.
- Raycus: Provides versatile laser sources with competitive pricing and widespread availability.
- JPT (Jiangsu Precise): Specializes in high-performance fiber lasers for precision cutting and marking applications.
- BWT (Beijing BWT): Known for innovative laser solutions with an emphasis on quality and technical support.
Exchange Worktable
- Enables continuous operation by alternating between multiple worktables. Reduces downtime for material handling and improves overall productivity.
Rotary Axis
- Essential for cutting cylindrical or tubular materials. Allows for 360-degree cutting, ideal for industries such as automotive, aerospace, and manufacturing of pipes or structural components.
Cooling Systems
- Air Cooling: Utilizes air to dissipate heat from the laser source and other components. Suitable for smaller machines or environments where water availability is limited.
- Water Cooling: Use water circulation to maintain the optimal temperature level of laser components. Water cooling provides excellent cooling efficiency and can ensure the continuous operation of high-power laser systems.
Control Systems
- Manages machine operations, including cutting parameters, motion control, and integration with CAD/CAM software. Enhances precision, flexibility, and ease of use with intuitive interfaces like FSCUT or CypCut.
Understanding these laser-cutting machine configurations empowers you to make informed decisions based on your specific application requirements, production demands, and long-term operational goals. Each configuration offers unique benefits, ensuring you can optimize efficiency, precision, and profitability in your manufacturing processes.
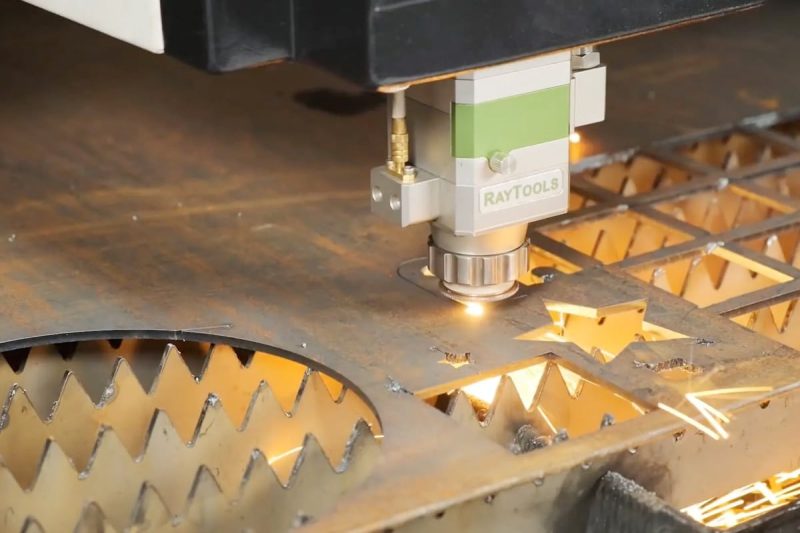
Industry and Application-Specific Considerations
When selecting a fiber laser cutting machine, it is critical to understand industry-specific requirements to ensure optimal performance and productivity. Here is a detailed exploration of each industry and application:
Automotive and Aerospace
- Precision Cutting Requirements: The automotive and aerospace industries place high demands on precision for complex parts and components. Fiber laser cutting machines with advanced cutting heads and precise control systems are essential.
- Material Diversity: Cutting a range of materials such as aluminum, stainless steel, and titanium alloys requires machines with versatile capabilities and powerful laser power options. 3D laser cutting capabilities for complex geometries in turbine blades, aircraft components, and automotive frames.
- Production Volume: High-volume production and rapid prototyping capabilities are essential. Machines with efficient swap tables and fast cutting speeds increase productivity in these dynamic fields.
Signage and Advertising
- Versatile Cutting Capabilities: From acrylics to metals, the signage and advertising industries require machines that can accurately handle a wide range of materials and deliver a high-quality finish.
- Complex Designs: The ability to cut complex patterns and designs can help create impactful signage and decorative elements. Machines equipped with 3D cutting heads or advanced software integration offer creative flexibility.
- Speedand Throughput: High cutting speeds and swap tables optimize production for signage companies that handle high-volume orders.
Metalworking
- Thickness and Speed Requirements: Metalworking relies on machines that can effectively handle varying thicknesses of steel, aluminum, and other metals. High-powered lasers and powerful cooling systems are beneficial.
- Cutting Accuracy: Maintaining tight tolerances and clean edges is critical. Machines equipped with autofocus cutting heads and reliable motion control systems ensure consistent cut quality.
Education and Prototyping
- User-Friendly Operation: Educational environments and prototyping labs benefit from machines with intuitive CNC control systems and easy-to-learn software interfaces.
- Versatility and Learning Opportunities: Machines that support a wide range of materials and cutting capabilities provide students with valuable hands-on experience and facilitate rapid prototyping of new designs.
Medical and Electronics
- Precision and Cleanliness: Cutting materials for medical devices and electronics requires high cleanliness standards and minimal heat-affected zones. Fiber lasers that can precisely control cutting parameters excel in these applications.
- Material Compatibility: Machines suitable for the medical and electronics manufacturing industries need to be able to cut thin metals with only minimal deformation.
Understanding these industry-specific considerations can help select a fiber laser cutting machine that meets special requirements, increases productivity, and ensures high-quality output tailored to specific applications. Evaluate your operational needs and the unique demands of your industry to make an informed decision and maximize the benefits of laser-cutting technology for your business.
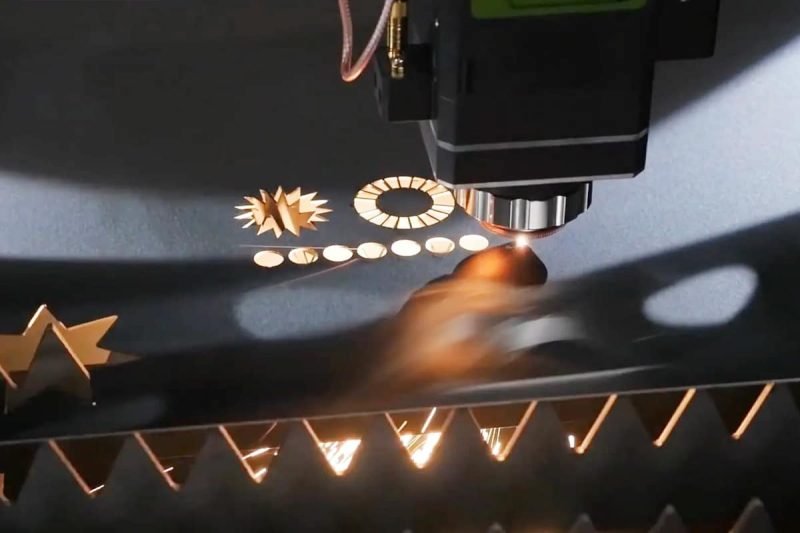
Research and Compare Options
When selecting a fiber laser cutting machine, conducting thorough research and comparison is crucial to making an informed decision. Here are key aspects to consider:
Technology Trends
- Advancements in Fiber Laser Technology: Stay updated on the latest developments in fiber laser cutting technology, such as improvements in laser sources, cutting speeds, and automation capabilities. Trends towards higher power outputs (e.g., 30 kW to 60 kW) for faster cutting speeds and increased material thickness capabilities.
- Innovative Features: Look for innovations like automatic focus cutting heads, 3D cutting capabilities, and integrated CAD/CAM software solutions that enhance operational efficiency and cutting precision.
Customer Reviews
- User Experiences and Feedback: Read customer reviews and testimonials to understand real-world experiences with different machine models and manufacturers. Focus on reviews that discuss reliability, performance, after-sales support, and overall satisfaction.
- Case Studies and Applications: Explore case studies from industries similar to yours to see how specific machines perform in practical applications. Look for success stories that highlight machine capabilities, ROI, and operational benefits achieved.
Manufacturer Reputation
- Industry Experience and Expertise: Evaluate the manufacturer’s background, industry experience, and specialization in fiber laser cutting technology. Established manufacturers with a proven track record often provide more reliable products and comprehensive support.
- Service and Support: Assess the manufacturer’s service network, availability of spare parts, and technical support capabilities. Reliable after-sales service ensures minimal downtime and effective resolution of technical issues.
- Warranty and Maintenance Programs: Review warranty terms, maintenance programs, and upgrade options offered by manufacturers. Comprehensive warranty coverage and proactive maintenance can extend machine lifespan and reduce long-term operational costs.
By researching technology trends, customer reviews, and manufacturer reputation, you can compare different fiber laser cutting machine options effectively. This approach enables you to identify the machine model that best aligns with your specific operational requirements, budget constraints, and long-term business goals.
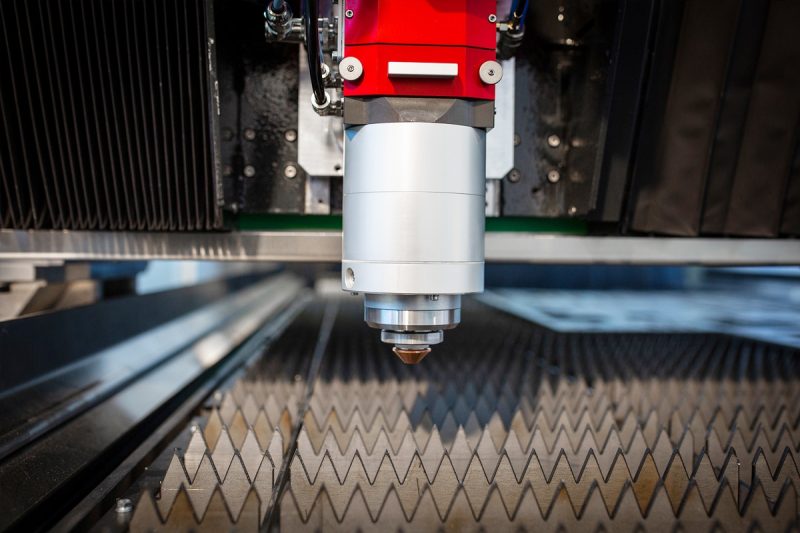
Evaluate Support and Services
When choosing a fiber laser cutting machine, evaluating the available support and services can ensure smooth operation and maximum uptime. Consider the following:
Technical Support
- Availability and Responsiveness: Evaluate the manufacturer’s reputation for technical support. Look for fast response times and 24/7 availability, especially if your operation runs continuously.
- Expertise and Training: Determine if the manufacturer offers training programs for machine operators and maintenance personnel. Training should cover machine operation, troubleshooting, and basic maintenance to optimize machine performance and minimize downtime.
- Remote Assistance: Check if remote diagnostics and troubleshooting are offered. Remote support can speed up problem resolution and reduce downtime by providing immediate technical assistance.
Warranty and Maintenance
- Warranty Coverage: Check the warranty terms and coverage offered by the manufacturer. Understand the components and types of damage covered by the warranty, as well as any exclusions or conditions that may apply.
- Regular Maintenance Schedule: Ask about the manufacturer’s regular maintenance schedule. Regular maintenance helps prevent unexpected breakdowns, extend the life of the machine, and ensure consistent cutting performance.
- Spare Parts Availability: Ensure the availability of genuine spare parts and consumables relevant to your laser cutting machine Timely availability of parts minimizes downtime and reduces the impact on production schedules.
- Service Contracts: Consider optional service contracts offered by the manufacturer or authorized dealers. These contracts may include scheduled maintenance, priority service, and discounted pricing on parts and labor.
User Communities and Resources
- Online Resources: Check out the online forums, knowledge bases, and user communities relevant to your laser-cutting machine model. These resources can provide valuable insights, troubleshooting tips, and best practices shared by other users.
- Customer Feedback: Consider feedback from existing customers on their experience with support services, including reliability, effectiveness of solutions, and overall satisfaction.
Long-Term Partnerships
- VendorReputation: Consider the manufacturer’s reputation for reliability, longevity in the industry, and commitment to customer satisfaction. Long-standing manufacturers with a proven track record typically provide better support and continually improve their products and services.
- Feedback Mechanisms: Determine if the manufacturer valuescustomer feedback and uses it to enhance its support services and product offerings. Partnering with a manufacturer that listens to its customers can result in better-customized solutions and a better overall experience.
Local Service Network
- Distance to Service Center: Evaluate the distance and accessibility of authorized service centers or technicians. Local support reduces response time for on-site repairs and improves overall service efficiency.
- Emergency Support and Spare Parts Inventory: In the event of unexpected failures or breakdowns, ask about emergency support options and the availability of critical spare parts. A well-equipped service network ensures minimal disruption to production operations.
By fully evaluating technical support capabilities, warranty terms, and maintenance services, you can choose a fiber laser cutting machine that not only meets your production needs but also ensures continuous support and reliability throughout its service life. This proactive approach helps reduce risk and improve the efficiency of manufacturing operations.
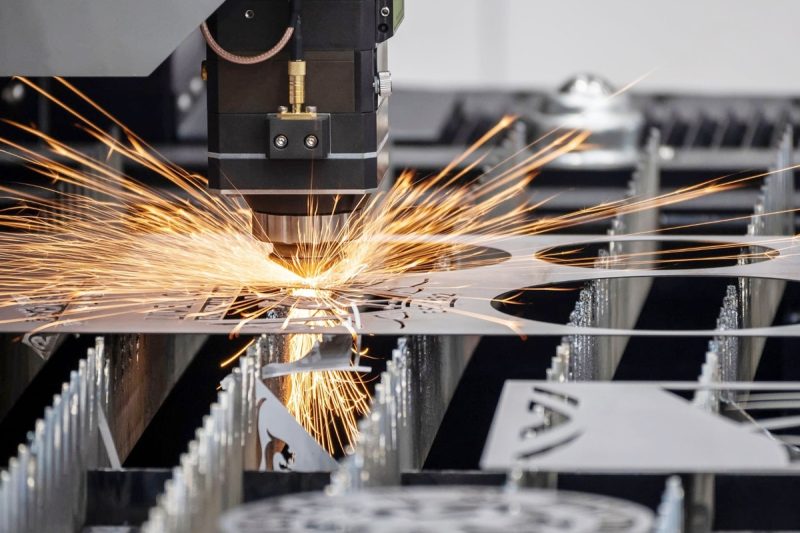
Make A Decision
Choosing the right fiber laser cutting machine requires synthesizing all the information gathered to make a decision that aligns with your business goals and operational requirements. Here is a structured approach to guide your decision-making process:
Decision Framework
- Define Priorities: Prioritize key factors such as cutting speed, accuracy, material compatibility, and budget constraints based on your specific application requirements.
- Technical Specifications: Compare machine features (laser power, cutting head options, table configuration) to your production needs and material processing requirements.
- ROI Analysis: Perform a comprehensive cost-benefit analysis, considering initial investment, operating costs (energy consumption, maintenance), and potential productivity gains.
Consulting
- Manufacturer Consulting: Work with the manufacturer or authorized distributor to discuss technical specifications, customization options, and potential challenges specific to your application.
- Industry Peers and Experts: Seek advice from industry peers or consultants who have experience with similar laser-cutting applications. Their insights can provide practical perspectives and highlight considerations you may have overlooked.
Final Considerations
- Long-term Viability: Evaluate the machine’s scalability and its compatibility with future business expansion plans. Consider technological advances and the machine’s adaptability to evolving industry standards.
- Support and Service Agreements: Review the warranty terms, maintenance agreements, and technical support capabilities offered by the manufacturer. Make sure they meet your expectations for responsiveness, expertise, and spare parts availability.
- User Feedback and Reviews: Consider feedback from current users on the machine’s reliability, performance under real-world conditions, and overall satisfaction with after-sales support.
- Risk Mitigation Strategies: Identify potential risks associated with the investment and develop mitigation strategies to address unforeseen challenges or disruptions to operations.
- Decision Timeline: Establish a timeline for the final decision, considering procurement lead times, installation requirements, and any training required for operators.
By following a systematic decision framework, consulting with stakeholders, and considering the final factors, you can confidently select the right fiber laser cutting machine to enhance your manufacturing capabilities, support business growth, and provide a favorable return on investment. This strategic approach ensures your investments are aligned with long-term operational goals and position your business competitively in the marketplace.
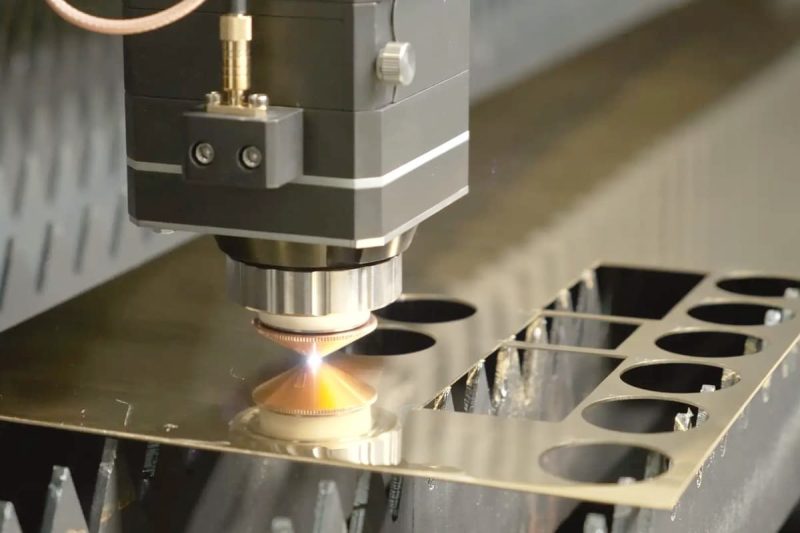
Summary
Choosing the right fiber laser cutting machine requires a meticulous evaluation of various factors to ensure it aligns with your business objectives and operational needs. Begin by defining your material requirements, production volumes, and desired cutting precision. Consider the specific configurations such as open or closed body designs, cutting head options, laser power, and control systems that best suit your application. Industry-specific considerations, from automotive and aerospace to signage and medical, further refine your selection criteria.
Research extensively, comparing technological advancements, customer reviews, and manufacturer reputations to gauge reliability and support. Evaluate technical support availability, warranty coverage, and maintenance services to minimize downtime and maximize machine uptime. Ultimately, your decision should be guided by a comprehensive understanding of the machine’s capabilities, its fit with future growth plans, and its ability to deliver consistent performance over the long term. By following this guide, you can confidently invest in a fiber laser cutting machine that enhances efficiency, precision, and competitiveness in your manufacturing operations.
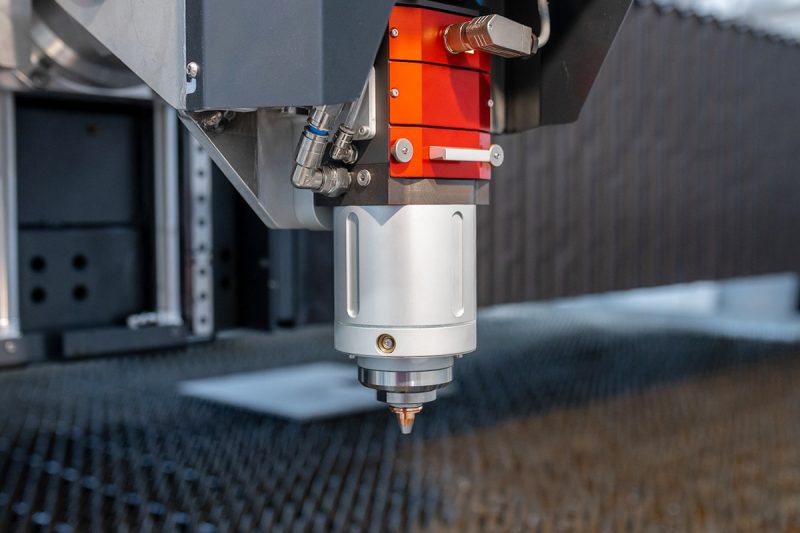
Get Laser Cutting Solutions
AccTek Laser offers a comprehensive range of fiber laser cutting machines designed to meet diverse industrial needs with precision and efficiency. Whether you are in automotive, aerospace, signage, metal fabrication, or other industries, we provide tailored solutions to enhance your manufacturing capabilities.
- Customization Options: AccTek Laser machines offer flexibility in configuration, including various laser powers (from 1kw to 60kw), cutting head options (manual focus, automatic focus, 3D), and worktable designs (exchange table, rotary axis) to suit specific applications.
- Advanced Technology: Benefit from cutting-edge fiber laser technology that ensures high-speed cutting, exceptional accuracy, and versatility across a wide range of materials metals (steel, aluminum, stainless steel).
- Support and Services: AccTek Laser provides reliable technical support, comprehensive warranty coverage, and maintenance services to minimize downtime and optimize machine performance. Our commitment extends to training programs and resources to empower your team in maximizing operational efficiency.
- Consultation and Demo: Contact AccTek Laser for expert consultation and schedule a demo to experience firsthand how our fiber laser cutting machines can elevate your production capabilities and meet your specific business requirements.
Choose AccTek Laser for cutting-edge technology, reliable performance, and dedicated support in advancing your manufacturing operations with precision laser cutting solutions.
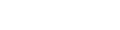
Contact information
- [email protected]
- [email protected]
- +86-19963414011
- No. 3 Zone A, Lunzhen Industrial Zone,Yucheng City , Shandong Province.
Get Laser Solutions