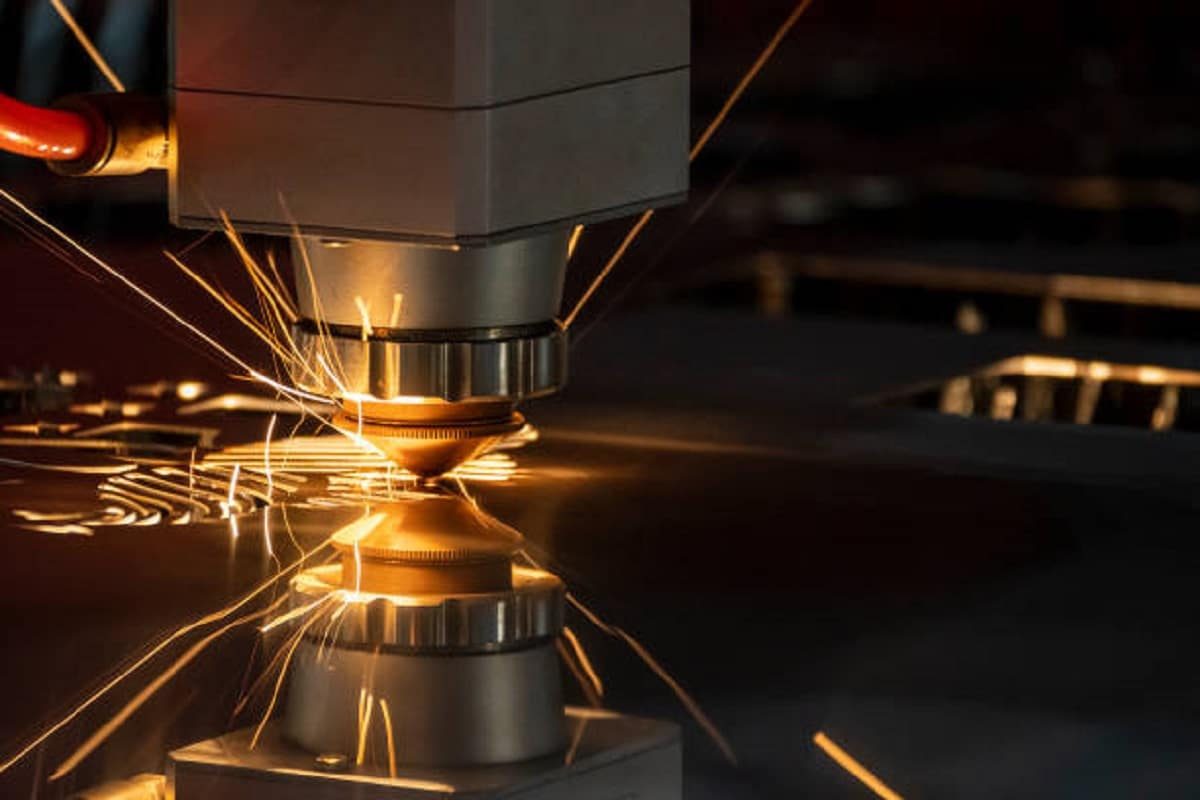
Choosing The Right Laser Cutting Machine For Your Specific Application
The widespread application of laser cutting technology has become an important part of modern manufacturing. However, when choosing the right laser-cutting machine, several key factors need to be considered to ensure optimal processing results and production efficiency. This article takes an in-depth look at this topic and provides a comprehensive guide to help manufacturers and producers make informed decisions.
It’s important to understand the key factors to consider when choosing a laser cutter. From material type to cutting accuracy, from degree of automation to return on investment, every factor plays a significant role in the final choice. In this article, we’ll delve into the importance of each factor and explore how to choose the best laser-cutting machine for your specific application needs. Whether you are just starting in manufacturing or looking to upgrade your existing cutting equipment, this article will provide you with valuable reference and guidance.
Table of Contents
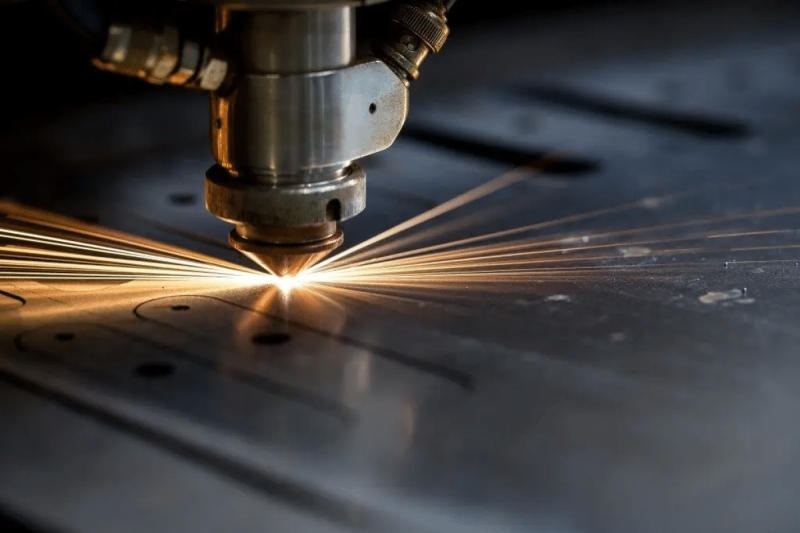
Basic principles of laser cutting machine
A laser cutting machine is a device that uses a high-energy-density laser beam to cut or process materials. Its basic principle is. The basic principle is to use the laser beam generated by the laser generator to focus the beam and control its energy density to generate a high-temperature area on the surface of the material, thereby melting, vaporizing, or chemically reacting the material, and ultimately achieving the purpose of cutting or processing. The basic principles of a laser-cutting machine include the following steps:
- Laser generator generates laser beam: Laser cutting machine uses CO2 laser generator or solid laser generator. The laser beam generated by energy excitation has high energy density and monochromaticity and is suitable for cutting and processing materials.
- The laser beam is focused through the optical system: the laser beam passes through optical components such as lenses or mirrors. After focusing, the energy is concentrated on a very small focus to form a high-energy density spot.
- Laser beam irradiates the material surface: A high-energy-density laser beam irradiates the material surface, causing the local area to rapidly heat up to a high-temperature state.
- Material and laser interaction: Materials will undergo different physical or chemical reactions under the action of the laser beam. For example, metallic materials may melt or vaporize, and non-metallic materials may undergo thermochemical reactions or ablation.
- Airflow or auxiliary gas-assisted cutting: During the laser cutting process, airflow or auxiliary gas is usually injected into the cutting area through a nozzle to help remove molten material or gasification products and speed up the cutting process.
Through the above steps, laser cutting machines can cut or process various materials with high precision and efficiency, and are widely used in metal processing, automobile manufacturing, electronic devices, aerospace, and other fields.
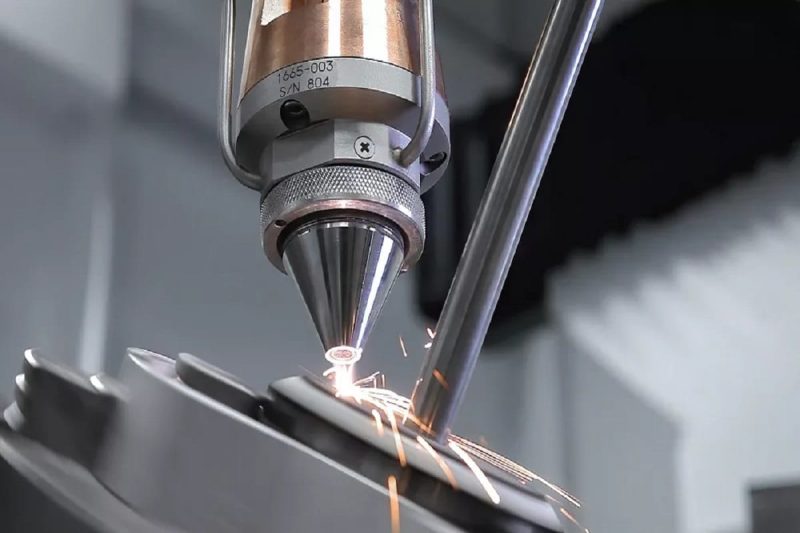
The Importance of Selecting a Laser Cutting Machine Suitable for a Specific Application
Choosing the right laser cutter for a specific application is critical, as different application scenarios and material requirements may require different types and specifications of laser cutters. Here’s why it’s important to choose the right laser cutter for your specific application:
- Increased productivity: Maximize productivity by choosing a laser cutting machine that meets your specific application needs. For example, some applications may require higher cutting speeds or larger cutting ranges, while others are more focused on cutting precision and quality.
- Guarantee cutting quality: Choosing a laser cutting machine suitable for a specific application can ensure that the cutting quality meets the requirements and avoid product quality problems or instability in subsequent processing processes caused by poor cutting quality.
- Lower costs: Choosing a laser cutter that’s right for a specific application can also help reduce production costs. Some applications may require a higher-end laser cutting machine, but for other applications, choosing the right low-cost model can meet the needs, thereby reducing investment costs and operating costs.
- Improve product flexibility: Choosing a laser cutting machine suitable for specific applications can increase product design flexibility to meet the processing needs of different products.
- Increase competitiveness: Choosing a laser cutting machine suitable for a specific application can help companies increase their competitiveness. By improving production efficiency, ensuring product quality, and reducing costs, companies can better meet customer needs and improve market competitiveness.
To sum up, choosing a laser cutting machine suitable for specific applications is of great significance to an enterprise’s production efficiency, product quality, cost control, and market competitiveness. Therefore, when choosing a laser cutting machine, companies should fully consider their own production needs and product characteristics, and choose the most suitable model and specifications.
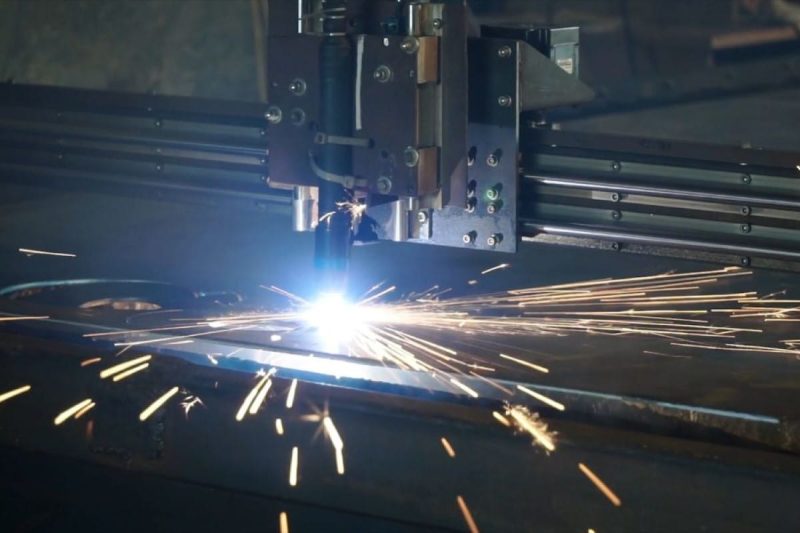
What are the key factors to consider when choosing a laser cutter for a specific application?
Choosing the right laser cutting machine for a specific application is a complex decision-making process involving several key factors. These factors are explored in detail below:
Material type
Different laser-cutting machines are suitable for different types of materials. For example, some machines are suitable for metallic materials, while others are better suited for non-metallic materials such as plastic or wood. So the first thing to consider is the type of material you need to work with.
Material shape and thickness
In addition to the type of material, consider the shape and thickness of the material. Some laser cutters may be better suited for processing flat materials, while others are better suited for processing tubular or shaped materials. Additionally, different machines may have different maximum cutting thickness capabilities, so you need to make sure the machine you choose can meet your specific needs.
Cutting speed and quality
Cutting speed and quality are important indicators for measuring laser cutting performance. Higher cutting speed means higher productivity without sacrificing cutting quality. Therefore, these two factors need to be balanced to ensure that the machine selected can increase production efficiency while maintaining high quality.
Cutting accuracy and range
For some applications, cutting accuracy and range are critical. Applications with high precision requirements may require a higher-precision laser cutting machine, and it is necessary to consider whether the cutting range of the machine can meet the needs.
Degree of automation
With the development of technology, many laser-cutting machines have varying degrees of automation functions. Automation can increase productivity and reduce operator workload. Therefore, it is necessary to consider whether the production process requires automation functions and select the corresponding machine.
Control systems and functions
The control system and functionality of a laser cutting machine are critical to operating and adjusting the machine. Make sure the machine you choose is equipped with an easy-to-use control system and has all the necessary features you need, such as cutting parameter adjustment, material identification, etc.
Initial purchase cost and operating cost
In addition to the cost of the machine itself, the operating costs of the machine also need to be considered, including maintenance, energy consumption, etc. A thorough cost analysis is required to ensure that the selected machine will remain economical over the long term.
Return on investment
The return on investment of a laser cutting machine needs to be evaluated, taking into account the initial purchase cost and operating costs. This includes considering factors such as increased productivity and improved product quality to determine whether the machine is worth the investment.
Service and Support
Last but not least, consider the service and support provided by your laser cutting machine supplier. Timely maintenance and technical support can ensure the stable operation of the machine and reduce downtime in production.
Only by comprehensively considering these factors can you make an informed decision to ensure that the selected laser-cutting machine can best meet your production needs and achieve a good return on investment.
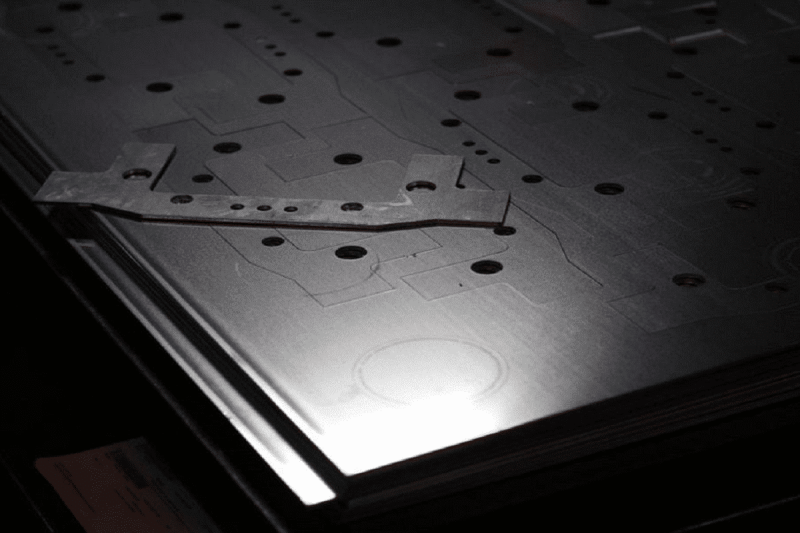
The impact of future development trends and technological innovation on choices
Future development trends and technological innovations will have a significant impact when choosing a laser cutting machine. As the manufacturing industry continues to develop, the demand for laser-cutting machines continues to evolve. The following are the impacts of future development trends and technological innovations on choices:
- Increased demand for intelligence and automation: With the advancement of artificial intelligence and automation technology, companies will be more inclined to choose intelligent and highly automated laser-cutting machines in the future to improve production efficiency and reduce labor costs.
- Wider material applicability: In the future, laser cutting technology may be more widely applicable to various materials, including metals, non-metals, composite materials, etc. Therefore, when choosing a laser cutting machine, you need to consider its applicable material range.
- High-speed and high-precision requirements: With the acceleration of product upgrading, enterprises will have higher requirements for cutting speed and precision in the future. Therefore, when choosing a laser cutting machine, you need to consider its cutting speed and precision performance.
- Green environmental protection and energy saving requirements: In the future, society will have stricter requirements for environmental protection and energy saving. Therefore, choosing a laser-cutting machine that can save energy and reduce emissions will become an important consideration.
- Enhanced data analysis and monitoring capabilities: Future laser cutting machines may have more powerful data analysis and monitoring capabilities to achieve real-time monitoring and optimization of the production process and improve production efficiency and product quality.
Summarize
In modern manufacturing, it is a critical and complex task. By considering these factors, you will be able to select the best laser-cutting machine for your specific application, resulting in increased productivity, lower costs, and a higher return on investment. In today’s world of ever-evolving technology, it’s vital to ensure you choose the right cutting machine for your specific needs, which will bring lasting success and competitive advantage to your business.
At AccTek Laser, we recognize the importance of choosing the right laser cutter for your specific application so you can make an informed decision. We are committed to delivering cutting-edge solutions, backed by industry expertise and innovative technology, ensuring that our customers not only receive state-of-the-art machinery but also comprehensive support and guidance throughout the entire process.
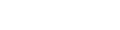
Contact information
- [email protected]
- [email protected]
- +86-19963414011
- No. 3 Zone A, Lunzhen Industrial Zone,Yucheng City , Shandong Province.
Get Laser Solutions