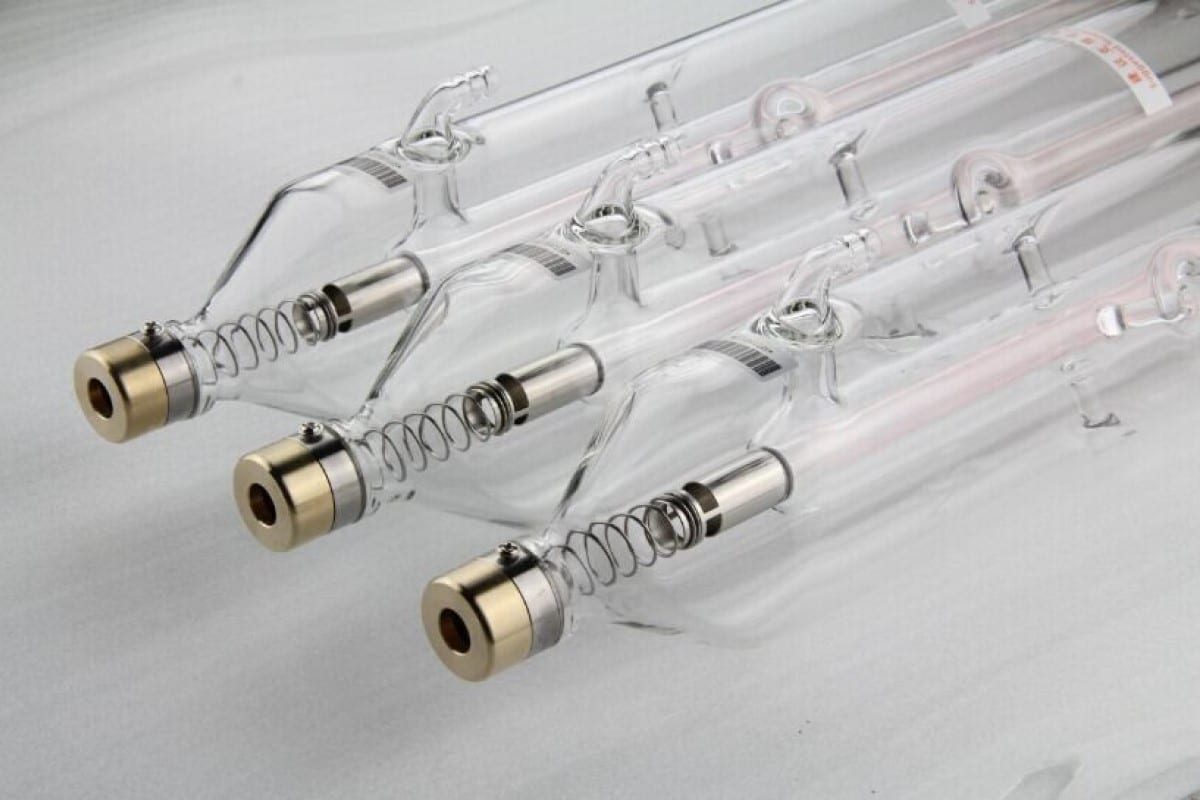
CO2 Laser Cutting Accuracy And Precision: Comprehensive Guide
In today’s world of advanced manufacturing and fabrication, precision and accuracy are critical. Precision cutting, CO2 laser cutting technology has become a cornerstone of various industries including automotive, aerospace, and electronics due to its ability to cut, engrave, and mark materials with exceptional accuracy and precision.
In this comprehensive article, we’ll take a deep dive into the world of CO2 laser cutting, exploring the typical accuracy and precision this cutting-edge technology can achieve. From understanding the fundamentals of CO2 laser cutting to the factors that impact accuracy and precision, AccTek Laser will provide a complete in-depth analysis.
Table of Contents
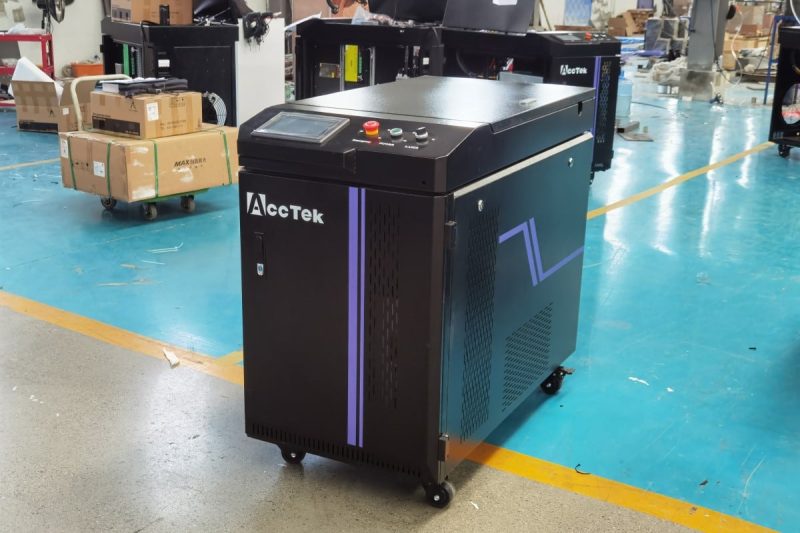
Overview of CO2 Laser Cutting
CO2 laser cutting is a high-precision, non-contact manufacturing process that uses a high-power laser beam to vaporize, melt, or burn through materials. At the heart of this technology is a CO2 laser generator that produces a concentrated beam of light, primarily in the infrared spectrum, with a wavelength of 10.6 microns. This invisible beam is highly focused, allowing for precise material removal.
How CO2 Laser Cutting Works
The working principle of CO2 laser cutting is very simple, which is to focus the high-power CO2 laser beam onto the surface of the material to be cut. The high-intensity energy of the laser beam vaporizes or melts material at the point of contact, while a stream of auxiliary gas blows away the molten material to create the cut. The precise movement of the laser head is controlled by computer numerical control (CNC), allowing for complex and precise cutting patterns.
Advantages of CO2 Laser Cutting
The CO2 laser cutting offers several advantages, including:
- High precision: capable of complex and precise cuts.
- Clean cut: The laser beam leaves behind little or no debris, resulting in a clean edge.
- Versatility: It can cut a variety of materials, including metals, plastics, and organic materials.
- Minimal heat-affected zone: The CO2 laser generator generates minimal heat, reducing the chance of material deformation.
- Automation: The process can integrate automation for high-volume production.
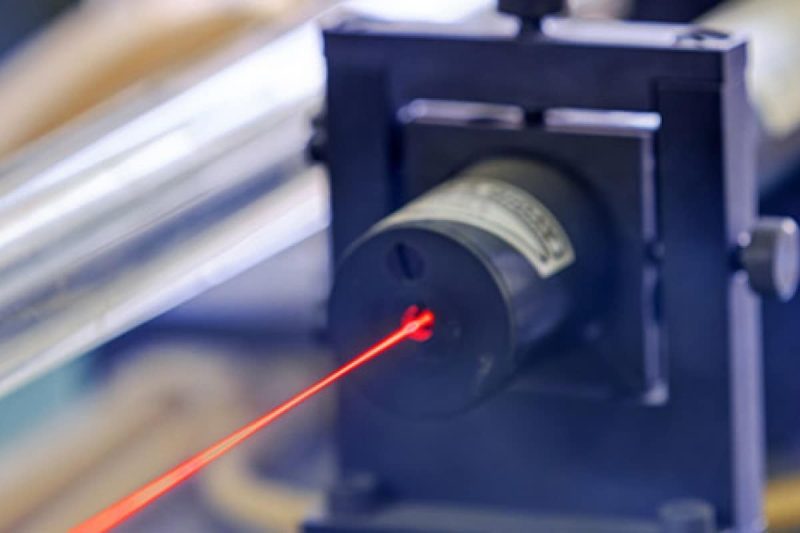
Accuracy and Precision
Difference Between Accuracy and Precision
In the context of CO2 laser cutting, accuracy and precision are often used interchangeably, but with different meanings:
- Accuracy: Accuracy refers to how close the measured or cut value is to the actual value. In laser cutting, it indicates how well the machine achieves the expected dimensions.
- Precision: Precision is related to the repeatability of a measurement or cut, it quantifies how consistently a machine reproduces the same cut.
Accuracy and precision are both critical in laser cutting, as deviations from the desired size or shape can lead to costly errors and wasted material.
The Importance of Laser Cutting Accuracy and Precision
The importance of accuracy and precision in CO2 laser cutting cannot be overstated because:
- Quality: High accuracy and precision bring excellent product quality, ensuring that parts fit perfectly during assembly.
- Material Saving: Precise cutting minimizes material waste, saves costs, and reduces environmental impact.
- Efficiency: Accurate, precise cutting reduces the need for post-processing, saving time and resources.
- Consistency: In high-volume production, maintaining consistent accuracy and precision helps ensure that all products meet the same specifications.
- Versatility: The ability to achieve high accuracy and precision allows cutting a variety of materials, expanding the range of CO2 laser cutting applications.
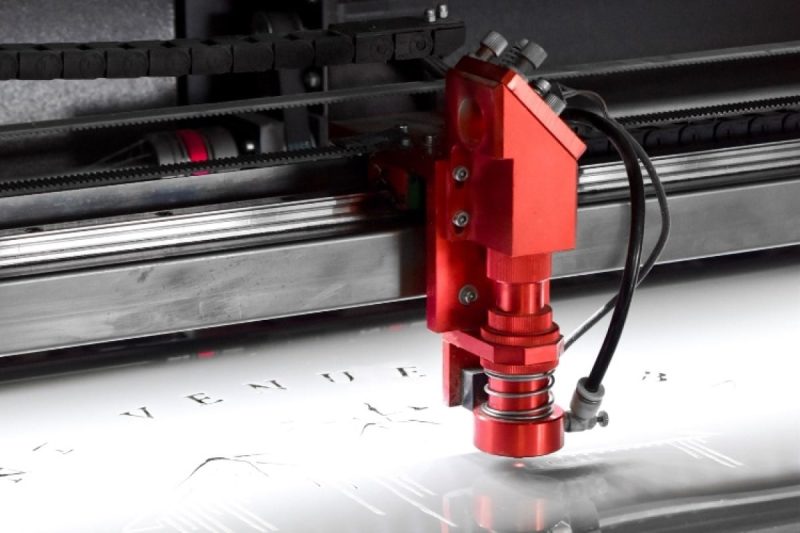
Factors Affecting CO2 Laser Cutting Accuracy and Precision
Several factors influence the accuracy and precision of CO2 laser cutting:
Beam Quality
The quality of the laser beam is a critical factor. A high-quality laser beam has a well-defined, circular cross-section, and its energy is evenly distributed across the beam. Beam quality can be affected by the resonator design and maintenance. A laser beam with poor quality may result in irregular cuts, affecting precision and accuracy.
Beam Diameter
The diameter of the laser beam determines the level of detail that can be achieved. Smaller beam diameters enable finer cuts, while larger diameters are better suited for thicker materials but may sacrifice detail. The choice of beam diameter is a trade-off between precision and cutting speed.
Cutting Speed
The speed at which the laser cutter moves along the material affects precision. High cutting speeds can lead to lower precision, while slower speeds provide greater precision but may result in higher production times. Finding the right balance is crucial for each specific application.
Material Type and Thickness
Different materials have varying thermal properties and behaviors when subjected to laser cutting. Metals, plastics, and organic materials each respond differently to the laser beam. The thickness of the material also plays a role, as thicker materials require more energy and, in turn, can affect precision.
Focus Position
The focus position also has a certain impact on the accuracy of CO2 laser cutting. The focus should be precisely positioned on the material surface to achieve ideal cutting results. Any deviation from the correct focus position will result in reduced accuracy.
Assist Gas
Auxiliary gas is often used during CO2 laser cutting to improve cutting quality. For non-metallic materials and some metallic materials, using compressed gas or inert gas to treat the melted and vaporized material can inhibit excessive burning in the cutting area. The type and flow rate of assist gas affects material removal and cleanliness of the cut.
Focusing Optics
Focusing optics, such as lenses, play a key role in shaping the laser beam and directing it to the material. The quality and alignment of these optics help achieve precise cuts. Any misalignment or contamination can cause the beam to diverge or deflect, resulting in reduced cutting accuracy.
CNC Control
CO2 laser cutting machines are controlled by computer numerical control (CNC) systems. The accuracy of these control systems, along with the precision of the motors and drive mechanisms, significantly affects the precision of the cuts.
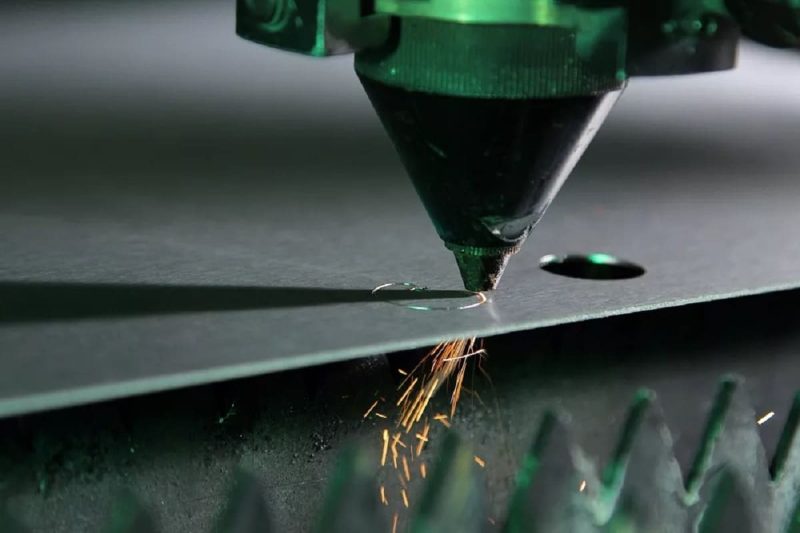
Typical Accuracy and Precision
The typical accuracy and precision of CO2 laser cutting can vary depending on the factors mentioned above and the specific equipment used. However, it is possible to provide some general guidelines for what can be expected in terms of accuracy and precision.
Accuracy
The accuracy of CO2 laser cutting is often measured in terms of how closely the actual cut matches the intended design. The accuracy can be expressed in terms of tolerance, which is the permissible deviation from the intended dimensions. For most industrial applications, the accuracy of CO2 laser cutting typically falls within a range of ±0.1mm to ±0.5mm. This level of accuracy makes CO2 laser cutting suitable for a wide range of applications, from cutting intricate patterns in paper to precision cutting of metal components.
Precision
Precision in CO2 laser cutting refers to the repeatability of the process. It measures how consistently the laser-cutting machine can reproduce the same cut over multiple runs. Precision is often expressed in terms of a percentage of the material thickness. A typical CO2 laser cutting system can achieve precision levels of around ±0.05% to ±0.1% of the material thickness. This means that for a 1mm thick material, the precision could be within ±0.05mm to ±0.1mm.
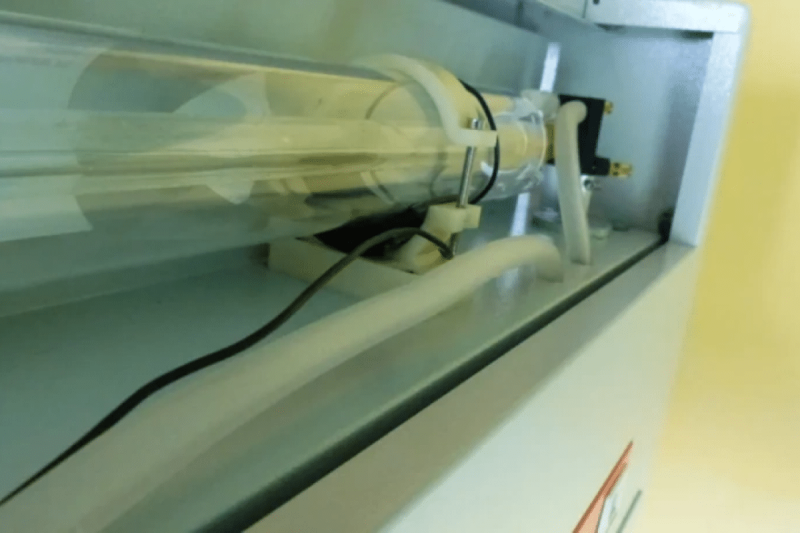
Improve Accuracy and Precision
Achieving and maintaining high levels of accuracy and precision in CO2 laser cutting involves several strategies:
Maintain Laser System
Regular maintenance of CO2 laser systems helps improve accuracy and precision. This includes cleaning optics, aligning the laser beam, and ensuring all mechanical components are in optimal condition. Well-maintained equipment is more likely to provide consistent cutting results.
Choose The Right Materials
Choosing the right material for a specific application is important to improve accuracy and precision. Different materials have different requirements and characteristics. For example, metals may require different cutting parameters than plastics, while specialty materials such as ceramics may require specialized methods.
Optimize Cutting Parameters
The key to achieving high accuracy and precision is fine-tuning cutting parameters, which involves adjusting laser power, cutting speed, assist gas type, and focal length to match the material and desired results. It often takes experimentation and testing to find the best settings.
Advanced Technology
Advanced technologies such as dynamic laser control and real-time monitoring can further improve accuracy and precision. These technologies enable laser systems to adapt to changes in material properties and maintain consistent cut quality.
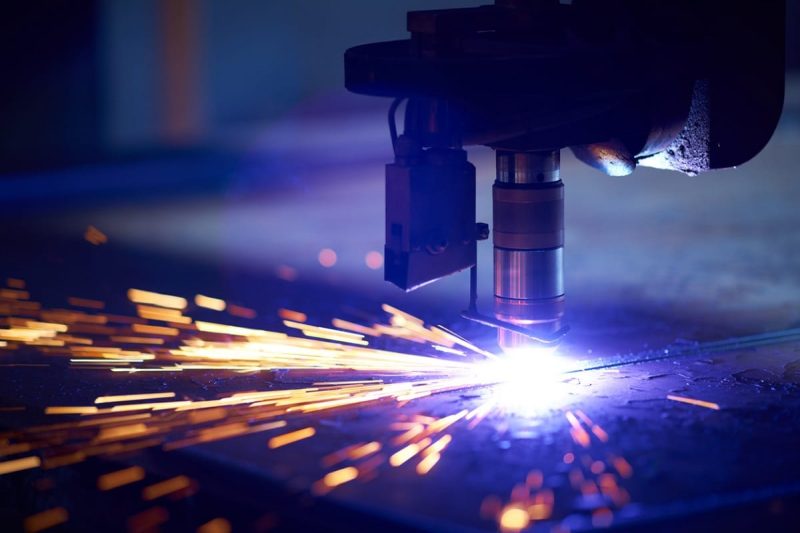
Application of CO2 Laser Cutting
CO2 laser cutting is widely used in various industries because of its ability to provide high precision and precision. Some noteworthy applications include:
- Signage and graphics industry: CO2 laser cutting’s ability to cut complex shapes and engrave detailed designs in materials such as acrylic, wood, and plastic makes it a popular choice for signage, prizes, and promotional materials.
- Textile and clothing industry: The textile industry uses CO2 lasers for high-precision pattern cutting to ensure efficient and precise production of clothing.
- Medical device manufacturing industry: CO2 laser cutting is used to manufacture complex components for medical devices, ensuring they meet strict quality and precision requirements.
- Paper and packaging industry: CO2 laser cutting is used for die-free cutting and scoring of paper and cardboard, allowing for highly customized packaging solutions.
- Aerospace industry: CO2 lasers are used to cut and shape composite materials used in aircraft and spacecraft, where precision and lightweight materials are critical.
- Art and design industry: In art and design, CO2 laser cutting enables the creation of detailed sculptures, intricate jewelry, and custom signage with high precision and accuracy.
Summarize
CO2 laser cutting is a technology that is revolutionizing precision cutting and engraving in various industries. Achieving high levels of accuracy and precision helps produce high-quality parts and minimize material waste. Understanding the typical accuracy and precision of CO2 laser cutting is critical to choosing the correct cutting method for a specific project. While the accuracy and precision of CO2 laser cutting are excellent, they can be affected by a variety of factors, such as beam quality, material type, and cutting speed.
As technology continues to advance, CO2 laser cutting is likely to become more precise and efficient, opening up new possibilities and applications in various fields. In a world where precision and accuracy are paramount, CO2 laser cutting is a testament to human ingenuity and innovation in manufacturing and manufacturing. If you are looking for a CO2 laser cutting machine, you can contact us. AccTek Laser can provide you with customized solutions based on your specific application.
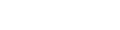
Contact information
- [email protected]
- [email protected]
- +86-19963414011
- No. 3 Zone A, Lunzhen Industrial Zone,Yucheng City , Shandong Province.
Get Laser Solutions