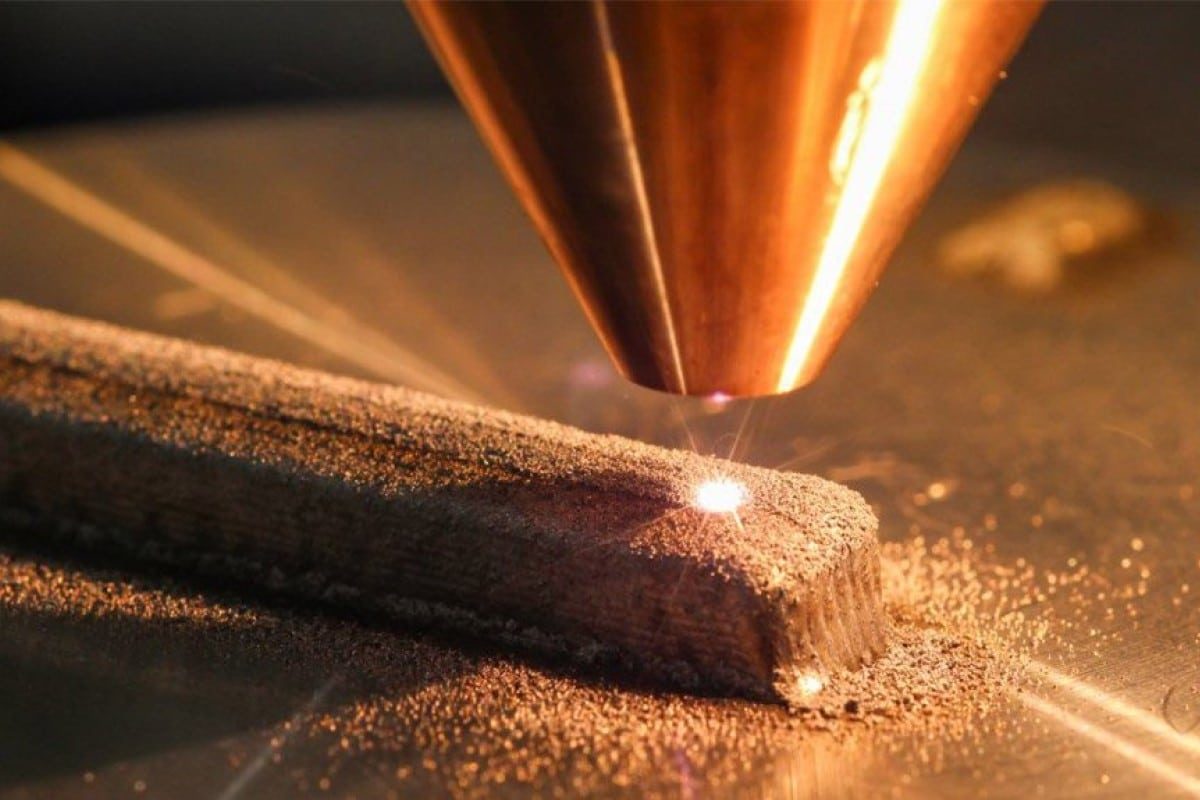
CO2 Laser Cutting Machine Operating Cost: Comprehensive Analysis
In the dynamic world of modern manufacturing, CO2 laser cutting machines have become transformative tools that redefine precision and efficiency in materials processing. As companies in different industries adopt these advanced technologies, the issue of average operating costs comes into focus. This article aims to delve into the complex structure of CO2 laser cutting machine average operating costs, elucidating the factors that influence these costs, effective strategies to reduce expenses, and the prospects for future trends and innovations shaping this landscape.
From dissecting the basic components that power these laser generators to understanding the multifaceted factors that impact their day-to-day costs, we’ll uncover the complexities companies encounter when integrating CO2 laser cutting machines into their operations. Beyond a mere review, our journey extends into practical insights on how to reduce operating costs, providing actionable strategies for businesses seeking to optimize financial resources while maximizing the benefits of this transformative technology.
But our journey didn’t end there. The vision of technological development continues to shape the appearance of CO2 laser-cutting machines. As we explore future trends and innovations, we will gain insight into emerging technologies and foresee their potential impact on operating costs. From advances in automation and software integration to the incorporation of sustainable practices, businesses will be able to foresee the evolving nature of these machines and the possibilities they offer for cost optimization and efficiency.
Table of Contents
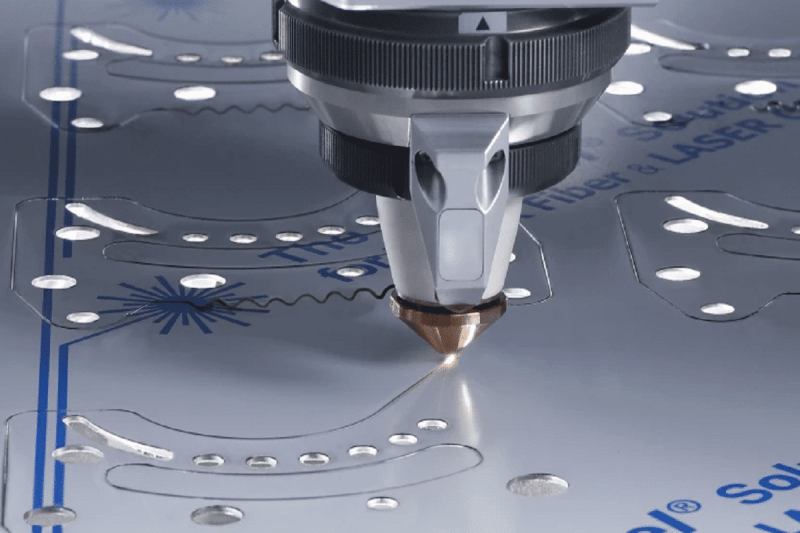
Factors Affecting CO2 Laser Cutting Machine Operating Costs
Energy Consumption
- Description: Power consumption is a significant component of operating costs and varies based on the machine’s power and usage time. Larger, more powerful machines tend to consume more energy, affecting operating expenses accordingly.
- Approximate Cost: Typical power consumption estimates range from $5 to $20 per operating hour, depending on the machine’s power output and local energy prices.
Laser Tube Life
- Description: The laser tube is the key component for emitting a laser beam. Over time, it will show wear and tear, requiring periodic maintenance or eventual replacement.
- Approximate Cost: Laser tube replacement costs range from $2,000 to $10,000, depending on the power and quality of the laser tube. Maintenance costs to extend the life of a laser tube, including regular cleaning and calibration, can run up to several hundred dollars per year.
Consumables And Spare Parts
- Description: Consumables such as lenses, nozzles, and gases (nitrogen and oxygen) help maintain optimal machine performance. Regular replacement of these consumables and spare parts is necessary.
- Approximate Cost: The cost of consumables may vary based on usage, but typically ranges from around 5-10% of total operating costs. Spare parts for other machine components may add to ongoing expenses, depending on the wear and tear on the machine.
Maintenance And Service Contracts
- Description: Regular maintenance helps prevent breakdowns and ensure consistent performance. Service contracts provided by the manufacturer cover routine maintenance and may include repair costs.
- Approximate Cost: Routine maintenance costs typically range from $2,000 to $5,000 per year, including inspections, adjustments, and minor repairs. Many manufacturers offer service contracts that cover routine maintenance and repairs. These contracts may add 5-10% to operating costs but help prevent unexpected expenses and downtime.
Labor Cost
- Description: A skilled operator is essential for setting up, programming, and monitoring CO2 laser-cutting machines. Labor costs include wages, training, and any additional personnel needed.
- Approximate Cost: Labor costs vary widely based on location, skill level, and number of operators required, and typically represent 10-20% of operating expenses.
Facility Requirements
- Description: The use of CO2 laser cutting machines requires adequate facility infrastructure, including ventilation, climate control, and safety measures. Meeting these requirements ensures a conducive environment for optimal machine performance.
- Approximate Cost: Costs associated with a facility can range from $5,000 to $15,000 per year, depending on the size of the facility and the extent of modifications required.
Software And Technology Upgrades
- Description: Regularly updating your machine’s software and technology helps you stay competitive and efficient. Costs may include software licenses, updates, and potential hardware upgrades.
- Approximate Cost: The costs associated with software upgrades and technology advancements can vary significantly depending on the manufacturer and the complexity of the upgrade. Businesses should allocate a budget for regular updates to promote long-term efficiency and compatibility.
A detailed understanding of these factors is critical for businesses seeking to effectively estimate and manage average CO2 laser-cutting machine operating costs. By carefully considering each element, businesses can make informed decisions, implement cost-saving strategies, and ensure the longevity and efficiency of their CO2 laser-cutting operations.
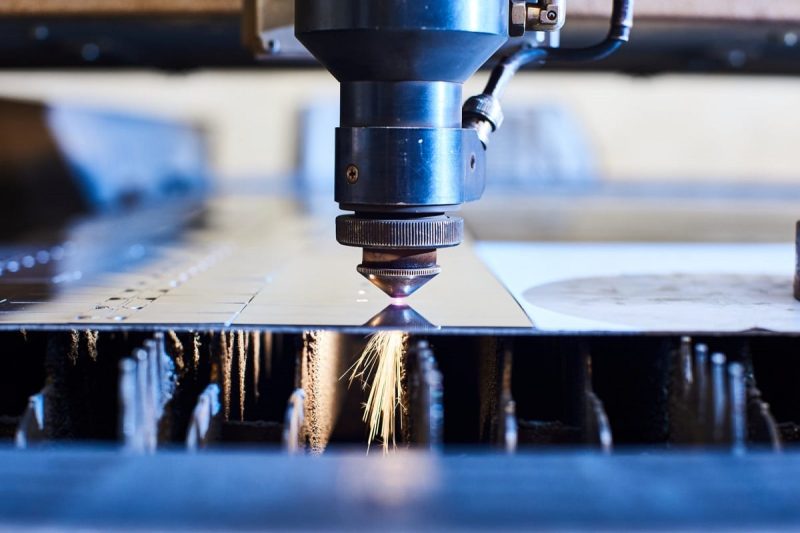
Reduce Operating Costs of CO2 Laser-Cutting Machines
While CO2 laser-cutting machines offer unrivaled precision and efficiency, businesses are acutely aware of the operating costs associated with leveraging this cutting-edge technology. Implementing strategic measures to reduce these costs is not only economically prudent but also critical to maintaining long-term competitiveness. The following discusses in detail how companies can effectively reduce the operating costs of CO2 laser-cutting machines:
Energy Saving Measures
- Invest in Energy-Saving Machines: Consider upgrading to a new CO2 laser cutting machine with advanced energy-saving features. Modern models often feature improved power management systems and more efficient components, helping to save significant energy over time.
- Optimize Cutting Parameters: Fine-tune cutting parameters such as speed, power and focus to achieve the best results with minimal energy consumption. Conduct periodic evaluations to determine the most energy-efficient settings for different materials and thicknesses.
- Implement Idle Shutdown Protocols: Configure machines to automatically enter an idle or low-power state when not in use. This practice prevents unnecessary energy consumption during periods of inactivity, thereby contributing to overall energy savings.
Consumables Management
- Use High-Quality Supplies: Invest in high-quality supplies, such as lenses and nozzles, to extend their lifespan. While these consumables have an upfront cost, long-term benefits include reduced replacement frequency and lower overall operating costs.
- Implement Recycling Practices: Explore opportunities to recycle gases used in the cutting process. Proper recycling not only contributes to environmental sustainability but also helps minimize the recurring costs of purchasing new gas for machines.
- Usage Optimization: Implement best practices to extend the life of consumables. Clean and maintain lenses, nozzles, and other parts regularly to prevent premature wear.
- Buy and Negotiate in Bulk: Consider buying consumables in bulk or negotiating better pricing with suppliers to reduce total unit costs.
Proactive Maintenance And Training
- Scheduled Maintenance Schedule: Follow a proactive maintenance schedule to identify and resolve potential issues before they escalate. Regular maintenance helps extend the life of critical components and reduces the frequency of costly replacements.
- Operator Training Program: Invest in a comprehensive training program for machine operators to improve their skills and knowledge of the equipment. Well-trained operators are more likely to optimize machine settings, detect problems early, and contribute to efficient, cost-effective operations.
Optimized Workflow Strategies
- Batch Processing: Whenever feasible, organize production schedules to include batch processing. Cutting multiple pieces in a single pass reduces setup time and energy consumption per unit, helping to save overall costs.
- Efficient Material Handling: Streamline material handling processes and minimize downtime between cuts. Implementing efficient material loading and unloading practices ensures machines stay running longer,
Invest Wisely in Technology Upgrades
- Prioritize Necessary Upgrades: While staying current on software and technology upgrades is critical, prioritize upgrades that directly impact efficiency and cost-effectiveness. Evaluate the specific benefits of each upgrade to determine its relevance to your production needs.
- Consider Long-Term ROI: Evaluate the return on investment (ROI) of each technology upgrade. Investments that can significantly increase efficiency or contribute to long-term cost savings should be prioritized, while non-essential upgrades can be postponed or carefully budgeted.
- Automation Integration: Explore automation options to streamline processes, reduce manual intervention, and optimize production to save costs in the long run.
Labor Efficiency And Training
- Streamline Operations: Optimize workflows and processes to maximize machine utilization and reduce idle time. Efficient scheduling and work planning can increase productivity and reduce labor costs.
- Ongoing Training: Invest in training programs for machine operators to improve their skills and efficiency, allowing them to handle operations more efficiently and minimize errors.
Facility Optimization
- Proper Facility Setup: Make sure the facility meets all requirements for the safe and efficient operation of a CO2 laser cutting machine. Adequate ventilation, climate control, and safety measures can prevent machine failure and extend service life, reducing repair costs.
- Energy-Efficient Infrastructure: Implement energy-efficient technologies in facilities, such as LED lighting or energy-efficient HVAC systems, to reduce overall energy bills.
Continuous Monitoring And Analysis
- Data-Driven Decision-Making: Implement monitoring systems to collect and analyze data on machine performance, energy consumption, and maintenance needs. Use this data to make informed decisions about adjusting operating parameters and scheduling maintenance activities.
- Periodic Cost Audits: Conduct periodic cost audits to identify areas for improvement. Analyze historical data on operating costs, energy consumption, and maintenance expenses to identify trends and areas where cost-saving measures can be implemented.
Systematically implementing these strategies can significantly reduce the average operating costs of a CO2 laser-cutting machine while maintaining or even improving productivity and quality standards. Each measure, when applied thoughtfully, helps provide a more cost-effective and efficient operating model for businesses that utilize these advanced cutting technologies.
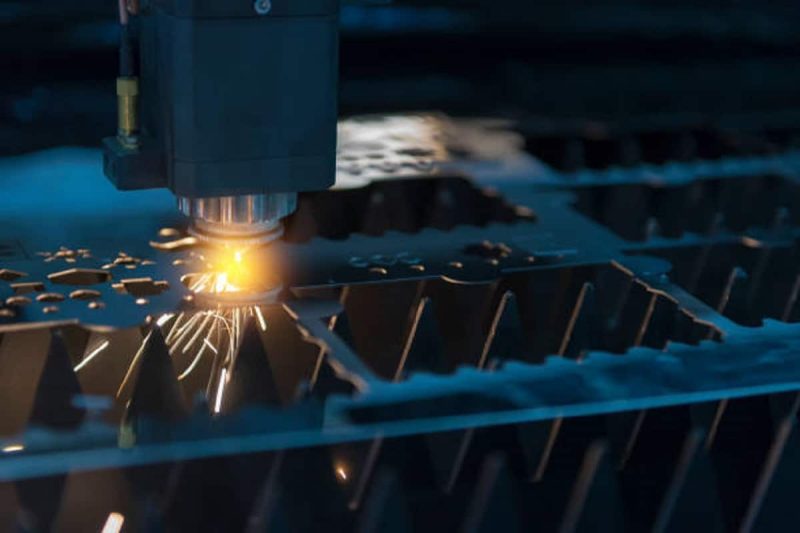
Future Trends And Innovations in CO2 Laser Cutting Machines
Advances in Automation
- Artificial Intelligence (AI) Integration: Artificial intelligence and machine learning applications are being explored to optimize the cutting process. Predictive algorithms can analyze historical data to predict potential problems, optimize cutting parameters, and improve overall efficiency. This trend aims to make CO2 laser-cutting machines more adaptable and intelligent.
- Robotic Integration: The integration of robotic arms and automated material handling systems will enhance the overall workflow, reduce manual intervention, and increase production efficiency.
Improve Accuracy And Speed
- Faster Cutting Speeds: Continued advancements in laser technology will lead to higher cutting speeds without compromising accuracy, resulting in faster turnaround times and increased throughput.
- Improved Precision: Innovations in control systems and laser technology will improve precision, allowing even complex designs and finer cuts to be made on a wider range of materials.
Green Sustainable Solutions
- Energy-Saving Technology: Future CO2 laser cutting machines will prioritize energy efficiency, adopting technology that reduces power consumption without sacrificing cutting performance.
- Environmentally Friendly Practices: Integrate environmentally friendly processes, such as utilizing recycled materials and reducing waste, to meet sustainability goals without compromising quality.
Enhanced Connectivity And Integration
- IoT Integration: The adoption of Internet of Things (IoT) technology will enable remote monitoring, diagnostics, and predictive maintenance, thereby reducing downtime and improving overall machine performance.
- Seamless Integration With CAD/CAM Software: Improved design software connectivity and compatibility will streamline workflows, enable seamless data transfer, and increase cutting accuracy.
Material Diversity And Versatility
- Expanded Material Compatibility: Future CO2 laser cutting machines are expected to be able to handle a wider range of materials, including advanced composites, alloys, and hybrid materials, opening up new avenues for cross-industry applications.
- Multifunctional: The machine can not only perform cutting, but also engraving, marking, and other functions, which will provide more versatility to meet different customer needs.
Miniaturization And Portability
- Compact Design: Advances may lead to smaller, more compact CO2 laser cutters suitable for small workshops or portable applications, thereby expanding accessibility and usability.
- Mobile Solutions: Portable models equipped with advanced features may emerge, facilitating on-site cutting and customization in various industries such as construction and repair.
Integration of Intelligent Manufacturing And Industry 4.0
- Industry 4.0 Integration: CO2 laser cutting machines will become part of a connected smart manufacturing ecosystem, enabling seamless communication between machines and optimizing the entire production line for greater efficiency and flexibility.
- Remote Monitoring: Manufacturers are integrating features that allow operators to monitor machine performance, troubleshoot issues, and adjust settings remotely. This trend helps improve operational efficiency and reduce downtime.
- Customization And Personalization: Easily meet customers’ individual needs using technology that allows for mass customization and personalized manufacturing.
Integrate With Other Cutting Technologies
- Fiber Laser Integration: Integrating fiber laser technology into CO2 laser cutting machines is a trend worth noting. Fiber laser generators increase efficiency and speed for faster, more precise cuts. This innovation is designed to improve overall performance while potentially reducing energy consumption.
- Hybrid Machines: The emergence of hybrid laser cutting machines, which combine different laser technologies such as CO2 and fiber optics, is gaining traction. These machines offer versatility by adapting to a variety of material-cutting requirements, providing manufacturers with more adaptable and efficient solutions.
As these trends and innovations unfold, the landscape for CO2 laser cutting machines is about to change. Businesses that adopt these advancements will benefit from increased efficiencies, reduced operating costs, and enhanced capabilities, positioning themselves at the forefront of the evolving manufacturing industry. In the future, it is expected that cutting-edge technology will be integrated to break through the limits of what CO2 laser-cutting machines can achieve.
Summarize
As we conclude our exploration of the average operating costs of CO2 laser cutting machines, it is clear that these technological marvels offer huge potential for precision cutting in various industries. Understanding the complexity of operating costs, from power consumption to maintenance and technology advancements, is critical for businesses seeking to leverage the capabilities of these machines while effectively managing expenses.
At AccTek Laser, we recognize the importance of making informed decisions when integrating a CO2 laser-cutting machine into your operation. We are committed to delivering cutting-edge solutions, backed by industry expertise and innovative technology, ensuring that our customers not only receive state-of-the-art machinery but also receive comprehensive support and guidance throughout their journey.
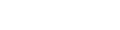
Contact information
- [email protected]
- [email protected]
- +86-19963414011
- No. 3 Zone A, Lunzhen Industrial Zone,Yucheng City , Shandong Province.
Get Laser Solutions