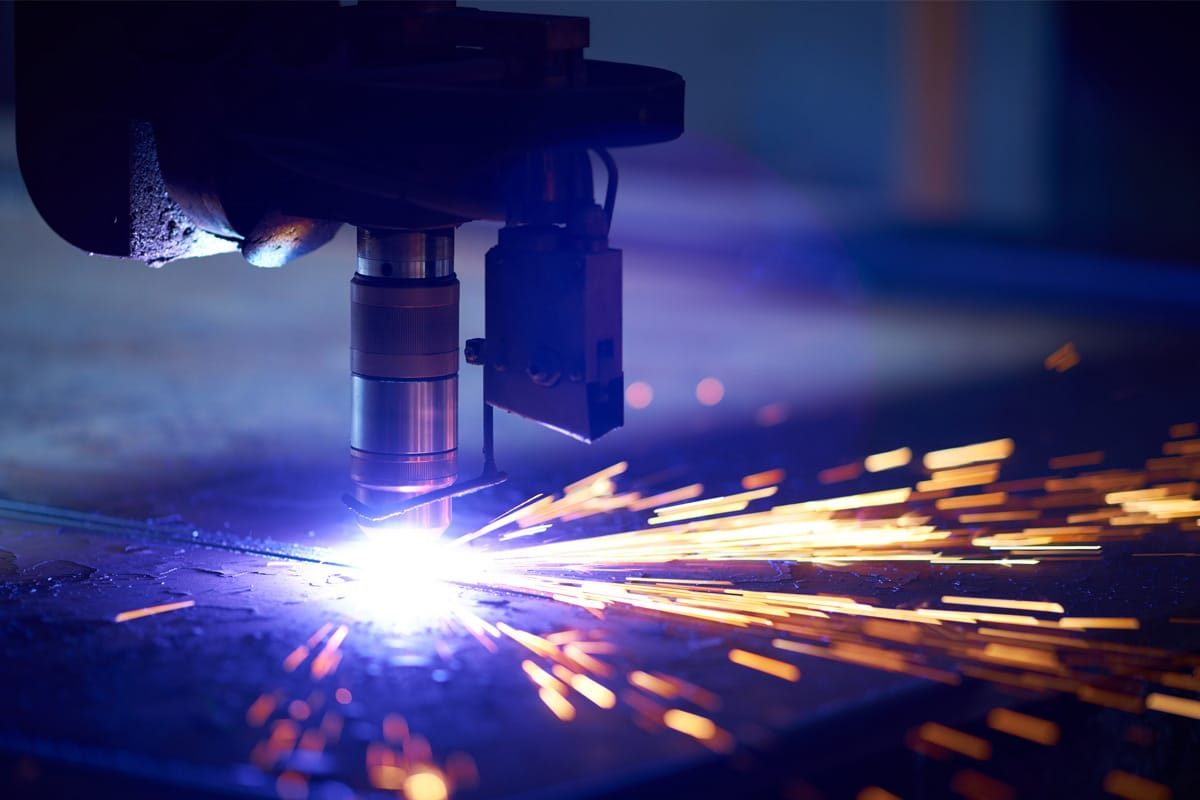
Common Problems and Solutions for Fiber Laser Cutting
Fiber laser cutting technology is widely used in the cutting and processing of various metal and non-metal materials due to its high efficiency, high precision, and flexible operation. It uses a high-power laser beam to irradiate the surface of the workpiece to melt or vaporize it, thereby achieving precise cutting of the workpiece. However, in practical applications, fiber laser cutting also faces some common problems and challenges, such as reduced cutting quality, low cutting efficiency, and fast equipment loss. Understanding and dealing with these problems can not only extend the life of the equipment but also improve production efficiency and processing quality.
Table of Contents
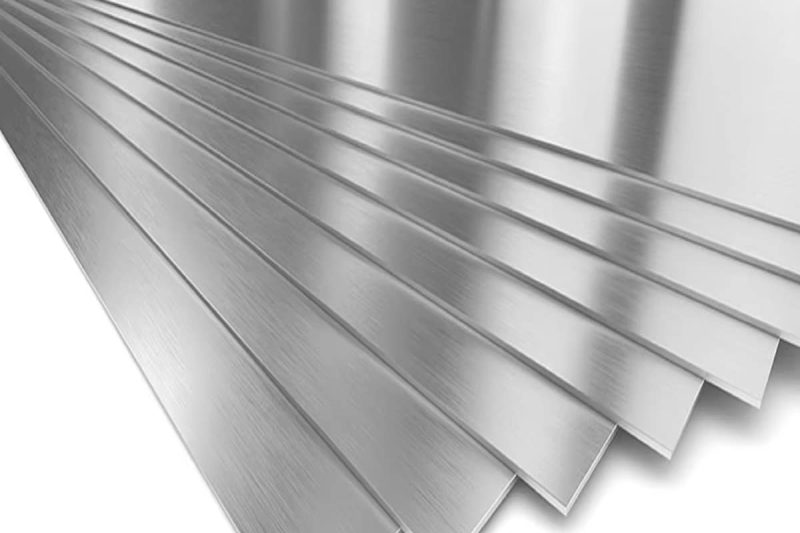
Materials-Related Challenges
Reflectivity and Conductivity
The better the conductivity of the material, the lower the absorption rate of laser energy. For example, gold, silver, copper, aluminum, and other materials have good conductivity and poor energy absorption, which can also be said to reflect the laser wavelength. Therefore, the higher the conductivity of the metal, the higher its reflectivity.
Challenge
- High reflectivity: Metals such as aluminum and copper have high reflectivity. Especially when the laser beam is incident at an angle close to the normal of the material surface, most of the laser energy will be reflected to the laser generator or laser transmission system, which not only reduces the processing efficiency but may also cause damage to the laser equipment, such as burning the lens or optical fiber.
- Insufficient energy absorption: Due to the high reflectivity, the effective laser energy absorbed by the material surface is reduced, resulting in insufficient processing depth, slow cutting speed, or substandard processing quality.
Solution
- Use high-power lasers: Increasing the power of the laser generator can directly increase the laser energy irradiated to the surface of the material. Even if part of the energy is reflected, the remaining energy is sufficient for efficient processing. Select a laser generator with a pulse width and frequency suitable for specific materials to optimize energy transfer and processing effects.
- Anti-reflection technology: By adjusting the shape and divergence angle of the laser beam, the laser energy is more evenly distributed on the surface of the material, reducing the problem of excessive local reflection. Use dynamically adjustable optical elements (such as deformable mirrors or liquid crystal spatial light modulators) to correct the wavefront distortion of the laser beam in real-time, improve the focusing quality of the laser beam, and reduce reflection and scattering. Some metals have different reflection characteristics for lasers in different polarization states. By adjusting the polarization direction of the laser, the reflection loss can be reduced.
- Optimize material surface treatment: Apply a coating or film that absorbs laser energy on the surface of the material to increase the absorption rate of laser energy and reduce the reflectivity. Increase the roughness of the material surface through mechanical, chemical, or laser pretreatment, improve the scattering and absorption of laser energy, and reduce direct reflection. Form an absorption layer on the surface of the material or change its surface chemical properties to increase the laser absorption rate.
- Adjust processing parameters: Optimize the incident angle of the laser beam to avoid the laser beam being incident directly perpendicular to the material surface to reduce specular reflection. Adjust the speed, power, focal length, and other parameters of the laser processing to find the best processing conditions to ensure processing quality and efficiency.
Material Warping and Deformation
Material deformation is caused by warping, which is caused by residual stress inside the material and is unevenly distributed along the width and length of the material.
Challenge
During the laser cutting process, local heating can cause material deformation, especially on thin plate materials. This is because the laser will concentrate a large amount of heat energy in a small area during cutting, causing the temperature of the area to rise rapidly, thus causing thermal expansion and contraction of the material, and ultimately causing the material to warp and deform.
Solution
- Adjust laser power: Reducing laser power can reduce heat concentration, thereby reducing the thermal deformation of the material.
- Optimize cutting speed: Properly increasing cutting speed can reduce the laser’s residence time on the material and reduce heat accumulation.
- Use auxiliary gas: Selecting a suitable auxiliary gas (such as nitrogen or oxygen) and adjusting its flow rate can effectively remove the heat generated during the cutting process and reduce material deformation.
Material Thickness
In the fiber laser cutting process, the thickness of the material will directly affect the cutting quality, efficiency, and machine performance. Thinner materials are easier to cut, with faster speed and higher precision, but thicker materials may result in rough cutting edges or require higher power and auxiliary gas.
Challenge
When cutting thicker materials, the laser takes longer to penetrate the material, which can easily lead to uneven cutting. Thick materials have poor thermal conductivity and heat is not easily dissipated, resulting in slag and irregular cutting surfaces on the cutting edge.
Solution
- Choose the appropriate laser power: Choose the appropriate laser power according to the thickness of the material to ensure that the beam energy is concentrated in the cutting area to achieve the best cutting effect.
- Adjust cutting parameters: including parameters such as cutting speed, focal position, and auxiliary gas pressure to ensure the stability and uniformity of the cutting process.
- Multiple cutting: For particularly thick materials, multiple cutting methods can be used, cutting a part of the thickness each time, cutting layer by layer, to reduce heat accumulation and uneven cutting problems.
Through the above methods, the problems of high material reflection, warping, deformation, and uneven cutting of thick materials during laser cutting can be effectively solved, and the cutting quality and efficiency can be improved.
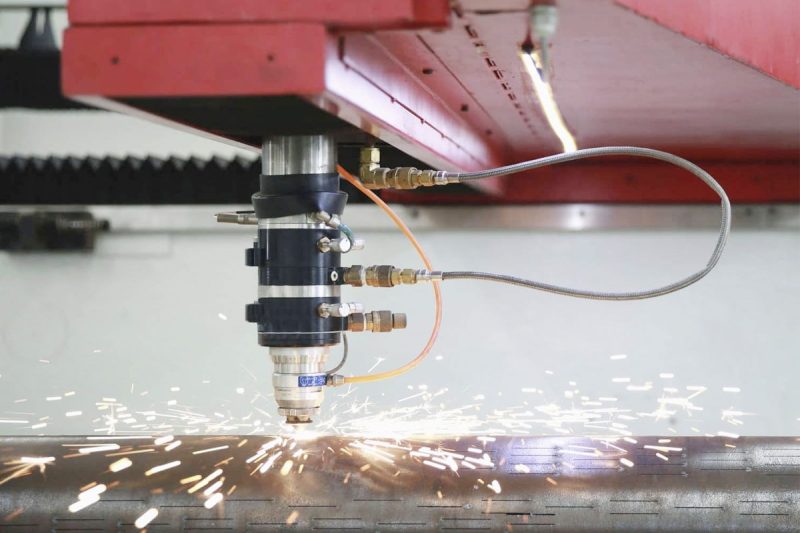
Edge Quality and Kerf Width
The smoothness of the cut edge and the amount of burrs are key to evaluating cutting accuracy. If the laser energy is unevenly distributed or the cutting speed is not appropriate, the edge may appear rough or burred. The width of the slit depends on the stability of the laser focus. If the focus is unstable or the laser power fluctuates, the width of the slit may vary inconsistently, affecting the cutting accuracy.
Rough Edges and Burrs
Challenge
- During laser cutting, if the energy is uneven or the cutting speed is too fast or too slow, the cutting edge will often have burrs and unevenness. Especially when the power output of the laser beam is unstable, the surface of the cut material may be locally overheated or melted unevenly, resulting in rough edges.
- For some metal materials (such as aluminum, stainless steel, etc.), uneven heat distribution will induce thermal stress, which further leads to the formation of burrs.
- In addition, improper use of auxiliary gas (insufficient airflow or inappropriate pressure) will also affect the discharge efficiency of the molten material and increase the number of burrs.
Solution
- It is critical to optimize the laser’s power settings and cutting speed. Make sure the laser power is high enough and the output is stable to maintain an even heat distribution on the material surface. At the same time, the cutting speed needs to be adjusted according to the thickness and characteristics of the material, neither too fast (to avoid insufficient cutting of the material) nor too slow (to prevent excessive melting).
- Using the right assist gas, such as nitrogen or oxygen, can improve cutting results and ensure a clean and smooth cut surface. Nitrogen is often used to prevent oxidation and reduce edge burrs, while oxygen helps to increase cutting efficiency and melting speed.
Slit Width Variation
Challenge
- The main reason for inconsistent slit width is usually related to the instability of the laser focus or the fluctuation of the laser power. When the laser focus is offset, the energy concentration will change accordingly, resulting in fluctuations in the slit width. If the laser power is unstable, the output fluctuation of energy will directly affect the cutting accuracy and cause changes in the slit width.
- In addition, contamination or damage to the optical components may also cause changes in the beam quality, thereby affecting the uniformity of the cutting line. The wear of the mechanical parts of the equipment, such as the guide rails and bearings, will also affect the movement accuracy of the laser head, resulting in inconsistent slits.
Solution
- Regularly check and maintain the optical system to ensure stable laser focus and energy.
- Clean or replace contaminated optical lenses to avoid unnecessary refraction or scattering during beam transmission.
- Regularly calibrate the focus and power output of the laser equipment to ensure its accuracy during operation.
- Maintain the mechanical parts of the equipment to ensure smooth and unobstructed movement of the laser head to reduce cutting errors caused by mechanical wear.
In summary, by correctly setting parameters and regularly maintaining the optical system, the edge quality can be effectively improved and the kerf width can be controlled.
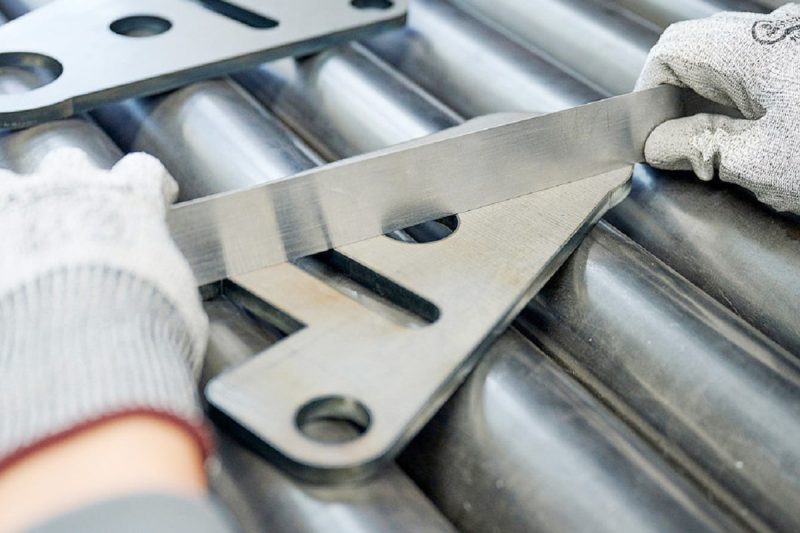
Process-Related Challenges
Process-related challenges mainly involve technical problems that may be encountered during the fiber laser cutting process. Common process-related challenges include slag accumulation, which is a common challenge in the fiber laser cutting process, especially when cutting thicker or difficult-to-cut materials. Usually, slag accumulation is caused by the failure of the material to fully melt or evaporate, or an insufficient supply of auxiliary gas to blow the molten material away from the cutting area in time.
Slag Accumulation
Challenge
- When the laser energy is insufficient or the laser beam focus is offset, the material surface cannot reach the temperature to melt or evaporate, resulting in some material remaining at the cutting edge. Especially in the processing of thick plates, the laser energy needs to be strong enough to penetrate the entire material thickness.
- Auxiliary gases such as oxygen or nitrogen are often used to help blow the molten material away from the cutting area. If the gas pressure is too low and the molten material cannot be effectively removed, slag will accumulate at the cutting edge.
- Too fast a cutting speed will cause the laser to not continue to act on the same area, the material is not fully melted, or the gas cannot expel the residue in time, resulting in slag accumulation.
Solution
- Ensure that sufficient gas pressure is provided to help effectively remove the molten material and avoid slag accumulation. Nitrogen is suitable for non-oxidizing materials, while oxygen can accelerate the cutting speed but requires higher gas pressure.
- Optimize the cutting speed according to the material thickness and characteristics to ensure that the laser energy can fully act on the cutting area. The appropriate combination of laser power and cutting speed can reduce unnecessary heat-affected zones, thereby avoiding the problem of incomplete melting of materials.
- Ensure that the optical components of the laser generator are in the best condition and can stably output the required laser power to ensure the consistency of the cutting process.
By comprehensively adjusting these parameters, slag accumulation problems can be significantly reduced, cutting quality improved, and subsequent grinding and cleaning work reduced.
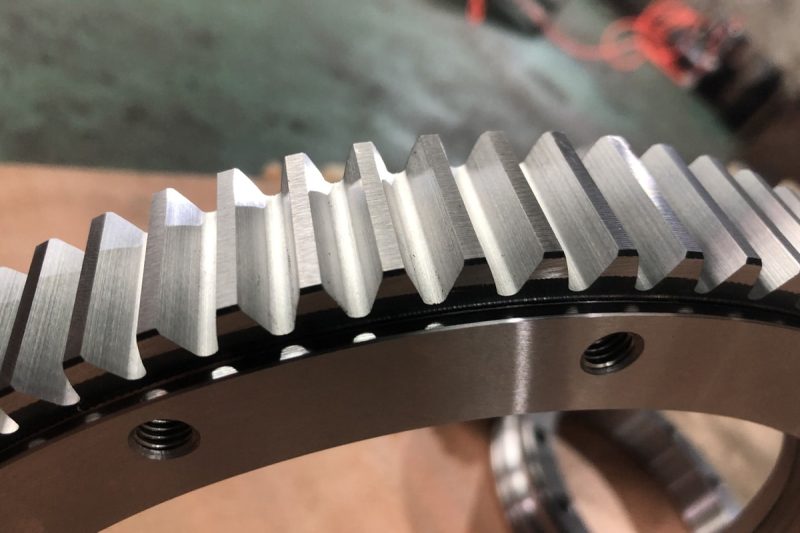
Puncture and Start-up Issues
During the fiber laser cutting process, perforation and startup issues are common challenges, especially when dealing with thicker or highly reflective materials. The perforation process is the starting point of laser cutting, and its stability and efficiency directly affect the effect of the entire cutting process. If the perforation time is too long or fails, it may lead to material waste, and equipment wear, and even affect the cutting quality. The instability of the startup process will lead to uneven slits and poor cutting-edge quality, affecting the accuracy and appearance of the finished product.
Piercing Delays and Failures
Challenge
Piercing delays are usually caused by the laser beam failing to quickly focus enough energy to penetrate the material, resulting in a long piercing time. Piercing delays are especially noticeable on thicker materials or reflective materials (such as aluminum and copper), and may even cause piercing failures. Reasons for piercing failures may include insufficient laser power, inaccurate laser focus, insufficient auxiliary gas, or inappropriate gas selection. This can cause uneven or failed cutting starts, waste material, and potentially damage the laser equipment.
Solution
- Ensure that the laser power can be concentrated quickly, especially on thick plate materials, where higher energy is required for perforation. Adjust the laser focus to ensure it is concentrated on the surface of the material, reducing energy dispersion and shortening the perforation time.
- By piercing in short pulse mode, material overheating and deformation can be reduced, while the chance of piercing failure is reduced. This technique is particularly suitable for thicker materials and highly reflective materials.
- The use of nitrogen and oxygen has a significant impact on the piercing process. Oxygen can speed up the perforation process, but may cause oxidation of the material, so the appropriate gas and pressure need to be selected based on the material characteristics.
- For very thick materials, multi-stage perforation techniques can be used, which penetrate the material layer by layer rather than all at once. This method can effectively avoid puncture failure and excessive thermal effects.
Unstable Startup
Challenge
The unstable startup is mainly manifested as uneven kerf width and poor edge quality at the beginning of laser cutting, and may even lead to failure of the cutting process. This is usually caused by unstable laser energy, changes in gas flow rate, inconsistent material surface characteristics (such as oxidation or coating), etc. An unstable startup can lead to poor cutting quality in the initial part, especially in precision cutting applications, this instability will affect the accuracy and consistency of the finished product.
Solution
- Before starting, the material surface can be preheated, especially on highly reflective materials. This helps reduce laser reflections and makes the cutting process smoother.
- Ensure that the laser generator quickly reaches a stable state at startup by adjusting the rate of increase of laser power and the flow rate of auxiliary gas. This can effectively avoid energy fluctuations at startup.
- For materials with oxide layers or other impurities on the surface, simple surface cleaning or coating removal can be performed before startup to reduce laser reflections and instability during the startup process.
- Use a real-time monitoring system to monitor the cutting process, especially during the startup phase, and ensure the stability and consistency of the cutting process by adjusting parameters.
In general, by optimizing laser parameters, selecting appropriate auxiliary gas, using pulse perforation technology, and preprocessing before starting, the problems of perforation delay, failure, and unstable start can be significantly reduced, and cutting efficiency and quality can be improved. These solutions not only improve operational efficiency but also ensure long-term stable operation of equipment.
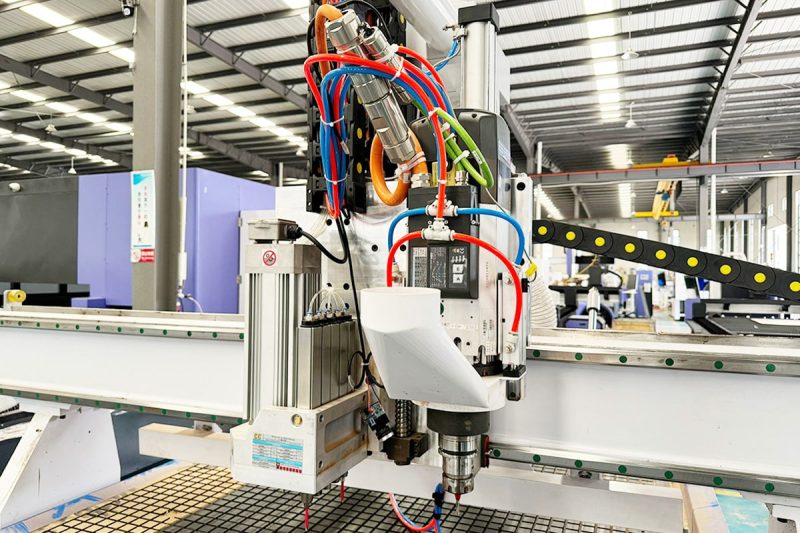
Machine-Related Challenges
In fiber laser cutting, the performance of the machine directly affects the cutting quality and efficiency. The beam transmission system and mechanical components of the machine itself may have various problems after long-term use, which will affect the accuracy and stability of laser cutting..
Beam Delivery System Problems
Challenge
The beam transmission system is the core system that transmits the energy of the laser source to the cutting head. Its performance directly determines the energy stability of the laser beam and the cutting quality. If the beam transmission system is not regularly inspected and maintained, dust, impurities or mechanical wear may also damage the optical components, further reducing the efficiency of the system.
Solution
- Optical lenses and lenses in fiber laser cutting systems are prone to dust and oil accumulation. Regular cleaning can avoid the decline of laser beam transmission efficiency and ensure beam stability.
- Ensuring the stability of fiber connectors and the precise alignment of laser beams can reduce energy loss. Check fiber connections regularly to ensure that there is no looseness or wear.
- If frequent beam instability problems occur, consider using adaptive optics technology to adjust the beam transmission system in real-time to ensure the best beam quality.
- Heat accumulation during beam transmission affects beam quality, so it is crucial to keep the cooling system running effectively. Check the cooling system regularly to ensure that it can dissipate heat normally and reduce the thermal impact during beam transmission.
Mechanical Wear
Challenge
The mechanical components in fiber laser cutting machines, including guide rails, servo motors, and drive systems, will gradually wear out over time under intensive use. Mechanical wear will not only cause unstable movement of the cutting head but may also affect the accuracy of the cutting path and ultimately the quality of the finished product. Especially under high-speed and high-precision cutting requirements, mechanical wear will accelerate equipment aging, and increase maintenance costs and downtime. In addition, increased vibration and noise are also common symptoms of mechanical wear.
Solution
- The guide rails and transmission systems need to be lubricated regularly to reduce friction and extend the service life of mechanical parts. At the same time, the lubrication system should be checked to ensure its normal operation and avoid excessive wear of parts due to insufficient lubrication.
- If the guide rails, gears, or other parts are found to be worn or offset, the damaged parts should be replaced in time to ensure the accuracy and stability of the machine.
- In high-precision operations, vibration may hurt cutting accuracy. By installing anti-vibration devices or optimizing the installation position of the machine, the impact of vibration on mechanical parts can be reduced, thereby delaying wear.
- Modern fiber laser cutting machines can be equipped with a monitoring system to monitor the status of mechanical parts in real-time, predict possible failures in advance through data analysis, and avoid sudden downtime caused by mechanical wear.
Through regular maintenance and optimization of the beam transmission system and mechanical components, the performance and stability of the fiber laser cutting machine can be significantly improved, ensuring the continuity and high quality of the cutting effect.
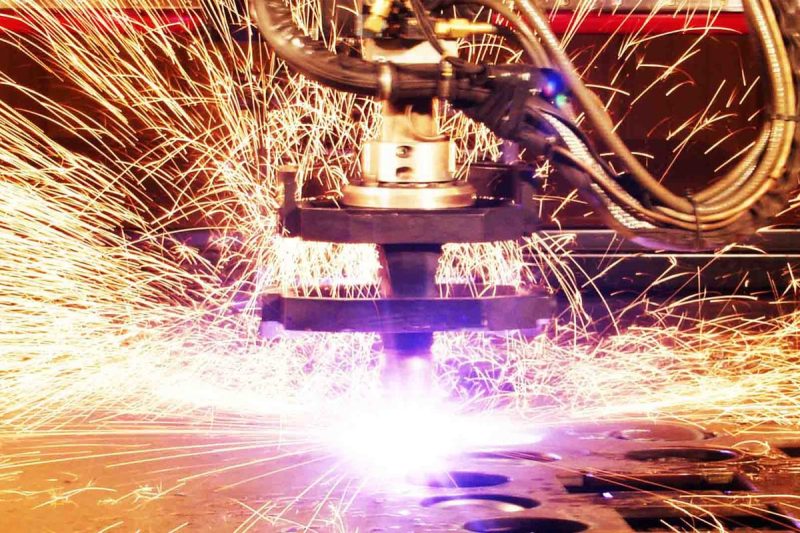
Taper and Angular Deviation
Taper and angle deviation are two common precision challenges in the fiber laser cutting process. Taper problems usually manifest as inconsistent upper and lower widths of the cut edge, while angle deviation refers to the lack of perpendicularity between the laser beam and the material, resulting in a tilted cut surface. These problems affect the quality and appearance of the final workpiece, especially in high-precision cutting tasks.
Taper
Challenge
The taper phenomenon usually occurs when cutting thick materials, and it manifests as the cutting edge being narrow at the top and wide at the bottom, or wide at the top and narrow at the bottom. This is because the energy distribution of the laser beam is uneven when passing through the material. The greater the cutting depth, the more obvious the laser energy attenuation, resulting in a difference in the upper and lower widths of the cutting edge. The taper will affect the accuracy of the workpiece, especially in the case of high-precision assembly. The taper will cause assembly difficulties and even scrap the workpiece. In addition, inappropriate auxiliary gas pressure and unstable laser power will also aggravate the taper phenomenon.
Solution
- Taper problems can be effectively reduced by optimizing the depth and position of the laser focus. Positioning the focus in the middle of the material rather than on the surface helps maintain an even distribution of laser energy throughout the cutting thickness.
- For thicker materials, using a higher-power laser generator can maintain a more stable energy output during the cutting process and reduce taper problems caused by laser attenuation.
- The taper can be reduced by properly adjusting the pressure of the auxiliary gas, keeping the cutting area clean, and effectively cooling the cutting edge. Especially in thick material cutting, the role of auxiliary gas is crucial.
- Any slight problem with the optical system will cause uneven energy distribution of the laser beam. Therefore, regular maintenance and cleaning of optical components to ensure laser beam quality can effectively reduce taper.
Angular Deviation
Challenge
Angular deviation refers to the lack of verticality of the laser beam relative to the material, resulting in an inclined cutting edge. This may be caused by unstable laser head installation, incorrect beam alignment, or insufficient precision of the mechanical system. Angular deviation will cause the cut surface of the workpiece to be uneven, affecting accuracy and appearance, especially when the workpiece is required to be cut at right angles.
Solution
- Ensuring that the laser head is firmly mounted and perpendicular to the material is the first step to solving the angle deviation problem. Regular calibration of the laser head and mechanical system ensures that the laser beam always maintains the correct angle during cutting.
- Cutting speed, power output, and auxiliary gas settings all affect angle deviation. By optimizing these parameters, the laser beam can be kept stable during cutting, thereby reducing angle deviation.
- Adaptive optics can adjust the propagation path and focus of the laser beam in real-time to ensure that the correct angle with the material is always maintained during cutting, thereby reducing angle deviation.
- External factors such as temperature and humidity changes and vibrations can affect the angle accuracy of laser cutting. Angle deviation can be further reduced by maintaining the stability of the cutting environment, such as reducing vibration, controlling temperature and humidity, etc.
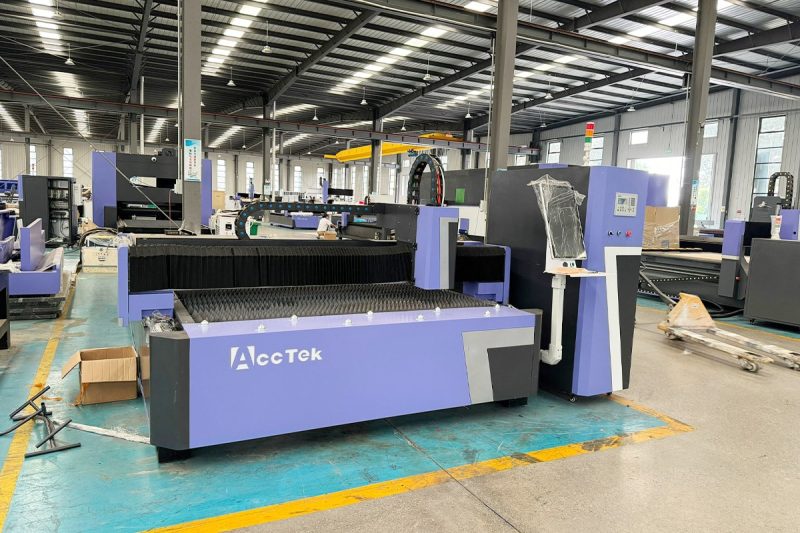
Environmental Factors
Environmental factors have a direct impact on the stability and quality of the fiber laser cutting process. Fluctuations in temperature and humidity, as well as changes in air quality, can negatively impact the performance of the laser system, the quality of the cut, and the life of the machine. Understanding and controlling these environmental factors can ensure that the equipment operates at its best, reducing unnecessary failures and maintenance requirements.
Temperature and Humidity Fluctuations
Challenge
Fluctuations in temperature and humidity are a major challenge in the laser cutting process. The laser generator and optical system are very sensitive to changes in temperature and humidity. For example, too high a temperature may cause the laser generator to overheat, affecting the quality and stability of the laser beam; while too low a temperature may cause the laser generator to fail to reach the required operating temperature, thus affecting the power output. Too high a humidity may cause condensation on the optical components, affecting the transmission efficiency of the laser beam and even damaging the optical devices. Too low humidity may increase the risk of static electricity, which may interfere with the normal operation of electronic components.
Solution
- To cope with temperature and humidity fluctuations, it is recommended to install specialized environmental control systems such as air conditioning and dehumidification equipment in the cutting workshop. These systems can maintain constant temperature and humidity in the workshop to ensure that the laser equipment works under optimal conditions.
- Install temperature and humidity sensors around the cutting equipment to monitor environmental conditions in real-time. Once an abnormality is detected, the environmental control system can be automatically adjusted, or the cutting process can be suspended if necessary to avoid damage to the equipment.
- In a dry environment, increase air humidity to reduce the risk of static electricity, and use anti-static floors and equipment grounding measures to ensure safe operation.
Air Quality
Challenge
The impact of air quality on the laser cutting process cannot be ignored. Dust, oil mist, and other pollutants suspended in the air may enter the optical system or cutting area of the laser generator, affecting the transmission and focusing of the laser beam. Pollutants in the air may also react with the laser beam during the cutting process, resulting in poor cutting results or even damage to the workpiece surface. In addition, long-term exposure to poor-quality air will increase the frequency of machine maintenance and shorten the service life of the equipment.
Solution
- Install an air purification system in the laser cutting workshop to filter out particulate matter and pollutants in the air to ensure clean air. Especially when cutting certain materials (such as plastics and wood), these materials may release harmful gases during the laser cutting process, so an effective air purification system is particularly important.
- Even with an air purification system, it is still necessary to clean the optical system of the laser generator regularly. Remove dust and pollutants that may accumulate to ensure the quality of the laser beam and the cutting effect.
- In some key equipment or areas, positive pressure protection measures can be adopted, that is, by introducing filtered air, the air pressure in the area is kept higher than the outside to prevent pollutants from entering.
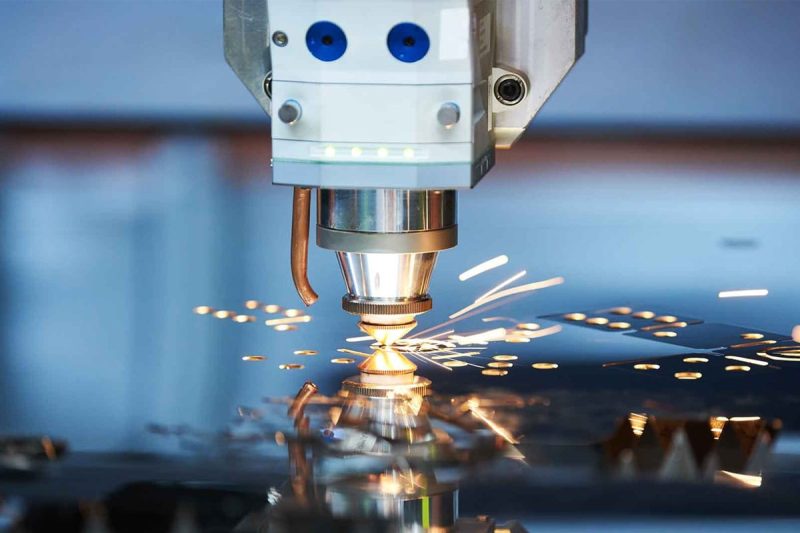
Operator-Related Challenges
In addition to environmental factors, the operator’s skill level and work efficiency also directly affect the quality and efficiency of fiber laser cutting. Lack of training and expertise, or inefficient workflow, can lead to improper operation, increased error rates, and even equipment damage or safety accidents. Therefore, improving the operator’s professionalism and optimizing the workflow are important links to ensure cutting quality and production efficiency.
Lack of Training and Expertise
Challenge
Fiber laser cutting is a high-precision technology that requires operators to have high professional knowledge and skills. However, in some companies, operators may lack sufficient training and cannot fully understand and master the complexity of laser cutting. This situation may cause operators to be unable to effectively respond when faced with technical problems or complex workpieces, which may affect cutting quality, increase equipment wear, and even cause safety hazards. In addition, the maintenance and care of the equipment requires specific skills and knowledge. The operator’s lack of knowledge may result in the equipment not being maintained and cared for promptly, shortening the service life of the equipment.
Solution
- Enterprises should provide systematic training for operators, including the basic principles of laser cutting, equipment operation guide, troubleshooting and solutions to common problems, etc. Through regular training, ensure that operators always master the latest technology and operating specifications.
- Establish an operation certification system for operators, and only certified personnel can operate laser cutting equipment. This not only improves the operator’s sense of responsibility but also ensures the quality and safety of operation.
- Provide strong technical support for operators, such as setting up a special technical consulting department, or hiring technical experts for regular guidance to help operators solve problems in daily operations.
Inefficient Workflow
Challenge
The efficiency of the workflow directly affects the overall efficiency of production and the quality of laser cutting. In some companies, due to unreasonable workflow design or insufficient coordination, operators may spend too much time switching tasks, debugging equipment, or handling materials. This inefficient workflow not only wastes time and resources but may also cause operator fatigue and increase the possibility of errors. In addition, if the company fails to optimize the workflow promptly, as the order volume increases, the inefficient process will become more prominent, seriously affecting production capacity and corporate competitiveness.
Solution
- By analyzing and evaluating the current workflow, we can identify bottlenecks and inefficient links and make targeted optimizations. For example, we can arrange the order of tasks reasonably, reduce the time for equipment commissioning and material handling, and improve work efficiency.
- The introduction of automation technologies, such as automatic loading and unloading systems and intelligent typesetting software, can significantly reduce the time and precision errors of manual operations and improve the efficiency of the overall workflow.
- Apply lean production principles to reduce waste and optimize resource allocation. Through continuous improvement and employee participation, we can establish an efficient and flexible workflow to ensure the efficiency and high quality of the laser cutting process.
By addressing these environmental and operator-related challenges, companies can greatly improve the efficiency and quality of fiber laser cutting, thereby gaining an advantage in the market competition.
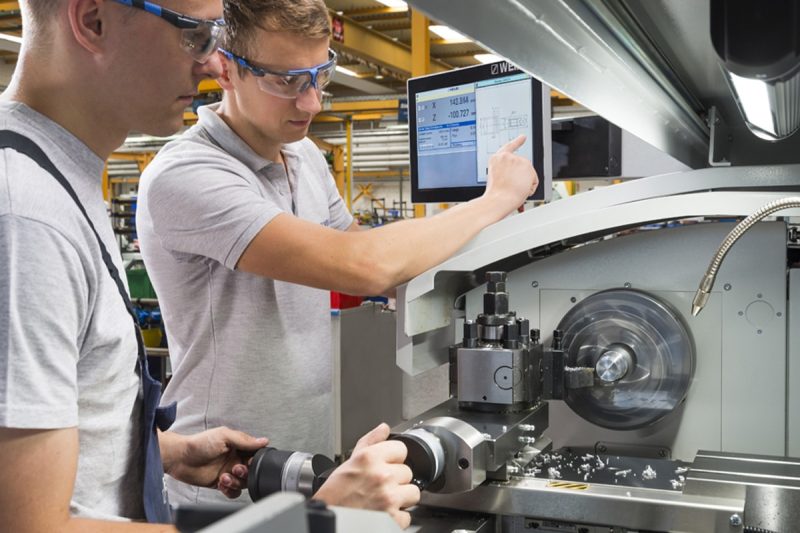
Precautions and Best Practices
To ensure the continued efficient operation of fiber laser cutting, it is critical to take preventive measures and best practices. Through regular machine maintenance, parameter optimization, operator training, and continuous improvement, companies can effectively reduce failure rates, improve cutting quality, and extend equipment life.
Regular Machine Maintenance
Challenge
Long-term operation of laser cutting equipment can lead to contamination of optical components, wear of the laser head, and failure of the cooling system. If there is a lack of regular maintenance, these problems may affect the performance of the laser generator, increase production downtime, and even cause equipment failure.
Solution
- Clean the optical system regularly to ensure the transmission efficiency of the laser beam.
- Check and replace vulnerable parts such as cutting nozzles, laser lenses, and filter systems.
- Check the cooling system regularly to ensure that it works properly to prevent the laser generator from overheating.
Parameter Optimization
Challenge
Different materials and thicknesses require different laser powers, cutting speeds, and gas pressures. Improper parameter settings may result in reduced cutting quality, such as increased burrs, or too wide or too narrow kerfs.
Solution
- Develop detailed cutting parameter tables for different materials to ensure accurate matching of power and speed.
- Regularly test the laser output of the equipment to ensure stable power and focus.
- Use auxiliary software for automated parameter optimization to improve cutting efficiency and quality.
Operator Training
Challenge
The operator’s lack of expertise or skills may lead to operational errors, increase the failure rate and affect the cutting effect.
Solution
- Provide technical training to operators regularly to ensure they master the operating specifications of laser equipment.
- Provide detailed equipment operation manuals and set up a technical support team to solve daily problems.
- Implement an operator certification system to ensure that only qualified people can operate the equipment.
Continuous Improvement
Challenge
Rapid changes in technology and markets require companies to continuously optimize production processes and technologies to remain competitive.
Solution
- Introduce lean production concepts, continuously analyze and optimize production processes, reduce waste, and improve efficiency.
- Track the development trend of laser cutting technology and update equipment and software promptly.
- Collect production data, analyze performance indicators, and continuously improve cutting parameters and operating procedures.
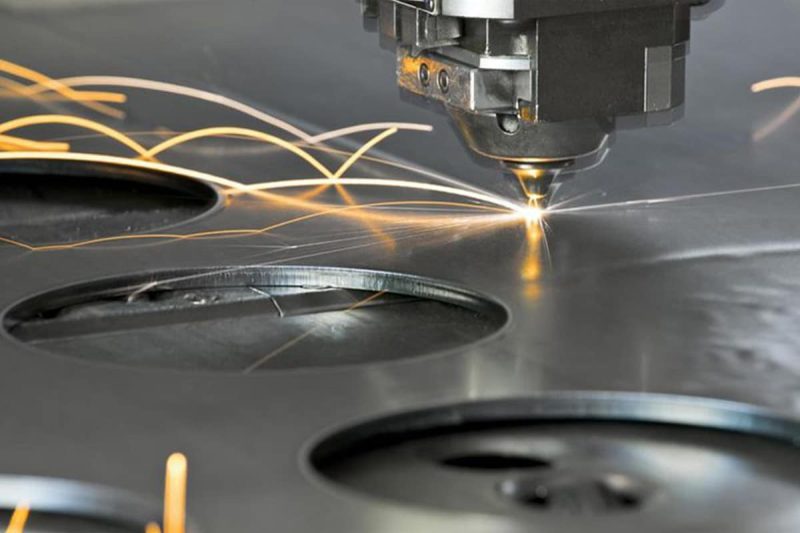
Summarize
The challenges of fiber laser cutting involve many aspects, including material properties, equipment performance, environmental conditions, etc. Through regular maintenance, optimized parameters, enhanced training, and the use of advanced technology, cutting quality and efficiency can be significantly improved. Solutions should be implemented on a case-by-case basis to improve the stability of the cutting process and reduce machine downtime and maintenance costs.
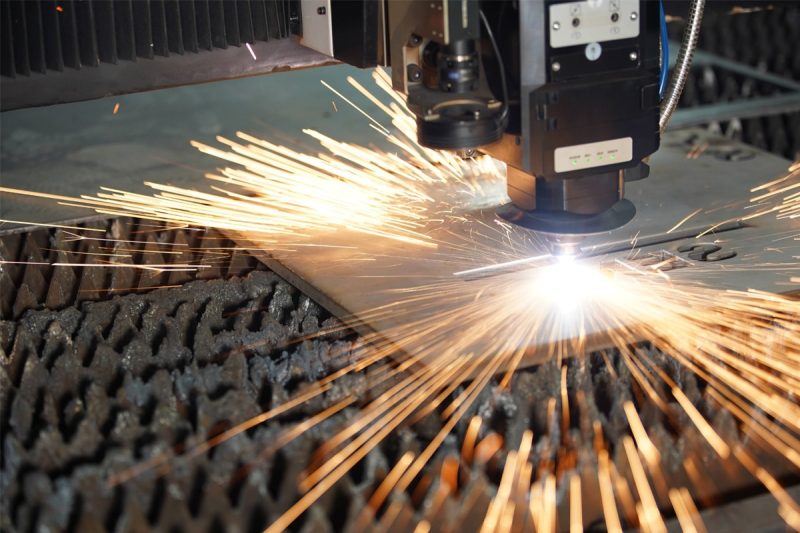
Get Laser Solutions
Choosing the right fiber laser cutting machine can help optimize power consumption and achieve high operational efficiency. Working with a trusted supplier ensures access to advanced technology, tailored advice, and ongoing support. At AccTek Laser, we offer a comprehensive range of fiber laser cutting machine equipment designed to meet a variety of industrial needs. Our experts can help you choose the most energy-efficient model and configuration, taking into account factors such as material type, thickness, and production volume. We also offer cutting-edge features such as high-efficiency laser generators, intelligent cooling systems, and energy management software to maximize performance and minimize energy use. In addition, our team provides regular maintenance services and technical support to keep your equipment at peak efficiency. By working with us, you can achieve significant energy savings, reduce operating costs, and enhance your sustainability efforts. If you have any questions, please contact us in time, AccTek Laser is committed to providing perfect laser solutions for every customer!
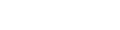
Contact information
- [email protected]
- [email protected]
- +86-19963414011
- No. 3 Zone A, Lunzhen Industrial Zone,Yucheng City , Shandong Province.
Get Laser Solutions