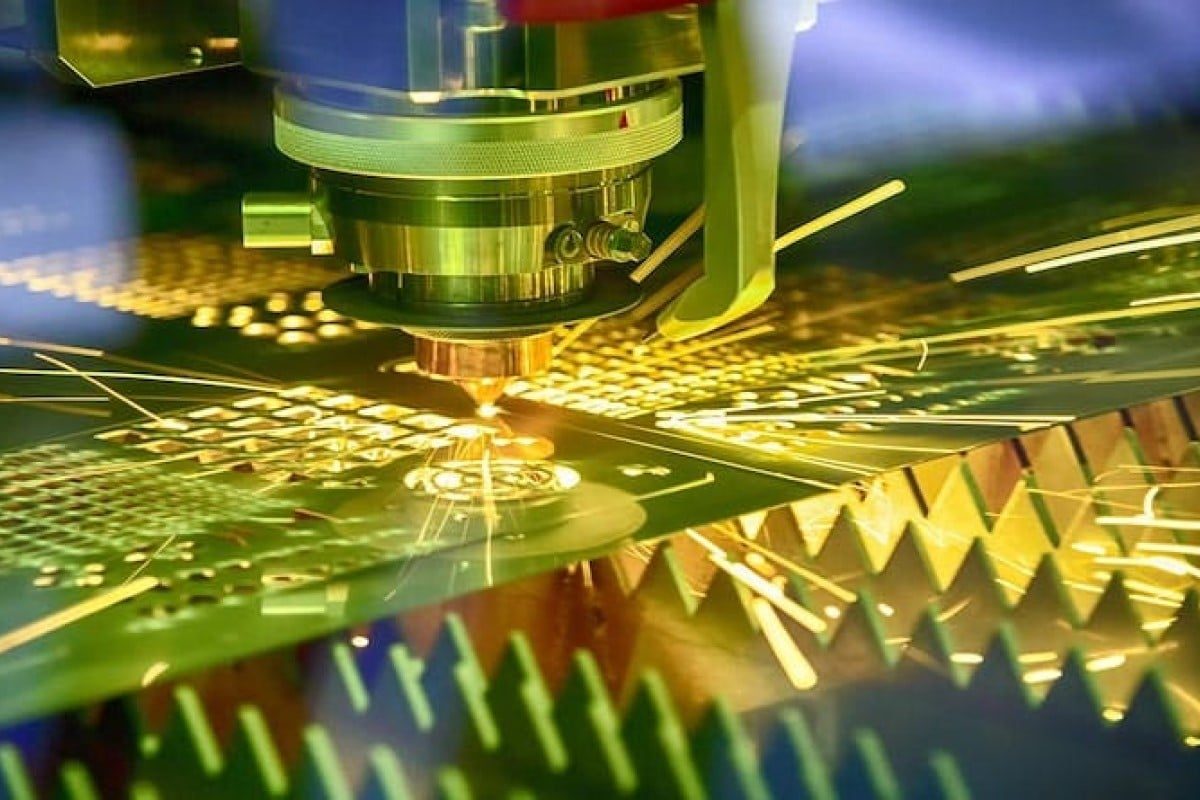
Comprehensive Guide of Laser Cutting: Types, Advantages and Applications of Laser Generator
In modern manufacturing and fabrication, precision and efficiency are crucial. As industries pursue higher quality and productivity, the role of cutting technology is becoming increasingly important. Among these technologies, laser cutting stands out as a versatile and effective method for the precise shaping of materials ranging from metals to composites.
At the heart of every laser cutting system is the laser generator, the power unit responsible for emitting a concentrated beam of light to perform complex cuts. However, not all laser generators are created equal. Laser generators are very diverse, with each type offering unique advantages for specific cutting tasks and materials.
In this comprehensive exploration, we’ll explore the various types of laser generators used in cutting applications. From venerable CO2 laser generators to cutting-edge fiber laser generators and more, we delve into the inner workings of each type to pinpoint their benefits and applications. Whether you’re a seasoned industry professional or an aspiring hobbyist, this guide will hopefully inspire and enlighten you, revealing the extraordinary capabilities of laser cutting and the remarkable machines that make it all possible.
Table of Contents
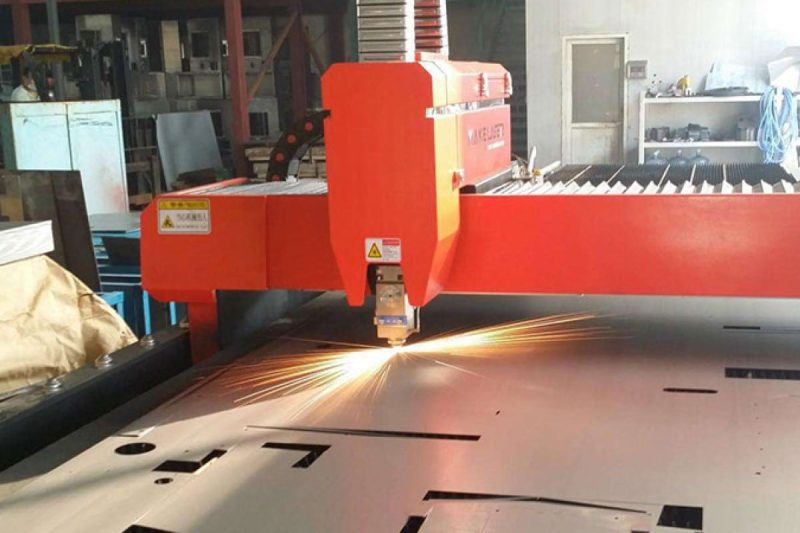
Laser Cutting Working Principle
Laser cutting works by converting electrical energy into a highly concentrated, coherent beam of light (called a laser beam). This concentrated beam is directed to the surface of the material to be cut, where it delivers controlled energy, resulting in precise, efficient material removal. How laser cutting works involves several key components and processes:
- Laser Generation: The process begins with a laser generator generating a laser beam. Depending on the type of laser generator used (eg CO2, fiber optic, disk, or Nd: YAG laser), different mechanisms are used to generate the laser beam. These lasers utilize various gain media, such as gases, optical fibers, or solid-state crystals, which are excited by an external energy source to emit photons.
- Beam Amplification: Once generated, a laser beam passes through a series of optical components, including mirrors and lenses, that amplify and focus the beam to achieve the desired intensity and spot size. The amplification process ensures that the laser beam maintains its coherence and energy density over long distances, enabling precise material processing.
- Material Interaction: A focused laser beam is then directed onto the surface of the material to be cut. When a laser beam interacts with a material, several basic processes occur:
- Absorption: The material absorbs the energy of the laser beam, causing localized heating and thermal expansion.
- Melting: When the temperature of a material rises above its melting point, it undergoes a phase change from solid to liquid.
- Vaporization: In addition to melting, high-energy laser beams can cause materials to vaporize directly, bypassing the liquid phase.
- Oxidation: Certain materials, especially metals, may undergo oxidation reactions when exposed to high temperatures in the presence of oxygen in the air.
- Material Removal: When a material absorbs the energy of a laser beam, it undergoes a physical change such as melting, vaporization, or a chemical reaction. The molten or vaporized material is then ejected from the cutting area by a variety of factors, including pressure from the laser beam, assist gases such as oxygen or nitrogen, and movement of the cutting head or workpiece.
- Cutting Path Control: Precisely control the path of the laser beam using a computer numerical control (CNC) system that guides the movement of a mirror or laser head along a predefined cutting path. By precisely controlling the position and intensity of the laser beam, complex shapes, and patterns can be cut with high precision.
- Cooling And Exhaust: During the cutting process, both the material and the laser system may generate heat, which needs to be dissipated to prevent overheating and maintain optimal performance. Cooling systems such as water cooling or air cooling are used to regulate the temperature of laser components, while exhaust systems remove debris and smoke generated during the cutting process to maintain a clean working environment.
By leveraging the principles of laser physics and advanced manufacturing technologies, laser cutting systems provide unparalleled precision, speed, and versatility in materials processing. Whether cutting complex designs from thin sheets of metal or shaping thick plates with complex geometries, laser cutting continues to revolutionize industries such as automotive, aerospace, electronics, and medical devices.

Types of Laser Generators
In the field of precision cutting, laser generators are the driving force behind transformative technological advances. From the versatility of CO2 laser generators to the efficiency of fiber laser generators, the robustness of disk laser generators, and the adaptability of Nd: YAG laser generators, each type has unique advantages and applications.
CO2 Laser Generator
- Introduction: CO2 lasers are one of the most widely used types of laser generators in cutting applications, using the energy of excited gas molecules to emit infrared laser light.
- Advantage:
- Versatility: CO2 laser generators reign supreme in terms of versatility, easily cutting through metal, plastic, wood, fabric, and more. This adaptability makes them indispensable in various industries.
- Accuracy: Boasting excellent beam quality, CO2 laser generators provide unparalleled accuracy to create complex designs and achieve tight tolerances.
- Cost-Effectiveness: CO2 laser generators provide a cost-effective solution for many cutting applications with relatively low operating and maintenance costs.
- Limit:
- Material Absorption: Highly reflective materials may not absorb CO2 laser energy effectively, resulting in slower cutting speeds or the need for additional processing steps.
- Maintenance Requirements: CO2 lasers require regular maintenance, including gas replenishment and optics cleaning, to maintain optimal performance.
- Applications: CO2 lasers are widely used in industries such as signage, electronics manufacturing, and prototyping. In these industries, precision cutting of various materials is crucial.
Fiber Laser Generator
- Introduction: Fiber laser generators utilize rare earth element-doped optical fiber as the gain medium to provide high efficiency and reliability in cutting applications.
- Advantage:
- High Efficiency: Fiber lasers have excellent efficiency, converting a higher proportion of electrical input into laser output. This efficiency means lower operating costs and energy consumption.
- Speed: With impressive cutting speeds, fiber lasers are the first choice in industries with high production requirements, facilitating rapid material processing.
- Beam Quality: Fiber lasers produce high-quality beams, ensuring smooth edges and precise cutting of a variety of materials.
- Limit:
- Material Limitations: While fiber laser generators are excellent at cutting metals, they may not be as effective with non-metallic materials such as ceramics or composites.
- Initial Cost: The upfront investment in fiber laser systems may be higher compared to other types, but this can often be justified by long-term cost savings.
- Applications: Fiber laser generators are widely used in metal manufacturing, automotive manufacturing, and aerospace industries for high-precision cutting of thin to medium-thickness metals.
Disk Laser Generator
- Introduction: Disk laser generators, also known as solid-state laser generators, use a thin disk-shaped gain medium doped with rare earth elements to provide high power output and reliability.
- Advantage:
- High Power Output: Disk laser generators enable high power levels, making them ideal for cutting thick materials and achieving high processing speeds.
- Reliability: Solid-state construction makes disk laser generators rugged and reliable, with minimal maintenance requirements compared to gas lasers.
- Beam Quality: Disk laser generators produce high-quality beams capable of accurately cutting complex shapes and contours.
- Limit:
- Complexity: Disk laser generator systems can be more complex to design and construct than other types of laser generators, potentially increasing initial setup and maintenance costs.
- Cooling Requirements: Disk laser generators generate large amounts of heat during operation and require efficient cooling systems to maintain optimal performance.
- Applications: Disk lasers are commonly used in applications that require high-power cutting, such as heavy metal fabrication, shipbuilding, and construction.
Nd:YAG laser generator
- Introduction: Nd: YAG laser generators utilize a solid-state crystal of neodymium-doped yttrium aluminum garnet as the gain medium, offering versatility and robustness in cutting various materials.
- Advantage:
- Versatility: Nd: YAG laser generators can cut a variety of materials, including metals, ceramics, and semiconductors, making them suitable for a variety of applications.
- Rugged and Durable: The solid-state construction makes the Nd: YAG laser generator rugged and reliable, capable of operating in harsh environments.
- Beam quality: Nd: YAG laser generators produce high-quality beams with excellent focus, enabling precise cutting even on reflective materials.
- Limit:
- Efficiency: Compared to fiber laser generators, Nd: YAG laser generators are less efficient, resulting in higher operating costs and energy consumption.
- Limited power scalability: While Nd: YAG laser generators can reach moderate power levels, they may not be suitable for high-power cutting applications.
- Applications: Nd: YAG laser generators can be used in industries such as aerospace, electronics, and medical equipment manufacturing that require precision cutting of a variety of material
Each type of laser generator makes a unique contribution to the field of precision cutting, providing tailor-made solutions for specific industry needs. By weighing the benefits, limitations, and applications of CO2 lasers, fiber lasers, disk lasers, and Nd: YAG lasers, manufacturers can make informed decisions to make their cutting processes more efficient, cost-effective, and accurate.
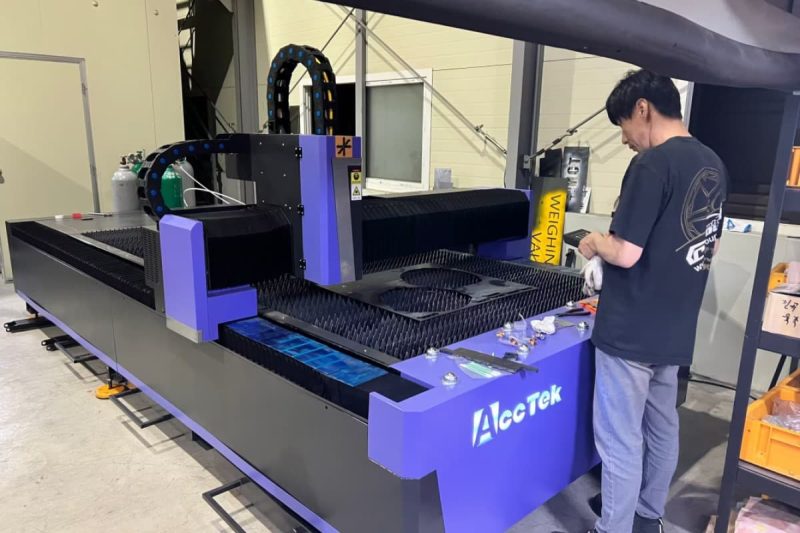
Comparative Analysis
Material Compatibility
- CO2 And Fiber Laser Generators: Excel in cutting a wide range of materials, making them versatile choices for various applications.
- Disk And Nd: YAG Laser Generators: Offer specific advantages for certain materials, such as heavy-duty metal cutting for disk laser generators and diverse material compatibility for Nd: YAG laser generators.
Cost Considerations
- CO2 Laser Generators: Recognized for cost-effectiveness, making them an economical choice for many applications.
- Fiber Laser Generators: Higher initial costs are offset by long-term savings due to high efficiency.
- Disk And Nd: YAG Laser Generators: May have higher initial costs but provide value through reliability and robustness.
Precision And Speed
- Fiber Laser Generators: Stand out for high cutting speeds and excellent beam quality, ideal for high-volume production.
- CO2 Laser Generators: Comparable precision and versatility, suitable for a broader range of materials.
Maintenance Requirements
- CO2 And Nd: YAG Laser Generators: Typically require more maintenance, including gas refills and optics cleaning.
- Fiber and Disk Laser Generators: Generally have simpler solid-state designs, leading to lower maintenance requirements.
Summarize
In the world of precision cutting, laser technology is a beacon of innovation, delivering unparalleled precision and efficiency. As we’ve explored, there are many types of laser generators, each with their unique benefits and applications:
- CO2 Laser Generator: Versatile and cost-effective, CO2 laser generators are praised for their ability to accurately cut a variety of materials.
- Fiber Laser Generators: Fiber laser generators are known for their high efficiency and fast cutting speeds, and perform well in industrial production environments, especially when it comes to cutting metal.
- Disk Laser Generators: With their rugged construction and high power output, disk laser generators are ideal for heavy-duty cutting applications such as thick metal fabrication.
- Nd:YAG Laser Generator: Nd:YAG laser generators offer versatility and reliability, making them ideal for cutting a variety of materials, including metals, ceramics, and semiconductors.
Each type of laser generator offers unique advantages to meet specific cutting requirements and material properties. Whether it’s the versatility of CO2 laser generators, the efficiency of fiber laser generators, the power of disk laser generators, or the adaptability of Nd: YAG laser generators, manufacturers have a wealth of options to optimize their cutting processes.
By understanding the nuances of each type of laser generator and performing comparative analysis, companies can make informed decisions to improve the accuracy, efficiency, and cost-effectiveness of their cutting operations. As laser technology continues to develop, we can foresee further advancements that will push the boundaries of what is possible with precision cutting and drive innovation and progress across industries.
Get Laser Cutting Solutions
Ready to revolutionize your cutting processes and achieve unparalleled precision? Our team of experts is here to guide you through the diverse landscape of laser cutting solutions, ensuring you choose the perfect fit for your unique requirements. Don’t miss the opportunity to revolutionize your cutting operations with cutting-edge laser technology. Contact us today, and let’s embark on a journey to redefine precision in your manufacturing and fabrication processes. Elevate your production capabilities with our laser cutting solutions, and witness the transformative impact on your business.
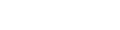
Contact information
- [email protected]
- [email protected]
- +86-19963414011
- No. 3 Zone A, Lunzhen Industrial Zone,Yucheng City , Shandong Province.
Get Laser Solutions