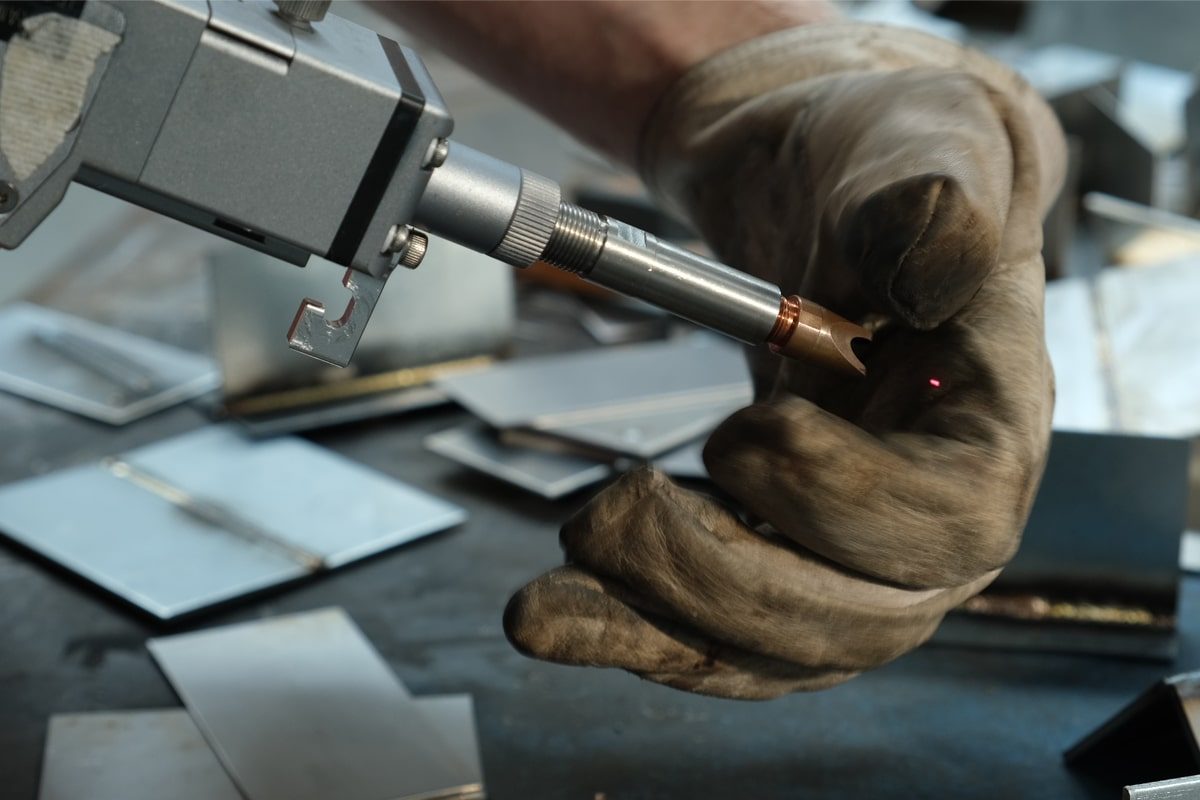
Cooling System And Maintenance Of Laser Welding Machine
Laser welding technology plays an important role in modern manufacturing, and its efficient and precise welding capabilities are widely used in various industrial fields. However, the high temperature generated during the laser welding process often causes the equipment to overheat, thus affecting the welding quality and equipment stability. To solve this problem, laser welding machines are usually equipped with a cooling system inside to effectively reduce the temperature of the equipment and ensure its stable operation.
The cooling system plays a vital role in laser welding machines. It absorbs the heat generated by the device by circulating coolant and dissipates it to the external environment, thereby preventing the device from overheating. This article will introduce the cooling system of the laser welding machine and its principles, the conditions for effective operation of the cooling system, the importance of maintaining the cooling system, and specific maintenance methods. Protect equipment from overheating damage, ensuring the stability and reliability of your laser welding process.
Table of Contents
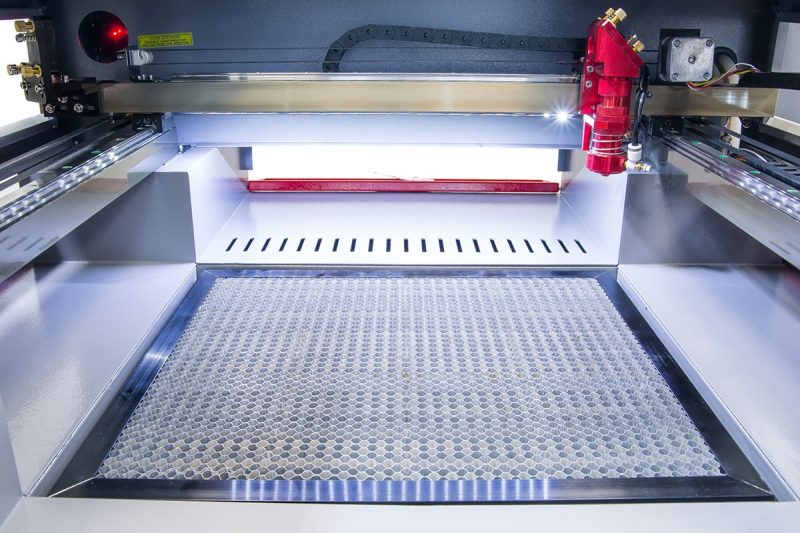
Cooling System Of Laser Welding Machine
The cooling system of the laser welding machine includes components such as a coolant, water pump, cooling pipes, radiator, and control system. The cooling sy stem effectively takes away the heat generated during the welding process through circulating coolant, maintains a stable temperature of the equipment, and ensures long-term efficient operation of the equipment. The specific composition and working principle are as follows:
Cooling System Composition
- Coolant: Water or coolant is usually used as a coolant, which can effectively absorb and remove heat.
- Water pump: Responsible for drawing coolant from the reservoir and pushing it to the cooling pipe inside the welding machine.
- Cooling pipe: transports coolant from the water pump to the welding head and welding area, taking away heat.
- Radiator: Dissipates the heat-laden coolant and releases the heat to the external environment.
- Control system: monitor and adjust the working status of the cooling system to ensure that the equipment operates within the appropriate temperature range.
How The Cooling System Works
- Heat generation: During the laser welding process, the laser beam is focused on the surface of the workpiece to generate a high-energy-density heat source, which rapidly heats up and melts the welding area.
- Coolant circulation: The coolant used in the cooling system, such as water or coolant, circulates through the piping system; the coolant is pumped in the system to the welding head and welding area, where it contacts the heat source and absorbs heat.
- Heat absorption: After the coolant contacts the heat source in the welding area, it absorbs a large amount of heat and reduces the temperature of the welding area.
- Heat dissipation: The coolant that has absorbed heat flows through the cooling pipe and brings the heat to the radiator or cooling device; the radiator or cooling device releases the heat through contact with the external environment, allowing the coolant to cool down.
- Reciprocating cycle: The coolant forms a closed loop in the cooling system and continuously circulates to continuously provide a cooling effect for the welding process; after cooling, the coolant is pumped to the welding area again and circulates back and forth to keep the temperature of the welding area stable.
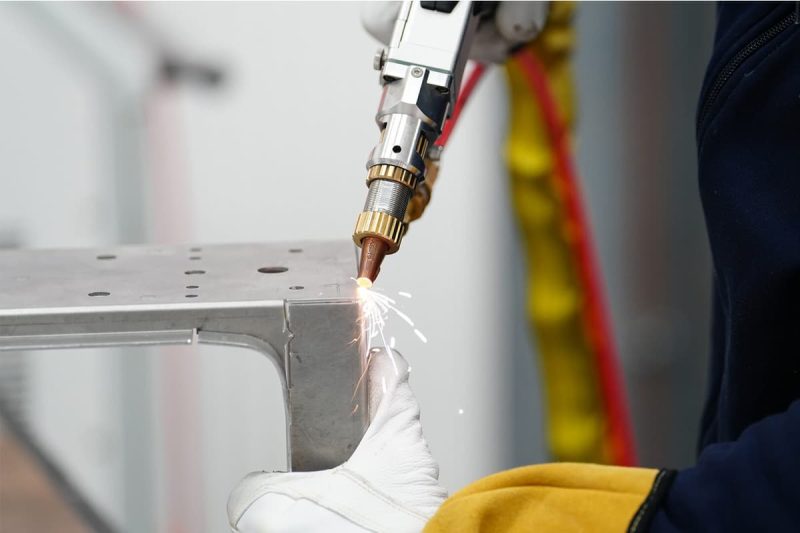
Conditions For Efficient Operation Of Cooling Systems
To ensure that the cooling system of the laser welding machine operates effectively, the following conditions need to be met:
- Sufficient cooling capacity: The cooling system needs to have sufficient cooling capacity to effectively absorb and take away the heat generated during the welding process to keep the equipment operating stably within a safe temperature range.
- Good circulation and heat dissipation performance: The coolant circulation flow of the cooling system should be unobstructed to ensure that the coolant can fully contact the welding area and absorb heat. The radiator or cooling device needs to have good heat dissipation performance and be able to quickly release the absorbed heat to the external environment to avoid overheating of the coolant and failure.
- Stable operating characteristics: The cooling system needs to have stable operating characteristics and be able to maintain the stability of the cooling effect under various working conditions and not be affected by external ambient temperature and pressure.
- Suitable coolant: Choosing the right coolant for your cooling system is very important. The coolant needs to have good thermal conductivity and cooling properties, while also having good compatibility with the equipment and piping system to avoid corrosion and damage to the equipment.
- Regular maintenance and upkeep: The cooling system needs to be cleaned, inspected, and maintained regularly to ensure that the coolant flows smoothly and the cooling pipes are not clogged. Aged or contaminated coolant must be replaced promptly to maintain the normal operation and cooling effect of the system.
- Good system design: The design of the cooling system needs to fully consider the working characteristics and heat generation rate of the equipment, and reasonably configure the cooling devices and cooling pipes to ensure that the cooling system can effectively absorb and take away the heat generated during the welding process.
- Security protection measures: The cooling system needs to be equipped with adequate safety protection measures, such as overheating protection devices and water leakage alarm systems, to ensure that timely measures are taken to protect equipment and personnel safety when abnormal conditions occur.
Maintaining the cooling system of the laser welding machine is of great significance to ensure the stable operation of the equipment, improve work efficiency, and extend the service life of the equipment. Only by regularly maintaining the cooling system to ensure its effective operation can the stability, reliability, and safety of the equipment be ensured.
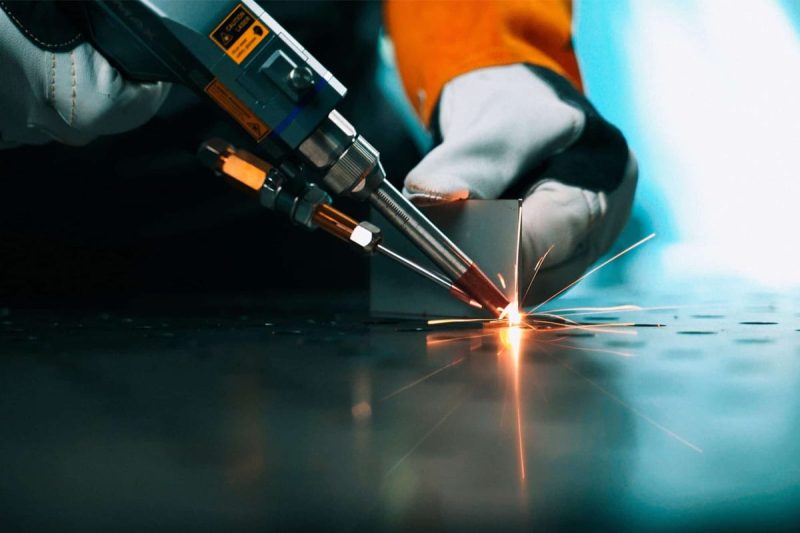
Cooling System Maintenance Methods
Specific methods for maintaining the cooling system of laser welding machines include the following aspects:
- Clean cooling pipes and radiators regularly: Cooling pipes and radiators are prone to accumulation of dust, grease, and other impurities, affecting the flow of coolant and heat dissipation. Therefore, it is very important to clean the cooling pipes and radiator regularly. You can use clean water or special cleaning agents to clean the cooling pipes and radiator surfaces to ensure they are smooth and clean.
- Check and replace coolant: The coolant will gradually degrade after long-term use, affecting its cooling effect. Therefore, check the quality and level of the coolant regularly and add or replace new coolant as necessary to ensure the normal operation and cooling effect of the cooling system. At the same time, you also need to pay attention to selecting a coolant suitable for the equipment to avoid corrosion and damage to the equipment.
- Inspect and maintain water pump: The water pump is an important part of the cooling system, responsible for pumping and pushing coolant from the reservoir to the welding head and welding area. Regularly check the working status of the water pump and the water pump drive system to ensure that the water pump is operating normally, and promptly discover and repair water pump failure or damage.
- Check the cooling system for tightness: Cooling system pipes and connections need to maintain a good seal to prevent coolant from leaking or air from entering the system. Regularly check the connections and gaskets of the cooling system to ensure they are intact and replace or repair them if necessary.
- Watch out for leaks and malfunctions: Regularly check the cooling system for water leaks or other malfunctions, such as broken pipes, failed valves, etc. Discover and resolve these issues promptly to prevent equipment damage due to insufficient cooling.
- Regular maintenance and repairs: The cooling system requires regular maintenance and upkeep, such as cleaning filters, replacing seals, checking pipe connections, etc. According to the usage of the equipment and the production environment, formulate corresponding maintenance plans and cycles to ensure the stable operation and good condition of the cooling system.
Regular cleaning, inspection, and replacement of various components of the cooling system as well as regular maintenance and repair are important methods and steps for maintaining the cooling system of the laser welding machine. Through these maintenance measures, the effective operation of the cooling system can be ensured. Extend the service life of equipment, improve work efficiency, and ensure production safety.
Summarize
In general, the cooling system of the laser welding machine is an important part of ensuring the stable operation of the equipment and protecting the equipment from overheating damage. Through reasonable design and regular maintenance, the cooling system can effectively absorb and take away the heat generated during the welding process, maintain the stable temperature of the equipment, extend the service life of the equipment, and improve the working efficiency of the equipment. Therefore, when using a laser welding machine, it is very important to maintain the cooling system in time, which will help ensure long-term stable operation of the equipment and high-quality welding results. If you are looking for a reliable way to join metals quickly and accurately, please feel free to contact AccTek Laser. We will answer any questions you have or provide professional advice on laser welding machine maintenance.
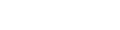
Contact information
- [email protected]
- [email protected]
- +86-19963414011
- No. 3 Zone A, Lunzhen Industrial Zone,Yucheng City , Shandong Province.
Get Laser Solutions