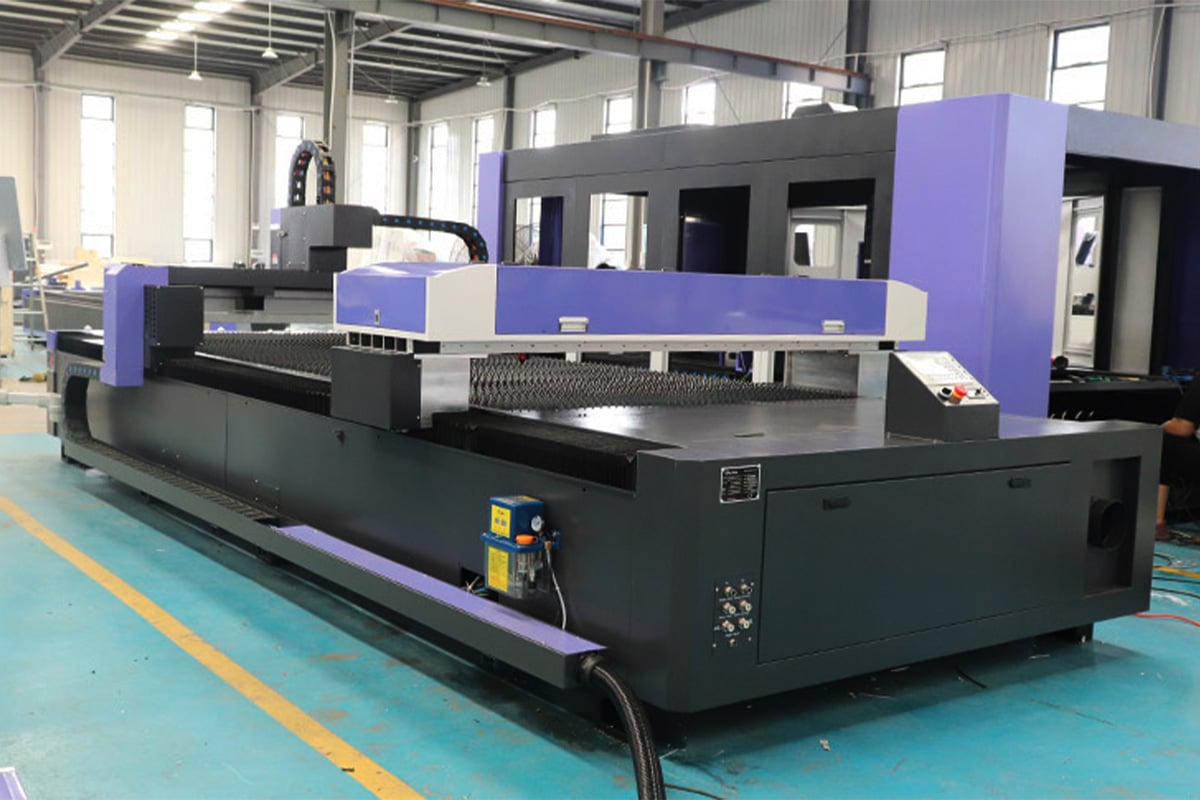
Jak dosáhnout minimální šířky řezu při řezání CO2 laserem?
Technologie řezání CO2 laserem je široce používána v procesu řezání různých materiálů, jako je zpracování kovů, plasty, dřevo, látky atd., díky svým výhodám vysoké přesnosti, vysoké rychlosti a bezkontaktnímu zpracování. Kerf Width označuje šířku řezu vytvořeného laserovým paprskem během procesu řezání. Tento ukazatel přímo ovlivňuje přesnost a kvalitu řezání. Menší šířka řezu může dosáhnout jemnějšího efektu zpracování, zlepšit přesnost produktu, snížit plýtvání materiálem a snížit výrobní náklady. Proto je důležitým kritériem pro měření kvality řezání laserem.
Kontrola šířky řezu má nejen zlepšit kvalitu produktu, ale také úzce souvisí s mírou využití materiálů, pohodlím následného zpracování a celkovou efektivitou výroby. Pro výrobce je optimalizace šířky řezu přímo spojena s kontrolou výrobních nákladů. Zejména ve velkovýrobě může příliš velká šířka řezu vést k plýtvání materiálem a ovlivnit hladký průběh následných procesů. Přesná kontrola šířky řezu je proto důležitým článkem k dosažení efektivní a levné výroby.
Obsah
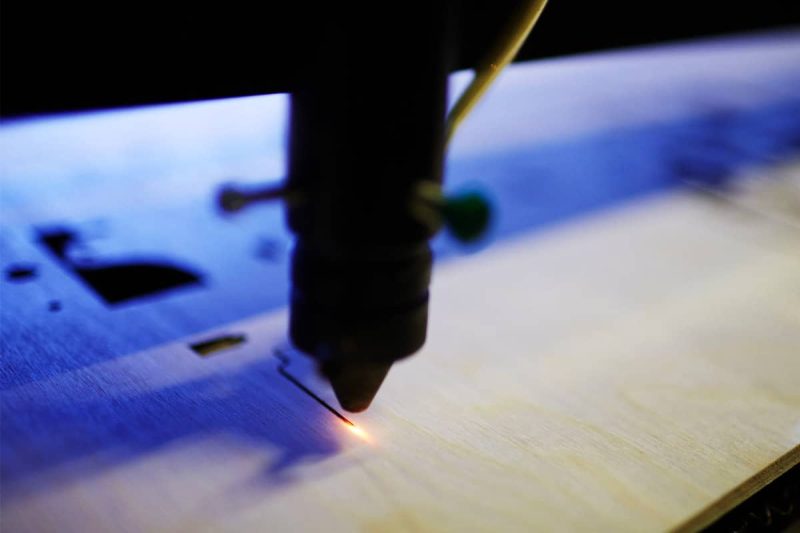
Klíčové faktory ovlivňující šířku zářezu řezání CO2 laserem
Řezný účinek technologie řezání CO2 laserem je ovlivněn mnoha faktory a šířka řezu je jedním z nejdůležitějších ukazatelů. Přiměřeným nastavením a optimalizací těchto faktorů mohou výrobci zlepšit efektivitu výroby a snížit ztráty materiálu při zajištění vysoké přesnosti. Níže je uvedeno několik klíčových faktorů ovlivňujících šířku řezu a jejich optimalizační strategie:
Velikost laserového ohniska: Velikost laserového ohniska přímo ovlivňuje průměr bodu a čím menší je bod, tím užší je šířka řezu. Čím přesnější je zaostření, tím vyšší je koncentrace energie laserového paprsku, čímž se zlepšuje přesnost řezání. Pro optimalizaci šířky řezu je důležité zvolit správnou ohniskovou vzdálenost objektivu. Obecně platí, že čočka s krátkou ohniskovou vzdáleností může poskytnout menší průměr ohniska, čímž se dosáhne jemnějšího řezného efektu. Pro různé materiály a požadavky na řezání lze velikost ohniska optimalizovat úpravou ohniskové vzdálenosti pro zajištění nejlepšího řezného efektu.
Výkon laseru: Výkon laseru přímo určuje intenzitu tepelné energie laserového paprsku, která ovlivňuje účinky tavení, odpařování a řezání během procesu řezání. Pokud je výkon laseru příliš vysoký, je snadné způsobit, že řez bude příliš široký nebo dokonce propálí materiál; pokud je výkon příliš nízký, nemusí být schopen zcela proniknout materiálem, což má za následek neúplné řezání. Rozhodující je nastavení výkonu laseru na optimální hodnotu podle tloušťky a vlastností různých materiálů. Například u silnějších materiálů je třeba příslušně zvýšit výkon, zatímco u tenkých materiálů lze výkon snížit, aby se zabránilo příliš široké incizi. Přesným nastavením výkonu mohou výrobci dosáhnout přesného a efektivního řezání.
Rychlost řezání: Při řezání laserem hraje důležitou roli také rychlost řezání. Správné zvýšení řezné rychlosti může nejen snížit tepelně ovlivněnou zónu a snížit dopad roztaveného materiálu na okraj řezu, ale také zlepšit efektivitu výroby. Pokud je však rychlost řezání příliš vysoká, laserový paprsek nemusí mít dostatek času na úplné proniknutí materiálu, což má za následek neúplné řezání; naopak příliš pomalá rychlost může způsobit, že řez bude příliš široký a vznikne přebytečná tavenina. Pro optimalizaci řezného účinku je potřeba přesně nastavit řeznou rychlost podle typu a tloušťky materiálu, aby byla zajištěna minimalizace řezné šířky.
Druh a tlak pomocného plynu: Pomocný plyn hraje zásadní roli při řezání laserem. Běžně používané pomocné plyny jsou kyslík, dusík a vzduch. Kyslík může zlepšit spalovací reakci během procesu řezání a je vhodný pro řezání materiálů, jako je železo a ocel; dusík může snížit oxidaci a je vhodný pro materiály, jako je nerezová ocel; vzduch je díky své hospodárnosti široce používán v různých materiálech. Kromě typu plynu ovlivňuje kvalitu řezu také tlak plynu. Vhodný tlak plynu může pomoci odstranit taveninu a zabránit jejímu přilnutí k okraji řezu, čímž se zmenší šířka řezu. Nižší tlak plynu může mít za následek nemožnost účinného odstranění taveniny a zvětšení šířky řezu, takže je nutné zvolit vhodný tlak plynu a typ pro optimalizaci řezného účinku.
Vlastnosti materiálu: Vlastnosti různých materiálů mohou výrazně ovlivnit přesnost řezání laserem. Vlastnosti materiálu jako rychlost absorpce, tepelná vodivost a bod tání přímo ovlivňují účinnost přenosu laserového paprsku a kvalitu řezu. Vysoce reflexní materiály (jako je hliník, měď atd.) mají tendenci způsobovat odraz a rozptyl laserového paprsku, čímž se snižuje efekt řezání. U těchto materiálů je nutné optimalizovat parametry laseru, zejména zvýšit hustotu výkonu, aby laser mohl efektivně pronikat do materiálu. Naopak materiály s nízkou odrazivostí, jako je ocel, se řežou snadněji. Při řezání různých materiálů by měli výrobci upravit řezné parametry podle vlastností materiálu, aby byla zajištěna nejlepší kvalita řezu a co nejmenší šířka řezu.
Optimalizace řezné dráhy: Optimalizace řezné dráhy je také zásadní pro řízení šířky řezu. Hladká řezná dráha může snížit chybu laserového paprsku při změně směru a vyhnout se nepravidelným řezům. Zejména při řezání složitých tvarů může rozumný návrh dráhy a omezení zatáček a nouzových zastavení výrazně zlepšit přesnost řezání. Kromě toho optimalizace strategií posuvu a zasouvání může také pomoci snížit ablaci materiálu a vyhnout se deformaci incize způsobené nadměrným zahříváním. Při navrhování dráhy je třeba se co nejvíce vyvarovat rychlých zatáček a nerovných cest, aby bylo zajištěno rovnoměrné rozložení energie během procesu řezání, a tím kontrola šířky řezu.
Přesným řízením a optimalizací těchto klíčových faktorů mohou výrobci snížit výrobní náklady, zlepšit využití materiálu a zvýšit efektivitu výroby a zároveň zajistit vysoce přesné řezání.
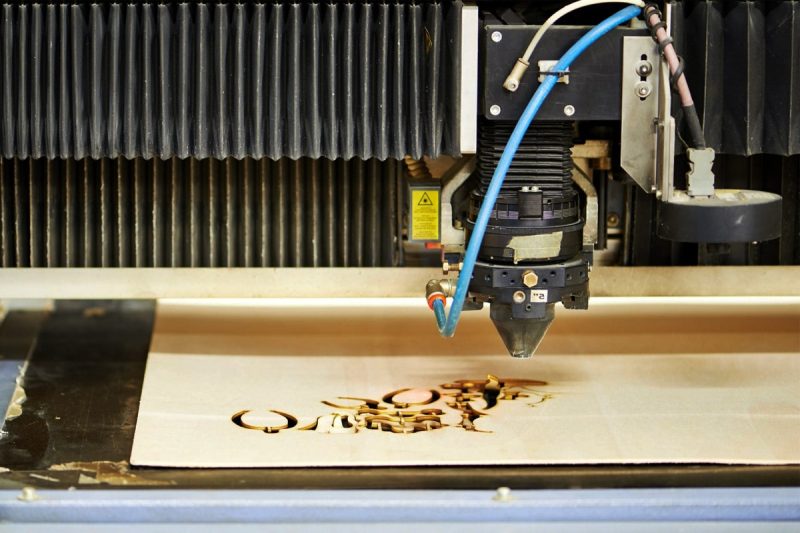
Strategie optimalizace pro dosažení minimální šířky řezu
Pro dosažení minimální šířky řezu při řezání CO2 laserem je třeba zvážit několik optimalizačních strategií. Tyto strategie mohou nejen zlepšit přesnost řezání, ale také účinně snížit plýtvání materiálem a zlepšit efektivitu výroby. Níže jsou uvedeny klíčové optimalizační metody pro dosažení minimální šířky řezu:
Optimalizace optického systému: Kvalita optického systému přímo ovlivňuje zaostřovací efekt laserového paprsku, což následně ovlivňuje jemnost řezu. Výběr vysoce kvalitní optické čočky může zajistit, že laserový paprsek bude rovnoměrně zaostřen na povrch cílového materiálu, čímž se získá stabilní a přesný řezný efekt. Použití čočky s krátkou ohniskovou vzdáleností (jako je 2,5palcová ohnisková vzdálenost) je důležitou strategií pro optimalizaci zaostření laserového paprsku. Čočka s krátkou ohniskovou vzdáleností může zaostřit menší průměr bodu, čímž se sníží difúze laserového paprsku a výrazně se zmenší šířka řezu. Menší bod může nejen zlepšit přesnost řezání, ale také snížit tepelný dopad na materiál a zajistit stabilitu během procesu řezání.
Přesně nastavte výkon a rychlost laseru: Výkon laseru a rychlost řezání jsou dva důležité faktory, které ovlivňují šířku řezu. Nejlepšího řezného efektu lze dosáhnout přesným nastavením kombinace výkonu a rychlosti laseru. Použití pulzního režimu může zkrátit dobu nepřetržitého ohřevu, a tím snížit tepelně ovlivněnou zónu (HAZ) a snížit jev tání na okraji řezu. Pulzní režim činí distribuci laserové energie rovnoměrnější a zabraňuje problémům s přehříváním způsobeným nepřetržitým výstupem vysokého výkonu. Nastavení výkonu laseru v kombinaci s tloušťkou materiálu zároveň může zajistit, že laserový paprsek může zcela proniknout materiálem a řídit šířku řezu. U tenčích materiálů přiměřeně snižte výkon, abyste zabránili nadměrné akumulaci tepla; u silnějších materiálů přiměřeně zvyšte výkon, abyste zajistili kvalitu řezu, ale stále věnujte pozornost kontrole šířky řezu.
Nastavení parametrů pomocného plynu: Pomocný plyn hraje důležitou roli při řezání CO2 laserem. Pomáhá nejen odstranit taveninu vznikající během procesu řezání, ale také kontroluje kvalitu řezání optimalizací tlaku plynu. Správné zvýšení tlaku plynu může účinně odstranit strusku produkovanou během procesu řezání a zabránit jejímu ulpívání na okraji zářezu, čímž se zachová úzká šířka zářezu. Při výběru pomocného plynu je dusík jedním z běžně používaných plynů, zejména u materiálů, které potřebují snížit oxidaci a zlepšit kvalitu řezu. Dusík dokáže nejen účinně snížit oxidaci povrchu materiálu, ale také zachovat hladkost řezu během procesu řezání, čímž se získá kvalitnější řezný efekt.
Optimalizujte software a parametry CNC: Vysoce přesné CNC systémy mohou účinně zlepšit přesnost řezání laserem a pomoci snížit odchylky řezání způsobené mechanickými chybami. Pomocí pokročilých CNC systémů můžete optimalizovat řeznou dráhu a omezit chyby způsobené změnami směru laserového paprsku. Přesné plánování dráhy pomáhá snižovat chyby způsobené zatáčkami a nerovnými cestami během řezání. Kromě toho je použití automatického zaostřovacího systému také důležitou strategií pro optimalizaci šířky řezu. Automatický zaostřovací systém může automaticky upravit polohu laserového zaostření podle tloušťky, tvaru a požadavků na řezání materiálu, aby bylo zajištěno, že laserový paprsek bude vždy zaostřen v nejlepší pozici, čímž se zabrání nerovnoměrným nebo příliš širokým řezům v důsledku nesprávné polohy zaostření.
Snížení tepelně ovlivněné zóny (HAZ): Velikost HAZ úzce souvisí s akumulací tepla během procesu řezání laserem. Nadměrné teplo může způsobit nadměrné natavení povrchu materiálu, čímž se zvětší šířka řezu a bude ovlivněna kvalita řezu. Pro snížení tepelně ovlivněné zóny je efektivní strategie vysokorychlostní řezání. Vysokorychlostní řezání může urychlit pohyb laserového paprsku, čímž se sníží akumulace tepla na povrchu materiálu a zabrání se roztavení a rozšíření hrany řezu. Při použití vysokorychlostního řezání je však nutné zajistit, aby energie laserového paprsku byla dostatečná k průniku do materiálu. Pro další optimalizaci kvality řezu lze kombinovat technologii chlazení, jako je chlazení rozprašováním nebo dvojité vstřikování plynu, které mohou účinně snížit teplotu oblasti řezání, zabránit přehřátí a zajistit přesnější a stabilnější řezný účinek.
Kombinací výše uvedených optimalizačních strategií mohou výrobci efektivně dosáhnout minimální šířky řezu při řezání CO2 laserem. Díky neustálému pokroku v technologii a neustálé optimalizaci zařízení pomohou tyto strategie dále zlepšit přesnost řezání, snížit plýtvání materiálem a zlepšit efektivitu výroby.
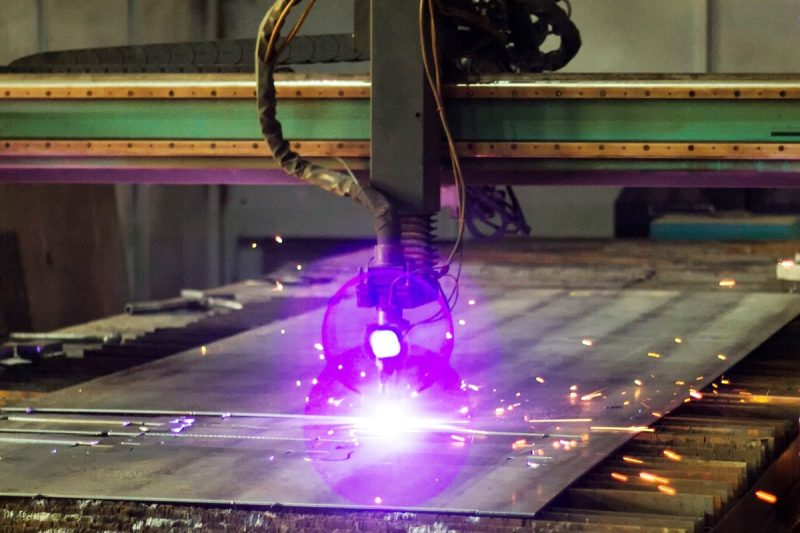
Shrnout
Dosažení minimální šířky zářezu není jen jednoduchá úprava parametrů, ale proces, který vyžaduje komplexní zvážení mnoha faktorů. Přesnou optimalizací zaostření laseru, nastavení výkonu, rychlosti řezání, typu a tlaku pomocného plynu a softwarového řízení mohou výrobci maximalizovat efektivitu výroby a snížit plýtvání materiálem a zároveň zajistit kvalitu řezání. Přesné nastavení laserového ostření může zajistit velikost místa řezu a vyhnout se nadměrnému tepelnému ovlivnění zón během procesu řezání, čímž je zajištěn jemný a hladký řez. Přesná kombinace výkonu a řezné rychlosti může zabránit nadměrnému hromadění tepla a snížit dopad taveniny na šířku řezu. Správný pomocný plyn může nejen odstranit strusku, ale také zabránit oxidaci a dále zlepšit kvalitu řezání. Využití pokročilého CNC softwaru a technologie automatického ostření zároveň dokáže průběžně optimalizovat řeznou dráhu a zaostření laserového paprsku, aby byla zajištěna stabilita a konzistentnost řezného efektu.
S neustálým vývojem technologií se také neustále zlepšuje výkon a přesnost ovládání CO2 laserových řezacích strojů. Výrobci mohou dosáhnout přesnějších řezných efektů neustálým nastavováním a optimalizací výše uvedených faktorů v kombinaci s neustálým pokrokem v optické technologii, automatizovaných řídicích systémech a efektivní technologii chlazení. V konečném důsledku dosažení minimální šířky řezu nejen zlepšuje přesnost řezání, ale přináší také vyšší efektivitu výroby, snižuje náklady na materiál a výrazně zlepšuje ekonomické výhody výrobní linky při dlouhodobém používání. Proto pro uživatele CO2 laserové řezací strojeNeustálé učení a zvládnutí těchto optimalizačních strategií bude klíčem ke zlepšení celkové výrobní kapacity a konkurenceschopnosti.
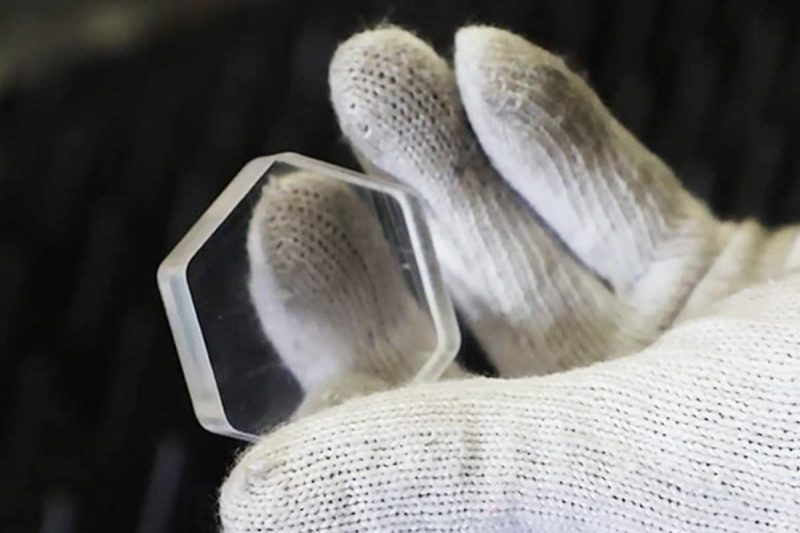
Získejte laserová řešení
AccTek Laser poskytuje vysoce přesné CO2 laserové řezací zařízení, které podporuje inteligentní zaostřování, automatickou optimalizaci dráhy a účinnou pomocnou kontrolu plynu pro zajištění minimální šířky řezu a dosažení přesného zpracování. Kontaktujte nás získat přizpůsobená řešení pro laserové řezání, která zlepší efektivitu vaší výroby a přesnost zpracování!
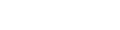
Kontaktní informace
- [email protected]
- [email protected]
- +86-19963414011
- č. 3 zóna A, průmyslová zóna Lunzhen, město Yucheng, provincie Shandong.
Získejte laserová řešení