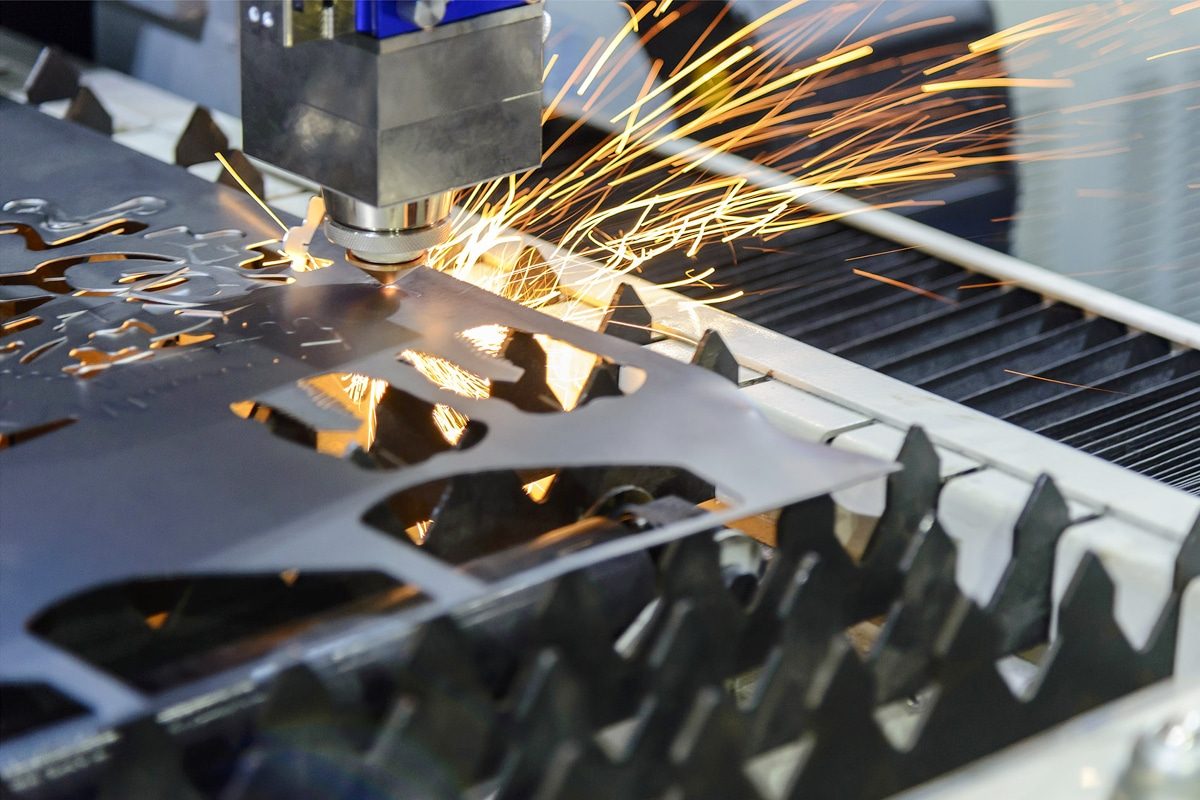
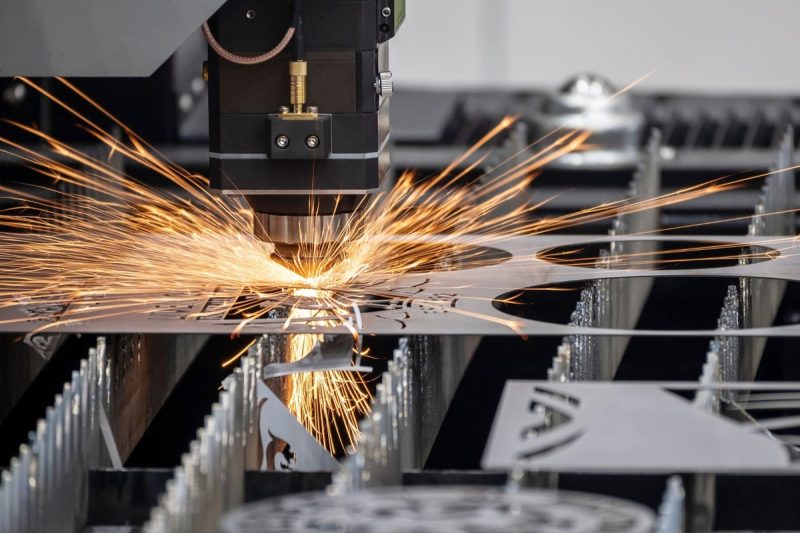
Přečtěte si o laserovém řezání
Popis řezání laserem
Typy laserů používaných v řezacích aplikacích
Vláknový laser
CO2 laser
Součásti systému laserového řezání
Typické laserový řezací systém se skládá z několika klíčových součástí, které spolupracují, aby poskytovaly přesný a účinný řezný výkon:
- Laserový zdroj: Toto je hlavní součást, která produkuje laserový paprsek. V závislosti na aplikaci může být zdrojem laseru vláknový laserový generátor, CO2 laserový generátor nebo jiný typ laserového generátoru.
- Optika: Zrcadla a čočky se používají k nasměrování a zaostření laserového paprsku na řezaný materiál. Kvalita optiky ovlivňuje přesnost a efektivitu procesu řezání.
- Řezací hlava: Řezací hlava obsahuje zaostřovací čočku a trysku, kterými je směrován laserový paprsek a pomocný plyn. Zodpovídá za udržení správné ohniskové vzdálenosti a zajištění optimálních řezných podmínek.
- Pracovní stůl: Podporuje řezaný materiál a obvykle obsahuje mechanismus pro přesun materiálu pod řezací hlavu.
- Řídicí jednotka CNC: Řídicí jednotka CNC řídí pohyb laserové řezací hlavy a obrobku po naprogramované řezné dráze pro vytvoření požadovaného tvaru a vzoru.
- Pomocný přívod plynu: Pomocný plyn napomáhá procesu řezání tím, že odfukuje roztavený materiál, ochlazuje řeznou zónu a zabraňuje oxidaci. Mezi běžné asistenční plyny patří kyslík, dusík a stlačený vzduch.
- Výfukový systém: Odstraňuje výpary a nečistoty vznikající během procesu řezání, aby se udrželo čisté pracovní prostředí a chránily optiky a laserové součásti.
- Chladicí systém: Řezání laserem generuje velké množství tepla, které je třeba odvést, aby nedošlo k poškození zdroje laseru a dalších součástí. K udržení optimálních provozních teplot se používají chladicí systémy, jako jsou vodní chladiče.
Klíčové parametry ovlivňující výkon laserového řezání
Výkon a kvalitu procesu laserového řezání může ovlivnit několik parametrů. Pochopení a optimalizace těchto parametrů může pomoci dosáhnout požadovaných výsledků:
- Výkon laseru: Výkon laserového zdroje určuje tloušťku a typ materiálu, který lze řezat. Vyšší výkony umožňují řezání silnějších materiálů, ale pro zachování kvality řezu může být nutné upravit další parametry.
- Řezná rychlost: Rychlost, kterou se řezná hlava pohybuje po obrobku. Optimální řezná rychlost zajišťuje rovnováhu mezi produktivitou a kvalitou řezu. Příliš vysoká rychlost může mít za následek neúplné řezání, zatímco příliš nízká rychlost může způsobit nadměrné zahřívání a poškození materiálu.
- Ohnisková poloha: Poloha ohniska laserového paprsku vzhledem k povrchu materiálu. Správné zaostření zajišťuje maximální hustotu energie v místě řezu, což má za následek čisté a přesné řezy. Nesprávné vyrovnání může mít za následek špatnou kvalitu řezu a sníženou účinnost.
- Typ a tlak pomocného plynu: Typ a tlak použitého pomocného plynu (kyslík, dusík nebo stlačený vzduch) má významný vliv na proces řezání. Správný výběr plynu a tlak optimalizuje odstraňování roztaveného materiálu, zabraňuje oxidaci a zlepšuje kvalitu řezu.
- Typ a tloušťka materiálu: Různé materiály a tloušťky reagují na řezání laserem různě. Při nastavování řezných parametrů je třeba vzít v úvahu vlastnosti materiálu, jako je odrazivost, tepelná vodivost a bod tání.
- Kvalita paprsku: Kvalita laserového paprsku, charakterizovaná jeho zaostřením a strukturou režimu, ovlivňuje přesnost a kvalitu řezu. Vysoce kvalitní paprsek s malou velikostí ohniska vytváří jemnější řezy s minimální šířkou řezu.
- Konstrukce trysky: Konstrukce trysky včetně jejího průměru a tvaru ovlivňuje proudění pomocného plynu a odvod roztaveného materiálu. Optimalizovaná konstrukce trysky zlepšuje účinnost a kvalitu řezání.
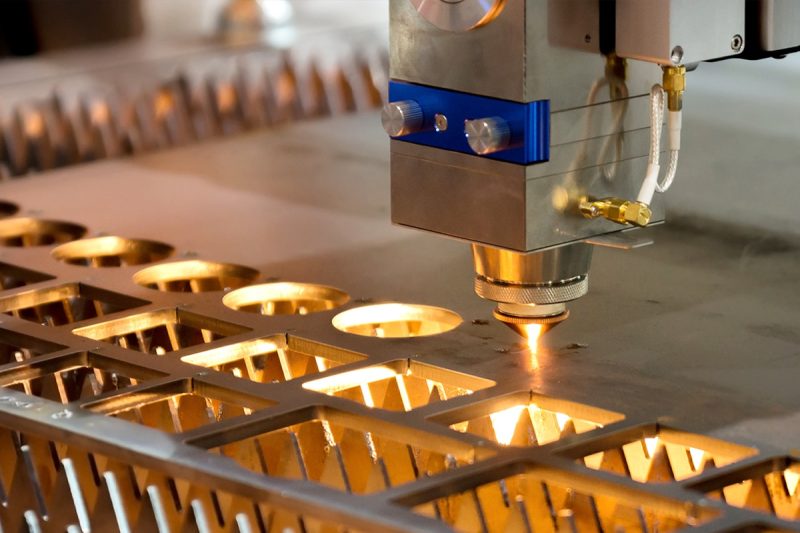
Role asistenčních plynů při řezání laserem
Odstranění roztaveného materiálu
Během procesu řezání laserem taví vysoce intenzivní laserový paprsek materiál v místě řezu. Pomocný plyn je nasměrován tryskou do oblasti řezání, kde pomáhá odstranit roztavený materiál z řezu (mezera vytvořená laserem). Efektivní odstraňování roztaveného materiálu udržuje kvalitu řezu a zabraňuje defektům.
- Efektivní tryskání: Vysoký tlak asistenčního plynu odfoukne roztavený materiál pryč od zářezu, čímž zabrání jeho opětovnému ztuhnutí na obrobek a zajistí čistý řez.
- Prevence tvorby strusky: Rychlou evakuací roztaveného materiálu asistenční plyn minimalizuje tvorbu strusky (zbytkový materiál ulpívající na spodním povrchu řezu), čímž se snižuje potřeba následného zpracování.
- Zachování šířky zářezu: Nepřetržité odstraňování roztaveného materiálu pomáhá udržovat požadovanou šířku zářezu a zajišťuje rozměrovou přesnost a přesnost konečného řezu.
Chlazení řezné zóny
Intenzivní teplo generované laserovým paprskem může způsobit významné tepelné účinky na obrobek, včetně deformace, deformace a změn vlastností materiálu. Asistenční plyn pomáhá kontrolovat tyto tepelné efekty chlazením řezné zóny.
- Odvod tepla: Proud asistenčního plynu absorbuje a odvádí přebytečné teplo v oblasti řezání, čímž zabraňuje přehřátí a minimalizuje tepelnou deformaci materiálu.
- Snížení tepelně ovlivněné zóny (HAZ): Chlazení zóny řezání pomáhá omezit velikost HAZ, zachovat mechanické vlastnosti materiálu a snížit riziko deformace nebo jiného tepelného poškození.
- Zvýšení řezné rychlosti: Účinné chlazení zvyšuje řeznou rychlost, protože je méně pravděpodobné, že se u materiálu vyvinou tepelně vyvolané vady, což vede k rychlejší a efektivnější výrobě.
Ochrana objektivu
Čočka v řezné hlavě zaostřuje laserový paprsek na obrobek. Nečistoty, jako je kouř, prach a nečistoty vznikající během procesu řezání, mohou poškodit čočku nebo snížit její výkon. Asistenční plyn chrání čočku před nečistotami.
- Kryt čočky: Pomocný plyn tvoří bariéru mezi čočkou a řeznou oblastí, čímž zabraňuje znečištění, aby se dostala na povrch čočky a usadila se na ní.
- Zachování optické kvality: Udržováním čočky čisté a bez nečistot zajišťuje asistenční plyn optimální zaostření paprsku a konzistentní řezný výkon.
- Prodloužení životnosti čočky: Prevence kontaminace snižuje opotřebení čočky, prodlužuje její životnost a snižuje náklady na údržbu.
Vylepšete reakci řezání
Pomocné plyny mohou ovlivnit chemické reakce, ke kterým dochází během řezání laserem, a tím zlepšit řezný výkon různých materiálů. Typ použitého plynu může podporovat nebo inhibovat určité reakce, které mohou ovlivnit kvalitu a účinnost řezání.
- Kyslík (O₂): Kyslík se běžně používá k řezání uhlíkové oceli. Podporuje exotermickou reakci s roztaveným kovem, vytváří dodatečné teplo, které zvyšuje řeznou rychlost. Tato reakce pomáhá vytvořit čistý řez s menším množstvím strusky, ale může způsobit oxidaci na hraně řezu.
- Dusík (N₂): Dusík je inertní plyn, který se běžně používá k řezání nerezové oceli, hliníku a dalších neželezných kovů. Zabraňuje oxidaci vytvořením inertní atmosféry kolem řezné zóny. To vytváří čistý okraj bez oxidů, takže je ideální pro aplikace, které vyžadují vysoce kvalitní povrchovou úpravu.
- Stlačený vzduch: Stlačený vzduch je cenově výhodná alternativa, kterou lze použít k řezání různých materiálů. Kombinuje vlastnosti kyslíku a dusíku a poskytuje odpovídající řezný výkon za nižší cenu. Může však vnášet nečistoty, které ovlivňují kvalitu řezu.
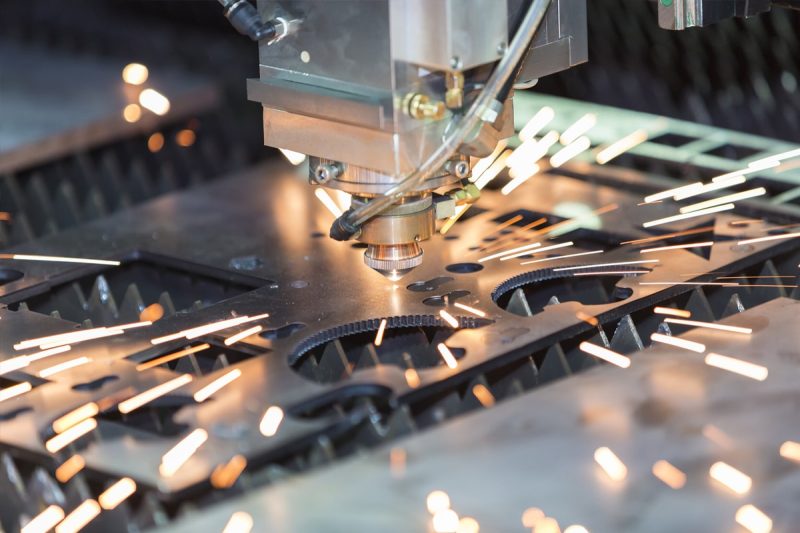
Druhy asistenčních plynů
kyslík (O₂)
Výhody
- Zvýšená rychlost řezání: Kyslík reaguje s materiálem exotermickou reakcí a uvolňuje další teplo. Toto dodatečné teplo zvyšuje řeznou rychlost, takže řezání s pomocí kyslíku je výrazně rychlejší, zejména u silnějších materiálů.
- Zlepšená účinnost: Exotermická reakce snižuje výkon laseru potřebný k řezání materiálu a zlepšuje celkovou energetickou účinnost procesu řezání.
- Čistší řezy na silných materiálech: Kyslík pomáhá vytvářet čistší řezy na silnějších materiálech, snižuje tvorbu strusky a strusky, což snižuje potřebu rozsáhlého následného zpracování.
Nevýhody
- Oxidace: Reakce mezi kyslíkem a materiálem může způsobit oxidaci řezné hrany, což má za následek hrubší povrchovou úpravu a možné problémy s korozí.
- Tepelně ovlivněná zóna (HAZ): Dodatečné teplo generované exotermickou reakcí zvětšuje velikost HAZ, což může změnit mechanické vlastnosti materiálu v blízkosti řezné hrany a způsobit problémy, jako je deformace nebo snížená strukturální integrita.
- Omezení pro neželezné kovy: Kyslík není tak účinný jako neželezné kovy, jako je hliník a měď, které nereagují tak snadno s kyslíkem.
dusík (N₂)
Výhody
- Řezání bez oxidace: Dusík je inertní plyn, který během procesu řezání nereaguje s materiálem. Tato vlastnost zabraňuje oxidaci a výsledkem je čistá, světlá hrana bez oxidu, která je ideální pro aplikace vyžadující vysoce kvalitní povrchovou úpravu.
- Vysoce kvalitní povrchová úprava: Absence oxidace má za následek hladší hranu a hladší povrchovou úpravu, což snižuje nebo eliminuje potřebu následného zpracování.
- Minimalizovaná tepelně ovlivněná zóna (HAZ): Dusík pomáhá udržovat malou tepelně ovlivněnou zónu, zachovává mechanické vlastnosti materiálu a minimalizuje tepelnou deformaci. Toho lze využít k dosažení přesných řezů a aplikací, které vyžadují úzké tolerance.
Nevýhody
- Nižší řezné rychlosti: Bez exotermické reakce zajišťované kyslíkem má řezání s pomocí dusíku obvykle za následek nižší řezné rychlosti, zejména u silnějších materiálů. Tato nižší rychlost ovlivňuje celkovou produktivitu.
- Vyšší požadavky na výkon laseru: Vzhledem k tomu, že dusík neposkytuje dodatečné teplo procesu řezání, musí laser poskytnout veškerou energii potřebnou k řezání materiálu. Tento požadavek může mít za následek vyšší spotřebu energie a provozní náklady.
- Úvahy o nákladech: Dusík může být dražší než jiné plyny a zvýšená spotřeba způsobená vyššími požadavky na výkon laseru může dále zvýšit provozní náklady.
Stlačený vzduch
Výhody
- Cenově efektivní: Stlačený vzduch je snadněji dostupný a levnější než čisté plyny, jako je dusík a kyslík. Díky tomu je ekonomickou volbou pro mnoho aplikací laserového řezání, zejména těch, které zahrnují tenčí materiály.
- Všestrannost: Stlačený vzduch lze použít k řezání široké škály materiálů, včetně měkké oceli, nerezové oceli a hliníku. Díky své všestrannosti je praktickou volbou pro univerzální řezání.
- Snížené provozní náklady: Vzhledem k tomu, že stlačený vzduch je levný a široce dostupný, použití stlačeného vzduchu může snížit celkové provozní náklady, díky čemuž je vhodný pro provozy v malém měřítku nebo projekty s ohledem na rozpočet.
- Ekologické výhody: Používání stlačeného vzduchu snižuje závislost na plyn v lahvích, což zase snižuje uhlíkovou stopu spojenou s výrobou a přepravou plynu, což je přínosem pro životní prostředí.
Nevýhody
- Nižší kvalita řezu: Kyslík a nečistoty ve stlačeném vzduchu mohou ovlivnit kvalitu řezu, což má za následek hrubší hrany, zvýšené otřepy a potenciální znečištění povrchu řezu. Tento problém je zvláště patrný v aplikacích, které vyžadují vysokou kvalitu povrchu nebo přesnost.
- Omezené rychlosti řezání: Stlačený vzduch obecně řeže nižšími rychlostmi než řezání s pomocí kyslíku, zejména u silnějších materiálů. Toto omezení ovlivňuje produktivitu a nemusí být vhodné pro velkoobjemovou výrobu.
- Nekonzistentní výsledky: Kvalita a výkon řezání stlačeným vzduchem může být nekonzistentní kvůli rozdílům ve složení a tlaku přiváděného vzduchu. Tato nekonzistence ztěžuje dosažení jednotných výsledků z jednoho řezu na druhý.
- Oxidace a tvorba strusky: Stlačený vzduch obsahuje různé plyny, včetně kyslíku, které mohou způsobit oxidaci a tvorbu strusky na řezné hraně, což vyžaduje dodatečné dodatečné zpracování k dosažení požadovaných výsledků.
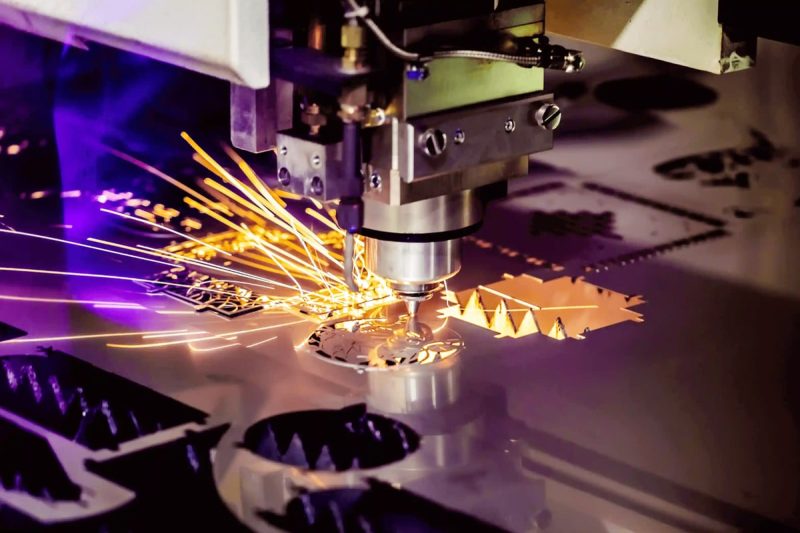
Dopad na různé materiály
Uhlíková ocel
Kyslík
- Výhody: K řezání uhlíkové oceli se často používá kyslík, protože exotermicky reaguje s materiálem. Tato reakce vytváří dodatečné teplo, které výrazně zvyšuje řeznou rychlost a účinnost. Výsledné řezy jsou typicky čisté s minimálním množstvím strusky a zvýšené teplo pomáhá řezat silnější profily z uhlíkové oceli.
- Nevýhody: Exotermická reakce s kyslíkem způsobuje oxidaci, která, pokud není ošetřena, může mít za následek hrubší povrchovou úpravu a možnou korozi. Tepelně ovlivněná zóna (HAZ) je také větší, což může ovlivnit mechanické vlastnosti materiálu v blízkosti řezné hrany.
Dusík
- Výhody: Dusík nereaguje s uhlíkovou ocelí, zabraňuje oxidaci a vytváří čistý řez bez oxidů. Výsledkem je kvalitní povrchová úprava a menší HAZ, což zachovává mechanické vlastnosti materiálu.
- Nevýhody: Neexistence exotermické reakce znamená, že řezání s pomocí dusíku je pomalejší než řezání s pomocí kyslíku. Pro dosažení stejné řezné rychlosti je potřeba vyšší výkon laseru, což zvyšuje provozní náklady.
Stlačený vzduch
- Výhody: Stlačený vzduch je cenově výhodná alternativa pro řezání uhlíkové oceli. Dosahuje rovnováhy mezi cenou a výkonem a je vhodný pro řezání tenčích profilů z uhlíkové oceli.
- Nevýhody: Kyslík ve stlačeném vzduchu může způsobit určitou oxidaci a tvorbu strusky, což ovlivňuje kvalitu řezu. Rychlost a kvalita řezu jsou obecně nižší než při použití čistého kyslíku nebo dusíku.
Nerezová ocel
Kyslík
- Výhody: Kyslík lze použít k řezání nerezové oceli, což poskytuje vysoké řezné rychlosti díky exotermické reakci. Tato reakce může také pomoci dosáhnout čistých řezů s minimem strusky.
- Nevýhody: Použití kyslíku může způsobit oxidaci, která může vést ke změně barvy hran a potenciálním problémům s korozí. Oxidová vrstva může vyžadovat dodatečné dodatečné zpracování pro dosažení požadované kvality povrchu.
Dusík
- Výhody: Dusík je preferovaný plyn pro řezání nerezové oceli, protože zabraňuje oxidaci, což má za následek čistý, lesklý okraj bez oxidu. Inertní povaha dusíku vytváří vysoce kvalitní řezy s minimální potřebou následného zpracování. Dusík také pomáhá udržovat mechanické vlastnosti materiálu tím, že minimalizuje tepelně ovlivněnou zónu.
- Nevýhody: Dusík má nižší řezné rychlosti a vyžaduje vyšší výkon laseru než kyslík, což má za následek zvýšenou spotřebu energie a provozní náklady.
Stlačený vzduch
- Výhody: Stlačený vzduch lze použít k řezání tenčích profilů nerezové oceli. Je nákladově efektivnější než čistý plyn a je životaschopnou možností pro aplikace, které nevyžadují vysokou přesnost.
- Nevýhody: Kyslík ve stlačeném vzduchu může způsobit oxidaci a tvorbu strusky, což ovlivňuje kvalitu řezu. Okraj může vyžadovat dodatečné čištění a konečnou úpravu po řezu.
Hliník a neželezné kovy
Kyslík
- Výhody: Kyslík se obecně nedoporučuje pro řezání hliníku a jiných neželezných kovů kvůli jejich vysoké odrazivosti a nízké absorpci laserového paprsku. V některých případech však může kyslík pomoci řezat silnější části podporou exotermické reakce.
- Nevýhody: Kyslík může způsobit silnou oxidaci, což má za následek drsný a porézní povrch řezu. Tato oxidace může negativně ovlivnit vlastnosti a vzhled materiálu, což vyžaduje rozsáhlé následné zpracování.
Dusík
- Výhody: Dusík je velmi účinný pro řezání hliníku a jiných neželezných kovů. Zabraňuje oxidaci, výsledkem je čistý, světlý a vysoce kvalitní okraj. Dusík také pomáhá minimalizovat tepelně ovlivněnou zónu a zachovává mechanické vlastnosti materiálu.
- Nevýhody: Řezání s pomocí dusíku je pomalejší než použití kyslíku a vyžaduje vyšší výkon laseru k řezání materiálu, což zvyšuje provozní náklady.
Stlačený vzduch
- Výhody: Stlačený vzduch je cenově výhodná volba pro řezání tenčích profilů hliníku a neželezných kovů. Může poskytnout uspokojivý řezný výkon pro aplikace, kde přesnost není kritická.
- Nevýhody: Kyslík ve stlačeném vzduchu může způsobit oxidaci a tvorbu strusky, což ovlivňuje kvalitu řezu. Hrany mohou vyžadovat dodatečné dodatečné zpracování, aby se dosáhlo požadované konečné úpravy.
Nekovové materiály
Kyslík
- Výhody: Kyslík lze použít k řezání nekovových materiálů, jako je dřevo, akryl a plast. Exotermická reakce s kyslíkem může u některých materiálů zvýšit řeznou rychlost a účinnost.
- Nevýhody: Použití kyslíku může způsobit popálení a spálení materiálů, jako je dřevo a akryl, což negativně ovlivňuje kvalitu povrchu. To může mít za následek potřebu dalších dokončovacích procesů pro dosažení požadovaného vzhledu.
Dusík
- Výhody: Dusík se dobře hodí pro řezání nekovových materiálů, jako jsou plasty a keramika, které je nutné chránit před oxidací. Zabraňuje změně barvy a vytváří čisté, vysoce kvalitní okraje a zároveň minimalizuje tepelné poškození.
- Nevýhody: Řezání s pomocí dusíku může být pomalejší než kyslík a vyžaduje vyšší výkon laseru k dosažení požadované rychlosti řezání.
Stlačený vzduch
- Výhody: Stlačený vzduch je cenově výhodné řešení pro řezání nekovových materiálů a poskytuje odpovídající řezný výkon pro různé aplikace. Je vhodný pro aplikace, kde přesnost a kvalita nejsou rozhodující.
- Nevýhody: Nečistoty ve stlačeném vzduchu mohou ovlivnit kvalitu řezu, což má za následek drsné hrany a potenciální znečištění. Kvalita a rychlost řezu nemusí být srovnatelná s čistými plyny, jako je kyslík nebo dusík.
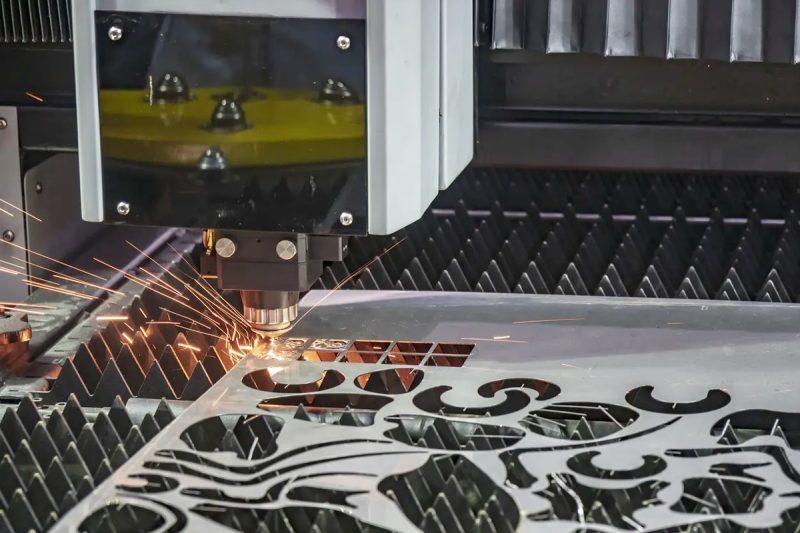
Optimalizace asistenčního výběru plynu
Typ a tloušťka materiálu
Typ a tloušťka řezaného materiálu jsou hlavními faktory při výběru pomocného plynu. Různé materiály reagují odlišně na různé plyny, což ovlivňuje kvalitu řezu a účinnost.
- Uhlíková ocel: Kyslík je často první volbou pro řezání uhlíkové oceli, protože reaguje exotermicky a zvyšuje řeznou rychlost a efektivitu. U tlustších uhlíkových ocelí může kyslík poskytnout teplo potřebné k efektivnímu řezání materiálu. U tenčích uhlíkových ocelí lze použít dusík k dosažení čistého řezu bez oxidace, i když pomaleji.
- Nerezová ocel: Dusík je ideální pro řezání nerezové oceli, protože zabraňuje oxidaci a vytváří vysoce kvalitní, hladké ostří. U velmi silné nerezové oceli lze ke zvýšení řezné rychlosti použít kyslík, ale způsobí oxidaci, která vyžaduje dodatečné zpracování.
- Hliník a neželezné kovy: Dusík je první volbou pro řezání hliníku a neželezných kovů, aby se zabránilo oxidaci a dosáhlo se čistého řezu. Pro méně kritické aplikace může být stlačený vzduch cenově výhodnou alternativou, i když může způsobit určitou oxidaci.
- Nekovové materiály: Pro řezání nekovů, jako jsou plasty, keramika a dřevo, se často používá dusík, aby se zabránilo změně barvy a dosáhlo se vysoce kvalitní hrany. Kyslík lze použít k rychlejšímu řezání určitých nekovů, ale může způsobit popálení nebo spálení.
Požadovaná kvalita řezu
Požadovaná kvalita řezu je klíčovým faktorem při výběru vhodného pomocného plynu. Přesné aplikace obvykle vyžadují vysoce kvalitní řez s minimální oxidací a hladkými hranami.
- Vysoce kvalitní povrchová úprava: Dusík je často nejlepší volbou pro aplikace, které vyžadují přesné, čisté řezy bez oxidace. Zabraňuje oxidaci, výsledkem jsou hladké hrany a vysoce kvalitní povrchová úprava.
- Obecná kvalita: Kyslík může zajistit vysoce kvalitní řez s minimální struskou, ale hrany mohou vyžadovat dodatečné čištění kvůli oxidaci. Stlačený vzduch může být vhodný pro méně kritické aplikace, kde není nutná povrchová úprava nejvyšší kvality.
Rychlost a účinnost řezání
Rychlost a účinnost řezání jsou ovlivněny typem použitého pomocného plynu. Cílem je dosáhnout co nejvyšší rychlosti bez snížení kvality řezu.
- Maximální rychlost: Poskytuje nejvyšší řezné rychlosti pro uhlíkovou ocel a silnější materiály díky exotermické reakci kyslíku, která dodává procesu řezání další teplo.
- Vyvážená rychlost a kvalita: Dusík vytváří rovnováhu mezi rychlostí a vysoce kvalitními řezy, i když může vyžadovat vyšší výkon laseru a řezání nižší rychlostí ve srovnání s kyslíkem.
- Nákladově efektivní rychlost: Stlačený vzduch nabízí kompromis mezi rychlostí a cenou, vhodný pro aplikace, kde jsou přijatelné střední řezné rychlosti a přiměřená kvalita.
Úvahy o nákladech
Cena je důležitým faktorem při výběru plynu, který ovlivňuje provozní náklady a celkovou nákladovou efektivitu.
- Snížené provozní náklady: Stlačený vzduch je nejekonomičtější volbou, protože je snadno dostupný a levnější než čisté plyny, jako je kyslík a dusík. Je ideální pro řezání méně kritických materiálů nebo když jsou prioritou rozpočtová omezení.
- Vyšší kvalita a vyšší náklady: Dusík, i když je dražší, poskytuje lepší kvalitu řezu. Dodatečné náklady jsou odůvodněny zlepšenou kvalitou a sníženou potřebou následného zpracování.
- Vyvážení nákladů a efektivity: Kyslík nabízí střední cestu, poskytuje vysoké řezné rychlosti a přiměřenou kvalitu za mírnou cenu. Je vhodný pro mnoho průmyslových aplikací, kde je důležitá rychlost i kvalita.
Požadavky na následné zpracování
Potřeby následného zpracování mohou ovlivnit pomocný výběr plynu, protože některé plyny vytvářejí čistší řezy, což může snížit dokončovací práce.
- Minimální následné zpracování: Dusík vytváří čisté řezy bez oxidace, což snižuje potřebu rozsáhlého následného zpracování a šetří čas a náklady na dokončovací operace.
- Mírné následné zpracování: Řezání kyslíkem může vyžadovat další kroky k odstranění oxidů a dosažení požadované povrchové úpravy. Vyšší řezné rychlosti však mohou kompenzovat některé dodatečné náklady.
- Zvýšené následné zpracování: Stlačený vzduch může způsobit více strusky a oxidace, což vyžaduje rozsáhlejší následné zpracování pro čištění a konečnou úpravu hrany. To může zvýšit celkovou dobu výroby a náklady.
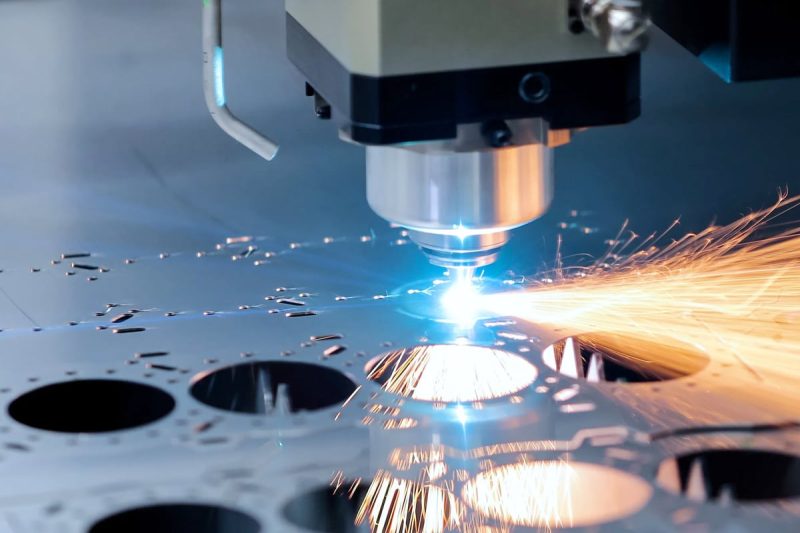
souhrn
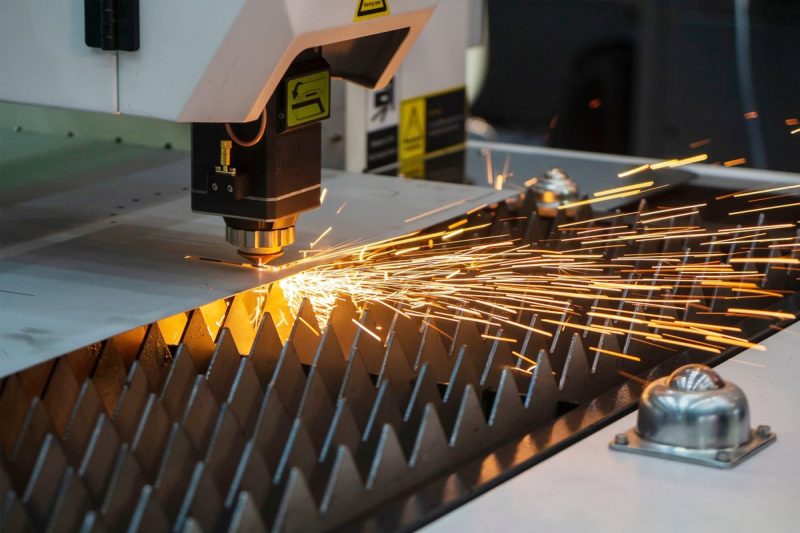
Získejte řešení pro řezání laserem
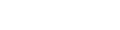
- [email protected]
- [email protected]
- +86-19963414011
- č. 3 zóna A, průmyslová zóna Lunzhen, město Yucheng, provincie Shandong.