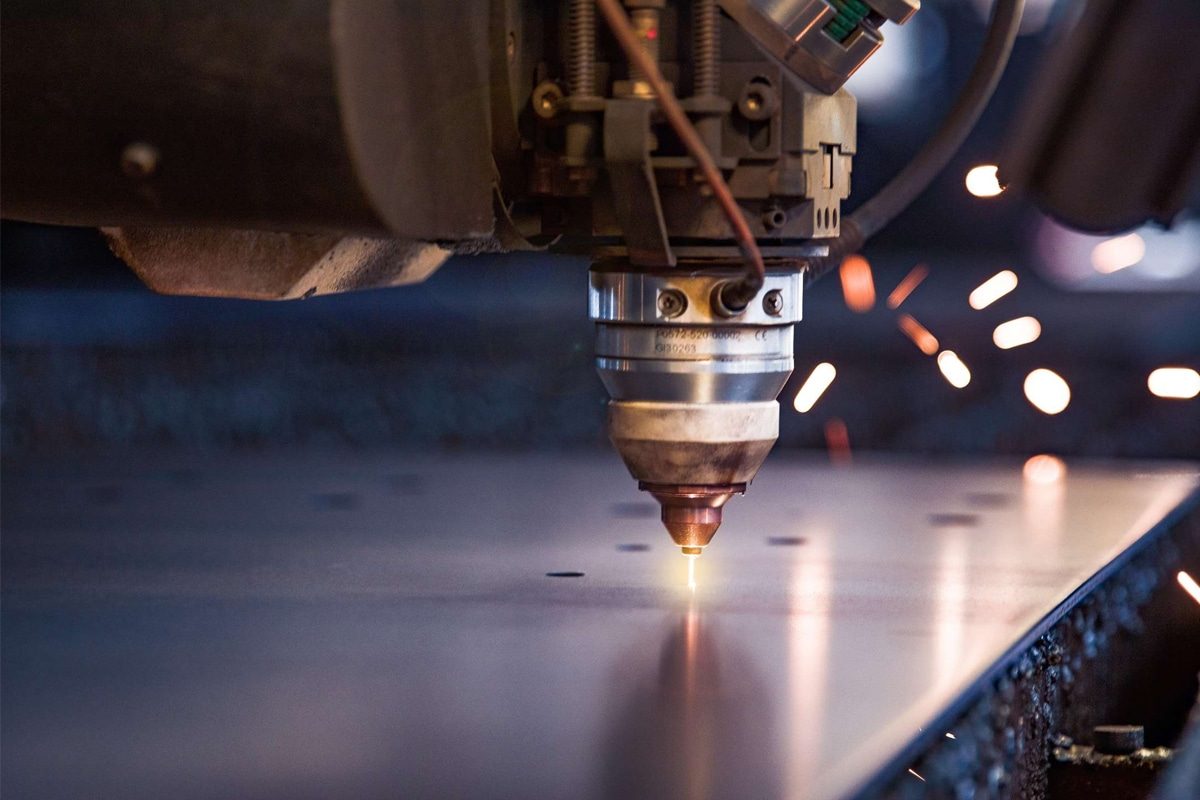
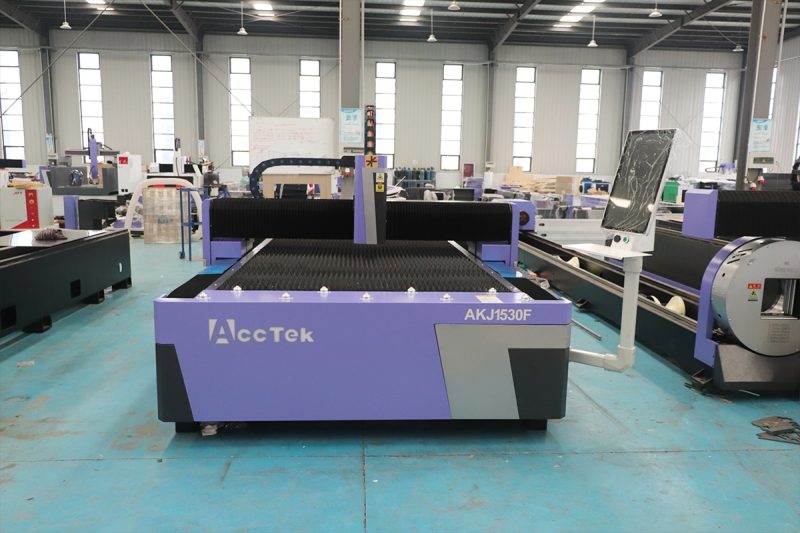
Importance of Daily Maintenance
Routine maintenance of your fiber laser cutting machine can ensure consistent performance and prevent operational issues. Here’s why it’s crucial:
- Optimal Performance: Regular maintenance keeps the machine running smoothly and efficiently. By checking and cleaning critical components like the laser lens, nozzles, and cutting bed, you ensure that the machine operates at its best capacity, delivering precise cuts with minimal errors. Routine tasks such as checking for loose parts or lubricating moving components ensure that the machine performs with maximum speed and accuracy.
- Extended Lifespan: Like any complex piece of equipment, fiber laser cutting machines benefit from regular upkeep, which can significantly extend their operational lifespan. Preventative maintenance helps avoid unnecessary wear and tear on essential parts, reducing the risk of early failure. Simple tasks, such as cleaning and lubrication, help protect the machine’s components and preserve their integrity, ensuring the machine functions effectively for years.
- Safety Enhancement: Safety is a top priority when working with powerful laser machines. Daily maintenance ensures that safety systems like interlocks, emergency stops, and protective shields are in good working condition. Regular checks help identify potential hazards, such as worn-out parts or gas leaks, which can pose risks to operators. By performing routine inspections, you can prevent accidents and maintain a safer work environment.
- Cost Efficiency: Neglecting daily maintenance can lead to costly breakdowns and repairs. By investing a small amount of time each day in routine tasks, you reduce the likelihood of major failures that require expensive parts or long downtime. Additionally, proper maintenance can help the machine run more efficiently, reducing power consumption and extending the lifespan of consumables, ultimately saving money in the long run.
- Quality Assurance: Maintaining high product quality is key to satisfying customer demands. Daily maintenance ensures that your fiber laser cutting machine consistently delivers clean, precise cuts with minimal waste. Tasks like cleaning the optics and checking the gas supply help maintain cutting accuracy, preventing defects or inconsistencies in your output. A well-maintained machine contributes to higher production standards and customer satisfaction.
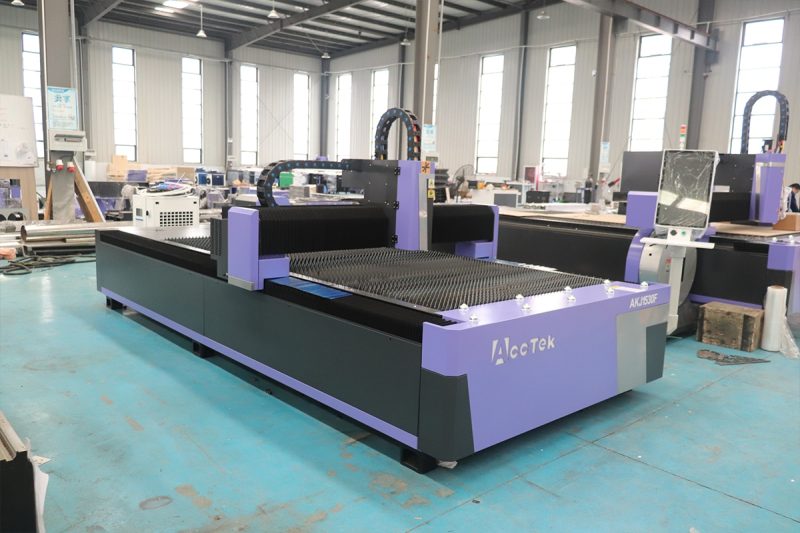
Safety Precautions
Personal Protective Equipment (PPE)
Using appropriate PPE is crucial to prevent injuries from laser radiation, flying debris, sharp metal parts, and chemical exposure during maintenance. The following gear must be worn by anyone maintaining or inspecting a fiber laser cutting machine:
- Safety Glasses or Goggles: Protects the eyes from laser reflections, dust, and debris. Use laser-rated eyewear when working near the laser source.
- Gloves: Cut-resistant gloves help prevent injuries from handling sharp metal pieces, while chemical-resistant gloves are recommended when working with lubricants, coolants, or cleaning agents.
- Protective Clothing: Flame-resistant, long-sleeved clothing shields the body from sparks or heat exposure during cleaning or lubrication.
- Safety Footwear: Steel-toed shoes protect feet from injuries caused by heavy objects, such as metal sheets or machine components.
- Ear Protection: In high-noise environments, such as workshops with multiple machines, earplugs or earmuffs protect hearing from long-term damage.
Machine Lockout/Tagout Procedures
Lockout/tagout (LOTO) procedures ensure the machine is completely de-energized and safe to maintain, preventing accidental startup during maintenance. Following these steps minimizes the risk of injury from electrical systems or moving parts.
- Shutdown: Use the control panel to turn off the machine following the manufacturer’s recommended shutdown process.
- Isolation: Disconnect the machine from its primary power source to prevent accidental reactivation. This includes electrical power, gas lines, and pneumatic systems.
- Release Stored Energy: Ensure that any residual energy is discharged. This applies to electrical circuits, compressed air, or hydraulic systems, which can remain energized after shutdown.
- Lockout/Tagout: Place locks on the machine’s energy-isolating devices and attach warning tags indicating that maintenance is in progress. Only authorized personnel should have access to the keys.
- Verification: Confirm that the machine is fully powered down by attempting to start it through the control panel. If it does not activate, the lockout procedure is successful.
- Communication: Notify all relevant personnel that the machine is undergoing maintenance. Display clear signage near the machine to prevent unauthorized access or tampering.
Environmental Considerations
The environment where the machine is maintained plays an important role in operator safety. Ensuring the right conditions helps prevent accidents and supports thorough inspection and cleaning.
- Ventilation: Proper ventilation prevents the buildup of hazardous fumes from assist gases or chemical cleaners used during maintenance. Ensure that the workspace is equipped with adequate ventilation systems or fume extraction units.
- Lighting: Adequate lighting ensures that operators can clearly inspect the machine’s components, identify issues, and safely perform maintenance tasks. Poor visibility can lead to missed defects or accidents.
- Cleanliness: A clean workspace minimizes the risks of slips, falls, and equipment malfunctions. Regularly remove dust, metal scraps, and debris from the work area and cutting bed. Keep tools and consumables organized to prevent clutter.
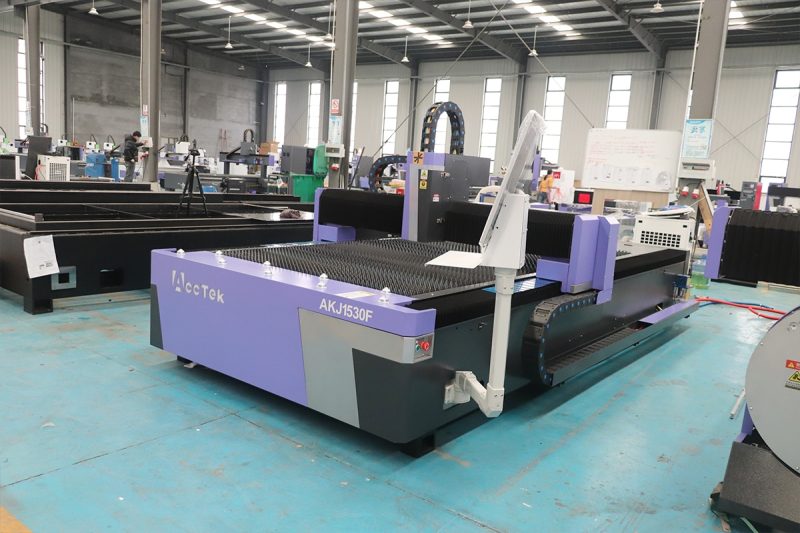
Daily Maintenance Checklist
External Inspection
Cleaning the Machine Surface
- Use a soft cloth or an antistatic wipe to remove dust and debris from the machine’s exterior.
- Clear any metal scraps or slag from the cutting bed to avoid interference with operations.
- Wipe down the control panel to prevent dirt accumulation and ensure smooth operation.
Checking for Loose Parts
- Inspect bolts, nuts, and screws to ensure they are tight, especially around moving parts.
- Verify that protective guards, shields, and covers are secure and intact.
- Check cable routing and attachments to avoid entanglement or damage during operation.
Optical Components Inspection
Cleaning the Protective Lens
- Use a blower to remove loose particles and clean the lens with a lint-free cloth and optical cleaner.
- Avoid touching the lens surface with bare hands to prevent smudges or contamination.
- Inspect the lens for scratches, cracks, or dirt buildup that could impact beam quality.
Checking the Fiber Cable
- Inspect the fiber cable for wear, kinks, or cuts along its length.
- Ensure connectors are clean, dry, and properly attached at both ends.
- Verify that the cable routing avoids sharp bends that could damage the internal fiber.
Mechanical Components Inspection
Guide Rails and Linear Bearings
- Wipe down the guide rails to remove dust and metal particles.
- Inspect rails and bearings for signs of corrosion or wear.
- Check the alignment of rails to ensure smooth movement during cutting.
Drive Systems
- Inspect drive belts for proper tension and adjust as needed.
- Examine rack-and-pinion systems for proper engagement and cleanliness.
- Monitor motor sounds for unusual noises that could indicate potential issues.
Electrical Components Inspection
Control Panel
- Ensure all buttons, switches, and touch screens respond correctly.
- Check the panel for error messages and resolve them promptly.
- Wipe the panel to keep it clean and maintain touch sensitivity.
Wiring and Connections
- Inspect wires for fraying, damage, or loose connections.
- Verify that all electrical connections are secure and free from corrosion.
- Ensure cables are routed properly to prevent wear or disconnection.
Electrical Components Inspection
Wiring and Connections
- Inspect wires for fraying, damage, or loose connections.
- Verify that all electrical connections are secure and free from corrosion.
- Ensure cables are routed properly to prevent wear or disconnection.
Wiring and Connections
- Inspect wires for fraying, damage, or loose connections.
- Verify that all electrical connections are secure and free from corrosion.
- Ensure cables are routed properly to prevent wear or disconnection.
Cooling System Maintenance
Checking the Chiller Unit
- Confirm that the chiller maintains the required temperature range for the laser source.
- Look for any coolant leaks around the chiller or hoses.
- Clean or replace air filters to maintain airflow and cooling efficiency.
Coolant Levels and Quality
- Check the coolant reservoir and top up if necessary with the correct coolant.
- Monitor coolant quality for discoloration or contamination and replace if needed.
- Follow the manufacturer’s guidelines for routine coolant replacement.
Gas Supply Maintenance
Gas Pressure and Flow Checks
- Monitor gas supply gauges to ensure the pressure is within the recommended range.
- Adjust gas regulators as needed to maintain the required flow rates.
- Perform a leak test using soapy water to detect any gas leaks.
Inspecting Gas Lines and Fittings
- Inspect gas hoses for cracks, kinks, or wear.
- Ensure all fittings are tight and secure to prevent gas loss.
- Verify that safety devices, such as flashback arrestors, are functioning properly.
Laser Source Maintenance
Monitoring Laser Output
- Use diagnostic tools to check laser output power and ensure it is stable.
- Observe the laser beam for irregularities that may indicate alignment issues.
- Review error logs for any warnings related to the laser source.
Warm-Up Procedures
- Follow the manufacturer’s recommended warm-up process to stabilize the laser.
- Start with low power and gradually increase to the required levels for cutting.
- Monitor for unusual noises or warnings during the warm-up phase.
Lubrication of Moving Parts
Lubricant Selection
- Use lubricants specified by the manufacturer to avoid compatibility issues.
- Ensure the lubricant is appropriate for high-speed components like guide rails and bearings.
Application Points
- Apply lubricant to guide rails, linear bearings, and ball screws to reduce friction.
- Avoid over-lubrication, which can attract dust and debris.
Frequency
- Perform lubrication daily or according to the manufacturer’s guidelines.
- Adjust the lubrication schedule based on usage and environmental conditions.
Software and Control System Checks
Software Updates
- Check for any firmware or software updates provided by the manufacturer.
- Install updates promptly to maintain system functionality and security.
Backup Settings
- Regularly back up machine parameters and software settings.
- Store backups securely to ensure quick recovery if settings are lost.
Calibration Verification
- Verify that all calibration settings are accurate and perform adjustments if necessary.
- Test the machine’s alignment to ensure cutting precision.
Housekeeping
Work Area Cleanliness
- Keep the area around the machine free from debris and metal scraps.
- Ensure that tools and consumables are organized to avoid clutter and confusion.
- Regularly wipe down surfaces to prevent dust buildup.
Waste Disposal
- Dispose of scrap materials and used consumables promptly and appropriately.
- Follow local environmental regulations for the disposal of hazardous waste.
Environmental Conditions
- Maintain optimal temperature and humidity levels in the workspace.
- Ensure the work area is well-ventilated to prevent the buildup of fumes and gases.
- Monitor environmental factors to prevent condensation, which can damage sensitive components.
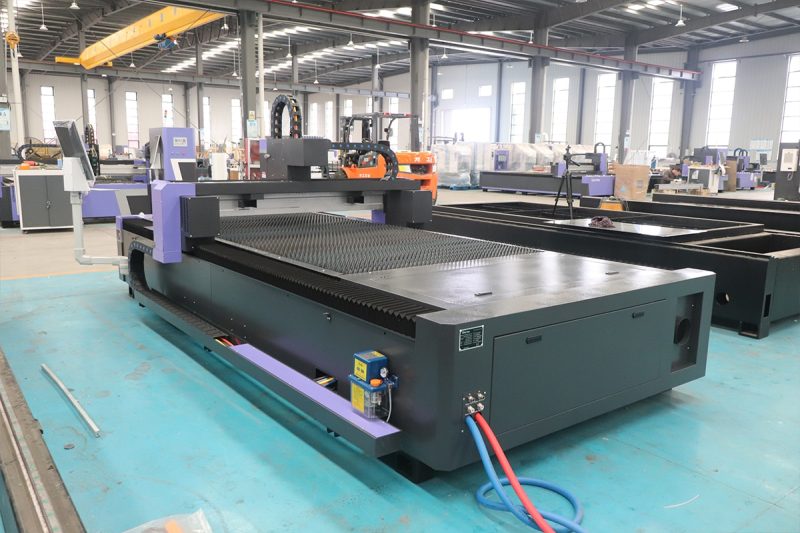
Operational Checks After Maintenance
Test Runs
Dry Run
- Perform a dry run (without material) to ensure the cutting head, guide rails, and other moving parts are operating smoothly.
- Monitor the machine’s movement to ensure it follows the programmed path without delays or irregularities.
- Verify that there are no warning messages or unusual behavior on the control panel during the dry run.
Sample Cuts
- Use a small piece of scrap material to perform sample cuts and test the machine’s cutting performance.
- Adjust laser power, speed, and gas flow as needed to ensure optimal results.
- Evaluate the cut edges for precision and cleanliness to confirm the machine is ready for production.
Monitoring for Anomalies
Sound Observation
- Listen for unusual sounds such as grinding, hissing, or knocking, which could indicate mechanical issues or air leaks.
- Pay attention to any sudden changes in the sound of the laser or motors, as these may signal a problem with alignment or bearings.
Vibration Check
- Monitor the machine for excessive vibrations during movement, which could indicate misaligned components or loose parts.
- Excessive vibration can reduce cut quality and damage mechanical components if not addressed promptly.
Visual Inspection
- Observe the machine during operation to ensure the laser beam, cutting head, and guide rails are functioning properly.
- Check for unexpected sparks, gas leaks, or misaligned cuts that could signal underlying issues.
- Verify that the assist gas is flowing correctly and that no abnormal buildup of debris is occurring.
Quality Assessment
Cut Analysis
- Inspect the sample cuts for edge quality, looking for clean, smooth cuts with minimal dross or slag.
- Ensure the kerf width (cut width) is consistent and suitable for the specific material and project.
- Identify any burn marks, rough edges, or signs of over- or underpowered cuts, and make necessary adjustments to the laser settings.
Dimensional Accuracy
- Use calipers or measuring tools to verify the accuracy of the cut dimensions against the programmed specifications.
- Confirm that the machine maintains precision, particularly for intricate or fine details.
- Ensure that repeated cuts produce consistent results, indicating the machine’s settings and alignment are correct.
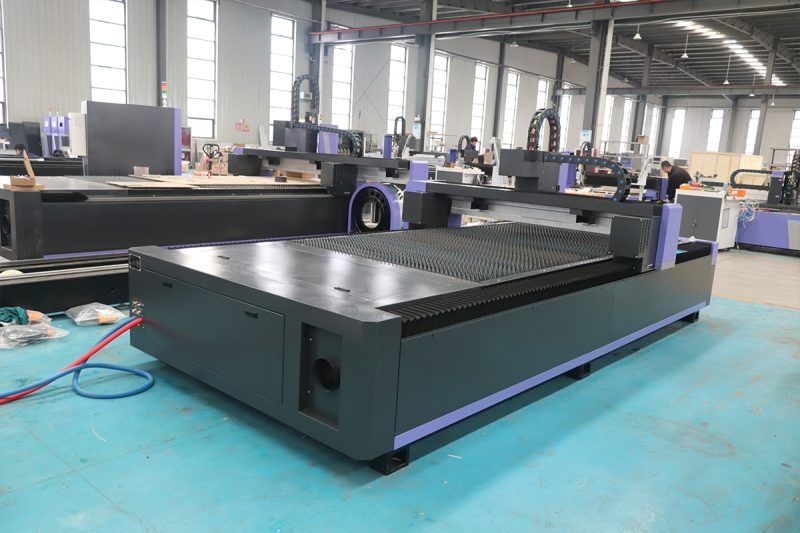
Record Keeping
Maintenance Logs
Activity Recording
- Record each maintenance task performed, including inspections, cleanings, lubrication, and repairs.
- Include the date, time, and type of maintenance to track how frequently each task is performed.
- Log any replacement of consumables, such as lenses or filters, and note when future replacements are due.
Observations
- Document any unusual findings during inspections, such as loose parts, misaligned components, or performance issues.
- Note any corrective actions taken, such as adjustments or minor repairs.
- Highlight recurring issues to facilitate root cause analysis and long-term solutions.
Signature Verification
- Ensure that the technician or operator performing the maintenance signs off on each completed task.
- Include supervisor verification for critical tasks to maintain accountability and confirm the accuracy of the work.
- Store signed logs securely for future reference and audits.
Scheduled Maintenance Planning
Preventive Maintenance Schedule
- Develop a preventive maintenance schedule based on the manufacturer’s recommendations and the machine’s usage patterns.
- Include tasks that go beyond daily checks, such as weekly, monthly, and annual inspections or part replacements.
- Automate reminders if possible, ensuring no scheduled task is missed.
Parts Inventory
- Maintain an inventory of spare parts, consumables, and essential tools to ensure that replacements are readily available when needed.
- Track inventory levels to avoid running out of critical components, such as nozzles, lenses, or filters.
- Reorder parts proactively based on usage trends recorded in maintenance logs.
Trend Analysis
- Use maintenance logs to identify recurring issues or component failures, enabling predictive maintenance strategies.
- Analyze patterns to adjust maintenance schedules, optimizing machine performance and reducing downtime.
- Track key performance indicators (KPIs), such as downtime frequency or repair costs, to evaluate the effectiveness of the maintenance program.
Reporting Issues
Immediate Communication
- Report any critical issues to supervisors or the maintenance team immediately.
- Use designated channels (e.g., maintenance management software or forms) to ensure efficient reporting and tracking of reported issues.
- Communicate any findings or delays to relevant stakeholders to prevent workflow disruptions.
Manufacturer Support
- Contact the machine’s manufacturer if specialized troubleshooting is required or if replacement parts are needed.
- Provide detailed records of maintenance and observations to facilitate faster support from the manufacturer.
- Collaborate with manufacturer technicians to perform remote diagnostics or on-site repairs if necessary.
Compliance Documentation
- Keep all maintenance records organized to demonstrate compliance with internal policies, industry standards, and regulatory requirements.
- Store reports of repairs, inspections, and part replacements for audits and inspections.
- Ensure that safety-related maintenance, such as interlock and emergency stop system checks, is documented properly to meet regulatory guidelines.
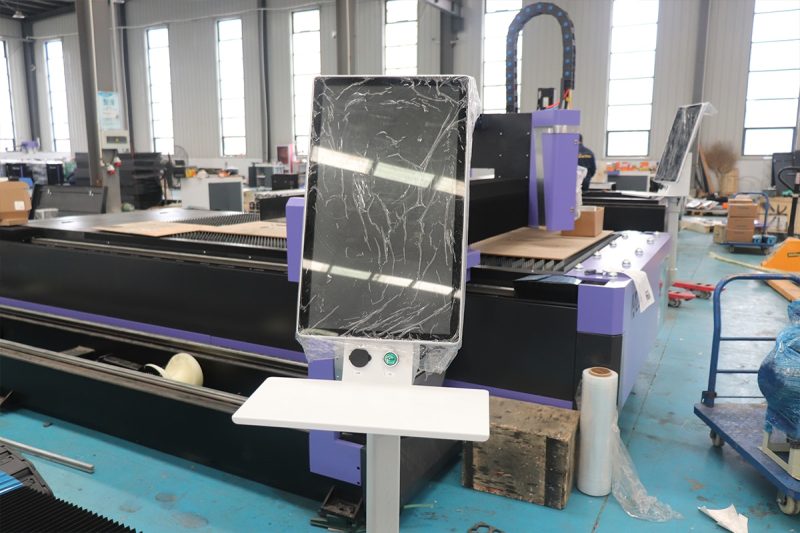
Best Practices for Maintenance
Training and Competency
Operator Training
- Provide comprehensive training on machine operation, maintenance procedures, and troubleshooting techniques.
- Ensure new operators receive hands-on experience under the supervision of experienced personnel.
- Familiarize operators with safety protocols, emergency stop procedures, and the correct use of personal protective equipment (PPE).
Continuous Education
- Offer regular training sessions to keep staff updated on new technologies, software upgrades, and industry best practices.
- Encourage participation in workshops, seminars, and online courses relevant to laser cutting and machine maintenance.
- Rotate operators through different roles to broaden their skills and improve cross-functional knowledge.
Certification
- Require operators to obtain certifications from recognized institutions or the machine manufacturer to validate their competency.
- Maintain up-to-date records of all staff certifications and schedule recertification where necessary.
- Recognize and reward operators who complete advanced training or achieve additional certifications.
Use of Genuine Parts and Consumables
Manufacturer-Approved Parts
- Use only genuine replacement parts recommended by the machine’s manufacturer to guarantee compatibility and performance.
- Avoid counterfeit or aftermarket components that could compromise machine safety and lead to malfunctions.
- Keep an inventory of essential spare parts, such as lenses, nozzles, and filters, to prevent disruptions during maintenance.
Quality Assurance
- Monitor the condition and quality of consumables such as assist gases, coolants, and lubricants to ensure they meet the required standards.
- Replace consumables according to the manufacturer’s guidelines to avoid premature wear or contamination.
- Regularly inspect parts and consumables for defects, ensuring they do not negatively impact machine performance.
Environmental Control
Clean Environment
- Ensure the workspace is kept free of dust, debris, and metal particles that could interfere with the machine’s optics and moving parts.
- Use fume extraction systems to remove smoke and vapor generated during cutting, preventing contamination of optical lenses.
- Establish housekeeping protocols to keep the area around the machine organized and safe.
Temperature and Humidity
- Monitor ambient temperature and maintain it within the recommended range to avoid thermal expansion or condensation that could affect performance.
- Use climate control systems to maintain stable humidity levels, protecting electrical components and optics from corrosion or moisture buildup.
- Avoid placing the machine in areas with high-temperature fluctuations, which could affect alignment and cutting precision.
Regular Audits
Maintenance Audits
- Perform periodic audits of maintenance activities to ensure tasks are completed accurately and on schedule.
- Review maintenance logs to identify trends or recurring issues that require further attention.
- Use audits to verify compliance with safety protocols, operational guidelines, and manufacturer recommendations.
Performance Metrics
- Track key performance indicators (KPIs), such as downtime frequency, repair costs, and maintenance time, to evaluate the effectiveness of the maintenance program.
- Set performance targets to continuously improve machine uptime and productivity.
- Use data-driven insights to adjust maintenance schedules and prioritize tasks that enhance machine reliability.
Safety Culture
Promote Safety
- Create a work environment where safety is a top priority, encouraging staff to follow safety protocols diligently.
- Display safety reminders and instructions near the machine to reinforce safe practices.
- Provide incentives or recognition for teams that consistently maintain a safe and efficient workspace.
Safety Meetings
- Hold regular safety meetings to discuss safety protocols, review incidents, and address potential risks.
- Use meetings to share lessons learned from maintenance tasks and encourage proactive problem-solving.
- Invite feedback from operators to improve safety practices and address any concerns.
Feedback Mechanism
- Establish a system for operators to report safety concerns, equipment issues, or process improvements without fear of reprisal.
- Act on feedback promptly, demonstrating a commitment to continuous improvement and safety.
- Encourage open communication between teams to foster collaboration and shared responsibility for safety and maintenance.
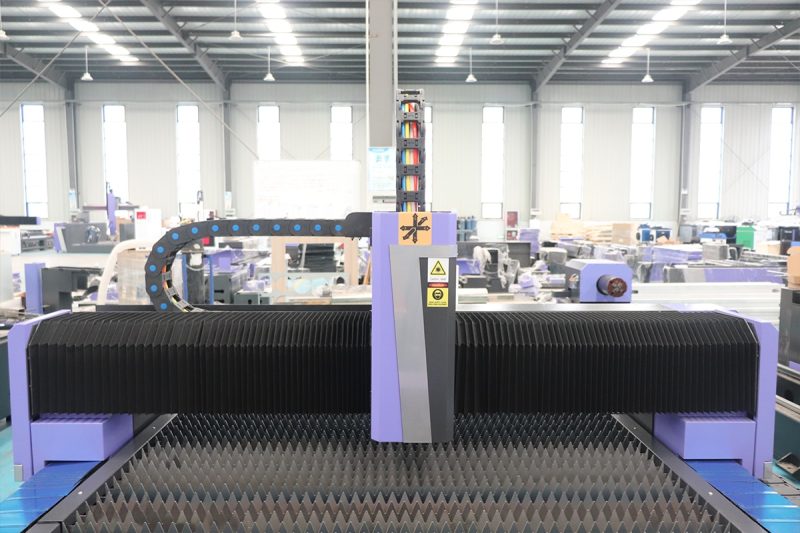
Summary
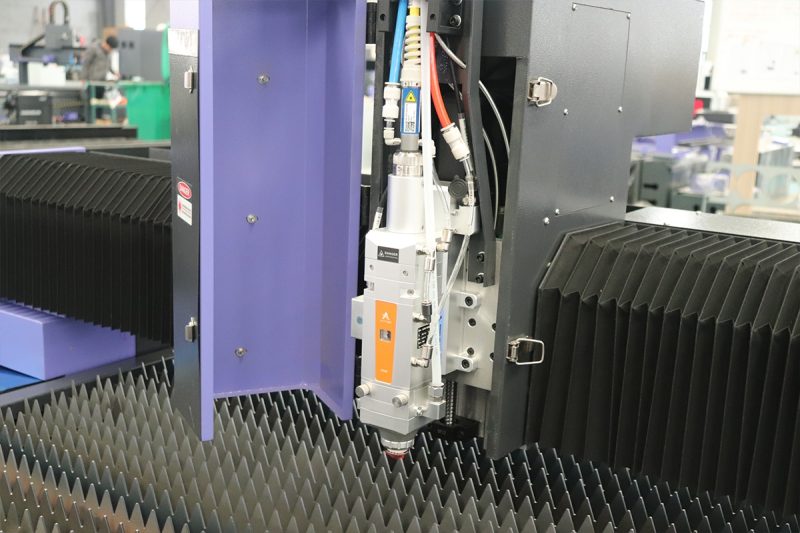
Get Laser Cutting Solutions
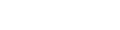
- [email protected]
- [email protected]
- +86-19963414011
- No. 3 Zone A, Lunzhen Industrial Zone,Yucheng City , Shandong Province.