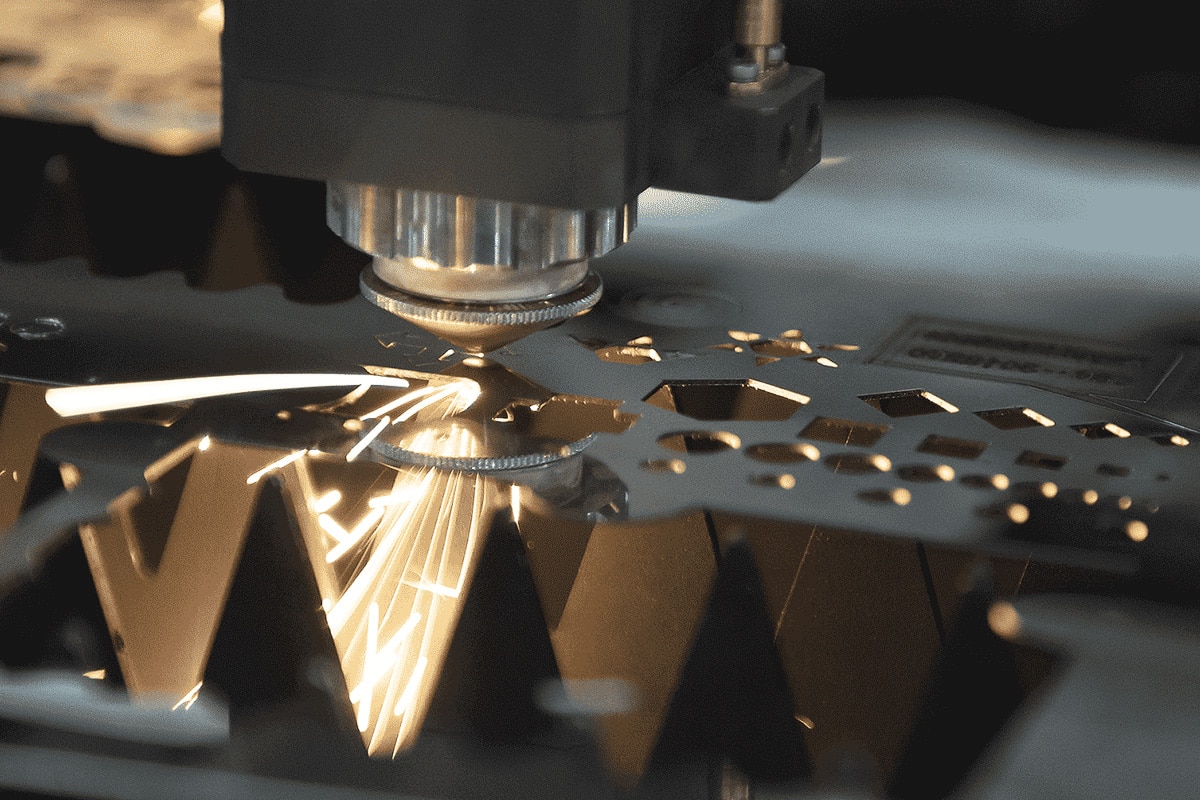
Der Einfluss des Autofokus auf die Schnittgenauigkeit einer Faserlaserschneidmaschine
Als wichtiges Gerät in der Metallverarbeitungsindustrie Faserlaser-Schneidemaschinen sind in verschiedenen Fertigungs- und Verarbeitungsbereichen von entscheidender Bedeutung. Ihre Schnittgenauigkeit und -effizienz beeinflussen nicht nur die Endqualität des Werkstücks, sondern stehen auch in direktem Zusammenhang mit den Produktionskosten und der Verarbeitungseffizienz. Die Fokuseinstellung der Anlage ist entscheidend für stabile und effiziente Schneidergebnisse. Die traditionelle manuelle Fokussierung ist anfällig für menschliche Fehler und erfordert häufige Anpassungen bei der Verarbeitung von Materialien unterschiedlicher Dicke und Art, was die Produktionseffizienz verringert.
Die Einführung der Autofokus-Technologie hat die Verarbeitungsmöglichkeiten von Faserlaserschneidmaschinen deutlich optimiert. Diese Technologie kann die Laserfokusposition dynamisch in Echtzeit anpassen, um den optimalen Schnittabstand zur Materialoberfläche ohne manuelles Eingreifen einzuhalten. Dies verbessert nicht nur die Schnittgenauigkeit, sondern verbessert auch die Anpassungsfähigkeit der Anlage an unterschiedliche Dicken und Materialien und gewährleistet so eine stabile Schnittqualität in verschiedenen komplexen Verarbeitungsszenarien.
Inhaltsverzeichnis
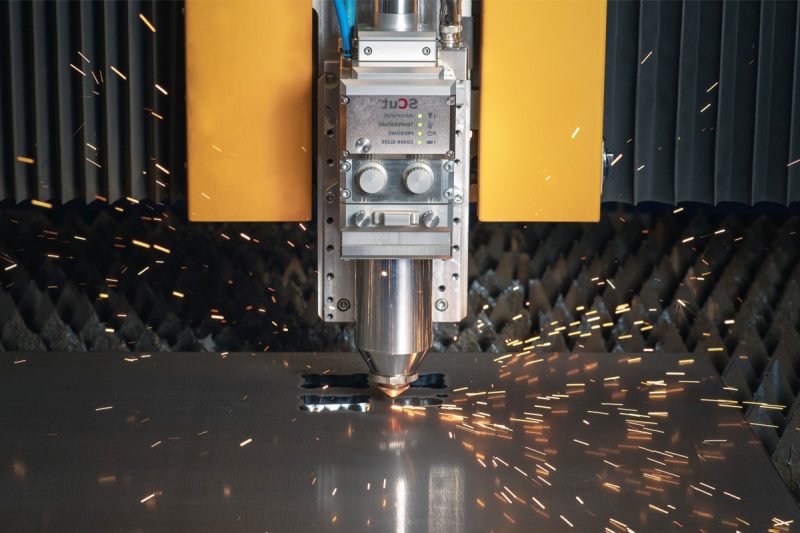
Autofokus beim Faserlaserschneiden verstehen
Definition und Funktion des Autofokus
Beim Faserlaserschneiden wirkt sich die präzise Fokussierung direkt auf Schnittqualität und -effizienz aus. Die herkömmliche manuelle Fokussierung ist nicht nur zeitaufwändig, sondern neigt auch zu Fokusabweichungen durch menschliches Versagen, was die Schnittgenauigkeit beeinträchtigt. Das Aufkommen des Autofokussystems hat die Intelligenz des Laserschneidens deutlich verbessert. Das Gerät kann die Laserfokushöhe automatisch an die Dicke und Oberflächenbeschaffenheit des Materials anpassen, um optimale Schnittbedingungen zu gewährleisten.
Zu den Kernfunktionen des Autofokus-Systems gehören:
- Echtzeit-Anpassung der Fokusposition: Verwenden Sie Sensoren und Steuerungssysteme, um die Materialoberflächenhöhe dynamisch zu erkennen und die Fokusposition in Echtzeit anzupassen, sodass sich der Laserstrahl immer im optimalen Schneidbereich befindet, um eine qualitativ hochwertige Bearbeitung zu gewährleisten.
- Reduzieren Sie manuelle Einstellungsfehler: Durch die automatische Einstellung werden die durch menschliche Eingriffe verursachten Unsicherheiten eliminiert und die Schnittgenauigkeit und -konsistenz verbessert, was insbesondere bei der Massenproduktion und komplexen Verarbeitungsaufgaben wichtig ist.
- Optimieren Sie die Verarbeitungswirkung unterschiedlicher Materialien und Dicken: Beim Schneiden unterschiedlicher Metallmaterialien oder Werkstücke mit großen Dickenunterschieden kann das Autofokussystem den Fokus schnell anpassen, Fehler und Effizienzverluste durch manuelle Anpassung vermeiden und die Anpassungsfähigkeit und Vielseitigkeit der Ausrüstung verbessern.
Mit der Entwicklung intelligenter Fertigungsverfahren ist die Autofokus-Technologie zum Standard hochwertiger Faserlaserschneidmaschinen geworden. Ihre Vorteile kommen insbesondere in Anwendungsszenarien zum Tragen, die hohe Geschwindigkeit, hohe Präzision und vielfältige Bearbeitung erfordern.
Arten von Autofokussystemen
Derzeit umfassen die gängigen Autofokussysteme in Faserlaserschneidmaschinen hauptsächlich kapazitiven Autofokus, berührungslosen Autofokus und Autofokussysteme mit intelligenter Steuerung. Verschiedene Systemtypen haben ihre eigenen Eigenschaften und eignen sich für unterschiedliche Verarbeitungsanforderungen.
Kapazitiver Autofokus
Das kapazitive Autofokussystem nutzt die Kapazitätsänderung zwischen Düse und Werkstückoberfläche, um die Fokusposition zu erkennen und die Laserkopfhöhe in Echtzeit anzupassen. Diese Technologie basiert auf dem Prinzip der elektrischen Feldinduktion und kann schnell auf Höhenänderungen der Materialoberfläche reagieren und während der Bearbeitung eine stabile Fokusposition aufrechterhalten.
Vorteil:
- Anwendbar auf eine Vielzahl von Metallmaterialien, einschließlich Edelstahl, Aluminiumlegierung, Kohlenstoffstahl, usw., mit einem breiten Anwendungsspektrum;
- Schnelle Reaktionsgeschwindigkeit, besonders geeignet für Hochgeschwindigkeitsschneidanwendungen, kann die Fokusposition genau anpassen und die Schnittstabilität verbessern;
- Die Systemstruktur ist relativ einfach, die Wartungskosten sind niedrig und das Preis-Leistungs-Verhältnis ist hoch.
Einschränkung:
- Schlechte Anpassungsfähigkeit an nichtleitende Materialien, wie etwa nichtmetallische Materialien wie Keramik und Kunststoffe, aufgrund der unbedeutenden Änderung der Kapazitätssignale nimmt die Erfassungsempfindlichkeit ab;
- Kann durch Oberflächenverunreinigungen wie Oxidation, Staub oder Öl beeinträchtigt werden, was die Genauigkeit der Kapazitätsmessung beeinträchtigen und zu Fehlern bei der Fokuseinstellung führen kann;
- Bei der Kontrolle extrem dünner oder dicker Materialien gibt es gewisse Einschränkungen und eine zusätzliche Optimierung der Schnittparameter ist erforderlich.
Die kapazitive Autofokus-Technologie eignet sich für die Metallverarbeitung, insbesondere in der Massenproduktion und standardisierten Verarbeitung. Für spezielle Materialien oder extreme Verarbeitungsumgebungen müssen ihre Stabilität und Anpassungsfähigkeit jedoch möglicherweise weiter optimiert werden.
Berührungsloser Autofokus
Der berührungslose Autofokus nutzt optische oder Laser-Entfernungsmessung, um den Abstand zwischen Düse und Materialoberfläche über einen Sensor zu erfassen und die Fokusposition dynamisch anzupassen. Im Vergleich zum kapazitiven Fokus vermeidet das berührungslose System den physischen Kontakt vollständig und eignet sich daher für mehr Materialarten.
Vorteil:
- Vermeiden Sie physischen Kontakt, reduzieren Sie den Sensorverschleiß, erhöhen Sie die Lebensdauer und senken Sie die Ausfallrate.
- Anwendbar auf mehr Materialtypen, einschließlich nichtleitender Metalle, plattierter Materialien und Verbundwerkstoffe, wodurch der Anwendungsbereich des Laserschneidens erweitert wird;
- Optische oder Laser-Entfernungsmessungstechnologien sind weniger anfällig für äußere Verschmutzung und können in komplexeren Umgebungen stabil arbeiten. Sie können eine hohe Erkennungsgenauigkeit aufrechterhalten, selbst wenn sich Öl, eine Oxidschicht oder Staub auf der Oberfläche des Werkstücks befindet.
- Höhere Genauigkeit: Im Vergleich zur kapazitiven Fokussierung ist die Erkennungsgenauigkeit berührungsloser Systeme höher und eignet sich besonders für hochpräzise Mikrobearbeitungsszenarien.
Einschränkung:
- Die Systemkosten sind höher. Im Vergleich zum kapazitiven System erfordert das berührungslose Fokussystem eine komplexere optische oder Laser-Sensortechnologie, die teurer ist.
- Erfordert eine präzisere Kalibrierung und Wartung. Da der Sensor auf optischen oder Lasermessungen basiert, muss er regelmäßig kalibriert werden, um eine langfristig stabile Fokuserkennungsgenauigkeit zu gewährleisten.
Die berührungslose Autofokus-Technologie eignet sich besonders für Verarbeitungsszenarien mit hoher Präzision und hohen Anforderungen, wie etwa die Herstellung von Mikroelektronik, das Schneiden von Präzisionsinstrumententeilen usw., kann jedoch aufgrund von Kostenfaktoren bei der allgemeinen industriellen Verarbeitung bestimmten Einschränkungen unterliegen.
Autofokus-Steuerung
Die Autofokussteuerung ist eine umfassende Fokussierungstechnologie, die Softwarealgorithmen, Sensorfeedback und intelligente Steuerungssysteme kombiniert. Sie kann nicht nur den Fokus in Echtzeit anpassen, sondern ist auch eng in das CNC-System integriert, um eine intelligentere Fokusoptimierung zur Anpassung an unterschiedliche Schneidanforderungen zu erreichen.
Vorteil:
- Es ist hochintelligent und kann automatisch unterschiedliche Materialien und Dicken erkennen, die optimale Fokusposition anpassen und manuelle Eingriffe reduzieren.
- Es kann nahtlos in das CNC-Steuerungssystem integriert werden, um ein vollautomatisches Schneiden zu erreichen und die Produktionseffizienz und Verarbeitungskonsistenz zu verbessern.
- Es optimiert die Schnittparameter durch Algorithmen, um die beste Schnittqualität aufrechtzuerhalten und den Energieverbrauch in verschiedenen Verarbeitungsumgebungen zu senken.
- Es verfügt über eine hohe Anpassungsfähigkeit und ist nicht nur für verschiedene Metallmaterialien geeignet, sondern kann auch für unterschiedliche Oberflächenbedingungen optimiert und angepasst werden, um die Schnittqualität und die Kantenbeschaffenheit zu verbessern.
Einschränkung:
- Hängt von der Stabilität der Software und Sensoren ab. Bei Störungen der Systemsoftware oder des Sensors kann die Genauigkeit der Fokussteuerung beeinträchtigt sein.
- Die Genauigkeit des Sensors wird stark von Umweltfaktoren beeinflusst. Beispielsweise können Temperatur- und Feuchtigkeitsschwankungen die Genauigkeit des Sensors beeinträchtigen, und die Parameter müssen für unterschiedliche Umgebungen optimiert werden.
- Es stellt hohe technische Anforderungen an die Bediener und es sind qualifizierte Techniker erforderlich, um die Parameter anzupassen und so die Leistung des Autofokussystems zu maximieren.
Die Autofokus-Steuerungstechnologie stellt die zukünftige Entwicklungsrichtung des Faserlaserschneidens dar, insbesondere im Kontext intelligenter Fertigung und Industrie 4.0. Ihre Vorteile werden immer deutlicher. Obwohl die Kosten hoch sind und ein hohes Maß an Bedienerkenntnissen erfordern, eröffnen ihre hochpräzisen und intelligenten Schneidfunktionen breite Anwendungsperspektiven im Bereich der High-End-Fertigung.
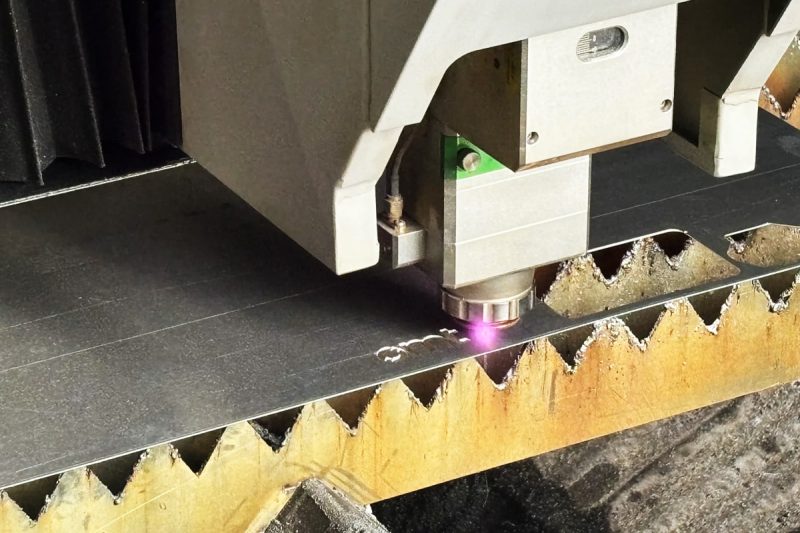
Faktoren, die die Schnittgenauigkeit beeinflussen
Zu den Faktoren, die die Genauigkeit des Faserlaserschneidens beeinflussen, gehören hauptsächlich Materialeigenschaften, Strahlqualität, Düsenabstand, Maschinenstabilität und Softwaresteuerung.
Materialeigenschaften: Unterschiedliche Materialien haben aufgrund ihrer Laserabsorptionsrate, Wärmeleitfähigkeit und Schmelzeigenschaften einen direkten Einfluss auf die Schnittgenauigkeit. Beispielsweise erzeugt Edelstahl aufgrund seiner hohen Laserabsorptionsrate in der Regel eine glattere Schneidkante, während stark reflektierende Materialien wie Aluminiumlegierungen und Kupfer kann den Laser reflektieren, was die Energieabsorption beeinträchtigt und zu instabilem Schneiden führt. Darüber hinaus beeinflusst die Materialdicke die Einstellung des Laserfokus. Dickere Materialien erfordern in der Regel eine höhere Laserleistung und langsamere Schnittgeschwindigkeiten, um präzises Schneiden zu gewährleisten.
Strahlqualität: Muster und Qualität des Laserstrahls bestimmen Größe und Energiedichte des Laserpunkts, was wiederum die Schnittpräzision beeinflusst. Ein hochwertiger Strahl hat in der Regel einen kleineren fokussierten Punkt, wodurch die Laserenergie konzentrierter wird, was die Schnittgenauigkeit verbessert und die Wärmeeinflusszone reduziert. Ein instabiles Strahlmuster oder eine ungleichmäßige Leistungsverteilung können raue Schnittkanten oder ungleichmäßige Schlackenrückstände verursachen.
Düsenabstand: Der Abstand zwischen Düse und Werkstückoberfläche beeinflusst den Hilfsgasstrom und die Schneidstabilität. Ist der Düsenabstand zu groß, kann der Hilfsgasdruck unzureichend sein, was zu übermäßigen Schlackenrückständen führt. Ist der Abstand zu klein, kann dies zu turbulenten Luftströmungen führen und die Schneidgenauigkeit beeinträchtigen. Daher ist während des Schneidvorgangs eine präzise Einstellung des Düsenabstands erforderlich, um den Gasstrom zu optimieren, Schnittfehler zu reduzieren und die Qualität der Schneidkante zu verbessern.
Maschinenstabilität: Die strukturelle Stabilität der Faserlaserschneidmaschine bestimmt direkt die Genauigkeit der Schnittbahn. Hochpräzise Führungsschienen, Leitspindeln und Servosysteme sorgen für einen reibungslosen Schneidprozess und reduzieren Vibrationsfehler. Ist die Maschine nicht stabil genug oder sind Teile nach längerem Betrieb locker, kann dies zu Schnittabweichungen führen und den endgültigen Bearbeitungseffekt beeinträchtigen. Daher ist eine regelmäßige Wartung und Überprüfung der Maschinenstabilität unerlässlich.
Softwaresteuerung: Fortschrittliche Softwaresteuerungssysteme optimieren Schneidpfade und passen Laserleistung und -geschwindigkeit an die Bearbeitungsanforderungen unterschiedlicher Materialien und Materialstärken an. Intelligente Software kompensiert Fehler basierend auf Materialeigenschaften automatisch und verbessert so die Schnittkonsistenz. Echtzeit-Überwachungs- und Feedbacksysteme können Parameter rechtzeitig anpassen, um die Schnittqualität zu optimieren. Eine ungenaue Softwaresteuerung oder falsche Betriebsparameter können zu Schnittabweichungen oder unnötigem Materialabfall führen.
Um ein hochpräzises Faserlaserschneiden zu erreichen, müssen die oben genannten Faktoren im Allgemeinen umfassend berücksichtigt und die Stabilität und Konsistenz der Verarbeitungsqualität durch Feineinstellung und optimierte Steuerung sichergestellt werden.
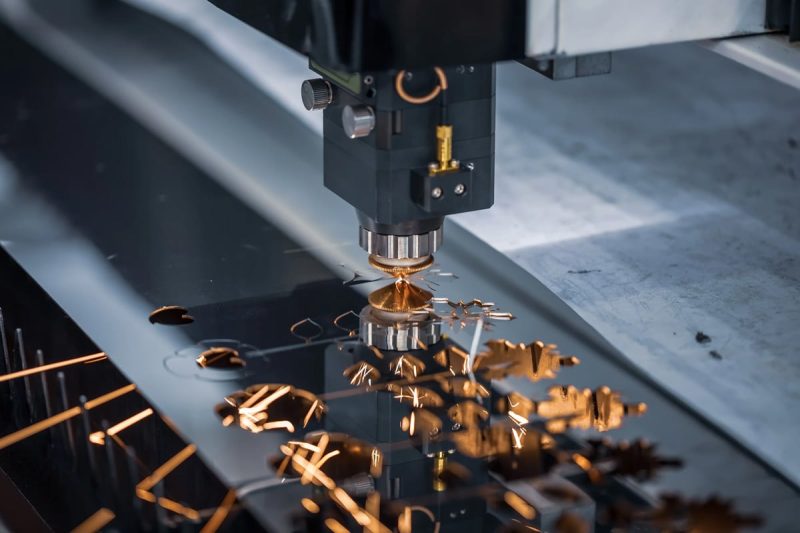
Der Einfluss des Autofokus auf die Schnittgenauigkeit
Die Autofokus-Technologie spielt eine Schlüsselrolle für die Präzision und Verarbeitungseffizienz beim Faserlaserschneiden, was sich hauptsächlich in den folgenden Aspekten widerspiegelt:
Präzision und Konsistenz: Das Autofokussystem passt die Fokusposition in Echtzeit an die Dicke und Oberflächenbeschaffenheit des Materials an und stellt sicher, dass der Laser stets im optimalen Fokusbereich arbeitet. Dies verbessert nicht nur die Schnittgenauigkeit, sondern sorgt auch für einen stabilen Verarbeitungseffekt in der Massenproduktion, reduziert Fehler durch manuelle Anpassung und verbessert die Produktkonsistenz.
Reduzierte Vorbereitungszeit: Bei der herkömmlichen manuellen Fokuseinstellung müssen Bediener beim Schneiden unterschiedlicher Stärken oder Materialien häufig nachjustieren, was zeitaufwändig und fehleranfällig ist. Das Autofokussystem kann die Fokuseinstellung schnell durchführen, die Produktionsvorbereitungszeit erheblich verkürzen und die Gesamtverarbeitungseffizienz verbessern, insbesondere bei der Verarbeitung mehrerer Sorten und kleiner Chargen.
Anpassungsfähigkeit an Materialänderungen: Unterschiedliche Materialien weisen unterschiedliche Laserabsorptionsraten und Schneidanforderungen auf. Das Autofokussystem optimiert den Fokus automatisch entsprechend den Materialeigenschaften, sodass sich die Schneidparameter an verschiedene Metallmaterialien – von Edelstahl über Aluminiumlegierungen bis hin zu hochreflektierenden Materialien – anpassen lassen. Dies gewährleistet eine stets stabile Schnittqualität und reduziert die durch Materialänderungen verursachten Fehlerbehebungskosten.
Auswirkungen auf die Kantenqualität: Eine präzise Fokussteuerung trägt zur Reduzierung der Wärmeeinflusszone bei, wodurch die Schneide glatter und vertikaler wird und Grate und Schlackenrückstände reduziert werden. Insbesondere bei hochpräzisen Bearbeitungen oder Werkstücken, die nachträglich geschweißt und beschichtet werden müssen, kann die Autofokus-Technologie die Schnittqualität deutlich verbessern und den Bedarf an Nachbearbeitung reduzieren.
Durch das Autofokussystem kann die Faserlaserschneidmaschine nicht nur eine höhere Bearbeitungsgenauigkeit erreichen, sondern auch die Produktionseffizienz verbessern, durch menschliches Eingreifen verursachte Fehler reduzieren und den Schneidprozess intelligenter und effizienter gestalten.
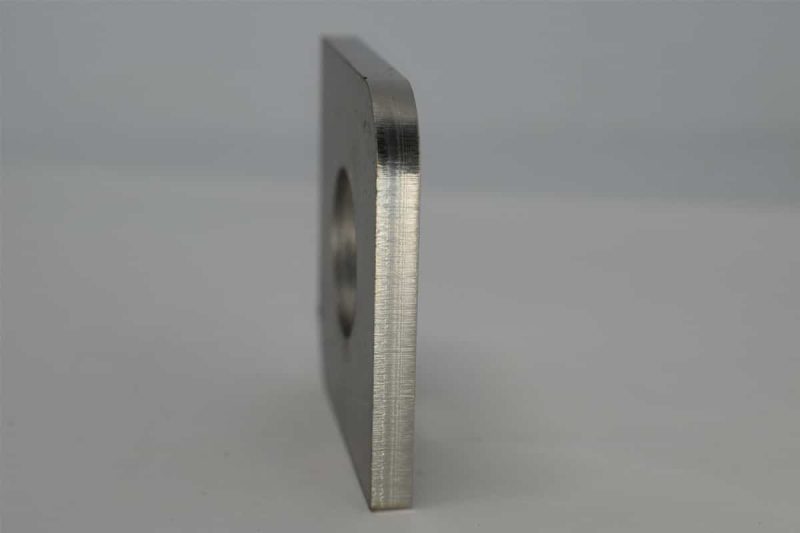
Herausforderungen und Lösungen
Obwohl die Autofokus-Technologie die Genauigkeit und Effizienz des Faserlaserschneidens deutlich verbessert hat, birgt sie in der Praxis immer noch einige Herausforderungen. Um den stabilen Betrieb des Autofokus-Systems zu gewährleisten, müssen effektive Lösungen für die folgenden Schlüsselprobleme gefunden werden.
Kalibrierung und Wartung: Das Autofokussystem basiert auf präzisen Sensoren und Aktoren. Bei längerem Betrieb oder mangelnder Wartung kann es zu Fokusabweichungen kommen und die Schnittqualität beeinträchtigen. Daher ist eine regelmäßige Kalibrierung des Autofokusgeräts sehr wichtig. Unternehmen sollten einen strengen Wartungsplan erstellen, der die Überprüfung der Sensorempfindlichkeit, die Reinigung optischer Komponenten und die Korrektur der Fokusparameter umfasst, um sicherzustellen, dass das Gerät stets in optimalem Zustand ist. Auch die Aktualisierung des Softwaresystems sollte nicht vernachlässigt werden. Optimierte Algorithmen und Kompensationsstrategien können die Genauigkeit des Autofokus weiter verbessern.
Umweltfaktoren: Auch die Arbeitsumgebung der Faserlaserschneidmaschine hat einen gewissen Einfluss auf die Stabilität des Autofokussystems. Faktoren wie Staub, Rauch, Temperatur und Luftfeuchtigkeit können beispielsweise die Erkennungsgenauigkeit des Sensors beeinträchtigen. Starker Staub oder Öl in der Schneidumgebung kann Linse und Sensor verunreinigen und zu einer fehlerhaften Fokuserkennung führen. Daher empfiehlt es sich, ein gutes Rauchabzugs- und Staubentfernungssystem rund um das Gerät zu installieren und Sensor und optische Komponenten regelmäßig zu reinigen. Gleichzeitig kann eine konstante Temperatur und Luftfeuchtigkeit die Auswirkungen von Wärmeausdehnung und -kontraktion auf den Laserweg und die Fokusgenauigkeit reduzieren.
Schulung und Fähigkeiten des Bedieners: Obwohl die Autofokus-Technologie manuelle Eingriffe reduziert, benötigen Bediener dennoch bestimmte technische Kenntnisse, um bei Abweichungen die Fokusparameter schnell anpassen und optimieren zu können. Ungeschickte Bedienung kann zu falschen Fokuseinstellungen führen, die den Schneideffekt beeinträchtigen. Daher sollten Unternehmen ihre Bediener systematisch schulen, damit sie die Funktionsweise des Autofokus-Systems beherrschen, häufige Fehler erkennen und beheben und den passenden Fokusmodus für unterschiedliche Materialien anpassen können. In Kombination mit dem intelligenten Überwachungssystem können Bediener zudem die Schneidstrategien durch Datenfeedback optimieren und die Gesamtproduktionseffizienz steigern.
Durch regelmäßige Kalibrierung und Wartung, Optimierung der Arbeitsumgebung und Verbesserung der Fähigkeiten der Bediener können die Herausforderungen der Autofokus-Technologie in praktischen Anwendungen effektiv gelöst werden. So wird sichergestellt, dass die Faserlaserschneidmaschine stets über hochpräzise und stabile Verarbeitungsfunktionen verfügt.
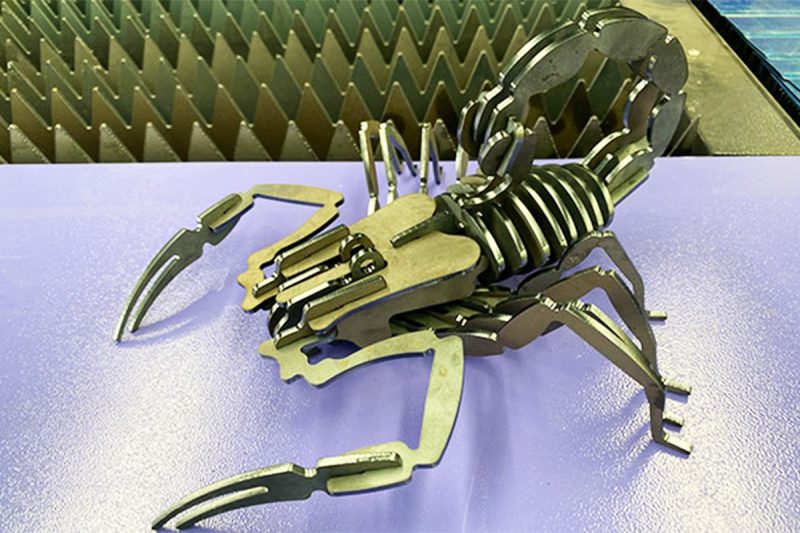
Zusammenfassen
Der Einsatz von Autofokus-Technologie in Faserlaserschneidmaschinen hat die Schnittgenauigkeit und Produktionseffizienz deutlich verbessert. Verschiedene Autofokus-Systeme haben ihre Vorteile. Durch gezielte Auswahl und Optimierung können sie die Schnittkonsistenz effektiv verbessern, den manuellen Einstellaufwand reduzieren und die Anpassungsfähigkeit an unterschiedliche Materialien und Dicken verbessern, wodurch qualitativ hochwertigere Bearbeitungsergebnisse gewährleistet werden. Der Einsatz dieser Technologie macht das Laserschneiden intelligenter, reduziert menschliche Fehler und verbessert die Produktionsstabilität und -genauigkeit.
Das Autofokussystem steht im praktischen Einsatz jedoch immer noch vor gewissen Herausforderungen, wie z. B. der Kalibrierungswartung, den Umwelteinflüssen und den Anforderungen an die Bedienerkenntnisse. Die Genauigkeit des Sensors, äußere Umgebungsfaktoren und das technische Niveau des Bedieners beeinflussen die Stabilität des Systems und den Schneideffekt. Daher müssen Unternehmen sinnvolle Wartungspläne für ihre Geräte erstellen, die Arbeitsumgebung optimieren und die Schulung der Bediener intensivieren, um die optimale Leistung des Autofokussystems zu gewährleisten und so die Gesamtverarbeitungsqualität und die Wettbewerbsfähigkeit der Produktion weiter zu verbessern.
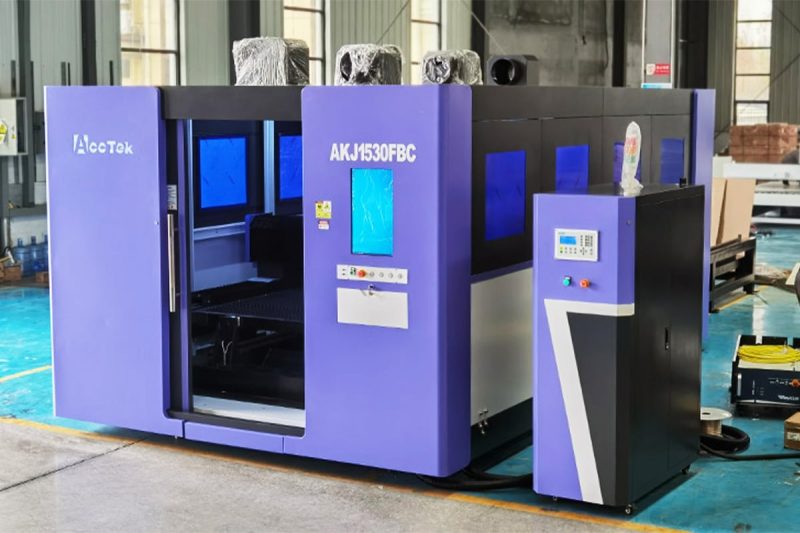
Holen Sie sich Laserlösungen
AccTek-Laser hat es sich zur Aufgabe gemacht, Anwendern weltweit fortschrittliche Lösungen für das Faserlaserschneiden anzubieten. Unsere Autofokus-Technologie ermöglicht eine präzise Echtzeit-Anpassung, um sicherzustellen, dass der Laserfokus stets optimal positioniert ist. Dadurch werden Schnittgenauigkeit und Bearbeitungsqualität deutlich verbessert. Ob bei der Bearbeitung von Metallmaterialien unterschiedlicher Dicke oder bei komplexen Schneidanforderungen – unser intelligentes Autofokus-System hilft Anwendern, Produktionsprozesse zu optimieren, die Effizienz zu steigern und menschliche Fehler zu reduzieren.
Unsere Laserschneidanlagen finden breite Anwendung in der Blechbearbeitung, im Automobilbau, in der Luft- und Raumfahrt, in der Elektronikindustrie und anderen Branchen. Dank ihrer hervorragenden Stabilität und effizienten Leistung haben sie das Vertrauen von Kunden weltweit gewonnen. Wenn Sie mehr über die Anwendung der Autofokus-Technologie und des hochpräzisen Laserschneidens erfahren oder eine Laserschneidlösung finden möchten, die Ihren Produktionsanforderungen entspricht, kontaktieren Sie uns gerne. kontaktiere uns! Unser professionelles Team bietet Ihnen ausführliche Beratung und technischen Support, um Ihr Unternehmen auf die nächste Ebene zu bringen.
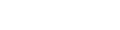
Kontaktinformationen
- [email protected]
- [email protected]
- +86-19963414011
- Nr. 3 Zone A, Industriegebiet Lunzhen, Stadt Yucheng, Provinz Shandong.
Holen Sie sich Laserlösungen