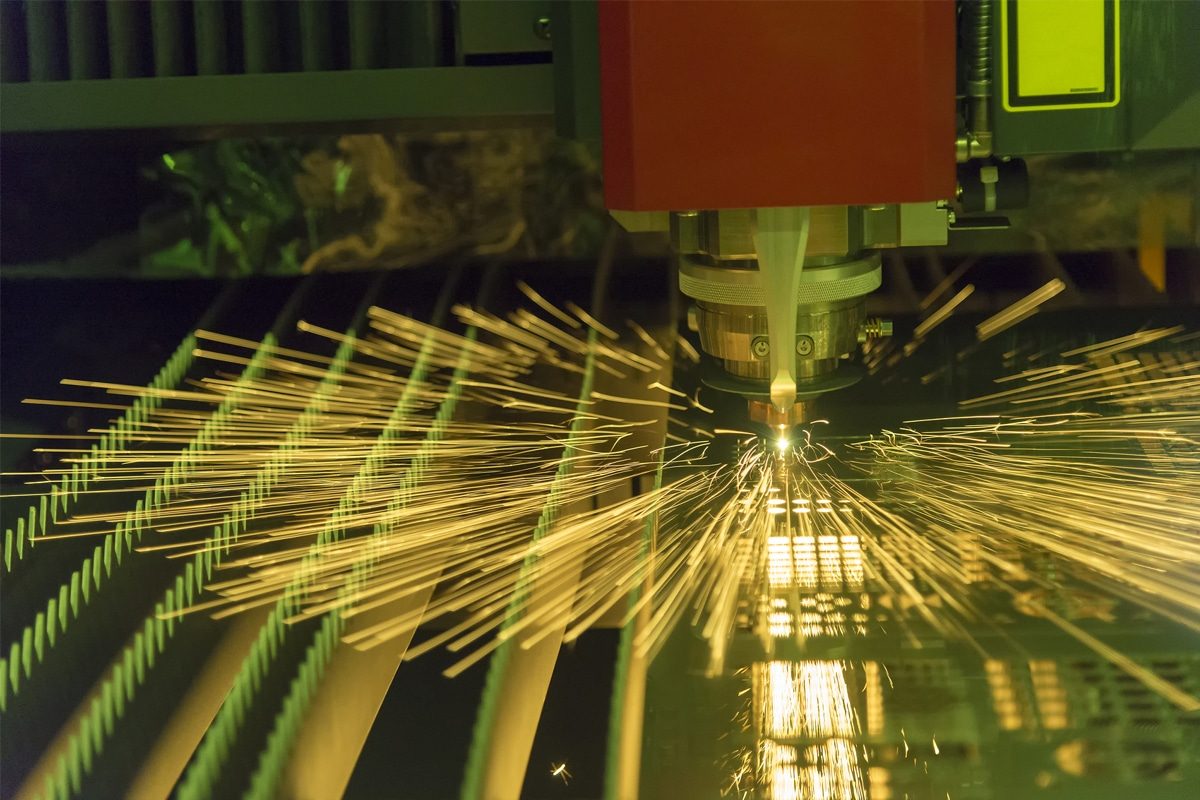
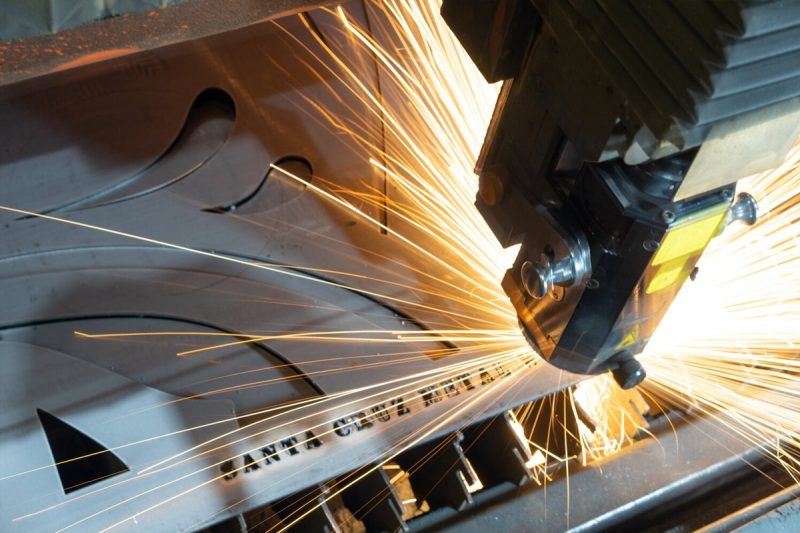
Unübertroffene Präzision und Genauigkeit
Hochpräzises Schneiden
Laserschneidmaschinen verwenden einen fokussierten Lichtstrahl, der nur einen Bruchteil eines Millimeters breit sein kann. Diese konzentrierte Energie ermöglicht äußerst präzise Schnitte mit minimalen Abweichungen. Die hochpräzise Schneidfähigkeit der Lasertechnologie stellt sicher, dass jeder Schnitt genau den angegebenen Designabmessungen entspricht.
- Genauigkeit im Submillimeterbereich: Laserschneidmaschinen können Toleranzen von bis zu ±0,01 mm erreichen und sind daher ideal für Anwendungen, bei denen es auf exakte Abmessungen ankommt.
- Saubere Schnittkanten: Der Laserstrahl schmilzt oder verdampft das Material, wodurch glatte und gratfreie Kanten entstehen, die kaum bis keine Nachbearbeitung erfordern.
- Komplexe Profile: Ob gerade Linien oder komplizierte Kurven, mit dem Laserschneiden lassen sich komplexe Profile ohne Kompromisse bei der Präzision bearbeiten.
Gleichbleibende Wiederholbarkeit
Konsistenz ist in der Fertigung von entscheidender Bedeutung, insbesondere bei der Herstellung großer Mengen identischer Teile. Laserschneidmaschinen sind mit fortschrittlichen Steuerungssystemen ausgestattet, die sicherstellen, dass jedes Teil jedes Mal auf die gleiche Weise geschnitten wird.
- Computergestützte numerische Steuerung (CNC): Die Integration von CNC-Systemen ermöglicht eine präzise Kontrolle des Schneidevorgangs. Digitale Entwürfe werden sorgfältig befolgt, wodurch menschliche Fehler reduziert werden.
- Automatisierte Einstellungen: Sobald die Parameter für einen bestimmten Auftrag eingestellt sind, kann die Maschine den Vorgang ohne Abweichungen wiederholt wiederholen.
- Qualitätssicherung: Durch gleichbleibende Wiederholbarkeit wird die Qualitätskontrolle verbessert, sodass sichergestellt wird, dass jedes Teil die erforderlichen Standards erfüllt und Ausschuss aufgrund von Mängeln reduziert wird.
Minimale Materialverzerrung
Bei herkömmlichen Schneideverfahren kann es zu Spannungen und Hitzeeinwirkung im Material kommen, was zu Verformungen und Verwerfungen führt. Beim Laserschneiden werden diese Probleme durch den berührungslosen Prozess und die gezielte Energieanwendung minimiert.
- Lokale Erwärmung: Der Laserstrahl erwärmt nur einen kleinen Bereich, wodurch die Wärmeeinflusszone (WEZ) reduziert und eine thermische Verformung des umgebenden Materials verhindert wird.
- Berührungsloses Schneiden: Da kein physischer Kontakt mit dem Material stattfindet, werden mechanische Belastungen, die zu Verbiegungen oder Verformungen führen können, eliminiert.
- Materialintegrität: Die strukturellen und mechanischen Eigenschaften des Metalls bleiben erhalten, wodurch Komponenten möglich werden, die strenge Leistungsstandards erfüllen.
Komplizierte Designs und komplexe Geometrien
Eine der herausragenden Eigenschaften des Laserschneidens ist die Fähigkeit, komplizierte Designs und komplexe Geometrien problemlos zu verarbeiten. Diese Fähigkeit eröffnet neue Möglichkeiten in Bezug auf Design und Funktionalität.
- Feine Detailarbeit: Laserschneidemaschinen können winzige Löcher, scharfe Ecken und komplizierte Muster erzeugen, die mit anderen Schneidemethoden schwierig oder unmöglich sind.
- Vielseitigkeit im Design: Designer haben mehr Freiheit bei der Entwicklung innovativer Produkte, ohne durch Fertigungsbeschränkungen eingeschränkt zu werden.
- Effizientes Prototyping: Die schnelle Produktion von Prototypen mit komplexen Funktionen beschleunigt den Entwicklungsprozess und ermöglicht schnelle Iterationen.
Anwendungsbeispiele
Die beispiellose Präzision und Genauigkeit des Laserschneidens haben transformative Auswirkungen auf zahlreiche Branchen:
- Luft- und Raumfahrtindustrie: Komponenten wie Motorteile, Halterungen und Strukturelemente erfordern exakte Abmessungen und makellose Oberflächen. Durch Laserschneiden wird sichergestellt, dass diese Teile strenge Sicherheits- und Leistungsstandards erfüllen.
- Medizinische Geräte: Chirurgische Instrumente und Implantate erfordern höchste Präzision. Durch Laserschneiden werden Komponenten mit den genauen Spezifikationen hergestellt, die für medizinische Anwendungen erforderlich sind, bei denen Fehler schwerwiegende Folgen haben können.
- Automobilbau: Von Karosserieteilen bis hin zu komplexen Innenkomponenten verlässt sich die Automobilindustrie auf das Laserschneiden, da damit Teile hergestellt werden können, die perfekt zusammenpassen und so die Leistung und Sicherheit der Fahrzeuge verbessern.
- Elektronik und elektrische Geräte: Bei der Herstellung von Gehäusen, Steckverbindern und Schaltungskomponenten profitiert man von der Fähigkeit des Laserschneidens, die präzisen und komplexen Designs zu erzeugen, die für kompakte und effiziente elektronische Geräte erforderlich sind.
- Architekturfertigung: Dekorative Metallarbeiten und Strukturkomponenten in der Architektur weisen oft komplexe Designs auf. Laserschneiden ermöglicht es Architekten und Bauherren, ihre kreativen Visionen mit präzisionsgeschnittenen Materialien umzusetzen.
- Maßgeschneiderte Lösungen: Unternehmen, die maßgeschneiderte Metallteile für Spezialgeräte benötigen, können mithilfe des Laserschneidens kleine Chargen produzieren, ohne dass dafür teure Werkzeuge oder längere Vorlaufzeiten erforderlich sind.
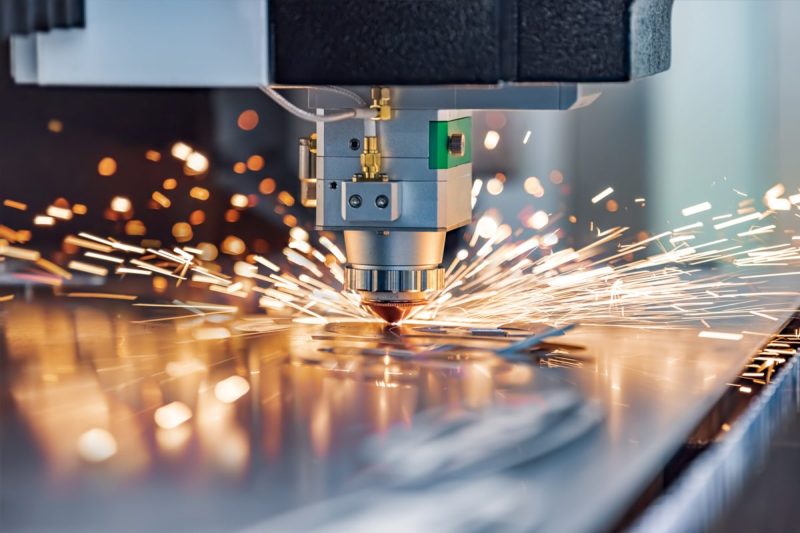
Vielseitigkeit und Flexibilität
Große Auswahl an Materialien
Eines der überzeugendsten Merkmale des Laserschneidens ist seine Kompatibilität mit einem breiten Spektrum an Materialien. Laserschneidmaschinen sind für die Verarbeitung einer breiten Palette an Metallen und Legierungen ausgelegt, sodass Hersteller die Anforderungen verschiedener Branchen erfüllen können.
- Metalle und Legierungen: Laserschneiden eignet sich gut für Materialien wie Kohlenstoffstahl, Edelstahl, Aluminium, Kupfer, Messing und Titan. Diese Vielseitigkeit ermöglicht Anwendungen in verschiedenen Branchen, von der Automobilindustrie bis zur Luft- und Raumfahrt.
- Reflektierende Materialien: Mit fortschrittlicher Lasertechnologie lassen sich reflektierende Metalle wie Aluminium und Kupfer hochpräzise schneiden. So lassen sich die Probleme überwinden, die bei der Verarbeitung dieser Materialien mit herkömmlichen Methoden auftreten.
- Spezialmetalle: Für Branchen, die exotische oder spezielle Metalle benötigen, bietet das Laserschneiden eine Lösung, bei der die Materialintegrität und die Leistungsmerkmale erhalten bleiben.
Verschiedene Dickenfähigkeiten
Laserschneidmaschinen sind für die Bearbeitung von Materialien unterschiedlicher Dicke ausgelegt und weisen eine Flexibilität auf, die herkömmliche Schneideverfahren nicht bieten können.
- Dünne Bleche bis dicke Platten: Laserschneidmaschinen können je nach Material und Laserleistung dünne Metallbleche von weniger als 1 mm Dicke bis hin zu dicken Platten von bis zu 30 mm Dicke verarbeiten.
- Einstellbare Leistungseinstellungen: Durch die Möglichkeit, die Laserleistungseinstellungen anzupassen, können optimale Schneidbedingungen für unterschiedliche Materialstärken geschaffen werden, sodass saubere Schnitte unabhängig von der Materialstärke gewährleistet sind.
- Gleichbleibende Qualität: Unabhängig davon, ob es sich um dünne oder dicke Materialien handelt, liefert das Laserschneiden eine gleichbleibende Kantenqualität und Präzision, wodurch die Notwendigkeit einer Nachbearbeitung reduziert wird.
Designflexibilität
Die Laserschneidtechnologie eröffnet neue Horizonte bei den Gestaltungsmöglichkeiten und ermöglicht schnelle Änderungen und Anpassungen ohne erhebliche Ausfallzeiten oder Kosten.
- Digitale Integration: Designs werden mithilfe von CAD-Software erstellt oder geändert und direkt an die Laserschneidmaschine übertragen. Diese nahtlose Integration ermöglicht schnelle Anpassungen und Iterationen.
- Keine Werkzeugänderungen: Anders als bei mechanischen Schneideverfahren, die für unterschiedliche Designs neue Werkzeuge oder Matrizen erfordern, sind beim Laserschneiden keine physischen Werkzeugänderungen erforderlich, was Zeit und Ressourcen spart.
- Anpassung: Hersteller können problemlos kundenspezifische Teile oder Kleinserien ohne den mit der Umrüstung verbundenen Aufwand produzieren und so auf spezielle Kundenbedürfnisse oder Marktnischen eingehen.
Komplexe Formen und Konturen
Laserschneidmaschinen arbeiten äußerst präzise und können komplexe Formen und detaillierte Merkmale erzeugen, die mit anderen Schneideverfahren nur schwer zu erreichen sind.
- Hochpräziser Strahl: Der feine Fokuspunkt des Lasers ermöglicht das Schneiden kleiner Radien und scharfer Winkel und erleichtert so komplexe Geometrien.
- Komplizierte Muster: Detaillierte Muster, Perforationen und Gravuren können einwandfrei ausgeführt werden und verbessern sowohl die Funktionalität als auch die Ästhetik der Komponenten.
- Nichtlineare Schneidpfade: Die Laserschneidmaschine kann komplexen, nichtlinearen Pfaden ohne mechanische Einschränkungen folgen und ist daher ideal für innovative Designs.
Schnelle Anpassung an unterschiedliche Projekte
Die Flexibilität der Laserschneidtechnologie stellt sicher, dass sich Hersteller schnell an neue Projekte oder Änderungen der Produktionsanforderungen anpassen können.
- Schnelle Einrichtung: Beim Wechsel zwischen Aufträgen ist nur eine minimale Einrichtungszeit erforderlich, da die Anpassungen digital und nicht physisch vorgenommen werden.
- Effiziente Produktionsumstellung: Die Möglichkeit, verschiedene Designdateien schnell zu laden, ermöglicht effiziente Übergänge zwischen verschiedenen Produkten oder Komponenten.
- Skalierbarkeit: Unabhängig davon, ob ein einzelner Prototyp oder die Massenproduktion erforderlich ist, können mit dem Laserschneiden Vorgänge problemlos nach oben oder nach unten skaliert werden.
Anwendungsbeispiele
Die Vielseitigkeit und Flexibilität des Laserschneidens finden in zahlreichen Branchen praktische Anwendung:
- Architektur und Bauwesen: Individuelle Metallplatten, dekorative Elemente und Strukturkomponenten profitieren von der Fähigkeit des Laserschneidens, einzigartige Designs mit Präzision herzustellen.
- Automobilindustrie: Vom Prototyping neuer Modelle bis zur Produktion komplexer Teile wie Motorkomponenten und komplizierter Karosserien unterstützt das Laserschneiden Innovation und Effizienz.
- Luft- und Raumfahrtsektor: Der Bedarf an leichten und dennoch robusten Komponenten aus Spezialmaterialien wird durch die Präzision und Materialvielseitigkeit des Laserschneidens erfüllt.
- Fertigung von Elektronikteilen: Kleine, präzise Komponenten wie Gehäuse und Halterungen werden effizient hergestellt und berücksichtigen dabei die schnellen Entwicklungszyklen der Branche.
- Kunst und Design: Künstler und Designer nutzen das Laserschneiden, um komplizierte Skulpturen, Installationen und funktionale Kunstwerke mit komplexen Mustern und Formen zu schaffen.
- Medizinische Geräte: Individuelle chirurgische Instrumente und medizinische Geräte erfordern präzise Schnitte und spezielle Materialien, die durch Laserschneiden ohne Beeinträchtigung der Sterilität oder Qualität erreicht werden.
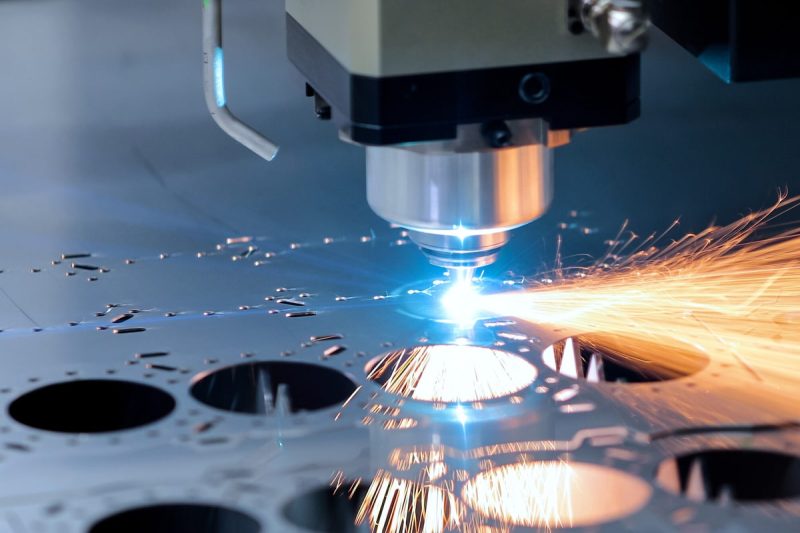
Reduzierter Materialabfall
Minimale Schnittbreite
Der Schnitt ist die Breite des beim Schneidvorgang entfernten Materials. Beim Laserschneiden ist die Schnittbreite im Vergleich zu herkömmlichen Schneideverfahren außergewöhnlich schmal.
- Präzisionsschneiden: Laserschneidmaschinen sind extrem fein, oft weniger als 0,1 mm im Durchmesser. Diese Präzision ermöglicht enge Schneidewege und minimiert die Materialmenge, die als Abfall entsteht.
- Effiziente Materialnutzung: Eine kleinere Schnittbreite bedeutet, dass die Teile näher beieinander liegen können, wodurch die Anzahl der aus einem einzelnen Blatt geschnittenen Teile maximiert wird.
- Geringerer Materialverlust: Im Schnittspalt wird weniger Material verbraucht, was sich direkt in geringeren Materialkosten und Abfall niederschlägt.
Fortschrittliche Nesting-Software
Laserschneidmaschinen sind mit ausgefeilter Nesting-Software ausgestattet, die die Platzierung der Teile auf dem Blech optimiert.
- Optimale Layouts: Die Software berechnet die effizienteste Anordnung verschiedener Formen und Größen, um jede mögliche Fläche des Blattes zu nutzen.
- Automatisierte Effizienz: Durch die Automatisierung des Verschachtelungsprozesses werden menschliche Fehler minimiert und die Materialnutzung maximiert.
- Anpassbare Parameter: Benutzer können die Einstellungen basierend auf spezifischen Projektanforderungen, Materialtypen und -stärken anpassen, um die Effizienz weiter zu steigern.
Weniger Verschnitt und Ausschuss
Bei herkömmlichen Schneideverfahren entstehen häufig erhebliche Verschnitte und Abfallmaterial. Beim Laserschneiden werden diese Reste minimiert.
- Präzises Verschachteln: Dank modernster Software und minimaler Schnittfuge werden die Teile eng verschachtelt, sodass weniger Material ungenutzt bleibt.
- Anpassung an komplexe Formen: Beim Laserschneiden können komplizierte Designs ohne erhöhten Abfall bearbeitet werden, im Gegensatz zu Methoden, die mit nicht standardmäßigen Formen Probleme haben.
- Effiziente Wiederverwendung von Materialien: Kleinere anfallende Abfälle können oft für kleinere Teile wiederverwendet werden, was den Abfall weiter reduziert.
Kosteneinsparungen durch Materialeffizienz
Die Reduzierung von Materialabfällen führt für Hersteller zu direkten Kosteneinsparungen.
- Geringere Materialkosten: Durch die Maximierung der Teileanzahl pro Blech wird die Gesamtmenge des benötigten Rohmaterials reduziert.
- Geringere Kosten für die Abfallentsorgung: Weniger Ausschuss bedeutet geringere Kosten für die Handhabung und Entsorgung von Abfallmaterial.
- Verbesserte Gewinnspannen: Eine effiziente Materialnutzung trägt zur allgemeinen Kostensenkung bei und steigert die Rentabilität.
Vorteile für die Umwelt
Materialeffizienz ist nicht nur gut fürs Geschäft – sie ist gut für den Planeten.
- Ressourcenschonung: Durch den geringeren Materialeinsatz werden natürliche Ressourcen geschont und die Umweltauswirkungen durch den Abbau und die Verarbeitung von Metallen verringert.
- Reduzierter CO2-Fußabdruck: Effiziente Herstellungsprozesse verbrauchen weniger Energie und erzeugen weniger Emissionen.
- Nachhaltige Produktion: Unternehmen können ihr Engagement für Nachhaltigkeit fördern und umweltbewusste Verbraucher und Partner ansprechen.
Anwendungsbeispiele
Die Vorteile einer Reduzierung des Materialabfalls zeigen sich branchenübergreifend:
- Luft- und Raumfahrtindustrie: Häufig werden teure Materialien wie Titan und Aluminium verwendet. Die Minimierung der Verschwendung dieser teuren Ressourcen senkt die Produktionskosten erheblich.
- Automobilherstellung: Die Produktion großer Stückzahlen profitiert von der Materialeffizienz, senkt die Kosten und hält gleichzeitig die Qualitätsstandards ein.
- Werkstätten für Sonderanfertigungen: Kleinere Unternehmen können durch die Reduzierung von Materialabfällen und die Gewinnung von mehr Kunden wettbewerbsfähige Preise anbieten.
- Elektronikindustrie: Präzise Komponenten erfordern minimalen Materialeinsatz; Laserschneiden gewährleistet eine effiziente Produktion ohne Kompromisse bei der Qualität.
- Architekturprojekte: Großformatige Designs mit komplizierten Mustern können mit minimalem Abfall ausgeführt werden, was Projekte kostengünstiger und umweltfreundlicher macht.
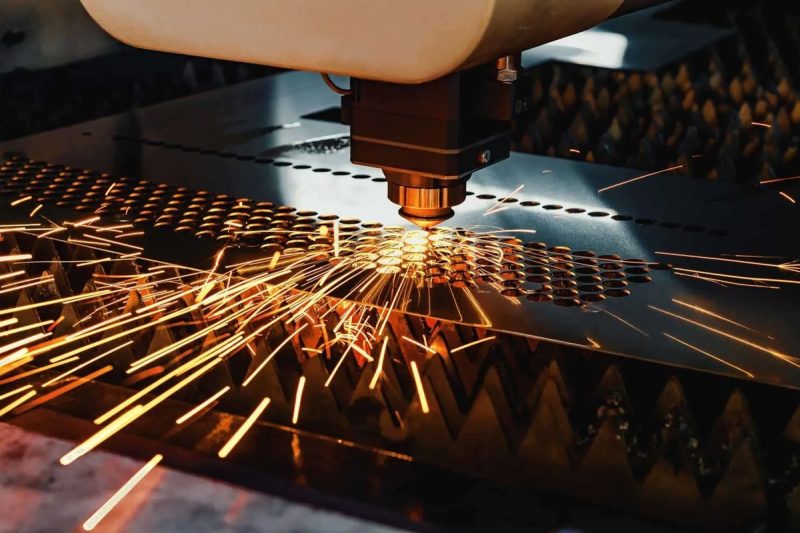
Kosteneffektivität
Niedrigere Arbeitskosten
Laserschneidmaschinen sind hochautomatisiert, was die Abhängigkeit von Handarbeit und die damit verbundenen Kosten reduziert.
- Automatisierungseffizienz: Laserschneidmaschinen verfügen über erweiterte Automatisierungsfunktionen, die einen Dauerbetrieb mit minimalem menschlichen Eingriff ermöglichen.
- Geringerer Personalbedarf: Im Vergleich zu herkömmlichen Schneidemethoden werden für die Bedienung von Laserschneidmaschinen weniger Bediener benötigt, was zu Einsparungen bei den Arbeitskosten führt.
- Geringere Schulungskosten: Benutzerfreundliche Schnittstellen und intuitive Bedienelemente ermöglichen eine schnelle und effektive Schulung der Bediener. Dadurch werden der Zeit- und Kostenaufwand für umfangreiche Schulungsprogramme reduziert.
Reduzierte Werkzeugkosten
Bei herkömmlichen Schneideverfahren sind häufig für jedes Design individuelle Werkzeuge erforderlich, deren Herstellung teuer und zeitaufwändig sein kann.
- Keine Notwendigkeit für physische Werkzeuge: Beim Laserschneiden wird ein fokussierter Laserstrahl zum Schneiden von Materialien verwendet, wodurch die Notwendigkeit für physische Schneidwerkzeuge, die sich abnutzen oder ersetzt werden müssen, entfällt.
- Designflexibilität ohne Mehrkosten: Änderungen im Produktdesign erfordern keine neuen Werkzeuge, Aktualisierungen können direkt in der Software vorgenommen werden, was Zeit und Geld spart.
- Geringere Wartungskosten: Ohne physische Werkzeuge müssen weniger Geräte gewartet oder ersetzt werden, was die laufenden Betriebskosten senkt.
Energieeffizienz
Der Energieverbrauch stellt einen erheblichen Betriebskostenfaktor in der Fertigung dar. Maschinen werden im Hinblick auf Energieeffizienz konstruiert.
- Fortschrittliche Lasertechnologie: Der Faserlasergenerator im Faserlaser-Schneidemaschine ist energieeffizienter als die CO2-Laserröhre der herkömmlichen CO2-Laserschneidmaschine, verbraucht weniger Strom und bietet gleichzeitig hervorragende Leistung.
- Reduzierte Betriebskosten: Ein geringerer Energieverbrauch führt zu niedrigeren Stromrechnungen und trägt so zu allgemeinen Kosteneinsparungen bei.
- Umweltfreundlich: Energieeffiziente Maschinen sparen nicht nur Geld, sondern reduzieren auch den CO2-Fußabdruck und unterstützen nachhaltige Herstellungsverfahren.
Langfristige Einsparungen
Die Investition in Laserschneidtechnologie bietet erhebliche finanzielle Vorteile auf lange Sicht.
- Haltbarkeit und Langlebigkeit: Laserschneidmaschinen werden aus hochwertigen Komponenten gebaut, die eine lange Lebensdauer mit minimalen Ausfallzeiten gewährleisten.
- Gleichbleibende Qualität reduziert Abfall: Die Präzision des Laserschneidens verringert Fehler und Materialabfall und spart auf lange Sicht Geld für Nacharbeit und Materialabfall.
- Kapitalrendite: Die Kombination aus reduzierten Betriebskosten und gesteigerter Produktivität führt zu einer schnelleren Kapitalrendite.
Skalierbarkeit
Die Laserschneidtechnologie bietet die Flexibilität, den Betriebsablauf ohne nennenswerte Kostenauswirkungen nach oben oder unten zu skalieren.
- Anpassbare Produktionsmengen: Ob bei der Erfüllung kleiner Sonderbestellungen oder großer Produktionsläufe – Laserschneidmaschinen können sich effizient an unterschiedliche Mengenanforderungen anpassen.
- Schnelle Umrüstungen: Durch die schnelle Einrichtung und minimale Ausfallzeiten zwischen den Aufträgen können Hersteller rasch auf die Marktnachfrage reagieren, ohne dass zusätzliche Kosten entstehen.
- Ressourcenoptimierung: Durch Skalierbarkeit wird eine optimale Nutzung der Ressourcen gewährleistet, wodurch unnötige Ausgaben für Arbeitskräfte oder Materialien bei Schwankungen des Produktionsbedarfs vermieden werden.
Anwendungsbeispiele
Die Wirtschaftlichkeit der Laserschneidtechnologie kommt verschiedenen Branchen und Anwendungen zugute:
- Kleine und mittlere Unternehmen (KMU): KMU können das Laserschneiden nutzen, um durch die Senkung der Produktionskosten wettbewerbsfähige Preise anzubieten und so mit größeren Unternehmen zu konkurrieren.
- Automobilherstellung: Die Teileproduktion in großen Stückzahlen profitiert von niedrigeren Arbeits- und Werkzeugkosten und verbessert so die Gewinnmargen ohne Einbußen bei der Qualität.
- Werkstätten für Sonderanfertigungen: Unternehmen, die maßgeschneiderte Metallarbeiten anbieten, können ihre Gemeinkosten senken und so Sonderprojekte für die Kunden erschwinglicher machen, ohne dass die Rentabilität darunter leidet.
- Elektronikindustrie: Energieeffizientes Laserschneiden reduziert die Betriebskosten bei der Massenproduktion elektronischer Komponenten und Gehäuse.
- Architektur und Bauwesen: Die Fähigkeit, komplexe Designs kostengünstig zu erstellen, ermöglicht es Architekten und Bauherren, innovative Metallelemente ohne übermäßige Kosten in Projekte zu integrieren.
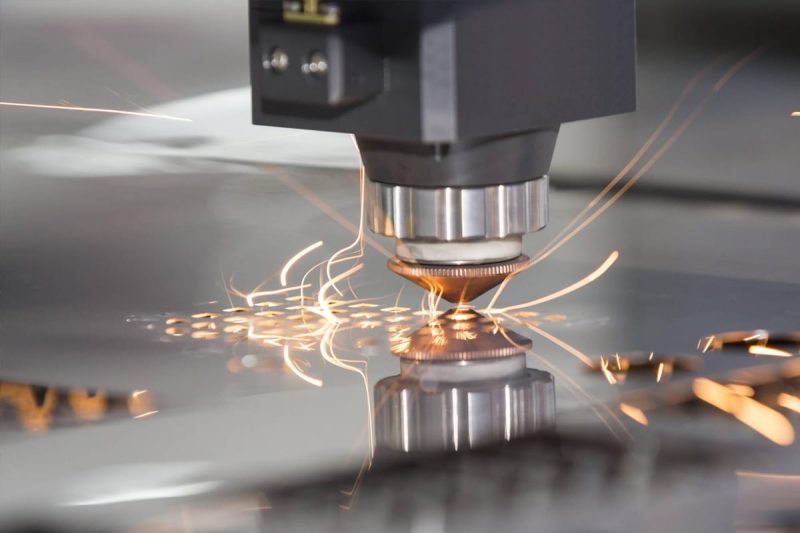
Berührungsloser Prozess reduziert Verzerrungen
Minimierung mechanischer Belastungen
Beim Laserschneiden ist kein physischer Kontakt zwischen Schneidwerkzeug und Material mehr erforderlich.
- Keine physikalische Krafteinwirkung: Der Laserstrahl schneidet das Material mit konzentrierter Lichtenergie, nicht mit mechanischer Kraft. Durch diese Berührungslosigkeit wird kein Druck auf das Blech ausgeübt.
- Reduziertes Risiko einer Verformung: Ohne mechanische Belastung behält das Material seine Ebenheit und Form, wodurch ein Verziehen oder Verbiegen verhindert wird, das bei herkömmlichen Schneideverfahren auftreten kann.
- Ideal für empfindliche Materialien: Dünne oder empfindliche Metalle, die durch mechanische Schneidwerkzeuge beschädigt werden könnten, werden mit dem Laserschneiden sicher bearbeitet, wobei ihre strukturelle Integrität erhalten bleibt.
Reduzierte Wärmeeinflusszone
Obwohl beim Laserschneiden hohe Temperaturen entstehen, ist der Vorgang stark lokalisiert.
- Konzentrierte Wärmeanwendung: Der Laser konzentriert die Wärme auf einen winzigen Bereich und schmilzt oder verdampft das Metall genau dort, wo der Schnitt erforderlich ist.
- Minimale Wärmeausbreitung: Das umgebende Material erfährt einen vernachlässigbaren Temperaturanstieg, wodurch die Wärmeeinflusszone (WEZ) reduziert und thermische Verzerrungen verhindert werden.
- Erhaltung der Materialeigenschaften: Durch die Begrenzung der Wärmeeinflusszone bleiben die mechanischen und chemischen Eigenschaften des Metalls außerhalb des unmittelbaren Schneidbereichs unverändert, wodurch eine gleichbleibende Materialleistung gewährleistet wird.
Saubere und glatte Kanten
Die Präzision des Laserschneidens führt zu einer überragenden Kantenqualität.
- Gratfreie Oberflächen: Der Laser erzeugt saubere Schnitte mit glatten Kanten, sodass keine nachträglichen Endbearbeitungsprozesse wie Schleifen oder Schmirgeln erforderlich sind.
- Verbesserte Ästhetik: Bei Anwendungen, bei denen die Kante sichtbar oder für das Design entscheidend ist, liefert das Laserschneiden ein hochwertiges Finish, das das Gesamterscheinungsbild verbessert.
- Verbesserte Passform und Montage: Glatte Kanten sorgen dafür, dass die Teile nahtlos zusammenpassen, was die Effizienz der Montageprozesse und die Qualität des Endprodukts verbessert.
Wahrung der Materialintegrität
Durch die Beibehaltung der ursprünglichen Eigenschaften des Metalls bleibt die Leistung der Teile erhalten.
- Keine Materialverunreinigung: Da das Laserschneiden berührungslos erfolgt, besteht keine Gefahr einer Verunreinigung durch Schneidwerkzeuge oder Schmiermittel, welche die Materialreinheit beeinträchtigen könnte.
- Erhalt der strukturellen Integrität: Durch die Vermeidung mechanischer und übermäßiger thermischer Belastung bleibt die innere Struktur des Metalls intakt, was Haltbarkeit und Zuverlässigkeit gewährleistet.
- Geeignet für hochpräzise Anwendungen: Branchen mit hohen Anforderungen an die Standards, wie etwa die Luft- und Raumfahrt oder die Medizintechnik, profitieren von der Fähigkeit des Laserschneidens, die Materialeigenschaften zu bewahren.
Anwendungsbeispiele
Die Vorteile eines berührungslosen Prozesses kommen in verschiedenen Branchen zum Einsatz:
- Luft- und Raumfahrtindustrie: Komponenten wie Turbinenschaufeln und Strukturelemente erfordern präzise Schnitte, ohne dass die Materialeigenschaften verändert werden. Durch Laserschneiden wird sichergestellt, dass diese Teile strenge Spezifikationen erfüllen, ohne sich zu verformen.
- Herstellung medizinischer Geräte: Chirurgische Instrumente und Implantate müssen mit exakten Abmessungen und glatten Oberflächen hergestellt werden, um die Patientensicherheit zu gewährleisten. Laserschneiden sorgt für die notwendige Präzision und Sauberkeit.
- Elektronik und Mikrofabrikation: Kleine, empfindliche Komponenten wie Leiterplatten und Mikrochips profitieren von der Präzision des Laserschneidens und der fehlenden mechanischen Belastung, wodurch Schäden während der Herstellung vermieden werden.
- Automobilsektor: Hochfeste Stähle und Speziallegierungen für Automobilteile erfordern Schneideverfahren, die die Materialintegrität nicht beeinträchtigen. Laserschneiden liefert verzugsfreie Komponenten, die die Fahrzeugleistung verbessern.
- Kunst und Design: Künstler und Designer nutzen das Laserschneiden, um komplizierte Metallarbeiten mit sauberen Kanten und präzisen Details zu erstellen, ohne das Material zu verzerren.
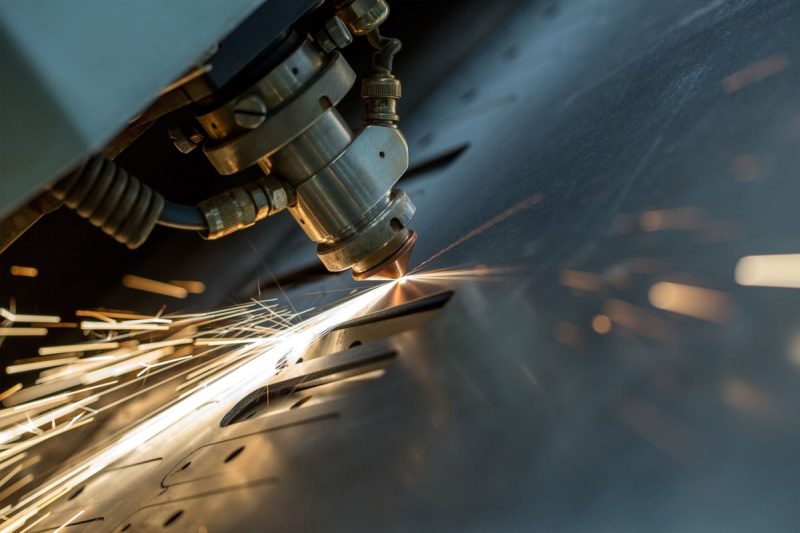
Zusammenfassung
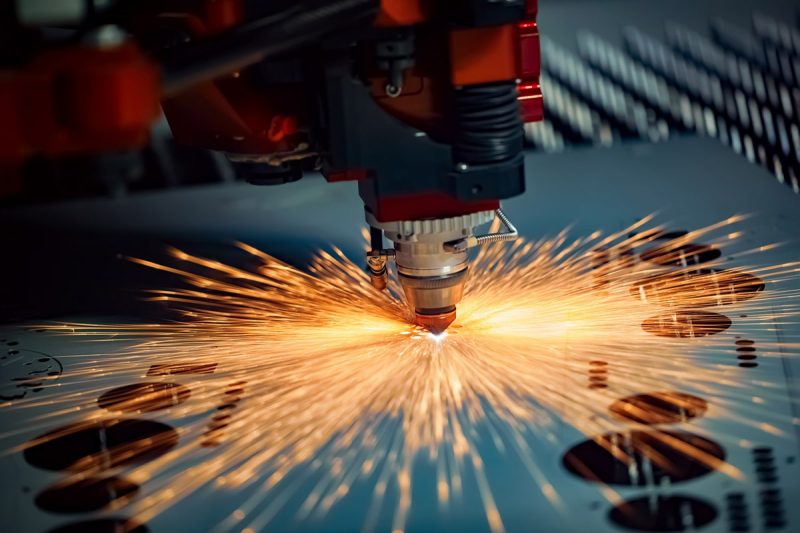
Holen Sie sich Laserschneidlösungen
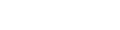
- [email protected]
- [email protected]
- +86-19963414011
- Nr. 3 Zone A, Industriegebiet Lunzhen, Stadt Yucheng, Provinz Shandong.