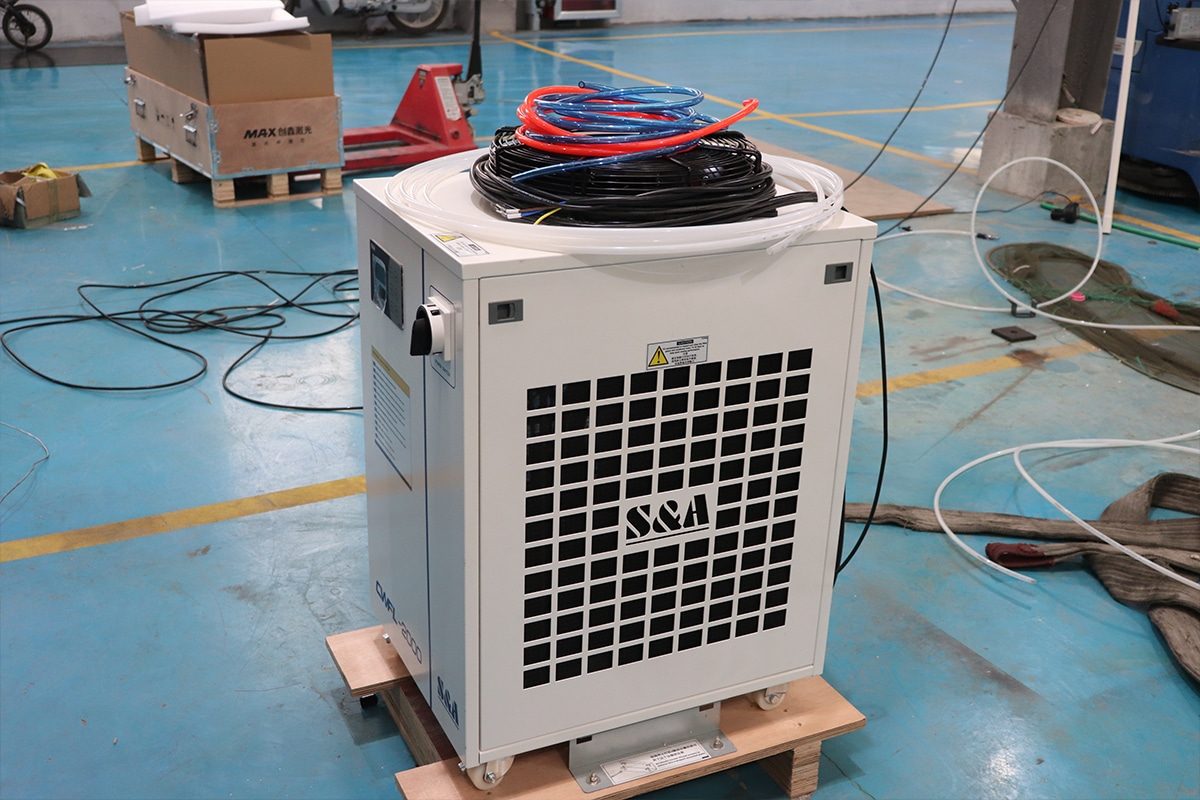
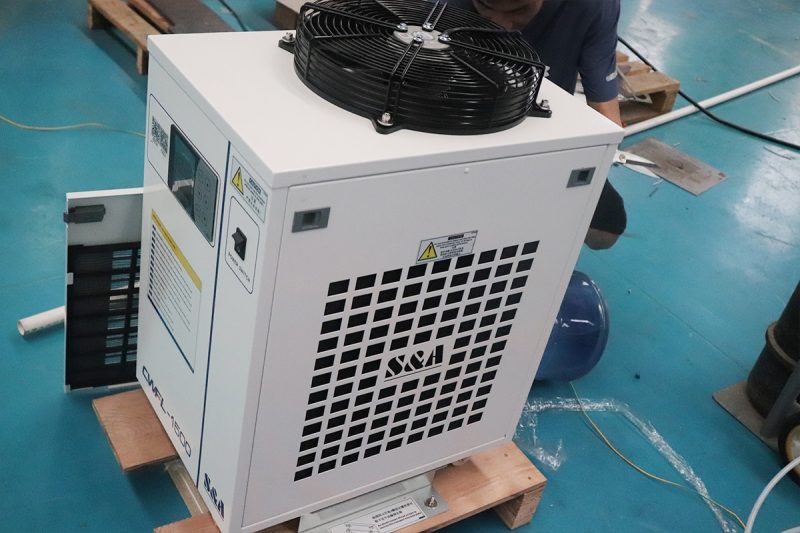
Was ist ein Kühlsystem
Hitzeerzeugung
In Laserschneidmaschinen entsteht Wärme vor allem durch zwei Prozesse:
- Laserbetrieb: Die Laserquelle (ob es sich nun um einen CO2-Lasergenerator, einen Faserlasergenerator oder einen anderen Typ handelt) erzeugt viel Wärme, wenn sie den zum Schneiden verwendeten Hochenergiestrahl aussendet. Die Umwandlung elektrischer Energie in Laserlicht ist nicht sehr effizient und die überschüssige Energie wird als Wärme freigesetzt.
- Materialinteraktion: Wenn der Laserstrahl mit dem zu schneidenden Material interagiert, verursacht er eine lokale Erwärmung, die zum Schmelzen, Verbrennen oder Verdampfen führt. Dieser Prozess wirkt sich nicht nur auf das Material aus, sondern erzeugt auch zusätzliche Wärme, die bewältigt werden muss.
Ohne ein wirksames Kühlsystem kann die aufgestaute Hitze eine Reihe von Problemen verursachen, darunter:
- Thermische Verformung: Übermäßige Hitze kann zu einer Verformung des Laserstrahls führen, was eine schlechte Schnittqualität zur Folge hat.
- Verschlechterte Komponentenleistung: Eine anhaltende Einwirkung hoher Temperaturen kann die Leistung der Laserquelle, der Optik und anderer wichtiger Komponenten beeinträchtigen und so ihre Lebensdauer verkürzen.
- Sicherheitsrisiken: Übermäßige Hitze birgt Sicherheitsrisiken, darunter Brand- oder Geräteausfallgefahr.
Komponenten eines Kühlsystems
Das typische Kühlsystem in einem Laser-Schneide-Maschine besteht aus mehreren Schlüsselkomponenten:
- Wärmetauscher: Geräte, die Wärme von der Laserschneidmaschine auf ein Kühlmedium (Luft oder Flüssigkeit) übertragen. Sie entfernen überschüssige Wärme und halten eine stabile Temperatur aufrecht.
- Lüfter: Lüfter werden in luftgekühlten Systemen verwendet, um den Luftstrom zwischen wärmeerzeugenden Komponenten zu erleichtern und so die Wärmeableitung durch Konvektion zu unterstützen.
- Kühlkörper: Kühlkörper bestehen üblicherweise aus Materialien mit hoher Wärmeleitfähigkeit, wie beispielsweise Aluminium oder Kupfer, und nehmen die Wärme von Komponenten auf und geben sie an die Umgebungsluft ab.
- Pumpen: In flüssigkeitsgekühlten Systemen zirkulieren Pumpen das Kühlmittel durch das System und sorgen so für eine kontinuierliche Wärmeaufnahme und -übertragung.
- Kühler: Aktive Kühlgeräte, die die Temperatur des Kühlmittels in einem flüssigkeitsgekühlten System regeln, indem sie dem Kühlmittel Wärme entziehen.
- Kühlmittel: Normalerweise Flüssigkeiten, wie zum Beispiel mit Frostschutzmittel vermischtes Wasser, die Wärme vom Lasergenerator und anderen Komponenten aufnehmen und abführen.
- Behälter: Sie speichern das Kühlmittel und ermöglichen seine Ausdehnung und Kontraktion aufgrund von Temperaturänderungen.
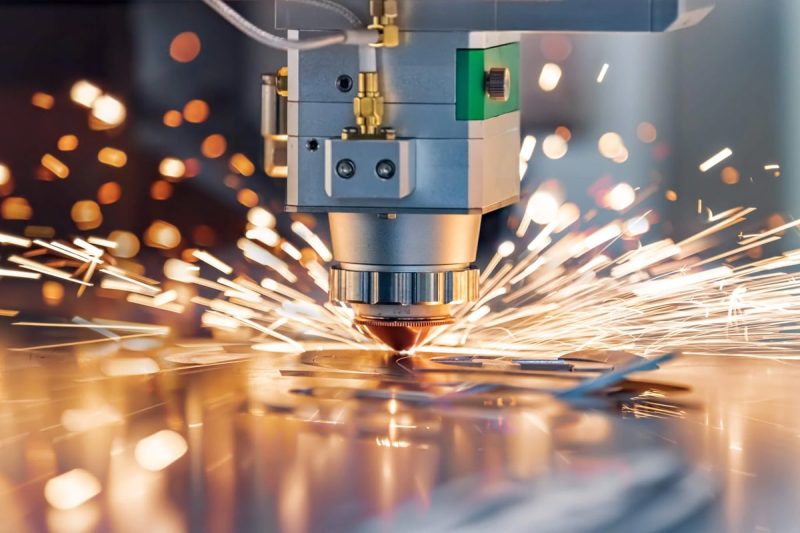
Bedeutung des Kühlsystems einer Laserschneidmaschine
Aufrechterhaltung der optimalen Lasertemperatur
Verbesserung der Schnittqualität
Verlängern Sie die Maschinenlebensdauer
Verbesserte Betriebseffizienz
Sicherheit
Energieeffizienz
Unterstützt die Materialvielseitigkeit
Reduzieren Sie Ausfallzeiten und Wartungsaufwand
Präzision und Wiederholbarkeit
Optimiert für Hochleistungsanwendungen
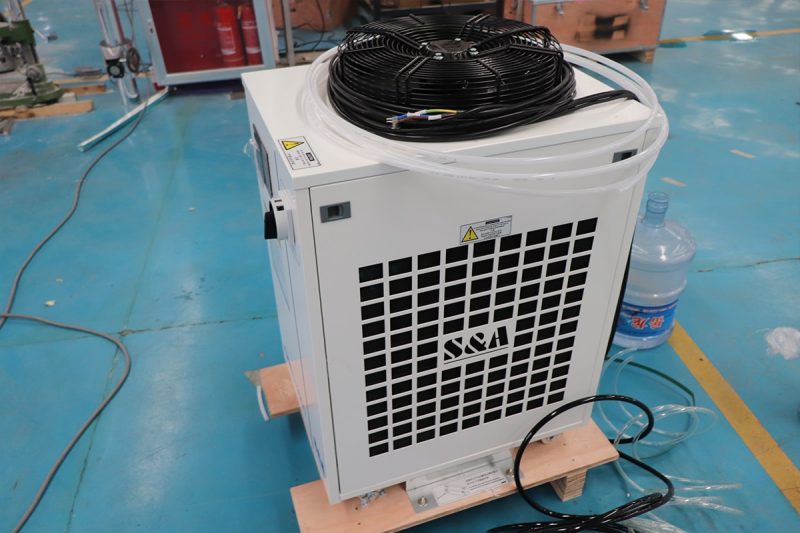
Arten von Kühlsystemen
Luftkühlungssysteme
Komponenten und Mechanismen
- Lüfter: Lüfter werden verwendet, um Luft über wärmeerzeugende Komponenten wie die Laserquelle und das Netzteil zu blasen. Dieser Prozess verbessert die konvektive Wärmeübertragung und trägt dazu bei, Wärme an die Umgebung abzugeben.
- Kühlkörper: Kühlkörper bestehen normalerweise aus Materialien mit hoher Wärmeleitfähigkeit, wie Aluminium oder Kupfer. Sie absorbieren Wärme von den Laserkomponenten und übertragen sie an die darüber strömende Luft.
Vorteile von Luftkühlsystemen
- Einfachheit: Luftkühlsysteme sind unkompliziert zu implementieren. Sie erfordern weniger Komponenten und sind weniger komplex als Flüssigkeitskühlsysteme.
- Niedrigere Kosten: Die Anschaffungskosten und Wartungskosten für Luftkühlsysteme sind im Allgemeinen niedriger als für Flüssigkeitskühlsysteme.
- Geringer Wartungsaufwand: Diese Systeme haben weniger Teile, die ausfallen können oder regelmäßig gewartet werden müssen, wodurch der Gesamtwartungsaufwand reduziert wird.
Nachteile von Luftkühlungssystemen
- Begrenzte Kühlleistung: Bei Hochleistungslasern oder Anwendungen mit großer Wärmeentwicklung ist die Luftkühlung weniger effektiv.
- Lärm: Lüfter können Lärm erzeugen, der in bestimmten Umgebungen störend sein kann.
- Platzbedarf: Eine effektive Luftkühlung erfordert oft viel Platz für die Luftzirkulation, was bei kompakten Maschinendesigns möglicherweise nicht möglich ist.
Flüssigkeitskühlsysteme
Komponenten und Mechanismen
- Kühlmittelzirkulation: Eine Pumpe zirkuliert das Kühlmittel durch das System und sorgt so für eine kontinuierliche Wärmeabsorption vom Laser und anderen wärmeerzeugenden Komponenten. Das Kühlmittel fließt durch Kanäle oder Rohre, die in direktem Kontakt mit diesen Komponenten stehen.
- Wärmetauscher: Wärmetauscher übertragen Wärme vom Kühlmittel auf ein anderes Medium, normalerweise Luft oder eine andere Flüssigkeit. Dieser Prozess kann Heizkörper umfassen, bei denen das erwärmte Kühlmittel durch Spulen fließt und Wärme an die Luft überträgt, oder Plattenwärmetauscher, die eine Reihe dünner Platten verwenden, um die Wärmeübertragung zwischen dem Kühlmittel und einer anderen Flüssigkeit zu erleichtern.
- Kühler: Kühler sind aktive Kühlgeräte, die die Temperatur des Kühlmittels regeln. Sie entziehen dem Kühlmittel Wärme und leiten diese nach außen ab. Dabei verwenden sie häufig einen Kühlkreislauf, um das Kühlmittel auf einer bestimmten Temperatur zu halten.
Vorteile von Flüssigkeitskühlsystemen
- Hohe Kühleffizienz: Flüssigkeitskühlsysteme leiten die Wärme äußerst effektiv ab und eignen sich daher für Hochleistungslaser und einen längeren Betrieb.
- Präzise Temperaturregelung: Diese Systeme ermöglichen eine genauere und stabilere Temperaturregelung und sorgen so für eine gleichbleibende Laserleistung.
- Leiser Betrieb: Flüssigkeitskühlsysteme sind tendenziell leiser als Luftkühlsysteme, da sie zur Wärmeableitung weniger auf Lüfter angewiesen sind.
Nachteile von Flüssigkeitskühlsystemen
- Höhere Anschaffungskosten: Die Komponenten und die Installation von Flüssigkeitskühlsystemen sind im Allgemeinen teurer als die von Luftkühlsystemen.
- Komplexität und Wartung: Flüssigkeitskühlsysteme erfordern regelmäßige Wartung, um Lecks, Kühlmittelverschlechterung und andere Probleme zu vermeiden. Die Komplexität dieser Systeme kann bei auftretenden Problemen auch zu höheren Reparaturkosten und Ausfallzeiten führen.
- Leckagegefahr: Flüssigkeitskühlsysteme sind anfällig für Leckagen, die zu Schäden an der Laserschneidmaschine und Betriebsstörungen führen können.
Vergleich und Anwendbarkeit
Die Wahl zwischen Luftkühlungs- und Flüssigkeitskühlungssystemen hängt von mehreren Faktoren ab, darunter der Leistung des Lasers, der Dauer und Intensität des Schneidvorgangs sowie den spezifischen Anforderungen der Anwendung.
- Anwendungen mit geringer bis mittlerer Leistung: Für Laserschneidmaschinen mit geringerem Leistungsbedarf reicht in der Regel ein Luftkühlsystem aus. Es bietet eine kostengünstige und einfache Lösung für das Wärmemanagement ohne komplexe Komponenten oder aufwändige Wartung.
- Hochleistungs- und Hochpräzisionsanwendungen: Für Anwendungen, die hohe Leistung erfordern oder bei denen Präzision entscheidend ist, sind Flüssigkeitskühlsysteme die bevorzugte Wahl. Ihre überlegenen Kühlfähigkeiten und die präzise Temperaturregelung stellen sicher, dass der Lasergenerator optimal arbeitet und eine gleichbleibende Leistung und hochwertige Schnitte liefert.
- Betriebsumgebung: Auch die Betriebsumgebung der Laserschneidmaschine kann sich auf die Wahl des Kühlsystems auswirken. In lauten oder beengten Umgebungen können Flüssigkeitskühlsysteme trotz höherer Kosten und Wartungsanforderungen vorteilhafter sein.
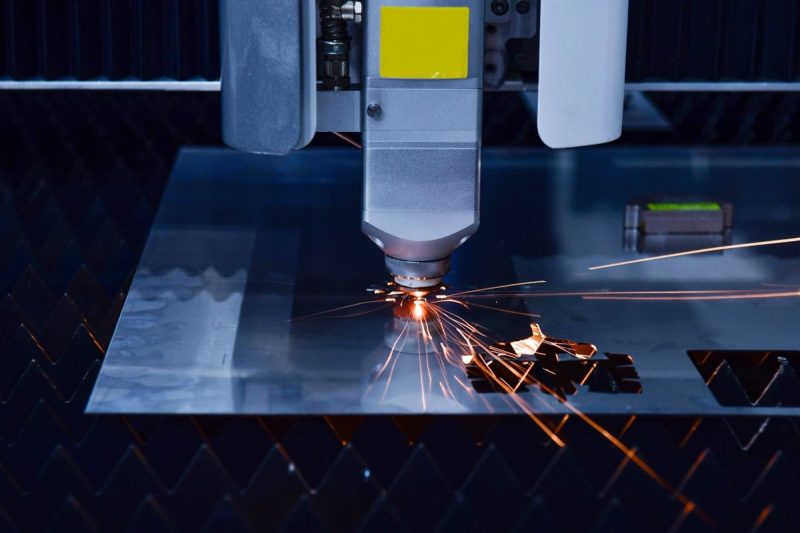
Wichtige Parameter, die die Leistung des Kühlsystems beeinflussen
Kühlkapazität
Die Kühlleistung bezeichnet die Wärmemenge, die das Kühlsystem in einem bestimmten Zeitraum abführen kann. Sie wird üblicherweise in Kilowatt (kW) oder British Thermal Units pro Stunde (BTU/h) gemessen. Die Kühlleistung muss gleich oder größer sein als die vom Laser und anderen Komponenten erzeugte Wärme, um eine Überhitzung zu vermeiden. Zu den Faktoren, die die Kühlleistung beeinflussen, gehören:
- Größe und Typ des Wärmetauschers: Größere oder effizientere Wärmetauscher können mehr Wärme ableiten.
- Kühlmitteldurchflussrate: Höhere Durchflussraten erhöhen die Wärmemenge, die von den Komponenten abgeführt werden kann.
Kühlmitteltyp und -eigenschaften
Art und Eigenschaften des in einem Flüssigkeitskühlsystem verwendeten Kühlmittels können die Leistung erheblich beeinflussen. Wichtige Kühlmitteleigenschaften sind:
- Wärmeleitfähigkeit: Eine höhere Wärmeleitfähigkeit ermöglicht es dem Kühlmittel, Wärme effizienter aufzunehmen und zu übertragen.
- Viskosität: Eine niedrigere Viskosität verringert den Strömungswiderstand und verbessert die Fähigkeit des Kühlmittels, zu zirkulieren und Wärme abzuleiten.
- Spezifische Wärmekapazität: Eine höhere spezifische Wärmekapazität bedeutet, dass das Kühlmittel mehr Wärme aufnehmen kann, bevor die Temperatur deutlich ansteigt.
Durchflussrate und Druck
Umgebungstemperatur und Umweltbedingungen
Wärmetauscher-Effizienz
Die Effizienz von Wärmetauschern wie Heizkörpern, Plattenwärmetauschern und Kühlschlangen bestimmt, wie effizient Wärme vom Kühlmittel an die Umgebung abgegeben wird. Zu den Faktoren, die die Effizienz von Wärmetauschern beeinflussen, gehören:
- Oberfläche: Je größer die Oberfläche, desto mehr Raum steht für die Wärmeübertragung zur Verfügung und desto höher ist die Effizienz.
- Material: Materialien mit hoher Wärmeleitfähigkeit, wie Kupfer oder Aluminium, verbessern die Wärmeübertragung.
- Design: Effiziente Designs, wie gerippte Oberflächen oder gewellte Platten, erhöhen die Turbulenz im Kühlmittelstrom, was den Wärmeaustausch verbessert.
Lüfter- und Pumpenleistung
Bei luftgekühlten Systemen trägt die Leistung des Lüfters zu einer effektiven Wärmeableitung bei. Zu den Parametern, die die Lüfterleistung beeinflussen, gehören:
- Luftstromrate: Höhere Luftstromraten verbessern die konvektive Wärmeübertragung zum Kühlkörper.
- Lüftergeschwindigkeit: Die einstellbare Lüftergeschwindigkeit optimiert die Kühlung entsprechend den Betriebsbedingungen der Maschine.
Bei flüssigkeitsgekühlten Systemen ist die Pumpenleistung ebenso wichtig. Zu den wichtigsten Parametern gehören:
- Durchflussrate: Das pro Zeiteinheit zirkulierte Kühlmittelvolumen beeinflusst die Effizienz der Wärmeableitung.
- Druckhöhe: Der Druckunterschied, den die Pumpe aufrechterhalten kann, beeinflusst die Durchflussrate und die Fähigkeit des Systems, den Widerstand des Kühlmittelkreislaufs zu überwinden.
Steuerungssysteme und Sensoren
Fortschrittliche Steuerungssysteme und Sensoren verbessern die Leistung des Kühlsystems durch Echtzeitüberwachung und -anpassung. Wichtige Steuerungsparameter sind:
- Temperatursensoren: Die Überwachung der Temperaturen an kritischen Punkten ermöglicht eine präzise Steuerung des Kühlvorgangs.
- Durchflusssensoren: Durch die Gewährleistung eines ausreichenden Kühlmitteldurchflusses wird eine Überhitzung verhindert und die Effizienz verbessert.
- Rückkopplungsschleifen: Automatisierte Systeme, die Lüftergeschwindigkeiten, Pumpengeschwindigkeiten und Kühlereinstellungen basierend auf Echtzeitdaten anpassen, optimieren Kühlleistung und Energieeffizienz.
Wartung und Reinigung
Regelmäßige Wartung und Reinigung von Kühlsystemen tragen zu einer kontinuierlichen, gleichbleibenden Leistung bei. Zu den wichtigsten Wartungsaufgaben gehören:
- Reinigen von Wärmetauschern und Filtern: Durch das Entfernen von Staub und Schmutz von Wärmetauschern und Filtern wird eine effiziente Luftzirkulation und Wärmeübertragung gewährleistet.
- Kühlmittelstand und -qualität prüfen: Durch die Aufrechterhaltung des richtigen Kühlmittelstands und den Austausch von verbrauchtem Kühlmittel werden Überhitzung und Korrosion vermieden.
- Überprüfen und Ersetzen verschlissener Teile: Regelmäßiges Überprüfen und rechtzeitiges Ersetzen verschlissener Lüfter, Pumpen und Dichtungen beugen Ausfällen vor und gewährleisten eine anhaltende Kühlleistung.
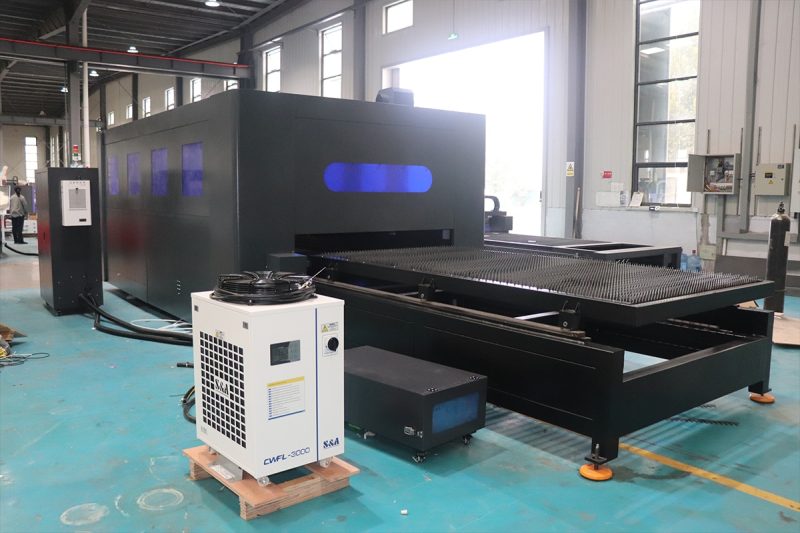
So wählen Sie ein geeignetes Kühlsystem
Bewerten Sie die Laserleistung und Wärmebelastung
Der erste Schritt bei der Auswahl eines geeigneten Kühlsystems besteht in der Beurteilung der Laserleistung und der damit verbundenen Wärmebelastung. Leistungsstärkere Laser erzeugen mehr Wärme und erfordern daher robustere Kühllösungen.
- Laserleistung: Bestimmen Sie die Leistung der Laserquelle, die normalerweise in Watt (W) gemessen wird. Leistungsstärkere Laser (z. B. 1 kW und mehr) erzeugen mehr Wärme und erfordern effizientere Kühlsysteme.
- Betriebsintensität: Berücksichtigen Sie die Betriebsintensität und den Arbeitszyklus der Maschine. Maschinen, die kontinuierlich oder mit hoher Geschwindigkeit laufen, erzeugen mehr Wärme und erfordern daher ein Kühlsystem, das längere Wärmebelastungen bewältigen kann.
Bestimmen Sie die erforderliche Kühlleistung
Nachdem Sie die Laserleistung und die Wärmebelastung ermittelt haben, berechnen Sie die Kühlleistung, die zur Aufrechterhaltung optimaler Betriebstemperaturen erforderlich ist.
- Berechnung der Wärmebelastung: Schätzen Sie die gesamte Wärmebelastung, die vom Laser und anderen Komponenten erzeugt wird. Dazu gehören der Lasergenerator, die Stromversorgung, Bewegungssysteme und alle Zusatzgeräte.
- Anpassung der Kühlleistung: Stellen Sie sicher, dass die Leistung des Kühlsystems, gemessen in Kilowatt (kW) oder British Thermal Units pro Stunde (BTU/h), der berechneten Wärmelast entspricht oder diese übersteigt. Um Schwankungen der Betriebsbedingungen Rechnung zu tragen, wird häufig eine Sicherheitsmarge von 10-20% empfohlen.
Kühlsystemtypen bewerten
Luftkühlungssysteme
Luftkühlsysteme verwenden Lüfter und Kühlkörper, um die Wärme vom Laser und anderen Komponenten abzuleiten.
- Einfachheit und Kosten: Luftkühlsysteme sind einfacher und kostengünstiger zu installieren und zu warten. Sie eignen sich für Laser mit geringer bis mittlerer Leistung.
- Überlegungen zu Platz und Lärm: Berücksichtigen Sie den verfügbaren Platz für die Luftzirkulation und den von den Lüftern erzeugten Lärm. Luftkühlsysteme können laut sein und benötigen möglicherweise viel Platz für eine effektive Wärmeableitung.
Flüssigkeitskühlsysteme
Flüssigkeitskühlsysteme verwenden ein Kühlmittel, normalerweise eine Mischung aus Wasser und Frostschutzmittel, um die Wärme vom Laser aufzunehmen und abzuleiten.
- Kühleffizienz: Flüssigkeitskühlsysteme sind für Hochleistungslasergeneratoren effizienter und effektiver, da sie eine präzise Temperaturregelung und höhere Kühlleistung bieten.
- Komplexität und Wartung: Diese Systeme sind komplexer und erfordern regelmäßige Wartung, um Probleme wie Lecks und Kühlmittelverschlechterung zu vermeiden. Berücksichtigen Sie die Verfügbarkeit von Wartungsressourcen und Fachwissen.
Berücksichtigen Sie Umwelt- und Betriebsfaktoren
Bei der Auswahl des geeigneten Kühlsystems spielen Umwelt- und Betriebsfaktoren eine wesentliche Rolle.
- Umgebungstemperatur: Hohe Umgebungstemperaturen verringern die Effizienz von Luftkühlsystemen. In solchen Umgebungen können Flüssigkeitskühlsysteme effektiver sein.
- Staub und Verunreinigungen: Staubige oder verunreinigte Umgebungen können Luftfilter und Wärmetauscher verstopfen und so die Kühlleistung verringern. Flüssigkeitskühlsysteme sind gegenüber solchen Bedingungen im Allgemeinen widerstandsfähiger.
- Platzbeschränkungen: Bewerten Sie den verfügbaren Platz für die Installation des Kühlsystems. Flüssigkeitskühlsysteme benötigen möglicherweise mehr Platz für Komponenten wie Behälter, Pumpen und Kühler.
Analysieren Sie die Gesamtbetriebskosten
Berücksichtigen Sie bei der Auswahl eines Kühlsystems die Gesamtbetriebskosten, einschließlich Anschaffungskosten, Betriebsausgaben und Wartungsaufwand.
- Anschaffungskosten: Vergleichen Sie die Anschaffungskosten von Luft- und Flüssigkeitskühlsystemen, einschließlich Installation und Einrichtung.
- Betriebskosten: Bewerten Sie den Energieverbrauch des Kühlsystems. Flüssigkeitskühlsysteme sind im Allgemeinen energieeffizienter, können aber höhere Anschaffungskosten verursachen.
- Wartungskosten: Berücksichtigen Sie den Wartungsaufwand und die damit verbundenen Kosten für jeden Kühlsystemtyp. Regelmäßige Wartung ist sowohl für Luft- als auch für Flüssigkeitskühlsysteme unerlässlich, um eine langfristige Leistung sicherzustellen.
Überprüfen Sie die Spezifikationen und Empfehlungen des Herstellers
Beachten Sie die Herstellerspezifikationen und Empfehlungen für Kühlsysteme der Laserschneidmaschine. Hersteller geben häufig Richtlinien zu den optimalen Kühllösungen für ihre Geräte an.
- Kompatibilität: Stellen Sie sicher, dass das Kühlsystem mit der jeweiligen Marke und dem Modell der Laserschneidmaschine kompatibel ist.
- Leistungsgarantien: Einige Hersteller bieten Leistungsgarantien oder Gewährleistungen bei Verwendung ihrer empfohlenen Kühlsysteme.
Berücksichtigen Sie zukünftige Skalierbarkeit
Berücksichtigen Sie das Potenzial für zukünftige Upgrades oder Änderungen der Betriebsanforderungen. Wählen Sie ein Kühlsystem, das bei Bedarf erhöhte Wärmelasten oder Lasergeneratoren mit höherer Leistung bewältigen kann.
- Modulare Systeme: Achten Sie auf modulare Kühlsysteme, die sich je nach Bedarf erweitern oder aufrüsten lassen.
- Flexibles Design: Stellen Sie sicher, dass sich das Kühlsystem an Änderungen der Betriebsbedingungen oder Maschinenkonfigurationen anpassen kann.
Suchen Sie eine Expertenberatung
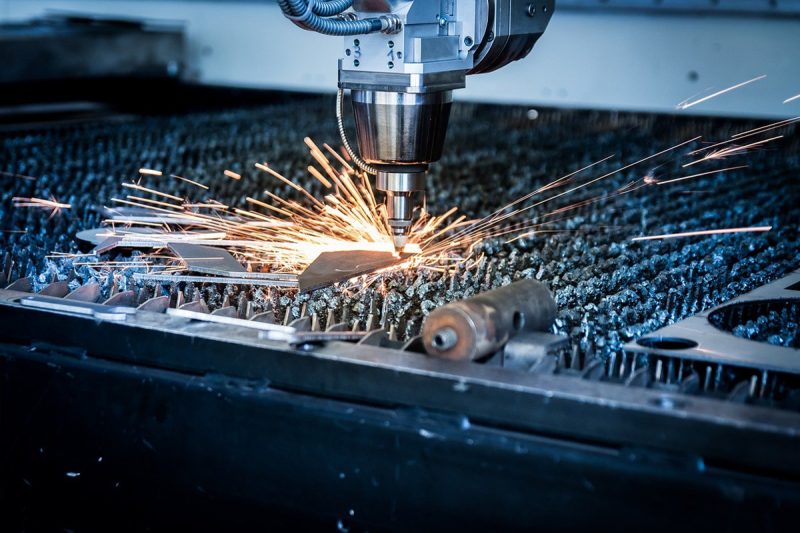
Zusammenfassung
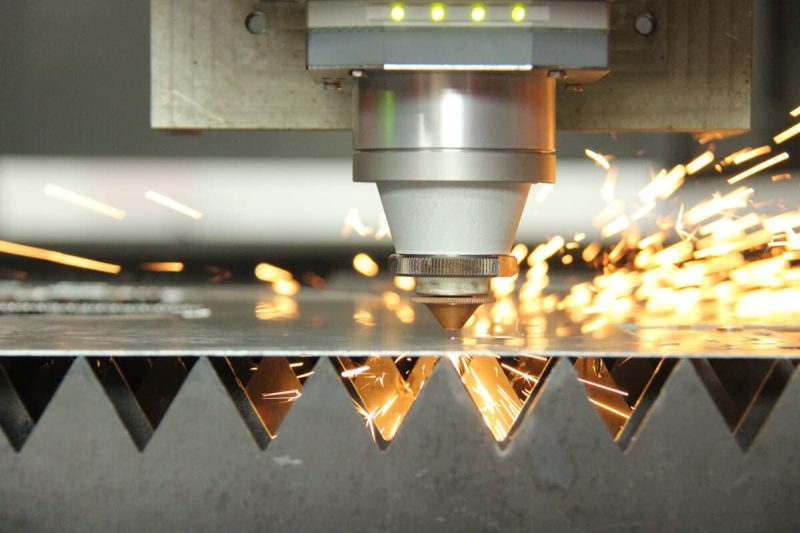
Holen Sie sich Laserschneidlösungen
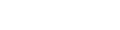
- [email protected]
- [email protected]
- +86-19963414011
- Nr. 3 Zone A, Industriegebiet Lunzhen, Stadt Yucheng, Provinz Shandong.