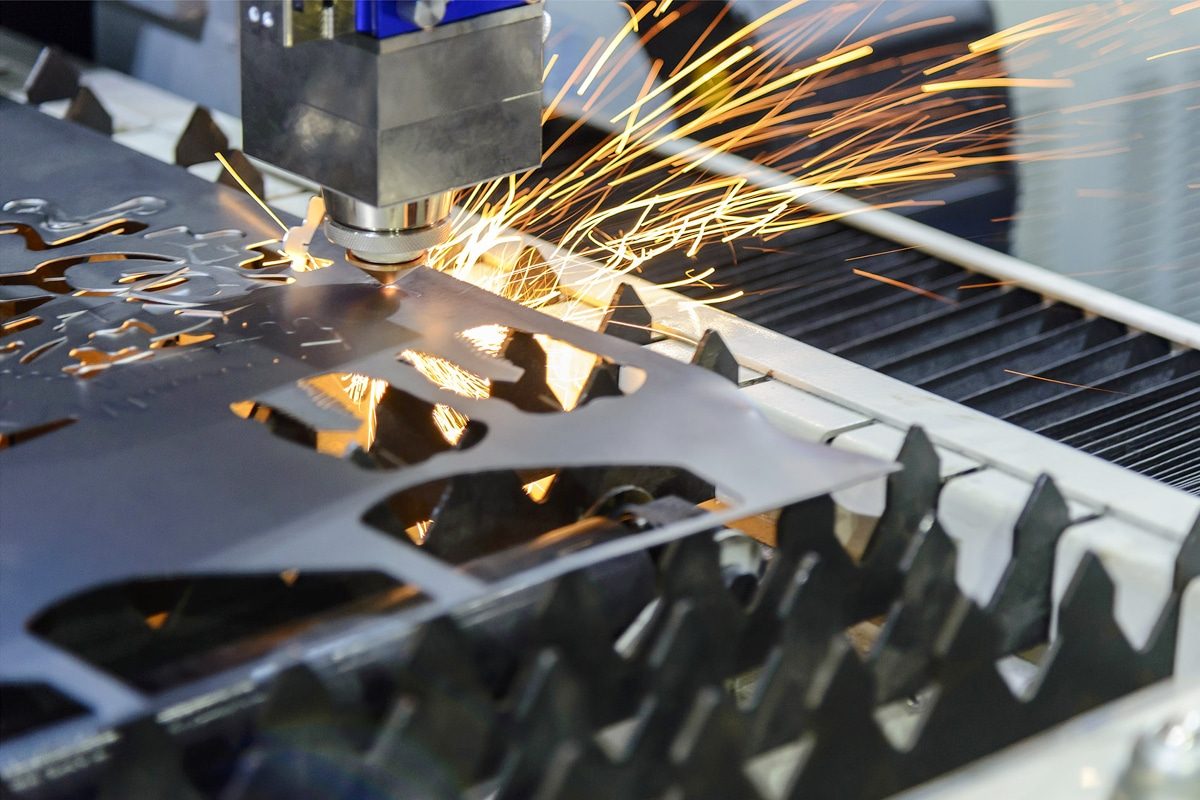
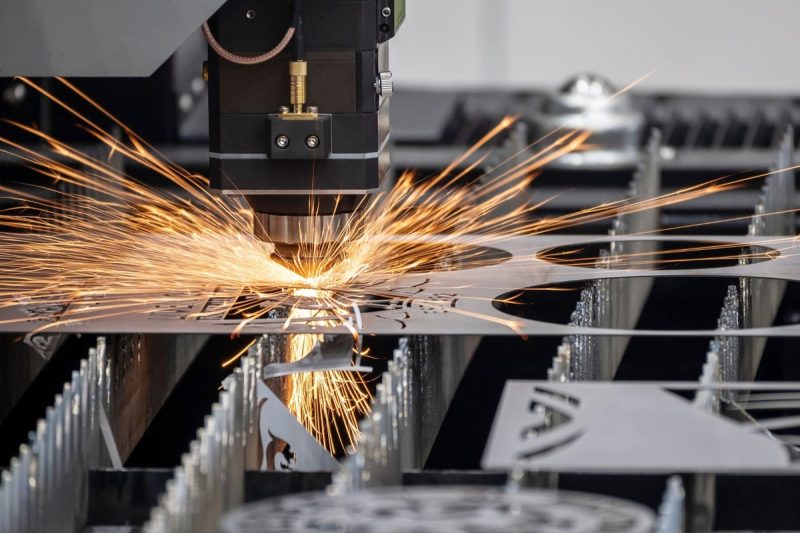
Erfahren Sie mehr über Laserschneiden
Beschreibung des Laserschneidens
Arten von Lasern, die in Schneidanwendungen verwendet werden
Faserlaser
CO2-Laser
Komponenten eines Laserschneidsystems
Das typische Laserschneidanlage besteht aus mehreren Schlüsselkomponenten, die zusammenarbeiten, um eine präzise und effiziente Schneidleistung zu gewährleisten:
- Laserquelle: Dies ist die Kernkomponente, die den Laserstrahl erzeugt. Je nach Anwendung kann die Laserquelle ein Faserlasergenerator, ein CO2-Lasergenerator oder ein anderer Lasergeneratortyp sein.
- Optik: Spiegel und Linsen dienen dazu, den Laserstrahl auf das zu schneidende Material zu lenken und zu fokussieren. Die Qualität der Optik beeinflusst die Genauigkeit und Effizienz des Schneidprozesses.
- Schneidkopf: Der Schneidkopf enthält die Fokussierlinse und die Düse, durch die der Laserstrahl und das Hilfsgas geleitet werden. Er ist für die Einhaltung der richtigen Brennweite und optimale Schneidbedingungen verantwortlich.
- Arbeitstisch: Unterstützt das zu schneidende Material und verfügt normalerweise über einen Mechanismus zum Bewegen des Materials unter den Schneidkopf.
- CNC-Steuerung: Die CNC-Steuerung steuert die Bewegung des Laserschneidkopfes und des Werkstücks und folgt dem programmierten Schneidpfad, um die gewünschte Form und das gewünschte Muster zu erzeugen.
- Hilfsgasversorgung: Hilfsgas unterstützt den Schneidvorgang, indem es geschmolzenes Material wegbläst, die Schneidzone kühlt und Oxidation verhindert. Übliche Hilfsgase sind Sauerstoff, Stickstoff und Druckluft.
- Absaugsystem: Entfernt beim Schneidvorgang entstehende Dämpfe und Rückstände, um eine saubere Arbeitsumgebung aufrechtzuerhalten und die Optik und Laserkomponenten zu schützen.
- Kühlsystem: Beim Laserschneiden entsteht viel Wärme, die abgeleitet werden muss, um Schäden an der Laserquelle und anderen Komponenten zu vermeiden. Kühlsysteme wie Wasserkühler werden verwendet, um optimale Betriebstemperaturen aufrechtzuerhalten.
Wichtige Parameter, die die Leistung beim Laserschneiden beeinflussen
Mehrere Parameter können die Leistung und Qualität des Laserschneidprozesses beeinflussen. Das Verständnis und die Optimierung dieser Parameter kann dazu beitragen, die gewünschten Ergebnisse zu erzielen:
- Laserleistung: Die Ausgangsleistung der Laserquelle bestimmt die Dicke und Art des Materials, das geschnitten werden kann. Höhere Leistungen ermöglichen das Schneiden dickerer Materialien, aber andere Parameter müssen möglicherweise angepasst werden, um die Schnittqualität beizubehalten.
- Schnittgeschwindigkeit: Die Geschwindigkeit, mit der sich der Schneidkopf über das Werkstück bewegt. Eine optimale Schnittgeschwindigkeit sorgt für ein Gleichgewicht zwischen Produktivität und Schnittqualität. Eine zu hohe Geschwindigkeit kann zu unvollständigen Schnitten führen, während eine zu niedrige Geschwindigkeit zu übermäßiger Hitzeentwicklung und Materialschäden führen kann.
- Brennpunkt: Die Position des Brennpunkts des Laserstrahls relativ zur Materialoberfläche. Der richtige Fokus gewährleistet eine maximale Energiedichte am Schnittpunkt, was zu sauberen und präzisen Schnitten führt. Eine Fehlausrichtung kann zu schlechter Schnittqualität und verringerter Effizienz führen.
- Art und Druck des Hilfsgases: Art und Druck des verwendeten Hilfsgases (Sauerstoff, Stickstoff oder Druckluft) haben erhebliche Auswirkungen auf den Schneidvorgang. Die richtige Gasauswahl und der richtige Druck optimieren die Entfernung des geschmolzenen Materials, verhindern Oxidation und verbessern die Schnittqualität.
- Materialart und -dicke: Unterschiedliche Materialien und Dicken reagieren unterschiedlich auf das Laserschneiden. Beim Einstellen der Schneidparameter müssen Materialeigenschaften wie Reflexionsgrad, Wärmeleitfähigkeit und Schmelzpunkt berücksichtigt werden.
- Strahlqualität: Die Qualität des Laserstrahls, charakterisiert durch Fokus und Modenstruktur, beeinflusst die Präzision und Qualität des Schnitts. Ein hochwertiger Strahl mit kleiner Brennfleckgröße erzeugt feinere Schnitte mit minimaler Schnittbreite.
- Düsendesign: Das Design der Düse, einschließlich Durchmesser und Form, beeinflusst den Hilfsgasfluss und die Entfernung des geschmolzenen Materials. Ein optimiertes Düsendesign verbessert die Schneidleistung und -qualität.
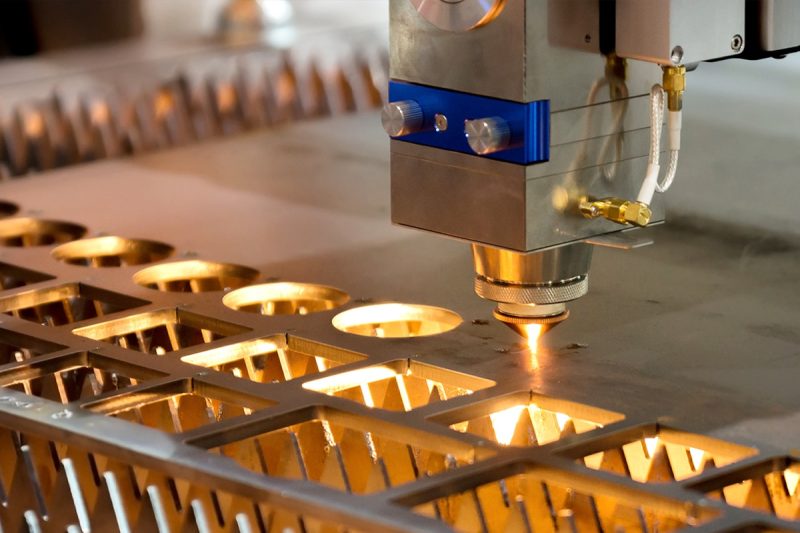
Die Rolle von Hilfsgasen beim Laserschneiden
Entfernen von geschmolzenem Material
Beim Laserschneiden schmilzt ein hochintensiver Laserstrahl das Material an der Schnittstelle. Hilfsgas wird durch eine Düse in den Schneidbereich geleitet und hilft dort, geschmolzenes Material aus dem Schnittspalt (dem vom Laser erzeugten Spalt) zu entfernen. Durch das effektive Entfernen von geschmolzenem Material bleibt die Schnittqualität erhalten und Fehler werden vermieden.
- Effizientes Strahlen: Der hohe Druck des Hilfsgases bläst geschmolzenes Material vom Schnittspalt weg, verhindert so ein erneutes Erstarren auf dem Werkstück und gewährleistet einen sauberen Schnitt.
- Verhinderung der Schlackenbildung: Durch die schnelle Abfuhr des geschmolzenen Materials minimiert das Hilfsgas die Bildung von Schlacke (an der Unterseite des Schnitts haftende Materialrückstände) und verringert so den Bedarf an Nachbearbeitung.
- Beibehaltung der Schnittbreite: Durch die kontinuierliche Entfernung des geschmolzenen Materials wird die gewünschte Schnittbreite beibehalten und die Maßgenauigkeit und Präzision des endgültigen Schnitts sichergestellt.
Kühlung der Schneidzone
Die vom Laserstrahl erzeugte intensive Hitze kann erhebliche thermische Auswirkungen auf das Werkstück haben, darunter Verformungen, Verformungen und Änderungen der Materialeigenschaften. Hilfsgas hilft, diese thermischen Effekte zu kontrollieren, indem es die Schneidzone kühlt.
- Wärmeableitung: Der Hilfsgasstrom absorbiert und leitet überschüssige Wärme im Schneidbereich ab, verhindert so eine Überhitzung und minimiert die thermische Verformung des Materials.
- Reduzierung der Wärmeeinflusszone (WEZ): Durch das Kühlen der Schneidzone wird die Größe der WEZ begrenzt, wodurch die mechanischen Eigenschaften des Materials erhalten bleiben und das Risiko von Verformungen oder anderen thermischen Schäden verringert wird.
- Höhere Schnittgeschwindigkeiten: Eine effiziente Kühlung erhöht die Schnittgeschwindigkeiten, da das Material weniger anfällig für thermisch bedingte Defekte ist. Dies führt zu einer schnelleren und effizienteren Produktion.
Schutz des Objektivs
Die Linse im Schneidkopf fokussiert den Laserstrahl auf das Werkstück. Verunreinigungen wie Rauch, Staub und Schmutz, die während des Schneidvorgangs entstehen, können die Linse beschädigen oder ihre Leistung beeinträchtigen. Hilfsgas schützt die Linse vor Verunreinigungen.
- Linsenabschirmung: Hilfsgas bildet eine Barriere zwischen der Linse und dem Schneidbereich und verhindert, dass Verunreinigungen auf die Linsenoberfläche gelangen und sich dort ablagern.
- Aufrechterhaltung der optischen Qualität: Indem die Linse sauber und frei von Schmutz gehalten wird, gewährleistet das Hilfsgas eine optimale Strahlfokussierung und konstante Schneidleistung.
- Verlängerung der Linsenlebensdauer: Durch die Vermeidung von Verunreinigungen wird der Verschleiß der Linse verringert, ihre Lebensdauer verlängert und die Wartungskosten gesenkt.
Verbesserte Schnittreaktion
Hilfsgase können die chemischen Reaktionen beim Laserschneiden beeinflussen und so die Schneidleistung verschiedener Materialien verbessern. Die Art des verwendeten Gases kann bestimmte Reaktionen fördern oder hemmen, was sich auf die Schnittqualität und -effizienz auswirken kann.
- Sauerstoff (O₂): Sauerstoff wird häufig zum Schneiden von Kohlenstoffstahl verwendet. Er fördert eine exotherme Reaktion mit dem geschmolzenen Metall und erzeugt zusätzliche Wärme, die die Schnittgeschwindigkeit erhöht. Diese Reaktion trägt zu einem sauberen Schnitt mit weniger Bartbildung bei, kann jedoch zu Oxidation an der Schnittkante führen.
- Stickstoff (N₂): Stickstoff ist ein inertes Gas, das häufig zum Schneiden von Edelstahl, Aluminium und anderen Nichteisenmetallen verwendet wird. Es verhindert Oxidation, indem es eine inerte Atmosphäre um die Schneidzone bildet. Dadurch entsteht eine saubere, oxidfreie Kante, was es ideal für Anwendungen macht, die eine hochwertige Oberflächenbeschaffenheit erfordern.
- Druckluft: Druckluft ist eine kostengünstige Alternative, die zum Schneiden einer Vielzahl von Materialien verwendet werden kann. Sie vereint die Eigenschaften von Sauerstoff und Stickstoff und bietet so eine ausreichende Schneidleistung zu geringeren Kosten. Allerdings können dabei Verunreinigungen entstehen, die die Schnittqualität beeinträchtigen.
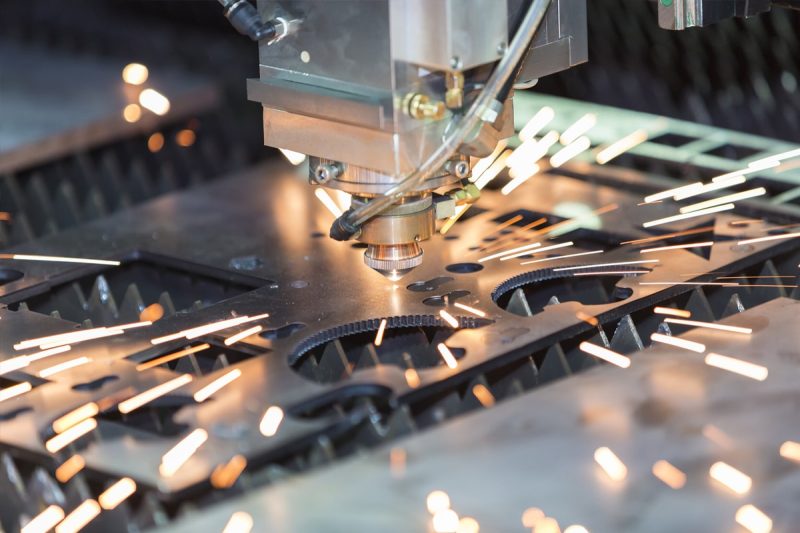
Arten von Hilfsgasen
Sauerstoff (O₂)
Vorteile
- Höhere Schnittgeschwindigkeit: Der Sauerstoff reagiert exotherm mit dem Material und setzt dabei zusätzliche Wärme frei. Diese zusätzliche Wärme erhöht die Schnittgeschwindigkeit, sodass das sauerstoffunterstützte Schneiden insbesondere bei dickeren Materialien deutlich schneller ist.
- Verbesserte Effizienz: Die exotherme Reaktion reduziert die zum Schneiden des Materials erforderliche Laserleistung und verbessert so die Gesamtenergieeffizienz des Schneidprozesses.
- Sauberere Schnitte bei dickeren Materialien: Sauerstoff hilft dabei, sauberere Schnitte bei dickeren Materialien zu erzeugen und reduziert Bart- und Schlackenbildung, was wiederum den Bedarf an aufwändiger Nachbearbeitung verringert.
Nachteile
- Oxidation: Die Reaktion zwischen Sauerstoff und dem Material kann zur Oxidation der Schnittkante führen, was eine rauere Oberfläche und mögliche Korrosionsprobleme zur Folge hat.
- Wärmeeinflusszone (WEZ): Die durch die exotherme Reaktion erzeugte zusätzliche Wärme vergrößert die WEZ, was die mechanischen Eigenschaften des Materials in der Nähe der Schnittkante verändern und Probleme wie Verformungen oder verringerte strukturelle Integrität verursachen kann.
- Einschränkungen bei Nichteisenmetallen: Sauerstoff ist nicht so wirksam wie Nichteisenmetalle wie Aluminium und Kupfer, die nicht so leicht mit Sauerstoff reagieren.
Stickstoff (N₂)
Vorteile
- Oxidationsfreies Schneiden: Stickstoff ist ein Inertgas, das während des Schneidvorgangs nicht mit dem Material reagiert. Diese Eigenschaft verhindert Oxidation und führt zu einer sauberen, hellen, oxidfreien Kante, die ideal für Anwendungen ist, die eine hochwertige Oberflächenbeschaffenheit erfordern.
- Hochwertige Oberflächenbeschaffenheit: Durch die fehlende Oxidation entstehen glattere Kanten und eine glattere Oberflächenbeschaffenheit, wodurch die Notwendigkeit einer Nachbearbeitung reduziert oder eliminiert wird.
- Minimierte Wärmeeinflusszone (WEZ): Stickstoff hilft, eine kleine Wärmeeinflusszone aufrechtzuerhalten, wodurch die mechanischen Eigenschaften des Materials erhalten bleiben und die thermische Verformung minimiert wird. Dies kann verwendet werden, um Präzisionsschnitte und Anwendungen zu erreichen, die enge Toleranzen erfordern.
Nachteile
- Langsamere Schnittgeschwindigkeiten: Ohne die exotherme Reaktion durch Sauerstoff führt das stickstoffunterstützte Schneiden typischerweise zu langsameren Schnittgeschwindigkeiten, insbesondere bei dickeren Materialien. Diese langsamere Geschwindigkeit wirkt sich auf die Gesamtproduktivität aus.
- Höherer Laserleistungsbedarf: Da Stickstoff dem Schneidprozess keine zusätzliche Wärme liefert, muss der Laser die gesamte zum Schneiden des Materials erforderliche Energie bereitstellen. Dieser Bedarf kann zu höherem Energieverbrauch und höheren Betriebskosten führen.
- Kostenüberlegungen: Stickstoff kann teurer als andere Gase sein und der erhöhte Verbrauch durch den höheren Leistungsbedarf des Lasers kann die Betriebskosten weiter erhöhen.
Druckluft
Vorteile
- Kostengünstig: Druckluft ist leichter verfügbar und kostengünstiger als reine Gase wie Stickstoff und Sauerstoff. Dies macht sie zu einer wirtschaftlichen Wahl für viele Laserschneidanwendungen, insbesondere bei dünneren Materialien.
- Vielseitigkeit: Druckluft kann zum Schneiden einer Vielzahl von Materialien verwendet werden, darunter Weichstahl, Edelstahl und Aluminium. Aufgrund ihrer Vielseitigkeit ist sie eine praktische Wahl für allgemeine Schneidarbeiten.
- Reduzierte Betriebskosten: Da Druckluft günstig und weithin verfügbar ist, können durch den Einsatz von Druckluft die Gesamtbetriebskosten gesenkt werden, sodass sich diese Methode für Kleinbetriebe oder kostenbewusste Projekte eignet.
- Vorteile für die Umwelt: Durch die Verwendung von Druckluft verringert sich die Abhängigkeit von Flaschengas, was wiederum den mit der Gasproduktion und dem Gastransport verbundenen CO2-Fußabdruck verringert und somit einen Vorteil für die Umwelt darstellt.
Nachteile
- Geringere Schnittqualität: Sauerstoff und Verunreinigungen in der Druckluft können die Schnittqualität beeinträchtigen, was zu raueren Kanten, erhöhter Bartbildung und potenzieller Verunreinigung der Schnittfläche führt. Dieses Problem ist insbesondere bei Anwendungen spürbar, die eine hohe Oberflächenqualität oder Präzision erfordern.
- Begrenzte Schnittgeschwindigkeiten: Druckluft schneidet im Allgemeinen langsamer als sauerstoffunterstütztes Schneiden, insbesondere bei dickeren Materialien. Diese Einschränkung wirkt sich auf die Produktivität aus und ist möglicherweise nicht für die Produktion großer Stückzahlen geeignet.
- Inkonsistente Ergebnisse: Die Qualität und Leistung beim Schneiden mit Druckluft kann aufgrund von Unterschieden in der Zusammensetzung und dem Druck der Luftzufuhr inkonsistent sein. Diese Inkonsistenz macht es schwierig, von einem Schneidauftrag zum nächsten einheitliche Ergebnisse zu erzielen.
- Oxidation und Schlackebildung: Druckluft enthält verschiedene Gase, darunter auch Sauerstoff, die an der Schnittkante zu Oxidation und Schlackebildung führen können, wodurch eine zusätzliche Nachbearbeitung erforderlich wird, um die gewünschten Ergebnisse zu erzielen.
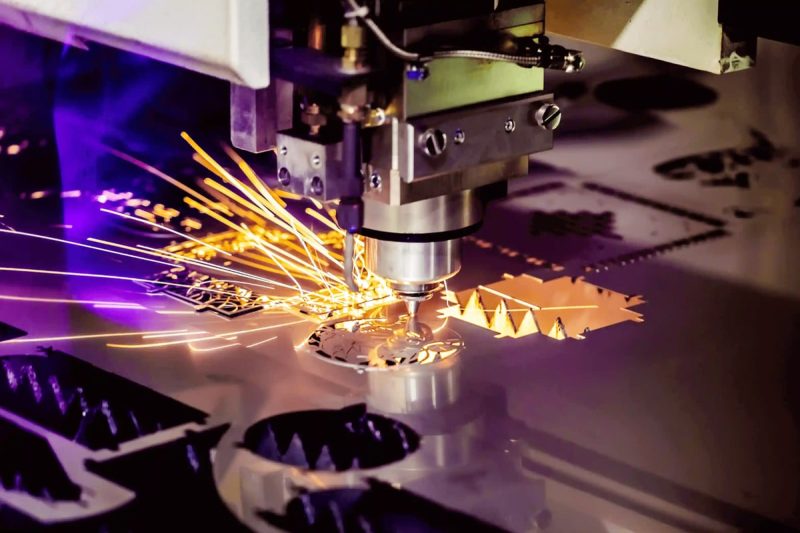
Auswirkungen auf verschiedene Materialien
Kohlenstoffstahl
Sauerstoff
- Vorteile: Sauerstoff wird häufig zum Schneiden von Kohlenstoffstahl verwendet, da er exotherm mit dem Material reagiert. Diese Reaktion erzeugt zusätzliche Wärme, die die Schnittgeschwindigkeit und -effizienz deutlich erhöht. Die resultierenden Schnitte sind normalerweise sauber mit minimaler Bartbildung, und die erhöhte Wärme hilft beim Schneiden dickerer Kohlenstoffstahlabschnitte.
- Nachteile: Die exotherme Reaktion mit Sauerstoff verursacht Oxidation, die, wenn sie nicht behandelt wird, zu einer raueren Oberflächenbeschaffenheit und möglicher Korrosion führen kann. Die Wärmeeinflusszone (WEZ) ist außerdem größer, was die mechanischen Eigenschaften des Materials in der Nähe der Schnittkante beeinträchtigen kann.
Stickstoff
- Vorteile: Stickstoff reagiert nicht mit Kohlenstoffstahl, wodurch Oxidation verhindert wird und ein sauberer, oxidfreier Schnitt entsteht. Dies führt zu einer hochwertigen Oberflächenbeschaffenheit und einer kleineren Wärmeeinflusszone, wodurch die mechanischen Eigenschaften des Materials erhalten bleiben.
- Nachteile: Durch die fehlende exotherme Reaktion ist das Stickstoffschneiden langsamer als das Sauerstoffschneiden. Um die gleiche Schneidgeschwindigkeit zu erreichen, ist eine höhere Laserleistung erforderlich, was die Betriebskosten erhöht.
Druckluft
- Vorteile: Druckluft ist eine kostengünstige Alternative zum Schneiden von Kohlenstoffstahl. Sie bietet ein ausgewogenes Verhältnis zwischen Kosten und Leistung und eignet sich zum Schneiden dünnerer Kohlenstoffstahlprofile.
- Nachteile: Der Sauerstoff in der Druckluft kann zu Oxidation und Schlackebildung führen, was die Schnittqualität beeinträchtigt. Schnittgeschwindigkeit und -qualität sind im Allgemeinen niedriger als bei Verwendung von reinem Sauerstoff oder Stickstoff.
Edelstahl
Sauerstoff
- Vorteile: Sauerstoff kann zum Schneiden von Edelstahl verwendet werden und sorgt aufgrund der exothermen Reaktion für hohe Schnittgeschwindigkeiten. Diese Reaktion kann auch dazu beitragen, saubere Schnitte mit minimaler Bartbildung zu erzielen.
- Nachteile: Durch die Verwendung von Sauerstoff kann es zu Oxidation kommen, die zu Verfärbungen der Kanten und potenziellen Korrosionsproblemen führen kann. Die Oxidschicht erfordert möglicherweise eine zusätzliche Nachbearbeitung, um die gewünschte Oberflächenqualität zu erreichen.
Stickstoff
- Vorteile: Stickstoff ist das Gas der Wahl zum Schneiden von Edelstahl, da es Oxidation verhindert und so eine saubere, helle, oxidfreie Kante ergibt. Die inerte Natur von Stickstoff erzeugt hochwertige Schnitte mit minimalem Nachbearbeitungsbedarf. Stickstoff hilft auch dabei, die mechanischen Eigenschaften des Materials zu erhalten, indem es die Wärmeeinflusszone minimiert.
- Nachteile: Stickstoff hat langsamere Schneidgeschwindigkeiten und erfordert eine höhere Laserleistung als Sauerstoff, was zu höherem Energieverbrauch und höheren Betriebskosten führt.
Druckluft
- Vorteile: Mit Druckluft lassen sich dünnere Abschnitte aus Edelstahl schneiden. Druckluft ist kostengünstiger als reines Gas und eine sinnvolle Option für Anwendungen, bei denen keine hohe Präzision erforderlich ist.
- Nachteile: Sauerstoff in der Druckluft kann zu Oxidation und Schlackebildung führen, was die Schnittqualität beeinträchtigt. Die Kante muss nach dem Schnitt möglicherweise zusätzlich gereinigt und nachbearbeitet werden.
Aluminium und Nichteisenmetalle
Sauerstoff
- Vorteile: Sauerstoff wird im Allgemeinen nicht zum Schneiden von Aluminium und anderen Nichteisenmetallen empfohlen, da diese eine hohe Reflektivität und geringe Absorption des Laserstrahls aufweisen. In einigen Fällen kann Sauerstoff jedoch beim Schneiden dickerer Abschnitte helfen, indem er eine exotherme Reaktion fördert.
- Nachteile: Sauerstoff kann zu starker Oxidation führen, was zu einer rauen und porösen Schnittoberfläche führt. Diese Oxidation kann sich negativ auf die Eigenschaften und das Aussehen des Materials auswirken und erfordert eine umfangreiche Nachbearbeitung.
Stickstoff
- Vorteile: Stickstoff ist sehr effektiv beim Schneiden von Aluminium und anderen Nichteisenmetallen. Es verhindert Oxidation und sorgt für eine saubere, helle und hochwertige Schneide. Stickstoff hilft auch, die Wärmeeinflusszone zu minimieren und so die mechanischen Eigenschaften des Materials zu bewahren.
- Nachteile: Stickstoffunterstütztes Schneiden ist langsamer als das Schneiden mit Sauerstoff und erfordert eine höhere Laserleistung zum Schneiden des Materials, was die Betriebskosten erhöht.
Druckluft
- Vorteile: Druckluft ist eine kostengünstige Option zum Schneiden dünnerer Abschnitte aus Aluminium und Nichteisenmetallen. Sie kann eine zufriedenstellende Schneidleistung für Anwendungen bieten, bei denen Präzision nicht entscheidend ist.
- Nachteile: Sauerstoff in der Druckluft kann zu Oxidation und Schlackebildung führen, was die Schnittqualität beeinträchtigt. Kanten können eine zusätzliche Nachbearbeitung erfordern, um das gewünschte Finish zu erzielen.
Nichtmetallische Werkstoffe
Sauerstoff
- Vorteile: Sauerstoff kann zum Schneiden nichtmetallischer Materialien wie Holz, Acryl und Kunststoff verwendet werden. Die exotherme Reaktion mit Sauerstoff kann bei einigen Materialien die Schnittgeschwindigkeit und -effizienz erhöhen.
- Nachteile: Durch die Verwendung von Sauerstoff können Materialien wie Holz und Acryl versengt und verbrannt werden, was sich negativ auf die Oberflächenqualität auswirkt. Dies kann dazu führen, dass zusätzliche Nachbearbeitungsprozesse erforderlich sind, um das gewünschte Erscheinungsbild zu erzielen.
Stickstoff
- Vorteile: Stickstoff eignet sich gut zum Schneiden nichtmetallischer Materialien wie Kunststoffe und Keramik, die vor Oxidation geschützt werden müssen. Es verhindert Verfärbungen und erzeugt saubere, hochwertige Kanten bei minimalen thermischen Schäden.
- Nachteile: Stickstoffunterstütztes Schneiden kann langsamer sein als Sauerstoff und erfordert eine höhere Laserleistung, um die gewünschte Schnittgeschwindigkeit zu erreichen.
Druckluft
- Vorteile: Druckluft ist eine kostengünstige Lösung zum Schneiden nichtmetallischer Materialien und bietet für eine Vielzahl von Anwendungen ausreichende Schneidleistung. Sie eignet sich für Anwendungen, bei denen Präzision und Qualität nicht entscheidend sind.
- Nachteile: Verunreinigungen in der Druckluft können die Schnittqualität beeinträchtigen und zu rauen Kanten und möglichen Verunreinigungen führen. Schnittqualität und -geschwindigkeit sind möglicherweise nicht mit denen von reinen Gasen wie Sauerstoff oder Stickstoff vergleichbar.
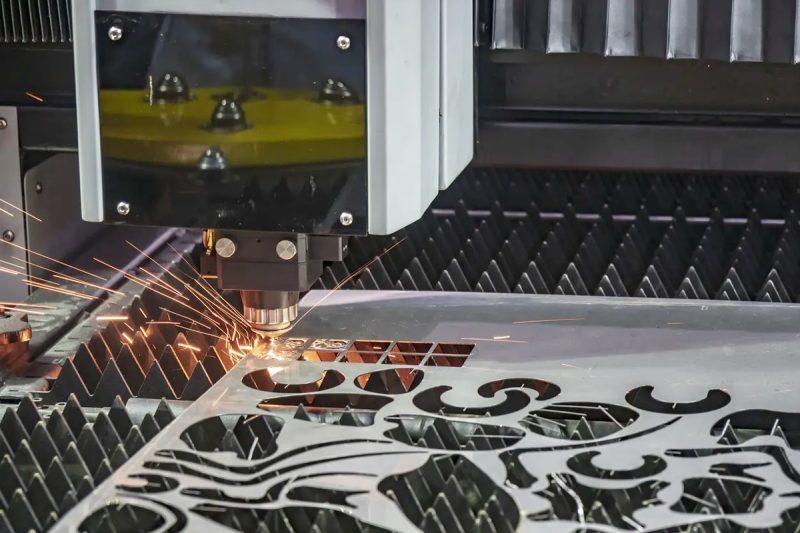
Optimierung der Hilfsgasauswahl
Materialart und -stärke
Die Art und Dicke des zu schneidenden Materials sind wichtige Überlegungen bei der Auswahl eines Hilfsgases. Verschiedene Materialien reagieren unterschiedlich auf verschiedene Gase, was sich auf die Schnittqualität und -effizienz auswirkt.
- Kohlenstoffstahl: Sauerstoff ist oft die erste Wahl zum Schneiden von Kohlenstoffstahl, da er exotherm reagiert und so die Schnittgeschwindigkeit und -effizienz erhöht. Bei dickerem Kohlenstoffstahl kann Sauerstoff die zum effektiven Schneiden des Materials erforderliche Wärme liefern. Bei dünnerem Kohlenstoffstahl kann Stickstoff verwendet werden, um einen sauberen, oxidationsfreien Schnitt zu erzielen, wenn auch langsamer.
- Edelstahl: Stickstoff ist ideal zum Schneiden von Edelstahl, da er Oxidation verhindert und eine hochwertige, glatte Schneide erzeugt. Bei sehr dickem Edelstahl kann Sauerstoff verwendet werden, um die Schnittgeschwindigkeit zu erhöhen, verursacht jedoch Oxidation, was eine Nachbearbeitung erforderlich macht.
- Aluminium und Nichteisenmetalle: Stickstoff ist die erste Wahl zum Schneiden von Aluminium und Nichteisenmetallen, um Oxidation zu vermeiden und einen sauberen Schnitt zu erzielen. Für weniger kritische Anwendungen kann Druckluft eine kostengünstige Alternative sein, obwohl sie etwas Oxidation verursachen kann.
- Nichtmetallische Materialien: Beim Schneiden von Nichtmetallen wie Kunststoffen, Keramik und Holz wird häufig Stickstoff verwendet, um Verfärbungen zu vermeiden und eine hochwertige Schneide zu erzielen. Sauerstoff kann verwendet werden, um bestimmte Nichtmetalle schneller zu schneiden, kann jedoch zu Versengungen oder Verbrennungen führen.
Erforderliche Schnittqualität
Die erforderliche Schnittqualität ist ein entscheidender Faktor bei der Auswahl des geeigneten Hilfsgases. Präzisionsanwendungen erfordern typischerweise einen hochwertigen Schnitt mit minimaler Oxidation und glatten Kanten.
- Hochwertige Oberflächenbeschaffenheit: Stickstoff ist oft die beste Wahl für Anwendungen, die präzise, saubere und oxidationsfreie Schnitte erfordern. Es verhindert Oxidation und sorgt so für glatte Kanten und eine hochwertige Oberflächenbeschaffenheit.
- Allgemeine Qualität: Sauerstoff kann einen hochwertigen Schnitt mit minimaler Bartbildung liefern, aber die Kanten müssen aufgrund von Oxidation möglicherweise zusätzlich gereinigt werden. Druckluft kann für weniger kritische Anwendungen geeignet sein, bei denen keine Oberflächengüte von höchster Qualität erforderlich ist.
Schnittgeschwindigkeit und Effizienz
Die Art des verwendeten Hilfsgases beeinflusst Schnittgeschwindigkeit und -effizienz. Ziel ist es, die höchstmögliche Geschwindigkeit zu erreichen, ohne die Schnittqualität zu beeinträchtigen.
- Maximale Geschwindigkeit: Ermöglicht die schnellsten Schnittgeschwindigkeiten für Kohlenstoffstahl und dickere Materialien aufgrund der exothermen Reaktion von Sauerstoff, die dem Schneidvorgang zusätzliche Wärme verleiht.
- Ausgewogene Geschwindigkeit und Qualität: Stickstoff schafft ein Gleichgewicht zwischen Geschwindigkeit und hochwertigen Schnitten, obwohl im Vergleich zu Sauerstoff möglicherweise eine höhere Laserleistung erforderlich ist und die Schnitte langsamer sind.
- Kostengünstige Geschwindigkeit: Druckluft bietet einen Kompromiss zwischen Geschwindigkeit und Kosten und eignet sich für Anwendungen, bei denen moderate Schnittgeschwindigkeiten und angemessene Qualität akzeptabel sind.
Kostenüberlegungen
Die Kosten sind ein wichtiger Faktor bei der Gasauswahl, da sie sich auf die Betriebskosten und die Gesamtkosteneffizienz auswirken.
- Reduzierte Betriebskosten: Druckluft ist die wirtschaftlichste Wahl, da sie leicht verfügbar und billiger als reine Gase wie Sauerstoff und Stickstoff ist. Sie ist ideal zum Schneiden weniger kritischer Materialien oder wenn Budgetbeschränkungen eine Priorität darstellen.
- Höhere Qualität und höhere Kosten: Stickstoff ist zwar teurer, bietet aber eine bessere Schnittqualität. Die Mehrkosten sind durch die verbesserte Qualität und den geringeren Nachbearbeitungsbedarf gerechtfertigt.
- Kosten und Effizienz ausbalancieren: Sauerstoff bietet einen Mittelweg und bietet schnelle Schnittgeschwindigkeiten und angemessene Qualität zu moderaten Kosten. Es eignet sich für viele industrielle Anwendungen, bei denen sowohl Geschwindigkeit als auch Qualität wichtig sind.
Anforderungen an die Nachbearbeitung
Die Anforderungen der Nachbearbeitung können sich auf die Auswahl des Hilfsgases auswirken, da einige Gase sauberere Schnitte erzeugen, wodurch die Nachbearbeitungsarbeiten reduziert werden können.
- Minimale Nachbearbeitung: Stickstoff erzeugt saubere, oxidationsfreie Schnitte, wodurch die Notwendigkeit einer umfangreichen Nachbearbeitung verringert und Zeit und Kosten bei den Endbearbeitungsvorgängen gespart werden.
- Moderate Nachbearbeitung: Beim Sauerstoffschneiden sind möglicherweise zusätzliche Schritte erforderlich, um Oxide zu entfernen und die gewünschte Oberflächengüte zu erzielen. Höhere Schnittgeschwindigkeiten können jedoch einige der zusätzlichen Kosten ausgleichen.
- Erhöhter Nachbearbeitungsaufwand: Druckluft kann zu mehr Schlacke und Oxidation führen, sodass eine umfangreichere Nachbearbeitung zum Reinigen und Veredeln der Kante erforderlich ist. Dies kann die Gesamtproduktionszeit und -kosten erhöhen.
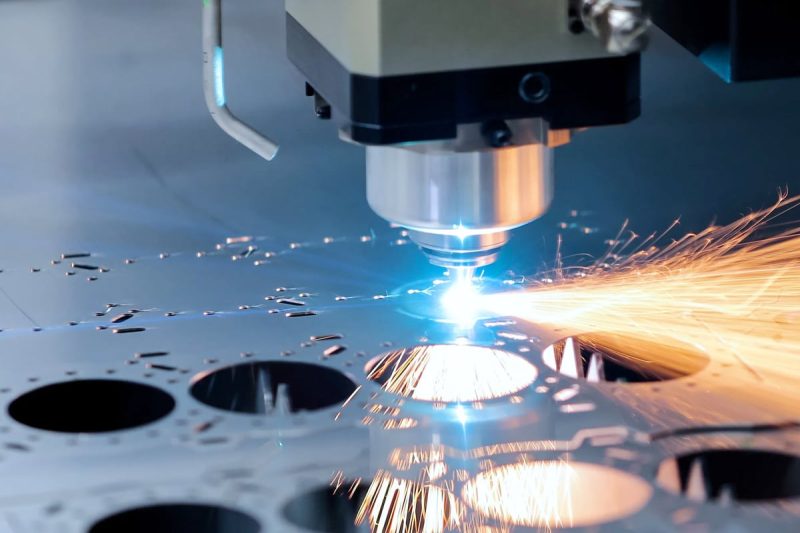
Zusammenfassung
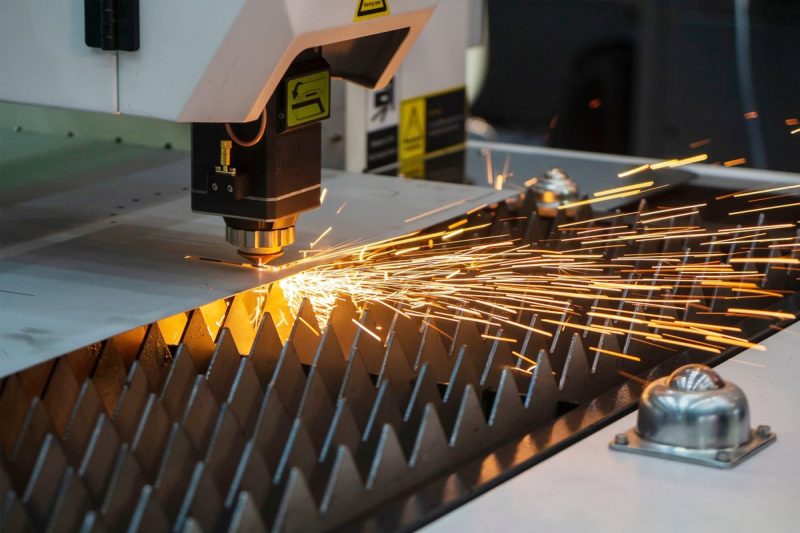
Holen Sie sich Laserschneidlösungen
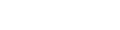
- [email protected]
- [email protected]
- +86-19963414011
- Nr. 3 Zone A, Industriegebiet Lunzhen, Stadt Yucheng, Provinz Shandong.