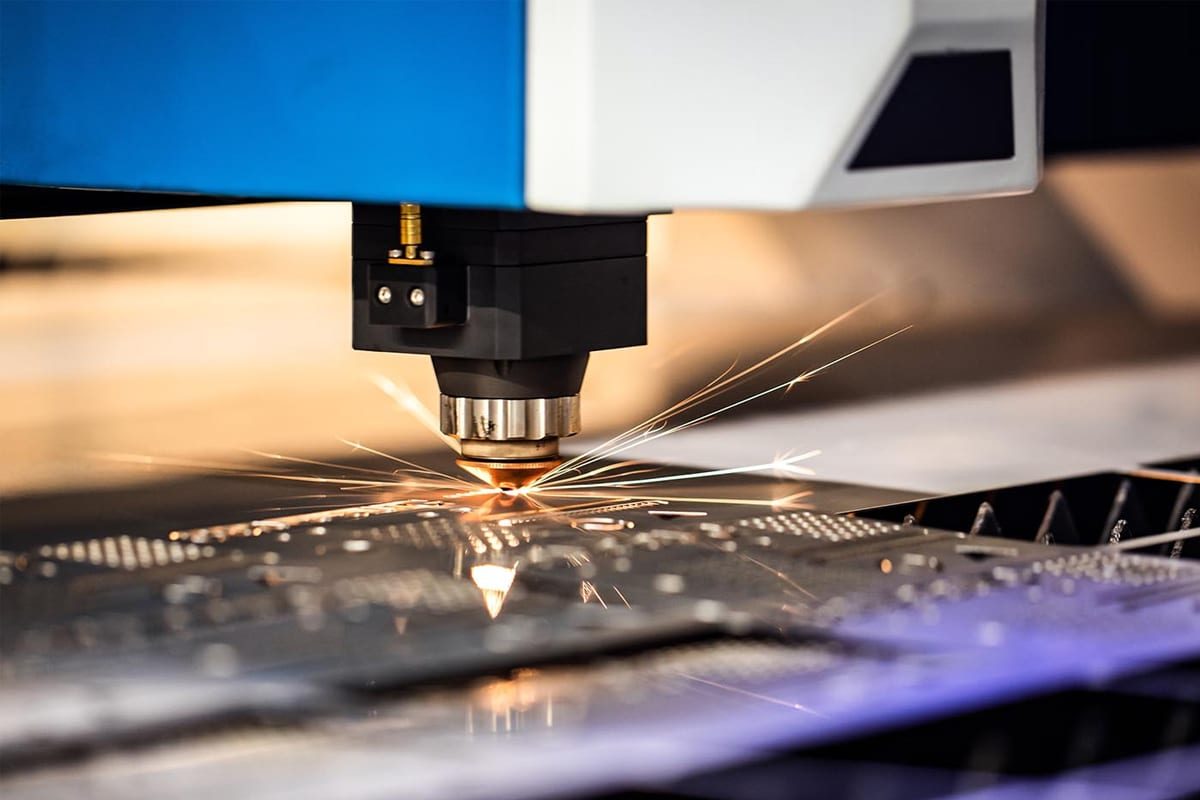
Faserlaserschneiden VS Plasmaschneiden
In der dynamischen Welt der Metallverarbeitung hilft die Wahl der richtigen Schneidtechnologie dabei, Präzision, Effizienz und Kosteneffizienz zu erreichen. Faserlaserschneiden und Plasmaschneiden sind zwei herausragende Methoden, die die Branche revolutioniert haben. Dieser Artikel bietet einen umfassenden Vergleich von Faserlaserschneiden und Plasmaschneiden und untersucht ihre Prinzipien, Vorteile, Einschränkungen und idealen Anwendungen. Indem wir uns mit den Besonderheiten jeder Methode befassen, möchten wir Ihnen das Wissen vermitteln, das Sie benötigen, um fundierte Entscheidungen zu treffen, die Ihren Fertigungsanforderungen entsprechen und Ihre Betriebskapazitäten verbessern.
Inhaltsverzeichnis
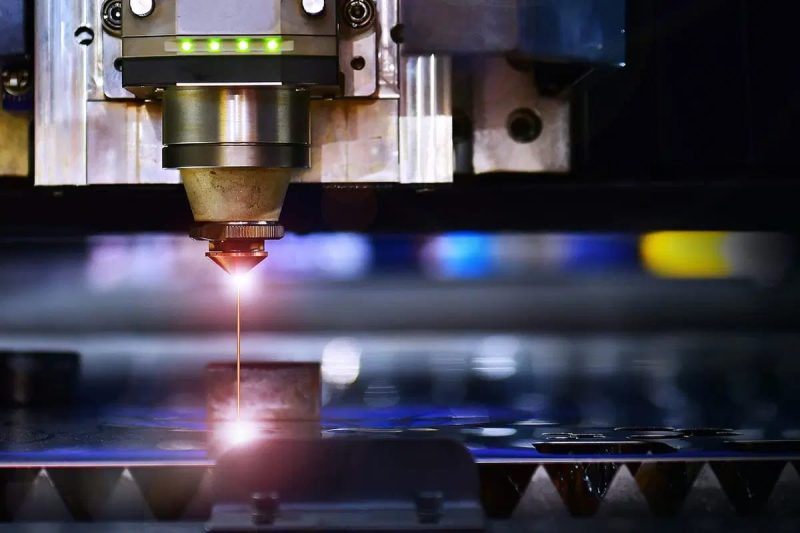
Was ist Faserlaserschneiden?
Definition und Grundprinzipien
Faserlaserschneiden ist ein modernes Fertigungsverfahren, bei dem ein Hochleistungsfaserlaserstrahl zum Schneiden und Gravieren von Materialien mit außergewöhnlicher Präzision und Geschwindigkeit verwendet wird. Die Technologie basiert auf der Verstärkung von Licht in mit Seltenerdelementen dotierten Glasfasern, wodurch ein fokussierter Laserstrahl entsteht, der Material kontrolliert schmelzen, verbrennen oder verdampfen kann. Diese Methode ist weithin für ihre Effizienz beim Schneiden von Metallen bekannt und bietet im Vergleich zu herkömmlichen Schneidtechniken eine überlegene Kantenqualität.
Funktionsweise von Faserlasern
Das Herzstück des Faserlaserschneidens ist der Faserlasergenerator selbst, der nach den folgenden Prinzipien arbeitet:
- Lasererzeugung: Ein Seedlaser sendet einen Lichtstrahl geringer Leistung aus, der dann in ein mit Seltenerdelementen wie Ytterbium dotiertes Glasfaserkabel eingespeist wird.
- Verstärkung: Während das Licht durch die dotierte Faser wandert, interagiert es mit den Seltenerdionen, wodurch diese zusätzliche Photonen der gleichen Wellenlänge und Phase aussenden – ein Vorgang, der als stimulierte Emission bezeichnet wird. Dadurch wird das Licht zu einem starken Laserstrahl verstärkt.
- Strahlführung: Das verstärkte Laserlicht wird über flexible Glasfaserkabel zum Schneidkopf übertragen, ohne dass komplexe Spiegel oder Linsen erforderlich sind.
- Fokussierung des Strahls: Der Schneidkopf enthält eine Linse, die den Laserstrahl auf einen sehr kleinen Punkt auf der Materialoberfläche fokussiert und so eine extrem hohe Leistungsdichte erreicht.
- Materialwechselwirkung: Die konzentrierte Energie schmilzt oder verdampft das Material im Brennpunkt. Hilfsgase wie Stickstoff oder Sauerstoff werden häufig verwendet, um geschmolzenes Material wegzublasen, was den Schneidprozess verbessert und Oxidation verhindert.
- Kontrollierte Bewegung: Ein computergestütztes numerisches Steuerungssystem (CNC) steuert die Bewegung des Schneidkopfes oder des Werkstücks und folgt präzisen Mustern, um die gewünschten Schnittformen zu erzielen.
Vorteile
- Hohe Präzision und Qualität: Faserlaser erzeugen einen kleinen Brenndurchmesser und eine hohe Energiedichte, was zu feinen, sauberen Schnitten mit minimaler thermischer Verzerrung führt.
- Effizienz: Sie bieten schnellere Schnittgeschwindigkeiten, insbesondere bei dünnen bis mitteldicken Materialien, und steigern so die Produktivität.
- Vielseitigkeit: Kann eine Vielzahl von Metallen schneiden, darunter Stahl, Edelstahl, Aluminium, Messing und Kupfer.
- Geringer Wartungsaufwand: Faserlasergeneratoren verfügen über ein Festkörperdesign ohne bewegliche Teile oder Spiegel in der Lichtquelle, was den Wartungsaufwand und die Ausfallzeiten reduziert.
- Energieeffizienz: Sie verbrauchen weniger Strom als herkömmliche CO2-Laserschneidmaschinen und Plasmaschneidsysteme, was zu niedrigeren Betriebskosten führt.
- Lange Betriebslebensdauer: Die Dioden in Faserlasern haben eine lange Lebensdauer, die oft über 100.000 Betriebsstunden beträgt.
- Kompaktes Design: Das Glasfaser-Zuführungssystem ermöglicht eine kompaktere Stellfläche der Maschine und spart so wertvolle Stellfläche.
Nachteile
- Hohe Anfangsinvestition: Die fortschrittliche Technologie und die Komponenten führen zu höheren Vorlaufkosten im Vergleich zu anderen Schneidmethoden wie dem Plasmaschneiden.
- Materialbeschränkungen: Faserlaser sind bei dickeren Materialien (normalerweise über 25 mm bei Stahl) weniger effektiv und nicht für nichtmetallische Materialien wie Holz oder Kunststoffe geeignet.
- Herausforderungen bei reflektierenden Materialien: Das Schneiden von stark reflektierenden Metallen wie Kupfer und Messing kann aufgrund der möglichen Rückreflexion, die die Laserquelle beschädigen kann, eine Herausforderung darstellen, obwohl moderne Maschinen über Funktionen verfügen, um dieses Risiko zu mindern.
- Erforderliches technisches Fachwissen: Die Bediener benötigen eine spezielle Schulung, um die Geräte zu handhaben und die Schnittparameter für verschiedene Materialien zu optimieren.
Anwendungen
Aufgrund seiner Präzision und Effizienz wird das Faserlaserschneiden in zahlreichen Branchen eingesetzt:
- Luft- und Raumfahrt: Zum Schneiden komplexer Komponenten, die hohe Präzision und minimale Wärmebelastung erfordern.
- Automobilindustrie: Herstellung von Teilen wie Karosserieteilen, Motorkomponenten und komplizierten Designs.
- Elektronik: Schneiden kleiner, präziser Teile, die in elektronischen Geräten und Schaltkreisen verwendet werden.
- Medizinische Geräte: Herstellung von chirurgischen Instrumenten und medizinischer Ausrüstung, die eine hohe Genauigkeit erfordern.
- Metallverarbeitung: Allgemeine Fertigungsarbeiten mit kundenspezifischen Metallteilen, Gehäusen und Strukturkomponenten.
- Schmuckherstellung: Anfertigen komplizierter Designs aus Edelmetallen mit hoher Präzision.
- Beschilderung und dekorative Kunst: Erstellen detaillierter Metallschilder, Kunstwerke und dekorativer Elemente.
Durch die Nutzung der Stärken des Faserlaserschneidens können Hersteller eine überragende Qualität erzielen, die Produktionszeiten verkürzen und ihre Kapazitäten erweitern, um den hohen Anforderungen moderner Industrien gerecht zu werden.
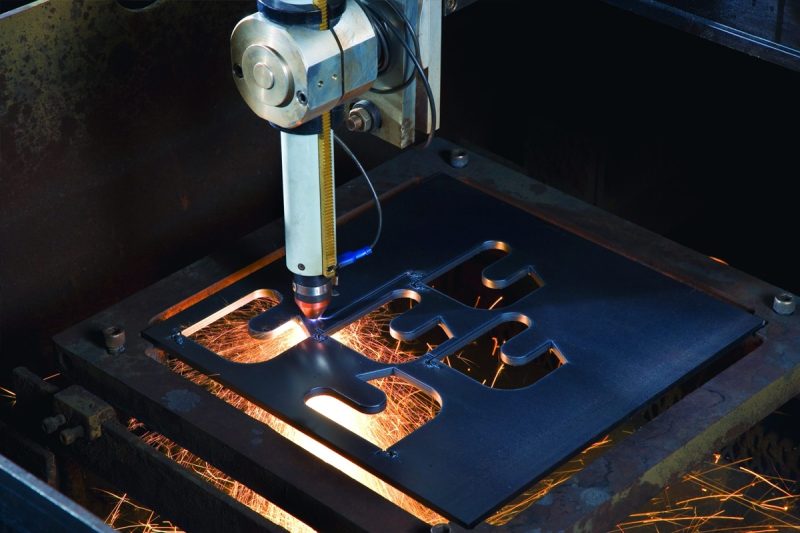
Was ist Plasmaschneiden?
Definition und Grundprinzipien
Plasmaschneiden ist ein thermisches Schneidverfahren, bei dem ein Hochgeschwindigkeitsstrahl aus ionisiertem Gas (Plasma) verwendet wird, um elektrisch leitfähige Materialien zu schmelzen und zu trennen. Bei diesem Verfahren wird ein elektrischer Lichtbogen erzeugt, der durch ein Gas strömt und dieses in Plasma umwandelt, das Temperaturen von bis zu 30.000 °C (54.000 °F) erreichen kann. Diese intensive Hitze schmilzt das Metall, während die kinetische Energie des Hochgeschwindigkeitsgases das geschmolzene Material entfernt und einen sauberen Schnitt erzeugt. Plasmaschneiden wird häufig verwendet, da es sich zum Schneiden dicker Metalle eignet und eine Vielzahl leitfähiger Materialien bearbeiten lässt.
So funktioniert Plasmaschneiden
Der Plasmaschneidprozess funktioniert nach folgenden Prinzipien:
- Zündung des Lichtbogens: Eine elektrische Stromquelle erzeugt einen Gleichstromlichtbogen (DC) zwischen einer Elektrode (negative Ladung) im Plasmabrenner und dem Werkstück (positive Ladung).
- Gasionisation: Komprimiertes Gas (wie Luft, Stickstoff, Argon oder Sauerstoff) wird mit hoher Geschwindigkeit durch eine enge Düse in den Lichtbogen gepresst. Die intensive Energie des Lichtbogens ionisiert das Gas und wandelt es in Plasma um.
- Bildung eines Plasmastrahls: Das Plasma tritt als fokussierter, hochgeschwindigkeitsstarker Strahl ionisierten Gases aus der Düse aus. Die schmale Düse verengt den Lichtbogen und erhöht so seine Temperatur und Geschwindigkeit.
- Materialschmelzen: Der Plasmastrahl erreicht extrem hohe Temperaturen und schmilzt das Material an der Kontaktstelle.
- Materialabtrag: Das Hochgeschwindigkeitsplasma und die Sekundärgase blasen das geschmolzene Metall vom Schnitt weg und hinterlassen einen schmalen Schnitt.
- Kontrollierte Bewegung: Der Plasmabrenner wird entweder manuell oder über ein CNC-System (Computerized Numerical Control) entlang des gewünschten Schneidpfads geführt, um präzise Schnitte zu erzielen.
Vorteile
- Fähigkeit zum Schneiden dicker Materialien: Plasmaschneiden eignet sich hervorragend zum Schneiden dicker Metallplatten, oft bis zu 80 mm (3 Zoll) oder mehr, abhängig von der Leistung des Plasmasystems.
- Vielseitigkeit: Wirksam auf allen elektrisch leitfähigen Metallen, einschließlich Kohlenstoffstahl, Edelstahl, Aluminium, Kupfer, Messing und Gusseisen.
- Hohe Schnittgeschwindigkeiten: Schneller als das autogene Brennschneiden bei Materialien mit einer Dicke von weniger als 50 mm, was die Produktivität bei Metallbearbeitungsaufgaben verbessert.
- Geringere Anfangsinvestition: Generell geringere Vorlaufkosten im Vergleich zu Faserlaserschneidsystemen, sodass es für kleine und mittlere Unternehmen erschwinglich ist.
- Benutzerfreundlichkeit: Einfachere Einrichtung und Bedienung, im Vergleich zu Laserschneidsystemen sind weniger technische Fachkenntnisse erforderlich.
- Tragbarkeit: Plasmaschneidgeräte können relativ kompakt und tragbar sein und eignen sich für Reparaturen und Bauarbeiten vor Ort.
Nachteile
- Geringere Präzision: Beim Plasmaschneiden entsteht ein breiterer Schnittspalt (Schnittbreite) und die Schnitte sind im Vergleich zum Faserlaserschneiden weniger präzise, sodass möglicherweise eine zusätzliche Nachbearbeitung erforderlich ist.
- Wärmeeinflusszone (WEZ): Erzeugt eine größere WEZ, die die Eigenschaften des Metalls in der Nähe der Schnittkante verändern und zu Verformungen oder Verzerrungen führen kann.
- Rauere Kantenqualität: Kanten können mehr Schlacke (Rückstände) und Rauheit aufweisen, was für Anwendungen, die eine hochwertige Oberflächenbehandlung erfordern, eine Nachbearbeitung erforderlich macht.
- Begrenzte Fähigkeit zur Feindetailbearbeitung: Aufgrund der Größe des Plasmalichtbogens und der Schnittbreite nicht ideal zum Schneiden komplizierter Muster oder kleiner Löcher.
- Höherer Energieverbrauch: Verbraucht im Allgemeinen mehr Strom als Faserlasersysteme, was im Laufe der Zeit zu höheren Betriebskosten führt.
- Sicherheitsrisiken: Erzeugt intensives Licht, Lärm und Dämpfe und erfordert entsprechende Sicherheitsmaßnahmen wie Augenschutz, Gehörschutz und ausreichende Belüftung.
Anwendungen
Plasmaschneiden wird häufig in Branchen und Anwendungen eingesetzt, in denen dicke, leitfähige Metalle geschnitten werden müssen:
- Bau und Infrastruktur: Schneiden von Stahlbauteilen für Gebäude, Brücken und Infrastrukturprojekte.
- Schiffbau: Herstellung großer Stahlprofile für Schiffe und Offshore-Plattformen.
- Autoreparatur und -herstellung: Schneiden und Reparieren von Fahrgestellkomponenten, Rahmen und Karosserieteilen.
- Metallverarbeitungsbetriebe: Allgemeine Fertigung von Hochleistungsmetallteilen, kundenspezifische Baugruppen und Reparaturarbeiten.
- Herstellung von landwirtschaftlichen und schweren Geräten: Produktion von Komponenten für Traktoren, Bagger und Industriemaschinen.
- Altmetallrecycling: Große Metallgegenstände werden zum Recycling in kleinere Stücke geschnitten.
- Wartungs- und Reparaturarbeiten: Vor-Ort-Zuschneiden und -Ändern von Metallstrukturen und -geräten in verschiedenen Branchen.
Wenn Hersteller die Grundlagen des Plasmaschneidens verstehen, können sie dessen Eignung für ihre spezifischen Anforderungen beurteilen. Plasmaschneiden bietet zwar Vorteile beim Schneiden dicker Materialien und geringere Anschaffungskosten, erreicht jedoch möglicherweise nicht die Präzision und Kantenqualität von Faserlaserschneidsystemen.
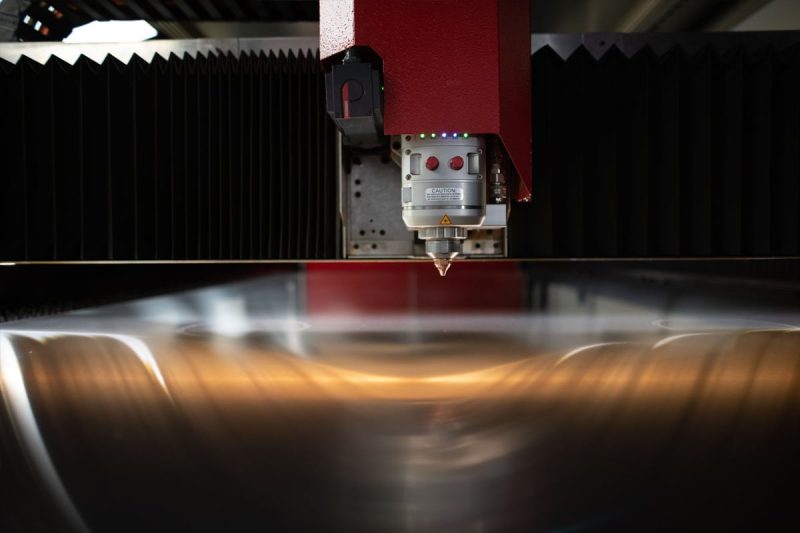
Vergleich zwischen Faserlaserschneiden und Plasmaschneiden
Bei der Entscheidung zwischen Faserlaserschneiden und Plasmaschneiden ist es wichtig zu verstehen, wie sich jede Methode in Bezug auf verschiedene Kriterien schlägt. Nachfolgend finden Sie einen detaillierten Vergleich, der die Stärken und Schwächen beider Technologien hervorhebt.
Schnittqualität
Faserlaserschneiden
- Kantenqualität: Erzeugt eine hervorragende Kantenqualität mit glatten, sauberen Schnitten und minimaler Bartbildung (Schlackerückstände).
- Wärmeeinflusszone (WEZ): Kleinere WEZ aufgrund des konzentrierten Laserstrahls, wodurch das Risiko einer thermischen Verformung verringert wird.
- Präzisionsschnitte: Ideal für komplizierte Designs und enge Toleranzen und daher für Anwendungen geeignet, die eine hohe Präzision erfordern.
Plasmaschneiden
- Kantenqualität: Erzeugt im Allgemeinen rauere Kanten mit mehr Bart, was möglicherweise zweite Endbearbeitungsprozesse erforderlich macht.
- Wärmeeinflusszone (WEZ): Größere WEZ aufgrund des breiteren Plasmalichtbogens, wodurch die Gefahr von Verformungen und Verzerrungen steigt.
- Grobe Schnitte: Besser geeignet für weniger detaillierte Arbeiten, bei denen es nicht unbedingt auf ultrafeine Präzision ankommt.
Schneidgeschwindigkeit
Faserlaserschneiden
- Dünne bis mitteldicke Materialien: Bietet schnellere Schnittgeschwindigkeiten bei dünnen bis mitteldicken Metallen (normalerweise bis zu 25 mm bei Stahl).
- Effizienz: Die Hochgeschwindigkeitsverarbeitung erhöht die Produktivität und verkürzt die Vorlaufzeiten.
Plasmaschneiden
- Dicke Materialien: Im Allgemeinen schneller beim Schneiden dickerer Materialien (über 25 mm), bei denen die Effizienz des Lasers abnimmt.
- Kompromiss zwischen Geschwindigkeit und Qualität: Obwohl hohe Geschwindigkeiten möglich sind, kann eine erhöhte Geschwindigkeit die Schnittqualität weiter verringern.
Materialkompatibilität
Faserlaserschneiden
- Metallische Materialien: Hervorragend geeignet zum Schneiden einer Vielzahl von Metallen, darunter Kohlenstoffstahl, Edelstahl, Aluminium, Messing und Kupfer.
- Nichtmetalle: Aufgrund der Wellenlängenabsorptionseigenschaften des Lasers nicht zum Schneiden nichtmetallischer Materialien geeignet.
- Reflektierende Metalle: Moderne Faserlaser können reflektierende Metalle wie Kupfer und Messing mit der entsprechenden Technologie verarbeiten, um Schäden durch Rückreflexion zu verhindern.
Plasmaschneiden
- Leitfähige Metalle: Kann alle elektrisch leitfähigen Metalle schneiden, einschließlich Stahl, Edelstahl, Aluminium, Kupfer, Messing und Gusseisen.
- Nichtmetalle: Unwirksam bei nichtleitenden Materialien wie Kunststoff, Glas oder Holz.
Dickenfähigkeiten
Faserlaserschneiden
- Optimaler Dickenbereich: Hocheffizient bei dünnen bis mitteldicken Materialien, normalerweise bis zu 25 mm bei Stahl.
- Einschränkungen bei dicken Materialien: Das Schneiden dickerer Materialien erfordert möglicherweise erheblich mehr Kraft und kann zu einer verringerten Schnittqualität und -geschwindigkeit führen.
Plasmaschneiden
- Schneiden von dickem Material: Kann dickere Materialien effektiv schneiden, oft bis zu 80 mm oder mehr, abhängig von der Leistung des Plasmasystems.
- Dünne Materialien: Kann dünne Materialien schneiden, kann jedoch zu übermäßiger Wärmezufuhr führen, was zu Verformungen oder verringerter Schnittqualität führen kann.
Präzision und Genauigkeit
Faserlaserschneiden
- Hohe Präzision: Erreicht extrem enge Toleranzen und komplizierte Schnitte mit Genauigkeitsstufen oft im Bereich von ±0,1 mm.
- Geringe Schnittbreite: Durch die schmale Fokussierung des Laserstrahls entsteht ein minimaler Schnitt, der Material schont und detaillierte Designs ermöglicht.
Plasmaschneiden
- Mittlere Präzision: Geeignet für Anwendungen, bei denen die Präzision weniger wichtig ist, mit Toleranzen im typischen Bereich von ±0,5 mm bis ±1 mm.
- Größere Schnittbreite: Der Plasmalichtbogen erzeugt einen breiteren Schnitt, was die Fähigkeit zum Schneiden feiner Strukturen oder eng beieinander liegender Komponenten einschränken kann.
Betriebskosten
Faserlaserschneiden
- Anfangsinvestition: Höhere Vorabkosten aufgrund fortschrittlicher Technologie und Ausrüstung.
- Betriebskosten: Niedrigere laufende Kosten sind auf eine höhere Energieeffizienz und einen geringeren Verbrauch von Verbrauchsmaterialien zurückzuführen.
- Energieverbrauch: Energieeffizienter, was im Laufe der Zeit zu niedrigeren Stromkosten führt.
Plasmaschneiden
- Anfangsinvestition: Der niedrigere Kaufpreis macht es für Unternehmen mit Budgetbeschränkungen erschwinglich.
- Betriebskosten: Höhere Betriebskosten aufgrund des höheren Energieverbrauchs und des häufigen Austauschs von Verbrauchsmaterialien wie Elektroden und Düsen.
- Verbrauchsmaterialien: Die laufenden Kosten für Verbrauchsmaterialien können sich summieren und die Gesamtbetriebskosten erhöhen.
Wartung
Faserlaserschneiden
- Geringer Wartungsaufwand: Das Halbleiterdesign mit weniger beweglichen Teilen reduziert den Wartungsbedarf.
- Langlebigkeit der Komponenten: Wichtige Komponenten wie Dioden haben eine lange Lebensdauer, die oft über 100.000 Stunden beträgt.
- Ausfallzeiten: Seltenere Wartungsarbeiten führen zu einer höheren Maschinenverfügbarkeit und Produktivität.
Plasmaschneiden
- Höherer Wartungsbedarf: Verbrauchsteile wie Elektroden und Düsen müssen aufgrund von Verschleiß regelmäßig ausgetauscht werden.
- Maschinenverschleiß: Die intensive Hitze und die Lichtbögen können zu häufigeren Wartungsarbeiten und Teileaustausch führen.
- Ausfallzeiten: Erhöhter Wartungsaufwand kann zu längeren Maschinenausfallzeiten führen und so die Produktivität beeinträchtigen.
Sicherheitsaspekte
Faserlaserschneiden
- Laserstrahlung: Erfordert strenge Sicherheitsmaßnahmen zum Schutz des Bedieners vor Laserstrahlung, einschließlich Schutzbrillen und -gehäusen.
- Rauchabsaugung: Beim Schneiden von Metallen können Dämpfe entstehen und es sind entsprechende Belüftungs- oder Absaugsysteme erforderlich.
- Geräuschpegel: Im Allgemeinen leiserer Betrieb im Vergleich zum Plasmaschneiden.
Plasmaschneiden
- Stromschlagrisiko: Bei Nichteinhaltung der Sicherheitsprotokolle besteht durch hohe Spannung und Stromstärke die Gefahr eines Stromschlags.
- UV- und Infrarotstrahlung: Erzeugt intensive UV- und IR-Strahlung, die Schutzkleidung und Augenschutz erforderlich macht.
- Rauch- und Lärmemissionen: Produziert erhebliche Rauchgase und hohe Lärmpegel, die Gehörschutz und wirksame Belüftungssysteme erfordern.
Umweltbelastung
Faserlaserschneiden
- Energieeffizienz: Höhere Energieeffizienz, wodurch der gesamte CO2-Fußabdruck des Betriebs reduziert wird.
- Reduzierte Emissionen: Erzeugt im Vergleich zum Plasmaschneiden weniger Dämpfe und Emissionen.
- Hilfsgase: Verwendet Inertgase wie Stickstoff, die nur minimale Auswirkungen auf die Umwelt haben.
Plasmaschneiden
- Höherer Energieverbrauch: Eine weniger effiziente Energienutzung trägt zu einem größeren ökologischen Fußabdruck bei.
- Rauchentwicklung: Produziert mehr Rauch und Partikel, die bei unzureichender Kontrolle die Luftqualität beeinträchtigen können.
- Verbrauchsmaterialabfall: Der häufige Austausch von Verbrauchsmaterialien trägt zur Abfallerzeugung bei.
Bei der Untersuchung dieser kritischen Faktoren wird deutlich, dass sowohl das Faserlaserschneiden als auch das Plasmaschneiden deutliche Vorteile und Nachteile haben. Das Faserlaserschneiden ist die bevorzugte Wahl für Anwendungen, die hohe Präzision, hervorragende Schnittqualität und Effizienz bei dünnen bis mitteldicken Materialien erfordern. Im Gegensatz dazu ist das Plasmaschneiden für das Schneiden dickerer Materialien vorteilhaft, bei denen ultrafeine Präzision weniger wichtig ist und die anfänglichen Investitionskosten eine Rolle spielen.
Die Wahl der richtigen Technologie hängt von Faktoren wie der Art der zu verarbeitenden Materialien, dem erforderlichen Dickenbereich, der gewünschten Schnittqualität, den Betriebskosten sowie Umwelt- und Sicherheitsprioritäten ab. Durch die Nutzung der Stärken jeder Methode können Hersteller ihre Produktionsprozesse optimieren, Kosten senken und die Gesamtproduktqualität verbessern.
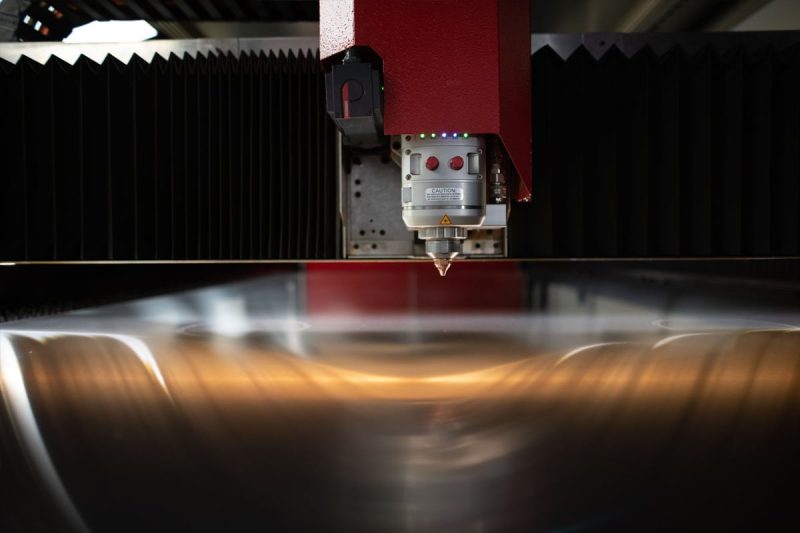
Auswahl zwischen Faserlaser- und Plasmaschneiden
Die Auswahl der geeigneten Schneidtechnologie für Ihre Fertigungsanforderungen ist eine wichtige Entscheidung, die Ihre Produktionseffizienz, Produktqualität und Gesamtbetriebskosten erheblich beeinflussen kann. Sowohl das Faserlaserschneiden als auch das Plasmaschneiden bieten einzigartige Vorteile und eignen sich für unterschiedliche Anwendungen.
Zu berücksichtigende Faktoren
Materialart und -stärke
- Materialkompatibilität: Faserlaserschneiden ist ideal für Metalle wie Kohlenstoffstahl, Edelstahl, Aluminium, Messing und Kupfer. Plasmaschneiden ist bei allen elektrisch leitfähigen Metallen wirksam, kann aber bei Nichteisenmetallen hinsichtlich der Schnittqualität Probleme bereiten.
- Dickenfähigkeiten: Faserlaser eignen sich hervorragend zum Schneiden dünner bis mittlerer Materialien (bis zu 25 mm) und bieten hohe Präzision und Geschwindigkeit. Plasmaschneider verarbeiten dickere Materialien (bis zu 80 mm oder mehr) effektiv, jedoch mit geringerer Präzision.
Schnittpräzision und -qualität
- Präzisionsanforderungen: Wenn Ihre Projekte eine hohe Genauigkeit bei minimaler Kantenrauheit erfordern, ist das Faserlaserschneiden die beste Wahl.
- Kantenqualität: Faserlaser erzeugen glattere Kanten mit einer kleineren Wärmeeinflusszone (WEZ), wodurch die Notwendigkeit einer Nachbearbeitung verringert wird. Beim Plasmaschneiden können rauere Kanten und eine größere WEZ entstehen.
Produktionsvolumen und -geschwindigkeit
- Schnittgeschwindigkeit: Bei dünnen Materialien bieten Faserlaser höhere Schnittgeschwindigkeiten und steigern so die Produktivität bei großen Produktionsmengen. Plasmaschneider können bei dickeren Materialien schneller sein, sind bei dünneren Materialien jedoch im Allgemeinen langsamer.
- Wiederholbarkeit: Faserlaser liefern konsistente Ergebnisse, was für die Massenproduktion von entscheidender Bedeutung ist, da es hier auf Einheitlichkeit ankommt.
Betriebskosten
- Erstinvestition: Faserlaser-Schneidmaschinen haben aufgrund der fortschrittlichen Technologie höhere Anschaffungskosten. Plasmaschneidmaschinen sind in der Anschaffung weniger teuer.
- Betriebskosten: Berücksichtigen Sie Energieverbrauch, Wartung und Verbrauchsmaterialien. Faserlaser sind energieeffizienter und haben langfristig geringere Wartungskosten.
Komplexität des Designs
- Komplizierte Schnitte: Faserlaser können komplexe und detaillierte Designs mit hoher Präzision bearbeiten. Plasmaschneider sind aufgrund eines breiteren Schnitts für komplizierte Arbeiten weniger geeignet.
Wartung und Ausfallzeiten
- Maschinenzuverlässigkeit: Faserlaser haben weniger bewegliche Teile und erfordern weniger häufige Wartung, was zu weniger Ausfallzeiten führt.
- Verbrauchsmaterial: Bei Plasmaschneidmaschinen ist ein regelmäßiger Austausch der Elektroden und Düsen erforderlich, was den Wartungsbedarf erhöht.
Sicherheit und Umweltauswirkungen
- Sicherheitsmaßnahmen: Bei Faserlasern sind Vorsichtsmaßnahmen gegen Laserstrahlung erforderlich, während beim Plasmaschneiden Risiken durch hohe Temperaturen, UV-Strahlung und Dämpfe bestehen.
- Umweltaspekte: Faserlaser sind energieeffizienter und erzeugen weniger Emissionen, was nachhaltigen Praktiken entspricht.
Anwendungsbeispiele
Automobilbau
- Faserlaserschneiden: Wird zum präzisen Schneiden von Karosserieteilen, komplexen Komponenten und Sonderteilen verwendet, bei denen es auf Genauigkeit ankommt.
- Plasmaschneiden: Geeignet zum Schneiden dickerer Strukturbauteile wie Rahmen und Fahrgestellteile.
Metallverarbeitung
- Faserlaserschneiden: Ideal zum Erstellen detaillierter Metallkunstwerke, Beschilderungen und Komponenten, die eine hohe Präzision erfordern.
- Plasmaschneiden: Effektiv für die allgemeine Herstellung von Hochleistungsteilen und -geräten, bei denen feine Details weniger wichtig sind.
Bauindustrie
- Faserlaserschneiden: Wird zum Schneiden von Metallbolzen, -klammern und -beschlägen verwendet, bei denen Präzision erforderlich ist.
- Plasmaschneiden: Geeignet zum Schneiden großer Stahlplatten und -träger, die in Baustrukturen verwendet werden.
Schiffbau und Schwermaschinenbau
- Faserlaserschneiden: Geeignet zum Schneiden dünnerer Materialien, die in bestimmten Schiffskomponenten und Maschinenteilen verwendet werden.
- Plasmaschneiden: Bevorzugt zum Schneiden dicker Stahlplatten und schwerer Komponenten in Schiffen und Industriemaschinen.
Luft-und Raumfahrtindustrie
- Faserlaserschneiden: Wird zum Präzisionsschneiden von Leichtmetallen und Legierungen verwendet, die in Flugzeugkomponenten verwendet werden.
- Plasmaschneiden: Aufgrund der geringeren Präzision nur begrenzt einsetzbar, kann aber zum Schneiden dickerer Stützstrukturen verwendet werden.
Kosten-Nutzen-Analyse
Erstinvestition
Faserlaserschneiden:
- Kosten: Höherer Anschaffungspreis aufgrund anspruchsvoller Technologie und Komponenten.
- Vorteile: Die Investition führt zu höherer Präzision, besserer Schnittqualität und langfristigen Betriebseinsparungen.
Plasmaschneiden:
- Kosten: Niedrigere Vorabkosten, wodurch es für Unternehmen mit Budgetbeschränkungen zugänglicher ist.
- Vorteile: Sofortige Möglichkeit, dicke Materialien ohne erheblichen Kapitalaufwand zu schneiden.
Betriebskosten
Faserlaserschneiden:
- Energieverbrauch: Energieeffizienter, was zu niedrigeren Stromrechnungen führt.
- Wartung: Geringere Wartungskosten durch weniger Verbrauchsmaterialien und selteneren Teileaustausch.
- Verbrauchsmaterial: Minimale Verbrauchsmaterialkosten, hauptsächlich beschränkt auf Hilfsgase.
Plasmaschneiden:
- Energieverbrauch: Ein höherer Energieverbrauch erhöht die Betriebskosten.
- Wartung: Höhere Wartungskosten durch häufigen Austausch von Verbrauchsmaterialien wie Elektroden und Düsen.
- Verbrauchsmaterialien: Laufende Kosten für Verbrauchsmaterialien können sich im Laufe der Zeit summieren.
Produktivität und Qualität
Faserlaserschneiden:
- Produktivität: Schnellere Schnittgeschwindigkeiten bei dünnen bis mittleren Materialien steigern den Durchsatz.
- Qualität: Überlegene Kantenqualität reduziert oder eliminiert die Notwendigkeit einer Nachbearbeitung und spart so Zeit und Arbeitskosten.
Plasmaschneiden:
- Produktivität: Effizient bei dickeren Materialien, kann jedoch aufgrund der geringeren Schnittqualität zusätzlichen Zeitaufwand für die Nachbearbeitung erfordern.
- Qualität: Um die gewünschte Kantenglätte zu erreichen, ist möglicherweise Schleifen oder Schmirgeln erforderlich, was die Arbeitskosten erhöht.
Kapitalrendite (ROI)
Faserlaserschneiden:
- Langfristige Einsparungen: Energieeffizienz und geringer Wartungsaufwand tragen langfristig zu Kosteneinsparungen bei.
- Marktvorteil: Hohe Präzision und Qualität können zu neuen Geschäftsmöglichkeiten und höherer Kundenzufriedenheit führen.
Plasmaschneiden:
- Kurzfristige Erschwinglichkeit: Niedrigere Anfangskosten ermöglichen eine schnellere Bereitstellung.
- Einschränkungen: Möglicherweise höhere langfristige Kosten aufgrund von Wartung und geringerer Effizienz.
Die Wahl zwischen Faserlaserschneiden und Plasmaschneiden hängt von Ihren spezifischen Betriebsanforderungen, Ihrem Budget und Ihren langfristigen Geschäftszielen ab. Wenn Ihre Arbeit hauptsächlich das Schneiden dünner bis mitteldicker Metalle umfasst und dabei hohe Präzision und hervorragende Kantenqualität erforderlich sind, ist die Investition in eine Faserlaserschneidmaschine vorteilhaft. Die höheren Anschaffungskosten werden durch niedrigere Betriebskosten und die Fähigkeit, qualitativ hochwertige Produkte herzustellen, die strengen Industriestandards entsprechen, ausgeglichen.
Wenn Sie hingegen dickere Materialien schneiden, bei denen es weniger auf Präzision ankommt, und Sie eine kostengünstige Lösung mit geringerer Anfangsinvestition benötigen, ist Plasmaschneiden möglicherweise die richtige Wahl. Damit können Sie schwere Schneidaufgaben effizient bewältigen.
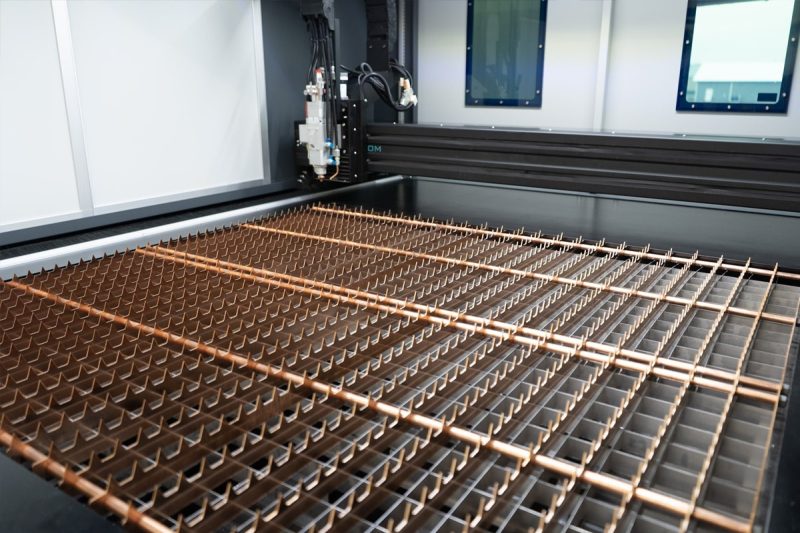
Zusammenfassung
Die Wahl der richtigen Schneidtechnik kann dabei helfen, die besten Ergebnisse bei der Metallverarbeitung zu erzielen. Das Faserlaserschneiden zeichnet sich durch hohe Präzision, hervorragende Kantenqualität und Effizienz beim Schneiden dünner bis mitteldicker Metalle aus. Es ist ideal für Branchen, die komplizierte Designs und enge Toleranzen erfordern. Das Plasmaschneiden hingegen eignet sich hervorragend zum Schneiden dickerer Materialien und erfordert eine geringere Anfangsinvestition, kann jedoch rauere Kanten erzeugen, die eine zusätzliche Nachbearbeitung erfordern. Faktoren wie Materialart und -dicke, erforderliche Präzision, Betriebskosten und spezifische Anwendungsanforderungen spielen eine wichtige Rolle bei der Bestimmung der am besten geeigneten Methode. Durch eine gründliche Bewertung dieser Faktoren können Hersteller die Schneidtechnologie auswählen, die am besten zu ihren Produktionszielen und Budgetbeschränkungen passt.
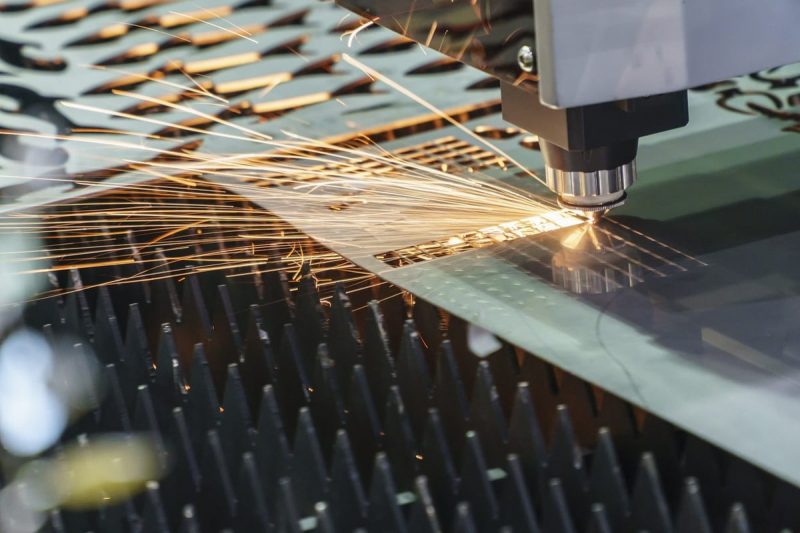
Holen Sie sich Laserschneidlösungen
Wenn Sie festgestellt haben, dass Faserlaserschneiden die optimale Wahl für Ihre Fertigungsanforderungen ist, ist AccTek Laser bereit, Ihnen hochmoderne Lösungen anzubieten. Als professioneller Hersteller von Laserschneidmaschinen sind wir auf die Bereitstellung hochwertiger Faserlaserschneidsysteme spezialisiert, die Präzision, Effizienz und Zuverlässigkeit vereinen. Unsere Maschinen sind für die Verarbeitung einer breiten Palette von Materialien und Stärken ausgelegt und eignen sich daher für verschiedene Branchen wie Luft- und Raumfahrt, Automobilindustrie, Elektronik und Metallverarbeitung.
Bei AccTek-Laserbieten wir personalisierte Lösungen, die auf Ihre spezifischen Anwendungen zugeschnitten sind. Unser Expertenteam arbeitet eng mit Ihnen zusammen, um Ihre Anforderungen zu verstehen und Ihnen die am besten geeignete Ausrüstung aus unserer umfangreichen Produktpalette zu empfehlen. Wir möchten Ihnen dabei helfen, Ihre Produktionskapazitäten zu verbessern, Betriebskosten zu senken und eine überragende Schnittqualität zu erzielen.
Zusätzlich zu Laserschneidmaschinen, wir bieten auch Laserschweißmaschinen, Laserreinigungsmaschinen, Und Laserbeschriftungsmaschinen, bietet eine umfassende Palette an Lasertechnologien, um alle Ihre Fertigungsherausforderungen zu meistern. Wenn Sie sich für AccTek Laser entscheiden, investieren Sie in fortschrittliche Technologie, die Ihnen auf dem heutigen schnelllebigen Markt einen Wettbewerbsvorteil verschafft.
Kontaktieren Sie uns noch heute, um zu erfahren, wie unsere Faserlaserschneidlösungen Ihren Betrieb verändern und Ihr Geschäft voranbringen können. Lassen Sie uns gemeinsam mit Ihnen Spitzenleistungen in der Präzisionsmetallbearbeitung erzielen.
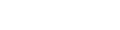
Kontaktinformationen
- [email protected]
- [email protected]
- +86-19963414011
- Nr. 3 Zone A, Industriegebiet Lunzhen, Stadt Yucheng, Provinz Shandong.
Holen Sie sich Laserlösungen