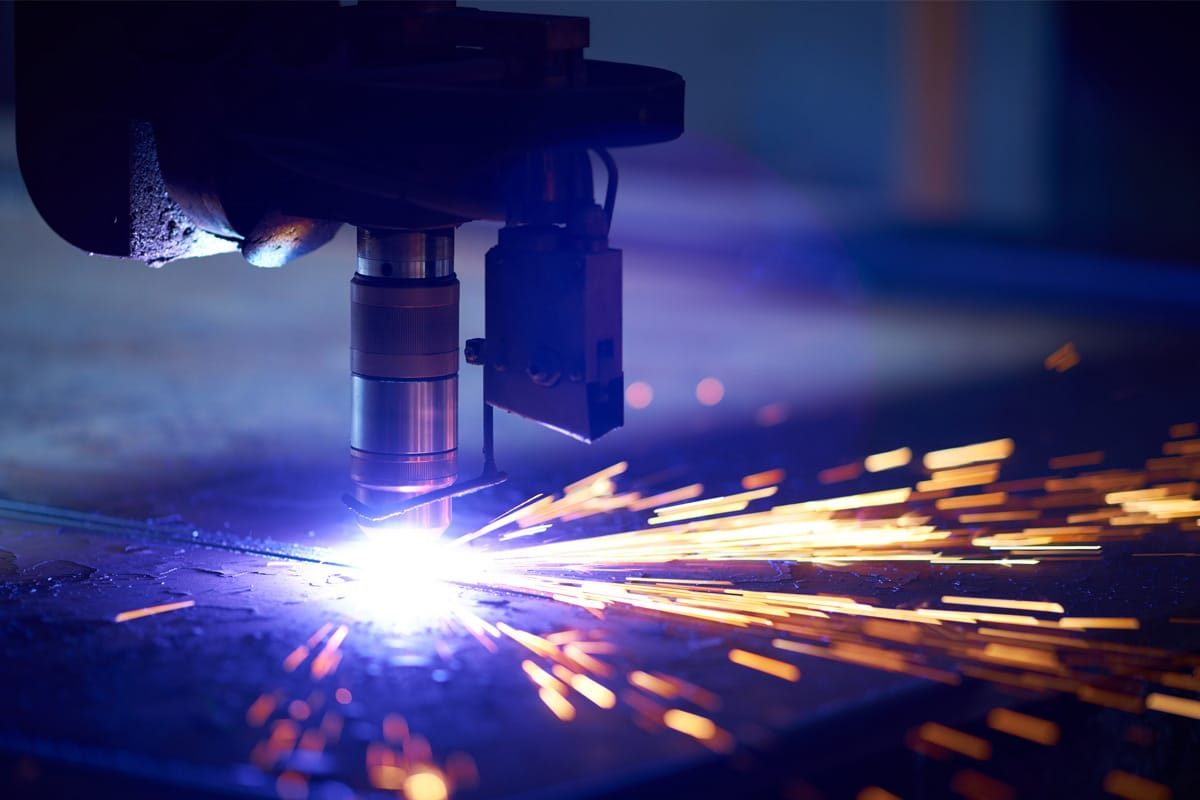
Häufige Probleme und Lösungen beim Faserlaserschneiden
Die Faserlaserschneidtechnologie wird aufgrund ihrer hohen Effizienz, Präzision und Flexibilität häufig zum Schneiden und Bearbeiten verschiedener metallischer und nichtmetallischer Materialien eingesetzt. Dabei wird ein Hochleistungslaserstrahl verwendet, um die Oberfläche des Werkstücks zu bestrahlen und es zu schmelzen oder zu verdampfen, wodurch ein präziser Schnitt des Werkstücks erreicht wird. In der Praxis ist das Faserlaserschneiden jedoch auch mit einigen häufigen Problemen und Herausforderungen verbunden, wie z. B. einer verringerten Schnittqualität, einer geringen Schneideffizienz und einem schnellen Geräteausfall. Das Verstehen und Bewältigen dieser Probleme kann nicht nur die Lebensdauer der Geräte verlängern, sondern auch die Produktionseffizienz und Verarbeitungsqualität verbessern.
Inhaltsverzeichnis
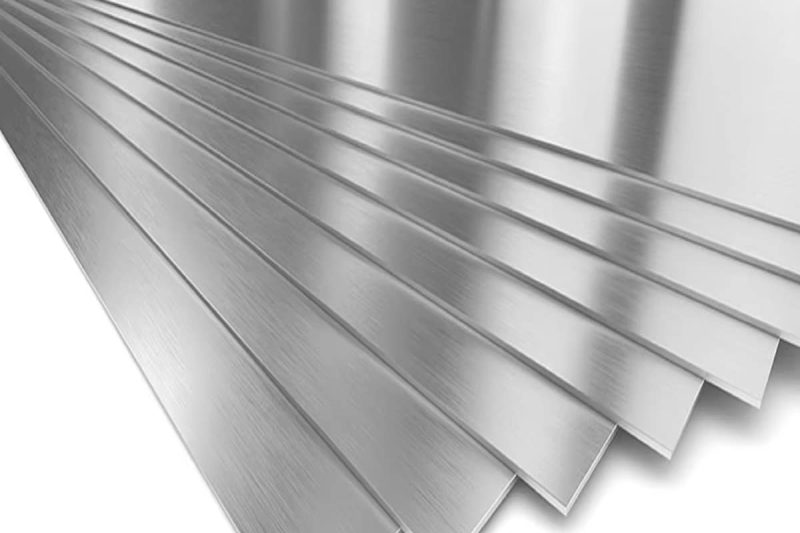
Materialbezogene Herausforderungen
Reflektivität und Leitfähigkeit
Je besser die Leitfähigkeit des Materials ist, desto geringer ist die Absorptionsrate der Laserenergie. Beispielsweise haben Gold, Silber, Kupfer, Aluminium und andere Materialien eine gute Leitfähigkeit und eine schlechte Energieabsorption, was auch als Reflexion der Laserwellenlänge gelten kann. Daher ist die Reflektivität umso höher, je höher die Leitfähigkeit des Metalls ist.
Herausforderung
- Hohe Reflektivität: Metalle wie Aluminium und Kupfer haben eine hohe Reflektivität. Insbesondere wenn der Laserstrahl in einem Winkel nahe der Normalen der Materialoberfläche auftrifft, wird der größte Teil der Laserenergie zum Lasergenerator oder zum Laserübertragungssystem reflektiert, was nicht nur die Bearbeitungseffizienz verringert, sondern auch zu Schäden an der Laserausrüstung führen kann, beispielsweise zum Verbrennen der Linse oder der Glasfaser.
- Unzureichende Energieabsorption: Aufgrund der hohen Reflektivität verringert sich die effektive Absorptionsenergie des Lasers durch die Materialoberfläche, was zu einer unzureichenden Bearbeitungstiefe, zu geringer Schnittgeschwindigkeit oder zu einer minderwertigen Bearbeitungsqualität führt.
Lösung
- Verwenden Sie Hochleistungslaser: Durch Erhöhen der Leistung des Lasergenerators kann die auf die Oberfläche des Materials abgestrahlte Laserenergie direkt erhöht werden. Auch wenn ein Teil der Energie reflektiert wird, reicht die verbleibende Energie für eine effiziente Verarbeitung aus. Wählen Sie einen Lasergenerator mit einer für bestimmte Materialien geeigneten Impulsbreite und Frequenz, um die Energieübertragung und Verarbeitungseffekte zu optimieren.
- Antireflexionstechnologie: Durch Anpassen der Form und des Divergenzwinkels des Laserstrahls wird die Laserenergie gleichmäßiger auf der Oberfläche des Materials verteilt, wodurch das Problem übermäßiger lokaler Reflexionen verringert wird. Verwenden Sie dynamisch anpassbare optische Elemente (wie verformbare Spiegel oder räumliche Flüssigkristall-Lichtmodulatoren), um die Wellenfrontverzerrung des Laserstrahls in Echtzeit zu korrigieren, die Fokussierungsqualität des Laserstrahls zu verbessern und Reflexion und Streuung zu verringern. Einige Metalle haben unterschiedliche Reflexionseigenschaften für Laser in unterschiedlichen Polarisationszuständen. Durch Anpassen der Polarisationsrichtung des Lasers kann der Reflexionsverlust verringert werden.
- Optimieren Sie die Oberflächenbehandlung des Materials: Tragen Sie eine Beschichtung oder einen Film auf, der Laserenergie auf der Oberfläche des Materials absorbiert, um die Absorptionsrate der Laserenergie zu erhöhen und die Reflektivität zu verringern. Erhöhen Sie die Rauheit der Materialoberfläche durch mechanische, chemische oder Laservorbehandlung, verbessern Sie die Streuung und Absorption der Laserenergie und verringern Sie die direkte Reflexion. Bilden Sie eine Absorptionsschicht auf der Oberfläche des Materials oder ändern Sie seine chemischen Oberflächeneigenschaften, um die Laserabsorptionsrate zu erhöhen.
- Passen Sie die Verarbeitungsparameter an: Optimieren Sie den Einfallswinkel des Laserstrahls, um zu vermeiden, dass der Laserstrahl direkt senkrecht auf die Materialoberfläche auftrifft, und verringern Sie dadurch die Spiegelreflexion. Passen Sie Geschwindigkeit, Leistung, Brennweite und andere Parameter der Laserverarbeitung an, um die besten Verarbeitungsbedingungen zu finden und so Verarbeitungsqualität und -effizienz sicherzustellen.
Materialverformung und Verformung
Eine Materialverformung entsteht durch Verziehen, welches durch Eigenspannungen im Material bedingt ist und ungleichmäßig über die Breite und Länge des Materials verteilt ist.
Herausforderung
Beim Laserschneiden kann es durch lokale Erwärmung zu Materialverformungen kommen, insbesondere bei dünnen Plattenmaterialien. Dies liegt daran, dass der Laser beim Schneiden eine große Menge Wärmeenergie auf einen kleinen Bereich konzentriert, wodurch die Temperatur des Bereichs schnell ansteigt, was wiederum zu einer thermischen Ausdehnung und Kontraktion des Materials führt und letztendlich dazu, dass sich das Material verzieht und verformt.
Lösung
- Passen Sie die Laserleistung an: Durch die Reduzierung der Laserleistung können Sie die Wärmekonzentration verringern und dadurch die thermische Verformung des Materials reduzieren.
- Schnittgeschwindigkeit optimieren: Durch entsprechende Erhöhung der Schnittgeschwindigkeit kann die Verweilzeit des Lasers auf dem Material verkürzt und der Wärmestau verringert werden.
- Hilfsgas verwenden: Durch die Auswahl eines geeigneten Hilfsgases (z. B. Stickstoff oder Sauerstoff) und die Anpassung seiner Durchflussrate kann die beim Schneidvorgang entstehende Wärme effektiv abgeführt und die Materialverformung verringert werden.
Materialstärke
Beim Faserlaserschneiden wirkt sich die Materialdicke direkt auf die Schnittqualität, Effizienz und Maschinenleistung aus. Dünnere Materialien lassen sich leichter, schneller und präziser schneiden, dickere Materialien können jedoch raue Schnittkanten aufweisen oder erfordern mehr Leistung und Hilfsgas.
Herausforderung
Beim Schneiden dickerer Materialien braucht der Laser länger, um in das Material einzudringen, was leicht zu ungleichmäßigem Schnitt führen kann. Dicke Materialien haben eine schlechte Wärmeleitfähigkeit und Wärme wird nicht leicht abgeleitet, was zu Schlacke und unregelmäßigen Schnittflächen an der Schneide führt.
Lösung
- Wählen Sie die geeignete Laserleistung: Wählen Sie entsprechend der Materialdicke die geeignete Laserleistung, um sicherzustellen, dass die Strahlenergie im Schneidbereich konzentriert ist und der beste Schneideffekt erzielt wird.
- Passen Sie die Schneidparameter an: Dazu gehören Parameter wie Schnittgeschwindigkeit, Fokusposition und Hilfsgasdruck, um die Stabilität und Gleichmäßigkeit des Schneidvorgangs sicherzustellen.
- Mehrfachschneiden: Bei besonders dicken Materialien können mehrere Schneideverfahren angewendet werden, wobei jedes Mal ein Teil der Dicke geschnitten wird, d. h. Schicht für Schicht, um Wärmestau und Probleme mit ungleichmäßigem Schneiden zu verringern.
Durch die oben genannten Methoden können die Probleme der hohen Materialreflexion, des Verziehens, der Verformung und des ungleichmäßigen Schneidens von dicken Materialien beim Laserschneiden wirksam gelöst und die Schnittqualität und -effizienz verbessert werden.
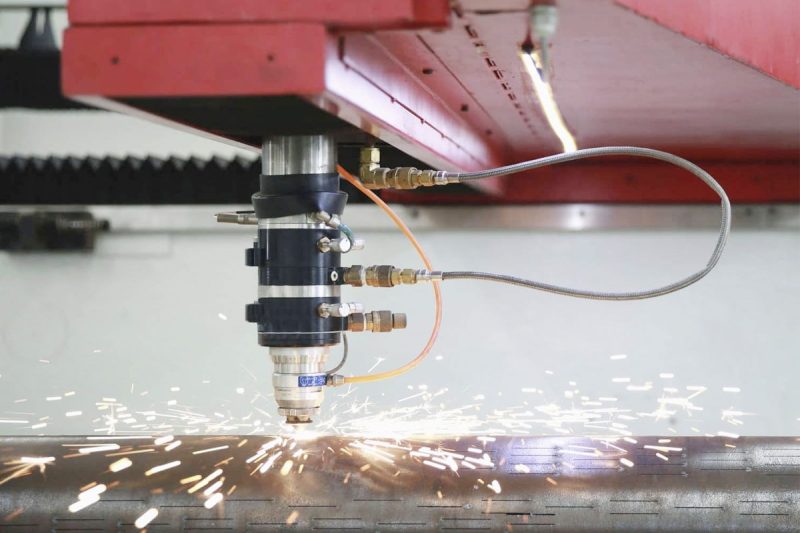
Kantenqualität und Schnittbreite
Die Glätte der Schnittkante und die Anzahl der Grate sind entscheidend für die Bewertung der Schnittgenauigkeit. Wenn die Laserenergie ungleichmäßig verteilt ist oder die Schnittgeschwindigkeit nicht angemessen ist, kann die Kante rau oder gratig erscheinen. Die Breite des Schlitzes hängt von der Stabilität des Laserfokus ab. Wenn der Fokus instabil ist oder die Laserleistung schwankt, kann die Breite des Schlitzes inkonsistent variieren, was die Schnittgenauigkeit beeinträchtigt.
Ecken und Kanten
Herausforderung
- Wenn beim Laserschneiden die Energie ungleichmäßig ist oder die Schnittgeschwindigkeit zu hoch oder zu niedrig ist, weist die Schnittkante häufig Grate und Unebenheiten auf. Insbesondere wenn die Leistungsabgabe des Laserstrahls instabil ist, kann die Oberfläche des geschnittenen Materials lokal überhitzt oder ungleichmäßig geschmolzen werden, was zu rauen Kanten führt.
- Bei einigen Metallmaterialien (wie Aluminium, Edelstahl usw.) führt eine ungleichmäßige Wärmeverteilung zu thermischem Stress, der wiederum zur Bildung von Graten führt.
- Darüber hinaus beeinträchtigt eine unsachgemäße Verwendung von Hilfsgas (unzureichender Luftstrom oder unangemessener Druck) auch die Entladungseffizienz des geschmolzenen Materials und erhöht die Anzahl der Grate.
Lösung
- Es ist wichtig, die Leistungseinstellungen und die Schnittgeschwindigkeit des Lasers zu optimieren. Stellen Sie sicher, dass die Laserleistung hoch genug und die Ausgabe stabil ist, um eine gleichmäßige Wärmeverteilung auf der Materialoberfläche aufrechtzuerhalten. Gleichzeitig muss die Schnittgeschwindigkeit entsprechend der Dicke und den Eigenschaften des Materials angepasst werden, weder zu schnell (um ein unzureichendes Schneiden des Materials zu vermeiden) noch zu langsam (um ein übermäßiges Schmelzen zu verhindern).
- Die Verwendung des richtigen Hilfsgases, wie Stickstoff oder Sauerstoff, kann das Schneidergebnis verbessern und eine saubere und glatte Schnittfläche gewährleisten. Stickstoff wird häufig verwendet, um Oxidation zu verhindern und Kantengrate zu reduzieren, während Sauerstoff hilft, die Schneideffizienz und die Schmelzgeschwindigkeit zu erhöhen.
Schlitzbreitenvariation
Herausforderung
- Der Hauptgrund für eine inkonsistente Spaltbreite liegt normalerweise in der Instabilität des Laserfokus oder der Schwankung der Laserleistung. Wenn der Laserfokus verschoben wird, ändert sich die Energiekonzentration entsprechend, was zu Schwankungen der Spaltbreite führt. Wenn die Laserleistung instabil ist, wirkt sich die Energieschwankung direkt auf die Schnittgenauigkeit aus und führt zu Änderungen der Spaltbreite.
- Darüber hinaus können Verunreinigungen oder Schäden an den optischen Komponenten auch zu Veränderungen der Strahlqualität führen und dadurch die Gleichmäßigkeit der Schnittlinie beeinträchtigen. Der Verschleiß der mechanischen Teile der Ausrüstung, wie z. B. der Führungsschienen und Lager, beeinträchtigt auch die Bewegungsgenauigkeit des Laserkopfes, was zu inkonsistenten Schlitzen führt.
Lösung
- Überprüfen und warten Sie das optische System regelmäßig, um einen stabilen Laserfokus und eine stabile Laserenergie sicherzustellen.
- Reinigen oder ersetzen Sie verunreinigte optische Linsen, um unnötige Brechungen oder Streuungen während der Strahlübertragung zu vermeiden.
- Kalibrieren Sie regelmäßig den Fokus und die Leistungsabgabe der Laserausrüstung, um deren Genauigkeit während des Betriebs sicherzustellen.
- Warten Sie die mechanischen Teile des Geräts, um eine reibungslose und ungehinderte Bewegung des Laserkopfes zu gewährleisten und so Schnittfehler durch mechanischen Verschleiß zu reduzieren.
Zusammenfassend lässt sich sagen, dass durch die richtige Einstellung der Parameter und die regelmäßige Wartung des optischen Systems die Kantenqualität effektiv verbessert und die Schnittbreite kontrolliert werden kann.
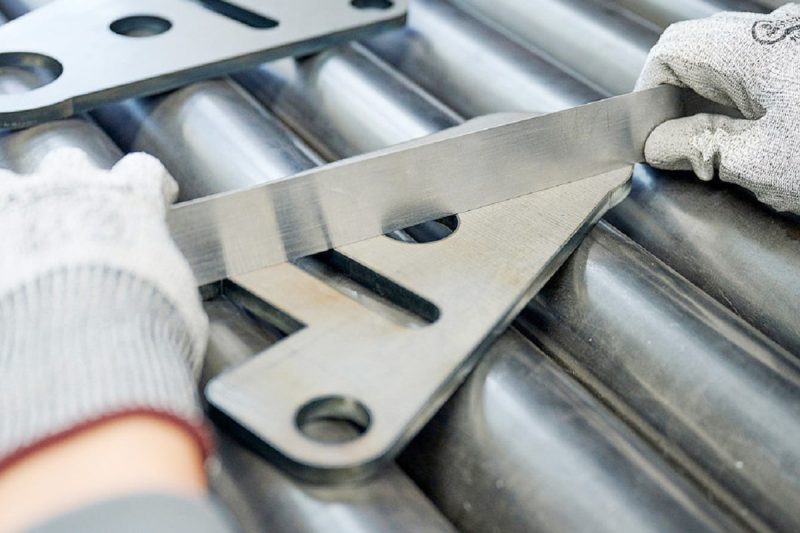
Prozessbezogene Herausforderungen
Prozessbedingte Herausforderungen betreffen hauptsächlich technische Probleme, die während des Faserlaserschneidprozesses auftreten können. Zu den üblichen prozessbedingten Herausforderungen gehört die Ansammlung von Schlacke, die beim Faserlaserschneidprozess häufig auftritt, insbesondere beim Schneiden dickerer oder schwer zu schneidender Materialien. Normalerweise wird die Ansammlung von Schlacke dadurch verursacht, dass das Material nicht vollständig schmilzt oder verdampft oder dass nicht genügend Hilfsgas zugeführt wird, um das geschmolzene Material rechtzeitig aus dem Schneidbereich zu blasen.
Schlackenansammlung
Herausforderung
- Wenn die Laserenergie nicht ausreicht oder der Fokus des Laserstrahls verschoben ist, kann die Materialoberfläche nicht die Temperatur erreichen, die zum Schmelzen oder Verdampfen erforderlich ist, sodass an der Schnittkante etwas Material zurückbleibt. Insbesondere bei der Bearbeitung dicker Platten muss die Laserenergie stark genug sein, um die gesamte Materialdicke zu durchdringen.
- Hilfsgase wie Sauerstoff oder Stickstoff werden häufig verwendet, um das geschmolzene Material vom Schneidbereich wegzublasen. Wenn der Gasdruck zu niedrig ist und das geschmolzene Material nicht effektiv entfernt werden kann, sammelt sich Schlacke an der Schneide.
- Eine zu hohe Schnittgeschwindigkeit führt dazu, dass der Laser nicht dauerhaft auf die gleiche Fläche einwirkt, das Material nicht vollständig schmilzt oder das Gas die Rückstände nicht rechtzeitig ausstößt und es zu Schlackenbildung kommt.
Lösung
- Stellen Sie sicher, dass ausreichend Gasdruck vorhanden ist, um das geschmolzene Material effektiv zu entfernen und Schlackenbildung zu vermeiden. Stickstoff eignet sich für nicht oxidierende Materialien, während Sauerstoff die Schnittgeschwindigkeit erhöhen kann, aber einen höheren Gasdruck erfordert.
- Optimieren Sie die Schnittgeschwindigkeit entsprechend der Materialdicke und -eigenschaften, um sicherzustellen, dass die Laserenergie vollständig auf den Schnittbereich einwirken kann. Die geeignete Kombination aus Laserleistung und Schnittgeschwindigkeit kann unnötige Wärmeeinflusszonen reduzieren und so das Problem des unvollständigen Schmelzens von Materialien vermeiden.
- Stellen Sie sicher, dass die optischen Komponenten des Lasergenerators in bestem Zustand sind und die erforderliche Laserleistung stabil abgeben können, um die Konsistenz des Schneidprozesses zu gewährleisten.
Durch eine umfassende Anpassung dieser Parameter können Schlackenbildungsprobleme deutlich verringert, die Schnittqualität verbessert und nachfolgende Schleif- und Reinigungsarbeiten reduziert werden.
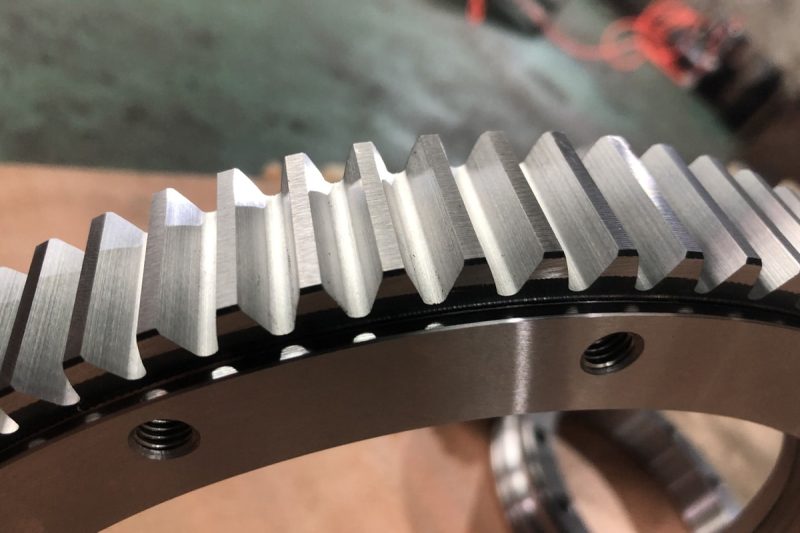
Reifenpanne und Startprobleme
Beim Faserlaserschneiden treten häufig Probleme mit der Perforation und beim Anfahren auf, insbesondere bei dickeren oder stark reflektierenden Materialien. Der Perforationsprozess ist der Ausgangspunkt des Laserschneidens, und seine Stabilität und Effizienz wirken sich direkt auf die Wirkung des gesamten Schneidprozesses aus. Wenn die Perforationszeit zu lang ist oder fehlschlägt, kann dies zu Materialverschwendung und Geräteverschleiß führen und sogar die Schnittqualität beeinträchtigen. Die Instabilität des Anfahrvorgangs führt zu ungleichmäßigen Schlitzen und schlechter Schnittkantenqualität, was sich auf die Genauigkeit und das Erscheinungsbild des fertigen Produkts auswirkt.
Piercing-Verzögerungen und -Fehler
Herausforderung
Verzögerungen beim Einstechen entstehen normalerweise dadurch, dass der Laserstrahl nicht schnell genug Energie bündelt, um das Material zu durchdringen, was zu einer langen Einstichzeit führt. Verzögerungen beim Einstechen sind besonders bei dickeren oder reflektierenden Materialien (wie Aluminium und Kupfer) erkennbar und können sogar zu Fehlschlägen beim Einstechen führen. Gründe für Fehlschläge beim Einstechen können unzureichende Laserleistung, ungenauer Laserfokus, unzureichendes Hilfsgas oder eine ungeeignete Gasauswahl sein. Dies kann zu ungleichmäßigen oder fehlgeschlagenen Schneidstarts, Materialabfall und möglicherweise zu Schäden an der Laserausrüstung führen.
Lösung
- Stellen Sie sicher, dass die Laserleistung schnell konzentriert werden kann, insbesondere bei dicken Plattenmaterialien, bei denen zum Perforieren mehr Energie erforderlich ist. Passen Sie den Laserfokus so an, dass er auf der Oberfläche des Materials konzentriert ist. Dadurch wird die Energiestreuung verringert und die Perforationszeit verkürzt.
- Durch das Einstechen im Kurzpulsmodus können Materialüberhitzung und Verformung verringert werden, während die Wahrscheinlichkeit eines Einstichfehlers reduziert wird. Diese Technik eignet sich besonders für dickere Materialien und stark reflektierende Materialien.
- Die Verwendung von Stickstoff und Sauerstoff hat erhebliche Auswirkungen auf den Perforationsprozess. Sauerstoff kann den Perforationsprozess beschleunigen, kann jedoch zur Oxidation des Materials führen. Daher müssen das geeignete Gas und der geeignete Druck basierend auf den Materialeigenschaften ausgewählt werden.
- Bei sehr dicken Materialien können mehrstufige Perforationstechniken eingesetzt werden, bei denen das Material nicht auf einmal, sondern schichtweise durchdrungen wird. Durch diese Methode können Durchstoßfehler und übermäßige thermische Effekte wirksam vermieden werden.
Instabiler Start
Herausforderung
Der instabile Start äußert sich hauptsächlich in einer ungleichmäßigen Schnittbreite und einer schlechten Kantenqualität zu Beginn des Laserschneidens und kann sogar zum Scheitern des Schneidvorgangs führen. Dies wird normalerweise durch instabile Laserenergie, Änderungen der Gasdurchflussrate, inkonsistente Materialoberflächeneigenschaften (wie Oxidation oder Beschichtung) usw. verursacht. Ein instabiler Start kann zu einer schlechten Schnittqualität im Anfangsteil führen, insbesondere bei Präzisionsschneidanwendungen. Diese Instabilität beeinträchtigt die Genauigkeit und Konsistenz des fertigen Produkts.
Lösung
- Vor dem Start kann die Materialoberfläche vorgewärmt werden, insbesondere bei stark reflektierenden Materialien. Dies trägt zur Reduzierung von Laserreflexionen bei und sorgt für einen gleichmäßigeren Schneidvorgang.
- Stellen Sie sicher, dass der Lasergenerator beim Start schnell einen stabilen Zustand erreicht, indem Sie die Steigerungsrate der Laserleistung und die Durchflussrate des Hilfsgases anpassen. Dadurch können Energieschwankungen beim Start wirksam vermieden werden.
- Bei Materialien mit Oxidschichten oder anderen Verunreinigungen auf der Oberfläche kann vor dem Start eine einfache Oberflächenreinigung oder Beschichtungsentfernung durchgeführt werden, um Laserreflexionen und Instabilitäten während des Startvorgangs zu verringern.
- Überwachen Sie den Schneidvorgang insbesondere in der Anlaufphase mithilfe eines Echtzeit-Überwachungssystems und stellen Sie durch die Anpassung der Parameter die Stabilität und Konstanz des Schneidprozesses sicher.
Im Allgemeinen können durch die Optimierung der Laserparameter, die Auswahl eines geeigneten Hilfsgases, den Einsatz der Impulsperforationstechnologie und die Vorverarbeitung vor dem Start die Probleme von Perforationsverzögerungen, Fehlern und instabilem Start erheblich reduziert und die Schneideffizienz und -qualität verbessert werden. Diese Lösungen verbessern nicht nur die Betriebseffizienz, sondern gewährleisten auch einen langfristig stabilen Betrieb der Geräte.
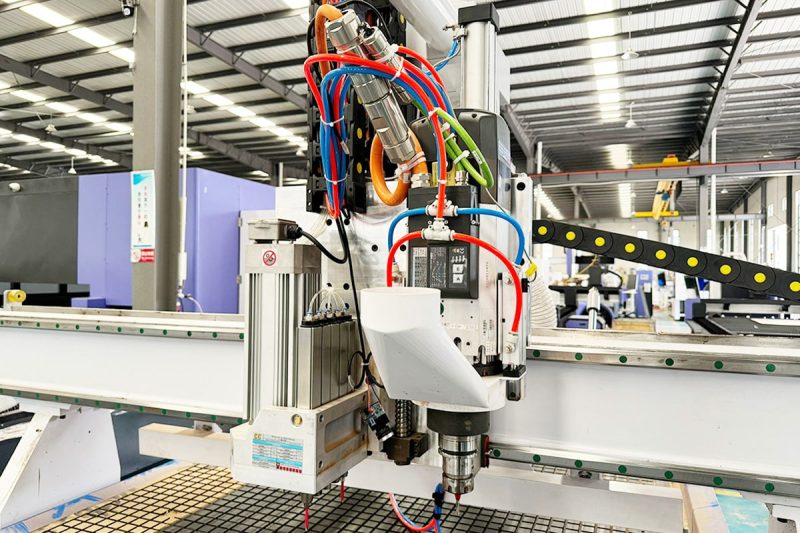
Maschinenbezogene Herausforderungen
Beim Faserlaserschneiden wirkt sich die Leistung der Maschine direkt auf die Schnittqualität und -effizienz aus. Das Strahlübertragungssystem und die mechanischen Komponenten der Maschine selbst können nach längerem Gebrauch verschiedene Probleme aufweisen, die die Genauigkeit und Stabilität des Laserschneidens beeinträchtigen.
Probleme mit dem Strahlführungssystem
Herausforderung
Das Strahlübertragungssystem ist das Kernsystem, das die Energie der Laserquelle an den Schneidkopf überträgt. Seine Leistung bestimmt direkt die Energiestabilität des Laserstrahls und die Schnittqualität. Wenn das Strahlübertragungssystem nicht regelmäßig überprüft und gewartet wird, können Staub, Verunreinigungen oder mechanischer Verschleiß auch die optischen Komponenten beschädigen und so die Effizienz des Systems weiter verringern.
Lösung
- Optische Linsen und Linsen in Faserlaserschneidsystemen neigen zur Ansammlung von Staub und Öl. Regelmäßiges Reinigen kann den Rückgang der Laserstrahlübertragungseffizienz verhindern und die Strahlstabilität gewährleisten.
- Durch die Gewährleistung der Stabilität der Glasfaseranschlüsse und die präzise Ausrichtung der Laserstrahlen können Energieverluste verringert werden. Überprüfen Sie die Glasfaserverbindungen regelmäßig, um sicherzustellen, dass keine Lockerheit oder Abnutzung vorliegt.
- Wenn häufig Probleme mit der Strahlinstabilität auftreten, sollten Sie die Verwendung adaptiver Optiktechnologie in Betracht ziehen, um das Strahlübertragungssystem in Echtzeit anzupassen und so die beste Strahlqualität sicherzustellen.
- Wärmestau während der Strahlübertragung beeinträchtigt die Strahlqualität. Daher ist es wichtig, dass das Kühlsystem effektiv läuft. Überprüfen Sie das Kühlsystem regelmäßig, um sicherzustellen, dass es die Wärme normal ableiten und die thermische Belastung während der Strahlübertragung reduzieren kann.
Mechanischer Verschleiß
Herausforderung
Die mechanischen Komponenten von Faserlaserschneidmaschinen, einschließlich Führungsschienen, Servomotoren und Antriebssystemen, verschleißen bei intensiver Nutzung mit der Zeit allmählich. Mechanischer Verschleiß führt nicht nur zu einer instabilen Bewegung des Schneidkopfes, sondern kann auch die Genauigkeit des Schneidpfads und letztlich die Qualität des fertigen Produkts beeinträchtigen. Insbesondere bei hohen Geschwindigkeits- und Präzisionsschneidanforderungen beschleunigt mechanischer Verschleiß die Alterung der Geräte und erhöht die Wartungskosten und Ausfallzeiten. Darüber hinaus sind erhöhte Vibrationen und Lärm ebenfalls häufige Symptome von mechanischem Verschleiß.
Lösung
- Die Führungsschienen und Übertragungssysteme müssen regelmäßig geschmiert werden, um die Reibung zu verringern und die Lebensdauer mechanischer Teile zu verlängern. Gleichzeitig sollte das Schmiersystem überprüft werden, um seinen normalen Betrieb sicherzustellen und übermäßigen Verschleiß von Teilen aufgrund unzureichender Schmierung zu vermeiden.
- Wenn sich herausstellt, dass Führungsschienen, Zahnräder oder andere Teile abgenutzt oder verschoben sind, sollten die beschädigten Teile rechtzeitig ausgetauscht werden, um die Genauigkeit und Stabilität der Maschine sicherzustellen.
- Bei hochpräzisen Operationen können Vibrationen die Schnittgenauigkeit beeinträchtigen. Durch den Einbau von Antivibrationsvorrichtungen oder die Optimierung der Installationsposition der Maschine können die Auswirkungen von Vibrationen auf mechanische Teile verringert und so der Verschleiß verzögert werden.
- Modern Faserlaser-Schneidemaschinen kann mit einem Überwachungssystem ausgestattet werden, um den Status mechanischer Teile in Echtzeit zu überwachen, mögliche Ausfälle durch Datenanalyse im Voraus vorherzusagen und plötzliche Ausfallzeiten durch mechanischen Verschleiß zu vermeiden.
Durch regelmäßige Wartung und Optimierung des Strahlübertragungssystems und der mechanischen Komponenten können Leistung und Stabilität der Faserlaserschneidmaschine deutlich verbessert und so die Kontinuität und hohe Qualität des Schneideffekts sichergestellt werden.
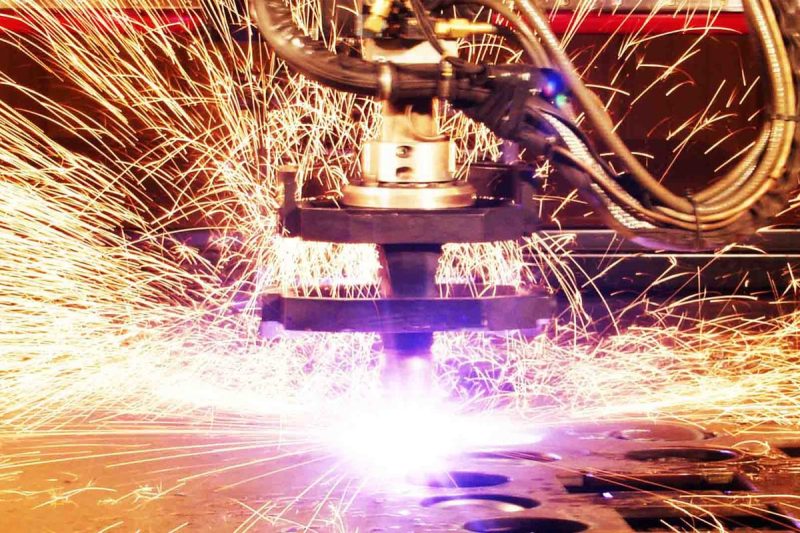
Konizität und Winkelabweichung
Konizität und Winkelabweichung sind zwei häufige Präzisionsprobleme beim Faserlaserschneiden. Konizitätsprobleme äußern sich normalerweise als uneinheitliche obere und untere Breite der Schnittkante, während sich Winkelabweichungen auf die fehlende Rechtwinkligkeit zwischen Laserstrahl und Material beziehen, was zu einer geneigten Schnittfläche führt. Diese Probleme beeinträchtigen die Qualität und das Aussehen des fertigen Werkstücks, insbesondere bei hochpräzisen Schneidaufgaben.
Verjüngung
Herausforderung
Das Verjüngungsphänomen tritt normalerweise beim Schneiden von dickem Material auf und äußert sich darin, dass die Schneide oben schmal und unten breit oder oben breit und unten schmal ist. Dies liegt daran, dass die Energieverteilung des Laserstrahls beim Durchgang durch das Material ungleichmäßig ist. Je größer die Schnitttiefe, desto deutlicher ist die Dämpfung der Laserenergie, was zu einem Unterschied in der oberen und unteren Breite der Schneide führt. Die Verjüngung beeinträchtigt die Genauigkeit des Werkstücks, insbesondere bei hochpräziser Montage. Die Verjüngung verursacht Montageschwierigkeiten und führt sogar zum Ausschuss des Werkstücks. Darüber hinaus verschlimmern auch ein unangemessener Hilfsgasdruck und eine instabile Laserleistung das Verjüngungsphänomen.
Lösung
- Konizitätsprobleme können durch die Optimierung der Tiefe und Position des Laserfokus effektiv reduziert werden. Die Positionierung des Fokus in der Mitte des Materials statt auf der Oberfläche trägt dazu bei, eine gleichmäßige Verteilung der Laserenergie über die gesamte Schnittdicke aufrechtzuerhalten.
- Bei dickeren Materialien kann die Verwendung eines Lasergenerators mit höherer Leistung eine stabilere Energieabgabe während des Schneidprozesses aufrechterhalten und durch Laserdämpfung verursachte Konizitätsprobleme verringern.
- Die Verjüngung kann durch die richtige Einstellung des Hilfsgasdrucks, das Sauberhalten des Schneidbereichs und die effektive Kühlung der Schneide verringert werden. Insbesondere beim Schneiden dicker Materialien ist die Rolle des Hilfsgases von entscheidender Bedeutung.
- Jedes kleine Problem mit dem optischen System führt zu einer ungleichmäßigen Energieverteilung des Laserstrahls. Daher kann eine regelmäßige Wartung und Reinigung der optischen Komponenten zur Sicherstellung der Laserstrahlqualität die Verjüngung wirksam reduzieren.
Winkelabweichung
Herausforderung
Winkelabweichung bezieht sich auf den Mangel an Vertikalität des Laserstrahls im Verhältnis zum Material, was zu einer geneigten Schnittkante führt. Dies kann durch eine instabile Installation des Laserkopfes, eine falsche Strahlausrichtung oder eine unzureichende Präzision des mechanischen Systems verursacht werden. Winkelabweichungen führen dazu, dass die Schnittfläche des Werkstücks uneben ist, was die Genauigkeit und das Aussehen beeinträchtigt, insbesondere wenn das Werkstück im rechten Winkel geschnitten werden muss.
Lösung
- Der erste Schritt zur Lösung des Winkelabweichungsproblems besteht darin, sicherzustellen, dass der Laserkopf fest montiert und senkrecht zum Material steht. Eine regelmäßige Kalibrierung des Laserkopfs und des mechanischen Systems stellt sicher, dass der Laserstrahl beim Schneiden immer den richtigen Winkel beibehält.
- Schneidgeschwindigkeit, Leistungsabgabe und Hilfsgaseinstellungen wirken sich alle auf die Winkelabweichung aus. Durch die Optimierung dieser Parameter kann der Laserstrahl während des Schneidens stabil gehalten und so die Winkelabweichung verringert werden.
- Adaptive Optiken können Ausbreitungsweg und Fokus des Laserstrahls in Echtzeit anpassen und so dafür sorgen, dass beim Schneiden immer der richtige Winkel zum Material eingehalten wird. Dadurch werden Winkelabweichungen reduziert.
- Externe Faktoren wie Temperatur- und Feuchtigkeitsschwankungen sowie Vibrationen können die Winkelgenauigkeit beim Laserschneiden beeinträchtigen. Winkelabweichungen können weiter reduziert werden, indem die Stabilität der Schneidumgebung aufrechterhalten wird, beispielsweise durch Reduzierung von Vibrationen, Kontrolle von Temperatur und Feuchtigkeit usw.
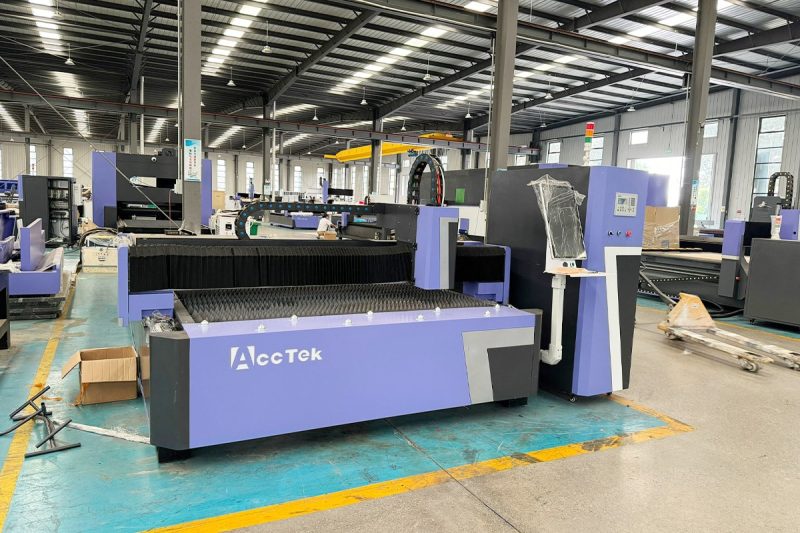
Umweltfaktoren
Umweltfaktoren haben einen direkten Einfluss auf die Stabilität und Qualität des Faserlaserschneidprozesses. Temperatur- und Feuchtigkeitsschwankungen sowie Veränderungen der Luftqualität können sich negativ auf die Leistung des Lasersystems, die Schnittqualität und die Lebensdauer der Maschine auswirken. Das Verständnis und die Kontrolle dieser Umweltfaktoren kann sicherstellen, dass die Ausrüstung optimal funktioniert und unnötige Ausfälle und Wartungsanforderungen reduziert werden.
Temperatur- und Feuchtigkeitsschwankungen
Herausforderung
Temperatur- und Feuchtigkeitsschwankungen stellen beim Laserschneidprozess eine große Herausforderung dar. Der Lasergenerator und das optische System reagieren sehr empfindlich auf Temperatur- und Feuchtigkeitsschwankungen. Eine zu hohe Temperatur kann beispielsweise dazu führen, dass der Lasergenerator überhitzt, was die Qualität und Stabilität des Laserstrahls beeinträchtigt; eine zu niedrige Temperatur kann dazu führen, dass der Lasergenerator die erforderliche Betriebstemperatur nicht erreicht, was sich wiederum auf die Leistungsabgabe auswirkt. Eine zu hohe Feuchtigkeit kann zu Kondensation auf den optischen Komponenten führen, was die Übertragungseffizienz des Laserstrahls beeinträchtigt und sogar die optischen Geräte beschädigen kann. Eine zu niedrige Feuchtigkeit kann das Risiko statischer Elektrizität erhöhen, die den normalen Betrieb elektronischer Komponenten stören kann.
Lösung
- Um Temperatur- und Feuchtigkeitsschwankungen zu bewältigen, empfiehlt es sich, in der Schneidwerkstatt spezielle Umweltkontrollsysteme wie Klimaanlagen und Entfeuchtungsgeräte zu installieren. Diese Systeme können Temperatur und Feuchtigkeit in der Werkstatt konstant halten, um sicherzustellen, dass die Laserausrüstung unter optimalen Bedingungen arbeitet.
- Installieren Sie Temperatur- und Feuchtigkeitssensoren rund um die Schneidausrüstung, um die Umgebungsbedingungen in Echtzeit zu überwachen. Sobald eine Anomalie erkannt wird, kann das Umgebungskontrollsystem automatisch angepasst oder der Schneidvorgang bei Bedarf unterbrochen werden, um Schäden an der Ausrüstung zu vermeiden.
- Erhöhen Sie in einer trockenen Umgebung die Luftfeuchtigkeit, um das Risiko statischer Elektrizität zu verringern, und verwenden Sie antistatische Böden und Maßnahmen zur Geräteerdung, um einen sicheren Betrieb zu gewährleisten.
Luftqualität
Herausforderung
Die Auswirkungen der Luftqualität auf den Laserschneidprozess können nicht ignoriert werden. Staub, Ölnebel und andere in der Luft schwebende Schadstoffe können in das optische System oder den Schneidbereich des Lasergenerators gelangen und die Übertragung und Fokussierung des Laserstrahls beeinträchtigen. Schadstoffe in der Luft können während des Schneidvorgangs auch mit dem Laserstrahl reagieren, was zu schlechten Schneidergebnissen oder sogar zu Schäden an der Werkstückoberfläche führt. Darüber hinaus erhöht eine langfristige Einwirkung von Luft schlechter Qualität die Häufigkeit der Maschinenwartung und verkürzt die Lebensdauer der Geräte.
Lösung
- Installieren Sie in der Laserschneidwerkstatt ein Luftreinigungssystem, um Partikel und Schadstoffe aus der Luft herauszufiltern und saubere Luft zu gewährleisten. Insbesondere beim Schneiden bestimmter Materialien (wie Kunststoff und Holz) können diese während des Laserschneidvorgangs schädliche Gase freisetzen, daher ist ein wirksames Luftreinigungssystem besonders wichtig.
- Auch mit einem Luftreinigungssystem ist es notwendig, das optische System des Lasergenerators regelmäßig zu reinigen. Entfernen Sie Staub und Schmutz, die sich dort ansammeln können, um die Qualität des Laserstrahls und die Schneidwirkung sicherzustellen.
- Bei einigen wichtigen Geräten oder Bereichen können Überdruckschutzmaßnahmen ergriffen werden. Das heißt, durch die Zufuhr gefilterter Luft wird der Luftdruck im Bereich höher gehalten als draußen, um das Eindringen von Schadstoffen zu verhindern.
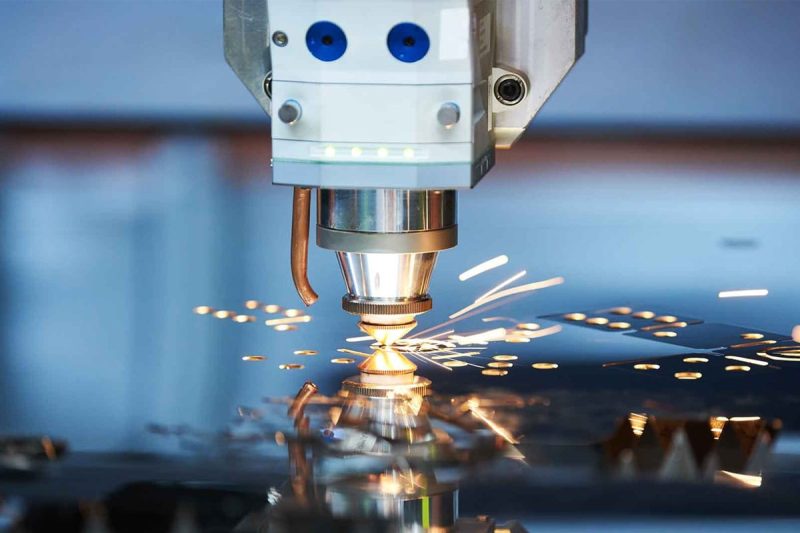
Betreiberbezogene Herausforderungen
Neben Umweltfaktoren wirken sich auch das Qualifikationsniveau und die Arbeitseffizienz des Bedieners direkt auf die Qualität und Effizienz des Faserlaserschneidens aus. Mangelnde Schulung und Fachkenntnisse oder ein ineffizienter Arbeitsablauf können zu unsachgemäßer Bedienung, erhöhten Fehlerquoten und sogar zu Geräteschäden oder Sicherheitsunfällen führen. Daher sind die Verbesserung der Professionalität des Bedieners und die Optimierung des Arbeitsablaufs wichtige Bindeglieder, um Schnittqualität und Produktionseffizienz sicherzustellen.
Mangelnde Ausbildung und Fachkenntnisse
Herausforderung
Das Faserlaserschneiden ist eine hochpräzise Technologie, die von den Bedienern ein hohes Maß an Fachwissen und Fähigkeiten erfordert. In einigen Unternehmen sind die Bediener jedoch möglicherweise nicht ausreichend geschult und können die Komplexität des Laserschneidens nicht vollständig verstehen und beherrschen. Diese Situation kann dazu führen, dass die Bediener bei technischen Problemen oder komplexen Werkstücken nicht effektiv reagieren können, was die Schnittqualität beeinträchtigen, den Geräteverschleiß erhöhen und sogar Sicherheitsrisiken verursachen kann. Darüber hinaus erfordert die Wartung und Pflege der Geräte spezielle Fähigkeiten und Kenntnisse. Der Mangel an Wissen des Bedieners kann dazu führen, dass die Geräte nicht rechtzeitig gewartet und gepflegt werden, was die Lebensdauer der Geräte verkürzt.
Lösung
- Unternehmen sollten ihren Bedienern systematische Schulungen anbieten, die die Grundprinzipien des Laserschneidens, Bedienungsanleitungen für Geräte, Fehlersuche und Lösungen für häufige Probleme usw. umfassen. Durch regelmäßige Schulungen stellen Sie sicher, dass die Bediener immer mit der neuesten Technologie und den neuesten Betriebsspezifikationen vertraut sind.
- Richten Sie ein Betriebszertifizierungssystem für Bediener ein, und nur zertifiziertes Personal darf Laserschneidgeräte bedienen. Dies verbessert nicht nur das Verantwortungsbewusstsein des Bedieners, sondern gewährleistet auch die Qualität und Sicherheit des Betriebs.
- Bieten Sie den Betreibern umfassenden technischen Support, beispielsweise durch die Einrichtung einer speziellen technischen Beratungsabteilung oder durch die Einstellung technischer Experten zur regelmäßigen Anleitung, um den Betreibern bei der Lösung von Problemen im täglichen Betrieb zu helfen.
Ineffizienter Workflow
Herausforderung
Die Effizienz des Arbeitsablaufs wirkt sich direkt auf die Gesamteffizienz der Produktion und die Qualität des Laserschneidens aus. In einigen Unternehmen verbringen die Bediener aufgrund einer unangemessenen Arbeitsablaufgestaltung oder unzureichender Koordination möglicherweise zu viel Zeit mit dem Wechseln von Aufgaben, dem Debuggen von Geräten oder dem Handhaben von Materialien. Dieser ineffiziente Arbeitsablauf verschwendet nicht nur Zeit und Ressourcen, sondern kann auch zur Ermüdung des Bedieners führen und die Fehlerwahrscheinlichkeit erhöhen. Wenn das Unternehmen den Arbeitsablauf nicht umgehend optimiert, wird der ineffiziente Prozess mit zunehmendem Auftragsvolumen noch deutlicher hervortreten und die Produktionskapazität und die Wettbewerbsfähigkeit des Unternehmens ernsthaft beeinträchtigen.
Lösung
- Durch die Analyse und Auswertung des aktuellen Arbeitsablaufs können wir Engpässe und ineffiziente Verknüpfungen identifizieren und gezielte Optimierungen vornehmen. So können wir beispielsweise die Reihenfolge der Aufgaben sinnvoll gestalten, die Zeit für die Inbetriebnahme der Geräte und die Materialhandhabung verkürzen und die Arbeitseffizienz verbessern.
- Durch die Einführung von Automatisierungstechnologien, wie automatischen Be- und Entladesystemen und intelligenter Satzsoftware, lassen sich Zeit- und Präzisionsfehler bei manuellen Vorgängen deutlich reduzieren und die Effizienz des gesamten Arbeitsablaufs verbessern.
- Wenden Sie Lean-Production-Prinzipien an, um Abfall zu reduzieren und die Ressourcenzuweisung zu optimieren. Durch kontinuierliche Verbesserung und Mitarbeiterbeteiligung können wir einen effizienten und flexiblen Arbeitsablauf etablieren, um die Effizienz und hohe Qualität des Laserschneidprozesses sicherzustellen.
Indem sie sich diesen ökologischen und bedienerbezogenen Herausforderungen stellen, können Unternehmen die Effizienz und Qualität des Faserlaserschneidens deutlich verbessern und sich so einen Wettbewerbsvorteil auf dem Markt verschaffen.
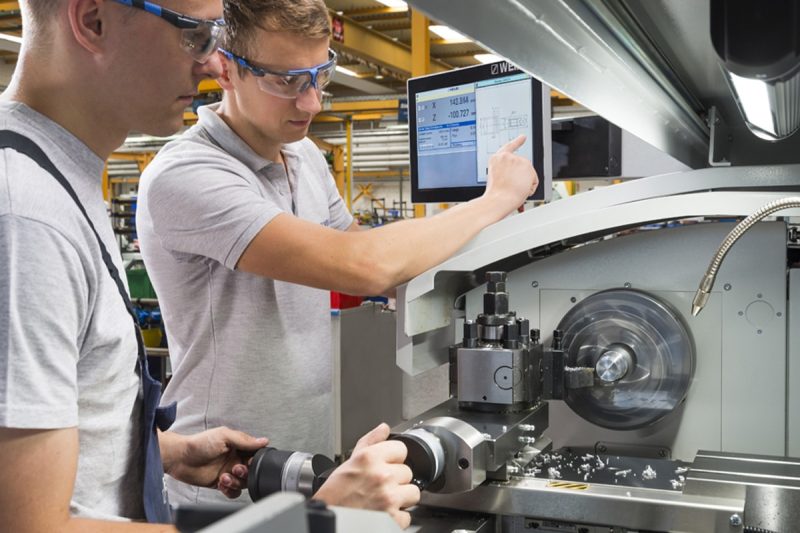
Vorsichtsmaßnahmen und bewährte Vorgehensweisen
Um einen kontinuierlich effizienten Betrieb des Faserlaserschneidens zu gewährleisten, ist es wichtig, vorbeugende Maßnahmen und bewährte Verfahren zu ergreifen. Durch regelmäßige Maschinenwartung, Parameteroptimierung, Schulung des Bedieners und kontinuierliche Verbesserung können Unternehmen die Ausfallraten effektiv senken, die Schnittqualität verbessern und die Lebensdauer der Geräte verlängern.
Regelmäßige Maschinenwartung
Herausforderung
Der Langzeitbetrieb von Laserschneidanlagen kann zur Verschmutzung optischer Komponenten, zum Verschleiß des Laserkopfes und zum Ausfall des Kühlsystems führen. Bei fehlender regelmäßiger Wartung können diese Probleme die Leistung des Lasergenerators beeinträchtigen, Produktionsausfallzeiten verlängern und sogar zu Geräteausfällen führen.
Lösung
- Reinigen Sie das optische System regelmäßig, um die Übertragungseffizienz des Laserstrahls sicherzustellen.
- Überprüfen und ersetzen Sie empfindliche Teile wie Schneiddüsen, Laserlinsen und Filtersysteme.
- Um eine Überhitzung des Lasergenerators zu verhindern, überprüfen Sie regelmäßig die ordnungsgemäße Funktion des Kühlsystems.
Parameteroptimierung
Herausforderung
Unterschiedliche Materialien und Dicken erfordern unterschiedliche Laserleistungen, Schnittgeschwindigkeiten und Gasdrücke. Falsche Parametereinstellungen können zu einer verringerten Schnittqualität führen, beispielsweise zu mehr Graten oder zu breiten oder zu schmalen Schnittfugen.
Lösung
- Entwickeln Sie detaillierte Schneidparametertabellen für verschiedene Materialien, um eine genaue Abstimmung von Leistung und Geschwindigkeit sicherzustellen.
- Testen Sie regelmäßig die Laserausgabe des Geräts, um eine stabile Leistung und Fokussierung sicherzustellen.
- Verwenden Sie Zusatzsoftware zur automatischen Parameteroptimierung, um die Schneidleistung und -qualität zu verbessern.
Bedienerschulung
Herausforderung
Mangelndes Fachwissen oder Geschick des Bedieners können zu Bedienungsfehlern führen, die Ausfallquote erhöhen und die Schneidwirkung beeinträchtigen.
Lösung
- Bieten Sie den Bedienern regelmäßig technische Schulungen an, um sicherzustellen, dass sie die Betriebsspezifikationen der Laserausrüstung beherrschen.
- Stellen Sie ausführliche Bedienungsanleitungen für die Geräte bereit und richten Sie ein technisches Supportteam zur Lösung alltäglicher Probleme ein.
- Implementieren Sie ein Bedienerzertifizierungssystem, um sicherzustellen, dass nur qualifiziertes Personal die Geräte bedienen kann.
Kontinuierliche Verbesserung
Herausforderung
Schnelle Veränderungen in Technologien und Märkten erfordern von Unternehmen eine kontinuierliche Optimierung ihrer Produktionsprozesse und Technologien, um wettbewerbsfähig zu bleiben.
Lösung
- Führen Sie Lean-Production-Konzepte ein, analysieren und optimieren Sie die Produktionsprozesse kontinuierlich, reduzieren Sie Abfall und verbessern Sie die Effizienz.
- Verfolgen Sie die Entwicklungstrends der Laserschneidtechnologie und aktualisieren Sie Geräte und Software umgehend.
- Erfassen Sie Produktionsdaten, analysieren Sie Leistungsindikatoren und verbessern Sie kontinuierlich Schneidparameter und Betriebsabläufe.
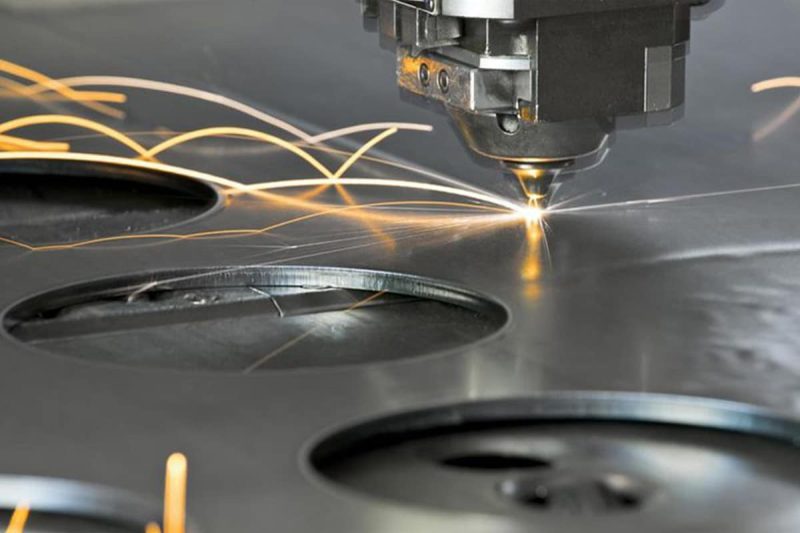
Zusammenfassen
Die Herausforderungen beim Faserlaserschneiden umfassen viele Aspekte, darunter Materialeigenschaften, Geräteleistung, Umgebungsbedingungen usw. Durch regelmäßige Wartung, optimierte Parameter, verbesserte Schulung und den Einsatz fortschrittlicher Technologie können Schnittqualität und Effizienz deutlich verbessert werden. Lösungen sollten von Fall zu Fall implementiert werden, um die Stabilität des Schneidprozesses zu verbessern und Maschinenausfallzeiten und Wartungskosten zu reduzieren.
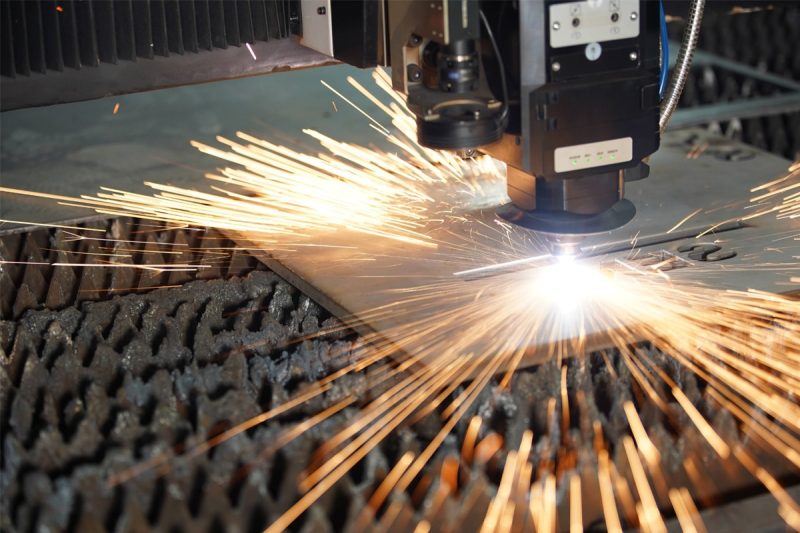
Holen Sie sich Laserlösungen
Die Wahl der richtigen Faserlaserschneidmaschine kann dazu beitragen, den Stromverbrauch zu optimieren und eine hohe Betriebseffizienz zu erreichen. Die Zusammenarbeit mit einem vertrauenswürdigen Lieferanten gewährleistet den Zugang zu fortschrittlicher Technologie, maßgeschneiderter Beratung und kontinuierlicher Unterstützung. Bei AccTek Laser bieten wir ein umfassendes Sortiment an Faserlaserschneidmaschinen an, die auf eine Vielzahl von industriellen Anforderungen zugeschnitten sind. Unsere Experten können Ihnen bei der Auswahl des energieeffizientesten Modells und der energieeffizientesten Konfiguration helfen und dabei Faktoren wie Materialart, Dicke und Produktionsvolumen berücksichtigen. Wir bieten außerdem hochmoderne Funktionen wie hocheffiziente Lasergeneratoren, intelligente Kühlsysteme und Energiemanagementsoftware, um die Leistung zu maximieren und den Energieverbrauch zu minimieren. Darüber hinaus bietet unser Team regelmäßige Wartungsdienste und technischen Support, um Ihre Geräte auf höchstem Niveau zu halten. Durch die Zusammenarbeit mit uns können Sie erhebliche Energieeinsparungen erzielen, Betriebskosten senken und Ihre Nachhaltigkeitsbemühungen verbessern. Wenn Sie Fragen haben, kontaktieren Sie uns bitte rechtzeitig. AccTek Laser ist bestrebt, jedem Kunden perfekte Laserlösungen zu bieten!
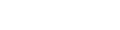
Kontaktinformationen
- [email protected]
- [email protected]
- +86-19963414011
- Nr. 3 Zone A, Industriegebiet Lunzhen, Stadt Yucheng, Provinz Shandong.
Holen Sie sich Laserlösungen