
Wie minimiert CO2-Laserschneiden den Materialabfall?
CO2 laser cutting technology has been widely used in manufacturing, especially in metal processing, plastic cutting, wood engraving, and other fields. Laser cutting is respected for its precision, speed, and flexibility. However, material waste is an issue that cannot be ignored during the cutting process. How to minimize material waste through CO2 laser cutting is not only related to cost control but also directly affects production efficiency and environmental sustainability. This article will explore how to reduce material waste by optimizing laser-cutting processes and technologies.
Inhaltsverzeichnis
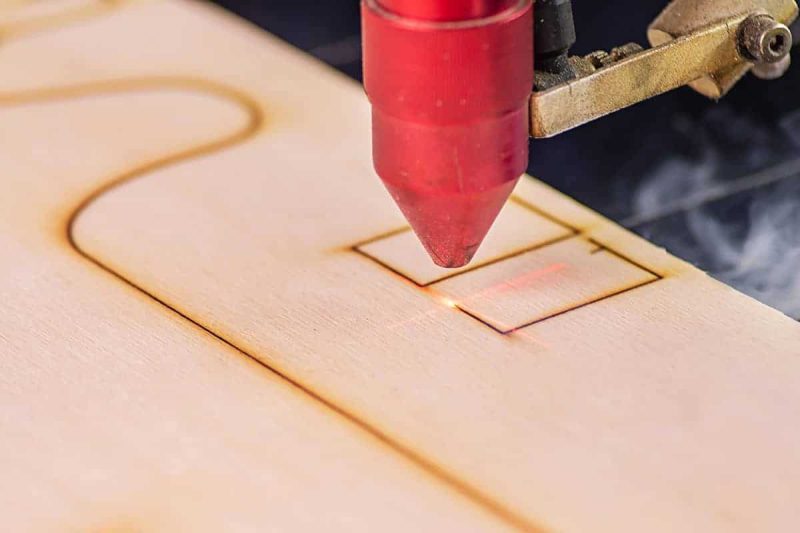
Precise Control of Cutting Parameters
The advantage of CO2 laser cutting is its excellent precision, which can minimize material waste by precisely controlling multiple cutting parameters. The main parameters include laser power, cutting speed, and gas flow. Optimizing these parameters can improve cutting results and increase production efficiency while reducing waste.
Anpassung der Laserleistung
Laser power directly determines the heat input during the cutting process. Excessive power will lead to excessive ablation of the material and irregular edges, resulting in unnecessary waste. Reasonable adjustment of laser power, according to the type and thickness of different materials, can ensure that the laser beam accurately concentrates energy on the cutting area, reduces the thermal impact of the surrounding area, and avoids excessive material loss. Appropriate power settings can also reduce melting and scorching during the cutting process and improve the quality of the cut surface.
Cutting Speed Optimization
Adjusting the cutting speed is crucial to reducing material waste. Too slow a speed will increase heat input, causing overheating of the cut surface, which may result in edge burns or excessive melting, wasting material, and reducing cut quality. Too fast a cutting speed may result in incomplete or irregular cuts, resulting in uncut residual material. Therefore, optimizing the cutting speed to ensure that it adapts to the characteristics and thickness of different materials can effectively reduce unnecessary waste and improve cutting quality.
Gas Flow Control
Gas flow plays a vital role in the CO2 laser cutting process, as it helps cool the cutting area and remove molten metal. Too much gas flow may lead to uneven cutting surface or slag spattering, unstable airflow, and increased waste; while too little gas flow may lead to unsatisfactory cutting effect, unable to effectively blow away molten metal or avoid oxidation. Therefore, by accurately adjusting the gas flow, cutting stability and high-quality cutting effect can be guaranteed, reducing unnecessary material waste.
Through precise control of these cutting parameters, not only can the cutting quality be improved, but also the material utilization efficiency can be effectively optimized, waste can be reduced, and production efficiency can be improved.
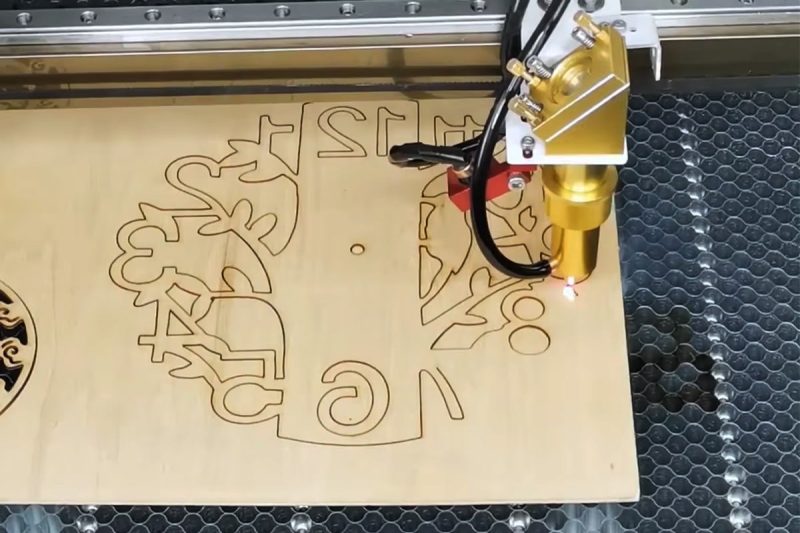
Material Layout Optimization
The importance of material arrangement in CO2 laser cutting is self-evident. Reasonable arrangements can not only improve the efficiency of material use but also reduce waste, and improve cutting accuracy and production efficiency. By optimizing the layout design, it is possible to minimize unused gaps, save materials, and reduce costs. In practical applications, optimizing material arrangement involves many aspects, including part layout, cutting path design, and cutting sequence arrangement.
Efficient Typography Design
Efficient layout design is the key to maximizing material utilization. Using professional layout software can help designers arrange the layout of parts accurately. Through the automatic layout function, designers can calculate the best arrangement of parts in a short time to ensure that waste is minimized as much as possible. When layout, it is very important to plan the cutting path and minimize the gap between parts (i.e. the waste part). Reasonable gap setting can not only reduce material waste but also reduce the subsequent post-processing time and cost.
When designing the layout, the specifications and thickness of the materials must also be considered. Different layout strategies are required for materials of different sizes. For example, for large-sized materials, a reasonable arrangement of the cutting path and direction can not only reduce waste but also avoid material deformation or poor cutting; while for small-sized materials, the layout needs to maximize the use of the cuttable area of each piece of material to avoid waste.
At the same time, the software can also simulate the cutting process and calculate the best cutting sequence to ensure that each part is cut in the right place, reducing unnecessary gaps and waste and improving production efficiency. For example, during the cutting process, avoiding too many blank areas can ensure that every piece of material is fully utilized.
Avoid Redundant Cutting
Redundant cutting refers to multiple cutting or unnecessary repeated cutting due to unreasonable design or improper cutting path planning. Redundant cutting not only wastes materials but also increases production time and reduces work efficiency. In the laser cutting process, it is crucial to avoid repeated cutting or meaningless paths as much as possible to improve material utilization.
Reasonable planning of cutting paths can ensure that each part can achieve the expected effect when cut for the first time, without generating additional waste due to subsequent adjustment of the path or supplementary cutting. Especially in mass production, avoiding redundant cutting is particularly important for improving production efficiency and saving materials. For example, using optimization software to determine the cutting sequence and ensure that the cutting path of each part is as short as possible and without intersection can greatly reduce the occurrence of redundant cutting.
At the same time, avoiding too many cutting pauses, moves, or repeated work during the cutting process can reduce unnecessary energy consumption and time waste, and improve overall production efficiency. By rationally planning the cutting sequence and path, it can ensure that each cutting action is necessary, thereby effectively avoiding redundant cutting and material waste.
Intelligent Typesetting and Process Collaboration
With the continuous advancement of laser cutting technology, more and more intelligent layout software can work with the production line to adjust the layout design in real time to meet different material requirements. Through data analysis and machine learning, intelligent layout can optimize the cutting path and layout based on historical data and real-time feedback, not only considering the size and shape of the material but also making optimal adjustments based on process requirements. This intelligent layout method greatly improves the utilization of materials and reduces the need for manual intervention.
For example, the intelligent system can automatically adjust the cutting path and sequence during the production process, dynamically adjust according to the characteristics of different materials and the production rhythm, and optimize the layout and cutting path in real time to minimize waste. This technology can make the production process more efficient and intelligent, significantly reduce material waste, and improve cutting accuracy.
Optimizing material layout is a key factor in improving material utilization and reducing waste during CO2 laser cutting. Through efficient layout design, avoiding redundant cutting, and intelligent layout technology, unnecessary waste can be effectively reduced, production efficiency can be improved and costs can be reduced. A reasonable layout can not only optimize material use but also improve cutting quality, ensuring that each cutting process is efficient and accurate. In modern manufacturing, optimizing material layout has become an important strategy to improve production efficiency and reduce waste.
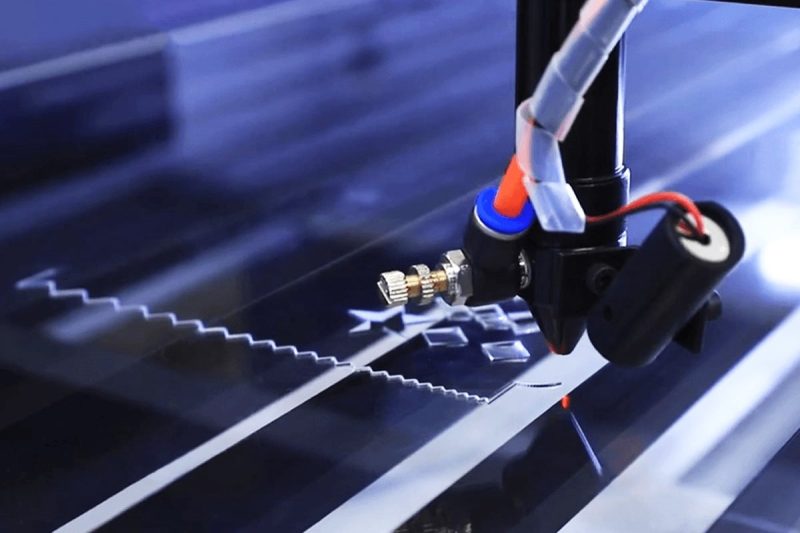
Use High Quality Laser Cutting Machine
The performance and technology of the equipment directly affect the cutting accuracy and material waste. In order to achieve the goal of high efficiency and low waste in the CO2 laser cutting process, it is very important to choose a high-quality laser cutting machine. High-quality laser cutting machines are not only equipped with advanced beam control technology and precise focus adjustment systems but also have stable performance and efficient cutting capabilities, which can ensure cutting accuracy while minimizing material waste.
Precision Beam Control
Modern high-end CO2 laser cutting machines are equipped with sophisticated beam control technology to ensure that the laser beam is always focused on the cutting area of the material. This technology includes high-precision adjustment of the laser beam and a focus control system that can accurately focus the laser energy on the material surface, resulting in a smaller heat-affected zone and cleaner cut edges. Reducing the heat-affected zone and scorching not only helps improve cutting quality but also reduces unnecessary material waste.
Precise control of the beam is the basis for ensuring high-quality cutting. When the laser focus position is accurate, the energy of the laser beam can be concentrated and transferred to the material, avoiding excessive energy scattering to the surrounding area, thereby reducing heat loss and unnecessary material loss. In addition, precise beam control can also keep the cutting surface flat and defect-free when cutting complex shapes and fine details, thereby avoiding material waste.
Automatic Adjustment System
Advanced CO2 laser cutting machines are equipped with an automatic adjustment system that can automatically adjust laser power, gas flow, cutting speed, and other parameters based on real-time feedback data to ensure that each cutting path is in the best condition. This automatic adjustment function plays an important role in the cutting process and can optimize cutting parameters in real time under different materials and cutting conditions to avoid instability caused by improper human operation or environmental changes.
For example, the automatic adjustment of laser power and gas flow can be dynamically optimized according to the thickness and type of the material, ensuring moderate heat input during the cutting process and reducing material ablation and deformation caused by excessive heat input. At the same time, the automatic adjustment of cutting speed can be adjusted according to the characteristics of the material and the complexity of cutting, thereby ensuring the continuity and quality of the cutting path. Through this efficient real-time monitoring and adjustment, the Laser-Schneide-Maschine can not only improve production efficiency but also significantly reduce unnecessary waste.
In addition, the automatic adjustment system can also make corrections based on real-time feedback data during the cutting process, correcting any errors caused by changes in workpiece position, material properties, or equipment accuracy, thereby maintaining stable cutting quality and minimal material waste. This real-time adjustment function greatly reduces waste caused by human errors or technological lags, ensuring that each cut is performed in the best condition.
Multi-Axis Cutting Technology
Many high-end CO2 laser cutting machines are also equipped with multi-axis cutting technology, which can achieve more complex and precise cutting paths. Multi-axis technology can cut in multiple directions at the same time, which not only improves cutting efficiency but also reduces material waste. For example, some cutting machines can adjust the position of the laser head to more accurately adjust the cutting angle and path, so that each cutting path minimizes gaps and reduces the generation of useless waste.
Multi-axis technology enables laser cutting machines to perform more flexible path planning during the cutting process, especially when cutting complex parts, which can effectively avoid excessive waste due to improper path planning. In addition, multi-axis cutting technology can also reduce the occurrence of repeated cutting and redundant paths, thereby further reducing material waste and production costs.
Laser Wavelength and Focusing Technology
Different CO2 laser-cutting machines may use laser beams of different wavelengths, and the choice of laser wavelength has an important impact on cutting accuracy and efficiency. CO2 laser generators usually use lasers with a wavelength of 10.6 microns, which has a very high absorption rate when cutting metals and some non-metallic materials, so it can effectively improve the cutting effect. High-quality CO2 laser cutting machines are equipped with advanced optical systems to ensure that the laser beam can be focused on the surface of the material and achieve high-precision cutting.
By finely controlling the laser wavelength and beam focus, CO2 laser cutting machines can achieve efficient and high-quality cutting results in cutting different materials. Higher beam quality means better concentration of laser energy, thereby reducing energy scattering and waste, ensuring that materials are used more efficiently.
Choosing a high-quality CO2-Laserschneidmaschine is the key to achieving efficient cutting and reducing material waste. The comprehensive application of precision beam control, automatic adjustment system, multi-axis cutting technology, laser wavelength, and focusing technology can not only improve cutting accuracy but also significantly reduce the heat-affected zone, and reduce material ablation and waste. With the continuous development of laser-cutting technology, modern laser-cutting machines have been able to achieve efficient and precise cutting, thereby significantly improving material utilization and reducing production costs while ensuring cutting quality.
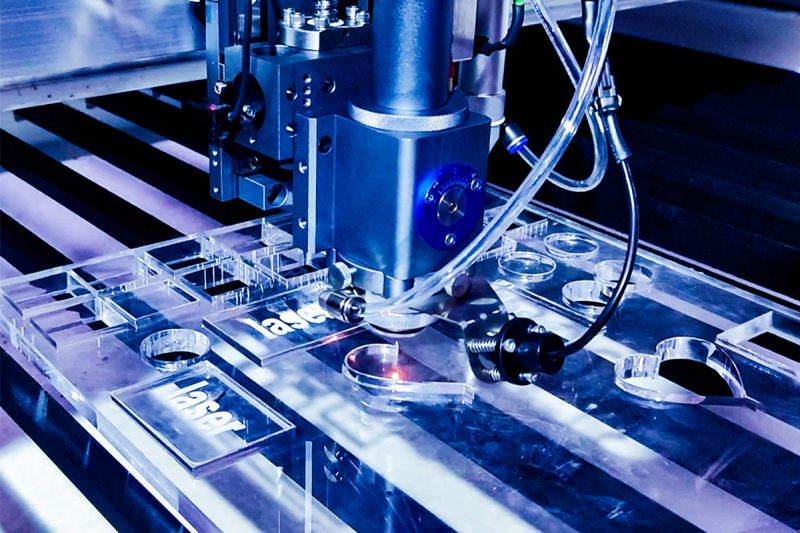
Reasonable Selection of Cutting Materials
Choosing the right cutting material is crucial to reducing material waste during CO2 laser cutting. CO2 laser cutting machines are mainly used for cutting non-metallic materials, especially some thermoplastics, wood, paper, and fabric. The absorptivity, thermal conductivity, reflectivity, and other characteristics of different materials during laser cutting have a direct impact on the cutting effect and material waste. Therefore, choosing the right cutting material is an important step to improve efficiency and reduce waste.
Applicable Material Selection
The advantage of the CO2 laser cutting machine lies in its high efficiency in cutting non-metallic materials. When choosing cutting materials, the material’s absorbance and reflectivity are crucial. For CO2 laser cutting machines, choosing materials that have high absorption of CO2 laser wavelength can help improve cutting efficiency and reduce waste.
- Paper and cardboard: Paper and cardboard have a high absorption rate for CO2 lasers, which can maintain high efficiency and reduce waste during cutting. These materials are often used in packaging, advertising, and design fields.
- Plastics (such as acrylic, PVC): CO2 lasers have a good cutting effect on thermoplastics (such as acrylic, PVC, etc.), and can accurately control the cutting edge to avoid unnecessary heat-affected zones and material waste.
- Wood and composite materials: CO2 laser cutting machines are also widely used for cutting wood and composite materials. These materials absorb CO2 lasers well, which can achieve clean cutting, reduce scorching and heat damage, and ensure maximum material utilization.
Wählen Sie die richtige Materialstärke
In addition to the type of material, the thickness of the material also affects the effect of CO2 laser cutting. For thinner materials, too high laser power may cause excessive heat input, resulting in excessive heat-affected zones, causing excessive ablation and waste of materials. Conversely, for thicker materials, too low laser power may result in incomplete cutting.
- Thin materials: When cutting thin materials, avoid excessive laser power or slow cutting speeds. Set power and speed appropriately to avoid excessive burning and waste.
- Thicker materials: Thicker materials require higher laser power to ensure a complete cut, but still avoid excessive power that causes heat loss or irregular edges.
Relationship Between Thermal Conductivity and Laser Cutting
The thermal conductivity of different materials also has a significant impact on the effectiveness of laser cutting. Materials with high thermal conductivity (such as metals) will quickly conduct heat away from the cutting area, which may result in incomplete cutting or excessive heat-affected zones, increasing material waste. In contrast, materials with lower thermal conductivity (such as wood and plastic) help to concentrate heat, thereby improving cutting results and reducing waste.
In CO2 laser cutting, common non-metallic materials such as plastics and wood have low thermal conductivity, which helps to effectively utilize laser energy and reduce the heat-affected zone during the cutting process.
The Influence of Material Surface Treatment on Cutting Effect
The surface treatment of materials is also crucial in CO2 laser cutting. For non-metallic materials, surface dirt, grease, oxide layer, etc. will reduce the absorption efficiency of the laser, resulting in energy waste. Therefore, before laser cutting, ensuring that the surface of the material is clean and pollution-free can effectively improve cutting efficiency and reduce waste.
For example, clean plastic or wood surfaces absorb laser energy more efficiently, resulting in more efficient cutting and less waste. If the material surface contains oil or impurities, the absorption rate of laser energy will be reduced, the cutting effect will be poor, and waste will be generated.
For CO2 laser cutting machines, it is very important to choose the right non-metallic material and material thickness. During the cutting process, the material’s absorption rate, thermal conductivity, and surface treatment status will directly affect the efficiency of laser energy utilization, thereby affecting material waste. Reasonable selection of suitable materials and adjustment of cutting parameters can not only improve cutting efficiency but also minimize material waste and reduce production costs. By optimizing material selection and cutting settings, companies can achieve higher material utilization while ensuring cutting quality.
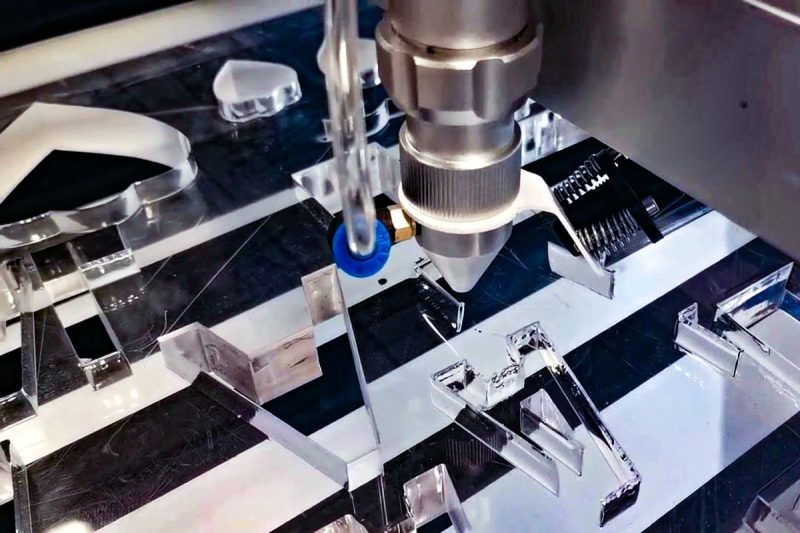
Maintain and Optimize Equipment Performance
Maintaining the good performance of the laser cutting machine is a key factor in ensuring cutting accuracy, improving production efficiency, and reducing material waste. Regular equipment maintenance can not only extend the service life of the laser cutting machine but also ensure the stability of the equipment during the cutting process, thereby effectively reducing waste caused by equipment failure or performance degradation. In order to maximize equipment performance, the laser cutting machine requires a series of regular inspections, maintenance, and optimization. Here are some key maintenance steps and suggestions:
Check the Optics Regularly
Optical components, such as laser heads, reflectors, and lenses, directly affect the focusing quality of the laser beam and the cutting accuracy. As time goes by, these optical components may be damaged or degraded due to dust, contaminants, or high temperatures, which will affect the quality of laser cutting. To ensure the best performance of the laser cutting machine, it is necessary to regularly check and clean the optical components. The specific operations are as follows:
- Clean the optical components: Use a dust-free cloth and professional cleaning fluid to clean the lens and lens regularly. Avoid using rough materials to avoid scratching the surface of the optical components. Keeping the lens and lens clean can ensure the focusing quality of the laser beam and reduce energy loss.
- Check the optical alignment: The alignment of the laser head, reflector, and lens directly affects the path and focal position of the laser beam. Regularly checking the alignment of the optical components to ensure that the laser beam is accurately focused on the cutting area will help improve the cutting quality and reduce waste.
Laser Head Maintenance and Cleaning
The laser head is one of the core components of the laser cutting machine, responsible for focusing the laser beam onto the material. Over time, the laser head may be contaminated or worn, resulting in inaccurate laser focusing and affecting the cutting effect. Therefore, regular cleaning and maintenance of the laser head is essential. When cleaning, avoid scratching or damaging the surface of the laser head to avoid secondary damage. When cleaning, pay special attention to the following points:
- Check the optical components of the laser head: The lenses and mirrors inside the laser head need to be checked regularly to ensure that there are no stains, scratches, or other defects. If damaged or contaminated, they should be replaced immediately.
- Check the cooling system: The laser head is usually equipped with a cooling system to ensure that the laser head works stably at high temperatures. Check the coolant and heat dissipation system regularly to ensure that they are operating properly to avoid degradation of the laser head performance due to overheating.
Calibrating and Optimizing Laser Cutting Parameters
The performance of a laser cutting machine depends not only on the quality of the hardware but also on its cutting parameters. Over time, the working state and cutting performance of the equipment may change, so the laser cutting machine needs to be calibrated and optimized regularly. Depending on the material, parameters such as laser power, cutting speed, gas flow ,and focus position may need to be adjusted. Ensuring that the parameter settings of the laser cutting machine are always in the best state can greatly reduce material waste during the cutting process.
- Regularly calibrate laser power and cutting speed: In the laser cutting process, power and cutting speed are key factors affecting cutting results and material waste. Regularly calibrate the equipment to ensure that the laser power and cutting speed are always in the optimal working range to avoid excessive heat input or incomplete cutting.
- Optimize the focal position and beam quality: The position of the laser focal point and the quality of the beam directly determine the accuracy and effect of the cutting. By calibrating the focal position, ensure that the energy of the laser beam is concentrated in the cutting area, effectively improve the cutting accuracy, and reduce the waste caused by inaccurate cutting.
Check Gas Flow and Cooling System Regularly
The auxiliary gas flow rate is crucial to the stability of the laser cutting process. Too high or too low a gas flow rate may affect the cutting quality and increase material waste. Therefore, regular inspection and optimization of the gas flow rate is a necessary measure to keep the laser cutting machine running efficiently. The stability of the gas flow rate has a direct impact on the cutting effect, the quality of the cutting edge, and the degree of material waste.
In addition, the maintenance of the cooling system cannot be ignored. The laser source and optical components of the laser cutting machine need to operate within the appropriate temperature range to avoid overheating or insufficient cooling that may cause equipment damage. Ensuring the normal operation of the cooling system can not only extend the life of the equipment but also improve cutting accuracy and reduce waste caused by equipment failure.
Equipment Failure Prevention and Timely Repair
Equipment failure is one of the main causes of problems in the laser cutting process. To avoid production interruptions and material waste caused by equipment failure, regular equipment inspection and fault prevention are essential. Regular inspections of mechanical parts, electrical systems, laser sources, etc. to ensure that they are in good working condition can effectively prevent equipment failure. In addition, when problems are found, repairs and replacement of damaged parts should be carried out promptly to avoid low production efficiency or material waste due to equipment failure.
Regular equipment maintenance and optimization not only helps to extend the service life of the laser cutting machine but also ensures that the equipment is always in the best working condition, thereby improving cutting accuracy, stability, and material utilization. By checking and cleaning optical components, calibrating cutting parameters, optimizing gas flow and cooling systems, etc., the waste caused by the decline of equipment performance can be greatly reduced. In addition, timely maintenance and fault prevention are also important means to ensure the continuous and efficient operation of equipment. Through comprehensive management and optimization of equipment performance, the laser cutting machine can maintain efficient operation for a long time, minimize material waste, and improve production efficiency.
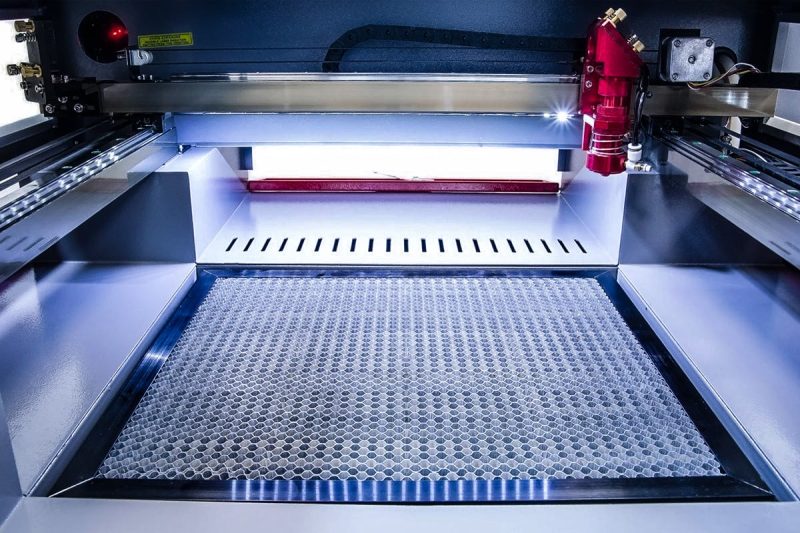
Zusammenfassen
CO2 laser cutting is an efficient and precise cutting technology, but in practical applications, material waste is still an important issue. By precisely controlling cutting parameters, optimizing material arrangement, and selecting appropriate equipment and materials, material waste can be minimized, production efficiency can be improved, and costs can be reduced. With the continuous development of laser technology and the improvement of equipment performance, CO2 laser cutting in the future will be more environmentally friendly and economical and will bring more sustainable development opportunities to the manufacturing industry.
In this regard, AccTek-Laser CO2 laser cutting machine, with its excellent technology, precise control system, and efficient cutting capabilities, can provide customers with more efficient and environmentally friendly cutting solutions, helping companies to minimize material waste and improve production efficiency and cost-effectiveness. If you need a CO2 laser cutting machine, please contact us immediately for a quote.
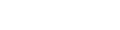
Kontaktinformationen
- [email protected]
- [email protected]
- +86-19963414011
- Nr. 3 Zone A, Industriegebiet Lunzhen, Stadt Yucheng, Provinz Shandong.
Holen Sie sich Laserlösungen