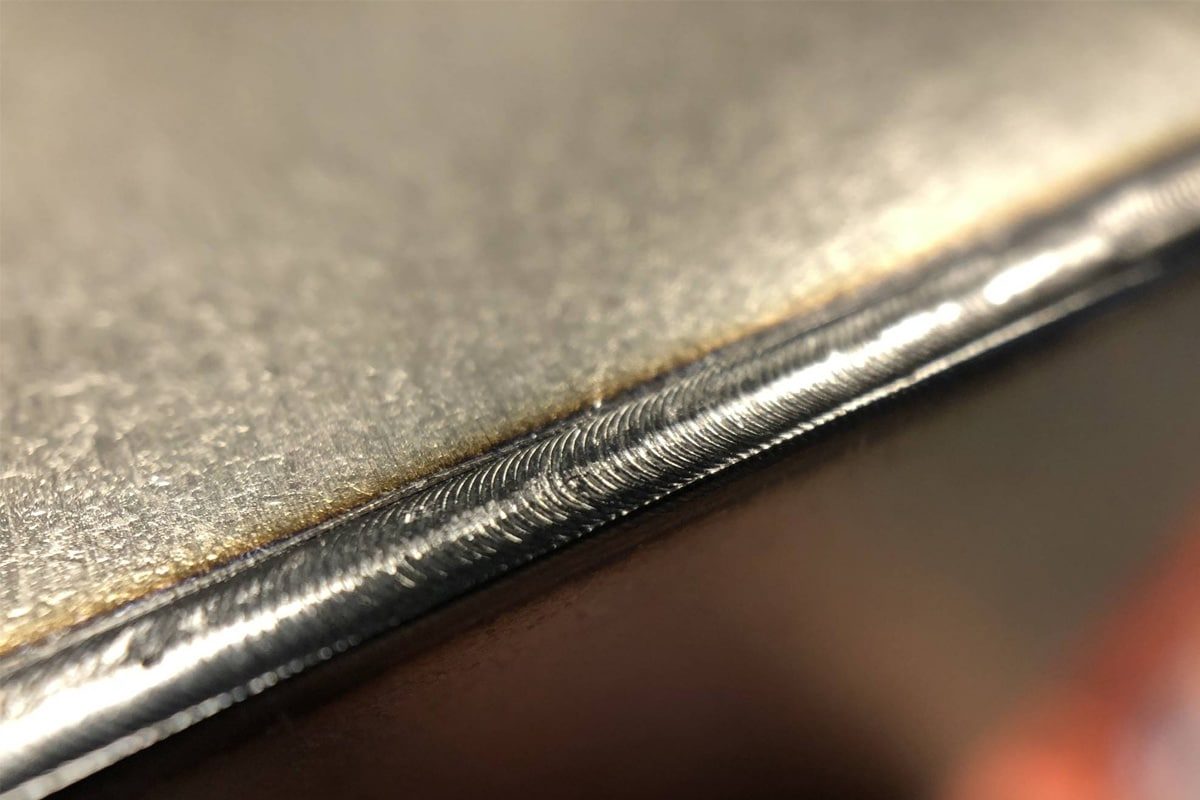
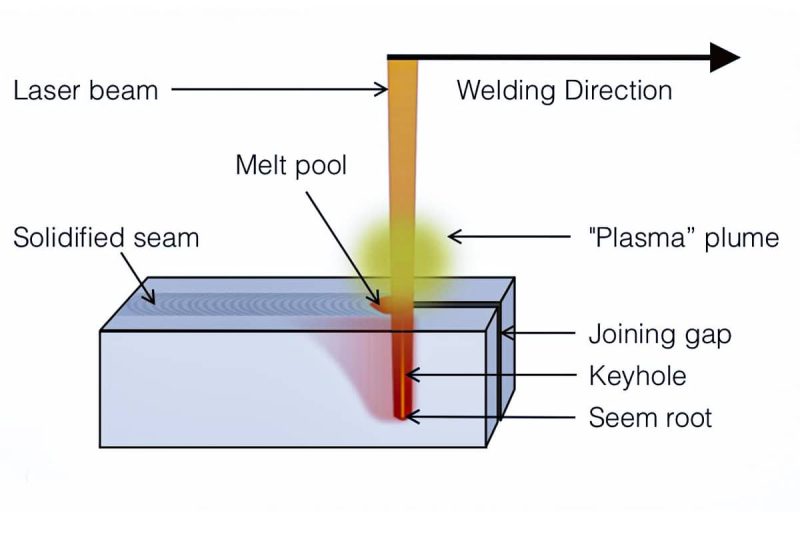
Laserschweißen verstehen
Grundlagen des Laserschweißens
Laserschweißtyp
- Dauerstrich-Laserschweißen: geeignet für langfristige, hochintensive Schweißanforderungen, wird häufig zum Verbinden und Abdichten dicker Metallplatten verwendet.
- Pulslaserschweißen: erhitzt das Material durch kurzzeitige Hochenergieimpulse, besser geeignet zum Schweißen dünner Platten oder Mikrokomponenten, mit höherer Steuergenauigkeit.
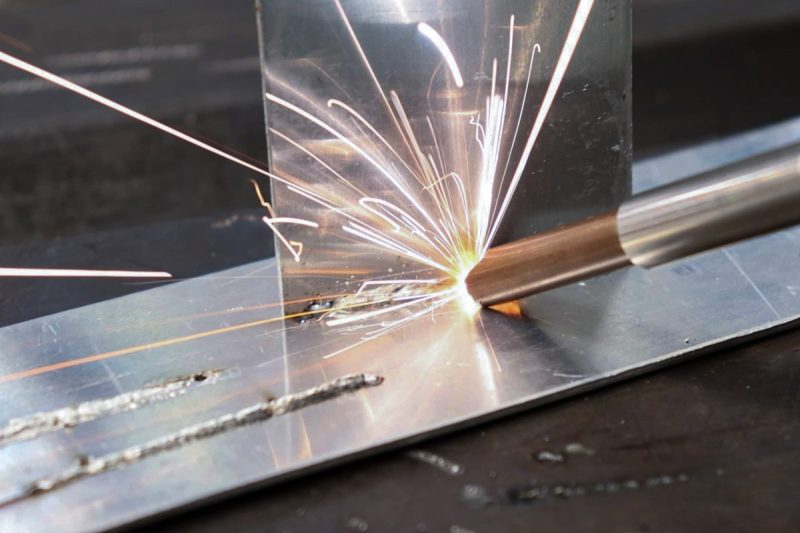
Faktoren, die die Schweißnahtbreite beeinflussen
Laserparameter
- Laserleistung: Die Laserleistung ist einer der entscheidendsten Parameter, die das Schweißergebnis beeinflussen. Je höher die Laserleistung, desto mehr Wärme wird erzeugt und desto größer wird auch das Volumen der Wärmeeinflusszone und des Schmelzbades, was wiederum die Schweißnahtbreite vergrößert. Umgekehrt kann bei zu geringer Leistung nicht genügend Energie zum Schmelzen des Materials bereitgestellt werden, und die Schweißnaht kann unzureichend sein, was zu einer schmalen Schweißnaht oder einer unvollständigen Schweißnaht führt. Daher muss die Laserleistung entsprechend der Dicke, Art und Schweißgeschwindigkeit des Materials angemessen ausgewählt werden, um die optimale Breite der Schweißnaht zu erreichen.
- Schweißgeschwindigkeit: Die Schweißgeschwindigkeit hat einen wichtigen Einfluss auf die Wärmezufuhr. Bei niedriger Schweißgeschwindigkeit bleibt der Laser länger im Schweißbereich, was zu einer stärkeren Wärmeübertragung auf das Grundmaterial führt, wodurch ein größeres Schmelzbad und eine größere Wärmeeinflusszone entstehen und die Schweißnahtbreite vergrößert wird. Umgekehrt verringert eine zu hohe Schweißgeschwindigkeit die Wärmezufuhr, was zu unvollständigem Schweißen, zu schmalen Schweißnähten und möglicherweise schwachen Schweißnähten führt. Daher ist eine angemessene Kontrolle der Schweißgeschwindigkeit der Schlüssel zur Gewährleistung der geeigneten Schweißnahtbreite.
- Wellenlänge: Die Wellenlänge des Lasers bestimmt, wie der Laser mit dem Material interagiert. Kurzwellige Laser (wie sie beispielsweise von Faserlasergeneratoren emittiert werden) können von Metallmaterialien besser absorbiert werden, da sie eine höhere Energiekonzentration aufweisen und mehr Energie auf einer kleineren Fläche bereitstellen können, wodurch die Schweißeffizienz verbessert und die Schweißnaht schmaler wird. Langwellige Laser (wie sie beispielsweise von CO2-Laserröhren emittiert werden) absorbieren Metallmaterialien relativ schlecht und die Energieverteilung beim Schweißen ist relativ breit, was leicht zu einer größeren Schweißnahtbreite führt. Daher eignen sich kurzwellige Laser besser für hochpräzises Schweißen.
- Pulsdauer: Das gepulste Laserschweißen bietet den einzigartigen Vorteil, dass das Schweißen durch Anpassen der Pulsdauer optimiert werden kann. Je kürzer die Pulsdauer, desto kürzer ist die Wärmezufuhrzeit des Lasers, was dazu beiträgt, die Ausdehnung der Wärmeeinflusszone zu verringern und eine kleinere Schweißnaht zu bilden. Längere Pulsdauern führen zu mehr Wärmezufuhr und einer breiteren Schweißnaht. Durch die Pulsformungstechnologie können die Pulsbreite und das Intervall des Lasers präzise gesteuert werden, um die Wärmeverteilung und die Schweißmorphologie während des Schweißens zu optimieren.
- Strahlqualität: Die Qualität und Fokussteuerung des Laserstrahls sind entscheidend für die Schweißgenauigkeit. Laser mit besserer Strahlqualität haben kleinere Fokusgrößen und konzentriertere Energie, wodurch ein präziseres Schweißen erreicht werden kann. Eine höhere Strahlqualität trägt dazu bei, die Wärmediffusion zu reduzieren, sodass die Wärme stärker im Schweißbereich konzentriert ist und die Schweißnahtbreite kleiner wird. Wenn die Strahlqualität schlecht ist, führt dies zu einer ungleichmäßigen Verteilung der Laserenergie, wodurch die Schweißnahtbreite zunimmt.
Materialeigenschaften
- Absorptionsrate: Die Absorptionsrate des Materials gegenüber dem Laser wirkt sich direkt auf die Schweißwirkung aus. Die Absorptionsrate von Metallmaterialien ist normalerweise hoch, insbesondere wenn der kurzwellige Laser mit dem Metall kombiniert wird, wird die Absorptionsrate weiter verbessert. Beim Laserschweißen bedeutet eine höhere Absorptionsrate, dass die Laserenergie effektiv in Wärmeenergie umgewandelt werden kann, was zu einer kleineren Schweißnaht führt. Umgekehrt ist bei einer niedrigen Absorptionsrate des Materials die effektive Nutzungsrate der Laserenergie schlecht, was dazu führen kann, dass die Schweißnaht zu breit oder unvollständig ist.
- Wärmeleitfähigkeit: Die Wärmeleitfähigkeit des Materials beeinflusst die Diffusionsrate der Wärme im Substrat. Materialien mit höherer Wärmeleitfähigkeit (wie Kupfer und Aluminium) wird die Wärme schnell ableiten, was zu einer übermäßigen Wärmeableitung im Schweißbereich und breiteren Schweißnähten führt. Im Gegensatz dazu Materialien mit geringerer Wärmeleitfähigkeit (wie Edelstahl) kann mehr Wärme im Schweißbereich konzentrieren und eine schmalere Schweißnaht bilden. Daher ist es beim Schweißen von Materialien mit unterschiedlicher Wärmeleitfähigkeit erforderlich, die Schweißparameter entsprechend ihren thermischen Eigenschaften anzupassen, um sicherzustellen, dass die Schweißnahtbreite angemessen ist.
- Reflektivität: Materialien mit hoher Reflektivität (wie Aluminium und Kupfer) erzeugen eine stärkere Reflexion des Lasers und verringern die Absorptionseffizienz der Laserenergie, was sich auf die Schweißqualität auswirkt und dazu führen kann, dass die Schweißnahtbreite zunimmt. Um dieses Problem zu lösen, können Sie einen Lasertyp wählen, der für stark reflektierende Materialien geeignet ist (z. B. einen Laser mit kurzer Wellenlänge), oder die Laserleistung erhöhen, um den Reflexionsverlust auszugleichen. Darüber hinaus kann die Verwendung eines fokussierten Strahls und einer geeigneten Laserwellenlänge auch dazu beitragen, die Laserabsorptionsrate reflektierender Materialien zu erhöhen.
Schweißumgebung
- Schutzgas: Schutzgas spielt beim Laserschweißen eine wichtige Rolle. Es verhindert nicht nur Oxidation und Verunreinigung während des Schweißens, sondern beeinflusst auch die Wärmeleitung und die Schweißnahtbreite, indem es den Gasfluss steuert. Beispielsweise werden beim Laserschweißen häufig Argon und Stickstoff als Schutzgase verwendet. Sie können den Bereich der Wärmeeinflusszone effektiv reduzieren und die Entstehung übermäßiger Schweißnähte vermeiden. Die Auswahl und Steuerung des Schutzgases muss entsprechend den spezifischen Materialien und Schweißanforderungen angepasst werden.
- Umgebungsbedingungen: Umgebungsfaktoren wie Temperatur und Luftfeuchtigkeit haben ebenfalls einen gewissen Einfluss auf die Wirkung des Laserschweißens. In Umgebungen mit niedrigen Temperaturen kann sich die Wärmeleitfähigkeit von Metallmaterialien ändern, was sich auf das Wärmemanagement während des Schweißens auswirkt. Darüber hinaus kann eine Umgebung mit hoher Luftfeuchtigkeit zu einer Streuung der Laserenergie führen und die Schweißqualität beeinträchtigen. Stabile Umgebungsbedingungen tragen dazu bei, die Stabilität des Laserstrahls aufrechtzuerhalten und die Konsistenz der Schweißnahtbreite während des Schweißens sicherzustellen.
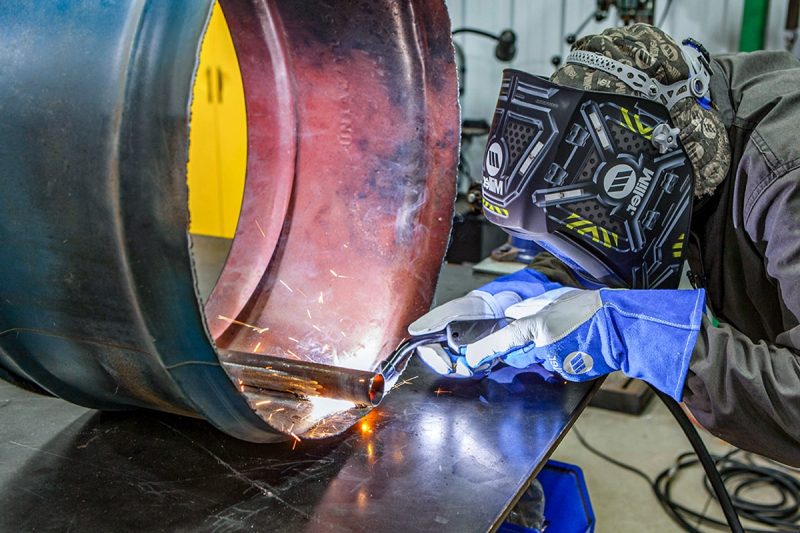
Technologie zur Erzielung minimaler Schweißnahtbreiten
Auswahl des Lasertyps
- Faserlasergenerator: Der Faserlasergenerator ist eine der am häufigsten verwendeten Laserquellen beim Laserschweißen. Er verfügt über hohe Leistung, hohe Strahlqualität und hervorragende Fokussierfähigkeit. Der Strahl des Faserlasergenerators kann präzise auf einen sehr kleinen Bereich fokussiert werden, wodurch die Schweißnahtbreite kleiner wird und dünne Plattenmaterialien effizient bearbeitet werden können. Faserlasergeneratoren eignen sich sehr gut für hochpräzise und schnelle Schweißaufgaben und können hochwertige kleine Schweißnähte erzielen und die Ausdehnung der Wärmeeinflusszone (WEZ) des Materials verringern.
- CO2-Laserröhre: Eine weitere Laserquelle, die häufig zum Metallschweißen verwendet wird, ist die CO2-Laserröhre. Obwohl die Strahlqualität von CO2-Laserröhren im Allgemeinen nicht so gut ist wie die von Faserlasergeneratoren, kann sie eine höhere Leistung und eine größere Eindringtiefe bieten, was zum Schweißen dickerer Materialien geeignet ist. Obwohl sie nicht so genau ist wie ein Faserlaser, können durch eine angemessene Leistungsregulierung und eine optimierte Schweißgeschwindigkeit relativ kleine Schweißbreiten erreicht werden.
Auswahl der Laserwellenlänge
Optimierung der Laserparameter
- Anpassung der Laserleistung: Die Laserleistung ist der Hauptfaktor, der die Wärmezufuhr beim Schweißen beeinflusst. Übermäßige Leistung führt dazu, dass sich übermäßige Wärme in die Umgebung ausbreitet, wodurch die Schweißnaht breiter wird und sogar Schweißfehler entstehen. Eine angemessene Reduzierung der Leistung kann dazu beitragen, die Wärmezufuhr zu reduzieren und die Schweißnahtbreite zu verringern, insbesondere beim Schweißen dünner Plattenmaterialien. Eine zu geringe Leistung kann jedoch zu unzureichendem Schweißen führen. Daher kann eine angemessene Anpassung der Laserleistung an Materialeigenschaften, Schweißgeschwindigkeit und Schweißanforderungen ein präzises Schweißen erreichen und die Schweißnahtbreite effektiv steuern.
- Pulsformungstechnologie: Die Pulslaserschweißtechnologie kann die Wärmezufuhr während des Schweißens durch Anpassen der Frequenz, Dauer und Energie des Laserpulses genau steuern. Je kürzer die Pulsbreite, desto kürzer die Wärmezufuhrzeit und desto geringer die Wärmeansammlung im Schweißbereich, wodurch die Schweißnaht schmaler wird. Darüber hinaus können durch Anpassen der Pulsfrequenz und -energie die Schweißgeschwindigkeit und die Morphologie des Schmelzbades gesteuert werden, was wiederum die Breite der Schweißnaht beeinflusst. Durch den Einsatz der Pulsformungstechnologie, insbesondere beim Mikroschweißen, kann die Wärmeverteilung jedes Pulses genau gesteuert werden, um effektiv die minimale Schweißnahtbreite zu erreichen.
- Strahlfokussteuerung: Die Genauigkeit und Schweißbreite beim Laserschweißen hängt eng mit der Fokusposition des Strahls zusammen. Je kleiner der Laserstrahlfokus ist, desto höher ist die Energiedichte, die im Schweißbereich konzentriert werden kann, wodurch eine schmale und feine Schweißnaht entsteht. Daher ist die Laserfokussteuerung sehr wichtig. Durch Anpassen der Fokusposition kann die Energie des Laserstrahls stärker im Schweißbereich konzentriert werden, wodurch eine Wärmediffusion in die Umgebung vermieden und dadurch die Breite der Schweißnaht verringert wird.
Material vorbereitung
- Oberflächenreinheit: Die Oberflächenreinheit des Schweißmaterials wirkt sich direkt auf die Wirkung des Laserschweißens aus. Oxide, Öl, Rost und andere Verunreinigungen auf der Oberfläche beeinträchtigen die Absorptionsrate des Lasers, wodurch die Wärme nicht effektiv im Schweißbereich konzentriert werden kann, was wiederum die Schweißqualität beeinträchtigt und die Schweißbreite erhöht. Die Gewährleistung einer sauberen und verunreinigungsfreien Schweißoberfläche ist eine Voraussetzung für die Optimierung der Schweißqualität. Oberflächenverunreinigungen können normalerweise durch chemische Reinigung, mechanische Reinigung oder Laserreinigung entfernt werden.
- Oberflächenbeschichtung: In einigen Fällen, insbesondere bei schwer schweißbaren Materialien, kann eine Oberflächenbeschichtung die Absorptionseffizienz des Lasers erheblich verbessern. Beschichtungsmaterialien (wie Kupferbeschichtung, Verzinkung usw.) können die Wechselwirkung zwischen dem Laser und dem Material verbessern und die Wärmeansammlung im Schweißbereich erhöhen, wodurch die Schweißnahtbreite während des Schweißvorgangs genau gesteuert werden kann. Darüber hinaus können spezielle Beschichtungen auch die Stabilität des Schmelzbades während des Schweißens verbessern und Fehler während des Schweißens reduzieren.
Fortschrittliche Schweißtechnologie
- Hybrid-Laserschweißen: Die Hybrid-Laserschweißtechnologie kombiniert die Vorteile von Laser- und herkömmlichen Schweißverfahren (wie WIG-Schweißen oder MIG-Schweißen) und verbessert die Wärmezufuhr und Schweißgenauigkeit durch die Kombination der Vorteile verschiedener Wärmequellen. Die Kombination von Laser- und herkömmlichen Schweißverfahren kann die Schweißnahtbreite effektiv reduzieren, insbesondere beim Schweißen dickerer Materialien. Die Hybrid-Laserschweißtechnologie kann eine höhere Stabilität des Schmelzbads und kleinere Wärmeeinflusszonen bieten und dadurch verfeinerte Schweißeffekte erzielen.
- Mikroschweißtechnologie: Mikrolaserschweißen ist eine hochpräzise Schweißtechnologie zur Verarbeitung ultrakleiner Schweißnähte, die sich besonders zum Verbinden kleiner Teile eignet. Die Mikroschweißtechnologie verwendet fein gesteuerte Laserimpulse, um eine effiziente Energieübertragung in einem sehr kleinen Schweißbereich zu erreichen und so die Bildung sehr schmaler Schweißnähte zu gewährleisten. Mikroschweißen wird häufig in Branchen wie der Elektronik, Präzisionsinstrumenten und medizinischen Geräten verwendet und kann eine hohe Schweißgenauigkeit erreichen und die thermische Auswirkung des Schweißbereichs minimieren.
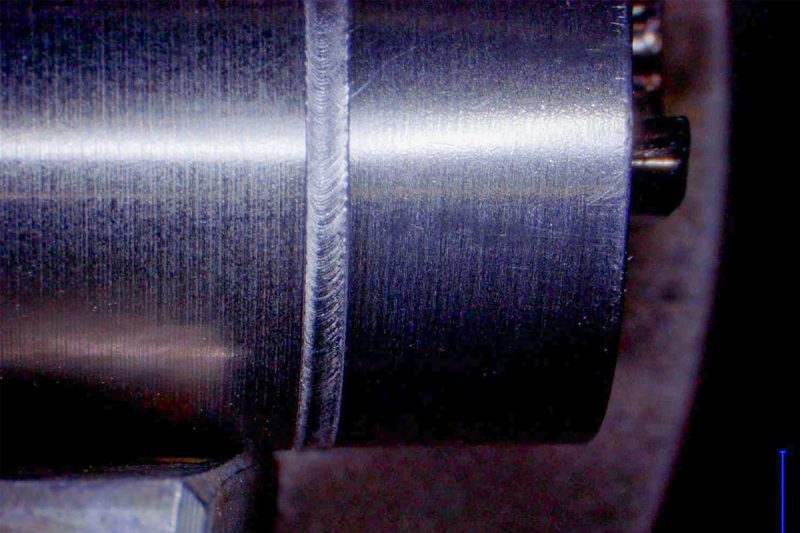
Herausforderungen und Lösungen
Wärmemanagement
Herausforderung
Lösung
- Verwenden Sie eine Hilfsgaskühlung: Die Verwendung eines geeigneten Schutzgases oder Hilfsgases (wie Argon, Stickstoff oder Sauerstoff) kann nicht nur die Oxidation des Schweißbereichs verhindern, sondern auch die beim Schweißen entstehende überschüssige Wärme effektiv abführen und so die Ausdehnung der Wärmeeinflusszone verringern. Die Durchflussrate und der Druck des Hilfsgases müssen entsprechend dem Schweißmaterial, der Schweißgeschwindigkeit und der Laserleistung optimiert werden, um den besten Kühleffekt zu gewährleisten.
- Optimierung der Schweißgeschwindigkeit: Durch eine angemessene Erhöhung der Schweißgeschwindigkeit kann die Wärmezufuhr pro Zeiteinheit verringert und die Aufheizzeit des Materials verkürzt werden, wodurch eine Überhitzung des Schweißbereichs wirksam vermieden wird. Höhere Schweißgeschwindigkeiten können dazu führen, dass sich die Wärme schnell auf einen größeren Bereich ausbreitet, den lokalen Temperaturanstieg verringert und so die Schweißnahtbreite und die Wärmeeinflusszone gesteuert werden.
- Wärmequellenregelung: Durch die Anpassung der Laserleistung oder den Einsatz eines gepulsten Lasers lässt sich die Wärmezufuhr beim Schweißvorgang präzise steuern. Gerade beim Pulsschweißen können kurze Pulse und höhere Pulsfrequenzen dafür sorgen, dass die Wärme schnell fokussiert und im Schweißbereich verteilt wird, um eine Wärmediffusion zu vermeiden.
Materialreflexion
Herausforderung
Lösung
- Verwenden Sie kurzwellige Laser: Kurzwellige Laser (wie sie von Faserlasergeneratoren erzeugt werden) haben eine höhere Absorptionsrate für stark reflektierende Materialien. Kurzwellige Laser können besser von Materialien absorbiert werden, reduzieren Reflexionen und stellen sicher, dass mehr Laserenergie effektiv im Schweißprozess eingesetzt wird, wodurch die Schweißeffizienz verbessert und die Schweißnahtbreite verringert wird. Im Vergleich zu langwelligen CO2-Lasern eignen sich Faserlasergeneratoren besser für die Bearbeitung von Materialien mit höherem Reflexionsgrad.
- Anpassung der Laserleistung: Bei Materialien mit hoher Reflektivität kann eine entsprechende Reduzierung der Laserleistung eine übermäßige Energiereflexion vermeiden. Niedrigere Leistungseinstellungen tragen dazu bei, Reflexionen zu reduzieren und Energieverschwendung zu vermeiden. Dadurch wird die Schweißbreite effektiv gesteuert und die Schweißqualität optimiert.
- Verwenden Sie beschichtete Materialien: Einige stark reflektierende Metallmaterialien wie Aluminium und Kupfer können Beschichtungstechnologien wie Aluminiumbeschichtung, Kupferbeschichtung und andere Oberflächenbehandlungsmethoden verwenden. Diese Beschichtungen haben ein geringeres Reflexionsvermögen, was die Absorptionseffizienz des Lasers verbessern und die Interferenz der Reflexion beim Schweißprozess verringern kann, wodurch die Schweißnahtbreite besser kontrolliert werden kann.
Prozessstabilität
Herausforderung
Lösung
- Fortschrittliches Lasersteuerungssystem: Durch den Einsatz fortschrittlicher Lasersteuerungssysteme können wichtige Parameter wie Laserleistung, Schweißgeschwindigkeit, Strahlfokus usw. in Echtzeit überwacht und angepasst werden, um die Konsistenz der Laserparameter während jedes Schweißvorgangs sicherzustellen. Moderne Laserschweißsysteme sind normalerweise mit hochpräzisen Sensoren und automatischen Anpassungsfunktionen ausgestattet, die die Temperatur des Schweißbereichs, die Morphologie des Schmelzbads und die Strahlposition in Echtzeit erkennen und die Laserleistung automatisch anpassen können, um die Stabilität des Schweißvorgangs aufrechtzuerhalten.
- Echtzeit-Feedback und Regelung: Durch den Einsatz von Echtzeit-Feedback und Regelungstechnologie können Parameter während des Schweißvorgangs in Echtzeit angepasst werden, um Änderungen der Materialeigenschaften und der Schweißumgebung zu berücksichtigen. Beispielsweise können Sensoren die Größe, Form und Temperatur des Schmelzbads überwachen, und das System kann die Laserleistung und Schweißgeschwindigkeit automatisch anpassen, um die Konsistenz der Schweißqualität aufrechtzuerhalten. Diese Technologie kann die Zuverlässigkeit des Schweißprozesses erheblich verbessern und Schweißprobleme vermeiden, die durch Prozessschwankungen verursacht werden.
- Schweißpfadoptimierung: Während des Schweißvorgangs ist die Optimierung der Laserpfadplanung ein weiterer wichtiger Weg zur Verbesserung der Prozessstabilität. Durch die genaue Steuerung des Schweißpfads und der Schweißreihenfolge können Materialverformungen und Veränderungen in der Wärmeeinflusszone reduziert werden. Dies gewährleistet eine gleichmäßige Temperaturverteilung während jedes Schweißvorgangs und führt so zu stabilen Schweißergebnissen.
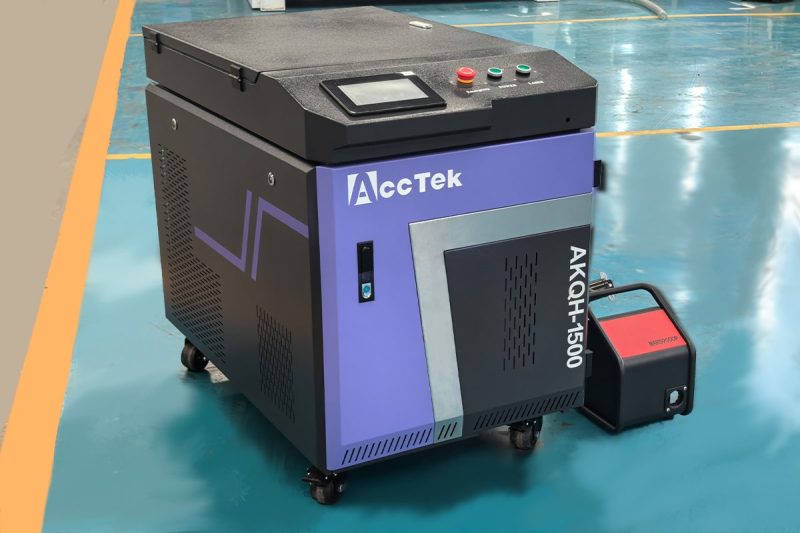
Zusammenfassen
In diesem Prozess Laserschweißmaschinen sind mit ihrer überlegenen Technologie und ihrem innovativen Design zu Branchenführern geworden. Die Laserschweißgeräte unseres Unternehmens verwenden die neueste Faserlasertechnologie, die effizientes Schweißen ermöglicht und gleichzeitig eine genaue Temperaturkontrolle während des Schweißvorgangs gewährleistet, wodurch die Schweißnahtbreite effektiv kontrolliert und die Wärmeeinflusszone reduziert wird. Unsere Schweißgeräte verfügen nicht nur über hochpräzise Laserstrahlanpassungsmöglichkeiten, sondern sind auch mit einem fortschrittlichen Temperaturkontrollsystem ausgestattet, das die Parameter während des Schweißvorgangs automatisch anpassen kann, wodurch der Schweißeffekt optimiert und eine stabile und gleichbleibende Qualität an jedem Schweißpunkt sichergestellt wird.
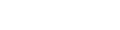
- [email protected]
- [email protected]
- +86-19963414011
- Nr. 3 Zone A, Industriegebiet Lunzhen, Stadt Yucheng, Provinz Shandong.