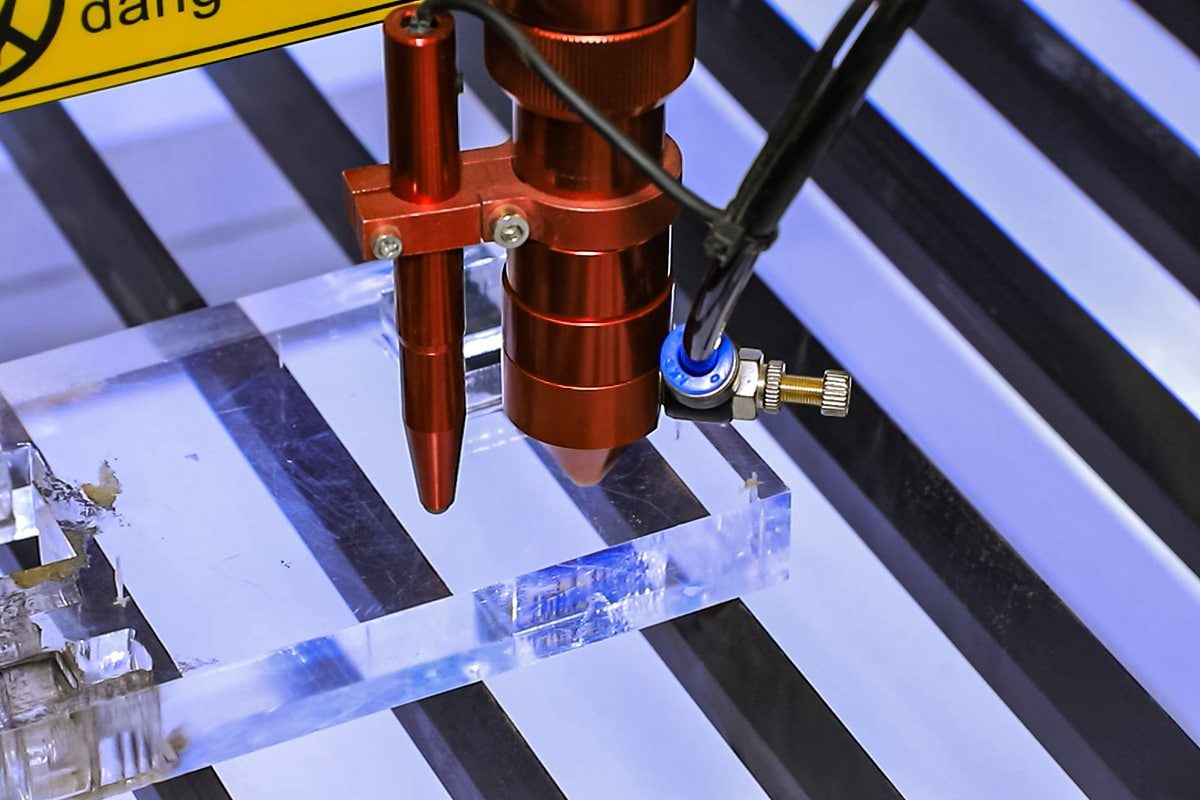
Können mit CO2-Laserschneiden hochpräzise komplexe Designs erreicht werden?
Das CO2-Laserschneiden ist zu einer Eckpfeilertechnologie in der modernen Fertigung geworden und hat die Art und Weise revolutioniert, wie Industrien an die Materialverarbeitung herangehen. Durch die Nutzung der Kraft eines konzentrierten Laserstrahls ist die Technologie in der Lage, eine Vielzahl von Materialien, darunter Metalle, Kunststoffe und Verbundwerkstoffe, präzise zu schneiden. Durch die berührungslose Natur wird die Materialverformung minimiert, was sie ideal für Anwendungen macht, die hohe Präzision und komplizierte Details erfordern. Die Vielseitigkeit von CO2-Laserschneidmaschinen hat ihren Einsatz in zahlreichen Bereichen, von der industriellen Fertigung bis zum kreativen Design, ermöglicht und so ihre Anpassungsfähigkeit und Effizienz unter Beweis gestellt.
CO2-Laserschneiden weist eine beispiellos hohe Präzision bei komplexen Designs auf und kann problemlos komplexe Muster und Details verarbeiten, um strenge Toleranzen sicherzustellen. Dies verbessert nicht nur die Qualität der fertigen Produkte und verringert den Bedarf an sekundärer Verarbeitung, sondern senkt auch die Kosten erheblich und verbessert die Produktionseffizienz. Mit der kontinuierlichen Innovation der Branche ist das CO2-Laserschneiden zu einer wichtigen treibenden Kraft für Feinmechanik und fortschrittliche Fertigung geworden.
Inhaltsverzeichnis
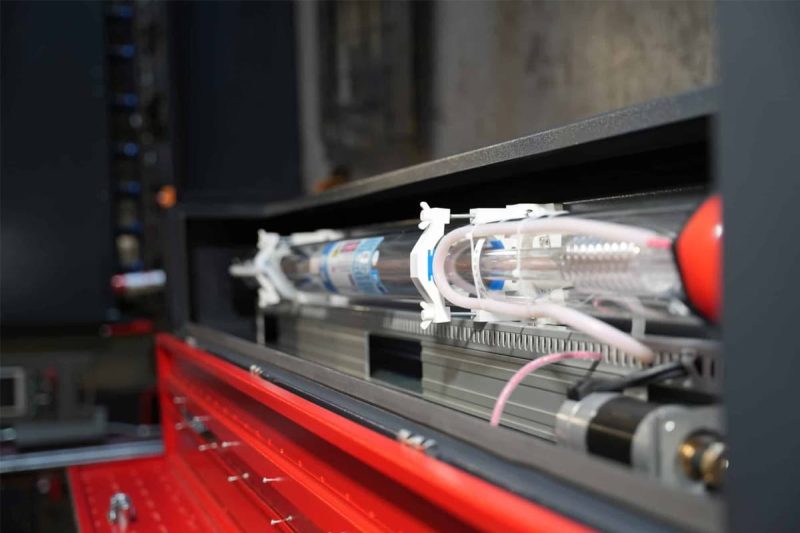
CO2-Laserschneiden verstehen
Das CO2-Laserschneiden ist aufgrund seiner hohen Präzision und seiner komplexen Konstruktionsmöglichkeiten zu einer Schlüsseltechnologie in der modernen Fertigung und im Design geworden. Ein tiefes Verständnis seiner Prinzipien und Funktionen kann Unternehmen dabei helfen, sein Potenzial zu maximieren und vielfältige Anwendungsanforderungen zu erfüllen.
Prinzipien des CO2-Laserschneidens
Beim CO2-Laserschneiden wird ein Kohlendioxidlasergenerator verwendet, um einen hochenergetischen Infrarotstrahl abzugeben, mit dem Materialien mit extrem hoher Präzision geschnitten, graviert oder geätzt werden können. Zu den Kernprinzipien gehören: Verwendung eines Lasermediums, das mit Kohlendioxid, Stickstoff und Helium gemischt ist, um einen Laserstrahl zu erzeugen; Fokussierung des Strahls auf die Oberfläche des Materials durch Linsen und Linsen; Verwendung automatisierter Systeme wie CNC, um den Laserkopf präzise zu führen und komplexe Muster zu vervollständigen; und Verwendung von Hilfsgasen wie Sauerstoff, Stickstoff oder Luft, um die Schneidleistung zu verbessern, Oxidation zu vermeiden und Schlacke zu entfernen.
Überblick über Schneidtechnologie und Präzisionsfähigkeiten
Der Schneidprozess des CO2-Lasersystems gewährleistet Genauigkeit und Qualität durch streng kontrollierte Schritte, einschließlich der Erzeugung des Laserstrahls, der Absorption von Energie durch das Material, die zum Schmelzen oder Verdampfen führt, und des Hilfsgases zum Entfernen des geschmolzenen Materials, wodurch eine saubere Kante entsteht. Seine Präzisionsfähigkeiten spiegeln sich in hoher Genauigkeit (Schneidtoleranz bis ±0,1 mm), schmalem Schnitt zur Reduzierung von Materialabfall, automatisiertem System zur Gewährleistung der Wiederholbarkeit und breiter Kompatibilität mit einer Vielzahl von Materialien wie Metall, Acryl, Holz usw. wider.
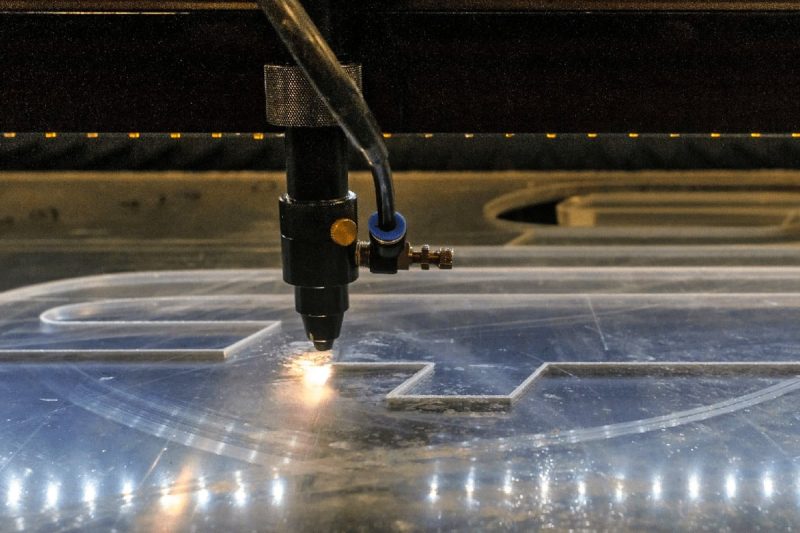
Schlüsselfaktoren, die die Präzision beim CO2-Laserschneiden beeinflussen
Das Erreichen hoher Präzision beim CO2-Laserschneiden hängt von mehreren kritischen Faktoren ab. Das Verstehen und Optimieren dieser Elemente kann die Schneidgenauigkeit und -effizienz verbessern.
Qualität des Laserstrahls: Die Qualität des Laserstrahls wird durch den M2-Faktor gemessen. Je näher der M2-Wert bei 1 liegt, desto konzentrierter ist der Laserstrahl und desto feiner ist der Schneideffekt. Ein hochwertiger Laserstrahl kann einen kleineren Punkt erzeugen, die Schnittgenauigkeit verbessern und die Wärmeeinflusszone verringern, wodurch die Genauigkeit des Schneidpfads gewährleistet wird.
Fokuseinstellungen: Die Fokusposition beeinflusst die Feinheit der Schnittkante. Die richtige Fokuseinstellung stellt sicher, dass der Laserstrahl einen geeigneten Punkt auf der Materialoberfläche bildet und so eine präzise Schnitttiefe und hochwertige Kanten gewährleistet.
Systemstabilität: Die Stabilität der Laserschneidmaschine bestimmt die Schnittgenauigkeit. Instabile Laserleistung oder mechanische Vibrationen führen zu Genauigkeitsschwankungen. Ein stabiler Lasergenerator und ein präzises Bewegungssystem können ein kontinuierliches hochpräzises Schneiden gewährleisten.
Erreichbare Toleranzen: Beim CO2-Laserschneiden kann eine Genauigkeit von ±0,1 mm erreicht werden, weshalb es sich für Bereiche eignet, in denen hohe Präzision erforderlich ist, wie etwa bei der Verarbeitung von Präzisionsteilen und elektronischen Produkten.
Kantenqualität: CO2-Laserschneiden sorgt für glatte Schnittkanten. Der hochwertige Laserstrahl und die Fokussteuerung reduzieren Grate und wärmebeeinflusste Zonen, verbessern die Schnittqualität und reduzieren den Bedarf an Nachbearbeitungen.
Bewegungssteuerungssysteme: Die Positioniergenauigkeit und die dynamische Reaktion der Schneidemaschine wirken sich direkt auf die Genauigkeit des Schneidpfads aus, insbesondere bei komplexen Designs.
Materialeigenschaften und -dicke: Dichte, Wärmeleitfähigkeit und Dicke des Materials wirken sich auf die Absorptionseffizienz der Laserenergie aus und beeinflussen somit Schneidwirkung und -genauigkeit.
Schnittgeschwindigkeit und Leistung: Eine zu hohe Schnittgeschwindigkeit oder unzureichende Leistung kann zu unvollständigem Schnitt führen, während zu viel Leistung zum Materialabtrag oder zur Beeinträchtigung der Kantenqualität führen kann.
Kurz gesagt: Das CO2-Laserschneiden ermöglicht hochpräzise Schnitte und hochwertige Kanteneffekte durch präzise Laserstrahlsteuerung und Systemstabilität und wird häufig in Bereichen der hochpräzisen Verarbeitung eingesetzt.
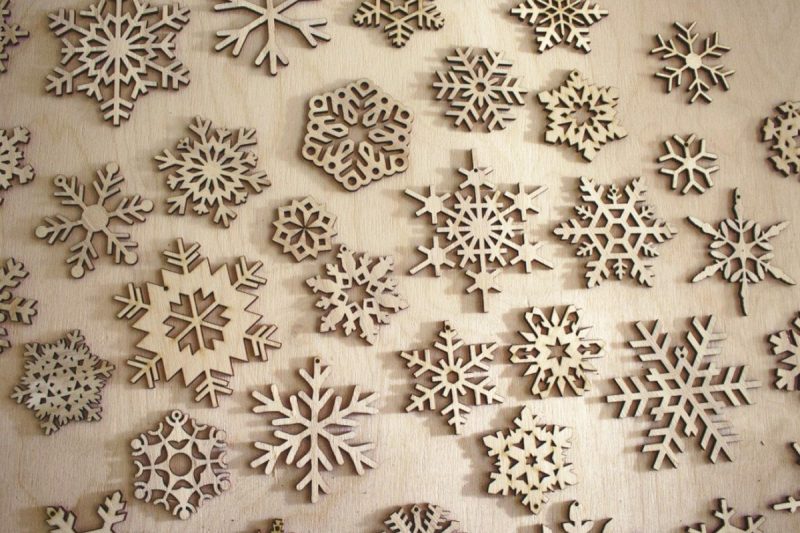
Komplexität des Designs
Im Bereich des Laserschneidens beziehen sich komplexe Designs auf Projekte, die feine Details und komplexe Muster enthalten und strenge Toleranzen erfordern. Die Realisierung dieser Designs stellt extrem hohe Anforderungen an die Genauigkeit, Stabilität und Verarbeitungsfähigkeiten der Geräte und bringt auch neue Herausforderungen für die Verarbeitungstechnologie mit sich.
Definition von komplexem Design im Kontext des Laserschneidens
Bei komplexen Konstruktionen handelt es sich in der Regel um Konstruktionen, die eine hohe Präzision und sorgfältige Handhabung erfordern. Dazu gehören:
- Feine Details wie Mikrogravuren oder dekorative Muster erfordern eine stabile und hochpräzise Positionierung der Laserschneidmaschine.
- Komplexe Muster: Bei unregelmäßigen Formen oder hierarchischen geometrischen Designs erfordert der Schnittpfad mehrere Anpassungen und eine effiziente Planung.
- Enge Toleranzen: Bei der Fertigung, die extrem hohe Präzision erfordert, müssen Schnittabweichungen im Bereich von Mikrometern oder 0,1 mm kontrolliert werden.
Diese Designs stellen hohe Anforderungen an die Kernleistung der Laserschneidanlage, wie etwa Strahlqualität, Bewegungssteuerung und Leistungsstabilität.
Herausforderungen komplexer Muster
Die Verarbeitung komplexer Muster stellt bei der Laserschneidtechnologie eine große Herausforderung dar, insbesondere bei der präzisen Reproduktion mehrschichtiger oder asymmetrischer Designs. Die folgenden Probleme treten dabei besonders in den Vordergrund:
- Komplexe Pfadplanung: Beim Schneiden komplexer Muster muss das CNC-System den variablen Schneidpfad optimieren, um Zeitverlust und Fehler zu reduzieren.
- Ansammlung thermischer Effekte: Langfristiges, kontinuierliches Schneiden komplexer Muster kann zu einer lokalen Wärmeansammlung führen, die eine Verformung oder Verformung des Materials zur Folge hat.
- Konsistenzkontrolle: Bei sich wiederholenden Verarbeitungsaufgaben muss sichergestellt werden, dass jedes fertige Produkt auch bei komplexen Designs konsistent und ohne Abweichungen oder Mängel bleibt.
Die Herausforderung feiner Details
Das Erzielen feiner Detailschnitte stellt höhere Anforderungen an die Leistung der Laserschneidmaschine:
- Begrenzung des Strahldurchmessers: Um feine Schnittlinien zu erzielen, muss der Spotdurchmesser des Laserstrahls sehr klein sein, üblicherweise im Mikrometerbereich.
- Leistungsstabilität: Leistungsschwankungen in der Laserleistung wirken sich direkt auf die Detailschärfe und die Kantenqualität aus, was zu ungleichmäßigem Schnitt oder Graten führen kann.
- Hohe Anforderungen an die Dynamik: Die Bewegungssteuerung des Laserkopfes muss schnell reagieren, um sicherzustellen, dass bei komplexen Schnitten in feinen Bereichen kein Versatz oder keine Überlappung des Pfads auftritt.
Diese technischen Anforderungen machen die Verarbeitung feiner Details beim Laserschneiden zu einer äußerst anspruchsvollen Aufgabe.
Die Herausforderungen enger Toleranzen
Enge Toleranzen sind eine unverzichtbare Voraussetzung in der High-End-Fertigung, insbesondere in Branchen wie der Medizin und der Luft- und Raumfahrt. Um diese Anforderungen zu erfüllen, muss das Laserschneiden die folgenden Schwierigkeiten bewältigen:
- Hochpräzise Positionierung: Die Laserschneidmaschine muss mit einem hochauflösenden Positionsrückmeldesystem ausgestattet sein, um die Positionierungsgenauigkeit des Schneidkopfes im Mikrometerbereich sicherzustellen.
- Thermische Verformungskompensation: Das Material kann sich während des Schneidvorgangs aufgrund von Hitze ausdehnen oder verformen. Die Laserschneidmaschine muss in Echtzeit überwacht und automatisch angepasst werden, um die Schnittgröße sicherzustellen.
- Strahlqualität: Durch die Verwendung hochwertiger optischer Komponenten können Strahlstreuung und -abweichung reduziert und so die Klarheit und Genauigkeit der Schneide sichergestellt werden.
Die Notwendigkeit, eine hohe Verarbeitungseffizienz beizubehalten und gleichzeitig strenge Toleranzen einzuhalten, erschwert den Schneidprozess zusätzlich.
Durch die Bewältigung dieser Herausforderungen ist die Laserschneidtechnologie zu einem unverzichtbaren Werkzeug für die Realisierung komplexer Designs geworden und eröffnet neue Möglichkeiten in der Welt der Präzisionsfertigung.
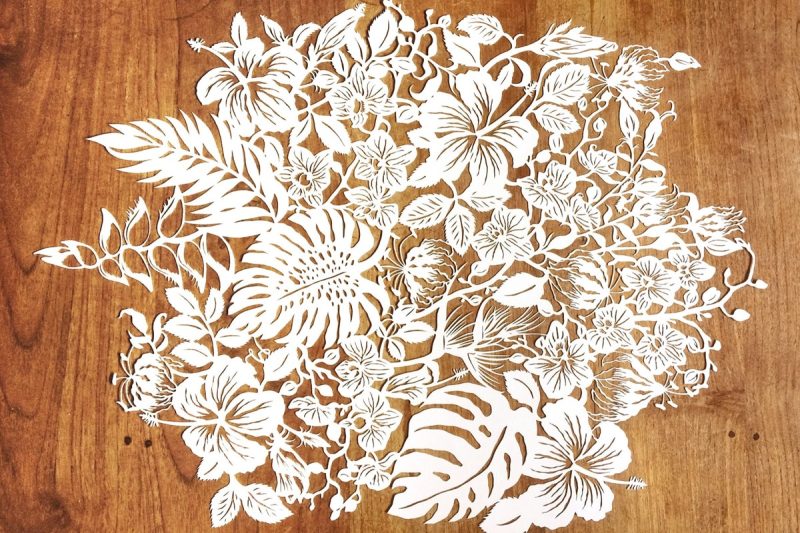
Technologie zur Verbesserung der Präzision beim Laserschneiden
Im sich ständig weiterentwickelnden Bereich des Laserschneidens haben technologische Fortschritte Präzision, Effizienz und Vielseitigkeit erheblich verbessert. Diese Innovationen bewältigen Herausforderungen im Zusammenhang mit Genauigkeit und Konsistenz, insbesondere beim Umgang mit komplizierten Designs und unterschiedlichen Materialarten. Im Folgenden untersuchen wir drei wichtige Durchbrüche beim CO2-Laserschneiden: Autofokuseinstellung, Echtzeit-Überwachungssysteme und CAD/CAM-Integration.
Autofokus-Anpassung: Verbesserte Genauigkeit bei allen Materialien
Die automatische Fokuseinstellung ist eine bahnbrechende Funktion in CO2-Laserschneidsystemen. Sie ermöglicht dem Laser die dynamische Anpassung an unterschiedliche Materialstärken und Oberflächenkonturen und stellt sicher, dass der Laserstrahl im optimalen Brennpunkt bleibt, was für präzises Schneiden entscheidend ist.
- Präzision bei allen Materialarten: Verschiedene Materialien (z. B. Metalle, Kunststoffe, Glas) erfordern spezifische Fokuseinstellungen für saubere Schnitte. Durch den Autofokus entfallen manuelle Anpassungen, was sowohl Ausfallzeiten als auch menschliche Fehler reduziert.
- Verbesserte Kantenqualität: Durch Beibehaltung der richtigen Brennweite minimiert der Autofokus Probleme wie raue Kanten, unvollständige Schnitte oder Materialdurchbrand, insbesondere bei komplizierten Mustern.
- Höhere Effizienz: Automatische Anpassungen optimieren den Schneidevorgang und machen ihn schneller und zuverlässiger, insbesondere beim Wechsel zwischen Materialien oder der Arbeit mit mehrschichtigen Designs.
Echtzeit-Überwachungssysteme: Konsistenz durch Live-Anpassungen sicherstellen
Echtzeit-Überwachungssysteme ermöglichen es CO2-Laserschneidmaschinen, während des gesamten Schneidvorgangs Präzision und Konsistenz aufrechtzuerhalten. Diese Systeme verwenden Sensoren und Rückkopplungsschleifen, um Parameter wie Leistungsabgabe, Strahlausrichtung und Materialinteraktion zu überwachen.
- Dynamische Anpassungen: Überwachungssysteme können Einstellungen wie Laserleistung und Schnittgeschwindigkeit automatisch anpassen, um Schwankungen der Materialdichte oder unerwartete Unregelmäßigkeiten zu berücksichtigen.
- Minimierte Defekte: Durch die Echtzeiterkennung von Problemen wie Hitzeverzerrung oder Strahlfehlausrichtung werden Defekte vermieden, bevor sie auftreten, und so qualitativ hochwertigere Ergebnisse sichergestellt.
- Verbesserte Produktivität: Kontinuierliches Feedback reduziert den Bedarf an Inspektionen und Nacharbeiten nach dem Schnitt und erhöht so den Durchsatz und die Kosteneffizienz.
CAD/CAM-Integration: Präzises Design und Ausführung
Die Integration von CAD- und CAM-Software (Computer Aided Design) mit CO2-Laserschneidsystemen hat die Umsetzung von Designs in physische Komponenten revolutioniert. Diese Synergie ermöglicht eine nahtlose Designausführung und -optimierung.
- Präzise Pfadplanung: CAD/CAM-Software generiert präzise Schnittpfade und stellt sicher, dass selbst die kompliziertesten Designs fehlerfrei ausgeführt werden. Dies ist von entscheidender Bedeutung für Branchen, in denen enge Toleranzen erforderlich sind, wie z. B. die Luft- und Raumfahrt und die Herstellung medizinischer Geräte.
- Materialoptimierung: Fortschrittliche Software simuliert Schnittpfade und Materialverbrauch, reduziert den Abfall und verbessert die Kosteneffizienz.
- Anpassbare Parameter: Bediener können die Einstellungen des Lasergenerators (wie Leistung und Schnittgeschwindigkeit) in der Software vorab festlegen und so die Konsistenz über mehrere Produktionsläufe und Materialien hinweg sicherstellen.
- Automatisierung und Skalierbarkeit: Die CAD/CAM-Integration unterstützt automatisierte Arbeitsabläufe und ermöglicht eine skalierbare Produktion ohne Kompromisse bei Präzision oder Qualität.
Die Kombination aus automatischer Fokuseinstellung, Echtzeitüberwachung und CAD/CAM-Integration setzt einen neuen Standard für die Genauigkeit beim CO2-Laserschneiden. Diese technologischen Fortschritte erhöhen nicht nur die Schnittgenauigkeit, sondern verbessern auch die Effizienz, reduzieren Materialabfall und senken die Betriebskosten. Zusammen ermöglichen sie es Herstellern, komplexe Designs in Angriff zu nehmen und eine hervorragende Konsistenz über eine breite Palette von Anwendungen hinweg zu erreichen.
Durch den Einsatz dieser Spitzentechnologien können Unternehmen das Potenzial von CO2-Lasergeneratoren maximieren und qualitativ hochwertige Ergebnisse erzielen, die den Anforderungen der modernen Industrie gerecht werden. Ob komplexe Schmuckdesigns, medizinische Präzisionskomponenten oder Autoteile – diese technologischen Fortschritte ebnen den Weg für die Zukunft der Laserschneidlösungen.
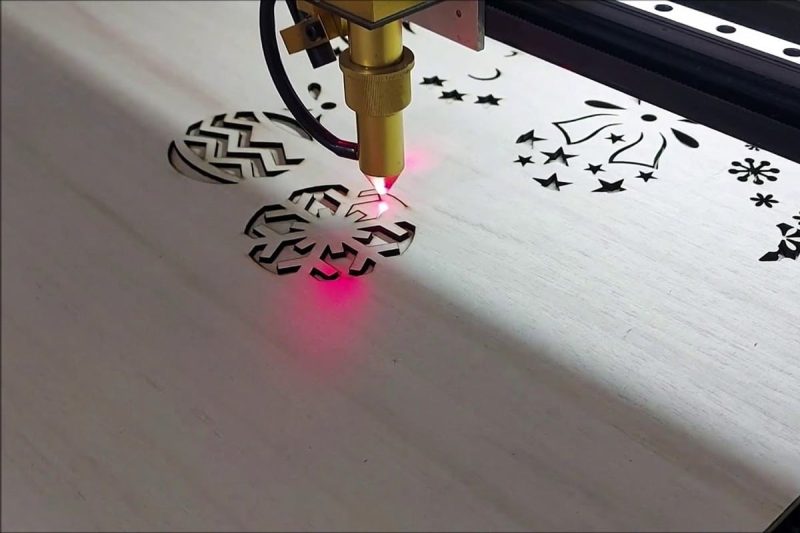
Vorteile des hochpräzisen CO2-Laserschneidens
Verbesserte Teilequalität und -konsistenz
Hochpräzises CO2-Laserschneiden sorgt für hervorragende Oberflächengüte und Gleichmäßigkeit. Diese Technologie stellt sicher, dass jedes Produkt eine hohe Konsistenz in Größe und Form aufweist, egal ob in Massenproduktion oder als Sonderanfertigung. Im Vergleich zu herkömmlichen Schneideverfahren reduziert das CO2-Laserschneiden Abweichungen, die durch menschliches Versagen oder mechanische Genauigkeitsprobleme verursacht werden, erheblich und verbessert so die Produktkonsistenz und -qualität erheblich. Insbesondere in Branchen mit strengen Anforderungen an die Oberflächenqualität, wie der Automobil-, Luft- und Raumfahrt- und Medizingeräteherstellung, erzeugt das Laserschneiden glattere Kanten mit weniger Graten und unregelmäßigen Formen.
Reduzierung des Sekundärverarbeitungsbedarfs
Die präzisen Schneidfunktionen von CO2-Lasergeneratoren reduzieren den Bedarf an Nachjustierungen nach dem Schneiden erheblich. Herkömmliche Schneideverfahren erfordern häufig mehrere sekundäre Arbeitsschritte, um Schnittkanten zu verfeinern oder Abmessungen anzupassen. Im Gegensatz dazu kann beim hochpräzisen Laserschneiden das gewünschte Schneidergebnis in einem Durchgang erzielt werden, wodurch Zeit und Kosten für nachfolgende Justierungen gespart werden. Dieser Vorteil ist besonders wertvoll bei der Herstellung komplexer oder präziser Teile wie Präzisionswerkzeugen, Luft- und Raumfahrtkomponenten und Elektronikgehäusen, da er Arbeitskosten und Produktionszeit reduziert.
Kosteneinsparungen und Produktivitätssteigerung
Durch die Minimierung der Sekundärverarbeitung und die Optimierung des Schneidprozesses steigert hochpräzises CO2-Laserschneiden die Produktionseffizienz erheblich. Lasergeneratoren können effizientes Schneiden mit minimalem menschlichen Eingriff durchführen, wodurch die Produktionszyklen verkürzt und eine gleichbleibende Teilequalität sichergestellt wird, was Nacharbeit und Materialabfall reduziert. Diese automatisierte und präzise Produktionsmethode senkt nicht nur die Betriebskosten, sondern erhöht auch den Durchsatz und verbessert so die Gesamtproduktivität der Unternehmen. Für Großhersteller ist hochpräzises CO2-Laserschneiden ein wichtiges Instrument zur Rationalisierung der Produktionsprozesse und Steigerung der Wettbewerbsfähigkeit.
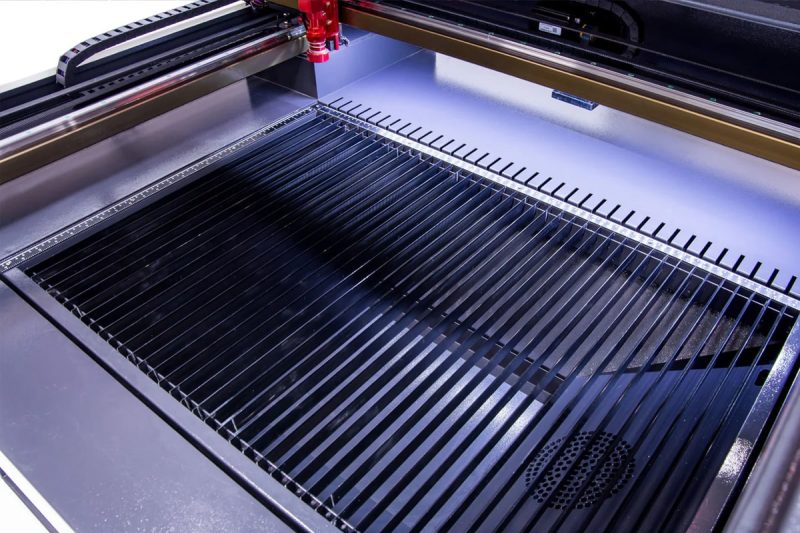
Anwendungen, die hochpräzises Schneiden erfordern
Hochpräzisionsschneiden wird in vielen verschiedenen Bereichen eingesetzt. Zu den wichtigsten Anwendungen zählen:
Luft- und Raumfahrtkomponenten: Die Luft- und Raumfahrtindustrie erfordert eine extrem hohe Schnittgenauigkeit, um die Leistung und Sicherheit der Komponenten zu gewährleisten. Beispielsweise erfordert die Herstellung von Motorkomponenten, Strukturrahmen und Präzisionsteilen Laserschneidtechnologie, um sicherzustellen, dass jede Komponente strenge Anforderungen in Bezug auf Größe, Form und Festigkeit erfüllt. Jede noch so kleine Abweichung kann die Gesamtleistung oder Sicherheit beeinträchtigen, daher ist eine hochpräzise Schneidtechnologie unerlässlich.
Elektronik und Mikroelektronik: Da elektronische Geräte immer kleiner werden, werden an mikroelektronische Komponenten immer strengere Präzisionsanforderungen gestellt. Bei Anwendungen wie Chip-Verpackungen, Leiterplattenschneiden und Sensorherstellung kann durch Laserschneiden eine extrem hohe Präzision erreicht werden, um sicherzustellen, dass jeder Schaltkreis und jede Komponente richtig angeschlossen ist, wodurch die Zuverlässigkeit und Leistung elektronischer Geräte sichergestellt wird.
Medizinische Geräte: Medizinische Geräte und Ausrüstungen, insbesondere minimalinvasive chirurgische Instrumente und Implantate, erfordern eine sehr hohe Schnittgenauigkeit. Diese Geräte weisen häufig komplexe Geometrien und extrem kleine Größen auf, und Laserschneiden kann Metalle, Kunststoffe und andere biokompatible Materialien mit äußerst hoher Präzision schneiden, um sicherzustellen, dass das Gerät hinsichtlich Funktion und Sicherheit strenge medizinische Standards erfüllt.
Architekturmodelle und Prototypen: In der Architekturgestaltung und beim Prototyping wird die Laserschneidtechnologie zum Erstellen komplexer Architekturmodelle und filigraner Komponenten eingesetzt. Sie kann eine Vielzahl von Materialien wie Holz, Kunststoff und Metall zur Designüberprüfung und Musterherstellung präzise schneiden. Dies ist sehr wichtig für die Demonstration von Designkonzepten, das Testen technischer Lösungen und die Kundenkommunikation.
Diese Anwendungen verdeutlichen die unersetzliche Rolle hochpräziser Schneidtechnologie in verschiedenen Bereichen, die strenge Toleranzen und komplexe Designanforderungen erfüllen kann, um die Leistung und Qualität des Produkts sicherzustellen.
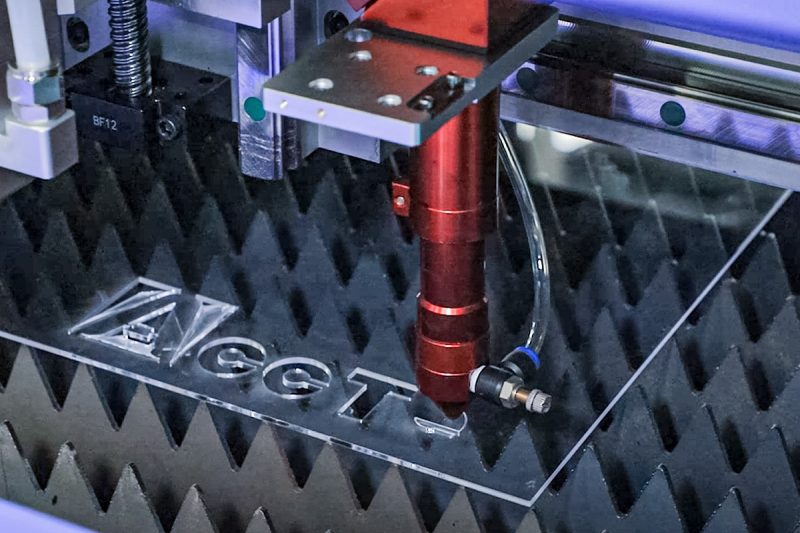
Zusammenfassen
Die CO2-Laserschneidtechnologie hat mit ihrer hohen Präzision und hervorragenden Anpassungsfähigkeit ihre beispiellosen Vorteile im Bereich komplexer Designs und enger Toleranzen bewiesen. Von der Laserstrahlqualität bis zu den Automatisierungsfunktionen unterstützt jeder Aspekt die Realisierung hochpräziser Schnitte. Ob es sich um Schlüsselteile für die Luft- und Raumfahrt oder die Präzisionsanforderungen von Mikroelektronik und medizinischen Geräten handelt, das CO2-Laserschneiden verbessert nicht nur die Konsistenz und Qualität der Teile, sondern senkt auch die Kosten der Sekundärverarbeitung erheblich und verbessert die Gesamtproduktionseffizienz.
Mit Blick auf die Zukunft wird das CO2-Laserschneiden dank kontinuierlicher technologischer Innovationen sein Potenzial in weiteren Bereichen unter Beweis stellen und der Fertigungsindustrie effizientere und wirtschaftlichere Lösungen für Präzisionsverarbeitung und komplexes Design bieten. Diese Technologie ist nicht nur ein Kernwerkzeug für die High-End-Fertigung, sondern wird die Industrie auch weiterhin in eine präzisere und effizientere Zukunft führen.
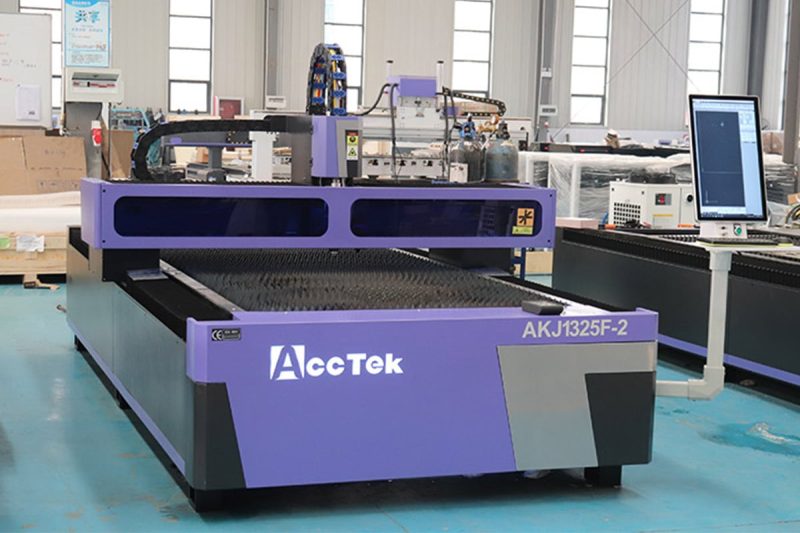
Holen Sie sich Laserlösungen
Möchten Sie komplexe Designs hochpräzise schneiden? AccTek-Laser bietet Ihnen die perfekte Lösung! Als Experten für Lasertechnologie konzentrieren wir uns darauf, unseren Kunden leistungsstarke und hochzuverlässige CO2-Laserschneidmaschinen anzubieten, die Ihren unterschiedlichen Anforderungen in der Präzisionsfertigung gerecht werden. Von Teilen für die Luft- und Raumfahrt bis hin zur Mikrobearbeitung elektronischer Geräte – unsere Schneidgeräte helfen Ihnen, komplexe Designherausforderungen mit hervorragender Genauigkeit und Stabilität problemlos zu meistern. Kontaktieren Sie uns jetzt, um eine maßgeschneiderte Laserschneidlösung zu erhalten, mit der Sie Ihren Herstellungsprozess effizienter und besser gestalten können!
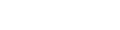
Kontaktinformationen
- [email protected]
- [email protected]
- +86-19963414011
- Nr. 3 Zone A, Industriegebiet Lunzhen, Stadt Yucheng, Provinz Shandong.
Holen Sie sich Laserlösungen