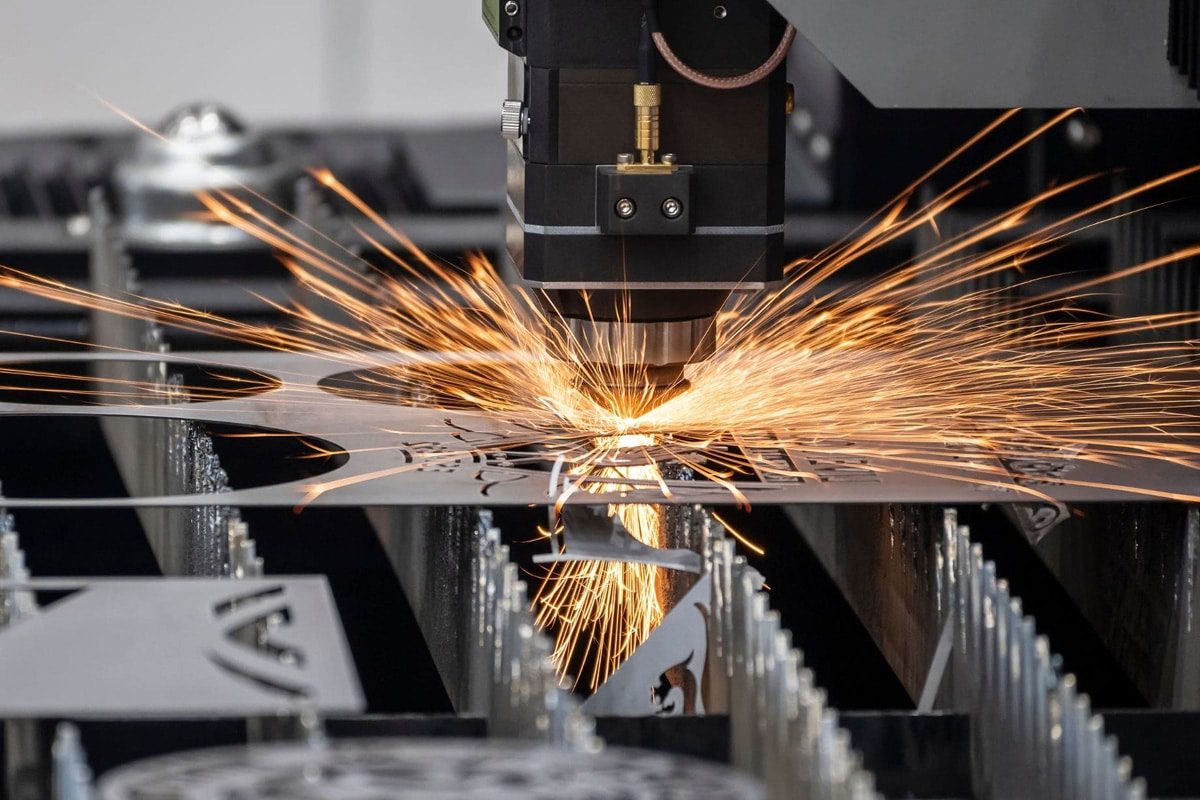
Lärm der Laserschneidmaschine
Laserschneidmaschinen werden aufgrund ihrer hohen Effizienz und präzisen Schneidefähigkeiten in vielen Branchen häufig eingesetzt, insbesondere in den Bereichen Fertigung, Automobil und Luftfahrt. Der von Laserschneidmaschinen während des Betriebs erzeugte Lärm ist jedoch auch ein Problem, das nicht ignoriert werden kann. Übermäßiger Lärm beeinträchtigt nicht nur die Arbeitsumgebung des Bedieners, sondern kann auch eine potenzielle Gefahr für die Gesundheit darstellen. Daher ist es besonders wichtig, die Lärmquelle, die Einflussfaktoren und die Gegenmaßnahmen zu verstehen.
Der Lärm von Laserschneidmaschinen hat hauptsächlich verschiedene Ursachen: das Laufgeräusch mechanischer Teile wie Motoren und Lüfter, Vibrationen beim Schneiden, Lärm von Abgas- und Belüftungssystemen sowie Lärm von Materialtransportsystemen. Unterschiedliche Schneidleistung, Geschwindigkeit und Materialeigenschaften beeinflussen die Lautstärke dieser Geräusche. Ein gutes Maschinendesign und effiziente Kühl- und Belüftungssysteme können zur Lärmreduzierung beitragen, während die Parameteranpassung beim Schneiden und die Materialeigenschaften den Lärm ebenfalls bis zu einem gewissen Grad beeinflussen.
In Bezug auf den Lärmschutz sind der rationelle Einsatz von Schallschutzausrüstung, ein optimiertes Maschinendesign sowie die regelmäßige Wartung und Schmierung der Ausrüstung wirksame Mittel zur Lärmreduzierung. Dies verbessert nicht nur die Arbeitsumgebung des Bedieners, sondern verringert auch wirksam die Gesundheitsrisiken einer langfristigen Belastung durch Umgebungen mit hohem Lärmpegel. Das Verstehen und Ergreifen geeigneter Lärmschutzmaßnahmen ist der Schlüssel zur Gewährleistung einer sicheren und gesunden Produktionsumgebung.
Inhaltsverzeichnis
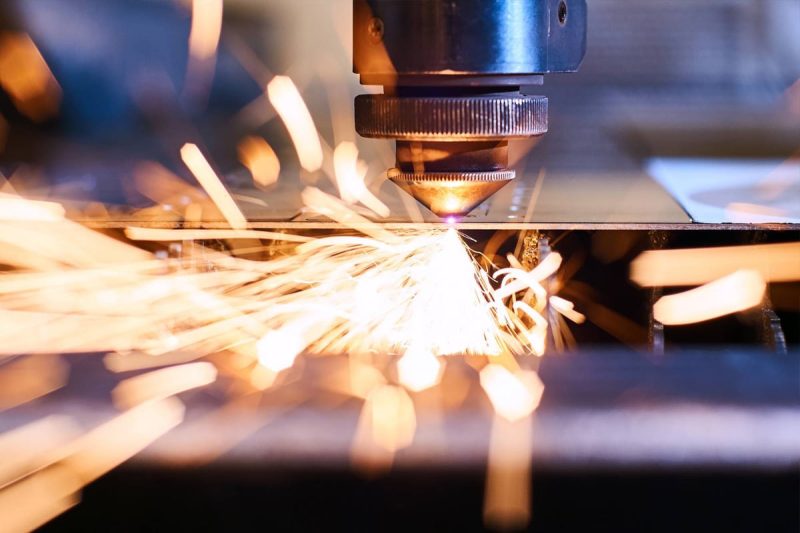
Lärm in Laserschneidmaschinen verstehen
Die Lärmquellen von Laserschneidmaschinen sind komplex und können in vier Hauptkategorien unterteilt werden: mechanische Teile, Vibrationen beim Schneiden, Absaug- und Belüftungssysteme sowie Materialtransportsysteme. Jede Art von Lärmquelle hat unterschiedliche Frequenzen und Eigenschaften, die den Geräuschpegel der Geräte während des Betriebs beeinflussen. Im Folgenden finden Sie eine detaillierte Analyse dieser Lärmquellen:
Mechanische Komponenten (z. B. Motoren, Lüfter)
Frequenz
Mechanische Komponenten wie Motoren und Lüfter erzeugen Geräusche bei Frequenzen, die in erster Linie von der Leistung und Geschwindigkeit des Geräts abhängen. Motorgeräusche liegen normalerweise zwischen 50 Hz und 300 Hz, wobei niedrigere Frequenzen hauptsächlich von großen oder leistungsstarken Motoren herrühren. Lüfter erzeugen Geräusche mittlerer und hoher Frequenz, die normalerweise zwischen 500 Hz und 2000 Hz liegen und eher zu den oberen Frequenzen tendieren, insbesondere wenn der Lüfter mit hoher Geschwindigkeit läuft.
Merkmal
Das Motorgeräusch ist relativ konstant und tritt normalerweise als niederfrequentes, kontinuierliches Brummen auf. Das Lüftergeräusch ist hauptsächlich ein scharfes, kontinuierliches Hochfrequenzgeräusch, das insbesondere bei hoher Geschwindigkeit deutlicher zu hören sein kann. Alternde Motoren oder Lüfter erzeugen normalerweise lautere Geräusche, insbesondere bei mangelnder Schmierung oder Verschleiß der Teile. Das Geräusch wird nicht nur lauter, sondern kann auch von Geräuschen wie mechanischer Reibung begleitet sein.
Vibrationen beim Schneiden
Frequenz
Während des Schneidvorgangs verursacht die Wechselwirkung zwischen dem Laser und dem Material Vibrationsgeräusche. Die Frequenz der Vibration hängt eng mit der Dicke und den Eigenschaften des Materials zusammen. Beim Schneiden dünnerer Materialien liegt die Geräuschfrequenz normalerweise zwischen 200 Hz und 1000 Hz; beim Schneiden dickerer Materialien, insbesondere Stahl oder anderer harter Materialien mit einer Dicke von mehr als 10 mm, liegt die durch die Vibration erzeugte Geräuschfrequenz normalerweise zwischen 100 Hz und 500 Hz.
Merkmal
Vibrationsgeräusche äußern sich normalerweise als unregelmäßige, kurze Aufprallgeräusche. Die Vibration dünner Materialien erzeugt höherfrequente Geräusche, die normalerweise schärfer sind; dicke Materialien verursachen niederfrequente und kontinuierliche Vibrationsgeräusche, die dumpf klingen. Darüber hinaus ändert sich die Intensität des Vibrationsgeräusches mit der Dicke des Materials und der Schnittgeschwindigkeit. Beim schnelleren Schneiden ist die Vibration deutlicher und der Geräuschpegel steigt entsprechend an.
Absaug- und Lüftungssysteme
Frequenz
Die Geräuschfrequenzen von Abluft- und Lüftungsanlagen liegen normalerweise zwischen 500 Hz und 4000 Hz. Je höher die Lüftergeschwindigkeit, desto höher ist die Frequenz des erzeugten Geräusches. Große Abluftanlagen erzeugen im Allgemeinen Geräusche mit niedrigerer Frequenz, während kleine, schnell laufende Lüfter eher Geräusche mit höherer Frequenz erzeugen.
Merkmal
Das Geräusch des Absaug- und Belüftungssystems ist normalerweise ein kontinuierliches und scharfes Windgeräusch, das deutlicher zu hören ist, wenn der Lüfter mit hoher Geschwindigkeit läuft. Wenn das Belüftungssystem nicht richtig ausgelegt ist oder der Luftkanal blockiert ist, wird der Luftstrom blockiert, was das Geräusch verstärkt. Darüber hinaus kann die Resonanz im Belüftungskanal auch bestimmte Geräuschfrequenzen verstärken und sie dadurch rauer machen. Da das Absaugsystem lange Zeit kontinuierlich laufen muss, kann diese Art von Geräusch während des Schneidvorgangs immer vorhanden sein.
Materialtransportsysteme
Frequenz
Die Geräuschfrequenzen von Materialtransportsystemen liegen normalerweise zwischen 100 Hz und 2000 Hz, abhängig vom Gewicht des Materials und der Funktionsweise des Systems. Leichte Materialien erzeugen bei der Handhabung im Allgemeinen höherfrequente Geräusche, während schwere Materialien niederfrequente Geräusche erzeugen.
Merkmal
Lärm bei der Materialhandhabung ist oft intermittierend und entsteht beim Laden, Entladen oder Transportieren von Materialien. Schwere Materialien erzeugen normalerweise niederfrequente Kollisionsgeräusche, die schwerer sind, während leichte Materialien höherfrequente Klopfgeräusche erzeugen können, die leichter, aber schärfer sind. Wenn die mechanischen Teile im System nicht gut gewartet werden, erzeugen Reibung und Blockieren zusätzlichen Lärm, wie beispielsweise scharfe Schleifgeräusche oder Kollisionsgeräusche von Metall auf Metall.
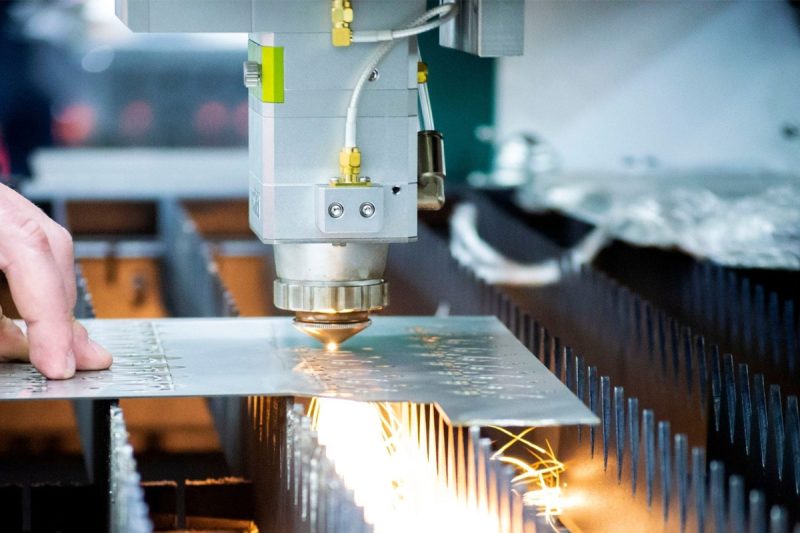
Faktoren, die den Geräuschpegel beeinflussen
Maschinendesign und Baumaterialien
Das Design und die Baumaterialien einer Laserschneidmaschine haben einen erheblichen Einfluss auf den Geräuschpegel. Eine gut konstruierte Maschine kann Vibrationen und Lärm effektiv reduzieren. Normalerweise werden dazu robuste Rahmen und hochsteife Materialien verwendet, um Resonanzeffekte zu reduzieren. Hochwertige Baumaterialien wie Stahl oder Aluminiumlegierungen können Vibrationen absorbieren und dämpfen und so die Ausbreitung von Schallwellen reduzieren. Darüber hinaus kann eine geeignete strukturelle Konstruktion, wie beispielsweise eine sinnvolle Komponentenanordnung und Verbindungsmethoden, die gegenseitige Beeinflussung verschiedener Komponenten effektiv reduzieren und so den Gesamtgeräuschpegel senken.
Schnittparameter
Schneidparameter, einschließlich Schneidleistung und -geschwindigkeit, wirken sich direkt auf den Betriebszustand und den Geräuschpegel der Laserschneidmaschine aus. Im Allgemeinen führen höhere Leistung und Geschwindigkeit zu stärkeren Vibrationen, was zu mehr Lärm führt. Beispielsweise muss beim Schneiden schwerer Materialien die Leistung erhöht werden, um die Schnittqualität sicherzustellen, was häufig zu stärkeren Vibrationen und Lärm führt. Daher kann eine ordnungsgemäße Anpassung der Schneidparameter, insbesondere bei der Verarbeitung unterschiedlicher Materialien, den Lärm wirksam reduzieren und gleichzeitig die Schneidwirkung sicherstellen.
Materialeigenschaften
Die Eigenschaften des zu schneidenden Materials, einschließlich Dicke, Dichte und Zusammensetzung, wirken sich alle auf den Geräuschpegel aus. Generell gilt, dass schwere oder harte Materialien, wie dicke Stahlplatten oder Legierungen, beim Schneiden normalerweise mehr Lärm erzeugen. Dies liegt daran, dass beim Laserschneiden härterer Materialien die erzeugte Hitze und Vibration stärker ist, was zu einer Zunahme der Schallwellenintensität führt. Darüber hinaus beeinflusst auch die Zusammensetzung des Materials die Klangeigenschaften beim Schneiden. Die Frequenz und Intensität des beim Schneiden von Materialien mit unterschiedlicher Zusammensetzung erzeugten Geräusches kann unterschiedlich sein.
Kühl- und Lüftungssysteme
Die Effizienz des Kühlsystems hängt direkt vom Betriebszustand des Lüfters ab, was wiederum den Geräuschpegel beeinflusst. Das Design des Kühlsystems muss sicherstellen, dass die beim Schneidvorgang entstehende Hitze und der Rauch effektiv abgeführt werden. Wenn das Kühlsystem ineffizient ist, erhöht sich die Belastung des Lüfters und er muss mit höherer Geschwindigkeit laufen, um die normale Temperatur des Geräts aufrechtzuerhalten, was zu zusätzlichem Lärm führt. Durch die Optimierung des Designs des Kühl- und Lüftungssystems kann nicht nur die Arbeitseffizienz des Geräts verbessert, sondern auch der Geräuschpegel während des Betriebs gesenkt werden.
Wirksamkeit von Schallschutzmaßnahmen
Bei der Konstruktion von Laserschneidmaschinen können angemessene Schallschutzmaßnahmen den Geräuschpegel deutlich reduzieren. Der Einbau von Schallschutzgehäusen und die Verwendung von schallabsorbierenden Materialien sind gängige Methoden zur Geräuschreduzierung. Die Wirksamkeit dieser Maßnahmen hängt jedoch eng mit der Qualität und dem Design der Schallschutzausrüstung zusammen. Hochwertige Schallschutzgehäuse und schallabsorbierende Materialien können Schall effektiv blockieren und absorbieren, während Schallschutzausrüstung, die schlecht konstruiert oder aus minderwertigen Materialien hergestellt ist, möglicherweise nur eine begrenzte Wirksamkeit hat. Daher ist es bei der Installation von Schallschutzmaßnahmen erforderlich, Materialeigenschaften, Designkonzepte und tatsächliche Anwendungsszenarien umfassend zu berücksichtigen, um den besten Geräuschreduzierungseffekt zu erzielen.
Wartung und Schmierung beweglicher Teile
Die beweglichen Teile der Laserschneidmaschine erzeugen während des Betriebs aufgrund von Reibung und Verschleiß zusätzliche Geräusche. Daher sind eine gute Wartung und regelmäßige Schmierung unerlässlich, um den Lärm zu reduzieren. Regelmäßige Inspektion und Wartung beweglicher Teile wie Führungen, Getriebe und Motoren können nicht nur die Reibung verringern, sondern auch die Lebensdauer der Geräte verlängern. Die Verwendung geeigneter Schmiermittel kann die Reibung zwischen mechanischen Teilen verringern und so den Lärm während des Betriebs reduzieren. Darüber hinaus kann das Sauberhalten beweglicher Teile verhindern, dass Schmutz und Ablagerungen den Betrieb des Geräts beeinträchtigen, was den Geräuschpegel weiter reduziert.
Zusammenfassend lässt sich sagen, dass der Geräuschpegel einer Laserschneidmaschine von vielen Faktoren beeinflusst wird. Durch Optimierung des Designs, Anpassung der Schneidparameter, Auswahl geeigneter Materialien, Verbesserung der Effizienz des Kühlsystems, wirksame Schalldämmungsmaßnahmen und gute Wartung kann der Lärm deutlich reduziert werden. Verbessern Sie den Komfort und die Sicherheit der Arbeitsumgebung.
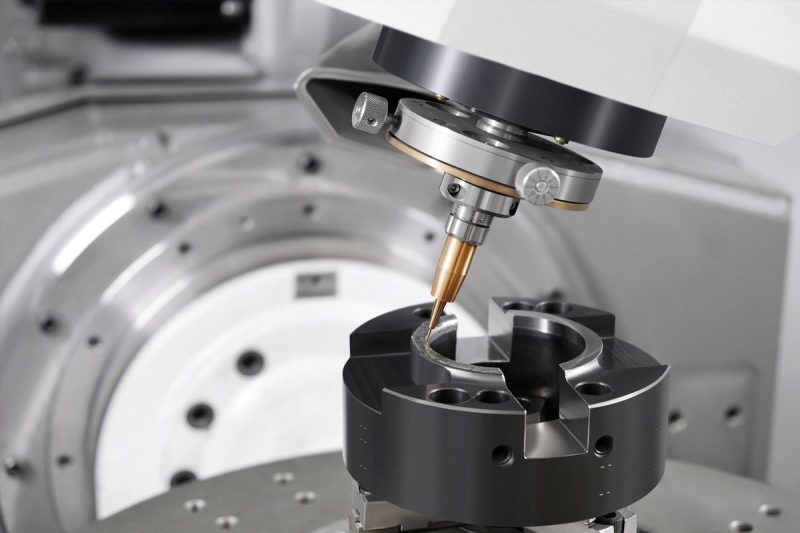
Gesundheits- und Sicherheitsprobleme
Der beim Betrieb der Laserschneidmaschine erzeugte Lärm beeinträchtigt nicht nur den Komfort der Arbeitsumgebung, sondern kann auch eine Gefahr für die Gesundheit und Sicherheit der Bediener darstellen. Im Folgenden finden Sie eine detaillierte Analyse der relevanten Gesundheits- und Sicherheitsprobleme:
Mögliche Gesundheitsrisiken im Zusammenhang mit der Belastung durch hohen Lärmpegel
Langfristige Belastung durch Lärm mit hoher Intensität kann zu einer Reihe von Gesundheitsproblemen führen. Die häufigste Auswirkung ist zunächst der Hörverlust, insbesondere der Hochfrequenz-Hörverlust, der sich allmählich verschlimmern kann, ohne dass man es bemerkt. Dauerhafte Lärmstimulation kann die Hörzellen im Ohr schädigen und zu irreversiblen Hörschäden führen. Darüber hinaus kann Lärm mit hoher Intensität auch Tinnitus verursachen, d. h., wenn keine äußere Schallstimulation vorliegt, ist immer noch ein Summen oder ein anderes Geräusch im Ohr zu hören. Dieses Symptom kann das tägliche Leben und die Arbeitseffizienz erheblich beeinträchtigen.
Neben Hörproblemen kann Lärm auch erhebliche Auswirkungen auf die psychische Gesundheit haben. Untersuchungen zeigen, dass langfristige Lärmbelastung zu psychischen Gesundheitsproblemen wie Stress, Angstzuständen und Depressionen führen kann. Lärm beeinträchtigt nicht nur die Konzentration bei der Arbeit und verringert die Produktivität, sondern kann auch die Schlafqualität beeinträchtigen und eine Reihe schlafbezogener Gesundheitsprobleme wie Müdigkeit und verminderte Immunität verursachen.
Arbeitsschutzbestimmungen im Zusammenhang mit Lärmbelastung am Arbeitsplatz
Um die Gesundheit der Arbeitnehmer zu schützen, haben viele Länder und Regionen Arbeitsschutzbestimmungen für die Lärmbelastung am Arbeitsplatz erlassen. Diese Bestimmungen legen in der Regel zulässige Belastungsgrenzwerte für Lärm fest, und wenn diese Grenzwerte überschritten werden, müssen die Arbeitgeber geeignete Maßnahmen zur Reduzierung des Lärms ergreifen. Diese Bestimmungen verlangen auch eine regelmäßige Überwachung des Lärmpegels am Arbeitsplatz und sehen entsprechende Gesundheitschecks vor, um lärmbedingte Gesundheitsprobleme frühzeitig zu erkennen.
Beispielsweise verlangt die US-amerikanische Arbeitsschutzbehörde OSHA von Arbeitnehmern, dass sie Lärmschutzmaßnahmen ergreifen oder geeignete persönliche Schutzausrüstung (wie Ohrenschützer und Ohrstöpsel) bereitstellen, wenn sie in einer Umgebung mit einem Lärmpegel von über 85 Dezibel arbeiten. Viele Unternehmen befolgen diese Vorschriften und führen häufig Lärmbelastungsbewertungen und Kontrollpläne durch, um sicherzustellen, dass die Arbeitsumgebung den Sicherheitsstandards entspricht.
Die Bedeutung von Lärmschutzmaßnahmen zum Schutz der Arbeitnehmer
Effektive Lärmschutzmaßnahmen sind für den Schutz der Gesundheit der Arbeitnehmer unerlässlich. Unternehmen sollten verschiedene Strategien zur Reduzierung des Lärmpegels am Arbeitsplatz ergreifen, beispielsweise:
- Designverbesserungen: Berücksichtigen Sie bei der Konstruktion und Anordnung der Geräte die Geräuschkontrolle und verwenden Sie hochwertige Materialien und Konstruktionsdesigns, um die Geräuschentwicklung zu reduzieren.
- Installieren Sie Schalldämmung: Durch die Verwendung von Schallschutzgehäusen und schallabsorbierenden Materialien können Sie die Geräuschentwicklung Ihrer Geräte erheblich reduzieren.
- Betriebsabläufe optimieren: Passen Sie Schneidparameter und Betriebsabläufe an, beispielsweise durch Reduzierung der Schneidgeschwindigkeit oder -leistung, um Vibrationen und Lärm zu verringern.
- Persönliche Schutzausrüstung: Stellen Sie den Mitarbeitern geeignete Ohrenschützer und Ohrstöpsel zur Verfügung, um sie vor Lärm mit hoher Intensität zu schützen.
- Regelmäßige Schulungen und Aufklärung: Bieten Sie Ihren Mitarbeitern Kenntnisse zum Thema Lärmschutz an, um ihr Verständnis für Lärmrisiken und ihr Bewusstsein für den Selbstschutz zu stärken.
Durch die Umsetzung der oben genannten Maßnahmen können Unternehmen nicht nur die Anforderungen der Arbeitsschutzbestimmungen erfüllen, sondern auch ein sichereres und komfortableres Arbeitsumfeld schaffen. Dies schützt nicht nur die Gesundheit der Arbeitnehmer, sondern verbessert auch die Arbeitszufriedenheit der Mitarbeiter und die Produktionseffizienz, wodurch letztendlich eine Win-Win-Situation für Unternehmen und Mitarbeiter entsteht.
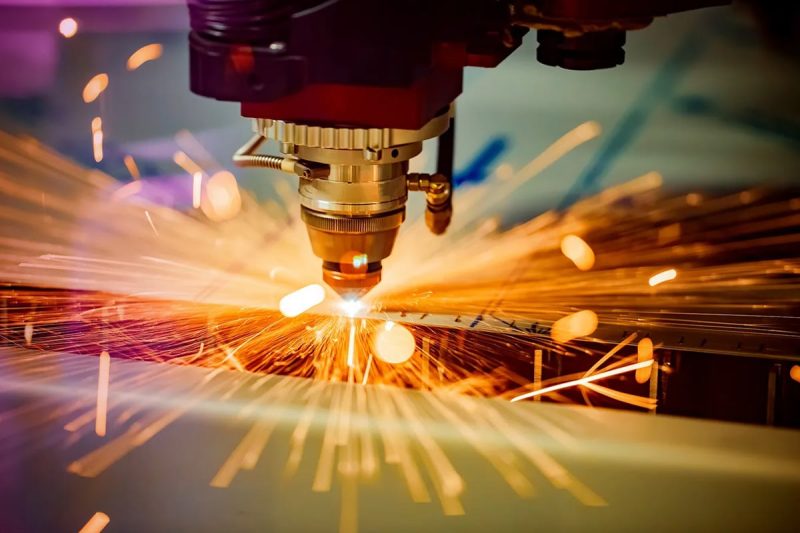
Rauschunterdrückungstechnologie
Die Geräuschreduzierungstechnologie spielt beim Betrieb von Laserschneidmaschinen eine wichtige Rolle. Im Folgenden finden Sie eine detaillierte Analyse mehrerer gängiger Technologien zur Geräuschreduzierung:
Schalldämmung
Ein Schallschutzgehäuse ist eine Struktur, die eine Geräuschquelle umgibt und die Ausbreitung von Schallwellen effektiv blockiert. Normalerweise kann der von den Betriebsteilen der Laserschneidmaschine (wie Motoren, Lüfter usw.) erzeugte Lärm durch ein Schallschutzgehäuse reduziert werden. Hochwertige Schallschutzgehäuse bestehen normalerweise aus mehreren Materialschichten, mit einer massiven Metallaußenschicht und schallabsorbierenden Materialien auf der Innenschicht, um eine gute Schalldämmung zu erreichen. Das Design des Schallschutzgehäuses muss Belüftung und Wärmeabgabe vollständig berücksichtigen, um Schäden am Gerät durch Überhitzung zu vermeiden.
Die Wirksamkeit der Schallschutzabdeckung hängt auch von ihrer Abdichtung ab. Eine gute Abdichtung kann das Austreten von Schallwellen verhindern. Darüber hinaus kann ein vernünftiges Design es den Bedienern auch bequem machen, tägliche Wartungs- und Reparaturarbeiten durchzuführen, ohne die Abdeckung demontieren zu müssen, wodurch sowohl der Geräuschreduzierungseffekt als auch die Benutzerfreundlichkeit berücksichtigt werden.
Schwingungsisolationssystem
Das Schwingungsisolationssystem reduziert Lärm hauptsächlich dadurch, dass es die Übertragung von Gerätevibrationen verringert. Wenn die Laserschneidmaschine läuft, können aufgrund der Bewegung mechanischer Teile starke Vibrationen entstehen. Diese Vibrationen werden über die Gerätebasis und den Boden übertragen, was zu einer Zunahme des Umgebungslärms führt. Durch die Installation von Schwingungsisolationspolstern oder Federstützen an der Unterseite des Geräts kann die Vibrationsübertragung wirksam reduziert werden.
Schwingungsisolationsmaterialien weisen normalerweise eine hohe Elastizität und Stoßdämpfungseigenschaften auf, die Schwingungsenergie absorbieren und dämpfen können. Ein gut konzipiertes Schwingungsisolationssystem kann auch die Stabilität der Ausrüstung verbessern, ihre Lebensdauer verlängern und die Wartungskosten senken. Darüber hinaus kann bei der Installation der Ausrüstung die Wahl eines geeigneten Installationsorts und Fundaments auch die Schwingungsisolationswirkung verbessern.
Schallabsorbierende Materialien
Die Verwendung schallabsorbierender Materialien ist eine weitere wirksame Technologie zur Geräuschreduzierung. Durch ihre poröse Struktur können schallabsorbierende Materialien Schallwellenenergie absorbieren und reflektierten und übertragenen Lärm reduzieren. Zu den üblichen schallabsorbierenden Materialien gehören Mineralwolle, Polyesterfaserplatten und Polyurethanschaum. Diese Materialien können an den Wänden, Böden oder Decken rund um die Laserschneidmaschine angebracht werden, um eine akustische Umgebung zu schaffen, die Lärm reduziert.
Bei der Auswahl schallabsorbierender Materialien sollten diese entsprechend ihrer Frequenzgangeigenschaften und den Spektrumeigenschaften der Geräuschquelle angemessen aufeinander abgestimmt werden. Unterschiedliche schallabsorbierende Materialien haben unterschiedliche Auswirkungen auf die Absorption von Geräuschen unterschiedlicher Frequenzen. Daher ist es sehr wichtig, Materialien entsprechend der tatsächlichen Situation auszuwählen und anzuordnen.
Regelmäßige Wartung und Schmierung
Regelmäßige Wartung und Schmierung sind wichtige Bestandteile für den normalen Betrieb der Geräte und auch entscheidend für die Reduzierung des Geräuschpegels. Verschleiß und Reibung beweglicher Teile können zusätzliche Geräusche verursachen, daher kann eine regelmäßige Inspektion und Wartung beweglicher Teile wie Führungen, Getriebe und Motoren das Betriebsgeräusch der Geräte effektiv reduzieren.
Durch die Verwendung des richtigen Schmiermittels können Reibung und Geräuschpegel verringert werden. Darüber hinaus kann das Sauberhalten mechanischer Teile und das Verhindern der Ansammlung von Staub und Schmutz die Betriebseffizienz der Geräte verbessern und unnötigen Lärm reduzieren. Regelmäßige Wartung kann potenzielle Probleme auch frühzeitig erkennen und hohe Geräuschpegel aufgrund von Geräteausfällen vermeiden.
Zusammenfassend lässt sich sagen, dass Technologien zur Geräuschreduzierung schalldichte Gehäuse, Schwingungsisolationssysteme, schallabsorbierende Materialien, regelmäßige Wartung und Schmierung usw. umfassen. Durch die kombinierte Verwendung dieser Technologien kann nicht nur der Geräuschpegel der Laserschneidmaschine effektiv reduziert, sondern auch die Leistung und Lebensdauer der Ausrüstung verbessert werden, wodurch eine sicherere und komfortablere Arbeitsumgebung für die Bediener geschaffen wird.
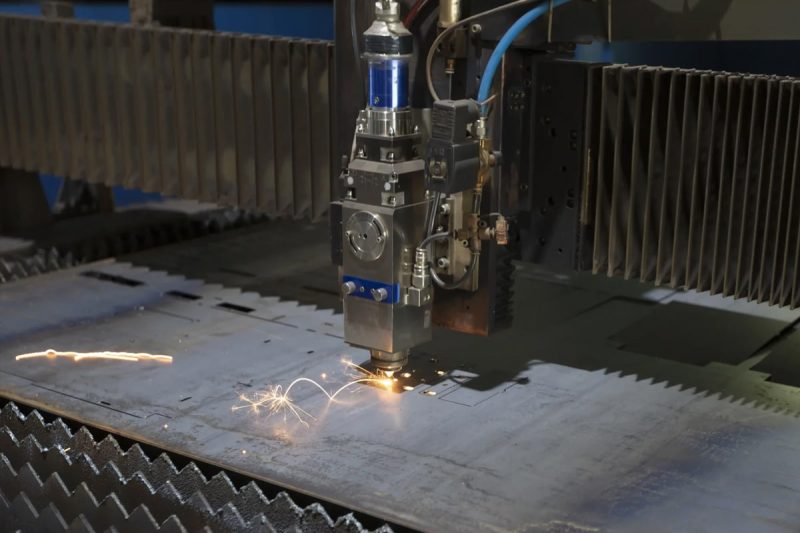
Zusammenfassen
Das Lärmproblem von Laserschneidmaschinen kann nicht ignoriert werden. Lärm beeinträchtigt nicht nur die Arbeitsumgebung der Bediener, sondern kann auch eine potenzielle Gefahr für ihre Gesundheit darstellen. Das Verständnis der Lärmquellen und ihrer Einflussfaktoren kann Unternehmen dabei helfen, wirksame Managementstrategien zu entwickeln. Durch die Umsetzung angemessener Lärmreduzierungstechnologien und Gesundheits- und Sicherheitsmaßnahmen kann die Betriebsumgebung erheblich verbessert und die Arbeitseffizienz und -sicherheit erhöht werden.
Durch die Aufrechterhaltung eines guten Gerätebetriebs und die Kombination moderner Geräuschreduzierungstechnologien wie Schallschutzgehäusen, Schwingungsisolationssystemen und schallabsorbierenden Materialien können Unternehmen den Geräuschpegel wirksam senken und einen ruhigeren und sichereren Arbeitsplatz schaffen. Gleichzeitig können regelmäßige Gerätewartung und -schmierung auch dazu beitragen, den Lärm zu reduzieren und die Gesamtleistung der Geräte zu verbessern.
Wenn Sie Fragen oder Wünsche zur Lärmminderung bei Laserschneidmaschinen haben, wenden Sie sich bitte an AccTek. Wir bieten Ihnen maßgeschneiderte Lösungen, um den effizienten Betrieb und die sichere Nutzung der Geräte zu gewährleisten und eine idealere Arbeitsumgebung für Ihr Unternehmen zu schaffen.
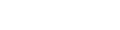
Kontaktinformationen
- [email protected]
- [email protected]
- +86-19963414011
- Nr. 3 Zone A, Industriegebiet Lunzhen, Stadt Yucheng, Provinz Shandong.
Holen Sie sich Laserlösungen