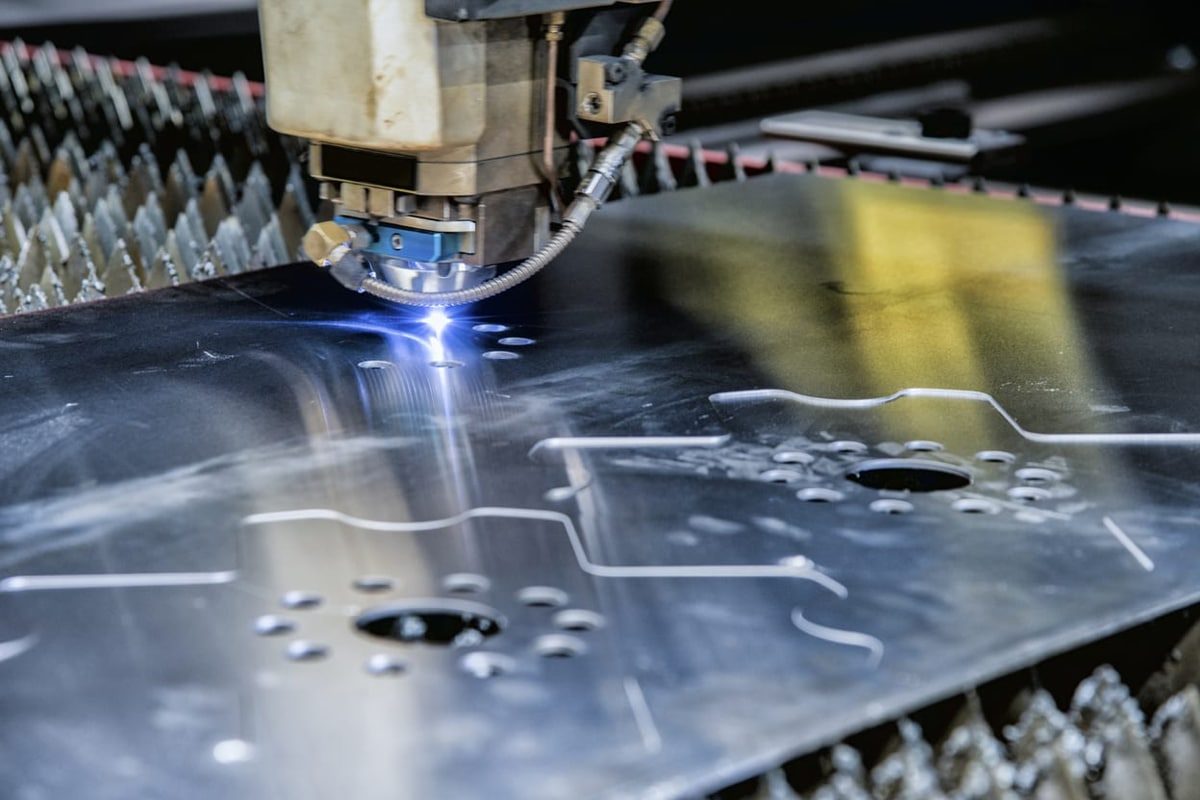
Laserschneiden: Optimierter Materialeinsatz und präzise Fertigung
In modern manufacturing, accuracy in manufacturing is very important. Enter laser cutting technology, a game-changer to optimize materials and streamline production processes. Laser cutting has a high degree of accuracy, so complex patterns and shapes can be created on a variety of materials. From metals to wood and plastics, the versatility of laser cutting has completely transformed traditional manufacturing methods, allowing for unprecedented levels of effectiveness and efficiency. In this article, we take a deep dive into the world of laser cutting, exploring its myriad applications, benefits, and its key role in shaping the future of precision production. Join us as we explore the transformative power of laser cutting and its impact on optimizing materials and raising the bar for precision manufacturing.
Inhaltsverzeichnis
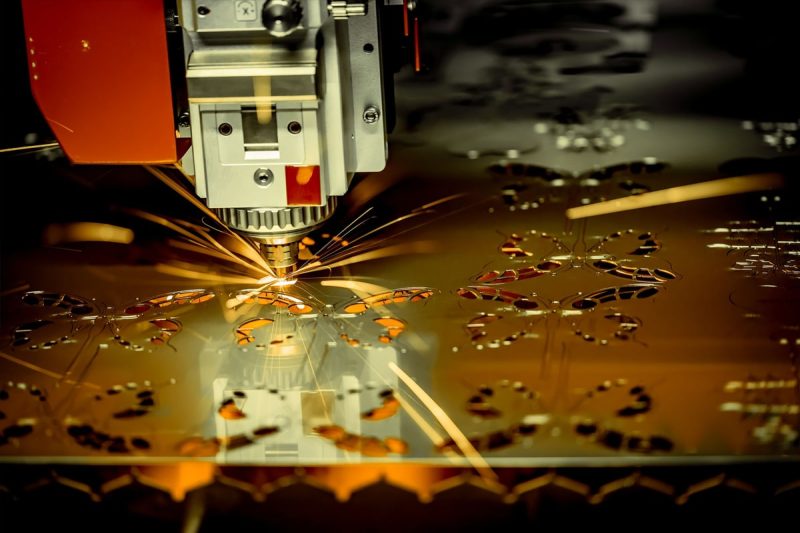
Introduction To Laser Cutting Technology
In the world of precision manufacturing, where even the smallest deviations can compromise quality, the accuracy of laser technology is very important. Laser schneiden technology operates on the principle of a focused laser beam precisely cutting or engraving materials. This process involves several key components: a laser source, a focusing mirror, the cutting material, and a computer control system to guide the movement of the laser beam. The basic principles of laser cutting technology are as follows:
- Focused beam: Laser cutting works by directing a highly focused beam onto the material surface. Focusing allows the laser generator to produce intense heat that melts, burns, or vaporizes materials along a designated cutting path.
- Material interaction: Different materials interact with the laser beam in different ways. Metals typically absorb laser energy, while non-metallic materials may reflect or partially absorb it. This variability allows for cutting a variety of materials, from metal and plastic to wood and fabric.
- Computer-controlled precision: Laser cutting is a digitally controlled process guided by computer-aided design (CAD) software. The software precisely determines cutting paths and parameters to ensure complex designs and shapes are accurately reproduced with minimal waste.
- Non-contact cutting: Unlike traditional methods such as sawing or milling, laser cutting is a non-contact process. The laser beam exerts no mechanical force on the material, reducing the risk of distortion or damage and enabling the production of complex, delicate components.
- Minimum heat-affected zone: Laser cutting minimizes the heat-affected zone (HAZ), which is the surrounding area where material properties may change due to heat exposure. This results in a clean, precise cut that benefits materials susceptible to heat damage.
By adjusting the digital design file to guide the computer control system, it can achieve extensive cutting depth and complexity, so that laser cutting can achieve effective and accurate manufacturing processes. In this article, we will further explore these principles.
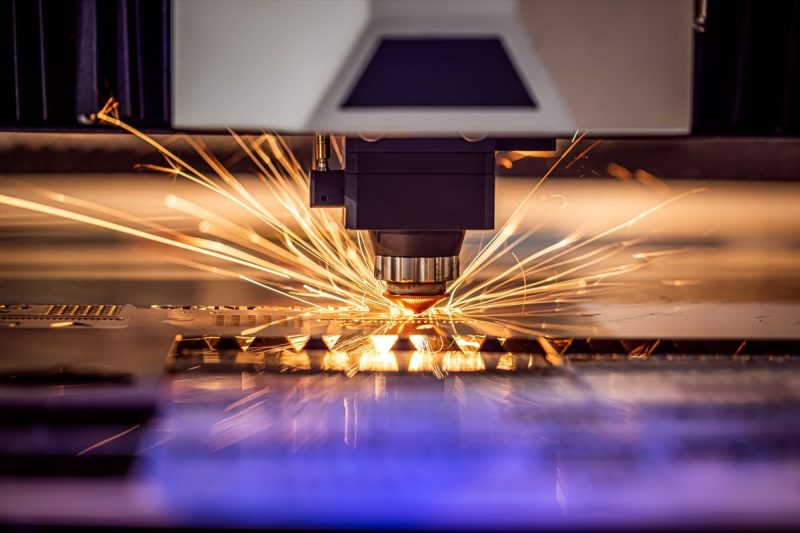
The Key Advantage Of Laser Cutting To Reduce Material Waste
How laser cutting technology is in terms of accuracy and accuracy, nested optimization, reduction of incision width, material flexibility, rapid production and design, less material treatment (reduced the possibility of material damage), prototype design and testing. Reduce material waste? The following will be explained for you:
Precise Cutting
Laserschneidmaschinen use high-powered lasers to precisely cut materials with incredible precision. This precision allows for a minimum margin or kerf width, which refers to the width of material removed by the cutting process. With laser cutting, cut widths can be as small as a few thousandths of an inch, significantly reducing material waste compared to traditional cutting methods like sawing or shearing. This precision ensures efficient use of materials, minimizing waste and optimizing production.
Verschachtelte Optimierung
Nested optimization software analyzes the shape of the parts to be cut and determines the most efficient way to arrange them on the material sheet, such as part geometry, size, quantity and material constraints. By intelligently nesting parts closely together, minimizing the space between them, this ensures that the entire surface area of the board is used efficiently. This is achieved by strategically positioning parts to reduce unused space between parts, thereby reducing the amount of wasted material.
Reduced Kerf Width
Reducing the kerf width in laser cutting involves narrowing the notch width, resulting in finer and more precise cuts. By minimizing the amount of material removed with each pass, laser cutting achieves greater efficiency in material utilization. This reduction in notch width ensures that more of the raw material is preserved, leading to a significant decrease in waste generation during the cutting process.
Material Flexibility
Material flexibility in laser cutting is integral to waste reduction. By accommodating a wide range of materials, laser cutting optimizes resource usage, minimizes setup times, maintains precision across materials, and facilitates customization and prototyping. This comprehensive approach ensures efficient production runs, reduced errors, and minimized waste generation throughout the manufacturing process.
Rapid Production And Design
Rapid production and design play a crucial role in helping laser cutting minimize material waste by facilitating efficient prototyping, on-demand manufacturing, customization, optimized production runs, and streamlined design iterations. This comprehensive approach ensures that the gap width is effectively reduced, leading to enhanced material utilization and waste reduction across various manufacturing processes.
Less Material Handling
Less material handling in laser cutting reduces the potential for material damage, thereby aiding in waste reduction. By minimizing the need to move or manipulate materials during the cutting process, laser cutting mitigates the risk of accidental damage or errors that could result in material waste. This streamlined approach ensures that materials remain intact and undamaged throughout the production process, maximizing their usability and minimizing waste generation.
Prototype Design And Test
An overview of prototyping and testing aspects supports laser cutting in reducing material waste by facilitating iterative design cycles, minimizing scrap, enabling customization, streamlining production processes, and optimizing resource utilization. This comprehensive approach ensures efficient material usage, contributing to waste reduction without redundancy.
In summary,Laser cutting offers a multi-faceted approach to minimizing material waste in manufacturing and streamlining the production process. These combined advantages ultimately enable efficient use of materials, making laser cutting an effective tool for reducing manufacturing waste.
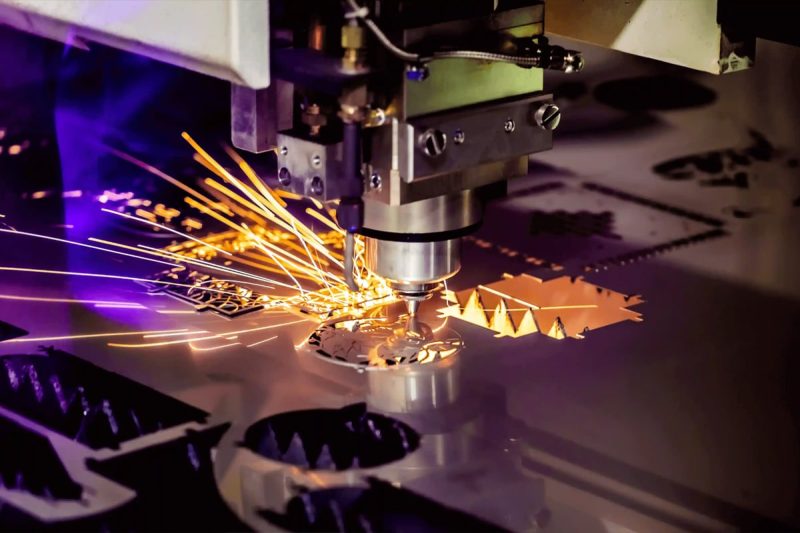
Other Advantages Of Laser Cutting In Material Utilization
In addition to the above advantages in terms of material use, laser cutting technology also has the advantages of complex design capabilities, minimum thermal influence areas, less tool wear, and capable of processing multiple materials. details as follows:
Complex Design Capabilities
Laser cutting excels at cutting complex shapes and geometries with high precision and can cut curves with extremely high precision. This feature enables designers to create complex designs and is especially beneficial for complex designs that require smooth curves or organic shapes. By accurately following the contours of the design, maximizing the use of available material, laser cutting minimizes the material waste associated with straight cuts or manual shaping.
The Smallest Heat Influence Area
Laser cutting technology has a minimal heat-affected zone, maintaining the structural integrity of the material and minimizing the need for post-processing. Traditional cutting methods, such as plasma or flame cutting, generate large amounts of heat, causing the material to warp or deform around the cut area. The minimal heat-affected zone of laser cutting minimizes this warping, ensuring the material retains its original shape and size with minimal additional finishing or refinement.
Reduce Tool Wear
Since laser cutting does not rely on physical tools that degrade with use, such as blades or drills, the lifespan of the cutting equipment is significantly extended. This prolonged tool lifespan reduces the frequency of tool replacements, minimizing material waste associated with discarded or worn-out tools. With minimal tool wear, the risk of tool-related defects, such as chipping or dulling, is mitigated, ensuring that each cut contributes to the final product with minimal material waste.
Machining Multiple Materials
Laser cutting technology is capable of cutting a variety of materials, including metal, plastic, wood, glass and composites. This versatility enables manufacturers to use one machine to cut different materials, eliminating the need for separate cutting equipment for each material type. By consolidating the cutting process into a single machine, manufacturers can minimize the material waste associated with setup time, tool changes and maintenance of multiple machines.
These capabilities can speed up complex designs with tight tolerances, maintain material integrity, extend tool life, and adapt to different material types to improve material utilization. Therefore, laser cutting maximizes the efficiency of material use in various industries, helping to save costs and improve product quality.
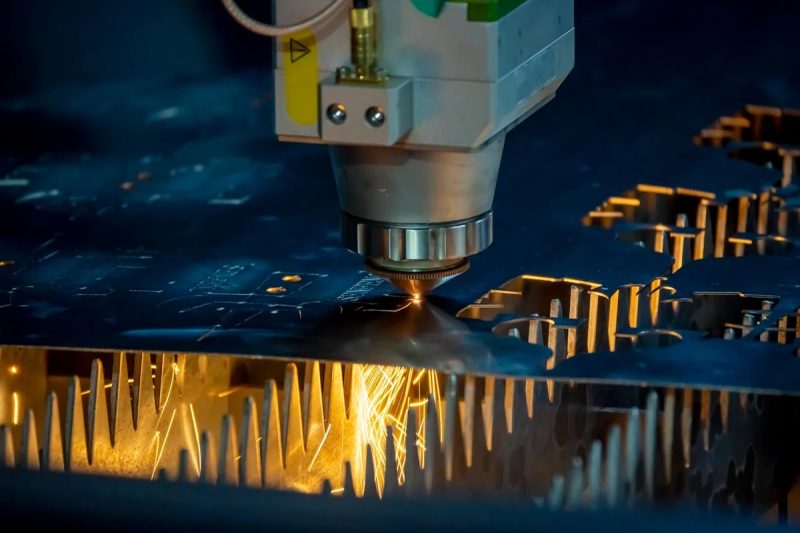
Application Of Laser Cutting In Cross-Industry
Laser-cutting technology finds diverse applications across various industries due to its precision, versatility, and efficiency. Here are some examples:
- Manufacturing and Fabrication: Laser cutting is extensively used in manufacturing and fabrication for cutting and shaping various materials such as metals (steel, aluminum, titanium), plastics, and composites. It is employed in industries producing automotive components, aerospace parts, machinery, consumer electronics, and more.
- Automotive Industry: Laser cutting is utilized for producing intricate parts and components in the automotive industry. It is used for cutting sheet metal for car bodies, chassis, exhaust systems, engine components, and interior fittings. Laser-cut parts often require minimal post-processing, reducing production time and costs.
- Aerospace and Defense: In aerospace and defense applications, laser cutting technology is employed for manufacturing lightweight and complex parts with high precision. It is used for cutting materials such as aluminum, titanium, and carbon fiber composites for aircraft components, missile systems, and defense equipment.
- Electronics and Consumer Goods: Laser cutting is utilized in the electronics industry for cutting and engraving various materials such as PCBs (Printed Circuit Boards), acrylics, and plastics for electronic enclosures, smartphone cases, laptop components, and decorative items. It offers precise cutting and marking capabilities for intricate designs.
- Medical Devices: Laser-cutting technology is used in the medical device industry for manufacturing precision components for surgical instruments, implants, medical devices, and diagnostic equipment. It enables the production of small, intricate parts with tight tolerances, critical for medical applications.
- Textile and Apparel: Laser cutting is employed in the textile and apparel industry for cutting fabrics, leather, and synthetic materials with high precision. It allows for intricate patterns, designs, and customization in clothing, footwear, accessories, and upholstery.
- Architecture and Interior Design: Laser cutting is utilized in architecture and interior design for creating decorative elements, signage, architectural models, and intricate patterns in building facades, wall panels, furniture, and lighting fixtures. It enables designers to translate complex designs into precise, customized products.
- Art and Crafts: Laser cutting technology is popular in the art and crafts community for creating intricate artworks, sculptures, jewelry, and decorative items. Artists and craftsmen use laser cutting to work with various materials such as wood, acrylic, paper, and glass, allowing for precise detailing and intricate designs.
These are just a few examples of the wide-ranging applications of laser cutting technology across industries. Its versatility and precision make it a valuable tool for enhancing productivity, efficiency, and creativity in diverse fields.
Zusammenfassen
The future of laser cutting technology helps to achieve significant progress, which is because the driver is constantly focusing on optimizing the use of materials and enhancing precise production capacity. With the efficiency of the industry’s demand, more and more flexibility, and sustainability, it is expected that laser cutting will play a key role in meeting these continuous development needs.
Optimized material utilization and precise production can help you maximize performance and minimize costs. If you need to help your company choose a laser cutting machine, we are always ready to provide your application with the best cutting solution. Contact AccTek-Laser immediately to start!
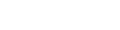
Kontaktinformationen
- [email protected]
- [email protected]
- +86-19963414011
- Nr. 3 Zone A, Industriegebiet Lunzhen, Stadt Yucheng, Provinz Shandong.
Holen Sie sich Laserlösungen