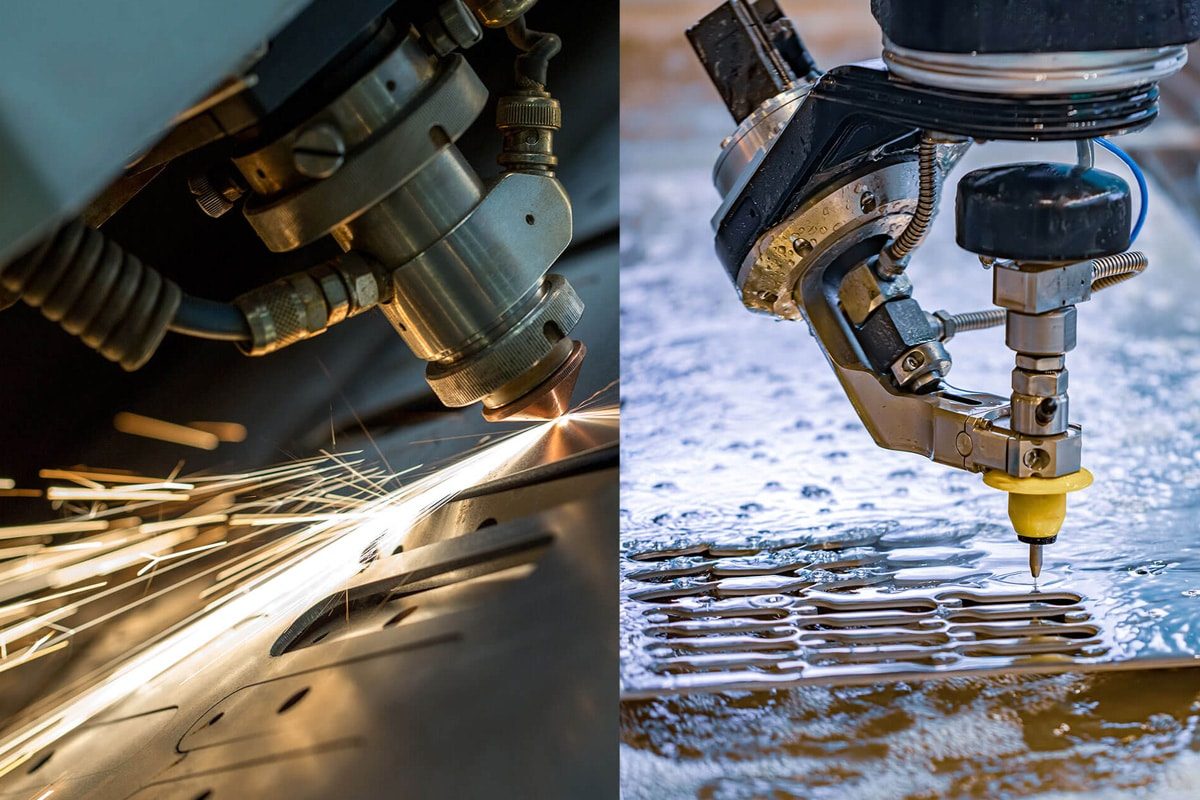
Laserschneiden vs. Wasserstrahlschneiden
In der modernen Fertigungs- und Verarbeitungsindustrie sind Laserschneiden und Wasserstrahlschneiden zwei beliebte hochpräzise Schneidtechnologien, die bei komplexen Verarbeitungsanforderungen in verschiedenen Branchen weit verbreitet sind. Aufgrund ihrer überlegenen Leistung und Vielseitigkeit sind beide Technologien die bevorzugte Lösung zum Schneiden einer Vielzahl von Materialien. Jede Technologie hat ihre einzigartigen Eigenschaften, Vorteile und Einschränkungen, um den Schneidanforderungen verschiedener Materialien gerecht zu werden, von Metallen und Kunststoffen bis hin zu Verbundwerkstoffen. Die Wahl der geeigneten Schneidmethode kann nicht nur die Verarbeitungseffizienz verbessern, sondern auch die Produktqualität und die Produktionskosten erheblich beeinflussen.
In diesem Artikel werden die Funktionsprinzipien des Laserschneidens und des Wasserstrahlschneidens im Detail analysiert und ihre spezifische Leistung in Bezug auf Schnittgenauigkeit, Materialanpassungsfähigkeit, Betriebskosten, Umweltschutz und Anwendungsszenarien untersucht. Durch den Vergleich dieser Schlüsselfaktoren erhalten Sie ein klareres Verständnis der Anwendungsszenarien und des potenziellen Werts dieser beiden Technologien und können so in der tatsächlichen Produktion fundiertere Entscheidungen treffen.
Inhaltsverzeichnis
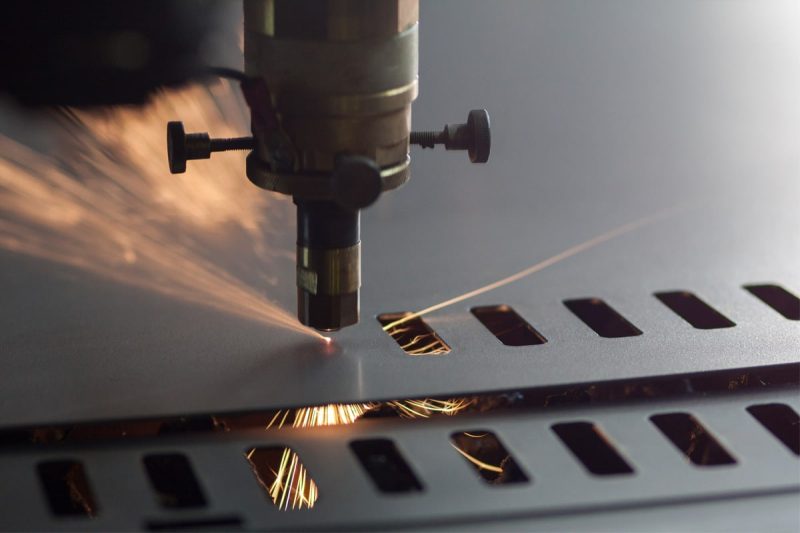
Einführung zum Laserschneiden
Laserschneiden ist das fortschrittlichste und am weitesten verbreitete Schneidverfahren in der modernen Fertigungstechnologie. Dabei wird ein Laserstrahl mit hoher Energiedichte verwendet, um Materialien mit hoher Präzision zu bearbeiten, und in vielen Branchen ist es als „unsichtbares Messer“ bekannt. Im Folgenden werden sein Funktionsprinzip, seine einzigartigen Vorteile und seine Grenzen erläutert.
Prinzip des Laserschneidens
Beim Laserschneiden kommt es auf die hohe Energie und Präzision von Lasern an. Der grundlegende Prozess kann in die folgenden Hauptschritte unterteilt werden:
- Lasererzeugung: Das Herzstück des Laserschneidens ist der Lasergenerator, der elektrische oder chemische Energie in einen hochenergetischen Strahl umwandelt. Zu den gängigen Lasertypen gehören CO2-Lasergeneratoren, Faserlasergeneratoren und Festkörperlasergeneratoren. Verschiedene Typen sind für unterschiedliche Materialien und Schneidanforderungen geeignet.
- Strahlübertragung: Der Laser wird über eine Glasfaser oder einen Reflektor zum Schneidkopf übertragen. Dieser Übertragungsprozess erfordert eine präzise Kalibrierung und hochwertige optische Komponenten, um die Konzentration und Stabilität der Strahlenergie zu gewährleisten.
- Fokussierung: Nachdem der Laser durch die Linse fokussiert wurde, konzentriert sich die Energie stark auf der Oberfläche des Materials und bildet einen Laserpunkt mit kleinem Durchmesser und hoher Temperatur. Diese extrem hohe Energiedichte kann das Material sofort lokal schmelzen oder verdampfen und so ein Schneiden ermöglichen.
- Materialinteraktion: Der fokussierte Laserstrahl kommt mit dem Material in Kontakt und führt bei Erhitzung zu einer chemischen Reaktion, bei der das Material schmilzt, verdampft oder schnell verbrennt. Mit diesem Verfahren können Schnitttiefe und -verlauf präzise gesteuert werden, um die Schnittqualität sicherzustellen.
- Hilfsgas: Hilfsgas (wie Sauerstoff, Stickstoff oder Druckluft) wird durch den Schneidkopf ausgestoßen und arbeitet in Verbindung mit dem Laserstrahl. Einerseits kann das Gas die Schmelze wegblasen, um eine glatte Schnittkante zu erhalten; andererseits kann der Sauerstoff auch mit dem Material reagieren, um die Schneidleistung weiter zu verbessern.
Vorteile des Laserschneidens
Aufgrund seiner Präzision und Effizienz ist das Laserschneiden die ideale Wahl für eine Vielzahl industrieller Verarbeitungsanforderungen:
- Präzision und Genauigkeit: Laserschneiden ist für seine ultrahohe Präzision bekannt, die Schnitttoleranzen im Mikronbereich ermöglicht und die strengen Anforderungen hochpräziser Branchen wie der Elektronikfertigung und der Luft- und Raumfahrt erfüllt. Laser eignen sich auch hervorragend zum Schneiden komplexer Muster oder winziger Teile.
- Schnittgeschwindigkeit: Die Laserschneidgeschwindigkeit ist deutlich höher als bei herkömmlichen Schneideverfahren, insbesondere bei der Bearbeitung dünner Plattenmaterialien ist die Effizienz besonders herausragend. Es verkürzt den Produktionszyklus erheblich und eignet sich besonders für Massenproduktionsumgebungen.
- Vielseitigkeit: Das Laserschneiden eignet sich für eine Vielzahl von Materialien, darunter auch Metalle (Stahl, Edelstahl, Aluminium), Nichtmetalle (Kunststoff, Holz, Glas) und mehr. Unabhängig von Härte, Dicke oder Form des Materials kann das Laserschneiden problemlos damit umgehen.
- Minimaler Materialabfall: Der Schneidschlitz des Laserstrahls ist extrem schmal und greift nur minimal in die Materialoberfläche ein, wodurch der Materialabfall minimiert wird. Dies senkt nicht nur die Produktionskosten, sondern schont auch die Umwelt.
- Berührungsloser Prozess: Laserschneiden ist ein berührungsloser Verarbeitungsprozess. Es besteht kein direkter Kontakt zwischen Schneidkopf und Material, wodurch mechanische Belastungen und Verformungen der Schnittfläche vermieden und die Integrität des Materials geschützt werden.
- Automatisierung und Flexibilität: Die Laserschneidtechnologie ist mit CNC-Systemen kompatibel und ermöglicht hochautomatisierte Abläufe. Ob Massenproduktion oder individuelle Kleinserienfertigung – das Laserschneiden ist flexibel handhabbar und bietet eine hohe Anpassungsfähigkeit.
Einschränkungen beim Laserschneiden
Obwohl das Laserschneiden viele Vorteile bietet, gibt es in einigen Anwendungsszenarien dennoch gewisse Einschränkungen:
- Wärmeeinflusszone: Laserschneiden ist ein thermischer Verarbeitungsprozess, und hohe Temperaturen können zu einer Verhärtung oder Verformung der Materialkanten führen. Dieses Problem ist besonders beim Schneiden dünner Materialien von Bedeutung, aber die Auswirkungen der Wärmeeinflusszone können durch die Optimierung von Parametern wie Laserleistung und Schnittgeschwindigkeit wirksam gemildert werden.
- Materialbeschränkungen: Bei stark reflektierenden Materialien (wie Kupfer und Aluminium) kann es beim Laserschneiden zu einer verringerten Effizienz oder einem instabilen Schnitt kommen. Moderne Faserlasergeneratoren haben diese Einschränkung jedoch durch verbesserte Wellenlängen- und Energiesteuerungstechnologie allmählich überwunden.
- Anschaffungskosten: Die Anschaffungs- und Installationskosten von Laserschneidanlagen sind vor allem für kleine und mittlere Unternehmen relativ hoch. Auf lange Sicht zahlt sich diese Anfangsinvestition jedoch aufgrund geringer Betriebskosten und hoher Produktivität in der Regel schnell aus.
- Sicherheitsprobleme: Die hohe Energieabgabe von Lasern birgt gewisse Sicherheitsrisiken, wie etwa mögliche Augen- und Hautschäden. Die meisten modernen Laserschneidgeräte sind jedoch mit strengen Sicherheitsvorrichtungen ausgestattet, um die Sicherheit des Bedieners zu gewährleisten.
Aus der obigen Analyse ist ersichtlich, dass das Laserschneiden aufgrund seiner Präzision, Geschwindigkeit und Flexibilität zu einer unersetzlichen und wichtigen Technologie in der industriellen Verarbeitung geworden ist. Bei der Auswahl eines Schneidverfahrens eignet sich das Laserschneiden besonders für Szenarien, die hohe Effizienz und Präzision erfordern.
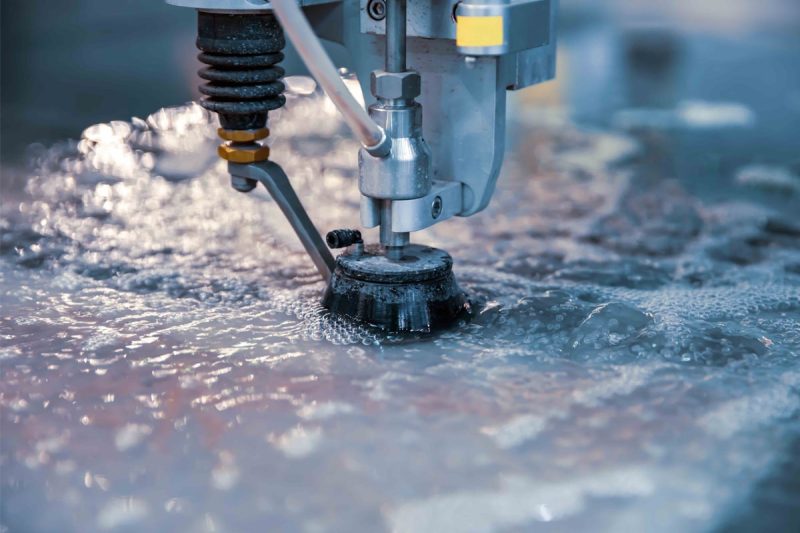
Einführung in das Wasserstrahlschneiden
Wasserstrahlschneiden ist ein Kaltschneideverfahren, bei dem Materialien durch die Kombination von Hochdruckwasser und Schleifmitteln getrennt werden. Als effiziente und umweltfreundliche Verarbeitungstechnologie wird das Wasserstrahlschneiden häufig in Branchen eingesetzt, in denen eine präzise Verarbeitung und das Schneiden mehrerer Materialien erforderlich ist. Im Folgenden werden die Prinzipien, Vorteile und Einschränkungen im Detail vorgestellt.
Prinzip des Wasserstrahlschneidens
- Wasserdruck: Die Hochdruckpumpe ist eines der Kerngeräte beim Wasserstrahlschneiden. Sie erzeugt einen Ultrahochdruck-Wasserstrom, indem sie normales Wasser auf 3000–4000 bar oder sogar noch mehr Druck bringt. Dieser starke Druck ist die Grundlage des Schneidprozesses.
- Schleifmittelzugabe: Während des Schneidvorgangs werden dem Wasserstrom normalerweise Schleifmittel (z. B. Granatapfelsand) zugesetzt, um die Schneidfähigkeit zu verbessern. Durch die Zugabe von Schleifmitteln können Wasserstrahlen härtere Materialien wie Metall, Glas und Stein schneiden.
- Düsenantrieb: Ein Hochdruckwasserstrahl wird mit sehr hoher Geschwindigkeit durch die Düse gespritzt und bildet einen Hochgeschwindigkeitsschneidstrahl. Diese Düsen bestehen aus verschleißfesten Materialien (wie Wolframkarbid oder Diamant), um ihre Haltbarkeit und Stabilität zu gewährleisten.
- Materialinteraktion: Hochgeschwindigkeitswasserfluss und Schleifmittel wirken gemeinsam auf die Oberfläche des Materials, und die kinetische Energie des Wasserflusses und die Schleifwirkung der Schleifmittel entfernen das Material schnell, um den Schnitt abzuschließen.
- CNC-Steuerung: Durch die Kombination von Wasserstrahlschneiden und einem CNC-System ist eine präzise Steuerung des Schneidwegs und der Geschwindigkeit möglich, sodass eine Anpassung an komplexe Schneidanforderungen wie die Bearbeitung von Kurven, speziell geformten Mustern oder hochpräzisen Teilen möglich ist.
Vorteile des Wasserstrahlschneidens
Das Wasserstrahlschneiden eignet sich aufgrund seiner einzigartigen Prozesseigenschaften für viele Anwendungsszenarien:
- Kaltschneideverfahren: Im Gegensatz zum Laser- oder Plasmaschneiden entstehen beim Wasserstrahlschneiden keine hohen Temperaturen, sodass keine Wärmeeinflusszone im Material entsteht. Die physikalischen Eigenschaften des Materials (wie Härte und Zähigkeit) ändern sich durch das Schneiden nicht, was sich sehr gut für die Verarbeitung wärmeempfindlicher Materialien eignet.
- Vielseitigkeit: Wasserstrahlschneiden ist für fast alle Materialien geeignet, darunter Metalle (wie Stahl und Aluminium), Nichtmetalle (wie Glas, Stein und Keramik), Verbundwerkstoffe (wie Kohlefaser) usw. Egal, ob es sich um weiche oder harte Materialien handelt, Wasserstrahlen können es bearbeiten.
- Dickenfähigkeit: Die Dickenfähigkeit des Wasserstrahlschneidens ist beeindruckend. Es können über 30 cm dicke Materialien geschnitten werden, was von anderen Schneidverfahren nicht erreicht wird, insbesondere bei der Verarbeitung ultradicker Materialien.
- Umweltvorteile: Beim Wasserstrahlschneiden werden hauptsächlich Wasser und natürliche Schleifmittel als Medien verwendet, es entstehen keine schädlichen Gase oder chemischen Abfälle und es ist ein umweltfreundliches Verarbeitungsverfahren. Darüber hinaus kann Abwasser nach der Behandlung recycelt werden, was die Umweltbelastung weiter verringert.
- Kantenqualität: Die Schnittfläche beim Wasserstrahlschneiden ist glatt und gratfrei, eine zusätzliche Nachbearbeitung ist in der Regel nicht erforderlich. Dies verbessert die Produktionseffizienz und senkt gleichzeitig die Produktionskosten.
- Berührungsloser Prozess: Das Wasserstrahlschneiden ist ein berührungsloses Bearbeitungsverfahren, bei dem das Material nicht mechanisch beansprucht wird. Dadurch werden Materialverformungen oder mechanische Beschädigungen vermieden und Schnittgenauigkeit und -qualität sichergestellt.
Einschränkungen beim Wasserstrahlschneiden
Obwohl das Wasserstrahlschneiden viele Vorteile bietet, unterliegt es unter bestimmten Bedingungen dennoch gewissen Einschränkungen:
- Geringere Geschwindigkeit: Die Schnittgeschwindigkeit beim Wasserstrahlschneiden ist geringer als beim Laserschneiden, insbesondere bei der Bearbeitung dünner Materialien. Dieser Unterschied ist besonders deutlich. Daher ist das Wasserstrahlschneiden möglicherweise nicht die beste Wahl in Szenarien, in denen eine hocheffiziente Produktion erforderlich ist.
- Kosten für Schleifmittel: Der Verbrauch von Schleifmitteln (z. B. Granat) ist einer der größten Betriebskosten beim Wasserstrahlschneiden. Insbesondere beim Schneiden harter Materialien steigt der Verbrauch von Schleifmitteln erheblich an, was wiederum die Gesamtverarbeitungskosten erhöht.
- Materialhandhabung: Das beim Hochdruckwasserschneiden entstehende Abwasser enthält häufig Schleifmittel und Schneidrückstände und erfordert eine spezielle Behandlung, bevor es abgeleitet oder recycelt werden kann. Dieser Prozess erhöht die Geräte- und Betriebskosten.
- Präzision: Im Vergleich zum Laserschneiden ist die Präzision des Wasserstrahlschneidens etwas geringer. Insbesondere bei der Bearbeitung komplexer Muster oder winziger Teile kann es schwierig sein, die Präzision des Laserschneidens zu erreichen. Für die meisten routinemäßigen Bearbeitungsanforderungen ist die Genauigkeit des Wasserstrahlschneidens jedoch immer noch ausreichend.
Das Wasserstrahlschneiden nimmt aufgrund seiner Umweltverträglichkeit, seines Kaltschnitts und seiner Vielseitigkeit eine wichtige Stellung in der industriellen Verarbeitung ein. Es ist eine unersetzliche Technologiewahl, insbesondere in Szenarien, in denen dicke oder wärmeempfindliche Materialien geschnitten werden müssen. Durch die Optimierung der Schneidparameter und Materialhandhabungsmethoden kann das Wasserstrahlschneiden die Effizienz und Anwendbarkeit weiter verbessern und bietet mehr Möglichkeiten für die moderne Fertigung.
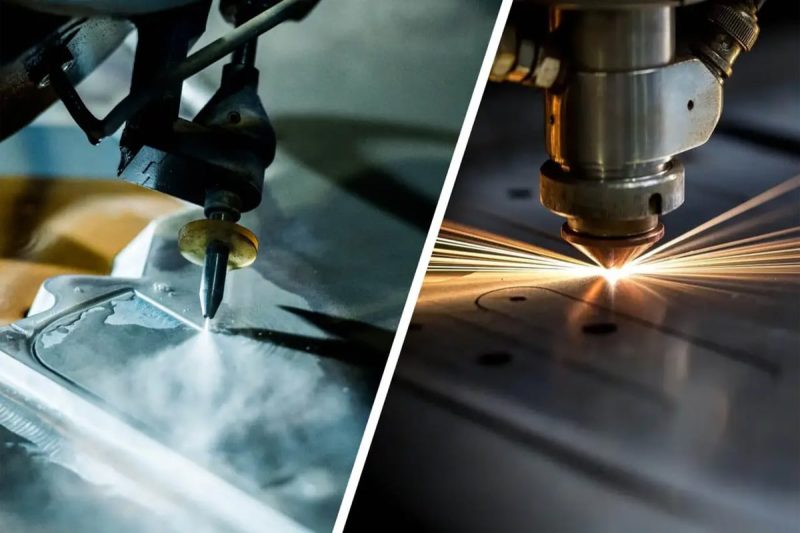
Vergleichende Analyse
In diesem Abschnitt besprechen wir ausführlich die Unterschiede zwischen Laserschneiden und Wasserstrahlschneiden in mehreren wichtigen Dimensionen, darunter Genauigkeit, Schnittgeschwindigkeit, Materialvielseitigkeit, Kosten, Umweltauswirkungen und Kantenqualität.
Präzision und Genauigkeit: Laserschneiden ist für seine hohe Präzision bekannt und eignet sich besonders für Bereiche, die Präzisionsbearbeitung erfordern, wie etwa Luft- und Raumfahrt, Elektronikfertigung und Schmuckverarbeitung. Seine Schnittgenauigkeit kann bis in den Mikrometerbereich reichen, sodass komplexe Muster und detaillierte Designs problemlos fertiggestellt werden können. Diese Funktion macht es in Anwendungen, die hohe Genauigkeit und Wiederholbarkeit erfordern, dominant. Obwohl Wasserstrahlschneiden ebenfalls eine hohe Präzision aufweist, ist es aufgrund der physikalischen Eigenschaften seines Schneidstrahls bei der Verarbeitung wundervoller Details und komplexer Muster etwas weniger effektiv als Laserschneiden. Daher ist Laserschneiden für Aufgaben, die eine höhere Präzision erfordern, die bessere Wahl.
Schnittgeschwindigkeit und Effizienz: Die Geschwindigkeit des Laserschneidens bietet erhebliche Vorteile beim Schneiden dünner und mitteldicker Materialien. Seine effiziente Schneidleistung kann die Produktionseffizienz, insbesondere in der Massenproduktion, erheblich verbessern. Im Vergleich dazu ist das Wasserstrahlschneiden aufgrund seines Kaltschneideprozesses und der Notwendigkeit, Schleifmittel hinzuzufügen, langsamer, insbesondere beim Schneiden dünnerer Materialien. Die Schneidfähigkeiten von Wasserstrahlen funktionieren jedoch gut bei der Bearbeitung extrem dicker Materialien, dies ist jedoch nur für bestimmte Szenarien geeignet. In den meisten industriellen Anwendungen ist das Laserschneiden effizienter.
Materialvielfalt: Das Wasserstrahlschneiden bietet große Vorteile bei der Materialanpassung und schneidet nahezu alle Arten von Materialien, darunter hochreflektierende Metalle, Glas, Keramik und Verbundwerkstoffe. Dies macht es zu einem sehr vielseitigen Schneidwerkzeug. Das Laserschneiden eignet sich jedoch auch gut für eine Vielzahl von Materialien und kann problemlos Metalle (wie Stahl, Edelstahl und Aluminium) und Nichtmetalle (wie Kunststoffe, Holz und Textilien) schneiden. Obwohl das Laserschneiden bei der Verarbeitung hochreflektierender Materialien (wie Kupfer und Aluminium) zusätzliche Anpassungen erfordert, hat die Entwicklung moderner Lasertechnologie (wie Faserlasergeneratoren) die Schneideffizienz und -qualität bei diesen Materialien erheblich verbessert. Insgesamt ist das Laserschneiden für die meisten Metall- und allgemeinen Materialverarbeitungsanforderungen eine effizientere und wirtschaftlichere Wahl.
Kosten: Die Anfangsinvestition in Laserschneidanlagen ist höher, insbesondere bei Hochleistungslasergeneratoren für den industriellen Einsatz. Aufgrund der schnellen Verarbeitungsfähigkeiten und der geringeren Betriebskosten (wie Energieverbrauch und Wartungskosten) ist es jedoch im langfristigen Einsatz wirtschaftlicher. Darüber hinaus verfügt das Laserschneiden über einen hohen Automatisierungsgrad und seine hohe Kompatibilität mit CNC-Systemen kann die Arbeitskosten weiter senken. Im Vergleich dazu ist die Anfangsinvestition in Wasserstrahlschneidanlagen etwas niedriger, aber die Kosten für Schleifmittel sind höher. Insbesondere bei der Produktion im großen Maßstab erhöht der kontinuierliche Verbrauch von Schleifmitteln die Betriebskosten erheblich. Daher ist das Laserschneiden insgesamt besser für Unternehmen geeignet, die eine langfristige und großvolumige Produktion benötigen.
Umweltauswirkungen: Obwohl beim Laserschneiden eine gewisse Wärmemenge entsteht und möglicherweise zusätzliche Abgasbehandlungsgeräte erforderlich sind, sind moderne Industrieanlagen normalerweise mit einem vollständigen Filtersystem ausgestattet, um thermische Effekte und schädliche Gasemissionen zu minimieren. Im Gegensatz dazu erzeugt das Wasserstrahlschneiden als Kaltschneideverfahren keine Wärme und hat keinen Einfluss auf die physikalischen Eigenschaften des Materials, sodass es hinsichtlich der Umweltleistung mehr Vorteile bietet. Das beim Wasserstrahlschneiden entstehende Abwasser und die Schleifmittelrückstände erfordern jedoch eine spezielle Behandlung, da sie sonst die Umwelt verschmutzen können. Dies macht das Laserschneiden in der modernen industriellen grünen Fertigung, insbesondere in Branchen, die sich auf Umweltschutz und saubere Produktion konzentrieren, wichtiger.
Kantenqualität: Sowohl Laserschneiden als auch Wasserstrahlschneiden weisen eine hervorragende Schnittkantenqualität auf, aber Laserschneiden kann aufgrund seines extrem feinen Strahlfokus und seiner gut steuerbaren Schnittbahn sehr glatte Kanten erzielen, was für Präzisionskomponenten und Verarbeitungsanforderungen geeignet ist, die hohe Ästhetik erfordern. Wasserstrahlschneiden hat keine Wärmeeinflusszone, daher ist die Schnittkante relativ glatt und erfordert keine zusätzliche Verarbeitung. Unter den doppelten Anforderungen von hoher Geschwindigkeit und hoher Präzision schneidet Laserschneiden jedoch besser ab, insbesondere bei der Verarbeitung mitteldünner Materialien und hochpräziser Teile.
Thermischer Effekt: Aufgrund der hohen Temperaturen, die beim Laserschneiden entstehen, kann sich an der Schnittkante eine Wärmeeinflusszone (WEZ) bilden, die zu einer Verhärtung oder Verformung der Materialkante führen kann. Moderne Lasergeräte können diesen Effekt durch Optimierung der Schneidparameter (wie Leistung, Geschwindigkeit und Gasfluss) erheblich reduzieren, sodass thermische Effekte bei der Verarbeitung der meisten Materialien fast keinen Einfluss haben. Wasserstrahlschneiden hat überhaupt keine thermischen Effekte, was es bei der Verarbeitung wärmeempfindlicher Materialien wie Glas, Keramik oder Verbundwerkstoffen noch vorteilhafter macht. Für die meisten Metallmaterialien und industriellen Anwendungen sind jedoch die Effizienz und Präzision des Laserschneidens besser geeignet.
Umwelt- und Sicherheitsaspekte: Beim Laserschneiden muss besonders auf die Sicherheit der Laserstrahlung geachtet werden. Moderne Lasergeräte sind jedoch in der Regel mit umfassenden Sicherheitsvorkehrungen (wie Schutzabdeckungen und Strahlenschutz) ausgestattet, um die Betriebssicherheit zu gewährleisten. Andererseits erfordert das Wasserstrahlschneiden eine ordnungsgemäße Behandlung von Abwasser und Schleifrückständen, da es sonst zu Umweltverschmutzung kommen kann. Angesichts des zunehmenden Fokus auf Umweltschutz in der modernen Fertigung kann diese Eigenschaft die Anwendung der Wasserstrahltechnologie einschränken.
Durch einen umfassenden Vergleich von Laserschneiden und Wasserstrahlschneiden wird deutlich, dass Laserschneiden klare Vorteile in Bezug auf Präzision, Schnittgeschwindigkeit und Effizienz bietet und sich besonders für hochpräzise Anforderungen und Massenproduktionsszenarien eignet. Obwohl Wasserstrahlschneiden einzigartige Vorteile bei der Verarbeitung komplexer Materialien und der Vermeidung thermischer Effekte bietet, wird Laserschneiden aufgrund seiner Schnelligkeit, Effizienz und Kosteneffizienz in der modernen Fertigung häufig eingesetzt. Die Auswahl der geeigneten Schneidtechnologie sollte auf den spezifischen Anwendungsanforderungen und Materialeigenschaften basieren. Laserschneiden ist zweifellos die bevorzugte Lösung für viele Branchen, die Präzision und Effizienz anstreben.
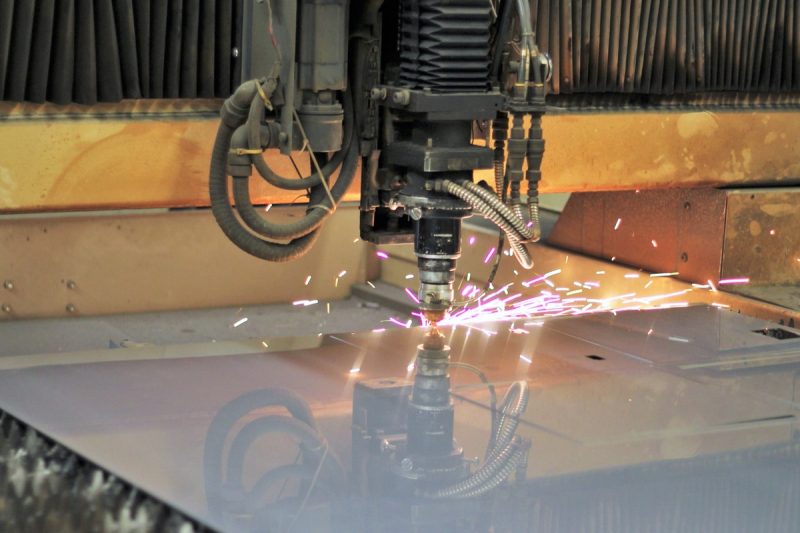
Zusammenfassen
Laserschneiden und Wasserstrahlschneiden haben jeweils ihre eigenen Vorteile und Einschränkungen und eignen sich für unterschiedliche industrielle Anforderungen. Bei der Auswahl einer Schneidtechnologie ist es wichtig, eine Entscheidung auf der Grundlage der spezifischen Verarbeitungsanforderungen zu treffen. Wenn Sie nach hoher Präzision und hoher Schnittgeschwindigkeit suchen, insbesondere beim Schneiden dünner Materialien, ist das Laserschneiden zweifellos die effizienteste Wahl. Laserschneiden bietet nicht nur extreme Präzision, sondern verbessert auch die Produktionseffizienz und reduziert Materialabfall.
Wenn Sie hingegen dickere Materialien schneiden müssen oder Hitzeeinwirkungen vermeiden müssen, um die physikalischen Eigenschaften des Materials zu schützen, ist das Wasserstrahlschneiden die geeignetere Lösung. Das Wasserstrahlschneiden eignet sich für eine größere Bandbreite an Materialien und kann aufgrund seiner Kaltschneideeigenschaften Schäden an hitzeempfindlichen Materialien vermeiden.
AccTek-Laser ist bestrebt, seinen Kunden fortschrittliche und kostengünstige Laserschneidgeräte mit hervorragender Leistung und Zuverlässigkeit bereitzustellen, um den Produktionsanforderungen verschiedener Branchen gerecht zu werden. Durch die Wahl des Laserschneidens können Sie nicht nur die Produktionseffizienz verbessern, sondern auch verfeinerte Verarbeitungsergebnisse erzielen. Für weitere Informationen und professionelle Beratung zu Geräten können Sie sich gerne an uns wenden. Wir bieten Ihnen eine maßgeschneiderte Lösung!
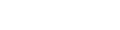
Kontaktinformationen
- [email protected]
- [email protected]
- +86-19963414011
- Nr. 3 Zone A, Industriegebiet Lunzhen, Stadt Yucheng, Provinz Shandong.
Holen Sie sich Laserlösungen