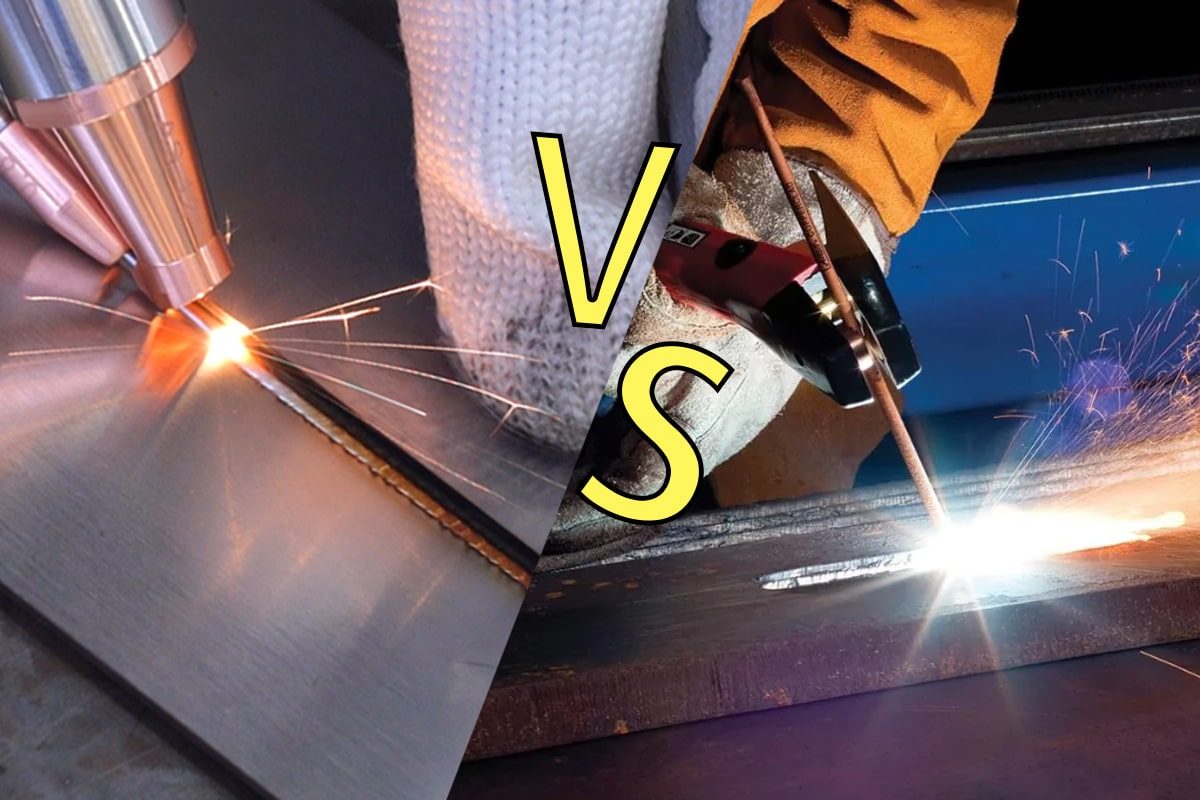
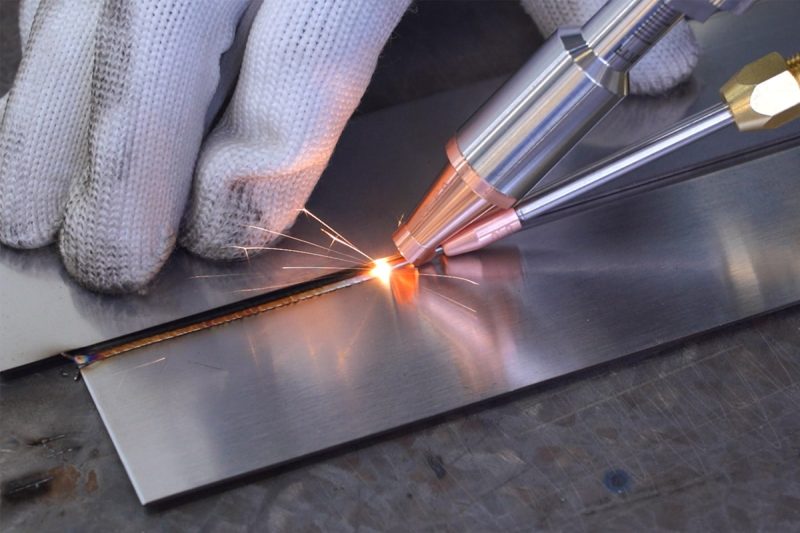
Laserschweißen Übersicht
Prinzip und Verfahren des Laserschweißens
- Materialvorbereitung: Stellen Sie sicher, dass die Oberfläche des zu schweißenden Materials sauber ist und entfernen Sie Oxide, Öl und andere Verunreinigungen, um die Schweißqualität nicht zu beeinträchtigen.
- Fokussierung des Laserstrahls: Fokussieren Sie den Laserstrahl mittels einer Linse oder einem Reflektor auf die Schweißstelle, um eine ausreichend hohe Energiedichte zu gewährleisten.
- Bildung eines Schmelzbades: Der Laserstrahl bestrahlt die Oberfläche des Materials, erhitzt es schnell und schmilzt, sodass ein Schmelzbad entsteht. Während der Bewegung des Lasers dehnt sich das Schmelzbad allmählich aus.
- Erstarren und Abkühlen: Nach dem Entfernen des Laserstrahls kühlt das Schmelzbad ab und es bildet sich eine durchgehende Schweißnaht.
Arten von Laserschweißtechnologien
Laserstrahlschweißen
- Diese Methode wird hauptsächlich zum Flachschweißen verwendet. Der Laserstrahl erhitzt die Oberfläche des Materials und schmilzt es lokal. Da die Wärme langsam diffundiert und das Schmelzbad flach ist, eignet es sich im Allgemeinen zum Verbinden dünner Materialien oder für Szenen mit hohen Anforderungen an das Aussehen der Schweißnaht. Das Laserstrahlschweißen eignet sich zum Schweißen präziser elektronischer Geräte oder dünnwandiger Metallmaterialien.
Laser-Stichlochschweißen
- Bei hochenergetischer Laserbestrahlung schmilzt das Material nicht nur an der Oberfläche. Die starke Energie des Lasers verdampft das Metall und bildet im Schweißbereich ein kleines Loch (ein sogenanntes „Schlüsselloch“). Dieses kleine Loch ist tief und schmal, sodass der Laser tief in das Material eindringen und durch Mehrfachreflexionen Energie auf die umgebenden Materialien übertragen kann. Diese Technologie eignet sich für das Tiefenschweißen dicker Materialien und wird häufig in Branchen wie der Automobil-, Luftfahrt- und Schiffbauindustrie eingesetzt, in denen eine hohe Schweißfestigkeit erforderlich ist.
Vorteile und Grenzen des Laserschweißens
Vorteile des Laserschweißens:
- Hohe Präzision: Beim Laserschweißen kann die Energie präzise auf einen sehr kleinen Bereich fokussiert werden, die Tiefe und Reichweite des Schweißens gesteuert und eine extrem hohe Schweißgenauigkeit erreicht werden, was sich besonders für die Bearbeitung komplexer Teile eignet.
- Kleine Wärmeeinflusszone: Aufgrund der hohen Energiekonzentration beim Laserschweißen ist die Wärmeeinflusszone klein, was Materialverformungen und innere Spannungen reduziert und so die Schweißqualität sicherstellt.
- Schnelle Schweißgeschwindigkeit: Durch das Laserschweißen können Schweißvorgänge in sehr kurzer Zeit abgeschlossen werden, was die Produktionseffizienz erheblich verbessert und sich besonders für automatisierte Produktionslinien im großen Maßstab eignet.
- Berührungslose Bearbeitung: Beim Laserschweißen ist kein direkter Kontakt mit dem Werkstück erforderlich, es werden also keine äußeren Kräfte eingebracht und es entstehen keine mechanischen Schäden.
- Anwendbar auf eine Vielzahl von Materialien: Neben herkömmlichen Metallmaterialien kann das Laserschweißen auch auf nichtmetallischen Materialien wie Kunststoffen und Keramik angewendet werden und bietet ein breites Anwendungsspektrum.
Einschränkungen des Laserschweißens:
- Hohe Gerätekosten: Laserschweißgeräte sind komplex und die Kosten für Lasergeneratoren, Steuerungssysteme und Zusatzgeräte sind hoch, insbesondere bei Hochleistungslasersystemen, was kleine und mittlere Unternehmen unter wirtschaftlichen Druck setzen kann.
- Hohe Anforderungen an die Materialoberfläche: Beim Laserschweißen werden strenge Anforderungen an die Sauberkeit der Werkstückoberfläche gestellt. Öl, Oxid oder andere Verunreinigungen beeinträchtigen die Absorptionseffizienz des Lasers und die Schweißqualität.
- Geeignet für dünne Materialien oder Präzisionsschweißen: Obwohl sich mit dem Laserschweißen eine Vielzahl von Materialien schweißen lässt, ist es bei dicken Strukturmaterialien möglicherweise nicht so effizient wie herkömmliche Schweißverfahren.
Anwendung des Laserschweißens in verschiedenen Branchen
- Automobilherstellung: Laserschweißen wird in der Automobilindustrie häufig eingesetzt, insbesondere beim Karosserieschweißen, Türschweißen und Schweißen von Motorteilen. Aufgrund seiner hohen Geschwindigkeit und Präzision verbessert es den Automatisierungsgrad der Produktionslinie erheblich. Darüber hinaus wird Laserschweißen auch zum Schweißen gemischter Metalle wie Aluminiumlegierungen und Stahl verwendet.
- Luft- und Raumfahrt: In der Luft- und Raumfahrt müssen Schweißmaterialien häufig leicht und hochfest sein. Aufgrund seiner hohen Präzision und hervorragenden Schweißqualität wird das Laserschweißen häufig für Flugzeug- und Raumfahrzeugstrukturen verwendet, darunter Turbinenschaufeln, Motorgehäuse und andere Komponenten.
- Elektronik- und Mikroelektronikindustrie: Da beim Laserschweißen winzige Bereiche präzise geschweißt werden können und die Wärmeeinflusszone sehr klein ist, wird es in der Elektronikindustrie, insbesondere in der Mikroelektronikfertigung, häufig eingesetzt. Beispielsweise beim Schweißen kleiner Präzisionsteile wie Mobiltelefonen, Leiterplatten und Batteriegehäusen.
- Medizinische Geräte: Das Laserschweißen spielt bei der Herstellung medizinischer Geräte eine wichtige Rolle. Es wird zum Schweißen präziser und anspruchsvoller Metallinstrumente wie chirurgischer Instrumente, Implantate und verschiedener Geräte aus Edelstahl und Titanlegierungen verwendet.
- Energiebranche: In den Bereichen Neue Energien, Solarenergie und Batterieherstellung wird das Laserschweißen aufgrund seiner berührungslosen, hohen Effizienz und Anpassungsfähigkeit an eine Vielzahl von Materialien häufig eingesetzt, insbesondere bei der Verpackung und Verbindung von Batterien für Neue Energien.
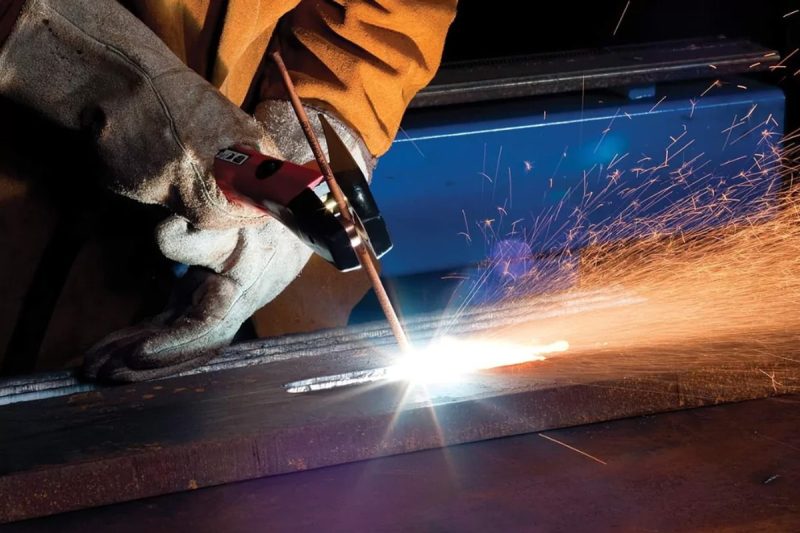
Lichtbogenschweißen Übersicht
Prinzip und Verfahren des Lichtbogenschweißens
- Lichtbogenerzeugung: Durch Annähern der Schweißelektrode an das Werkstück entsteht zwischen Elektrode und Werkstück ein Lichtbogen.
- Metallschmelzen: Die durch den Lichtbogen erzeugte hohe Temperatur (bis zu 5000–6000 °C) schmilzt das Metall und es bildet sich ein Schmelzbad.
- Schmelzbadfüllung: Das Material der Elektrode vermischt sich mit der Metallschmelze an der Werkstückoberfläche und bildet einen Füllstoff, der das Schmelzbad nach und nach füllt.
- Abkühlung und Erstarrung: Nach der Bewegung des Lichtbogens kühlt das Schmelzbad rasch ab und erstarrt zu einer Schweißnaht.
- Während des Lichtbogenschweißvorgangs bestimmt die Steuerung der Schweißparameter (wie Strom, Spannung, Schweißgeschwindigkeit) und der Schweißhaltung die Qualität der Schweißnaht und das Schweißergebnis.
Arten von Lichtbogenschweißtechniken
Lichtbogenschweißen mit Schutzgas
MIG/MAG-Schweißen
Wolfram-Inertgasschweißen
Unterpulverschweißen
Vorteile und Grenzen des Lichtbogenschweißens
Vorteile des Lichtbogenschweißens:
- Niedrige Gerätekosten: Lichtbogenschweißgeräte sind relativ einfach, mit niedrigen Anfangsinvestitionskosten und wirtschaftlichen Wartungskosten, weshalb sie für großindustrielle Anwendungen geeignet sind.
- Flexibler Betrieb: Lichtbogenschweißen lässt sich an eine Vielzahl von Schweißpositionen und komplexen Strukturen anpassen und kann im Innen- und Außenbereich sowie in engen Räumen durchgeführt werden.
- Starke Materialverträglichkeit: Lichtbogenschweißen kann eine Vielzahl von Metallen schweißen, darunter kohlenstoffarmen Stahl, Edelstahl, Aluminium, Kupfer usw., und hat ein breites Anwendungsspektrum.
- Breite Anwendung: Von dünnen Platten bis hin zu schweren Strukturmaterialien bietet das Lichtbogenschweißen eine starke Anpassungsfähigkeit hinsichtlich Dicke und Strukturform, insbesondere in der Schwermaschinen- und Bauindustrie.
Einschränkungen beim Lichtbogenschweißen:
- Große Wärmeeinflusszone: Beim Lichtbogenschweißen entsteht eine große Wärmezufuhr, wodurch leicht eine große Wärmeeinflusszone entstehen kann, die wiederum zu Verformungen, Rissen oder anderen wärmebehandlungsbedingten Problemen des Materials führen kann.
- Relativ geringe Schweißgenauigkeit: Im Vergleich zu hochpräzisen Schweißverfahren wie dem Laserschweißen mangelt es beim Lichtbogenschweißen an Schweißgenauigkeit und auch die Feinheit und Ästhetik der Schweißnaht ist gering.
- Hohe Rauch- und Gasemissionen: Beim Lichtbogenschweißen entstehen große Mengen Rauch und schädliche Gase, die die Gesundheit der Bediener und die Umwelt beeinträchtigen können. Daher sind eine gute Belüftung und Schutzausrüstung erforderlich.
- Hohe technische Anforderungen: Insbesondere beim manuellen Schweißen hat das Können des Schweißers großen Einfluss auf die Schweißqualität und unzureichende technische Kenntnisse führen zu Schweißfehlern.
Anwendung des Lichtbogenschweißens in verschiedenen Branchen
- Bauindustrie: Lichtbogenschweißen wird häufig beim Schweißen von Baustrukturen verwendet, insbesondere beim Bau von Stahlkonstruktionen und Brücken. Die hochfesten Schweißnähte und die Bedienbarkeit des Lichtbogenschweißens machen es zu einem der bevorzugten Verfahren zum Schweißen von Stahlkonstruktionen.
- Schiffbauindustrie: Bei der Rumpfherstellung ist eine große Menge an Stahlschweißen erforderlich, und Lichtbogenschweißen kann schwere Stahlplatten verarbeiten und gute mechanische Eigenschaften bieten. Insbesondere das Unterpulverschweißen wird häufig beim Schweißen großer Rümpfe und Schalen verwendet.
- Öl- und Gasindustrie: Beim Pipelineschweißen ist das Lichtbogenschweißen aufgrund seiner Flexibilität und hohen Materialverträglichkeit das wichtigste Schweißverfahren für Öl- und Gaspipelines, das Zuverlässigkeit auch in Hochdruckumgebungen gewährleisten kann.
- Herstellung schwerer Geräte: Bei der Herstellung schwerer Geräte wie Bergbaumaschinen, Baumaschinen und landwirtschaftlichen Maschinen wird das Lichtbogenschweißen häufig zum Schweißen großer Strukturteile wie Schaufeln, Rahmen und Ausleger verwendet. Diese Teile erfordern eine hochfeste und langlebige Schweißtechnologie.
- Reparatur und Wartung: Aufgrund der einfachen und bequemen Bedienung von Lichtbogenschweißgeräten werden diese häufig bei der Reparatur und Wartung verschiedener Arten mechanischer Geräte eingesetzt. Von der Autoreparatur bis zur Reparatur industrieller Geräte ist das Lichtbogenschweißen ein gängiges Werkzeug für Wartungspersonal.
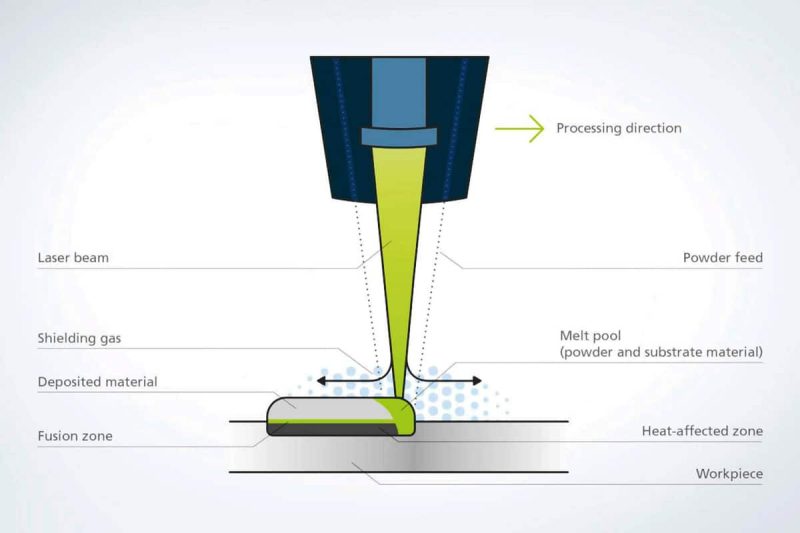
Prinzip des Laserschweißens
So funktioniert das Laserschweißen
- Laserstrahlerzeugung: Ein Lasergenerator, bei dem es sich um einen Faserlasergenerator, einen CO₂-Lasergenerator oder einen Festkörperlasergenerator handeln kann, erzeugt einen hochintensiven Laserstrahl. Der Laserstrahl zeichnet sich durch eine einzelne Wellenlänge, eine hohe Richtwirkung und eine hohe Energiedichte aus.
- Fokussierung des Laserstrahls: Der Laserstrahl wird durch ein optisches System (z. B. eine Linse oder ein Reflektor) auf einen sehr kleinen Punkt von normalerweise nur etwa 0,1 mm Durchmesser fokussiert. Dies ermöglicht sehr hohe Leistungsdichten (Hunderte bis Tausende Watt pro Quadratmillimeter), die ausreichen, um Metall schnell zu schmelzen.
- Materialschmelzen und -schweißen: Wenn der Laserstrahl auf die Oberfläche des Materials gerichtet wird, absorbiert das Material die Laserenergie und erwärmt sich schnell bis zum Schmelzpunkt, wodurch ein Schmelzbad entsteht. Während sich der Laserstrahl entlang des Schweißpfads bewegt, dehnt sich das Schmelzbad allmählich aus und bildet nach dem Abkühlen eine feste Schweißnaht.
- Abkühlung und Verfestigung: Nachdem sich der Laserstrahl bewegt hat, kühlt sich der Schmelzbadbereich ab und das geschmolzene Metall verfestigt sich zu einer durchgehenden Schweißnaht. Durch die Steuerung der Laserleistung, der Schweißgeschwindigkeit und der Fokusposition können Form und Qualität der Schweißnaht präzise gesteuert werden.
Wechselwirkung zwischen Laser und Metall
- Absorption der Laserenergie: Wenn der Laserstrahl auf die Metalloberfläche trifft, absorbiert das Metall einen Teil der Laserenergie. Dies hängt von der Reflektivität des Metalls und der Wellenlänge des Lasers ab. Beispielsweise haben hochreflektierende Materialien wie Aluminium und Kupfer eine geringe Absorptionsrate für bestimmte Wellenlängen von Lasern, sodass zum Schweißen eine höhere Leistung oder geeignetere Wellenlängen erforderlich sind. Bei normalem Stahl und Edelstahl ist die Absorptionsrate höher und das Laserschweißen ist effizienter.
- Wärmeleitung und Schmelzen: Die vom Metall absorbierte Laserenergie diffundiert durch Wärmeleitung in das Material, wodurch das Material erhitzt wird und der Schmelzpunkt erreicht wird. Die höhere Leistungsdichte bewirkt, dass das Material lokal und schnell schmilzt und ein Schmelzbad bildet. Während der Bewegung des Laserstrahls verfestigt sich das Metall im Schmelzbad weiter und bildet schließlich eine Schweißnaht.
- Schlüssellocheffekt: Beim Hochleistungslaserschweißen schmilzt die Energie des Laserstrahls nicht nur das Material, sondern verdampft auch einen Teil des Metalls, erzeugt lokalen Druck und drückt das geschmolzene Metall, sodass ein kleines Loch entsteht. Dieser Schlüssellocheffekt ermöglicht es dem Laserstrahl, tief in das Material einzudringen, durch Mehrfachreflexionen weitere Energie zu übertragen und die Schweißtiefe und -effizienz zu verbessern. Das Schlüssellochschweißen eignet sich sehr gut für dicke Materialien oder das Tiefschweißen.
- Dynamisches Verhalten des Schmelzbades: Während des Schweißvorgangs beeinflussen die Fließfähigkeit und Oberflächenspannung des Schmelzbades die Qualität und Form der Schweißnaht. Eine geeignete Laserleistung und Schweißgeschwindigkeit können das Schmelzbad stabil halten und Schweißfehler wie Spritzer und Porosität vermeiden.
Wichtige Parameter beim Laserschweißen
- Laserleistung: Die Leistung des Lasers bestimmt die auf das Material angewendete Energieintensität. Eine höhere Leistung eignet sich zum Schweißen dicker Platten oder zum Tiefschweißen. Wenn die Leistung jedoch zu hoch ist, kann dies zu übermäßigem Schmelzen oder Spritzen des Materials führen. Eine geringere Leistung eignet sich für dünne Platten oder Präzisionsschweißen, wodurch Wärmeeintrag und Verformung wirksam reduziert werden können.
- Schweißgeschwindigkeit: Die Schweißgeschwindigkeit bezeichnet die Geschwindigkeit, mit der sich der Laserstrahl über die Oberfläche des Materials bewegt. Eine höhere Schweißgeschwindigkeit kann die Größe der Wärmeeinflusszone und die Materialverformung verringern, eine zu hohe Geschwindigkeit kann jedoch zu unvollständigen oder instabilen Schweißnähten führen. Eine niedrigere Geschwindigkeit begünstigt das Tiefschweißen, kann jedoch die Wärmezufuhr erhöhen, was zu zu breiten Schweißnähten oder einer größeren Wärmeeinflusszone führt.
- Brennpunktposition: Die Position des Fokus des Laserstrahls relativ zur Werkstückoberfläche ist der Schlüssel zur Steuerung der Schweißtiefe und Schweißform. Eine Fokussierung unterhalb der Werkstückoberfläche kann die Schweißtiefe erhöhen und eignet sich zum Schweißen dicker Platten; eine Fokussierung oberhalb der Oberfläche eignet sich zum Oberflächenpräzisionsschweißen. Eine genaue Steuerung der Fokusposition hilft dabei, die Form und Festigkeit der Schweißnaht zu optimieren.
- Schutzgas: Schutzgas (wie Argon, Helium oder Kohlendioxid) wird beim Laserschweißen häufig verwendet, um zu verhindern, dass das Schmelzbad mit Sauerstoff und Stickstoff in der Luft reagiert, und so Schweißoxidation oder Porenbildung zu vermeiden. Verschiedene Gase haben unterschiedliche Auswirkungen auf Schweißnahtbildung und -qualität. Argon wird normalerweise verwendet, um die Oberflächenbeschaffenheit der Schweißnaht zu verbessern, während Helium verwendet wird, um die Schweißnahttiefe zu erhöhen.
- Laserwellenlänge: Die Wellenlänge des Lasers beeinflusst die Absorptionseffizienz des Materials. Unterschiedliche Materialien reagieren unterschiedlich empfindlich auf Laserwellenlängen. Die Wahl der richtigen Wellenlänge trägt dazu bei, die Energieeffizienz und die Schweißergebnisse zu verbessern. Beispielsweise liegen Faserlasergeneratoren normalerweise im Wellenlängenbereich von 1 μm, der zum Schweißen von Stahl, Edelstahl und anderen Materialien geeignet ist, während CO₂-Lasergeneratoren eine längere Wellenlänge (10,6 μm) haben und besser zum Schweißen nichtmetallischer Materialien geeignet sind.
- Schweißumgebung: Umgebungsbedingungen wie Feuchtigkeit, Temperatur und Luftstrom können sich ebenfalls auf die Stabilität des Laserschweißens auswirken, insbesondere bei Arbeiten im Freien oder in rauen Umgebungen. Zur Gewährleistung der Schweißqualität müssen die erforderlichen Schutzmaßnahmen getroffen werden.
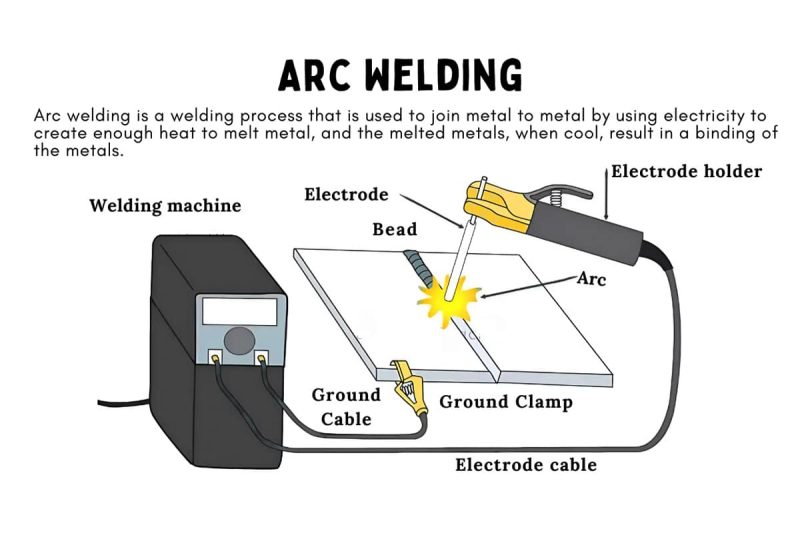
Prinzip des Lichtbogenschweißens
So funktioniert Lichtbogenschweißen
- Lichtbogenerzeugung: Wenn die Schweißelektrode das Werkstück berührt, wird der Stromkreis geschlossen und es fließt Strom. Die Elektrode wird dann vom Werkstück getrennt und der erzeugte Lichtbogen überträgt Energie durch die Luft oder das Schutzgas, wodurch das Metall in der Umgebung schnell bis zum Schmelzpunkt erhitzt wird.
- Schmelzen und Füllen der Elektrode: Die hohe Temperatur des Lichtbogens schmilzt nicht nur das Werkstück, sondern auch die Schweißelektrode. Das geschmolzene Metall der Elektrode gelangt in das Schmelzbad und verbindet sich mit dem geschmolzenen Metall des Werkstücks, um den Schweißbereich allmählich zu füllen.
- Bildung und Bewegung des Schmelzbades: Während sich der Lichtbogen entlang des Schweißpfads bewegt, wird das Schmelzbad kontinuierlich gebildet und bewegt, und der Bereich hinter dem Schmelzbad kühlt nach dem Verlassen des Lichtbogens schnell ab und erstarrt zu einer Schweißnaht.
- Schutz und Kühlung: Bei einigen Lichtbogenschweißverfahren, wie etwa dem Metalllichtbogenschweißen (MIG/MAG-Schweißen), werden Inertgase (wie etwa Argon, Kohlendioxid usw.) zum Schutz des Schmelzbades verwendet, um zu verhindern, dass Sauerstoff und Stickstoff in der Luft mit dem Hochtemperaturmetall reagieren und Oxide oder Poren bilden, welche die Qualität der Schweißnaht beeinträchtigen.
Lichtbogen- und Schweißbadbildung
Lichtbogenbildung
Schmelzbadbildung und dynamisches Verhalten
Schweißposition und Schmelzbadströmung
Wichtige Parameter, die das Lichtbogenschweißen beeinflussen
- Schweißstrom: Der Strom ist einer der wichtigsten Parameter, die die Wärmezufuhr beim Schweißvorgang bestimmen. Ein höherer Strom kann mehr Wärme erzeugen, die Größe des Schmelzbads und die Tiefe der Schweißnaht erhöhen und eignet sich zum Schweißen dickerer Materialien; ein niedrigerer Strom eignet sich dagegen für dünnere Materialien, um übermäßiges Schmelzen und Deformationen zu vermeiden. Ein zu hoher Strom führt zum Überlaufen der Schweißnaht und zur Instabilität des Schmelzbads, während ein zu niedriger Strom zu unzureichendem Schmelzen und unzureichender Schweißnahtfestigkeit führt.
- Schweißspannung: Die Spannung steuert die Länge und Stabilität des Lichtbogens. Eine höhere Spannung erzeugt einen längeren Lichtbogen, wodurch die Wärmeverteilung gleichmäßiger wird, was für die Bildung breiter Schweißnähte geeignet ist; eine niedrigere Spannung erzeugt einen kürzeren Lichtbogen und die Wärme konzentriert sich auf einen kleineren Bereich, was für Tiefschweißen geeignet ist. Spannungsänderungen wirken sich direkt auf die Form und Stabilität des Lichtbogens aus, was wiederum die Fließfähigkeit des Schmelzbades und die Form der Schweißnaht beeinflusst.
- Schweißgeschwindigkeit: Die Schweißgeschwindigkeit bezieht sich auf die Geschwindigkeit, mit der sich der Lichtbogen über das Werkstück bewegt. Sie hat einen wichtigen Einfluss auf die Form des Schmelzbads, die Größe der Wärmeeinflusszone (WEZ) und die Qualität der Schweißnaht. Höhere Schweißgeschwindigkeiten verkürzen die Zeit bis zur Bildung des Schmelzbads, verringern die Wärmeeinflusszone und die Verformung, können jedoch zu unterbrochenen Schweißnähten oder schlechter Verschmelzung führen. Niedrigere Schweißgeschwindigkeiten erhöhen die Wärmezufuhr und eignen sich für Tiefschmelzschweißen, können jedoch zu einer Überhitzung des Materials, zu breiten Schweißnähten oder großen Verformungen führen.
- Elektrodentyp und -durchmesser: Die Wahl der Elektrode wirkt sich direkt auf die Schweißwirkung aus. Verschiedene Elektrodentypen (wie Schweißstäbe, elektrische Schweißdrähte usw.) eignen sich für unterschiedliche Materialien und Schweißverfahren. Der Durchmesser der Elektrode beeinflusst auch die Stabilität des Lichtbogens und die Breite der Schweißnaht. Dickere Elektroden eignen sich zum Schweißen dickerer Materialien und können breite und dicke Schweißnähte bilden, während dünnere Elektroden zum Präzisionsschweißen oder zum Schweißen dünner Platten geeignet sind.
- Schweißumgebung: Auch Umgebungsfaktoren wie Temperatur, Luftfeuchtigkeit, Windgeschwindigkeit usw. wirken sich auf das Lichtbogenschweißen aus. Eine übermäßige Windgeschwindigkeit kann das Schutzgas wegblasen, was zu Oxidation oder Porenbildung der Schweißnaht führt. Um die Schweißqualität sicherzustellen, sind unter rauen Außenbedingungen geeignete Schutzmaßnahmen wie Windbarrieren und beheizte Werkstücke erforderlich.
- Schutzgas: Beim Metalllichtbogenschweißen (MIG/MAG-Schweißen) und Wolframlichtbogenschweißen (WIG-Schweißen) wird Schutzgas verwendet, um die Luft zu isolieren und zu verhindern, dass das Schmelzbad mit Sauerstoff und Stickstoff in Kontakt kommt. Verschiedene Schutzgase (wie Argon, Kohlendioxid, Helium usw.) haben unterschiedliche Auswirkungen auf die Morphologie, Eindringtiefe und Oberflächenbeschaffenheit der Schweißnaht. Beispielsweise kann Argon eine bessere Oberflächenbeschaffenheit erzielen, während Kohlendioxid dazu beiträgt, die Schweißtiefe zu erhöhen.
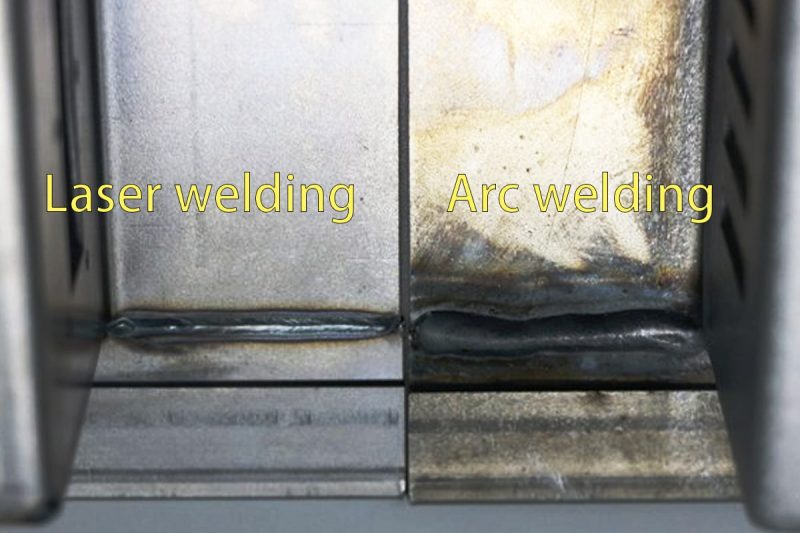
Vergleich zwischen Laserschweißen und Lichtbogenschweißen
Effizienz und Geschwindigkeit
Präzision und Genauigkeit
Wärmeeinflusszone und Verformung
Schweißqualität und -festigkeit
Ausrüstung und Einrichtung
Das Design von Laserschweißgeräten ist in der Regel komplex, aber mit dem Fortschritt der Technologie, moderne tragbare Laserschweißmaschinen sind zu einem Highlight in der Schweißindustrie geworden. Diese Geräte integrieren nicht nur Lasergeneratoren, optische Systeme und automatische Steuereinheiten, sondern verfügen auch über effiziente Schutzgasgeräte, um die Qualität und Leistung der Materialien beim Schweißen sicherzustellen. Die benutzerfreundliche Bedienoberfläche tragbarer Laserschweißgeräte ermöglicht den Bedienern einen schnellen Einstieg und reduziert die Abhängigkeit von komplexen Einstellungen. Gleichzeitig ist die Wartung moderner Laserschweißgeräte relativ einfach, was die Häufigkeit von Geräteausfällen effektiv reduzieren und eine kontinuierliche Produktionseffizienz gewährleisten kann.
Kostenüberlegungen
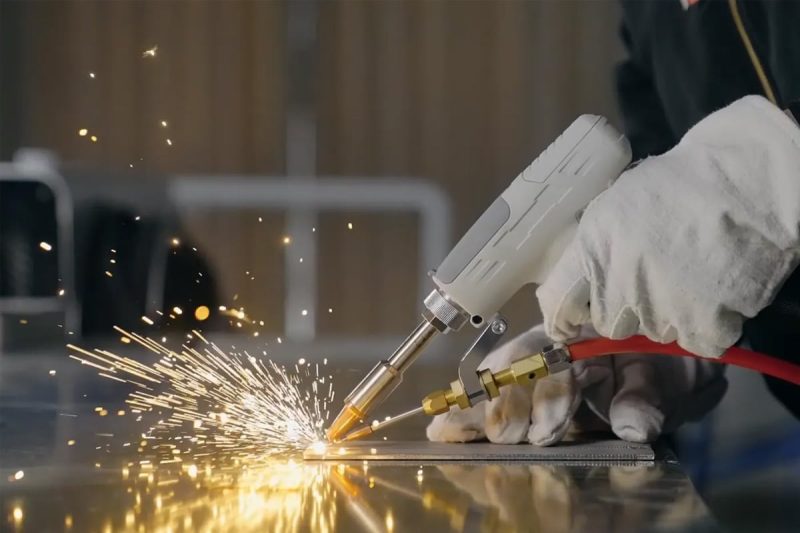
Anwendungen des Laserschweißens und Lichtbogenschweißens
Automobilindustrie
Luft- und Raumfahrt
Elektronik- und Mikroelektronikindustrie
Herstellung medizinischer Geräte
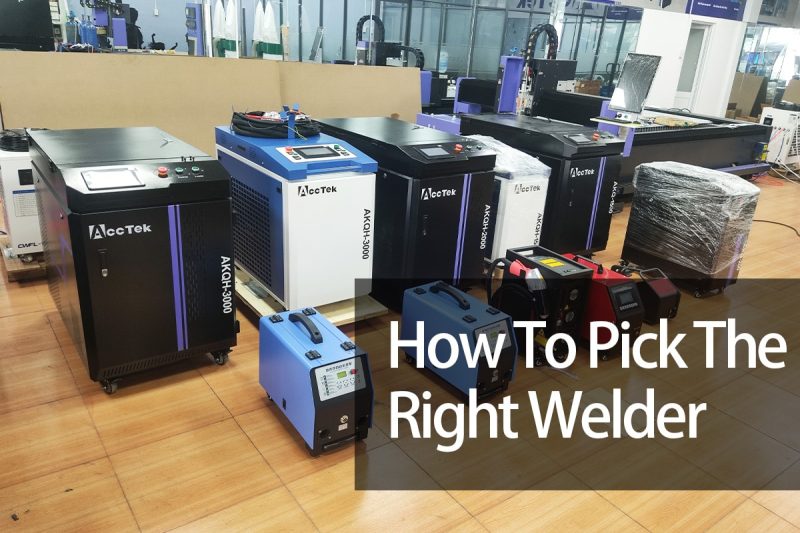
Die Wahl der richtigen Schweißtechnologie
Zu berücksichtigende Faktoren bei der Auswahl eines Schweißverfahrens
- Materialart und -dicke: Unterschiedliche Materialien und Materialdicken erfordern unterschiedliche Schweißtechniken. Beispielsweise eignen sich dünne Blechmaterialien eher zum Laserschweißen, während dicke Platten oder Baustähle häufig mit Lichtbogenschweißen geschweißt werden.
- Schweißpräzision und -komplexität: Komplexe Teile, feine Schweißnähte oder hochpräzise Schweißanforderungen erfordern normalerweise Präzisionsschweißtechniken wie das Laserschweißen.
- Schweißgeschwindigkeit: Die Forderung nach groß angelegter Produktion mit hoher Geschwindigkeit tendiert häufig dazu, Schweißtechniken mit einem hohen Automatisierungsgrad zu bevorzugen, wie beispielsweise das Laserschweißen, mit dem qualitativ hochwertige Schweißarbeiten in kurzer Zeit durchgeführt werden können.
- Wärmeeinfluss- und Verformungskontrolle: Wärmeempfindliche Materialien oder Projekte, die eine geringe Wärmeeinflusszone erfordern, eignen sich häufig zum Laserschweißen; während bei unempfindlichem Baustahl oder dickeren Materialien das Lichtbogenschweißen eine tiefe Durchdringung ermöglichen kann.
Projektspezifikationen und Ziele
Überlegungen zu Budget und Ressourcen
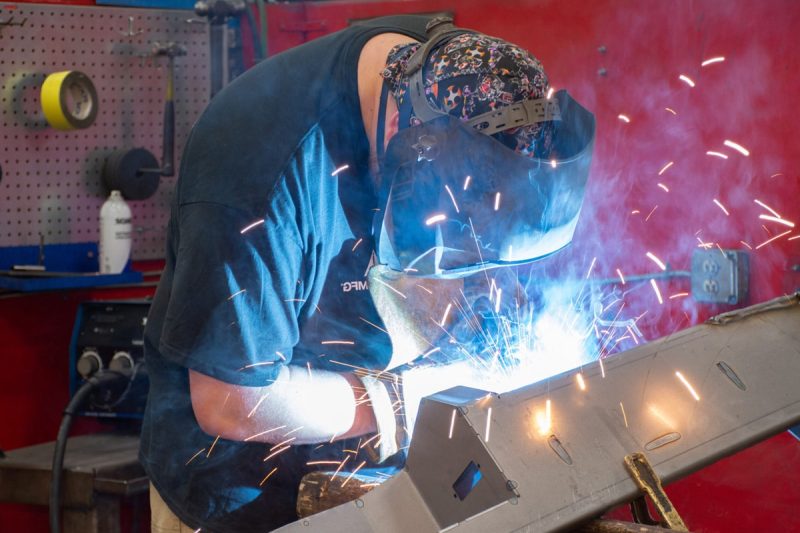
Umwelt- und Sicherheitsaspekte
Emissionen und Umweltbelastung
Gefahren für Gesundheit und Sicherheit am Arbeitsplatz
Einhaltung gesetzlicher Vorschriften und Standards
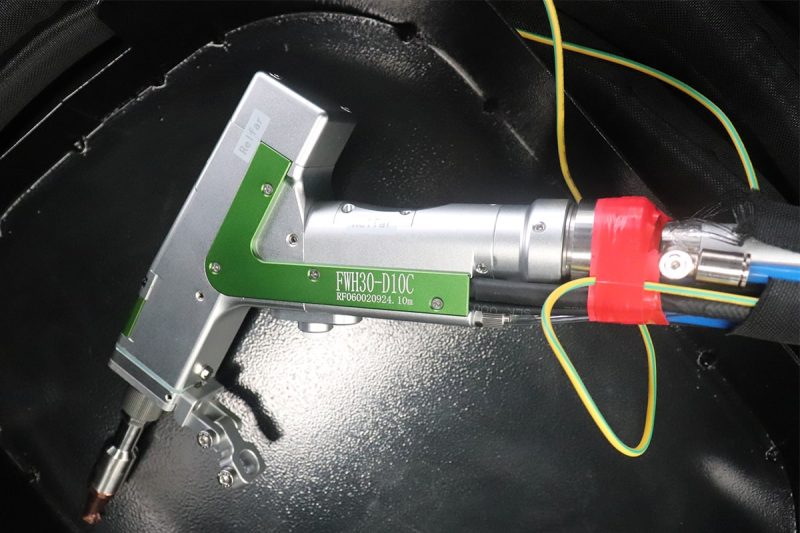
Zusammenfassen
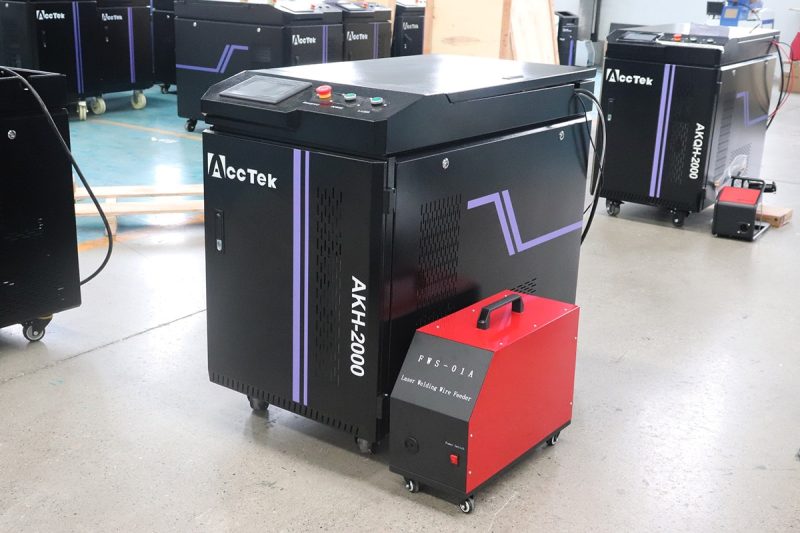
Holen Sie sich Laserlösungen
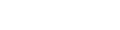
- [email protected]
- [email protected]
- +86-19963414011
- Nr. 3 Zone A, Industriegebiet Lunzhen, Stadt Yucheng, Provinz Shandong.