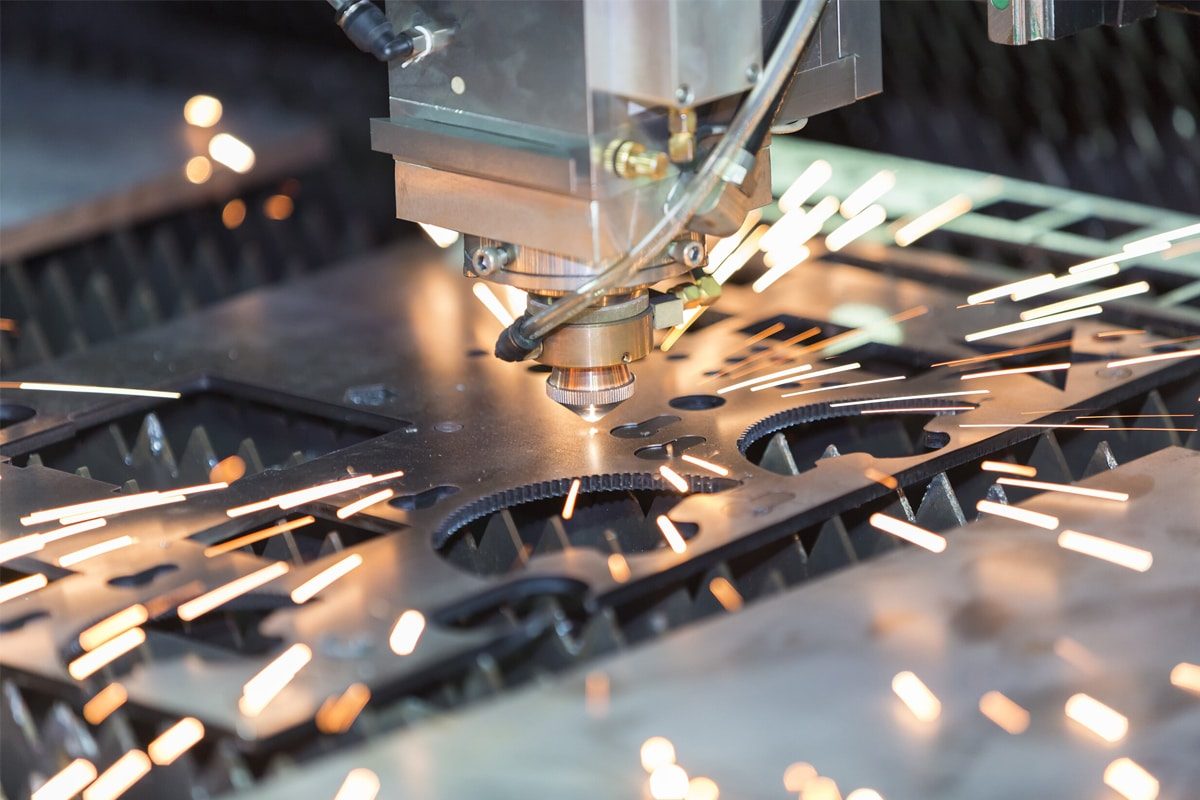
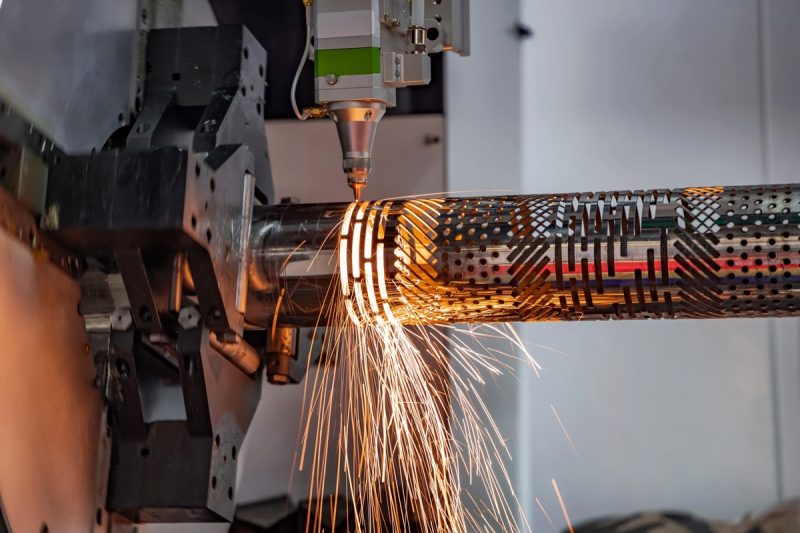
Laserleistung verstehen
Was ist Laserleistung?
Wie sich die Laserleistung auf den Schneidprozess auswirkt
Die Laserleistung spielt beim Laserschneidprozess eine Schlüsselrolle und beeinflusst mehrere wichtige Aspekte:
- Schnittgeschwindigkeit: Eine höhere Laserleistung ermöglicht schnellere Schnittgeschwindigkeiten. Dies liegt daran, dass mehr Energie zum Schmelzen, Verdampfen oder Verbrennen des Materials zur Verfügung steht, was ein schnelleres Schneiden ermöglicht. Bei industriellen Anwendungen, bei denen eine hohe Produktivität entscheidend ist, kann die Auswahl einer höheren Laserleistung die Produktionszeit erheblich verkürzen.
- Kantenqualität: Die Qualität der Schnittkante wird durch die Laserleistung beeinflusst. Die optimale Leistungseinstellung erzeugt eine glatte, saubere Kante und minimiert gleichzeitig Grate und thermische Verformungen. Eine zu hohe Leistung kann jedoch zu Kantenverbrennungen, Überschmelzen und einer breiteren Wärmeeinflusszone (WEZ) führen, was die Kantenqualität beeinträchtigen kann.
- Materialdurchdringung: Die Laserleistung bestimmt die Fähigkeit, unterschiedliche Materialstärken zu schneiden. Dickere Materialien erfordern höhere Leistungen, um sicherzustellen, dass der Laserstrahl die gesamte Materialtiefe durchdringen kann. Bei dünnen Materialien reichen oft niedrigere Leistungseinstellungen aus und können unnötige Hitzeentwicklung und Materialschäden verhindern.
- Materialabtragsrate: Die Materialabtragsrate wird durch die Laserleistung beeinflusst. Höhere Leistungen führen zu höheren Materialabtragsraten, was bei dickeren Materialien von Vorteil ist, bei dünneren Materialien jedoch zum Überschmelzen oder Verbrennen führen kann.
- Präzision und Detailgenauigkeit: Für komplizierte Designs und feine Details sind niedrigere Laserleistungen oft die bessere Wahl. Dies ermöglicht eine präzise Steuerung des Laserstrahls, verringert das Risiko von Überschnitten und stellt sicher, dass detaillierte Merkmale genau wiedergegeben werden.
- Thermische Effekte: Übermäßige Laserleistung kann zu spürbaren thermischen Effekten wie Verformungen oder Verfärbungen führen, insbesondere bei wärmeempfindlichen Materialien. Eine ordnungsgemäße Leistungskalibrierung kann diese nachteiligen Effekte minimieren.
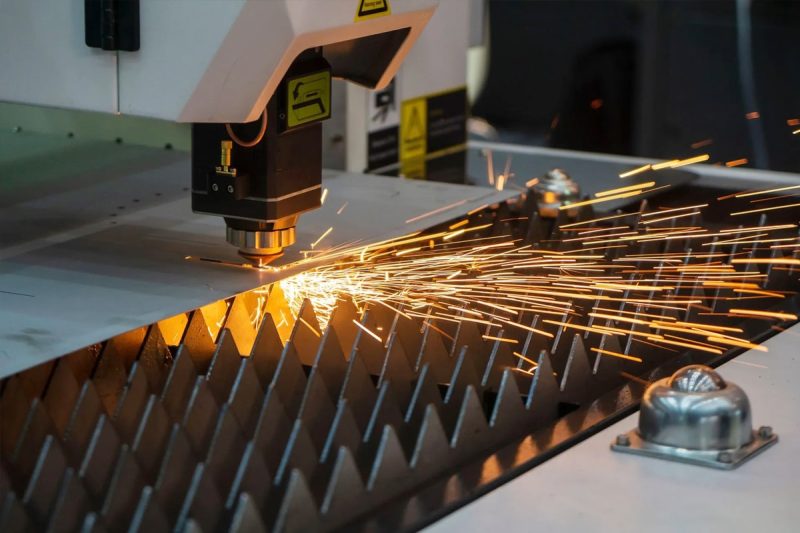
Arten von Laserschneidmaschinen
Faserlaser-Schneidemaschine
Haupteigenschaften
- Wellenlänge: Typischerweise etwa 1,06 Mikrometer, ideal zum Schneiden von Metallen.
- Effizienz: Hohe elektrooptische Effizienz, typischerweise über 30%, was zu geringeren Betriebskosten und geringerem Energieverbrauch führt.
- Strahlqualität: Überlegene Strahlqualität ermöglicht feineres, präziseres Schneiden, insbesondere bei dünnen Materialien.
- Wartung: Da die Laserquelle keine beweglichen Teile enthält, ist der Wartungsaufwand gering.
Anwendungen
- Material: Ideal zum Schneiden von Metallen, einschließlich Stahl, Edelstahl, Aluminium, Messing und Kupfer.
- Dicke: Geeignet für hochpräzises Schneiden von dünnen bis mitteldicken Materialien.
- Branchen: Weit verbreitet in der Luft- und Raumfahrt, der Automobil-, Elektronik- und Metallverarbeitungsindustrie.
Vorteile
- Geschwindigkeit: Schnellere Schnittgeschwindigkeiten im Vergleich zu CO₂- und Nd-Lasern, insbesondere beim Schneiden dünner Materialien.
- Präzision: Hohe Präzision und hohe Kantenqualität durch dünnen Strahl.
- Hohe elektrooptische Effizienz: Höhere Effizienz, die zu geringerem Energieverbrauch und niedrigeren Betriebskosten führt.
- Wirtschaftlichkeit: Lange Lebensdauer und geringer Wartungsaufwand.
Nachteile
- Anschaffungskosten: Höhere Anschaffungskosten im Vergleich zu CO2-Lasergeneratoren.
- Materialbeschränkungen: Weniger wirksam bei nichtmetallischen Materialien wie Holz und Kunststoff.
CO2-Laser-Schneidemaschine
Hauptmerkmale
- Wellenlänge: ca. 10,6 Mikrometer, ideal zum Schneiden einer großen Bandbreite an Materialien, einschließlich Nichtmetallen.
- Wirkungsgrad: Der elektrische Wirkungsgrad ist im Vergleich zu Faserlasern geringer.
- Strahlqualität: Gute Strahlqualität, geeignet für vielfältige Schneide- und Gravuraufgaben.
- Wartung: Erfordert regelmäßige Wartung, einschließlich Gasnachfüllung und Spiegelkalibrierung.
Anwendungen
- Materialien: Kann eine breite Palette von Materialien schneiden, darunter Metalle, Holz, Acryl, Glas, Textilien und Kunststoffe.
- Dicke: Effektiv zum Schneiden dünner und dicker Materialien.
- Branchen: Wird in der Beschilderungs-, Verpackungs-, Holzverarbeitungs-, Automobil- und Textilindustrie verwendet.
Vorteile
- Vielseitigkeit: Kann neben Metallen auch eine Vielzahl anderer Materialien schneiden.
- Kosten: Niedrigere Anschaffungskosten im Vergleich zu Faserlasern.
- Verfügbarkeit: Ausgereifte Technologie, in verschiedenen Modellen und Konfigurationen erhältlich.
Nachteile
- Geschwindigkeit: Beim Schneiden von Metallen langsamer als bei Faserlasern.
- Wartung: Der Wartungsaufwand ist hoch und umfasst das Nachfüllen von Gas und regelmäßige Spiegeleinstellungen.
- Energieverbrauch: Der Energieverbrauch ist aufgrund der geringen elektrischen Effizienz hoch.
Nd-Laserschneidmaschine
Haupteigenschaften
- Wellenlänge: ca. 1,064 Mikrometer, ähnlich wie Faserlaser, geeignet zum Metallschneiden.
- Betriebsmodi: Kann sowohl im Dauerstrichmodus (CW) als auch im Impulsmodus betrieben werden und bietet Flexibilität für Schneide- und Gravuranwendungen.
- Strahlqualität: Hohe Strahlqualität für präzises Schneiden und Bohren.
- Wartung: Normalerweise geringer Wartungsaufwand, robustes Design und lange Lebensdauer.
Anwendungen
- Material: Geeignet zum Schneiden von Metallen, Keramik und einigen Kunststoffen.
- Dicke: Geeignet für Präzisionsschneiden und Bohren dünner Materialien.
- Branchen: Wird häufig in der Elektronik-, Medizingeräte-, Schmuck- und Luft- und Raumfahrtindustrie verwendet.
Vorteile
- Genauigkeit: Hohe Genauigkeit, kann feine Details wiedergeben.
- Impulsbetrieb: Impulsbetrieb möglich, ideal zum Bohren und Feingravieren.
- Materialverträglichkeit: Wirksam für eine Vielzahl von Materialien, einschließlich harter und spröder Materialien.
Nachteile
- Geschwindigkeit: Langsamere Schnittgeschwindigkeiten im Vergleich zu Faserlasergeneratoren.
- Kosten: Höhere Anschaffungskosten und geringere Effizienz im Vergleich zu CO2-Lasern.
- Kühlanforderungen: Erfordert ein effizientes Kühlsystem zur Steuerung der Wärmeableitung.
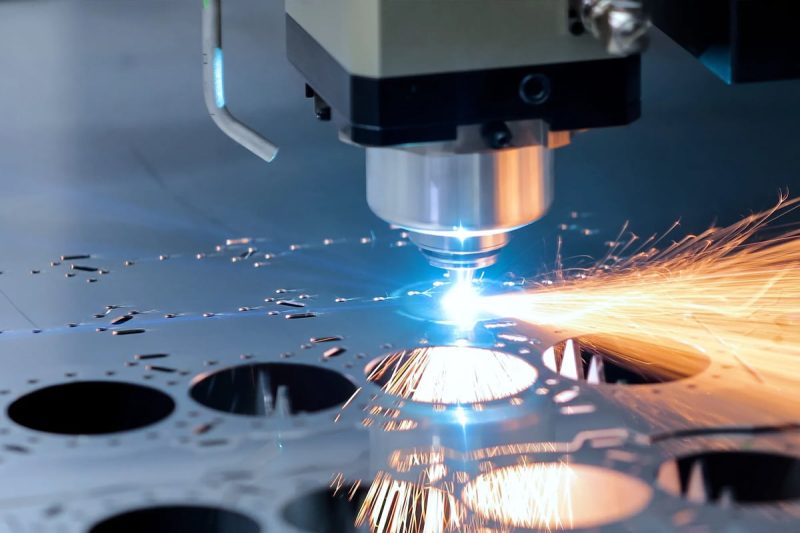
Faktoren, die die Laserleistung beeinflussen
Materialtyp
Metalle
- Stahl: Aufgrund seines hohen Schmelzpunkts erfordert er im Allgemeinen höhere Laserleistungen. Weichstahl, Edelstahl und andere Stahllegierungen können andere Leistungsanforderungen haben.
- Aluminium: Aufgrund seiner hohen Reflektivität und Wärmeleitfähigkeit erfordert es hohe Laserleistungen.
- Kupfer und Messing: Diese Materialien sind stark reflektierend und leitfähig und erfordern höhere Leistungsstufen oder spezielle Lasergeneratoren, wie z. B. Faserlasergeneratoren, um ein effizientes Schneiden zu gewährleisten.
Nichtmetalle
- Kunststoffe und Acryl: Im Allgemeinen ist eine geringere Leistung erforderlich als bei Metallen. Die erforderliche Leistung kann je nach Art und Dicke des Kunststoffs variieren.
- Holz: Es ist eine mittlere Leistung erforderlich, die erforderliche Leistung kann jedoch je nach Holzart und Feuchtigkeitsgehalt stark variieren.
- Stoff und Papier: Da diese Materialien dünn und brennbar sind, ist beim Schneiden eine geringere Leistung erforderlich.
Materialstärke
Die Materialdicke ist direkt proportional zur erforderlichen Laserleistung. Dickere Materialien erfordern mehr Leistung zum Schneiden, da der Laser tiefer eindringen und mehr Material entfernen muss.
- Dünne Materialien (≤ 1 mm): Niedrigere Leistungsstufen sind ausreichend. Niedrigere Leistungen ermöglichen hohe Präzision und feine Details.
- Mittlere Dicke (1-5 mm): Es sind mittlere Leistungsstufen erforderlich. Die genau erforderliche Leistung hängt vom Materialtyp und der gewünschten Schnittgeschwindigkeit ab.
- Dicke Materialien (> 5 mm): Um eine vollständige Durchdringung und effizientes Schneiden zu gewährleisten, ist eine hohe Leistung erforderlich. Bei extrem dicken Materialien kann ein Mehrdurchgangsverfahren oder ein spezieller Hochleistungslasergenerator erforderlich sein.
Anforderungen an die Schnittgeschwindigkeit
Die gewünschte Schnittgeschwindigkeit beeinflusst maßgeblich die Wahl der Laserleistung. Je schneller die Schnittgeschwindigkeit, desto höher ist in der Regel die erforderliche Leistung, um die Schnittqualität aufrechtzuerhalten und unvollständige Schnitte oder übermäßige Grate zu vermeiden.
- Hochgeschwindigkeitsschneiden: Für Anwendungen, bei denen es auf die Geschwindigkeit ankommt, wie etwa bei der Massenproduktion, sind höhere Laserleistungen erforderlich. Eine höhere Leistung stellt sicher, dass der Laser das Material schnell schneiden kann, ohne dass die Qualität darunter leidet.
- Mittelschnelles Schneiden: In Szenarien, in denen die Schnittgeschwindigkeit nicht so wichtig ist, können mittlere Leistungseinstellungen verwendet werden. Dies ist häufig bei der Kleinserienproduktion oder Sonderanfertigung der Fall.
- Langsames Schneiden: Für sehr detaillierte oder komplexe Schnitte können niedrigere Schnittgeschwindigkeiten und niedrigere Leistungseinstellungen verwendet werden. Dies ermöglicht eine höhere Präzision und Kontrolle.
Erforderliche Schnittqualität
Die erforderliche Schnittqualität wirkt sich auch auf die Einstellung der Laserleistung aus. Unterschiedliche Anwendungen haben unterschiedliche Standards für Kantenqualität, Genauigkeit und Verarbeitung.
- Hochwertiges Schneiden: Für Anwendungen, die glatte Kanten, hohe Qualität und minimale Nachbearbeitung erfordern, sind in der Regel höhere Laserleistungen und langsamere Schneidgeschwindigkeiten erforderlich. Dies gewährleistet einen sauberen Schnitt mit minimaler Bart- und Gratbildung.
- Schneiden in Standardqualität: Für Anwendungen, bei denen kleinere Unvollkommenheiten akzeptabel sind, sind mittlere Leistungsstufen ausreichend. Dies ist häufig bei Anwendungen in der Schwerindustrie der Fall, bei denen Geschwindigkeit Vorrang vor ästhetischer Qualität hat.
- Grobschneiden: Wenn es vor allem um Geschwindigkeit und nicht um Kantenqualität geht, können höhere Leistungen und schnellere Schnittgeschwindigkeiten eingesetzt werden. Dieser Ansatz wird häufig in den vorbereitenden Schnittphasen oder für Materialien verwendet, die einer weiteren Verarbeitung unterzogen werden.
Komplexität des Designs
Die Komplexität des zu schneidenden Designs oder Musters wirkt sich auch auf die erforderliche Laserleistung aus. Komplizierte und detaillierte Designs erfordern im Allgemeinen eine präzisere Steuerung des Lasers, was sich auf die Leistungseinstellung auswirkt.
- Komplexe Designs: Komplexe Muster mit scharfen Winkeln, kleinen Löchern und detaillierten Merkmalen erfordern eine präzise Steuerung der Laserleistung. Niedrigere Leistungseinstellungen in Kombination mit langsameren Geschwindigkeiten tragen dazu bei, eine hohe Präzision zu erreichen und eine Überhitzung oder Verformung des Materials zu vermeiden.
- Mittlere Designs: Designs mittlerer Komplexität können mit ausgewogenen Leistungseinstellungen geschnitten werden. Diese Designs können Kurven und unterschiedliche Linienstärken enthalten, erfordern aber keine extreme Präzision.
- Einfache Designs: Einfache Schnitte mit minimalen Details, wie einfache Formen und gerade Linien, können mit höheren Leistungseinstellungen und höheren Geschwindigkeiten ausgeführt werden.
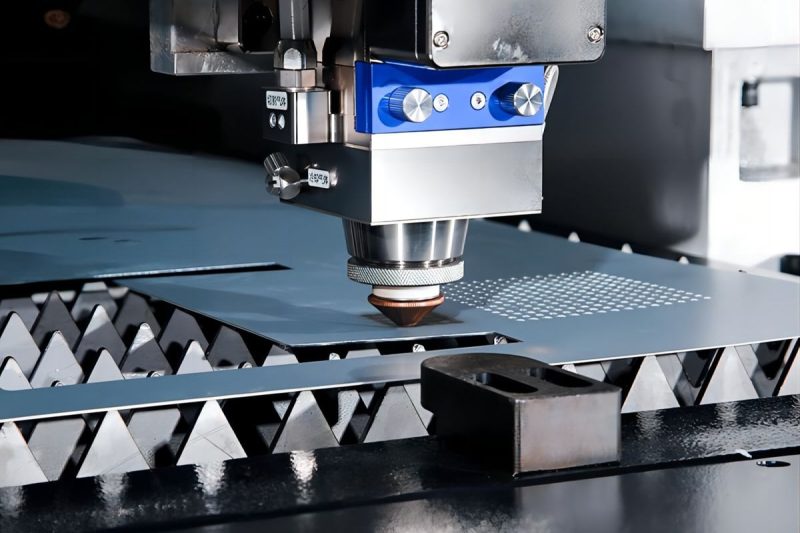
Laserleistungsbereiche für unterschiedliche Materialien
Metalle
Baustahl
- Dünne Platte (bis 3 mm dick): 1.000–2.000 Watt
- Mittlere Dicke (3-6 mm): 2.000-4.000 Watt
- Dicke Platte (6-12 mm): 4.000-8.000 Watt
- Extra dicke Platte (über 12 mm dick): 8.000–12.000 Watt
Edelstahl
- Dünne Platte (bis 2 mm dick): 1.000–2.000 Watt
- Mittlere Dicke (2-5 mm): 2.000-4.000 Watt
- Dicke Platte (5-10 mm): 4.000-6.000 Watt
- Extra dicke Platte (über 10 mm dick): 6.000–12.000 Watt
Aluminium
- Dünne Platte (bis 2 mm dick): 1.000–2.000 Watt
- Mittlere Dicke (2–6 mm): 2.000–4.000 Watt
- Dicke Platte (6-10 mm): 4.000-8.000 Watt
- Extra dicke Platte (über 10 mm): 8.000–12.000 Watt
Kupfer und Messing
- Dünne Platte (bis 1 mm dick): 1.000–2.000 Watt
- Mitteldick (1-3 mm): 2.000-4.000 Watt
- Dicke Platte (3-6 mm): 4.000-6.000 Watt
- Extra dicke Platte (über 6 mm): 6.000–8.000 Watt
Nichtmetalle
Kunststoffe (zB Polycarbonat, Polypropylen, PVC)
- Dünne Bleche (bis 2 mm Dicke): 25-40 Watt
- Mittlere Dicke (2-5 mm): 40-100 Watt
- Dicke Bleche (5-10 mm): 100-150 Watt
- Extra dicke Bleche (über 10 mm dick): 200-600 Watt
Acryl
- Dünne Bleche (bis 2 mm Dicke): 60-100 Watt
- Mittlere Dicke (2-5 mm): 100-200 Watt
- Dicke Bleche (5-10 mm): 200-400 Watt
- Extra dicke Platten (über 10 mm dick): 400–600 Watt
Holz (zB Sperrholz, MDF, Hartholz)
- Dünne Bleche (bis 3 mm Dicke): 100-150 Watt
- Mittlere Dicke (3-6 mm): 150-300 Watt
- Dicke Bleche (6–12 mm): 300–500 Watt
- Extra dicke Bleche (über 12 mm): 500–600 Watt
Textilien und Leder
- Dünne und mittlere Dicke: 60-150 Watt
- Dicke Materialien: 150–300 Watt
Verbundwerkstoffe
Kohlenstofffaserverstärkter Kunststoff (CFK)
- Dünne Bleche (bis 1 mm Dicke): 100-200 Watt
- Mittlere Dicke (1-3 mm): 200-400 Watt
- Dickes Blech (3-6 mm): 400-600 Watt
Glasfaserverstärkter Kunststoff (GFK)
- Dünne Bleche (bis 1 mm Dicke): 100-200 Watt
- Mittlere Dicke (1-3 mm): 200-400 Watt
- Dickes Blech (3-6 mm): 400-600 Watt
Andere Verbundwerkstoffe (z. B. Kevlar, Borverbundwerkstoffe)
- Dünne Bleche (bis 1 mm Dicke): 100-200 Watt
- Mittlere Dicke (1-3 mm): 200-400 Watt
- Dickes Blech (3-6 mm): 400-600 Watt
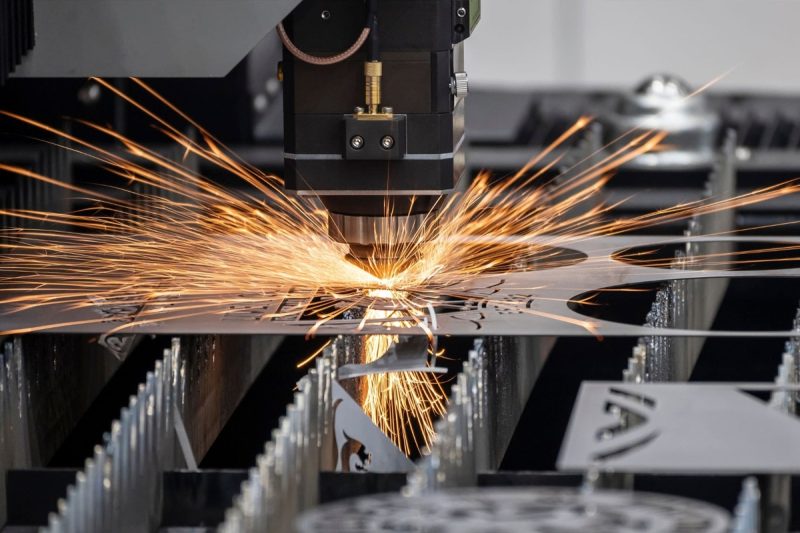
Methoden zur Bestimmung der Laserleistung
Materialverträglichkeitstabellen
Materialverträglichkeitsdiagramme sind eine wertvolle Ressource, die allgemeine Hinweise zu den für verschiedene Materialien erforderlichen Laserleistungseinstellungen bietet.
- Zweck: Mithilfe dieser Diagramme können Benutzer die Startleistungseinstellungen für verschiedene Materialien basierend auf Materialart und -dicke schnell ermitteln.
- Aufbau: Kompatibilitätstabellen listen die Materialien normalerweise in einer Spalte auf, gefolgt von den empfohlenen Leistungseinstellungen, Schnittgeschwindigkeiten und anderen relevanten Parametern.
- Quellen: Diese Diagramme finden Sie in Benutzerhandbüchern, Laserschneidesoftware und auf Hersteller-Websites.
Vorteile
- Kurzreferenz: Bietet sofortige Anleitung ohne die Notwendigkeit umfangreicher Berechnungen oder Experimente.
- Standardisierte Einstellungen: Bietet standardisierte Energieeinstellungen basierend auf bewährten Methoden der Branche.
Nachteile
- Allgemeine Informationen: Hierbei werden möglicherweise keine spezifischen Abweichungen hinsichtlich der Materialqualität oder der Umgebungsbedingungen berücksichtigt.
- Nur Ausgangspunkt: Dies sollte als Grundlage für weitere Anpassungen und Optimierungen dienen.
Werkstoffprüfung
Bei der Materialprüfung werden tatsächliche Tests durchgeführt, um die Laserleistungseinstellungen für bestimmte Materialien und Anwendungen zu optimieren.
- Ersteinrichtung: Beginnen Sie mit den empfohlenen Einstellungen, die Sie in einer Materialverträglichkeitstabelle oder im Handbuch des Herstellers finden.
- Inkrementelle Anpassung: Passen Sie Laserleistung, Geschwindigkeit und andere Parameter schrittweise an, während Sie die Ergebnisse überwachen.
- Bewertung: Bewerten Sie die Schnittqualität, die Kantenglätte und etwaige Anzeichen von Materialverschleiß oder Überhitzung.
Vorteile
- Genauigkeit: Ermöglicht eine präzise Kalibrierung basierend auf spezifischen Materialeigenschaften und Schnittanforderungen.
- Optimierung: Ermöglicht die Feinabstimmung für optimale Schneidleistung und verbessert so Effizienz und Qualität.
Nachteile
- Zeitaufwändig: Erfordert Zeit und Ressourcen, um mehrere Tests und Auswertungen durchzuführen.
- Materialverschwendung: Bedeutet, dass beim Testen etwas Material verbraucht wird.
Empfehlungen des Herstellers
Zur Bestimmung der geeigneten Laserschneidleistung ist das Befolgen der Empfehlungen des Herstellers entscheidend.
- Quelle: Empfehlungen finden Sie in Benutzerhandbüchern, technischen Supportdokumenten und offiziellen Mitteilungen der Hersteller von Laserschneidmaschinen.
- Inhalt: Diese Anleitungen enthalten normalerweise detaillierte Leistungseinstellungen, Schnittgeschwindigkeiten und andere Parameter, die auf umfangreichen Tests und realen Anwendungen basieren.
Vorteile
- Zuverlässigkeit: Die Empfehlungen des Herstellers basieren auf umfassenden Tests und sind auf die spezifischen Fähigkeiten der Laserschneidmaschine zugeschnitten.
- Support: Bei Fragen und Anliegen steht Ihnen der technische Support des Herstellers zur Verfügung.
Nachteile
- Allgemeine Empfehlungen: Diese Empfehlungen sind zwar zuverlässig, müssen jedoch unter Umständen je nach Anwendungsfall und Materialbeschaffenheit noch verfeinert werden.
- Abhängigkeit: Übermäßiges Vertrauen auf Herstellerempfehlungen kann die Erforschung optimierter Einstellungen für einzigartige Anwendungen einschränken.
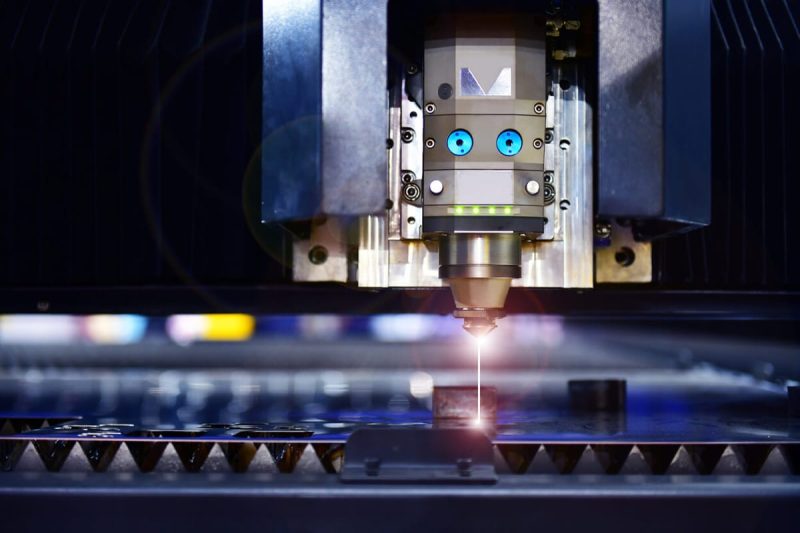
Praktische Überlegungen zur Auswahl der Laserschneidleistung
Maschinenspezifikationen
Maximale und minimale Leistungsabgabe
- Reichweite: Stellen Sie sicher, dass Ihre Maschine die für Ihr Material erforderlichen Leistungseinstellungen verarbeiten kann. Faserlaser haben normalerweise eine Leistung von 1.000 bis 12.000 Watt (für Metalle), während CO2-Laser eine Leistung von 60 bis 600 Watt (für Nichtmetalle) haben.
- Flexibilität: Maschinen mit einem großen Leistungsbereich bieten mehr Flexibilität beim Schneiden unterschiedlicher Materialien und Dicken.
Strahlqualität
- Fokusgröße: Die Qualität des Laserstrahls beeinflusst die Schnittgenauigkeit. Eine hohe Strahlqualität und eine kleinere Fokusgröße ermöglichen feinere, präzisere Schnitte.
- Stabilität: Eine gleichbleibende Strahlqualität gewährleistet gleichmäßige Schnitte und reduziert den Bedarf an häufigen Anpassungen.
Schnittgeschwindigkeit und Beschleunigung
- Geschwindigkeitsfähigkeit: Eine höhere Laserleistung ermöglicht schnellere Schnittgeschwindigkeiten, aber die mechanischen Komponenten der Maschine müssen diese Geschwindigkeiten unterstützen, ohne die Genauigkeit zu beeinträchtigen.
- Beschleunigung: Eine Maschine mit hohem Beschleunigungsvermögen kann schnelle Änderungen der Schnittrichtung bewältigen, was beim Erzielen komplexer Designs hilft.
Kontrollsystem
- Software: Erweiterte Steuerungssoftware kann Schnittpfade und Leistungseinstellungen optimieren und so Effizienz und Qualität verbessern.
- Integration: Stellen Sie sicher, dass das Steuerungssystem nahtlos in andere Produktionsgeräte und Software integriert werden kann, um den Betrieb zu vereinfachen.
Kosten- und Energieeffizienz
Betriebskosten
- Stromverbrauch: Höhere Laserleistungseinstellungen verbrauchen mehr Strom. Bewerten Sie den Energiebedarf und die Betriebskosten, die mit unterschiedlichen Leistungsstufen verbunden sind.
- Hilfsgas: Art und Menge des verwendeten Hilfsgases (z. B. Sauerstoff, Stickstoff, Druckluft) können die Gesamtkosten beeinflussen. Höhere Leistungseinstellungen können mehr Hilfsgas erfordern, um die Schnittqualität aufrechtzuerhalten. Wenn Sie mehr über Hilfsgase erfahren möchten, lesen Sie den „Einfluss der Hilfsgasauswahl auf das Laserschneiden“-Artikel.
Anfangsinvestition vs. langfristige Einsparungen
- Anschaffungskosten: Eine leistungsstärkere Laserschneidmaschine erfordert im Allgemeinen eine höhere Anfangsinvestition. Sie kann jedoch durch höhere Schnittgeschwindigkeit und Effizienz langfristig Einsparungen bringen.
- Effizienzsteigerung: Ein leistungsstärkerer Laser kann die Schneidzeit verkürzen und den Produktionsdurchsatz steigern, wodurch Arbeits- und Betriebskosten gespart werden.
Energieeffizienz
- Lasereffizienz: Faserlasergeneratoren sind im Allgemeinen energieeffizienter als CO2-Lasergeneratoren. Berücksichtigen Sie bei der Auswahl einer Leistungseinstellung die Energieeffizienz des Lasergeneratortyps.
- Kühlsystem: Ein effizientes Kühlsystem kann den Energieverbrauch senken und die Lebensdauer des Lasergenerators verlängern.
Wartung und Ausfallzeiten
Routinewartung
- Häufigkeit: Höhere Leistungseinstellungen beschleunigen den Verschleiß der Maschinenkomponenten. Erstellen Sie einen regelmäßigen Wartungsplan, um Teile nach Bedarf zu überprüfen und auszutauschen.
- Teile: Wichtige Komponenten wie Linsen, Spiegel und Düsen müssen häufig gereinigt und ausgetauscht werden, um eine optimale Leistung aufrechtzuerhalten.
Ausfallzeitmanagement
- Geplante Ausfallzeiten: Planen Sie Wartungsaktivitäten während der geplanten Ausfallzeiten, um Produktionsunterbrechungen zu minimieren.
- Vorbeugende Wartung: Implementieren Sie eine Strategie zur vorbeugenden Wartung, um potenzielle Probleme zu erkennen und zu beheben, bevor sie zu Maschinenausfällen führen.
Hersteller-Support
- Servicevereinbarungen: Erwägen Sie die von Herstellern angebotenen Servicevereinbarungen und Supportpakete. Diese können für Sicherheit sorgen und das Risiko längerer Ausfallzeiten verringern.
- Technische Unterstützung: Stellen Sie den Zugriff auf den technischen Support sicher, um Probleme zu beheben und die Maschinenleistung zu optimieren.
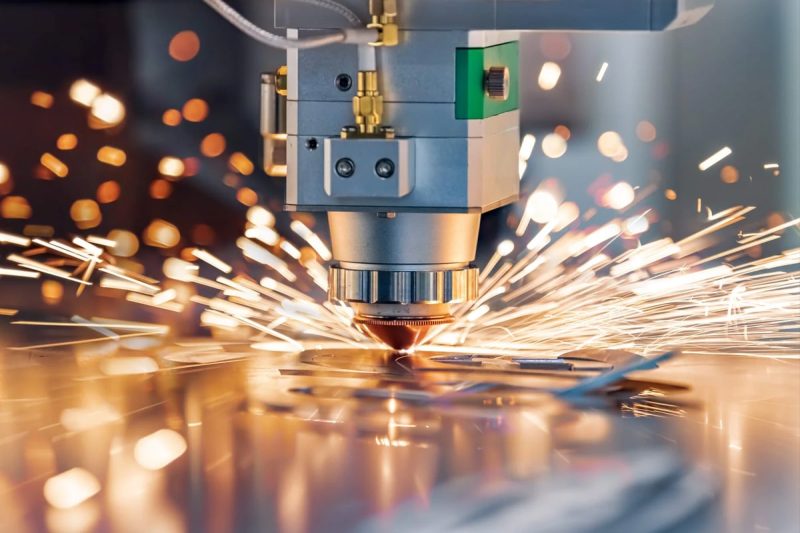
Fehlerbehebung bei Problemen mit der Laserleistung
Nicht tief genug schneiden
Ungenügende Energie
- Ursache: Die Laserleistungseinstellung ist möglicherweise zu niedrig, um das Material zu schneiden.
- Lösung: Erhöhen Sie die Laserleistung schrittweise und führen Sie Probeschnitte durch, bis die gewünschte Tiefe erreicht ist. Stellen Sie sicher, dass die Leistungsstufe im sicheren Betriebsbereich der Maschine liegt.
Schnittgeschwindigkeit zu hoch
- Ursache: Die Schnittgeschwindigkeit ist möglicherweise zu hoch, sodass dem Laser nicht genügend Zeit bleibt, das Material vollständig zu durchdringen.
- Lösung: Reduzieren Sie die Schnittgeschwindigkeit, damit mehr Energie auf das Material konzentriert werden kann. Gleichen Sie die Geschwindigkeits- und Leistungseinstellungen aus, um die Schnitttiefe zu optimieren.
Verpasster Fokus
- Ursache: Der Laserstrahl ist möglicherweise nicht richtig auf die Materialoberfläche fokussiert, wodurch die Schneideffizienz verringert wird.
- Lösung: Passen Sie die Fokushöhe an, um sicherzustellen, dass der Laserstrahl richtig auf das Material fokussiert ist. Verwenden Sie das Fokussierwerkzeug der Maschine oder passen Sie es bei Bedarf manuell an.
Materialstärke
- Ursache: Das Material ist möglicherweise dicker als erwartet und erfordert mehr Leistung oder mehrere Durchgänge.
- Lösung: Überprüfen Sie die Materialstärke und passen Sie die Leistungseinstellung entsprechend an. Bei sehr dicken Materialien sollten Sie mehrere Durchgänge oder die Verwendung eines Lasers mit höherer Leistung in Betracht ziehen.
Übermäßiges Brennen oder Schmelzen
Übermäßige Leistung
- Ursache: Die Laserleistungseinstellung ist möglicherweise für das zu schneidende Material zu hoch.
- Lösung: Reduzieren Sie die Laserleistung schrittweise, bis das Brennen oder Schmelzen minimiert ist. Stellen Sie sicher, dass die Leistungseinstellung für das Material geeignet ist.
Langsame Schnittgeschwindigkeit
- Ursache: Die Schnittgeschwindigkeit ist möglicherweise zu niedrig, wodurch es zu übermäßiger Hitzeentwicklung und Verbrennungen kommen kann.
- Lösung: Erhöhen Sie die Schnittgeschwindigkeit, um die Hitzeeinwirkungszeit zu verkürzen. Finden Sie das richtige Gleichgewicht zwischen Geschwindigkeit und Leistung, um einen sauberen Schnitt ohne Verbrennungen zu erzielen.
Falscher Fokus
- Ursache: Der Laserfokus ist möglicherweise zu konzentriert, was zu einer Überhitzung in einem kleinen Bereich führt.
- Lösung: Passen Sie die Fokushöhe so an, dass die Laserenergie gleichmäßiger über den Schnittbereich verteilt wird. Stellen Sie sicher, dass der Strahl richtig ausgerichtet und fokussiert ist.
Materialempfindlichkeit
- Ursache: Manche Materialien reagieren empfindlicher auf Hitze und neigen zum Verbrennen oder Schmelzen.
- Lösung: Verwenden Sie nach Möglichkeit Materialien mit besserer Hitzebeständigkeit. Erwägen Sie auch die Verwendung eines Hilfsgases wie Stickstoff, das durch Verdrängung des Sauerstoffs im Schnittbereich Verbrennungen reduzieren kann.
Inkonsistente Schnittergebnisse
Variable Leistungsabgabe
- Ursache: Die Leistungsabgabe des Lasergenerators kann schwanken, was zu einer inkonsistenten Schneidleistung führt.
- Lösung: Überprüfen Sie den Lasergenerator auf Stabilitätsprobleme und stellen Sie sicher, dass er ordnungsgemäß funktioniert. Regelmäßige Wartung und Kalibrierung können dazu beitragen, eine konstante Leistungsabgabe aufrechtzuerhalten.
Materialvariationen
- Ursache: Abweichungen in den Materialeigenschaften, beispielsweise in der Dicke oder Zusammensetzung, können zu ungleichmäßigem Schneiden führen.
- Lösung: Verwenden Sie hochwertige, einheitliche Materialien, um Materialkonsistenz sicherzustellen. Führen Sie Testschnitte an verschiedenen Materialchargen durch, um die Einstellungen nach Bedarf anzupassen.
Unsachgemäße Maschinenkalibrierung
- Ursache: Die Maschine ist möglicherweise nicht richtig kalibriert, was die Schnittgenauigkeit und -konsistenz beeinträchtigt.
- Lösung: Kalibrieren Sie die Laserschneidmaschine regelmäßig gemäß den Richtlinien des Herstellers. Achten Sie auf mechanische Probleme oder Fehlausrichtungen, die die Schneidleistung beeinträchtigen könnten.
Verschmutzte oder beschädigte Optik
- Ursache: Eine verschmutzte oder beschädigte Optik kann den Laserstrahl streuen und so zu ungleichmäßigen Schneidergebnissen führen.
- Lösung: Reinigen Sie die Optik regelmäßig und überprüfen Sie sie auf Schäden. Ersetzen Sie beschädigte Komponenten, um optimale Strahlqualität und -konsistenz sicherzustellen.
Umweltfaktoren
- Ursache: Änderungen der Umgebungstemperatur, Luftfeuchtigkeit oder des Luftstroms können den Schneidvorgang beeinträchtigen.
- Lösung: Sorgen Sie für eine kontrollierte Umgebung für Ihre Laserschneidmaschine. Sorgen Sie für konstante Temperatur- und Feuchtigkeitsniveaus, um die Auswirkungen von Umweltfaktoren auf den Schneidprozess zu reduzieren.
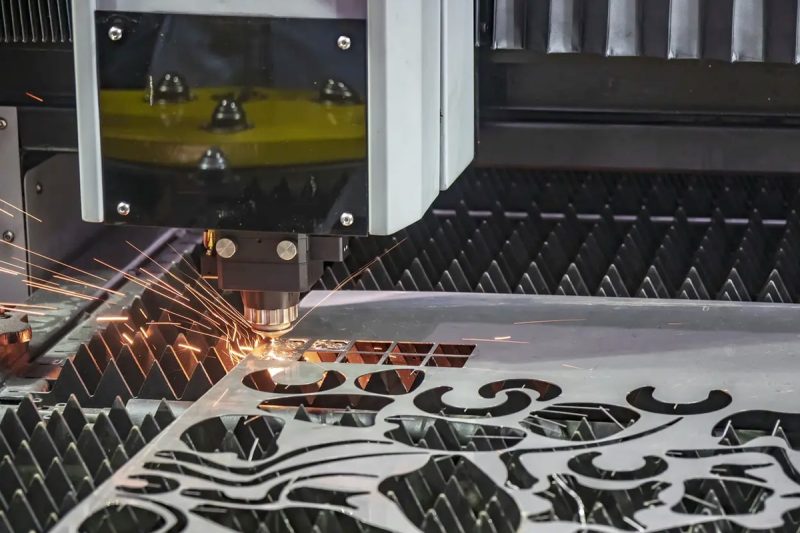
Zusammenfassung
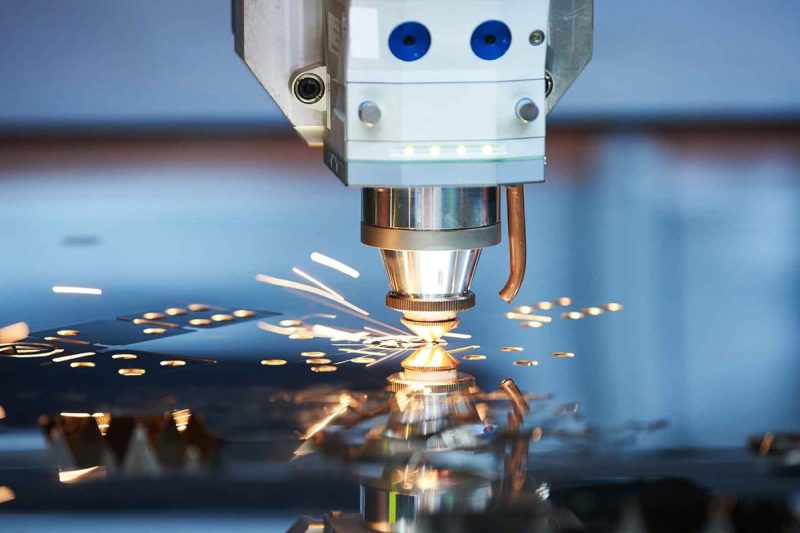
Holen Sie sich Laserschneidlösungen
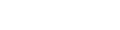
- [email protected]
- [email protected]
- +86-19963414011
- Nr. 3 Zone A, Industriegebiet Lunzhen, Stadt Yucheng, Provinz Shandong.