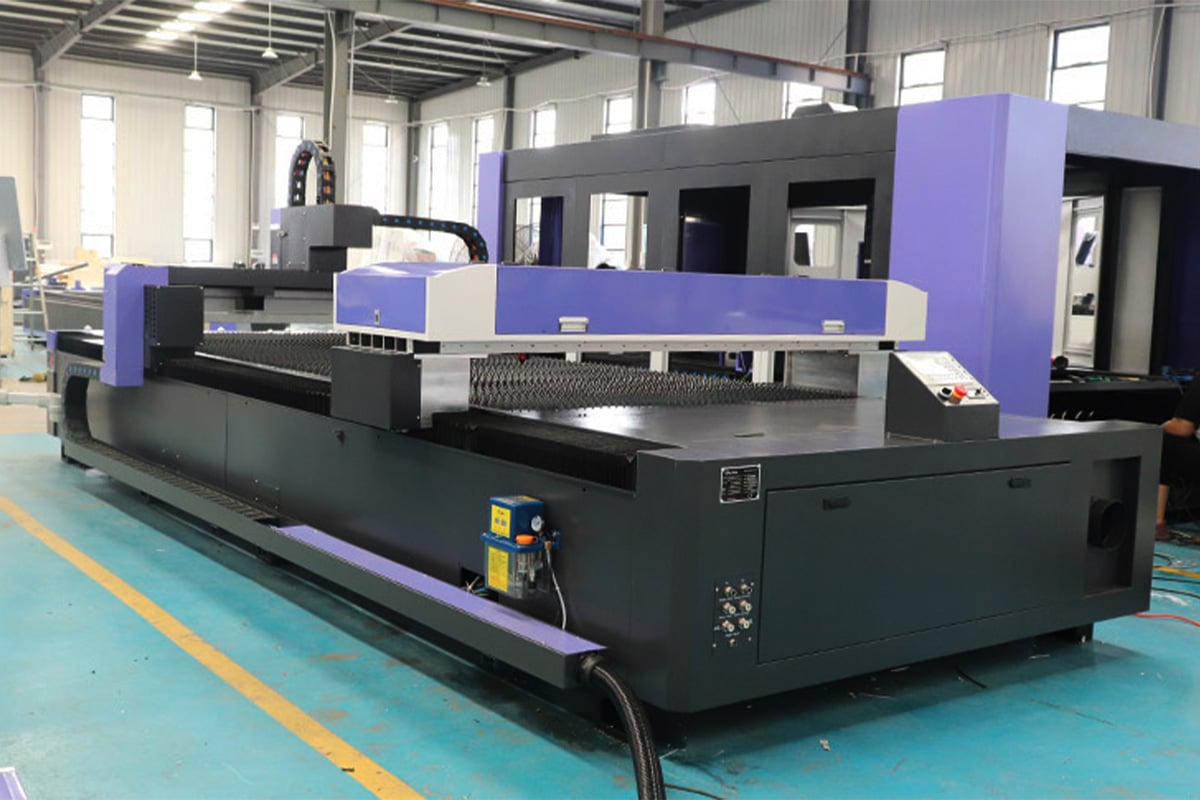
Wie erreicht man die minimale Schnittbreite beim CO2-Laserschneiden?
Die CO2-Laserschneidtechnologie wird aufgrund ihrer Vorteile wie hoher Präzision, hoher Geschwindigkeit und berührungsloser Bearbeitung häufig zum Schneiden verschiedener Materialien wie Metall, Kunststoff, Holz und Stoff eingesetzt. Die Schnittbreite bezeichnet die Breite des vom Laserstrahl während des Schneidvorgangs erzeugten Schnitts. Dieser Indikator beeinflusst direkt die Präzision und Qualität des Schnitts. Eine geringere Schnittbreite kann einen feineren Bearbeitungseffekt erzielen, die Produktpräzision verbessern, Materialabfall reduzieren und die Produktionskosten senken. Daher ist sie ein wichtiges Kriterium zur Messung der Laserschneidqualität.
Die Kontrolle der Schnittbreite dient nicht nur der Verbesserung der Produktqualität, sondern steht auch in engem Zusammenhang mit der Materialausnutzung, der späteren Verarbeitung und der Gesamtproduktionseffizienz. Für Hersteller steht die Optimierung der Schnittbreite in direktem Zusammenhang mit der Kontrolle der Produktionskosten. Insbesondere in der Großserienproduktion kann eine zu große Schnittbreite zu Materialverschwendung führen und den reibungslosen Ablauf nachfolgender Prozesse beeinträchtigen. Daher ist die präzise Kontrolle der Schnittbreite ein wichtiger Faktor für eine effiziente und kostengünstige Produktion.
Inhaltsverzeichnis
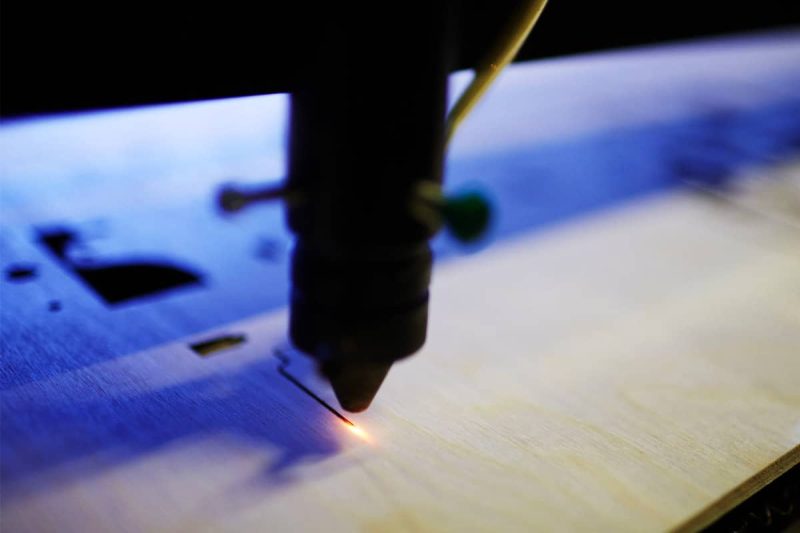
Schlüsselfaktoren, die die Schnittbreite beim CO2-Laserschneiden beeinflussen
Die Schneidwirkung der CO2-Laserschneidtechnologie wird von vielen Faktoren beeinflusst, wobei die Schnittbreite einer der wichtigsten Indikatoren ist. Durch die sinnvolle Anpassung und Optimierung dieser Faktoren können Hersteller die Produktionseffizienz steigern, Materialverluste reduzieren und gleichzeitig hohe Präzision gewährleisten. Im Folgenden sind einige Schlüsselfaktoren aufgeführt, die die Schnittbreite und ihre Optimierungsstrategien beeinflussen:
Laserfokusgröße: Die Größe des Laserfokus beeinflusst direkt den Durchmesser des Laserpunkts. Je kleiner der Punkt, desto schmaler die Schnittbreite. Je präziser der Fokus, desto höher die Konzentration der Laserstrahlenergie und damit die Schnittgenauigkeit. Um die Schnittbreite zu optimieren, ist die Wahl der richtigen Brennweite wichtig. Im Allgemeinen ermöglicht eine Linse mit kurzer Brennweite einen kleineren Fokusdurchmesser und damit einen feineren Schneideffekt. Für unterschiedliche Materialien und Schneidanforderungen lässt sich die Fokusgröße durch Anpassung der Brennweite optimieren, um den besten Schneideffekt zu erzielen.
Laserleistung: Die Laserleistung bestimmt direkt die thermische Energieintensität des Laserstrahls, die sich auf Schmelz-, Verdampfungs- und Schneideffekte während des Schneidprozesses auswirkt. Bei zu hoher Laserleistung kann der Schnitt leicht zu breit werden oder sogar das Material durchbrennen. Bei zu geringer Leistung kann das Material möglicherweise nicht vollständig durchdringen, was zu einem unvollständigen Schnitt führt. Es ist wichtig, die Laserleistung entsprechend der Dicke und den Eigenschaften verschiedener Materialien optimal einzustellen. Beispielsweise muss bei dickeren Materialien die Leistung entsprechend erhöht werden, während bei dünnen Materialien die Leistung reduziert werden kann, um zu breite Schnitte zu vermeiden. Durch die genaue Leistungsanpassung erzielen Hersteller präzises und effizientes Schneiden.
Schnittgeschwindigkeit: Auch die Schnittgeschwindigkeit spielt beim Laserschneiden eine wichtige Rolle. Eine angemessene Erhöhung der Schnittgeschwindigkeit kann nicht nur die Wärmeeinflusszone verkleinern und den Einfluss des geschmolzenen Materials auf die Schnittkante verringern, sondern auch die Produktionseffizienz verbessern. Ist die Schnittgeschwindigkeit jedoch zu hoch, hat der Laserstrahl möglicherweise nicht genügend Zeit, das Material vollständig zu durchdringen, was zu einem unvollständigen Schnitt führt. Umgekehrt kann eine zu niedrige Geschwindigkeit zu einem zu breiten Schnitt und zu übermäßiger Schmelzebildung führen. Um den Schneideffekt zu optimieren, muss die Schnittgeschwindigkeit präzise an Art und Dicke des Materials angepasst werden, um eine minimale Schnittbreite zu gewährleisten.
Hilfsgasart und -druck: Das Hilfsgas spielt beim Laserschneiden eine entscheidende Rolle. Häufig verwendete Hilfsgase sind Sauerstoff, Stickstoff und Luft. Sauerstoff kann die Verbrennungsreaktion während des Schneidvorgangs fördern und eignet sich zum Schneiden von Materialien wie Eisen und Stahl. Stickstoff kann die Oxidation reduzieren und eignet sich für Materialien wie Edelstahl. Luft wird aufgrund ihrer Wirtschaftlichkeit häufig für eine Vielzahl von Materialien verwendet. Neben der Gasart beeinflusst auch der Gasdruck die Schnittqualität. Ein geeigneter Gasdruck kann dazu beitragen, die Schmelze zu entfernen und ein Anhaften an der Schnittkante zu verhindern, wodurch die Schnittbreite reduziert wird. Ein niedrigerer Gasdruck kann dazu führen, dass die Schmelze nicht effektiv entfernt werden kann und die Schnittbreite zunimmt. Daher müssen der richtige Gasdruck und die richtige Gasart gewählt werden, um die Schneidwirkung zu optimieren.
Materialeigenschaften: Die Eigenschaften verschiedener Materialien können die Genauigkeit des Laserschneidens erheblich beeinflussen. Materialeigenschaften wie Absorptionsrate, Wärmeleitfähigkeit und Schmelzpunkt wirken sich direkt auf die Transmissionseffizienz des Laserstrahls und die Schnittqualität aus. Stark reflektierende Materialien (wie Aluminium, Kupfer usw.) neigen dazu, den Laserstrahl zu reflektieren und zu streuen, wodurch die Schneidwirkung verringert wird. Für diese Materialien ist es notwendig, die Laserparameter zu optimieren, insbesondere die Leistungsdichte zu erhöhen, um sicherzustellen, dass der Laser das Material effektiv durchdringen kann. Im Gegensatz dazu lassen sich schwach reflektierende Materialien wie Stahl leichter schneiden. Beim Schneiden verschiedener Materialien sollten Hersteller die Schneidparameter entsprechend den Materialeigenschaften anpassen, um eine optimale Schnittqualität und eine minimale Schnittbreite zu gewährleisten.
Optimierung des Schneidpfads: Die Optimierung des Schneidpfads ist auch entscheidend für die Kontrolle der Schnittbreite. Ein gleichmäßiger Schneidpfad kann den Fehler des Laserstrahls bei Richtungswechseln reduzieren und unregelmäßige Schnitte vermeiden. Insbesondere beim Schneiden komplexer Formen können eine sinnvolle Gestaltung des Pfads und die Reduzierung von Kurven und Notstopps die Schnittgenauigkeit deutlich verbessern. Darüber hinaus kann die Optimierung der Vorschub- und Rückzugsstrategien dazu beitragen, den Materialabtrag zu reduzieren und Schnittverformungen durch übermäßige Erwärmung zu vermeiden. Bei der Gestaltung des Pfads sollten schnelle Kurven und unebene Strecken möglichst vermieden werden, um eine gleichmäßige Energieverteilung während des Schneidvorgangs zu gewährleisten und so die Schnittbreite zu kontrollieren.
Durch die präzise Kontrolle und Optimierung dieser Schlüsselfaktoren können Hersteller die Produktionskosten senken, die Materialausnutzung verbessern und die Produktionseffizienz steigern, während gleichzeitig ein hochpräzises Schneiden gewährleistet wird.
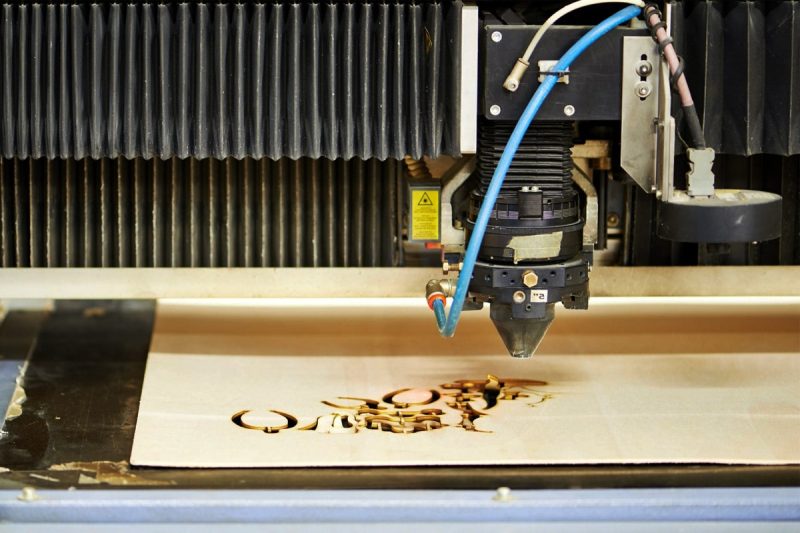
Optimierungsstrategie zur Erzielung einer minimalen Schnittbreite
Um die minimale Schnittbreite beim CO2-Laserschneiden zu erreichen, müssen verschiedene Optimierungsstrategien berücksichtigt werden. Diese Strategien können nicht nur die Schnittgenauigkeit verbessern, sondern auch den Materialabfall effektiv reduzieren und die Produktionseffizienz steigern. Die folgenden Optimierungsmethoden sind wichtig, um die minimale Schnittbreite zu erreichen:
Optimieren Sie das optische System: Die Qualität des optischen Systems beeinflusst direkt die Fokussierung des Laserstrahls und damit die Feinheit des Schnitts. Die Wahl einer hochwertigen optischen Linse sorgt für eine gleichmäßige Fokussierung des Laserstrahls auf die Oberfläche des Zielmaterials und somit für einen stabilen und präzisen Schneideffekt. Die Verwendung einer Linse mit kurzer Brennweite (z. B. 2,5 Zoll) ist eine wichtige Strategie zur Optimierung der Laserstrahlfokussierung. Eine Linse mit kurzer Brennweite kann einen kleineren Punktdurchmesser fokussieren, wodurch die Streuung des Laserstrahls reduziert und die Schnittbreite deutlich verringert wird. Ein kleinerer Punkt verbessert nicht nur die Schnittgenauigkeit, sondern verringert auch die thermische Belastung des Materials und sorgt für Stabilität während des Schneidprozesses.
Laserleistung und -geschwindigkeit präzise anpassen: Laserleistung und Schnittgeschwindigkeit sind zwei wichtige Faktoren, die die Schnittbreite beeinflussen. Optimale Schneidergebnisse erzielen Sie durch die präzise Abstimmung von Laserleistung und -geschwindigkeit. Der Pulsmodus verkürzt die Dauerheizzeit, verkleinert die Wärmeeinflusszone (WEZ) und reduziert das Schmelzen am Schnittrand. Der Pulsmodus sorgt für eine gleichmäßigere Laserenergieverteilung und verhindert Überhitzung durch hohe Dauerleistung. Gleichzeitig gewährleistet die Anpassung der Laserleistung an die Materialdicke, dass der Laserstrahl das Material vollständig durchdringt und die Schnittbreite kontrolliert. Reduzieren Sie bei dünneren Materialien die Leistung entsprechend, um übermäßige Hitzeentwicklung zu vermeiden. Erhöhen Sie bei dickeren Materialien die Leistung entsprechend, um die Schnittqualität zu gewährleisten, achten Sie aber dennoch auf die kontrollierte Schnittbreite.
Hilfsgasparameter anpassen: Das Hilfsgas spielt beim CO2-Laserschneiden eine wichtige Rolle. Es hilft nicht nur, die beim Schneiden entstehende Schmelze zu entfernen, sondern steuert durch Optimierung des Gasdrucks auch die Schnittqualität. Durch eine gezielte Erhöhung des Gasdrucks kann die beim Schneiden entstehende Schlacke effektiv entfernt und deren Anhaften an der Schnittkante verhindert werden, wodurch eine schmale Schnittbreite gewährleistet wird. Stickstoff ist eines der am häufigsten verwendeten Hilfsgase, insbesondere für Materialien, deren Oxidation reduziert und deren Schnittqualität verbessert werden muss. Stickstoff reduziert nicht nur effektiv die Oxidation der Materialoberfläche, sondern erhält auch die Glätte des Schnitts während des Schneidvorgangs und erzielt so ein qualitativ hochwertigeres Schneidergebnis.
Optimieren Sie Software und CNC-Parameter: Hochpräzise CNC-Systeme verbessern die Genauigkeit des Laserschneidens effektiv und reduzieren Schnittabweichungen durch mechanische Fehler. Mit modernen CNC-Systemen optimieren Sie den Schneidpfad und reduzieren Fehler durch Richtungsänderungen des Laserstrahls. Eine präzise Bahnplanung trägt dazu bei, Fehler durch Kurven und ungleichmäßige Schnittbahnen zu reduzieren. Darüber hinaus ist der Einsatz eines automatischen Fokussiersystems eine wichtige Strategie zur Optimierung der Schnittbreite. Das automatische Fokussiersystem passt die Laserfokusposition automatisch an Dicke, Form und Schnittanforderungen des Materials an, um sicherzustellen, dass der Laserstrahl stets optimal fokussiert ist. So werden ungleichmäßige oder zu breite Schnitte aufgrund einer falschen Fokusposition vermieden.
Reduzierung der Wärmeeinflusszone (WEZ): Die Größe der WEZ hängt eng mit der Wärmeentwicklung während des Laserschneidprozesses zusammen. Übermäßige Hitze kann zu einem übermäßigen Schmelzen der Materialoberfläche führen, wodurch die Schnittbreite vergrößert und die Schnittqualität beeinträchtigt wird. Zur Reduzierung der Wärmeeinflusszone ist Hochgeschwindigkeitsschneiden eine effektive Strategie. Hochgeschwindigkeitsschneiden kann die Bewegung des Laserstrahls beschleunigen, wodurch die Wärmeentwicklung auf der Materialoberfläche reduziert und ein Schmelzen und eine Verbreiterung der Schnittkante vermieden wird. Beim Hochgeschwindigkeitsschneiden muss jedoch sichergestellt werden, dass die Energie des Laserstrahls ausreicht, um das Material zu durchdringen. Um die Schnittqualität weiter zu optimieren, können Kühltechnologien wie Sprühkühlung oder duale Gasinjektion kombiniert werden. Diese senken die Temperatur im Schneidbereich effektiv, vermeiden Überhitzung und sorgen für einen präziseren und stabileren Schneideffekt.
Durch die Kombination der oben genannten Optimierungsstrategien können Hersteller die minimale Schnittbreite beim CO2-Laserschneiden effektiv erreichen. Dank der kontinuierlichen Weiterentwicklung der Technologie und der kontinuierlichen Optimierung der Anlagen tragen diese Strategien dazu bei, die Schnittgenauigkeit weiter zu verbessern, Materialverschwendung zu reduzieren und die Produktionseffizienz zu steigern.
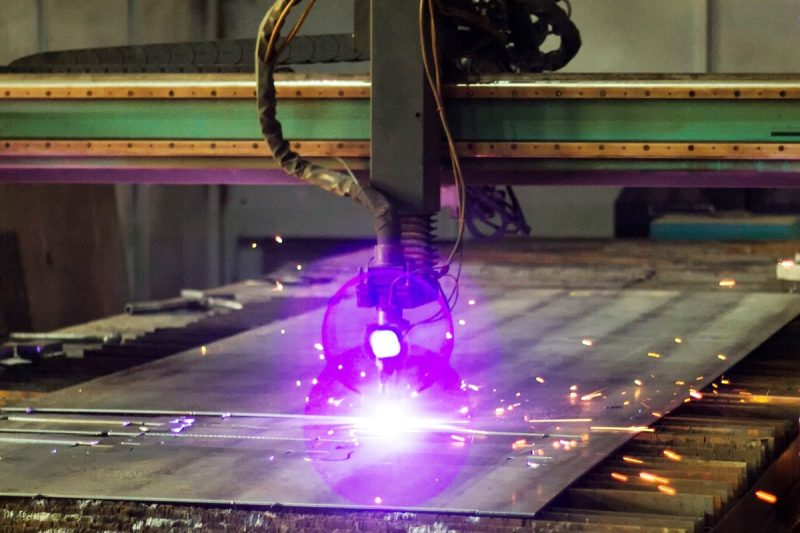
Zusammenfassen
Das Erreichen der minimalen Schnittbreite ist nicht nur eine einfache Parameteranpassung, sondern ein Prozess, der die umfassende Berücksichtigung vieler Faktoren erfordert. Durch die präzise Optimierung von Laserfokus, Leistungseinstellung, Schnittgeschwindigkeit, Hilfsgasart und -druck sowie Softwaresteuerung können Hersteller die Produktionseffizienz maximieren, Materialabfall reduzieren und gleichzeitig die Schnittqualität sicherstellen. Die präzise Einstellung des Laserfokus gewährleistet die optimale Schnittpunktgröße und vermeidet übermäßige Wärmeeinflusszonen während des Schneidprozesses. Dies gewährleistet einen feinen und glatten Schnitt. Die präzise Kombination aus Leistung und Schnittgeschwindigkeit verhindert übermäßige Wärmestaus und reduziert den Einfluss der Schmelze auf die Schnittbreite. Das richtige Hilfsgas entfernt nicht nur Schlacke, sondern verhindert auch Oxidation und verbessert so die Schnittqualität. Gleichzeitig können durch den Einsatz fortschrittlicher CNC-Software und automatischer Fokussierungstechnologie der Schneidweg und der Laserstrahlfokus kontinuierlich optimiert werden, um die Stabilität und Konsistenz des Schneideffekts zu gewährleisten.
Mit der kontinuierlichen technologischen Weiterentwicklung verbessern sich auch die Leistung und Regelgenauigkeit von CO2-Laserschneidmaschinen stetig. Hersteller können präzisere Schneidergebnisse erzielen, indem sie die oben genannten Faktoren kontinuierlich anpassen und optimieren, kombiniert mit der kontinuierlichen Weiterentwicklung optischer Technologien, automatisierter Steuerungssysteme und effizienter Kühltechnik. Das Erreichen der minimalen Schnittbreite verbessert letztendlich nicht nur die Schnittgenauigkeit, sondern steigert auch die Produktionseffizienz, senkt die Materialkosten und verbessert den wirtschaftlichen Nutzen der Produktionslinie im Langzeiteinsatz deutlich. Daher für Nutzer von CO2-Laserschneidmaschinen, kontinuierliches Lernen und Beherrschen dieser Optimierungsstrategien wird der Schlüssel zur Verbesserung der gesamten Produktionskapazität und Wettbewerbsfähigkeit sein.
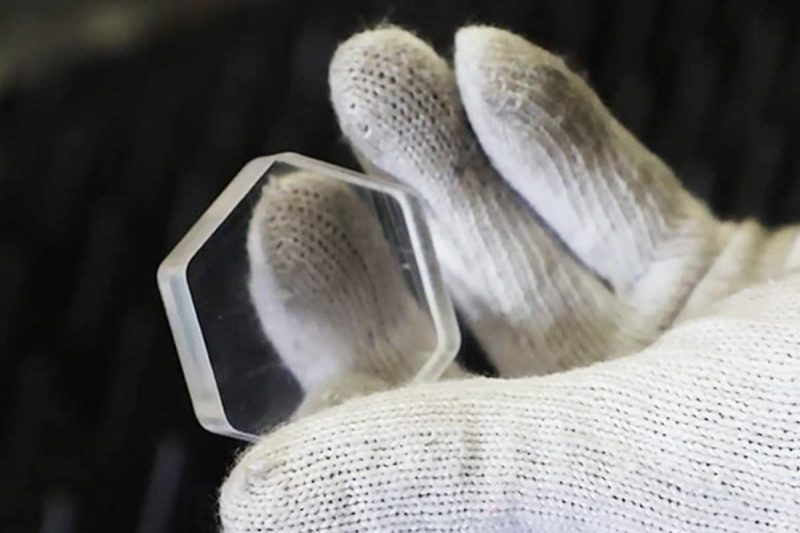
Holen Sie sich Laserlösungen
AccTek-Laser bietet hochpräzise CO2-Laserschneidgeräte, die intelligente Fokussierung, automatische Pfadoptimierung und effiziente Hilfsgassteuerung unterstützen, um die minimale Schnittbreite sicherzustellen und eine präzise Verarbeitung zu erreichen. Kontaktiere uns um maßgeschneiderte Laserschneidlösungen zu erhalten, die Ihre Produktionseffizienz und Verarbeitungsgenauigkeit verbessern!
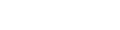
Kontaktinformationen
- [email protected]
- [email protected]
- +86-19963414011
- Nr. 3 Zone A, Industriegebiet Lunzhen, Stadt Yucheng, Provinz Shandong.
Holen Sie sich Laserlösungen