
Wie minimiert CO2-Laserschneiden den Materialabfall?
Die CO2-Laserschneidtechnologie wird in der Fertigung häufig eingesetzt, insbesondere in der Metallverarbeitung, beim Kunststoffschneiden, beim Holzgravieren und in anderen Bereichen. Laserschneiden wird für seine Präzision, Geschwindigkeit und Flexibilität geschätzt. Materialabfall ist jedoch ein Problem, das beim Schneidvorgang nicht ignoriert werden kann. Die Minimierung von Materialabfall durch CO2-Laserschneiden hängt nicht nur mit der Kostenkontrolle zusammen, sondern wirkt sich auch direkt auf die Produktionseffizienz und die ökologische Nachhaltigkeit aus. In diesem Artikel wird erläutert, wie Materialabfall durch die Optimierung von Laserschneidprozessen und -technologien reduziert werden kann.
Inhaltsverzeichnis
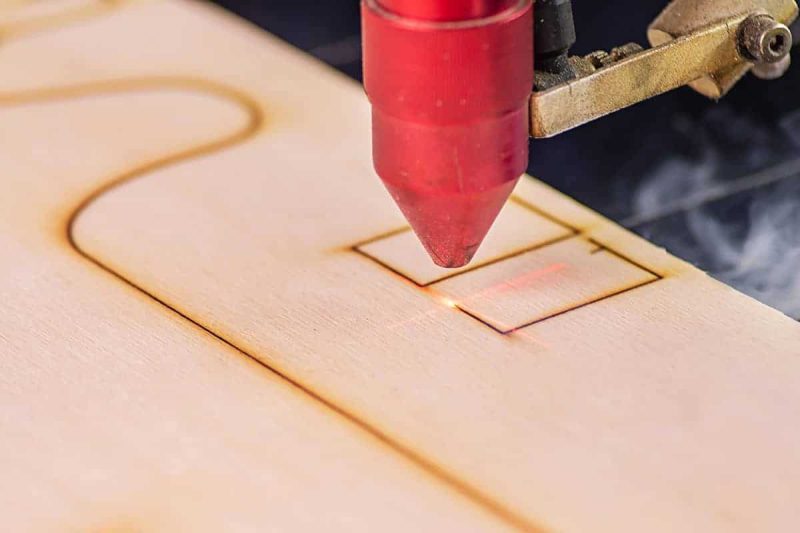
Präzise Kontrolle der Schnittparameter
Der Vorteil des CO2-Laserschneidens liegt in seiner hohen Präzision, die durch die präzise Steuerung mehrerer Schneidparameter den Materialabfall minimieren kann. Zu den wichtigsten Parametern zählen Laserleistung, Schneidgeschwindigkeit und Gasfluss. Durch die Optimierung dieser Parameter können die Schneidergebnisse verbessert und die Produktionseffizienz gesteigert werden, während gleichzeitig der Abfall reduziert wird.
Anpassung der Laserleistung
Die Laserleistung bestimmt direkt die Wärmezufuhr während des Schneidvorgangs. Übermäßige Leistung führt zu übermäßiger Ablation des Materials und unregelmäßigen Kanten, was zu unnötigem Abfall führt. Eine angemessene Anpassung der Laserleistung je nach Art und Dicke verschiedener Materialien kann sicherstellen, dass der Laserstrahl die Energie genau auf den Schneidbereich konzentriert, die thermische Auswirkung des umgebenden Bereichs verringert und übermäßigen Materialverlust vermeidet. Geeignete Leistungseinstellungen können auch Schmelzen und Versengen während des Schneidvorgangs verringern und die Qualität der Schnittfläche verbessern.
Optimierung der Schnittgeschwindigkeit
Die Anpassung der Schnittgeschwindigkeit ist entscheidend, um Materialabfall zu reduzieren. Eine zu niedrige Geschwindigkeit erhöht die Wärmezufuhr und führt zu einer Überhitzung der Schnittfläche, was zu Kantenverbrennungen oder übermäßigem Schmelzen führen kann, Materialverschwendung und eine Verschlechterung der Schnittqualität. Eine zu hohe Schnittgeschwindigkeit kann zu unvollständigen oder unregelmäßigen Schnitten führen, was zu ungeschnittenem Restmaterial führt. Daher kann die Optimierung der Schnittgeschwindigkeit, um sicherzustellen, dass sie sich an die Eigenschaften und Dicke verschiedener Materialien anpasst, unnötigen Abfall effektiv reduzieren und die Schnittqualität verbessern.
Gasflusskontrolle
Der Gasfluss spielt beim CO2-Laserschneidprozess eine entscheidende Rolle, da er den Schneidbereich kühlt und geschmolzenes Metall entfernt. Ein zu starker Gasfluss kann zu einer unebenen Schnittfläche oder Schlackenspritzern, einem instabilen Luftstrom und erhöhtem Abfall führen; ein zu geringer Gasfluss kann zu einem unbefriedigenden Schneidergebnis führen, da geschmolzenes Metall nicht effektiv weggeblasen oder Oxidation vermieden werden kann. Durch genaues Einstellen des Gasflusses können daher Schnittstabilität und ein hochwertiges Schneidergebnis gewährleistet und unnötiger Materialabfall reduziert werden.
Durch die präzise Steuerung dieser Schnittparameter kann nicht nur die Schnittqualität verbessert, sondern auch die Materialnutzungseffizienz effektiv optimiert, der Abfall reduziert und die Produktionseffizienz verbessert werden.
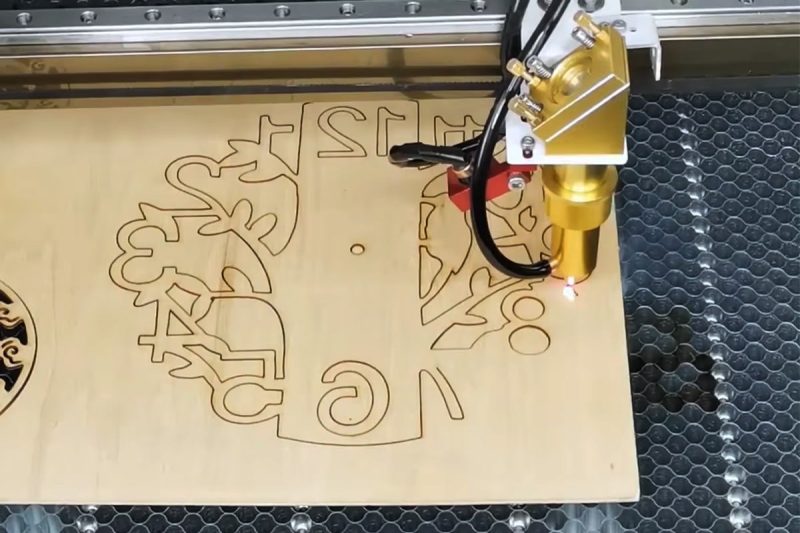
Optimierung des Materiallayouts
Die Bedeutung der Materialanordnung beim CO2-Laserschneiden liegt auf der Hand. Eine sinnvolle Anordnung kann nicht nur die Effizienz der Materialnutzung verbessern, sondern auch den Abfall reduzieren und die Schnittgenauigkeit und Produktionseffizienz verbessern. Durch die Optimierung des Layoutdesigns können ungenutzte Lücken minimiert, Material gespart und Kosten gesenkt werden. In praktischen Anwendungen umfasst die Optimierung der Materialanordnung viele Aspekte, darunter Teilelayout, Schnittpfaddesign und Anordnung der Schnittsequenz.
Effizientes Typografie-Design
Eine effiziente Layoutgestaltung ist der Schlüssel zur maximalen Materialausnutzung. Die Verwendung professioneller Layoutsoftware kann Designern dabei helfen, das Layout der Teile genau anzuordnen. Durch die automatische Layoutfunktion können Designer in kurzer Zeit die beste Anordnung der Teile berechnen, um sicherzustellen, dass der Abfall so weit wie möglich minimiert wird. Beim Layout ist es sehr wichtig, den Schneidpfad zu planen und den Abstand zwischen den Teilen (d. h. den Abfallteil) zu minimieren. Eine angemessene Abstandseinstellung kann nicht nur den Materialabfall reduzieren, sondern auch die nachfolgende Nachbearbeitungszeit und -kosten senken.
Bei der Gestaltung des Layouts müssen auch die Spezifikationen und die Dicke der Materialien berücksichtigt werden. Für Materialien unterschiedlicher Größe sind unterschiedliche Layoutstrategien erforderlich. Beispielsweise kann bei großformatigen Materialien eine sinnvolle Anordnung des Schnittpfads und der Schnittrichtung nicht nur den Abfall reduzieren, sondern auch Materialverformungen oder schlechte Schnitte vermeiden. Bei kleinformatigen Materialien hingegen muss das Layout die schneidbare Fläche jedes Materialstücks optimal nutzen, um Abfall zu vermeiden.
Gleichzeitig kann die Software auch den Schneidvorgang simulieren und die beste Schneidreihenfolge berechnen, um sicherzustellen, dass jedes Teil an der richtigen Stelle geschnitten wird. Dadurch werden unnötige Lücken und Abfall vermieden und die Produktionseffizienz verbessert. Wenn beispielsweise während des Schneidvorgangs zu viele leere Bereiche vermieden werden, kann sichergestellt werden, dass jedes Stück Material vollständig genutzt wird.
Vermeiden Sie überflüssiges Schneiden
Redundantes Schneiden bezieht sich auf mehrfaches Schneiden oder unnötiges wiederholtes Schneiden aufgrund unangemessenen Designs oder falscher Schnittpfadplanung. Redundantes Schneiden verschwendet nicht nur Material, sondern erhöht auch die Produktionszeit und verringert die Arbeitseffizienz. Beim Laserschneidprozess ist es wichtig, wiederholtes Schneiden oder sinnlose Pfade so weit wie möglich zu vermeiden, um die Materialausnutzung zu verbessern.
Eine vernünftige Planung der Schnittpfade kann sicherstellen, dass jedes Teil beim ersten Schnitt den erwarteten Effekt erzielt, ohne dass zusätzlicher Abfall durch nachträgliche Anpassung des Pfads oder zusätzliche Schnitte entsteht. Insbesondere in der Massenproduktion ist die Vermeidung redundanter Schnitte besonders wichtig, um die Produktionseffizienz zu verbessern und Material zu sparen. Beispielsweise kann die Verwendung einer Optimierungssoftware zur Bestimmung der Schnittreihenfolge und zur Sicherstellung, dass der Schnittpfad jedes Teils so kurz wie möglich und ohne Kreuzungen ist, das Auftreten redundanter Schnitte erheblich reduzieren.
Gleichzeitig kann das Vermeiden zu vieler Schnittpausen, Bewegungen oder wiederholter Arbeit während des Schneidvorgangs unnötigen Energieverbrauch und Zeitverschwendung reduzieren und die Gesamtproduktionseffizienz verbessern. Durch rationales Planen der Schnittfolge und des Schnittpfads kann sichergestellt werden, dass jeder Schnittvorgang notwendig ist, wodurch redundantes Schneiden und Materialverschwendung effektiv vermieden werden.
Intelligenter Schriftsatz und Prozesszusammenarbeit
Mit der kontinuierlichen Weiterentwicklung der Laserschneidtechnologie kann immer mehr intelligente Layoutsoftware mit der Produktionslinie zusammenarbeiten, um das Layoutdesign in Echtzeit an unterschiedliche Materialanforderungen anzupassen. Durch Datenanalyse und maschinelles Lernen kann intelligentes Layout den Schneidpfad und das Layout basierend auf historischen Daten und Echtzeit-Feedback optimieren und dabei nicht nur die Größe und Form des Materials berücksichtigen, sondern auch optimale Anpassungen basierend auf den Prozessanforderungen vornehmen. Diese intelligente Layoutmethode verbessert die Materialnutzung erheblich und reduziert den Bedarf an manuellen Eingriffen.
Beispielsweise kann das intelligente System den Schnittpfad und die Schnittreihenfolge während des Produktionsprozesses automatisch anpassen, dynamisch an die Eigenschaften verschiedener Materialien und den Produktionsrhythmus anpassen und das Layout und den Schnittpfad in Echtzeit optimieren, um den Abfall zu minimieren. Diese Technologie kann den Produktionsprozess effizienter und intelligenter machen, den Materialabfall deutlich reduzieren und die Schnittgenauigkeit verbessern.
Die Optimierung des Materiallayouts ist ein Schlüsselfaktor zur Verbesserung der Materialnutzung und zur Reduzierung des Abfalls beim CO2-Laserschneiden. Durch effizientes Layoutdesign, Vermeidung redundanter Schnitte und intelligente Layouttechnologie können unnötige Abfälle effektiv reduziert, die Produktionseffizienz verbessert und Kosten gesenkt werden. Ein vernünftiges Layout kann nicht nur den Materialverbrauch optimieren, sondern auch die Schnittqualität verbessern und sicherstellen, dass jeder Schneidvorgang effizient und präzise ist. In der modernen Fertigung ist die Optimierung des Materiallayouts zu einer wichtigen Strategie geworden, um die Produktionseffizienz zu verbessern und Abfall zu reduzieren.
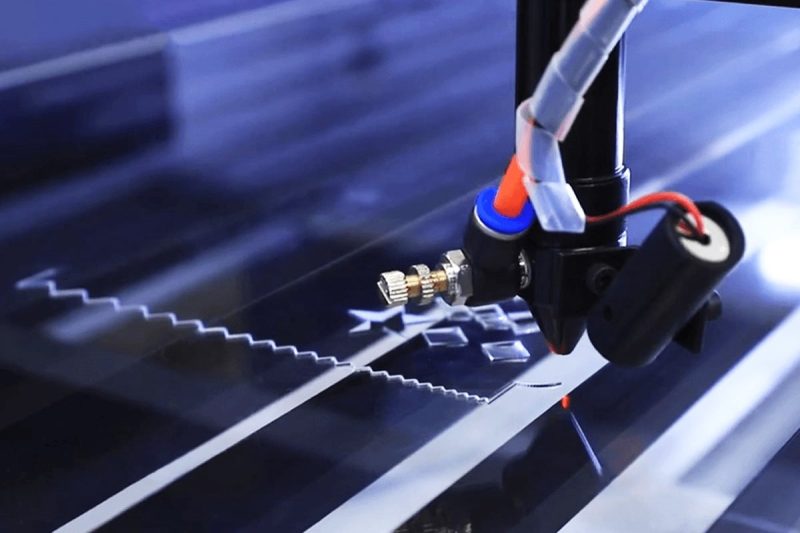
Verwenden Sie eine hochwertige Laserschneidmaschine
Die Leistung und Technologie der Geräte wirken sich direkt auf die Schnittgenauigkeit und den Materialabfall aus. Um das Ziel einer hohen Effizienz und geringen Abfallmenge beim CO2-Laserschneidprozess zu erreichen, ist es sehr wichtig, eine hochwertige Laserschneidmaschine auszuwählen. Hochwertige Laserschneidmaschinen sind nicht nur mit fortschrittlicher Strahlsteuerungstechnologie und präzisen Fokuseinstellungssystemen ausgestattet, sondern verfügen auch über eine stabile Leistung und effiziente Schneidfunktionen, die eine Schnittgenauigkeit gewährleisten und gleichzeitig den Materialabfall minimieren können.
Präzise Strahlsteuerung
Moderne High-End-CO2-Laserschneidmaschinen sind mit einer ausgeklügelten Strahlsteuerungstechnologie ausgestattet, um sicherzustellen, dass der Laserstrahl immer auf den Schnittbereich des Materials fokussiert ist. Diese Technologie umfasst eine hochpräzise Einstellung des Laserstrahls und ein Fokussteuerungssystem, das die Laserenergie präzise auf die Materialoberfläche fokussieren kann, was zu einer kleineren Wärmeeinflusszone und saubereren Schnittkanten führt. Die Reduzierung der Wärmeeinflusszone und des Anbrennens trägt nicht nur zur Verbesserung der Schnittqualität bei, sondern reduziert auch unnötigen Materialabfall.
Eine präzise Steuerung des Strahls ist die Grundlage für eine hohe Schnittqualität. Wenn die Fokusposition des Lasers genau ist, kann die Energie des Laserstrahls konzentriert und auf das Material übertragen werden. Dadurch wird eine übermäßige Energiestreuung in die Umgebung vermieden und Wärmeverlust und unnötiger Materialverlust reduziert. Darüber hinaus kann eine präzise Strahlsteuerung auch beim Schneiden komplexer Formen und feiner Details die Schnittfläche flach und fehlerfrei halten und so Materialverschwendung vermeiden.
Automatisches Anpassungssystem
Moderne CO2-Laserschneidmaschinen sind mit einem automatischen Anpassungssystem ausgestattet, das Laserleistung, Gasfluss, Schnittgeschwindigkeit und andere Parameter basierend auf Echtzeit-Feedbackdaten automatisch anpassen kann, um sicherzustellen, dass jeder Schneidpfad im besten Zustand ist. Diese automatische Anpassungsfunktion spielt eine wichtige Rolle im Schneidprozess und kann die Schneidparameter in Echtzeit unter verschiedenen Materialien und Schneidbedingungen optimieren, um Instabilitäten durch unsachgemäße menschliche Bedienung oder Umgebungsänderungen zu vermeiden.
Beispielsweise kann die automatische Anpassung der Laserleistung und des Gasflusses dynamisch entsprechend der Dicke und Art des Materials optimiert werden, wodurch eine moderate Wärmezufuhr während des Schneidvorgangs gewährleistet und Materialabtrag und Verformung durch übermäßige Wärmezufuhr reduziert werden. Gleichzeitig kann die automatische Anpassung der Schnittgeschwindigkeit entsprechend den Eigenschaften des Materials und der Komplexität des Schneidens angepasst werden, wodurch die Kontinuität und Qualität des Schneidpfads sichergestellt wird. Durch diese effiziente Echtzeitüberwachung und -anpassung wird die Laser-Schneide-Maschine kann nicht nur die Produktionseffizienz verbessern, sondern auch unnötigen Abfall deutlich reduzieren.
Darüber hinaus kann das automatische Anpassungssystem während des Schneidvorgangs auf der Grundlage von Echtzeit-Feedbackdaten Korrekturen vornehmen und alle Fehler korrigieren, die durch Änderungen der Werkstückposition, der Materialeigenschaften oder der Gerätegenauigkeit verursacht werden. Dadurch wird eine stabile Schnittqualität und minimaler Materialabfall aufrechterhalten. Diese Echtzeit-Anpassungsfunktion reduziert Abfall, der durch menschliche Fehler oder technologische Verzögerungen verursacht wird, erheblich und stellt sicher, dass jeder Schnitt unter den besten Bedingungen ausgeführt wird.
Mehrachsige Schneidetechnologie
Viele hochwertige CO2-Laserschneidmaschinen sind zudem mit Mehrachsen-Schneidtechnologie ausgestattet, die komplexere und präzisere Schneidewege ermöglicht. Die Mehrachsentechnologie kann gleichzeitig in mehrere Richtungen schneiden, was nicht nur die Schneideeffizienz verbessert, sondern auch den Materialabfall reduziert. Beispielsweise können einige Schneidemaschinen die Position des Laserkopfes anpassen, um den Schnittwinkel und -weg genauer einzustellen, sodass jeder Schneideweg Lücken minimiert und die Entstehung von nutzlosem Abfall reduziert.
Die Mehrachsentechnologie ermöglicht Laserschneidmaschinen eine flexiblere Bahnplanung während des Schneidvorgangs, insbesondere beim Schneiden komplexer Teile, wodurch übermäßiger Abfall aufgrund unsachgemäßer Bahnplanung wirksam vermieden werden kann. Darüber hinaus kann die Mehrachsen-Schneidtechnologie auch das Auftreten wiederholter Schnitte und redundanter Bahnen reduzieren und so den Materialabfall und die Produktionskosten weiter senken.
Laserwellenlänge und Fokussierungstechnologie
Verschiedene CO2-Laserschneidmaschinen können Laserstrahlen unterschiedlicher Wellenlänge verwenden, und die Wahl der Laserwellenlänge hat einen wichtigen Einfluss auf die Schneidgenauigkeit und -effizienz. CO2-Lasergeneratoren verwenden normalerweise Laser mit einer Wellenlänge von 10,6 Mikrometern, die beim Schneiden von Metallen und einigen nichtmetallischen Materialien eine sehr hohe Absorptionsrate aufweisen, sodass die Schneidwirkung effektiv verbessert werden kann. Hochwertige CO2-Laserschneidmaschinen sind mit fortschrittlichen optischen Systemen ausgestattet, um sicherzustellen, dass der Laserstrahl auf die Oberfläche des Materials fokussiert werden kann und ein hochpräzises Schneiden erreicht wird.
Durch die Feinsteuerung der Laserwellenlänge und des Strahlfokus können CO2-Laserschneidmaschinen beim Schneiden verschiedener Materialien effiziente und qualitativ hochwertige Schneidergebnisse erzielen. Eine höhere Strahlqualität bedeutet eine bessere Konzentration der Laserenergie, wodurch Energiestreuung und -abfall reduziert werden und Materialien effizienter genutzt werden können.
Die Wahl eines hochwertigen CO2-Laserschneidmaschine ist der Schlüssel zum effizienten Schneiden und zur Reduzierung von Materialabfall. Die umfassende Anwendung von präziser Strahlsteuerung, automatischem Anpassungssystem, mehrachsiger Schneidtechnologie, Laserwellenlänge und Fokussierungstechnologie kann nicht nur die Schnittgenauigkeit verbessern, sondern auch die Wärmeeinflusszone erheblich verkleinern und Materialabtrag und -abfall reduzieren. Durch die kontinuierliche Weiterentwicklung der Laserschneidtechnologie konnten moderne Laserschneidmaschinen ein effizientes und präzises Schneiden erreichen, wodurch die Materialnutzung erheblich verbessert und die Produktionskosten bei gleichzeitiger Gewährleistung der Schnittqualität gesenkt wurden.
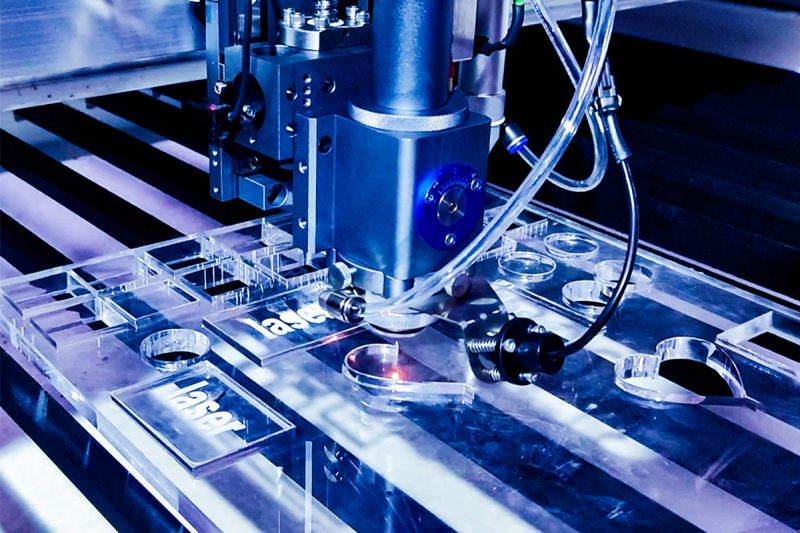
Sinnvolle Auswahl der Schneidstoffe
Die Wahl des richtigen Schneidmaterials ist entscheidend, um Materialabfall beim CO2-Laserschneiden zu reduzieren. CO2-Laserschneidmaschinen werden hauptsächlich zum Schneiden nichtmetallischer Materialien verwendet, insbesondere einiger Thermoplaste, Holz, Papier und Gewebe. Die Absorptionsfähigkeit, Wärmeleitfähigkeit, Reflektivität und andere Eigenschaften verschiedener Materialien beim Laserschneiden wirken sich direkt auf den Schneideffekt und den Materialabfall aus. Daher ist die Wahl des richtigen Schneidmaterials ein wichtiger Schritt zur Verbesserung der Effizienz und zur Abfallreduzierung.
Auswahl des geeigneten Materials
Der Vorteil der CO2-Laserschneidmaschine liegt in ihrer hohen Effizienz beim Schneiden nichtmetallischer Materialien. Bei der Auswahl der Schneidmaterialien sind die Absorption und Reflektivität des Materials entscheidend. Bei CO2-Laserschneidmaschinen kann die Auswahl von Materialien mit hoher Absorption der CO2-Laserwellenlänge dazu beitragen, die Schneideffizienz zu verbessern und Abfall zu reduzieren.
- Papier und Karton: Papier und Karton haben eine hohe Absorptionsrate für CO2-Laser, wodurch eine hohe Effizienz aufrechterhalten und der Abfall beim Schneiden reduziert werden kann. Diese Materialien werden häufig in den Bereichen Verpackung, Werbung und Design verwendet.
- Kunststoffe (wie Acryl, PVC): CO2-Laser haben eine gute Schneidwirkung bei Thermoplasten (wie Acryl, PVC usw.) und können die Schnittkante präzise steuern, um unnötige Wärmeeinflusszonen und Materialverschwendung zu vermeiden.
- Holz und Verbundwerkstoffe: CO2-Laserschneidmaschinen werden auch häufig zum Schneiden von Holz und Verbundwerkstoffen verwendet. Diese Materialien absorbieren CO2-Laser gut, wodurch saubere Schnitte erzielt, Verbrennungen und Hitzeschäden reduziert und eine maximale Materialausnutzung gewährleistet werden können.
Wählen Sie die richtige Materialstärke
Neben der Art des Materials beeinflusst auch die Dicke des Materials die Wirkung des CO2-Laserschneidens. Bei dünneren Materialien kann eine zu hohe Laserleistung zu übermäßiger Wärmezufuhr führen, was zu übermäßigen Wärmeeinflusszonen führt, was wiederum zu übermäßiger Ablation und Materialverschwendung führt. Umgekehrt kann bei dickeren Materialien eine zu geringe Laserleistung zu unvollständigem Schneiden führen.
- Dünne Materialien: Vermeiden Sie beim Schneiden dünner Materialien übermäßige Laserleistung oder langsame Schnittgeschwindigkeiten. Stellen Sie Leistung und Geschwindigkeit entsprechend ein, um übermäßiges Verbrennen und Abfall zu vermeiden.
- Dickere Materialien: Dickere Materialien erfordern eine höhere Laserleistung, um einen vollständigen Schnitt zu gewährleisten. Vermeiden Sie jedoch dennoch eine übermäßige Leistung, die zu Wärmeverlust oder unregelmäßigen Kanten führt.
Zusammenhang zwischen Wärmeleitfähigkeit und Laserschneiden
Auch die Wärmeleitfähigkeit verschiedener Materialien hat einen erheblichen Einfluss auf die Effektivität des Laserschneidens. Materialien mit hoher Wärmeleitfähigkeit (wie Metalle) leiten die Wärme schnell vom Schneidbereich ab, was zu unvollständigem Schneiden oder übermäßig wärmebeeinflussten Zonen führen kann, was zu mehr Materialabfall führt. Materialien mit geringerer Wärmeleitfähigkeit (wie Holz und Kunststoff) hingegen helfen, die Wärme zu konzentrieren, wodurch die Schneidergebnisse verbessert und Abfall reduziert wird.
Beim CO2-Laserschneiden weisen gängige nichtmetallische Materialien wie Kunststoffe und Holz eine geringe Wärmeleitfähigkeit auf, was dazu beiträgt, die Laserenergie effektiv zu nutzen und die Wärmeeinflusszone während des Schneidvorgangs zu reduzieren.
Der Einfluss der Oberflächenbehandlung des Materials auf die Schneidwirkung
Auch die Oberflächenbehandlung von Materialien ist beim CO2-Laserschneiden von entscheidender Bedeutung. Bei nichtmetallischen Materialien verringern Oberflächenschmutz, Fett, Oxidschichten usw. die Absorptionseffizienz des Lasers, was zu Energieverschwendung führt. Daher kann das Sicherstellen, dass die Oberfläche des Materials sauber und frei von Verunreinigungen ist, vor dem Laserschneiden die Schneideffizienz effektiv verbessern und Abfall reduzieren.
Beispielsweise absorbieren saubere Kunststoff- oder Holzoberflächen die Laserenergie effizienter, was zu effizienterem Schneiden und weniger Abfall führt. Wenn die Materialoberfläche Öl oder Verunreinigungen enthält, verringert sich die Absorptionsrate der Laserenergie, die Schneidwirkung ist schlecht und es entsteht Abfall.
Bei CO2-Laserschneidmaschinen ist es sehr wichtig, das richtige nichtmetallische Material und die richtige Materialstärke auszuwählen. Während des Schneidvorgangs wirken sich die Absorptionsrate, die Wärmeleitfähigkeit und der Oberflächenbehandlungszustand des Materials direkt auf die Effizienz der Laserenergienutzung aus und beeinflussen somit den Materialabfall. Eine sinnvolle Auswahl geeigneter Materialien und die Anpassung der Schneidparameter können nicht nur die Schneideffizienz verbessern, sondern auch den Materialabfall minimieren und die Produktionskosten senken. Durch die Optimierung der Materialauswahl und der Schneideinstellungen können Unternehmen eine höhere Materialausnutzung erreichen und gleichzeitig die Schnittqualität sicherstellen.
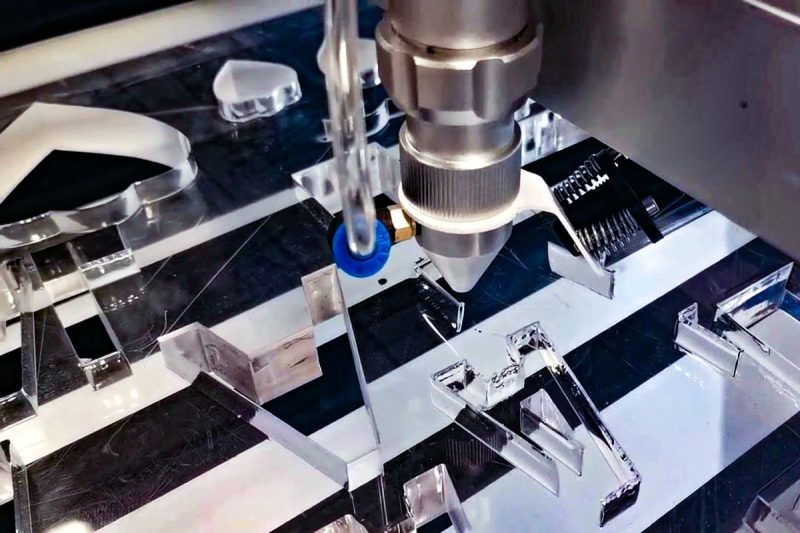
Aufrechterhaltung und Optimierung der Geräteleistung
Die Aufrechterhaltung der guten Leistung der Laserschneidmaschine ist ein Schlüsselfaktor zur Gewährleistung der Schnittgenauigkeit, zur Verbesserung der Produktionseffizienz und zur Reduzierung von Materialabfällen. Regelmäßige Gerätewartung kann nicht nur die Lebensdauer der Laserschneidmaschine verlängern, sondern auch die Stabilität der Geräte während des Schneidvorgangs sicherstellen und so Abfälle durch Geräteausfälle oder Leistungseinbußen wirksam reduzieren. Um die Geräteleistung zu maximieren, erfordert die Laserschneidmaschine eine Reihe regelmäßiger Inspektionen, Wartungen und Optimierungen. Hier sind einige wichtige Wartungsschritte und -vorschläge:
Überprüfen Sie regelmäßig die Optik
Optische Komponenten wie Laserköpfe, Reflektoren und Linsen wirken sich direkt auf die Fokussierungsqualität des Laserstrahls und die Schnittgenauigkeit aus. Mit der Zeit können diese optischen Komponenten durch Staub, Verunreinigungen oder hohe Temperaturen beschädigt oder abgenutzt werden, was die Qualität des Laserschneidens beeinträchtigt. Um die optimale Leistung der Laserschneidmaschine zu gewährleisten, müssen die optischen Komponenten regelmäßig überprüft und gereinigt werden. Die spezifischen Vorgänge sind wie folgt:
- Reinigen Sie die optischen Komponenten: Reinigen Sie die Linse und das Objektiv regelmäßig mit einem staubfreien Tuch und professioneller Reinigungsflüssigkeit. Vermeiden Sie die Verwendung rauer Materialien, um ein Verkratzen der Oberfläche der optischen Komponenten zu vermeiden. Das Sauberhalten der Linse und des Objektivs kann die Fokussierungsqualität des Laserstrahls sicherstellen und den Energieverlust verringern.
- Überprüfen Sie die optische Ausrichtung: Die Ausrichtung von Laserkopf, Reflektor und Linse wirkt sich direkt auf den Weg und die Brennpunktposition des Laserstrahls aus. Durch regelmäßiges Überprüfen der Ausrichtung der optischen Komponenten, um sicherzustellen, dass der Laserstrahl genau auf den Schneidbereich fokussiert ist, können Sie die Schnittqualität verbessern und Abfall reduzieren.
Wartung und Reinigung des Laserkopfes
Der Laserkopf ist eine der Kernkomponenten der Laserschneidmaschine und ist für die Fokussierung des Laserstrahls auf das Material verantwortlich. Mit der Zeit kann der Laserkopf verunreinigt oder abgenutzt werden, was zu einer ungenauen Laserfokussierung führt und den Schneideffekt beeinträchtigt. Daher ist eine regelmäßige Reinigung und Wartung des Laserkopfes unerlässlich. Vermeiden Sie beim Reinigen Kratzer oder Beschädigungen der Oberfläche des Laserkopfes, um Folgeschäden zu vermeiden. Achten Sie beim Reinigen besonders auf die folgenden Punkte:
- Optische Komponenten des Laserkopfes prüfen: Die Linsen und Spiegel im Inneren des Laserkopfes müssen regelmäßig auf Flecken, Kratzer oder andere Mängel geprüft werden. Bei Beschädigung oder Verschmutzung sollten sie umgehend ausgetauscht werden.
- Überprüfen Sie das Kühlsystem: Der Laserkopf ist normalerweise mit einem Kühlsystem ausgestattet, um sicherzustellen, dass der Laserkopf bei hohen Temperaturen stabil arbeitet. Überprüfen Sie das Kühlmittel und das Wärmeableitungssystem regelmäßig, um sicherzustellen, dass sie ordnungsgemäß funktionieren, um eine Verschlechterung der Leistung des Laserkopfs durch Überhitzung zu vermeiden.
Kalibrieren und Optimieren der Laserschneidparameter
Die Leistung einer Laserschneidmaschine hängt nicht nur von der Qualität der Hardware ab, sondern auch von ihren Schneidparametern. Im Laufe der Zeit können sich der Betriebszustand und die Schneidleistung der Ausrüstung ändern, daher muss die Laserschneidmaschine regelmäßig kalibriert und optimiert werden. Je nach Material müssen möglicherweise Parameter wie Laserleistung, Schneidgeschwindigkeit, Gasfluss und Fokusposition angepasst werden. Wenn sichergestellt wird, dass die Parametereinstellungen der Laserschneidmaschine immer im optimalen Zustand sind, kann der Materialabfall während des Schneidvorgangs erheblich reduziert werden.
- Laserleistung und Schnittgeschwindigkeit regelmäßig kalibrieren: Beim Laserschneiden sind Leistung und Schnittgeschwindigkeit entscheidende Faktoren, die sich auf das Schneidergebnis und den Materialabfall auswirken. Kalibrieren Sie die Ausrüstung regelmäßig, um sicherzustellen, dass Laserleistung und Schnittgeschwindigkeit immer im optimalen Arbeitsbereich liegen, um übermäßige Wärmezufuhr oder unvollständiges Schneiden zu vermeiden.
- Optimieren Sie die Brennpunktposition und Strahlqualität: Die Position des Laserbrennpunkts und die Qualität des Strahls bestimmen direkt die Genauigkeit und Wirkung des Schneidens. Stellen Sie durch Kalibrieren der Brennpunktposition sicher, dass die Energie des Laserstrahls im Schneidbereich konzentriert ist, verbessern Sie effektiv die Schneidgenauigkeit und reduzieren Sie den durch ungenaues Schneiden verursachten Abfall.
Überprüfen Sie regelmäßig den Gasfluss und das Kühlsystem
Die Hilfsgasdurchflussrate ist entscheidend für die Stabilität des Laserschneidprozesses. Eine zu hohe oder zu niedrige Gasdurchflussrate kann die Schnittqualität beeinträchtigen und den Materialabfall erhöhen. Daher ist eine regelmäßige Überprüfung und Optimierung der Gasdurchflussrate eine notwendige Maßnahme, um den effizienten Betrieb der Laserschneidmaschine aufrechtzuerhalten. Die Stabilität der Gasdurchflussrate hat direkte Auswirkungen auf den Schneideffekt, die Qualität der Schnittkante und den Grad des Materialabfalls.
Darüber hinaus darf die Wartung des Kühlsystems nicht vernachlässigt werden. Die Laserquelle und die optischen Komponenten der Laserschneidmaschine müssen innerhalb des entsprechenden Temperaturbereichs betrieben werden, um eine Überhitzung oder unzureichende Kühlung zu vermeiden, die zu Geräteschäden führen kann. Die Gewährleistung des normalen Betriebs des Kühlsystems kann nicht nur die Lebensdauer des Geräts verlängern, sondern auch die Schnittgenauigkeit verbessern und den durch Geräteausfälle verursachten Abfall reduzieren.
Vermeidung von Geräteausfällen und rechtzeitige Reparatur
Geräteausfälle sind eine der Hauptursachen für Probleme beim Laserschneidprozess. Um Produktionsunterbrechungen und Materialverschwendung durch Geräteausfälle zu vermeiden, sind regelmäßige Geräteinspektionen und Fehlerprävention unerlässlich. Regelmäßige Inspektionen mechanischer Teile, elektrischer Systeme, Laserquellen usw., um sicherzustellen, dass sie in gutem Betriebszustand sind, können Geräteausfällen wirksam vorbeugen. Darüber hinaus sollten bei festgestellten Problemen Reparaturen und der Austausch beschädigter Teile umgehend durchgeführt werden, um eine geringe Produktionseffizienz oder Materialverschwendung aufgrund von Geräteausfällen zu vermeiden.
Regelmäßige Wartung und Optimierung der Ausrüstung trägt nicht nur dazu bei, die Lebensdauer der Laserschneidmaschine zu verlängern, sondern stellt auch sicher, dass die Ausrüstung immer in optimalem Betriebszustand ist, wodurch Schnittgenauigkeit, Stabilität und Materialausnutzung verbessert werden. Durch Überprüfen und Reinigen optischer Komponenten, Kalibrieren der Schneidparameter, Optimieren des Gasflusses und der Kühlsysteme usw. kann der durch Leistungsabfall der Ausrüstung verursachte Abfall erheblich reduziert werden. Darüber hinaus sind rechtzeitige Wartung und Fehlervermeidung ebenfalls wichtige Mittel, um den kontinuierlichen und effizienten Betrieb der Ausrüstung sicherzustellen. Durch umfassendes Management und Optimierung der Ausrüstungsleistung kann die Laserschneidmaschine lange Zeit effizient arbeiten, Materialabfall minimieren und die Produktionseffizienz verbessern.
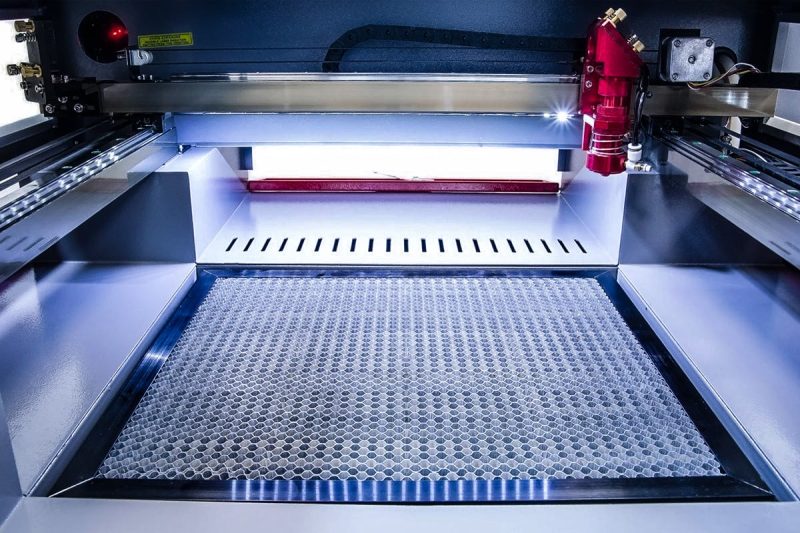
Zusammenfassen
CO2-Laserschneiden ist eine effiziente und präzise Schneidtechnologie, aber in der Praxis ist Materialabfall immer noch ein wichtiges Problem. Durch genaue Kontrolle der Schneidparameter, Optimierung der Materialanordnung und Auswahl geeigneter Geräte und Materialien kann Materialabfall minimiert, die Produktionseffizienz verbessert und Kosten gesenkt werden. Mit der kontinuierlichen Weiterentwicklung der Lasertechnologie und der Verbesserung der Geräteleistung wird das CO2-Laserschneiden in Zukunft umweltfreundlicher und wirtschaftlicher sein und der Fertigungsindustrie mehr nachhaltige Entwicklungsmöglichkeiten bieten.
In diesem Zusammenhang AccTek-Laser CO2-Laserschneidmaschinen bieten Kunden mit ihrer hervorragenden Technologie, ihrem präzisen Steuerungssystem und ihren effizienten Schneidfunktionen effizientere und umweltfreundlichere Schneidlösungen und helfen Unternehmen, Materialabfälle zu minimieren und die Produktionseffizienz und Kosteneffizienz zu verbessern. Wenn Sie eine CO2-Laserschneidmaschine benötigen, kontaktieren Sie uns bitte umgehend für ein Angebot.
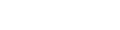
Kontaktinformationen
- [email protected]
- [email protected]
- +86-19963414011
- Nr. 3 Zone A, Industriegebiet Lunzhen, Stadt Yucheng, Provinz Shandong.
Holen Sie sich Laserlösungen