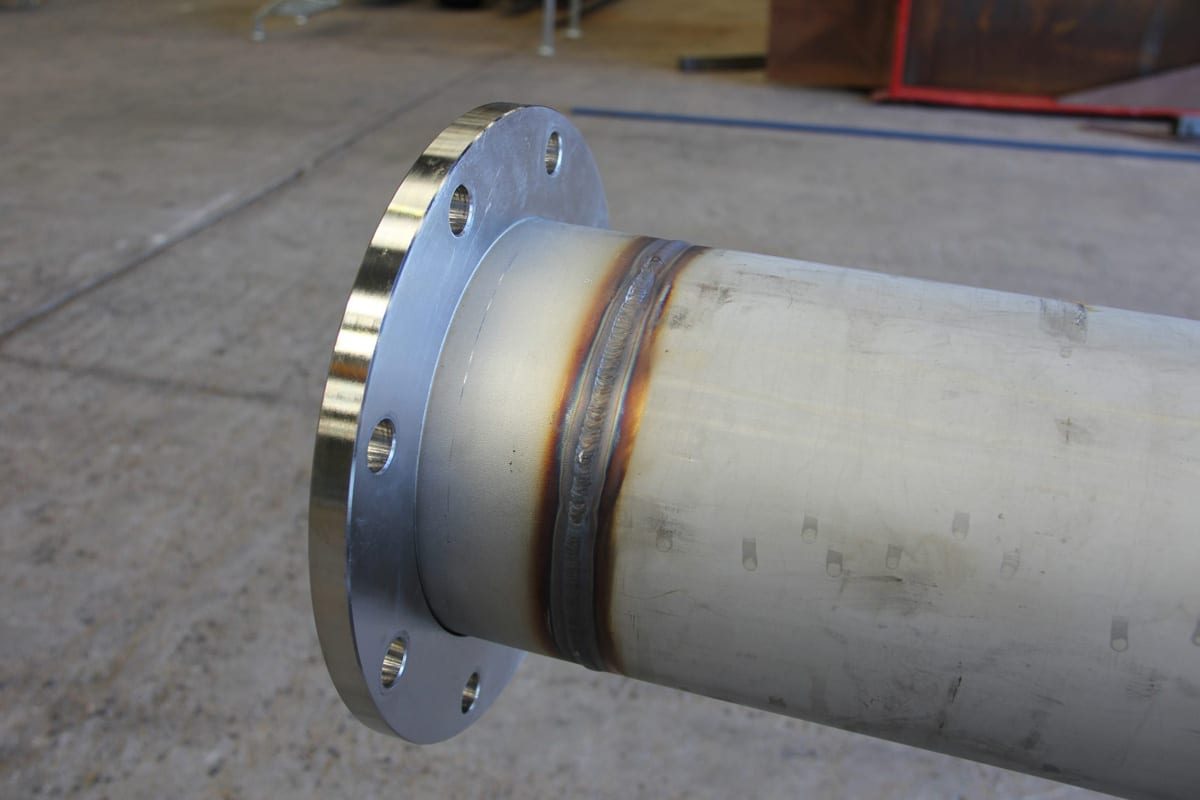
So verbessern Sie die Festigkeit von Laserschweißverbindungen
Laserschweißen wird aufgrund seiner geringen Wärmezufuhr, der tiefen Durchdringung und der hervorragenden Automatisierungsmöglichkeiten häufig in der Automobilherstellung, der Luft- und Raumfahrt sowie der Elektronikindustrie als effiziente und präzise Schweißtechnologie eingesetzt. Diese Technologie kann die Produktionseffizienz erheblich verbessern und gleichzeitig die Schweißqualität sicherstellen sowie Materialverformungen und Verarbeitungsschritte reduzieren. Daher ist das Laserschweißen zu einem unverzichtbaren und wichtigen Mittel in der modernen Fertigung geworden.
Die Festigkeit von Schweißverbindungen steht jedoch in direktem Zusammenhang mit der Leistung und Zuverlässigkeit von Produkten, insbesondere bei Anwendungen mit hoher Beanspruchung oder komplexen Arbeitsumgebungen. Die Optimierung von Materialien, Prozessen und Konstruktionen zur weiteren Verbesserung der Festigkeit von Schweißverbindungen ist ein zentrales Thema in der Technologieforschung und -entwicklung sowie in industriellen Anwendungen. Dieser Artikel beginnt mit den wichtigsten Faktoren, die die Schweißfestigkeit beeinflussen, analysiert detailliert die fortschrittlichen Technologien zur Verbesserung der Festigkeit, untersucht die Bedeutung der Nachbehandlung von Schweißnähten und bietet Lösungen für häufige Herausforderungen.
Inhaltsverzeichnis
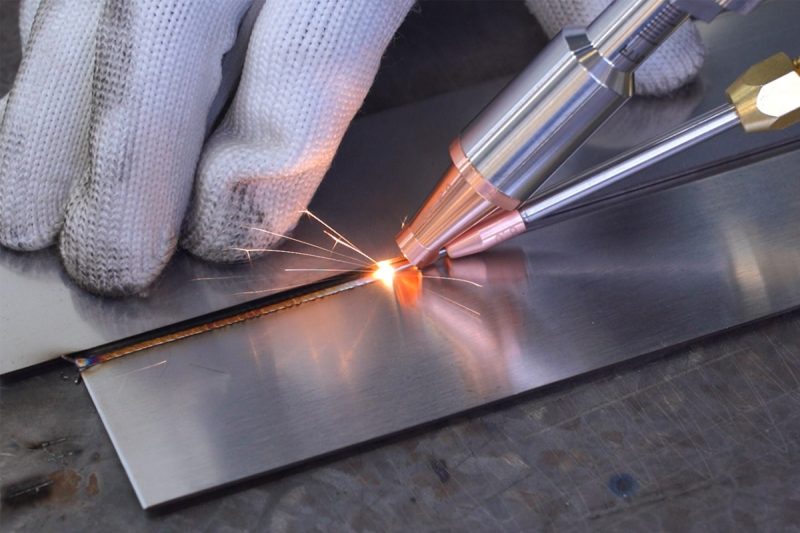
Erfahren Sie mehr über Laserschweißen
Beim Laserschweißen wird ein energiereicher Laserstrahl als Wärmequelle verwendet, der auf einen sehr kleinen Punkt fokussiert werden kann, um eine geringe Wärmezufuhr und tiefe Durchdringungsschweißeffekte zu erzielen. Die einzigartigen Vorteile dieser Technologie sind ihre Genauigkeit und Flexibilität, wodurch sie sich besonders für komplexe geometrische Strukturen, hohe Präzisionsanforderungen und schwer zugängliche Schweißbereiche eignet. Im Vergleich zu herkömmlichen Schweißverfahren kann das Laserschweißen nicht nur die thermische Verformung und die Eigenspannung deutlich reduzieren, sondern auch die Verarbeitungsgeschwindigkeit und Produktionseffizienz verbessern.
Zusätzlich, Laserschweißgerät kann zum Verbinden einer Vielzahl von Materialien, einschließlich verschiedener Metalle und Legierungsmaterialien, verwendet werden und spielt eine wichtige Rolle, insbesondere im Zusammenhang mit der steigenden Nachfrage nach leichten und hochfesten Komponenten in der Fertigungsindustrie. Bei der Erzielung eines effizienten Schweißens bleibt jedoch die Festigkeit der Schweißverbindung ein Schlüsselfaktor, der sich auf die Leistung und Zuverlässigkeit des Produkts auswirkt. Dies erfordert eine kontinuierliche Verbesserung der Schweißqualität durch Optimierung von Materialien, Prozessen und Designs, um den Anforderungen anspruchsvoller Industrieanwendungen gerecht zu werden.
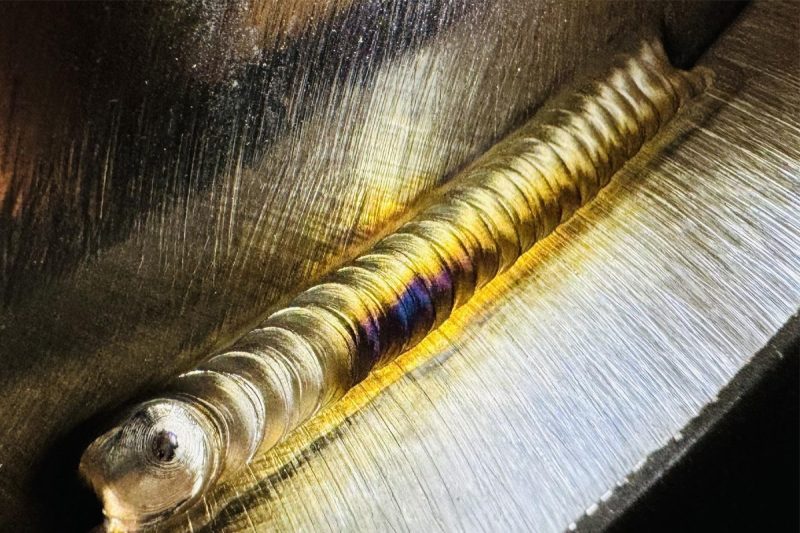
Faktoren, die die Schweißfestigkeit beeinflussen
Die Festigkeit lasergeschweißter Verbindungen wird durch eine Kombination von Faktoren beeinflusst, darunter Materialeigenschaften, Laserparameter, Verbindungsdesign und Schweißumgebung. Um qualitativ hochwertige Schweißverbindungen zu erzielen, ist ein tiefes Verständnis der spezifischen Rolle dieser Faktoren und ihrer gegenseitigen Beeinflussung erforderlich, um jede Verbindung in praktischen Anwendungen zu optimieren. Im Folgenden werden diese Faktoren im Detail analysiert.
Materialeigenschaften
Eine wichtige Grundlage zur Ermittlung des Schweißergebnisses sind die Werkstoffeigenschaften, die sich im Wesentlichen in der Zusammensetzung des Grundwerkstoffs, der Materialstärke und der Oberflächenbeschaffenheit äußern.
- Substratzusammensetzung: Unterschiedliche Materialien haben unterschiedliche Absorptionsraten für Laser. Beispielsweise haben stark reflektierende Metalle (wie Aluminium und Kupfer) niedrige Absorptionsraten für Laserenergie, was leicht zu unzureichender Durchdringung führen kann. Es ist notwendig, den Schweißeffekt durch Anpassen der Laserparameter oder Beschichten der Oberfläche mit absorbierenden Materialien zu verbessern.
- Materialdicke: Die Materialdicke wirkt sich direkt auf die Energieverteilung des Lasers aus. Zu dicke Materialien können eine unzureichende Laserdurchdringung verursachen, was zu unvollständigen Durchdringungsschweißungen führt; während zu dünne Materialien aufgrund übermäßiger Laserenergie zum Durchbrennen neigen, was eine sorgfältige Anpassung der Parametereinstellungen erfordert.
- Oberflächenzustand: Die Sauberkeit, Oxidschicht und Rauheit der Materialoberfläche beeinflussen die Transmission und Absorption des Lasers. Oberflächenverunreinigungen oder Oxidation können zu einer ungleichmäßigen Schmelzbadbildung führen und die Schweißfestigkeit verringern. Daher sind eine Reinigung vor dem Schweißen und eine ordnungsgemäße Oberflächenbehandlung unerlässlich.
Laserparameter
Die Wärmezufuhr und die Schmelzbadbildung beim Schweißen werden direkt von den Laserparametern bestimmt.
- Laserleistung: Eine zu geringe Leistung kann zu unzureichender Durchdringung und geschwächter Schweißfestigkeit führen, während eine zu hohe Leistung leicht zu Materialdurchbrand oder Bildung eines übermäßig großen Schmelzbads führen kann, wodurch die Festigkeit der Schweißverbindung geschwächt wird. Daher ist es notwendig, die geeignete Leistungsstufe entsprechend den Materialeigenschaften und der Materialdicke auszuwählen.
- Schweißgeschwindigkeit: Eine zu hohe Schweißgeschwindigkeit kann zu einer unzureichenden Schmelzbadbildung führen und in der Schweißnaht können Poren oder Risse auftreten. Eine zu niedrige Geschwindigkeit kann hingegen zu einer übermäßigen Wärmezufuhr führen, die eine Überhitzung oder sogar Verformung des Materials zur Folge hat.
- Fokusposition: Eine genaue Positionierung des Laserfokus trägt dazu bei, die effektive Energienutzung zu maximieren und die Tiefe und Gleichmäßigkeit des Schmelzbades sicherzustellen. Eine Fokusabweichung führt zu einer verringerten Schweißeffizienz und kann zu Qualitätsmängeln führen.
- Pulsparameter: Beim gepulsten Laserschweißen wirkt sich die Einstellung von Pulsbreite und -frequenz direkt auf den Bildungsprozess und die Erstarrung des Schmelzbades aus. Durch die Optimierung der Pulsparameter kann die Entstehung von Rissen und Poren verringert und die Schweißfestigkeit verbessert werden.
Steckverbinderdesign
Die Gestaltung der Verbindung wirkt sich nicht nur auf die Leichtigkeit des Schweißens aus, sondern steht auch in direktem Zusammenhang mit den mechanischen Eigenschaften und der Zuverlässigkeit der Schweißnaht.
- Verbindungskonfiguration: Verschiedene Verbindungsarten (z. B. Stumpfstöße, Überlappstöße) eignen sich für unterschiedliche strukturelle Anforderungen und mechanische Leistungsanforderungen. Beispielsweise eignen sich Stumpfstöße für hochfestes Schweißen, während Überlappstöße besser für das Schweißen dünner Platten geeignet sind.
- Montage und Ausrichtung: Schlechte Montage oder Ausrichtungsfehler können zu Schweißbadwanderung oder Schweißfehlern führen und so die Schweißfestigkeit verringern. Im tatsächlichen Betrieb kann die Verwendung von Präzisionsvorrichtungen oder automatischen Ausrichtungssystemen die Montagegenauigkeit erheblich verbessern.
- Kantenvorbereitung: Die Qualität der Kantenvorbereitung ist für das Schweißergebnis entscheidend. Unebene oder gratige Kanten können Risse oder Einschlussfehler verursachen, daher sind für die Bearbeitung der Kanten Präzisionsbearbeitungsgeräte erforderlich.
Schweißumgebung
Die Schweißumgebung ist ein externer Faktor, der die Schweißqualität beeinflusst, einschließlich der Auswahl des Schutzgases und der Kontrolle der Umgebungsbedingungen.
- Schutzgas: Die richtige Art und Strömung des Schutzgases kann die Oxidation des Schmelzbades verhindern und die Kompaktheit und Korrosionsbeständigkeit der Schweißverbindung verbessern. Beispielsweise werden Argon und Helium häufig als Schutzgase verwendet, und eine zu große oder zu geringe Strömung beeinträchtigt die Schutzwirkung.
- Umgebungsbedingungen: Eine Umgebung mit hoher Luftfeuchtigkeit, zu viel Staub oder starken Temperaturunterschieden kann sich negativ auf den Schweißprozess auswirken und sogar die Leistung der Schweißnaht verschlechtern. Daher ist die Aufrechterhaltung einer guten Umgebungskontrolle im Schweißbereich eine wichtige Maßnahme zur Gewährleistung der Schweißqualität.
Die Faktoren, die die Festigkeit von Laserschweißverbindungen beeinflussen, sind komplex und vielfältig und betreffen alle Aspekte der Materialeigenschaften, Laserparameter, Verbindungskonstruktion und Schweißumgebung. In praktischen Anwendungen müssen diese Faktoren umfassend berücksichtigt werden, und durch eine angemessene Prozessoptimierung und Geräteanpassung können qualitativ hochwertige, hochfeste Schweißverbindungen erzielt werden.
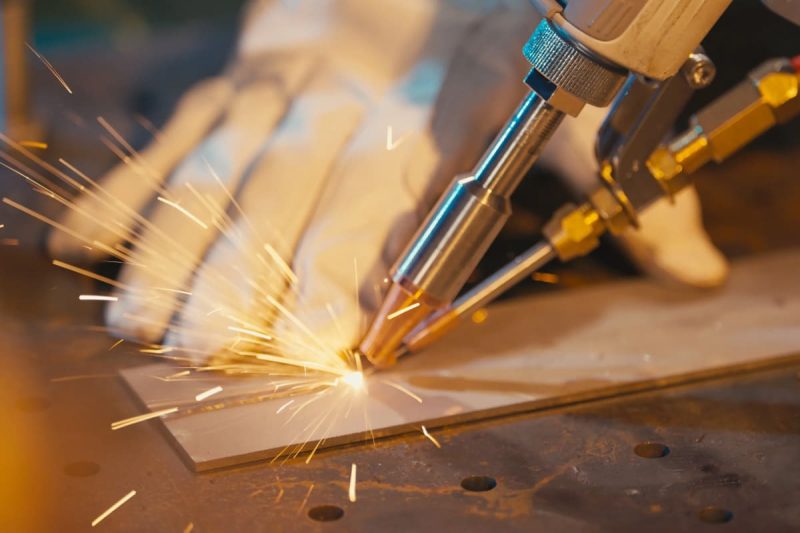
Technologie zur Verbesserung der Schweißfestigkeit
Um die Festigkeit von lasergeschweißten Verbindungen zu verbessern, müssen die Materialeigenschaften, die Lasertechnologie, die Schweißprozesssteuerung und die Nachbehandlung optimiert werden. Dazu gehört nicht nur die Auswahl und Vorbereitung der Schweißmaterialien, sondern auch die genaue Anpassung der Laserparameter, die Gestaltung sinnvoller Verbindungsformen und der Einsatz fortschrittlicher Prozesssteuerungstechnologie. Durch eine umfassende Optimierung dieser Verbindungen können die mechanischen Eigenschaften und die Zuverlässigkeit der Schweißnaht erheblich verbessert werden. Spezifische technische Methoden zur Verbesserung der Schweißfestigkeit werden im Folgenden erläutert.
Materialauswahl und -vorbereitung
Materialien bilden die Grundlage der Schweißleistung und spielen eine entscheidende Rolle für die Festigkeit von Schweißverbindungen.
- Legierungsoptimierung: Durch die Auswahl hochfester, für das Laserschweißen geeigneter Materialien und die Anpassung der Legierungszusammensetzung können die Schweißergebnisse deutlich verbessert werden. Durch das Hinzufügen bestimmter Elemente zur Verbesserung der Schweißbarkeit und Ermüdungsbeständigkeit des Materials kann die Schweißnaht beispielsweise auch in rauen Umgebungen stabil bleiben.
- Oberflächenreinigung: Reinigen Sie die Materialoberfläche vor dem Schweißen gründlich, um Fett, Oxidschichten und andere Verunreinigungen zu entfernen, eine effiziente Übertragung der Laserenergie sicherzustellen und Schweißfehler zu reduzieren. Zu den gängigen Methoden gehören mechanische Reinigung, chemische Reinigung und Laserreinigung.
- Vorwärmen: Bei sehr hitzeempfindlichen oder zur Rissbildung neigenden Werkstoffen kann durch entsprechendes Vorwärmen der Temperaturgradient beim Schweißvorgang verringert und die thermische Spannung reduziert werden, was zu einer verbesserten Schweißqualität führt.
Laseroptimierung
Die Anpassung der Laserparameter beeinflusst unmittelbar die Umformqualität und die mechanischen Eigenschaften der Schweißnaht.
- Steuerung der Leistungsdichte: Passen Sie die Laserleistungsdichte präzise an, um eine gleichmäßige Verteilung des Schmelzbads zu gewährleisten und so die Dichte und Festigkeit der Schweißnaht zu verbessern. Eine geringere Leistungsdichte kann zu unzureichender Durchdringung führen, während eine zu hohe Leistungsdichte leicht zu Durchbrand oder Metallspritzern führen kann.
- Strahlformung: Durch die Optimierung der Form des Laserspots kann die Wärmeverteilung während des Schweißvorgangs verbessert werden. So kann beispielsweise die Änderung des kreisförmigen Spots in eine elliptische oder linear verteilte Strahlform das Auftreten von Schweißporen deutlich reduzieren und die Stabilität der Schweißnaht verbessern.
- Fokuseinstellung: Die genaue Positionierung des Laserfokus ist der Schlüssel zur Verbesserung der Schweißqualität. Ein zu tiefer Fokus kann zu unzureichender Durchdringung führen, während ein zu flacher Fokus zu Oberflächenablationsproblemen führen kann. Eine optimale Durchdringung der Schweißnaht wird daher durch automatische Fokuseinstellung oder präzise mechanische Einstellung sichergestellt.
Prozesssteuerung
Eine moderne Prozesskontrolltechnologie gewährleistet die Stabilität der Schweißqualität.
- Adaptives Steuerungssystem: Verwenden Sie Echtzeit-Überwachungsgeräte (wie Kameras und Sensoren), um wichtige Parameter im Schweißprozess zu überwachen, und passen Sie Laserleistung, Schweißgeschwindigkeit usw. automatisch an, um sicherzustellen, dass die Schweißqualität immer optimal ist.
- Geschlossener Feedback-Kreislauf: Der Sensor erfasst Daten wie Form und Temperatur des Schmelzbads und gibt diese in Echtzeit an das Steuerungssystem zurück, wodurch die Schweißparameter dynamisch optimiert und Schweißfehler reduziert werden können.
- Algorithmus für maschinelles Lernen: Durch die Einführung künstlicher Intelligenz und maschineller Lerntechnologie werden große Mengen an Schweißdaten analysiert, die beste Parameterkombination vorhergesagt, der Schweißprozess weiter optimiert und der Automatisierungsgrad verbessert.
Fugengestaltung und -vorbereitung
Die Fugenkonstruktion und Kantenvorbereitung spielen eine wichtige Rolle für die Festigkeit von Schweißverbindungen.
- Optimierte Fugengeometrie: Die Fugenform wird entsprechend dem Schweißverfahren und den strukturellen Anforderungen ausgelegt. Beispielsweise eignen sich Stumpfstöße für hochfeste Schweißungen, während Überlappstöße eher für dünne Blechverbindungen geeignet sind. Durch eine Optimierung der Fugengeometrie können die mechanischen Eigenschaften der Schweißnaht deutlich verbessert werden.
- Präzise Montage und Ausrichtung: Verwenden Sie hochpräzise Vorrichtungen und automatische Positionierungsgeräte, um die Ausrichtungsgenauigkeit der Verbindungen sicherzustellen. Dadurch werden Schweißversatz und schlechte Verbindungen vermieden und die Gesamtfestigkeit der Schweißnähte verbessert.
- Kantenvorbereitung: Bearbeiten Sie die Schweißkante mit Präzisionsgeräten, um sie glatt und gratfrei zu machen. Dadurch kann die Rissneigung wirksam verringert und die Konsistenz und Zuverlässigkeit der Schweißnaht verbessert werden.
Nachbehandlung nach dem Schweißen
Durch eine Schweißnachbehandlung können Schweißeigenspannungen weiter gelöst und die mechanischen Eigenschaften sowie die Lebensdauer der Schweißnaht verbessert werden.
- Wärmebehandlung: Schweißspannungen durch Glühen oder Anlassen lösen, die Mikrostruktur der Schweißnaht und der umgebenden Materialien verbessern und die Zähigkeit und Festigkeit des Materials steigern.
- Oberflächenbearbeitung: Entfernen Sie raue Teile und Defekte auf der Schweißoberfläche durch Schleifen oder Polieren und verbessern Sie so ihre Ermüdungsbeständigkeit und Ästhetik.
- Zerstörungsfreie Prüfung: Verwenden Sie zerstörungsfreie Prüfmethoden wie Ultraschall- und Röntgenprüfungen, um sicherzustellen, dass in der Schweißnaht keine versteckten Gefahren wie Risse und Poren vorhanden sind, und verbessern Sie so die Zuverlässigkeit des Produkts weiter.
- Mechanische Bearbeitung: Verbessern Sie die Verteilung der Eigenspannung auf der Schweißnahtoberfläche durch Methoden wie Kugelstrahlen und verwenden Sie Walztechnologie, um die Dichte und Ermüdungsbeständigkeit der Schweißnaht durch mechanischen Druck zu verbessern. Diese mechanischen Bearbeitungsmethoden können zusätzliche Verstärkungsmaßnahmen für die Schweißnaht bieten.
Die Verbesserung der Festigkeit von Laserschweißverbindungen erfordert eine umfassende Optimierung vieler Aspekte, von der Materialauswahl und -vorbereitung über die genaue Einstellung der Laserparameter bis hin zur fortschrittlichen Prozesssteuerung und Nachbehandlung nach dem Schweißen. Jedes Glied ist entscheidend. Durch wissenschaftliche und sinnvolle Prozesskombinationen können nicht nur die mechanischen Eigenschaften von Schweißverbindungen verbessert werden, sondern auch die allgemeine Schweißqualität und -zuverlässigkeit, was eine starke Unterstützung für anspruchsvolle industrielle Anwendungen bietet.
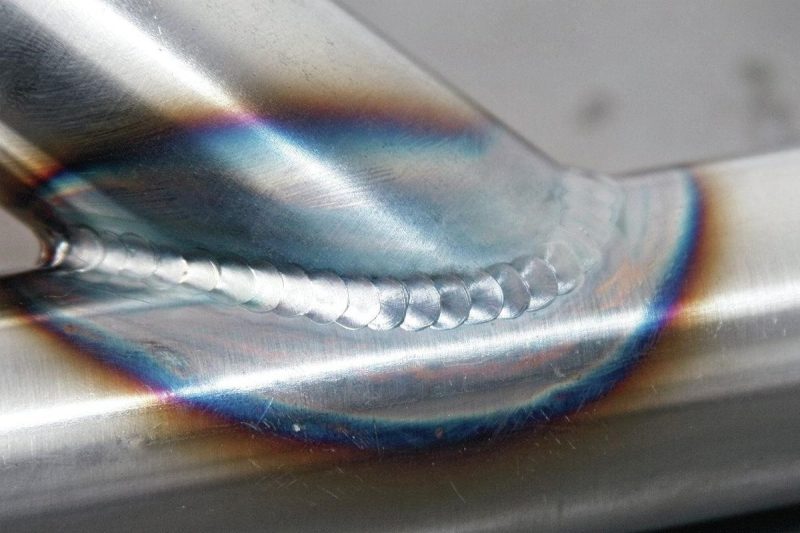
Herausforderungen und Lösungen
Obwohl die Effizienz und Präzision der Laserschweißtechnologie viele Branchenanwendungen stark unterstützt, gibt es in der Praxis immer noch einige Herausforderungen, die sich direkt auf die Qualität und Stabilität der Schweißverbindungen auswirken. Um diese Herausforderungen zu bewältigen, können effektive Lösungen nicht nur die Schweißqualität verbessern, sondern auch den Anwendungsbereich des Laserschweißens erweitern. Im Folgenden werden die drei wichtigsten Herausforderungen Wärmemanagement, Materialverträglichkeit und Prozessstabilität sowie ihre Lösungen ausführlich erörtert.
Wärmemanagement
Das Wärmemanagement ist ein wichtiges Thema, das beim Laserschweißen berücksichtigt werden muss. Beim Laserschweißen kann es aufgrund der konzentrierten Wärmezufuhr leicht zu einer lokalen Überhitzung des Materials kommen, was zu Verformungen, thermischen Rissen oder Eigenspannungen führen kann, was wiederum die Festigkeit und Lebensdauer der Schweißverbindung verringern kann.
Herausforderungsanalyse
- In Umgebungen mit hoher Wärmezufuhr kann eine ungleichmäßige Ausdehnung und Kontraktion von Materialien zu Verformungen führen, insbesondere beim Schweißen dünner Materialien und Präzisionsteile.
- Zu hohe Temperaturen können zu Rissen oder interkristalliner Korrosion in der Schweißnaht führen und so die Schweißleistung beeinträchtigen.
Lösung
- Schweißpfad optimieren: Optimieren Sie den Schweißpfad durch computergestütztes Design (CAD), verteilen Sie die Wärmezufuhr und reduzieren Sie die Temperatur im Wärmestaubereich.
- Kühlgerät: Durch den Einsatz einer Kühlwasservorrichtung oder einer Luftkühlung während des Schweißens kann die Wärmezufuhrintensität des Schweißbereichs wirksam gesteuert und die Wahrscheinlichkeit thermischer Verformungen und Risse verringert werden.
- Pulslasermodus: Durch die Verwendung des Pulslaserschweißens anstelle des kontinuierlichen Laserschweißens kann die Wärmezufuhr besser kontrolliert, der Bereich der Wärmeeinflusszonen verringert und somit die Schweißqualität verbessert werden.
Materialkompatibilität
In der industriellen Produktion kommt das Schweißen unterschiedlicher Materialien wie Stahl und Aluminium, Kupfer und Edelstahl usw. immer häufiger vor. Die Unterschiede in den physikalischen und chemischen Eigenschaften dieser Materialien können zu Schweißschwierigkeiten führen.
Herausforderungsanalyse
- Beim Schweißen ungleicher Materialien kommt es häufig zu schlechter Verschmelzung, spröden Phasen oder Schnittstellenrissen, welche die Festigkeit und Zuverlässigkeit der Schweißverbindung erheblich beeinträchtigen.
- Die unterschiedlichen Ausdehnungskoeffizienten der Materialien können beim Abkühlen zu großen Restspannungen in der Schweißnaht führen und so die Rissgefahr erhöhen.
Lösung
- Wählen Sie kompatible Legierungen: Wählen Sie durch Optimieren der Materialformel Legierungen mit höherer Kompatibilität als Grundmaterial aus, um das Auftreten von schlechter Verschmelzung und Rissen zu reduzieren.
- Verwenden Sie Füllmaterialien: Das Hinzufügen bestimmter Füllmaterialien (wie Vorlegierungen oder Schweißdrähte) während des Schweißvorgangs kann die Fusionsleistung der beiden Materialien verbessern und gleichzeitig die Komplexität der Grenzflächenreaktion verringern.
- Optimierung der Laserparameter: Passen Sie Laserleistung, Schweißgeschwindigkeit und Fokusposition präzise an, um die spezifischen Anforderungen des Schweißens ungleichartiger Materialien zu erfüllen und die Stabilität und Gleichmäßigkeit des Schmelzbades sicherzustellen.
Prozessstabilität
Laserschweißen ist ein stark von Parametern abhängiger Prozess. Schwankungen der Schweißparameter können zu Ungleichmäßigkeiten in der Schweißqualität führen und so die Produktionseffizienz und Produktleistung beeinträchtigen.
Herausforderungsanalyse
- Eine instabile Laserleistung oder Schweißgeschwindigkeit kann zu einer ungleichmäßigen Schweißtiefe, -breite und -stärke führen.
- Vibrationen in der Schweißausrüstung oder eine lockere Materialklemmung können zu Schweißfehlern wie mangelnder Verschmelzung, Porosität oder Versatz führen.
Lösung
- Adaptive Steuerung: Einführung eines intelligenten adaptiven Steuerungssystems zur dynamischen Anpassung der Laserleistung und Schweißgeschwindigkeit entsprechend der in Echtzeit überwachten Schweißparameter (wie Temperatur, Form des Schmelzbads usw.) und damit zur Gewährleistung einer hohen Prozessstabilität.
- Geschlossenes Rückkopplungssystem: Verwenden Sie hochpräzise Sensoren, um wichtige Daten im Schweißprozess zu erfassen und diese zur automatischen Anpassung an das Steuerungssystem zurückzugeben. Beispielsweise wird die Fokusposition durch Echtzeitüberwachung der Formänderungen des Schmelzbads dynamisch angepasst, um die Konsistenz der Schweißnaht sicherzustellen.
- Optimierung durch künstliche Intelligenz: Einführung eines auf maschinellem Lernen basierenden Algorithmus, um durch Big Data-Analyse und Parametervorhersage eine automatische Optimierung des Laserschweißprozesses zu erreichen, die Auswirkungen von Parameterschwankungen zu verringern und die Zuverlässigkeit und Wiederholbarkeit des Schweißens zu verbessern.
Bei Laserschweißanwendungen sind Wärmemanagement, Materialverträglichkeit und Prozessstabilität die drei wichtigsten Herausforderungen, die die Schweißqualität beeinflussen. Diese Probleme können durch den Einsatz optimierter Schweißwege, kompatibler Legierungen, Füllmaterialien und intelligenter Steuerungstechnologie effektiv gelöst werden, um die mechanischen Eigenschaften und die Prozessstabilität der Schweißnaht zu verbessern. Diese Lösungen können nicht nur die hohen Anforderungen der aktuellen industriellen Produktion erfüllen, sondern auch eine solide Grundlage für die Weiterentwicklung der Laserschweißtechnologie bieten.
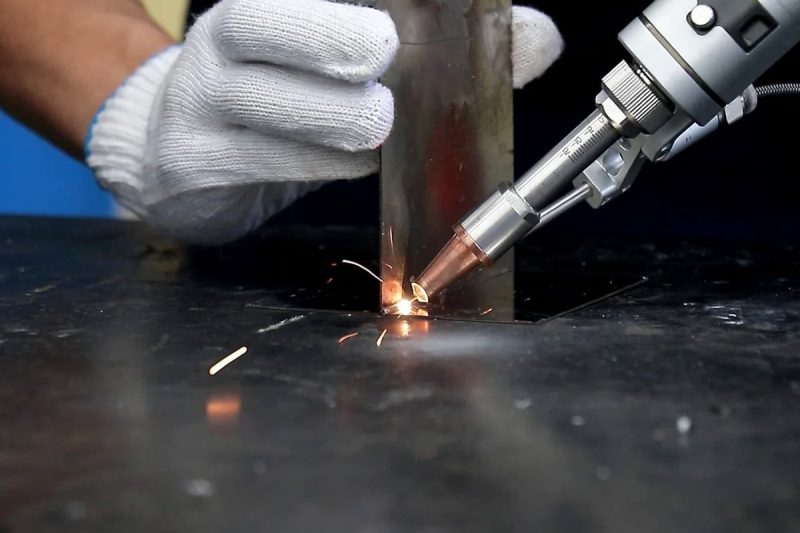
Zusammenfassen
Als effizientes und präzises Schweißverfahren bietet die Laserschweißtechnologie großes Potenzial zur Verbesserung der Verbindungsfestigkeit. Durch Optimierung der Materialauswahl, der Laserparameter, der Verbindungskonstruktion und der Nachbehandlung können die Festigkeit und Zuverlässigkeit von Schweißverbindungen effektiv verbessert werden. Eine präzise Steuerung der Laserleistung, eine ordnungsgemäße Oberflächenreinigung, eine geeignete Konstruktion der Verbindungsgeometrie und eine Wärmebehandlung nach dem Schweißen während des Schweißens können dazu beitragen, thermische Verformungen zu verringern und die Ermüdungsbeständigkeit von Schweißverbindungen zu verbessern. Darüber hinaus wurden durch die Weiterentwicklung der Prozesssteuerungstechnologie, insbesondere durch die Anwendung von maschinellem Lernen und adaptiven Steuerungssystemen, die Stabilität und Qualität des Laserschweißens auf beispiellose Weise gewährleistet. Die Integration all dieser Technologien macht das Laserschweißen in industriellen Anwendungen wettbewerbsfähiger und bietet verschiedenen Branchen effizientere und zuverlässigere Schweißlösungen.
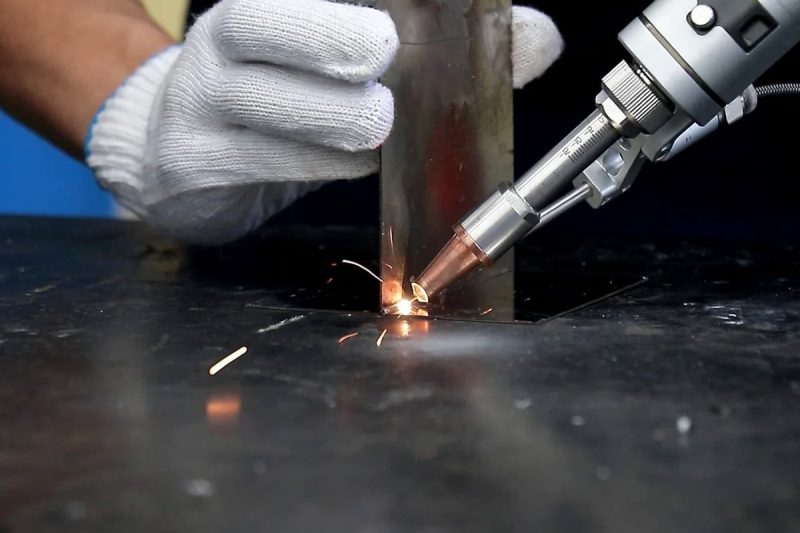
Holen Sie sich Laserlösungen
Als führendes Unternehmen im Bereich des Laserschweißens AccTek-Laser Lasergeneratoren bieten hochfeste und hochstabile Schweißlösungen mit hervorragender Leistung und Präzisionstechnologie. Wir konzentrieren uns darauf, Lösungen für unsere Kunden zuzuschneiden, um sicherzustellen, dass sich jedes Gerät perfekt an Ihre spezifischen Anforderungen anpassen kann. Ob Materialverträglichkeit, Steuerung des Schweißprozesses oder Nachbearbeitung nach dem Schweißen – unsere Lasertechnologie kann Ihnen helfen, das beste Schweißergebnis zu erzielen und die Produktionseffizienz und Produktqualität zu verbessern. Wir sind bestrebt, jedem Kunden umfassenden technischen Support und Lösungen zu bieten, um sicherzustellen, dass Ihr Schweißprozess immer auf dem branchenweit führenden Niveau ist. Wenn Sie Fragen oder Wünsche zur Laserschweißtechnologie haben, können Sie sich gerne an uns wenden. Wir bieten Ihnen die professionellste Beratung und Dienstleistungen, damit Sie auf dem Weg zum Laserschweißen erfolgreich sind!
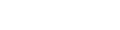
Kontaktinformationen
- [email protected]
- [email protected]
- +86-19963414011
- Nr. 3 Zone A, Industriegebiet Lunzhen, Stadt Yucheng, Provinz Shandong.
Holen Sie sich Laserlösungen