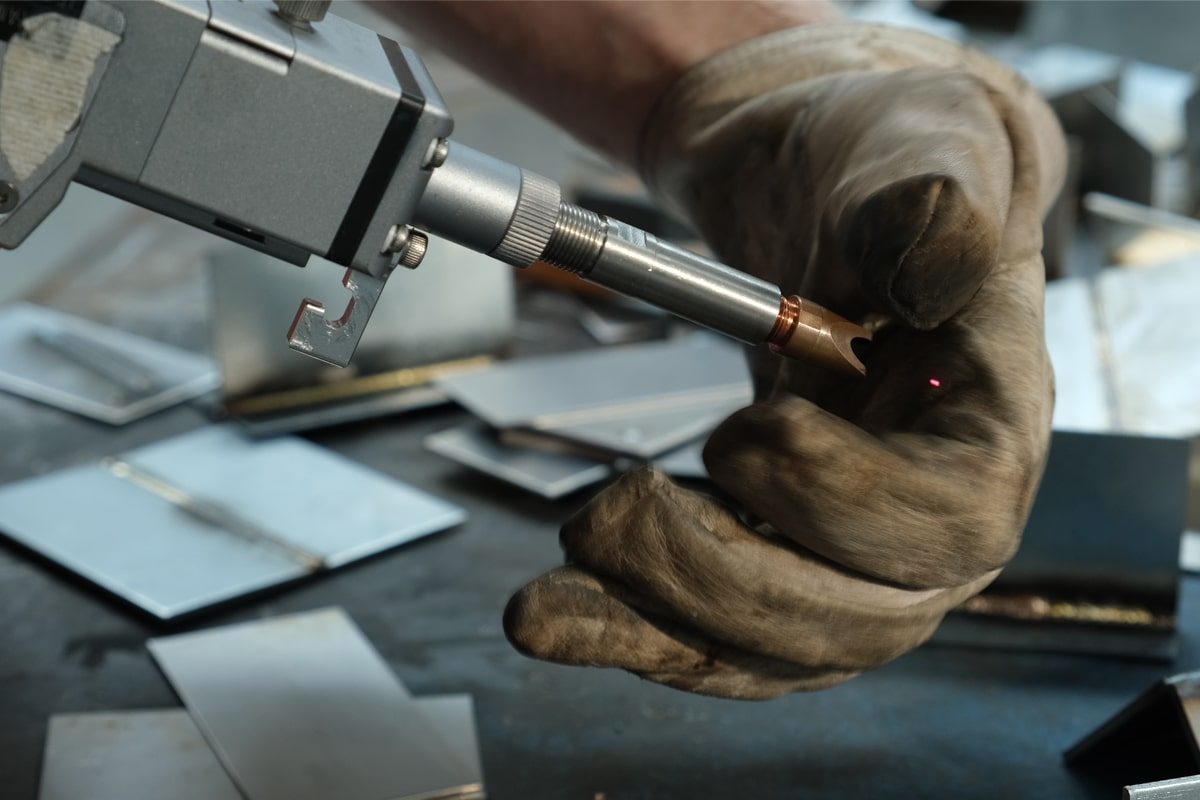
Laserschweißgeräte: Umfassender Leitfaden
Willkommen zu Ihrem umfassenden Leitfaden zu Laserschweißgeräten, Ihrem detaillierten Einblick in eine der fortschrittlichsten Technologien, die die moderne Fertigungslandschaft prägen. In einem Zeitalter, in dem Präzision, Effizienz und Qualität von größter Bedeutung sind, zeichnet sich das Laserschweißen als hocheffiziente Methode aus, die beispiellose Möglichkeiten in Branchen von der Automobil- und Luftfahrtindustrie bis hin zu Elektronik und Medizingeräten bietet.
In diesem umfassenden Leitfaden untersuchen wir die Funktionen, Vorteile, Anwendungen und wichtigsten Überlegungen zur Implementierung. Dieser Artikel befasst sich mit den Grundlagen des Laserschweißens und untersucht die komplexen Wechselwirkungen zwischen Laserstrahlen und Materialien, um präzise und zuverlässige Verbindungen zu erzielen. Vom Verständnis der verschiedenen Arten der Laserschweißtechnologie bis hin zur Erforschung fortschrittlicher Methoden und neuer Trends lassen wir nichts unversucht, um Ihnen das Wissen zu vermitteln, das Sie benötigen, um das volle Potenzial der Laserschweißtechnologie auszuschöpfen. Egal, ob Sie ein erfahrener Branchenprofi sind, der seine Produktionsprozesse optimieren möchte, oder ein Neuling, der die Spitzentechnologien beherrschen möchte, die Innovationen vorantreiben, dieser Leitfaden hat alles für Sie.
Inhaltsverzeichnis
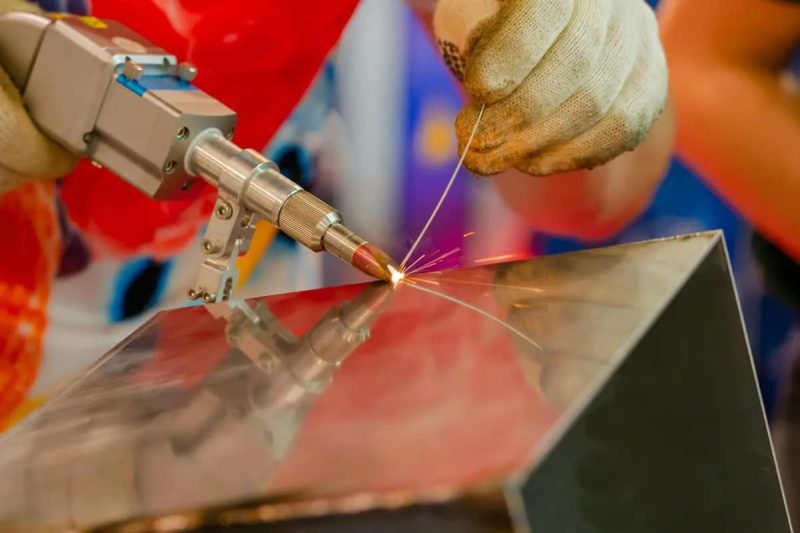
Vorteile des Laserschweißens
Darin untersuchen wir die vielen Vorteile, die das Laserschweißen zu einer wichtigen Technologie für die moderne Fertigung machen. Das Laserschweißen bietet viele Vorteile, die es gegenüber herkömmlichen Schweißverfahren hervorheben und den Produktionsprozess in verschiedenen Branchen revolutionieren.
Präzision und Genauigkeit
Einer der größten Vorteile des Laserschweißens ist sein hohes Maß an Präzision und Genauigkeit. Der fokussierte Strahl des Lasers ermöglicht eine präzise Steuerung, um komplexe Schweißnähte mit minimaler Fehlerquote zu erzeugen. Diese Präzision gewährleistet gleichbleibende Qualität und Maßgenauigkeit, was das Laserschweißen ideal macht, wenn es auf Präzisionsanwendungen ankommt, wie etwa in der Luft- und Raumfahrt- und Elektronikindustrie.
Geschwindigkeit und Effizienz
Laserschweißen ist wesentlich schneller und effizienter als herkömmliche Schweißverfahren. Die konzentrierte Wärmequelle des Laserstrahls fördert das schnelle Schmelzen von Materialien, wodurch die Schweißzeit effektiv verkürzt und die Leistung erhöht wird. Diese Effizienz bedeutet höhere Produktivität und niedrigere Produktionskosten, was das Laserschweißen zur ersten Wahl für die Fertigung großer Stückzahlen macht.
Minimale Wärmeeinflusszone
Im Gegensatz zu herkömmlichen Schweißverfahren, bei denen zum Verbinden von Materialien große Hitze erforderlich ist, entsteht beim Laserschweißen eine minimale Wärmeeinflusszone (WEZ). Die Fokussierung des Laserstrahls sorgt dafür, dass die Wärmezufuhr lokalisiert wird, wodurch Verformungen, Verwerfungen und metallografische Veränderungen im umgebenden Bereich reduziert werden. Diese Minimierung der Wärmeeinflusszone ist beim Schweißen wärmeempfindlicher Materialien oder Komponenten mit engen Maßtoleranzen von Vorteil.
Vielseitigkeit
Laserschweißmaschinen bieten beispiellose Vielseitigkeit und können eine Vielzahl von Materialien schweißen, darunter Metalle, Kunststoffe, Keramik und Verbundwerkstoffe. Ob beim Verbinden unterschiedlicher Materialien oder bei der Anpassung an komplexe Geometrien – das Laserschweißen ist dort hervorragend, wo herkömmliche Methoden versagen. Darüber hinaus kann das Laserschweißen in automatisierte Systeme integriert werden, was seine Vielseitigkeit und Anwendbarkeit in einer Vielzahl von Herstellungsprozessen weiter erhöht.
Kontaktlos
Ein weiterer wesentlicher Vorteil des Laserschweißens ist seine berührungslose Natur. Während des Schweißvorgangs besteht kein physischer Kontakt zwischen dem Schweißwerkzeug und dem Werkstück, wodurch das Risiko einer Verunreinigung, Verformung oder Beschädigung von Präzisionskomponenten verringert wird. Diese Funktion ist in Branchen wertvoll, in denen Sauberkeit und Präzision von entscheidender Bedeutung sind, wie beispielsweise in der Herstellung von Elektronik und medizinischen Geräten.
Zusammenfassend lässt sich sagen, dass die Vorteile des Laserschweißens – darunter Präzision und Genauigkeit, Geschwindigkeit und Effizienz, minimale Wärmeeinflusszone, Vielseitigkeit und berührungsloser Betrieb – es zu einer transformativen Technologie machen, die Innovation und Spitzenleistung in der modernen Fertigung vorantreibt.
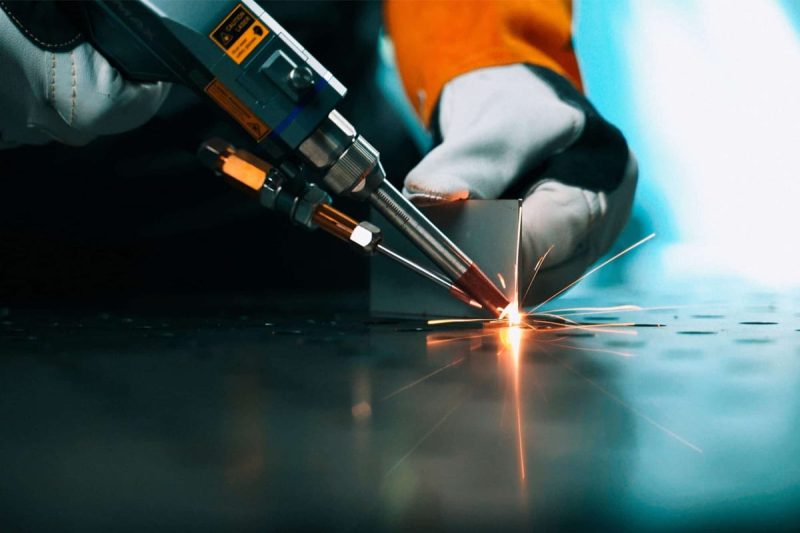
Nachteile des Laserschweißens
Obwohl das Laserschweißen viele Vorteile bietet, ist es wichtig zu wissen, dass es wie jede Technologie seine Grenzen und Nachteile hat. Hier sind einige der Hauptnachteile des Laserschweißens:
Anfängliche Investitionskosten
Einer der Hauptnachteile des Laserschweißens ist die hohe Anfangsinvestition, die für den Kauf und die Einrichtung der erforderlichen Ausrüstung erforderlich ist. Laserschweißmaschinen sind komplexe und hochentwickelte Systeme, die fortschrittliche Optik, Präzisionssteuerungen und Hochleistungslasergeneratoren umfassen. Daher können die Vorlaufkosten für den Kauf und die Installation eines Laserschweißsystems hoch sein, insbesondere für kleine und mittlere Unternehmen.
Qualifikationsanforderungen
Die Bedienung einer Laserschweißmaschine erfordert spezielle Schulungen und Fachkenntnisse. Im Gegensatz zu einigen herkömmlichen Schweißverfahren, die ein höheres Maß an Bedienerkenntnissen erfordern, erfordert das Laserschweißen ein hohes Maß an Präzision und Kontrolle. Bediener müssen über umfassende Kenntnisse der Lasertechnologie, der Materialeigenschaften und der Schweißparameter verfügen, um erfolgreiche Ergebnisse zu erzielen. Diese Fähigkeitsanforderung kann für Unternehmen, die das Laserschweißen einführen möchten, ohne Zugang zu geschultem Personal oder Schulungsressourcen zu haben, eine Herausforderung darstellen.
Begrenzter Dickenbereich
Während sich Laserschweißen gut zum Verbinden dünner bis mitteldicker Materialien eignet, ist es möglicherweise nicht zum Schweißen sehr dicker Abschnitte geeignet. Im Vergleich zu einigen anderen Schweißverfahren ist die erreichbare Eindringtiefe beim Laserschweißen begrenzt, was seine Eignung für bestimmte Anwendungen, wie z. B. Schwerlastfertigung oder Strukturschweißen, einschränken kann. Darüber hinaus kann das Erreichen einer gleichbleibenden Schweißqualität über verschiedene Materialstärken hinweg eine Herausforderung sein und spezielle Techniken oder Geräte erfordern.
Reflektierendes Material
Laserschweißen ist bei stark reflektierenden Materialien wie Kupfer, Aluminium und bestimmten Legierungen weniger effektiv. Diese Materialien neigen dazu, einen Großteil der Laserenergie zu reflektieren, was den Schweißprozess weniger effizient macht und zu Problemen wie schlechter Schweißdurchdringung oder Oberflächenfehlern führen kann. Während Techniken wie Strahlformung oder die Verwendung bestimmter Wellenlängen dazu beitragen können, diese Einschränkung bis zu einem gewissen Grad zu verringern, bleibt das Schweißen reflektierender Materialien mit Lasern im Vergleich zu anderen Schweißmethoden eine Herausforderung.
Sicherheitsfrage
Beim Laserschweißen werden hochintensive Laserstrahlen verwendet, die bei unsachgemäßer Handhabung ein Sicherheitsrisiko darstellen können. Direkte Einwirkung von Laserstrahlen kann schwere Verbrennungen oder Augenschäden verursachen, daher sind strenge Sicherheitsprotokolle und Schutzmaßnahmen erforderlich. Darüber hinaus können beim Laserschweißen schädliche Dämpfe, Schwaden oder Partikel entstehen, sodass eine ausreichende Belüftung und persönliche Schutzausrüstung erforderlich sind, um die Sicherheit der Arbeiter zu gewährleisten.
Zusammenfassend lässt sich sagen, dass das Laserschweißen zwar zahlreiche Vorteile in Bezug auf Präzision, Effizienz und Vielseitigkeit bietet, seine Grenzen und die damit verbundenen Herausforderungen jedoch berücksichtigt werden müssen. Durch die Berücksichtigung von Faktoren wie anfänglichen Investitionskosten, Qualifikationsanforderungen, Materialverträglichkeit und Sicherheitsaspekten können die Vorteile des Laserschweißens maximiert und potenzielle Nachteile minimiert werden.
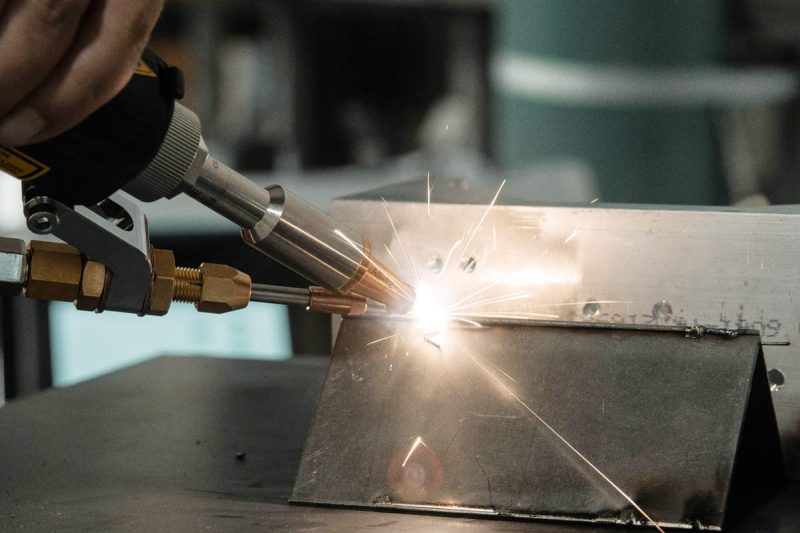
Was kostet das Laserschweißen?
Wenn Sie die Implementierung der Laserschweißtechnologie in Erwägung ziehen, ist es wichtig, die damit verbundenen Kosten zu verstehen. Beim Kauf einer Laserschweißmaschine ist es wichtig, die anfängliche Investition und die laufenden Kosten abzuwägen, um eine fundierte Entscheidung treffen zu können. Im Folgenden finden Sie einen Überblick über die mit dem Laserschweißen verbundenen Kostenaspekte:
Anfängliche Ausrüstungsinvestition
Der größte Kostenfaktor beim Laserschweißen ist die Anfangsinvestition in die Ausrüstung. Die Preise für Laserschweißgeräte variieren stark und hängen von Faktoren wie Leistungsabgabe, technischen Merkmalen und dem Ruf des Herstellers ab. Die Einstiegsgeräte von AccTek Laser beginnen bei $4.000, während High-End-Geräte für den industriellen Einsatz $30.000 oder mehr kosten können. Darüber hinaus können Zusatzgeräte wie Laserschutzschilde, Kühleinheiten und Rauchabzugssysteme die Gesamtanfangsinvestition erhöhen.
Wartung und Service
Wie jede Präzisionsmaschine erfordern Laserschweißsysteme regelmäßige Wartung und Instandhaltung, um optimale Leistung und Langlebigkeit zu gewährleisten. Zu den Wartungsaufgaben können das Reinigen der Optik, das Kalibrieren der Laserparameter und das Ersetzen von Verbrauchsteilen wie Schutzfenstern, Düsen und Gasfiltern gehören. Die routinemäßigen Wartungskosten liegen normalerweise zwischen einigen hundert und einigen tausend Dollar pro Jahr. Die Wartungskosten können je nach Komplexität und Nutzungsgrad des Systems variieren, für den fortlaufenden Betrieb sollte jedoch ein Budget vorgesehen werden.
Verbrauchsmaterialien und Zubehör
Beim Laserschweißen fallen außerdem Kosten für Verbrauchsmaterialien und Zubehör an. Dazu können Schweißgase wie Argon oder Helium, Schutzgase zur Vermeidung von Oxidation und Füllmaterialien für einige Schweißarten gehören. Darüber hinaus müssen Verbrauchsmaterialien wie Schutzkappen für Linsen, Düsenspitzen und Kühlmittel möglicherweise regelmäßig nachgefüllt werden. Die Kosten für Verbrauchsmaterialien können je nach Marke und Modell der Maschine, Nutzungsintensität und den erforderlichen spezifischen Verbrauchsmaterialien stark variieren. Die jährlichen Kosten für Verbrauchsmaterialien können zwischen einigen Hundert und einigen Tausend Dollar liegen.
Energieverbrauch
Laserschweißgeräte benötigen für ihren Betrieb große Mengen Strom, insbesondere die Hochleistungssysteme, die in industriellen Anwendungen eingesetzt werden. Die Energiekosten können je nach Faktoren wie Laserleistung, Arbeitszyklus und lokalen Strompreisen variieren. Das Verständnis und die Verwaltung des Energieverbrauchs sind entscheidend für die Kontrolle der Betriebskosten und die Optimierung der Kosteneffizienz Ihres Laserschweißprozesses. Strompreise werden normalerweise in Cent pro Kilowattstunde (kWh) gemessen und können zwischen einigen Cent und einigen Cent pro kWh liegen. Höhere Stromrechnungen führen zu höheren Energiekosten für den Betrieb eines Laserschweißgeräts.
Schulung und Kompetenzentwicklung
Investitionen in Schulungen und Kompetenzentwicklung für Bediener und Techniker sind ein weiterer Kostenfaktor beim Laserschweißen. Eine angemessene Schulung stellt sicher, dass das Personal über das Wissen und die Erfahrung verfügt, um Geräte sicher und effizient zu bedienen, wodurch das Risiko von Fehlern, Unfällen und Ausfallzeiten minimiert wird. Die Kosten für Schulungen und Kompetenzentwicklung für Laserschweißgeräte betragen Hunderte bis Tausende von Dollar pro Person, abhängig von Faktoren wie der Art der Schulung, dem Schulungsanbieter und dem erforderlichen Fachwissen.
Zusammenfassend lässt sich sagen, dass das Laserschweißen zwar zahlreiche Vorteile in Bezug auf Genauigkeit, Effizienz und Vielseitigkeit bietet, die damit verbundenen Kosten jedoch berücksichtigt werden müssen, um eine fundierte Entscheidung treffen zu können. Durch die Bewertung von Faktoren wie Geräteinvestition, Wartung und Service, Verbrauchsmaterialien, Energieverbrauch und Schulung können Unternehmen die finanziellen Auswirkungen der Einführung der Laserschweißtechnologie effektiv einschätzen und sicherstellen, dass sie kostengünstig in den Herstellungsprozess integriert wird.
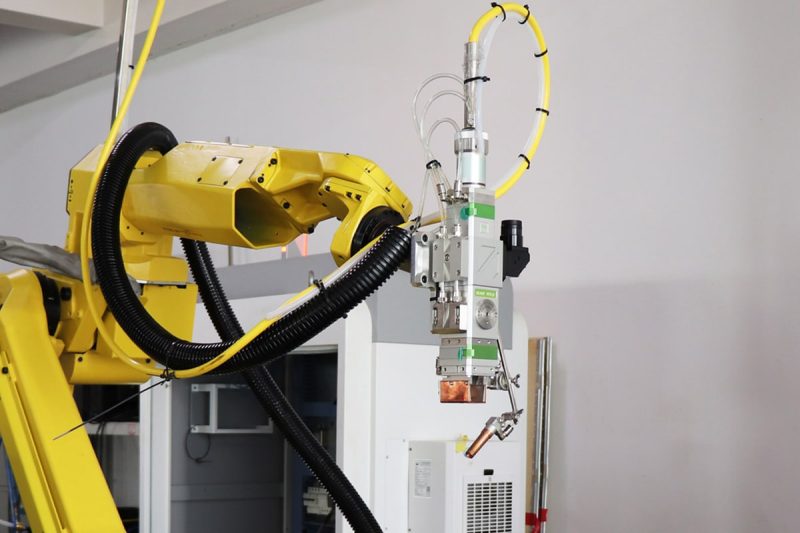
Gasanforderungen für das Laserschweißen
Beim Laserschweißen ist eine präzise Kontrolle der Gasumgebung erforderlich, um optimale Schweißqualität, Effizienz und Sicherheit zu erreichen. Die Auswahl und Handhabung der Schweißgase spielen eine entscheidende Rolle für den Erfolg des Laserschweißprozesses. Im Folgenden finden Sie einen Überblick über die Gasanforderungen beim Laserschweißen:
Schutzgas
Schutzgase werden verwendet, um das Schweißbad vor atmosphärischen Verunreinigungen wie Sauerstoff und Stickstoff zu schützen, die Defekte wie Porosität und Oxidation verursachen können. Zu den üblichen Schutzgasen beim Laserschweißen gehören Argon, Helium und Mischungen dieser Gase. Argon wird im Allgemeinen aufgrund seiner Erschwinglichkeit und Wirksamkeit beim Schutz der meisten Metalle bevorzugt, während Helium eine bessere Wärmeleitfähigkeit aufweist, die Durchdringung verbessert und bei einigen Anwendungen wärmebeeinflusste Zonen reduziert.
Hilfsgas
Hilfsgase erfüllen beim Laserschweißen verschiedene Aufgaben, z. B. verbessern sie die Schweißdurchdringung, kontrollieren Spritzer und verbessern die allgemeine Prozessstabilität. Sauerstoff und Stickstoff werden häufig als Hilfsgase verwendet, wobei Sauerstoff besonders effektiv ist, um die Schneid- und Schweißgeschwindigkeit bei bestimmten Materialien zu erhöhen, während Stickstoff aufgrund seiner Fähigkeit, Oxidation zu reduzieren und die Schweißnahtgeometrie zu verfeinern, bevorzugt wird.
Spülgas
Bei Anwendungen, bei denen auf der Rückseite einer Verbindung oder in einem geschlossenen Raum geschweißt wird, wird Spülgas verwendet, um eine inerte Atmosphäre zu erzeugen, die Oxidation verhindert und die Schweißqualität sicherstellt. Argon wird aufgrund seiner Inertheit und Wirtschaftlichkeit häufig als Spülgas verwendet. Die Durchflussrate und Verteilung des Spülgases müssen sorgfältig kontrolliert werden, um die erforderliche Atmosphäre aufrechtzuerhalten und Verunreinigungen zu vermeiden.
Kühlgas
Hochleistungs-Laserschweißsysteme erzeugen große Mengen Wärme und erfordern eine effektive Kühlung, um die Systemleistung aufrechtzuerhalten und Schäden an kritischen Komponenten zu verhindern. Kühlgas, normalerweise in Form eines Kühlluftstroms oder einer Wasserzirkulation, wird verwendet, um Wärme von Laseroptiken, Fokussierlinsen und anderen wärmeempfindlichen Komponenten abzuleiten.
Gasqualität und -reinheit
Die Qualität und Reinheit des Schweißgases sind Schlüsselfaktoren für eine gleichbleibende Schweißqualität und Prozessstabilität. Verunreinigungen wie Feuchtigkeit, Öl und Partikel können die Qualität des Laserstrahls beeinträchtigen, Defekte verursachen und die Produktivität verringern. Daher ist die Verwendung hochwertiger Gase von namhaften Lieferanten und die Implementierung geeigneter Gasfilter- und -reinigungssysteme für eine optimale Laserschweißleistung von Vorteil.
Zusammenfassend lässt sich sagen, dass Hersteller durch das Verständnis der spezifischen Gasanforderungen für Schutz-, Hilfs-, Spül- und Kühlgase ihre Laserschweißprozesse optimieren können, um den Anforderungen ihrer Anwendung gerecht zu werden und gleichzeitig qualitativ hochwertige, effiziente und zuverlässige Schweißnähte sicherzustellen.
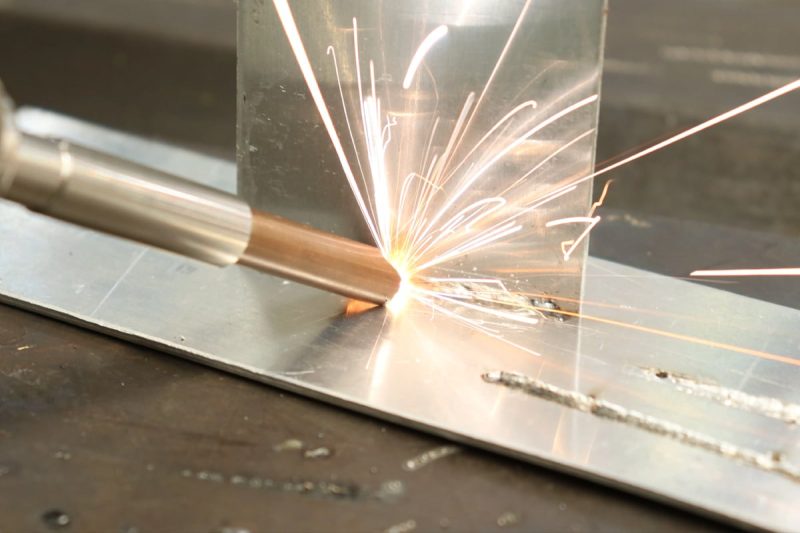
Welche Metalle sind mit dem Laserschweißen kompatibel?
Das Verständnis der Kompatibilität verschiedener Metalle mit dem Laserschweißen ermöglicht optimale Schweißqualität, Effizienz und Leistung. Nachfolgend finden Sie eine Übersicht über Metalle, die häufig mit Laserschweißverfahren geschweißt werden:
Kohlenstoffstahl
Kohlenstoffstahl ist aufgrund seiner Erschwinglichkeit, Vielseitigkeit und Festigkeit eines der am häufigsten verwendeten Metalle in der Fertigung. Das Laserschweißen ist mit Kohlenstoffstahl sehr gut kompatibel, ermöglicht eine präzise Kontrolle der Schweißparameter und erzeugt starke und langlebige Verbindungen. Anwendungsgebiete für das Laserschweißen von Kohlenstoffstahlkomponenten erstrecken sich über eine Vielzahl von Branchen, darunter Automobilbau, Bauwesen und Maschinenbau.
Edelstahl
Edelstahl wird wegen seiner Korrosionsbeständigkeit, Ästhetik und mechanischen Eigenschaften geschätzt und ist daher eine beliebte Wahl für Anwendungen, bei denen Haltbarkeit und Hygiene erforderlich sind. Laserschweißen eignet sich besonders gut zum Verbinden von Edelstahl, da es saubere, präzise Schweißnähte mit minimaler Verformung und Wärmeeinflusszonen erzeugt. Von Geräten zur Lebensmittelverarbeitung bis hin zu medizinischen Geräten sind lasergeschweißte Edelstahlkomponenten in der modernen Fertigung allgegenwärtig.
Aluminium
Aluminium und seine Legierungen werden wegen ihres geringen Gewichts, ihres hohen Festigkeits-Gewichts-Verhältnisses und ihrer ausgezeichneten Wärmeleitfähigkeit geschätzt. Laserschweißen ist eine effiziente Methode zum Verbinden von Aluminiumkomponenten und ermöglicht starke, schöne Schweißnähte mit minimaler Verformung. Die Anwendungsgebiete für das Laserschweißen von Aluminium reichen von der Luft- und Raumfahrt über Automobilteile bis hin zu Unterhaltungselektronik und Gebäudestrukturen.
Titan
Titan wird wegen seiner außergewöhnlichen Festigkeit, Korrosionsbeständigkeit und Biokompatibilität geschätzt und ist daher das Material der Wahl für Anwendungen in der Luft- und Raumfahrt, Medizin und Schifffahrt. Laserschweißen ist ideal zum Verbinden von Titanlegierungen, da es eine präzise Kontrolle der Wärmezufuhr ermöglicht und das Kontaminationsrisiko minimiert. Lasergeschweißte Titankomponenten sind für kritische Anwendungen wie Flugzeugstrukturen, medizinische Implantate und Schiffsausrüstung unverzichtbar.
Kupfer und Messing
Kupfer- und Messinglegierungen werden wegen ihrer elektrischen, thermischen und dekorativen Eigenschaften geschätzt und sind daher wichtige Materialien in der Elektronik, im Sanitärbereich und in der dekorativen Kunst. Während das Laserschweißen von Kupfer und Messing aufgrund ihrer hohen Reflektivität und Wärmeleitfähigkeit eine Herausforderung darstellt, können diese Materialien mit speziellen Techniken wie Impulsformung und Wellenlängenoptimierung erfolgreich geschweißt werden. Das Laserschweißen von Kupfer- und Messingkomponenten kann in elektrischen Steckverbindern, Wärmetauschern und architektonischer Dekoration eingesetzt werden.
Nickel-Legierung
Nickellegierungen weisen eine ausgezeichnete Korrosionsbeständigkeit, Hochtemperaturfestigkeit und Oxidationsbeständigkeit auf und eignen sich für anspruchsvolle Anwendungen in der Luft- und Raumfahrt, der chemischen Verarbeitung und der Stromerzeugung. Das Laserschweißen ermöglicht eine präzise Steuerung des Schweißprozesses und die Herstellung hochwertiger Schweißnähte in Nickellegierungen mit minimaler Verzerrung und metallurgischen Veränderungen. Das Laserschweißen von Komponenten aus Nickellegierungen ist für kritische Anwendungen wie Gasturbinen, chemische Reaktoren und Kernkraftwerke von entscheidender Bedeutung.
Zusammengefasst bietet die Laserschweißtechnologie eine vielseitige und effektive Möglichkeit, eine Vielzahl von Metallen zu verbinden, von Kohlenstoff- und Edelstahl bis hin zu Aluminium-, Titan-, Kupfer-, Messing- und Nickellegierungen. Durch das Verständnis der einzigartigen Eigenschaften und Schweißcharakteristika jedes Metalls können Hersteller Laserschweißverfahren nutzen, um hochwertige, zuverlässige Schweißnähte basierend auf den spezifischen Anforderungen ihrer Anwendung herzustellen.
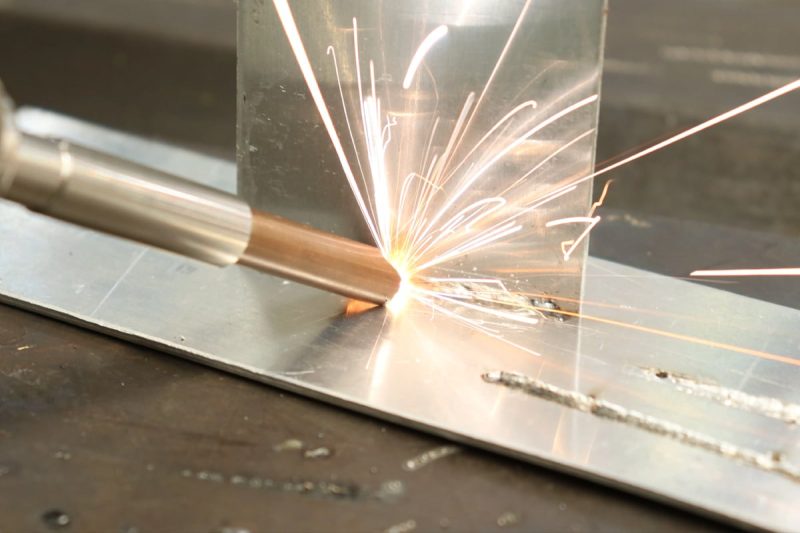
Anwendungen des Laserschweißens in verschiedenen Branchen
Die Laserschweißtechnologie wird aufgrund ihrer Präzision, Effizienz und Vielseitigkeit in verschiedenen Branchen häufig eingesetzt. Im Folgenden finden Sie eine detaillierte Einführung in die Anwendung des Laserschweißens in Schlüsselbereichen:
Automobilindustrie
In der Automobilindustrie spielt das Laserschweißen eine entscheidende Rolle bei der Fahrzeugproduktion, da es die Herstellung komplexer Teile mit hoher Präzision und Effizienz ermöglicht. Laserschweißen wird zum Verbinden von Karosserieteilen, Fahrwerkskomponenten, Auspuffsystemen, Kraftstofftanks und Motorkomponenten verwendet. Laserschweißen erzeugt starke, langlebige Schweißnähte mit minimalen Wärmeeinflusszonen und ist daher ideal für Automobilanwendungen, bei denen strukturelle Integrität, Gewichtsreduzierung und Ästhetik wichtig sind.
Elektronische Fertigung
Laserschweißen wird in der Elektronikfertigung häufig eingesetzt, um Teile mit Präzisionsmerkmalen und engen Toleranzen zusammenzusetzen. Es wird verwendet, um elektronische Gehäuse, Steckverbinder, Sensoren und mikroelektronische Geräte zu verbinden. Laserschweißen ermöglicht eine präzise Steuerung der Wärmezufuhr, was zu sauberen, schönen Schweißnähten führt, ohne empfindliche elektronische Komponenten zu beschädigen. Da es berührungslos ist, wird auch das Kontaminationsrisiko minimiert, was es ideal für Reinraumumgebungen macht.
Medizinische Ausrüstung
Die Medizingeräteindustrie setzt bei der Herstellung von Implantaten, chirurgischen Instrumenten, Diagnosegeräten und Gehäusen für Medizingeräte auf Laserschweißen. Laserschweißen kann kleine, komplexe Schweißnähte mit minimaler thermischer Verformung erzeugen, was es ideal für die Montage mikroskopischer Komponenten macht, die in Medizingeräten verwendet werden. Darüber hinaus bietet Laserschweißen den Vorteil biokompatibler Schweißverfahren bei Materialien wie Titan und Edelstahl, wodurch die Verträglichkeit mit dem menschlichen Körper gewährleistet wird.
Luft- und Raumfahrt und Verteidigung
In der Luft- und Raumfahrt sowie im Verteidigungssektor, wo Zuverlässigkeit, Leistung und Sicherheit von entscheidender Bedeutung sind, wird das Laserschweißen häufig zum Verbinden kritischer Komponenten in Flugzeugen, Raumfahrzeugen, Raketen und Verteidigungssystemen eingesetzt. Laserschweißen wird zum Schweißen von Flugzeugstrukturen, Motorkomponenten, Treibstofftanks, Fahrwerken und Waffensystemen verwendet. Die Fähigkeit, hochfeste Schweißnähte mit minimalem Gewichtsverlust zu erzeugen, macht es für Luft- und Raumfahrtanwendungen unverzichtbar, bei denen Gewichtsreduzierung und Treibstoffeffizienz oberste Priorität haben.
Neben diesen Branchen wird das Laserschweißen auch in Bereichen wie Schiffbau, Energie, Schmuckherstellung und Konsumgüterproduktion eingesetzt. Seine Vielseitigkeit, Präzision und Fähigkeit, eine Vielzahl von Materialien zu schweißen, machen es zu einer vielseitigen und unverzichtbaren Technologie in der modernen Fertigung. Da Fortschritte in der Lasertechnologie weiterhin zu Verbesserungen bei Geschwindigkeit, Effizienz und Leistungsfähigkeit führen, ist zu erwarten, dass die Anwendungen des Laserschweißens weiter zunehmen und verschiedenen Branchen neue Möglichkeiten eröffnen.
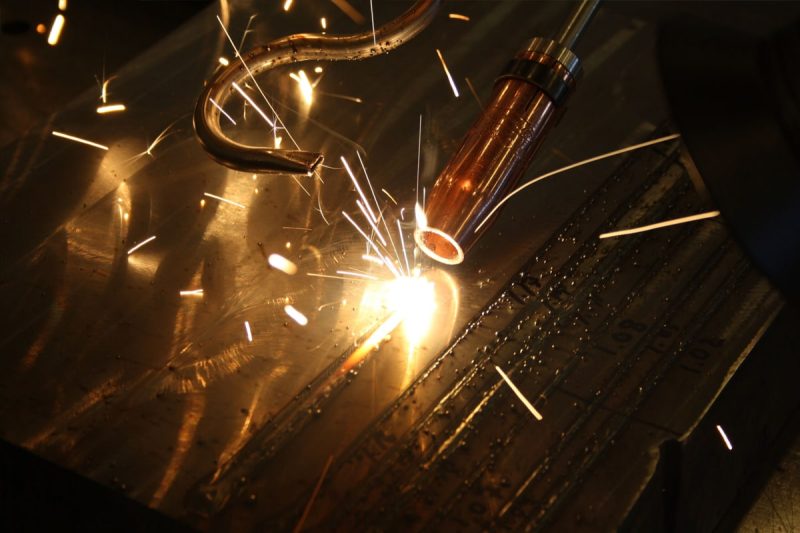
Häufige Gefahren bei der Verwendung von Laserschweißgeräten
Obwohl Laserschweißgeräte viele Vorteile bieten, müssen die mit ihrem Betrieb verbundenen potenziellen Gefahren erkannt und gemindert werden. Im Folgenden finden Sie eine Übersicht über die häufigsten Gefahren bei der Verwendung von Laserschweißgeräten:
Optische Strahlung
Laserschweißgeräte geben hochintensive optische Strahlung in Form von Laserstrahlen ab, die bei unzureichender Kontrolle oder Abschirmung schwere Augenschäden und Hautverbrennungen verursachen können. Direkte oder indirekte Einwirkung von Laserstrahlen kann zu dauerhaften Schäden an Augen und Haut führen. Daher ist es wichtig, geeignete Laserschutzmaßnahmen zu ergreifen, darunter die Verwendung von Schutzbrillen, Gehäusen und Verriegelungen, um das Risiko optischer Strahlungsgefahren zu minimieren.
Hitze und Rauch
Beim Laserschweißen entsteht große Hitze, die Materialien zum Schmelzen und Verdampfen bringt, wodurch gefährliche Dämpfe, Schwaden und Partikel entstehen. Das Einatmen von Schweißrauch und die Einwirkung hoher Temperaturen können für die Bediener gesundheitliche Risiken bergen, darunter Atemwegsreizungen, Lungenschäden und hitzebedingte Erkrankungen. Durch geeignete Belüftung, Absaugsysteme und persönliche Schutzausrüstung (PSA) wie Atemschutzmasken und hitzebeständige Kleidung können Hitze- und Rauchgefahren in Laserschweißumgebungen wirksam gemindert werden.
Gefahr von Stromschlägen
Laserschweißgeräte benötigen zum Betrieb Strom. Wenn sie nicht ordnungsgemäß installiert, geerdet und gewartet werden, besteht die Gefahr von Stromschlägen, Stromschlägen und Bränden. Elektrische Gefahren können durch falsche Verkabelung, beschädigte elektrische Komponenten oder unsachgemäße Handhabung elektrischer Verbindungen entstehen. Regelmäßige Inspektion, Wartung und Einhaltung elektrischer Sicherheitsstandards können als vorbeugende Maßnahmen dienen, um Stromunfälle zu verhindern und den sicheren Betrieb von Laserschweißgeräten zu gewährleisten.
Brandgefahr
Die beim Laserschweißen erzeugte starke Hitze kann entflammbare Materialien wie Staub, Gas, Schmiermittel und brennbare Werkstückmaterialien entzünden und Brände und Explosionen verursachen. Darüber hinaus können beim Schweißen entstehende Funken und heiße Partikel eine Zündgefahr für die Umgebung darstellen. Durch die Umsetzung von Brandschutzmaßnahmen wie dem Entfernen brennbarer Materialien, dem Sauberhalten von Arbeitsbereichen und der Installation von Brandmelde- und -unterdrückungssystemen können Brandgefahren bei Laserschweißvorgängen minimiert werden.
Mechanische Gefahren
Laserschweißgeräte enthalten bewegliche Teile wie Roboterarme, Werkstückmanipulatoren und Werkzeugvorrichtungen, die mechanische Gefahren verursachen können, wenn sie nicht ordnungsgemäß geschützt oder kontrolliert werden. Ein versehentlicher Kontakt mit beweglichen Teilen oder Quetschstellen kann zu Quetschverletzungen, Schnittwunden oder Amputationen führen. Die Implementierung von Maschinenschutzvorrichtungen, Sicherheitsverriegelungen und Schulungsprogrammen für Bediener kann dazu beitragen, mechanische Gefahren zu verringern und den sicheren Betrieb von Laserschweißgeräten sicherzustellen.
Zusammenfassend lässt sich sagen, dass Hersteller durch die Umsetzung geeigneter Sicherheitsmaßnahmen, Schulungsprogramme und Risikobewertungen die mit Laserschweißvorgängen verbundenen Risiken minimieren und eine sichere Arbeitsumgebung für alle Beteiligten schaffen können.
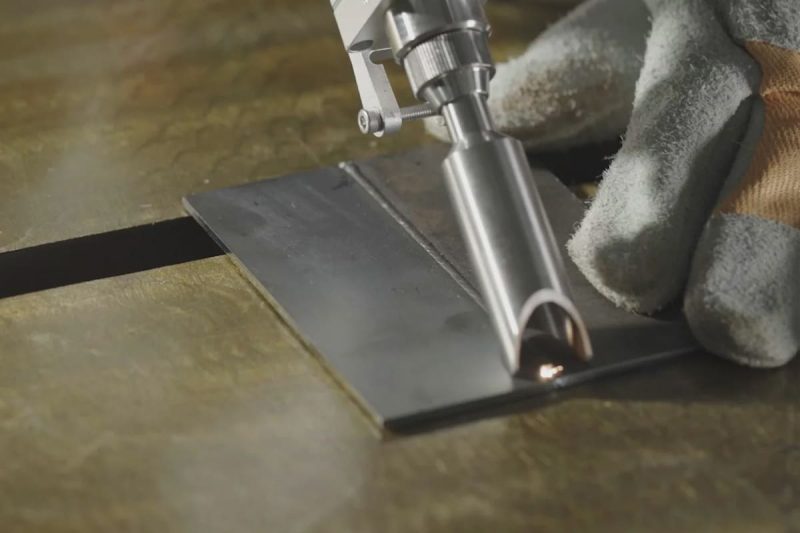
Die Verwendung von Schweißdraht beim Laserschweißen
Laserschweißen ist ein vielseitiges und präzises Verbindungsverfahren mit vielen Vorteilen, darunter hohe Geschwindigkeit, minimale Verformung und hervorragende Schweißqualität. Während das Laserschweißen normalerweise ohne Füllmaterial durchgeführt wird, kann die Verwendung von Schweißdraht den Prozess verbessern und seine Eignung für bestimmte Anwendungen erweitern. Im Folgenden finden Sie einen Überblick über die Verwendung von Schweißdraht beim Laserschweißen:
Füllstoff
Schweißdraht, auch Fülldraht oder Füllstab genannt, ist ein Verbrauchsmaterial, das während des Schweißvorgangs verwendet wird, um der Schweißnaht zusätzliches Material hinzuzufügen. Beim Laserschweißen wird Fülldraht normalerweise manuell oder über ein automatisches Drahtzufuhrsystem in den Schweißbereich eingeführt. Das Hinzufügen von Füllmaterial kann dazu beitragen, Lücken zwischen Werkstückkanten zu füllen, die Verbindungsfestigkeit zu verbessern und die Schweißraupengeometrie zu steuern.
Legierungskompatibilität
Der Schweißdraht wird so ausgewählt, dass er die erforderlichen Schweißeigenschaften erreicht und die Kompatibilität mit dem Schweißgrundmetall gewährleistet. Schweißdrähte sind in verschiedenen Zusammensetzungen und Legierungen erhältlich, um den Eigenschaften von Grundmetallen wie Kohlenstoffstahl, Edelstahl, Aluminium, Titan und Nickellegierungen zu entsprechen. Die Abstimmung der Zusammensetzung und Eigenschaften des Schweißdrahtes auf diejenigen des Grundmetalls ist eine wichtige Voraussetzung für die Herstellung hochwertiger Schweißnähte mit gleichmäßigen mechanischen Eigenschaften.
Schweißgeometrie steuern
Laserschweißanwendungen erfordern eine präzise Kontrolle der Schweißgeometrie. Der Einsatz von Schweißdrähten hilft dabei, das gewünschte Schweißprofil und die gewünschte Größe zu erzielen. Durch Anpassen der Vorschubgeschwindigkeit und Positionierung des Schweißdrahts im Verhältnis zum Laserstrahl können Bediener die Größe, Form und Eindringtiefe der Schweißnaht steuern. Diese Kontrollmöglichkeit ist besonders bei Anwendungen von Vorteil, bei denen eine gleichbleibende Schweißnahtgröße und Ästhetik erforderlich sind, wie z. B. bei dekorativen Schweißnähten an Karosserieteilen oder Zierelementen von Kraftfahrzeugen.
Spaltüberbrückung und Fugentoleranzen
Bei Abweichungen in Passung, Fugenausrichtung oder Spalttoleranzen zwischen Werkstückkanten kann Schweißdraht verwendet werden, um Lücken zu überbrücken und Maßunterschiede auszugleichen. Durch Hinzufügen von Füllmaterial wird eine vollständige Durchdringung und Verschmelzung der Verbindung sichergestellt, selbst in Situationen, in denen eine perfekte Passung nicht möglich ist. Diese Funktion ist vorteilhaft beim Schweißen unterschiedlicher Materialien, beim Verbinden von Teilen mit komplexen Geometrien oder beim Reparieren abgenutzter oder beschädigter Teile.
Prozessoptimierung
Der Einsatz von Schweißdraht beim Laserschweißen kann auch zur Prozessoptimierung und Effizienzsteigerung beitragen. Durch Zugabe eines Füllmaterials zur Steuerung der Ablagerungsrate und Wärmezufuhr können Bediener die Schweißparameter für optimale Schweißqualität, Produktivität und Materialnutzung feinabstimmen. Darüber hinaus erhöht die Verwendung von Schweißdraht die allgemeine Prozesszuverlässigkeit, da die Wahrscheinlichkeit von Schweißfehlern wie mangelnder Verschmelzung, mangelnder Durchdringung oder Einbrandkerben verringert wird.
Zusammenfassend lässt sich sagen, dass Laserschweißen zwar normalerweise ohne Füllmaterial durchgeführt wird, die Verwendung von Schweißdraht jedoch viele Vorteile hinsichtlich Schweißkontrolle, Verbindungsqualität und Prozessoptimierung bieten kann. Durch die Auswahl des geeigneten Schweißdrahts und die Anpassung der Drahtzufuhrparameter können Hersteller die Möglichkeiten der Laserschweißtechnologie verbessern und ihre Anwendbarkeit auf eine breite Palette von Branchen und Anwendungen ausweiten.
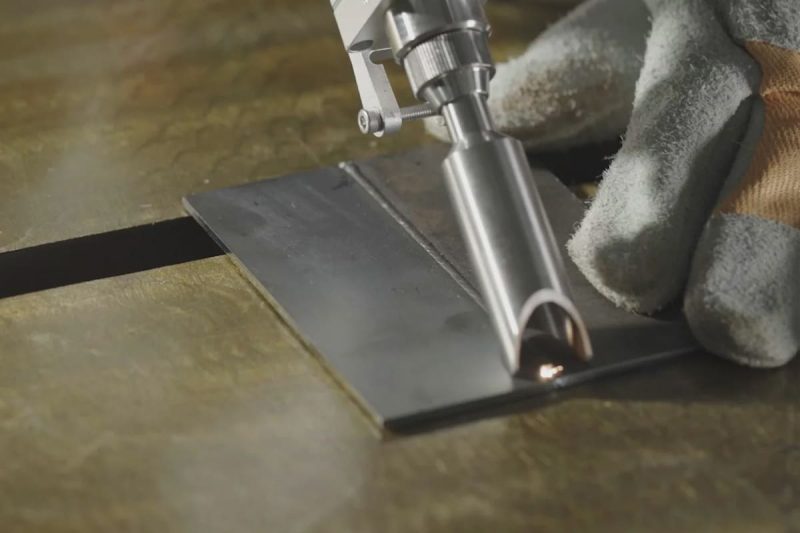
Pflege und Wartung des Laserschweißens
Die Wartung Ihrer Laserschweißmaschine ist entscheidend für optimale Leistung, Zuverlässigkeit und Langlebigkeit. Regelmäßige Wartungs- und Serviceverfahren helfen, Ausfälle zu vermeiden, Ausfallzeiten zu minimieren und die Lebensdauer wichtiger Komponenten zu verlängern. Im Folgenden finden Sie eine Übersicht über die wichtigsten Wartungsaufgaben für Laserschweißmaschinen:
Regelmäßige Reinigung
Regelmäßiges Reinigen verhindert die Verschmutzung der Laserschweißmaschine, erhält die optische Klarheit und sorgt für gleichbleibende Leistung. Zu den Reinigungsverfahren kann die Verwendung eines fusselfreien Tuchs und einer geeigneten Reinigungslösung gehören, um Staub, Schmutz und Ablagerungen von optischen Komponenten wie Linsen, Spiegeln und Schutzfenstern zu entfernen. Darüber hinaus trägt das Reinigen der Werkstückhalterung, des Maschinengehäuses und des umgebenden Arbeitsbereichs dazu bei, eine saubere und sichere Betriebsumgebung für Laserschweißvorgänge aufrechtzuerhalten.
Ausrichtungsprüfung
Die richtige Ausrichtung der Optik ist entscheidend für eine präzise Strahlführung und gleichbleibende Schweißqualität beim Laserschweißen. Eine regelmäßige Überprüfung der optischen Ausrichtung stellt sicher, dass der Laserstrahl richtig fokussiert und auf das Werkstück gerichtet ist, wodurch Strahldivergenz und Energieverlust minimiert werden. Bei Ausrichtungsprüfungen kann die Verwendung eines Ausrichtungswerkzeugs, eines Laserausrichtungssystems oder eines Laserstrahlprofilers erforderlich sein, um die Ausrichtung der Laseroptik zu überprüfen und alle erforderlichen Anpassungen zur Leistungsoptimierung vorzunehmen.
Wartung des Kühlsystems
Laserschweißgeräte sind auf Kühlsysteme angewiesen, um die während des Betriebs erzeugte Wärme abzuleiten und die Betriebstemperatur wichtiger Komponenten wie Laserquellen, Optiken und Stromversorgungen stabil zu halten. Eine regelmäßige Wartung des Kühlsystems, einschließlich der Überprüfung des Kühlmittelstands, der Überprüfung von Schläuchen und Armaturen auf Lecks oder Schäden sowie der Reinigung von Kühlmittelfiltern und Wärmetauschern, kann dazu beitragen, eine effektive Wärmeableitung sicherzustellen und Überhitzungsproblemen vorzubeugen.
Kalibrierung
Die Kalibrierung von Laserschweißgeräten hilft dabei, die Genauigkeit von Schweißparametern wie Laserleistung, Impulsdauer, Strahlqualität und Fokusgröße aufrechtzuerhalten. Regelmäßige Kalibrierungsprüfungen mit kalibrierten Instrumenten, Referenzstandards oder integrierten Kalibrierungsverfahren können dazu beitragen, die Genauigkeit der Maschineneinstellungen zu überprüfen und die Einhaltung der angegebenen Toleranzen sicherzustellen. Die Kalibrierungsintervalle können je nach Nutzungsgrad, Umgebungsbedingungen und Herstellerempfehlungen variieren.
Routine Inspektion
Regelmäßige Inspektionen Ihrer Laserschweißmaschine können dabei helfen, potenzielle Probleme, Verschleiß oder Schäden zu erkennen, bevor sie zu teuren Reparaturen oder Ausfallzeiten führen. Inspektionen können eine Sichtprüfung von Maschinenkomponenten wie Kabeln, Anschlüssen, Motoren und Lagern auf Anzeichen von Verschleiß, Korrosion oder Ermüdung umfassen. Darüber hinaus kann die Überwachung von Systemleistungsmetriken wie Laserausgangsleistung, Strahlqualität und Prozessstabilität dabei helfen, Abweichungen vom Normalbetrieb zu erkennen und bei Bedarf Korrekturmaßnahmen einzuleiten.
Zusammenfassend lässt sich sagen, dass Hersteller durch die Implementierung eines proaktiven Wartungsprogramms, das regelmäßige Reinigung, Ausrichtungsprüfungen, Wartung des Kühlsystems, Kalibrierung und Routineinspektionen umfasst, die Effizienz und Langlebigkeit ihrer Laserschweißgeräte maximieren und gleichzeitig ungeplante Ausfallzeiten und das Risiko teurer Reparaturen minimieren können.
Zusammenfassen
Zusammengefasst ist dieser umfassende Leitfaden für Laserschweißmaschinen bietet eine umfassende Untersuchung der Funktionen, Vorteile, Anwendungen und Wartungsaspekte dieser transformativen Technologie. Von Präzision und Effizienz bis hin zu Vielseitigkeit und Zuverlässigkeit bieten Laserschweißgeräte beispiellose Vorteile für so unterschiedliche Branchen wie die Automobil-, Elektronik-, Medizingeräte-, Luft- und Raumfahrtindustrie und mehr. Durch das Verständnis der Grundlagen, potenziellen Gefahren und bewährten Verfahren im Zusammenhang mit dem Laserschweißen können Hersteller das volle Potenzial dieser fortschrittlichen Technologie nutzen, um Innovationen voranzutreiben, Produktionsprozesse zu optimieren und eine überragende Schweißqualität zu erzielen. Egal, ob Sie ein erfahrener Branchenprofi oder ein Neuling in der Laserschweißtechnologie sind, dieser Leitfaden dient Ihnen als umfassende Ressource, um die Feinheiten von Laserschweißgeräten zu meistern und neue Möglichkeiten in der modernen Fertigung zu erschließen.
Angetrieben durch sich entwickelnde Technologien und Branchenregeln wird sich die Vielseitigkeit von Laserschweißgeräten weiter verbessern und dem Bereich der industriellen Fertigung eine effizientere und zuverlässigere Produktionsumgebung bieten. Nur durch die umfassende Nutzung der verschiedenen Vorteile von Laserschweißmaschinen und deren flexible Wartung entsprechend den spezifischen Anforderungen können wir die Produktionseffizienz des Laserschweißens maximieren. Wenn Sie Laserschweißen in Betracht ziehen, wenden Sie sich bitte an AccTek-Laser und wir werden die beste Option für Ihre Bedürfnisse finden.
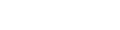
Kontaktinformationen
- [email protected]
- [email protected]
- +86-19963414011
- Nr. 3 Zone A, Industriegebiet Lunzhen, Stadt Yucheng, Provinz Shandong.
Holen Sie sich Laserlösungen