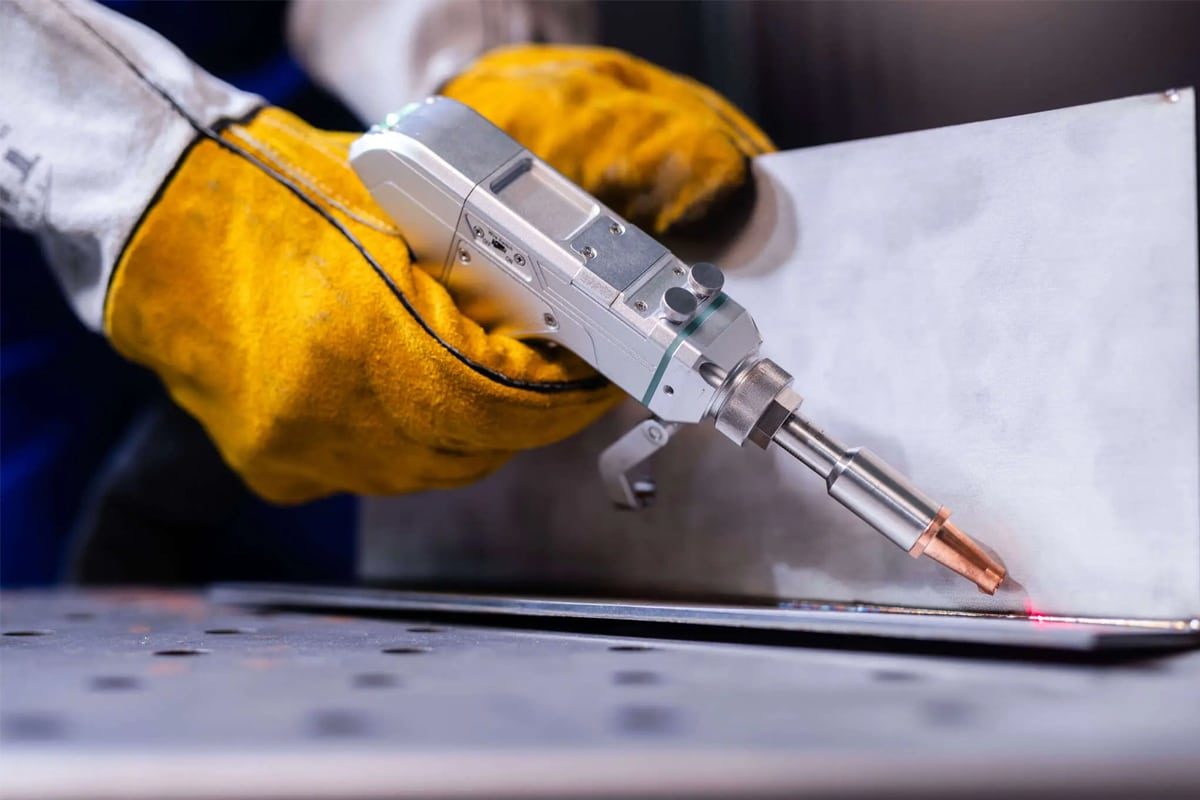
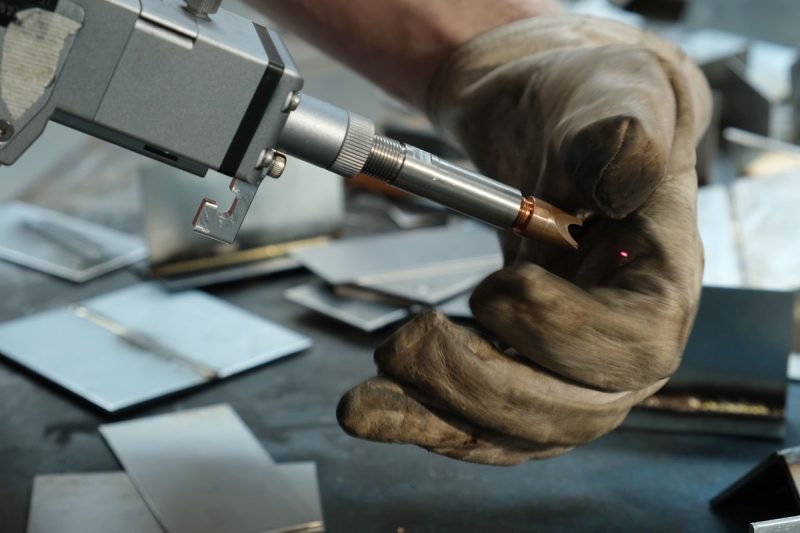
So funktioniert das Laserschweißen
Prinzipien des Laserschweißens
Beim Laserschweißen wird hochenergetische Laserstrahlung auf eine kleine Fläche des Materials fokussiert. Diese konzentrierte Energie erhitzt das Material schnell, sodass es schmilzt und verschmilzt. Anders als beim herkömmlichen Schweißen, bei dem oft breitere Wärmezonen verwendet werden, liegt der Schwerpunkt beim Laserschweißen auf der Schaffung minimaler wärmebeeinflusster Zonen, der Reduzierung von Verzerrungen und der Herstellung sauberer, hochwertiger Verbindungen. Die Verschmelzung erfolgt in einem von zwei Hauptmodi: Leitungsmodus oder Schlüssellochmodus.
- Laserleistung und Fokus: Die Leistungsdichte und Punktgröße des Lasers bestimmen die Tiefe und Breite der Schweißnaht. Höhere Leistungsdichten erzeugen tiefere Schweißnähte, während niedrigere Leistungseinstellungen für feinere, flachere Schweißnähte verwendet werden.
- Wärmekontrolle: Beim Laserschweißen ist eine präzise Kontrolle der Wärmezufuhr möglich, was für das Verbinden wärmeempfindlicher Materialien oder komplizierter Teile von entscheidender Bedeutung ist.
Arten von Laserschweißmodi
Leitungsmodusschweißen
Merkmale:
- Geringe Schweißdurchdringung, normalerweise weniger als 2 mm.
- Glatte, breite Schweißnähte mit minimaler Oberflächenverformung.
- Minimales Risiko der Bildung von Schlüssellöchern, wodurch die Wahrscheinlichkeit von Porosität oder Hohlräumen verringert wird.
Anwendungen:
- Wird häufig für dünne Materialien und Anwendungen verwendet, bei denen die visuelle Qualität entscheidend ist.
- Ideal für Anwendungen in den Bereichen Schmuck, medizinische Geräte und Elektronik, bei denen eine saubere Oberflächenbeschaffenheit erforderlich ist.
Schlüsselloch-Modus-Schweißen
Merkmale:
- Tiefe Schweißeinbrandtiefe (bis zu mehreren Zentimetern) bei geringer Breite.
- Hohes Aspektverhältnis, das zu starken, fokussierten Schweißnähten führt.
- Eine effiziente Energieabsorption durch Mehrfachreflexionen im Schlüsselloch ermöglicht eine tiefere Schweißdurchdringung.
Anwendungen:
- Geeignet für Hochleistungsanwendungen, die starke, langlebige Verbindungen erfordern, wie beispielsweise bei Automobil- und Luftfahrtkomponenten.
- Wirksam für dicke Materialien und hochfeste Metalle, bei denen eine tiefe Verschmelzung erforderlich ist.
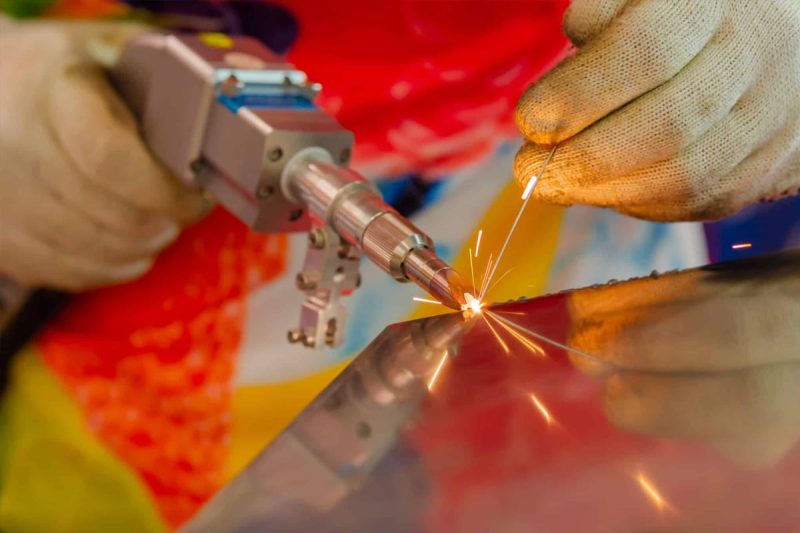
Vorteile des Laserschweißens
Präzision und Genauigkeit
Hohe Schweißgeschwindigkeit
Berührungsloser Prozess
Tiefe Durchdringung und schmale Schweißnähte
Fähigkeit zum Schweißen schwieriger Materialien
Minimale Verzerrung und Wärmeeinflusszonen
Saubere und ästhetische Schweißnähte
Geringe Wartungs- und Betriebskosten
Energieeffizienz
Automatisierung und Flexibilität
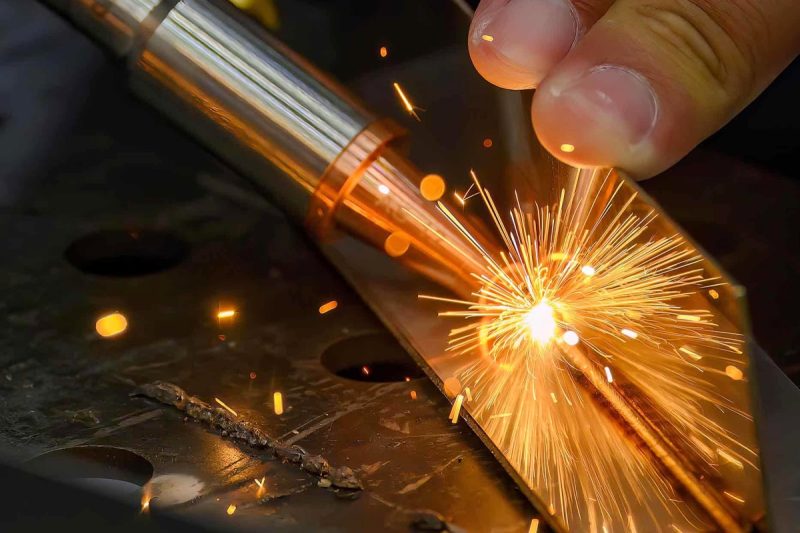
Nachteile des Laserschweißens
Hohe Anfangsinvestition
Schweißen mit begrenzter Dicke
Sensibilität gegenüber der Gelenkanpassung
Sicherheits-Bedenken
Probleme mit der Reflektivität
Technische Komplexität
Geräteempfindlichkeit
Eingeschränkter Einsatz im Feld
Erfordert qualifizierte Bediener
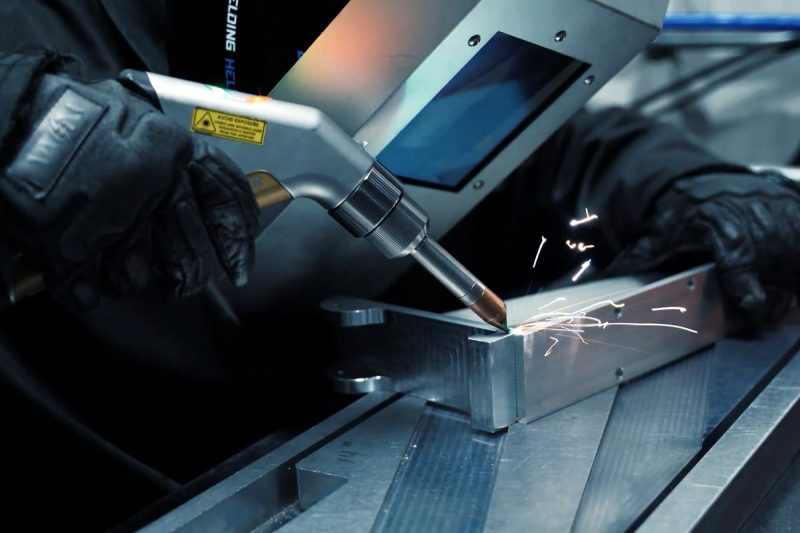
Anwendungen des Laserschweißens
Automobilindustrie
Anwendungen im Automotive-Bereich:
- Karosserieteile und Tailored Blanks.
- Motorkomponenten, einschließlich Getriebeteile.
- Airbaggehäuse erfordern Präzision und Zuverlässigkeit.
- Abgassysteme benötigen Schweißnähte, die hohen Temperaturen und Drücken standhalten.
Luft-und Raumfahrtindustrie
Anwendungen in der Luft- und Raumfahrt:
- Kraftstoffsysteme und Hydraulikleitungen erfordern dichte Schweißnähte.
- Strukturkomponenten, einschließlich Rumpfteile und Fahrwerk.
- Turbinenschaufeln und andere Motorteile, bei denen Festigkeit und Temperaturbeständigkeit entscheidend sind.
- Für die langfristige Zuverlässigkeit von Luft- und Raumfahrtelektronik sind präzise und saubere Schweißnähte erforderlich.
Herstellung medizinischer Geräte
Anwendungen in der Herstellung medizinischer Geräte:
- Chirurgische Instrumente, bei denen Korrosionsbeständigkeit und Sauberkeit von entscheidender Bedeutung sind.
- Medizinische Implantate wie Herzschrittmachergehäuse und orthopädische Geräte erfordern biokompatible, luftdichte Schweißnähte.
- Katheter und Endoskope erfordern feine, präzise Schweißnähte an kleinen Komponenten.
- Batteriegehäuse für medizinische Geräte, bei denen die Integrität der Schweißnaht für den Langzeitgebrauch von entscheidender Bedeutung ist.
Elektronikindustrie
Anwendungen in der Elektronik:
- Leiterplattenverbindungen ermöglichen feine, präzise Schweißnähte, ohne benachbarte Komponenten zu beschädigen.
- Sensorgehäuse und Batterieanschlüsse erfordern starke, langlebige Verbindungen.
- Gehäuse für empfindliche elektronische Komponenten, die Schutz vor Umwelteinflüssen gewährleisten.
- Mikroschweißen in der Halbleiterherstellung, wo Präzision und Sauberkeit entscheidend sind.
Schmuckindustrie
Anwendungen in Schmuck:
- Reparaturen an vorhandenem Schmuck, wie etwa die Größenanpassung von Ringen oder die Reparatur gerissener Ketten.
- Steinfassung, ermöglicht sichere Schweißnähte in der Nähe von Edelsteinen ohne Hitzeschäden.
- Aufwändige Metallarbeiten an individuellen Schmuckdesigns, bei denen detaillierte, filigrane Schweißnähte erforderlich sind.
- Erstellen von Metall-Mix-Designs, beispielsweise durch Verbinden von Gold und Platin, mit sauberen, unsichtbaren Schweißnähten.
Energiesektor
Anwendungen im Energiebereich:
- Batterieherstellung, bei der durch Laserschweißen dauerhafte Verbindungen zwischen Zellen und Anschlüssen hergestellt werden.
- Brennstoffzellen- und Solarpanelkomponenten profitieren von sauberen, präzisen Schweißnähten.
- Öl- und Gasleitungen, bei denen hochfeste Schweißnähte für die Sicherheit unter hohem Druck unverzichtbar sind.
- Windturbinenkomponenten, einschließlich Strukturteile, müssen Witterungseinflüssen und mechanischen Belastungen standhalten.
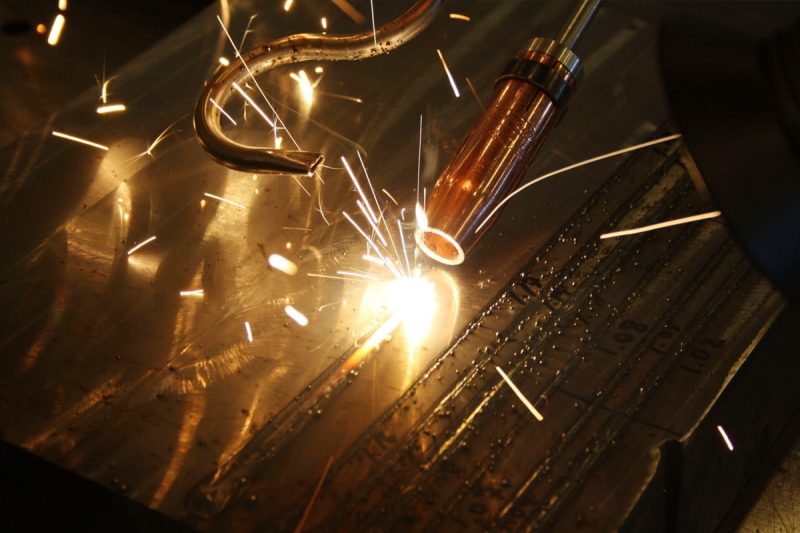
Vergleich mit herkömmlichen Schweißverfahren
Laserschweißen vs. WIG-Schweißen
- Wolfram-Inertgasschweißen (WIG) ist für die Herstellung hochwertiger, sauberer Schweißnähte bei einer Vielzahl von Metallen bekannt, darunter Aluminium, Edelstahl und Kupfer. Beim WIG-Schweißen wird eine Wolframelektrode verwendet, um einen Lichtbogen zwischen der Elektrode und dem Werkstück zu erzeugen, der das Metall schmilzt und häufig ein Füllmaterial erfordert.
- Präzision und Genauigkeit: Sowohl Laser- als auch WIG-Schweißen bieten hohe Präzision, aber das Laserschweißen hat aufgrund seines fokussierten Strahls einen Vorteil, der extrem schmale Schweißnähte mit minimalen Wärmeeinflusszonen (WEZ) erzeugen kann. WIG-Schweißen erfordert mehr manuelle Kontrolle und ist langsamer, weshalb es sich weniger für kleine, komplizierte Schweißnähte an empfindlichen Bauteilen eignet.
- Wärmeeintrag und Verformung: Die konzentrierte Energiezufuhr beim Laserschweißen erzeugt im Vergleich zum WIG-Schweißen eine viel kleinere Wärmezone. Dadurch wird das Risiko einer thermischen Verformung verringert, was insbesondere bei dünnen Materialien und wärmeempfindlichen Anwendungen wichtig ist. Beim kontrollierten WIG-Schweißen wird mehr Wärme über eine größere Fläche verteilt, was bei dünneren Materialien zu Verformungen führen kann.
- Geschwindigkeit: Laserschweißen ist deutlich schneller als WIG-Schweißen und eignet sich daher besser für die Produktion großer Stückzahlen. WIG-Schweißen kann zwar qualitativ hochwertige Ergebnisse liefern, ist aber aufgrund der manuellen Bedienung und der erforderlichen Präzision langsamer und eignet sich daher besser für kleinere Projekte oder Reparaturen.
- Anwendungen: WIG-Schweißen wird häufig bei kleinen und präzisen Projekten wie in der Luft- und Raumfahrt und bei Automobilteilen eingesetzt, ist aber im Allgemeinen in Bezug auf Geschwindigkeit und Automatisierungskompatibilität begrenzt. Laserschweißen ist ideal für Anwendungen, bei denen sowohl Geschwindigkeit als auch Präzision erforderlich sind, wie z. B. Elektronik, medizinische Geräte und Automobilkomponenten in großen Stückzahlen.
Laserschweißen vs. MIG-Schweißen
- Metall-Inertgasschweißen (MIG) ist ein gängiges Schweißverfahren zum Verbinden dickerer Materialien, insbesondere bei Anwendungen, bei denen Geschwindigkeit und Produktionsvolumen im Vordergrund stehen. Beim MIG-Schweißen wird eine kontinuierlich zugeführte Drahtelektrode verwendet, die schmilzt und eine Schweißnaht bildet. Dabei entsteht oft eine breitere Schweißfläche und es ist eine Nachbearbeitung zum Entfernen von Schweißspritzern erforderlich.
- Durchdringung und Schweißnahtbreite: Beim Laserschweißen kann eine tiefe Durchdringung mit einer schmalen Schweißnaht erreicht werden, sogar bei dicken Materialien, ohne dass Füllmaterial erforderlich ist. Beim MIG-Schweißen entsteht eine breitere, weniger präzise Schweißnaht, die häufig zusätzliche Reinigung und Nachbearbeitung erfordert. Für Anwendungen, die starke, schmale Schweißnähte erfordern, ist das Laserschweißen besser geeignet.
- Wärmeeinflusszone: Beim MIG-Schweißen wird mehr Wärme erzeugt als beim Laserschweißen, wodurch eine größere Wärmeeinflusszone entsteht und das Risiko einer thermischen Verformung steigt. Die konzentrierte Wärme beim Laserschweißen reduziert die Wärmeeinflusszone, bewahrt die mechanischen Eigenschaften des umgebenden Materials und minimiert Verformungen nach dem Schweißen, insbesondere bei dünnen oder wärmeempfindlichen Materialien.
- Automatisierung und Produktionsgeschwindigkeit: Laserschweißen ist sehr gut mit Automatisierung kompatibel und kann mit viel höheren Geschwindigkeiten durchgeführt werden, was es ideal für Produktionsumgebungen mit hohem Volumen macht. MIG-Schweißen ist zwar schneller als WIG, eignet sich jedoch aufgrund der Notwendigkeit von Drahtzufuhr und Schutzgas im Allgemeinen besser für manuelle oder halbautomatische Prozesse.
- Materialien: MIG-Schweißen ist effektiv bei dickeren Materialien und häufig verwendeten Metallen wie Stahl und Aluminium, hat jedoch Probleme bei ungleichen Materialien und sehr dünnen Materialien, bei denen Präzision und geringe Wärmezufuhr erforderlich sind. Laserschweißen eignet sich aufgrund seiner präzisen Energiekontrolle hervorragend zum Verbinden sowohl dünner als auch ungleicher Metalle, wie Kupfer mit Edelstahl.
Laserschweißen vs. Elektronenstrahlschweißen
- Elektronenstrahlschweißen (EB-Schweißen) ist ein Hochenergieschweißverfahren, das dem Laserschweißen in seiner Fähigkeit ähnelt, tiefe, präzise Schweißnähte zu erzeugen. Beim EB-Schweißen werden Materialien mit einem fokussierten Elektronenstrahl in einem Vakuum verbunden. Daher eignet es sich für anspruchsvolle Anwendungen, die eine sehr tiefe Durchdringung und eine kontrollierte Umgebung erfordern.
- Umgebung und Aufbau: Anders als beim Laserschweißen, das im Freien durchgeführt werden kann, ist beim Elektronenstrahlschweißen eine Vakuumkammer erforderlich, um den Elektronenstrahl aufrechtzuerhalten. Dieser Vakuumaufbau macht das Elektronenstrahlschweißen komplexer, teurer und weniger flexibel als das Laserschweißen, das in einer größeren Bandbreite von Umgebungen eingesetzt werden kann, darunter Reinräume oder halbautomatische Produktionslinien.
- Eindringtiefe und -stärke: Beim Elektronenstrahlschweißen kann eine tiefere Eindringtiefe als beim Laserschweißen erreicht werden. Daher ist es ideal für dicke Materialien oder Strukturanwendungen, die sehr starke Schweißnähte erfordern. Bei mitteldicken bis dünnen Materialien ist das Laserschweißen jedoch häufig effizienter und einfacher umzusetzen.
- Geschwindigkeit und Automatisierung: Beim Laserschweißen können höhere Geschwindigkeiten erreicht werden und es lässt sich leichter in automatisierte Produktionslinien integrieren, sodass es sich für die Produktion großer Stückzahlen eignet. Das Elektronenstrahlschweißen ist zwar effektiv, aber aufgrund der Anforderungen an die Vakuumkammer im Allgemeinen langsamer und weniger gut an automatisierte, schnelllebige Produktionsumgebungen anpassbar.
- Kosten und Wartung: Elektronenstrahlschweißsysteme sind teuer und erfordern eine spezielle Wartung, insbesondere das Vakuumsystem. Laserschweißen erfordert weniger Wartung und ist daher für die reguläre Fertigung zugänglicher und kostengünstiger. Darüber hinaus können die Rüstzeit und Wartung beim Elektronenstrahlschweißen im Vergleich zum Laserschweißen zu längeren Ausfallzeiten führen.
Vergleich
- Präzise und saubere Schweißnähte: Das Laserschweißen übertrifft das MIG- und WIG-Schweißen hinsichtlich der Präzision, konkurriert jedoch mit dem EB-Schweißen hinsichtlich sauberer, präziser Ergebnisse.
- Geschwindigkeit: Laserschweißen ist schneller als WIG- und MIG-Schweißen und eignet sich im Allgemeinen besser für die automatisierte Hochgeschwindigkeitsproduktion, insbesondere wenn Präzision erforderlich ist.
- Umgebung: Die Flexibilität des Laserschweißens in luftbasierten Umgebungen macht es vielseitiger als das EB-Schweißen, das ein Vakuum erfordert.
- Wärmeeinflusszone: Aufgrund der minimalen Wärmeeinflusszone ist das Laserschweißen ideal für dünne und wärmeempfindliche Materialien und übertrifft in dieser Hinsicht das WIG- und MIG-Schweißen.
- Kosten und Komplexität: Die Anschaffungskosten des Laserschweißens sind zwar höher, die Wartungs- und Betriebskosten sind jedoch im Vergleich zum Elektronenstrahlschweißen, das mit einer komplexeren Ausrüstung und einem höheren Wartungsbedarf verbunden ist, geringer.
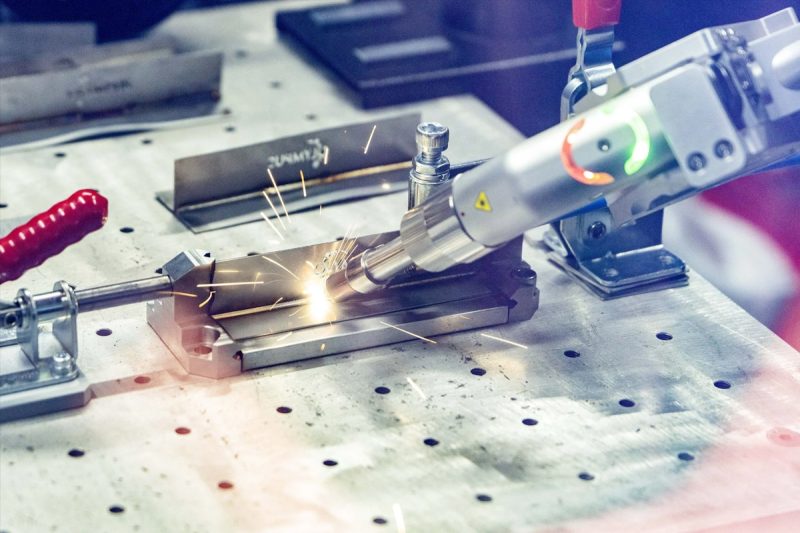
Faktoren, die die Qualität des Laserschweißens beeinflussen
Laserparameter
Die Einstellungen und Eigenschaften des Lasers selbst spielen eine entscheidende Rolle bei der Bestimmung der Qualität der Schweißnaht. Zu den wichtigsten Laserparametern gehören Leistung, Fokusfleckgröße, Schweißgeschwindigkeit und Pulsfrequenz (bei gepulsten Lasern).
- Laserleistung: Höhere Leistung erhöht die Eindringtiefe und ermöglicht schnelleres Schweißen, kann aber bei unsachgemäßer Steuerung zu übermäßiger Hitze führen. Zu viel Leistung kann zu Spritzern oder Verbrennungen führen, während zu wenig Leistung zu schwachen oder unvollständigen Schweißnähten führen kann.
- Schweißgeschwindigkeit: Die Geschwindigkeit, mit der sich der Laser über das Werkstück bewegt, beeinflusst die Schweißqualität. Hohe Schweißgeschwindigkeiten können die Wärmezufuhr verringern, die Wärmeeinflusszone (WEZ) minimieren und Verformungen reduzieren. Zu hohe Geschwindigkeiten können jedoch eine vollständige Verschmelzung der Materialien verhindern, was zu schwachen Verbindungen führt. Niedrigere Geschwindigkeiten ermöglichen ein tieferes Eindringen, können jedoch den Wärmestau erhöhen und möglicherweise thermische Verformungen verursachen.
- Fokuspunktgröße: Eine kleinere Fokuspunktgröße konzentriert die Energie auf einen winzigen Bereich und ermöglicht so feine, schmale Schweißnähte. Die Fokuspunktgröße sollte der Breite der Fuge entsprechen. Ist sie zu groß, kann dies zu übermäßiger Hitze und Verformung führen. Ist sie zu klein, dringt sie bei dickeren Materialien möglicherweise nicht tief genug ein.
- Pulsfrequenz (gepulste Laser): Bei Anwendungen, die gepulste Laser erfordern, hilft die Anpassung der Pulsfrequenz dabei, die Energiemenge zu steuern, die an die Schweißnaht abgegeben wird. Höhere Pulsfrequenzen können glattere, kontinuierliche Schweißnähte liefern, während niedrigere Frequenzen intermittierende Energiestöße liefern, die für Anwendungen nützlich sind, die nur minimale Wärmezufuhr erfordern.
Materialeigenschaften
Das zu schweißende Material beeinflusst, wie der Laser mit der Oberfläche interagiert und in das Metall eindringt. Faktoren wie Reflexionsgrad, Wärmeleitfähigkeit und Legierungszusammensetzung wirken sich alle auf die Schweißqualität aus.
- Reflektivität: Materialien mit hoher Reflektivität, wie Aluminium und Kupfer, können einen erheblichen Teil der Laserenergie reflektieren und so die Absorption verringern. Niedrigere Laserwellenlängen oder die Vorbehandlung reflektierender Materialien können dazu beitragen, die Absorption zu erhöhen und die Schweißqualität zu verbessern.
- Wärmeleitfähigkeit: Materialien mit hoher Wärmeleitfähigkeit, wie Kupfer, leiten Wärme schnell ab und erfordern eine höhere Laserleistung oder angepasste Parameter, um eine ausreichende Durchdringung zu erreichen. Materialien mit geringer Leitfähigkeit, wie Titan, speichern Wärme und ermöglichen tiefere Schweißnähte mit weniger Leistung.
- Legierungszusammensetzung: Legierungen haben oft unterschiedliche Schmelzpunkte und erfordern möglicherweise unterschiedliche Lasereinstellungen, um gleichmäßige Schweißnähte zu erzielen. Einige Legierungen erzeugen auch mehr Spritzer oder erfordern unterschiedliche Pulsfrequenzen, um Risse zu vermeiden, insbesondere solche mit Elementen, die bei Schweißtemperaturen verdampfen können.
- Oberflächenbeschaffenheit: Die Sauberkeit und Oberflächenbeschaffenheit des Materials beeinflussen, wie gut der Laserstrahl absorbiert wird. Oxide, Öle oder Oberflächenverunreinigungen können den Schweißvorgang stören und zu schwächeren Verbindungen führen. Eine Reinigung oder Oberflächenvorbereitung vor dem Schweißen kann die Konsistenz und Festigkeit der Schweißnaht verbessern.
Fugendesign und -anpassung
Die Gestaltung der Verbindung und die Passqualität beeinflussen die endgültige Schweißqualität erheblich. Eine ordnungsgemäße Gestaltung der Verbindung und eine dichte Passung stellen sicher, dass der Laser die Materialien präzise und ohne Lücken oder Fehlausrichtungen verschmelzen kann.
- Fugendesign: Verschiedene Fugenarten (z. B. Stumpfstöße, Überlappstöße und Kehlnähte) erfordern spezielle Lasereinstellungen und Fokussierung, um optimale Ergebnisse zu erzielen. Beispielsweise können Stumpfstöße eine tiefere Penetration erfordern, während Überlappstöße flacher sein können, aber kontrolliert werden müssen, um eine übermäßige Wärmeausbreitung zu vermeiden.
- Passgenauigkeit: Eine präzise Ausrichtung der Teile ist für eine gleichbleibende Schweißqualität unerlässlich. Lücken oder Fehlausrichtungen können zu einer unvollständigen Verschmelzung führen und Schwachstellen in der Schweißnaht verursachen. Enge Passungen stellen sicher, dass die Laserenergie effektiv über die Verbindung absorbiert wird, wodurch die Wahrscheinlichkeit von Defekten minimiert wird. Für Anwendungen, die extrem enge Toleranzen erfordern, können Klemm- und Vorrichtungssysteme verwendet werden, um die Teile während des Schweißens sicher zu halten.
- Dickenkompatibilität: Die Dicke der Verbindung beeinflusst auch die Festigkeit der Schweißnaht. Beim Schweißen dicker Materialien müssen die Laserparameter so angepasst werden, dass sie vollständig eindringen, ohne das umgebende Material zu überhitzen. Dünne Materialien erfordern dagegen niedrigere Leistungseinstellungen, um Verformungen oder Durchbrennen zu vermeiden.
Schutzgas
Die Verwendung von Schutzgas schützt den Schweißbereich vor Verunreinigungen und Oxidation, die die Qualität und das Aussehen der Schweißnaht beeinträchtigen können. Die Wahl und der Durchfluss des Schutzgases spielen eine wichtige Rolle beim Erreichen hochwertiger Schweißnähte.
- Gasart: Zu den üblichen Schutzgasen gehören Argon, Helium und Stickstoff. Argon sorgt für eine stabile Atmosphäre und wird häufig für eine Vielzahl von Metallen verwendet. Helium wird aufgrund seiner hohen Wärmeleitfähigkeit häufig für tiefe Penetrationen verwendet, ist aber teurer. Stickstoff wird manchmal für bestimmte Materialien wie Edelstahl verwendet, kann jedoch bei einigen Metallen Nitride verursachen, was möglicherweise die Festigkeit beeinträchtigt.
- Gasdurchflussrate: Die Durchflussrate des Schutzgases muss entsprechend den Material- und Schweißparametern angepasst werden. Eine zu hohe Durchflussrate kann das Schweißbad stören und zu Turbulenzen führen, während eine zu niedrige Durchflussrate die Schweißnaht möglicherweise nicht vollständig schützt, was zu Oxidation und Verfärbungen oder Porosität führen kann.
- Zufuhrmethode: Schutzgas kann direkt durch eine Düse in der Nähe des Laserkopfes oder in einigen Fällen durch eine sekundäre Gasleitung für eine größere Abdeckung zugeführt werden. Die richtige Gaszufuhr gewährleistet eine gleichmäßige Verteilung, schützt die Schweißnaht vor Lufteinwirkung und sorgt für ein sauberes, ästhetisches Schweißergebnis.

Zusammenfassung
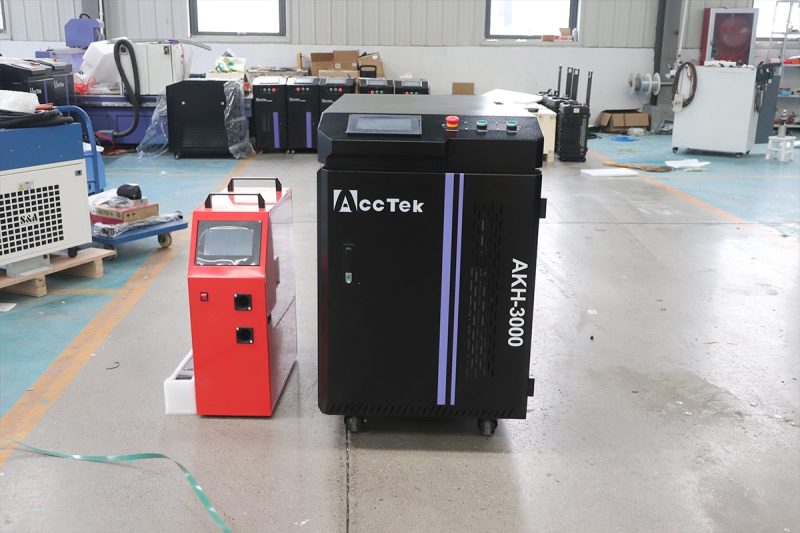
Holen Sie sich Laserschweißlösungen
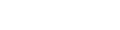
- [email protected]
- [email protected]
- +86-19963414011
- Nr. 3 Zone A, Industriegebiet Lunzhen, Stadt Yucheng, Provinz Shandong.