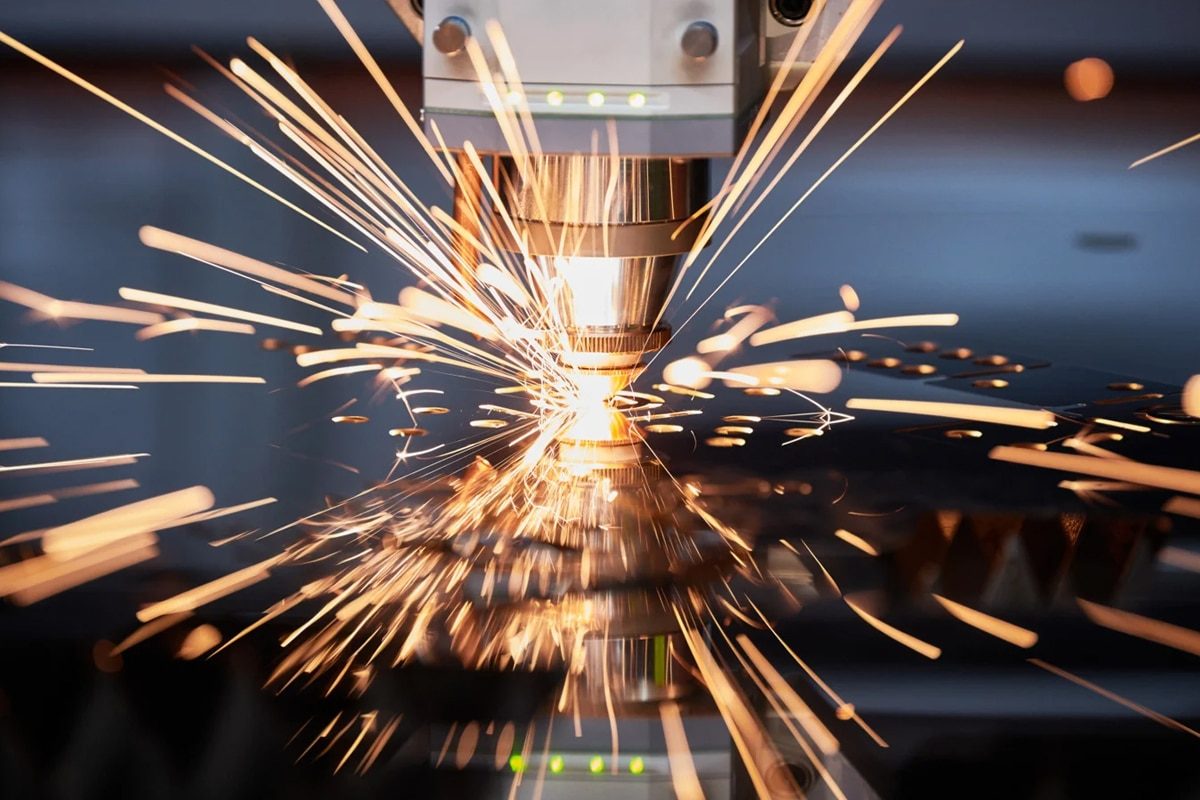
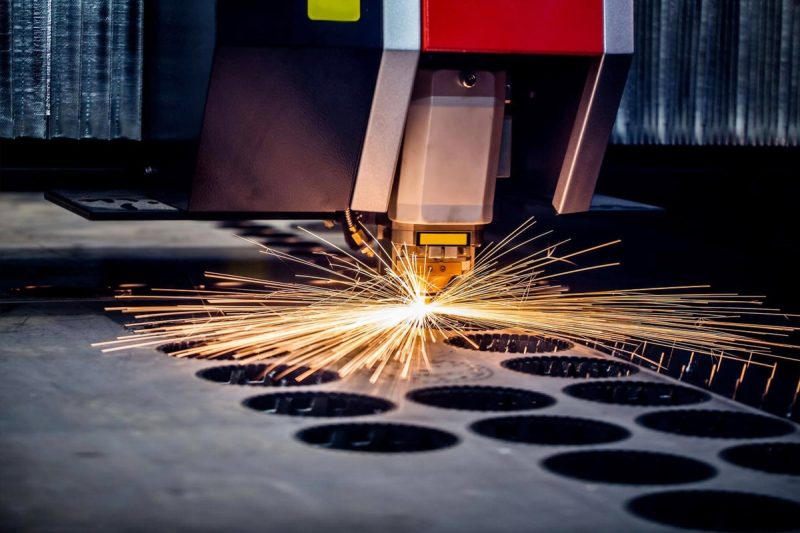
Überblick über das Laserschneiden
So funktioniert das Laserschneiden
Laserschneiden ist ein thermischer, berührungsloser Prozess, bei dem ein fokussierter Laserstrahl Material schmilzt, verbrennt oder verdampft, wodurch eine saubere und präzise Schnittkante entsteht. Hier ist eine schrittweise Beschreibung des Prozesses:
- Laserquelle: Ein Laserstrahl wird durch die Stimulation eines Lasermediums (normalerweise CO2, Faser oder YAG) in einer abgedichteten Kammer erzeugt.
- Strahlführung: Der Laserstrahl wird über Spiegel oder Glasfaser geleitet und mittels einer Linse auf das Material fokussiert, wodurch eine hochkonzentrierte Wärmequelle entsteht.
- Fokussierungs- und Schneidkopf: Der Laserstrahl wird durch einen Schneidkopf geleitet, der auch eine Düse enthält, die ein Hilfsgas (inert oder reaktiv) abgibt, um das Schneiden und die Materialentfernung zu erleichtern.
- CNC-Steuerung: Die Bewegung des Laserkopfes und des Materials wird durch ein CNC-System gesteuert, das den Laserpfad präzise gemäß einem programmierten Entwurf führt.
- Schneidvorgang: Der fokussierte Strahl interagiert mit dem Material und schmilzt, verbrennt oder verdampft es, während das Hilfsgas Splitter und geschmolzenes Material aus der Schneidzone bläst.
Vorteile des Laserschneidens
- Hohe Präzision und Genauigkeit: Durch Laserschneiden können komplizierte und komplexe Formen mit engen Toleranzen geschnitten werden, wodurch die Notwendigkeit einer Nachbearbeitung reduziert wird.
- Vielseitigkeit: Es kann eine Vielzahl von Materialien schneiden, darunter Metalle, Kunststoffe, Holz, Keramik und mehr, wodurch es branchenübergreifend äußerst anpassungsfähig ist.
- Minimaler Materialabfall: Der schmale Laserschnitt (Schnittbreite) sorgt für minimalen Materialabfall, optimiert den Ertrag und senkt die Kosten.
- Saubere Schnitte und weniger Nachbearbeitung: Beim Laserschneiden entstehen saubere Kanten mit minimalen Graten, sodass die Nachbearbeitung häufig nicht oder nur sehr wenig erforderlich ist.
- Hochgeschwindigkeitsverarbeitung: Im Vergleich zu herkömmlichen Methoden können Aufgaben mit dem Laserschneiden schneller erledigt werden, was die Produktivität steigert und die Vorlaufzeiten verkürzt.
- Berührungsloses Verfahren: Da der Laserstrahl das Material nicht physisch berührt, besteht ein geringeres Risiko einer Verformung, insbesondere bei dünnen oder empfindlichen Materialien.
- Automatisierungskompatibilität: Laserschneidsysteme können problemlos in automatisierte Lösungen integriert werden, was die Produktionseffizienz und -konsistenz verbessert.
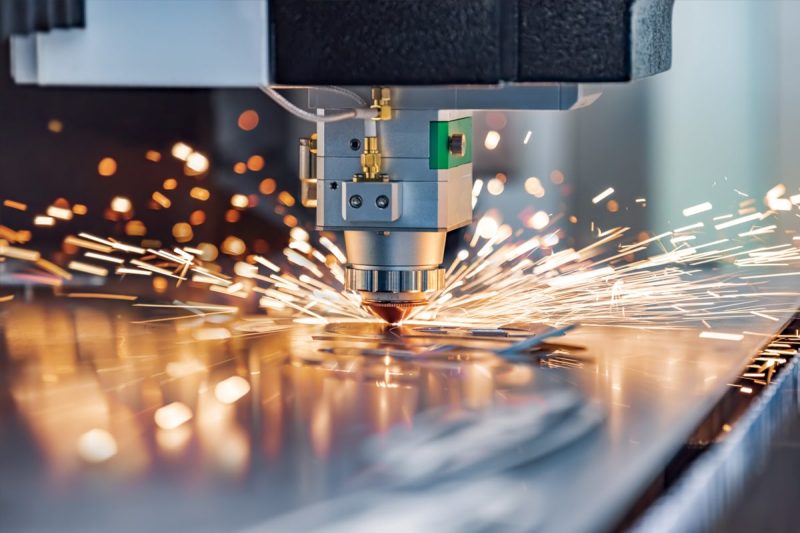
Die drei Hauptarten des Laserschneidens
Schmelzschneiden (Schmelzen und Blasen)
Erläuterung des Vorgangs
Die wichtigsten Schritte beim Schmelzschneiden sind:
- Schmelzen: Der Laserstrahl konzentriert intensive Energie auf einen kleinen Bereich, wodurch das Material schnell erhitzt und geschmolzen wird.
- Materialauswurf: Das inerte Hilfsgas bläst das geschmolzene Material vom Schnitt weg, verhindert so ein erneutes Erstarren und gewährleistet eine glatte Kante.
- Kontinuierliches Schneiden: Während sich der Laser entlang des festgelegten Pfads bewegt, wiederholt sich dieser Vorgang und erzeugt einen kontinuierlichen Schnitt.
Zum Schmelzschneiden geeignete Werkstoffe
Schmelzschneiden ist ideal für Materialien, die hochwertige, oxidationsfreie Kanten erfordern. Geeignete Materialien sind:
- Edelstahl: Wird üblicherweise mit Stickstoff geschnitten, um Oxidbildung zu verhindern.
- Aluminium und seine Legierungen: Erfordert aufgrund der hohen Reflektivität und Wärmeleitfähigkeit eine höhere Laserleistung.
- Titan- und Nickellegierungen: Nützlich für die Luft- und Raumfahrt sowie medizinische Anwendungen, bei denen die Materialintegrität von entscheidender Bedeutung ist.
- Nichteisenmetalle: Wie Messing Und Kupfer, obwohl sie aufgrund der Reflektivität möglicherweise spezielle Laser benötigen.
Vorteile des Schmelzschneidens
- Oxidfreie Kanten: Die Verwendung von Inertgas verhindert Oxidation und macht eine Oxidentfernung nach dem Schneiden überflüssig.
- Hohe Präzision und Qualität: Erzeugt glatte, saubere Schnitte mit minimaler thermischer Verzerrung.
- Minimale Nachbearbeitung: Reduziert den Bedarf an sekundären Endbearbeitungsvorgängen.
- Geeignet für komplexe Geometrien: Kann komplizierte Formen und feine Details präzise schneiden.
Anwendungsgebiete des Schmelzschneidens
- Luft- und Raumfahrtindustrie: Herstellung von Komponenten, die Präzision und hochwertige Verarbeitung erfordern.
- Herstellung medizinischer Geräte: Produktion chirurgischer Instrumente und Implantate unter Einhaltung strenger Hygienestandards.
- Elektronik: Schneiden von Teilen für elektronische Geräte, bei denen Präzision an erster Stelle steht.
- Automobilindustrie: Herstellung von Teilen, die aus Montage- und ästhetischen Gründen hochwertige Kanten erfordern.
Technische Überlegungen
- Laserleistung: Um das Material effizient zu schmelzen, ist eine ausreichende Leistung erforderlich, insbesondere bei dickeren Abschnitten.
- Hilfsgasdruck: Hochdruck-Inertgas ist für die effektive Entfernung von geschmolzenem Material unerlässlich.
- Fokusposition: Präzise Fokussierung gewährleistet optimale Energiekonzentration und Schneideffizienz.
- Düsendesign: Die richtige Düsenauswahl kann den Gasfluss optimieren und die Schnittqualität verbessern.
- Materialreflexion: Stark reflektierende Materialien wie Aluminium erfordern möglicherweise spezielle Laser oder Beschichtungen, um eine Strahlenreflexion zu verhindern.
Brennschneiden (Reaktives Schmelzschneiden)
Erläuterung des Vorgangs
Wichtige Schritte beim Brennschneiden:
- Erhitzen: Der Laserstrahl erhitzt das Material auf seine Zündtemperatur.
- Exotherme Reaktion: Sauerstoff reagiert mit dem erhitzten Metall, verbrennt es und erzeugt zusätzliche Wärme.
- Materialabtrag: Das geschmolzene Oxid wird durch den Sauerstoffstrom weggeblasen und erzeugt so den Schnitt.
Zum Brennschneiden geeignete Werkstoffe
Das Brennschneiden ist am effektivsten bei Eisenmetallen, die oxidieren können, wie zum Beispiel:
- Kohlenstoffstahl: Aufgrund seiner Reaktivität mit Sauerstoff das primäre Material zum Brennschneiden.
- Niedriglegierte Stähle: Stähle mit einem geringen Anteil an Legierungselementen.
- Weichstahl: Wird häufig im Bauwesen und in der Fertigung verwendet.
Vorteile des Brennschneidens
- Schnittdicke: Im Vergleich zum Schmelzschneiden können mit der gleichen Laserleistung dickere Materialien geschnitten werden.
- Reduzierter Laserleistungsbedarf: Die exotherme Reaktion ergänzt den Laser und ermöglicht ein effizientes Schneiden mit geringerer Leistung.
- Erhöhte Schnittgeschwindigkeit: Besonders effektiv bei dicken Stahlabschnitten.
- Kostengünstig: Sauerstoff ist weniger teuer als Inertgase wie Stickstoff oder Argon.
Anwendungen des Brennschneidens
- Schwerindustrie: Herstellung von Strukturkomponenten wie Balken und Platten.
- Schiffsbau: Schneiden großer Stahlprofile für Rümpfe und andere Strukturen.
- Baumaschinen: Herstellung von Teilen für schwere Maschinen.
- Stahl-Service-Center: Anarbeitung von Stahlblechen und -platten für verschiedene Industrien.
Technische Überlegungen
- Oxidation der Schnittkanten: Durch den Prozess entstehen oxidierte Kanten, die möglicherweise eine Nachbearbeitung wie Schleifen oder Sandstrahlen erfordern, wenn eine saubere Kante erforderlich ist.
- Wärmeeinflusszone (WEZ): Größere WEZ im Vergleich zu anderen Schneidmethoden, was die mechanischen Eigenschaften des Materials in der Nähe des Schnitts beeinträchtigen kann.
- Reinheit des Hilfsgases: Hochreiner Sauerstoff verbessert die Konsistenz und Qualität des Schnitts.
- Laserfokus und -ausrichtung: Entscheidend für die Einleitung und Aufrechterhaltung der exothermen Reaktion.
- Materialstärke: Am besten geeignet für dickere Materialien, bei denen die exotherme Reaktion den größten Nutzen bietet.
Sublimationsschneiden (Verdampfungsschneiden)
Erläuterung des Vorgangs
Wichtige Schritte beim Sublimationsschneiden:
- Verdampfung: Der Laserstrahl erhitzt das Material schnell bis zum Siedepunkt und bringt es so zum Verdampfen.
- Materialauswurf: Das Hilfsgas stößt das verdampfte Material aus dem Schneidbereich aus.
- Präzisionsschneiden: Das Fehlen von geschmolzenem Material führt zu präzisen Schnitten mit minimalen thermischen Effekten.
Für den Sublimationsschnitt geeignete Materialien
Das Sublimationsschneiden eignet sich ideal für Materialien, die einen niedrigen Schmelzpunkt haben oder schlecht brennen oder schmelzen. Geeignete Materialien sind:
- Holz und Papierprodukte: Für Gravuren und präzise Schnitte.
- Kunststoffe und Polymere: Wie Acryl, Polycarbonatund andere Thermoplaste.
- Textilien und Stoffe: Schneiden ohne Ausfransen oder Beschädigung des Materials.
- Keramik und Verbundwerkstoffe: Materialien, die spröde sind oder einen hohen Schmelzpunkt haben.
- Dünne Metalle: Wenn extreme Präzision erforderlich ist.
Vorteile des Sublimationsschneidens
- Hohe Präzision und Detailgenauigkeit: Ideal für komplizierte Designs und feine Details aufgrund der minimalen Schnittbreite.
- Saubere Schnitte: Erzeugt glatte Kanten ohne Grate oder geschmolzene Rückstände.
- Minimaler thermischer Schaden: Durch die reduzierte Wärmezufuhr wird die Wärmeeinflusszone minimiert.
- Vielseitigkeit: Kann ein breites Spektrum nichtmetallischer Materialien verarbeiten.
- Berührungsloser Prozess: Eliminiert mechanische Belastungen empfindlicher Materialien.
Anwendungen des Sublimationsschneidens
- Elektronikindustrie: Schneiden und Bohren von Leiterplatten (PCBs).
- Beschilderungen und Displays: Präzises Schneiden von Acryl und Kunststoff für hochwertige Displays.
- Medizinische Geräte: Herstellung von Komponenten, die exakte Abmessungen und saubere Kanten erfordern.
- Mode und Textilien: Stoffe für Kleidung und Accessoires zuschneiden, ohne dass die Kanten ausfransen.
- Kunst und Handwerk: Erstellen detaillierter Designs aus Holz, Papier und anderen Materialien.
Technische Überlegungen
- Laserleistungsdichte: Um eine Verdampfung zu erreichen, ist eine hohe Leistungsdichte erforderlich, insbesondere bei Materialien mit hohen Verdampfungstemperaturen.
- Materialstärke: Am besten geeignet für dünne Materialien; dicke Materialien erfordern deutlich mehr Energie.
- Unterstützung bei der Gasauswahl: Inertgase verhindern unerwünschte chemische Reaktionen und helfen beim Entfernen von verdampftem Material.
- Anforderungen an die Belüftung: Bei der Verdampfung entstehen Dämpfe, für die möglicherweise entsprechende Absaug- und Filtersysteme erforderlich sind.
- Materialeigenschaften: Das Verständnis der thermischen Eigenschaften des Materials ist entscheidend, um ein Verbrennen oder Verkohlen zu verhindern.
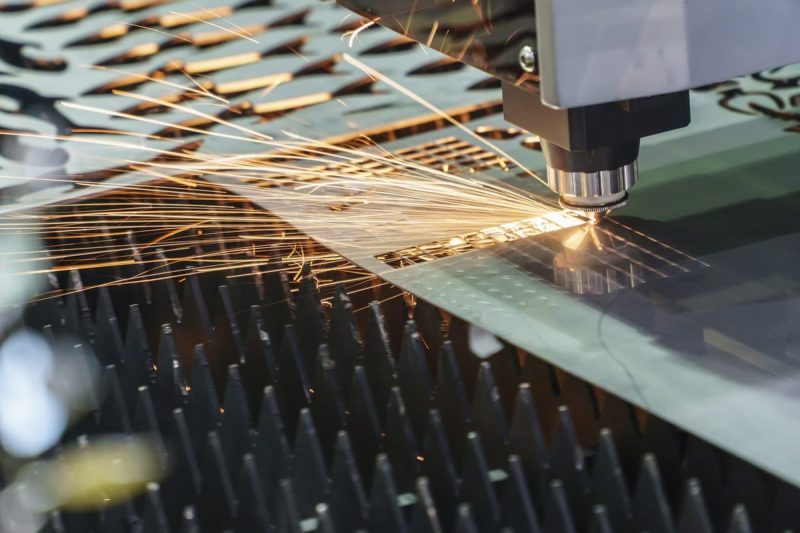
Vergleich der drei Schneideverfahren
Prozessmechanismus
- Schmelzschneiden (Schmelzen und Blasen): Bei dieser Methode wird das Material mithilfe eines Lasers geschmolzen und das geschmolzene Metall mit einem inerten Hilfsgas (z. B. Stickstoff oder Argon) weggeblasen. Es erzeugt saubere, oxidfreie Kanten und ist ideal für Präzisionsschnitte.
- Brennschneiden (Reaktives Schmelzschneiden): Beim Brennschneiden wird Sauerstoff als Hilfsgas verwendet, das mit dem erhitzten Material reagiert und eine exotherme Reaktion erzeugt, die dem Prozess Wärme zuführt und so ein effizientes Schneiden von dicken Materialien wie Kohlenstoffstahl ermöglicht. Es hinterlässt jedoch eine oxidierte Kante.
- Sublimationsschneiden (Verdampfungsschneiden): Bei diesem Verfahren wird das Material direkt durch die Hitze des Laserstrahls verdampft, wobei ein Inertgas zum Ausstoßen des verdampften Materials verwendet wird. Es eignet sich gut für präzise Schnitte in dünnen und nichtmetallischen Materialien.
Materialkompatibilität
- Schmelzschneiden: Geeignet für eine Vielzahl von Materialien, insbesondere Metalle wie Edelstahl, Aluminium und Nichteisenmetalle. Es ermöglicht hochwertige, oxidationsfreie Schnitte.
- Brennschneiden: Wird hauptsächlich zum Schneiden von Eisenmetallen wie Kohlenstoffstahl und niedriglegiertem Stahl verwendet, da es auf einer Oxidationsreaktion beruht.
- Sublimationsschneiden: Am besten für dünne Materialien geeignet, darunter Holz, Kunststoffe, Textilien, Keramik und bestimmte Metalle, bei denen präzise, komplizierte Schnitte erforderlich sind.
Kantenqualität
- Schmelzschneiden: Erzeugt saubere, glatte Kanten mit minimalen Graten und ohne Oxidation, wodurch die Notwendigkeit einer Nachbearbeitung reduziert wird.
- Brennschneiden: Führt zu oxidierten Kanten, die möglicherweise eine zusätzliche Nachbearbeitung, wie z. B. Schleifen, erfordern, um die Oxidschicht zu entfernen, wenn eine saubere Oberfläche gewünscht wird.
- Sublimationsschneiden: Erzeugt außergewöhnlich saubere Kanten mit minimaler thermischer Verformung oder Graten und ist daher ideal für Anwendungen, bei denen die Kantenqualität von größter Bedeutung ist.
Schnittgeschwindigkeit und Dickenfähigkeit
- Schmelzschneiden: Wirksam für dünne bis mitteldicke Materialien mit hoher Präzision, die Schnittgeschwindigkeit nimmt jedoch mit zunehmender Materialdicke ab.
- Brennschneiden: Ermöglicht aufgrund der exothermen Reaktion mit Sauerstoff hohe Schneidgeschwindigkeiten für dicke Materialien und ist daher für die Fertigung schwerer Bauteile und Strukturkomponenten effizient.
- Sublimationsschneiden: Aufgrund der hohen Energie, die zum Verdampfen benötigt wird, am besten für dünne Materialien geeignet. Obwohl es eine hohe Präzision bietet, ist es für dickere Abschnitte möglicherweise nicht effizient.
Unterstützung bei der Gasnutzung
- Schmelzschneiden: Inertgase wie Stickstoff oder Argon werden verwendet, um Oxidation zu verhindern und eine saubere Schnittkante zu erzeugen.
- Brennschneiden: Hierbei wird Sauerstoff verwendet, der mit dem Metall reagiert und durch eine exotherme Reaktion den Schneidvorgang beschleunigt.
- Sublimationsschneiden: Je nach Material wird häufig ein Inertgas oder gar kein Gas verwendet, um verdampftes Material auszustoßen.
Wärmeeinflusszone (HAZ)
- Schmelzschneiden: Erzeugt eine relativ kleine Wärmeeinflusszone durch die Konzentration auf das Schmelzen ohne zusätzliche Reaktionen.
- Brennschneiden: Aufgrund der exothermen Reaktion entsteht dabei eine größere Wärmeeinflusszone, die die Materialeigenschaften in der Nähe der Schnittkante verändern kann.
- Sublimationsschneiden: Minimiert die Wärmeeinflusszone durch schnelle Verdampfung und bewahrt so die Integrität des umgebenden Materials.
Anwendungen
- Schmelzschneiden: Ideal für Anwendungen, bei denen hohe Präzision und oxidationsfreie Kanten entscheidend sind, wie beispielsweise in der Luft- und Raumfahrt, der Medizin- und der Elektronikindustrie.
- Brennschneiden: Wird häufig in der Schwerindustrie, im Baugewerbe, im Schiffsbau und bei anderen Anwendungen verwendet, bei denen dicke Stahlprofile geschnitten werden müssen.
- Sublimationsschneiden: Am besten für Detailarbeiten an dünnen oder empfindlichen Materialien geeignet, beispielsweise in der Elektronik-, Textil- sowie Kunst- und Designbranche.
Kosten- und Effizienzüberlegungen
- Schmelzschneiden: Erfordert höhere Leistung und teurere Inertgase, bietet jedoch eine bessere Kantenqualität und Präzision.
- Brennschneiden: Durch die Verwendung von Sauerstoff ist es kostengünstiger, dickes Kohlenstoffstahl zu schneiden. Durch die Nachbearbeitung können jedoch zusätzliche Kosten entstehen.
- Sublimationsschneiden: Energieintensiv für dickere Materialien, daher besser geeignet für spezielle Anwendungen mit dünnen Materialien.
Übersichtstabelle
Besonderheit | Schmelzschneiden | Brennschneiden | Sublimationsschneiden |
Prozessmechanismus | Schmilzt Material, Inertgas entfernt Schmelze | Verwendet Sauerstoff für eine exotherme Reaktion | Verdampft Material |
Materialien | Metalle wie Edelstahl, Aluminium | Kohlenstoffstahl, niedriglegierte Stähle | Dünne Metalle, Nichtmetalle, Kunststoffe |
Kantenqualität | Sauber, oxidfrei | Oxidiert, muss möglicherweise nachbearbeitet werden | Sauber, präzise |
Schnittstärke | Dünn bis mittel | Dicke Materialien | Dünne Materialien |
Hilfsgas | Inertgas (z. B. Stickstoff, Argon) | Sauerstoff | Inertgas oder keines |
HAZ | Klein | Groß | Minimal |
Anwendungen | Luft- und Raumfahrt, Elektronik, Medizin | Strukturbauteile, Schwerindustrie | Elektronik, Textilien, Kunst |
Kosteneffizienz | Höhere Kosten, hohe Präzision | Kostengünstig für dicke Schnitte | Hohe Präzision, dünne Materialien |
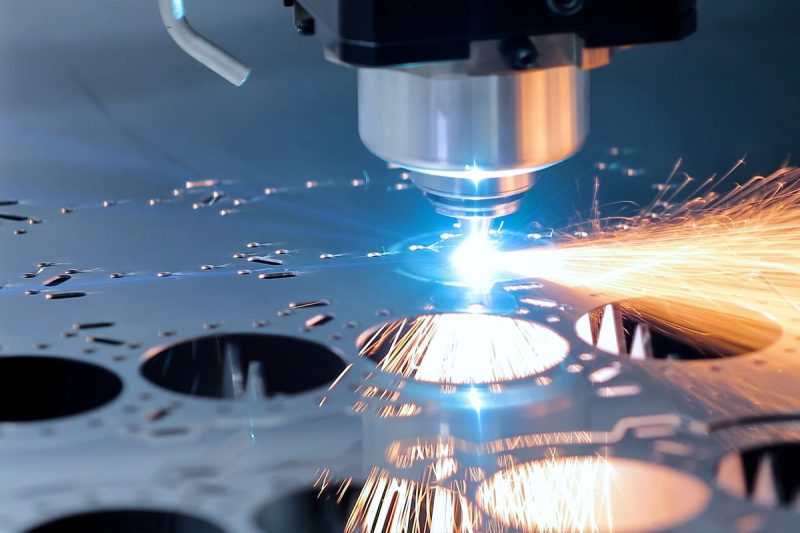
Auswahl der richtigen Schneidemethode
Materialtyp und Eigenschaften
- Metallische Materialien: Für Metalle wie Edelstahl, Aluminium und andere Nichteisenmetalle, die saubere, oxidfreie Kanten erfordern, ist Schmelzschneiden oft die beste Option. Die Verwendung von Inertgasen verhindert Oxidation und führt zu hochwertigen, präzisen Schnitten.
- Eisenmetalle: Wenn Sie Kohlenstoffstahl oder andere Eisenmaterialien schneiden, bietet das Brennschneiden aufgrund der Verwendung von Sauerstoff zur Erzeugung einer exothermen Reaktion eine hervorragende Leistung. Diese Methode ermöglicht das effiziente Schneiden dicker Materialien, kann jedoch zu oxidierten Kanten führen.
- Nichtmetallische und dünne Materialien: Sublimationsschneiden ist ideal für nichtmetallische Materialien wie Kunststoffe, Holz, Keramik und Textilien. Es eignet sich am besten für komplizierte Designs und präzise Schnitte, insbesondere für dünne Materialien.
Gewünschte Kantenqualität
- Saubere, oxidfreie Kanten: Wenn eine hochwertige, saubere Kante ohne Oxidation für Ihre Anwendung entscheidend ist, ist das Schmelzschneiden aufgrund der Verwendung von Inertgasen, die eine Oxidation während des Schneidvorgangs verhindern, vorzuziehen.
- Oxidierte Kanten: In Fällen, in denen eine starke exotherme Reaktion erforderlich ist und oxidierte Kanten akzeptabel sind oder nachbearbeitet werden können, ist das Brennschneiden eine geeignete Option.
- Hohe Präzision und glatte Kanten: Für Anwendungen, die extreme Präzision und glatte Kanten mit minimaler thermischer Verzerrung erfordern, wie z. B. in der Elektronik und der bildenden Kunst, ist das Sublimationsschneiden die richtige Wahl.
Materialstärke
- Dünne bis mittlere Dicke: Das Schmelzschneiden eignet sich hervorragend für dünne bis mitteldicke Materialien und bietet Präzision und hochwertige Kanten.
- Dicke Materialien: Das Brennschneiden eignet sich besser für dickere Materialien, da die exotherme Reaktion ein effizientes Schneiden mit geringerem Laserleistungsbedarf ermöglicht.
- Sehr dünne Materialien: Sublimationsschneiden ist ideal für sehr dünne Materialien und bietet hohe Präzision für komplizierte Muster und Formen.
Schnittgeschwindigkeit und Effizienz
- Hochgeschwindigkeitsproduktion: Wenn es vor allem beim Schneiden dicker Stahlplatten auf Geschwindigkeit ankommt, ist das Brennschneiden aufgrund seiner exothermen Reaktion auf Sauerstoffbasis äußerst effizient.
- Präzision vor Geschwindigkeit: Für Anwendungen, bei denen Präzision wichtiger ist als Geschwindigkeit, liefern Schmelzschneiden und Sublimationsschneiden hervorragende Ergebnisse.
- Serienfertigung vs. Sonderanfertigung: Berücksichtigen Sie die Art Ihrer Produktion. Schmelzschneiden eignet sich für hochpräzise Serienfertigung, während Sublimationsschneiden ideal für Sonderanfertigungen mit komplexen Details ist.
Kostenüberlegungen
- Kosten für Hilfsgas: Beim Schmelzschneiden werden Inertgase wie Stickstoff oder Argon verwendet, die teurer sein können als der beim Brennschneiden verwendete Sauerstoff. Allerdings bietet es eine bessere Kantenqualität.
- Stromverbrauch: Sublimationsschneiden kann bei dicken Materialien energieintensiv sein, ist aber bei dünnen Abschnitten effizient. Beim Brennschneiden ist aufgrund der durch die Sauerstoffreaktion erzeugten Wärme eine geringere Laserleistung erforderlich, was es bei dicken Schnitten kostengünstig macht.
- Anforderungen an die Nachbearbeitung: Die Notwendigkeit einer Nachbearbeitung (z. B. Oxidentfernung beim Brennschneiden) kann die Gesamtkosten erhöhen, was bei der Entscheidung berücksichtigt werden sollte.
Bewerbungsvoraussetzungen
- Präzisionskritische Anwendungen: Für Branchen wie die Luft- und Raumfahrt, die Elektronik und die Herstellung medizinischer Geräte, in denen es auf Präzision und saubere Kanten ankommt, werden Schmelzschneiden und Sublimationsschneiden bevorzugt.
- Schwerlastfertigung: Das Brennschneiden ist ideal für Strukturkomponenten, schwere Maschinen und andere Anwendungen, die das Schneiden dicker Metalle erfordern.
- Komplizierte Designs: Wenn feine Details und komplizierte Schnitte erforderlich sind, insbesondere bei nichtmetallischen Materialien, ist Sublimationsschneiden die beste Option.
Überlegungen zu Ausrüstung und Einrichtung
- Laserleistung und -typ: Stellen Sie sicher, dass das von Ihnen gewählte Lasersystem über ausreichend Leistung verfügt und mit der ausgewählten Schneidmethode kompatibel ist. Beispielsweise können stark reflektierende Metalle beim Schmelzschneiden spezielle Laserquellen erfordern.
- Verfügbarkeit von Hilfsgasen: Berücksichtigen Sie die Verfügbarkeit und Kosten von Hilfsgasen. Beim Brennschneiden wird normalerweise Sauerstoff verwendet, während beim Schmelzschneiden Inertgase erforderlich sind.
- Automatisierung und Integration: Wenn Sie das Laserschneiden in eine automatisierte Produktionslinie integrieren möchten, bieten Schmelzschneiden und Sublimationsschneiden aufgrund ihrer Präzisionsfunktionen häufig eine bessere Kompatibilität.
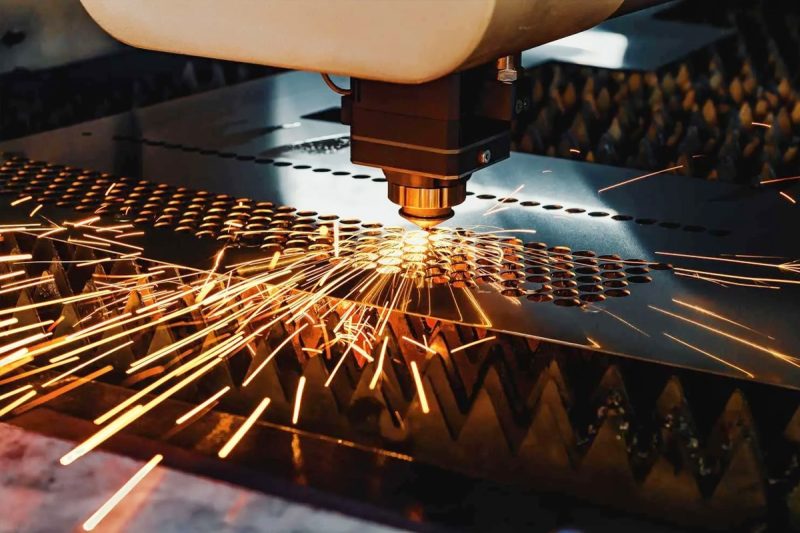
Zusammenfassung
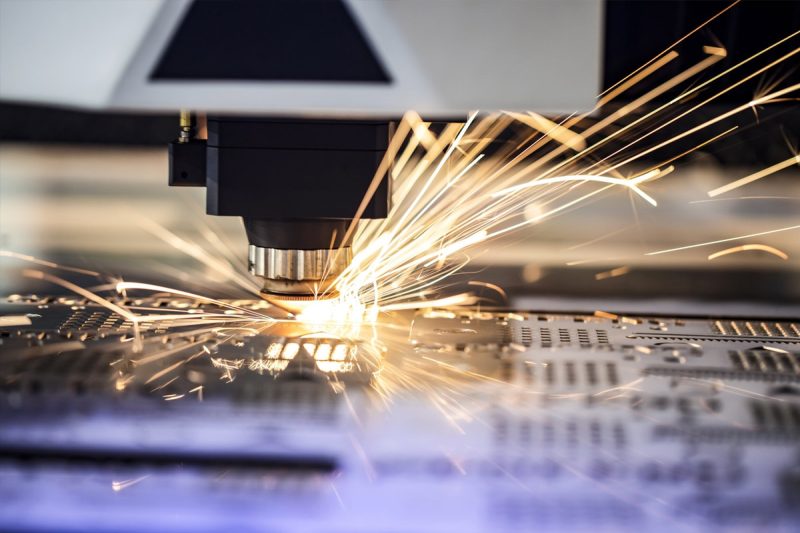
Holen Sie sich Laserschneidlösungen
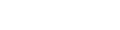
- [email protected]
- [email protected]
- +86-19963414011
- Nr. 3 Zone A, Industriegebiet Lunzhen, Stadt Yucheng, Provinz Shandong.