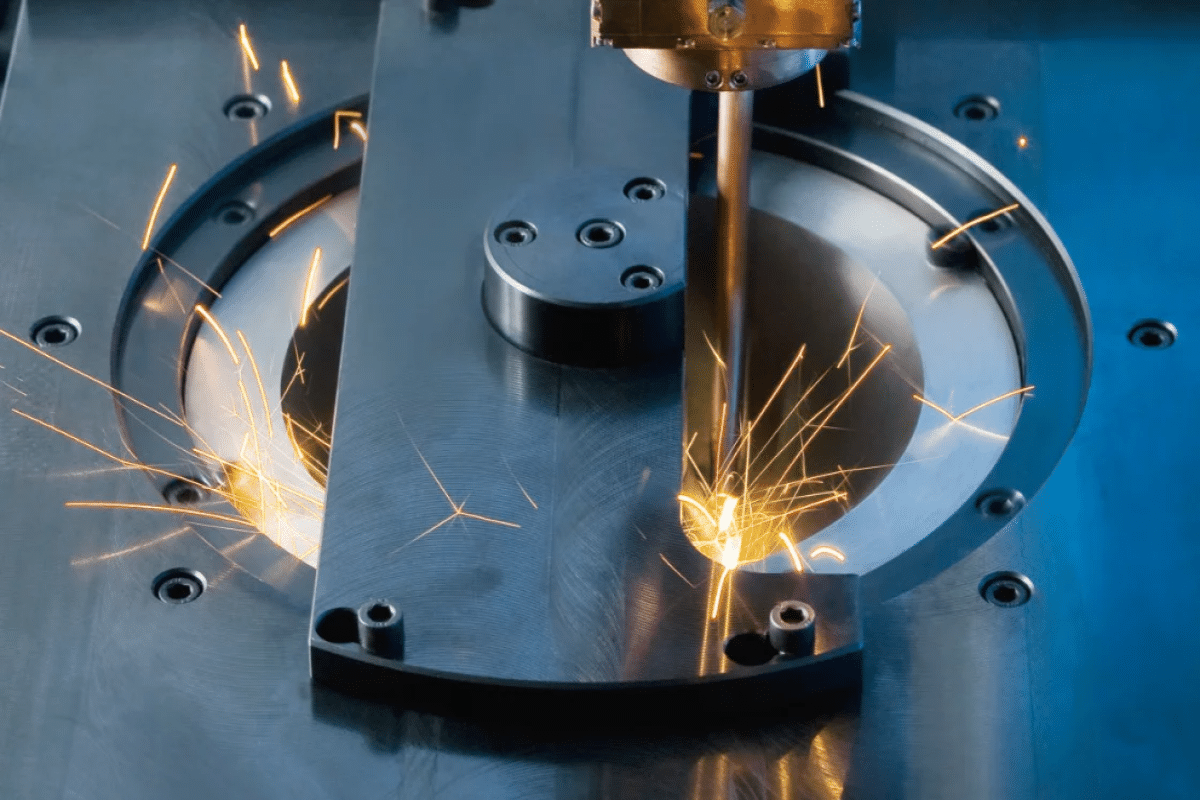
Welche Faktoren beeinflussen die Dicke des Laserschweißens?
Laserschweißen ist eine gängige Metallverbindungstechnik, die in der Fertigung und im Bauwesen weit verbreitet ist. Dabei ist die Schweißdicke ein wichtiger Parameter, und die Schweißdicke bezieht sich auf die Dicke der Schweißverbindung, die sich direkt auf die Festigkeit und Stabilität der Schweißverbindung auswirkt. Das Verständnis der Faktoren, die die Schweißdicke beeinflussen, ist entscheidend für die Gewährleistung der Schweißform und -qualität. In diesem Artikel werden die wichtigsten Faktoren erläutert, die die Dicke beim Laserschweißen beeinflussen, darunter Schweißmethode, Metallmaterial, Schweißprozess und Konstruktionsanforderungen.
Inhaltsverzeichnis
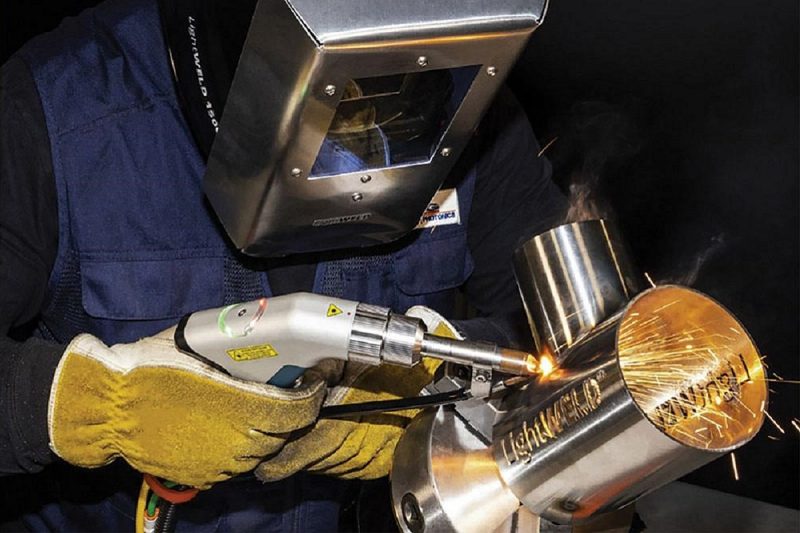
Einfluss der Laserschweißmethode auf die Schweißdicke
Unterschiedliche Laserschweißverfahren eignen sich für unterschiedliche Anwendungsszenarien und stellen unterschiedliche Anforderungen an die Schweißdicke. Diese Methoden weisen während des Schweißprozesses Unterschiede in Leistung, Heizgeschwindigkeit, Fokussierungsmodus und Schweißenergie auf, sodass für unterschiedliche Schweißdicken unterschiedliche Einschränkungen gelten.
Laserleistung und Strahlqualität
Laserleistung und Strahlqualität sind zwei wichtige Parameter, die einen gewissen Einfluss auf die Dicke des Laserschweißens haben.
- Laserleistung: Unter Laserleistung versteht man die vom Laserstrahl übertragene Energie. Bei gleichen Material- und Schweißbedingungen kann eine höhere Laserleistung im Allgemeinen eine größere Eindringtiefe der Schweißnaht ermöglichen, was zum Schweißen dickerer Materialien geeignet ist. Eine zu hohe Laserleistung kann jedoch zu einem übermäßigen Schmelzen der Schweißnaht und einer Vergrößerung der Wärmeeinflusszone führen, was möglicherweise zu Verformungen und Qualitätsproblemen führt. Daher ist es notwendig, bei der Auswahl der Laserleistung die Anforderungen an Schweißqualität und -geschwindigkeit in Einklang zu bringen.
- Strahlqualität: Die Strahlqualität hat einen erheblichen Einfluss auf die Energieverteilung und die Fokussierungsleistung beim Schweißen. Eine bessere Strahlqualität kann zu einer kleineren Brennfleckgröße und einer höheren Fokussierungsfähigkeit des Strahls führen, wodurch die Schweißenergie konzentrierter wird und so die Schweißpräzision und Steuerungsleistung verbessert wird.
Strahlfokussierungsmethode und Fokusposition
Auch die Strahlfokussierungsmethode und die Fokuslage haben einen gewissen Einfluss auf die Schweißdicke beim Laserschweißprozess.
- Strahlfokussierungsmethode: Zu den üblichen Strahlfokussierungsmethoden gehören die Flachfokussierung, die Konvexlinsenfokussierung, die Konkavlinsenfokussierung usw. Unterschiedliche Fokussierungsmethoden weisen unterschiedliche Anpassungsmöglichkeiten an die Schweißdicke auf.
- Fokusposition: Wenn die Fokusposition über der Schweißnahtoberfläche liegt, kann eine größere Einschweißtiefe und eine größere Wärmeeinflusszone erreicht werden. Diese Fokusposition eignet sich zum Schweißen dickerer Materialien und kann die Eindringtiefe der Schweißnaht erhöhen. Wenn die Fokusposition unterhalb der Schweißnahtoberfläche liegt, können eine geringere Schweißeindringtiefe und eine kleinere Wärmeeinflusszone erreicht werden. Diese Fokusposition eignet sich zum Schweißen dünnerer Materialien, wodurch Verformungen und Hitzeschäden reduziert werden können.
Scangeschwindigkeit und Laserstrahldurchmesser
- Scangeschwindigkeit: Die Geschwindigkeit, mit der sich der Laserstrahl beim Laserschweißen im Schweißbereich bewegt, wird als Scangeschwindigkeit bezeichnet. Eine niedrigere Scangeschwindigkeit kann zu einer längeren Schweißzeit führen, sodass die Wärme vollständiger auf den Schweißbereich übertragen werden kann, was zum Schneiden dickerer Materialien geeignet ist. Durch die höhere Scangeschwindigkeit bleibt der Laserstrahl kürzer im Schweißbereich, was sich besser zum Schneiden dünnerer Materialien eignet.
- Laserstrahldurchmesser: Ein kleinerer Laserstrahldurchmesser kann eine höhere Energiedichte liefern und die Wärme im Schweißbereich konzentrierter machen. Dies trägt zu einer geringeren Einschweißtiefe bei und eignet sich zum Schweißen dünnerer Materialien. Größere Laserstrahldurchmesser sind vorteilhaft beim Schweißen dickerer Materialien oder bei Schweißaufgaben, die das Füllen größerer Flächen erfordern.
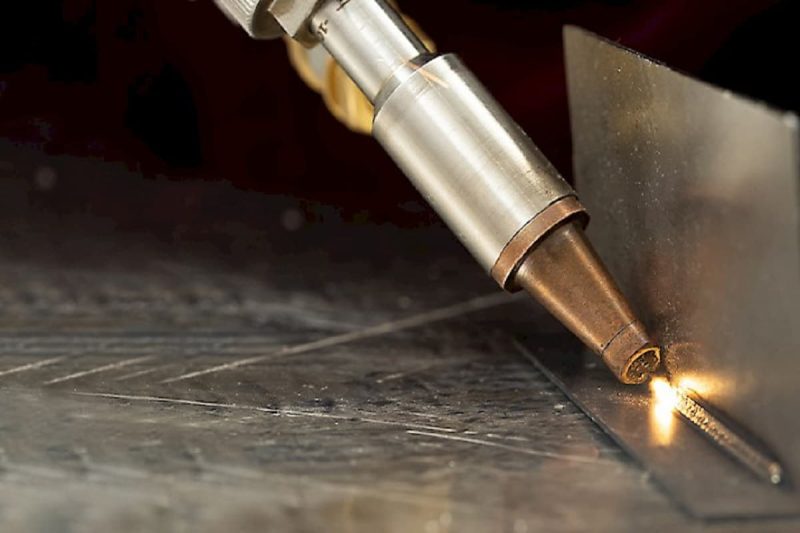
Einfluss der Materialeigenschaften auf die Schweißnahtdicke
Der Einfluss verschiedener Materialien auf die Dicke beim Laserschweißen ist vielfältig, da verschiedene Materialien unterschiedliche Wärmeleitfähigkeiten, Schmelzpunkte und Schmelzverhalten aufweisen. Hier sind einige Schlüsselfaktoren, die Sie berücksichtigen sollten:
Absorptionskoeffizient
Der Absorptionskoeffizient eines Materials bestimmt, wie effizient es Laserenergie absorbiert. Materialien mit hohen Absorptionskoeffizienten für die im Schweißprozess verwendeten Laserwellenlängen neigen dazu, mehr Energie zu absorbieren und sich schneller zu erwärmen, was zu einer tieferen Eindringtiefe und dickeren Schweißnähten führt. Beispielsweise haben Metalle wie Stahl hohe Absorptionskoeffizienten für bestimmte Laserwellenlängen, was ein tieferes Eindringen und dickere Schweißnähte ermöglicht als Materialien mit niedrigeren Absorptionskoeffizienten wie Aluminium.
Wärmeleitfähigkeit
Die Wärmeleitfähigkeit von Materialien beeinflusst die Wärmeverteilung beim Laserschweißen. Materialien mit geringer Wärmeleitfähigkeit, wie zum Beispiel Edelstahl, neigen dazu, mehr Wärme zu speichern, was zu einer tieferen Eindringtiefe und dickeren Schweißnähten führt. Materialien mit hoher Wärmeleitfähigkeit, wie etwa Kupfer oder Aluminium, leiten die Wärme tendenziell effizienter vom Schweißbereich ab, was zu einer geringeren Schweißnahtdurchdringung und einer geringeren Schweißnahtdicke führt. Daher benötigen sie eine höhere Laserleistung oder längere Belichtungszeiten, um eine tiefe Eindringtiefe und dickere Schweißnähte zu erzielen.
Schmelzpunkt
Der Schmelzpunkt eines Materials beeinflusst die zum Schmelzen und Schweißen erforderliche Temperatur. Beim Laserschweißen muss das Material seinen Schmelzpunkt erreichen, um ein Schweißbad zu bilden. Materialien mit niedrigeren Schmelzpunkten benötigen weniger Laserenergie, um die Schmelztemperatur zu erreichen, was zu einer höheren Eindringtiefe und Schweißnahtdicke führt. Umgekehrt erfordern Materialien mit höheren Schmelzpunkten möglicherweise eine höhere Laserenergie, was zu einer geringeren Schweißnahtdurchdringung und einer geringeren Schweißnahtdicke führt.
Reflektierend
Das Reflexionsvermögen des Materials beeinflusst die Menge der absorbierten oder reflektierten Laserenergie. Hochreflektierende Materialien (wie Aluminium oder Kupfer) reflektieren den Großteil der Laserenergie, was zu einer geringeren Absorption und einer begrenzten Schweißtiefe führt. Im Gegensatz dazu absorbieren Materialien (z. B. Kohlenstoffstahl) mit geringerem Reflexionsvermögen (z. B. Kohlenstoffstahl) mehr Laserenergie und erzielen dadurch tiefere und dickere Schweißnähte.
Dicke
Auch die Dicke des Schweißmaterials beeinflusst die Dicke der Schweißnaht. Laserschweißen eignet sich in der Regel besser für dünnere Materialien, da die Laserenergie präziser und effektiver sein kann. Dickere Materialien erfordern möglicherweise mehrere Schweißspuren oder eine höhere Laserleistung, um ein vollständiges Schmelzen zu erreichen, was sich auf die endgültige Schweißdicke auswirken kann.
Wärmeausdehnungskoeffizient
Der Wärmeausdehnungskoeffizient ist der Grad der Ausdehnung oder Kontraktion des Materials bei Temperaturänderungen. Wenn beim Schweißen Laserenergie angewendet wird, erfährt das Material eine schnelle Erwärmung und anschließende Abkühlung. Materialien mit hohen Wärmeausdehnungskoeffizienten (z. B. bestimmte Kunststoffe) können beim Schweißen erheblich auftreten, was zu Änderungen der Schweißnahtdicke führt.
Metallurgische Leistung
Auch die metallurgische Leistungsfähigkeit von Werkstoffen, etwa deren Inhaltsstoffe, Kornstruktur und Legierungselemente, kann die Schweißdicke beeinflussen. Beispielsweise können bestimmte Legierungselemente den Absorptionskoeffizienten oder die Wärmeleitfähigkeit des Materials verändern und dadurch den Wärmeeintrag und die Schweißtiefe beeinflussen.
Verdampfungs- und Siedeverhalten
Einige Materialien neigen eher dazu, zu verdampfen oder zu sieden, wenn sie hohen Temperaturen ausgesetzt werden. Während des Laserschweißprozesses kann dieses Verdampfen oder Sieden dazu führen, dass das schmelzende Material verspritzt wird und die Schmelztiefe der Schweißnaht sowie die Schweißdicke abnimmt. Das Formverhalten wird durch Faktoren wie Materialdampfdruck, Siedepunkt und Verdampfungspotentialwärme beeinflusst.
Folge- und Erstarrungsverhalten
Unterschiedliche Materialien haben unterschiedliche Schmelz- und Erstarrungseigenschaften, die sich auf die Bildung und Erstarrung des Schmelzbades auswirken. Enge oder im Schmelzbereich verfestigte Materialien oder offensichtliche Koagulation und Kontraktion wirken sich auf die erreichbare Schweißdicke aus.
Es ist zu beachten, dass diese Faktoren miteinander interagieren und mit den Parametern des Laserschweißprozesses (wie Laserleistung, Strahldurchmesser und Schweißgeschwindigkeit) interagieren. Daher muss die Optimierung des Laserschweißprozesses für bestimmte Materialien in Betracht gezogen und diese Materialien ausbalanciert werden, um die erforderliche Schweißdicke und -qualität zu erreichen. Darüber hinaus kann auch der spezifische Laserschweißprozess (z. B. das Schweißen kleiner Löcher oder das Konduktionsschweißen) die Beziehung zwischen Materialeigenschaften und Schweißnahtdicke beeinflussen.
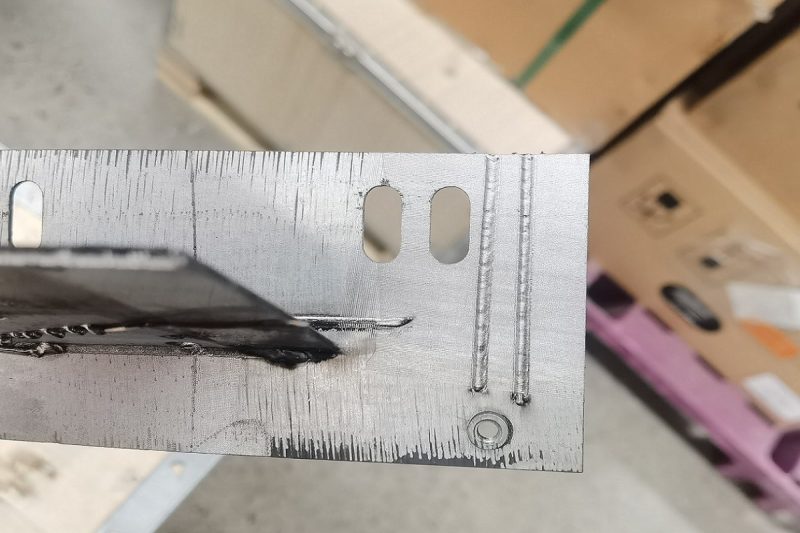
Einfluss der Laserschweißprozesssteuerung auf die Schweißnahtdicke
Die Parametereinstellung und die Betriebsweise beim Laserschweißprozess wirken sich auch auf die Schweißdicke aus. Beispielsweise hat die Auswahl von Parametern wie Schweißstrom, Schweißgeschwindigkeit und Schweißzeit direkten Einfluss auf die Größe und Form der Schweißverbindung. Darüber hinaus sind Prozesse wie Vorwärmen und Nachwärmen während des Schweißprozesses wichtige Faktoren zur Steuerung der Schweißdicke.
Vorwärmen und Nachwärmen
Vorwärmen und Nachwärmen sind zwei häufig verwendete Methoden zur Steuerung des Schweißprozesses. Das Folgende ist eine allgemeine Situation der Auswirkung von Vorwärmung und Nachwärmebehandlung auf die Schweißnahtdicke:
- Vorwärmen: Der Zweck des Vorwärmens besteht darin, die thermische Belastung und Abkühlgeschwindigkeit während des Schweißprozesses zu verbessern. Durch das Vorwärmen kann die Temperatur des Materials erhöht, der Temperaturgradient während des Schweißprozesses verringert und die thermische Spannung reduziert werden, wodurch die Gefahr von Verformungen und Rissen verringert wird. Das Vorwärmen dünnerer Materialien sollte im Einzelfall beurteilt und angepasst werden.
- Nachwärmebehandlung: Bei der Nachwärmebehandlung wird der Schweißbereich nach dem Schweißen erwärmt oder abgekühlt. Der Zweck der Nachwärmebehandlung besteht darin, die Struktur und Leistung der Schweißnaht zu verbessern, Restspannungen zu reduzieren und die Schweißqualität zu verbessern.
Auswahl an Schweißnahtform und Schweißzusatz
- Schweißnahtform: Die Schweißnahtform umfasst lineare Schweißnähte, V-förmige Schweißnähte, U-förmige Schweißnähte, J-förmige Schweißnähte usw. Unterschiedliche Schweißnahtformen haben unterschiedliche Auswirkungen auf die Schweißdicke. Gerade Schweißnähte eignen sich beispielsweise zum Schweißen dünnerer Materialien, was zu einer besseren Schweißfestigkeit und Abdichtung führen kann. Die V-förmige Schweißnaht hat eine größere Schweißtiefe und eignet sich zum Schweißen dickerer Materialien usw.
- Füllstoff: Ein Füllstoff ist ein Material, das während des Schweißprozesses der Schweißnaht hinzugefügt wird, um den Schweißbereich zu füllen und zu verstärken. Bei dünneren Materialien sind die Füllstoffoptionen möglicherweise eingeschränkter. Bei dickeren Materialien können Füllstoffe verwendet werden, um Schweißnähte mit größerer Breite und Tiefe zu füllen.
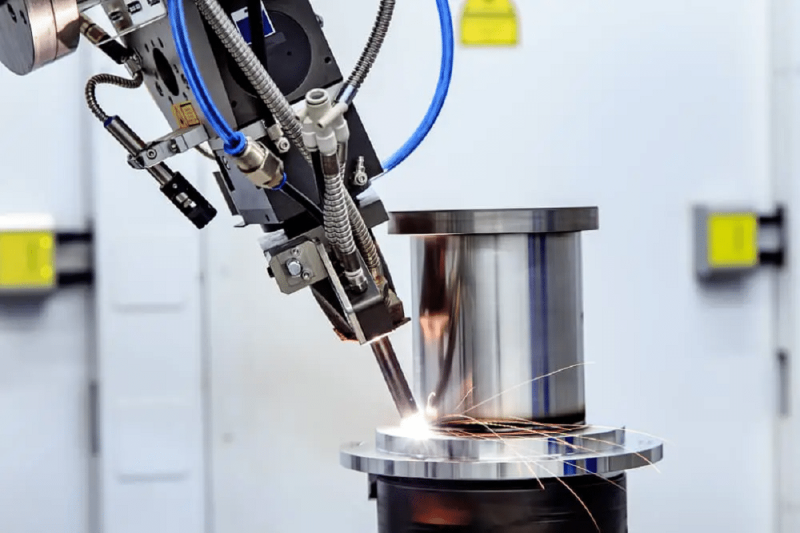
Einfluss von Design- und Anwendungsanforderungen auf die Schweißnahtdicke
Designanforderungen beziehen sich auf die Anforderungen an Produkte oder Strukturen für das Laserschweißen, einschließlich Festigkeit, Abdichtung, Aussehen usw. Der Einfluss von Designanforderungen auf die Dicke des Laserschweißens ist wie folgt:
Höhere Festigkeitsanforderungen
Bei Produkten oder Konstruktionen, die eine höhere Festigkeit erfordern, kann es erforderlich sein, die Festigkeit der Schweißverbindung durch eine Erhöhung der Schweißnahtdicke zu erhöhen.
Höhere Dichtheitsanforderungen
Wenn das Produkt oder die Struktur eine hohe Dichtleistung aufweisen muss, kann es auch erforderlich sein, die Dichtleistung des Schweißbereichs durch eine Erhöhung der Schweißdicke zu erhöhen.
Anforderungen an das Aussehen
Wenn an das Produkt oder die Struktur hohe Anforderungen an das Erscheinungsbild gestellt werden, muss auf Unebenheiten und Oberflächenqualität im Schweißbereich geachtet werden. Größere Schweißnahttiefen und Schweißnahtgrößen können das Erscheinungsbild beeinträchtigen, daher muss dies im Design ausgeglichen werden.
Bewerbungsvoraussetzungen
Anwendungsanforderungen beziehen sich auf die spezifischen Anwendungsszenarien und Anforderungen des Laserschweißens. Der Einfluss der Arbeitsumgebung auf die Dicke des Laserschweißens spiegelt sich hauptsächlich in der Temperatur, der Vibration und der Umgebungsatmosphäre wider. Beispielsweise kann eine Umgebung mit hohen Temperaturen dazu führen, dass sich die Wärmeeinflusszone des Schweißbereichs ausdehnt, und es müssen entsprechende Maßnahmen zur Steuerung der Schweißdicke ergriffen werden.
Zusammenfassen
Kurz gesagt, viele Faktoren beeinflussen die Dicke des Laserschweißens. Dabei geht es neben Schweißverfahren, Materialeigenschaften, Schweißverfahren und Konstruktionsanforderungen auch um viele Aspekte. Bei der Durchführung von Schweißarbeiten müssen diese Faktoren umfassend berücksichtigt werden und die geeignete Schweißdicke sollte entsprechend der spezifischen Situation ausgewählt werden.
Nur wenn die Schweißdicke den Anforderungen entspricht, kann die Qualität und Zuverlässigkeit der Schweißverbindung gewährleistet werden, um den Anforderungen an Technik und Produkte gerecht zu werden. Wenn Sie überlegen Laserschweißen, kontaktieren Sie bitte AccTek-Laser und wir schlagen Ihnen die beste Lösung für Ihre Bedürfnisse vor.
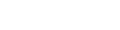
Kontaktinformationen
- [email protected]
- [email protected]
- +86-19963414011
- Nr. 3 Zone A, Industriegebiet Lunzhen, Stadt Yucheng, Provinz Shandong.
Holen Sie sich Laserlösungen