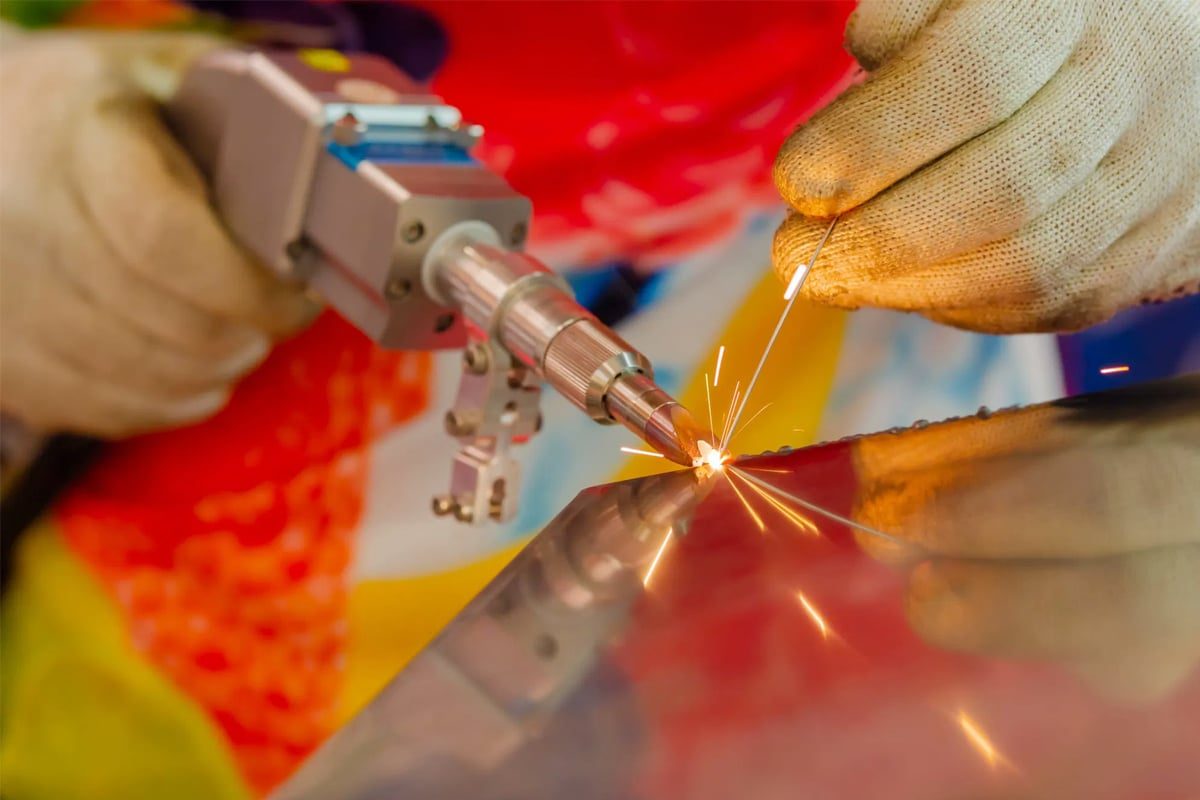
Welche Faktoren beeinflussen die Dicke des Laserschweißens?
Beim Laserschweißen ist die Kontrolle der Schweißnahtdicke entscheidend, um die Festigkeit, Haltbarkeit und ästhetische Qualität der Verbindung sicherzustellen. Die Dicke einer Laserschweißnaht wird von einer Vielzahl von Faktoren beeinflusst, von Lasereinstellungen wie Leistung, Strahlfokus und Geschwindigkeit bis hin zu den physikalischen und chemischen Eigenschaften des zu schweißenden Materials. Darüber hinaus spielen das Design der Verbindung, die Wahl des Schutzgases und die Umgebungsbedingungen im Arbeitsbereich eine entscheidende Rolle bei der Bestimmung, wie tief der Laser in das Material eindringt und wie das Gesamtschweißprofil aussieht. Durch die Optimierung dieser Faktoren können Hersteller eine präzise Schweißnahtdicke erzielen, was besonders in Branchen wichtig ist, in denen Präzision und Konsistenz entscheidend sind, wie z. B. in der Automobil-, Luft- und Raumfahrt- und Elektronikbranche. Dieser Artikel untersucht die vielen Variablen, die die Schweißnahtdicke beim Laserschweißen beeinflussen, und bietet Einblicke, wie sich Anpassungen der Prozessparameter und Materialien auf die Schweißnahttiefe und -qualität auswirken können.
Inhaltsverzeichnis
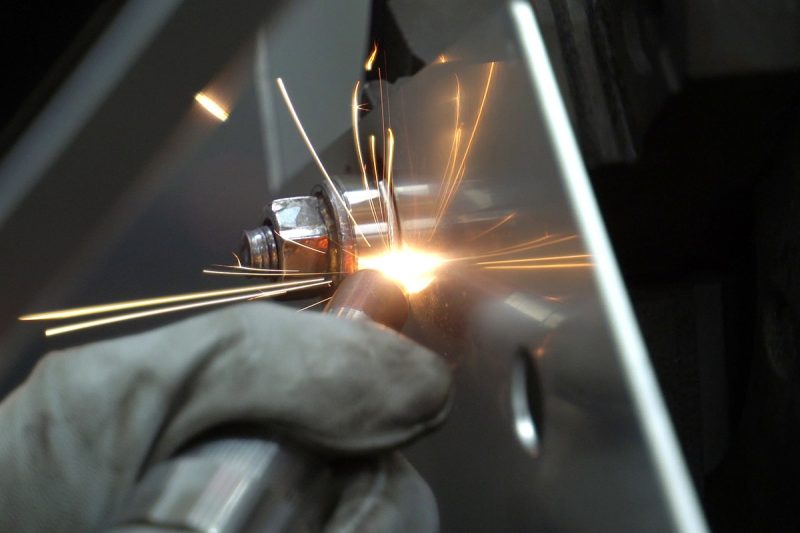
Laserschweißen verstehen
Beim Laserschweißen wird ein fokussierter Laserstrahl als intensive Wärmequelle zum Verbinden von Materialien, hauptsächlich Metallen, verwendet. Der Laserstrahl, der normalerweise von einer Laserquelle wie einem Faser-, CO2- oder Festkörperlaser erzeugt wird, wird auf die Oberfläche des Materials fokussiert. Die intensive Energie des Lasers erhitzt und schmilzt den Zielbereich schnell, wodurch ein Schmelzbad entsteht, das die Teile miteinander verbindet. Während sich der Laser entlang der Verbindung bewegt, verfestigt sich das Schmelzbad, wodurch eine durchgehende Schweißnaht entsteht.
Die hohe Energiedichte des Lasers ermöglicht ein präzises und tiefes Eindringen mit minimalen Wärmeeinflusszonen (WEZ), wodurch die thermische Verformung im Vergleich zu herkömmlichen Schweißverfahren reduziert wird. Laserschweißen kann in verschiedenen Umgebungen durchgeführt werden, darunter Vakuumkammern, Inertgasatmosphären oder im Freien, je nach spezifischer Anwendung und Materialanforderungen. Diese Vielseitigkeit und Präzision machen das Laserschweißen für komplexe Geometrien und Materialien mit unterschiedlichen thermischen Eigenschaften äußerst effektiv.
Grundlagen des Laserschweißprozesses
Der Laserschweißprozess umfasst typischerweise drei Hauptphasen: Vorbereitung vor dem Schweißen, Wechselwirkung zwischen Laser und Material und Abkühlen und Erstarren nach dem Schweißen.
- Vorbereitung vor dem Schweißen: Vor dem Schweißen müssen die Oberflächen der Materialien sauber, frei von Verunreinigungen und richtig ausgerichtet sein. Verunreinigungen wie Öle, Oxide oder Schmutz können die Energieabsorption beeinträchtigen und die Schweißqualität mindern.
- Laser-Material-Interaktion: Beim Schweißen wird der Laserstrahl auf das Werkstück fokussiert, wo seine Energie von der Oberfläche absorbiert wird, was zu lokalem Schmelzen führt. Es gibt zwei Hauptarten der Laser-Material-Interaktion:
- Konduktionsschweißen: Dies geschieht, wenn die Laserleistungsdichte relativ gering ist, was zu Oberflächenschmelzen ohne Verdampfung führt. Die Wärme wird in das Material geleitet, was zu flachen und breiten Schweißnähten führt. Dieser Modus wird häufig für Anwendungen verwendet, bei denen Ästhetik und geringe Wärmezufuhr im Vordergrund stehen.
- Stichlochschweißen: Wenn die Laserleistungsdichte hoch genug ist, um das Material zu verdampfen, bildet sich im Schmelzbad ein Stichloch oder Dampfhohlraum. Das Stichloch ermöglicht der Laserenergie, tief einzudringen, wodurch schmale und tiefe Schweißnähte mit einem hohen Aspektverhältnis entstehen. Stichlochschweißen eignet sich gut für dicke Materialien und Anwendungen, die starke Verbindungen erfordern.
- Abkühlung und Verfestigung nach dem Schweißen: Während sich der Laser entlang der Schweißnaht bewegt, verfestigt sich das Schmelzbad und bildet eine kontinuierliche Verbindung zwischen den Materialien. Die richtige Abkühlungsrate kann Defekte wie Risse oder Eigenspannungen verhindern und die gewünschten mechanischen Eigenschaften der Schweißnaht erreichen.
Laserschweißen bietet hohe Präzision, minimale Verzerrung und die Möglichkeit, saubere und robuste Verbindungen herzustellen. Allerdings müssen Faktoren wie Laserleistung, Strahlfokus, Schweißgeschwindigkeit und Materialeigenschaften sorgfältig kontrolliert werden, um die gewünschte Schweißdicke und -qualität zu erreichen, was das Laserschweißen zu einem komplexen und hochgradig anpassungsfähigen Prozess für die moderne Fertigung macht.
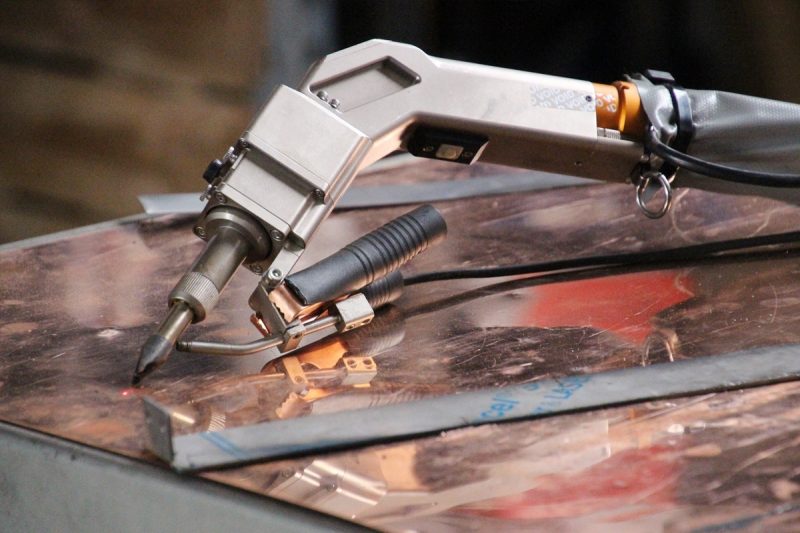
Anwendungen des Laserschweißens
Das Laserschweißen hat sich in zahlreichen Branchen zu einer Eckpfeilertechnologie entwickelt, da es präzise, schnell und in der Lage ist, qualitativ hochwertige, gleichmäßige Schweißnähte mit minimaler thermischer Verformung zu erzeugen. Angesichts der steigenden Fertigungsanforderungen bleibt das Laserschweißen aufgrund seiner Vielseitigkeit und Anpassungsfähigkeit weiterhin ein unverzichtbares Werkzeug.
- Automobilindustrie: Im Automobilsektor wird das Laserschweißen häufig zur Montage von Karosserien, Motorkomponenten, Getrieben, Abgassystemen und Batteriemodulen für Elektrofahrzeuge eingesetzt. Das Verfahren ermöglicht starke, hochpräzise Verbindungen bei gleichzeitiger Minimierung des Gewichts der Komponenten. Da das Laserschweißen auch unterschiedliche Materialien wie Aluminium und Stahl verbinden kann, eignet es sich besonders für leichte und energieeffiziente Fahrzeugkonstruktionen.
- Luft- und Raumfahrtindustrie: Das Laserschweißen ist in der Luft- und Raumfahrtindustrie von entscheidender Bedeutung, da es präzise und hochfeste Verbindungen für kritische Komponenten wie Turbinenschaufeln, Strukturrahmen und Kraftstofftanks herstellen kann. Die minimale Wärmeeinflusszone trägt dazu bei, die strukturelle Integrität leichter und hitzeempfindlicher Luft- und Raumfahrtmaterialien wie Titanlegierungen und Verbundwerkstoffe aufrechtzuerhalten. Die Präzision des Laserschweißens gewährleistet die Einhaltung strenger Sicherheits- und Leistungsstandards.
- Energie und Stromerzeugung: Im Energiesektor wird das Laserschweißen zur Herstellung von Komponenten für Windturbinen, Solarmodule, Öl- und Gasanlagen sowie Kernkraftwerke eingesetzt. Die Fähigkeit, starke, fehlerfreie Schweißnähte herzustellen, gewährleistet Zuverlässigkeit und Sicherheit in Umgebungen mit hohem Druck und hohen Temperaturen. Das Laserschweißen unterstützt auch die Herstellung von Wärmetauschern, Rohren und Hochdruckbehältern.
- Schiffbau und Marineindustrie: Die Schiffbauindustrie profitiert von der Fähigkeit des Laserschweißens, starke, korrosionsbeständige Schweißnähte zu erzeugen. Es wird zum Verbinden von Baustahlplatten, Rumpfkomponenten und Innenausstattungen verwendet. Das Verfahren reduziert das Gesamtgewicht von Schiffen, erhöht die Kraftstoffeffizienz und unterstützt komplexe Designs mit hoher Präzision.
- Unterhaltungselektronik und Haushaltsgeräte: Laserschweißen wird bei der Montage von Unterhaltungselektronik wie Smartphones, Tablets und Haushaltsgeräten eingesetzt. Es sorgt für zuverlässige und ästhetisch ansprechende Verbindungen in Metallgehäusen, Steckverbindern und Akkupacks. Der Prozess unterstützt automatisierte Hochgeschwindigkeitsproduktionslinien und verbessert Produktivität und Konsistenz.
- Lebensmittel- und Getränkeindustrie: Laserschweißen wird in der Lebensmittel- und Getränkeindustrie zur Herstellung von Edelstahlgeräten wie Rohren, Brauereianlagen und Abfüllmaschinen eingesetzt. Die hygienischen und nahtlosen Schweißnähte, die durch Laserschweißen entstehen, verhindern Bakterienwachstum und vereinfachen Reinigungsprozesse, wodurch das Verfahren ideal für Anwendungen in Lebensmittelqualität ist.
- Bauwesen und Architektur: Laserschweißen wird im Bauwesen und in der Architektur eingesetzt, um stabile und ästhetisch ansprechende Metallstrukturen zu schaffen. Es wird zur Herstellung von Strukturträgern, dekorativen Elementen, Fassaden und vielem mehr verwendet. Die Präzision und Geschwindigkeit des Verfahrens ermöglichen die Erstellung individueller Designs und komplexer Geometrien.
- Landwirtschaft und Schwermaschinen: Die Landwirtschaftsindustrie setzt bei der Herstellung robuster Komponenten für Maschinen und Geräte wie Pflüge, Traktoren und Lader auf Laserschweißen. Lasergeschweißte Verbindungen bieten hohe Festigkeit und Haltbarkeit, um rauen Betriebsbedingungen standzuhalten.
Die vielfältigen Anwendungen des Laserschweißens in verschiedenen Branchen unterstreichen seine Rolle als wichtiges Werkzeug für die moderne Fertigung und Technik. Die Fähigkeit, die Dicke und Qualität von Schweißnähten präzise zu steuern, stellt sicher, dass das Laserschweißen den hohen Anforderungen von Hochleistungsprodukten, komplexen Baugruppen und strengen gesetzlichen Normen gerecht wird.
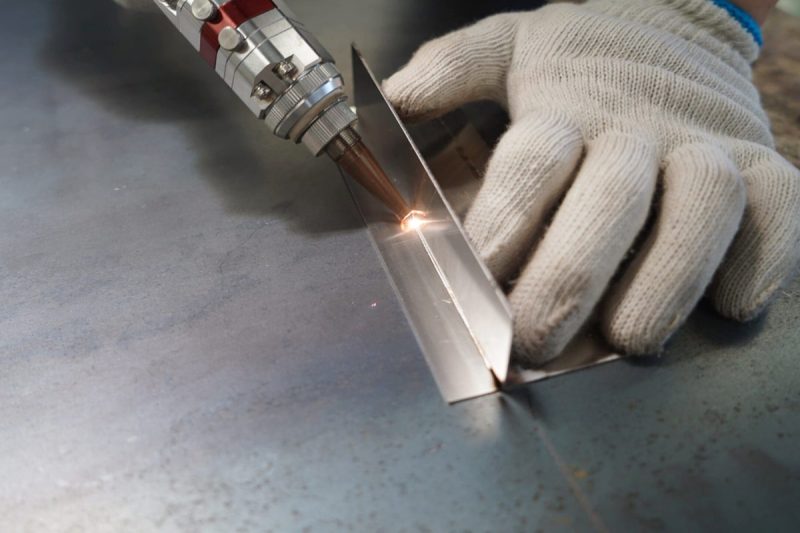
Faktoren, die die Dicke beim Laserschweißen beeinflussen
Das Erreichen der gewünschten Dicke beim Laserschweißen ist ein komplexer Prozess, der von zahlreichen Faktoren beeinflusst wird. Jeder dieser Faktoren wirkt sich direkt auf die Eindringtiefe, Qualität und Integrität der Schweißnaht aus. Das Verständnis dieser Variablen ermöglicht es Herstellern, den Laserschweißprozess auf optimale Dicke, Festigkeit und Präzision abzustimmen.
Laserleistung
- Einfluss auf die Schweißnahtdicke: Die Laserleistung ist einer der entscheidendsten Faktoren bei der Bestimmung der Schweißnahtdicke. Eine höhere Laserleistung erhöht die Energiezufuhr und ermöglicht eine tiefere Durchdringung und dickere Schweißnähte. Umgekehrt führen niedrigere Leistungsstufen zu flacheren Schweißnähten, die sich möglicherweise besser für dünne Materialien oder Anwendungen eignen, bei denen nur eine minimale Wärmezufuhr erforderlich ist.
- Optimierung: Durch die Anpassung der Laserleistung an die Materialdicke und die gewünschte Eindringtiefe wird eine effektive Energienutzung gewährleistet. Bei dickeren Materialien oder tiefen Schweißnähten muss ausreichend Leistung eingesetzt werden, um die erforderliche Eindringtiefe zu erreichen, ohne übermäßige Wärmeeinflusszonen (WEZ) zu verursachen.
Schweißgeschwindigkeit
- Einfluss auf die Schweißnahtdicke: Die Schweißgeschwindigkeit oder die Geschwindigkeit, mit der sich der Laser entlang der Verbindung bewegt, beeinflusst die Schweißnahtdicke erheblich. Bei einer langsameren Schweißgeschwindigkeit kann mehr Laserenergie vom Material absorbiert werden, was zu dickeren und tieferen Schweißnähten führt. Umgekehrt verringert eine höhere Geschwindigkeit die Wärmezufuhr, was zu flacheren Schweißnähten führt.
- Optimierung: Um die gewünschte Dicke zu erreichen, ist es wichtig, die Schweißgeschwindigkeit mit der Laserleistung abzustimmen. Zu langsame Geschwindigkeiten können zu Überhitzung und Defekten führen, während hohe Geschwindigkeiten zu unvollständiger Verschmelzung oder mangelnder Durchdringung führen können.
Fokusposition
- Einfluss auf die Schweißnahtdicke: Die Brennpunktposition des Laserstrahls beeinflusst, wo die Energie auf dem Werkstück konzentriert wird. Durch Fokussieren des Strahls genau auf oder knapp unter der Oberfläche des Materials kann die Eindringtiefe erhöht werden, was zu dickeren Schweißnähten führt. Eine Fehlausrichtung des Brennpunkts kann zu einer inkonsistenten oder unzureichenden Eindringtiefe führen.
- Optimierung: Durch Anpassen des Brennpunkts entsprechend der Materialstärke und des Schweißmodus (Leitungs- oder Schlüssellochschweißen) können Hersteller eine besser kontrollierte Schweißdicke erreichen. Eine genaue Fokussierung verbessert die Energiekonzentration und sorgt für eine gleichmäßige Tiefe.
Strahlqualität und -modus
- Auswirkungen auf die Schweißnahtdicke: Strahlqualität und -modus (TEM00, TEM01 usw.) beeinflussen, wie die Laserenergie über den Arbeitsbereich verteilt wird. Ein hochwertiger Singlemode-Strahl (TEM00) erzeugt einen fokussierteren und intensiveren Punkt und ermöglicht so eine tiefere Durchdringung und dickere Schweißnähte. Multimode-Strahlen hingegen können aufgrund der Energieverteilung zu breiteren, aber flacheren Schweißnähten führen.
- Optimierung: Die Auswahl eines Lasers mit der geeigneten Strahlqualität und dem richtigen Modus verbessert die Kontrolle über die Schweißnahtdicke. Für Anwendungen, die tiefe, schmale Schweißnähte erfordern, ist ein hochwertiger Singlemode-Laser ideal.
Materialeigenschaften
- Auswirkungen auf die Schweißnahtdicke: Unterschiedliche Materialien reagieren je nach Eigenschaften wie Wärmeleitfähigkeit, Schmelzpunkt und Reflexionsgrad unterschiedlich auf Laserenergie. Beispielsweise leiten Metalle mit hoher Wärmeleitfähigkeit wie Aluminium und Kupfer Wärme schnell ab, sodass eine höhere Laserleistung erforderlich ist, um die gewünschte Durchdringung zu erreichen. Materialien mit hohem Reflexionsgrad können auch die Energieabsorption verringern, was sich auf die Dicke auswirkt.
- Optimierung: Das Verständnis der spezifischen Materialeigenschaften hilft dabei, die Laserparameter anzupassen, um die Zieldicke zu erreichen. Reflektierende Materialien können beispielsweise von Oberflächenbehandlungen zur Verbesserung der Absorption profitieren oder erfordern eine höhere Leistung für eine effektive Durchdringung.
Vorwärmen
- Auswirkungen auf die Schweißnahtdicke: Durch Vorwärmen des Materials vor dem Schweißen können thermische Gradienten reduziert werden, was eine gleichmäßigere Durchdringung und dickere Schweißnähte ermöglicht. Außerdem wird dadurch das Risiko von Rissen bei Materialien minimiert, die anfällig für thermische Spannungen sind, wie z. B. Kohlenstoffstähle.
- Optimierung: Vorwärmen hilft dabei, eine gleichmäßige Dicke zu erreichen, insbesondere bei dickeren Abschnitten, bei denen eine schnelle Abkühlung sonst zu Defekten führen könnte. Der Grad des Vorwärmens sollte kontrolliert werden, um eine übermäßige Wärmezufuhr zu vermeiden.
Zustand der Oberfläche
- Einfluss auf die Schweißnahtdicke: Der Oberflächenzustand des Materials, einschließlich Sauberkeit und Oxidation, beeinflusst die Energieabsorption und -durchdringung. Verunreinigungen wie Öle, Oxide und Schmutz können die Absorption der Laserenergie verringern, was zu ungleichmäßiger Dicke und schwächeren Schweißnähten führt.
- Optimierung: Durch Reinigen und Vorbereiten der Oberfläche vor dem Schweißen wird sichergestellt, dass die Laserenergie effektiv absorbiert wird, was zu einer kontrollierten Dicke führt. Oberflächenbehandlungen wie Schleifen oder Sandstrahlen können die Schweißqualität ebenfalls verbessern.
Schutzgas und Hilfsgas
- Einfluss auf die Schweißdicke: Schutzgas (wie Argon, Helium oder Stickstoff) schützt das Schweißbad vor atmosphärischer Verunreinigung und kann die Schweißnahtdurchdringung und -dicke beeinflussen. Verschiedene Gase haben unterschiedliche thermische Eigenschaften, die sich auf die Wärmezufuhr und die Schweißeigenschaften auswirken. Hilfsgase, die häufig beim Schneiden verwendet werden, können ebenfalls zur Aufrechterhaltung eines stabilen Schweißbads beitragen.
- Optimierung: Die Wahl des geeigneten Schutzgases verbessert die Schweißnahtdurchdringung. Helium beispielsweise kann aufgrund seiner hohen Wärmeleitfähigkeit die Durchdringung erhöhen und so die Schweißnahtdicke beeinflussen. Durch die Anpassung der Gasdurchflussraten wird eine ausreichende Abschirmung gewährleistet, ohne Turbulenzen oder Defekte zu verursachen.
Schweißmodus (Leitung VS. Schlüsselloch)
- Auswirkungen auf die Schweißnahtdicke: Das Laserschweißen kann im Leitungs- oder im Keyhole-Modus erfolgen, wobei sich beide Verfahren auf die erzielbare Schweißnahtdicke auswirken. Beim Leitungsschweißen entstehen breite und flache Schweißnähte, die sich für Anwendungen auf Oberflächenebene eignen, während beim Keyhole-Schweißen tiefe, schmale Schweißnähte entstehen, die sich ideal für dickere Materialien eignen.
- Optimierung: Durch Auswahl des geeigneten Schweißmodus ist eine präzise Kontrolle der Dicke möglich. Der Leitungsmodus wird verwendet, wenn ästhetische Oberflächenschweißnähte erforderlich sind, während der Schlüssellochmodus ideal für Anwendungen ist, die eine größere Eindringtiefe erfordern.
Gelenkkonfiguration
- Auswirkungen auf die Schweißdicke: Die Konfiguration der Verbindung, z. B. Stumpf-, Überlapp- oder T-Verbindung, beeinflusst, wie die Laserenergie mit den Materialien interagiert und bestimmt die erreichbare Dicke. Beispielsweise ermöglichen Stumpfverbindungen ein vollständiges Durchschweißen, während Überlappverbindungen für eine gleichwertige Tiefe möglicherweise mehr Laserleistung erfordern.
- Optimierung: Die Wahl der richtigen Verbindungskonfiguration auf Grundlage der Materialstärke und der Anwendungsanforderungen gewährleistet eine effektive Energieverteilung und Schweißnahtstärke.
Laserwellenlänge
- Einfluss auf die Schweißnahtdicke: Die Wellenlänge des Lasers beeinflusst, wie effektiv das Material Energie absorbiert. Beispielsweise werden kürzere Wellenlängen, wie die von Faserlasern, von Metallen besser absorbiert als längere Wellenlängen von CO2-Lasern, was sich auf die Eindringtiefe und die Schweißnahtdicke auswirkt.
- Optimierung: Durch die Auswahl eines Lasers mit einer Wellenlänge, die den Absorptionseigenschaften des Materials entspricht, wird eine effiziente Energienutzung gewährleistet, wodurch eine optimale Schweißnahtdicke erreicht wird.
Vor- und Nachbearbeitung
- Vorbehandlung vor dem Schweißen: Oberflächenvorbereitung, Reinigung und Ausrichtung vor dem Schweißen verbessern die Energieabsorption des Lasers und führen zu einer gleichmäßigen Dicke. Verunreinigungen oder Fehlausrichtungen können zu Defekten oder ungleichmäßiger Durchdringung führen.
- Nachbehandlung nach dem Schweißen: Nachbehandlungen wie Wärmebehandlung oder kontrollierte Abkühlung beeinflussen die Schweißstruktur und -stabilität. Kontrollierte Abkühlungsraten helfen dabei, eine gleichmäßige Dicke aufrechtzuerhalten, indem sie Restspannungen oder Verformungen verhindern.
- Optimierung: Die richtige Vor- und Nachbearbeitung des Schweißens verbessert die Schweißqualität und ermöglicht eine gleichbleibende Schweißdicke und bessere mechanische Eigenschaften.
Jeder dieser Faktoren spielt eine entscheidende Rolle bei der Bestimmung der Dicke und Qualität von Laserschweißnähten. Durch sorgfältiges Anpassen und Optimieren jeder Variablen können Hersteller die gewünschten Schweißdicken erzielen und sicherstellen, dass das Laserschweißen die strengen Anforderungen verschiedener industrieller Anwendungen erfüllt.
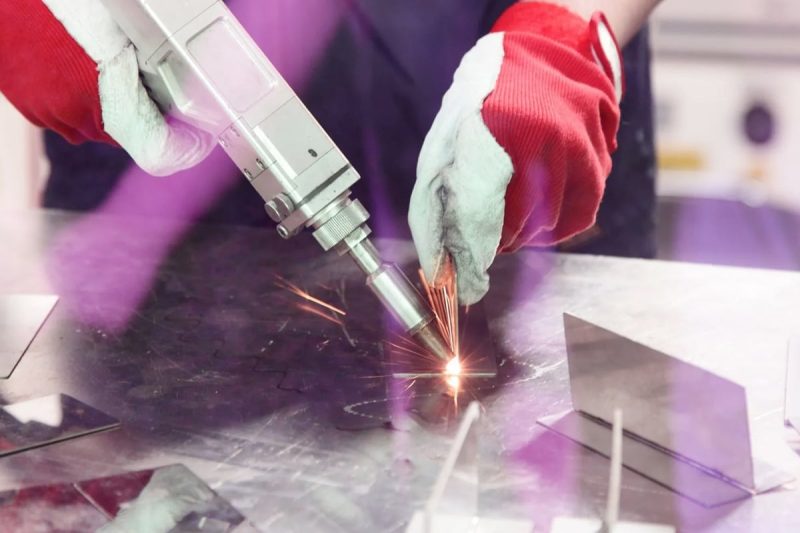
Optimierung der Schweißnahtdicke
Die Optimierung der Schweißdicke beim Laserschweißen erfordert das sorgfältige Ausbalancieren mehrerer Prozessparameter und den Einsatz von Strategien zur präzisen Steuerung. Das Erreichen der gewünschten Schweißdicke ist entscheidend, um die Schweißfestigkeit sicherzustellen, Defekte zu minimieren und die Konstruktionsspezifikationen zu erfüllen.
Anpassung der Prozessparameter
Anpassung der Laserleistung
- Auswirkungen: Die Laserleistung wirkt sich direkt auf die Eindringtiefe und die Schweißnahtdicke aus. Eine höhere Leistung führt dem Schweißbad mehr Energie zu, wodurch tiefere und dickere Schweißnähte möglich sind. Eine geringere Leistung führt hingegen zu einer geringeren Eindringtiefe.
- Optimierungsstrategie: Um eine optimale Schweißnahtdicke zu erreichen, sollte die Laserleistung sorgfältig auf Grundlage der Materialeigenschaften, der Fugenkonfiguration und der Dickenanforderungen angepasst werden. Übermäßige Leistung kann zu Defekten wie Porosität oder übermäßigem Schmelzen führen. Daher ist es wichtig, ein Gleichgewicht zu finden, das die Durchdringung maximiert und gleichzeitig unerwünschte Effekte minimiert.
Regelung der Schweißgeschwindigkeit
- Auswirkungen: Die Schweißgeschwindigkeit bestimmt, wie lange der Laser mit dem Material interagiert. Niedrigere Geschwindigkeiten erhöhen die Energieabsorption, was zu tieferen und dickeren Schweißnähten führt, während höhere Geschwindigkeiten die Wärmezufuhr verringern und dünnere Schweißnähte ergeben.
- Optimierungsstrategie: Durch Anpassen der Schweißgeschwindigkeit in Verbindung mit der Laserleistung wird eine gleichmäßige Dicke gewährleistet. Bei dickeren Materialien oder tieferer Durchdringung können langsamere Geschwindigkeiten verwendet werden, diese müssen jedoch kontrolliert werden, um Überhitzung oder übermäßige Wärmeeinflusszonen zu vermeiden.
Anpassung der Brennweite
- Auswirkungen: Die Position des Laserfokus im Verhältnis zur Materialoberfläche beeinflusst die Energiekonzentration. Ein fokussierter Strahl auf oder knapp unter der Oberfläche maximiert die Durchdringung und erhöht die Schweißdicke, während eine falsch ausgerichtete Fokusposition zu inkonsistenten Ergebnissen führen kann.
- Optimierungsstrategie: Durch die präzise Einstellung des Brennpunkts wird eine gleichmäßige Energiezufuhr zum Werkstück gewährleistet, wodurch die Schweißnahtdicke verbessert wird. Um die gewünschten Ergebnisse zu erzielen, müssen bei unterschiedlichen Materialien oder Verbindungskonfigurationen möglicherweise Anpassungen der Brennpunktposition vorgenommen werden.
Strahlqualität und Modusoptimierung
- Auswirkungen: Hochwertige Laserstrahlen mit stabiler Modusstruktur bieten eine bessere Energiekonzentration, was zu tieferen und kontrollierteren Schweißnähten führt.
- Optimierungsstrategie: Durch die Verwendung hochwertiger Strahlen und die Auswahl des geeigneten Strahlmodus lässt sich eine präzise und gleichmäßige Schweißnahtdicke erzielen. Die Aufrechterhaltung einer stabilen Laserleistung und Strahlqualität durch regelmäßige Gerätewartung ist von entscheidender Bedeutung.
Schutz- und Hilfsgasfluss
- Auswirkungen: Art und Durchflussrate des Schutzgases beeinflussen die Stabilität und Durchdringung des Schweißbades. Eine ordnungsgemäße Abschirmung schützt vor Verunreinigungen und kann die Energieabsorption verbessern, während Hilfsgase dabei helfen, eine stabile Schweißumgebung aufrechtzuerhalten.
- Optimierungsstrategie: Auswahl des geeigneten Schutzgases (z. B. Argon, Helium oder Stickstoff) und Anpassung der Durchflussraten, um optimale Schweißdurchdringung und -dicke sicherzustellen. Das Schutzgas muss auf das Material und die Schweißbedingungen abgestimmt sein, um seine Wirksamkeit zu maximieren.
Vorheiz- und Abkühlraten
- Auswirkungen: Vorwärmen von Materialien verringert den Wärmegradienten und verbessert die Energieabsorption und -durchdringung. Die Abkühlgeschwindigkeit beeinflusst den Erstarrungsprozess und die Schweißstruktur.
- Optimierungsstrategie: Durch kontrolliertes Vorwärmen und Abkühlen nach dem Schweißen wird eine gleichmäßige Dicke gewährleistet und das Risiko von Defekten wie Rissen oder Verwerfungen minimiert.
Strategien zur Kontrolle
Prozessabbildung und -simulation
Die Entwicklung einer Prozesskarte, die Laserparameter (z. B. Leistung, Geschwindigkeit, Brennpunkt) mit der Schweißnahtdicke korreliert, hilft bei der Ermittlung optimaler Einstellungen für unterschiedliche Materialien und Verbindungskonfigurationen. Schweißsimulationssoftware kann außerdem dabei helfen, die Auswirkungen von Parameteränderungen auf die Schweißnahtdicke vorherzusagen, wodurch kostspielige Versuche und Irrtümer vermieden werden.
Echtzeit-Überwachungs- und Feedbacksysteme
Der Einsatz von Sensoren und Überwachungssystemen beim Laserschweißen liefert Echtzeitdaten zu Schweißdurchdringung, -dicke und -qualität. Automatisierte Rückkopplungssysteme können Parameter als Reaktion auf Änderungen in der Schweißumgebung anpassen und so eine gleichbleibende Schweißdicke gewährleisten.
Adaptive Steuerungssysteme
Moderne Laserschweißsysteme können Laserleistung, Geschwindigkeit und andere Parameter automatisch anhand von Echtzeit-Feedback anpassen. Diese Funktion minimiert die Variabilität und gewährleistet eine gleichmäßige Schweißnahtdicke bei komplexen Geometrien oder unterschiedlichen Materialbedingungen.
Oberflächenvorbereitung und Materialaufbereitung
Eine ordnungsgemäße Oberflächenvorbereitung, einschließlich Reinigung und Konditionierung, verbessert die Energieabsorption und die Schweißkonsistenz. Strategien wie Schleifen, Sandstrahlen oder das Auftragen von Oberflächenbeschichtungen verbessern die Wechselwirkung der Laserenergie und führen zu einer gleichmäßigeren Dicke.
Optimierung der Verbindungskonstruktion und Passung
Durch Minimieren von Lücken und Sicherstellen einer präzisen Ausrichtung der Komponenten werden die Energieübertragung und die Konsistenz der Schweißdicke verbessert. Durch die Verwendung geeigneter Klemm- und Fixiertechniken können optimale Verbindungsbedingungen während des Schweißens aufrechterhalten werden.
Prozessvalidierung und -prüfung
Durch regelmäßige Tests und Validierungen von Laserschweißprozessen können optimale Parametereinstellungen für bestimmte Anwendungen ermittelt werden. Durch kontinuierliche Prozessverbesserung wird sichergestellt, dass die Schweißdicke innerhalb der gewünschten Toleranzen bleibt.
Durch die Anpassung wichtiger Prozessparameter und die Implementierung effektiver Kontrollstrategien können Hersteller eine optimale Schweißnahtdicke erzielen, die Qualität der Verbindung verbessern und die Gesamteffizienz ihrer Laserschweißvorgänge steigern. Diese Praktiken stellen sicher, dass das Laserschweißen eine zuverlässige und vielseitige Lösung für verschiedene industrielle Anwendungen bleibt.
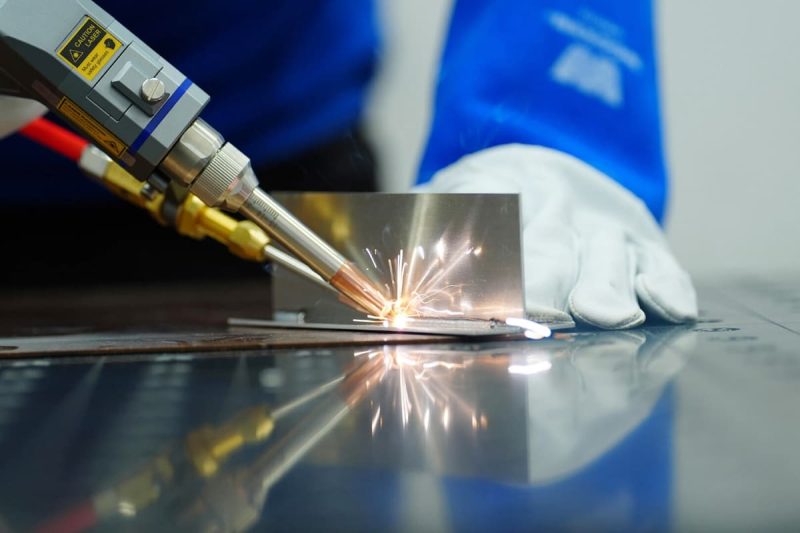
Herausforderungen und Überlegungen
Die Optimierung der Dicke beim Laserschweißen ist nicht ohne Herausforderungen. Verschiedene Faktoren können die Konsistenz, Qualität und Leistung der Schweißnaht beeinflussen. Durch das Verständnis allgemeiner Probleme und die Umsetzung robuster Qualitätskontrollmaßnahmen können Hersteller ihre Prozesse verbessern und zuverlässige Schweißnähte gewährleisten.
Häufige Probleme
Inkonsistente Eindringtiefe
- Herausforderung: Schwankungen bei Laserleistung, Strahlfokus, Materialstärke oder Fugenausrichtung können zu uneinheitlichen Eindringtiefen führen, die sich auf die Schweißnahtdicke auswirken. Diese Uneinheitlichkeit kann zu schwachen Fugen, mangelnder Verschmelzung oder Strukturdefekten führen und so die Integrität der Schweißnaht beeinträchtigen.
- Überlegung: Eine regelmäßige Kalibrierung der Laserquelle, die Überwachung des Strahlfokus und eine präzise Kontrolle der Schweißparameter sind für eine gleichmäßige Durchdringung und Schweißnahtdicke unerlässlich.
Wärmeeinflusszonen (WEZ)
- Herausforderung: Übermäßiger Wärmeeintrag kann eine große Wärmeeinflusszone erzeugen, die die Mikrostruktur des Materials verändert und die mechanischen Eigenschaften in der Nähe der Schweißnaht verringert. Dies kann zu Verformungen, Eigenspannungen oder Rissbildung führen, insbesondere bei Materialien, die empfindlich auf thermische Spannungen reagieren.
- Überlegung: Durch die Optimierung der Laserleistung und Schweißgeschwindigkeit sowie die Verwendung geeigneter Schutzgase können Wärmeeinflusszonen minimiert und eine gleichmäßige Schweißnahtdicke aufrechterhalten werden.
Porosität und Gaseinschluss
- Herausforderung: Eingeschlossene Gase im Schweißbad können Porosität verursachen, die die mechanische Festigkeit der Schweißnaht mindert und zu Unregelmäßigkeiten in der Schweißnahtdicke führt. Porosität kann durch Verunreinigungen, unzureichendes Schutzgas oder falsche Prozesseinstellungen entstehen.
- Überlegung: Das Reinigen der Oberfläche vor dem Schweißen, die Optimierung des Schutzgasflusses und die Reduzierung von Verunreinigungen können die Porosität minimieren. Durch Echtzeitüberwachung können Porositätsprobleme frühzeitig im Prozess erkannt und behoben werden.
Reflektivität von Materialien
- Herausforderung: Hochreflektierende Materialien wie Aluminium und Kupfer reflektieren einen erheblichen Teil der Laserenergie, was zu Schwierigkeiten bei der Erzielung einer ausreichenden Durchdringung und einer gleichmäßigen Dicke führt. Bei diesen Materialien sind möglicherweise besondere Überlegungen erforderlich, um die Energieabsorption zu verbessern.
- Überlegung: Oberflächenbehandlungen wie Beschichtungen oder Strukturierung sowie die Verwendung von Lasern mit kürzeren Wellenlängen können die Energieabsorption und Konsistenz reflektierender Materialien verbessern.
Gelenkfehlstellungen und -lücken
- Herausforderung: Falsch ausgerichtete Verbindungen oder Lücken zwischen den Komponenten verringern die Fähigkeit des Lasers, eine gleichmäßige Durchdringung zu erreichen. Dies kann zu Unterschnitten, unvollständiger Verschmelzung und unterschiedlicher Schweißdicke führen.
- Überlegung: Die richtige Vorrichtung, Ausrichtung und Passungskontrolle gewährleisten gleichbleibende Verbindungsbedingungen und verringern die Wahrscheinlichkeit von Defekten.
Thermische Verformung und Spannung
- Herausforderung: Ungleichmäßige Wärmeverteilung und schnelles Abkühlen können zu thermischem Verzug, Eigenspannung und Verformungen führen, die sich auf die Schweißdicke und die Integrität der Verbindung auswirken können.
- Überlegung: Vorwärmen, kontrolliertes Abkühlen und optimierte Schweißgeschwindigkeiten tragen dazu bei, thermische Spannungen zu reduzieren und gleichmäßige Schweißabmessungen aufrechtzuerhalten.
Maßnahmen zur Qualitätskontrolle
Prozessüberwachung in Echtzeit
- Messen: Die Implementierung von Echtzeit-Überwachungssystemen liefert Feedback zu wichtigen Parametern wie Laserleistung, Schweißgeschwindigkeit und Eindringtiefe. Dies ermöglicht sofortige Anpassungen, reduziert Abweichungen in der Schweißdicke und verbessert die Gesamtkonsistenz.
- Überlegung: Optische Sensoren, Temperaturmonitore und Laser-Feedbacksysteme sind Beispiele für Werkzeuge, die zur Aufrechterhaltung der Prozessstabilität eingesetzt werden können.
Oberflächenvorbereitung vor dem Schweißen
- Maßnahme: Um eine gleichbleibende Energieabsorption und Schweißqualität zu erreichen, ist es wichtig, sicherzustellen, dass die Werkstückoberfläche sauber, frei von Verunreinigungen und richtig vorbereitet ist.
- Überlegung: Oberflächenbehandlungen wie Schleifen, Entfetten oder das Aufbringen von Beschichtungen tragen dazu bei, Verunreinigungen zu minimieren, die die Energieübertragung beeinträchtigen könnten.
Kalibrierung und Wartung der Ausrüstung
- Maßnahme: Regelmäßige Kalibrierung und Wartung von Laserquellen, Optiken und anderen Systemkomponenten gewährleisten eine stabile Strahlqualität, Leistungsabgabe und Präzision.
- Überlegung: Regelmäßige Kontrollen verhindern Leistungseinbußen, die sich auf die Schweißdicke und die Gesamtqualität auswirken könnten.
Zerstörungsfreie Prüfung (NDT)
- Messen: Techniken wie Ultraschallprüfung, Röntgen und Sichtprüfung helfen dabei, die Schweißqualität zu beurteilen, ohne das Teil zu beschädigen. NDT-Methoden erkennen Porosität, Risse, unvollständige Verschmelzung und andere Probleme.
- Überlegung: Die Implementierung von NDT-Verfahren hilft dabei, die Schweißkonsistenz und die Einhaltung der Spezifikationen zu überprüfen und verringert so die Wahrscheinlichkeit von Produktausfällen.
Verwendung von Schutzgas und Hilfsgas
- Maßnahme: Die richtige Auswahl und Durchflusskontrolle der Schutzgase schützt das Schweißbad vor atmosphärischen Verunreinigungen und beeinflusst die Schweißdurchdringung.
- Überlegung: Durch Anpassen der Art und Durchflussrate der Schutzgase können Oxidation, Porosität und Inkonsistenzen in der Schweißdicke minimiert werden.
Schweißprozessoptimierung
- Maßnahme: Durch die Entwicklung einer Prozesskarte, die die Laserparameter (z. B. Leistung, Geschwindigkeit, Brennpunkt) mit der Schweißnahtdicke korreliert, werden optimale Einstellungen für unterschiedliche Materialien und Verbindungskonfigurationen gewährleistet.
- Überlegung: Eine kontinuierliche Prozessverbesserung, unterstützt durch Tests und Simulation, verbessert die Kontrolle über die Schweißdicke und verringert die Variabilität.
Schulung und qualifiziertes Bedienpersonal
- Maßnahme: Erfahrene Bediener mit umfassenden Kenntnissen der Parameter, Materialien und Techniken des Laserschweißens tragen wesentlich zur Aufrechterhaltung der Konsistenz und Qualität der Schweißnähte bei.
- Überlegung: Laufende Schulungen und die Weiterentwicklung ihrer Fähigkeiten ermöglichen es den Bedienern, Probleme schnell zu erkennen und zu lösen und so die Prozesskontrolle zu verbessern.
Durch die Bewältigung gängiger Herausforderungen und die Implementierung robuster Qualitätskontrollmaßnahmen können Hersteller Laserschweißprozesse optimieren, um eine gleichmäßige Schweißnahtdicke, hohe strukturelle Integrität und überragende Qualität zu erzielen.

Zusammenfassung
Die Dicke beim Laserschweißen ist ein entscheidender Faktor, der die Festigkeit, Präzision und Gesamtleistung von Schweißverbindungen beeinflusst. Um die optimale Dicke zu erreichen, ist ein tiefes Verständnis verschiedener Faktoren erforderlich, darunter Laserleistung, Schweißgeschwindigkeit, Strahlqualität, Brennpunktposition, Materialeigenschaften und Schutzgase. Durch die Anpassung dieser Parameter wird eine präzise Energiezufuhr und eine gleichmäßige Durchdringung gewährleistet, was zu hochwertigen, fehlerfreien Schweißnähten führt. Behandlungen vor und nach dem Schweißen sowie die Konfiguration der Verbindung und die Oberflächenbedingungen wirken sich zusätzlich auf das Schweißergebnis aus. Durch die Bewältigung gängiger Herausforderungen wie inkonsistente Durchdringung, Porosität und thermische Verformung können Hersteller die Schweißdicke optimieren und die allgemeine Prozesszuverlässigkeit verbessern. Die Implementierung robuster Qualitätskontrollmaßnahmen, einschließlich Echtzeitüberwachung, ordnungsgemäßer Gerätekalibrierung und Schulung der Bediener, gewährleistet konsistente und zuverlässige Ergebnisse. Mit diesen Erkenntnissen bleibt das Laserschweißen eine unverzichtbare Lösung für Branchen, die Präzision, Festigkeit und hohe Produktivität verlangen.
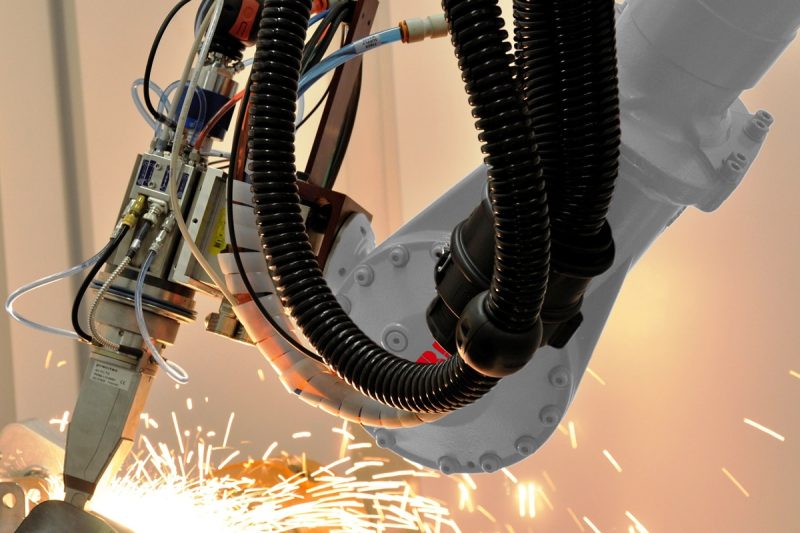
Holen Sie sich Laserschweißlösungen
Die Optimierung der Dicke beim Laserschweißen ist für das Erreichen präziser, starker und zuverlässiger Schweißnähte in verschiedenen Anwendungen von entscheidender Bedeutung. Bei AccTek Laser bieten wir fortschrittliche Laserschweißlösungen, die auf die besonderen Anforderungen Ihrer Branche zugeschnitten sind. Unsere hochmodernen Laserschweißsysteme bieten außergewöhnliche Kontrolle über wichtige Parameter wie Laserleistung, Strahlfokus und Schweißgeschwindigkeit und gewährleisten so eine gleichmäßige Durchdringung und qualitativ hochwertige Ergebnisse. Unser Expertenteam unterstützt Sie gerne bei der Auswahl der richtigen Laserschweißmaschine basierend auf Ihrem Materialtyp, der Verbindungskonfiguration und den spezifischen Anwendungsanforderungen.
Egal, ob Sie dünne, empfindliche Komponenten oder dicke Strukturteile schweißen müssen, die Lösungen von AccTek Laser bieten höchste Präzision, minimale Wärmeeinflusszonen und unübertroffene Effizienz. Mit unserer umfassenden Unterstützung, einschließlich Beratung vor dem Verkauf, Systemintegration, Schulung und Wartung, können Sie Ihren Schweißprozess optimieren und eine beispiellose Leistung erzielen. Kontaktiere uns Entdecken Sie noch heute die perfekte Laserschweißlösung für Ihre Produktionsanforderungen.
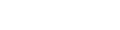
Kontaktinformationen
- [email protected]
- [email protected]
- +86-19963414011
- Nr. 3 Zone A, Industriegebiet Lunzhen, Stadt Yucheng, Provinz Shandong.
Holen Sie sich Laserlösungen