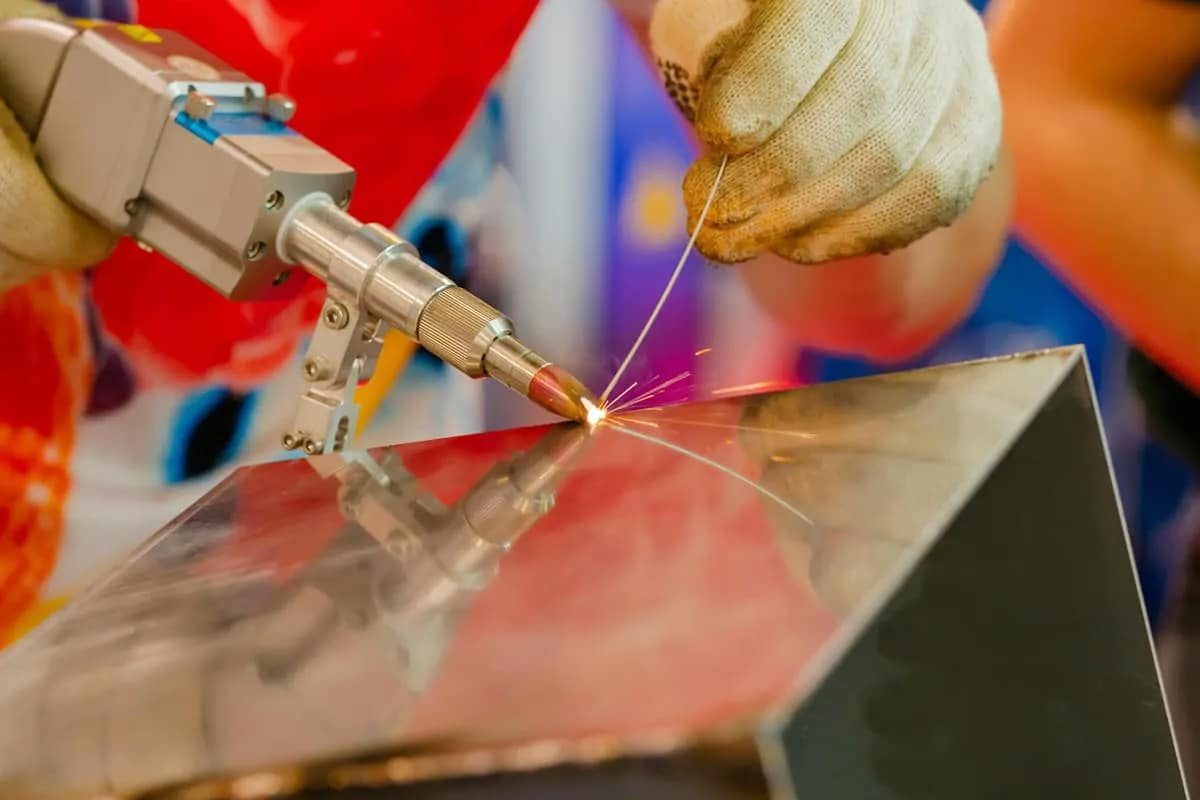
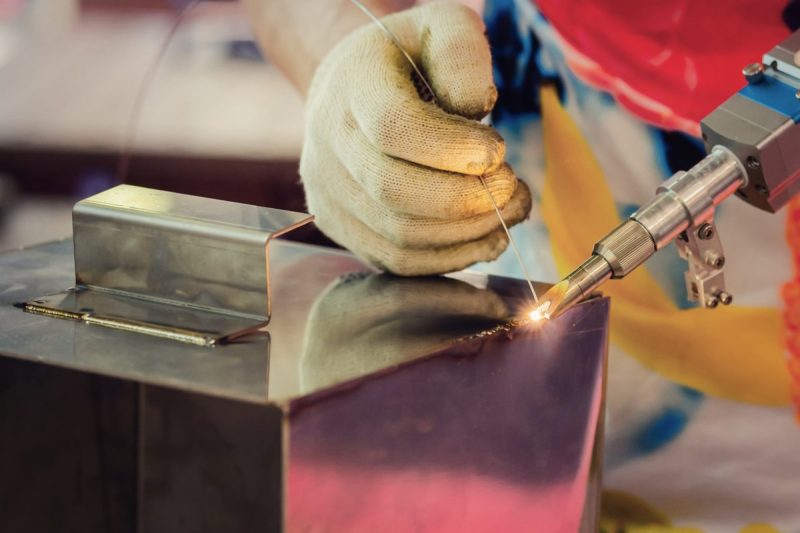
Laserparameter
Laserleistung
Die Laserleistung ist ein grundlegender Parameter beim Laserschweißen und bestimmt die Energiemenge, die an den Schweißbereich abgegeben wird. Die Leistungseinstellung beeinflusst die Schweißgeschwindigkeit und die Eindringtiefe.
- Hohe Leistung: Die Verwendung einer hohen Laserleistung erhöht die Schweißgeschwindigkeit und die Eindringtiefe und ermöglicht das Schweißen dickerer Materialien. Dies ist besonders nützlich für Anwendungen, die tiefe Schweißnähte oder eine hohe Produktivität erfordern. Eine zu hohe Leistung kann jedoch zu Überhitzung, übermäßigem Schmelzen und Defekten wie Spritzern und Porosität führen.
- Geringe Leistung: Niedrigere Laserleistungen eignen sich für dünnere Materialien und Anwendungen, die hohe Präzision erfordern, wie z. B. Mikroschweißen. Eine unzureichende Leistung kann jedoch aufgrund unvollständiger Verschmelzung oder unzureichender Durchdringung zu schwachen Schweißnähten führen.
- Optimierung: Um eine optimale Laserleistung zu erreichen, müssen die erforderlichen Durchdringungs- und Geschwindigkeitsanforderungen mit den Defektrisiken in Einklang gebracht werden. Dies erfordert eine sorgfältige Kalibrierung basierend auf Materialart, Dicke und spezifischen Schweißanforderungen.
Wellenlänge
Die Wellenlänge eines Lasers beeinflusst, wie gut das zu schweißende Material die Laserenergie absorbiert. Unterschiedliche Materialien haben bei unterschiedlichen Wellenlängen unterschiedliche Absorptionseigenschaften.
- Gängige Wellenlängen: Typische Wellenlängen beim Laserschweißen sind Infrarot (IR), sichtbares Licht und Ultraviolett (UV). Jede Wellenlänge hat ihre Vorteile, je nach Material und Anwendung.
- Infrarotlaser (IR): IR-Laser wie CO2- und Faserlaser werden häufig zum Schweißen von Metallen verwendet und eignen sich gut für Materialien mit hoher Absorption im Infrarotspektrum.
- Sichtbare und UV-Laser: Diese Wellenlängen werden von Nichtmetallen und einigen reflektierenden Metallen leichter absorbiert, was sie für Anwendungen mit Kunststoffen und Keramik nützlich macht.
- Materialspezifische Überlegungen: Materialien wie Aluminium und Kupfer, die im Infrarotbereich stark reflektieren, erfordern möglicherweise Laser mit Wellenlängen, die von diesen Metallen leichter absorbiert werden. Spezielle Beschichtungen oder Laserquellen mit bestimmten Wellenlängen können die Absorption und Schweißeffizienz verbessern.
Pulsdauer und Frequenz
Pulsdauer und -frequenz sind entscheidende Parameter beim gepulsten Laserschweißen, bei dem der Laser mit kurzen Impulsen statt mit einer kontinuierlichen Welle arbeitet.
- Pulsdauer: Die Länge jedes Laserpulses kann die thermischen Eigenschaften der Schweißnaht erheblich beeinflussen. Kürzere Pulse liefern Energie in kurzen, intensiven Stößen, wodurch die Wärmeeinflusszone (WEZ) minimiert und die thermische Verformung verringert wird. Längere Pulsdauern liefern mehr Energie, können aber die WEZ und das Risiko thermischer Schäden erhöhen.
- Pulsfrequenz: Die Pulsfrequenz oder die Anzahl der Pulse pro Sekunde beeinflusst die Gesamtenergieabgabe und die Schweißgeschwindigkeit. Höhere Frequenzen können die Schweißgeschwindigkeit erhöhen, können aber auch das Risiko einer kumulativen Hitzeentwicklung erhöhen, die Defekte verursachen kann.
- Optimierung: Die Kombination aus Pulsdauer und Frequenz muss basierend auf den Materialeigenschaften und den gewünschten Schweißeigenschaften optimiert werden. Durch die Feinabstimmung dieser Parameter lässt sich ein Gleichgewicht zwischen Schweißgeschwindigkeit, Eindringtiefe und thermischer Wirkung erreichen.
Strahlqualität
Die Qualität eines Laserstrahls wird durch Parameter wie Modusstruktur und Strahlprofil bestimmt, die sich direkt auf die Schweißeffizienz auswirken.
- Strahlmodus: Der Modus eines Laserstrahls (z. B. TEM00) bestimmt dessen Intensitätsverteilung. Eine hochwertige Modusstruktur sorgt für eine konzentrierte und gleichmäßige Energieabgabe, was zu gleichmäßigem und präzisem Schweißen führt.
- Strahlprofil: Ein gleichmäßiges und gut definiertes Strahlprofil minimiert Energieverluste und gewährleistet eine maximale Energiezufuhr zum Schweißbereich. Eine schlechte Strahlqualität (gekennzeichnet durch ein verzerrtes oder unregelmäßiges Profil) führt zu ungleichmäßiger Erwärmung und Schweißfehlern.
- Machbarkeit: Eine hohe Strahlqualität ermöglicht eine bessere Fokussierung, sodass der Laser kleinere Punktgrößen für Anwendungen erreichen kann, die hohe Präzision und feine Details erfordern.
Fokusposition
Die Position des Laserbrennpunkts im Verhältnis zur Materialoberfläche ist ein entscheidender Parameter, der sich auf die Schweißeffizienz und -qualität auswirkt.
- Richtiger Fokus: Die richtige Fokussierung des Laserstrahls auf die Schweißstelle sorgt für maximale Energiedichte und effizientes Aufschmelzen des Materials. Die optimale Fokusposition hängt von der Materialdicke und den gewünschten Schweißeigenschaften ab. Beim Tiefschweißen wird der Fokuspunkt meist knapp unterhalb der Materialoberfläche gesetzt.
- Brennweite: Die Brennweite der Laseroptik bestimmt die Brennweite und Brennweite. Kurze Brennweiten erzeugen kleinere Punktgrößen und höhere Energiedichten für feine Schweißaufgaben. Längere Brennweiten bieten größere Brennweiten, die beim Schweißen dickerer Materialien von Vorteil sind.
- Fokustoleranz: Die Beibehaltung einer konstanten Fokusposition kann zu einer gleichmäßigen Schweißqualität beitragen. Abweichungen in der Fokusposition können zu inkonsistenter Durchdringung, unvollständiger Verschmelzung und Defekten führen. Automatisierte Systeme mit Fokusanpassung in Echtzeit können dabei helfen, während des Schweißvorgangs einen optimalen Fokus beizubehalten.
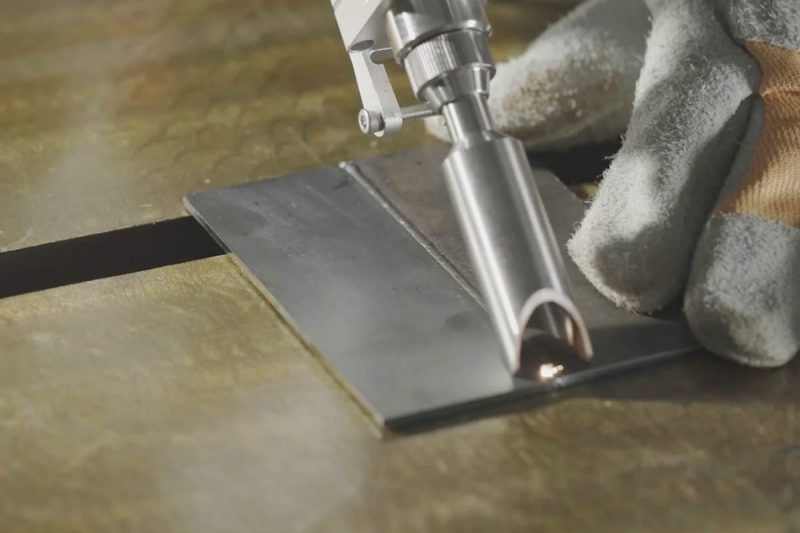
Materialeigenschaften
Materialtyp
Die Art des zu schweißenden Materials ist der wichtigste Faktor für die Effizienz des Laserschweißens. Verschiedene Materialien absorbieren und leiten Laserenergie auf unterschiedliche Weise, was sich auf die Schweißqualität und die Prozessparameter auswirkt.
- Metalle: Zu den häufig geschweißten Metallen gehören Stahl, Aluminium, Titan und Kupfer. Jedes Metall hat unterschiedliche Eigenschaften:
- Stahl: Er lässt sich aufgrund seiner guten Absorption von Laserenergie im Allgemeinen gut mit einem Laser schweißen. Verschiedene Stahlsorten, darunter Kohlenstoffstahl, Edelstahl und legierter Stahl, erfordern möglicherweise unterschiedliche Lasereinstellungen.
- Aluminium: Aluminium ist für seine hohe Reflektivität und Wärmeleitfähigkeit bekannt und das Schweißen von Aluminium mit einem Laser kann eine Herausforderung sein. Spezielle Wellenlängen oder Beschichtungen können die Absorption verbessern.
- Titan: Titan kann aufgrund seiner moderaten Reflektivität und thermischen Eigenschaften effektiv mit einem Laser geschweißt werden. Es wird häufig in der Luft- und Raumfahrt sowie in medizinischen Anwendungen eingesetzt.
- Kupfer: Die hohe Reflektivität und Wärmeleitfähigkeit von Kupfer erschweren das Schweißen mit einem herkömmlichen Lasersystem. Um die Effizienz zu verbessern, werden häufig Faserlaser mit bestimmten Wellenlängen verwendet.
- Nichtmetalle: Auch Materialien wie Kunststoffe, Keramik und Verbundwerkstoffe können lasergeschweißt werden. Jedes Nichtmetall erfordert spezifische Laserparameter für effizientes Schweißen:
- Kunststoffe: Kunststoffe absorbieren Laserenergie im Allgemeinen gut, ihre thermischen Eigenschaften erfordern jedoch eine sorgfältige Kontrolle der Schweißparameter, um ein Verbrennen oder Schmelzen zu vermeiden.
- Keramik: Keramik ist spröde und kann unter thermischer Belastung reißen. Beim Laserschweißen von Keramik ist im Allgemeinen eine Vorwärmung und die Verwendung von Lasern mit bestimmten Wellenlängen erforderlich, um die Spannung zu reduzieren.
- Verbundwerkstoffe: Verbundwerkstoffe kombinieren verschiedene Materialien und erfordern eine sorgfältige Anpassung der Parameter, um eine einheitliche Schweißqualität über verschiedene Komponenten hinweg zu gewährleisten.
Dicke
Die Materialdicke ist ein entscheidender Faktor für die Effizienz des Laserschweißens. Sie beeinflusst die erforderliche Laserleistung, die Schweißgeschwindigkeit und die allgemeine Prozessstabilität.
- Dünne Materialien: Dünne Materialien erfordern eine geringere Laserleistung und höhere Schweißgeschwindigkeiten, um Durchbrennen und übermäßige Wärmezufuhr zu verhindern. Eine präzise Steuerung der Laserparameter ermöglicht saubere, fehlerfreie Schweißnähte.
- Dicke Materialien: Das Schweißen dicker Materialien erfordert eine höhere Laserleistung und langsamere Schweißgeschwindigkeiten, um eine ausreichende Durchdringung und Verschmelzung sicherzustellen. Um eine vollständige Durchdringung zu erreichen, können fortgeschrittene Techniken wie Mehrlagenschweißen oder Hybridschweißen (Kombination aus Laser- und Lichtbogenschweißen) eingesetzt werden.
- Übergangszone: Beim Schweißen von Materialien unterschiedlicher Dicke müssen die Laserparameter dynamisch angepasst werden, um Unterschiede bei der Wärmeabsorption und -leitung auszugleichen.
Zustand der Oberfläche
Die Oberflächenbeschaffenheit eines Materials kann sich auf die Laserabsorption, die Wärmeübertragung und die allgemeine Schweißqualität auswirken. Eine ordnungsgemäße Oberflächenvorbereitung trägt zu einem effizienten Laserschweißen bei.
- Sauberkeit: Verunreinigungen wie Öl, Fett, Schmutz und Oxidschichten können die Laserabsorption beeinträchtigen und zu Defekten in der Schweißnaht führen. Um optimale Ergebnisse zu erzielen, ist eine gründliche Reinigung der Oberfläche vor dem Schweißen erforderlich.
- Oberflächenrauheit: Die Rauheit der Oberfläche eines Materials kann die Interaktion mit Laserstrahlen beeinflussen. Glattere Oberflächen führen im Allgemeinen zu einer besseren Laserabsorption und gleichmäßigeren Schweißnähten. Oberflächenbehandlungen wie Polieren oder Sandstrahlen können zur Verbesserung der Oberflächenbedingungen eingesetzt werden.
- Beschichtungen und Behandlungen: Einige Materialien können Beschichtungen oder Behandlungen aufweisen, die das Laserschweißen beeinträchtigen. Beispielsweise hat verzinkter Stahl eine Zinkbeschichtung, die spezielle Lasereinstellungen erfordert, um Verdunstung und Porosität zu verhindern. Wenn Sie die Auswirkungen dieser Beschichtungen verstehen, können Sie die Schweißparameter entsprechend anpassen.
Thermische Eigenschaften
Die thermischen Eigenschaften eines Materials, einschließlich Wärmeleitfähigkeit, spezifische Wärmekapazität und Schmelzpunkt, beeinflussen, wie das Material mit Laserenergie interagiert.
- Wärmeleitfähigkeit: Materialien mit hoher Wärmeleitfähigkeit, wie Kupfer und Aluminium, leiten Wärme schnell ab und erfordern höhere Laserleistungen, um eine ordnungsgemäße Verschmelzung zu erreichen. Materialien mit geringer Wärmeleitfähigkeit, wie Edelstahl, speichern Wärme länger, daher muss die Wärmezufuhr sorgfältig kontrolliert werden, um ein übermäßiges Schmelzen zu vermeiden.
- Spezifische Wärmekapazität: Die spezifische Wärmekapazität eines Materials bestimmt die Energiemenge, die zum Erhöhen seiner Temperatur erforderlich ist. Materialien mit hoher spezifischer Wärmekapazität erfordern mehr Energie zum Schweißen, was sich auf die Wahl der Laserleistung und der Schweißgeschwindigkeit auswirkt.
- Schmelzpunkt: Der Schmelzpunkt eines Materials bestimmt die Energiemenge, die zum Schmelzen und Verschmelzen erforderlich ist. Materialien mit hohem Schmelzpunkt, wie Titan und bestimmte Legierungen, erfordern höhere Laserleistungen und eine präzise Kontrolle der Schweißparameter, um ein effizientes Schweißen zu erreichen.
Metallurgische Eigenschaften
Die metallurgischen Eigenschaften eines Materials, einschließlich seiner Zusammensetzung, Mikrostruktur und Phasenumwandlungen, spielen beim Laserschweißprozess eine entscheidende Rolle.
- Zusammensetzung: Die chemische Zusammensetzung eines Materials beeinflusst seine Schweißbarkeit. Legierungselemente beeinflussen die Absorption von Laserenergie durch das Material, sein Schmelzverhalten und die Anfälligkeit für Defekte wie Rissbildung und Porosität. Das Verständnis der Zusammensetzung hilft bei der Auswahl geeigneter Laserparameter und Schutzgase.
- Mikrostruktur: Die Mikrostruktur eines Materials, einschließlich Korngröße und Phasenverteilung, beeinflusst seine mechanischen Eigenschaften und sein Schweißverhalten. Feinkörnige Materialien lassen sich im Allgemeinen besser schweißen als grobkörnige Materialien, bei denen besondere Aufmerksamkeit erforderlich sein kann, um Risse und Verformungen zu vermeiden.
- Phasenumwandlungen: Einige Materialien durchlaufen beim Schweißen Phasenumwandlungen, die die endgültigen Schweißeigenschaften beeinflussen können. Beispielsweise wandeln sich einige Stähle beim Abkühlen von Austenit zu Martensit um, was zu einer harten und spröden Schweißnaht führt. Die Kontrolle der Abkühlgeschwindigkeit und der Wärmebehandlung nach dem Schweißen können dazu beitragen, diese Umwandlungen zu kontrollieren und die Schweißqualität zu verbessern.
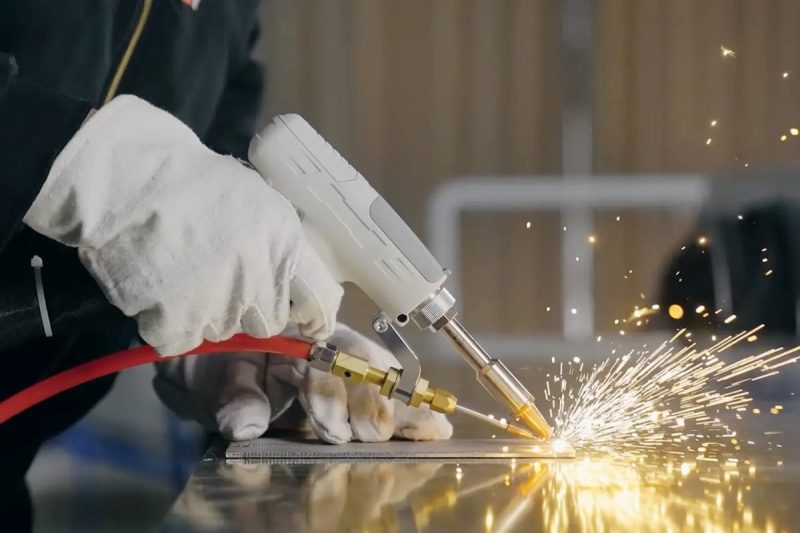
Fugenkonstruktion
Gelenkkonfiguration
Die Verbindungskonfiguration hat erhebliche Auswirkungen auf den Laserschweißprozess. Verschiedene Verbindungstypen bieten unterschiedliche Grade der Zugänglichkeit, Schweißfreundlichkeit und mechanischen Festigkeit.
- Stumpfstoß: Bei einem Stumpfstoß werden zwei Materialstücke Kante an Kante platziert. Diese Konfiguration ist beim Laserschweißen üblich, da sie einfach ist und ein tiefes Eindringen ermöglicht. Allerdings können nur eine präzise Ausrichtung und minimale Lücken eine qualitativ hochwertige Schweißnaht gewährleisten.
- Überlappverbindung: Bei einer Überlappverbindung überlappt ein Materialstück ein anderes. Diese Konfiguration wird häufig zum Schweißen dünner Materialien verwendet und ist einfach zu montieren. Allerdings ist eine sorgfältige Kontrolle der Laserparameter erforderlich, um ein übermäßiges Schmelzen zu vermeiden und sicherzustellen, dass die beiden Schichten richtig verschmolzen werden.
- T-Verbindung: T-Verbindungen entstehen, indem ein Stück Material senkrecht zu einem anderen verschweißt wird. Diese Konfiguration wird häufig bei strukturellen Anwendungen verwendet. Die Herausforderung bei T-Verbindungen besteht darin, eine gleichmäßige Durchdringung zu erreichen und Defekte an der Schnittstelle zu vermeiden.
- Eckverbindung: Eckverbindungen werden verwendet, um zwei Materialstücke im rechten Winkel zu verbinden. Sie werden häufig bei kastenförmigen Strukturen und Rahmen verwendet. Um eine ordnungsgemäße Verbindung an den Ecken sicherzustellen, ist eine genaue Kontrolle der Laserparameter und der Verbindungsvorbereitung erforderlich.
- Randverbindung: Bei Randverbindungen wird entlang der Kante eines oder beider Materialstücke geschweißt. Diese Konfiguration eignet sich für dünne Materialien und Anwendungen, bei denen eine minimale Überlappung erforderlich ist. Um gleichmäßige Schweißnähte bei Randverbindungen zu erzielen, sind eine präzise Ausrichtung und Spaltkontrolle erforderlich.
Gemeinsame Vorbereitung
Eine ordnungsgemäße Nahtvorbereitung trägt zu hochwertigen Schweißnähten bei. Der Zustand der Nahtoberfläche wirkt sich direkt auf die Laserabsorption, die Wärmeübertragung und die allgemeine Schweißintegrität aus.
- Sauberkeit: Die Verbindungsfläche muss frei von Verunreinigungen wie Öl, Fett, Schmutz und Oxiden sein. Verunreinigungen können die Laserabsorption beeinträchtigen und Defekte wie Porosität und unvollständige Verschmelzung verursachen. Je nach Material und vorhandenen Verunreinigungen können Reinigungsmethoden wie Entfetten, Drahtbürsten und chemische Reinigung verwendet werden.
- Oberflächenbehandlung: Oberflächenbehandlungen wie Sandstrahlen, Schleifen oder maschinelle Bearbeitung können den Oberflächenzustand verbessern und die Laserabsorption erhöhen. Diese Behandlungen tragen zur Schaffung einer glatten, gleichmäßigen Oberfläche mit geringerem Fehlerrisiko bei.
- Kantenvorbereitung: Eine ordnungsgemäße Kantenvorbereitung gewährleistet eine gute Passung und minimiert Lücken. Techniken wie Abschrägen, Anfasen und Kantenrunden können die Passung der Verbindung verbessern und eine bessere Verschmelzung fördern.
Lückentoleranz
Durch die Einhaltung enger Spalttoleranzen können gleichbleibende und qualitativ hochwertige Laserschweißungen erzielt werden. Lücken zwischen den Verbindungsflächen können zu unvollständiger Verschmelzung, schwachen Schweißnähten und Defekten führen.
- Minimaler Abstand: Idealerweise sollten Verbindungsflächen einen minimalen Abstand aufweisen, um eine vollständige Verschmelzung und eine starke Schweißnaht zu gewährleisten. Kleine Abstände können durch geschmolzenes Material überbrückt werden, aber übermäßige Abstände können zu einer unvollständigen Verschmelzung und einer schwachen Verbindung führen.
- Zulässige Toleranz: Die zulässige Spalttoleranz hängt vom Material, der Verbindungskonfiguration und den Schweißparametern ab. Im Allgemeinen erfordern hochpräzise Anwendungen und dünne Materialien engere Toleranzen, während dickere Materialien etwas größere Spalte tolerieren können.
- Anpassungen: Wenn Lücken vorhanden sind, kann das Anpassen der Laserleistung, der Schweißgeschwindigkeit und der Fokusposition helfen, diese auszugleichen und eine ausreichende Verschmelzung sicherzustellen. Zu große Lücken sollten jedoch vermieden werden, da sie die Schweißqualität und -festigkeit beeinträchtigen können.
Vorrichtungen und Klemmen
Effektive Vorrichtungen und Klemmvorrichtungen können die Stabilität und Ausrichtung der Verbindung während des Laserschweißvorgangs gewährleisten. Richtige Vorrichtungen und Klemmvorrichtungen verhindern Bewegung, Verformung und Fehlausrichtung und verbessern so die Schweißeffizienz und -qualität.
- Stabilität: Die Vorrichtung muss das Material fest an seinem Platz halten, um jegliche Bewegung während des Schweißvorgangs zu verhindern. Selbst leichte Bewegungen können zu Fehlausrichtungen, Defekten und Veränderungen der Schweißqualität führen.
- Ausrichtung: Das Spannsystem sollte sicherstellen, dass die Verbindungsflächen genau ausgerichtet sind. Eine Fehlausrichtung kann zu schlechter Verschmelzung und schwachen Schweißnähten führen. Einstellbare Vorrichtungen und Präzisionsspannwerkzeuge können dabei helfen, eine präzise Ausrichtung zu erreichen.
- Wärmemanagement: Die Vorrichtungen und Klemmen sollten auch die während des Schweißvorgangs erzeugte Wärme regulieren. Übermäßige Hitze kann dazu führen, dass sich die Verbindung verformt und bewegt. Die Verwendung von Materialien mit guter Wärmeleitfähigkeit für die Vorrichtung oder integrierte Kühlsysteme kann dabei helfen, die Hitze zu regulieren und die Stabilität aufrechtzuerhalten.
- Zugänglichkeit: Das Design der Vorrichtung und des Klemmsystems sollte es dem Laserstrahl ermöglichen, den Schweißbereich problemlos zu erreichen. Komplexe Geometrien und enge Räume erfordern maßgeschneiderte Vorrichtungen, um einen ordnungsgemäßen Laserzugang und optimale Schweißbedingungen zu gewährleisten.
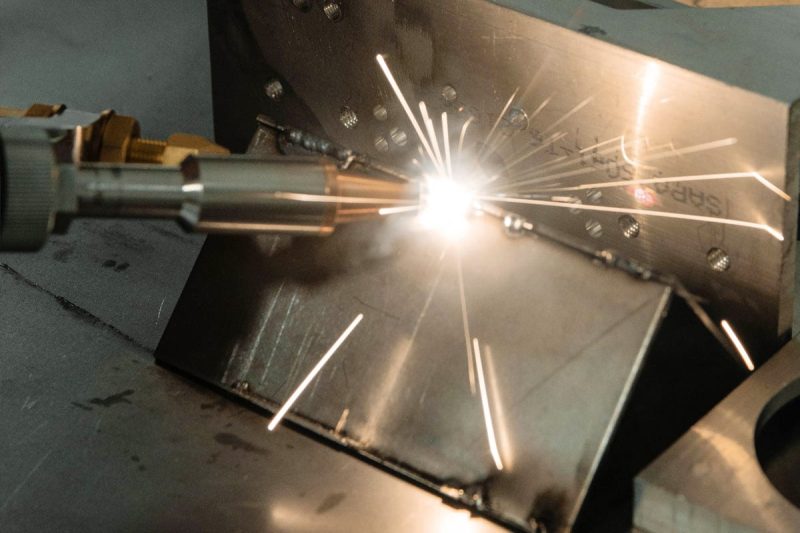
Umweltbedingungen
Umgebungstemperatur
Die Umgebungstemperatur kann den Laserschweißprozess auf verschiedene Weise beeinflussen. Die Aufrechterhaltung einer kontrollierten Temperaturumgebung gewährleistet eine gleichbleibende Schweißqualität und verhindert Geräteprobleme.
- Gleichbleibende Schweißleistung: Extreme Temperaturen, entweder zu hoch oder zu niedrig, können die thermischen Eigenschaften der zu schweißenden Materialien beeinträchtigen. Hohe Umgebungstemperaturen können zu übermäßiger Wärmezufuhr und erhöhter thermischer Verformung führen, während niedrige Temperaturen zu schneller Abkühlung und potenzieller Rissbildung führen können.
- Gerätestabilität: Laserschweißgeräte, einschließlich Laserquelle und Kühlsystem, funktionieren am besten in einem bestimmten Temperaturbereich:
- Hohe Temperatur: Übermäßige Hitze kann zu einer thermischen Ausdehnung des Schweißmaterials führen, was zu Fehlausrichtung und Verformung führt. Es kann auch die Abkühlgeschwindigkeit der Schweißnaht beeinträchtigen und sich auf die Mikrostruktur und die mechanischen Eigenschaften der Verbindung auswirken.
- Niedrige Temperaturen: Extrem kalte Umgebungen können Kondensation auf der Laseroptik und den Materialoberflächen verursachen, was die Laserabsorption beeinträchtigt und möglicherweise Defekte verursacht. Niedrige Temperaturen können auch die Wärmeleitfähigkeit und das Schmelzverhalten des Materials beeinträchtigen.
- Kontrollmaßnahmen: Die Implementierung eines Klimakontrollsystems in der Schweißumgebung kann dazu beitragen, eine stabile Umgebungstemperatur aufrechtzuerhalten. Dies gewährleistet ein konsistentes Materialverhalten und eine gleichbleibende Geräteleistung, was zu einem effizienteren und zuverlässigeren Schweißprozess führt.
Feuchtigkeit
Die Luftfeuchtigkeit in der Schweißumgebung kann sich sowohl auf die Laserausrüstung als auch auf die zu schweißenden Materialien auswirken.
- Kondensation: Hohe Luftfeuchtigkeit kann zur Bildung von Kondensation auf der Laseroptik und den Materialoberflächen führen. Dies kann den Laserstrahl streuen, seine Intensität und Präzision verringern und außerdem zu Verunreinigungen in der Schweißnaht führen.
- Oxidation und Korrosion: Materialien, die anfällig für Oxidation und Korrosion sind, werden durch hohe Luftfeuchtigkeit beeinträchtigt. Das Vorhandensein von Feuchtigkeit kann diese Prozesse beschleunigen und zu Oberflächenverunreinigungen und Schweißfehlern führen.
- Materialverhalten: Einige Materialien, insbesondere feuchtigkeitsempfindliche, können durch Feuchtigkeit Veränderungen ihrer Eigenschaften aufweisen. Dies kann sich auf ihre Schweißbarkeit und die Qualität der endgültigen Schweißnaht auswirken.
- Kontrollmaßnahmen: Die Verwendung eines Luftentfeuchters und die Gewährleistung einer angemessenen Belüftung können zur Kontrolle der Luftfeuchtigkeit beitragen. Wenn der Schweißbereich trocken und feuchtigkeitsfrei gehalten wird, können optimale Schweißbedingungen aufrechterhalten werden.
Schutzgas
Der Einsatz von Schutzgas kann zum erfolgreichen Laserschweißen beitragen, indem es den Schweißbereich vor atmosphärischen Verunreinigungen schützt und die Schweißqualität verbessert.
- Arten von Schutzgasen: Zu den beim Laserschweißen häufig verwendeten Schutzgasen gehören Argon, Helium, Stickstoff und Mischungen dieser Gase. Die Wahl des Schutzgases hängt vom Schweißmaterial und den erforderlichen Schweißeigenschaften ab.
- Argon: Argon wird aufgrund seiner Inertheit häufig verwendet und bietet einen hervorragenden Schutz gegen Oxidation und Verunreinigung. Es eignet sich zum Schweißen einer Vielzahl von Metallen, darunter Stahl, Aluminium und Titan.
- Helium: Helium kann die Schweißdurchdringung erhöhen und die Porosität verringern, weshalb es sich ideal für tiefe Schweißnähte und Materialien mit hoher Wärmeleitfähigkeit wie Kupfer und Aluminium eignet.
- Stickstoff: Stickstoff wird häufig in Kombination mit anderen Gasen verwendet, um die Schweißqualität bei einigen Materialien zu verbessern. Aufgrund seiner möglichen Reaktivität mit einigen Metallen muss jedoch Vorsicht walten gelassen werden.
- Durchfluss und Abdeckung: Durchfluss und Abdeckung des Schutzgases müssen sorgfältig kontrolliert werden, um einen ausreichenden Schutz des Schweißbereichs zu gewährleisten. Unzureichender Gasdurchfluss kann zu Verunreinigungen und Defekten führen, während übermäßiger Durchfluss Turbulenzen und Kühlprobleme verursachen kann.
- Düsendesign: Das Design und die Positionierung der Schutzgasdüse können dazu beitragen, eine effektive Gasabdeckung zu erreichen. Ein geeignetes Düsendesign gewährleistet einen kontinuierlichen und gleichmäßigen Gasfluss über den Schweißbereich und verbessert so die Schweißqualität und -effizienz.
Belüftung
Eine ausreichende Belüftung des Schweißbereichs trägt dazu bei, eine sichere und effiziente Schweißumgebung aufrechtzuerhalten.
- Rauchabsaugung: Beim Laserschweißen entstehen Rauch und Gase, die für den Bediener schädlich sind und den Schweißprozess beeinträchtigen können. Ein wirksames Rauchabsaugungssystem entfernt diese Verunreinigungen aus dem Arbeitsbereich und sorgt so für eine saubere und sichere Umgebung.
- Luftstromregelung: Ein kontrollierter Luftstrom trägt zur Aufrechterhaltung einer stabilen Schweißumgebung bei, indem er Rauchansammlungen verhindert und eine gleichmäßige Gasabdeckung des Schweißbereichs gewährleistet. Unkontrollierter Luftstrom oder Turbulenzen können das Schutzgas stören und die Schweißqualität beeinträchtigen.
- Wärmemanagement: Belüftung hilft, die beim Schweißen entstehende Wärme zu regulieren. Ein ausreichender Luftstrom verhindert eine Überhitzung von Materialien und Geräten und verringert das Risiko von thermischen Verformungen und Geräteausfällen.
- Luftqualität: Eine gute Luftqualität in der Schweißumgebung verhindert die Ansammlung von Staub und anderen Partikeln, die den Laserstrahl und den Schweißprozess beeinträchtigen können. Saubere Luft gewährleistet eine gleichbleibende Strahlqualität und verringert das Risiko von Defekten.
- Sicherheitsmaßnahmen: Eine ausreichende Belüftung verringert das Risiko einer Exposition gegenüber gefährlichen Dämpfen und verbessert die allgemeine Sicherheit am Arbeitsplatz. Außerdem trägt sie dazu bei, die Integrität der Laseroptik und anderer empfindlicher Komponenten zu erhalten, indem sie Verunreinigungen und Partikelansammlungen verhindert.
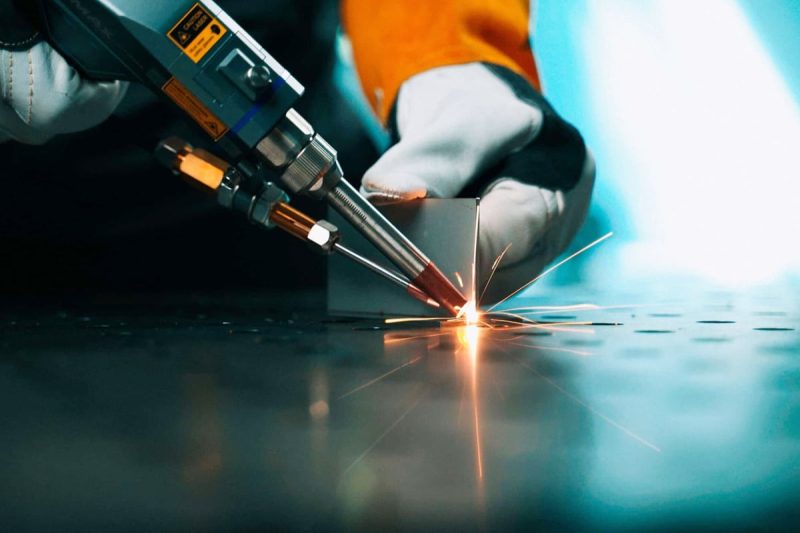
Schweißgeschwindigkeit
Optimale Schweißgeschwindigkeit
Das Erreichen der optimalen Schweißgeschwindigkeit ist ein heikles Gleichgewicht zwischen Schweißqualität und Produktivität. Die richtige Geschwindigkeit stellt sicher, dass die Materialien vollständig und ohne Defekte verschmolzen werden.
- Vollständige Verschmelzung: Bei optimaler Schweißgeschwindigkeit liefert der Laser genügend Energie, um die Materialien vollständig zu schmelzen und zu verschmelzen. Dadurch entsteht eine starke, fehlerfreie Schweißnaht mit guten mechanischen Eigenschaften.
- Gleichbleibende Qualität: Konstante Schweißgeschwindigkeiten gewährleisten eine gleichmäßige Wärmezufuhr entlang der Schweißnaht, was zu einer gleichbleibenden Schweißqualität führt. Geschwindigkeitsschwankungen können Unregelmäßigkeiten verursachen, die die Festigkeit und das Aussehen der Schweißnaht beeinträchtigen.
Auswirkungen hoher Schweißgeschwindigkeiten
Hohe Schweißgeschwindigkeiten können die Produktivität steigern, bringen jedoch auch bestimmte Herausforderungen und potenzielle Nachteile mit sich.
- Höhere Produktivität: Höhere Schweißgeschwindigkeiten verkürzen die Zykluszeit, sodass in einer bestimmten Zeit mehr Schweißungen durchgeführt werden können. Dies ist insbesondere in Produktionsumgebungen mit hohem Volumen von Vorteil.
- Mögliche Mängel: Zu schnelles Schweißen kann zu unzureichender Wärmezufuhr führen, was zu unvollständiger Verschmelzung, schwachen Schweißnähten und möglichen Rissen führen kann. Schnelle Bewegungen lassen den Materialien möglicherweise nicht genügend Zeit zum Schmelzen und zur richtigen Verbindung.
- Oberflächenunregelmäßigkeiten: Bei sehr hohen Geschwindigkeiten hat das Schmelzbad möglicherweise nicht genug Zeit, sich zu beruhigen, was zu Oberflächenunregelmäßigkeiten wie Wellen und Spritzern führen kann.
Auswirkungen niedriger Schweißgeschwindigkeiten
Zwar kann eine langsamere Schweißgeschwindigkeit die Schweißqualität verbessern, es gibt jedoch gewisse Einschränkungen und Überlegungen.
- Verbesserte Durchdringung: Niedrigere Schweißgeschwindigkeiten erhöhen die Wärmezufuhr pro Schweißlängeneinheit, was die Durchdringung verbessert und eine vollständige Verschmelzung dickerer Materialien gewährleistet.
- Größere Wärmeeinflusszone (WEZ): Niedrigere Geschwindigkeiten führen zu übermäßiger Wärmezufuhr, was eine größere WEZ zur Folge hat. Dies kann zu thermischer Verformung, verringerten mechanischen Eigenschaften und möglichem Verziehen des geschweißten Bauteils führen.
- Reduzierte Produktivität: Langsamere Schweißgeschwindigkeiten verringern die Produktivität und erhöhen die Gesamtzeit, die zum Abschließen einer Schweißaufgabe erforderlich ist. In einer Produktionsumgebung mit hohem Volumen kann dies ein erheblicher Nachteil sein.
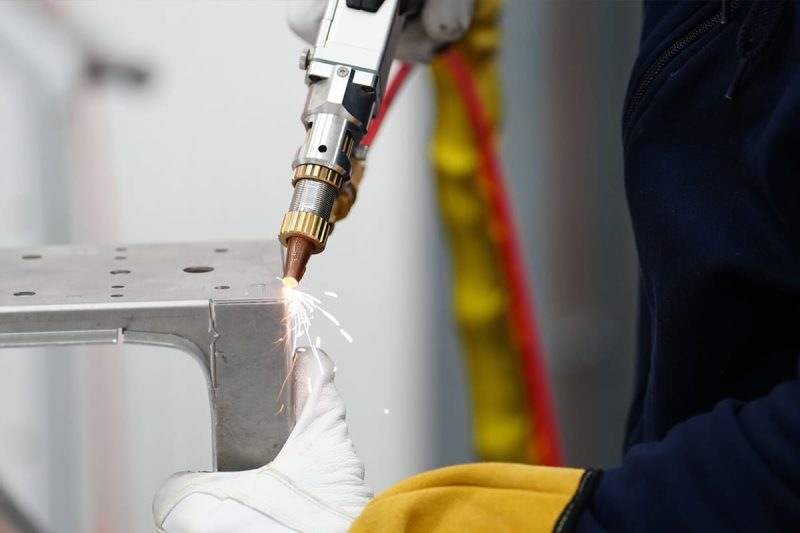
Fähigkeiten und Erfahrung des Bedieners
Bedeutung der Fähigkeiten und Erfahrungen des Bedieners
Die Kompetenz des Bedieners ist aus mehreren Gründen von entscheidender Bedeutung. Dazu gehören die ordnungsgemäße Einrichtung der Schweißausrüstung, die genaue Parametereinstellung und die Fähigkeit, während des Schweißvorgangs auftretende Probleme schnell zu erkennen und zu lösen.
- Einrichtung und Kalibrierung: Erfahrene Bediener sind mit der Einrichtung und Kalibrierung von Laserschweißgeräten vertraut. Dazu gehört das Ausrichten des Lasers, das Anpassen des Fokus, das Einstellen der geeigneten Laserleistung und das Konfigurieren des Schutzgasflusses. Die richtige Einrichtung stellt sicher, dass der Schweißprozess mit der richtigen Grundlage beginnt, wodurch das Risiko von Defekten und Ineffizienzen minimiert wird.
- Parameteranpassung: Erfahrene Bediener verfügen über ein tiefes Verständnis für die Beziehung zwischen Schweißparametern und Schweißqualität. Sie können Parameter wie Schweißgeschwindigkeit, Laserleistung und Pulsfrequenz präzise anpassen, um den Schweißprozess für verschiedene Materialien und Verbindungskonfigurationen zu optimieren.
- Fehlersuche und Problemlösung: Während des Schweißvorgangs können verschiedene Probleme auftreten, wie z. B. Fehlausrichtung, schlechte Durchdringung oder die Bildung von Defekten wie Porosität und Rissen. Erfahrene Bediener können diese Probleme schnell diagnostizieren und Korrekturmaßnahmen ergreifen, um minimale Ausfallzeiten und eine gleichbleibende Schweißqualität sicherzustellen.
- Prozessanpassung: Unterschiedliche Materialien, Verbindungskonfigurationen und Schweißaufgaben erfordern spezifische Anpassungen. Erfahrene Bediener können die Prozessparameter an unterschiedliche Bedingungen anpassen und so eine gleichbleibende Schweißqualität bei allen Anwendungen sicherstellen.
Schulung und Zertifizierung
Eine angemessene Schulung und Zertifizierung trägt dazu bei, ein hohes Niveau an Bedienerkenntnissen zu entwickeln und aufrechtzuerhalten. Das umfassende Schulungsprogramm sollte Folgendes abdecken:
- Theoretische Kenntnisse: Es ist wichtig, die Prinzipien des Laserschweißens zu verstehen, einschließlich der Wechselwirkung zwischen Laserenergie und Materialien. Die Bediener sollten mit der Wissenschaft hinter dem Prozess gut vertraut sein, um fundierte Entscheidungen treffen zu können.
- Praktische Erfahrung: Durch praktische Schulungen mit Laserschweißgeräten können Bediener Erfahrungen beim Einrichten, Kalibrieren und Bedienen der Maschine sammeln. Praktische Erfahrung hilft, Vertrauen und Kompetenz in der realen Welt aufzubauen.
- Sicherheitsprotokolle: Laserschweißen birgt potenzielle Gefahren, darunter intensives Licht, Rauch und Hitze. In der Schulung sollten Sicherheitsprotokolle hervorgehoben werden, um die Bediener zu schützen und eine sichere Arbeitsumgebung zu gewährleisten.
- Zertifizierungsprogramme: Zertifizierungsprogramme bestätigen die Fähigkeiten und Kenntnisse der Bediener und erkennen ihr Fachwissen formal an. Zertifizierte Bediener sind im Allgemeinen besser in der Lage, komplexe Schweißaufgaben zu bewältigen und Probleme effektiv zu beheben.
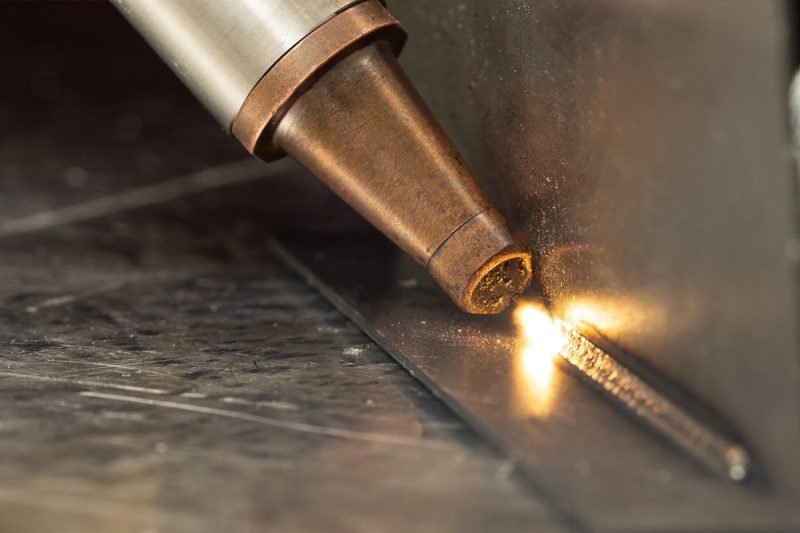
Ausrüstung und Wartung
Laserquelle
Die Laserquelle ist das Herzstück eines Faserlaserschweißsystem, wodurch der zum Schweißen erforderliche Hochintensitätsstrahl erzeugt wird.
- Faserlaser: Faserlaser sind für ihre hohe Effizienz, hervorragende Strahlqualität und Robustheit bekannt und eignen sich ideal zum Schweißen einer breiten Palette von Materialien, einschließlich reflektierender Metalle wie Aluminium und Kupfer.
- Wartung: Überwachen Sie regelmäßig die Leistungsabgabe, um eine gleichbleibende Leistung sicherzustellen, reinigen Sie die Optik, um Verunreinigungen zu vermeiden, und überprüfen Sie die Ausrichtung, um die Strahlgenauigkeit aufrechtzuerhalten.
Optik
Die Optik lenkt und fokussiert den Laserstrahl auf den Schweißbereich und sorgt so für eine präzise Energieabgabe.
- Strahlführungssystem: Enthält Glasfaser und Kollimator, um den Laserstrahl mit minimalen Verlusten zuzuführen.
- Fokussieroptik: Linsen oder Fokussierköpfe, die den Laserstrahl auf eine kleine Punktgröße konzentrieren und so die Energiedichte erhöhen.
- Wartung: Regelmäßige Reinigung von Linsen, Spiegeln und Schutzfenstern sowie Überprüfung auf Beschädigungen und Ausrichtungskontrollen tragen zur Aufrechterhaltung einer optimalen Strahlqualität bei.
Bewegungssystem
Das Bewegungssystem steuert die Bewegung des Laserstrahls und des Werkstücks und sorgt für eine präzise Positionierung und einen reibungslosen Betrieb.
- Typen: Kartesische Systeme für dreiachsige lineare Bewegung, Roboterarme für mehrachsige Bewegung und Portalsysteme für groß angelegte Anwendungen.
- Wartung: Regelmäßiges Schmieren beweglicher Teile, regelmäßige Kalibrierung für präzise Bewegung und Überprüfung auf Verschleiß oder Fehlausrichtung tragen zu einem zuverlässigen Betrieb bei.
Kühlsystem
Das Kühlsystem verhindert eine Überhitzung der Laserquelle und anderer wichtiger Komponenten und sorgt für einen stabilen Betrieb.
- Wasserkühlung: Wird aufgrund der guten Wärmeableitungswirkung häufig in Hochleistungs-Faserlasergeneratoren verwendet.
- Komponenten: Pumpen, Wärmetauscher und Kühlmittelbehälter sind zentrale Elemente des Kühlsystems.
- Wartung: Überprüfen Sie regelmäßig, ob Lecks und Verstopfungen vorliegen, überwachen Sie die Kühlmittelqualität und ersetzen Sie die Filter nach Bedarf, um eine effiziente Kühlung zu gewährleisten.
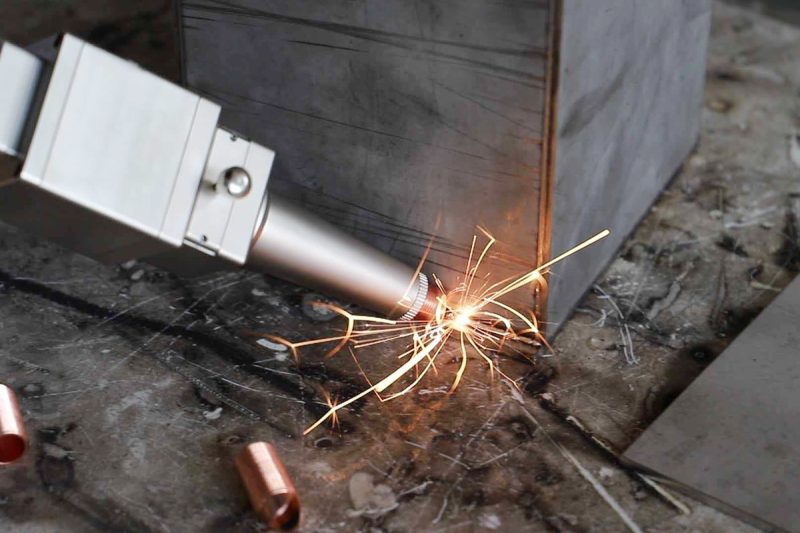
Automatisierungs- und Steuerungssysteme
Echtzeitüberwachung
Echtzeit-Überwachungssysteme liefern kontinuierliches Feedback zum Schweißvorgang und ermöglichen sofortige Anpassungen, um eine optimale Leistung sicherzustellen.
- Überwachung der Schweißqualität: Sensoren und Kameras überwachen das Schweißbad und erkennen in Echtzeit Defekte wie Porosität, Risse und Fehlausrichtung. Dadurch kann der Bediener die Laserleistung, -geschwindigkeit und -fokussierung in Echtzeit anpassen.
- Überwachung der Laserleistung: Das System überwacht kontinuierlich die Laserleistung, um sicherzustellen, dass sie im gewünschten Bereich bleibt. Dies trägt dazu bei, eine konstante Energieabgabe und Schweißdurchdringung aufrechtzuerhalten.
Adaptive Steuerung
Adaptive Steuerungssysteme passen die Schweißparameter dynamisch auf Grundlage von Echtzeitdaten an, um den Prozess an unterschiedliche Bedingungen zu optimieren.
- Parameteranpassung: Diese Systeme passen Laserleistung, Schweißgeschwindigkeit und Fokusposition automatisch an Änderungen der Materialeigenschaften, Dicke und Fugenkonfiguration an. Dies gewährleistet eine gleichmäßige und konsistente Schweißqualität über verschiedene Teile des Werkstücks hinweg.
- Rückkopplungsschleifen: Durch die Einbindung von Rückkopplungsschleifen kann das System aus früheren Schweißvorgängen lernen und so mit der Zeit die Genauigkeit und Effizienz verbessern.
Integration mit Robotersystemen
Die Integration des Faserlaserschweißens in Robotersysteme verbessert Automatisierung, Flexibilität und Wiederholbarkeit.
- Mehrachsenbewegung: Der Roboterarm ermöglicht Mehrachsenbewegungen zum präzisen Schweißen komplexer Geometrien und schwer erreichbarer Bereiche.
- Konstante Qualität: Der Roboter gewährleistet eine gleichbleibende Schweißqualität durch präzise Steuerung von Schweißweg, Geschwindigkeit und Winkel und reduziert so die beim manuellen Schweißen auftretenden Abweichungen.
- Durchsatz erhöhen: Roboterautomatisierung erhöht den Durchsatz, indem sie einen kontinuierlichen Betrieb ermöglicht und die Zykluszeiten verkürzt, was zu erheblichen Produktivitätssteigerungen führt.
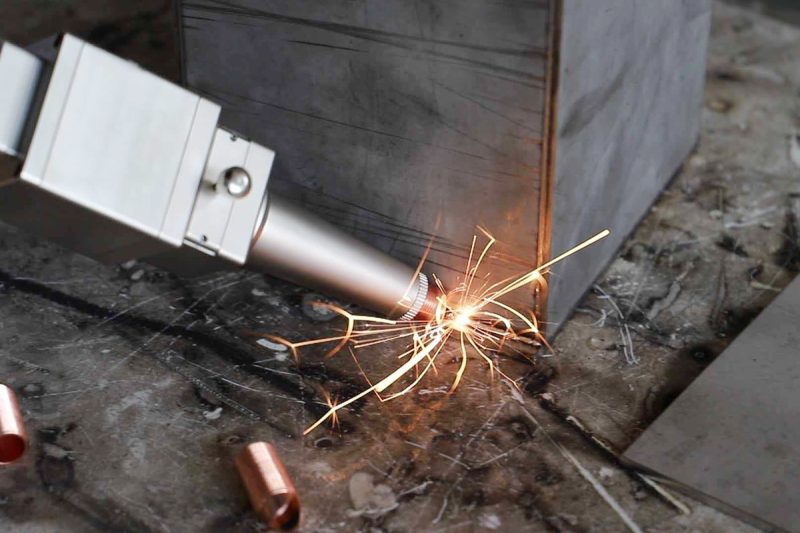
Anwendungsspezifische Überlegungen
Materialkombinationen
Verschiedene Materialien reagieren unterschiedlich auf das Laserschweißen und ihre Kombination kann besondere Herausforderungen mit sich bringen.
- Ungleiche Materialien: Das Schweißen unterschiedlicher Materialien, wie Aluminium und Stahl, kann aufgrund unterschiedlicher Schmelzpunkte, Wärmeleitfähigkeiten und Laserabsorptionsraten eine Herausforderung darstellen. Faserlaser sind beim Schweißen dieser Kombinationen effektiv, erfordern jedoch eine präzise Kontrolle der Parameter, um die Wärmezufuhr zu steuern und Defekte zu vermeiden.
- Reflektierende Materialien: Materialien wie Kupfer und Aluminium reflektieren einen erheblichen Teil der Laserenergie, was die Schweißeffizienz verringern kann. Faserlaser, insbesondere mit kürzeren Wellenlängen, sind für diese Materialien besser geeignet, aber die Optimierung der Laserparameter ist unerlässlich, um eine effektive Energieabsorption zu gewährleisten.
- Legierungen und Verbundwerkstoffe: Für optimales Schweißen sind für jede Legierung und jedes Verbundmaterial möglicherweise spezielle Einstellungen erforderlich. Um qualitativ hochwertige Schweißnähte zu erzielen, ist es wichtig, die Materialeigenschaften zu verstehen und die Laserleistung, -geschwindigkeit und -fokussierung entsprechend anzupassen.
Schweißgeometrie
Die Geometrie der Schweißverbindung beeinflusst den Schweißvorgang und muss zur Gewährleistung der Effizienz sorgfältig berücksichtigt werden.
- Komplexe Geometrien: Das Schweißen komplexer Geometrien, wie gekrümmter oder komplizierter Formen, erfordert eine präzise Steuerung des Laserstrahls und des Bewegungssystems. Faserlaser können diese Geometrien effektiv handhaben, wenn sie mit fortschrittlichen Bewegungssystemen und Roboterarmen integriert werden.
- Dünne VS. dicke Abschnitte: Das Schweißen dünner Abschnitte erfordert weniger Leistung und höhere Präzision, um ein Durchbrennen zu vermeiden, während dicke Abschnitte mehr Leistung und niedrigere Geschwindigkeiten erfordern, um vollständig einzudringen. Durch Anpassen der Laserparameter an bestimmte Geometrien kann ein effizientes Schweißen erreicht werden.
- Kantenvorbereitung: Eine ordnungsgemäße Kantenvorbereitung, wie z. B. Abschrägen oder Reinigen, sorgt für eine bessere Passform und Verschmelzung. Die Beibehaltung einer gleichbleibenden Kantenqualität kann dazu beitragen, gleichmäßige Schweißnähte zu erzielen.
Produktionsvolumen
Das Produktionsvolumen beeinflusst die Wahl der Laserschweißausrüstung und der Prozessparameter.
- Kleinserien- oder Sonderanfertigungen: Bei Kleinserien- oder Sonderanfertigungen sind Flexibilität und Anpassungsfähigkeit entscheidend. Die Vielseitigkeit von Faserlasern ermöglicht eine schnelle Anpassung der Schweißparameter und -konfigurationen, sodass sie für eine Vielzahl spezialisierter Schweißaufgaben geeignet sind.
- Großserienproduktion: Großserienproduktion erfordert Konsistenz, Geschwindigkeit und Automatisierung. Faserlasersysteme, die mit automatisierten Steuerungssystemen und Roboterarmen integriert sind, sorgen für die erforderliche Präzision und Wiederholbarkeit und steigern so Produktion und Effizienz deutlich.
- Optimierung der Zykluszeit: In einer Produktionsumgebung kann die Minimierung der Zykluszeit die Effizienz steigern. Faserlasersysteme mit Echtzeitüberwachung und adaptiver Steuerung können die Rüstzeit verkürzen und optimale Schweißgeschwindigkeiten gewährleisten, wodurch die Gesamtproduktivität gesteigert wird.
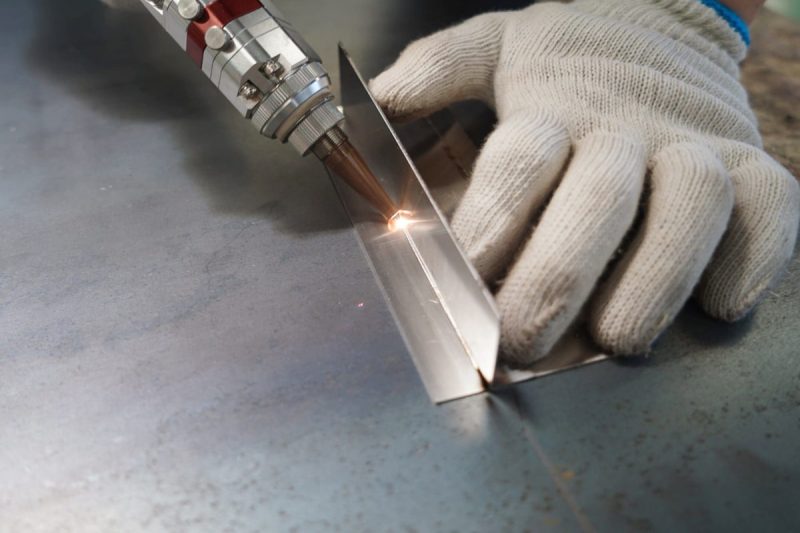
Zusammenfassung
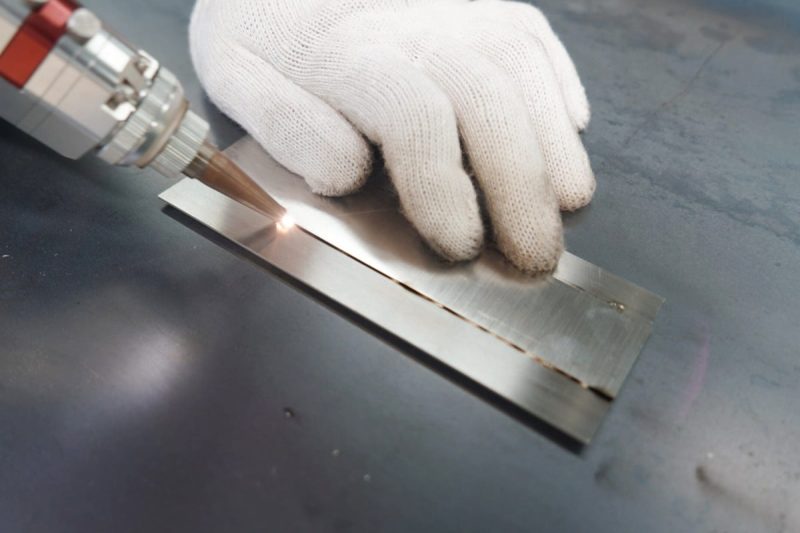
Holen Sie sich Laserschweißlösungen
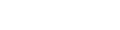
- [email protected]
- [email protected]
- +86-19963414011
- Nr. 3 Zone A, Industriegebiet Lunzhen, Stadt Yucheng, Provinz Shandong.