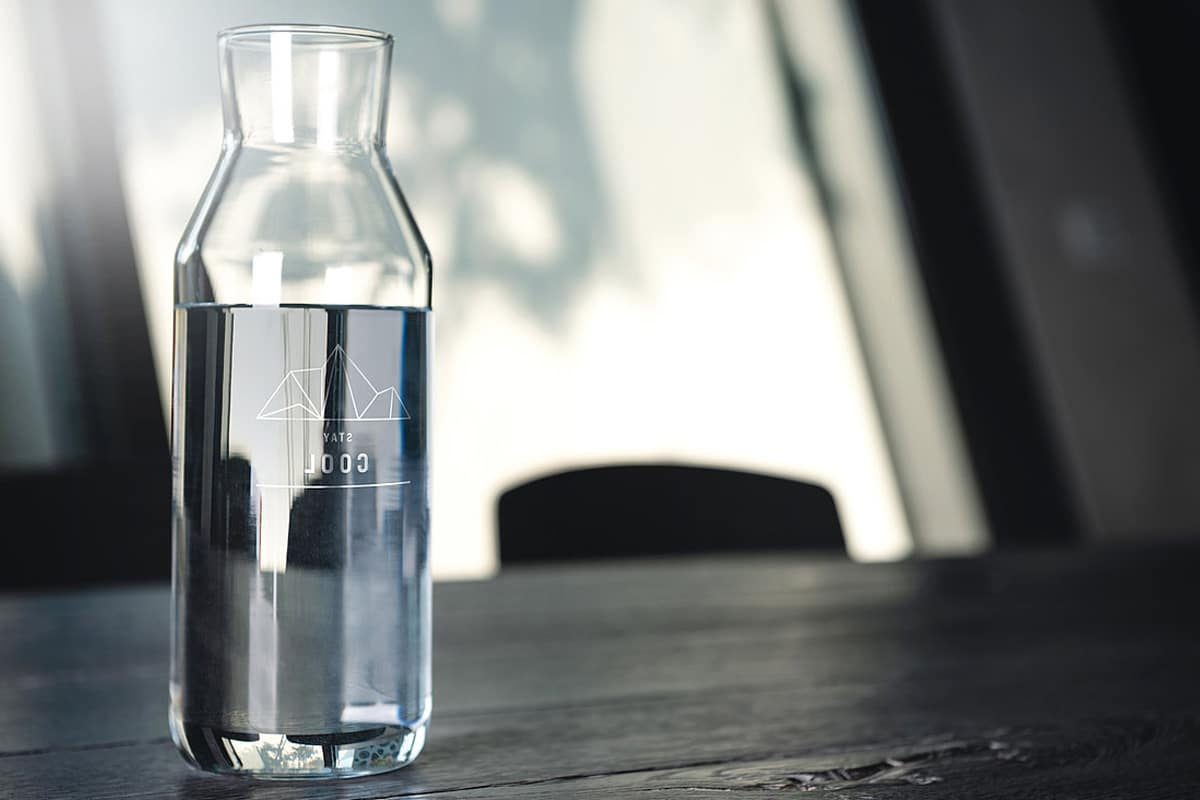
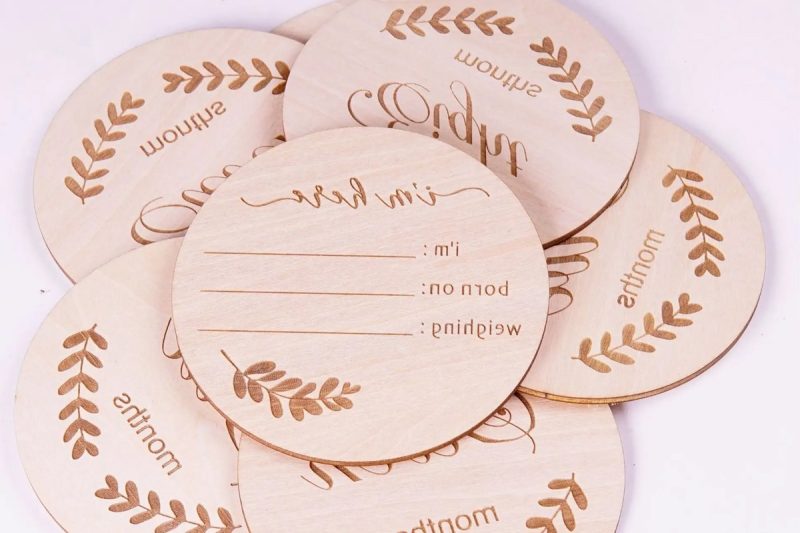
Lasertyp und -quelle
- Faserlaser: Aufgrund ihrer hohen Energiedichte und hervorragenden Fokussierungseigenschaften eignen sich Faserlasergeneratoren sehr gut zum Markieren von Metallmaterialien, insbesondere von Materialien wie Stahl, Aluminium und Kupfer. Faserlasermarkierung kann eine extrem hohe Präzision erreichen und wird häufig in hochpräzisen Anwendungen eingesetzt, die extrem feine Muster und Texte erfordern, wie z. B. das Markieren von elektronischen Komponenten, medizinischen Geräten und Autoteilen. Darüber hinaus haben Faserlaser einen geringen Energieverbrauch und eine lange Lebensdauer, was sie zur ersten Wahl für die Metallmarkierung macht.
- CO2-Laser: CO2-Laser werden hauptsächlich zum Markieren nichtmetallischer Materialien verwendet, insbesondere für Materialien wie Holz, Kunststoff, Leder und Papier. Mit einer Wellenlänge von 10,6 Mikrometern kann es die Energie nichtmetallischer Materialien effizient absorbieren und wird daher häufig in Branchen wie Verpackung, Bekleidung und Kunsthandwerk eingesetzt. Die Schneid- und Gravurfunktionen von CO2-Lasermarkierung Auch in der Werbeproduktion, Möbeldekoration und im Modellbau ist es hervorragend einsetzbar.
- Ultravioletter (UV) Laser: UV-Laser werden aufgrund ihrer kurzen Wellenlänge (normalerweise 355 nm) als Kaltlichtquellen bezeichnet. Im Vergleich zu anderen Lasertypen haben UV-Laser eine sehr kleine Wärmeeinflusszone, was bedeutet, dass thermische Verformungen und Schäden am Material während des Markierungsprozesses stark reduziert werden. Dadurch eignet er sich sehr gut für feine Markierungen, insbesondere auf wärmeempfindlichen Materialien wie Glas, Kunststoff und Keramik. UV-Lasermarkierungen werden häufig in hochpräzisen Branchen wie elektronischen Produkten, Kosmetikverpackungen und pharmazeutischen Etiketten verwendet und können extrem feine und klare Markierungseffekte erzielen.
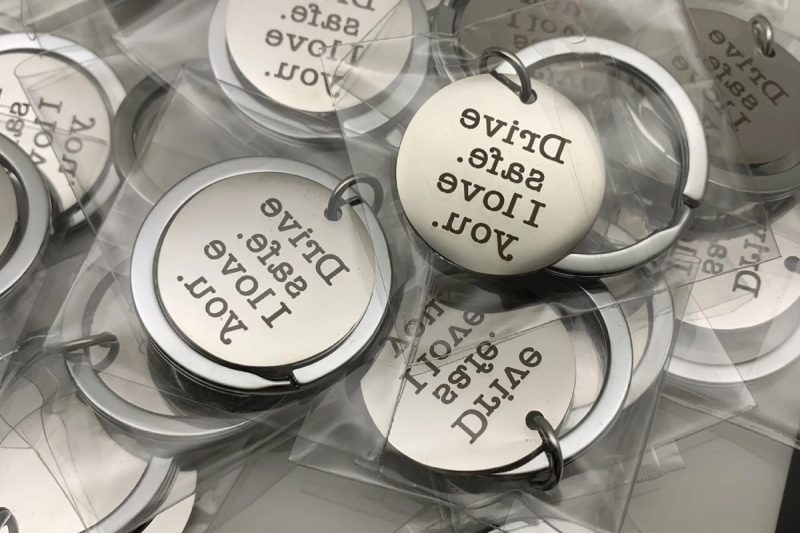
Einfluss von Materialeigenschaften
- Absorption und Reflektivität: Materialien haben unterschiedliche Absorptions- und Reflektionsfähigkeiten für Laser verschiedener Wellenlängen. Materialien mit hoher Absorption können Laserenergie besser absorbieren und bessere Markierungseffekte erzielen, während Materialien mit hoher Reflektivität eine große Menge Laserlicht reflektieren und die Markierungseffizienz verringern. Beispielsweise haben Metallmaterialien wie Aluminium und Kupfer eine hohe Reflektivität für Faserlaser, was zu einer unzureichenden oder unklaren Markierung führen kann. Aus diesem Grund ist es beim Markieren dieser Materialien mit hoher Reflektivität normalerweise erforderlich, die Laserparameter anzupassen oder Laser mit bestimmten Wellenlängen zu verwenden, um die Absorptionsrate zu verbessern und den idealen Markierungseffekt zu erzielen. Im Gegensatz dazu haben nichtmetallische Materialien wie Kunststoffe oder Glas eine hohe Absorptionsrate für CO2- und UV-Laser und die Markierungstiefe und der Kontrast sind leichter zu steuern.
- Wärmeleitfähigkeit: Die Wärmeleitfähigkeit des Materials beeinflusst direkt die Wärmeverteilung während des Markierungsprozesses. Materialien mit hoher Wärmeleitfähigkeit, wie Kupfer, Aluminium und andere Metalle, können die während des Markierungsprozesses erzeugte Wärme schnell ableiten, lokale Überhitzung reduzieren und ein Schmelzen oder Verbrennen der Materialoberfläche vermeiden. Solche Materialien erfordern während der Lasermarkierung normalerweise eine erhöhte Laserleistung oder eine längere Markierungszeit, um sicherzustellen, dass ausreichend Energie auf den Markierungsbereich angewendet wird. Bei Materialien mit geringer Wärmeleitfähigkeit, wie Kunststoff oder Holz, ist es schwierig, Wärme schnell abzuleiten, und während des Markierungsprozesses kommt es wahrscheinlich zu Überhitzung, was zu Verformungen oder Schäden führt. Daher ist es bei der Verarbeitung solcher Materialien normalerweise erforderlich, die Laserleistung zu reduzieren oder die Kühlmaßnahmen zu erhöhen, um eine Überhitzung zu vermeiden.
- Oberflächenbeschaffenheit: Auch die Oberflächenbeschaffenheit des Materials kann einen wichtigen Einfluss auf die Markierwirkung haben. Eine glatte, saubere Oberfläche sorgt dafür, dass der Laser gleichmäßig wirkt und ein klares und gleichmäßiges Markiermuster erzeugt. Eine raue oder beschichtete Oberfläche kann jedoch zu einer ungleichmäßigen Verteilung der Laserenergie führen, was zu einer unklaren Markierung oder unzureichendem Kontrast führt. Besonders wichtig sind dabei die Dicke und Gleichmäßigkeit der Beschichtung. Bei einer ungleichmäßigen Beschichtung kann der Laser an verschiedenen Stellen unterschiedliche Effekte erzeugen, was zu einer inkonsistenten Markierung führt. Eine ordnungsgemäße Oberflächenvorbereitung vor der Markierung, wie Reinigen, Schleifen oder Beschichten, kann die Markierwirkung deutlich verbessern.
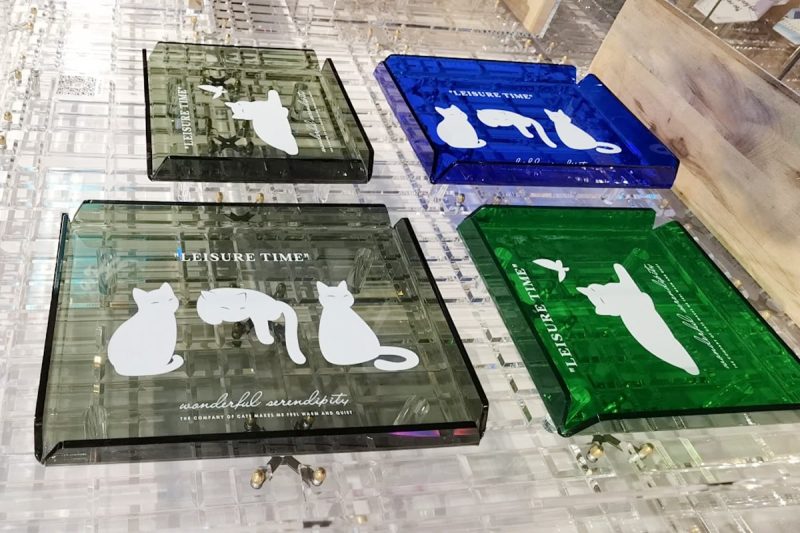
Einfluss der Laserparameter
- Leistungseinstellung: Die Laserleistung ist ein wichtiger Faktor, der die Tiefe und Wirkung der Markierung beeinflusst. Wenn die Leistungseinstellung zu hoch ist, ist die Laserenergie zu groß, was leicht zu übermäßiger Ablation, Schmelzen oder Verformung der Materialoberfläche führen kann, insbesondere bei wärmeempfindlichen Materialien wie Kunststoffen oder dünnen Metallen. Übermäßige Leistung kann auch raue und unebene Kanten der Markierung verursachen, was das Gesamtbild beeinträchtigt. Wenn die Leistung zu niedrig ist, reicht die Laserenergie nicht aus und kann nicht effektiv auf die Materialoberfläche einwirken, was zu unklaren oder sogar schwer erkennbaren Markierungen führt. Daher muss die Leistungseinstellung entsprechend den Materialeigenschaften und den spezifischen Anforderungen der Markierung genau angepasst werden, um sicherzustellen, dass eine ausreichende Markierungstiefe erreicht werden kann, ohne die Materialoberfläche zu beschädigen.
- Pulsfrequenz: Die Pulsfrequenz bezeichnet die Anzahl der vom Lasergenerator pro Sekunde abgegebenen Pulse, die einen wichtigen Einfluss auf die Geschwindigkeit und Oberflächenqualität der Markierung hat. Eine höhere Pulsfrequenz bedeutet, dass die Laserenergie gleichmäßiger verteilt ist, was zu einer glatteren Markierungsoberfläche beiträgt und für Anwendungen geeignet ist, die eine feine Markierung erfordern. Eine zu hohe Frequenz kann jedoch auch dazu führen, dass die Laserenergie zu stark gestreut wird, was sich auf die Tiefe und den Kontrast der Markierung auswirkt. Eine niedrigere Pulsfrequenz macht die Laserenergie konzentrierter, was für Szenen geeignet ist, die eine größere Markierungstiefe erfordern, kann jedoch zu einer leichten Rauheit auf der Oberfläche führen. Daher kann die Wahl der richtigen Pulsfrequenz je nach Material und Markierungsanforderungen ein Gleichgewicht zwischen Tiefe und Oberflächenbeschaffenheit herstellen.
- Markierungsgeschwindigkeit: Die Markierungsgeschwindigkeit bezieht sich auf die Geschwindigkeit, mit der sich der Laser auf der Oberfläche des Materials bewegt, was direkte Auswirkungen auf die Tiefe, Effizienz und Wirkung der Markierung hat. Höhere Markierungsgeschwindigkeiten können die Produktionseffizienz verbessern und sind für Verarbeitungsanforderungen im großen Maßstab geeignet. Mit zunehmender Geschwindigkeit bleibt der Laser jedoch kürzer auf dem Material und die Markierungstiefe nimmt ebenfalls ab, was die Klarheit und den Kontrast der Markierung beeinträchtigen kann. Bei Anwendungen, die eine tiefe Markierung oder höhere Präzision erfordern, ist es normalerweise erforderlich, die Markierungsgeschwindigkeit zu verringern, um sicherzustellen, dass der Laser genügend Zeit hat, effektiv mit dem Material zu interagieren. Die Geschwindigkeitseinstellung muss die Markierungsanforderungen und die Eigenschaften des Materials umfassend berücksichtigen, um ein Gleichgewicht zwischen Effizienz und Qualität zu erreichen.
- Brennweiteneinstellung: Die Genauigkeit der Laserbrennweite ist entscheidend für die Qualität der Markierung. Die Brennweite bezieht sich auf den Abstand zwischen dem Laserstrahl und der Oberfläche des Materials. Die Laserenergie wird bei der optimalen Brennweite konzentriert, wodurch klare und genaue Markierungseffekte auf der Oberfläche des Materials erzeugt werden können. Wenn die Brennweite nicht richtig eingestellt ist, wird die Energie des Laserstrahls gestreut, was zu verschwommenen und unscharfen Markierungen führt und es unmöglich ist, klare Muster oder Texte zu erzielen. Insbesondere bei feinen Markierungen hat selbst eine geringe Abweichung der Brennweite erhebliche Auswirkungen auf den Endeffekt. Das regelmäßige Kalibrieren des Fokus des Geräts und das Bestätigen der Genauigkeit der Brennweite vor dem Markieren sind wichtige Schritte, um die Konsistenz des Markierungseffekts sicherzustellen.
Generell ist die richtige Einstellung der Laserparameter entscheidend, um qualitativ hochwertige Lasermarkierungsergebnisse zu erzielen. Durch die richtige Einstellung von Leistung, Pulsfrequenz, Markierungsgeschwindigkeit und Brennweite können Klarheit, Tiefe und Kontrast der Markierung effektiv verbessert werden, wodurch sichergestellt wird, dass die Lasermarkierung bei verschiedenen Materialien und Anwendungen optimale Ergebnisse liefert.
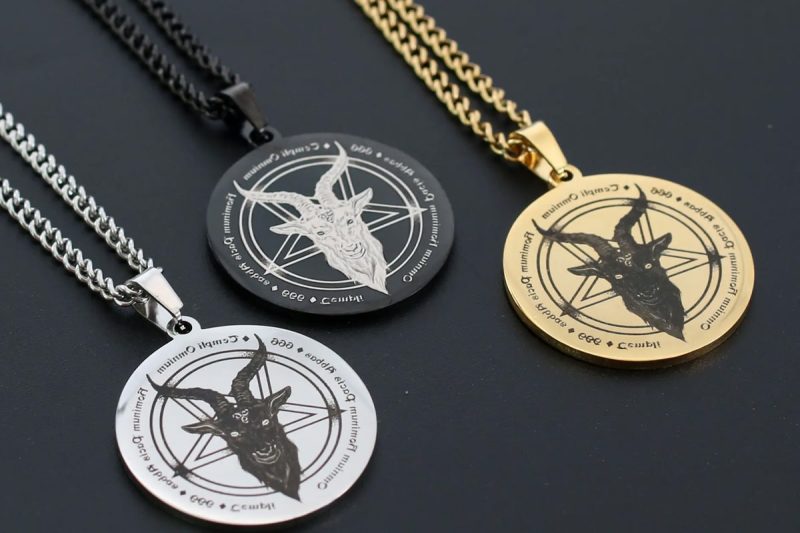
Einfluss der Umgebungsbedingungen
- Temperatur: Die Umgebungstemperatur hat einen direkten Einfluss auf den Betriebszustand der Laserbeschriftungsmaschine. Übermäßige Temperaturen können zu einer Überhitzung des Gerätes führen, insbesondere der Laserquelle und der elektronischen Komponenten. Überhitzung verringert die Arbeitseffizienz des Geräts und kann sogar zu Ausfällen oder Schäden führen. Darüber hinaus kann die Ausgangsleistung des Lasergenerators in einer Umgebung mit hohen Temperaturen instabil werden, was zu Schwankungen der Intensität des Laserstrahls während des Markierungsvorgangs führt und die Konsistenz und Klarheit der Markierung beeinträchtigt. Im Gegenteil, eine zu niedrige Temperatur kann auch den Start und den normalen Betrieb des Geräts beeinträchtigen, insbesondere in kalten Gegenden oder Jahreszeiten, in denen der Lasergenerator länger zum Aufwärmen braucht. Daher ist es für den stabilen Betrieb der Laserbeschriftungsmaschine entscheidend, die Umgebungstemperatur des Geräts innerhalb des vom Hersteller empfohlenen Bereichs (normalerweise 15 °C bis 30 °C) zu halten.
- Feuchtigkeit: Übermäßige Feuchtigkeit ist eine weitere große versteckte Gefahr, die die Leistung von Lasermarkierungsgeräten beeinträchtigt. Eine Umgebung mit hoher Luftfeuchtigkeit kann dazu führen, dass die optischen Komponenten der Lasermarkierungsmaschine feucht werden, wie z. B. Linsen, Linsen und andere wichtige Komponenten. Wenn diese optischen Komponenten feucht sind, wird der Laserstrahl während der Übertragung gestreut und gedämpft, was zu unklaren oder verschwommenen Markierungseffekten führt. Darüber hinaus kann hohe Luftfeuchtigkeit die Oxidation und Korrosion im Inneren des Geräts beschleunigen und die Lebensdauer des Geräts verkürzen. Um Feuchtigkeitsprobleme zu vermeiden, sollte das Markierungsgerät in einer Umgebung mit guter Feuchtigkeitskontrolle installiert werden, insbesondere in Regenzeiten oder feuchten Gebieten. Es wird empfohlen, Geräte wie Luftentfeuchter zu verwenden, um die Umgebungsfeuchtigkeit zwischen 40% und 60% zu halten und zu verhindern, dass die optischen Komponenten und Geräte nass werden.
- Sauberkeit: Die Sauberkeit der Arbeitsumgebung hat einen erheblichen Einfluss auf die Genauigkeit und Qualität der Lasermarkierung. Partikel wie Staub, Schmutz und Ölflecken können sich auf der Oberfläche des Markierungsmaterials oder den optischen Komponenten des Geräts ablagern und die Übertragung des Laserstrahls und die Genauigkeit der Brennweite beeinträchtigen, wodurch die Klarheit und der Kontrast der Markierung verringert werden. In einer Produktionsumgebung, insbesondere in einem Industriegebiet, befinden sich viele Staubpartikel in der Luft, die die Wechselwirkung zwischen dem Laserstrahl und der Oberfläche des Materials beeinträchtigen und zu einer ungleichmäßigen Markierung führen können. Um den besten Markierungseffekt zu gewährleisten, wird empfohlen, das Gerät, insbesondere die Linse und die optischen Komponenten, regelmäßig zu reinigen, um die Oberfläche des Markierungsmaterials sauber und staubfrei zu halten. Verwenden Sie während des Reinigungsvorgangs geeignete Reinigungswerkzeuge und -methoden, um ein Verkratzen der optischen Komponenten oder eine Beschädigung der Materialoberfläche zu vermeiden.
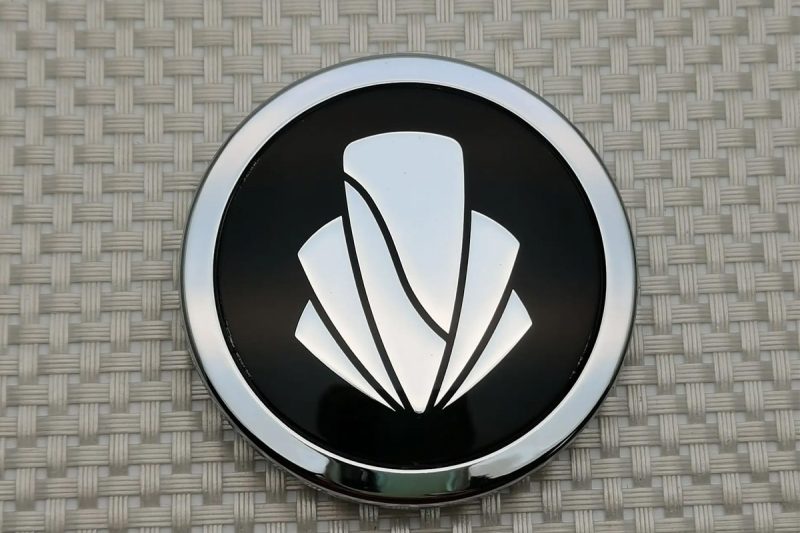
Der Einfluss optischer Komponenten
- Linsenqualität: Die Linse ist eine der wichtigsten optischen Komponenten im Lasersystem. Ihre Funktion besteht darin, den Laserstrahl zu fokussieren und ihn präzise auf die Oberfläche des Materials zu projizieren. Wenn die Linsenqualität schlecht ist, z. B. Kratzer, Staub oder unzureichende optische Leistung auf der Linsenoberfläche, weicht der Laserstrahl während des Fokussierungsprozesses ab oder verliert Energie, was die Genauigkeit und Klarheit der Markierung beeinträchtigt. Linsen von schlechter Qualität können zu verschwommenen Markierungen, Unschärfe oder ungleichmäßiger Energieverteilung führen, insbesondere in Fällen, in denen eine feine Verarbeitung erforderlich ist, erscheint der Markierungseffekt rau und ungleichmäßig. Daher ist die Auswahl hochwertiger optischer Linsen und deren regelmäßige Reinigung und Wartung, um ihre stabile optische Leistung sicherzustellen, der Schlüssel zur Gewährleistung der Markierungsgenauigkeit.
- Strahlübertragungssystem: Das Strahlübertragungssystem ist für die Übertragung des Lasers von der Laserquelle auf die Oberfläche des Markierungsmaterials verantwortlich. Während dieses Vorgangs muss die Energie des Lasers effizient und ohne Energieverlust oder Strahlstreuung übertragen werden. Jeder Verlust während des Übertragungsvorgangs beeinträchtigt die Intensität und Fokussierungswirkung des Lasers, was zu einer unzureichenden Markierungstiefe oder verringerter Klarheit führt. Um die Effizienz der Strahlübertragung sicherzustellen, müssen die verschiedenen Komponenten des Übertragungssystems, wie Reflektoren und optische Übertragungsfasern, sehr sauber und intakt gehalten werden. Staub, Schmutz oder Schäden an den optischen Komponenten führen dazu, dass der Strahl gestreut und schlecht reflektiert wird, was sich auf die Markierungsergebnisse auswirkt. Ein effizientes und verlustfreies Strahlübertragungssystem kann die Stabilität und Konsistenz des Markierungsprozesses gewährleisten und sicherstellen, dass jedes Mal der ideale Effekt erzielt werden kann.
- Galvanometerscanner: Der Galvanometerscanner ist eine Schlüsselkomponente, die die schnelle Bewegung und präzise Positionierung des Laserstrahls steuert, was direkt die Geschwindigkeit, Genauigkeit und Konsistenz des Markierungsmusters bestimmt. Der Galvanometerscanner passt die Richtung des Laserstrahls durch einen Hochgeschwindigkeitsreflektor an, um das gewünschte Muster oder Zeichen auf die Oberfläche des Materials zu zeichnen. Seine Scangeschwindigkeit und -genauigkeit sind für den Markierungseffekt besonders wichtig. Hochpräzise Galvanometerscanner können die präzise Positionierung des Laserstrahls in komplexen oder winzigen Mustern sicherstellen, um Abweichungen in Linien oder Mustern zu vermeiden. Hochgeschwindigkeits-Galvanometerscanner können die Markierungseffizienz verbessern und sind für die Anforderungen der Massenproduktion geeignet. Eine zu schnelle Scangeschwindigkeit kann jedoch zu einer ungleichmäßigen Energieverteilung führen, was sich auf die Tiefe und den Kontrast der Markierung auswirkt. Daher muss neben der Sicherstellung der Geschwindigkeit auch sichergestellt werden, dass die Genauigkeit des Galvanometers in einem angemessenen Bereich bleibt. Die Qualität und Leistung des Galvanometerscanners sind entscheidend für die Stabilität des Markierungseffekts. Daher sollte ein Hochleistungs-Galvanometersystem kalibriert ausgewählt und regelmäßig gewartet werden, um sicherzustellen, dass es auch beim Hochgeschwindigkeitsscannen genaue Markierungseffekte erzielen kann.
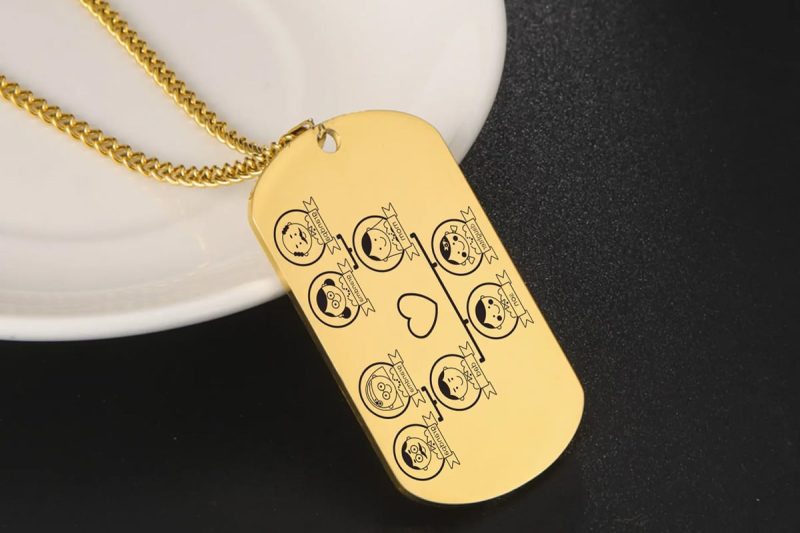
Der Einfluss von Software und Steuerungssystemen
- Markierungssoftware: Markierungssoftware ist ein wichtiges Werkzeug zur Steuerung von Lasermarkierungsgeräten. Sie ist für die Einstellung und Anpassung der Parameter des Lasergenerators wie Laserleistung, Markierungsgeschwindigkeit, Pulsfrequenz usw. verantwortlich. Hochwertige Software kann diese wichtigen Parameter nicht nur genau steuern, sondern bietet auch umfangreiche Markierungsfunktionen wie Musterdesign, Schriftartauswahl, Barcode- und QR-Code-Generierung usw. Darüber hinaus kann Markierungssoftware mehrstufige Markierungen durchführen und verschiedene Verarbeitungsanforderungen verschiedener Materialien unterstützen, wie z. B. hochpräzise und unterschiedlich tiefe Markierungen auf Metall, Kunststoff, Glas und anderen Materialien. Fortschrittliche Markierungssoftware verfügt normalerweise über eine benutzerfreundliche Oberfläche, vereinfacht den Bedienungsprozess, ermöglicht es den Bedienern, sich schnell mit dem System vertraut zu machen und es zu beherrschen, reduziert menschliche Bedienungsfehler und verbessert so die Produktionseffizienz und Markierungsqualität. Gleichzeitig ist auch die Aktualisierbarkeit der Software sehr wichtig. Mit der Entwicklung der Technologie und den Änderungen der Marktnachfrage muss die Markierungssoftware kontinuierlich aktualisiert und optimiert werden, um sich an neue Markierungsanforderungen anzupassen.
- Bewegungssteuerungssystem: Das Bewegungssteuerungssystem ist die Kernkomponente der Laserbeschriftungsmaschine, die die koordinierte Bewegung zwischen dem Laserkopf und dem Werkstück steuert. Es stellt sicher, dass während des Markierungsvorgangs der Laserkopf und das zu bearbeitende Werkstück genau synchronisiert werden können, sodass sich der Laserstrahl gemäß der festgelegten Flugbahn auf der Materialoberfläche bewegt. Diese Synchronisierung ist wichtig, um Konsistenz und Genauigkeit des Markierungsmusters zu erreichen. Bewegungssteuerungssysteme umfassen normalerweise Hardware wie Motoren, Sensoren und Steuerungen und arbeiten mit Markierungssoftware zusammen, um eine Echtzeitüberwachung und -anpassung zu ermöglichen. Bei hochpräzisen Markierungen, insbesondere wenn komplexe Muster auf großen Materialflächen markiert werden müssen, sind die Genauigkeit und Reaktionsgeschwindigkeit des Bewegungssteuerungssystems besonders wichtig. Wenn das Bewegungssteuerungssystem nicht empfindlich genug ist, kann der Lasermarkierungskopf abweichen, was zu Problemen wie Musterverformungen und ungleichmäßigen Linien führt. Daher ist ein stabiles und effizientes Bewegungssteuerungssystem einer der Schlüsselfaktoren, um die Konsistenz und Klarheit der Lasermarkierung sicherzustellen.
- Automatisierung: Ein hochautomatisiertes Lasermarkierungssystem kann die Produktionseffizienz erheblich verbessern, Fehler bei der menschlichen Bedienung reduzieren und sicherstellen, dass jede Produktcharge konsistente Markierungseffekte erzielt. Durch die Einführung eines automatisierten Steuerungssystems können Lasermarkierungsgeräte nahtlos an die Produktionslinie angeschlossen werden, um Chargen- und kontinuierliche Markierungsvorgänge zu ermöglichen. Beispielsweise kann das automatisierte System das Werkstück automatisch identifizieren und lokalisieren, die Höhe und Brennweite des Lasermarkierungskopfes anpassen und sicherstellen, dass jede Markierung unter optimalen Bedingungen durchgeführt wird. Das automatisierte System kann auch das Markierungsmuster und die Parameter verschiedener Chargen ohne menschliches Eingreifen automatisch ändern, was die Produktionsflexibilität erheblich verbessert. Darüber hinaus kann das Automatisierungssystem mit anderen Fabrikmanagementsystemen verbunden werden, um eine Echtzeitüberwachung und -analyse von Produktionsdaten zu erreichen und Unternehmen dabei zu helfen, Produktionsprozesse zu optimieren, die Produktqualität zu verbessern und Kosten zu senken. Das automatisierte Markierungssystem kann auch den Bedienereinsatz reduzieren und die Arbeitskosten senken, insbesondere in Produktionsumgebungen mit hoher Nachfrage und hohem Volumen, in denen seine Vorteile besonders deutlich werden.
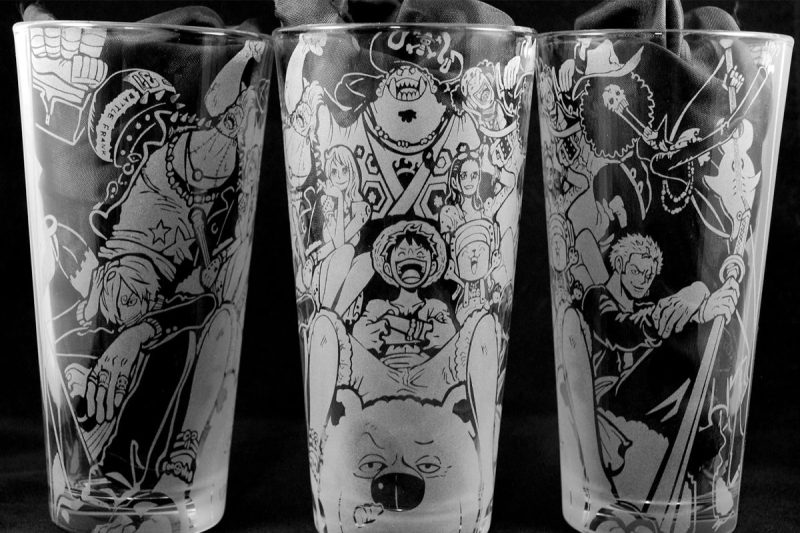
Wirkung des Kühlsystems
- Luftkühlung: Luftkühlungssysteme werden häufig für Lasergeräte mit geringer Leistung verwendet, wie beispielsweise für einige kleine Faserlaserbeschriftungsmaschinen. Diese Kühlmethode entfernt Wärme vom Lasergenerator und anderen wichtigen Komponenten durch Luftzirkulationsvorrichtungen wie Lüfter. Aufgrund der einfachen Struktur und der geringen Wartungskosten des Luftkühlungssystems eignet es sich für Anwendungsszenarien mit geringen Wärmeableitungsanforderungen. Das Luftkühlungssystem hat die Vorteile eines geringen Platzbedarfs und eines kompakten Designs. Es wird normalerweise ohne externe Kühlgeräte in das Gerät integriert. Daher wird es häufig in kleinen Laserbeschriftungsmaschinen mit begrenztem Volumen verwendet. Der Wärmeableitungseffekt der Luftkühlung ist jedoch relativ schwach und kann die große Wärmemenge, die von Hochleistungslasergeneratoren erzeugt wird, nicht bewältigen. Wenn Hochleistungsgeräte mit Luft gekühlt werden, kann es zu einem Wärmestau kommen, der die Leistung und Lebensdauer des Lasergenerators beeinträchtigt. Daher eignet sich das Luftkühlungssystem hauptsächlich für Lasergeräte mit geringer Leistung und geringen Wärmeableitungsanforderungen.
- Wasserkühlsystem: Im Vergleich zur Luftkühlung eignet sich das Wasserkühlsystem für Hochleistungslasermarkierungsgeräte, insbesondere wenn ein langfristiger Dauerbetrieb erforderlich ist, da es eine effektivere Wärmeableitung bietet. Das Wasserkühlsystem zirkuliert das Kühlmittel (normalerweise Wasser oder Kühlmittel) über eine Wasserpumpe in die Nähe des Lasergenerators und anderer wärmeerzeugender Komponenten und entfernt die Wärme durch die effiziente Wärmeübertragung des Wassers schnell. Im Vergleich zur Luftkühlung verfügt das Wasserkühlsystem über eine höhere Wärmekapazität und Leitfähigkeit, wodurch sichergestellt werden kann, dass das Gerät in Umgebungen mit hohen Temperaturen oder unter Arbeitsbedingungen mit hoher Intensität stabil betrieben werden kann, und Leistungsabnahme oder Verschlechterung der Markierungsqualität durch Überhitzung des Lasergenerators vermieden werden. Darüber hinaus kann das Wasserkühlsystem Temperaturschwankungen kontrollieren und sicherstellen, dass der Lasergenerator immer im optimalen Temperaturbereich arbeitet, wodurch die Lebensdauer des Geräts verlängert wird.
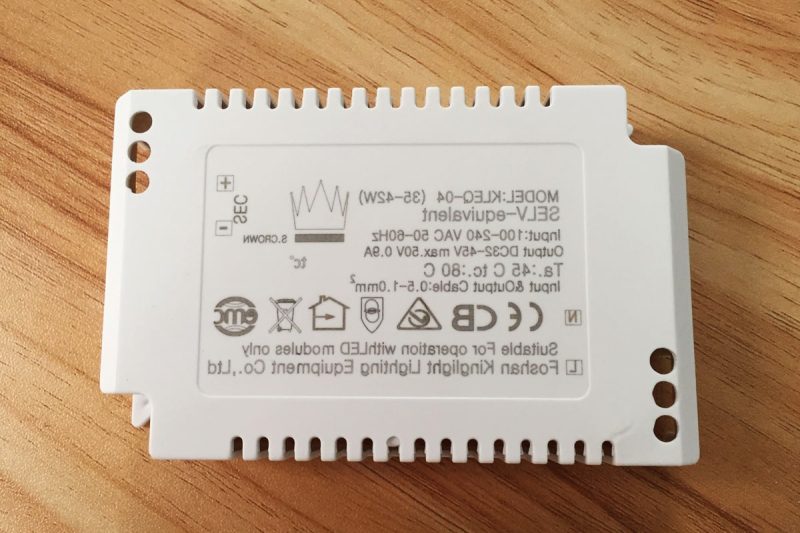
Fähigkeiten und Schulung des Bedieners
- Fachwissen: Lasermarkierer müssen über fundiertes Fachwissen verfügen, insbesondere über Kenntnisse der unterschiedlichen Materialeigenschaften und Laserparameter. Unterschiedliche Materialien weisen unterschiedliche Absorptionsraten, Reflexionsvermögen und Wärmeleitfähigkeit von Lasern auf, sodass die Bediener die Laserparameter wie Laserleistung, Markiergeschwindigkeit, Pulsfrequenz usw. entsprechend den Materialeigenschaften angemessen anpassen müssen. Beispielsweise erfordern Metallmaterialien normalerweise Faserlasergeneratoren mit höherer Leistung, während nichtmetallische Materialien wie Kunststoffe oder Glas möglicherweise besser für UV-Laser oder CO2-Lasergeneratoren geeignet sind. Wenn der Bediener nicht über ausreichende Kenntnisse der Materialeigenschaften und Lasergeneratortypen verfügt, kann dies zu unbefriedigenden Markierergebnissen, ungleichmäßiger Tiefe, Unschärfe und Einbrennen führen. Durch systematisches Training können Bediener die Markieranforderungen verschiedener Materialien meistern und sicherstellen, dass jede Markierung die besten Ergebnisse erzielt.
- Kalibrierung und Wartung: Bei Lasermarkierungsgeräten kann es bei längerem Gebrauch zu Verschleiß oder Abweichungen wichtiger Komponenten wie Linsen, Galvanometern und Strahlübertragungssystemen kommen. Daher sind eine regelmäßige Kalibrierung und Wartung der Geräte unerlässlich, um sicherzustellen, dass die Strahlqualität und Markierungsgenauigkeit der Geräte immer im besten Zustand sind. Die Bediener müssen in der Lage sein, tägliche Inspektionen und einfache Fehlerbehebungen der Geräte durchzuführen, um Probleme umgehend zu erkennen und zu lösen. Beispielsweise beeinträchtigen die Leistungsdämpfung des Lasergenerators, die verringerte Genauigkeit der Galvanometerabtastung und die Verschmutzung der optischen Komponenten den Markierungseffekt. Gut geschulte Bediener können die Geräte regelmäßig kalibrieren, um den stabilen Betrieb der Lasermarkierungsgeräte sicherzustellen und Produktionsstagnation oder Qualitätseinbußen aufgrund von Geräteausfällen oder Parameterabweichungen zu reduzieren. Darüber hinaus kann die Wartung nicht nur die Lebensdauer der Geräte verlängern, sondern auch unerwartete Ausfallzeiten oder größere Ausfälle vermeiden und Reparaturkosten senken.
- Bedienkompetenz und Sicherheitsbewusstsein: Obwohl die Bedienung von Lasermarkierungsgeräten mittlerweile einfach ist, müssen die Bediener dennoch über ein gewisses Maß an Kompetenz verfügen, um die Geräte effizient bedienen zu können. Die Bediener sollten die Betriebsabläufe verschiedener Markierungsaufgaben bei der Arbeit beherrschen, z. B. das Einstellen des Markierungspfads, das Anpassen der Brennweite und das Auswählen der geeigneten Markierungsgeschwindigkeit und -leistung. Erfahrene Bediener können Parameter schnell beurteilen und anpassen, um unterschiedliche Markierungsanforderungen zu erfüllen und so die Produktionseffizienz zu verbessern. Darüber hinaus müssen die Bediener auch ein gewisses Maß an Sicherheitsbewusstsein haben. Bei der Bedienung von Lasergeräten können während des Betriebs bestimmte Sicherheitsrisiken wie Laserstrahlung und Wärmeentwicklung auftreten. Bediener, die eine professionelle Schulung erhalten haben, können Sicherheitsprobleme aufgrund unsachgemäßer Bedienung wirksam vermeiden und die Sicherheit der Produktionsumgebung gewährleisten.
- Kontinuierliches Lernen und Technologie-Updates: Die Lasermarkierungstechnologie wird ständig aktualisiert und es werden auch neue Markierungsgeräte und Softwarefunktionen eingeführt. Daher müssen die Bediener weiterhin neue Technologien lernen und sich an sie anpassen, den Betrieb neuer Lasergeneratoren und Markierungssoftware durch Schulungen beherrschen und die neuesten Prozessverbesserungen verstehen. Kontinuierliches Lernen der Bediener kann Unternehmen dabei helfen, ihre Wettbewerbsfähigkeit aufrechtzuerhalten, die Markierungseffizienz und Produktqualität zu verbessern und sich ändernden Marktanforderungen gerecht zu werden.
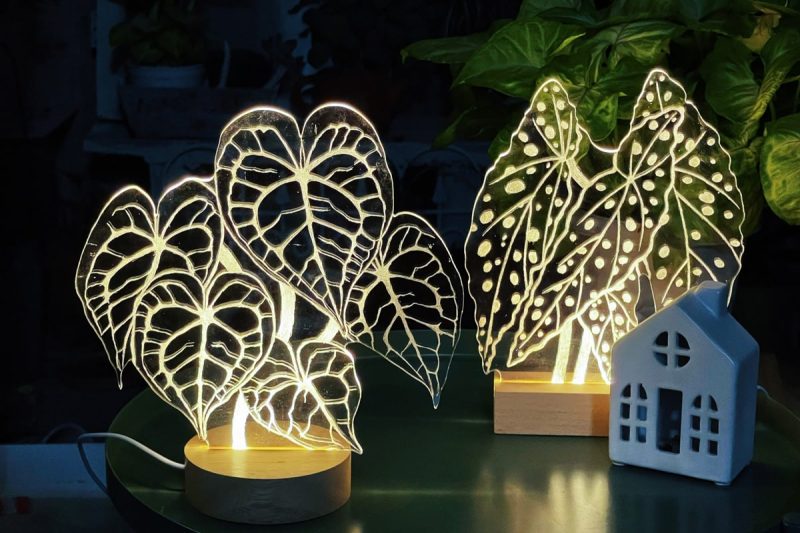
Der Einfluss von Materialhandhabung und Vorrichtung
Vorrichtung
- Gewährleistung der Werkstückstabilität: Präzises Klemmen und Fixieren verhindert, dass sich das Werkstück während des Markiervorgangs leicht bewegt, und gewährleistet so eine genaue Positionierung und Konsistenz des Markiermusters. Dies ist besonders wichtig für hochpräzise Markieraufgaben, wie das Markieren winziger Zeichen oder komplexer Muster.
- Fehler reduzieren: Eine stabile Vorrichtung kann Markierungsfehler, die durch Änderungen der Position des Werkstücks verursacht werden, wirksam reduzieren und so die Produktkonsistenz und -qualität verbessern. Insbesondere bei der Produktion in großem Maßstab können konsistente Vorrichtungseinstellungen sicherstellen, dass jedes Werkstück unter den gleichen Bedingungen markiert wird.
- Anpassung an unterschiedliche Werkstücke: Das Design der Vorrichtung sollte Werkstücke unterschiedlicher Form und Größe berücksichtigen, damit sie flexibel in verschiedenen Produktionsaufgaben eingesetzt werden kann. Die Vorrichtung sollte über eine Schnellverstellfunktion verfügen, damit der Bediener sie entsprechend den unterschiedlichen Werkstückanforderungen einstellen und so die Produktionseffizienz verbessern kann.
Material vorbereitung
- Reinigung: Vor dem Markieren ist die Sauberkeit der Materialoberfläche von entscheidender Bedeutung. Verunreinigungen wie Schmutz, Fett und Staub können die Übertragung des Laserstrahls beeinträchtigen, was zu verschwommenen und ungleichmäßigen Markierungsmustern führt. Durch die Verwendung geeigneter Reinigungsmethoden wie Ultraschallreinigung oder chemischer Reinigung können Oberflächenverunreinigungen wirksam entfernt und die Klarheit und Konsistenz der Lasermarkierung sichergestellt werden.
- Behandlung: Einige Materialien erfordern möglicherweise eine zusätzliche Oberflächenbehandlung wie Schleifen, Sandstrahlen oder chemische Behandlung, um ihre Oberflächenbeschaffenheit und Laserhaftung zu verbessern. Diese Behandlungsschritte können die Unebenheit der Materialoberfläche verringern und den Markierungseffekt verbessern, insbesondere in Anwendungsszenarien, in denen eine hohe Glätte erforderlich ist.
- Inspektion: Vor dem Markieren sollte die Materialoberfläche überprüft werden, um sicherzustellen, dass sie den Markierungsanforderungen entspricht. Materialien mit offensichtlichen Mängeln oder unebenen Oberflächen erfordern möglicherweise eine zusätzliche Behandlung, um den endgültigen Markierungseffekt nicht negativ zu beeinflussen.
Stapelverarbeitung
- Standardisierung: Um bei der Massenproduktion konsistente Markierungsergebnisse zu erzielen, müssen standardisierte Betriebsverfahren und Vorrichtungsdesigns übernommen werden. Durch Standardisierung können Markierungsfehler reduziert werden, die durch Betriebsunterschiede oder inkonsistente Werkstückpositionen verursacht werden.
- Automatisierung: In der Massenproduktion kann der Einsatz von Automatisierungssystemen die Produktionseffizienz und -konsistenz erheblich verbessern. Automatisierte Systeme können die Aufgabe der Markierung großer Stückzahlen von Werkstücken schnell und effizient erledigen und sicherstellen, dass jedes Werkstück unter den gleichen Bedingungen verarbeitet wird, wodurch menschliche Fehler und Produktionsschwankungen reduziert werden.
- Qualitätskontrolle: Bei der Massenproduktion müssen strenge Qualitätskontrollmaßnahmen durchgeführt werden, darunter regelmäßige Inspektionen und Tests, um sicherzustellen, dass jede Produktcharge den Qualitätsstandards entspricht. Durch die Echtzeitüberwachung des Markierungseffekts können potenzielle Probleme umgehend erkannt und behoben werden, um die Produktkonsistenz und -stabilität sicherzustellen.
Zusammenfassend lässt sich sagen, dass Vorrichtungsdesign, Materialvorbereitung und Stapelverarbeitung wichtige Faktoren sind, die die Qualität der Lasermarkierung beeinflussen. Durch die Optimierung der Stabilität der Vorrichtung, die Verbesserung der Sauberkeit und Konsistenz der Materialoberfläche sowie die Implementierung von Standardisierung und Automatisierung in der Stapelproduktion können Unternehmen eine hohe Präzision, hohe Effizienz und hohe Qualität des Markierungsprozesses sicherstellen.
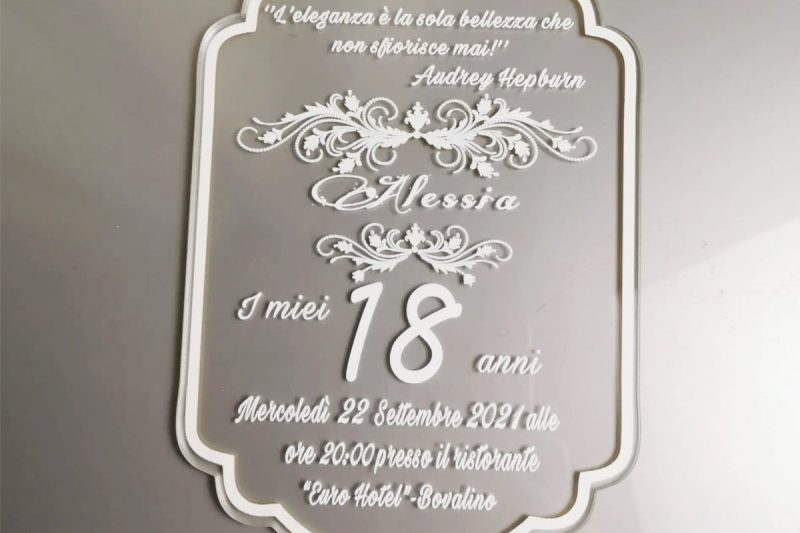
Einfluss anwendungsspezifischer Faktoren
Markierungstiefe
- Tiefenanforderungen: Bei einigen speziellen Anwendungen, wie z. B. bei Fertigungs- und Industrieteilen, kann eine tiefere Markierung erforderlich sein, um sicherzustellen, dass die Markierung dauerhaft ist und bei längerem Gebrauch lesbar bleibt. Beispielsweise erfordern Teile und Werkzeuge in der Luft- und Raumfahrt oft eine tiefere Markierung, um in Umgebungen mit hoher Reibung und rauen Bedingungen lesbar zu bleiben. Tiefe Markierungen tragen nicht nur zur Verbesserung der Haltbarkeit der Markierung bei, sondern erhöhen auch ihre Verschleißfestigkeit.
- Oberflächenmarkierung: Im Gegensatz dazu reicht für einige Anwendungen, die nur eine Oberflächenmarkierung erfordern, wie z. B. Etiketten für Verbraucherprodukte oder dekorative Markierungen, eine geringere Markierungstiefe aus. In diesem Fall kann eine geringere Markierungstiefe den Materialverlust und die Verarbeitungskosten verringern und gleichzeitig die Lesbarkeitsanforderungen der Markierung erfüllen.
Markierungskontrast
- QR-Codes und Barcodes: Für maschinenlesbare Markierungen wie QR-Codes und Barcodes ist ein hoher Kontrast unerlässlich. Markierungen mit hohem Kontrast sorgen dafür, dass Scangeräte Informationen genau lesen können und Lesefehler aufgrund verschwommener Markierungen oder unzureichenden Kontrasts vermieden werden. Durch die Verwendung geeigneter Laserparameter und Materialverarbeitungstechnologie kann der Kontrast der Markierung erhöht werden, um eine zuverlässige Informationsübertragung zu gewährleisten.
- Visuelle Markierung: Hoher Kontrast ist ebenso wichtig bei einigen Anwendungen, die eine manuelle Identifizierung erfordern, wie z. B. bei Produktnummern, Markenlogos usw. Eine klare Markierung kann die Erkennungseffizienz und -genauigkeit verbessern und die Möglichkeit einer Fehlidentifizierung verringern. In diesen Fällen muss die Markierungsmaschine die Parameter entsprechend den Eigenschaften verschiedener Materialien anpassen, um die Klarheit und Lesbarkeit der Markierung sicherzustellen.
Haltbarkeit der Markierung
- Raue Umgebungen: In einigen industriellen Anwendungen muss die Markierung rauen Umgebungen wie hohen Temperaturen, chemischer Korrosion und ultravioletter Strahlung standhalten. Beispielsweise sind Autoteile und mechanische Geräte während des Gebrauchs verschiedenen äußeren Einflüssen ausgesetzt, weshalb die Markierung eine hohe Haltbarkeit und Widerstandsfähigkeit gegen Verlust aufweisen muss. Die Wahl des richtigen Lasertyps und Materialverarbeitungsprozesses kann die Haltbarkeit der Markierung verbessern und sicherstellen, dass die Markierung bei langfristigem Gebrauch klar und lesbar bleibt.
- Langfristige Nutzung: Bei einigen Markierungen, die für lange Zeit erhalten bleiben müssen, wie Seriennummern auf elektronischen Komponenten oder Logos auf medizinischen Geräten, ist die Haltbarkeit ebenso wichtig. Die Laserbeschriftungsmaschine muss die Laserparameter anpassen, um sicherzustellen, dass die Markierung bei langfristiger Nutzung nicht verblasst, sich abnutzt oder verloren geht, um ihren ursprünglichen Zustand und ihre Funktion beizubehalten.
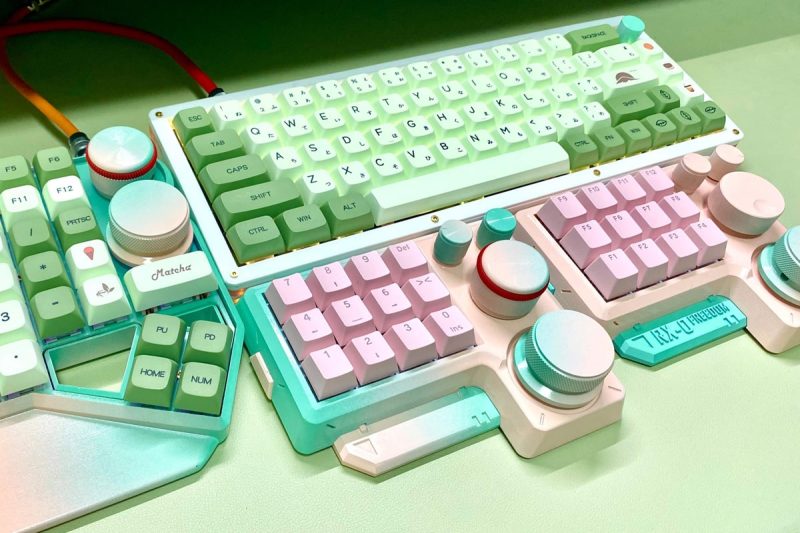
Zusammenfassen
- Die Wahl der Laserquelle bestimmt direkt die anwendbaren Materialien und Markierungsergebnisse. Beispielsweise eignen sich Faserlaser für Metallmaterialien, CO2-Laser für nichtmetallische Materialien und Ultraviolettlaser (UV) für Anwendungen, die eine feine Markierung erfordern.
- Materialeigenschaften wie Absorption, Reflexion und Oberflächenbeschaffenheit beeinflussen die Übertragung des Laserstrahls und den endgültigen Markierungseffekt. Materialhandhabung und Oberflächenvorbereitung wirken sich ebenfalls direkt auf die Markierungsqualität aus.
- Zu den Laserparametern gehören Leistungseinstellungen, Pulsfrequenz, Markierungsgeschwindigkeit und Brennweiteneinstellung, die genau eingestellt werden müssen, um eine klare und konforme Markierung zu gewährleisten.
- Umgebungsbedingungen wie Temperatur, Feuchtigkeit und Sauberkeit beeinflussen die Stabilität des Geräts und die Qualität des Laserstrahls.
- Die Leistung optischer Komponenten wie Linsenqualität, Strahlführungssystem und Galvanometerscanner steht ebenfalls in direktem Zusammenhang mit der Genauigkeit und Konsistenz der Markierung.
- Die Qualität von Software und Steuerungssystemen bestimmt die Genauigkeit der Markierung und die Benutzerfreundlichkeit. Hervorragende Software und Automatisierungssysteme können die Effizienz und Qualität der Markierung verbessern.
- Das Kühlsystem ist für den stabilen Betrieb von Lasergeräten von entscheidender Bedeutung. Ein effizientes Kühlsystem kann die Lebensdauer des Geräts verlängern und die Geräteleistung aufrechterhalten.
- Die Fähigkeiten und die Schulung des Bedieners sind die Grundlage für die Gewährleistung der Markierungsqualität. Ein professioneller Bediener kann die Geräteparameter richtig einstellen und regelmäßige Wartungsarbeiten durchführen, um die optimale Leistung des Geräts sicherzustellen.
- Materialhandhabung und Vorrichtungsdesign sind ebenfalls wichtige Faktoren, die den Markierungseffekt beeinflussen. Stabile Vorrichtungen und ordnungsgemäße Materialhandhabung können die Konsistenz und Genauigkeit der Markierung verbessern.
- Anwendungsspezifische Faktoren wie Markierungstiefe, Kontrast und Haltbarkeit. Je nach Anwendungsanforderungen sind auch die Markierungsqualitätsstandards unterschiedlich.
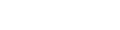
- [email protected]
- [email protected]
- +86-19963414011
- Nr. 3 Zone A, Industriegebiet Lunzhen, Stadt Yucheng, Provinz Shandong.