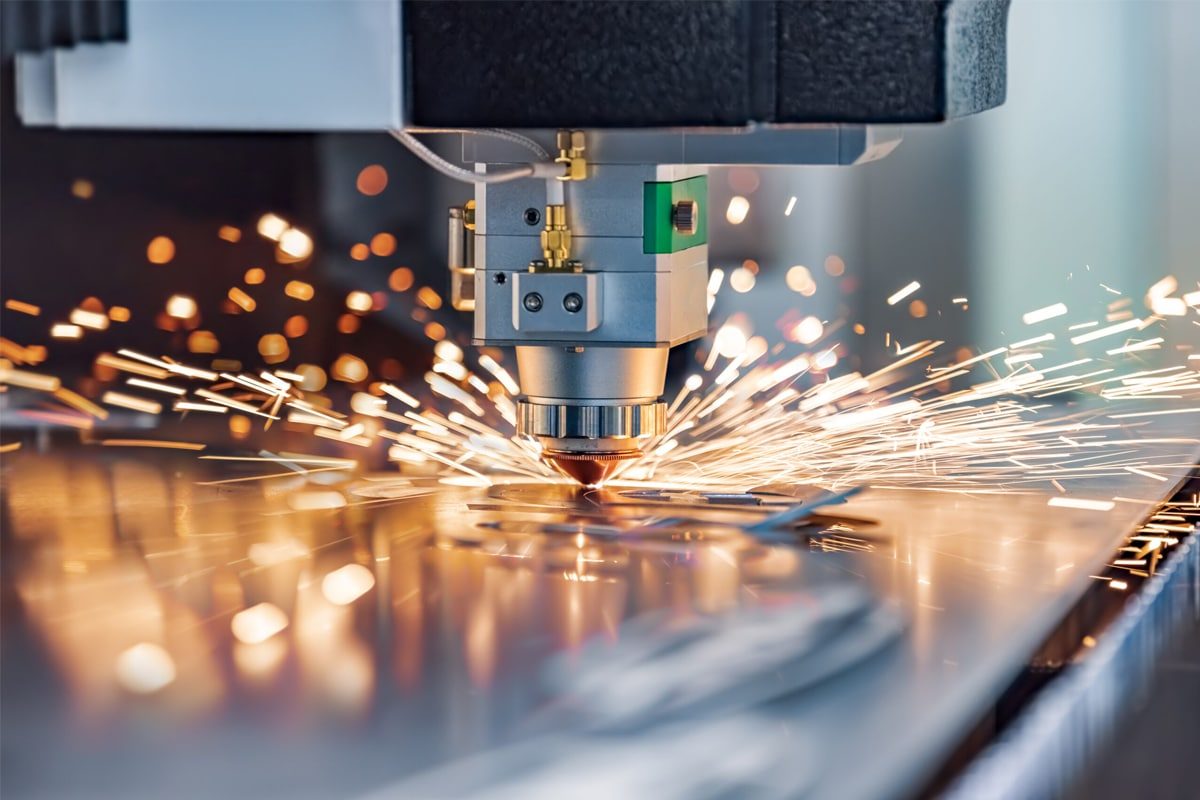
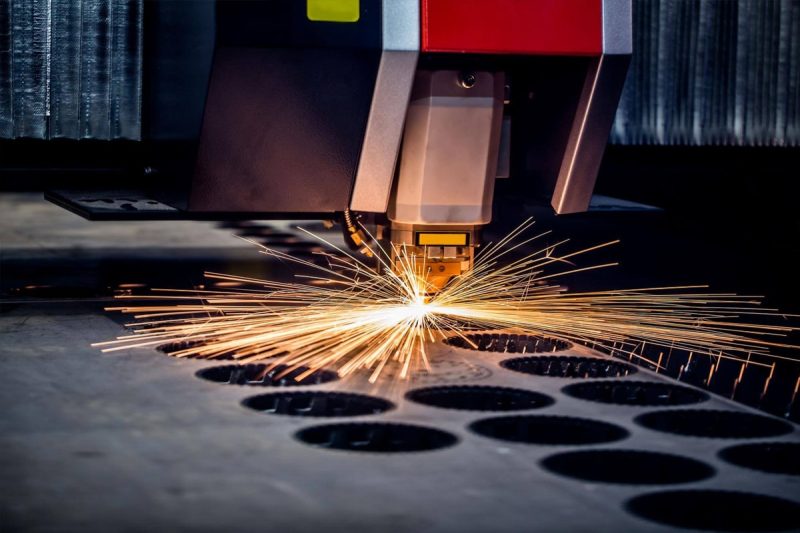
Überblick über die Laserschneidtechnologie
So funktioniert das Laserschneiden
Arten von Laserschneidmaschinen
- Faserlaser-Schneidemaschinen: Faserlaser verwenden mit Seltenerdelementen dotierte optische Fasern, um den Laserstrahl zu verstärken, was sie besonders effektiv zum Schneiden von Metallen macht. Faserlaser sind ideal zum Schneiden reflektierender Materialien wie Aluminium, Kupfer und Messing. Sie sind energieeffizient und bieten schnellere Schneidgeschwindigkeiten für dünne und mitteldicke Metalle.
- CO2-Laserschneidmaschinen: CO2-Laser verwenden Kohlendioxidgas als Lasermedium und eignen sich daher gut zum Schneiden nichtmetallischer Materialien wie Holz, Acryl, Stoff und Kunststoff. Aufgrund ihrer hochwertigen Kantenverarbeitung werden sie häufig zum Gravieren und Schneiden in Branchen wie Beschilderung, Dekoration und Textilien verwendet.
Vorteile des Laserschneidens
Das Laserschneiden bietet mehrere Vorteile, die es in vielen Branchen zur bevorzugten Wahl gemacht haben:
- Präzision und Genauigkeit: Durch Laserschneiden werden feine Details und enge Toleranzen erreicht, ideal für komplizierte Designs und präzise Teile.
- Vielseitigkeit: Das Laserschneiden ist mit einer großen Bandbreite an Materialien kompatibel, darunter Metalle, Nichtmetalle und Verbundwerkstoffe, und kommt so den unterschiedlichsten Branchen entgegen.
- Geschwindigkeit und Effizienz: Das Laserschneiden ermöglicht eine schnelle Verarbeitung mit minimaler Einrichtungszeit und ist damit schneller als herkömmliche Schneidemethoden, insbesondere in Umgebungen mit hoher Produktion.
- Minimaler Abfall: Beim Laserschneiden wird durch den fokussierten Strahl und die optimierten Schneidpfade der Materialabfall minimiert, was zu Kosteneinsparungen und weniger Materialverlust führt.
- Hochwertige Kantenbearbeitung: Durch das Laserschneiden ist eine Nachbearbeitung häufig nicht erforderlich, da glatte, gratfreie Kanten entstehen, was insbesondere bei Anwendungen wichtig ist, bei denen eine anspruchsvolle Ästhetik erforderlich ist.
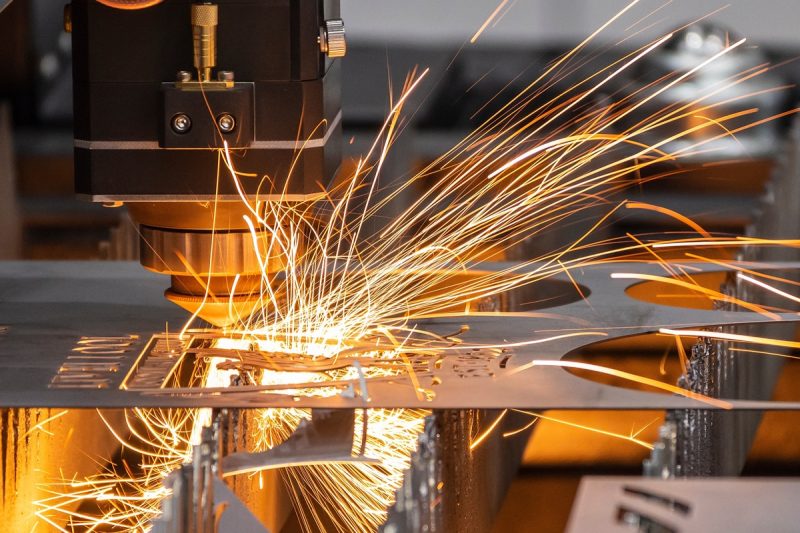
Zum Laserschneiden geeignete Materialien
Metalle
Kohlenstoffstahl
Kohlenstoffstahl ist aufgrund seiner Festigkeit, Haltbarkeit und Verfügbarkeit eines der am häufigsten verwendeten Materialien zum Laserschneiden. Es wird normalerweise mit Faserlasern verarbeitet, die schnelle und präzise Schnitte mit minimaler thermischer Verformung ermöglichen. Durch Laserschneiden können komplexe Formen schnell und mit hervorragender Kantenqualität hergestellt werden.
- Anwendungen: Zu den üblichen Anwendungen gehören Autoteile (wie Rahmen und Verkleidungen), Baumaterialien, Werkzeuge, Maschinenkomponenten und Strukturteile.
- Vorteile: Laserschneiden ermöglicht präzise Schnitte, scharfe Kanten und Hochgeschwindigkeitsverarbeitung. Kohlenstoffstahl kann in einem breiten Dickenbereich, von dünnen Blechen bis hin zu schweren Platten, mit hoher Wiederholgenauigkeit und Genauigkeit geschnitten werden.
Edelstahl
Edelstahl bietet hohe Festigkeit, Korrosionsbeständigkeit und eine optisch ansprechende Oberfläche, was es zu einem bevorzugten Material für viele Branchen macht. Laserschneiden liefert präzise Schnitte mit minimalen Wärmeeinflusszonen, wodurch die Eigenschaften des Materials erhalten bleiben. Es entstehen saubere, glatte Kanten, die oft keine Nachbearbeitung erfordern, wodurch es sich sowohl für dekorative als auch für funktionale Anwendungen eignet.
- Anwendungen: Geräte zur Lebensmittelverarbeitung, medizinische Geräte, Architekturelemente, Küchengeschirr, Dekorplatten und Autoteile.
- Vorteile: Laserschneiden bietet hohe Präzision, hervorragende Kantenqualität und die Möglichkeit, komplizierte Designs zu schneiden. Es minimiert thermische Verformungen und bewahrt die ästhetischen und mechanischen Eigenschaften von Edelstahl.
Aluminium
Aluminium ist ein leichtes, vielseitiges Metall, das in verschiedenen Branchen verwendet wird. Seine reflektierende Oberfläche stellt herkömmliche Schneidemethoden vor Herausforderungen, aber Faserlaser machen das Laserschneiden von Aluminium effizient und präzise. Zur Optimierung der Schneidleistung werden häufig geeignete Lasereinstellungen und Antireflexbeschichtungen verwendet.
- Anwendungen: Luft- und Raumfahrtkomponenten (z. B. Flugzeugplatten), Elektronikgehäuse, Autoteile, Dekorationsartikel und Beschilderungen.
- Vorteile: Hochgeschwindigkeitsschneiden, minimale Verzerrung und hervorragende Oberflächengüte, selbst bei dünnen oder komplizierten Designs. Beim Laserschneiden können Aluminiumbleche unterschiedlicher Dicke bearbeitet werden.
Kupfer und Messing
Kupfer Und Messing sind für ihre hohe thermische und elektrische Leitfähigkeit sowie ihre reflektierenden Oberflächen bekannt. Faserlaser eignen sich gut zum Schneiden dieser Metalle, da sie eine präzise Kontrolle über die Wellenlänge und Leistungsabgabe des Lasers ermöglichen, Reflexionen minimieren und gleichmäßige Schnitte gewährleisten.
- Anwendungen: Elektrische Komponenten (wie Steckverbinder und Kontakte), Sanitärarmaturen, dekorative Elemente und künstlerische Designs.
- Herausforderungen: Die Reflektivität dieser Metalle muss sorgfältig kontrolliert werden, um eine Beschädigung der Laserquelle zu verhindern.
- Vorteile: Laserschneiden ermöglicht hohe Präzision und Konsistenz und ist daher ideal für komplizierte Formen und feine Details bei Kupfer- und Messinganwendungen.
Titan
Titan ist aufgrund seines hohen Festigkeits-Gewichts-Verhältnisses sowie seiner Korrosions- und Hitzebeständigkeit ein hochwertiges Material für Spezialanwendungen. Laserschneiden eignet sich hervorragend für die Bearbeitung von Titan, da es präzise, saubere Schnitte ermöglicht, bei denen die Integrität und Eigenschaften des Materials erhalten bleiben.
- Anwendungen: Luft- und Raumfahrtteile (einschließlich Strukturkomponenten), medizinische Implantate und Geräte, Hochleistungssportgeräte und chemische Verarbeitungsgeräte.
- Vorteile: Laserschneiden gewährleistet hohe Genauigkeit, minimale thermische Schäden und saubere Kanten, selbst bei der Herstellung komplexer Formen.
Andere Legierungen
Das Laserschneiden wird häufig zur Bearbeitung verschiedener anderer Metalllegierungen eingesetzt, darunter Nickellegierungen, Superlegierungen und Sondermischungen, die in industriellen und Hochleistungsanwendungen zum Einsatz kommen.
- Anwendungen: Turbinenschaufeln, Komponenten für Industrieanlagen, Spezialwerkzeuge und Hochtemperaturanwendungen.
- Vorteile: Laserschneiden bietet Präzision, Wiederholbarkeit und die Möglichkeit, komplexe Formen mit hohen Toleranzen zu schneiden.
Nichtmetalle
Holz
Das Laserschneiden und -gravieren von Holz wird häufig für Anwendungen eingesetzt, die komplizierte Muster und präzise Schnitte erfordern. CO2-Laser sind besonders effektiv für die Bearbeitung verschiedener Arten von Holz, einschließlich Nadelhölzer, Laubhölzer, Sperrholz, Und MDF (mitteldichte Faserplatte).
- Anwendungen: Maßgefertigte Möbel, Dekorationsartikel, Spielzeug, Modellbau und Beschilderung.
- Vorteile: Laserschneiden ermöglicht komplizierte Details, glatte Kanten und minimale Verkohlungen oder Verfärbungen, wenn optimale Einstellungen verwendet werden. Der berührungslose Prozess verhindert außerdem, dass das Holz beim Schneiden splittert oder beschädigt wird.
Acryl und Kunststoff
Acryl und andere Kunststoffe sind aufgrund ihrer Transparenz, Flexibilität und glatten Oberfläche beliebte Materialien zum Laserschneiden. CO2-Laser bieten hohe Präzision und können diese Materialien schneiden oder gravieren, ohne dass es zum Schmelzen oder Verziehen kommt.
- Anwendungen: Beschilderung, Point-of-Sale-Displays, dekorative Paneele, Schutzbarrieren und kundenspezifische Prototypen.
- Vorteile: Durch Laserschneiden entstehen polierte, glatte Kanten, es sind keine sekundären Endbearbeitungsprozesse erforderlich und das detaillierte Gravieren und Schneiden komplizierter Muster ist möglich.
Leder
Laserschneiden wird häufig zum Schneiden und Gravieren von Leder verwendet. Es ermöglicht präzise Formen und Muster, ohne dass es zu Ausfransungen oder Verzerrungen kommt. CO2-Laser sind für diesen Zweck besonders effektiv und ermöglichen eine hohe Individualisierung und künstlerische Gestaltung.
- Anwendungen: Taschen, Geldbörsen, Gürtel, Schuhe und individuelle Accessoires.
- Vorteile: Laserschneiden gewährleistet Präzision, scharfe Schnitte und komplizierte Details. Es bietet eine hohe Wiederholgenauigkeit und gleichbleibende Qualität, was besonders bei der Produktion im großen Maßstab wichtig ist.
Papier und Karton
Laserschneiden ist eine hervorragende Methode zum Erstellen detaillierter Designs und individueller Formen in Papier- und Kartonprodukten. Es ermöglicht präzise Schnitte ohne mechanische Schneidwerkzeuge und ist daher ideal für kreative und kommerzielle Projekte.
- Anwendungen: Grußkarten, Verpackungsprototypen, Schablonen, Kunstprojekte und Werbematerialien.
- Vorteile: Laserschneiden ermöglicht eine Hochgeschwindigkeitsproduktion mit detaillierter Genauigkeit, sauberen Kanten und der Möglichkeit, problemlos komplexe Muster zu erstellen.
Stoffe und Textilien
Das Laserschneiden von Stoffen und Textilien ist aufgrund seiner Präzision und des berührungslosen Verfahrens in der Mode-, Polster- und Industrietextilindustrie beliebt geworden. Der Laser sorgt für saubere Schnitte, die Ausfransen und Verformungen verhindern.
- Anwendungen: Bekleidung, Stickereien, Polsterungen, technische Textilien und Industriestoffe.
- Vorteile: Laserschneiden sorgt für präzise und gleichmäßige Formen, reduziert Materialabfall und ermöglicht die Erstellung detaillierter Muster und komplexer Designs.
Gummi
Das Laserschneiden wird häufig für Gummikomponenten verwendet, da es präzise, konsistente Formen ohne Verformung oder Werkzeugverschleiß liefert. Das berührungslose Schneidverfahren minimiert außerdem das Risiko von Materialschäden.
- Anwendungen: Dichtungen, Werbeartikel, Matten und Industriekomponenten.
- Vorteile: Laserschneiden gewährleistet hohe Genauigkeit, gleichbleibende Qualität und die Möglichkeit, komplizierte Designs zu erstellen, ohne die Integrität des Materials zu beeinträchtigen.
Verbundwerkstoffe
Verbundwerkstoffe, wie sie in der Luft- und Raumfahrt und in industriellen Anwendungen verwendet werden, können mit herkömmlichen Werkzeugen schwierig zu schneiden sein. Das Laserschneiden bietet eine präzise und effiziente Lösung, mit der komplexe Formen mit hoher Genauigkeit geschnitten werden können.
- Anwendungen: Luft- und Raumfahrtteile, Automobilkomponenten, Industrieplatten und kundenspezifische Prototypen.
- Vorteile: Durch Laserschneiden lassen sich komplexe Geometrien bearbeiten und selbst bei anspruchsvollen Verbundstrukturen eine hohe Präzision erreichen.
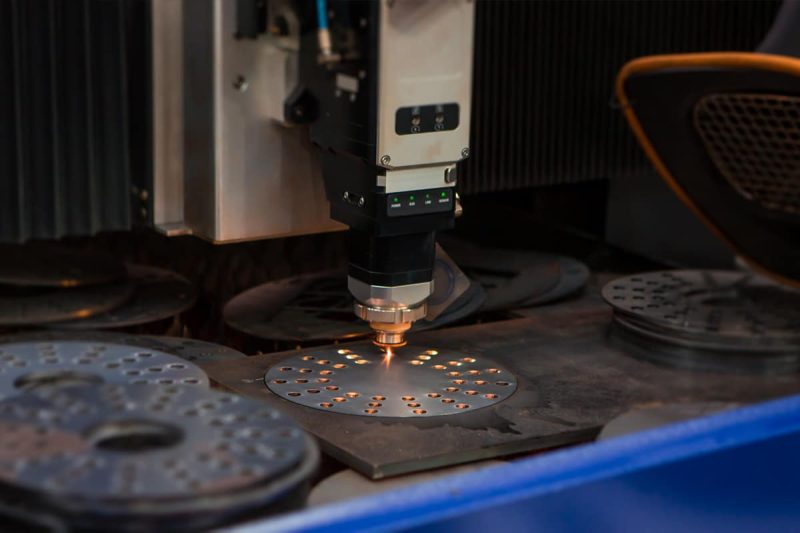
Einschränkungen und Überlegungen beim Laserschneiden
Materialien, die nicht zum Laserschneiden geeignet sind
Trotz der Vielseitigkeit des Laserschneidens sind bestimmte Materialien aufgrund von Sicherheitsrisiken, giftigen Emissionen oder Einschränkungen der Laserkompatibilität für dieses Verfahren nicht geeignet.
- PVC (Polyvinylchlorid): Das Schneiden von PVC mit Lasertechnologie wird nicht empfohlen, da giftiges Chlorgas freigesetzt wird, das sowohl für die Maschine als auch für den Bediener schädlich ist. Dieses Gas kann die Laserausrüstung korrodieren und die Sicherheit am Arbeitsplatz gefährden.
- Polytetrafluorethylen (PTFE): PTFE, auch als Teflon bekannt, setzt bei großer Hitze giftige Dämpfe frei. Das Laserschneiden dieses Materials kann zu ernsthaften Gesundheitsrisiken und Geräteschäden führen, weshalb es für Laseranwendungen ungeeignet ist.
- Polycarbonat (für Dicken über 1 mm): Dünnes Polycarbonat kann zwar graviert werden, das Schneiden von dickerem Polycarbonat kann jedoch aufgrund seines niedrigen Schmelzpunkts und seiner Neigung zur Verfärbung zum Schmelzen und zu rauen Kanten führen. Außerdem werden beim Laserschneiden von dickerem Polycarbonat gefährliche Dämpfe freigesetzt.
- Fiberglas: Fiberglas besteht sowohl aus Glas als auch aus Harz, das beim Verdampfen erhebliche Gesundheitsrisiken bergen kann. Der Harzanteil setzt giftige Dämpfe frei, während der Glasanteil die Laseroptik beschädigt und sie somit zum Laserschneiden ungeeignet macht.
- Bestimmte Metalle mit hoher Reflektivität (für bestimmte Lasertypen): Einige stark reflektierende Metalle, wie bestimmte Kupfer- und Aluminiumsorten, können beim Laserschneiden, insbesondere mit CO2, eine Herausforderung darstellen. Die reflektierende Natur dieser Materialien kann den Laserstrahl zurück in die Maschine lenken und so möglicherweise deren Komponenten beschädigen. Faserlaser mit Antireflextechnologie sind im Allgemeinen besser zum Schneiden reflektierender Metalle geeignet.
Sicherheitsaspekte
Beim Laserschneiden müssen Sicherheitsprotokolle eingehalten werden, um Bediener und Geräte vor den Gefahren zu schützen, die mit Hochleistungslasern, Dämpfen und Materialnebenprodukten verbunden sind.
- Belüftung und Rauchabsaugung: Beim Laserschneiden entstehen häufig Dämpfe, Schwaden und Rauch, insbesondere beim Schneiden von Kunststoffen, Gummi und anderen organischen Materialien. Diese Emissionen können für die Bediener giftig oder reizend sein, daher sind geeignete Belüftungs- und Rauchabsaugungssysteme unerlässlich, um die Luftqualität aufrechtzuerhalten und Gesundheitsrisiken zu verringern.
- Schutzbrille: Beim Laserschneiden entsteht hochintensives Licht, das für die Augen schädlich sein kann. Um Augenverletzungen vorzubeugen, sollten Bediener eine für die jeweilige Laserwellenlänge geeignete Schutzbrille tragen.
- Brandrisikomanagement: Beim Laserschneiden entsteht große Hitze, die ein Brandrisiko darstellt, insbesondere beim Schneiden brennbarer Materialien wie Holz, Stoff und Papier. Brandschutzmaßnahmen wie Feuerlöschsysteme und Feuerlöscher sollten leicht zugänglich sein. Eine kontinuierliche Überwachung des Schneidbereichs kann dazu beitragen, das Brandrisiko zu verringern.
- Sicherheitsgehäuse der Maschine: Moderne Laserschneidmaschinen sind häufig mit Sicherheitsgehäusen ausgestattet, die den Laserstrahl eindämmen, eine versehentliche Exposition verhindern und die Sicherheit des Bedieners verbessern. Es ist wichtig sicherzustellen, dass die Gehäuse intakt sind und ordnungsgemäß funktionieren.
- Gefährliche Nebenprodukte: Bestimmte Materialien wie PVC und Polycarbonat setzen beim Laserschneiden giftige Dämpfe frei. Das Schneiden dieser Materialien kann gesundheitsschädlich sein und sollte vermieden oder nur mit geeigneten Rauchabzugs- und Filtersystemen durchgeführt werden.
Materialstärkenbeschränkungen
Die Dicke des zu schneidenden Materials wirkt sich direkt auf die Leistung, Qualität und Effizienz des Laserschneidens aus. Die Leistung und Art des Lasers sowie die Materialeigenschaften beeinflussen die maximale Dicke, die effektiv geschnitten werden kann.
- Laserleistung und Materialkompatibilität: Jede Laserschneidmaschine hat eine bestimmte Nennleistung, die die Dicke bestimmt, die sie schneiden kann. Leistungsstärkere Laser (z. B. 10 kW oder mehr) können dickere Materialien schneiden, dies geht jedoch häufig auf Kosten langsamerer Schnittgeschwindigkeiten und eines höheren Energieverbrauchs. Beispielsweise sind Faserlaser besser für dicke Metalle geeignet, während CO2-Laser bei dünnen bis mitteldicken Nichtmetallen die beste Leistung erbringen.
- Metalldickengrenzen: Bei Metallen wie Kohlenstoffstahl und Edelstahl können Faserlaser beträchtliche Dicken von bis zu 25–30 mm oder mehr für industrielle Anwendungen verarbeiten. Das Überschreiten der optimalen Dickengrenze der Maschine kann jedoch zu raueren Kanten, Graten und verringerter Präzision führen, was sich auf die Qualität des Schnitts auswirkt.
- Dickengrenzen für Nichtmetalle: Bei Materialien wie Holz, Acryl und Kunststoff liefern CO2-Laser normalerweise hervorragende Ergebnisse bis zu mittleren Dicken. Beim Schneiden dickerer Nichtmetalle kann es zu Verkohlungen, Schmelzen und langsameren Schnittgeschwindigkeiten kommen. Dickeres Acryl kann beispielsweise schmelzen oder sich verfärben, wenn es mit CO2-Lasern mit geringerer Leistung geschnitten wird.
- Auswirkungen auf die Schnittqualität: Mit zunehmender Materialdicke wird es immer schwieriger, qualitativ hochwertige Kanten zu erhalten. Dickere Materialien weisen häufiger wärmebeeinflusste Zonen auf, was zu raueren, weniger präzisen Schnitten führt. Es ist wichtig, die richtige Laserleistung und die richtigen Einstellungen auszuwählen, um eine optimale Schnittqualität zu erzielen und gleichzeitig Materialabfall und Maschinenverschleiß zu minimieren.
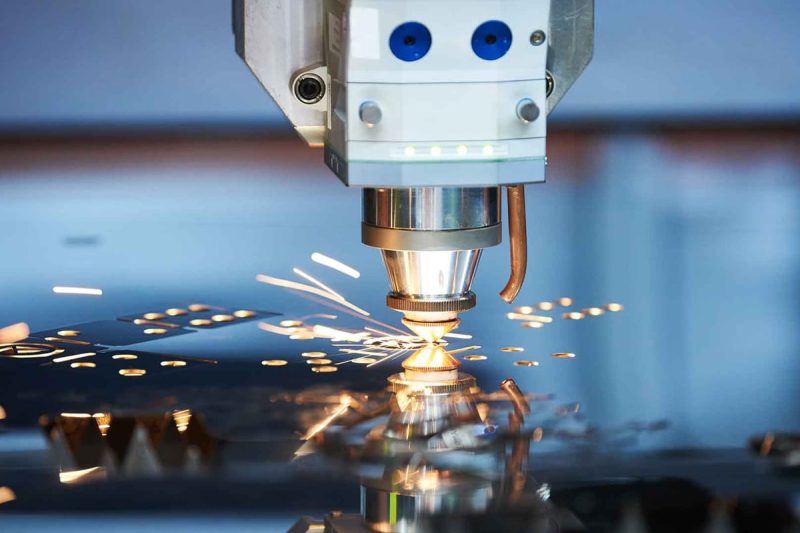
Faktoren, die die Qualität des Laserschneidens beeinflussen
Materialeigenschaften
Die Eigenschaften des zu schneidenden Materials spielen eine wichtige Rolle bei der Bestimmung der Qualität des Laserschneidens. Verschiedene Materialien reagieren unterschiedlich auf Laserenergie und ihre einzigartigen Eigenschaften können den Schneidprozess beeinflussen.
- Materialtyp: Metalle und Nichtmetalle reagieren unterschiedlich auf Laserschneiden. Beispielsweise sind Faserlaser aufgrund ihrer hohen Energieabsorptionsrate effektiver für Metalle wie Kohlenstoffstahl, Edelstahl, Aluminium und Kupfer, während CO₂-Laser gut für Nichtmetalle wie Holz, Acryl und Stoffe geeignet sind. Das Verständnis der Kompatibilität zwischen Lasertyp und Material ist entscheidend für das Erreichen hochwertiger Schnitte.
- Dicke: Die Materialdicke beeinflusst die Qualität des Laserschneidens erheblich. Dickere Materialien erfordern im Allgemeinen eine höhere Laserleistung, um einen sauberen Schnitt zu erzielen. Mit zunehmender Dicke wird es jedoch aufgrund größerer wärmebeeinflusster Zonen, langsamerer Schnittgeschwindigkeiten und möglicher Rauheit an den Kanten schwieriger, scharfe Kanten und präzise Schnitte beizubehalten. Um diese Probleme zu minimieren, ist die Optimierung der Laserleistung und -geschwindigkeit für bestimmte Dicken unerlässlich.
- Reflektivität: Stark reflektierende Materialien wie Aluminium, Kupfer und Messing können den Laserstrahl reflektieren, wodurch die Laseroptik möglicherweise beschädigt und die Schneidleistung verringert wird. Um reflektierende Materialien effektiv zu bearbeiten, sind häufig besondere Maßnahmen wie das Anpassen der Lasereinstellungen und die Verwendung von Antireflexbeschichtungen erforderlich.
- Wärmeleitfähigkeit: Materialien mit hoher Wärmeleitfähigkeit wie Kupfer und Aluminium leiten Wärme schnell ab, was zu langsameren Schnittgeschwindigkeiten und ungleichmäßigen Kanten führen kann. Um der Wärmeableitung entgegenzuwirken und saubere Schnitte zu erzielen, sind eine effektive Lasersteuerung und optimierte Schneidparameter erforderlich.
- Oberflächenbeschaffenheit: Oberflächenbeschaffenheit und Sauberkeit können die Qualität des Laserschneidens beeinflussen. Beispielsweise können Rost, Schmutz oder Öl auf der Oberfläche von Metallen zu ungleichmäßigem Schneiden und schlechter Kantenqualität führen. Eine ordnungsgemäße Vorbereitung und Reinigung des Materials vor dem Schneiden kann die Qualität der Ergebnisse erheblich verbessern.
Laserparameter
Die Parameter des Lasers selbst, einschließlich Leistung, Frequenz und Strahlqualität, spielen eine entscheidende Rolle bei der Bestimmung der Schnittqualität.
- Laserleistung: Die Leistungsabgabe des Lasers muss je nach Materialart und -dicke angepasst werden. Zum Schneiden dicker Metalle sind möglicherweise hohe Leistungsstufen erforderlich, aber zu viel Leistung kann bei dünneren Materialien zu Verkohlungen, rauen Kanten und übermäßigen Wärmeeinflusszonen führen. Eine ausgewogene Leistung gewährleistet präzise Schnitte ohne Beeinträchtigung der Kantenqualität.
- Strahlqualität: Die Qualität des Laserstrahls, oft als Strahlmodus oder M2-Faktor bezeichnet, beeinflusst, wie präzise der Laser auf einen bestimmten Punkt fokussieren kann. Ein hochwertiger Strahl erzeugt einen feineren, konzentrierteren Laserpunkt, was zu saubereren Schnitten und komplexeren Details führt. Eine schlechte Strahlqualität kann zu größeren Schnittbreiten und raueren Kanten führen.
- Frequenz- und Pulseinstellungen: Bei gepulsten Lasern kann die Anpassung der Frequenz und Pulsdauer den Schneidvorgang beeinflussen. Höhere Frequenzen können für feine, detaillierte Schnitte verwendet werden, während niedrigere Frequenzen besser für dickere Schnitte geeignet sind, die eine tiefere Durchdringung erfordern. Die Optimierung dieser Einstellungen für das jeweilige Material ist entscheidend, um die gewünschte Schnittqualität zu erreichen und Defekte zu minimieren.
- Art und Druck des Hilfsgases: Hilfsgase wie Sauerstoff, Stickstoff oder Druckluft werden beim Laserschneiden verwendet, um geschmolzenes Material aus dem Schnittbereich zu entfernen, das Werkstück abzukühlen und Oxidation zu verhindern. Die Art des Gases und sein Druck wirken sich auf die Kantenqualität und die Schnittgeschwindigkeit aus. Beispielsweise erzeugt Sauerstoff einen reaktiven Schnitt, der die Geschwindigkeit erhöht, aber eine oxidierte Kante hinterlassen kann, während Stickstoff saubere, nicht oxidierte Kanten erzeugt, die ideal für Edelstahl sind.
Schnittgeschwindigkeit und Fokus
Die Geschwindigkeit, mit der sich der Laser über das Material bewegt, und die Präzision seiner Fokussierung sind entscheidende Faktoren, die die Schnittqualität beeinflussen.
- Schnittgeschwindigkeit: Die Schnittgeschwindigkeit muss sorgfältig auf Materialart und -dicke abgestimmt werden. Zu schnelles Schneiden kann zu unvollständigen Schnitten, rauen Kanten und schlechter Qualität führen. Umgekehrt kann zu langsames Schneiden zu übermäßiger Hitzeentwicklung führen, was zu Materialverformungen, vermehrten Graten und breiteren hitzebeeinflussten Zonen führt. Die optimale Schnittgeschwindigkeit gewährleistet glatte, präzise Schnitte und hohe Produktivität.
- Fokusposition: Für eine optimale Schnittqualität muss der Brennpunkt des Laserstrahls genau auf die Materialoberfläche eingestellt werden. Die Fokusposition beeinflusst die Energiekonzentration am Schnittpunkt und damit die Breite des Schnittspalts und die Kantenqualität. Richtig fokussierte Strahlen erzeugen schmale Schnitte mit minimalen wärmebeeinflussten Zonen, während eine falsche Fokussierung zu rauen Kanten, geringerer Präzision und Schnitten von schlechter Qualität führen kann. Autofokusfunktionen in modernen Lasermaschinen verbessern die Schnittgenauigkeit, indem sie den Fokus dynamisch an die Materialdicke und die Oberflächenbedingungen anpassen.
- Schnittbreite: Die Schnittbreite, auch Schnittbreite genannt, wird durch den Fokus des Lasers und die Materialeigenschaften beeinflusst. Ein schmaler Schnitt verbessert die Präzision und reduziert den Materialabfall. Die Beibehaltung eines konstanten Fokus und die Optimierung der Laserparameter sind der Schlüssel zum Erreichen gleichmäßiger Schnittbreiten über alle Schnitte hinweg.
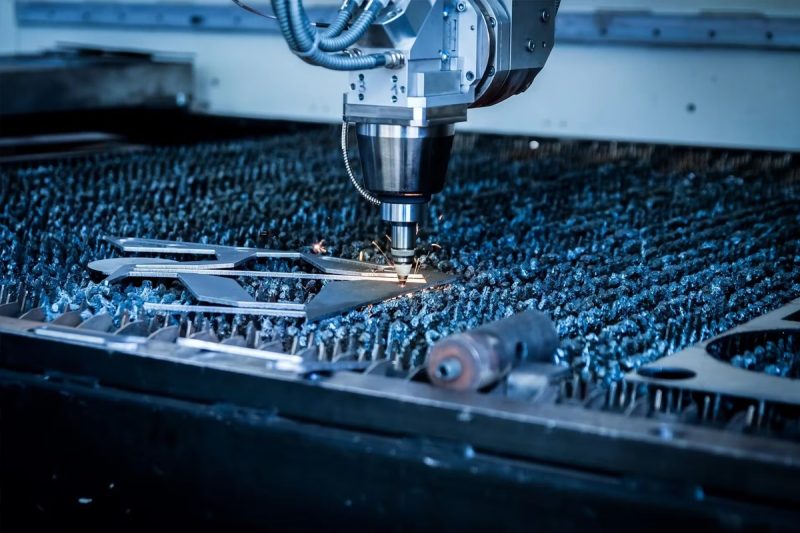
Auswahl der richtigen Laserschneidmaschine
Materialtyp und Kompatibilität
Verschiedene Laserschneidmaschinen sind für bestimmte Materialarten optimiert. Daher ist es wichtig, die Materialien zu kennen, die Sie schneiden möchten. Es gibt zwei Haupttypen von Laserschneidmaschinen, die jeweils für bestimmte Materialeigenschaften geeignet sind:
- Faserlaser-Schneidemaschinen: Faserlaser sind aufgrund ihrer hohen Energiedichte und Effizienz ideal zum Schneiden von Metallen. Sie eignen sich gut zum Schneiden reflektierender Metalle wie Aluminium, Kupfer und Messing sowie anderer Metalle wie Kohlenstoffstahl, Edelstahl und Titan. Faserlaser bieten außerdem hervorragende Präzision und Schnittgeschwindigkeit, was sie zur ersten Wahl für Branchen wie die Automobil-, Luft- und Raumfahrt- und Metallverarbeitung macht.
- CO2-Laserschneidmaschinen: CO2-Laser sind sehr effektiv für nichtmetallische Materialien wie Holz, Acryl, Leder, Stoff, Gummi und Papier. Diese Laser werden häufig in Branchen wie Beschilderung, Holzverarbeitung, Textilien und Verpackung eingesetzt. CO2-Laser können auch dünne Metalle schneiden, eignen sich jedoch am besten für Anwendungen, bei denen präzise, saubere Schnitte in nichtmetallischen Materialien erforderlich sind.
Materialdicke und Laserleistungsbedarf
Die Dicke des zu schneidenden Materials hat direkte Auswirkungen auf den Leistungsbedarf der Laserschneidmaschine. Dickere Materialien erfordern eine höhere Leistung, um saubere und effiziente Schnitte zu erzielen, während dünnere Materialien von niedrigeren Leistungseinstellungen für Präzision und Kontrolle profitieren.
- Hohe Leistung für dicke Metalle: Zum Schneiden dicker Metalle (z. B. 10 mm oder mehr) wird ein Faserlaser mit hoher Leistung, z. B. 3 kW oder mehr, empfohlen. Diese Leistungsstufe stellt sicher, dass der Laser das Material vollständig durchdringen und eine saubere Kante ohne übermäßige Wärmeeinflusszonen erzeugen kann.
- Mittlere Leistung für dünne bis mittlere Materialien: Laser mittlerer Leistung (1-2 kW) eignen sich gut zum Schneiden dünner bis mitteldicker Metalle und Nichtmetalle. Dieser Leistungsbereich ist vielseitig und wird häufig für Anwendungen in der Metallverarbeitung, Werbung und Konsumgütern verwendet.
- Geringe Leistung für dünne und empfindliche Materialien: Laser mit geringerer Leistung sind ideal für dünne Materialien wie Papier, Stoff und einige Kunststoffe. Sie verhindern ein Verbrennen oder Verziehen, insbesondere bei hitzeempfindlichen Materialien. CO2-Laser mit einstellbarer Leistungseinstellung eignen sich gut für diese Anwendungen und bieten Flexibilität für filigrane und komplizierte Designs.
Präzisions- und Detailanforderungen
Laserschneidmaschinen unterscheiden sich in ihrer Fähigkeit, komplizierte Details und feine Schnitte zu erzeugen. Wenn die Anwendung hohe Präzision und komplizierte Designs erfordert, werden Strahlqualität, Genauigkeit des Steuerungssystems und Fokuspräzision zu kritischen Faktoren.
- Hohe Präzision für komplexe Designs: Faserlaser bieten hohe Präzision und sind daher ideal für Anwendungen, die komplexe Formen und komplizierte Details erfordern. Branchen wie die Elektronik, die Herstellung medizinischer Geräte und die Schmuckherstellung profitieren von Laserschneidmaschinen mit feiner Fokussierung und stabilen Steuerungssystemen.
- Mittlere Präzision für einfache Formen und große Schnitte: Für Anwendungen, die keine extreme Präzision erfordern, wie etwa allgemeine Metallverarbeitung, Bau oder Beschilderung, reicht oft ein Standard-CO2- oder Faserlaser mit moderater Präzision aus. Diese Maschinen eignen sich gut für einfache Schnitte und größere Teile, bei denen extreme Details nicht so wichtig sind.
Geschwindigkeit und Produktionsvolumen
Auch die erforderliche Schnittgeschwindigkeit und das Produktionsvolumen beeinflussen die Maschinenauswahl. Einige Laserschneidmaschinen sind für die Hochgeschwindigkeitsproduktion optimiert, während andere auf Präzision bei niedrigeren Geschwindigkeiten ausgerichtet sind.
- Hochgeschwindigkeitsproduktion: Faserlaser sind für ihre Hochgeschwindigkeitsleistung bei Metallen bekannt und ermöglichen schnellere Produktionszeiten in Branchen wie der Automobil- und Luftfahrtindustrie. Dieser Geschwindigkeitsvorteil trägt zur Aufrechterhaltung der Effizienz bei und ist in der Massenproduktion von entscheidender Bedeutung.
- Moderate Geschwindigkeit für Detailarbeiten: CO2-Laser können im Vergleich zu Faserlasern langsamer arbeiten, insbesondere beim Schneiden von Metallen. Für Detailarbeiten an Nichtmetallen bieten CO2-Laser jedoch ein ausgezeichnetes Gleichgewicht zwischen Geschwindigkeit und Präzision.
Maschinenfunktionen und Anpassungsoptionen
Erweiterte Funktionen und Anpassungsoptionen verbessern die Anpassungsfähigkeit und Effizienz einer Laserschneidmaschine in bestimmten Anwendungen. Berücksichtigen Sie bei der Auswahl einer Laserschneidmaschine je nach Ihren Anforderungen die folgenden Funktionen:
- Autofokus und einstellbare Betthöhe: Maschinen mit Autofokus-Funktionen und einstellbarer Betthöhe ermöglichen präzise Anpassungen beim Schneiden von Materialien unterschiedlicher Dicke. Der Autofokus optimiert die Laserposition für einen klaren, sauberen Schnitt, während die Anpassung der Betthöhe Materialien unterschiedlicher Größe ermöglicht.
- Drehachse und doppelte Arbeitstische: Für Benutzer, die zylindrische oder röhrenförmige Materialien schneiden müssen, ist eine Drehachsenoption von Vorteil. Doppelte Arbeitstische steigern auch die Produktivität, da ein Werkstück geladen oder entladen werden kann, während ein anderes geschnitten wird.
- Rauchabsaugung und Sicherheitsgehäuse: Hochwertige Rauchabsaugungssysteme und Sicherheitsgehäuse sind für die Aufrechterhaltung einer sicheren Arbeitsumgebung unerlässlich, insbesondere beim Schneiden von Materialien, die giftige Dämpfe freisetzen. Maschinen mit integrierten Absaugsystemen reduzieren luftgetragene Schadstoffe und schützen die Bediener vor Laserstrahlung.
- Software und Steuerungssysteme: Laserschneidmaschinen werden normalerweise durch CNC-Software gesteuert, die eine präzise Kontrolle über Schneidweg, Geschwindigkeit und Leistung ermöglicht. Zu den erweiterten Softwarefunktionen gehören Mustererkennung, automatisches Verschachteln und Echtzeitüberwachung, die die Effizienz verbessern und Materialabfall reduzieren können.
Budget- und Kostenüberlegungen
Laserschneidmaschinen gibt es in unterschiedlichen Preisklassen, die von Faktoren wie Leistungsabgabe, Maschinentyp und Zusatzfunktionen beeinflusst werden. Es ist wichtig, die Anschaffungskosten gegen die langfristige Produktivität und den ROI abzuwägen.
- Einsteigermaschinen: Einsteigermaschinen mit geringerer Leistung und weniger Funktionen eignen sich für kleine Unternehmen und Hobbybastler, die mit dünnen Materialien arbeiten. Diese Maschinen bieten oft grundlegende Funktionen zu einem erschwinglichen Preis und sind daher eine erschwingliche Option für Personen mit bescheidenen Anforderungen.
- Mittelklassemaschinen: Mittelklasse-Laserschneider mit mäßiger Leistung und grundlegenden Funktionen eignen sich für kleine bis mittlere Unternehmen und Branchen, die zuverlässige, vielseitige Maschinen ohne höchste Spezifikationen benötigen. Diese Maschinen bieten ein ausgewogenes Verhältnis von Leistung und Kosten und sind daher eine gute Wahl für Unternehmen mit mäßigem Produktionsbedarf.
- Hochwertige Industriemaschinen: Leistungsstarke Maschinen mit vielen Funktionen sind für groß angelegte Arbeiten konzipiert, bei denen schnelles und präzises Schneiden unterschiedlicher Materialien erforderlich ist. Diese Maschinen sind zwar mit höheren Anschaffungskosten verbunden, bieten jedoch häufig eine schnellere Verarbeitung, höhere Produktivität und Langlebigkeit, was die Investition in anspruchsvollen Umgebungen rechtfertigt.

Zusammenfassung
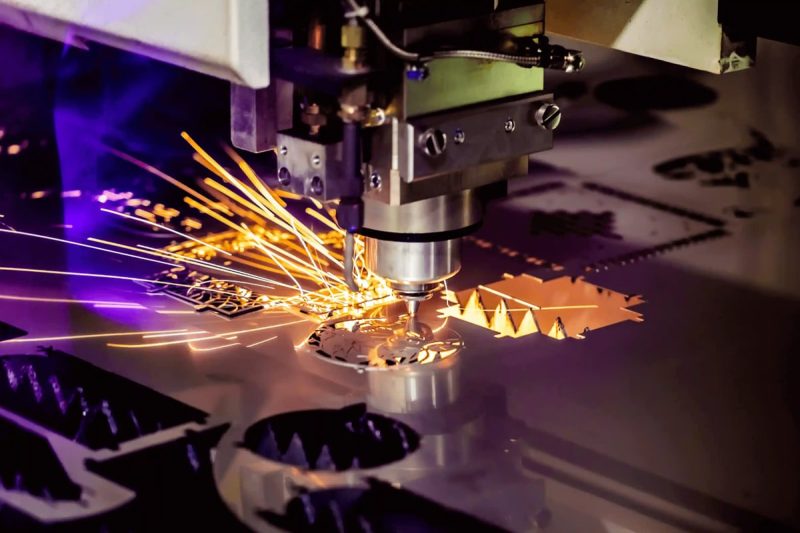
Holen Sie sich Laserschneidlösungen
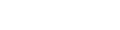
- [email protected]
- [email protected]
- +86-19963414011
- Nr. 3 Zone A, Industriegebiet Lunzhen, Stadt Yucheng, Provinz Shandong.