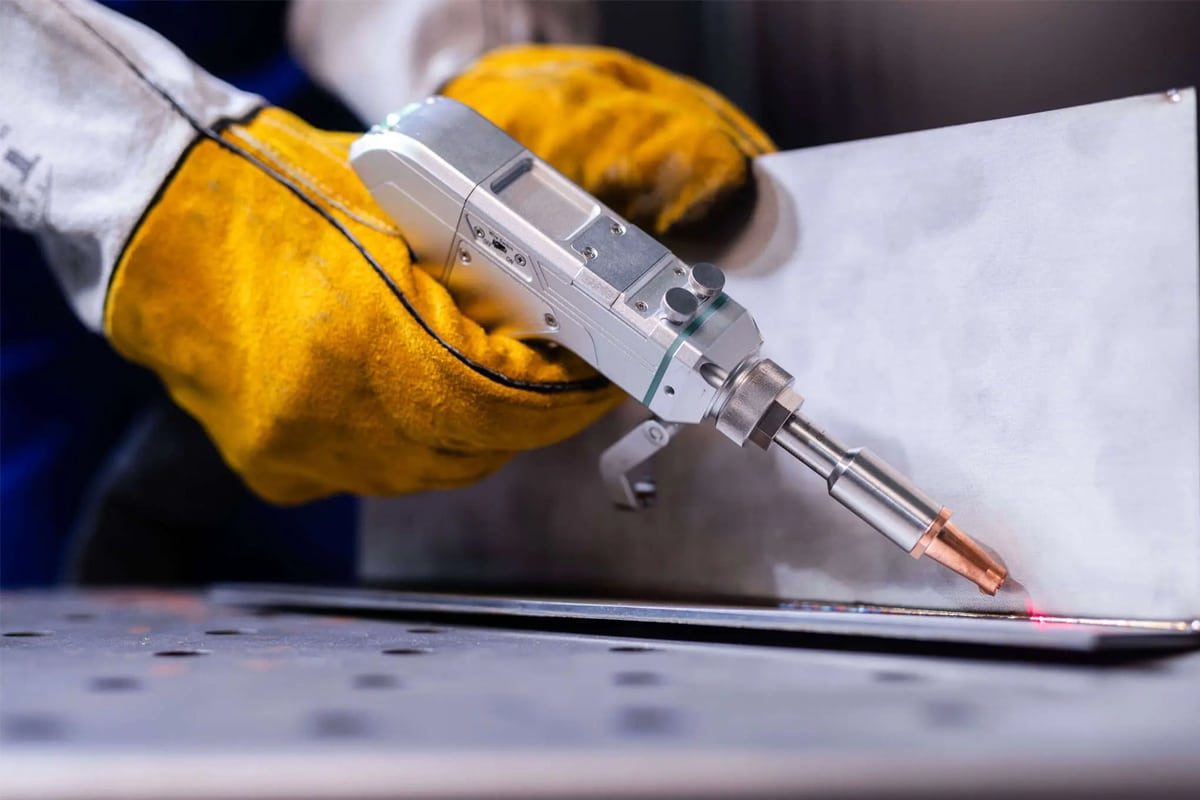
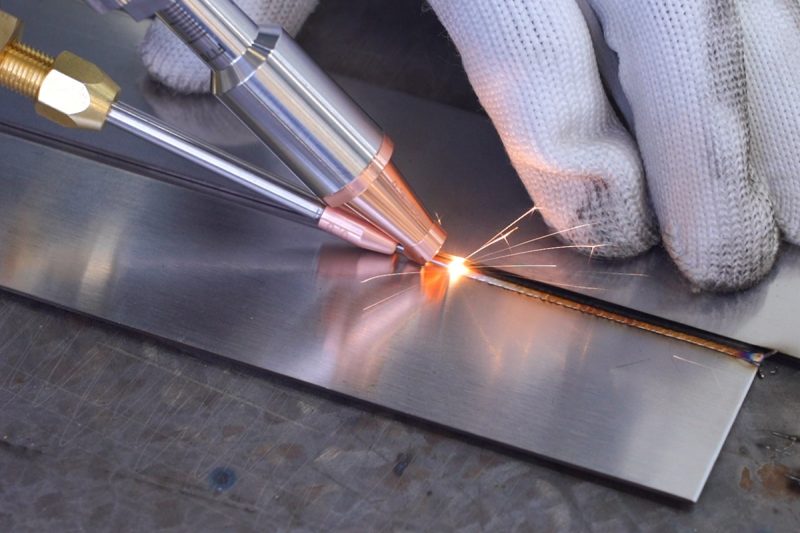
Überblick über das Laserschweißen
Was ist Laserschweißen?
Laserschweißen ist ein präziser und effizienter Fügeprozess, bei dem ein hochfokussierter Laserstrahl zum Erhitzen und Verschmelzen von Materialien verwendet wird. Der Laserstrahl erzeugt eine konzentrierte Wärmequelle, die schmale, tiefe Schweißnähte mit minimalen Wärmeeinflusszonen (WEZ) ermöglicht. Das Laserschweißen funktioniert in zwei Hauptmodi, abhängig von der Leistungsdichte und den Materialeigenschaften:
- Keyhole-Modus-Schweißen: In diesem Modus verdampft ein Laserstrahl mit hoher Leistungsdichte das Material und erzeugt ein schmales, tiefes Keyhole, das mit geschmolzenem Metall und Dampf gefüllt ist. Das Keyhole fungiert als Kanal für die Laserenergie und ermöglicht tiefes Eindringen und Schweißnähte mit hohem Aspektverhältnis. Dieser Modus ist ideal für Anwendungen, die tiefe und schmale Schweißnähte erfordern, wie beispielsweise in der Automobil- und Luftfahrtindustrie.
- Konduktionsschweißen: Dieser Modus wird bei niedrigeren Leistungsdichten als beim Stichlochschweißen verwendet, bei dem der Laser das Material erhitzt, ohne es zu verdampfen. Durch Wärmeleitung von der Oberfläche entsteht ein flacheres, breiteres Schweißbad. Konduktionsschweißen eignet sich für dünne Materialien oder wenn nur minimale Durchdringung und Wärmezufuhr erwünscht sind.
Vorteile des Laserschweißens
Das Laserschweißen bietet gegenüber herkömmlichen Schweißverfahren mehrere Vorteile:
- Präzision und Genauigkeit: Der konzentrierte Laserstrahl ermöglicht eine präzise Steuerung und erzeugt präzise Schweißnähte mit minimaler Verzerrung.
- Hochgeschwindigkeitsverarbeitung: Die hohe Energiedichte des Lasers ermöglicht schnelle Schweißgeschwindigkeiten, erhöht die Produktivität und verkürzt die Zykluszeiten.
- Minimale Wärmeeinflusszone: Durch die verringerte Wärmeausbreitung werden Verzerrungen minimiert, sodass sich das Laserschweißen für empfindliche oder dünne Komponenten eignet.
- Automatisierungsfähigkeit: Das Laserschweißen lässt sich problemlos in automatisierte Systeme und Roboterarme integrieren und steigert so die Effizienz bei der Produktion großer Stückzahlen.
- Materialvielseitigkeit: Kann eine große Bandbreite an Metallen und Legierungen schweißen, darunter auch schwer schweißbare Materialien wie Titan und Edelstahl.
- Berührungsloser Prozess: Es ist kein physischer Kontakt erforderlich, wodurch der Verschleiß der Werkzeuge reduziert und das Risiko einer Elektrodenkontamination eliminiert wird.
Anwendungen des Laserschweißens
Aufgrund seiner einzigartigen Fähigkeiten und Präzision wird das Laserschweißen in zahlreichen Branchen eingesetzt:
- Automobilindustrie: Wird zum Schweißen von Karosserieteilen, Zahnrädern, Getriebekomponenten und Auspuffsystemen verwendet, bei denen hohe Präzision und Geschwindigkeit entscheidend sind.
- Luft- und Raumfahrtindustrie: Geeignet zum Schweißen leichter, hochfester Komponenten wie Turbinenschaufeln, Strukturteile und Motorkomponenten.
- Elektronikindustrie: Ideal zum Mikroschweißen empfindlicher Schaltkreise, Anschlüsse und Gehäuse in elektronischen Geräten.
- Herstellung medizinischer Geräte: Wird zum Schweißen komplexer medizinischer Geräte, chirurgischer Instrumente und implantierbarer Komponenten verwendet, bei denen Präzision und Sauberkeit von größter Bedeutung sind.
- Schmuck und Kunst: Ermöglicht komplizierte Reparaturen und die Herstellung komplexer Schmuckdesigns und künstlerischer Metallarbeiten.
- Industrielle Fertigung: Wird in verschiedenen Industriezweigen beim Verbinden von Metallblechen, Rohren und hochbelastbaren Strukturkomponenten angewendet.
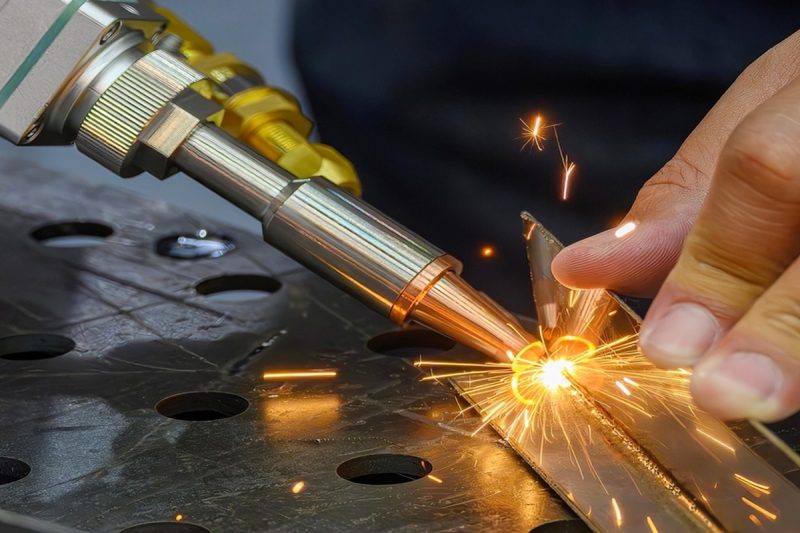
Häufige Schweißfehler beim Laserschweißen
Porosität
Ursachen
- Oberflächenverunreinigung: Öl, Fett, Feuchtigkeit und Rost auf der Werkstückoberfläche können bei Erhitzung Gase erzeugen, die zu eingeschlossenen Blasen in der Schweißnaht führen.
- Probleme mit Schutzgas: Unzureichende Schutzgasabdeckung, niedrige Durchflussraten oder ein ungeeigneter Gastyp können zu Luftverunreinigungen führen, wie etwa dem Eindringen von Sauerstoff und Stickstoff, wodurch Gaseinschlüsse entstehen.
- Materialzusammensetzung: Hohe Konzentrationen von Wasserstoff, Schwefel, Kohlenstoff oder anderen Verunreinigungen im Grundmetall können beim Schweißen zur Gasentwicklung führen.
- Schnelle Abkühlung: Durch die schnelle Verfestigung des Schmelzbades kann Gas eingeschlossen werden, bevor es entweicht.
Lösungen
- Oberflächenreinigung: Werkstücke vor dem Schweißen gründlich reinigen und Verunreinigungen wie Fett, Öl und Rost entfernen.
- Optimierter Schutzgasfluss: Verwenden Sie geeignete Schutzgase wie Argon oder Helium und stellen Sie die richtige Durchflussrate und Abdeckung sicher, um das Schweißbad zu schützen.
- Materialauswahl und -vorbereitung: Wählen Sie Materialien mit geringem Verunreinigungsgehalt und führen Sie vor dem Schweißen Behandlungen wie z. B. Entgasen durch.
- Parameterabstimmung: Passen Sie die Laserparameter an, um eine kontrollierte Kühlung zu ermöglichen und den Gasen Zeit zum Entweichen zu geben.
Knacken
Arten von Rissen
- Heißrissbildung: Entsteht bei hohen Temperaturen während der Erstarrung aufgrund von Zugspannungen oder der Ausscheidung von Verunreinigungen (z. B. Schwefel).
- Kaltrissbildung: Bildet sich nach dem Abkühlen, oft im Zusammenhang mit Wasserstoffversprödung, Eigenspannungen oder falscher Materialzusammensetzung.
Ursachen
- Hohe Temperaturgradienten: Schnelle Heiz- und Abkühlzyklen können zu Restspannungen führen, die die Rissbildung begünstigen.
- Materialzusammensetzung: Bestimmte Legierungen, insbesondere solche mit hohem Schwefel- oder Kohlenstoffgehalt, sind anfälliger für Risse.
- Verunreinigungen: Elemente wie Schwefel und Phosphor können sich an Korngrenzen ablagern und die Struktur schwächen.
- Wasserstoffaufnahme: Durch Feuchtigkeit, verunreinigtes Schutzgas oder unedle Metalle eingebrachter Wasserstoff kann zu verzögerter Rissbildung führen.
Lösungen
- Vorwärmen und Wärmebehandlung nach dem Schweißen: Wärmen Sie das Werkstück vor, um Wärmegradienten zu verringern, und führen Sie nach dem Schweißen Wärmebehandlungen durch, um Restspannungen abzubauen.
- Materialkontrolle: Wählen Sie Materialien mit geringem Verunreinigungsgrad und optimieren Sie ihre chemische Zusammensetzung, um die Rissanfälligkeit zu verringern.
- Wasserstoffkontrolle: Trocknen Sie die Materialien und verwenden Sie wasserstoffarme Prozesse, wie z. B. die Verwendung trockener Schutzgase und die Vermeidung von Feuchtigkeit.
- Techniken zur Spannungsbeseitigung: Verwenden Sie Vorrichtungen und geeignete Verbindungskonstruktionen, um Spannungskonzentrationen zu minimieren.
Unterbieten
Ursachen
- Übermäßige Wärmezufuhr: Hohe Laserleistung oder langsame Bewegungsgeschwindigkeiten können ohne ausreichend Füllmetall zu lokalem Schmelzen und Materialverlust führen.
- Falscher Strahlwinkel: Eine Fehlausrichtung des Laserstrahls im Verhältnis zur Verbindung kann zum Materialabtrag statt zur Verschmelzung führen.
- Unsachgemäßer Fokus: Ein ungenaues Laserfokussieren kann zu einer ungleichmäßigen Konzentration der Energie führen.
Lösungen
- Wärmezufuhr optimieren: Passen Sie Laserleistung, Bewegungsgeschwindigkeit und Strahldurchmesser an, um die Wärmeverteilung zu steuern.
- Strahlausrichtung: Richten Sie den Laserstrahl richtig auf die Verbindung aus, um ein gleichmäßiges Schmelzen und Füllen sicherzustellen.
- Schweißtechnik: Passen Sie den Winkel und die Positionierung des Lasers an, um Materialverlust zu reduzieren.
Fehlende Fusion
Ursachen
- Unzureichende Wärmezufuhr: Eine geringe Laserleistung oder eine zu hohe Vorschubgeschwindigkeit können eine vollständige Verschmelzung der Grundmaterialien verhindern.
- Unsachgemäße Vorbereitung der Verbindung: Schlechte Passung, Lücken oder Fehlausrichtungen zwischen den Werkstücken können eine vollständige Verschmelzung verhindern.
- Verunreinigung: Oberflächenoxide, Schmutz oder andere Verunreinigungen können die Fusion behindern.
Lösungen
- Erhöhen Sie die Wärmezufuhr: Verwenden Sie ausreichend Laserleistung oder reduzieren Sie die Bewegungsgeschwindigkeit, um eine ordnungsgemäße Verschmelzung zu erreichen.
- Verbessern Sie die Passung der Verbindungen: Sorgen Sie für die richtige Ausrichtung und Passung zwischen den Werkstücken, um eine gleichmäßige Schweißdurchdringung zu gewährleisten.
- Oberflächenreinigung: Entfernen Sie Oxide, Öle und andere Verunreinigungen von den Schweißoberflächen.
Unvollständige Penetration
Ursachen
- Geringe Laserleistung: Unzureichende Energiezufuhr, um die gesamte Materialstärke zu durchschmelzen.
- Hohe Bewegungsgeschwindigkeit: Der Laser bewegt sich zu schnell, um die Verbindung vollständig zu erhitzen und zu schmelzen.
- Unsachgemäßer Strahlfokus: Eine falsche Fokussierung des Lasers kann zu einer oberflächlichen Eindringung führen.
Lösungen
- Erhöhen Sie die Laserleistung: Passen Sie die Leistungseinstellungen an, um eine vollständige Durchdringung der Verbindung sicherzustellen.
- Reduzieren Sie die Bewegungsgeschwindigkeit: Geben Sie dem Laser mehr Zeit, das Material zu erhitzen und zu schmelzen.
- Richtiger Strahlfokus: Fokussieren Sie den Laser richtig, um eine gleichmäßige Eindringtiefe zu erreichen.
Spritzer
Ursachen
- Übermäßige Laserleistung: Hohe Leistungseinstellungen können ein heftiges Kochen des Schmelzbades verursachen.
- Verunreinigungen: Oberflächenverunreinigungen können mit der Hitze reagieren und eine schnelle Verdampfung verursachen.
- Ungeeignetes Schutzgas: Unzureichender Schutz kann zu Oxidation und dadurch zu Spritzern führen.
Lösungen
- Passen Sie die Laserparameter an: Reduzieren Sie die Laserleistung und optimieren Sie die Pulseinstellungen, um eine übermäßige Energiezufuhr zu verhindern.
- Oberflächenreinigung: Stellen Sie vor dem Schweißen sicher, dass die Oberflächen frei von Verunreinigungen sind.
- Optimierung des Schutzgases: Verwenden Sie ein geeignetes Schutzgas und halten Sie die richtigen Durchflussraten ein.
Unregelmäßigkeiten in der Schweißnaht
Ursachen
- Inkonsistente Fahrgeschwindigkeit: Geschwindigkeitsschwankungen führen zu einer ungleichmäßigen Wärmezufuhr.
- Variabilität der Laserleistung: Änderungen der Leistungsabgabe können zu ungleichmäßigem Schmelzen führen.
- Falscher Strahlfokus: Ein falsch ausgerichteter Fokus führt zu einer ungleichmäßigen Energieverteilung.
Lösungen
- Konstante Geschwindigkeit beibehalten: Sorgen Sie für eine gleichmäßige Geschwindigkeit während des gesamten Schweißvorgangs.
- Stabilisieren Sie die Leistungsabgabe: Verwenden Sie eine stabile Stromquelle, um eine konstante Laserleistung aufrechtzuerhalten.
- Strahlfokus anpassen: Sorgen Sie für die korrekte Strahlausrichtung und Fokussierung für eine gleichmäßige Energieabgabe.
Durchbrennen
Ursachen
- Übermäßiger Wärmeeintrag: Eine hohe Laserleistung oder langsame Bewegungsgeschwindigkeiten können zu übermäßigem Schmelzen führen.
- Dünnes Material: Dünne Blätter neigen eher zum Durchbrennen.
- Falscher Strahlfokus: Die Konzentration der Energie auf einen kleinen Bereich kann das Schmelzen verschlimmern.
Lösungen
- Wärmezufuhr reduzieren: Laserleistung verringern oder Bewegungsgeschwindigkeit erhöhen.
- Erweitern Sie den Strahlfokus: Verteilen Sie die Laserenergie gleichmäßiger.
- Verwenden Sie eine geeignete Materialstärke: Passen Sie die Materialstärke den Schweißanforderungen an.
Deformation und Verzerrung
Ursachen
- Thermische Spannungen: Schnelle Heiz- und Kühlzyklen führen zu Ausdehnung und Kontraktion.
- Dünne Materialien: Anfälliger für Verziehen und Verbiegen.
- Übermäßige Wärmezufuhr: Eine hohe Energiezufuhr kann zu starken Verformungen führen.
Lösungen
- Wärmezufuhr optimieren: Verwenden Sie kontrollierte Laserparameter, um übermäßige Hitze zu minimieren.
- Fixierung und Klemmung: Halten Sie Werkstücke mit Vorrichtungen an ihrem Platz, um Bewegungen zu reduzieren.
- Ausgeglichenes Schweißen: Verwenden Sie Techniken, die die Erwärmung ausgleichen und die Belastung minimieren.
Oxidation und Verfärbung
Ursachen
- Unzureichendes Schutzgas: Ein geringer Gasfluss oder eine mangelhafte Abdeckung kann dazu führen, dass das Schweißbad der Luft ausgesetzt wird.
- Falsche Gaszusammensetzung: Die Wahl des falschen Schutzgases kann die Oxidation möglicherweise nicht verhindern.
- Verunreinigungen: Oberflächenverunreinigungen können reagieren und Oxidation verursachen.
Lösungen
- Sorgen Sie für eine ausreichende Abschirmung: Verwenden Sie einen ausreichenden Schutzgasstrom, um das Schweißbad zu schützen.
- Wählen Sie eine geeignete Gaszusammensetzung: Wählen Sie ein Schutzgas, das Oxidation wirksam verhindert (z. B. Argon).
- Oberflächenreinigung: Reinigen Sie die Werkstückoberflächen gründlich, um Reaktionen während des Schweißens zu minimieren.
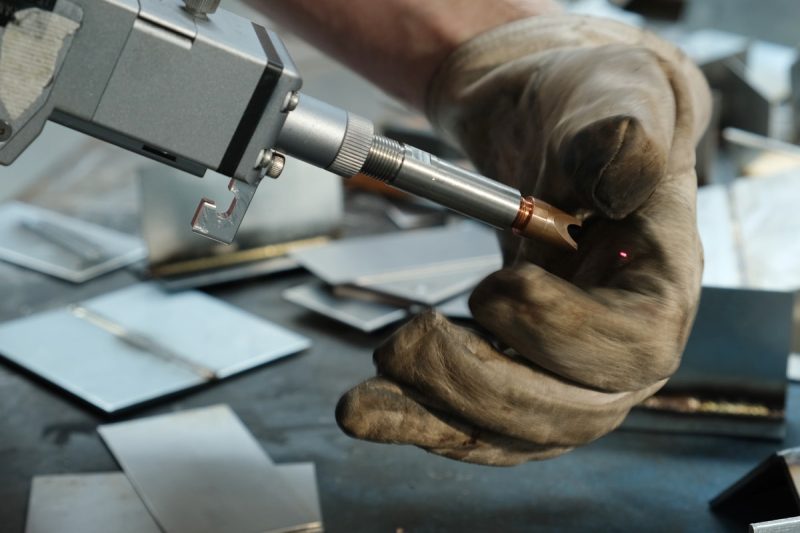
Einflussfaktoren auf Schweißfehler
Materialeigenschaften
Die Eigenschaften der zu schweißenden Materialien spielen eine entscheidende Rolle bei der Bestimmung der Schweißqualität und der Fehlerwahrscheinlichkeit.
- Wärmeleitfähigkeit: Materialien mit hoher Wärmeleitfähigkeit, wie z. B. Aluminium, neigen dazu, Wärme schnell abzuleiten. Daher ist eine höhere Laserleistung oder langsamere Bewegungsgeschwindigkeit erforderlich, um eine ausreichende Durchdringung und Verschmelzung zu erreichen. Unzureichende Kontrolle kann zu Defekten wie fehlender Verschmelzung oder unvollständiger Durchdringung führen.
- Schmelzpunkt: Materialien mit unterschiedlichen Schmelzpunkten erfordern unterschiedliche Laserparameter. Titan hat beispielsweise einen hohen Schmelzpunkt und erfordert eine höhere Energiezufuhr, während niedrigschmelzende Materialien wie Zink bei unsachgemäßer Handhabung durchbrennen können.
- Reflektivität: Stark reflektierende Materialien wie Kupfer und bestimmte Aluminiumlegierungen können einen Teil der Laserenergie reflektieren und so die effektive Wärmezufuhr verringern. Dies kann zu unvollständiger Verschmelzung, ungleichmäßiger Durchdringung oder Spritzern führen, da reflektierte Energie die umliegenden Bereiche beeinträchtigen kann.
- Materialzusammensetzung und Verunreinigungen: Elemente wie Schwefel, Phosphor und Wasserstoff im Material können die Wahrscheinlichkeit von Defekten wie Porosität und Rissbildung erhöhen. Ein hoher Wasserstoffgehalt kann beispielsweise Porosität verursachen, während Schwefel und Phosphor das Risiko von Heißrissen erhöhen. Die Auswahl von Materialien mit geringem Verunreinigungsgrad oder die Durchführung von Vorschweißbehandlungen können dazu beitragen, diese Probleme zu mildern.
Schweißparameter
Die richtige Auswahl und Kontrolle der Laserschweißparameter ist entscheidend für die Vermeidung von Defekten. Zu den wichtigsten Parametern gehören:
- Laserleistung: Eine ausreichende Laserleistung ist für eine vollständige Durchdringung und Verschmelzung unerlässlich. Unzureichende Leistung kann zu einem Mangel an Verschmelzung oder unvollständiger Durchdringung führen, während übermäßige Leistung Durchbrand, Spritzer und Verformungen verursachen kann.
- Fahrgeschwindigkeit: Die Fahrgeschwindigkeit beeinflusst die Wärmezufuhr pro Längeneinheit der Schweißnaht. Eine zu hohe Geschwindigkeit kann dazu führen, dass das Material nicht ausreichend erhitzt wird, was zu Defekten wie fehlender Verschmelzung und unvollständiger Durchdringung führt. Umgekehrt kann eine zu niedrige Geschwindigkeit zu einer übermäßigen Wärmezufuhr führen, was zu Durchbrennen und Verformungen führt.
- Strahlfokus: Der richtige Strahlfokus ist für die Energiekonzentration entscheidend. Eine Fehlausrichtung oder falsche Fokusposition kann zu unzureichender Durchdringung, unregelmäßigen Nahtprofilen und Schweißporosität führen. Für eine tiefe Durchdringung ist ein fokussierter Strahl mit kleiner Punktgröße erforderlich, während ein defokussierter Strahl für breitere, flache Schweißnähte geeignet sein kann.
- Pulsdauer (beim gepulsten Laserschweißen): Die Pulsdauer beeinflusst die Energiemenge, die in jedem Puls abgegeben wird. Kurze Pulse reduzieren die Wärmezufuhr und minimieren das Risiko einer Verformung, weshalb sie sich ideal für empfindliche oder hitzeempfindliche Materialien eignen. Längere Pulse ermöglichen eine größere Durchdringung, können jedoch das Risiko von Defekten wie Spritzern und Porosität erhöhen.
Fugenkonstruktion
Die Gestaltung und Vorbereitung der Verbindung können die Schweißqualität und die Fehlerwahrscheinlichkeit erheblich beeinflussen.
- Passungstoleranz: Eine korrekte Passung der Verbindung ist für eine gleichbleibende Schweißqualität unerlässlich. Lücken oder Fehlausrichtungen zwischen Werkstücken können zu mangelnder Verschmelzung, Porosität oder ungleichmäßiger Durchdringung führen. Enge Passungen ermöglichen eine bessere Kontrolle des Schmelzbads und minimieren das Risiko von Defekten.
- Verbindungstyp: Verschiedene Verbindungstypen (z. B. Stumpf-, Überlapp-, Kehlnahtverbindungen) erfordern unterschiedliche Laserschweißtechniken und -parameter. Beispielsweise können Stumpfverbindungen mit schlechter Ausrichtung zu Hinterschneidungen oder mangelnder Verschmelzung führen, während Überlappverbindungen mit übermäßiger Überlappung zu Spritzern und unzureichender Verschmelzung führen können.
- Zugänglichkeit: Bei komplexen Strukturen kann ein eingeschränkter Zugang zur Verbindung die Reichweite des Laserstrahls einschränken, was zu unvollständiger Verschmelzung oder unregelmäßiger Perlenbildung führen kann. Bei Verbindungen mit eingeschränkter Zugänglichkeit sind eine ordnungsgemäße Befestigung und Laserausrichtung erforderlich.
- Vorbereitung und Reinigung: Die richtige Vorbereitung und Reinigung des Verbindungsbereichs ist entscheidend, da Oberflächenverunreinigungen zu Porosität, Rissbildung und Spritzern führen können. Durch die Reinigung werden Oxide, Öle und andere Verunreinigungen entfernt, die die Verschmelzung beeinträchtigen und Defekte verursachen können.
Umweltfaktoren
Die Umgebungsbedingungen im Schweißbereich können die Schweißqualität und das Auftreten von Defekten direkt beeinflussen.
- Umgebungstemperatur: Schweißen bei extremen Temperaturen, entweder zu kalt oder zu heiß, kann die Abkühlgeschwindigkeit der Schweißnaht beeinträchtigen und zu thermischer Spannung und Rissbildung führen. Kalte Umgebungen können beispielsweise zu einer schnellen Abkühlung führen, was zu spröden Schweißnähten und Rissen führt.
- Feuchtigkeit und Nässe: Feuchtigkeit in der Umgebung kann Wasserstoff in das Schweißbad einbringen, was das Risiko von Porosität und wasserstoffbedingten Rissen erhöht. Für qualitativ hochwertige Schweißnähte ist das Schweißen in einer trockenen, kontrollierten Umgebung oder das Ergreifen von Vorsichtsmaßnahmen zum Schutz vor Feuchtigkeitsbelastung unerlässlich.
- Qualität und Fluss des Schutzgases: Schutzgas schützt das geschmolzene Schweißbad vor atmosphärischer Verunreinigung. Unzureichender Schutzgasfluss oder die Verwendung von Gas mit geringer Reinheit kann zu Oxidation, Porosität und Verfärbung führen. Zusätzlich sollten je nach Materialanforderungen Schutzgase wie Argon und Helium verwendet werden, um Verunreinigungen vorzubeugen.
- Vibration und Bewegung: Umgebungsvibrationen oder Bewegungen in der Schweißvorrichtung können zu ungleichmäßigen Schweißnähten und anderen Defekten führen. Eine stabile Befestigung und die Minimierung externer Bewegungen sind unerlässlich, um gleichbleibende Ergebnisse zu gewährleisten.
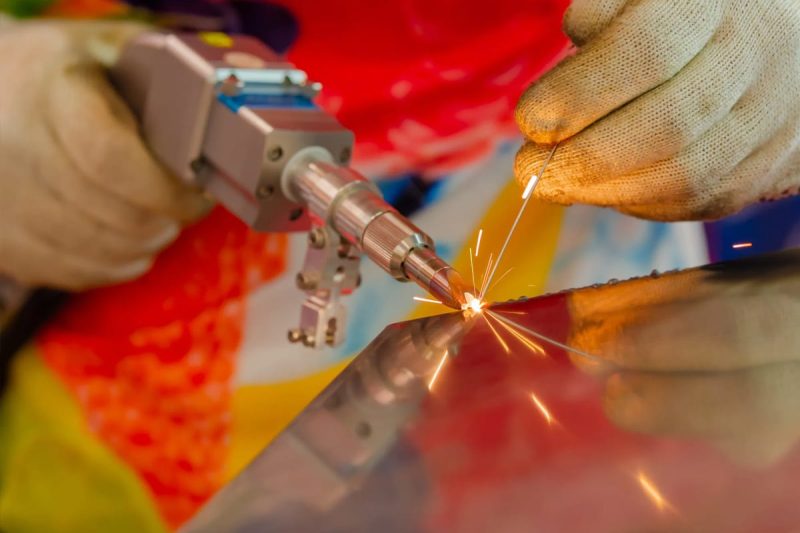
Weitere Überlegungen und bewährte Methoden
Richtige Materialauswahl
Die Auswahl der richtigen Materialien für das Laserschweißen ist von entscheidender Bedeutung, um qualitativ hochwertige Schweißnähte zu erzielen und Defekte zu minimieren.
- Materialkompatibilität: Stellen Sie sicher, dass die Grundmaterialien mit dem Laserschweißen kompatibel sind. Unterschiedliche Materialien reagieren aufgrund unterschiedlicher Schmelzpunkte, Wärmeleitfähigkeit und Reflektivität unterschiedlich auf Laserenergie. Beispielsweise können reflektierende Materialien wie Aluminium besondere Maßnahmen erfordern, um die Reflektion zu verringern und die Wärmeabsorption zu optimieren.
- Materialreinheit: Verwenden Sie Materialien mit geringen Mengen an Verunreinigungen wie Schwefel und Phosphor, die zu Porosität, Rissen und anderen Defekten führen können.
- Materialstärke: Berücksichtigen Sie die Stärke der zu schweißenden Materialien, da diese Einfluss auf die erforderliche Laserleistung und Wärmezufuhr hat.
Lasertyp und Einstellungen
Die Auswahl des geeigneten Lasertyps und die Feinabstimmung seiner Einstellungen sind entscheidende Faktoren für ein erfolgreiches Laserschweißen.
- Lasertyp: Wählen Sie je nach Anwendung zwischen Dauerstrichlasern (CW) und gepulsten Lasern. CW-Laser sind ideal für Hochgeschwindigkeitsschweißen, während gepulste Laser für empfindliche oder wärmeempfindliche Komponenten geeignet sind.
- Leistungs- und Geschwindigkeitseinstellungen: Optimieren Sie Laserleistung, Bewegungsgeschwindigkeit und Impulsdauer, um die gewünschte Durchdringung zu erreichen, Defekte wie Spritzer oder Porosität zu minimieren und die Wärmezufuhr zu steuern.
- Strahlfokus und -positionierung: Die richtige Strahlausrichtung und -fokussierung sind für eine gleichmäßige Energieverteilung und konsistente Schweißnähte von entscheidender Bedeutung.
Fugendesign und -anpassung
Eine ordnungsgemäße Konstruktion und Passung der Verbindungen gewährleistet eine gleichbleibende Schweißqualität und verringert die Wahrscheinlichkeit von Defekten wie mangelnder Verschmelzung, Porosität und Fehlausrichtung.
- Passungstoleranzen: Stellen Sie sicher, dass die Verbindungen dicht und gleichmäßig passen und minimieren Sie Lücken, die zu ungleichmäßiger Verschmelzung oder Porosität führen könnten.
- Zugänglichkeit der Fugen: Gestalten Sie die Fugen so, dass sie für den Laserstrahl leicht zugänglich sind. So wird das Risiko einer unvollständigen Verschmelzung oder unregelmäßiger Perlen minimiert.
- Vorbereitung der Verbindung: Reinigen und bereiten Sie die Verbindungsflächen gründlich vor, um Verunreinigungen wie Öle, Oxide und andere Verunreinigungen zu entfernen.
Auswahl des Schutzgases
Schutzgas schützt das geschmolzene Schweißbad vor atmosphärischer Verunreinigung und verhindert Oxidation, Porosität und andere Defekte.
- Gasart: Wählen Sie je nach Grundmaterial und gewünschten Schweißeigenschaften geeignete Schutzgase wie Argon, Helium oder Mischungen aus. Beispielsweise wird Argon häufig für Edelstahl verwendet, während Helium die Durchdringung bei dickeren Materialien verbessern kann.
- Durchflussrate: Stellen Sie sicher, dass die Durchflussrate des Schutzgases ausreicht, um das Schweißbad ohne Turbulenzen oder unzureichende Abdeckung abzudecken.
- Reinheit: Verwenden Sie hochreines Schutzgas, um Verunreinigungen zu vermeiden.
Behandlungen vor und nach dem Schweißen
Durch Behandlungen vor und nach dem Schweißen kann die Wahrscheinlichkeit von Defekten erheblich verringert und die Gesamtqualität der Schweißnaht verbessert werden.
- Reinigung vor dem Schweißen: Reinigen Sie Werkstücke gründlich, um Verunreinigungen wie Öl, Rost und Feuchtigkeit zu entfernen, die zu Porosität, Rissen und anderen Defekten führen können.
- Vorwärmen: Durch das Vorwärmen von Materialien, insbesondere solchen, die zur Rissbildung neigen, können Temperaturgradienten verringert und Eigenspannungen minimiert werden.
- Wärmebehandlung nach dem Schweißen: Führen Sie nach dem Schweißen Wärmebehandlungen wie Glühen oder Spannungsabbau durch, um Restspannungen zu reduzieren und die mechanischen Eigenschaften der Schweißnaht zu verbessern.
Bedienerschulung
Erfahrene Bediener spielen eine entscheidende Rolle bei der Gewährleistung gleichbleibend hochwertiger Laserschweißnähte.
- Techniktraining: Schulen Sie die Bediener im richtigen Umgang mit Laserschweißgeräten, einschließlich Positionierung, Geschwindigkeitskontrolle und Parameteranpassungen.
- Identifizierung von Mängeln: Schulen Sie die Bediener darin, häufige Mängel und deren Ursachen zu erkennen und die erforderlichen Anpassungen vorzunehmen, um ein erneutes Auftreten zu verhindern.
- Sicherheitsprotokolle: Stellen Sie sicher, dass die Bediener in den Lasersicherheitsverfahren geschult sind, um sich selbst und die Arbeitsumgebung zu schützen.
Wartung der Ausrüstung
Eine regelmäßige Wartung der Laserschweißausrüstung ist unerlässlich, um eine gleichbleibende Leistung sicherzustellen und Defekte zu vermeiden.
- Reinigung der Optik: Reinigen Sie Linsen, Spiegel und andere optische Komponenten regelmäßig, um die Strahlqualität und -genauigkeit aufrechtzuerhalten.
- Kalibrierung: Kalibrieren Sie Lasersysteme regelmäßig, um eine genaue Leistungsabgabe, Strahlausrichtung und Fokussierung sicherzustellen.
- Komponentenprüfung: Überprüfen und ersetzen Sie abgenutzte oder beschädigte Komponenten wie Düsen und Linsen, um die Schweißkonsistenz aufrechtzuerhalten.
Prozessüberwachung
Um gleichbleibende, fehlerfreie Schweißnähte zu erzielen, sind Prozessüberwachung und -kontrolle von entscheidender Bedeutung.
- Echtzeitüberwachung: Verwenden Sie Sensoren und Überwachungssysteme, um Abweichungen bei Schweißparametern wie Leistungsschwankungen, Vorschubgeschwindigkeit und Strahlfokus in Echtzeit zu erkennen und zu korrigieren.
- Datenprotokollierung: Zeichnen Sie Schweißparameter und -ergebnisse auf, um Trends zu analysieren, Grundursachen von Defekten zu ermitteln und kontinuierliche Verbesserungsmaßnahmen umzusetzen.
- Qualitätskontrollen: Führen Sie regelmäßige Kontrollen durch, einschließlich zerstörungsfreier Prüfmethoden (NDT), um die Schweißqualität zu überprüfen.
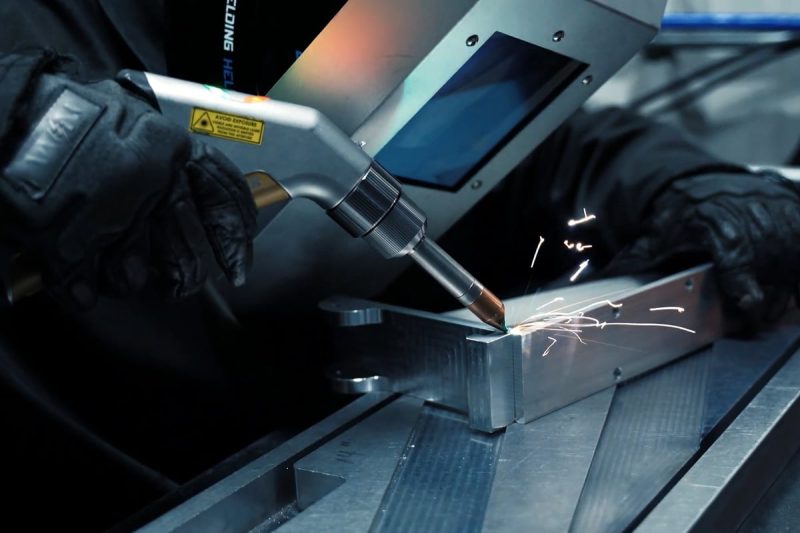
Zusammenfassung
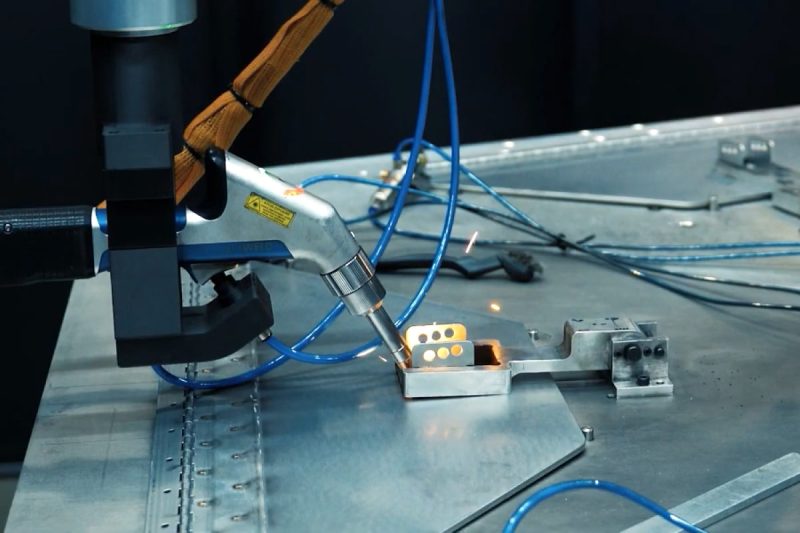
Holen Sie sich Laserschweißlösungen
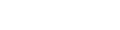
- [email protected]
- [email protected]
- +86-19963414011
- Nr. 3 Zone A, Industriegebiet Lunzhen, Stadt Yucheng, Provinz Shandong.