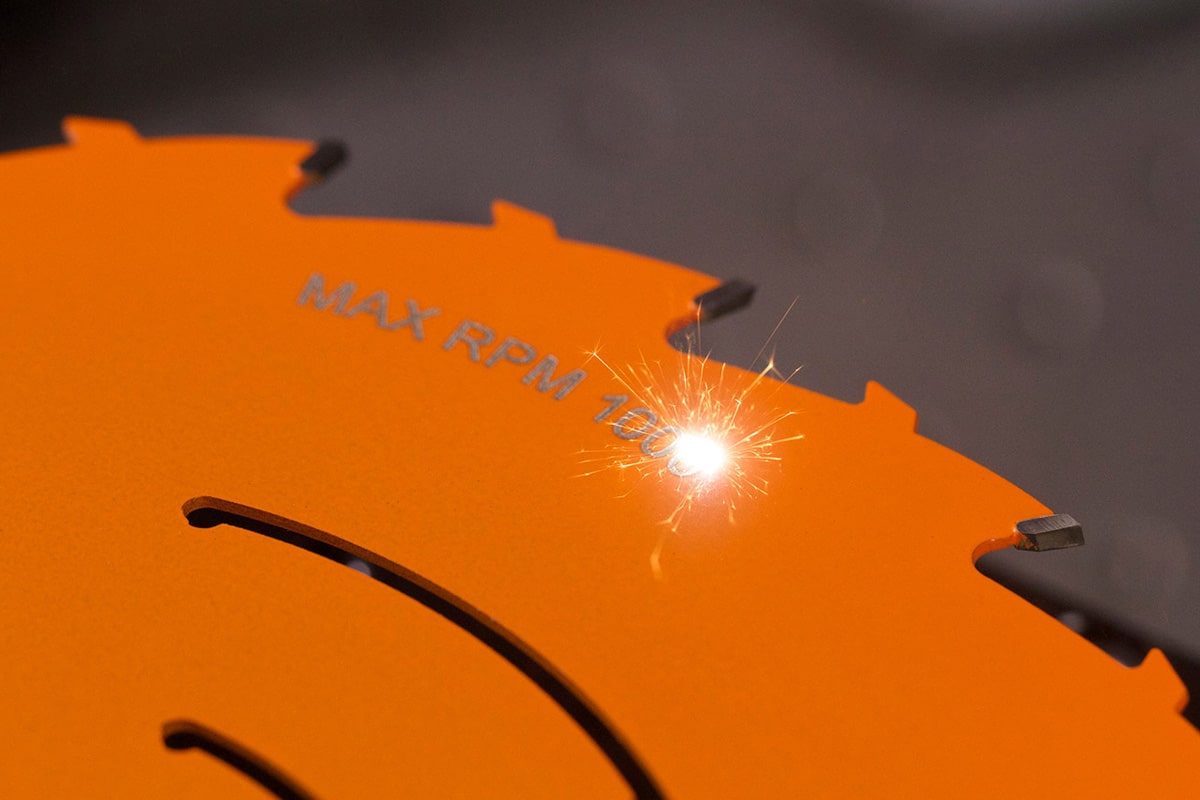
Was sind die Vorteile und Einschränkungen der Lasermarkierung?
Laser marking is an advanced and efficient marking technology widely used in industrial manufacturing for its precise and durable marking effects. According to different laser sources, laser marking systems are mainly divided into three types: fiber laser, CO2 laser, and UV laser. Each technology has unique advantages and limitations. Fiber laser is famous for its high precision and high speed, and is suitable for metals and some non-metals; CO2 laser performs well in non-metal applications, with both material compatibility and cost-effectiveness; and UV laser relies on cold marking technology and extremely high Precision, especially when working with transparent or exotic materials.
This article will focus on the characteristics of the three laser marking technologies, analyze them from multiple aspects such as material compatibility, efficiency, precision, and cost, and help readers gain a deep understanding of the advantages and disadvantages of each technology and their applicable scenarios. Through comparison and analysis, you will be able to choose the laser marking system that best suits your specific needs and provide accurate and efficient solutions for industrial production.
Inhaltsverzeichnis
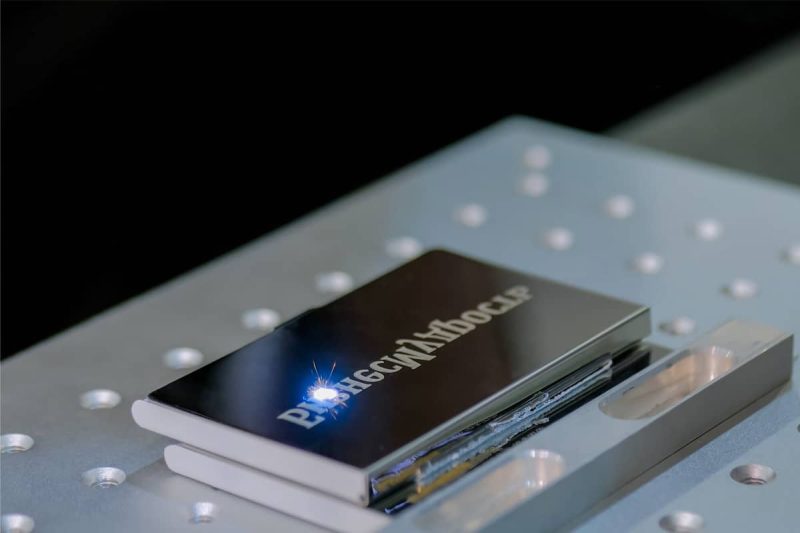
Einführung in die Lasermarkierung
Übersicht zur Lasermarkierung
Laser marking is a technology that uses a high-energy laser beam to permanently mark the surface of a material. By focusing the laser beam on a specific area, a physical or chemical reaction will occur on the surface of the material, forming a high-contrast mark. Compared with traditional marking methods, laser marking has the characteristics of non-contact, no consumables, high precision, and environmental protection. It can realize diversified markings such as text, patterns, QR codes, etc. on various materials. It is widely used in industrial manufacturing fields such as electronic products, medical devices, automotive parts, packaging, and handicrafts.
Types of Laser Marking Systems
Laser marking systems are mainly divided into the following three types according to different laser sources, each type is suitable for different materials and application scenarios:
Fiber laser marking system: A fiber laser generator is a laser generator that uses optical fiber doped with rare earth elements (such as erbium or ytterbium) as the gain medium. Fiber laser marking systems are known for their efficient energy conversion, ultra-long life, and high precision. They are particularly suitable for deep engraving, micro-processing, and high-speed marking of metals materials.
CO2 laser marking system: CO2 laser generator uses carbon dioxide gas as the working medium and is a common gas laser generator. CO2 laser marking system is mainly used for non-metallic materials such as wood, plastic, glass, paper, and fabric. It can achieve rapid marking on a large area and is widely used in the packaging and decoration industries for its cost-effective characteristics.
UV laser marking system: UV laser generator uses a shorter wavelength ultraviolet beam and adopts a “cold processing” process to mark the material surface with almost no heat effect. The UV laser marking system can achieve extremely high precision and details and is suitable for processing transparent or reflective materials such as glass, plastics, wafers, and medical products. It is an ideal choice for high-demand application scenarios.
These three laser marking systems each have their advantages and limitations, and users can choose the most suitable technology based on the marking material, accuracy requirements, and cost budget.
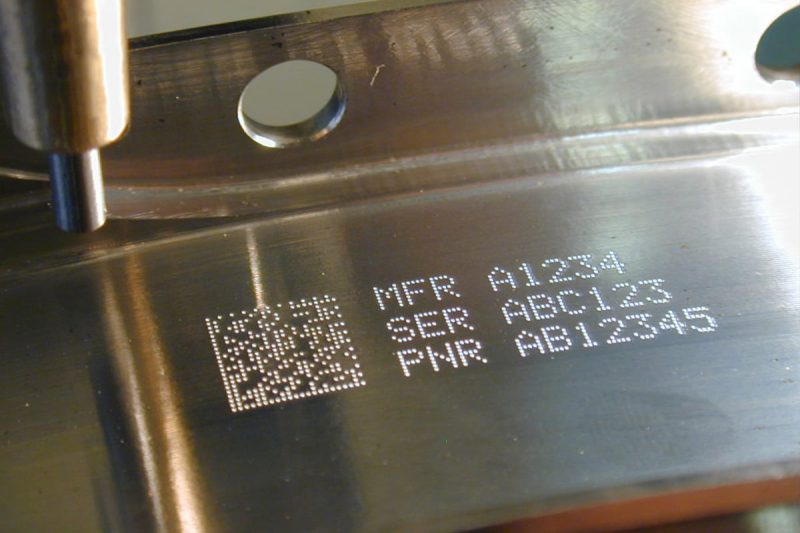
Advantages and Limitations of Fiber Laser Marking
A Faserlaser-Markierungsmaschine is a device that uses a high-energy beam generated by a fiber laser generator to accurately mark the surface of a material. With its high efficiency, stability, and versatility, the fiber laser marking machine occupies an important position in industrial production and is widely used in industries such as electronics, automobiles, medical, and consumer goods. The following will analyze its main advantages and limitations in detail.
Vorteil
High precision and quality: Fiber laser marking machines can focus an extremely fine light spot, making its marking accuracy reach the micron level. This high-precision feature makes it very suitable for use in production areas that require extremely high marking quality, such as marking electronic components, numbering medical devices, and engraving complex patterns.
Speed and efficiency: The fiber laser marking machine has an extremely fast marking speed, which can complete large-volume marking tasks in a short time and improve production efficiency. This makes it particularly practical in high-intensity production environments, such as high-speed marking applications on assembly lines.
Versatility (applicable to a variety of materials): Fiber laser marking machines are suitable for a variety of materials, including metals (such as stainless steel, aluminum, and copper) and some non-metals (such as plastics and ceramics). This versatility enables it to meet the diverse needs of different industries and applications.
Durability and reliability: Fiber laser generators have an extremely long service life (usually up to 100,000 hours or more) and require almost no maintenance during operation. This high reliability enables the equipment to work stably for a long time, reducing downtime and maintenance costs.
Low operating cost: Fiber laser marking machine does not need to consume consumables such as ink and chemicals, and only relies on electricity to operate, so the operating cost is low. At the same time, its high energy efficiency further reduces energy consumption, making it an economical and environmentally friendly choice.
Minimal material damage: The fiber laser marking machine uses non-contact processing, which will not cause mechanical damage or excessive thermal effects on the material surface, ensuring the marking quality while protecting the integrity of the material.
Limitation
Limited effectiveness on certain materials: Although fiber laser marking machines perform well on metal materials, they are limited in effectiveness on certain non-metallic materials (such as glass or transparent plastics). Such materials usually require other types of laser generators (such as UV lasers) to process.
High initial cost: The equipment purchase cost of the fiber laser marking machine is relatively high, which may be a large initial investment, especially for small businesses. However, low operating costs and long-term stability usually make up for this disadvantage.
Complex setup: Fiber laser marking machines require professional setup and debugging, including precise adjustment of laser power, marking speed, and focal length. This places certain demands on the operator’s technical level and may increase the initial learning and training costs.
Fiber laser marking machines have significant advantages in industrial manufacturing due to their high precision, high efficiency, versatility, and low operating costs. However, its limitations on specific materials, high initial costs, and complex setup also bring certain application challenges. When selecting a fiber laser marking machine, its advantages and disadvantages need to be weighed against specific production needs and budgets to maximize the potential of its technology.
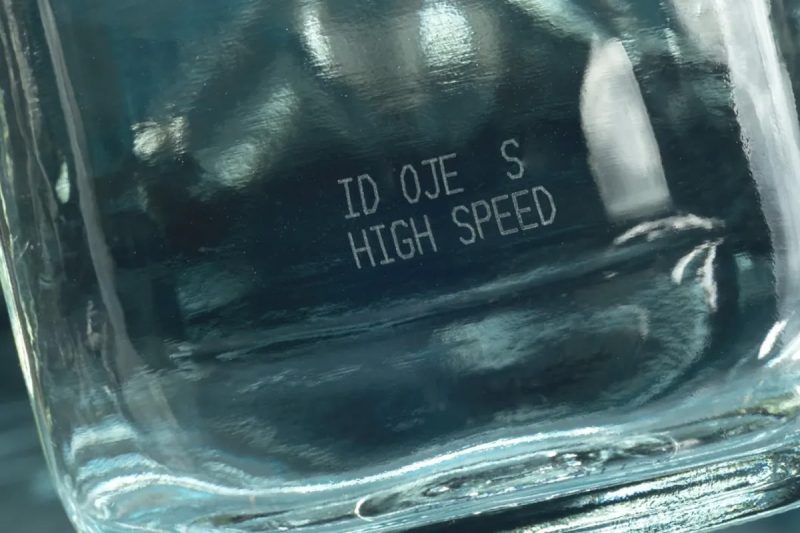
Advantages and Limitations of CO2 Laser Marking
A CO2-Laserbeschriftungsmaschine is a laser marking device that uses carbon dioxide gas as the working medium. It is mainly suitable for marking and engraving non-metallic materials. Due to its high stability, strong compatibility, and cost-effectiveness, it is widely used in packaging, decoration, electronics, clothing, and handicraft manufacturing industries. The following will elaborate on its advantages and limitations.
Vorteil
Versatility of material compatibility: CO2 laser marking machines excel in processing non-metallic materials and are compatible with a variety of materials such as plastics, wood, paper, leather, glass, ceramics, etc. This wide range of material adaptability makes it the preferred tool for marking and engraving in the non-metallic field, able to meet the diverse needs of multiple industries.
High-speed marking: CO2 laser marking machines work at high speeds and are particularly suitable for large-volume non-metallic product marking. For example, in the food and beverage industry, information such as production dates and barcodes can be quickly marked on packaging, greatly improving production efficiency.
Large marking area: Compared with other types of laser generators, CO2 laser marking machines can cover a larger marking range, which is very suitable for application scenarios that require processing large-size materials or large-volume markings, such as fabric pattern engraving or advertising material production.
Cost-effectiveness for non-metallic applications: CO2 laser marking machines are cost-effective on non-metallic materials, and can complete high-quality marking or engraving tasks at a lower cost. At the same time, their low consumables requirements help reduce operating costs in the long run.
Easy to integrate: CO2 laser marking machines are easy to integrate into existing production lines or automation systems. Through simple configuration, the equipment can be seamlessly connected to the assembly line to support efficient industrial production needs.
Limitation
Limited effectiveness on metals: Due to the laser wavelength characteristics of CO2 laser marking machines, their marking effect on metal materials is not as good as that of fiber laser generators. This limits its application in the field of metal processing and requires reliance on other types of laser generators to supplement it.
High maintenance requirements: The optical components of CO2 laser marking machines require regular cleaning and calibration, and their laser tubes have a limited life and need to be replaced. This high maintenance requirement may increase the long-term cost of use and downtime of the equipment.
Heat generation: CO2 laser marking machines generate a lot of heat during operation, which may cause thermal damage to some sensitive materials. At the same time, an additional cooling system is required to control the temperature of the equipment, which further increases the complexity of equipment operation.
CO2 laser marking machines play an important role in many industries due to their excellent material compatibility and cost-effective non-metallic applications. However, their limitations in metal processing, floor space requirements, and maintenance costs also need to be taken into account. In practical applications, users should reasonably evaluate the advantages and disadvantages of CO2 laser marking machines based on their own material and process requirements, so as to achieve efficient and economical production goals.
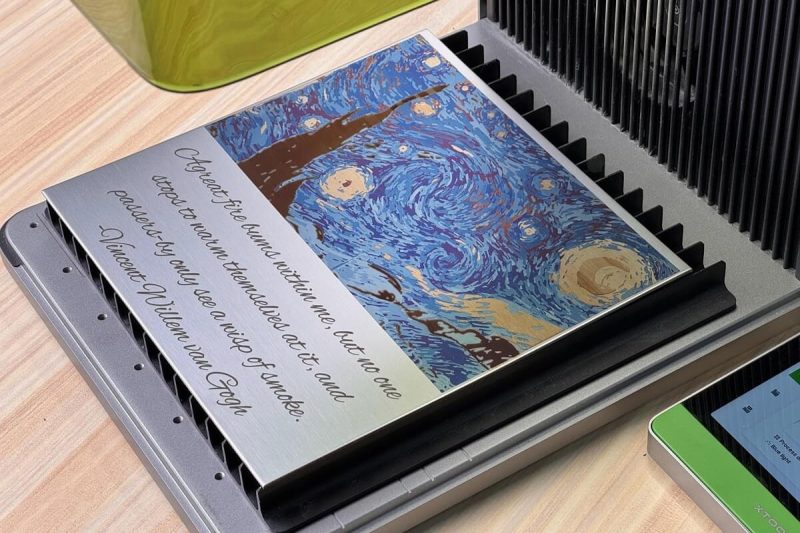
Advantages and Limitations of UV Laser Marking
UV laser marking machines use short-wavelength ultraviolet beams to mark the surface of materials in a “cold processing” manner. This technology effectively avoids deformation or damage to the material by reducing thermal effects and is particularly suitable for high-precision and high-demand marking applications. UV laser marking machines are widely used in electronics, medical devices, semiconductors, and high-end consumer products, and are ideal for processing special materials such as glass, transparent plastics, and reflective materials. The following will detail its advantages and limitations.
Vorteil
High precision and details: UV laser marking machine can focus a very small spot, making the marking details visible, with an accuracy of up to a micron level. It is suitable for marking needs of complex patterns, tiny text, or high-precision QR codes, such as chips, circuit boards, and precision instruments.
Cold marking process (no thermal damage): The UV laser marking machine adopts a “cold processing” process, which avoids material burning, deformation, or edge blur by reducing the thermal effect on the material surface. This feature makes it the preferred technology for processing heat-sensitive materials (such as plastic films and medical devices).
Effective for transparent and reflective materials: UV lasers have excellent marking performance on glass, crystal, transparent plastics, and metal coatings due to their short wavelength and can penetrate transparent materials or act on highly reflective surfaces. This makes them widely used in medical packaging and optical component manufacturing.
Minimum heat-affected zone (HAZ): The “cold processing” characteristics of UV lasers make the heat-affected zone extremely small, with almost no change to the physical properties and surface structure of the material. This is especially important for high-precision processing scenarios that require maintaining the original properties of the material.
Diverse material compatibility: UV laser marking machines can process almost all materials, including plastics, glass, ceramics, silicon wafers metal coatings, etc. This wide range of material adaptability makes it an important tool for processing special or difficult materials.
Limitation
Higher initial cost: The manufacturing cost of the laser generator of the UV laser marking machine is higher, and the equipment price is significantly higher than that of fiber laser and CO2 laser equipment. This can be a significant financial burden for small businesses with limited budgets.
Slow marking speed: Compared with fiber and CO2 lasers, UV laser marking machines have a slow processing speed, and are difficult to meet the extreme demand for efficiency in mass production. This may become a major limitation in scenarios that require high productivity.
Limited penetration depth: Due to the low power of UV lasers, their marking depth is shallow, which makes it difficult to meet some requirements for deep engraving or cutting of material surfaces. This may be limited to thick materials or heavy industrial applications.
Complex maintenance and short life: UV laser generators have a short service life and require high maintenance of optical components, which may increase operating costs and equipment downtime. This places higher demands on technical support for daily use.
Complex setup and operation: UV laser marking machines require precise adjustment of optical parameters (such as focal length, power, and wavelength), and their setup and debugging process is relatively complex. This requires the high technical skills of operators and high initial training costs.
UV laser marking machines have become the preferred equipment for special applications due to their high precision, cold processing, and multi-material compatibility. However, their high initial cost, speed limitations, and maintenance complexity may bring certain challenges to applications. When selecting a UV laser marking machine, users should comprehensively evaluate its advantages and disadvantages, combined with specific materials and application requirements, to ensure the efficiency and economy of technology selection.
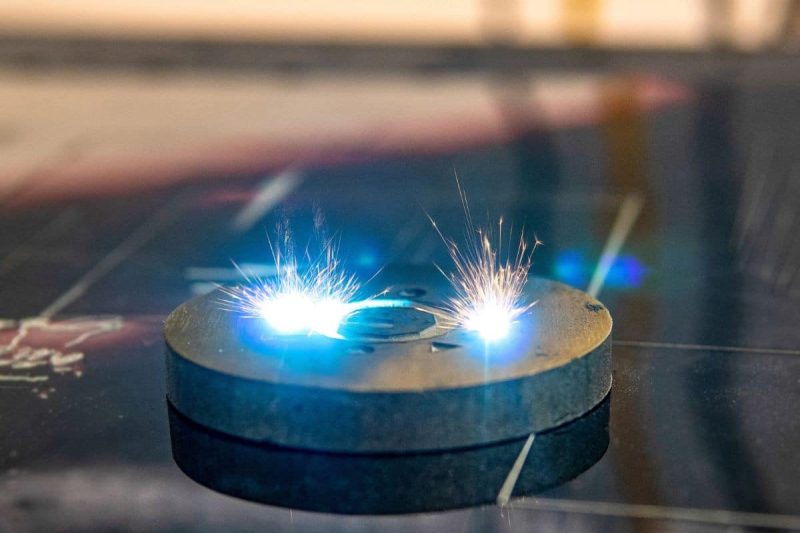
Comparative Analysis of Fiber Optic, CO2 and UV Lasers
Fiber laser, CO2 laser, and UV laser have their characteristics and are suitable for different materials and scenarios. Fiber laser is suitable for metal processing, CO2 laser is good for non-metallic applications, and UV laser is good at high precision and cold processing. Next, we will compare these three marking methods in detail from many aspects.
Materialkompatibilität
- Fiber laser: mainly suitable for metal materials, and also has good processing performance for some non-metals (such as plastics).
- CO2 laser: good at processing non-metal materials, and also has certain compatibility with some metals.
- UV laser: particularly suitable for processing transparent materials (such as glass, and transparent plastic) and reflective materials, and has a wide range of material adaptability.
Markiergeschwindigkeit und -effizienz
- Fiber laser: The fastest marking speed, suitable for efficient production needs.
- CO2 laser: The speed is also relatively high, suitable for large-scale non-metallic marking.
- UV laser: The speed is relatively slow, more suitable for high-precision and special material marking applications.
Anschaffungskosten
- Fiber laser: The initial equipment cost is high, but the long-term economical use is good.
- CO2 laser: The cost is relatively medium, and it is an economical choice for non-metal processing.
- UV laser: The equipment cost is the highest, suitable for high-end and special application scenarios.
Betriebskosten
- Fiber laser: Lowest operating cost due to low maintenance and low energy consumption.
- CO2 laser: Moderate operating cost, requires regular maintenance and laser tube replacement.
- UV laser: Moderate operating cost, requires more frequent maintenance and replacement of optical components.
Precision and Detail
- Fiber laser: has high precision and good detail performance, suitable for most industrial applications.
- CO2 laser: has medium precision and detail performance, suitable for non-metallic marking and large-size engraving.
- UV laser: has the highest precision and detail performance, especially suitable for micro-processing and demanding application scenarios.
Wärmeeinflusszone (HAZ)
- Fiber laser: small heat-affected zone, which can reduce material damage.
- CO2 laser: large heat-affected zone, which may cause damage to heat-sensitive materials.
- UV laser: the heat-affected zone is the smallest, achieving “cold processing” and almost zero thermal damage to the material.
Through the above comparison, users can choose the most suitable laser marking technology according to factors such as material type, precision requirements, production efficiency, and budget.
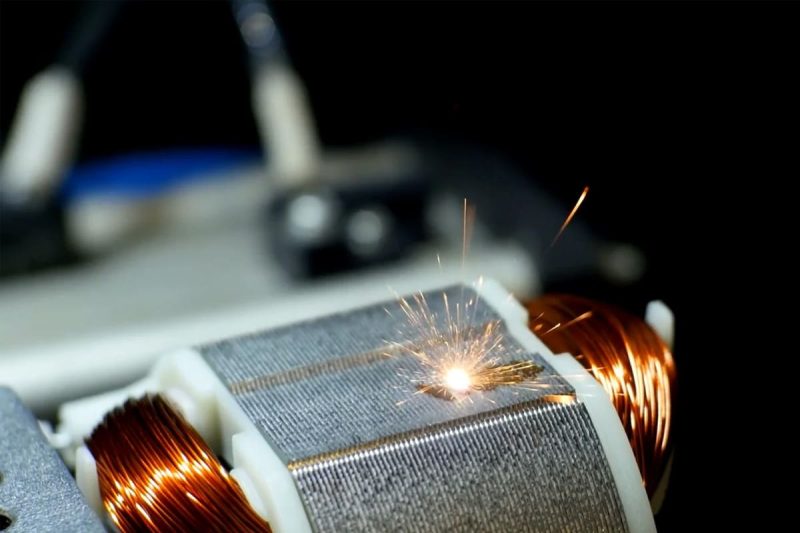
Application of Laser Marking Technology
Laser marking technology has become a core tool in modern industry due to its accuracy, efficiency, and wide material adaptability. According to the characteristics of different laser types, fiber laser, CO2 lase,r and UV laser play a unique role in their respective fields and meet diverse application needs. The following will analyze the main application scenarios of the three laser technologies.
Applications of Fiber Laser
Fiber laser marking machines are widely used in industrial manufacturing due to their excellent metal processing capabilities and high-speed marking performance.
- Metal marking: Fiber lasers can efficiently process a variety of metal materials such as stainless steel, aluminum, copper, and iron, making them ideal for marking serial numbers, QR codes, and logos in the manufacture of automotive parts, aviation equipment, and tools.
- High-speed marking: Fiber lasers are widely used in the assembly line production of electronic components, communication equipment, and consumer electronics due to their fast and accurate marking capabilities, and can quickly complete large-scale marking tasks.
- Deep engraving and micromachining: Fiber lasers can also be used to deeply engrave metals or achieve high-precision micromachining on complex shapes to meet the special needs of the mold manufacturing and precision instrument industries.
Application of CO2 laser
CO2 laser marking machines have become an important tool in the packaging, decoration, and handicraft industries due to their compatibility with non-metallic materials.
- Plastic marking: CO2 lasers can make clear and lasting marks on plastic materials such as PVC and ABS, and are widely used in marking home appliance housings, bottle caps, and electronic housings.
- Wood engraving: Suitable for fine engraving and decoration of wood, such as texture and pattern production for furniture, crafts, and building materials.
- Glass and ceramic marking: On glass and ceramic surfaces, CO2 lasers can achieve high-contrast markings for high-end packaging, kitchenware, and decorative products.
- Fabric processing: In the clothing and textile industries, CO2 lasers are used for fabric cutting and engraving of personalized patterns, combining efficiency and beauty.
Application of UV laser
UV laser marking machines focus on special fields that require extremely delicate markings due to their high precision and cold processing characteristics.
- Precision electronic components: UV lasers mark important information such as model, brand logo, and production batch on chips, semiconductors, and circuit boards with micron-level precision to ensure product traceability.
- Medical devices: In medical devices and packaging, UV lasers are used to mark fine text or patterns while avoiding any damage to the surface of the material. They are commonly used in the marking of surgical instruments and disposable medical devices.
- Glass products: UV lasers are suitable for marking high-precision patterns or characters on glass surfaces. They are used in optical components, glass screens, and high-end packaging.
- For high-end consumer products: Such as watches, jewelry, and cosmetics packaging, UV lasers can achieve delicate pattern markings to enhance the brand value and market competitiveness of products.
Through the analysis of the application of fiber laser, CO2 laser, and UV laser in different materials and industries, it can be seen that each laser technology has its unique advantages. When enterprises choose laser marking equipment, they should choose the most appropriate technical solution according to their material requirements, precision requirements, and production scale to achieve the best processing effect and economic benefits.
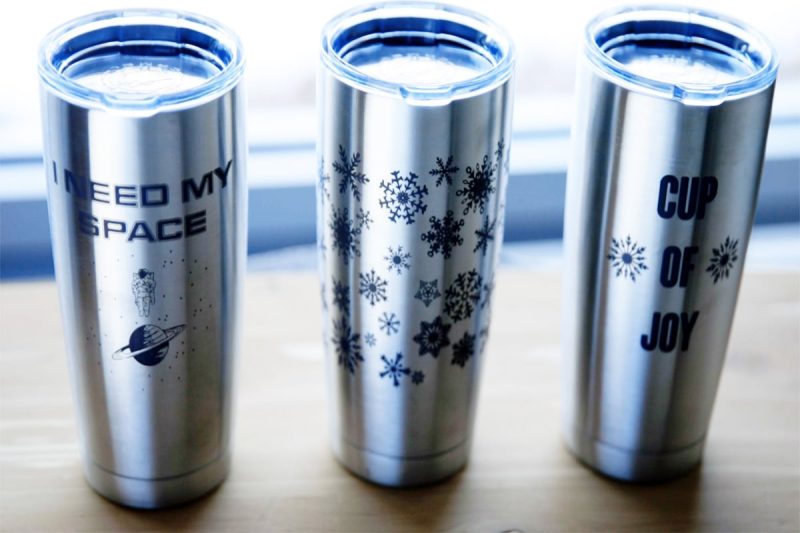
Zusammenfassen
Laser marking technology has occupied an important position in the modern manufacturing industry with its high efficiency, precision, and environmental protection. Fiber laser, CO2, and UV laser systems have their characteristics and can meet the diverse needs from metal to non-metal, from high-speed processing to high-precision micro-marking. Fiber laser is suitable for metal processing with its fast speed, low cost, and strong compatibility; CO2 laser has an advantage in the non-metal field with its wide material adaptability and economic efficiency; UV laser stands out in special materials and high-end applications with its cold processing technology and extremely high precision.
In practical applications, choosing the right laser marking technology requires comprehensive consideration of factors such as material type, processing requirements, production efficiency, and budget. By rationally selecting and configuring laser marking equipment, companies can achieve higher production efficiency, better processing quality, and lower operating costs, bringing long-term competitive advantages to modern manufacturing.
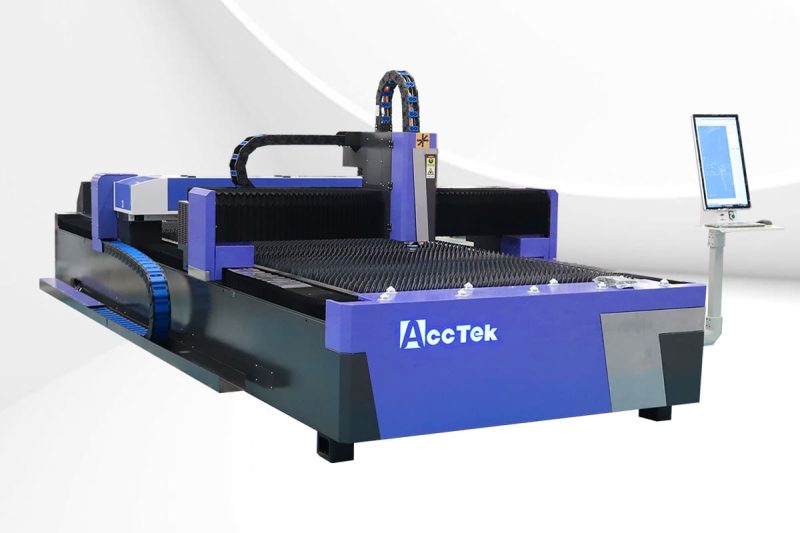
Holen Sie sich Laserlösungen
When choosing laser marking equipment, it is important to find a machine that suits your needs. AccTek-Laser is your trusted partner. We offer a wide range of Laserbeschriftungsmaschinen, covering three types: fiber laser, CO2 laser and UV laser. Whether you need to process metal, non-metal, or special materials, we can recommend the most suitable solution for you.
Just tell us your daily marking materials and specific needs, and our professional team will recommend the most cost-effective equipment for you. At the same time, we provide full-service support, including machine warranty, installation guidance, and comprehensive operation training, to ensure that every customer can quickly get started and give full play to the performance of the equipment. Choosing AccTek Laser means choosing professional, efficient, and considerate services to add a strong boost to your production!
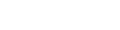
Kontaktinformationen
- [email protected]
- [email protected]
- +86-19963414011
- Nr. 3 Zone A, Industriegebiet Lunzhen, Stadt Yucheng, Provinz Shandong.
Holen Sie sich Laserlösungen