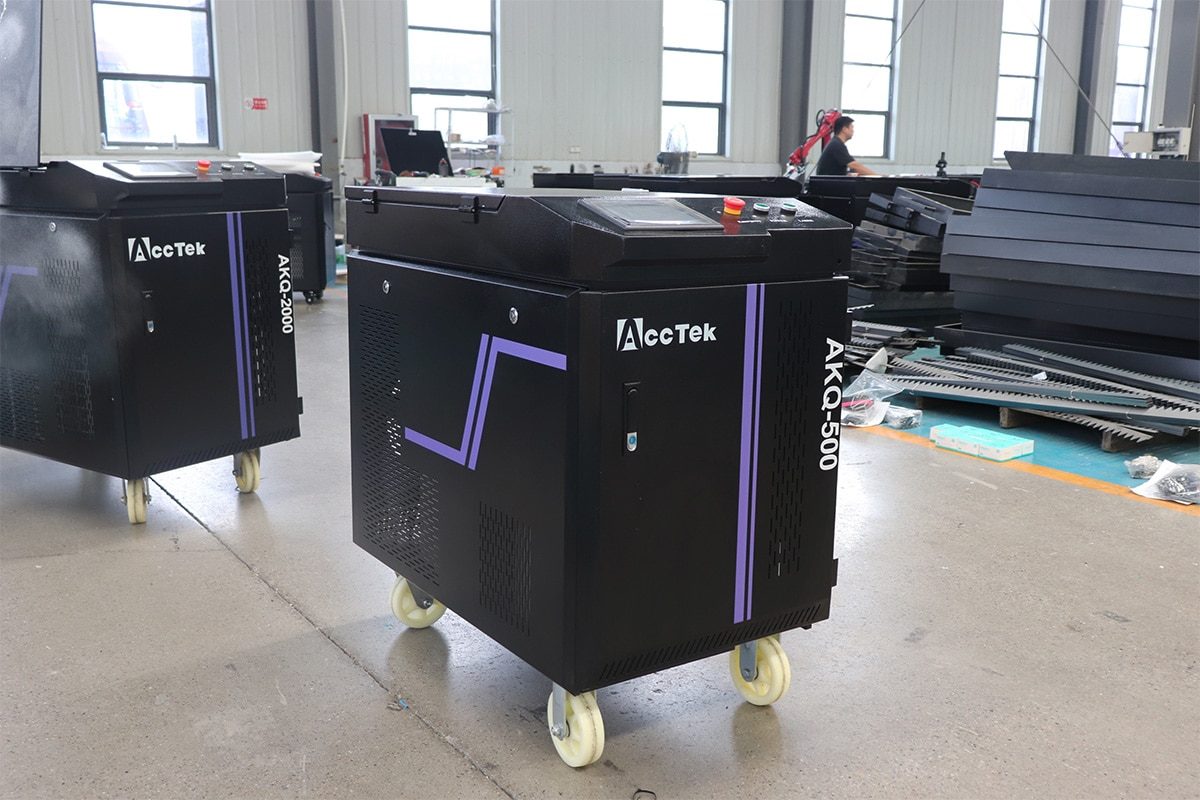
Was sind die häufigsten Probleme bei Laserreinigungsgeräten?
Als fortschrittliches berührungsloses Reinigungsgerät entfernt eine Laserreinigungsmaschine mit hochenergetischen Laserstrahlen Schadstoffe von der Oberfläche des Substrats. Sie wird häufig zur industriellen Rostentfernung, Beschichtungsentfernung, Schimmelreinigung und zum Schutz kultureller Relikte eingesetzt. Im Vergleich zu herkömmlichen Reinigungsmethoden hat sich die Laserreinigungstechnologie aufgrund ihrer Vorteile wie hoher Effizienz, Umweltschutz und geringer Beschädigung des Substrats in vielen Branchen allmählich zur bevorzugten Reinigungsmethode entwickelt.
Jedoch, Laserreinigungsmaschinen Im tatsächlichen Betrieb treten immer noch einige häufige Probleme auf, z. B. unzureichende Reinigungseffizienz, thermische Schäden an Substraten, hohe Betriebskosten, Sicherheitsrisiken und eingeschränkte Materialverträglichkeit. Diese Probleme können die Reinigungswirkung und die langfristige Nutzung der Geräte beeinträchtigen. Daher ist es sehr wichtig, diese Probleme gründlich zu verstehen und richtig zu lösen.
Inhaltsverzeichnis
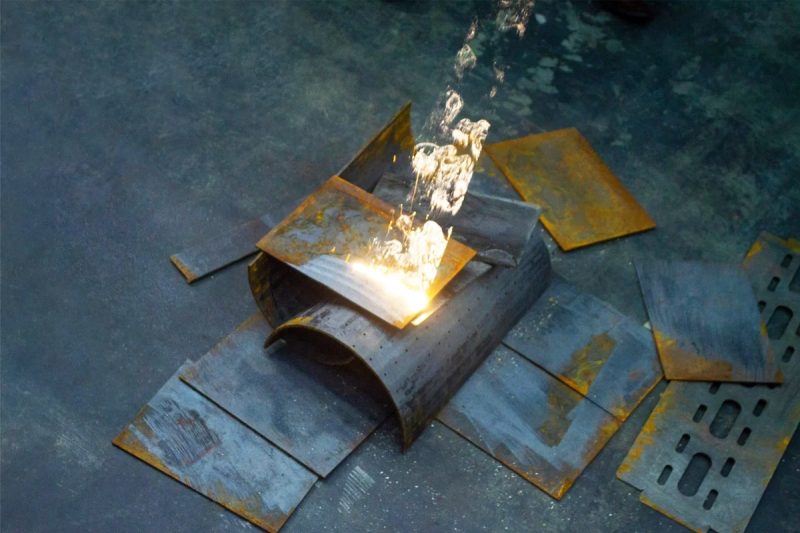
Überblick zur Laserreinigungstechnologie
Laserreinigung ist eine moderne zerstörungsfreie Reinigungstechnologie, bei der ein hochenergetischer Laserstrahl auf die Oberfläche des Materials einwirkt, um Schadstoffe, Oxidschichten oder andere unerwünschte Anhaftungen schnell zu verdampfen, zu zersetzen oder abzulösen, ohne das Substrat physisch abzunutzen. Diese Technologie hat in den letzten Jahren große Aufmerksamkeit erhalten und wurde nach und nach in vielen Bereichen wie der industriellen Fertigung, der Automobilwartung, der Luft- und Raumfahrt, dem Schiffbau und dem Schutz kultureller Relikte eingesetzt. Aufgrund ihrer präzisen und umweltfreundlichen Eigenschaften ist sie in vielen Branchen zur bevorzugten Reinigungsmethode geworden.
So funktioniert die Laserreinigung
Das Kernprinzip der Laserreinigung besteht darin, einen hochintensiven Laserstrahl auf die Reinigungsoberfläche zu fokussieren, wodurch die Verunreinigungen die Lichtenergie absorbieren und sich schnell ausdehnen, verdampfen oder zersetzen und durch physikalische Kraft und Wärmeenergie entfernt werden. Der spezifische Prozess umfasst zwei Hauptschritte:
- Laserwirkungsprozess: Der Laserstrahl konzentriert sich mit extrem hoher Energiedichte auf die Oberfläche des Schadstoffs, und die Temperatur der Schadstoffoberfläche steigt stark an, wodurch sich die Schadstoffmoleküle ausdehnen oder verdampfen. Das Substrat absorbiert weniger Laserenergie und behält eine niedrigere Temperatur bei, wodurch übermäßige thermische Effekte vermieden werden.
- Sofortiges Ablösen: Der erhitzte Schadstoff löst sich aufgrund der schnellen Ausdehnung vom Substrat und bildet winzige Partikel, Gas oder Plasma. Im Allgemeinen wird es mit einem Rauchabscheider kombiniert, um zu verhindern, dass diese verdampften Produkte und Partikel in die Luft gelangen.
Vorteile der Laserreinigungstechnologie
Im Vergleich zu herkömmlichen mechanischen, chemischen und Ultraschall-Reinigungsmethoden bietet die Laserreinigung eine Reihe wesentlicher Vorteile:
- Berührungslos: Bei der Laserreinigung ist kein Kontakt mit der Materialoberfläche erforderlich, wodurch Reibung und Verschleiß vermieden werden. Daher eignet es sich für Teile mit hohen Präzisionsanforderungen und wärmeempfindlichen Materialien.
- Umweltschutz: Bei der Laserreinigung werden keine chemischen Lösungsmittel benötigt, der Abfall besteht nur aus wenigen Partikeln und Gasen und die entstehenden Schadstoffe haben weniger negative Auswirkungen auf die Umwelt.
- Hohe Präzision und Steuerbarkeit: Der Laser kann Energie, Wellenlänge und Pulsdauer genau steuern und eignet sich für die Feinbearbeitung und Reinigung im Mikronbereich, wodurch eine Beschädigung der Substratoberfläche vermieden wird.
- Breites Spektrum an Materialanwendbarkeit: Die Laserreinigung kann auf eine Vielzahl von Materialien wie Metalle, Keramik, Gummi, Glas usw. angewendet werden und bietet ein breites Spektrum an Anpassungsmöglichkeiten.
Typische Anwendungen der Laserreinigung
Die Anwendungsmöglichkeiten der Laserreinigung sind vielfältig und decken viele Bereiche ab:
- Industrielle Rostentfernung: Durch die Laserreinigung können Oxidschichten, Rost usw. effektiv von Metalloberflächen entfernt werden und sie eignet sich besonders für die Rostentfernung von Präzisionsteilen und großen Strukturen.
- Entfernen von Beschichtungen: Wird zum Entfernen von Farbe, Beschichtungen usw. auf Metalloberflächen verwendet und häufig zum Entfernen von Beschichtungen im Automobilbau sowie in der Luft- und Raumfahrt eingesetzt.
- Formenreinigung: Durch die Laserreinigung können Rückstände auf der Oberfläche von Kunststoff- und Gummiformen präzise entfernt, der Formverlust reduziert und die Produktqualität verbessert werden.
- Schutz von Kulturdenkmälern: Mithilfe der Laserreinigungstechnologie können Schmutz und Oxidschichten von Kulturdenkmälern, Steinmetzarbeiten und anderen Kunstwerken entfernt und diese repariert und geschützt werden, ohne die Kulturdenkmälern zu beschädigen.
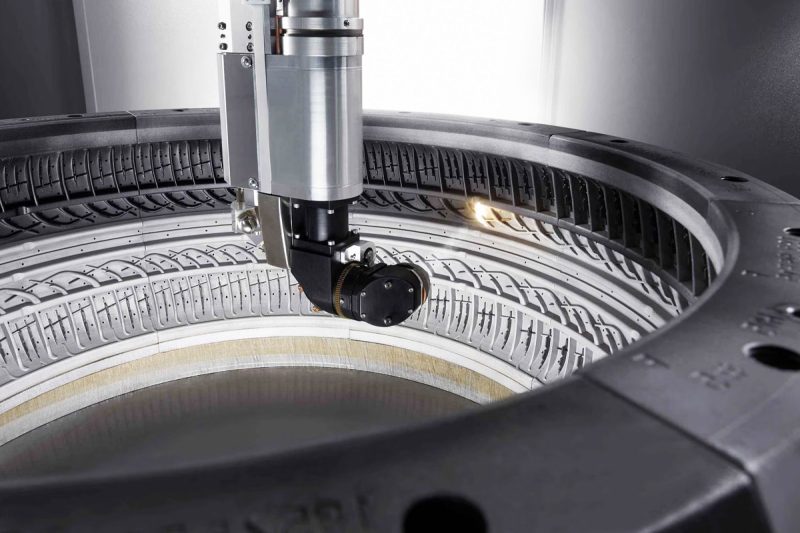
Häufige Probleme bei Laserreinigungsmaschinen
Als neue Art industrieller Reinigungsmethode wird die Laserreinigung in vielen Bereichen häufig eingesetzt. Im tatsächlichen Einsatz gibt es jedoch immer noch einige häufige Probleme in Bezug auf die Reinigungswirkung der Geräte, den Substratschutz, die Betriebskosten, die Sicherheit und die Materialverträglichkeit. Diese Probleme beeinträchtigen nicht nur die Reinigungswirkung, sondern können auch zu erhöhten Betriebskosten der Geräte oder Sicherheitsrisiken führen. Um die Reinigungseffizienz und die Lebensdauer der Geräte zu verbessern, ist es daher sehr wichtig, die Ursachen dieser Probleme zu verstehen und geeignete Gegenmaßnahmen zu ergreifen.
Unzureichende Reinigungsleistung
Eine unzureichende Reinigungsleistung ist eines der häufigsten Probleme bei der Laserreinigung. Sie äußert sich in der Regel in langsamer Reinigungsgeschwindigkeit, vielen Oberflächenrückständen nach der Reinigung oder ungleichmäßiger Reinigung. Die Gründe für dieses Problem sind:
- Falsche Laserparameter: Die Kernparameter der Laserreinigung wie Pulsenergie, Wellenlänge, Pulsdauer und Strahldurchmesser wirken sich direkt auf die Reinigungswirkung aus. Wenn die Pulsenergie zu niedrig ist, reicht die Energiedichte des Lasers nicht aus, um die Verunreinigungen effektiv zu entfernen, was zu einer unvollständigen Reinigung führt. Wenn die Pulsenergie zu hoch ist, können die Verunreinigungen zwar entfernt werden, es kann jedoch auch zu Schäden am Substrat kommen, insbesondere bei spröderen Materialien.
- Probleme mit der Strahlqualität: Die Strahlqualität des Lasers wirkt sich direkt auf die Reinigungseffizienz und -qualität aus. Ungleichmäßige Strahlen oder ein instabiler Fokus führen dazu, dass die Laserenergie nicht auf die Verunreinigungen fokussiert werden kann, was die Reinigungswirkung verringert. Darüber hinaus führt die Inkonsistenz des Strahlprofils auch dazu, dass der Reinigungsbereich ungleichmäßig wird, was dazu führt, dass einige Bereiche über- oder untergereinigt werden.
- Oberflächenverunreinigungstyp: Verschiedene Arten von Verunreinigungen haben unterschiedliche Absorptionsraten für Laser. Beispielsweise gibt es große Unterschiede in den Absorptionsraten von Metalloxidschichten, Fett, Farbschichten usw. Einige Verunreinigungen verdampfen leichter durch die Einwirkung von Hochenergielasern, während andere spezifische Parameter erfordern, um die Reinigungseffizienz zu verbessern. Die Wahl der geeigneten Kombination von Laserparametern ist für den Umgang mit verschiedenen Verunreinigungen von entscheidender Bedeutung.
Thermische Beschädigung des Substrats
Da bei der Laserreinigung ein hochenergetischer Laserstrahl auf die Materialoberfläche einwirkt, kann es bei unsachgemäßer Handhabung zu thermischen Schäden an der Substratoberfläche kommen:
- Oberflächenschmelzen oder -verformen: Wenn die Laserleistung zu hoch eingestellt ist oder die Reinigungszeit zu lang ist, steigt die Oberflächentemperatur des Materials schnell an, was dazu führen kann, dass die Oberflächenschicht schmilzt oder sich verformt, insbesondere bei wärmeempfindlichen Materialien wie Metallen oder Kunststoffen. Dieser thermische Effekt beeinträchtigt die physikalischen Eigenschaften des Materials und kann sogar strukturelle Schäden verursachen.
- Bildung von Mikrorissen: Bei einigen spröden Materialien (wie Keramik, Glas usw.) kann die hohe Temperatur der Laserreinigung Mikrorisse verursachen, insbesondere bei wiederholter Reinigung oder langfristiger hoher Leistung. Mikrorisse beeinträchtigen nicht nur das Aussehen, sondern können auch die mechanische Festigkeit des Materials schwächen, was zu einer verkürzten Lebensdauer führt.
Hohe Betriebskosten
Die hohen Betriebskosten von Laserreinigungsgeräten sind in der Regel einer der wichtigsten Faktoren, über die sich Benutzer Sorgen machen. Diese Kosten ergeben sich hauptsächlich aus den folgenden Aspekten:
- Energieverbrauch: Laserreinigungsgeräte verbrauchen viel Energie, wenn sie mit hoher Leistung arbeiten, insbesondere beim Reinigen großer Flächen und starker Verschmutzung. Der Energiebedarf der Geräte kann zu höheren Betriebskosten führen. Insbesondere bei häufigem Einsatz fallen die Kosten für den Energieverbrauch höher aus.
- Wartungs- und Reparaturkosten: Laserreinigungsgeräte enthalten mehrere Präzisionskomponenten wie Laseroptik, Laserquellen und Kühlsysteme usw. Diese Komponenten müssen regelmäßig gewartet werden, um den normalen Betrieb des Geräts zu gewährleisten. Insbesondere optische Komponenten und Laserquellen können bei langfristigem Hochleistungsbetrieb leicht beschädigt werden, und die Ersatzkosten sind hoch. Darüber hinaus ist auch die Wartung des Kühlsystems von entscheidender Bedeutung. Wenn das Kühlsystem ausfällt, kann das Laserreinigungsgerät aufgrund von Überhitzung abgeschaltet werden.
Sicherheitsfrage
Beim Laserreinigungsprozess kommen Hochleistungslaser zum Einsatz. Unsachgemäßer Betrieb birgt Sicherheitsrisiken für Bediener und Umwelt, vor allem in den folgenden Aspekten:
- Augen- und Hautschäden: Der bei der Laserreinigung erzeugte Hochenergielaser ist direkt schädlich für Haut und Augen, insbesondere für die Augen des Bedieners, und die Einwirkung des Lasers kann zu dauerhaften Schäden führen. Daher müssen Bediener Laserschutzbrillen und Schutzausrüstung tragen, die den Standards entsprechen und den Sicherheitsvorschriften entsprechen.
- Rauch- und Partikelemissionen: Bei der Laserreinigung verdampfen Schadstoffe bei hohen Temperaturen und bilden Rauch und winzige Partikel. Wenn diese Gase und Partikel nicht rechtzeitig entfernt werden, können sie die Luftqualität beeinträchtigen und sich negativ auf die Gesundheit des Bedieners auswirken. Aus diesem Grund ist es besonders wichtig, mit einem wirksamen Rauchabzugs- und Filtersystem ausgestattet zu sein.
Begrenzte Materialkompatibilität
Die Anwendbarkeit der Laserreinigung hängt eng mit den Materialeigenschaften zusammen. Nicht alle Materialien sind für die Laserreinigung geeignet. Die folgenden Materialien haben bei der Laserreinigung nur begrenzte Anwendungseffekte:
- Reflektierende Oberflächen: Hochreflektierende Materialien wie Aluminium und Edelstahl reflektieren Laserenergie stark, und der Großteil der Laserenergie wird zum Gerät zurückreflektiert, was die Reinigungseffizienz verringert. Darüber hinaus können diese reflektierten Energien die internen optischen Komponenten des Laserreinigungsgeräts beschädigen.
- Transparente Materialien: wie Glas oder einige Kunststoffe absorbieren weniger Laserenergie und die Laserenergie kann nur schwer effektiv auf die Schmutzschicht einwirken, was zu schlechten Reinigungsergebnissen führt. In diesem Fall ist eine bestimmte Wellenlänge oder ein Vorbehandlungsprozess erforderlich, um die Reinigungswirkung zu verbessern.
Geräteausfallzeiten
Aufgrund technischer Probleme kann es gelegentlich vorkommen, dass Laserreinigungsgeräte während des Betriebs ausfallen, was zu Produktionsverzögerungen führt. Hier sind einige häufige Gründe für Ausfallzeiten:
- Ausfall der Laserquelle: Die Laserquelle ist die Kernkomponente der Laserreinigungsanlage. Wenn die Laserquelle ausfällt, muss sie von Fachleuten repariert oder ersetzt werden, was zu langen Ausfallzeiten und höheren Betriebskosten führen kann.
- Ausfall des Kühlsystems: Laserreinigungsgeräte erzeugen bei hoher Leistung viel Wärme, daher ist das Kühlsystem von entscheidender Bedeutung. Wenn das Kühlsystem ausfällt oder nicht ordnungsgemäß gewartet wird, kann das Gerät überhitzen und automatisch abschalten, was den Reinigungsvorgang beeinträchtigt.
Das Verständnis und die wirksame Lösung dieser häufigen Probleme von Laserreinigungsmaschinen ist von großer Bedeutung, um die Reinigungseffizienz zu verbessern, die Betriebskosten der Geräte zu senken und eine sichere Verwendung zu gewährleisten.
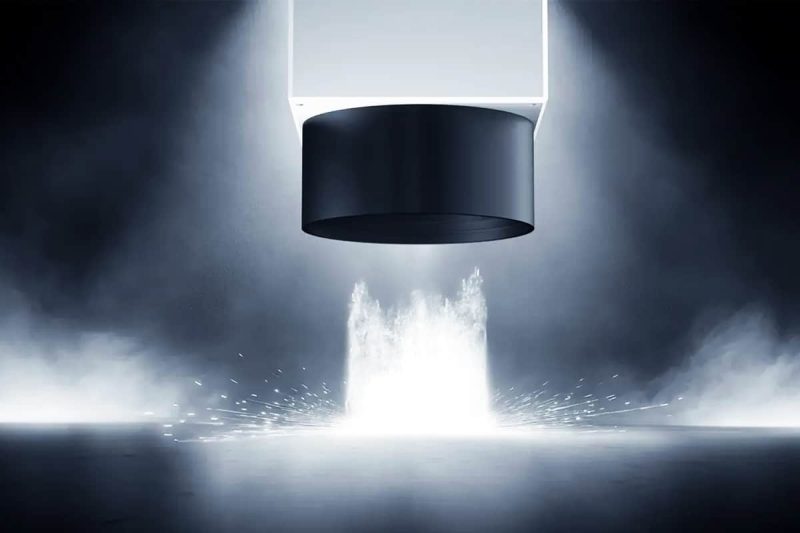
Fehlerbehebung und vorbeugende Maßnahmen
Um einen effizienten und sicheren Betrieb von Laserreinigungsmaschinen zu gewährleisten, ist es wichtig, eine sinnvolle Strategie zur Fehlervermeidung und -behebung zu entwickeln. Dies trägt nicht nur zur Verbesserung der Reinigungseffizienz bei, sondern verlängert auch die Lebensdauer der Geräte und gewährleistet die Sicherheit der Bediener. Im Folgenden finden Sie einige allgemeine Vorschläge zur Fehlervermeidung und -behebung, die die Optimierung der Laserparameter, regelmäßige Wartung, Sicherheitsprotokolle, Materialverträglichkeitsprüfungen und Bedienerschulungen umfassen.
Optimierung der Laserparameter
Je nach Material und Art der Verunreinigungen des Reinigungsobjekts ist es ein wichtiger Teil des Laserreinigungsprozesses, die Laserparameter angemessen anzupassen, um den idealen Reinigungseffekt zu erzielen. Durch Parameteroptimierung kann die Reinigungseffizienz effektiv verbessert, die Beschädigung des Substrats verringert und ein gleichmäßiger Reinigungseffekt sichergestellt werden.
- Pulsdauer: Durch die richtige Einstellung der Dauer des Laserpulses kann die Wärmediffusion auf der Materialoberfläche kontrolliert, die Wärmeeinflusszone auf dem Substrat verkleinert und mögliche Schmelzen oder Mikrorisse verhindert werden. Kürzere Pulsdauern sind in der Regel für empfindliche Materialien geeignet, während längere Pulsdauern bei dicken Verunreinigungen hilfreich sind.
- Impulsenergie: Die Impulsenergie sollte je nach Art der Verunreinigung und des Materials ausgewählt werden, um eine gründliche Reinigung zu gewährleisten. Eine geringere Impulsenergie kann Verunreinigungen möglicherweise nicht effektiv entfernen, während eine zu hohe Energie das Substrat beschädigt. Insbesondere bei Metalloberflächen mit dicken Oxidschichten sollte der Energiebereich angepasst werden, um eine Nachbearbeitung zu vermeiden.
- Wiederholungsrate und Wellenlänge: Die Eigenschaften des Materials bestimmen die optimale Wiederholungsrate und Wellenlänge des Lasers. Beispielsweise erfordern Metallmaterialien oft eine höhere Wiederholungsrate, und die Wellenlänge sollte den Absorptionseigenschaften des Schadstoffs entsprechen. Dies gewährleistet eine bessere Absorption des Schadstoffs und erhöht die Reinigungsgeschwindigkeit.
- Strahlprofil: Die Gleichmäßigkeit der Reinigungswirkung hängt weitgehend von der Gleichmäßigkeit des Laserstrahls ab. Durch die Optimierung des Strahlprofils, um eine gleichmäßige und stabile Strahlverteilung zu erzielen, können nicht nur Spuren auf der gereinigten Oberfläche vermieden, sondern auch lokale Überhitzungen vermieden und die Gesamtreinigungswirkung verbessert werden.
Routinewartung
Die tägliche Wartung der Laserreinigungsmaschine steht in direktem Zusammenhang mit der Stabilität und Lebensdauer des Geräts. Durch die Ausarbeitung eines wissenschaftlichen Wartungsplans und dessen regelmäßige Umsetzung kann die Ausfallrate wirksam gesenkt werden.
- Reinigung der Laseroptik: Optische Komponenten können leicht durch Staub, Öl und andere Verunreinigungen verunreinigt werden, was zu einer Verschlechterung der Strahlqualität führt. Eine regelmäßige Reinigung optischer Linsen, Linsen und Reflektoren kann die Intensität und Klarheit des Strahls aufrechterhalten und den Reinigungseffekt sicherstellen.
- Überprüfung des Kühlsystems: Die Laserreinigungsmaschine erzeugt bei hoher Leistung viel Wärme und das Kühlsystem ist für die Regulierung der Temperatur des Geräts verantwortlich. Eine regelmäßige Überprüfung des Kühlsystems, um einen stabilen Betrieb sicherzustellen, trägt dazu bei, Schäden an der Laserquelle und anderen wichtigen Komponenten durch Überhitzung zu vermeiden.
- Komponentenaustausch: Einige Verbrauchsteile (wie Filter, Kühlmittel, Faserköpfe usw.) müssen rechtzeitig ausgetauscht werden, wenn sie das Ende ihrer Lebensdauer erreichen oder abgenutzt sind, um die Leistung der Geräte aufrechtzuerhalten. Richten Sie einen Ersatzteilbestand für wichtige Komponenten ein, um Notfälle zu bewältigen und die Gerätekontinuität sicherzustellen.
Sicherheitsprotokoll
Beim Laserreinigungsprozess kommen Hochenergielaser zum Einsatz und für den Betrieb der Geräte sind strenge Sicherheitsvorschriften erforderlich, um die Sicherheit des Bedieners und der Arbeitsumgebung zu gewährleisten.
- Schutzausrüstung: Die Laserreinigung kann zu direkten Schäden an Haut und Augen des Bedieners führen. Daher muss der Bediener spezielle Schutzbrillen und Schutzkleidung tragen, um zu verhindern, dass der Laser mit der Haut in Berührung kommt oder direkt in die Augen eindringt. So wird das Risiko versehentlicher Verletzungen verringert.
- Sicherheitsverriegelungsvorrichtung: Die Sicherheitsverriegelungsvorrichtung kann Fehlbedienungen wirksam verhindern, den Betriebsbereich von der Laserquelle isolieren, das Betreten des Reinigungsbereichs durch unbefugtes Personal und ein versehentliches Starten des Geräts verhindern.
- Rauchabsaugsystem: Der bei der Laserreinigung entstehende Rauch und die Partikel wirken sich auf die Luftqualität aus. Ausgestattet mit einem geeigneten Rauchabsaug- und Filtersystem kann die Partikelkonzentration reduziert, das Eindringen von Schadstoffen in die Atemwege des Bedieners verhindert, die Luft sauber gehalten und eine gesunde Arbeitsumgebung gewährleistet werden.
Materialverträglichkeitsprüfung
Die Wirkung der Laserreinigung hängt eng mit den Materialeigenschaften zusammen. Durch die Durchführung von Materialverträglichkeitstests vor der eigentlichen Reinigung können nachteilige Auswirkungen während des Reinigungsvorgangs wirksam vermieden und die Reinigungsqualität sichergestellt werden.
- Reflektivität und Transparenz: Die Reflektivität und Transparenz verschiedener Materialien haben einen großen Einfluss auf den Laserreinigungseffekt. Bei stark reflektierenden Materialien (wie Aluminium, Edelstahl) und transparenten Materialien (wie Glas, Kunststoff) sollte die Laserabsorptionswirkung des Materials getestet und die Laserwellenlänge oder -parameter bei Bedarf angepasst werden, um sie an die Materialeigenschaften anzupassen.
- Vorbehandlung: Einige stark reflektierende oder spezielle Materialien können vor der Reinigung vorbehandelt werden, z. B. durch Auftragen einer absorbierenden Beschichtung, um die Absorptionsrate des Lasers durch das Material zu erhöhen. Dieser Vorgang kann die Reinigungswirkung effektiv verbessern und sicherstellen, dass die Schmutzschicht effektiv entfernt wird.
Schulung und Kompetenzentwicklung
Erfahrene Bediener können nicht nur die Reinigungseffizienz effektiv verbessern, sondern auch das Risiko von Bedienungsfehlern und Geräteschäden verringern. Daher sind Schulungen und die Weiterentwicklung der Fähigkeiten der Bediener von entscheidender Bedeutung.
- Schulung des Bedieners: Die Bediener müssen die Grundprinzipien, Betriebsverfahren, Parametereinstellungen und andere Kenntnisse der Geräte beherrschen, um sicherzustellen, dass jeder Vorgang den Standards entspricht. Der Schulungsinhalt sollte den korrekten Betrieb der Geräte, die Einstellung der Laserparameter und die Notfallbehandlung häufiger Fehler abdecken.
- Kompetenzentwicklung: Mit der Weiterentwicklung der Laserreinigungstechnologie müssen Bediener ihre Fähigkeiten kontinuierlich verbessern, neue Technologien und Fehlerdiagnosemethoden erlernen, um komplexe Reinigungsanforderungen besser bewältigen zu können. Regelmäßiger technischer Austausch, spezielle Schulungen und praktische Übungen können es Bedienern ermöglichen, Reinigungsaufgaben effizienter und sicherer zu erledigen.
Zusammenfassend lässt sich sagen, dass die oben genannten Präventions- und Behandlungsmaßnahmen den effizienten und sicheren Betrieb von Laserreinigungsgeräten zuverlässig unterstützen. Durch regelmäßige Wartung, Parameteroptimierung, sicheren Betrieb, Materialverträglichkeitsprüfung und Personalschulung kann die Ausfallrate von Laserreinigungsmaschinen effektiv gesenkt und die Leistung und Lebensdauer der Geräte verbessert werden.
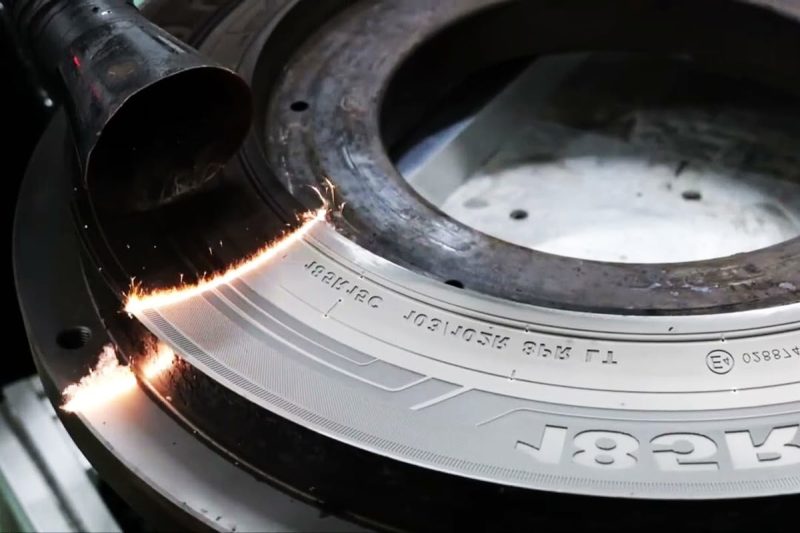
Zusammenfassen
Als effiziente und umweltfreundliche Reinigungslösung wird die Laserreinigungstechnologie häufig in der Industrie, im verarbeitenden Gewerbe, beim Schutz kultureller Relikte und in anderen Bereichen eingesetzt. In der Praxis können Benutzer jedoch mit Herausforderungen wie unzureichender Reinigungseffizienz, Geräteausfallzeiten und Materialverträglichkeit konfrontiert werden. Eine unzureichende Reinigungseffizienz ist häufig auf falsche Laserparametereinstellungen, Probleme mit der Strahlqualität und Unterschiede bei den Schadstoffarten zurückzuführen. Durch die Optimierung von Energie, Dauer, Wiederholungsrate und Wellenlänge des Laserimpulses können die Reinigungsergebnisse deutlich verbessert werden. Darüber hinaus gewährleisten regelmäßige Gerätewartungen und Materialverträglichkeitsprüfungen die Effizienz und Zuverlässigkeit des Reinigungsvorgangs.
Sicherheit ist auch ein wichtiger Aspekt der Laserreinigung. Der Betrieb von Hochenergielasern erfordert die strikte Einhaltung von Sicherheitsprotokollen, um die Sicherheit der Bediener zu gewährleisten. Die Laserreinigungsmaschinen von AccTek verfügen über mehrere Sicherheitsvorkehrungen wie Sicherheitsverriegelungen und Rauchabzugssysteme, um Betriebsrisiken wirksam zu reduzieren. Gleichzeitig bieten wir detaillierte Bedienschulungen an, um sicherzustellen, dass die Bediener die Fähigkeiten zur Gerätenutzung und Notfallmaßnahmen beherrschen und so potenzielle Ausfälle reduzieren.
Kurz gesagt, obwohl die Laserreinigungstechnologie mit vielen Herausforderungen konfrontiert ist, können Unternehmen durch wirksame Präventivmaßnahmen und die hochwertigen Geräte und Dienstleistungen von AccTek die wichtige Rolle der Laserreinigung in verschiedenen Branchen voll ausschöpfen und effizientere und umweltfreundlichere Produktionsmethoden fördern. Wir sind bestrebt, Kunden dabei zu unterstützen, den Reinigungsprozess zu optimieren und die Zuverlässigkeit der Geräte zu verbessern, um so den Reinigungseffekt zu maximieren und einen höheren Wert für die Benutzer zu schaffen.
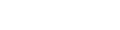
Kontaktinformationen
- [email protected]
- [email protected]
- +86-19963414011
- Nr. 3 Zone A, Industriegebiet Lunzhen, Stadt Yucheng, Provinz Shandong.
Holen Sie sich Laserlösungen