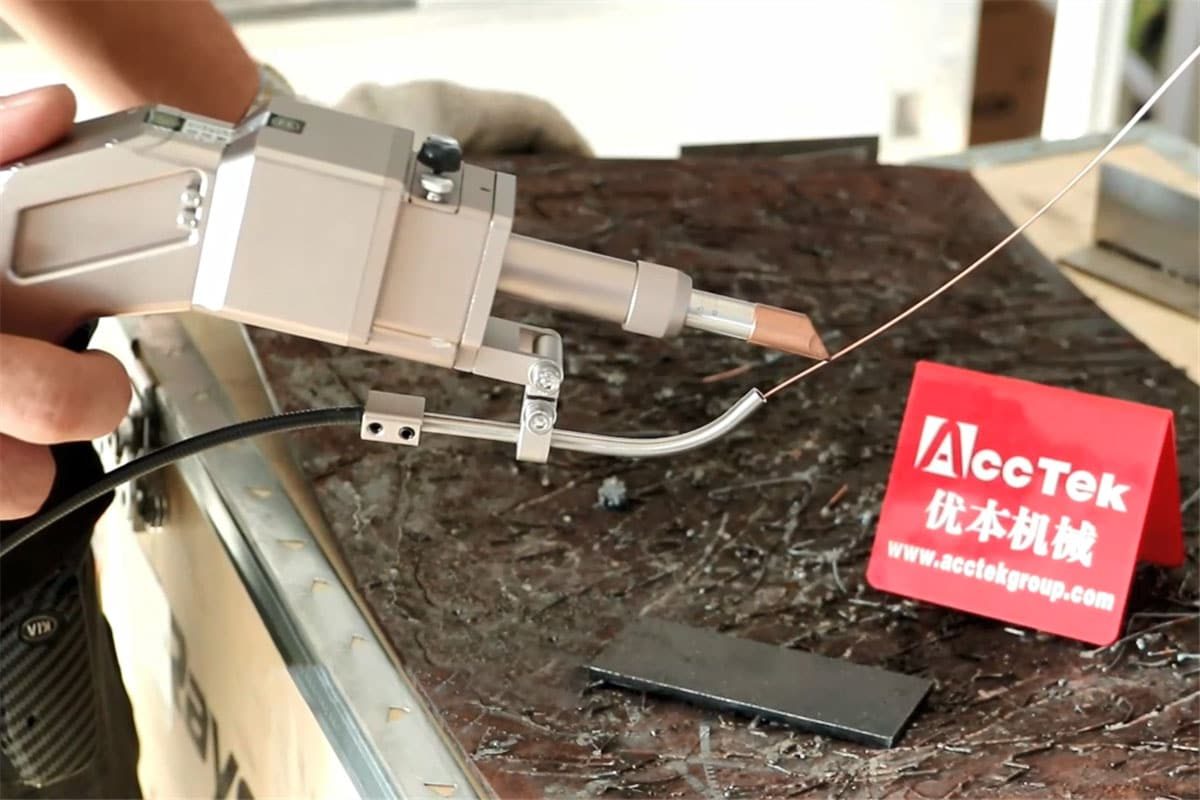
Does Laser Welding Require The Use of Welding Wire?
Welding is a basic process in automobile manufacturing, construction and various industries that require the joining of metal materials. In recent years, laser welding has gained popularity due to its precision, speed and ability to weld a wide range of materials. While traditional welding methods often rely on consumable materials like welding wire, one common question that arises when discussing laser welding is whether it requires the use of welding wire. In this comprehensive article, we will examine the fundamentals of laser welding, explore the various laser welding techniques, and determine whether or not the use of welding wire is necessary. Finally, you will have a clear understanding of the different aspects of laser welding and the role of the welding wire in the process.
Table of Contents
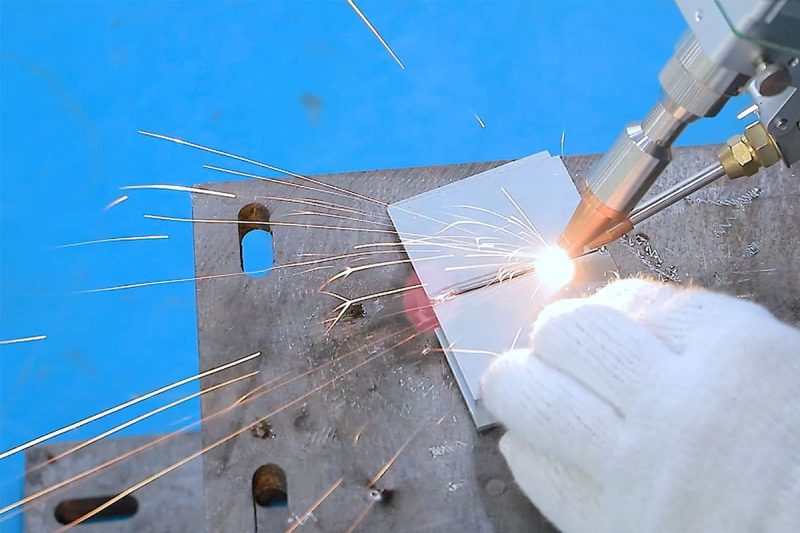
Understanding laser welding
Laser welding is a highly versatile and precise welding method that offers numerous advantages in terms of speed, accuracy, and minimal heat-affected zones. Before discussing the role of welding wire in laser welding, let’s first understand basic laser welding information.
What is laser welding?
Laser welding is a process that joins metal materials together through the use of a high-energy laser beam. The fundamental principle behind laser welding involves concentrating a highly focused laser beam onto the material’s surface, creating a localized melt zone. This molten region is where the welding occurs, and upon cooling, it forms a strong bond. Unlike traditional welding methods that use an electric arc or flame, laser welding relies on the intense heat generated by the laser.
What materials can laser welding be used for?
Laser welding can be applied to stainless steel, carbon steel, aluminum, titanium, and other metal materials. Laser welding’s compatibility with different materials is one of its strengths. The ability to weld dissimilar materials is particularly valuable in certain applications. For instance, in the automotive industry, laser welding is used to join steel and aluminum components. Materials compatibility is determined by the materials’ melting points, thermal conductivities, and other physical properties.
What types of laser welding are there?
Laser welding comes in various types, including continuous wave (CW) laser welding and pulsed laser welding. CW laser welding provides a continuous, uninterrupted beam that is ideal for high-speed welding applications. Pulsed laser welding, on the other hand, involves intermittent laser pulses that allow for better control over heat and are often used in precision welding.
What are the advantages of laser welding?
As a new welding technology, laser welding offers numerous advantages, including:
- High Welding Precision: Laser welding is highly precise, making it ideal for applications where accuracy is crucial.
- Fast Welding Speed: The high energy density of the laser beam allows for rapid welding, increasing productivity.
- Minimal Heat Affected Zone (HAZ): Laser welding generates a small HAZ, reducing the risk of material distortion or damage.
- Minimal Distortion: The precise control of the laser beam minimizes distortion in the welded materials.
- Automation: It is easily adaptable for automated systems, further enhancing welding efficiency.
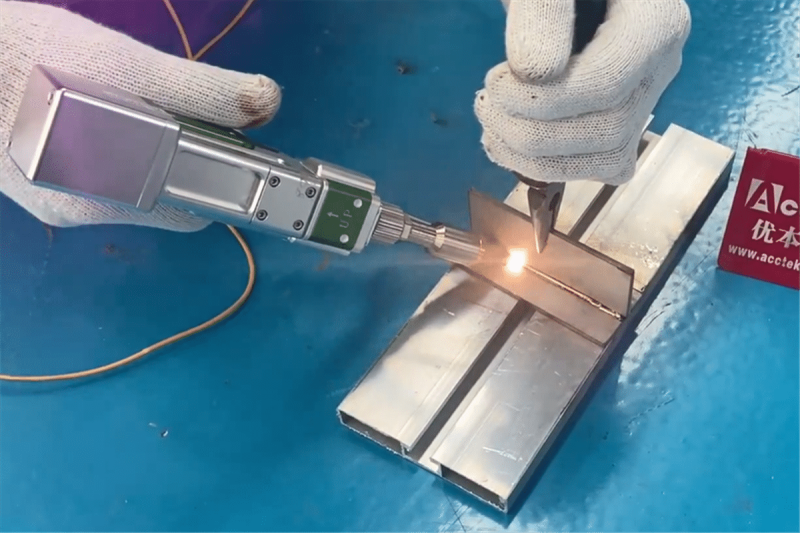
Advantages and disadvantages of using welding wire in laser welding
As introduced above, in some applications, using welding wire will achieve better laser welding quality, but there are also some disadvantages and limitations. Here are the advantages and disadvantages of using welding wire for laser welding.
Advantages
- Improved Joint Quality: Welding wire can enhance the quality of the weld by filling gaps, ensuring proper fusion, and reducing the risk of defects. In addition, the addition of filler wire can significantly improve the strength of the weld, making it suitable for demanding applications.
- Controlled Heat Input: Welding wire allows for precise control over heat input, which is critical in applications where overheating can lead to material distortion or other issues.
- Enhanced Productivity: In some cases, the use of welding wire can lead to faster welding speeds, improving productivity.
- Bridging Gaps: Filler wire is invaluable when dealing with materials that have irregular or inconsistent joint gaps.
- Alloy Compatibility: Using a filler wire of the appropriate alloy ensures compatibility with the base materials, reducing the risk of incompatibility issues. It enables the joining of dissimilar materials and variable thicknesses, expanding the range of applications for laser welding.
- Improved Process Control: During the welding process, filler wire provides welders with greater control over the weld pool, making it easier to achieve the desired results.
Disadvantages
- Material Selection: Not all materials require filler wire in laser welding. Selecting the appropriate base material and filler wire can help achieve a successful weld.
- Process Complexity: The integration of wire feed mechanisms and filler materials can increase the complexity of the welding process, requiring a higher level of skill and expertise.
- Cost: The cost of welding wire and the associated equipment can add to the overall expenses of the welding process. So it should be used judiciously, considering the cost-benefit ratio.
- Material Waste: The use of welding wire can generate waste material, especially in applications where excess wire is trimmed.
- Weld Quality: The skill of the welder and the choice of welding parameters are critical in ensuring the quality of the weld when using filler wire.
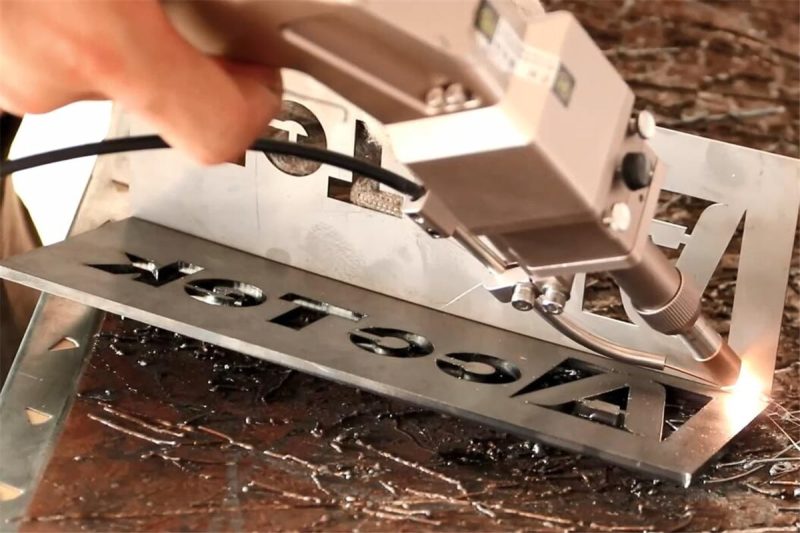
Laser welding technology demand for welding wire
To understand the necessity of welding wire in laser welding, it’s essential to compare this process to traditional welding methods. In traditional welding, a filler material, often in the form of a welding wire, is used to bridge gaps and create a stronger joint. In contrast, laser welding encompasses several techniques, each with its own set of advantages and applications. These techniques determine whether the use of welding wire is necessary. Let’s explore some of the most common laser welding methods:
Conduction mode welding
Conduction mode welding, also known as heat conduction welding, is a laser welding technique used for thin materials and when precise control is required. In this method, the laser beam generates heat at the surface of the materials, causing them to melt and fuse together. Conduction mode welding typically does not require the use of welding wire, as the materials themselves form the weld pool.
Keyhole mode welding
Keyhole mode welding is primarily used for thicker materials and applications where deeper penetration is necessary. In this method, the laser beam creates a keyhole in the materials by vaporizing a portion of the material. This keyhole is then filled with molten material, creating a strong weld. While keyhole mode welding often does not require welding wire, there are situations where using welding wire can be beneficial, such as increasing joint strength or bridging gaps in materials.
Hybrid welding
Hybrid welding combines laser welding with other welding techniques, such as gas metal arc welding (GMAW) or tungsten inert gas (TIG) welding. In hybrid welding, a laser beam is used in conjunction with traditional welding processes, and the use of welding wire depends on the specific application and the chosen welding method. This technique offers greater flexibility but may require the use of welding wire when using GMAW or TIG welding in combination with the laser.
Pulsed laser welding
Pulsed laser welding combines the benefits of conduction and keyhole modes. It involves intermittent laser pulses that provide greater control over the heat input, is suitable for a wide range of materials, often without the need for welding wire. This mode is widely used in precision welding applications and can be adapted to use welding wire when necessary to meet specific requirements.
Laser welding with filler wire
In some laser welding applications, especially when joining dissimilar materials or filling gaps between materials, the use of welding wire, also known as filler wire, becomes essential. Filler wire is a metal wire that is added to the weld pool during the laser welding process. It provides additional material to ensure a complete and strong weld, especially when dealing with materials that have different thermal properties.
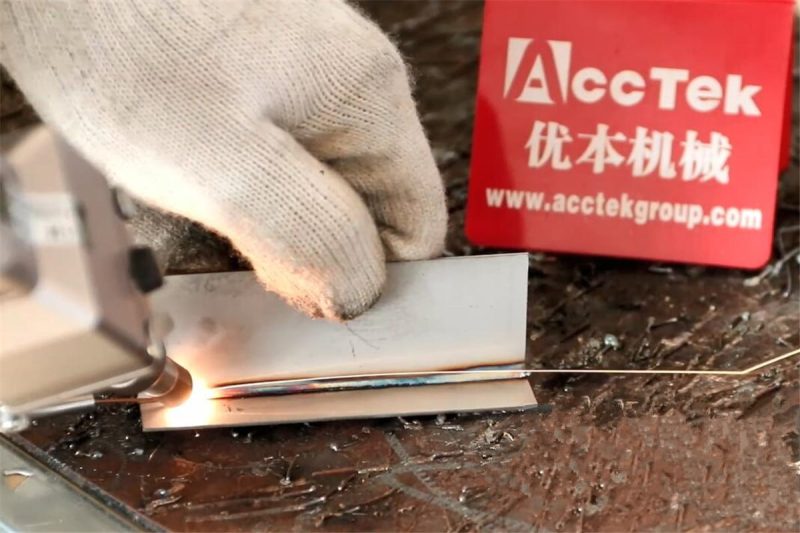
When is welding wire necessary in laser welding?
Now that we’ve explored different laser welding techniques, we have learned that welding wire is very important for successful laser welding results. In many cases, laser welding can be performed without welding wire, thanks to the precision and control it offers. However, there are instances where welding wire is advantageous. Several factors determine the need for filler wire in laser welding:
- Material Type: The type of material being welded plays a significant role in determining whether welding wire is required. For materials with similar melting points, like stainless steel to stainless steel, the need for welding wire may be minimal. However, when welding dissimilar materials with significantly different thermal properties, using welding wire can improve joint quality and bridge gaps, helping to maintain a balanced weld and ensure a reliable bond. For instance, when joining aluminum to steel, a filler wire made of a compatible alloy can be used.
- Gap Bridging: Laser welding is highly precise, but it may struggle to bridge larger gaps between materials. In such cases, welding wire can be used to fill the gap and create a robust connection.
- Joint Strength: Complex joint designs or applications with specific requirements may necessitate the use of welding wire to optimize the welding process. Depending on the application, additional material from welding wire can enhance the overall strength and durability of the weld.
- Accuracy Requirements: In some cases, using filler wire can provide better control of the molten pool, especially when welding accuracy is critical.
- Process Efficiency: While laser welding is fast, the use of filler wire can further enhance process efficiency and speed by ensuring consistent weld quality.
- Material Thickness: The thickness of the materials being joined is an essential factor in laser welding. Thinner materials require less heat input, making them suitable for conduction mode welding without the need for welding wire. In contrast, thicker materials may benefit from the use of welding wire to ensure a complete fusion and robust weld joint.
- Specific Applications: The decision to use welding wire in laser welding also depends on the specific application’s requirements. Such as the need for structural integrity, corrosion resistance, or hermetic sealing, will guide the choice of whether welding wire should be used in laser welding. Applications with stringent quality standards may opt for welding wire to ensure reliable and robust welds. In contrast, applications that prioritize speed and cost-efficiency may opt for minimal or no welding wire.
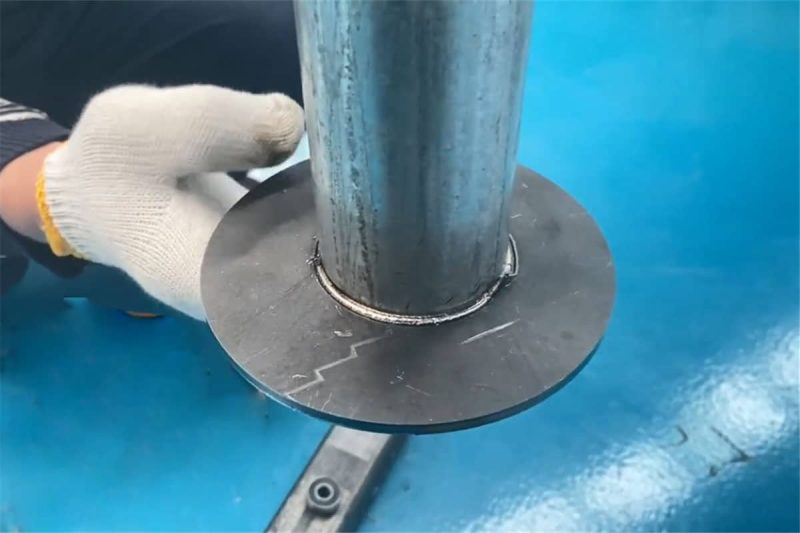
How to get the best laser welding results when using welding wire
When using welding wire in laser welding, it’s essential to follow best practices to achieve optimal results:
- Select the Right Filler Wire: Choose a welding wire that is compatible with the base materials in terms of alloy and properties.
- Precise Control: Adjust the laser parameters and welding conditions to ensure precise control over the welding process.
- Weld Pool Management: Maintain proper management of the weld pool to ensure the even distribution of the filler wire and to prevent irregularities.
- Quality Assurance: Implement quality control measures to verify the integrity and strength of the welds, such as non-destructive testing.
Summarize
In summary, the necessity of wire in laser welding depends on a variety of factors and should be determined based on the unique needs of each welding project. While some laser welding techniques do not require the use of welding wire, especially in applications where speed and efficiency are a priority. However, in industries with stringent quality standards and complex joint configurations, the use of wire in laser welding remains a valuable and reliable option. Understanding the role of welding wire in laser welding is critical for professionals in the field, as well as those seeking to utilize laser welding technology for industrial production.
At AccTek Laser, the laser welding machines we provide you are equipped with automatic wire feeders, and you can choose whether to use welding wire according to your actual welding needs. If you want to get more information about laser welding machines, you can contact us at any time. Our professional sales team will provide you with complete solutions based on your specific application and provide you with detailed pricing information.
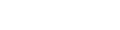
Contact information
- [email protected]
- [email protected]
- +86-19963414011
- No. 3 Zone A, Lunzhen Industrial Zone,Yucheng City , Shandong Province.
Get Laser Solutions